冲压模具设计评审流程
冲压工艺方案及模具资料审签程序

1 范围本程序适用于新开发的所有车型的冲压零件工艺方案评审和模具结构评审(铸件模具)。
本程序适用于哈飞汽车集团(以下简称哈飞汽车)本部。
2 目的旨在规范工艺技术部在新车冲压工艺方案评审和模具结构评审(铸件模具)的要求,以及在评审过程中应注意的问题。
3 术语和定义无。
4 职责4.1 模具供应商(以下简称被评审方):4.1.1 负责提出评审申请,并提供工艺方案图、模具图等评审资料。
4.2 工艺技术部技术处(以下简称评审方):4.2.1 负责组织对自制件工艺方案图、模具图进行评审;4.2.2 负责对评审进行结论并输出评审纪要;4.2.3 参与其他单位组织的冲压件及模具资料的评审。
5 工作要求及程序5.1 被评审方按下列要求进行工艺方案及模具资料的准备。
5.1.1 工艺方案准备(1)方案评审时,被评审方提供冲压零件工艺方案图,工艺方案图要求为AutoCAD格式文件。
(2)方案评审时,被评审方提供冲压零件工艺方案3D数模,工艺方案3D数模要求为Catia V5R18或以下版本格式文件。
(3)针对成形类零件,成形工序必须进行CAE仿真分析,同时提供CAE分析设置文件,CAE 分析软件仅限Dynaform, Autoform或Pam-stamp。
5.1.2 模具结构图准备在模具结构图评审时,被评审方提供冲压零件模具结构图,模具结构图要求为AutoCAD 和Catia V5R18或以下版本格式文件。
5.2 评审方按附录A.1进行工艺方案评审。
5.3 评审方按附录A.2进行模具结构评审。
5.4 评审方输出评审纪要。
5.5 工作流程(2)冲压工艺方案及图纸资料审签流程说明见表1。
表1 冲压工艺方案及图纸资料审签流程说明6 记录7 附录附录A 参考标准附录A.1 工艺方案评审要求1 明确产品的特点。
1.1产品形状特点。
1.2 产品在车身上的位置,及其与周边零件的装配关系。
1.3 产品GDT是否对该产品有特殊要求。
2 以往车型类似产品参考。
冲模设计程序与步骤

3、冲模设计程序与步骤3.1冲模和冲压件的相关选择1)根据所提供的产品图样,分析冲压模具的形状、尺寸、精度、断面质量、装配关系等要求。
2)根据冲压件的生产批量,决定模具的结构形式、选用模具的材料。
3)分析图样上冲压件所用材料是否符合冲压工艺要求。
决定选择采用条料、板料、卷料还试边角废料。
4)根据工厂现有设备情况以及冲压件和冲压件批量对设备的要求选择合适的压力机。
5)根据工厂的制造水平及装备情况,为模具结构设计提供依据。
6)了解模具标准部件商品的供应状况。
3.2 确定合理的冲压工艺方案1)根据对制件所作的工艺分析,确定基本的工序性质,如切边、冲孔、弯曲等。
2)进行工艺计算,确定工序数目,如折弯次数等。
3)根据冲件生产批量和条件(材料、设备冲件精度)确定工序组合,如采用复合冲压工序或连续冲压工序。
4)根据各工序的变形特点、尺寸要求等确定工序排列顺序,如采用先冲孔后弯曲,还是先弯曲后冲孔。
3.3 进行工艺计算1)计算毛坯尺寸,合理排样并绘制排样图,计算出材料利用率。
2)计算冲压力,其中包括冲裁力、弯曲力、拉深力、卸料力、推件力、压边力等,以确定压力机。
3)选定压力机型号、规格。
4)计算压力中心,以免模具受偏心负荷而影响模具的使用寿命。
5)计算并确定模具主要零件(凸模、凹模、凸模固定板、垫板等)的外形尺寸以及弹性元件的自由高度。
6)确定凸凹模间隙,计算凸凹模工作部分的尺寸。
7)确定拉深模的压边圈、拉深次数、各种中间工序模具的尺寸分配,以及半成品尺寸计算等。
3.4 模具总体设计3.4.1进行模具结构设计,确定结构件形式和标准1)成形工作零件与标准确定:如凸模、凹模及凸凹的结构形式是整体、组合还是镶拼的。
图3.1 级进模模具结构2)选定定位元件:如采用定位板或挡料销或导正销等。
对于级进模,还要考虑是否用始用挡料销、导正销和定距凸模(侧刃)等。
紧固零件有:螺钉用于固定模具零件,而销钉则起定位作用。
卸料螺钉M8固定螺钉M8以及φ8销钉。
冲压模具流程
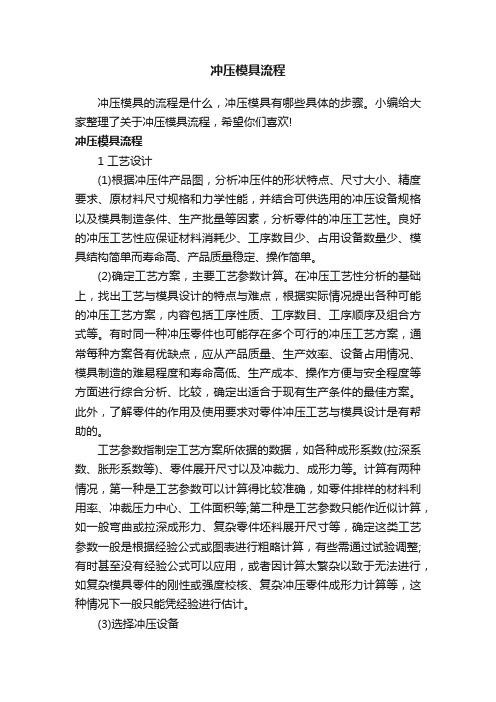
冲压模具流程冲压模具的流程是什么,冲压模具有哪些具体的步骤。
小编给大家整理了关于冲压模具流程,希望你们喜欢!冲压模具流程1 工艺设计(1)根据冲压件产品图,分析冲压件的形状特点、尺寸大小、精度要求、原材料尺寸规格和力学性能,并结合可供选用的冲压设备规格以及模具制造条件、生产批量等因素,分析零件的冲压工艺性。
良好的冲压工艺性应保证材料消耗少、工序数目少、占用设备数量少、模具结构简单而寿命高、产品质量稳定、操作简单。
(2)确定工艺方案,主要工艺参数计算。
在冲压工艺性分析的基础上,找出工艺与模具设计的特点与难点,根据实际情况提出各种可能的冲压工艺方案,内容包括工序性质、工序数目、工序顺序及组合方式等。
