表面粗糙度数
常用零件表面粗糙度参数值
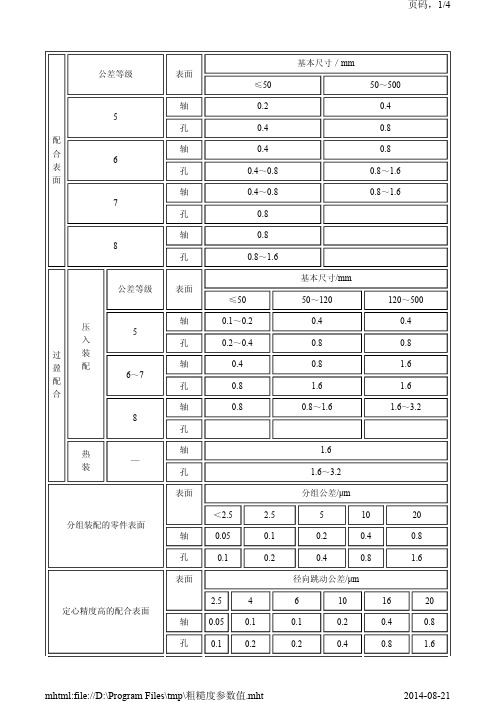
公差等级
5
配
合
表
6
面
7
8
公差等级
压 入 过装 盈配 配 合
热 装
5 6~7
8 —
分组装配的零件表面
定心精度高的配合表面
表面
轴 孔 轴 孔 轴 孔 轴 孔
表面
轴 孔 轴 孔 轴 孔
≤50 0.2 0.4 0.4 0.4~0.8 0.4~0.8 0.8 0.8 0.8~1.6
≤50 0.1~0.2 0.2~0.4
页码,4/4
50~100 12.5~25 100或更大 0.2~0.4抛光 0.2抛光 0.8~1.6
1.6~3.2 6.3
15.2~52
mhtml:file://D:\Program Files\tmp\粗糙度参数值.mht
2014-08-21
0.4 0.8 0.8
3.2
蜗杆牙型面
0.1 0.2 0.2 0.4 0.4 0.8 1.6 ~ ~1.6 ~
0.8
3.2
根圆
和工作面同或接近的更粗的优先数
顶圆
3.2~12.5
应 用 精度
普通的
提高的
链轮
工作表面
3.2~6.3
1.6~3.2
根圆
6.3
3.2
顶圆
3.2~12.5
3.2~12.5
定位精度/μm
0.8
1.6
3.2
0.1
0.2
0.4
0.8
1.6
0.1
0.2
0.4
0.8
1.6
0.05
0.1
0.2
0.4
0.8
密封结合
零件上有配合要求或有相对运动的表面粗糙度参数值
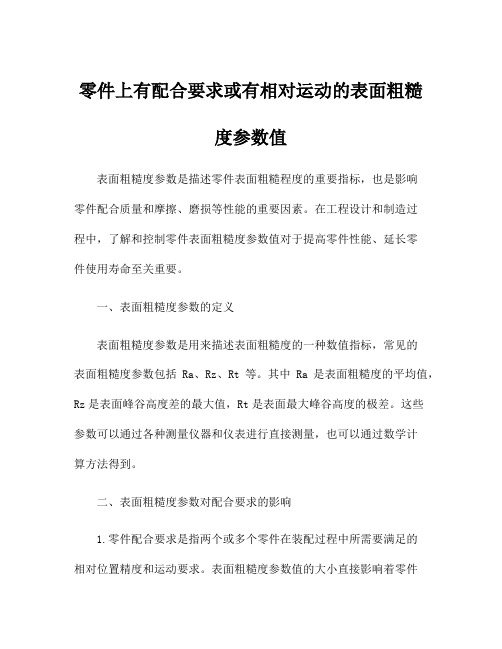
零件上有配合要求或有相对运动的表面粗糙度参数值表面粗糙度参数是描述零件表面粗糙程度的重要指标,也是影响零件配合质量和摩擦、磨损等性能的重要因素。
在工程设计和制造过程中,了解和控制零件表面粗糙度参数值对于提高零件性能、延长零件使用寿命至关重要。
一、表面粗糙度参数的定义表面粗糙度参数是用来描述表面粗糙度的一种数值指标,常见的表面粗糙度参数包括Ra、Rz、Rt等。
其中Ra是表面粗糙度的平均值,Rz是表面峰谷高度差的最大值,Rt是表面最大峰谷高度的极差。
这些参数可以通过各种测量仪器和仪表进行直接测量,也可以通过数学计算方法得到。
二、表面粗糙度参数对配合要求的影响1.零件配合要求是指两个或多个零件在装配过程中所需要满足的相对位置精度和运动要求。
表面粗糙度参数值的大小直接影响着零件的配合要求。
一般来说,表面粗糙度参数值越大,零件的配合质量越差,配合间隙越大,相对运动时的摩擦和磨损也会增加。
2.当零件的配合要求较高时,需要控制表面粗糙度参数值在一定的范围内,以保证零件的配合质量。
在一些精密零件的设计和制造过程中,需要对表面粗糙度进行严格的控制和检查,以确保零件的配合要求得到满足。
三、表面粗糙度参数对相对运动的影响1.表面粗糙度参数值的大小会对零件的相对运动产生影响。
在两个相对运动的表面之间,如果表面粗糙度参数值较大,会增加摩擦力和磨损,影响零件的运动性能和使用寿命。
2.通过合理控制表面粗糙度参数值,可以减少零件的摩擦和磨损,提高零件的运动性能和使用寿命。
在一些需要进行相对运动的零件中,合理选择表面粗糙度参数值,能够有效地减少能量损耗和材料磨损,延长零件的使用寿命。
四、控制表面粗糙度参数值的方法1.在零件设计阶段,可以通过合理设计零件的表面形状和加工工艺,选择适当的加工方法和工艺参数,来控制表面粗糙度参数值。
选择合理的刀具和切削速度、进给量等加工参数,可以有效地减小表面粗糙度。
2.在零件加工过程中,可以通过加工前的表面粗糙度检查和加工后的表面粗糙度检测,及时调整加工参数,对零件表面进行细微加工,以保证零件的表面粗糙度参数值在允许范围内。
表面粗糙度数值的含义
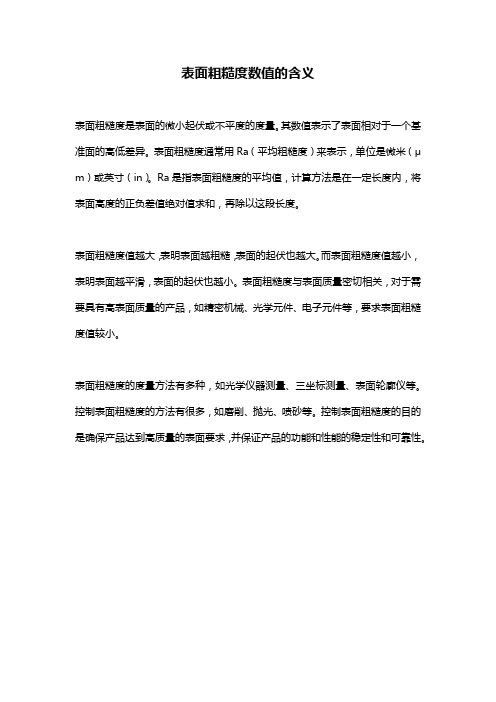
表面粗糙度数值的含义
表面粗糙度是表面的微小起伏或不平度的度量。
其数值表示了表面相对于一个基准面的高低差异。
表面粗糙度通常用Ra(平均粗糙度)来表示,单位是微米(μm)或英寸(in)。
Ra是指表面粗糙度的平均值,计算方法是在一定长度内,将表面高度的正负差值绝对值求和,再除以这段长度。
表面粗糙度值越大,表明表面越粗糙,表面的起伏也越大。
而表面粗糙度值越小,表明表面越平滑,表面的起伏也越小。
表面粗糙度与表面质量密切相关,对于需要具有高表面质量的产品,如精密机械、光学元件、电子元件等,要求表面粗糙度值较小。
表面粗糙度的度量方法有多种,如光学仪器测量、三坐标测量、表面轮廓仪等。
控制表面粗糙度的方法有很多,如磨削、抛光、喷砂等。
控制表面粗糙度的目的是确保产品达到高质量的表面要求,并保证产品的功能和性能的稳定性和可靠性。
金属表面粗糙度参数表

金属表面粗糙度参数一览表
表面粗糙度是指加工表面所具有的较小间距和微小峰谷的微观几何形状的尺寸特征。
工件加工表面的这些微观几何形状误差称为表面粗糙度。
