高耐碱分散染料染色一浴法工艺
TC混纺针织物气流缸碱性一浴二步法染色工艺

印染专业参评项目染色新工艺改造——T/C混纺针织物气流缸碱性一浴二步法染色工艺绍兴县职业教育中心纺织专业部王国栋一、构思采用老的染色工艺方法来染T/C混纺针织物在漂底时需要控制漂液在碱性(pH值约为10-11),漂底结束后用常规分散染料染涤纶(pH值约为4-5),染涤结束后需要还原清洗(pH值又变为12-13),再套染棉纤维(pH值为10-11)。
我们可以看出,用老的工艺来染色pH值范围波动很大(碱性——酸性——碱性),从而出现一系列的问题(易染花、低聚物析出、色光不稳及手感差)。
而新的染色工艺所用的分散染料是由浙江龙盛所生产的碱性分散染料来代替常规的分散染料,使得在染涤纶时染缸内的染液的pH值也处于碱性条件下,一般控制其pH 值为10-12。
控制加工液的pH值始终处于碱性条件,能有效控制涤纶酸性条件下染色的弊病(低聚物问题),同时稳定染色后织物的色光,染色均匀性提高,使织物手感更佳,并能大幅降低染色成本。
二、原理棉纤维的漂底(包括涤纶的去油)需要在碱性条件下进行,且需要用双氧水;传统的涤纶分散染料染色需要在弱酸性条件下(一般用醋酸)进行。
涤纶染色染浴的pH值和棉纤维漂底染浴的pH值上存在着矛盾,前道漂底的碱如果去除不净,还会引起涤纶酸性条件的pH值波动,引起染色色光的波动。
而涤纶纤维中所含的低聚物量约占1%~3%,它们在常温下不溶于水,高温(约130℃) 下微溶于水,冷却时能析出。
涤纶在酸性条件下染色时,会产生大量低聚物,低聚物在酸性条件下溶解度很低,沉积在纤维上,使纤维变得粗糙,摩擦系数增大,从而影响纤维性能及外观,会造成染斑、色点、色花、色泽变化、手感差等情况,也会影响以后的加工过程,因此很难获得高品质的产品。
另外,在酸性条件下染色时,所产生的大量油状低聚物也牢固地附着在高温高压气流染色缸内壁及管道中,这样就增加了缸体清洁的难度;低聚物对染料有亲和性,以它为核心,会使染料的二次聚集,尤其是在染色用水中含有金属离子(Ca2+、Mg2+) 的情况下,低聚物冷却时更易析出。
涤棉针织物分散_活性染料一浴一步法染色工艺

2 分散 /活性一浴一步法染色工艺
2 . 1 染料的选择 选择染料时应防止两种染料产生沉淀 (可用 防沉淀剂 ), 防止沾色影响色光、牢度。考虑到染 料或助剂之间会相互作用影响到染色进行, 要选 择牢度相近的染料。这不仅对服用性能而言, 还 需要考虑后续染整加工的忍受程度。如分散活性 染料上染涤棉时, 在热定形处理中应考虑分散染
化纤与纺织技术 14 Chem ica l F iber & T ex tile T echno logy
第 1期 2005 年 3 月
型活性染料的反应性比 K 型活性染料高, 其反应 式如下 :
N D NH C N C R N D NH C N C R C N O cell + N CO OH C N N COOH + HO cell
第 1期 2005 年 3 月
化纤与纺织技术 Che m ical F iber & T extile T echno logy 13
文章编号 : 1672- 500X ( 2005) 01- 0013- 04
涤棉针织物分散 /活性染料一浴一步法染色工艺
李伟勇, 郑向红
(广东纺织职业技术学院, 广东 佛山 528041)
收稿日期 : 2004- 09- 24
1 染色基本原理
1 . 1 分散 /活性染料一浴一步法技术关键 很多分散染料分子中含有酯基、酰胺基、氰 基等基团, 这些基团在高温碱性条件下易发生水 解。例如: CH 2 C H 2OCOCH3 + H 2O CH3 COOH NH COCH 3 + H 2 O CN + H 2O
浴比 染色操作曲线同前。
1#40
2 . 2 . 3 分散匀染剂 用于分散 /活 性染料一浴一步法的分散匀染 剂必须要耐元明粉和耐高温。分散匀染剂用量必 须适当 , 过多会降低染 料上染量或产生 焦油状 物 ; 用量过少, 则分散液稳定性差。常用的分散 剂一般选用阴离子表面活性剂和非离子表面活性 剂作为染色匀染剂, 前者的作用是其亲油基吸附 在染料微粒表面 , 而亲水基则围绕在外 , 形成胶 束溶液 , 借助于胶束之间的相斥作用 , 使染料微 粒保持分散状态 , 防止了染料的聚集。这类分散 剂扩散效果好, 在高温时比较稳定, 对得色的影 响小。后者的作用是增加染料的溶解作用, 并抑 制染色 开始时的急剧 吸色, 加强染色的 匀染作 用。这类分散剂 分散效果 明显, 并 兼有匀 染作 用 , 但对得色量有一定的影响。 