有时同一种冲压零件也可能存在多个可行的冲压工艺方案,通常每种方案各有优缺点,应从产品质量、生产效率、设备占用情况、模具制造的难易程度和寿命高低、生产成本、操作方便与安全程度等方面进行综合分析、比较,确定出适合于现有生产条件的最佳方案。
此外,了解零件的作用及使用要求对零件冲压工艺与模具设计是有帮助的。
工艺参数指制定工艺方案所依据的数据,如各种成形系数(拉深系数、胀形系数等)、零件展开尺寸以及冲裁力、成形力等。
计算有两种情况,第一种是工艺参数可以计算得比较准确,如零件排样的材料利用率、冲裁压力中心、工件面积等;第二种是工艺参数只能作近似计算,如一般弯曲或拉深成形力、复杂零件坯料展开尺寸等,确定这类工艺参数一般是根据经验公式或图表进行粗略计算,有些需通过试验调整;有时甚至没有经验公式可以应用,或者因计算太繁杂以致于无法进行,如复杂模具零件的刚性或强度校核、复杂冲压零件成形力计算等,这种情况下一般只能凭经验进行估计。
(3)选择冲压设备根据要完成的冲压工序性质和各种冲压设备的力能特点,考虑冲压加工所需的变形力、变形功及模具闭合高度和轮廓尺寸的大小等主要因素,结合工厂现有设备情况来合理选定设备类型和吨位。
常用冲压设备有曲柄压力机、液压机等,其中曲柄压力机应用最广。
冲压模具设计流程

参考资料1、邓展主编,《冲压工艺与冲模设计手册》,化学工业出版社,2013年4月2、魏春雷,吴俊超主编,《冲模设计与案例分析》,北京理工大学出版社,2010年12月表1表2 弹压与固定卸料搭边值表3 最小搭边值表4 拉深件修边余量表5 拉深系数表6 拉深次数图1所示冲裁件,材料为A3,厚度为2mm ,大批量生产。
试制定工件冲压艺规程、设计其模具、编制模具零件的加工工艺规程。
2.1冲压件基本情况 零件名称:止动件 生产批量:大批 材料:A3 t=2mm2.2冲压件工艺分析①材料:该冲裁件的材料A3钢是普通碳素钢,具有较好的可冲压性能。
②零件结构:该冲裁件结构简单,并在转角有四处R2圆角,比较适合冲裁。
③尺寸精度:零件图上所有未注公差的尺寸,属自由尺寸,可按工T14级确定工件尺寸的公差.孔边距12二的公差为-0.11,属11级精度。
查公差表可得各尺寸公差为: 零件外形: 65074.0-mm 24052.0-mm 30052.0-mm R30052.0- mm R2025.0-mm 零件内形: 1036.00+ mm孔中心距3731.031.0+-mm有好的冲压性能,良好的冲压性质以及精确地公差等级所有该件适合冲裁。
2.3方案及模具结构类型该零件包括落料、冲孔两个基本工序,可以采用以下三种工艺方案: ①先落料,再冲孔,采用单工序模生产; ②落料一冲孔复合冲压,采用复合模生产; ③中孔一落料连续冲压,采用级进模生产。
方案①模具结构简单,但需要两道工序、两套模具才能完成零件的加工,生产效率较低,难以满足零件大批量生产的需求.由于零件结构简单,为提高生产效率,主要应采用复合冲裁或级进冲裁方式。
方案②只需要一套模具,冲压件的形位精度和尺寸易于保证,且生产效率也高。
尽管模具结构较方案一复杂,但由于零件的几何形状简单对称,模具制造并不困难。
方案③也只需要一套模具,生产效率也很高,但零件的冲压精度较复合模的低。
毕业设计冲压模具设计

毕业设计冲压模具设计冲压模具设计是指根据零部件的形状和要求,通过模具设计软件对压制工艺和模具结构进行详细设计并完成加工制造的过程。
本文将以零部件的冲压模具设计为例,详细介绍冲压模具设计的步骤和关键技术。
一、冲压模具设计的步骤1.零件分析与加工工艺确定:首先对待设计的零件进行分析,了解其形状、材料及加工工艺要求。
通过对零件的尺寸测量、材料分析和工艺流程确定,确定适宜的冲压模具设计方案。
2.模具结构确定:根据零件形状和工艺要求,确定模具的基本结构形式,包括上、下模块的形状和结构、导向方式以及顶出装置的设计。
3.模具零件设计:根据模具的结构形式,对上、下模板、定位销、导柱、导套、顶出器等模具零件进行详细设计,并确定其尺寸、形位公差和表面粗糙度。
4.模具装配设计:根据模具零件的设计,进行模具的装配设计,确定模具各零件的加工工艺和装配工艺。
5.3D模型的建立:采用模具设计软件对模具的各个零件进行建模,并对其进行装配,实现模型的全面展示和动态演示。
6.模具结构的强度分析:采用有限元分析法对模具结构进行强度分析,确定模具零件的受力状态,从而提高模具的刚度和寿命。
7.模具工艺文件的编制:编制模具的工艺文件,包括工艺流程、工装设计和使用说明,为模具的制造和使用提供详细的技术支持。
二、冲压模具设计的关键技术1.零件厚度均衡设计:保证冲压零件的均衡受力,在模具的设计中尽量避免出现片厚不均的问题,从而避免在冲压过程中产生变形或裂纹等缺陷。
2.弹性顶出设计:在模具设计中合理设置顶针或顶出器,以保证冲压零件在顶出过程中不会卡死或破碎,从而提高冲压的质量和效率。
3.导向方式优化设计:合理选择导向方式,减小模具的摩擦阻力,从而提高模具的导向精度和工作寿命。