1 表面粗糙度的评定参数
按国家标准规定,表面粗糙度的评定参数应在轮廓算术平均偏差(R a)、微观平面度十点高度(R z和轮廓最大高度(R y)项目中选取。
国家标准推荐优先选用R a。
有关R a、R z、R y参数的数值如下:
(1)轮廓算术平均偏差R a的数值,如表1所示。
表1 轮廓算术平均偏差R a的数值/μm
(2)微观平面度十点高度R z和轮廓最大高度R y的数值,如表2所示。
表2 微观平面度十点高度Rz和轮廓最大高度Ry的数值 /μm
2 表面粗糙度代(符)号
表面粗糙度代(符)号如表3所示
表3 表面粗糙度代(符)号
各级表面粗糙度的表面特征、经济加工方法及应用举例如表4所示。
表4 各级表面粗糙度的表面特征、经济加工方法及应用举例。
第一节表面粗糙度的评定参数

❖ 1.L 2 表面粗糙度测量的基本原则
❖
(1)测量方向
❖ 按现行标准所定义的各种粗糙度评定参数,是基于轮廓法确定数值,是在被测表面的法向截面上的 实际轮廓上进行测量的结果。由于垂直于被测表面的法向截面存在各种不同的测量方向.所以规定在垂 直于加工纹理力向的d向截面(参R图g”8)测得的结果,称作横向轮廊的表面粗糙度数值(d);在平行于加 工纹理方向的5向截面上所作的测量,称为纵向轮廓的粗糙度数值(6)。试验表明,大多数的切削加工表
2.表面粗糙度:是一种微观几何形状误差又称微观不平度。 3.表面粗糙度的产生原因:在加工过程中,刀具和零件表面
间产生磨擦、高频振动及切削时在工作表面上留下的微观 痕迹。
二.表面粗糙度的影响
❖ 表面粗糙度对机器零件的使用性能有着重要的影响,主要表 现在:
1.对摩擦和磨损的影响 2.对配合性的影响 3.对接触刚度的影响 4.对疲劳强度的影响 5.对抗腐蚀性的影响 6.对结合密封性的影响 ❖ 此外表面粗糙度还影响检验零件时的测量不确定度、零件外
1、轮廓算术平均偏差Ra
在取样长度L内,轮廓偏转距绝对值的算术平均值。
用公式表示为:
1l
Ra L 0 y(x) dx
Ra
1 n
n i 1
yi
Rz
图4-3 表面粗糙度的高度参数
2.微观不平度十点高度
❖ 在取样长度内五个最大的轮廓峰高的平均值与五个最大的轮
廓谷深的平均值之和,如图4-3所示。用公式表示为:
§4-1 表面粗糙度的评定参数
主要内容:
1、主要术语及定义 取样长度L 评定长度L
n
轮廓中线m 2、6个评定参数
3个基本、3个附加 3、一般规定
重点: 3个基本评定参数
表面粗糙度符号及数值说明

表面细糙度标记及其标注证明之阳早格格创做细糙度是衡量整件表面细糙程度的参数,它反映的是整件表面微瞅的几许形状缺面,必须借帮搁大镜等举止丈量.它是由于整件加工历程中刀具与加工表面之间的摩揩、挤压以及加工时的下频振荡等圆里的本果制成的.表面细糙度对付整件的处事细度、耐磨性、稀启性、耐蚀性以及整件之间的协共皆有着曲交的做用.细糙度的评比时常使用表面算术仄衡偏偏好Ra、表面最大下度Ry、微瞅没有服度十面下度Rz三个参数表示.数值越小,整件的表面越光润,数值越大整件的表面越细糙.1、表面算术仄衡偏偏好Ra与样少度:与样少度是指具备细糙度几许特性的一段少度,正在与样少度内该当具备几个波峰战波谷.丈量时可选5倍的与样少度动做丈量少度举止丈量.Ra是指正在与样少度内,表面偏偏距千万于值的算术仄衡值,不妨表示为:闭于表面细糙度的数值战表面特性、赢得要领、应用举例请拜睹下表.从上图中也不妨瞅出,细糙度参数的数值.基础上成倍数的闭系.标注时应当采用那些数值,没有克没有及采用其余的数值.2、表面最大下度Ry3、表面没有服度十面下度Rz标注细糙度代号不妨分为:标记,细糙度名目及数值.时常使用标注参数是Ra, 标注Ra时Ra不妨简略,标注Rz战Ry时,正在细糙度数值前加对付应的标记Rz战Ry.2.2 标注准则1)、正在共一图样上每一致况只注一次细糙度代号,且应注正在可睹表面线、尺寸界线、引出线或者它们的延少线上,并尽大概靠拢有闭尺寸线.2)、当整件的大部分表面具备相共的细糙度央供时,对付其中使用最多的一种,代(符)号,可统一注正在图纸的左上角.并加注“其余”二字.3)、正在分歧目标的表面上标注时,代号中的数字及标记的目标必须下图的确定标注.4)、代号中的数字目标应与尺寸数字的目标普遍.5)、标记的尖端必须从资料中指背表面.标注举例:6)、齿轮、蜗轮齿里对付于齿轮、蜗轮齿里的细糙度,应标注正在表示分度圆的面绘线上.如果图形中的位子有限,细糙度也不妨引出标注或者注正在尺寸线的延少线上.7)、二个表面的细糙度央供相共,也不妨一个标记使用二个指引线.8)、细糙度的数值与尺寸公好具备一定的闭系,普遍标注尺寸公好、形位公好的表面,央供的细糙度数值较矮.用于定位的较要害的仄里普遍采用6.3或者3.2.有协共央供的圆柱里普遍采用1.6或者3.2,要害的定位圆柱里不妨采用0.8或者0.4.简曲采用时应根据整件的处事情况而定,相对付疏通的表面细糙度数值应矮于非疏通表面.。