常用的分散高温匀染剂如 FZ - 802 匀染剂 ( 南京钟山化工厂 ) 、高温匀 染剂 GS( 上 海助剂 厂 ) 、高温匀染剂 A- 10( 常州曙光化工厂 )等 , 具 有匀染性强、 竭染性好、 价格低等优点, 并可替代 日本进口的 Toho Sa lt A - 10 、UF - 350 。通过试 验 , 选用南京钟山化工厂的 FZ- 802 匀染剂 , 染 色织物无染斑、色花等疵病 , 效果理想。其用量 一般控制在 0 . 5~ 1g /L。 2 . 2 . 4 皂洗和固色 ( 1) 皂洗 用分散 /活性染料一 浴一步法染色后, 既要 去除吸附在织物上的水解活性染料, 又要去除纤 维素纤维上吸附的分散染料, 因此必须对被染织 物进行皂洗。 取染毕的棉针织物 2g , 置于 100mL 的 1g /L 皂液中, 从室温升至 95∀ , 皂煮 15m in、 洗净 , 然 后做皂洗牢度试验, 试验结果为原样变色达 4~ 5 级 , 白布沾色达 4级 , 染色牢度良好。 ( 2) 固色 选用 R 型活性染料与分散染料进行 一浴一 步法染色 时, 织物 应先经 皂洗 , 再用 固色剂 固 色 , 以防止活性染料与纤维素的共价键水解断键 后 , 使色布的水洗牢度下降。 按染色深度 , 固色处理为 : 浅色品种 ( < 0 . 5 % ), 一般不需要进行固色
学习分散/活性染料一浴法生产工艺

学习分散/活性染料一浴法生产工艺聚酯纤维和纤维素纤维混纺织物常采用活性染料和分散染料染色,染色方法一般可以分为:二浴法、一浴两步法、一浴一步法。
一浴法染色主要优势是:缩短染色时间;节约能耗和用水,减少污水;简化染液配制与加料的操作,以及减少由此带来的相关问题。
本文主要对聚酯/纤维素一浴法染色及其所用中性固色活性染料进行综述。
1分散/活性一浴法染色难点1、染色温度分散染料在聚酯纤维中扩散速率很低,所以染色温度高,一般为110~130℃,远高于常用活性染料染色温度,载体染色时,虽然可在100℃左右,这对活性染料来说还是较高的,活性染料染色大部分温度在60~90℃,温度高不仅固色效率低,而且染料直接性降低后难染的深色。
2、染色pH值活性染料大部分是在碱性条件下固色的,而分散染料高温高压染色应在弱酸性介质中进行,载体法染色也是在弱酸性介质中进行。
因大多数分散染料在碱性条件下很容易发生水解或还原破坏,使染料发生色变或退色,而活性染料如在弱酸性条件下固色,不仅固色效率低,而且染料和纤维之间的共价键的断裂速度也快。
3、电解质活性染料浸染时为了提高上染速率和上染百分率,需要加入一定量的中性电解质,特列是在染色温度高和浴比大时,加入量更多。
分散染料是靠分散剂呈悬浮体分散在染液中,分散稳定性随染液中电解质含量的增加而降低,大量的电解质使分散染料颗粒增大,甚至产生沉淀,从而降低其上染率和匀染效果。
4、染料之间或活性染料和分散剂之间的相互作用许多分散染料及分散剂在温度较高的条件下,会与活性染料发生反应,使分散染料和活性染料的固色率均降低,特别容易发生在染色或固色温度较高的情况下,如高温高压法染色。
采用载体法染色时,载体也会与活性染料发生反应。
5、染色牢度由于两种染料不仅上染对应的纤维,还会严重对另一种纤维发生沾色,特别是分散染料对纤维素纤维,例如对棉纤维的沾色,会大大降低其皂洗和摩擦牢度,这也是当前这类混纺织物染色牢度较差的重要原因。
分散/活性染料染涤棉新工艺—一浴法

新技术分散微胶囊/活性染料染涤棉(一浴法)姓名:摘要本文采用原位聚合法对分散染料进行双层造壁,制得分散染料微胶囊并应用于分散染料微胶囊/活性染料涤棉一浴法染色。
通过改变染色条件中的浴比、染色温度、保温时间,研究分散染料微胶囊/活性染料染涤棉织物的一浴法染色新工艺,并比较全面的分析一浴法比传统染色法的优势。
关键词:涤棉混纺活性染料分散染料微胶囊一浴法1.传统分散/活性染料染色工艺及其流程1)一浴二步法图1工艺(一浴二段,7~8 h)工艺曲线2)传统工艺(二浴二步法)图2传统工艺(二浴二段.10~11 h)工艺曲线3)一浴一步法图3分散/活性染料一浴法染色工艺曲线2.分散染料微胶囊/活性染料一浴法染色工艺1)分散染料微胶囊的制备分散染料、系系统调节剂MS、蒸馏水于高剪切混合乳化机中高速均化后,调节pH值至4~6。
将乳化好的乳液倒入三颈圆底烧瓶中,放入恒温水浴,在一定搅拌条件下滴加一定量的密胺树脂预聚体,升温至65度,保温1小时,进行单层造壁;冷却至室温后,在条件下继续滴加一定量的密胺树脂预聚体,升温至75度,保温2.5小时,进行双层造壁,降温,洗涤,抽滤,干燥,待用。