4.材料选择与热处理:合理选择模具材料,并根据工艺要求进行适当的热处理,以提高模具的硬度和耐磨性,延长模具的使用寿命。
5.模腔润滑与冷却设计:在模具设计中设置合理的润滑和冷却装置,以提高冲压的质量和效率,并减少模具的磨损和热变形。
冲压模具设计评审流程

钣金模具结构与钣金生产工艺评审制度09试用版一、钣金模具结构与钣金生产工艺评审流程图:二、钣金模具结构与钣金生产工艺评审程序:1、制图表:A <模具结构与生产工艺预案>、B<钣金模具制造立项清单>、C模具2d3d图2、审定程序:①、一般程序简单或常规产品:由模具设计组长审查产品2D 3D图,评估产品结构对钣金工艺及模具结构实现的影响,将意见反馈到技术部协商更改.选择性地对个别结构复杂模具举行组内结构评审会议召集人:模具设计组长;与会人员:模具设计负责人和技术骨干,特邀相关人员.②、特别程序复杂或全新产品:举行产品与模具联席评审会议召集人:设计组负责人;与会人员:技术部产品结构/工艺相关工程师、模具生产负责人及模具结构设计员,解决产品结构对钣金工艺及模具结构的影响,技术难点的解决以及改进方案和钣金工艺及模具结构的最终定案.③、模具图会审,模具设计完成后对钣金工艺及模具结构的复核和对模具图的技术性及标准化审核,设计组长.模具设计责任人.技术骨干及特邀相关人员④、岗位责任确立:联席会议的参与者负钣金工艺及模具结构负失当责任.设计员岗位对模具结构、工艺的正确性负具体工作人为出错的主要责任,负技术出错的部分责任.3、产品与模具联席评审会议具体操作程序:在开模具评审会前,由设计组负责人以书面形式通知各相关项目模具设计工程师、跟模工程师、项目产品工师程师、生产公司工艺科工程师、模具车间负责人.会议通知单上内容:模具评审会时间、地点、参会人员、评审内容、产品图路径.目的:钣金生产工艺流程及模具结构的定案.钣金模具结构与钣金生产工艺评审表模具结构与生产工艺预案4、模具结构及钣金生产工艺终审程序:终审程序分为设计内终审和跨部门会审两类.跨部门会审由设计组负责人提供钣金工艺图及模具结构图路径,然后相关项目模具设计工程师、跟模工程师、项目产品工程师共同研讨并审定,在模具结构评审表上会签通过,所有参会人员共同负模具设计结构审定责任.设计员岗位对模具结构、工艺的正确性负具体工作人为出错的主要责任,负技术出错的部分责任.。
外发冲压模具验收标准

外发冲压模具验收标准(ISO9001-2015)1.0 目的规范模具设计,制造,验收等流程,缩短模具交期,提升公司效益。
2.0 适用范围适用于本公司外发设计制作的所有模具。
3.0 总则3.1模具设计前需给出《模具设计、制造、交付进度表》,表中需详细列出模具图纸设计、模具制造(线割/热处理/精磨等)及模具组装/试模三大阶段时间安排,并由供应商组织技术评审会议;表中需详细列出模具装配、初次试模交样时间。
3.2供应商对图纸设计中的<<工序图>>及<<排样图>>完成后,设计方需要将上述资料递交XX相关负责人,XX相关责任人在接到上述相关资料后经过内部评审。
然后与供应商进行双方沟通评审,确认模具设计方案,供应商在未收到XX 项目负责人书面确认模具方案时不得进行模具加工制造。
且供应商不得随意更改模具设计方案及不按照图面要求加工,否则由此造成的一切损失由供应商全部承担。
原则上供应商需对《工序图》、<<排样图>>、设计进度及评审结果承担全部风险责任。
模具设计寿命要求保证为100万次。
整个设计过程中,XX模具技术公司只作为技术支持。
所有部件设计时必须考虑便于模修人员安装、拆卸。
应尽量避免为更换冲头,而出现过多拆卸的情况。
3.3图纸作为XX验收的重要依据,所有模具零部件需确保与图纸一致,否则按照不合格品处理。
模具交付后,XX将按照图纸对模具零部件进行实测,如发现设计与制造不符合,将不予以验收。
产品验收后,保留最终验收工件及全尺寸报告作为参考样品,后期模具更改完成后需保证产品质量与样品稳定一致。
3.4模具尺寸不小于报价时模具预算尺寸,如模具为工程模工序数必须与报价时所报的工序数一致。
4.0 实施细则4.1 第一阶段——模具设计4.1.1 设计图纸要求4.1.1.1 工艺流程图(1)工艺流程图中必须详细列出每道工位的内容,用不同颜色区分工作内容。
OP10 、OP20、OP30 等为工位序号,颜色与工位对应。
冲压模具设计的一般流程
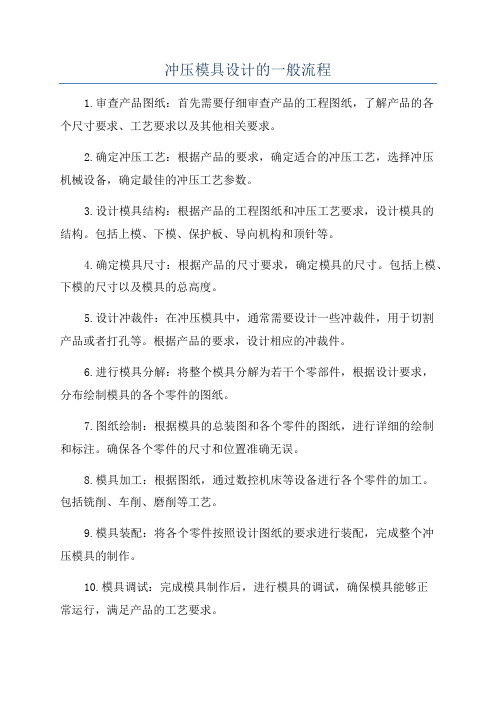
冲压模具设计的一般流程
1.审查产品图纸:首先需要仔细审查产品的工程图纸,了解产品的各
个尺寸要求、工艺要求以及其他相关要求。
2.确定冲压工艺:根据产品的要求,确定适合的冲压工艺,选择冲压
机械设备,确定最佳的冲压工艺参数。
3.设计模具结构:根据产品的工程图纸和冲压工艺要求,设计模具的
结构。
包括上模、下模、保护板、导向机构和顶针等。
4.确定模具尺寸:根据产品的尺寸要求,确定模具的尺寸。
包括上模、下模的尺寸以及模具的总高度。
5.设计冲裁件:在冲压模具中,通常需要设计一些冲裁件,用于切割