(完整版)常用表面粗糙度数值

0.1
0.2
0.4
0.8
1.6
定心精度高
的
配合表面
表面
径向跳动公差/ □m
2.5
4
6
10
16
20
轴
0.05
0.1
0.1
0.2
0.4
0.8
孔
0.1
0.2
0.2
0.4
0.8
1.6
滑动轴承
表面
表面
公差 等级
液体润滑
IT6 〜IT9
IT10 〜IT12
轴
0.4〜0.8
0.8〜3.2
0.1〜0.4
孔
0.8〜1.6
1.6〜3.2
0.2〜0.8
导
轨
面
性质
速度
/m • s1
平面度公差/(卩m/100mm)
〜6
10
20
60
>60
滑动
〜0.5
0.2
0.4
0.8
1.6
3.2
>0.5
0.1
0.2
0.4
0.8
1.6
滚动
〜0.5
0.1
0.2
0.4
0.8
1.6
>0.5
0.05
0.1
0.2
0.4
0.8
(转下表)
(续前表)
圆锥结合
3.2〜12.5
分度机构表面
女口:分度板
插销
定位 精度/□m
〜4
6
10
25
63
>63
0.1
0.2
0.4
0.8
1.6
表面光洁度等级与表面粗糙度高度参数推荐转换表
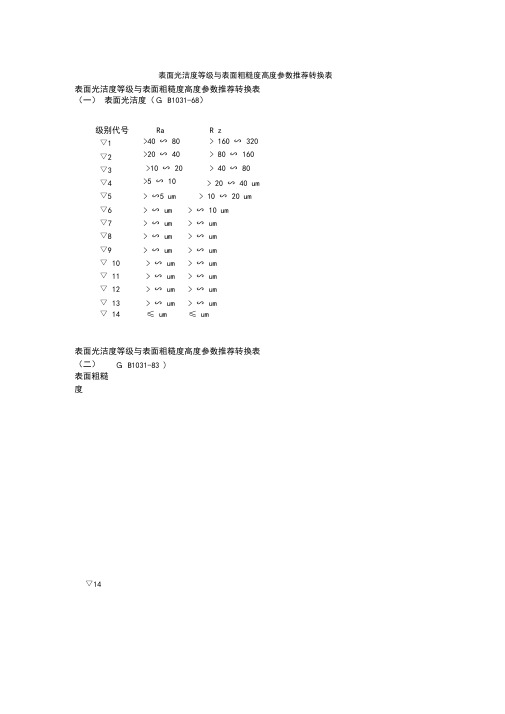
表面光洁度等级与表面粗糙度高度参数推荐转换表▽14表面光洁度等级与表面粗糙度高度参数推荐转换表(一) 表面光洁度(G B1031-68)级别代号 Ra R z▽1 >40 ∽ 80 um > 160 ∽ 320 um ▽2 >20 ∽ 40 um > 80 ∽ 160 um ▽3 >10 ∽ 20 um > 40 ∽ 80 um▽4 >5 ∽ 10 um> 20 ∽ 40 um▽5 > ∽5 um > 10 ∽ 20 um ▽6 > ∽ um > ∽ 10 um ▽7 > ∽ um > ∽ um ▽8 > ∽ um > ∽ um ▽9 > ∽ um > ∽ um ▽ 10 > ∽ um > ∽ um ▽ 11 > ∽ um > ∽ um ▽ 12> ∽ um > ∽ um ▽ 13 > ∽ um > ∽ um ▽ 14≤ um≤ um表面光洁度等级与表面粗糙度高度参数推荐转换表(二) 表面粗糙度G B1031-83 )表面光洁度等级与表面粗糙度高度参数推荐转换表▽14别代Ra R Ⅰz Ⅱ1 50um 100um 80um▽2 25um50um 40um ▽325um 20um▽410um 40um ▽55um 20um▽610um▽7▽8▽9um▽ 10▽ 11▽12▽13 um320um ▽ 160um表面粗糙度值的选用表面粗糙度值的选用实例使用时代TR200 粗糙度仪测量时需要选定取样长度,这又牵涉到被测工件本身的粗糙度范围,摘编本表就是希望对此有帮助。
表面光洁度& 表面粗糙度(2010-06-12 17:40:53)转载标签:分类:机械知识表面光洁度表面粗糙度平均值杂谈此处有很多机械相关的书本或教材,不错的一.表面光洁度是表面粗糙度的旧标准它们的对应关系 :表面光洁度 14 级 =Ra表面光洁度 13 级 =Ra表面光洁度 12 级 =Ra表面光洁度 11 级 =Ra表面光洁度 10 级 =Ra表面光洁度 9 级 =Ra表面光洁度 8 级 =Ra表面光洁度 7 级 =Ra表面光洁度 6 级 =Ra表面光洁度 5 级 =Ra表面光洁度 4 级 =Ra表面光洁度 3 级=Ra 25表面光洁度 2 级=Ra 50表面光洁度 1 级=Ra 100 以上表面粗糙度单位均为μ m,即微米 =10^-6 米。
表面粗糙度数值

表面粗糙度数值
表面粗糙度是表明表面技术性能的重要指标。
它直接关系到产品质量和稳定性。
表面粗糙度的规定可以从表面粗糙度的数值上来看:
①Ra:粗糙度半径(表面光滑程度和斜度),可测量物体表面不规则性的程度。
Ra的取值为0.1μm~1.25μm。
②Rz:相邻峰值上高度差,即表面粗糙高度,表示物体表面细微的凹凸不平度。
Rz部位取值为2.5μm~6.3μm。
③Rmax:表面深坑最大深度,取值为2.5μm~25μm。
④Ry:表面深坑最高处和表面主线之间的高度,多指表面凹凸度,取值为0.8μm~3.2μm。
⑤Sm:表面的垂直精度、梯度角,取值由0.001~25,决定表面形状的平滑程度。
⑥Sv:表面平缓行进距离,取值为2μm~50μm。
为保证产品质量,应选择合适的表面粗糙度数值。
根据表面粗糙度,一般情况下Ra值在0.3~3.2μm,Rz值在6.3μm以下,Rmax值在
2.5~25μm之间,Ry值在1.6~
3.2μm之间,Sm值在0.001~2,
Sv值在2~50μm之间。
此外,表面粗糙度的取值也可以根据具体的使用条件和相关的机械表
面性能参数来确定。
例如,在尺寸检测中,通常可以根据Ra值、不同