2)分散染料微胶囊/活性染料一浴法染色工艺流程取涤棉织物,于芯材:壁材=1:1 的分散染料微胶囊(芯材即分散染料用量:2%织物重量比)、活性染料(用量:2%织物重量比)、元明粉(用量:40g/L)一道置于染色软中,加入蒸馏水(浴比分别为1:10,1:20,1:30,1:40)至刻度,染色密封后置于红外线高温高压染色机按图1所示染色工艺染色。
图4分散染料微胶囊/活性染料一浴法染色工艺曲线3)测试染色皂洗工艺:皂片2g/L,浴比1:20,90度*20min,水洗,烘干。
为对比起见,传统的分散/活性染料一浴法染色中的分散染料使用分散染料,其中不含任何分散助剂,染色时再另外加入分散助剂以配合染色。
这样以保证不同染色工艺的分散染料的实际用量相同。
涤棉织物一浴练染工艺
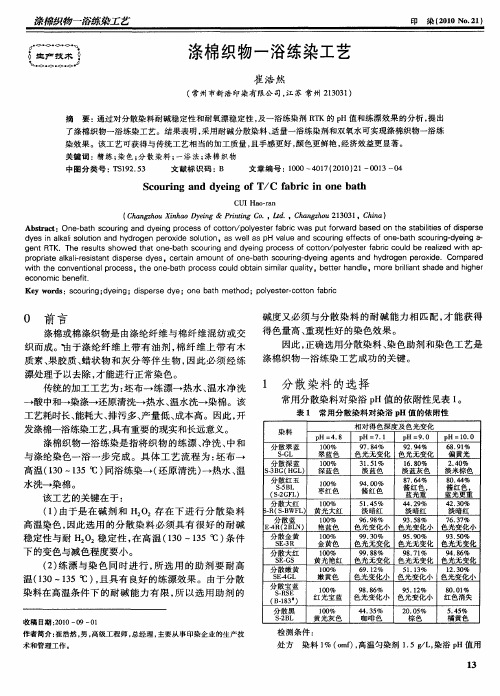
( h nzo i a yig& Pit gC . Ld , h nzo 10 1 C i ) C a gh uXn oD e h n r i o 。 t. C a ghu2 33 。 hn nn a
Ab ta t s r c :O n — a h s ou i g a d d en r c s fc tO / Oy s e a r a u o w a d b s d o h t bl is o ip r e e b t c r n y ig p o e s o O t n p le t r b i w s p tf r r a e n t e s a it fds e s n f c ie d e n ak ls u i n a d h d o n p r xd o u i n s w el s p a u n c u ig e f c s o e b t c u ig d en — y s i la i olt n y r ge e o i e s lto ,a la H v l e a d s o r fe t fon - a h s o r — y i g a o n n
1 分 散 染 料 的选 择
常用 分散染 料对 染浴 p H值 的依附性 见表 I 。
表 1 常 用 分 散 染 料 对 染 浴 p 值 的依 附 大 、 排污 多 、 量低 、 产 成本 高。 因此 , 开
发涤棉一浴练染工艺 , 具有 重要 的现实和长远意义 。 涤棉 织物 一浴练 染是 指将 织 物 的练 漂 、 净洗 、 中和
g n TK e tR .T e r s l h we h ton — a h s o r g a d d e n r c s fc t n p le t rf b i c u d b e l e i p h e ut s o s d t a e b t c u i n y ig p o e s o 0 t / oy s e a r o l e r ai d w t a - n O c z h
涤纶碱减量和染色—浴处理工艺研究
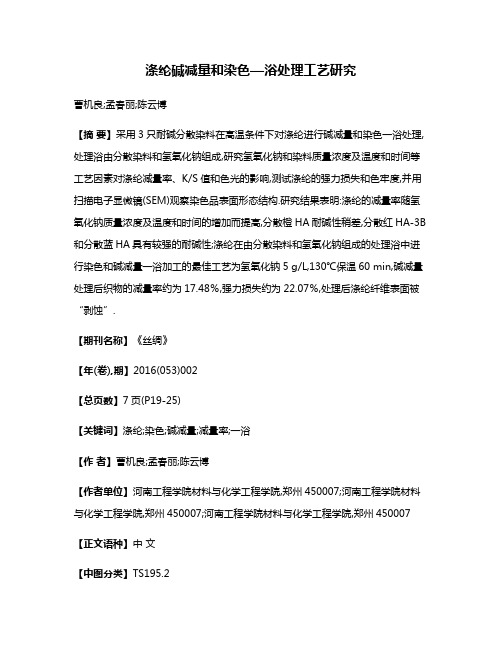
涤纶碱减量和染色—浴处理工艺研究曹机良;孟春丽;陈云博【摘要】采用3只耐碱分散染料在高温条件下对涤纶进行碱减量和染色一浴处理,处理浴由分散染料和氢氧化钠组成,研究氢氧化钠和染料质量浓度及温度和时间等工艺因素对涤纶减量率、K/S值和色光的影响,测试涤纶的强力损失和色牢度,并用扫描电子显微镜(SEM)观察染色品表面形态结构.研究结果表明:涤纶的减量率随氢氧化钠质量浓度及温度和时间的增加而提高,分散橙HA耐碱性稍差,分散红HA-3B 和分散蓝HA具有较强的耐碱性;涤纶在由分散染料和氢氧化钠组成的处理浴中进行染色和碱减量一浴加工的最佳工艺为氢氧化钠5 g/L,130℃保温60 min,碱减量处理后织物的减量率约为17.48%,强力损失约为22.07%,处理后涤纶纤维表面被“剥蚀”.【期刊名称】《丝绸》【年(卷),期】2016(053)002【总页数】7页(P19-25)【关键词】涤纶;染色;碱减量;减量率;一浴【作者】曹机良;孟春丽;陈云博【作者单位】河南工程学院材料与化学工程学院,郑州450007;河南工程学院材料与化学工程学院,郑州450007;河南工程学院材料与化学工程学院,郑州450007【正文语种】中文【中图分类】TS195.2为解决涤纶亲水性、手感等方面的缺陷,常对其进行仿真丝处理,处理后的织物可获得真丝般手感,亲水性也得到一定的提高[1-2]。
大多数涤纶的染色在仿真丝整理后进行,分散染料是其常用染料,染色后织物可获得优良的色泽和满意的牢度[3-4]。
传统的涤纶染色和仿真丝处理一般分两步进行:首先在烧碱和阳离子表面活性剂溶液中对涤纶进行仿真丝处理,然后用分散染料对涤纶进行染色[5]。
