IE分析方法和常用计算公式
IE 常见图文符号及运算公式

四.常用基本公式: 常用基本公式:
例:一天上班時間為480分,早會20分,生產過程中機器故障20分,模治具故障20分,一天共生產產品420sets,生產一個產品須時20分 ,流水線瓶頸工時為0.5分(含有寬放),不良率為5%,試計算: 1)總標準工時 2)作業效率 3)生產效率 4)設備綜合效率 解:根據以上介紹可知如下信息: 停止時間=早會20分 停機時間=機器故障20分+模治具故障20分=40分 總投入工時=480分 不良率=5% 1)總標準工時=420*0.5=210(分) 2)作業效率=(總標準工時/總使用工時)*100% =(總標準工時/總投入工時-停止時間-停機時間)*100% =[210/(480-20-40)]*100% =50% 3)生產效率=(總標準工時/總投入工時) *100% =(210/480)*100% =43.75% 4)設備綜合效率=時間稼動率*性能稼動率*良品率 時間稼動率=(總投入工時-停機時間)/總投入工時) *100% =[(480-40)/480]*100% =91.67% 性能稼動率=(總標準工時/負荷工時) *100% =[總標準工時/(總投入工時-停止時間)]*100% =[210/(480-20)]*100% =45.65% 良品率=1-不良率=1-5%=95% 故: 設備綜合效率=時間稼動率*性能稼動率*良品率 =91.67%*45.65%*95% =39.75%
S
1
三. 常見圖文符號
18种動素的定義及符號
動素分析是由美國工程師Frank Bunker Gilbreth(1862-1924)創立的,動作分析基本要素共有18种動作,也 有文獻定義為17种,本書設定為18种.(詳見下圖)
A.工 作 有 效 推 進 的 動 作 動 素 定 義 分 類 符號 B.造 成 工 作 遲 延 的 動 作 C.動 作 本 身 不 能 推 進 作 業 NO 1 名稱 伸手 英文及縮寫 Transport Empty (TE) Grasp (G) Transport Loaded (TL) Assemble (A) Disassemble (D) Use (U) Release Load (RL) 符號說明 手中無物的形狀 分類 A 定義 空 手 移 動 ,伸 向 目 標 ,又 稱空運 手或身體的某些部位充 分控制物體 手或身體某些部位移動 物 品 的 動 作 ,又 稱 運 實 將零部件組合成一件物 體的動作 將零部物進得分離和拆 解的動作 利用器具或裝置所做的 動 作 ,稱 使 用 或 應 用 握 取 的 相 反 動 作 ,放 開 控 制物的動作
IE常用公式
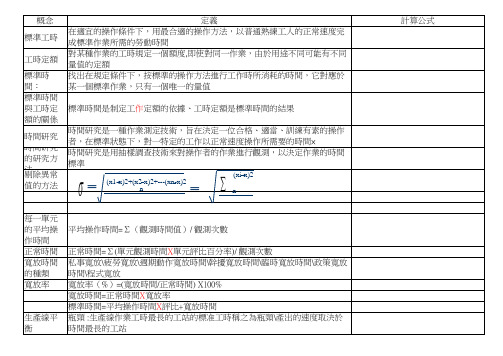
客戶緊急稽核﹐現場看板准備﹑5S抽查1.客戶緊急稽核﹐現場看板准備﹑5S抽查
2.C07棟廠房暖氣管道重新布置規划AYOUT繪制
棟廠房暖氣管道重新布置規划AYOUT繪制
跟工務檢討確認C07棟廠房1.5樓VIP辦公室施工方案及更新LAYOUT
應服務單位要求﹐准備客戶過來稽核的文件及相關事項
1.應服務單位要求﹐准備客戶過來稽核的文件及相關事項
廊坊SRM三樓清洗制程LAYOUT重新規划及現場數據調查
ALONA機種連線自動化改善效果驗証及收集和分析數據
1.應服務單位要求﹐准備客戶過來稽核的文件及相關事項
2。
IE的定义及公式计算

I E的定义及公式计算------------------------------------------作者xxxx------------------------------------------日期xxxxIE培训技术资料IE的定义:IE(Industrial Enginccring)即工业工程与现场改善。
生产线平衡率(编程率)=各站标准工时之和/瓶颈时间*站数*100%平衡时间 = 60分*60秒*8H*(8H)产能/(1+宽放率)标准工时= 60分*8H*(站数)/产能(8H)標準工時簡稱「標時」。
在傳統產業,尤其是勞力密集的產業中是一種重要的標準。
舉凡每日標準的工作量衡量、計件工資、生產獎勵辦法的指標設定、加工成本的估算、員額設定、‧‧等等都以標時為基準。
正常工時─以一個正常效能的工人,在無干擾的正常情況下完成一項指定作業所需要的工作時間。
標準工時─以一個正常效能的工人,在考量某些無法免除的正常因素下完成一項指定作業所需要的工作時間。
─上述所謂「無法免除的正常因素」是指在現行的管理體制下和現有工作環境及設備、方法條件下從事長期的相同且重覆性工作。
其平均完成一項指定作業所需要的工作時間。
在標準工時計算公式中,一般稱之為「寬放」。
一般工業測定標準工時之方法大概採用兩種方式,其一為預測法;另一種則為實測法。
這兩種方式通常都會交叉採用,相互印證。
預測法─以預定動作時間訂定時間標準預測法在工業工程專門學科中叫做「PTS法」─其全名稱為Predetermined Time Standard ─中文譯為「預定時間標準法」。
最早的PTS法又以MTM法─Method Time Measurement 、WF法─Work Factor 為最早發展完成且係最佳的兩種方式。
PTS法係將工人之操作動作拍成影片,然後詳細分析其動作和條件。
分析後發現工人之作業皆由若干基本動作和若干條件所構成。
於是在確立各種基本動作和條件因素後再求出以正常合格工人實施各種基本動作所需要的時間,最後將這些確定的時間值整理成「數據卡」。
IE计算公式
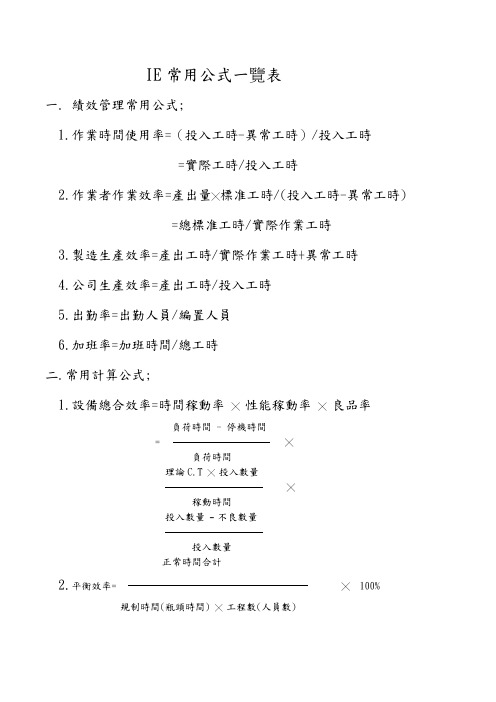
IE常用公式一覽表
一. 績效管理常用公式;
1.作業時間使用率=(投入工時-異常工時)/投入工時
=實際工時/投入工時
2.作業者作業效率=產出量╳標准工時/(投入工時-異常工時)
=總標准工時/實際作業工時
3.製造生產效率=產出工時/實際作業工時+異常工時
4.公司生產效率=產出工時/投入工時
5.出勤率=出勤人員/編置人員
6.加班率=加班時間/總工時
二.常用計算公式;
1.設備總合效率=時間稼動率╳性能稼動率╳良品率
負荷時間- 停機時間
= ╳
負荷時間
理論C.T ╳投入數量
╳
稼動時間
投入數量–不良數量
投入數量
正常時間合計
2.平衡效率= ╳100%
規制時間(瓶頭時間) ╳工程數(人員數)
1.時間利用率
實際作業時間
總投入時間
2.作業效率
總標準工時
總實際工時
單位時間實際產出標準人數
標準產出實際人數
實際作業時間內之效率指針
3.生產效率
生產效率= 作業效率x 時間利用率
單位時間實際產出標準人數
標準產出實際人力總標準時間總投入時間
總投入時間內之效率指針(含除外工時在內)
1.生產線平衡率
T1+T2+T3+…+T n
n.T m a x
T m a x﹕瓶頸工時
2.平衡率提升途徑
1.合併
2.重排
3.取消