表面质量等级的数值确定表面状态;同时也应考虑到表面的机械性能,比如耐磨性和抗腐蚀性等参数的取值。
为满足日益增长的客户需求,合理的表面粗糙度规范无疑可以更好地
满足客户的要求,并有助于形成行业规范和标准。
表面粗糙度的评定标准及方法

表面粗糙度的评定标准及方法当钢材表面经喷射清理后,就会获得一定的表面粗糙度或表面轮廓。
表面粗糙度可以用形状和大小来进行定性。
经过喷射清理,钢板表面积会明显增加很多,同时获得了很多的对于涂层系统有利的锚固点。
当然,并不是粗糙度越大越好,因为涂料必须能够覆盖住这些粗糙度的波峰。
太大的粗糙度要求更多的涂料消耗量。
一般的涂料系统要求的粗糙度通常为 Rz40~75微米.1.粗糙度的定义对表面粗糙度的定义有以下几种:hy:在取样长度内,波峰到波谷的最大高度, ISO8503—3(显微镜调焦法)Ry:在取样长度内,波峰到波谷的最大高度,ISO8503—4(触针法)Ra:波峰和波谷到虚构的中心线的平均距离, ISO 3274Ry5:在取样长度内,五个波峰到波谷最大高度的算术平均值,ISO8503—4(触针法)有关 Rz的表述与 Ry5其实是相同的,Rz的表述来自于德国标准 DIN 4768-1.Ra和 Rz 之间的关系是 Rz相当于 Ra 的 4~6倍。
2. 表面粗糙度的评定标准为了测定钢板表面粗糙度,不同的标准规定了相应的仪器可以使用,测量值以微米(µm)为单位。
国际标准分 ISO 8503 成五个部分在来说明表面粗糙度:ISO8503—1:1995表面粗糙度比较样块的技术要求和定义ISO8503-2:1995喷射清理后钢材表面粗糙度分级―样板比较法ISO8503-3:1995 ISO基准样块的校验和表面粗糙度的测定方法―显微镜调焦法ISO8503—4:1995 ISO基准样块的校验和表面粗糙度的测定方法,触针法ISO8503-5:2004表面轮廓的复制胶带测定法我国的国家标准 GB/T 13288-91《涂装前钢材表面粗糙度等级的评定(比较板块法)》,参照 ISO8503所制订。
3。
比较样块法评定表面粗糙度在涂装现场较为常用的粗糙度评定方法是比较样块法。
常用的粗糙度比较块有英国易高elcometer125,荷兰TQC LD2040、LD2050以及英国PTE R2006、R2007等。
表面粗糙度符号及数值说明 (1)
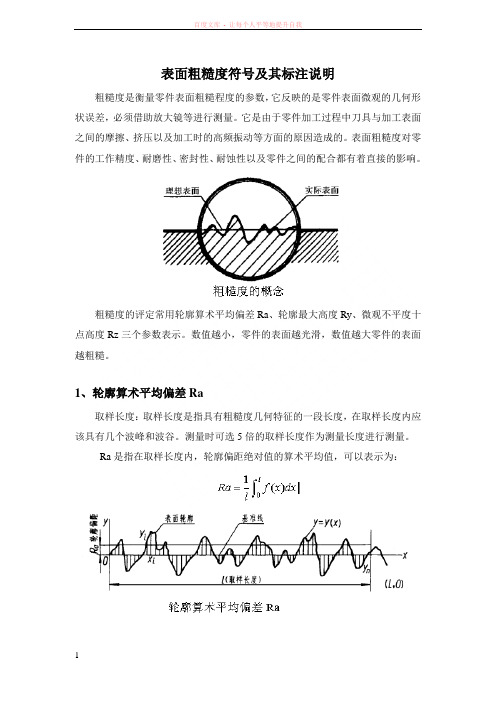
表面粗糙度符号及其标注说明粗糙度是衡量零件表面粗糙程度的参数,它反映的是零件表面微观的几何形状误差,必须借助放大镜等进行测量。
它是由于零件加工过程中刀具与加工表面之间的摩擦、挤压以及加工时的高频振动等方面的原因造成的。
表面粗糙度对零件的工作精度、耐磨性、密封性、耐蚀性以及零件之间的配合都有着直接的影响。
粗糙度的评定常用轮廓算术平均偏差Ra、轮廓最大高度Ry、微观不平度十点高度Rz三个参数表示。
数值越小,零件的表面越光滑,数值越大零件的表面越粗糙。
1、轮廓算术平均偏差Ra取样长度:取样长度是指具有粗糙度几何特征的一段长度,在取样长度内应该具有几个波峰和波谷。
测量时可选5倍的取样长度作为测量长度进行测量。
Ra是指在取样长度内,轮廓偏距绝对值的算术平均值,可以表示为:关于表面粗糙度的数值和表面特征、获得方法、应用举例请参见下表。
从上图中也可以看出,粗糙度参数的数值.基本上成倍数的关系。
标注时应当选用这些数值,不能选用其他的数值。
2、轮廓最大高度Ry3、轮廓不平度十点高度Rz标注2.1代号及意义粗糙度代号可以分为:符号,粗糙度项目及数值。
常用标注参数是Ra, 标注Ra时Ra可以省略,标注Rz和Ry时,在粗糙度数值前加对应的符号Rz和Ry。
2.2 标注原则1)、在同一图样上每一表面只注一次粗糙度代号,且应注在可见轮廓线、尺寸界线、引出线或它们的延长线上,并尽可能靠近有关尺寸线。
2)、当零件的大部分表面具有相同的粗糙度要求时,对其中使用最多的一种,代(符)号,可统一注在图纸的右上角。
并加注“其余”二字。
3)、在不同方向的表面上标注时,代号中的数字及符号的方向必须下图的规定标注。
4)、代号中的数字方向应与尺寸数字的方向一致。
5)、符号的尖端必须从材料外指向表面。
标注举例:6)、齿轮、蜗轮齿面对于齿轮、蜗轮齿面的粗糙度,应标注在表示分度圆的点画线上。
如果图形中的位置有限,粗糙度也可以引出标注或注在尺寸线的延长线上。
GB/T1031-2009《产品几何技术规范(GPS)表面结构轮廓法表面粗糙度参数及其数值》介绍

踩 寸 寸躲 距 ∞0 0 .l
机 械
工
业
标
准
化 与 质
量
GB T 1 3 - 2 0 产 品几何技术规 0 0 9《 / 1 - 范 ( GP S)表 面 结构 轮廓 法 表 面 粗糙度参数及其数值》介绍
0 1 m~ 5 m)推荐优 先 选 用 。根据 表 面功 .u 2 p 能 的需 要 ,除 表 面粗 糙度 高 度参 数 ( a R ) R 、 z 外 可选 用轮 廓单 元 的平均 宽度—— , 和轮 廓 7 7
