重质润滑油基础油的原料制备及加工工艺的研究
润滑油基础油生产工艺

润滑油基础油生产工艺
润滑油基础油是润滑油的主要成分,它是从原油中提炼出来的一种石化产品。
润滑油基础油的生产工艺包括原油精炼、脱蜡、加氢裂化、溶剂抽提等步骤。
首先是原油精炼,原油经过蒸馏塔的分馏,得到不同馏分的原油。
其中较重的馏分经过真空蒸馏,得到具有一定粘度的润滑油基础油。
接下来是脱蜡的过程,脱蜡是为了去除原油中的蜡质,提高润滑油的流动性。
通过将原油加热至一定温度,使蜡在溶剂的作用下融化并与溶剂分离,最后通过过滤去除溶剂和蜡质。
加氢裂化是润滑油基础油生产中的一个重要步骤,它通过在高温高压下对重质馏分进行加氢处理,使其发生裂化反应。
通过这个反应,可以将较重的原油转化为较轻的润滑油基础油,同时减少芳烃和硫等杂质的含量,提高产品质量。
最后是溶剂抽提,溶剂抽提是为了进一步提纯润滑油基础油。
将加氢裂化得到的产品与溶剂混合,在一定的温度和压力下进行萃取,将一些较轻的杂质和芳烃物质去除,得到较纯净的润滑油基础油。
以上就是润滑油基础油的生产工艺,通过这些步骤,可以生产出优质的润滑油基础油。
润滑油基础油在生产出来后,还需要根据不同的使用需要进行配方,并加入适量的添加剂,制成适用于不同机械设备的润滑油产品。
基础油生产工艺
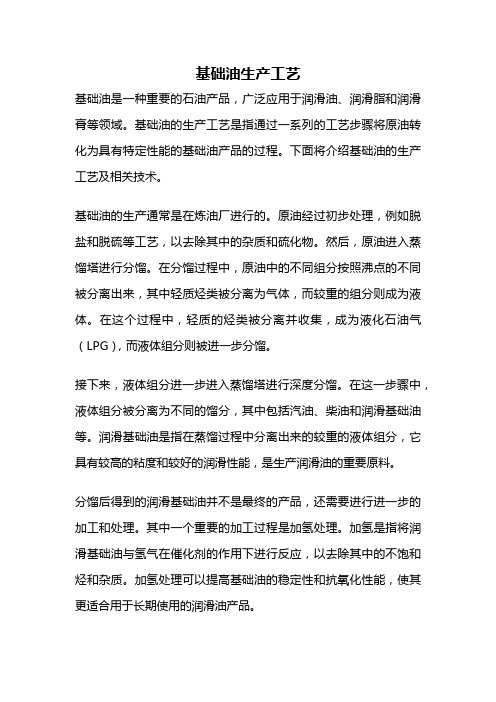
基础油生产工艺基础油是一种重要的石油产品,广泛应用于润滑油、润滑脂和润滑膏等领域。
基础油的生产工艺是指通过一系列的工艺步骤将原油转化为具有特定性能的基础油产品的过程。
下面将介绍基础油的生产工艺及相关技术。
基础油的生产通常是在炼油厂进行的。
原油经过初步处理,例如脱盐和脱硫等工艺,以去除其中的杂质和硫化物。
然后,原油进入蒸馏塔进行分馏。
在分馏过程中,原油中的不同组分按照沸点的不同被分离出来,其中轻质烃类被分离为气体,而较重的组分则成为液体。
在这个过程中,轻质的烃类被分离并收集,成为液化石油气(LPG),而液体组分则被进一步分馏。
接下来,液体组分进一步进入蒸馏塔进行深度分馏。
在这一步骤中,液体组分被分离为不同的馏分,其中包括汽油、柴油和润滑基础油等。
润滑基础油是指在蒸馏过程中分离出来的较重的液体组分,它具有较高的粘度和较好的润滑性能,是生产润滑油的重要原料。
分馏后得到的润滑基础油并不是最终的产品,还需要进行进一步的加工和处理。
其中一个重要的加工过程是加氢处理。
加氢是指将润滑基础油与氢气在催化剂的作用下进行反应,以去除其中的不饱和烃和杂质。
加氢处理可以提高基础油的稳定性和抗氧化性能,使其更适合用于长期使用的润滑油产品。
除了加氢处理,基础油的生产过程中还包括脱蜡和脱色等工艺。
脱蜡是指将基础油中的蜡质成分去除,以提高其低温流动性。
脱蜡通常采用溶剂脱蜡或催化脱蜡的方法。
脱色是指通过吸附剂或其他化学物质将基础油中的色素和杂质去除,以提高其外观和纯度。
在基础油的生产过程中,还可以通过添加剂的方式改善其性能。
添加剂可以提高基础油的抗磨损、抗氧化和抗腐蚀等性能,使其更适合不同类型的润滑应用。
常见的添加剂包括抗氧化剂、抗磨剂、摩擦改进剂和粘度指数改进剂等。
基础油的生产工艺包括原油初步处理、蒸馏分馏、加氢处理、脱蜡、脱色和添加剂等工艺步骤。
通过这些工艺步骤,原油可以被转化为具有特定性能的基础油产品,为润滑油行业提供了重要的原料。
高效润滑油基础油制备的技术研究

高效润滑油基础油制备的技术研究高效润滑油在现代工业生产中起着重要作用。
其基础油是润滑油的重要组成部分,其品质对润滑油的性能有着决定性影响。
因此,越来越多的研究人员开始关注高效润滑油基础油的制备技术。
近年来,随着石油资源的逐渐枯竭和环保意识的不断提高,人们对可再生能源和环保新材料的需求日益增加。
于是,关注生物能源的研究也逐渐兴起。
生物基润滑油因其环保性和优异性能而备受关注。
其中,生物醇基润滑油作为一种新型润滑油已成为了人们研究的热点。
而生物醇基润滑油的一大关键技术就是基础油的制备。
当前的生物醇基润滑油基础油制备技术可以分为化学合成和生物合成两种。
其中,生物合成是一种环保的制备方法,其产物具有较高的品质和低的环境风险,已成为了发展趋势。
目前,生物合成的高效润滑油基础油制备技术主要有三种:微生物法、植物油法和化学催化法。
下面将具体介绍各个方法的特点。