两步加工能保证涤纶仿真丝和染色产品的质量,但其工艺流程复杂,能源和化学品消耗大,不符合当前节能减排的发展趋势[6-7]。
因此,如何缩短涤纶仿真丝和染色工艺流程成为当前研究的方向之一。
仿真丝处理需要在碱性条件下进行,故涤纶仿真丝和染色一浴加工的实现需要采用耐碱分散染料。
分散/活性浸染一浴法生产实践

升 温 至 1 5 C , 间 3 n 保 温 完 毕 , 按 2 C/ n 3 时 0mi ; 再 mi 降温至 7 0℃ ; 出样 杯 , 开 , 于 7 _ 浴 锅 内 , 取 旋 置 0 C水 加 入 适 量 纯 碱 , 玻 璃 棒 不 停 搅 拌 , 温 3 n, 出 染 用 保 0mi 取
根 据 B 型 活 性 染 料 的 特 征 , 分 散 / 性 一 浴 法 浸 染 工 艺 进 行 了 小 样 试 验 , 进 行 中 样 和 大 生 产 。结 果 表 明 , 对 活 并
该一 浴 法工 艺是 可行 的 , 色光 比二 浴法 更稳 定 。 且 叙 词 : 浸染 一 浴 法 分 散 染 料 活 性 染 料
样冷水洗 , 洗 ( 皂 阴离 子 型 净 洗 剂 1g i) 熨 烫 , 色 。 / , 对 () 2 比较 同 浴 与 二 浴 的 小 样 和 大 样 , 者 的 差 别 仅 两 是 色 光 略 有 差 别 , 度 、 面 匀 染 性 无 差 异 , 色 牢 度 深 布 染 达 到 国家 标 准 。
化 钠 、 碱 纯
2 中样 试 验
在 化 验 室 小 样 的 色 光 、 色 牢 度 及 工 艺 达 到 预 期 染 标 准 要 求 后 , 此 工 艺 进 行 中 样 试 验 。 用 国 产 单 管 对
RWP 高 温 高 压 喷 射 染 色 中 样 机 进 行 试 验 。 试 样 数 量
4 5 3 ×7 3英 寸 涤 棉 混 纺 细 平 布 2 g, 以 5 ×4 1 3 2 6 0k 按
活 性 基 和 乙 烯 砜 硫 酸 酯 活 性 基 , 者 与 染 色 物 产 生 的 前
共 价 键 耐 碱 不 耐 酸 , 者 则 耐 酸 不 耐 碱 。B型 活 性 染 料 后 综 合 这 两 者 的优 势 , 耐 酸 又 耐 碱 。 同 时 , 既 B型 活性 染 料 耐 高 温 , 就 为 设 想 的 分 散 / 性 同 浴 工 艺 创 造 了 有 这 活 利条件 。
采用分散-活性一浴法染色工艺解决涤锦显色性及色牢差问题

采用分散/活性一浴法染色工艺解决涤锦显色性及色牢差问题涤锦复合超细纤维线密度低,比表面积大,且由于涤锦两种纤维结构不同,在匀染性和显色性上存在差异,色牢度也较差。
适用于涤纶染色的染料主要是分散染料;能用于锦纶染色的染料主要有分散染料、中性染料、酸性染料、酸性媒染染料和活性染料等。
其中分散染料、中性染料和酸性(媒染)染料对锦纶色牢度较差,活性染料染色牢度较好,但其在锦纶织物上的提升性和移染性欠佳,且若与分散染料同浴浸染,在染色温度、pH值和电解质上有差异。
为了获得较好的染色牢度,特别是对于一些湿牢度要求高的产品,很多厂家还是希望采用活性染料进行染色。
本课题通过对活性染料和分散染料进行选择,并改进了染色工艺,确定了适合于涤锦复合超细纤维分散/活性染料一浴法染色的高色牢度浸染工艺。
试验材料、药品和仪器材料涤锦复合纤维织物[将178 dtex/72f×16p 涤锦复合纤维摇成袜筒, 18G, (160±10)g/m2,广东河源市新东江化纤有限公司];涤纶细旦针织物(44 dt- ex/36 ,f 40 G, (130±10)g/m2,杰典纺织品有限公司);锦纶细旦针织物(77 dtex/68 ,f 36 G, (180± 10) g/m2,杰典纺织品有限公司)。
药品NaOH, HAc, Na2CO3, CaCl2, Na2S2O4, NH4Ac,NaC,l NaHCO3,渗透促进剂Cibaflow Je,t分散剂Univadine DP,交联剂EriofastFix,扩散促进剂Uni- vadine PB,匀染剂UnivadineMC new,清洗剂Ciba Eri- opon ols,渗透剂JFC,Eriofast活性染料系列,TerasilW 分散染料系列,HT、KE、HE系列高温型活性染料(对比试验用),酸性染料系列。
仪器电子分析天平、电热恒温烘箱、高温染色小样机、电脑测色仪、耐洗色牢度试验机、可见分光光度计。
涤棉一浴一步法染色加工方法的探究
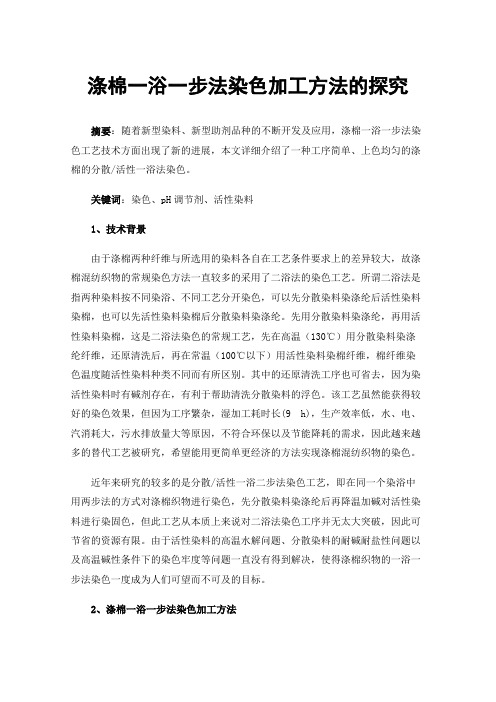