4.簡化。
IE计算公式

IE计算公式
IE相关计算公式1.标准产量= (上班总工时/周程)*总工作人数
2.平衡率= 周程时间/ (瓶颈工序时间* 总人数)3.目标(实际)产量= 标准产量* 平衡率
5.标准人均时= 3600 / 周程
6.实际人均时= 总产量/ 总工时
7.人均时达标率= 实际人均/ 标准人均*100% 8.TAKT TIME=日计划可实际利用的工作时间/日目标产量9.实际产距= 总工时/ 实际产量
10.目标产距= 总工时/ 目标产量
11.周程时间=各工序标准工时之和
12.标准产能=日总工时/标准工时
13.计划人力=目标产能/标准产能
14.瓶颈工时=最高人均工时
15.总瓶颈工时=最高人均工时*实际人力
16.平衡率%=周程时间/总瓶颈工时
17.损失率%=1-平衡率%。
IE数据处理与常用公式
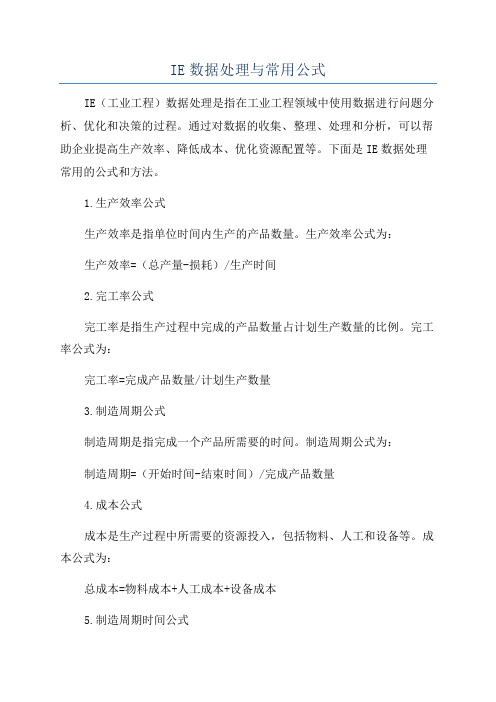
IE数据处理与常用公式IE(工业工程)数据处理是指在工业工程领域中使用数据进行问题分析、优化和决策的过程。
通过对数据的收集、整理、处理和分析,可以帮助企业提高生产效率、降低成本、优化资源配置等。
下面是IE数据处理常用的公式和方法。
1.生产效率公式生产效率是指单位时间内生产的产品数量。
生产效率公式为:生产效率=(总产量-损耗)/生产时间2.完工率公式完工率是指生产过程中完成的产品数量占计划生产数量的比例。
完工率公式为:完工率=完成产品数量/计划生产数量3.制造周期公式制造周期是指完成一个产品所需要的时间。
制造周期公式为:制造周期=(开始时间-结束时间)/完成产品数量4.成本公式成本是生产过程中所需要的资源投入,包括物料、人工和设备等。
成本公式为:总成本=物料成本+人工成本+设备成本5.制造周期时间公式制造周期时间是指完成一个产品所需要的总时间,包括加工时间、等待时间和运输时间等。
制造周期时间公式为:制造周期时间=加工时间+等待时间+运输时间6.资源利用率公式资源利用率是指生产过程中所使用的资源占总资源的比例。
资源利用率公式为:资源利用率=生产所使用的资源/总资源7.效率公式效率是指生产过程中实际产出与标准产出之间的比例。
效率公式为:效率=实际产出/标准产出8.容量公式容量是指生产过程中单位时间内能够完成的工作量。
容量公式为:容量=总资源/单位时间9.平均停留时间公式平均停留时间是指在生产过程中产品在其中一工序的平均停留时间。
平均停留时间公式为:平均停留时间=生产时间/生产数量10.时间效率公式时间效率是指单位时间内完成的工作量。
时间效率公式为:时间效率=完成工作量/单位时间以上是IE数据处理常用的公式和方法。
通过对数据进行准确的收集、整理、处理和分析,可以帮助企业发现问题、优化流程,并做出合理的决策,以提高生产效率和降低成本。
IE数据处理与常用公式

步骤六:改善过程
1、装配线人员定岗、定置作业
a) 固定岗(作业员)与移动岗区分 (移动岗位:修理员、物料员、拉长、多能工) b) 由员工自已离岗去拿物料,变为专人配送物料到岗(编
岗位物料配送清单,明确数量/次、频次/天); c) 员工的作业范围要规划合理,减少不必要的走动; d) 员工离岗,设定顶岗人员机制(多能工配置)。
出勤时间
8H(28800S)或10H(36000S)(是否倒班)
出勤方式
单班/两班/三班
步骤一:现状数据调查
实际节拍时间
=实际出勤时间/实际产量
目前人均时产量
人员配置
出勤方式
步骤二:实物数据分析
1. 编制生产节拍测定表
能够看出每个岗位中的作业内容和作业顺序,所需物料、工作工具都列明
步骤二:实物数据分析
➢实施强制节拍(在自动生产线上) ➢虚拟强制节拍(在手推滚筒线上) ➢岗位之间“一个流”传递(作业台传递)
4、动作浪费改善
使用最低级动作作业
➢改善瓶颈岗位的浪费动作(明显+细小)
➢改善每个岗位的浪费动作(明显→细小)
浪费动作消除后,平衡也会打破,需重新调整生产平衡
步骤六:改善过程
常见的12种动作浪费:
活动程序
PD AC
PD AC
P-Plan D-Do C-Check A-Action
活动基本步骤
改善对象选定
现状调查
总结及标准化
效果确认
改善实施
问题点提出 设定改善目标 改善案确立
步骤一:现状调查
选定改善对象
XX工段XX生产线(班) 针对XX品号(系列)进行改善
计划产量
XX台/8H(或XX台/10H)
电流ie的计算公式
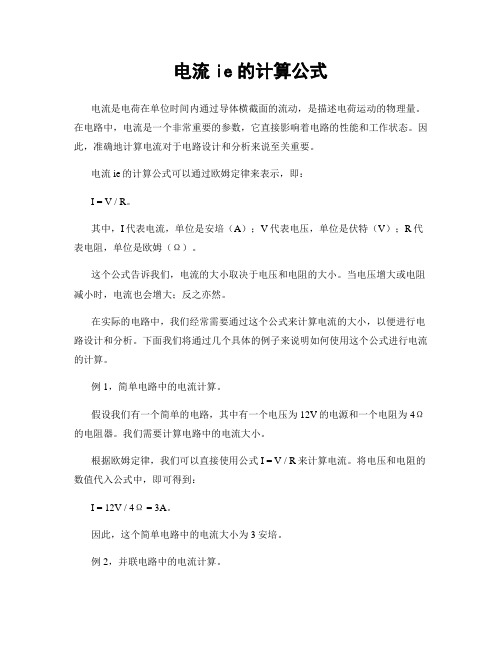
电流ie的计算公式电流是电荷在单位时间内通过导体横截面的流动,是描述电荷运动的物理量。
在电路中,电流是一个非常重要的参数,它直接影响着电路的性能和工作状态。
因此,准确地计算电流对于电路设计和分析来说至关重要。
电流ie的计算公式可以通过欧姆定律来表示,即:I = V / R。
其中,I代表电流,单位是安培(A);V代表电压,单位是伏特(V);R代表电阻,单位是欧姆(Ω)。
这个公式告诉我们,电流的大小取决于电压和电阻的大小。
当电压增大或电阻减小时,电流也会增大;反之亦然。
在实际的电路中,我们经常需要通过这个公式来计算电流的大小,以便进行电路设计和分析。
下面我们将通过几个具体的例子来说明如何使用这个公式进行电流的计算。
例1,简单电路中的电流计算。
假设我们有一个简单的电路,其中有一个电压为12V的电源和一个电阻为4Ω的电阻器。
我们需要计算电路中的电流大小。
根据欧姆定律,我们可以直接使用公式I = V / R来计算电流。
将电压和电阻的数值代入公式中,即可得到:I = 12V / 4Ω = 3A。
因此,这个简单电路中的电流大小为3安培。
例2,并联电路中的电流计算。
接下来,我们考虑一个稍微复杂一点的情况,即一个并联电路。
假设我们有一个电压为6V的电源,并联连接了两个电阻,分别为2Ω和4Ω。
我们需要计算整个电路中的电流大小。
对于并联电路,我们需要先计算每个电阻上的电流,然后将它们相加得到总电流。
根据欧姆定律,我们可以分别计算每个电阻上的电流:I1 = 6V / 2Ω = 3A。
I2 = 6V / 4Ω = 1.5A。
然后将它们相加得到总电流:I = I1 + I2 = 3A + 1.5A = 4.5A。
因此,这个并联电路中的总电流大小为4.5安培。
例3,复杂电路中的电流计算。
最后,我们考虑一个更为复杂的情况,即一个由多个电阻和电压源组成的复杂电路。
在这种情况下,我们可以通过串联和并联的组合来计算整个电路中的电流大小。
ie人机比计算公式
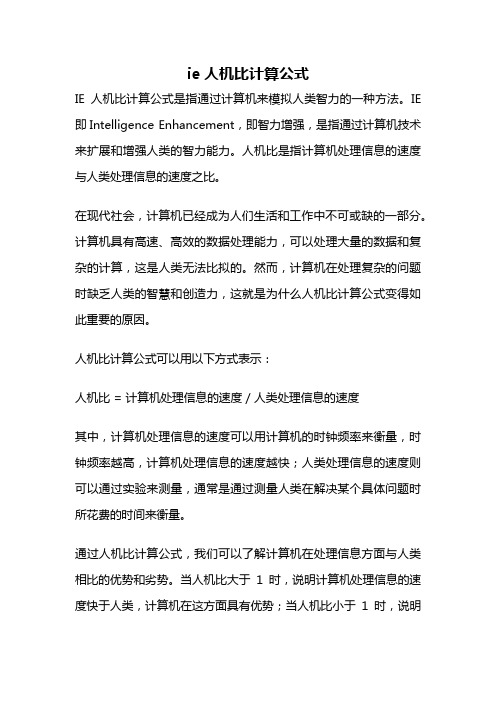
ie人机比计算公式IE人机比计算公式是指通过计算机来模拟人类智力的一种方法。
IE 即Intelligence Enhancement,即智力增强,是指通过计算机技术来扩展和增强人类的智力能力。
人机比是指计算机处理信息的速度与人类处理信息的速度之比。