微生物法是通过对微生物菌群的优化培养,使其产生生物醇基物质,并利用酵母菌对其进行代谢分解,得到高效润滑油基础油。
这种方法具有工艺简单,反应条件温和,无毒无污染的优点。
但是其缺点是产品收率低,且对微生物菌群的选型和培养条件要求较高。
植物油法是将植物油经过酯化反应得到酯化油脂,然后经过加氢裂解反应得到高品质基础油。
这种方法具有原材料来源广泛,生产成本低,且产品品质稳定的优点。
但是,由于酯化反应中产生大量的副产物,对环境造成负面影响。
化学催化法是利用酸催化剂对生物醇和植物油进行催化反应,获得高效润滑油基础油。
这种方法具有反应条件温和,适用于各种材料的优点。
但由于酸催化剂本身的毒性,反应所产生的有机酸和副产物对环境造成较大的影响。
综上所述,生物醇基润滑油基础油的制备技术是一个不断发展的领域,目前已经有了多种方法和方向。
未来的发展趋势是生物合成技术的进一步研究和应用,同时还要加强对基础油品质的监测和评估工作,不断提高生物醇基润滑油的质量和应用水平。
润滑油基础油生产工艺研究
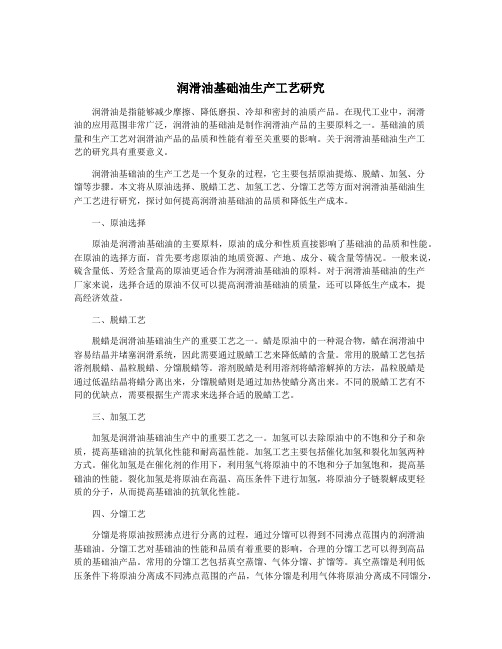
润滑油基础油生产工艺研究润滑油是指能够减少摩擦、降低磨损、冷却和密封的油质产品。
在现代工业中,润滑油的应用范围非常广泛,润滑油的基础油是制作润滑油产品的主要原料之一。
基础油的质量和生产工艺对润滑油产品的品质和性能有着至关重要的影响。
关于润滑油基础油生产工艺的研究具有重要意义。
润滑油基础油的生产工艺是一个复杂的过程,它主要包括原油提炼、脱蜡、加氢、分馏等步骤。
本文将从原油选择、脱蜡工艺、加氢工艺、分馏工艺等方面对润滑油基础油生产工艺进行研究,探讨如何提高润滑油基础油的品质和降低生产成本。
一、原油选择原油是润滑油基础油的主要原料,原油的成分和性质直接影响了基础油的品质和性能。
在原油的选择方面,首先要考虑原油的地质资源、产地、成分、硫含量等情况。
一般来说,硫含量低、芳烃含量高的原油更适合作为润滑油基础油的原料。
对于润滑油基础油的生产厂家来说,选择合适的原油不仅可以提高润滑油基础油的质量,还可以降低生产成本,提高经济效益。
二、脱蜡工艺脱蜡是润滑油基础油生产的重要工艺之一。
蜡是原油中的一种混合物,蜡在润滑油中容易结晶并堵塞润滑系统,因此需要通过脱蜡工艺来降低蜡的含量。
常用的脱蜡工艺包括溶剂脱蜡、晶粒脱蜡、分馏脱蜡等。
溶剂脱蜡是利用溶剂将蜡溶解掉的方法,晶粒脱蜡是通过低温结晶将蜡分离出来,分馏脱蜡则是通过加热使蜡分离出来。
不同的脱蜡工艺有不同的优缺点,需要根据生产需求来选择合适的脱蜡工艺。
三、加氢工艺加氢是润滑油基础油生产中的重要工艺之一。
加氢可以去除原油中的不饱和分子和杂质,提高基础油的抗氧化性能和耐高温性能。
加氢工艺主要包括催化加氢和裂化加氢两种方式。
催化加氢是在催化剂的作用下,利用氢气将原油中的不饱和分子加氢饱和,提高基础油的性能。
裂化加氢是将原油在高温、高压条件下进行加氢,将原油分子链裂解成更轻质的分子,从而提高基础油的抗氧化性能。
四、分馏工艺分馏是将原油按照沸点进行分离的过程,通过分馏可以得到不同沸点范围内的润滑油基础油。
HVI500基础油生产工艺研究

322根据市场调研结果,某公司为了开发HVI500基础油,增产新品种以满足客户的调油需求, 进行HVI500基础油生产工作。
试生产按‘减压蒸馏→一糠醛→酮苯轻油→白土精制→组份油罐’的流程顺序进行。
由技术、调度等单位共同制定了详细的试验方案和计划:确定各工序试生产的时间安排以及工艺操作条件和馏出口质量控制计划,安排中间罐区专罐专用,保证所有贮罐在贮存HVI500前均经过置换处理,以最大限度减少不同油品之间的混线。
在试验过程中,各生产装置的大力配合,积极按方案要求安排调整工艺操作条件,并根据生产中出现的问题及时进行优化。
试生产过程中各装置生产情况如下:1 质量馏出口控制计划馏出口质量控制计划主要根据HVI500基础油质量标准(Q/SHR001-95),及HVI350、HVI650实际生产中粘度、碱氮、比色等在各工序的变化情况而制定。