产品或者打孔等。
根据产品的要求,设计相应的冲裁件。
6.进行模具分解:将整个模具分解为若干个零部件,根据设计要求,
分布绘制模具的各个零件的图纸。
7.图纸绘制:根据模具的总装图和各个零件的图纸,进行详细的绘制
和标注。
确保各个零件的尺寸和位置准确无误。
8.模具加工:根据图纸,通过数控机床等设备进行各个零件的加工。
包括铣削、车削、磨削等工艺。
9.模具装配:将各个零件按照设计图纸的要求进行装配,完成整个冲
压模具的制作。
10.模具调试:完成模具制作后,进行模具的调试,确保模具能够正
常运行,满足产品的工艺要求。
11.产出产品:经过模具调试后,使用冲压机械设备进行批量生产,产出满足产品要求的冲压件。
12.模具维护和修理:冲压模具在使用过程中,需要进行定期的维护和修理,确保模具长时间稳定运行。
模具设计评审规范
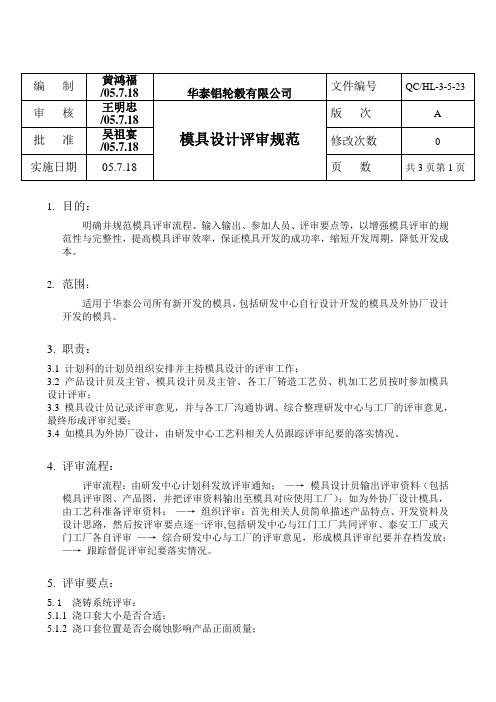
1.目的:明确并规范模具评审流程、输入输出、参加人员、评审要点等,以增强模具评审的规范性与完整性,提高模具评审效率,保证模具开发的成功率,缩短开发周期,降低开发成本。
2.范围:适用于华泰公司所有新开发的模具,包括研发中心自行设计开发的模具及外协厂设计开发的模具。
3.职责:3.1 计划科的计划员组织安排并主持模具设计的评审工作;3.2 产品设计员及主管、模具设计员及主管、各工厂铸造工艺员、机加工艺员按时参加模具设计评审;3.3 模具设计员记录评审意见,并与各工厂沟通协调、综合整理研发中心与工厂的评审意见,最终形成评审纪要;3.4 如模具为外协厂设计,由研发中心工艺科相关人员跟踪评审纪要的落实情况。
4.评审流程:评审流程:由研发中心计划科发放评审通知;—→模具设计员输出评审资料(包括模具评审图、产品图,并把评审资料输出至模具对应使用工厂);如为外协厂设计模具,由工艺科准备评审资料;—→组织评审:首先相关人员简单描述产品特点、开发资料及设计思路,然后按评审要点逐一评审,包括研发中心与江门工厂共同评审、泰安工厂或天门工厂各自评审—→综合研发中心与工厂的评审意见,形成模具评审纪要并存档发放;—→跟踪督促评审纪要落实情况。
5.评审要点:5.1浇铸系统评审:5.1.1 浇口套大小是否合适;5.1.2 浇口套位置是否会腐蚀影响产品正面质量;5.1.4 是否存在铸件排气不畅、充型困难的部位。
5.2 补缩评审:5.2.1 上、下轮辋补缩梯度是否合适,补缩梯度是设计在上下模、还是在侧模上;5.2.2 轮辐补缩通道大小是否合适;5.2.3上模掏料深度是否影响了轮辐的补缩通道;5.2.4 上模芯掏料深度是否会影响到补缩通道;5.2.5是否需要通过其他方式以增加热节部位的补缩通道。
5.3 冷却系统评审:5.3.1.下模水冷位置是否合适,是否需要两个下模水冷盘;5.3.2.是否需要下模内爪风,其深度、角度、位置是否合适;5.3.3下模外爪风深度、角度、位置及风爪个数是否合适;5.3.4 上模芯水冷位置是否合适;5.3.5 上模内爪风深度、位置及爪风个数是否合适;5.3.6 上模外爪风深度、位置及风爪个数是否合适;5.3.7 上模外环爪风深度、位置、角度及风爪个数是否合适;5.3.8 侧模是否需要设置风冷;5.3.9 分流锥水冷的深度是否合适;5.3.10 是否需要其他非常规的冷却方式。
冲压模具设计与制造_冲压工艺过程设计的步骤与内容
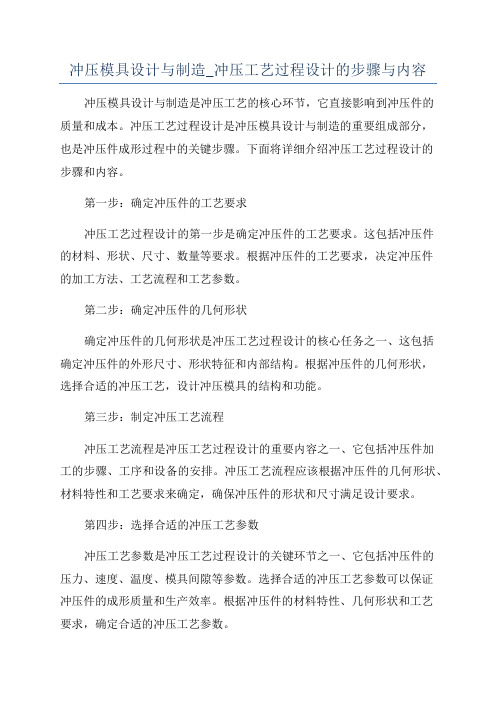
冲压模具设计与制造_冲压工艺过程设计的步骤与内容冲压模具设计与制造是冲压工艺的核心环节,它直接影响到冲压件的质量和成本。
冲压工艺过程设计是冲压模具设计与制造的重要组成部分,也是冲压件成形过程中的关键步骤。
下面将详细介绍冲压工艺过程设计的步骤和内容。
第一步:确定冲压件的工艺要求冲压工艺过程设计的第一步是确定冲压件的工艺要求。
这包括冲压件的材料、形状、尺寸、数量等要求。
根据冲压件的工艺要求,决定冲压件的加工方法、工艺流程和工艺参数。
第二步:确定冲压件的几何形状确定冲压件的几何形状是冲压工艺过程设计的核心任务之一、这包括确定冲压件的外形尺寸、形状特征和内部结构。
根据冲压件的几何形状,选择合适的冲压工艺,设计冲压模具的结构和功能。
第三步:制定冲压工艺流程冲压工艺流程是冲压工艺过程设计的重要内容之一、它包括冲压件加工的步骤、工序和设备的安排。
冲压工艺流程应该根据冲压件的几何形状、材料特性和工艺要求来确定,确保冲压件的形状和尺寸满足设计要求。
第四步:选择合适的冲压工艺参数冲压工艺参数是冲压工艺过程设计的关键环节之一、它包括冲压件的压力、速度、温度、模具间隙等参数。
选择合适的冲压工艺参数可以保证冲压件的成形质量和生产效率。
根据冲压件的材料特性、几何形状和工艺要求,确定合适的冲压工艺参数。
第五步:设计冲压模具设计冲压模具是冲压工艺过程设计的重要内容之一、它包括冲压模具的结构、尺寸、材料和加工工艺等方面。