在现代社会,计算机已经成为人们生活和工作中不可或缺的一部分。
计算机具有高速、高效的数据处理能力,可以处理大量的数据和复杂的计算,这是人类无法比拟的。
然而,计算机在处理复杂的问题时缺乏人类的智慧和创造力,这就是为什么人机比计算公式变得如此重要的原因。
人机比计算公式可以用以下方式表示:人机比 = 计算机处理信息的速度 / 人类处理信息的速度其中,计算机处理信息的速度可以用计算机的时钟频率来衡量,时钟频率越高,计算机处理信息的速度越快;人类处理信息的速度则可以通过实验来测量,通常是通过测量人类在解决某个具体问题时所花费的时间来衡量。
通过人机比计算公式,我们可以了解计算机在处理信息方面与人类相比的优势和劣势。
当人机比大于1时,说明计算机处理信息的速度快于人类,计算机在这方面具有优势;当人机比小于1时,说明计算机处理信息的速度慢于人类,计算机在这方面具有劣势。
人机比计算公式的应用范围非常广泛。
在科学研究领域,人机比可以帮助科学家加快数据处理和分析的速度,提高研究的效率;在工程设计领域,人机比可以帮助工程师快速优化设计方案,提高产品的性能和质量;在金融领域,人机比可以帮助投资者分析市场数据,制定投资策略;在医学领域,人机比可以帮助医生快速诊断疾病,提高医疗水平。
然而,人机比计算公式也存在一些限制和挑战。
首先,计算机处理信息的速度虽然很快,但在某些复杂的问题上仍然无法比拟人类的智慧和创造力。
其次,人类处理信息的速度在不同的个体之间存在差异,因此在计算人机比时需要考虑个体差异的影响。
此外,人机比只是衡量信息处理速度的一种指标,不能完全代表计算机和人类在智力方面的差异。
服装IE常用计算工式
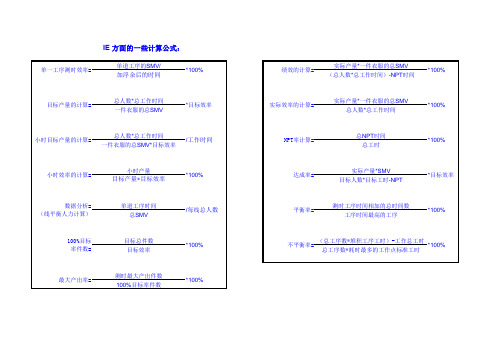
IE 方面的一些计算公式:
单一工序测时效率=单道工序的SMV/
*100%绩效的计算=实际产量
*一件衣服的总SMV
*100%加浮余后的时间(总人数*总工作时间)-NPT时间
目标产量的计算=总人数*总工作时间
*目标效率实际效率的计算=实际产量
*一件衣服的总SMV
*100%一件衣服的总SMV总人数*总工作时间
小时目标产量的计算=
总人数*总工作时间
/工作时间NPT率计算=总
NPT时间
*100%一件衣服的总SMV*目标效率总工时
小时效率的计算=
小时产量
*100%达成率=实际产量
*SMV
*目标效率目标产量*目标效率目标人数*目标工时-NPT
数据分析=单道工序时间
/每线总人数平衡率=测时工序时间相加的总时间数*100%(线平衡人力计算)总SMV工序时间最高的工序
100%目标目标总件数
*100%不平衡率=(总工序数*堆积工序工时)-工作总工时*100%率件数=目标效率总工序数*耗时最多的工作点标准工时
最大产出率=测时最大产出件数
*100% 100%目标率件数。
电离平衡常数计算题型分析与解题归纳

电离平衡常数计算题型分析与解题归纳电离平衡常数(IE)是衡量一种物质可以电离的程度表示出来的,是一个很重要的知识点。
其计算公式为:IE=K=a/b,其中a是物质A+离子的浓度,b是物质B-离子的浓度。
在计算IE时,可以按照一下题型来设计:(1)给出电离平衡常数K值,求电离平衡状态下物质A+离子和物质B-离子的浓度;(2)给出电离平衡常数K值,求添加某物质后物质A+离子和物质B-离子的浓度;(3)给出电离平衡状态下物质A+离子和物质B-离子的浓度,求IE值;(4)给出添加某物质后物质A+离子和物质B-离子的浓度,求IE值。
第二部分算电离平衡常数的解题步骤归纳1.先,要搞清楚题目中给出的元素是什么,物质A+离子和物质B-离子代表什么。
2.据IE计算公式:IE=K=a/b,其中a是物质A+离子的浓度,b是物质B-离子的浓度,确定求IE的公式。
3.据不同的题型,把题目中的信息代入公式,得出结果。
第三部分离平衡常数计算题型练习(1)已知K=0.0000579M,电离平衡状态下A+离子的浓度和B-离子的浓度?解:根据IE=K=a/b,有a=Kb,b=Ka,由K=0.0000579M,得a=0.0000579Mb,b=0.0000579Ma,即A+离子的浓度和B-离子的浓度分别为0.0000579Mb和0.0000579Ma 。
(2)已知a=0.000147M,b=0.0000836M,求IE值?解:根据IE=K=a/b,有IE=K=0.000147M/0.0000836M=1.76M,即IE值为1.76M。
结论电离平衡常数是一个重要的知识点,计算IE可以按照给出的不同题型来完成,其解题步骤有:搞清楚题目中给出的元素是什么,根据IE计算公式确定求IE的公式,把题目中的信息代入公式,得出结果。
通过练习,可以更好地掌握计算IE的方法,掌握电离平衡常数的知识点。
IE常用计算公式及报价成本计算表

IE常用计算公式及报价成本计算表一、IE常用计算公式在工业工程(Industrial Engineering,简称IE)领域中,有一些常用的计算公式可以帮助IE工程师更好地进行生产过程的规划和优化。
下面介绍几个常用的计算公式。
1. 直接工时(Direct Labor Hours,简称DLH)计算公式直接工时是指直接用于生产产品或提供服务的工人所需的工时。
计算直接工时的公式为:DLH = TPH × QT其中,DLH表示直接工时,TPH表示每单位产品或服务所需的标准工时,QT表示生产或服务的数量或需求量。
2. 间接工时(Indirect Labor Hours,简称ILH)计算公式间接工时是指用于辅助生产过程或提供支持服务的工人所需的工时。
计算间接工时的公式为:ILH = TPIH × QT其中,ILH表示间接工时,TPIH表示每单位产品或服务所需的标准间接工时,QT表示生产或服务的数量或需求量。
3. 有效工时(Effective Work Hours,简称EWH)计算公式有效工时是指在给定时间段内,工人实际用于生产或提供服务的工时。
计算有效工时的公式为:EWH = TH × (1 - RE)其中,EWH表示有效工时,TH表示总工时,RE表示损耗时间的比例。
二、报价成本计算表在IE工程中,报价成本计算表是用于估计生产过程中各项成本的工具。
下面是一个示例的报价成本计算表:项目计算公式说明原材料成本MC = (CCI × MCI) + (CCS ×MCS) + (CCP × MCP)CCI、CCS、CCP分别表示原材料的成本系数,MCI、MCS、MCP表示原材料的消耗量直接人工成本DLBC = DLH × DLRC DLH表示直接工时,DLRC表示直接人工的单位成本间接人工成本ILBC = ILH × ILRC ILH表示间接工时,ILRC表示间接人工的单位成本设备折旧成本DDC = (DPC × DPY) / BPT DPC表示设备购买价值,DPY表示设备折旧年限,BPT表示生产总时间设备维护成本EMC = (EPC × CT) / BPT EPC表示设备的年维护费用,CT表示设备维护次数,BPT表示生产总时间水电费用UEC = UER × MEP UER表示单位用电成本,MEP表示月用电量其他费用OEC = OEB × T OEB表示其他费用的标准,T表示生产总时间总成本TC = MC + DLBC + ILBC +DDC + EMC + UEC + OEC通过填写每个项目的具体数值,可以计算出总成本。