表1 各工序馏出口质量控制计划项目运动粘度比色残炭闪点馏程凝点碱性氮旋氧中和值外观单位mm 2/s #%℃℃℃Ppm min.mgKOH/g三蒸馏8.6~9.6<4.5<0.2>235<100/////一糠醛实测<3.5<0.15>235//实测///酮苯(轻)///>235/<-9////白土实测<3<0.15>235/实测<130>130<0.03透明标准95~107<3.5<3.5>235/倾点<-5报告>130<0.03透明2 生产工艺条件工艺条件是依据最终产品质量要求及馏份油在各工序加工过程中质量控制项目的变化而制定的,并在试产时根据操作实际调整形成的。
2.1 减压切割表2 HVI500减压馏份质量(平均值)分析项目馏程,℃500℃馏出粘度比色残炭闪点2%10%50%90%ml mm 2/s #%℃质量分析422450481492988.884.0~4.50.15252~258加工量在7000~8700吨/日时,减压塔的操作可满足预定质量控制要求,生产出合格的润滑油料。
润滑油基础油的生产

4
润滑油的生产工序
①切取原料(蒸馏) ②脱沥青(对残渣原料) ③精制 ④脱蜡 ⑤补充精制和后处理 ⑥调合
5
减一线
常压 渣油 减
溶 剂
压
精
蒸
制
馏
两
烷 脱 沥
青
渣油
减二线 白
酮
土
减三线
苯 脱
或
加
减四线
蜡
氢 精
减压渣油
❖ 以比色或残碳作馏出口控 制指标。
萃取系统示意图
36
基础油生产---糠醛精制
控制抽提塔温度的原因:从塔底到塔顶,原料
中的理相组分逐渐减少,糠醛在混合液中的比重 相对增加,因而在溶剂中临界溶解温度也相应提 高,这就需要操作温度从下至上逐步提高,以保 证精制深度。而底部温度逐步降低,使溶剂中的 部分理想组分逐渐分离出来,回到精制液中去, 从而减少理想组分的损失,提高精制油收率 。
性差,脱沥青油质量差; 丙烷既具有一定的溶解能力,又有较好的选择性,
是良好的脱沥青溶剂,特别适合于用作生产润滑油 料。 当目的产品为催化裂化或加氢裂化原料时,多采用 丁烷或戊烷作溶剂。 为了调节溶剂的溶解能力和选择性,或受溶剂来源 限制,也可采用混合溶剂。
25
图11-5 脱沥青油收率与溶剂比关系
4)抗氧化安定性 非烃类化合物安定性差。
5)残炭 6)溶解能力 7)闪点
形成残炭主要物质是润滑油中的多环芳烃、胶质、 沥青质。
提高蒸馏精度,脱除胶质沥青质。
溶解能力指对添加剂和氧化产物的溶解能力。一般 来说,烷烃的溶解能力差,芳烃的溶解能力强。
安全性指标。馏分越轻闪点越低,轻组分含量越多 闪点越低。
润滑油基础油的生产工艺优化选择
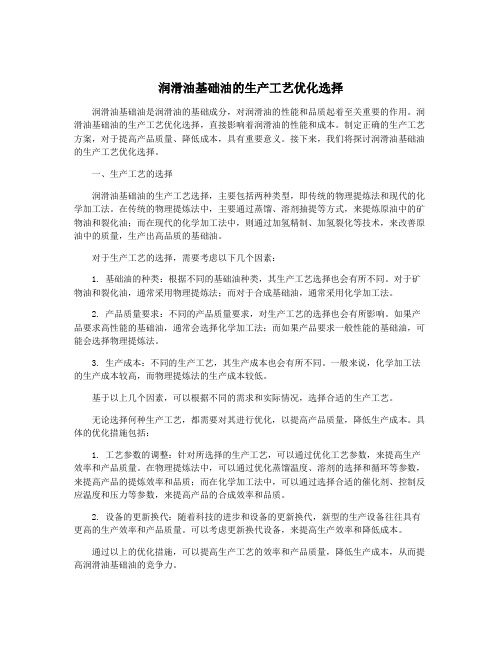
润滑油基础油的生产工艺优化选择润滑油基础油是润滑油的基础成分,对润滑油的性能和品质起着至关重要的作用。
润滑油基础油的生产工艺优化选择,直接影响着润滑油的性能和成本。
制定正确的生产工艺方案,对于提高产品质量、降低成本,具有重要意义。
接下来,我们将探讨润滑油基础油的生产工艺优化选择。
一、生产工艺的选择润滑油基础油的生产工艺选择,主要包括两种类型,即传统的物理提炼法和现代的化学加工法。
在传统的物理提炼法中,主要通过蒸馏、溶剂抽提等方式,来提炼原油中的矿物油和裂化油;而在现代的化学加工法中,则通过加氢精制、加氢裂化等技术,来改善原油中的质量,生产出高品质的基础油。
对于生产工艺的选择,需要考虑以下几个因素:1. 基础油的种类:根据不同的基础油种类,其生产工艺选择也会有所不同。
对于矿物油和裂化油,通常采用物理提炼法;而对于合成基础油,通常采用化学加工法。
2. 产品质量要求:不同的产品质量要求,对生产工艺的选择也会有所影响。
如果产品要求高性能的基础油,通常会选择化学加工法;而如果产品要求一般性能的基础油,可能会选择物理提炼法。
3. 生产成本:不同的生产工艺,其生产成本也会有所不同。
一般来说,化学加工法的生产成本较高,而物理提炼法的生产成本较低。
基于以上几个因素,可以根据不同的需求和实际情况,选择合适的生产工艺。
无论选择何种生产工艺,都需要对其进行优化,以提高产品质量,降低生产成本。
具体的优化措施包括:1. 工艺参数的调整:针对所选择的生产工艺,可以通过优化工艺参数,来提高生产效率和产品质量。
在物理提炼法中,可以通过优化蒸馏温度、溶剂的选择和循环等参数,来提高产品的提炼效率和品质;而在化学加工法中,可以通过选择合适的催化剂、控制反应温度和压力等参数,来提高产品的合成效率和品质。
2. 设备的更新换代:随着科技的进步和设备的更新换代,新型的生产设备往往具有更高的生产效率和产品质量。