的支承 长度率—— r( )附加 参数 。 C
R z相当于 旧标准中高度参数 尺 ,数值保持不变。
表 3 轮 廓 单 元 的 平 均 宽 度 R m 的 数 值 s
00 6 .o O0l 5 . 2
Rs m
m m
16 . 32 . 63 .
l . 25
01 . 02 . 04 .
08 .
00 5 .2
0. 05
表 4 轮 廓 的 支承 长度 率 R mr ( )的数 值 c
中附加评 定参 数 。即轮廓 微观 不 平度 的平均 间
13—19 《 面 粗糙 度 0 1 95 表
参 数 及 其 数 值》
( 简称 I标 准 ) t 3 。新 标准 依据 GBT3 0 - 2 0 / 5 5 0 9
《 品 几何 技术 规 范 ( S 表 面 结构 轮 廓 产 GP )
表 5R a的 补 充 系列 值
00 8 .0
R0 001 . 0
x I m
2O .
表面粗糙度Ra、Rz数值与光洁度对照换算关系

具(方法) 钻石膏抛光
加工材料及硬度要求 S136 8407 DF-2 XW-10 S136 718SUPREME 54HRC 52HRC 58HRC 60HRC 300HB 300HB
光度描述 光洁度非常高,镜面 效果 光洁度较低,没有砂 纸纹 光洁度更低一级,但 没有砂纸纹 没有光亮度,有轻微 3000#砂纸纹 没有光亮度,有轻微 2000#砂纸纹 没有光亮度,有轻微 1000#砂纸纹 不辨加工痕迹的方向 微辨加工痕迹的方向 可辨加工痕迹的方向
\精铣\磨\铰\刮
\精铣\磨\铰\刮
标准等级代号 SPI(A1) SPI(A2) SPI(A3) SPI(B1) SPI(B2) SPI(B3)
表面粗糙度 粗研磨砂粒粒度 Ra0.005 Ra0.01 Ra0.02 Ra0.05 Ra0.1 Ra0.2
加工工具(方法) 精研磨砂粒粒度
Ra0.4 Ra0.8 Ra1.6
精加工:精车\精刨\精铣\磨\铰\刮 精加工:精车\精刨\精铣\磨\铰\刮
表面粗糙度参数

第4章表面粗糙度4.1 概述在机械加工过程中,由于切削会留下切痕,切削过程中切屑分离时的塑性变形,工艺系统中的高频振动,刀具和已加工表面的磨擦等等原因,会使被加工零件的表面产生许多微小的峰谷,这些微小峰谷的高低程度和间距状况就称为表面粗糙度。
一、表面粗糙度的实质表面粗糙度是一种微观的几何形状误差,通常按波距的大小分为:波距≤1mm的属表面粗糙度;波距在1~10mm间的属表面波度;波距>10mm的属于形状误差。
二、表面粗糙度对零件使用性能的影响1.对摩擦和磨损的影响一般地,表面越粗糙,则摩擦阻力越大,零件的磨损也越快。
2.对配合性能的影响表面越粗糙,配合性能越容易改变,稳定性越差。
3. 对疲劳强度的影响当零件承受交变载荷时,由于应力集中的影响,疲劳强度就会降低,表面越粗糙,越容易产生疲劳裂纹和破坏。
4.对接触刚度的影响表面越粗糙,实际承载面积越小,接触刚度越低。
5.对耐腐蚀性的影响表面越粗糙,越容易腐蚀生锈。
此外,表面粗糙度还影响结合的密封性,产品的外观,表面涂层的质量,表面的反射能力等等,所以要给予充分的重视。
4.2 表面粗糙度的评定一.基本术语1.轮廓滤波器把轮廓分成长波和短波成分的滤波器。
2.λ滤波器确定粗糙度与波纹度成分之间相交界限的滤波器。
3.取样长度用以判别具有表面粗糙度特征的一段基准线长度。
规定和选取取样长度的目的是为了限制和削弱表面波纹度对表面粗糙度测量结果的影响。
推荐的取样长度值见表4-1。
在取样长度内一般应包含五个以上的轮廓峰和轮廓谷。
4.评定长度评定表面粗糙度时所必须的一段基准线长度。
为了充分合理地反映表面的特性,一般取ln =5l。
5.轮廓中线m 用以评定表面粗糙度值的基准线。
⑴轮廓的最小二乘中线具有几何轮廓形状并划分轮廓的基准线。
在取样长度范围内,使被测轮廓线上的各点至该线的偏距的平方和为最小。
即:⎰lr i Z02dx = min⑵轮廓的算术平均中线在取样长度内,将实际轮廓划分为上、下两部分,并使上、下两部分的面积相等的基准线。
表面粗糙度参数电子版本
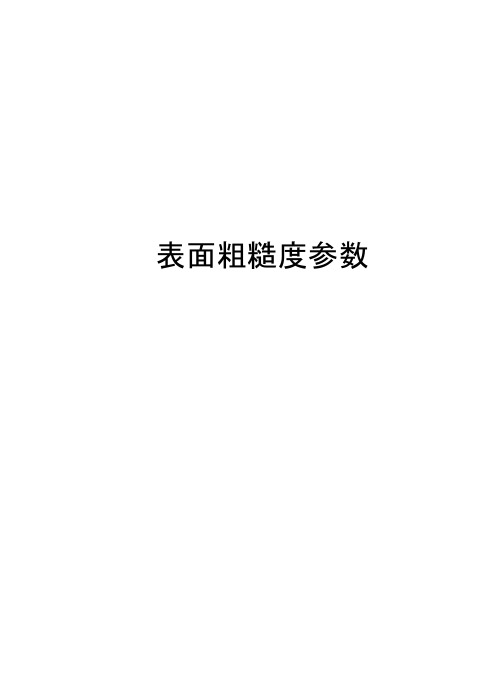
表面粗糙度参数第4章表面粗糙度4.1 概述在机械加工过程中,由于切削会留下切痕,切削过程中切屑分离时的塑性变形,工艺系统中的高频振动,刀具和已加工表面的磨擦等等原因,会使被加工零件的表面产生许多微小的峰谷,这些微小峰谷的高低程度和间距状况就称为表面粗糙度。
一、表面粗糙度的实质表面粗糙度是一种微观的几何形状误差,通常按波距的大小分为:波距w 1mm的属表面粗糙度;波距在1~10mm间的属表面波度;波距〉10mm的属于形状误差。
二、表面粗糙度对零件使用性能的影响1•对摩擦和磨损的影响一般地,表面越粗糙,则摩擦阻力越大,零件的磨损也越快。