IE分析方法和常用计算公式
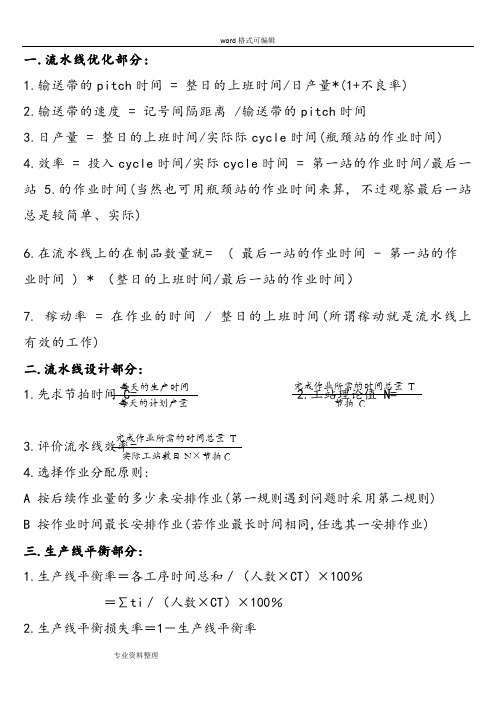
一.流水线优化部分:1.输送带的pitch 时间 = 整日的上班时间/日产量*(1+不良率)2.输送带的速度 = 记号间隔距离 /输送带的pitch 时间3.日产量 = 整日的上班时间/实际际cycle 时间(瓶颈站的作业时间)4.效率 = 投入cycle 时间/实际cycle 时间 = 第一站的作业时间/最后一站5.的作业时间(当然也可用瓶颈站的作业时间来算, 不过观察最后一站总是较简单、实际)6.在流水线上的在制品数量就= ( 最后一站的作业时间 - 第一站的作业时间 ) * (整日的上班时间/最后一站的作业时间)7. 稼动率 = 在作业的时间 / 整日的上班时间(所谓稼动就是流水线上有效的工作) 二.流水线设计部分:1.先求节拍时间 C=2.工站理论值 N=3.评价流水线效率=4.选择作业分配原则:A 按后续作业量的多少来安排作业(第一规则遇到问题时采用第二规则)B 按作业时间最长安排作业(若作业最长时间相同,任选其一安排作业) 三.生产线平衡部分:1.生产线平衡率=各工序时间总和/(人数×CT )×100% =∑ti /(人数×CT )×100%2.生产线平衡损失率=1-生产线平衡率每天的生产时间每天的计划产量 完成作业所需的时间总量 T节拍 C完成作业所需的时间总量 T 实际工站数目N ×节拍C3、生产线平衡改善的方法工时长的工序的改善方法:A.细分作业内容,将一部分作业转移至其他工序B.改善作业本身C.谋求工序机械化D.通过改良,增大机器的运作能力E.增加作业人数F.调配经验丰富,作业技能高的熟练作业人员G.“瓶颈”工序能力不足的部分,利用加班完成,或用其他方法完成 工时短的工序的改善方法:A.细分作业内容,将作业转移至其他工序,取消该工序B.从其他工序转移来部分作业内容,增加作业量C.将同是作业工时短的工序合并起来D.在不影响后工序的前提下,采用继续集中作业方式4、生产线平衡分析步骤决定分析对象和要达到的目标取得相关人员的理解和帮助分解各工序的作业单元测定每个作业单元的时间实际修正测定工时求出每个线点时间作成线点运行表计算平衡效率(浪费率)研讨工序平衡5、现场生产线平衡分析对生产中的生产线进行分析时,依下述步骤进行:1)对生产线的各工程顺序(作业单位)予认定,并填入生产流动平衡表中2)测算各工序实质作业时间以DM(Decimal Minute)为单位记入平衡表内(1人实质时间栏)注:1DM=0.01分=0.6秒3)清点各工序作业人数,并记入人员栏内4)1人实质作业时间÷人数 = 分配时间,记入时间栏5)依此分配时间划出柱状图或曲线图6)在分配的实质时间最高的这一工序顶点横向划一条点线7)计算不平衡损失上面斜线部分的总和即为不平衡损失的总和 T(Lose)=Σ|Tm-Ti| 不平衡损失=(最高的DM×合计人数)-(各工序时间的合计)如下图8)生产线平衡率生产线平衡率=——————————————9)生产线不平衡损失率=1-生产线平衡率10)如使用输送带之动力传送,则应计算输送带的流动速度(M/时间单位)称为节拍时间,符号TC 。
IE工业工程分析过程

IE工业工程分析过程IE的组成─九大功能IE──工业工程(也为企化部)是关于人员、物料、设备及能源成本等整体系统的设计,改善与装置的一门技术。
一:时间分析(1)测量技术:设备,以马表、时间观测表.(化分动作单位约0.06秒)。
(2)测量方法:归零法(单程测试法),连续测试法(以30个一组测10次)。
(3)测时步骤:测时状况:正常时间=测试时间?(1+评比系数)标准时间=正常时间×(1+宽放)SCT=MAX(标准时间)标准工时=SCT×人力评比系数分为:熟练度﹑努力度﹑工作环境﹑一致性.又为:理想(0.1)﹑优(0.075)﹑良(0.05)﹑平均(0)﹑可(-0.1)﹑不良(-0.22)(4)宽放种类分:私事宽放(男:10分?女:14分)?工厂宽放疲劳宽放?延迟宽放系数订于5%-10%之间,也就是宽放时间。
例:总工作时间设定为Y:工厂宽放时间设定为C:疲劳宽放时间设为A:疲劳宽的放为R:私事宽放为B:延迟宽放为D:净工作时间设X:A=R?X:Y=X+A+B+C+D:R=(Y-X-B-C-D)?X测试时间评比系数正常时间四类宽放标准时间不平衡率=(单站(MAX)?人数-总站时间和)?单站(MAX)?人数二:产能分析(1):加工作业──机器周程产能(凈产能)。
(2):取放作业──周程产能。
(3):箅料?调整治工具?检验──非周期性产能。
(4):四种宽放──标准工时产能。
(5):不良率?更换治具?机器宽放?停工等料──最适当产能。
(6):加工速度慢?消极怠工──现场实际产能。
分析目的就是让:实际产能最接近机器周程产能的一种方式。
三:动作分析总概:有18种基本动作组成分析手法,它用目视观察将各种基本动作进行组合也可称作目视分析法。
动作归类?时间测试法(VF法)。
意义──改善:把凈作业动作?附加动作?可去除动作区分开来进行改善。
动作分类:第一类:推行工作中必须的动作。
*虽不可免去但通过变动调整尽量减短动作时间。
IE常用概念定义公式
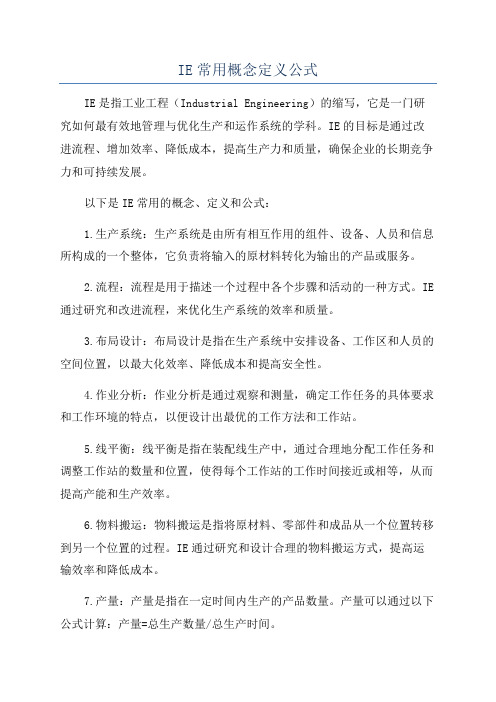
IE常用概念定义公式IE是指工业工程(Industrial Engineering)的缩写,它是一门研究如何最有效地管理与优化生产和运作系统的学科。
IE的目标是通过改进流程、增加效率、降低成本,提高生产力和质量,确保企业的长期竞争力和可持续发展。
以下是IE常用的概念、定义和公式:1.生产系统:生产系统是由所有相互作用的组件、设备、人员和信息所构成的一个整体,它负责将输入的原材料转化为输出的产品或服务。
2.流程:流程是用于描述一个过程中各个步骤和活动的一种方式。
IE 通过研究和改进流程,来优化生产系统的效率和质量。
3.布局设计:布局设计是指在生产系统中安排设备、工作区和人员的空间位置,以最大化效率、降低成本和提高安全性。
4.作业分析:作业分析是通过观察和测量,确定工作任务的具体要求和工作环境的特点,以便设计出最优的工作方法和工作站。
5.线平衡:线平衡是指在装配线生产中,通过合理地分配工作任务和调整工作站的数量和位置,使得每个工作站的工作时间接近或相等,从而提高产能和生产效率。
6.物料搬运:物料搬运是指将原材料、零部件和成品从一个位置转移到另一个位置的过程。
IE通过研究和设计合理的物料搬运方式,提高运输效率和降低成本。