可以考虑更新换代设备,来提高生产效率和降低成本。
润滑油基础油生产工艺研究
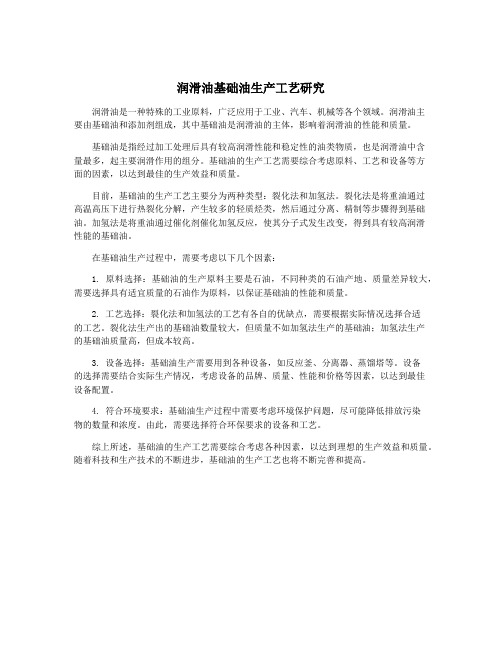
润滑油基础油生产工艺研究润滑油是一种特殊的工业原料,广泛应用于工业、汽车、机械等各个领域。
润滑油主要由基础油和添加剂组成,其中基础油是润滑油的主体,影响着润滑油的性能和质量。
基础油是指经过加工处理后具有较高润滑性能和稳定性的油类物质,也是润滑油中含量最多,起主要润滑作用的组分。
基础油的生产工艺需要综合考虑原料、工艺和设备等方面的因素,以达到最佳的生产效益和质量。
目前,基础油的生产工艺主要分为两种类型:裂化法和加氢法。
裂化法是将重油通过高温高压下进行热裂化分解,产生较多的轻质烃类,然后通过分离、精制等步骤得到基础油。
加氢法是将重油通过催化剂催化加氢反应,使其分子式发生改变,得到具有较高润滑性能的基础油。
在基础油生产过程中,需要考虑以下几个因素:1. 原料选择:基础油的生产原料主要是石油,不同种类的石油产地、质量差异较大,需要选择具有适宜质量的石油作为原料,以保证基础油的性能和质量。
2. 工艺选择:裂化法和加氢法的工艺有各自的优缺点,需要根据实际情况选择合适的工艺。
裂化法生产出的基础油数量较大,但质量不如加氢法生产的基础油;加氢法生产的基础油质量高,但成本较高。
3. 设备选择:基础油生产需要用到各种设备,如反应釜、分离器、蒸馏塔等。
设备的选择需要结合实际生产情况,考虑设备的品牌、质量、性能和价格等因素,以达到最佳设备配置。
4. 符合环境要求:基础油生产过程中需要考虑环境保护问题,尽可能降低排放污染物的数量和浓度。
由此,需要选择符合环保要求的设备和工艺。
综上所述,基础油的生产工艺需要综合考虑各种因素,以达到理想的生产效益和质量。
随着科技和生产技术的不断进步,基础油的生产工艺也将不断完善和提高。
日本出光兴产将在上海成立润滑油研发中心

第2期张翠侦等.重质润滑油基础油的原料制备及加工工艺的研究35OIL RESEARCH &APPLICATION油品研究与应用由表8可知,两种脱沥青油采用合适的加工工艺制备的重质润滑油基础油分别满足中国石油企业标准(Q /SH 44-2009)中150BS 光亮油和90BS 光亮油的指标要求。
4结论(1)不同性质的减压渣油,所得的脱沥青油性质差别较大。
较石蜡基脱沥青油性质,环烷基脱沥青油运动黏度、硫含量和氮含量较高,凝点、蜡含量和C P 值较低。
(2)石蜡基减压渣油可采用加氢处理-补充精制-酮苯脱蜡工艺进行重质润滑油基础油的生产;环烷基减压渣油根据脱沥青油的含蜡量不同,可选择加氢处理-临氢降凝-补充精制工艺或加氢处理-异构脱蜡-补充精制工艺进行重质润滑油基础油的生产。
参考文献:[1]裴文军.润滑油基础油生产工艺的选择[J ].炼油技术与工程,2012,42(7):25-29.[2]李晓文.溶剂脱沥青的技术进展与工艺优化[J ].中外能源,2007,12(2):68-75.[3]徐春明,杨朝合.石油炼制工程[M ].北京:石油工业出版社,2017.[4]范思远,程国香,高鲜会,等.减压渣油性质对丙烷脱沥青过程的影响[J ].当代化工,2011,40(4):354-356.[5]张志娥.国内外润滑油基础油生产技术及发展趋势[J ].当代石油石化,2005,13(4):25-30.[6]熊春珠,汪军平,马莉莉,等.稠油脱沥青油减压深拔提高150BS 光亮油黏度指数[J ].炼油技术与工程,2008,38(6):20-22.[7]侯克,胡宝其.荆门分公司120BS 光亮油的生产[J ].广东化工,2012,39(14):44-45.[8]蔡烈奎,刘剑峰,张健,等.新疆春风稠油减压渣油生产150BS 光亮油工艺研究[J ].润滑油,2018,33(2):56-60.[9]MVH 1208Q -SY44-2009通用润滑油基础油标准[S/OL ].https ://wenku.baidu.com/view/74b821c94693daef5ef73d48.html.2014.01.28.收稿日期:2018-06-07。
润滑油基础油生产工艺研究

润滑油基础油生产工艺研究
润滑油是一个具有广泛应用的化工产品,目前已成为了现代工业不可或缺的重要物质。
润滑油的质量取决于基础油的质量和加工工艺,因此研究和提高润滑油基础油的生产工艺