根据冲压件的几何形状、工艺要求和生产效率要求,设计合理的冲压模具。
冲压模具应具备高精度、高强度和高耐磨性的特点,确保冲压件的成形质量和生产效率。
第六步:制造冲压模具制造冲压模具是冲压工艺过程设计的最后一步。
它包括冲压模具的加工工艺、装配和调试等环节。
冲压模具的制造应根据设计要求和工艺要求,选择合适的材料和加工工艺,确保冲压模具的质量和寿命。
制造冲压模具还需要进行装配和调试,确保冲压模具的合理性和可靠性。
总结:冲压工艺过程设计是冲压模具设计与制造的重要环节,它直接关系到冲压件的质量和生产效率。
冲压模具设计审查技巧

产品开发可行性评估-冲压件
昆山长盈精密技术有限公司 管理制度化 制造标准化 品质国际化 服务优质化 *文件仅供公司内部使用*
冲模开发之前需要根据产品的材质,厚度,折弯工艺 ,产品尺寸公差,冲压和收料方向,模具零 件加工 可行性后续电镀和模具的量产性等方面进行评估,对 于有问题的地方应及时提出,要求产品结构做改进, 具体评估项目如下:
特殊折弯有无材料压延方向要求?
是否需要多料号共用模具? 机器的吨位和产能是否足够? 是否需加装特殊的模具保护装置?
多料号 共模
昆山长盈精密技术有限公司 管理制度化 制造标准化 品质国际化 服务优质化 *文件仅供公司内部使用*
检验规范是否周全?检验方法是否标准化?
每冲程的冲成数?SPM?
周边设备是否足够?
预断 凸包
切边
下料
下料
下料
倒角
成形
成形
成形
调整 成形
下料
倒角
成形
调整 成形 调整 扇形
排样图
三:定位和浮升等:
是否有扇形,偏摆,翘曲等调整机构. 模仁,浮料块等是否被导板或压板压住.
导料板
扇形调整
昆山长盈精密技术有限公司 管理制度化 制造标准化 品质国际化 服务优质化
浮升块
*文件仅供公司内部使用*
切边冲子
导料板
冲子形状过于 简单,易跳屑 ,需增加卡料
昆山长盈精密技术有限公司 管理制度化 制造标准化 品质国际化 服务优质化 *文件仅供公司内部使用*
是否需要特殊周边装置(料厚0.15以下).
是否需要特殊的送料装置.
模板及零件的加工方式是否可行.
修改前R0.05线割无法加工
修改后R0.08线割可以加工
冲压模具设计规范标准

一、目的:本标准是根据公司产品结构特点及模具设计、制作实际需要,统一模具设计标准,提高冲压模具设计质量,为模具设计提供指导。
二、适用范围:公司所有冲压模具;三、具体规定:第一节模具制作流程标准工艺/项目/生产提模具开发电子流相关主管审核批准模具设计出图相关主管审核批准模具制作试模品管检验、开合格证生产验收!第二节图纸审核标准拿到设计任务时,首先应对产品图纸作一个全面的审核、确认,主要从以下几方面入手:1.图框內容确认产品名称、版次、视图投影角法、视图比例、材质、料厚(英制需转换为公制)。
2.图面注解內容确认依图面注解逐项确认3.视图正确性确认三视图画法、尺寸标注、各主要视图和各局部视图是否一致,特殊公差要求确认。
4.特殊要求確認a. 有无表面处理要求b. 不锈钢、铍銅、铝等材质产品需注意片纹方向要求。
c. 是否有压毛边,方向,范围?d. 产品的重点管控尺寸,公差等?e. 压铆钉的规格、工序等?f. 若有抽牙,须了解抽牙功用,重点尺寸(内径、外径、高度)g. 产品如果有工艺缺口处,连续模连料,接刀须客户确认回复。
h. 产品有没有标注尺寸公差的地方,能否做到?i. 一些孔和产品的外形可否圆整?j. 产品有没有外观要求,如平面度,垂直度等?k. 现有的工艺槽是否太窄?l. 产品若有半剪,则半剪要保证的尺寸是位置还是高度等?m. 产品若有凸点,则其功用,重要尺寸是什么?n. 产品的批量大小?o. 产品压沙拉的尺寸确认?p. 产品折弯展开可否依内R为零展开?q. 产品有包角若因高度原因可能会造成拉裂或起皱可否做工艺处理?经仔细审核确认后即可对产品进行展开,排工序等后序作业。
第三节展开图标准1.展开图中必須包含产品图中的所有內孔,內部成型和外部成型的展开的图元1)展开图的毛刺面必须向下.2)展开图中所有图元须串取成复线.3)冲裁尖角(除特殊情況外)均要倒圓角R=0.3或R=0.5(具体可根据产品料厚定)4)成形工位折线位置必须画出及注意虚实线。
冲压模具设计全套步骤和流程总算是弄明白了

冲压模具设计全套步骤和流程总算是弄明白了一起探讨,一起学习,一起进步。
大家的每一次点赞,每一次评论,每一次转发。
都是我创作的动力,期待你的加入一、取得必要的资料根据相关资料分析共建的冲压工艺性,对工件进行工艺审核及标准化审核。
1)取得注明具体技术要求的产品零件图样。
了解工件的形状、尺寸与精度要求。
关键孔的尺寸(大小和位置),关键表面,分析并确定工件的基准面。
其实,冲压件的各项工艺性要求并不是绝对的。
尤其在当前冲压技术迅速发展的情况下,根据生产实际的需要和可能,综合应用各种冲压技术,合理选择冲压方法,正确进行冲压工艺的制定和模具结构的选择,使之既满足产品的技术要求,又符合冲压工艺的条件。