7.产量:产量是指在一定时间内生产的产品数量。
产量可以通过以下公式计算:产量=总生产数量/总生产时间。
8.效率:效率是指在给定的资源条件下,生产系统所能实现的最大产量。
效率可以通过以下公式计算:效率=实际产量/理论产量。
9.制造周期:制造周期是指完成一个产品的全部生产过程所需的时间。
制造周期可以通过以下公式计算:制造周期=生产终点时间-生产起点时间。
10.供应链管理:供应链管理是指对供应链中的物流、货物和信息流进行规划、控制和协调的过程,以实现最优的供应链运作。
11.质量管理:质量管理是指通过制定标准、监控过程、改进方法和培训人员,来确保产品或服务符合质量要求的一种管理方法。
12.总质量管理:总质量管理是一种以顾客需求为中心,通过持续的质量改进和员工参与,提高产品和服务质量的管理方法。
【全】IE术语定义计算公式

【全】IE术语定义计算公式术语定义/计算公式1、标准工时/标准时间在适宜的操作条件下,用最合适的操作方法,以普通熟练工人的正常速度完成标准作业所需的劳动时间标准时间=正常时间*(1+宽放率)=(观测时间*评比系数)*(1+宽放率)2、工时定额对某种作业的工时规定一个额度,即使对同一作业,由于用途不同可能有不同量值的定额,如现行定额、计划定额、目标定额等3、标准时间与工时定额的关系标准时间是制定工作定额的依据、工时定额是标准时间的结果4、时间研究时间研究是一种作业测定技术,旨在决定一位合格、适当、训练有素的操作者,在标准状态下,对一特定的工作以正常速度操作所需要的时间5、时间研究的研究方法时间研究是用抽样调查技术来对操作者的作业进行观测,以决定作业的时间标准6、剔除异常值的方法三倍标准偏差法:正常值为x+/-3 内的数据,超出者为异常值7、每一单元的平均操作时间平均操作时间=Σ(观测时间值)/ 观测次数8、正常时间正常时间=Σ(单元观测时间X单元评比百分率)/ 观测次数9、宽放时间的种类私事宽放\疲劳宽放\周期动作宽放时间\干扰宽放时间\临时宽放时间\政策宽放时间\程序宽放10、宽放率宽放率(%)=(宽放时间/正常时间) X100% 宽放时间=正常时间X宽放率标准时间=平均操作时间X评比+宽放时间11、瓶颈生产线作业工时最长的工站的标准工时称之为瓶颈\产出的速度取决于时间最长的工站12、实测时间作业者完成操作的实际时间13、节拍根据生产计划所得的一个工程所需的时间14、平衡率生产线各工程工作分割的均衡度,用于衡量流程中各工站节拍符合度的一个综合比值平衡率=Σ(T1+T2+......+Tk)/TT*K15、不平衡率生产线各工程工作分割的不均衡度不平衡率=(最大值-最小值)/平均值*100%16、平衡损失平衡损失=瓶颈工站的实际时间×工站数×FG-正常时间17、操作损失生产中异常及不良造成的损失操作损失=(设定产能-实际产量)*单件标准时间-额外产出工时=不良品损失+计划外停线(机)工时18、总损失总损失=稼动损失+平衡损失+操作损失19、快速切换通过各种手段,尽可能的缩短作业切换时间,以减少时间浪费,达成提高综合效益之目的20、作业切换时间是指前一品种加工结束到下一品种加工出良品的这段时间21、外部切换时间不必停机也能进行的切换作业时间22、内部切换时间必须停机才能进行的切换以及为保证质量进行的调整、检查等占用的切换时间23、JIT的基本思想只在需要的时候、按需要的量、生产所需的产品,故又被称为准时制生产、适时生产方式、广告牌生产方式24、JIT的核心零库存和快速应对市场变化25、劳动定额的时间构成劳动定额的时间构成=作业时间+布置工作地时间+休息与生理需要时间+准备与结束时间/批量劳动定额的时间构成可供时间:上班时间内,为某产品生产而投入的所有时间可供工时=可供时间 *人数-借出工时投入工时=可供工时-计划停线工时稼动率=投入工时/可供工时 *100%计划停线工时=计划停线时间*人数计划停线时间=无计划时间+换线时间+判停时间设定产能(H) =3600(S)/瓶颈时间(S)设定产能(班)=投入时间/瓶颈时间(S)总工时=瓶颈时间*作业人数实际产量是可供时间内所产出的良品数人均产能=实际产量/投入时间/人数单机台产能=实际产量/投入时间/机台数平衡损失=(总工时-单件标准时间)*设定产能操作效率=实际产量/设定产能*100%整体工厂效率(OPE)=平衡率*稼动率*操作效率平衡损失=(瓶颈*作业人数-单件标准时间)*设定产能操作损失=(设定产能-实际产量)*单件标准时间-额外产出工时=不良品损失+计划外停线(机)工时26、工费率平均每小时发生费用=单位时间内发生总费用/单位时间内投入工时27、单件成本平均每件分摊成本=某批产品花费总成本/该批产品总量28、成本下降率Σ[(上期单件成本-本期单件成本)*实际产量]/Σ(上期单件成本*实际产量)*100%29、机会成本机会成本=投资额*行业平均盈利率经营收益=收益-机会成本节省成本﹕=(改善前需求工时-改善后需求工时)*工费率交付周期=∑(CT*批量)30、所有机器效率=Total S.T*Output/(可利用时间*机台数)人工利用率= 人工操作时间*目标产能/工作时间机器稼动率 = 机器作业时间*目标产能/工作时间MFG效率=实际产量/除非计划停机损失后可生产数量总生产效率=实际产量/可生产数量31、无效时间指花费在进行与生产不是有直接关系的活动之时间,如:开会,培训,消防演习,健康枪查,5S等.32、生产是一切社会组织将它的输入转化为输出的过程,是人们创造物质产品的有组织的活动33、时间序列模型 以时间为独立变量,利用过去需求随时间变化的关系来预测未来的需求34、预测监控 通过预测监控来检验过去起作用的预测模型是否仍然有效35、因果关系模型 利用变量(包括时间,如广告投入vs 销量)之间的相互关系,通过一种变量的变化来预测另一种变量的未来变化36、周期时间CYCLE TIME(CT) 每单位工序中1个循环的作业所需的时间 单位工序CT 的和/ 测试次数 37、节拍时间(TT )制造一件物品时所需要的实际时间 作业时间/ 需求数 38、NECK TIME整个工序中1个循环作业时间最长的工序时间 39、RATING作业按标准方法进行时作业速度的快或慢的程度用数字进行换算的时间 很快︰125%;快︰100%;一般︰85%; 慢︰60% 40、净作业时间作业按标准方法进行时所需的最少时间 CYCLE TIME*RATING(%) 41、运转率产品所需的时间及实际生产中所用的时间之比 NECK TIME /TACT × 100 % 42、运转损失生产产品所需的时间和实际所用的时间之比 (Tact Time -Neck Time)/ TACT TIME× 100 % 43、平衡损失作业人员之间由于作业量的不公平导致的作业要素时间的不均衡程度的比 (Neck Time -Cycle Time)/TACT TIME× 100 % 