涤棉一浴一步法染色加工方法的探究摘要:随着新型染料、新型助剂品种的不断开发及应用,涤棉一浴一步法染色工艺技术方面出现了新的进展,本文详细介绍了一种工序简单、上色均匀的涤棉的分散/活性一浴法染色。
关键词:染色、pH调节剂、活性染料1、技术背景由于涤棉两种纤维与所选用的染料各自在工艺条件要求上的差异较大,故涤棉混纺织物的常规染色方法一直较多的采用了二浴法的染色工艺。
所谓二浴法是指两种染料按不同染浴、不同工艺分开染色,可以先分散染料染涤纶后活性染料染棉,也可以先活性染料染棉后分散染料染涤纶。
先用分散染料染涤纶,再用活性染料染棉,这是二浴法染色的常规工艺,先在高温(130℃)用分散染料染涤纶纤维,还原清洗后,再在常温(100℃以下)用活性染料染棉纤维,棉纤维染色温度随活性染料种类不同而有所区别。
其中的还原清洗工序也可省去,因为染活性染料时有碱剂存在,有利于帮助清洗分散染料的浮色。
该工艺虽然能获得较好的染色效果,但因为工序繁杂,湿加工耗时长(9 h),生产效率低,水、电、汽消耗大,污水排放量大等原因,不符合环保以及节能降耗的需求,因此越来越多的替代工艺被研究,希望能用更简单更经济的方法实现涤棉混纺织物的染色。
近年来研究的较多的是分散/活性一浴二步法染色工艺,即在同一个染浴中用两步法的方式对涤棉织物进行染色,先分散染料染涤纶后再降温加碱对活性染料进行染固色,但此工艺从本质上来说对二浴法染色工序并无太大突破,因此可节省的资源有限。
由于活性染料的高温水解问题、分散染料的耐碱耐盐性问题以及高温碱性条件下的染色牢度等问题一直没有得到解决,使得涤棉织物的一浴一步法染色一度成为人们可望而不可及的目标。
2、涤棉一浴一步法染色加工方法将布料加入到染色浴中,其中染色浴温度为40℃时,依次加入染料及pH调节剂07,运行10分钟后再加染色助剂,其中,染色助剂的添加分两次,第一次添加总添加量的1/3,运行10分钟后将剩余2/3添加进去,保持20 分钟;然后升温至80℃,升温速率为 2 ℃/min,保持20分钟;继续升温至130℃,升温速率为1.67℃/min,在此温度下,保持30分钟,完成染色;降温到80℃后,依次进行初水洗、皂洗和后水洗,初水洗温度为常温,初水洗时间为10分钟;皂洗采用的是酸性皂洗剂DM261,皂洗温度为98℃,皂洗时间为10分钟;后水洗温度为常温,后水洗时间为10分钟。
分散活性一浴两步法热熔染色浅析
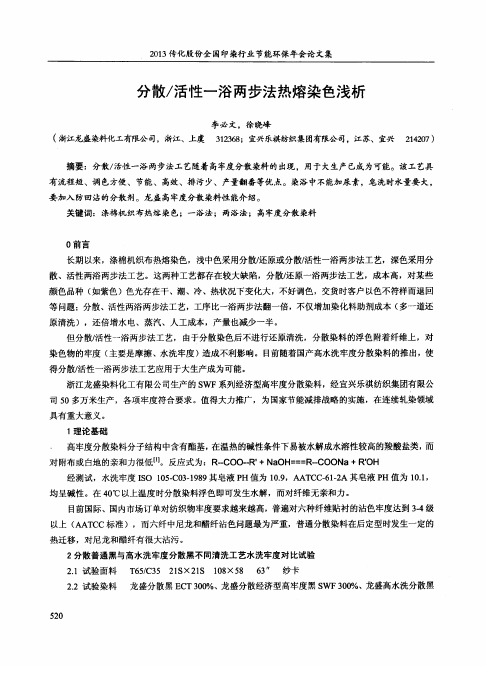
2013传化股份全国印染行业节能环保年会论文集分散/活性一浴两步法热熔染色浅析李必文,徐晓峰(浙江龙盛染料化工有限公司,浙江、上虞312368;宜兴乐祺纺织集团有限公司,江苏、宜兴214207)摘要:分散/活性一浴两步法工艺随着高牢度分散染料的出现,用于大生产已成为可能。
该工艺具有流程短、调色方便、节能、高效、排污少、产量翻番等优点。
染浴中不能加尿素,皂洗时水量要大,要加入防回沾的分散剂。
龙盛高牢度分散染料性能介绍。
关键词:涤棉机织布热熔染色;一浴法;两浴法;高牢度分散染料0前言长期以来,涤棉机织布热熔染色,浅中色采用分散,还原或分散/活性一浴两步法工艺,深色采用分散、活性两浴两步法工艺。
这两种工艺都存在较大缺陷,分散/还原一浴两步法工艺,成本高,对某些颜色品种(如紫色)色光存在干、潮、冷、热状况下变化大,不好调色,交货时客户以色不符样而退回等问题;分散、活性两浴两步法工艺,工序比一浴两步法翻一倍,不仅增加染化料助剂成本(多一道还原清洗),还倍增水电、蒸汽、人工成本,产量也减少一半。
但分散/活性一浴两步法工艺,由于分散染色后不进行还原清洗,分散染料的浮色附着纤维上,对染色物的牢度(主要是摩擦、水洗牢度)造成不利影响。
目前随着国产高水洗牢度分散染料的推出,使得分散/活性一浴两步法工艺应用于大生产成为可能。
浙江龙盛染料化工有限公司生产的SWF系列经济型高牢度分散染料,经宜兴乐祺纺织集团有限公司50多万米生产,各项牢度符合要求。
值得大力推广,为国家节能减排战略的实施,在连续轧染领域具有重大意义。
1理论基础高牢度分散染料分子结构中含有酯基,在温热的碱性条件下易被水解成水溶性较高的羧酸盐类,而对附布或白地的亲和力很低【l】。
反应式为:R—COO—R-+NaOH===R—COONa+R。
OH 经测试,水洗牢度IsO105.C03.1989其皂液PH值为10.9,AAl℃c.61.2A其皂液PH值为10.1,均呈碱性。
一浴两步法浸染工艺流程
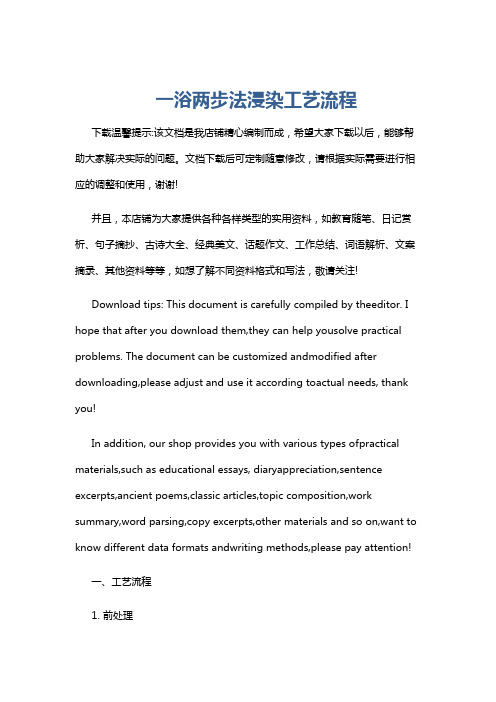
一浴两步法浸染工艺流程下载温馨提示:该文档是我店铺精心编制而成,希望大家下载以后,能够帮助大家解决实际的问题。