2.对配合性能的影响表面越粗糙,配合性能越容易改变,稳定性越差。
3.对疲劳强度的影响当零件承受交变载荷时,由于应力集中的影响,疲劳强度就会降低,表面越粗糙,越容易产生疲劳裂纹和破坏。
4•对接触刚度的影响表面越粗糙,实际承载面积越小,接触刚度越低。
5•对耐腐蚀性的影响表面越粗糙,越容易腐蚀生锈。
此外,表面粗糙度还影响结合的密封性,产品的外观,表面涂层的质量,表面的反射能力等等,所以要给予充分的重视。
4.2表面粗糙度的评定一.基本术语1.轮廓滤波器把轮廓分成长波和短波成分的滤波器。
2.入滤波器确定粗糙度与波纹度成分之间相交界限的滤波器。
3.取样长度用以判别具有表面粗糙度特征的一段基准线长度。
规定和选取取样长度的目的是为了限制和削弱表面波纹度对表面粗糙度测量结果的影响。
推荐的取样长度值见表4-1。
在取4.评定长度评定表面粗糙度时所必须的一段基准线长度。
为了充分合理地反映表面的特性,一般取In =51。
5.轮廓中线m用以评定表面粗糙度值的基准线。
⑴轮廓的最小二乘中线具有几何轮廓形状并划分轮廓的基准线。
在取样长度范围内,使被测轮廓线上的各点至该线的偏距的平方和为最小。
即:dx = min⑵轮廓的算术平均中线在取样长度内,将实际轮廓划分为上、下两部分,并使上、下两部分的面积相等的基准线。
表面粗糙度的评定参数

? 4.表面缺陷:评定过程中,不应把表面缺陷(如沟槽、气孔、 划伤等)包含进去。必要时,应单独规定表面缺陷要求。
? 5 .测量部位:为了完整地反映零件表面的实际状况,需要在其 若干具有代表性的位置上进行测量,一般可采取在均匀分布的三 个以上的位置上取其平均值作为最终结果。
1.5 表而粗糙度测量方法综述及测量的基本原则
? 15.1 测量方法综述 ? 对加工表面质量的评定,除了用视觉和触觉进行定性地比较检验的方
第四章 表面粗糙度的测量
一.表面形貌误差的概念与形成
1.表面形貌误差分类: 实际加工表面通常包含如下三种表面形貌误差:
? 表面粗糙度:波距λ小于1mm ,大体呈周期性变化, 属于微观几何形状误差;
? 表 面 波度:波距λp在1~10mm ,呈周期性变化, 属于中间几何形状误差;
? 形状 误 差:波距大于10mm ,无明显周期性变化, 属于宏观几何状误差 。
形的美观等等。
三.表面形貌测量的特点与范围
? 特点:通常为量程小、测量分辨率高( nm )、 ? 表面粗糙度测量的范围
现在表面分析技术已远走出机器零件,如 :
? 微电子工业:硅片、磁盘表面、光盘、光学元件、 窗片
? 材料科学:表面形貌分析、材料微裂纹 ? 生物工程:细胞生物、芯片、遗传学 ? 科学研究:纳米技术、物理、化学、生物等基础
实际轮廓图
横向实际轮廓图
2.取样长度l:用于判别和测量表面粗糙度时所规定的一段基 准线长度。
表面粗糙度数值的含义
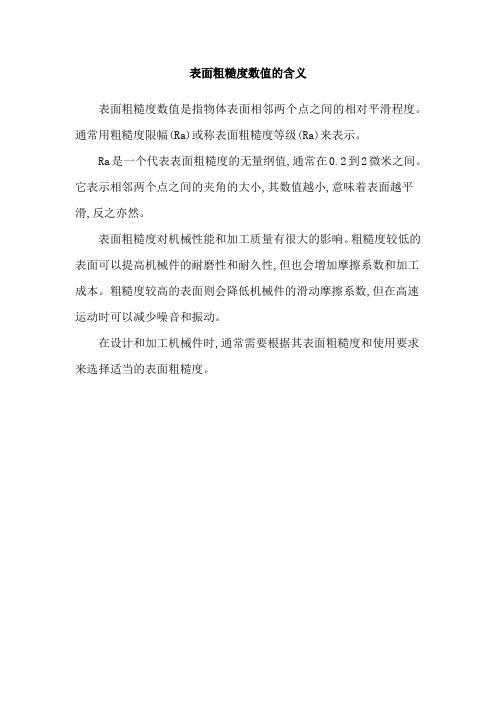
表面粗糙度数值的含义
表面粗糙度数值是指物体表面相邻两个点之间的相对平滑程度。
通常用粗糙度限幅(Ra)或称表面粗糙度等级(Ra)来表示。
Ra是一个代表表面粗糙度的无量纲值,通常在0.2到2微米之间。
它表示相邻两个点之间的夹角的大小,其数值越小,意味着表面越平滑,反之亦然。
表面粗糙度对机械性能和加工质量有很大的影响。
粗糙度较低的表面可以提高机械件的耐磨性和耐久性,但也会增加摩擦系数和加工成本。
粗糙度较高的表面则会降低机械件的滑动摩擦系数,但在高速运动时可以减少噪音和振动。
在设计和加工机械件时,通常需要根据其表面粗糙度和使用要求来选择适当的表面粗糙度。
- 1、下载文档前请自行甄别文档内容的完整性,平台不提供额外的编辑、内容补充、找答案等附加服务。
- 2、"仅部分预览"的文档,不可在线预览部分如存在完整性等问题,可反馈申请退款(可完整预览的文档不适用该条件!)。
- 3、如文档侵犯您的权益,请联系客服反馈,我们会尽快为您处理(人工客服工作时间:9:00-18:30)。
表面粗糙度理论与标准的发展表面粗糙度标准的提出和发展与工业生产技术的发展密切相关,它经历了由定性评定到定量评定两个阶段。
表面粗糙度对机器零件表面性能的影响从1918年开始首先受到注意,在飞机和飞机发动机设计中,由于要求用最少材料达到最大的强度,人们开始对加工表面的刀痕和刮痕对疲劳强度的影响加以研究。
但由于测量困难,当时没有定量数值上的评定要求,只是根据目测感觉来确定。
在20世纪20~30年代,世界上很多工业国家广泛采用三角符号(▽)的组合来表示不同精度的加工表面。
为研究表面粗糙度对零件性能的影响和度量表面微观不平度的需要,从20年代末到30年代,德国、美国和英国等国的一些专家设计制作了轮廓记录仪、轮廓仪,同时也产生出了光切式显微镜和干涉显微镜等用光学方法来测量表面微观不平度的仪器,给从数值上定量评定表面粗糙度创造了条件。