44、效率损失按标准方法进行作业时需要的最少时间和与实际作业中所用的时间之差的比 (Cycle Time -净作业时间)/ TACT TIME× 100 % 45、综合损耗损耗的总合计 运转损失+平衡损失+效率损失 46、时间观测法用秒表观测分析作业人员的作业时间或设备运转的方法 47、防呆法作业人员或设备上装上无需小心作业也绝不出错的防止出错装置48、生产率一般用产量对投入的比 OUT PUT /IN PUT 49、工时人或机器能做的或已做的量用时间来表示 50、拥有工时拥有人员的工时 拥有人员×正常作业时间 51、考勤工时实际上没投入到作业的工时(缺勤、休假、出差、支持等) 相关人员×相关时间 52、出勤工时实际投入到作业的人员的工时 拥有工时-考勤工时 53、追加工时 正常出勤工时以外追加作业的工时,即加班,特殊出勤、接受支持等相关人员×相关时间54、作业工时 投入到作业中的总工时 出勤工时+追加工时55、实际生产工时 作业工时中去掉损失工时,实际投入到作业的工时 作业工时-损失工时56、损失工时不属于作业人员责任范围的损耗工时(会议、教育、早会、待料、材料不良、机械故障、机型变更、不良返工等) 相关人员×相关时间57、作业工时效率 生产产品所需的时间(标准时间)和实际用的时间之比 标准工时/作业工时× 100 %58、实际生产工时效率 损失工时以外的纯作业时间和实际生产所用的时间之比 标准工时/实动工时× 100 %59、实际生产率 生产产品所需的时间和纯生产所需的时间之比 标准工时/实动工时× 100 %60、效率管理为了减少生产要素的损耗,用一线监督人员的指导监督来达到适当地提升并维持作业人员对作业的态度的一种管理模式 标准时间/实际时间61、PAC (Performance Analysis & Control) 为了能做到只要作业努力就能提升及维持能力的效率管理模式的一种。
IE公式汇总
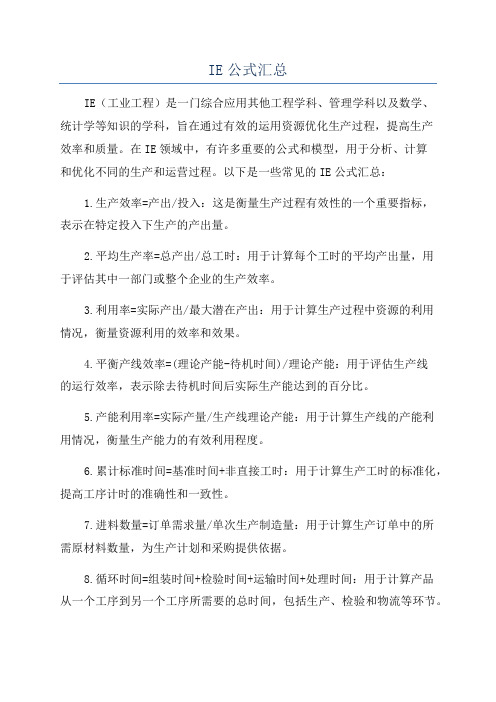
IE公式汇总IE(工业工程)是一门综合应用其他工程学科、管理学科以及数学、统计学等知识的学科,旨在通过有效的运用资源优化生产过程,提高生产效率和质量。
在IE领域中,有许多重要的公式和模型,用于分析、计算和优化不同的生产和运营过程。
以下是一些常见的IE公式汇总:1.生产效率=产出/投入:这是衡量生产过程有效性的一个重要指标,表示在特定投入下生产的产出量。
2.平均生产率=总产出/总工时:用于计算每个工时的平均产出量,用于评估其中一部门或整个企业的生产效率。
3.利用率=实际产出/最大潜在产出:用于计算生产过程中资源的利用情况,衡量资源利用的效率和效果。
4.平衡产线效率=(理论产能-待机时间)/理论产能:用于评估生产线的运行效率,表示除去待机时间后实际生产能达到的百分比。
5.产能利用率=实际产量/生产线理论产能:用于计算生产线的产能利用情况,衡量生产能力的有效利用程度。
6.累计标准时间=基准时间+非直接工时:用于计算生产工时的标准化,提高工序计时的准确性和一致性。
7.进料数量=订单需求量/单次生产制造量:用于计算生产订单中的所需原材料数量,为生产计划和采购提供依据。
8.循环时间=组装时间+检验时间+运输时间+处理时间:用于计算产品从一个工序到另一个工序所需要的总时间,包括生产、检验和物流等环节。
9.作业单元时间=作业时间/作业数量:用于计算单个作业的平均生产时间,衡量作业的效率和生产能力。
10.生产指数=实际生产量/计划生产量:用于评估生产计划的完成情况,衡量生产计划的执行进度和效果。
11.转换效率=成品产量/原料消耗量:用于衡量生产过程中资源的转化效率,评估生产过程的节能和减排效果。
12.效益率=实际效益/标准效益:用于评估工作站或生产线的操作效果,衡量生产过程中的不良率和错误率。
13.加工时间=累计周期时间/产品数量:用于计算生产一个产品所需的平均加工时间,为生产进度和计划提供参考。
以上只是IE领域中一些常用的公式和模型,还有许多其他的公式可以基于具体的工业工程问题来应用。
工业工程-IE知识简介

IE知识简介
1.工时如何计算:
将整台机拆开,分析其动作,然后将时间记录下来,就是生产一台机所需时间。
计算公式:8小时/ 一台时间= 每天1人生产机台之数量
例:每做1台机器需时间40分钟,1人1天可以做12台,如果一条线有50人,8小时可以做600台;如果每天生产1200台,需1200人。
平均工时:8小时*60分=480分/600台=0.8分=48秒
2.以标准工时来算生产效率,须乘宽放率。
IE有两种算法:
第一种为:生产一台的总工时* 合理之宽放(0.01),然后再出每一工作站的工时。
第二种为:生产一台工时不变,算出每一工作站之工时再科以宽放。
學習曲線
不會階段漸會階段成熟階段發揮高效率階段
3.各动作的工时有二种算法:
一种为固定标准工时;
一种为实测10PCS平均数(动作要正常)
理论≠实际;还要记得给检查材料的工时,拿取物品的工时。
4.IE在排作业站时,每一站位工时约为标准的±2秒,如有异常,生产干部自选调整或请IE到在线调整。
IE常用计算公式及报价成本计算

IE常用计算公式及报价成本计算IE工程师在生产流程优化和成本控制中扮演着重要角色,在计算生产成本和报价时,IE常用的计算公式和方法如下:1.标准工时计算公式标准工时=标准产量/标准产能标准工时是指在标准产能条件下完成一定产量所需要的时间。
IE工程师通过对生产过程的研究和分析,确定产品的标准产量和标准产能,进而计算出标准工时,用于生产计划和生产效率评估。
2.进料与产出的关系产出数量=进料数量*制程利用率*一次合格率进料数量是指制程开始前所需要的原材料或零部件的数量,制程利用率是指在制程过程中能够得到有用产品的比例,一次合格率是指在制程过程中得到合格产品的比例。
IE工程师通过计算进料与产出的关系,可以确定生产过程中的损失率和成品率,进而制定改进措施,提高生产效率和产品质量。
3.生产效率计算公式生产效率=产出数量/实际工时生产效率是指在给定的时间内完成产量的能力。
IE工程师通过计算生产效率,可以评估生产效益,并找出生产中的瓶颈和问题所在,提出改进方案。
4.报价成本计算公式报价成本=直接材料成本+直接人工成本+制造费用+间接费用直接材料成本是指制造产品所需的直接材料的成本,直接人工成本是指直接参与产品制造的人员的工资和福利费用,制造费用是指生产过程中所涉及到的设备折旧、维修、能耗等费用,间接费用是指与生产过程相关但无法直接分配到具体产品上的费用,如生产管理人员的工资、办公费用等。
IE工程师通过计算每个成本项的费用,并根据产品的数量和预计产量,计算出报价成本,用于确定产品的售价和利润。
以上是IE工程师常用的计算公式和报价成本计算方法,通过这些方法,IE工程师可以评估生产效益,制定生产计划,优化生产流程,并确定产品的售价和利润。
IE常用公式范文
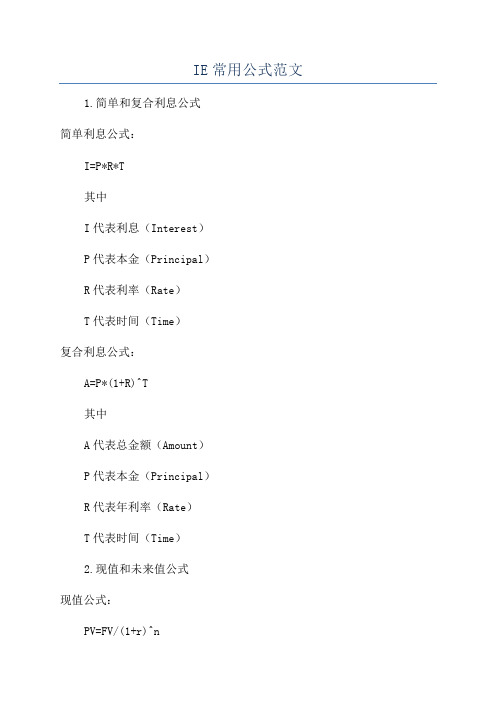