文档下载后可定制随意修改,请根据实际需要进行相应的调整和使用,谢谢!并且,本店铺为大家提供各种各样类型的实用资料,如教育随笔、日记赏析、句子摘抄、古诗大全、经典美文、话题作文、工作总结、词语解析、文案摘录、其他资料等等,如想了解不同资料格式和写法,敬请关注!Download tips: This document is carefully compiled by theeditor. I hope that after you download them,they can help yousolve practical problems. The document can be customized andmodified after downloading,please adjust and use it according toactual needs, thank you!In addition, our shop provides you with various types ofpractical materials,such as educational essays, diaryappreciation,sentence excerpts,ancient poems,classic articles,topic composition,work summary,word parsing,copy excerpts,other materials and so on,want to know different data formats andwriting methods,please pay attention!一、工艺流程1. 前处理退浆:去除织物上的浆料,使织物更加柔软。
涤纶织物分散染料减染一浴法染色

2 0 1 4年 6月
染 整 技 术
T e x t i l e Dy e i n g a n d Fi n i s h i n g J o u r n a l
V0 1 - 3 6 N0 . 6
J u n . 2 0 1 4
涤纶织物分散染料减染一浴法染色
Ab s t r a c t T h e t r a d i t i o n a l p r o c e s s o f a l k a l i p e e l i n g a n d d y e i n g wa s c a  ̄i e d o u t i n t wo b a t h p r o c e s s , wh i c h i s n o t o n l y wa s t e o f e n e r g y b u t a l s o c o mp l i c a t e d . Ac c o r d i n g t o t h r e e k i n d s o f d y e i n g p r o c e s s e s , p o l y e s t e r f a b r i c lk a a l i p e e l i n g a n d d y e i n g w i t h
良 ,但存在手感 、透气性差 等缺点 ,可通 过碱减量来
改善 。碱减量是指涤纶织物在浓碱液 或热的稀碱 液作 用下 ,纤维表 面的大分子 发生水解 ,一层层 地剥落下
Ke y wo r d s p o l y e s t e r f a b r i c ;a lk a l i p e e l i n g ;d y e i n g ;o n e b a t h p r o c e s s
涤纶针织物碱减量和染色一浴一步法工艺

涤纶针织物碱减量和染色一浴一步法工艺发布时间:2021-05-19T15:10:03.227Z 来源:《基层建设》2020年第35期作者:圣光[导读] 摘要:为解决常规涤纶织物染整加工需要碱减量、染色、还原清洗、水洗分步分浴进行所带来的耗时耗能等问题,使用耐碱分散染料,采用“碱减量和染色一浴一步法”工艺对涤纶针织物进行染整加工。
杭州卓达染整有限公司摘要:为解决常规涤纶织物染整加工需要碱减量、染色、还原清洗、水洗分步分浴进行所带来的耗时耗能等问题,使用耐碱分散染料,采用“碱减量和染色一浴一步法”工艺对涤纶针织物进行染整加工。
分别探讨一浴一步法工艺中烧碱质量浓度、温度、时间对涤纶针织物性能的影响,得到最优工艺:处理温度为130℃,保温时间为50min,烧碱质量浓度为10g/L。