2)收集工件加工的工艺过程卡片。
由此可研究其前后工序间的相互关系和在各工序间必须相互保证的加工工艺要求及装配关系等。
3)了解工件的生产批量。
零件的生产对冲压加工的经济性起着决定性的作用,为此,必须根据零件的生产批量和零件的质量要求,来决定模具的型式、结构、材料等有关事项,并由此分析模具加工工艺的经济性及公建生产的合理性,描绘冲压工步的轮廓。
4)确定工件原材料的规格及毛料情况(如板料、条料、卷料、废料等),了解材料的性质和厚度,根据零件的工艺性确定是否采用少无废料拍样吗,并初步确定材料的规格和精度等级。
在满足使用性能和冲压性能要求的前提下,应尽量采用廉价的材料。
5)分析设计和工艺上对材料纤维方向的要求、毛刺的方向。
6)分析工(模)具车间制造模具的技术能力和设备条件以及可采用的模具标准件的情况。
7)熟悉冲压车间的设备资料或情况。
8)研究消化上述资料,初步构思模具的结构方案。
必要时可对既定的产品设计和工艺过程提出修改意见,使产品设计、工艺过程和模具设计与制造三者之间能更好的结合,以取得更加完善的效果。
二、确定工艺方案及模具结构型式工艺方案的确定是冲压件工艺性分析之后应进行的一个最重要的环节。
它包括:1)根据工件的形状特征、尺寸精度及表面质量的要求,进行工艺分析,判断出它的主要属性,确定基本工序的性质。
模具检验流程规划方案

模具检验流程规划方案模具检验是制造过程中的一项关键环节,用于检查模具的质量是否符合要求。
一个合理的模具检验流程能够提高检验效率,节省时间成本,确保模具的质量稳定可靠。
以下是一个模具检验流程规划方案的示例,供参考:一、准备工作1. 制定检验计划:根据模具的特点和要求,制定合理的检验计划,包括检验项目、检验标准等,确保检验工作的有序进行。
2. 准备检验设备和工具:根据检验计划,准备好适当的检验设备和工具,如显微镜、测量仪器、千分尺等,以便进行具体的检验工作。
3. 准备检验记录表和标签:为每个模具准备好相应的检验记录表和标签,方便记录检验结果和追踪模具的质量情况。
二、检验流程1. 外观检验:首先进行外观检验,观察模具的表面是否有划痕、凹陷、气泡等缺陷,确保模具的外观符合要求。
2. 尺寸检验:根据模具的设计图纸,使用测量仪器对模具的各个尺寸进行检测,确保模具的尺寸精度和准确性。
3. 材料检验:对模具的材料进行化学成分、力学性能等方面的检测,检验模具的材质是否符合要求。
4. 功能检验:将模具安装在相应的设备上,进行功能性测试,检验模具是否能够正常运作,如剪切模具是否能够正常剪切、冲压模具是否能够正常冲压等。
5. 特殊检验:根据具体的模具类型和要求,进行相应的特殊检验,如电气性能、耐磨性能、防腐蚀性能等。
三、记录和分析1. 记录检验结果:在检验记录表上记录每个模具的检验结果,包括尺寸、材料、功能等方面的情况,确保检验结果准确完整。
2. 分析不良现象:对于出现的不良现象,进行详细分析,并记录下原因和影响,以便后续改进和优化。
3. 整理归档:将检验记录和分析结果进行整理和归档,方便日后的追溯和分析。
四、改进和优化1. 定期评估:对模具的检验流程进行定期评估,发现存在的问题和不足,并进行相应的改进和优化。
2. 培训和提升:对模具检验人员进行培训和提升,提高其专业水平和技术能力,确保模具检验工作的质量和效率。
以上是一个模具检验流程规划方案的简要说明,具体的流程规划需要根据实际情况进行具体化设计和调整。
冲压模具设计评审流程
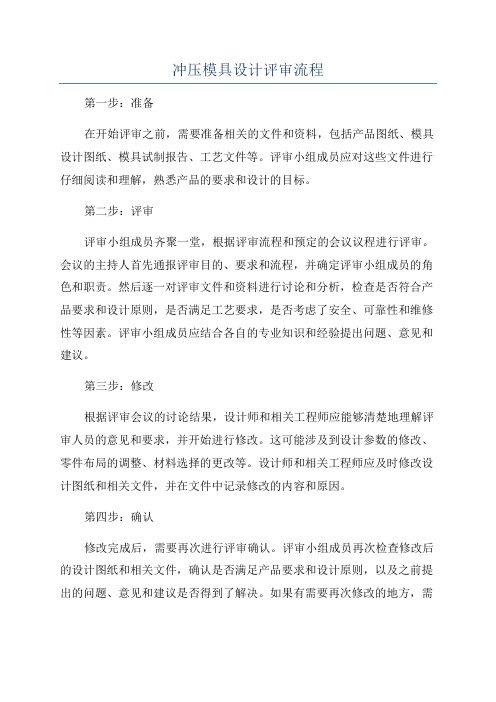
冲压模具设计评审流程
第一步:准备
在开始评审之前,需要准备相关的文件和资料,包括产品图纸、模具设计图纸、模具试制报告、工艺文件等。
评审小组成员应对这些文件进行仔细阅读和理解,熟悉产品的要求和设计的目标。
第二步:评审
评审小组成员齐聚一堂,根据评审流程和预定的会议议程进行评审。
会议的主持人首先通报评审目的、要求和流程,并确定评审小组成员的角色和职责。
然后逐一对评审文件和资料进行讨论和分析,检查是否符合产品要求和设计原则,是否满足工艺要求,是否考虑了安全、可靠性和维修性等因素。
评审小组成员应结合各自的专业知识和经验提出问题、意见和建议。
第三步:修改
根据评审会议的讨论结果,设计师和相关工程师应能够清楚地理解评审人员的意见和要求,并开始进行修改。
这可能涉及到设计参数的修改、零件布局的调整、材料选择的更改等。
设计师和相关工程师应及时修改设计图纸和相关文件,并在文件中记录修改的内容和原因。
第四步:确认
修改完成后,需要再次进行评审确认。
评审小组成员再次检查修改后的设计图纸和相关文件,确认是否满足产品要求和设计原则,以及之前提出的问题、意见和建议是否得到了解决。
如果有需要再次修改的地方,需
要记录下来,并返工修改。
只有在评审小组成员达成一致意见并认可设计方案后,才能够进行下一步的模具制造和模具试制。
总结起来,冲压模具设计评审流程主要包括准备、评审、修改和确认四个步骤。