非常重要。
1.原料的选择与制备
润滑油基础油的生产主要以石油为原料,而石油中的不同成分有不同的烷基结构和碳
氢化合物组成,因此对于不同类型的润滑油,选取适当的石油原料非常重要。
此外,还需
要对原料进行适当的净化和加工,以去除其中的杂质和不纯物,保证生产的润滑油基础油
质量稳定。
2.加氢处理
加氢处理是润滑油基础油生产中非常重要的一步,能够改善原油的分子结构,提高润
滑油的氧化稳定性和抗磨性能。
加氢过程中,需要控制反应温度、催化剂种类和反应时间
等因素,以达到最佳效果。
3.分馏分离
分馏分离是润滑油基础油生产过程中的关键步骤,是将加氢处理后的油品分离出不同
的级别和组分的过程。
分馏过程中,需要根据不同油品的沸点范围和密度等物理性质进行
分离,以保证所得的基础油质量符合要求。
4.净化处理
净化处理是润滑油基础油生产过程中最后的一道工序,其目的是去除油品中的杂质和
不纯物,提高润滑油基础油的品质和性能。
净化处理方法包括沉淀法、过滤法、溶剂法以
及离子交换等。
总体来说,润滑油基础油的生产工艺建立在对原料、反应条件以及净化工艺的深入研
究上,只有通过对生产工艺的不断优化与改进,才能生产出更加符合市场需求的高品质润
滑油基础油。
润滑油基础油的制备与应用

润滑油基础油的制备与应用润滑油在工业生产中扮演着不可或缺的重要角色。
润滑油最核心的组成部分便是基础油。
基础油的质量直接影响到润滑油的性能指标,如粘度、氧化安定性、低温流动性等。
因此,研发更高品质的润滑油基础油具有重要的意义。
一、润滑油基础油的制备润滑油基础油通常分为矿物油、合成油和生物油三类。
其中,矿物油是指从石油提炼出的基础油。
石油本身就是复杂的有机化合物,经过多个步骤的加工和分离,才能提炼出适用于制备润滑油的基础油。
合成油是指通过化学合成得到的基础油。
合成油的优点在于可以根据需要精确控制关键的化学性质,以满足不同类型润滑油的要求。
生物油是指从植物或动物中提取的基础油。
相对于传统油品,生物油环保性更高,但同时其生产成本也更高。
在润滑油基础油的制备过程中,最为关键的是加工工艺的优化。
例如,合成油的制备过程中需要根据反应物浓度、反应温度等参数的优化而得到最佳的产率和产品性能。
同时,矿物油的开采和提炼过程中,需要减少对环境和人体的影响,尽可能降低产品污染和环境污染的风险。
二、润滑油基础油的应用润滑油基础油的应用范围非常广泛。
在机械制造业中,润滑油可以用于汽车、航空器、火箭等各类发动机的润滑。
同时,润滑油也常常被用于海运、轨道交通领域的机械设备。
相比较于传统的矿物油基础油,合成油和生物油的应用范围也在逐渐扩展。
合成油适用于高温、高负荷的工作环境,可以提高润滑油的稳定性和热稳定性。
生物油的环保性使得其在一些特定环境、如国家公园等使用较多。
值得注意的是,不同的润滑油基础油在性能方面也存在差异。
例如,矿物油在耐氧化性方面较差;合成油的界面活性较低;生物油可能存在微生物污染的风险。
因此,在润滑油选择及使用过程中,需要根据具体使用条件和性能需求来选择合适的润滑油基础油。
三、结论润滑油基础油是润滑油中最核心的组成部分。
在润滑油基础油的制备过程中,加工工艺的优化是关键。
润滑油基础油的应用范围广泛,包括机械制造业、海运、轨道交通等领域。
润滑油基础油生产工艺研究

润滑油基础油生产工艺研究随着工业化的快速发展,润滑油已成为各个领域中必不可少的一种石化产品。
其中,润滑油基础油是润滑油的重要组成部分,其质量对润滑油的性能和使用寿命起着至关重要的作用。
本文将对润滑油基础油的生产工艺进行研究,探讨其生产过程中的技术特点和影响质量的因素。
1. 克提取工艺克提取工艺是其中比较常见的一种工艺类型,利用溶剂从石油裂化轻油中提取基础油。
该工艺有以下几个步骤:石油裂解轻油的先冷却急冷,硫酸钠碱法去除酸性物质,再通过一系列的精馏操作,得到不同粘度等级的基础油。
2. 改质工艺改质工艺是对浓缩提取出的基础油进行一定程度的化学改性处理,以改变其分子量、分子结构和性能,提高基础油的耐高温、抗氧化、抗磨性和清洁分散性等。
3. 深加工工艺深加工工艺是在改质基础油的基础上,进一步加工成特殊的润滑油和油剂产品。
一般包括添加各种添加剂、合成脂肪酸酯类的润滑油,以及合成酰胺油剂等。
1. 基本为连续式生产。