结果表明:使用相同的染料、助剂及烧碱量对涤纶针织物处理,采用一浴一步法工艺得到织物的染色深度值比常规工艺处理得到的织物大,增深10%左右,若要达到相同的颜色,一浴一步法工艺可有效节省染料的用量;采用一浴一步法得到的染色涤纶针织物能达到免还原清洗的效果,染色产品色光稳定,色牢度优异。
关键词:涤纶针织物;耐碱分散染料;涤纶染色;碱减量;一浴一步法;染色性能涤纶特有的结构和分子链的排列方式使得涤纶织物存在吸湿困难、触感差、手感硬等缺点,服用性能不像天然纤维那么优异。
为了使涤纶织物具有良好的垂悬性、蓬松度和柔软度以及较好的吸湿性和透气性,通常需先对涤纶织物进行碱减量处理。
传统的分散染料结构中通常含有—HNCO—、—CN、—OCO—等基团,这些基团会在高温且有碱的条件下水解导致染料性能如色光、上染百分率等的变化。
为了使其获得良好的手感,避免染色后再进行碱减量处理对已经上染到涤纶上的染料分子造成破坏,传统染色方法采用先碱减量再染色的工艺路线。
本文使用高耐碱分散染料进行涤纶织物的染色和碱减量一浴处理。
由于高温条件下析出的涤纶低聚物在碱性染浴中具有较好的分散性,染色结束后织物可不进行还原清洗,染色设备也不必因涤纶低聚物的不断黏附和积累而需要定期停机清洗。
- 1、下载文档前请自行甄别文档内容的完整性,平台不提供额外的编辑、内容补充、找答案等附加服务。
- 2、"仅部分预览"的文档,不可在线预览部分如存在完整性等问题,可反馈申请退款(可完整预览的文档不适用该条件!)。
- 3、如文档侵犯您的权益,请联系客服反馈,我们会尽快为您处理(人工客服工作时间:9:00-18:30)。
高耐碱分散染料染色一浴法工艺
高耐碱性分散染料应运
高耐碱性分散染料不但适应于在弱酸性条件下对涤纶的染色,也适用于在中性和碱性条件下对涤纶进行染色,工艺执行过程就是把涤纶的前处理和染色一浴进行。
以涤锦珊瑚绒为例给出了涤纶超细纤维在高碱性条件下染色、开纤、碱减量等工序的工艺参数和操作要点。
该工艺极大地缩短了工艺流程,节约了时间,从而达到了节能、减排、降低生产成本的目的,同时减少了环境污染。
经测试,色牢度、色光等指标都符合要求,是值得推崇的新工艺。
传统涤纶的染色与高耐碱性分散
涤纶是目前应用量很大的一类合成纤维,多年以来,涤纶的染色都是在弱酸性条件下采用高温高压染色的传统工艺。
对需要高碱处理的涤纶材料来中,该工艺工序多,流程长,水、电、汽消耗量大,已产效率低,生产成本高,污水排放量大,加重了环笔污染程度,也增加了处理废水的负担。
采用高耐碱性分散染料染色涤纶可以克服以上这些缺点。
蓬莱嘉信染料化工有限公司近年来致力于高耐碱型分散染料的研究,生产研制了这套由黄、洋红、兰、深兰、:等十几只颜色组成的高耐碱性分散染料,可以在pH=4.5~14.0的范围内对涤纶进行染色,由于它可以耐10g/L的强碱和6g/L的双氧水,从而可以应用在很多涤纶面料的各种染色工艺中。
本研究以涤锦珊瑚绒为例来探讨高耐碱性分散染料的染色工艺。
涤锦珊瑚绒的一般染色工艺
涤锦珊瑚绒面料(一般是涤锦质量比80:20)的染整加工,一般采用先碱性下开纤、碱减量,然后水洗中和,再在酸性下染涤纶的工艺。
染整工艺流程如下:
毛坯布→退卷→缝头→预定形→碱减量(开纤)→水洗→酸洗中和→高温高压染色→还原清洗→水洗→中和→上柔→脱水→烘干→拉毛→梳毛→剪毛→(摇粒)→拉幅定形→后整理。
1.预定形
涤锦珊瑚绒的加工,预定形是关键的一道工序,不经过预定形的毛坯布在经过碱减量(开纤)、染色后,珊瑚丝弯曲凌乱,不规整,达不到珊瑚绒的风格。
经过预定形后,珊瑚丝排列规整、顺直且蓬松,底丝结构紧密而稳定,在后续染整加工过程中不易卷边。
珊瑚绒毛坯布的预定形,一般温度为165~90℃,时间根据车速而定,张力达到织物平整即可。
2.碱减量(开纤)
在印染工厂中,采用液碱(一般30%的液碱用量5~8 g/L,也可以用片碱换算用量)进行碱减量(开纤),将涤纶纤维中的水溶性聚酯溶解掉,原本粘合在一起的涤/锦两种纤维丝条分散蓬松,成为涤/锦超细纤维单丝束[2]。
再经过水洗、酸中和,使布面不合碱液,呈中性或弱酸性,有利于后面工序在高温高压条件下酸性染色。
在上述染整加工过程中,纤维减量率大约为5.O%~6.0%,减量率不足会影响手感,减量率太大会破坏织物纤维结构,影响强力等。
必须经过实验,找出合理的用碱量,制定合理的工艺条件,保证减量率稳定正常的范围内,不能超过7%~8%。
染整加工过程消耗大量的水、冰醋酸,电力、蒸汽用量都比较大,同时排放了大量的碱性污水,无形中增加了生产成本。
碱减量配方
去油渗透剂EPD l.0g/L,30%的NaOH 10.0g/L,减量促进剂1.0~1.5g/L,浴比1:15~1:20,温度130℃,时间20~30 min。