从30年代起,已对表面粗糙度定量评定参数进行了研究,如美国的Abbott就提出了用距表面轮廓峰顶的深度和支承长度率曲线来表征表面粗糙度。
1936年出版了Schmaltz论述表面粗糙度的专著,对表面粗糙度的评定参数和数值的标准化提出了建议。
但粗糙度评定参数及其数值的使用,真正成为一个被广泛接受的标准还是从40年代各国相应的国家标准发布以后开始的。
首先是美国在1940年发布了ASA B46.1国家标准,之后又经过几次修订,成为现行标准ANSI/ASME B46.1-1988《表面结构表面粗糙度、表面波纹度和加工纹理》,该标准采用中线制,并将R a作为主参数;接着前苏联在1945年发布了ΓOCT2789-1945《表面光洁度、表面微观几何形状、分级和表示法》国家标准,而后经过了3次修订成为ΓOCT2789-1973《表面粗糙度参数和特征》,该标准也采用中线制,并规定了包括轮廓均方根偏差(即现在的R q)在内的6个评定参数及其相应的参数值。
另外,其它工业发达国家的标准大多是在50年代制定的,如联邦德国在1952年2月发布了DIN4760和DIN4762有关表面粗糙度的评定参数和术语等方面的标准等。
以上各国的国家标准中都采用了中线制作为表面粗糙度参数的计算制,具体参数千差万别,但其定义的主要参数依然是R a(或R q),这也是国际间交流使用最广泛的一个参数。
2 表面粗糙度标准中的基本参数定义随着工业的发展和对外开放与技术合作的需要,我国对表面粗糙度的研究和标准化愈来愈被科技和工业界所重视,为迅速改变国内表面粗糙度方面的术语和概念不统一的局面,并达到与国际统一的作用,我国等效采用国际标准化组织(ISO)有关的国际标准制订了GB3505-1983《表面粗糙度术语表面及其参数》。
GB3505专门对有关表面粗糙度的表面及其参数等术语作了规定,其中有三个部分共27个参数术语:a.与微观不平度高度特性有关的表面粗糙度参数术语。
其中定义的常用术语为:轮廓算术平均偏差R a、轮廓均方根偏差R q、轮廓最大高度R y和微观不平度十点高度R z等11个参数。
b.与微观不平度间距特性有关的表面粗糙度参数术语。
其中有轮廓微观不平度的平均间距S m、轮廓峰密度D、轮廓均方根波长λq以及轮廓的单峰平均间距S等共9个参数。
c.与微观不平度形状特性有关的表面粗糙度参数术语。
这其中有轮廓偏斜度S k、轮廓均方根斜率∆q和轮廓支承长度率t p等共5 个参数。
3 精密加工表面性能评价的内容及其迫切性表面粗糙度参数这一概念开始提出时就是为了研究零件表面和其性能之间的关系,实现对表面形貌准确的量化的描述。
随着加工精度要求的提高以及对具有特殊功能零件表面的加工需求,提出了表面粗糙度评价参数的定量计算方法和数值规定,同时这也推动了国家标准及国际标准的形成和发展。
在现代工业生产中,许多制件的表面被加工而具有特定的技术性能特征,诸如:制件表面的耐磨性、密封性、配合性质、传热性、导电性以及对光线和声波的反射性,液体和气体在壁面的流动性、腐蚀性,薄膜、集成电路元件以及人造器官的表面性能,测量仪器和机床的精度、可靠性、振动和噪声等等功能,而这些技术性能的评价常常依赖于制件表面特征的状况,也就是与表面的几何结构特征有密切联系。
因此,控制加工表面质量的核心问题在于它的使用功能,应该根据各类制件自身的特点规定能满足其使用要求的表面特征参量。
不难看出,对特定的加工表面,我们总希望用最(或比较)恰当的表面特征参数去评价它,以期达到预期的功能要求;同时我们希望参数本身应该稳定,能够反映表面本质的特征,不受评定基准及仪器分辨率的影响,减少因对随机过程进行测量而带来参数示值误差。
但是从标准制定的特点和内容上我们容易发现,随着现代工业的发展,特别是新型表面加工方法不断出现和新的测量器具及测量方法的应用,标准中的许多参数已无法适应现代生产的需求,尤其是在一些特殊加工场合,如精加工时,用不同方法加工得到的R a值相同(或很相近)的表面就不一定会具有相同的使用功能,可见,此时R a值对这类表面的评定显得无能为力了,而且传统评定方法过于注重对高度信息做平均化处理,而几乎忽视水平方向的属性,未能反映表面形貌的全面信息。
近年来在表面特性研究的领域内,相对地说,关于零件表面功能特性方面的研究本身就较为薄弱,因为它牵涉到很多学科和技术领域。
机器的各类零件在使用中各有不同的要求,研究表面特征的功能适应性将十分复杂,这也限制了对表面形貌与其功能特性关系的研究。
工业生产的飞速发展迫切需要更加行之有效且适应性更强的表面特征评价参数的出现,为解决这一矛盾,各国的许多学者都在这方面加大研究力度,以期在不远的将来制订出一套功能特性显著的参数。
另一方面,为了防止“参数爆炸”,同时也防止大量相关参数的出现,要做到用一个参数来评价多个性能特性,用数量很少的一组参数实现对表面的本质特征的准确描述。