润滑油基础油生产的生产过程大多数情况下都采用连续生产方式,具有连续性和稳定性等优点,生产效率高,生产成本低。
2. 工艺流程较长。
润滑油生产工艺较为复杂,需要多道工艺流程,涉及到很多化学反应和物理性处理,所以工艺流程较长。
3. 技术装备需求较高。
润滑油基础油生产需要采用高效的技术装备,如高效精馏塔、氢气生成装置、催化反应器等,以满足润滑油基础油的生产要求。
4. 环保要求高。
润滑油生产的过程中会产生大量的污染物,对环境会造成一定的危害。
因此,对润滑油基础油生产过程进行环保处理和监测尤为重要。
三、影响润滑油基础油质量的因素分析润滑油基础油的质量对于润滑油的性能和使用寿命起着至关重要的作用。
影响润滑油基础油质量的因素主要有以下几点:1. 原料的质量。
原料的质量是影响润滑油基础油质量的首要因素,而原料的品质又取决于石油的来源和加工工艺。
2. 工艺的操作技术。
润滑油基础油生产的工艺操作技术非常精细,其中任何一个步骤出现问题都会影响到基础油的品质。
润滑油基础油生产工艺研究

润滑油基础油生产工艺研究
润滑油是一种常用的工业润滑剂,用于减少机械运动部件之间的摩擦和磨损,以提高
机械设备的性能和寿命。
润滑油的基础油是润滑油的主要成分,它决定了润滑油的性能和
品质。
基础油的生产工艺是指将原油经过一系列的分离、脱硫、脱蜡和精制等工艺步骤,得
到适合作为润滑油基础油的产品。
基础油的生产工艺研究旨在优化工艺条件,提高基础油
的质量和产量。
原油经过加热后进入蒸馏塔,根据不同组分的沸点差异,将原油分离成不同沸点范围
的馏分。
常见的原油分离方法有常压蒸馏和真空蒸馏。
经过蒸馏的原油馏分中含有硫、氮、微量金属和杂质等有害物质,需要进行脱硫和脱
杂处理。
脱硫方法包括水洗、氢气脱硫和催化剂吸附等,脱杂方法主要是利用吸附剂吸附
杂质。
然后,经过脱硫脱杂处理的馏分进一步进行脱蜡处理。
蜡是基础油中的一种固态物质,会降低润滑油的流动性。
脱蜡方法主要有晶体破碎法和溶解脱蜡法等。
经过脱蜡处理的馏分还需要进行精制,以提高基础油的纯度和性能。
精制方法包括加
氢精制、油脱色、油漂白、脱臭等。
通过对基础油生产工艺的研究,可以优化工艺参数,提高生产设备的效率和稳定性,
从而提高基础油的纯度和性能。
还可以研究新型的工艺方法,如超临界流体萃取、离子液
体萃取等,以提高基础油的产率和质量。
润滑油基础油的生产工艺研究对于提高润滑油性能和品质具有重要意义,需要不断优
化工艺条件和研发新型工艺方法。
石蜡基减压渣油生产润滑油基础油的研究
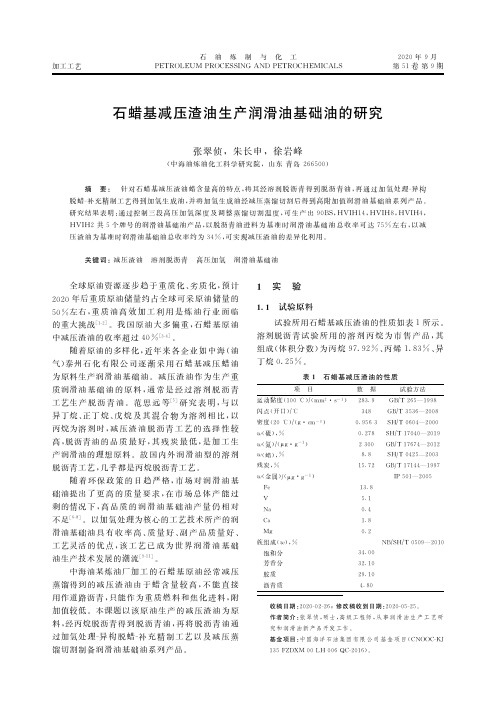
加工工艺石 油 炼 制 与 化 工PETROLEUMPROCESSINGANDPETROCHEMICALS2020年9月 第51卷第9期 收稿日期:2020 02 26;修改稿收到日期:2020 05 25。
作者简介:张翠侦,硕士,高级工程师,从事润滑油生产工艺研究和润滑油新产品开发工作。
基金项目:中国海洋石油集团有限公司基金项目(CNOOC KJzL@{|}:fX$%:@N:2+,张翠侦,朱长申,徐岩峰(中海油炼油化工科学研究院,山东青岛266500)摘 要: 针对石蜡基减压渣油蜡含量高的特点,将其经溶剂脱沥青得到脱沥青油,再通过加氢处理 异构脱蜡 补充精制工艺得到加氢生成油,并将加氢生成油经减压蒸馏切割后得到高附加值润滑油基础油系列产品。
研究结果表明:通过控制三段高压加氢深度及调整蒸馏切割温度,可生产出90BS,HVIH14,HVIH8,HVIH4,HVIH2共5个牌号的润滑油基础油产品,以脱沥青油进料为基准时润滑油基础油总收率可达75%左右,以减压渣油为基准时润滑油基础油总收率约为34%,可实现减压渣油的差异化利用。
关键词:减压渣油 溶剂脱沥青 高压加氢 润滑油基础油全球原油资源逐步趋于重质化、劣质化,预计2020年后重质原油储量约占全球可采原油储量的50%左右,重质油高效加工利用是炼油行业面临的重大挑战[1 2]。
我国原油大多偏重,石蜡基原油中减压渣油的收率超过40%[3 4]。
随着原油的多样化,近年来各企业如中海(油气)泰州石化有限公司逐渐采用石蜡基减压蜡油为原料生产润滑油基础油。
减压渣油作为生产重质润滑油基础油的原料,通常是经过溶剂脱沥青工艺生产脱沥青油。