通过这一流程,可以确保冲压模具设计符合要求,并能够生产出满足技术和质量要求的产品。
冲压模具设计审核要点

冲压模具设计审核要点《冲压模具设计审核要点》冲压模具设计是冲压成形过程中至关重要的环节。
为了确保模具设计的准确性和可靠性,设计审核变得尤为重要。
下面将介绍一些冲压模具设计审核的要点。
首先,模具设计审核要关注冲压件的几何形状和尺寸。
模具设计者需要确保冲压件的几何形状和尺寸与产品要求完全匹配。
审核人员应仔细核对设计文件中的尺寸标注是否准确,并验证冲压件的形状是否满足产品的功能和装配要求。
其次,模具设计审核要关注冲压件的材料选择和厚度。
模具设计者需要选择适合的材料和合适的厚度,以确保冲压件在使用过程中具有足够的强度和刚性。
审核人员应确认设计文件中的材料和厚度选择是否符合产品的要求,并评估其对产品性能的影响。
同时,模具设计审核还要关注模具结构的可靠性和稳定性。
模具设计者需要考虑模具的装配和拆卸工艺,以及尽量减少零部件的数量和复杂度。
审核人员应验证模具设计是否合理,是否能够经受冲击和负荷,并评估模具寿命和可维护性。
另外,模具设计审核还要关注模具的制造工艺和成本。
模具设计者需要选择适当的加工工艺和制造方法,以最大限度地减少材料浪费和加工时间。
审核人员应评估模具的制造难度和成本,并提出改进意见,以提高制造效率和降低成本。
最后,模具设计审核还要关注模具的安全性和环保性。
设计者需要采取必要的安全措施,以确保操作人员的人身安全。
审核人员应验证设计中是否考虑到了防护措施,并评估模具的环保性能,以降低对环境的影响。
综上所述,《冲压模具设计审核要点》主要包括关注冲压件的几何形状和尺寸、材料选择和厚度、模具结构的可靠性和稳定性、制造工艺和成本,以及安全性和环保性。
通过对这些要点的审核,可以确保冲压模具设计的质量和可靠性,提高冲压产品的质量和效率。
冲压模具设计步骤

冲压模具设计步骤第一步呢,得先把产品的要求搞清楚。
就像你要给一个人做衣服,得知道人家想要啥样的衣服风格、尺寸啥的。
对于冲压模具,你得知道要冲压出来的零件长啥样,尺寸精度要求多高,是啥材质的,这些信息就像设计的指南针 。
第二步,开始构思模具的大概结构啦。
这就好比搭积木,你得想好用哪些“积木块”,也就是模具的各个部件。
是用单工序模呢,还是复合模或者级进模。
这得根据产品的形状、产量这些因素来决定哦。
要是产品形状简单,产量又不大,单工序模可能就够啦;要是产量大,形状复杂,复合模或者级进模可能更合适呢。
第三步,计算各种参数。
这可不能马虎呀,就像厨师做菜得掌握好调料的量一样。
像冲压力得算准咯,这关系到模具的强度能不能承受。
还有模具的闭合高度,也得精心计算,不然和冲压设备不匹配可就麻烦啦。
第四步,画草图。
这就像是给模具画个简单的画像,把各个部件的位置关系大概表示出来。
草图不用画得特别精美,但得能让人看明白各个部分是咋回事。
第五步,详细设计。
这时候就像给画像上颜色、加细节啦。
把每个部件的尺寸、形状都精确地确定下来,还要考虑到加工工艺性哦。
比如说,有些形状在理论上可以设计出来,但是加工起来特别困难,那可不行,得调整设计,让它既满足功能要求,又好加工。
第六步,选择合适的模具材料。
这就像给战士选武器一样重要。
不同的冲压工艺、不同的产品要求,得选不同的材料。
要是冲压硬的材料,那模具材料就得更耐磨、更抗压才行呢。
最后呀,就是审核校对啦。
自己检查完了,最好再找个有经验的人帮忙看看,就像考试做完题要检查一样。
看看有没有啥不合理的地方,有没有计算错误啥的。
冲压工艺分析流程及要点
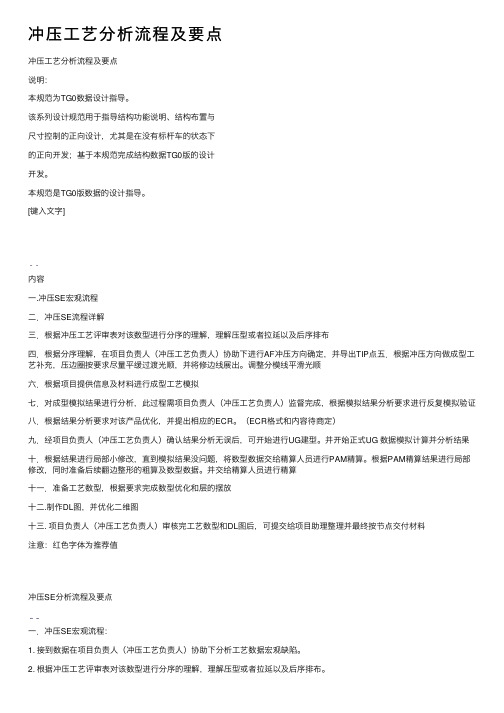
冲压⼯艺分析流程及要点冲压⼯艺分析流程及要点说明:本规范为TG0数据设计指导。
该系列设计规范⽤于指导结构功能说明、结构布置与尺⼨控制的正向设计,尤其是在没有标杆车的状态下的正向开发;基于本规范完成结构数据TG0版的设计开发。
本规范是TG0版数据的设计指导。
[键⼊⽂字]内容⼀.冲压SE宏观流程⼆.冲压SE流程详解三.根据冲压⼯艺评审表对该数型进⾏分序的理解,理解压型或者拉延以及后序排布四.根据分序理解,在项⽬负责⼈(冲压⼯艺负责⼈)协助下进⾏AF冲压⽅向确定,并导出TIP点五.根据冲压⽅向做成型⼯艺补充,压边圈按要求尽量平缓过渡光顺,并将修边线展出。
调整分模线平滑光顺六.根据项⽬提供信息及材料进⾏成型⼯艺模拟七.对成型模拟结果进⾏分析,此过程需项⽬负责⼈(冲压⼯艺负责⼈)监督完成,根据模拟结果分析要求进⾏反复模拟验证⼋.根据结果分析要求对该产品优化,并提出相应的ECR。
(ECR格式和内容待商定)九.经项⽬负责⼈(冲压⼯艺负责⼈)确认结果分析⽆误后,可开始进⾏UG建型。
并开始正式UG 数据模拟计算并分析结果⼗.根据结果进⾏局部⼩修改,直到模拟结果没问题,将数型数据交给精算⼈员进⾏PAM精算。
根据PAM精算结果进⾏局部修改,同时准备后续翻边整形的粗算及数型数据。