碱液用量及时间根据客户要求的失重率而定,先前必须做好测试;浴比根据设备不同适当选择。
有的印染厂采用温度98℃、时间60min或温度110℃、时间40min开纤,工艺配方根据实际情况均要相应调整。
3.高温高压染色工艺
经过碱减量后的珊瑚绒在pH=4.5~5.0的条件下进行涤纶染色,由于开纤后涤锦超细纤维的比表面积大,吸附性强,锦纶的初染温度要低,升温速率要慢,以防止色花、色斑的产生。
工艺配方(拼色):分散染料A用量X (omf),分散染料B用量Y (omf),高温匀染剂1.0g/L,醋酸1.0g/L(pH=4.5~5.0),浴比1:8~1:12,温度130℃,时间30~40min(视染料用量而定)。
还原清洗(或皂洗)工艺:保险粉2.0~4.0g/L,片碱2.0g/L,浴比1:10,温度90℃,时间20min。
耐碱分散染料一浴法染色新工艺
高耐碱分散染料的特点
常规的分散染料都是在酸性条件下染色,而开纤则是在碱性条件下进行,所以,常规的分散染料在碱性条件下染色,由于其绝大部分不耐碱(尤其在高温条件下),会发生色变甚至无色的现象。
经过大量的实验,证实常规分散染料无法实现开纤、染色一浴法工艺;而采用高耐碱分散染料却能使开纤、染色同时进行,大大缩短工艺流程。
高耐碱分散染料应用范围广,适应品种多,在pH=4.5~14.0条件下都可以进行;且提升力好,染深性好;分散性好。
由于在碱性条件下染色、排液,还解决了长期困扰涤纶染色的低聚物问题,避免了由于低聚物造成的色花、色斑及设备、管路清洗问题。
浅、中色染色后不需还原清洗,进行皂洗即可达到要求。
高耐碱分散染料的染色新工艺
1.工艺流程
毛坯布(经编或纬编)→(预定型)→开纤、染色一浴→水洗→(还原清洗或皂洗)→脱水→开幅定型(浸轧吸湿速干柔软剂)→后整理。
2.工艺配方
高耐碱分散染料用量X,30% NaOH 7.0 g/L,碱性分散剂FA l.0 g/L,去油精练剂EPD-C 1.0 g/L,浴比1:10~1:15,温度130℃,时间40~50 min。
3.注意事项
(1)耐碱性助剂的选择。
在高温高压碱性条件下染色对助剂有更高的要求:具有良好的耐碱性(在pH=14时分散稳定性良好)、匀染性,耐硬水,泡沫少、易于清洗,不沾污设备,环保无毒,符合纺织品环保要求。
筛选了国内外十几种碱性匀染剂,进行大量实验和测试,最后选择碱性高温分散剂FA。
(2)由于涤/锦超细纤维比表面积大,纤径细,对分散染料吸附速度快,易造成色花、色斑,因此,要严格控制升温速率,特别是温度在80℃以上时,要控制在1.0℃/min,防止上染过快,造成色花。
(3)由于高耐碱分散染料比常规分散染料粘性大,所以化料时,要先将分散剂化好,然后加入化料缸,同分散染料一起搅拌均匀,再打入染缸内。
必要时,要进行过滤网过滤,再打入染缸。
加入染料后,要先运行10 min,然后按照程序缓慢升温染。
染色效果
1.染色牢度
选取耐碱分散染料三原色分散黄HA-2RW 100%、分散红HA-R 200%、分散蓝HA-RL 200%作为代表,测试其在碱性条件下的染色牢度。
高耐碱分散染料三原色在碱性条件下染色的各项牢度均在4级以上,达到或超过规两浴法染色的牢度,能够满足印染厂的牢度要求。
2 .色光变化
分别测试96010片碱用量为2.0 g/L、4.0 g/L、6.0 g/L、8.0 g/L、10.0 g/L 时的色光变化,结果见表2。
可以看出,高耐碱分散染料三原色在片碱用量1-10 g/L范围内色光稳定,能够满足印染厂碱性一浴法加工的需要,特别适用于涤纶超细纤维开纤、碱减量工艺。
一浴法新工艺与传统工艺对比
经过大量的生产实践证明:高耐碱分散染料在涤纶超细纤维染色上,开纤、染色一浴法完全可行,并且产品质量稳定、重现性好、生产效率明显提高,生产成本大幅降低,是值得推崇的一种新工艺。
新工艺染色成本比传统工艺节约688元/t布(未包括减少的污水处理费用),约占40.4%;节水约42.9%,节电约50%,节约蒸汽40%;染色时间节省50%,生产效率提高1倍。
另外,减少污水排放,降低污水处理费用,经济效益非常明显。
生产成本下降
高耐碱分散染料染色一浴法工艺的.出现彻底改变了传统的两浴法染色。
经过大生产证明:采用高耐碱分散染料的同时用耐碱耐高温分散剂进行涤纶染色完全可行,生产总成本降低30%~40%,生产效率提高。
符合当前国家提倡的环境保护、节能减排的大趋势,受到印染企业的欢迎,经济效益和社会效益也非常明显,具有广阔的发展空间。
本文摘自变宝网-废金属_废塑料_废纸_废品回收_再生资源B2B交易平台网站;
变宝网官网:/?cjq
买卖废品废料,再生料就上变宝网,什么废料都有!。