IE常用公式范文1.简单和复合利息公式简单利息公式:I=P*R*T其中I代表利息(Interest)P代表本金(Principal)R代表利率(Rate)T代表时间(Time)复合利息公式:A=P*(1+R)^T其中A代表总金额(Amount)P代表本金(Principal)R代表年利率(Rate)T代表时间(Time)2.现值和未来值公式现值公式:PV=FV/(1+r)^n其中PV代表现值(Present Value)FV代表未来值(Future Value)r代表折现率(Discount Rate)n代表时间(Time)未来值公式:FV=PV*(1+r)^n其中PV代表现值(Present Value)FV代表未来值(Future Value)r代表折现率(Discount Rate)n代表时间(Time)3.折旧公式直线折旧法公式:D=(C-S)/T其中D代表折旧费用(Depreciation)C代表资产原值(Cost)S代表预计残值(Salvage Value)T代表使用寿命(Useful Life)4.利率转换公式年化利率公式:Ear = (1 + R/n)^n - 1其中Ear代表年化利率(Effective Annual Rate)R代表名义利率(Nominal Rate)n代表复利计算的次数5.均值和标准差公式均值公式:Mean = (X1 + X2 + ... + Xn) / n其中Mean代表均值X代表样本值标准差公式:SD = √[(Σ(Xi - Mean)^2) / n]其中SD代表标准差Xi代表样本值Mean代表均值n代表样本数量6.风险和回报公式夏普比率公式:Sharp Ratio = (Rp - Rf) / σp其中Sharp Ratio代表夏普比率Rp代表投资组合的年化收益率(Portfolio Return)Rf代表无风险利率(Risk-Free Rate)σp代表投资组合的年化标准差(Portfolio Standard Deviation)7.投资回报率公式投资回报率公式:ROI=(收益-成本)/成本其中ROI代表投资回报率(Return on Investment)收益代表投资获得的收益(Revenue)成本代表投资的成本(Cost)8.成长率公式成长率公式:成长率=(最终值-初始值)/初始值*100其中成长率代表其中一变量的增长率(Growth Rate)最终值代表变量的最终值(Final Value)初始值代表变量的初始值(Initial Value)9.成本平均公式成本平均公式:Average Cost = Σ(Ci * qi) / Σ(qi)其中Average Cost代表平均成本Ci代表产品单价(Unit Cost)。
- 1、下载文档前请自行甄别文档内容的完整性,平台不提供额外的编辑、内容补充、找答案等附加服务。
- 2、"仅部分预览"的文档,不可在线预览部分如存在完整性等问题,可反馈申请退款(可完整预览的文档不适用该条件!)。
- 3、如文档侵犯您的权益,请联系客服反馈,我们会尽快为您处理(人工客服工作时间:9:00-18:30)。
一.流水线优化部分:1.输送带的pitch 时间 = 整日的上班时间/日产量*(1+不良率)2.输送带的速度 = 记号间隔距离 /输送带的pitch 时间3.日产量 = 整日的上班时间/实际际cycle 时间(瓶颈站的作业时间)4.效率 = 投入cycle 时间/实际cycle 时间 = 第一站的作业时间/最后一站5.的作业时间(当然也可用瓶颈站的作业时间来算, 不过观察最后一站总是较简单、实际)6.在流水线上的在制品数量就= ( 最后一站的作业时间 - 第一站的作业时间 ) * (整日的上班时间/最后一站的作业时间)7. 稼动率 = 在作业的时间 / 整日的上班时间(所谓稼动就是流水线上有效的工作)二.流水线设计部分:1.先求节拍时间 C=2.工站理论值 N=3.评价流水线效率=4.选择作业分配原则:A 按后续作业量的多少来安排作业(第一规则遇到问题时采用第二规则)B 按作业时间最长安排作业(若作业最长时间相同,任选其一安排作业) 三.生产线平衡部分:1.生产线平衡率=各工序时间总和/(人数×CT )×100% =∑ti /(人数×CT )×100%2.生产线平衡损失率=1-生产线平衡率 3、生产线平衡改善的方法➢ 工时长的工序的改善方法:A .细分作业内容,将一部分作业转移至其他工序B .改善作业本身C .谋求工序机械化D .通过改良,增大机器的运作能力E .增加作业人数F .调配经验丰富,作业技能高的熟练作业人员G .“瓶颈”工序能力不足的部分,利用加班完成,或用其他方法完成 ➢ 工时短的工序的改善方法:A .细分作业内容,将作业转移至其他工序,取消该工序B .从其他工序转移来部分作业内容,增加作业量C .将同是作业工时短的工序合并起来D .在不影响后工序的前提下,采用继续集中作业方式 4、生产线平衡分析步骤➢ 决定分析对象和要达到的目标 ➢ 取得相关人员的理解和帮助 ➢ 分解各工序的作业单元 ➢ 测定每个作业单元的时间每天的生产时间每天的计划产量 完成作业所需的时间总量 T节拍 C完成作业所需的时间总量 T 实际工站数目N ×节拍C➢实际修正测定工时➢求出每个线点时间➢作成线点运行表➢计算平衡效率(浪费率)➢研讨工序平衡5、现场生产线平衡分析对生产中的生产线进行分析时,依下述步骤进行:1)对生产线的各工程顺序(作业单位)予认定,并填入生产流动平衡表中2)测算各工序实质作业时间以DM (Decimal Minute )为单位记入平衡表内(1人实质时间栏)注:1DM=0.01分=0.6秒3)清点各工序作业人数,并记入人员栏内4)1人实质作业时间÷人数 = 分配时间,记入时间栏 5)依此分配时间划出柱状图或曲线图6)在分配的实质时间最高的这一工序顶点横向划一条点线 7)计算不平衡损失上面斜线部分的总和即为不平衡损失的总和 T (Lose )=Σ|Tm-Ti|不平衡损失=(最高的DM×合计人数)-(各工序时间的合计)如下图8)生产线平衡率生产线平衡率=——————————————9)生产线不平衡损失率=1-生产线平衡率10)如使用输送带之动力传送,则应计算输送带的流动速度(M/时间单位) 称为节拍时间,符号TC 。
通常TC=实际工作时间 ÷ 生产量在TC 计算出来后,在横向划线,划上节拍时间的线后生产线是否平衡就清楚了,将生产线流动平衡图画出,并计算平衡损失率及节拍时间后一条生产线的基本面貌就呈现出来了,根据这个面貌进行进一步的改善。
改善依三个方向来进行: (1)、如何减少耗时最长工序(第1瓶颈)的作业时间。
A.作业分割, 将此作业的一部分分割出来移至工时较短的作业工序。
B.利用或改良工具、机器, 将手改为工具,或半自动或全自动机器,或在原有工具、夹具做改善,自然可提升产量缩短作业工时。
各工序实质时间(1人)合计最高DM ×合计人数C.提高机械效率, 研究如何把现有的机器产能提升。