范思远等[5]研究表明,与以异丁烷、正丁烷、戊烷及其混合物为溶剂相比,以丙烷为溶剂时,减压渣油脱沥青工艺的选择性较高,脱沥青油的品质最好,其残炭最低,是加工生产润滑油的理想原料。
故国内外润滑油型的溶剂脱沥青工艺,几乎都是丙烷脱沥青工艺。
- 1、下载文档前请自行甄别文档内容的完整性,平台不提供额外的编辑、内容补充、找答案等附加服务。
- 2、"仅部分预览"的文档,不可在线预览部分如存在完整性等问题,可反馈申请退款(可完整预览的文档不适用该条件!)。
- 3、如文档侵犯您的权益,请联系客服反馈,我们会尽快为您处理(人工客服工作时间:9:00-18:30)。
2019年4月Apr.2019润滑油LUBRICATING OIL第34卷第2期Vo l.34,No.2DOI:10.19532/j.cnki.cn21-1265/tq.2019.02.008文章编号:1002-3119(2019)02-0031-05重质润滑油基础油的原料制备及加工工艺的研究张翠侦,焦祖凯,朱长申,许海龙,徐岩峰(中国海油炼油化工科学研究院(北京)有限公司,山东青岛266500)摘要:文章研究了环烷基减压渣油和石蜡基减压渣油经丙烷脱沥青工艺生产脱沥青油的影响因素,并考察脱沥青油作为重质润滑油基础油原料的可行性。
结果表明:同样制备合格的重质润滑油基础油原料,环烷基减压渣油相比于石蜡基减压渣油,在生产工艺中需要较小的溶剂比和较高的抽提温度;因此,所得两种基础油原料的倾点、蜡含量等性质存在较大差异,故生产重质润滑油基础油的工艺将有所差别。
关键词:减压渣油;丙烷脱沥青;脱沥青油中图分类号:TE626.3文献标识码:AStudy on Feedstock Preparation and ProcessingTechnology of Heavy Lube-base OilsZHANG Cui-zhen,JIAO Zu-kai,ZHU Chang-shen,XU Hai-long,XU Yan-feng(CNOOCResearch Institute of Oil and Petrochemicals(Beijing)Co.Ltd.,Qingdao266500,China)Abstract:This paper investigated the influence factors of producing deasphalted oil(DAO)from naphthenic and paraffinic vacu-um residue with propane deasphalting process,and researched the feasibility of DAO as feedstock for heavy lube-base oils.The results illustrated that,compared with paraffin vacuum residue,producing the qualified feedstock for heavy lube-base oils from naphthenic vacuum residue requires lower solvent/oil ratio and higher extraction temperature.Therefore,there are large differences in the pour point and wax content of the obtained two base oil feedstocks,so the processes for producing heavy lubricating base oils will be diverse.Key words:vacuum residue;propane deasphalting;DAO0引言重质润滑油基础油广泛应用于内燃机油、车辆齿轮油、船舶发动机油、重负荷齿轮油和润滑脂等产品的生产,市场需求量较大。
而重质润滑油基础油缺乏,且资源难觅。
减压渣油作为生产重质润滑油基础油的原料,通常是经过溶剂脱沥青工艺生产脱沥青油,即残渣润滑油的原料[1-3]。
试验证明[4],以丙烷作溶剂时,选择性较高,脱沥青油的品质最好,其残炭值最低,是加工生产润滑油的理想原料。
故国内外润滑油型的溶剂脱沥青工艺,几乎都是丙烷脱沥青工艺。