并交给精算⼈员进⾏精算⼗⼀.准备⼯艺数型,根据要求完成数型优化和层的摆放⼗⼆.制作DL图,并优化⼆维图⼗三. 项⽬负责⼈(冲压⼯艺负责⼈)审核完⼯艺数型和DL图后,可提交给项⽬助理整理并最终按节点交付材料注意:红⾊字体为推荐值冲压SE分析流程及要点⼀.冲压SE宏观流程:1. 接到数据在项⽬负责⼈(冲压⼯艺负责⼈)协助下分析⼯艺数据宏观缺陷。
2. 根据冲压⼯艺评审表对该数型进⾏分序的理解,理解压型或者拉延以及后序排布。
3. 根据分序理解,在项⽬负责⼈(冲压⼯艺负责⼈)协助下进⾏AF冲压⽅向确定,并导出TIP点,此过程根据分析结果需反复操作。
4. 根据冲压⽅向做成型⼯艺补充,压边圈按要求尽量平缓过渡光顺,并将修边线展出。
冲压类模具开发评审及认可作业指导书
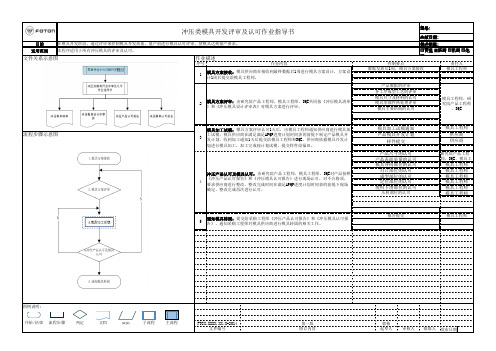
目的
在模具开发阶段,通过评审来控制模具开发质量,量产前进行模具认可评审,使模具达到量产要求。
适用范围 本程序适用于所有冲压模具的评审及认可。
文件关系示意图
作业描述
序号
作业内容
模具方案接收:模具供应商在接收到最终数据后1周进行模具方案设计,方案设 1 计1周后提交给模具工程师。
模具方案评审:由研究院产品工程师、模具工程师、SQE共同按《冲压模具清单 2
》和《冲压模具设计评审表》对模具方案进行评审。
流程步骤示意图
模具加工试模:模具方案评审认可1天后,由模具工程师通知供应商进行模具加 3 工试模,模具供应商在满足满足APQP进度计划时间表的前提下制定产品模具开
发计划,收到加工通知1天后提交给模具工程师和SQE,供应商依据模具开发计 划进行模具加工,加工完成按计划试模,提交样件给福田。
冲压产品认可及模具认可:由研究院产品工程师、模具工程师、SQE对产品按照 《冲压产品认可报告》和《冲压模具认可报告》进行现场认可,对不合格项, 4 要求供应商进行整改,整改完成时间在满足APQP进度计划时间表的前提下现场 确定。整改完成再次进行认可。
编号:
生效日期:
保存期限: □普通 ■秘密 □机密 □绝 密
文档
数据
子流程 主流程
FTCX.XXXX.XX.X-2014 文件编号
第一版 修订内容
郭栋 起草人
审核人 批准人 发布日期
控制要点 数据发放后1周,模具方案接收
责任人 模具工程师
产品数据的评审 各工序成型工艺的评审 模具尺寸及材料的认可 模具零部件热处理评审
模具主要结构的认可
模具工程师、研 究院产品工程师
- 1、下载文档前请自行甄别文档内容的完整性,平台不提供额外的编辑、内容补充、找答案等附加服务。
- 2、"仅部分预览"的文档,不可在线预览部分如存在完整性等问题,可反馈申请退款(可完整预览的文档不适用该条件!)。
- 3、如文档侵犯您的权益,请联系客服反馈,我们会尽快为您处理(人工客服工作时间:9:00-18:30)。
钣金模具结构与钣金生产工艺评审制度
(09试用版)
一、钣金模具结构与钣金生产工艺评审流程图:
二、钣金模具结构与钣金生产工艺评审程序:
1、制图表:A <模具结构与生产工艺预案>、B<钣金模具制造立项清单>、C模具2d3d图
2、审定程序:①、一般程序(简单或常规产品):由模具设计组长审查产品2D 3D图,评估产品结构对钣金工艺及模具结构实现的影响,将意见反馈到技术部协商更改。
选择性地对个别结构复杂模具举行组内结构评审会议(召集人:模具设计组长;与会人员:模具设计负责人和技术骨干,特邀相关人员)。
②、特别程序(复杂或全新产品):举行产品与模具联席评审会议(召集人:设计组负责人;与会人员:技术部产品结构/工艺相关工程师、模具生产负责人及模具结构设计员),解决产品结构对钣金工艺及模具结构的影响,技术难点的解决以及改进方案和钣金工艺及模具结构的最终定案。
③、模具图会审,模具设计完成后对钣金工艺及模具结构的复核和对模具图的技术性及标准化审核,(设计组长.模具设计责任人.技术骨干及特邀相关人员)
④、岗位责任确立:联席会议的参与者负钣金工艺及模具结构负失当责任。
设计员岗位对模具结构、工艺的正确性负具体工作人为出错的主要责任,负技术出错的部分责任。
3、产品与模具联席评审会议具体操作程序:
在开模具评审会前,由设计组负责人以书面形式通知各相关项目模具设计工程师、跟模工程师、项目产品工师程师、生产公司工艺科工程师、模具车间负责人。
会议通知单上内容:模具评审会时间、地点、参会人员、评审内容、产品图路径。
目的:钣金生产工艺流程及模具结构的定案。
钣金模具结构与钣金生产工艺评审表(模具结构与生产工艺预案)
4、模具结构及钣金生产工艺终审程序:
终审程序分为设计内终审和跨部门会审两类。
跨部门会审由设计组负责人提供钣金工艺图及模具结构图路径,然后相关项目模具设计工程师、跟模工程师、项目产品工程师共同研讨并审定,在模具结构评审表上会签通过,所有参会人员共同负模具设计结构审定责任。
设计员岗位对模具结构、工艺的正确性负具体工作人为出错的主要责任,负技术出错的部分责任。