D.提高作业者的技能, 运用工作教导,提升作业者技能。
E.调换作业者, 调换效率较高或熟练作业人员。
F.增加作业者, 上面的工作都做了,还未达到理想,可能就得考虑增加此一工序的人员了。
(2)从作业方法改善运用改善四要法(工作简化法)进行方法改善。
「剔除」不必要的动作。
「合并」微小的工作。
「重排」作业工序或动作。
「简化」复杂的动作。
(3)对于有防碍效率的布置或环境进行改善。
四.生产设备部分:某工序所需设备数S ί :①与流水线同步完成加工:S ί = t ί / C 式中:S ί——第i 道工序所需设备数;t ί——第i 道工序的单件时间定额,C 为流水线节拍。
②与流水线节拍不同步完成(设定完成时段)S ί =[工序工时(分)×产量]/[所设时段内有效工作日]计算出的设备需要量若不是整数,则采用的设备数S ί应取接近于计算数S ί的整数,合并“同类项”(所有车间共需同种设备),即可得某种设备的总数(可设不同时段),同理:可得各种设备的总数,工作地的数量可用同样方法求得。
③设备负荷数 K ί= S ί / S e ί 式中:K ί——第ί道工序的设备负荷系数, S ί ——第ί道工序的实际设备数量,S e ί ——第ί道工序的计算设备数量④工序数为m 的流水生产线的总设备负荷系数K 等于K = ∑S ί / ∑S e ί设备负荷系数决定了流水生产线的连续程度。
当K 值在O.75以下,宜组织间断流水生产线;当K 值在O.75以上,宜组织连续流水生产线。
⑤计算工人人数A.在以手工劳动为主的流水生产线上,工人人数可按下式计算:P ί = S e ί ×g×W 式中:P ί —— 第 ί 道工序的工人人数;g —— 每日工作班次;W —— 第 ί 道工序同时工作人数 整条流水生产线的工人人数是所有工序工人人数之和。
B.在以设备加工为主的流水生产线上,工人人数可按下式计算:P = (1+b )∑式中:P ——流水线工人总数;b ——考虑缺勤等因素的后备工人百分比; f ί ——第 ί 道工序每个工人的设备看管定额。
⑥在采用机械化传送带时,需要计算传送带的速度和长度。
在工作式传送带连续运动时,传送带速度V ,可按下式计算:V L 0 / R 式中: L 0——传送带分区(例相邻工位)单位长度。
工作式传送带的速度不能太快,以便工人安全顺利地完成工序作业,在工作式传送带间歇运动时、每隔一个节拍移动一次。
工作式传送带工作部分的总长度可按下式计算: L =∑L ί +L 0 式中:L ——传送带长度;L ί——第 ί 道工序工作地长度; L 0——后备长度。
在分配式传送带流水生产线上,传送带起运输和分配制品的作用。
分配式传送带的速度应该和流水生产线的节拍相配合,其长度计算方法与工作式传送带相同。
为使分配式传送带起分配制品的作用,必须在传送带上做号码标记。
按号码标记将制品分配给工人i =1 m S eί×gf ί加工。
例图如下:五.IE部分:IE七大手法:1)動作改善法(動改法)2)防止錯誤法(防錯法)3)5·5W1H法 (五五法)4)雙手操作法(雙手法)5)人機配合法(人機法)6)流程程序法(流程法)7)工作抽樣法(抽樣法)A.工作抽样的观测精度,一般取2σ的范围,根据统计学中的二项分布标准差σ,子一定条件下有:式中:P-觀測事件發生率,n-觀測次數,Z-正態分佈下的Z值,E为绝对精度B.相对精度为绝对精度与观测时间发生率之比:C.观测次数的多少由绝对误差和相对误差公式来确定:正式观测以前,需要进行一定次数的试观测,通过试观测,得出观测时间的发生率,然后根据公式(公式四)或(公式五)决定正式观测次数D.异常值剔除,运用三倍标准差法:设对某一操作单元观测n 次,所得时间为: x 1,x 2,x 3,---x n 则平均值为:= =标准差 ==正常值为 ±3 范围内的值,超出者为异常值应剔除。
E.剔除异常值后,决定每一单元的平均操作时间:每一单元的平均操作时间=xx 1+x 2+x 3+---+xn xi ∑nnσ(x 1-x)2+(x 2-x)2+---(x n -x)2n(x i -x)2 ∑i =1n ni =1 nx∑(观测时间值) 观测次数一般都将可靠度定为95%,相对精度为±5%F .G .观测次数是根据可靠度和精确度要求而定的,在可靠度取95%时,所需观测次数,可按下式计算:H 、 离散型数据分析:U (Unit ):元件,元件測定可能機會的細節DPU (Defect Per Unit ):每個元件內存在的缺陷數 DPO (Defect Per Opportunity ):每個機會損失數 DPMO (Defect Per Million opportunity )(每百萬要會損失數) ❖ 1,000,000單元存在的損失數❖ DPO × 1,000,000轉換Six Sigma 比率P (ND )=None Defect :無損失,機會不能成為損失的可能性,P (ND )=1-DPO❖ 利用泊松公式計算收率利用泊松公式❖ 這里Y :收率,DPU :元件缺陷數,R :,e :指數函數2.71828… r=0時n= 4P(1-P) E 24(1-P)S 2P用绝对精度E 用相对精度S n=∴Y=e -dpu∴對缺陷機會數越大,“Y ”越接近“0”六、制程能力分析:Cp (capability of precision )精确度:是衡量工序能力对产品规格要求满足程度的数量值,记为CP ,通常以规格范围T 与工序能力6×σ的比值来表示,即 Cp = =规格公差/6×标准差规格公差=UCL-LCL=规格上限-规格下限1、 制程精密度,其值越高表示制程实际值间的离散程度越小,亦表示制程稳定而变异小,离中趋势与σ有关;2、 当公差范围内能纳入越多的σ个数,则此制程表现越好,其本身是一种制程固有的特性,代表一直那个潜在的能力。
Ca (capability of accuracy)准确度:代表制程平均值偏离规格中心值的程度,若其值越小,表示制程平均值越接近规格中心值,亦即品质越接近规格要求的水准,值越大,表示制程平均值越偏离规格中心值,所造成的不良率将越大。
Ca= =规格允差 T= 规格上限-规格下限,U 为规格中心, Ca 等级评定后处理原则:T6×σ 制程平均值-规格中心值 规格允差之半×100% T/2 X-U×100%规格中心值X 实绩X 实绩X 实绩规格上限(下限)12.5% 25% 50% 100%A 、作业员依作业标准继续维持B 、有必要时,尽可能改为A 级C 、作业员可能看错规格或未按照作业标准操作,应加强训练,检讨规格及作业标准D 、应采取紧急措施,全面检讨可能影响因素,必要时停产Cpk 制程能力指数:一种以量度某一特性的变化趋势及概率的统计指标,Cpk = Cp ×(1- |Ca |)=Cpk =min (Cpu = ,Cpl = )即,取两者最小值,但不管采用哪种方式,结果都是一样的。