4 表面粗糙度理论的新进展表面形貌评定的核心在于特征信号的无失真提取和对使用性能的量化评定,国内外学者在这一方面做了大量工作,提出了许多分离与重构方法。
随着当今微机处理技术、集成电路技术、机电一体化技术等的发展,出现了用分形法、Motif法、功能参数集法、时间序列技术分析法、最小二乘多项式拟合法、滤波法等各种评定理论与方法,取得了显著进展,下面对相对而言比较成熟的分形法、Motif法、特定功能参数集法进行介绍。
1.分形几何理论最近,国内外在表征和研究机加工表面的微观结构、接触机理和表面粗糙度等方面越来越多地使用分形几何理论这一有力的数学工具。
研究表明,很多种机加工表面呈现出随机性、多尺度性和自仿射性,即具有分形的基本特征,因而使用分形几何来研究表面形貌将是合理地、有效地。
确定分形的重要参数有分形维数D和特征长度A,它们可以衡量机加工表面轮廓的不规则性,理论上不随取样长度变化和仪器分辨率变化,并能反映表面形貌本质的特征,能够提供传统的表面粗糙度评定参数(如R a、R y、R z等)所不能提供的信息。
美国TopoMetrix公司生产的扫描探针显微镜(SPM)软件体系中,已将分形维数作为评价表面微观形貌的参数之一。
机械加工表面分形维数表达了表面所具有的复杂结构的多少以及这些结构的微细程度,微细结构在整个表面中所占能量的相对大小。
分形维数越大,表面中非规则的结构就越多,并且结构越精细,精细结构所具有的能量相对越大,具有更强的填充空间的能力。
Mandelbrot于1982年在Weierstrass函数基础上提出一种分形曲线的函数表达式,称为Weierstrass-Mandelbrot函数,结合工程表面的特性,往往将W-M函数写成如下形式。
Z(x)=A(D-1)∞∑n=n1cos2πr n xr(2-D)nR>11<D<2(1)Z(x)为机械加工表面轮廓。
这样,就在工程表面的函数描述中引入了分形维数D这一参数,式中r n是表面上各次谐波的频率。
它的取值范围取决于采样长度L和采样的最高分辨率,即截止频率,A为特征长度。
对W-M函数求功率谱可以得到S(ωA2(D-1) 12lnr ω(5-2D)(2)轮廓的功率谱服从幂定律,在式(2)两端取对数为lgs(ω)=B+klgω(3)B=2(D-1)lgA-lg(2lnr)k=2D-5在双对数坐标lgs(ω)-lgω中,k是斜率,ω是截距,从上式可以看出分形维数D决定着图线的斜率,特征长度A和分形维数D决定着图线的位置(截距)。
因此对于机械加工表面,可以通过其双对数坐标下的功率谱图,由(3)式算得分形维数D 和特征长度A 。
分形理论在实际应用中还有许多工作有待进一步研究。
一是并非所有表面都具有分形特征,分形维数能否完全表征实际表面,还有待进一步研究;二是现有的分形数学模型并没有考虑表面的功能特性,也没有一种方法能唯一确定分形参数。
Motif 法随着制造技术的不断进步,表面质量不仅表现为表面的形状误差、波度、表面粗糙度等要求,而且对表面的峰、谷及其形成的沟、脉走向与分布等也有要求,需要对与表面功能密切相关的表面纹理结构进行综合评定。
显然,现在普遍采用的以2维参数为基础的表面形貌评定方法过于注重高度信息,对高度信息做平均化处理,而几乎忽视水平方向的属性,不能反映表面的其实形貌。
Motif 法基于地貌学理论从表面原始信息出发,不采用任何轮廓滤波器,通过设定不同的阈值将波度和表面粗糙度分离开来,强调大的轮廓峰和谷对功能的影响,在评定中选取了重要的轮廓特征,而忽略了不重要的特征,该方法被引入法国汽车工业表面粗糙度和波度标准,也已制订成国际标准ISO12085。
Motif 由两个单个轮廓峰的最高点之间的基本轮廓部分组成,两个峰之间的谷为一个单个的Motif ,如图1所示,并用平行于轮廓的总走向的长度AR ,垂直于基本轮廓总走向的两个深度H j 和H j+1,以及特征量T(T=min[H j ,H j+1])表征。
在设定阈值条件下,Motifs 经过不断的合并,得到评定表面功能的Motifs 集合,ISO12085推荐的参数见表1。
图1 粗糙度Motif2个相邻的峰不能被合并,只能作为单个的Motif处理。
1.包络条件如果两个相邻Motif的中间峰大于两边的峰,则2个Motif不能合并。
2.宽度条件2个相邻Motif合并后的长度不大于A(对表面粗糙度Motif)或B(对表面波度),则可以合并。
预先设定的Motif宽度的最大值A可以分离表面粗糙度和表面波度,实际上即为阈值。
设定的B值则可以分离波度和残留形状。
3.扩大条件2个Motif合并后的高度必须大于或等于原来的2个Motif。
4.深度条件单个Motif的高度必须小于合并后Motif高度的60%。
Motif法仅用7个参数就能对表面粗糙度和波纹度进行完整的描述,它尤其适合没有预行程或延迟行程的轮廓;在未知表面和过程上进行技术分析;与表面的包络面相关的性能研究;辩识粗糙度和波度具有相当接近波长的轮廓。