本文以环烷基原油经常减压工艺所得的减压渣油和石蜡基原油经常减压工艺所得的减压渣油为原料,考察溶剂脱沥青试验影响因素,包括抽提温度、剂油体积比等对脱沥青油性质的影响,旨在拓宽生产重质润滑油基础油的资源。
1实验部分1.1试验材料试验原料为环烷基原油经常减压工艺所得的减压渣油(1#减压渣油)和石蜡基原油经常减压工艺所得的减压渣油(2#减压渣油),主要性质见表1。
表1减压渣油性质项目1#减压渣油2#减压渣油分析方法密度(20ħ)/g·cm-31.01300.9563GB/T1884运动黏度(100ħ)/mm2·s-13600283.9GB/T265闪点(开口)/ħ>260348GB/T3536残炭/%20.1315.72GB/T1714432润滑油2019年第34卷表1(续)项目1#减压渣油2#减压渣油分析方法硫含量/mg ·kg -144302780ASTM D5453氮含量/mg ·kg -137002300ASTM D4629四组分/%T 0618*饱和分19.6034.00芳香分32.2032.10胶质41.1929.10沥青质7.014.80注:*方法源于交通运输部发布的行业标准“JTG E20-2011公路工程沥青及沥青混合料试验规程”。
由表1可知,两种减压渣油的硫含量、氮含量、胶质及残炭等均偏高,性质较差;且两种减压渣油的组成差别较大,石蜡基减压渣油的饱和分较环烷基减压渣油高,胶质和沥青质含量较低。
1.2试验装置及催化剂丙烷脱沥青试验采用连续式丙烷脱沥青试验装置,处理能力为1.0kg /h ,萃取塔内装填规整填料,操作压力为4MPa 。
工艺原则流程如图1所示。
图1丙烷脱沥青中试装置原则流程丙烷为市售产品,纯度为97.92%。
溶剂组成如表2所示。
表2溶剂组成物料名称体积组成/%丙烷97.92表2(续)物料名称体积组成/%丙烯1.83异丁烷0.252结果与讨论2.11#减压渣油丙烷脱沥青试验该试验以1#减压渣油为原料,对丙烷脱沥青工艺操作参数如剂油比、抽提温度等进行考察。
2.1.1剂油比对脱沥青油性质的影响剂油比作为一个重要的影响因素,其大小决定了溶剂循环量的大小,对脱沥青油收率、质量和工艺过程的能耗都会产生直接的影响。
故以1#减压渣油为原料,在其他影响因素固定的前提下,进行剂油比的考察试验,试验条件和结果如表3所示。
表31#减压渣油不同剂油比下丙烷脱沥青试验结果(系统压力4MPa ,进料量700g /h ,抽提温度60ħ/77ħ)项目剂油比4ʒ16ʒ18ʒ110ʒ1脱沥青油收率/%23.728.432.735.8脱油沥青收率/%76.371.667.364.2脱沥青油性质残炭/%0.351.051.431.63100ħ运动黏度/mm 2·s-146.4350.6054.4158.02硫含量/mg ·kg -12920307032003500氮含量/mg ·kg -11830206022712413由表3可知:(1)在抽提温度等条件固定的前提下,剂油比由4ʒ1提高至10ʒ1,脱沥青油的收率由23.7%增至35.8%,但残炭、硫含量及氮含量等指标呈上升趋势,油品质量变差;(2)剂油比为6ʒ1时,所得脱沥青油的残炭值为1.05%,满足加氢试验的进料要求(要求残炭值<1.2%)。
2.1.2抽提温度对脱沥青油性质的影响抽提温度对脱沥青过程影响较大,且最灵敏,作为控制脱沥青油收率和选择性的主要控制因素。
因1#减压渣油最佳抽提剂油比为6ʒ1,本试验固定该剂油比进行抽提温度的考察,试验条件和结果如表4所示。
表41#减压渣油不同抽提温度下丙烷脱沥青试验结果(系统压力4MPa ,剂油比6ʒ1,进料量700g /h )项目抽提温度/ħ58/7560/7763/8067/8470/88脱沥青油收率/%30.528.426.324.923.0脱油沥青收率/%69.571.673.775.177.0第2期张翠侦等.重质润滑油基础油的原料制备及加工工艺的研究33表4(续)项目抽提温度/ħ58/7560/7763/8067/8470/88脱沥青油性质残炭/%1.291.050.880.680.52 100ħ运动黏度/mm2·s-152.3650.643.4137.2334.45硫含量/mg·kg-132603070300029602870氮含量/mg·kg-122702060201019101770由表4可知:(1)随着抽提温度的增大,脱沥青油收率和残炭值逐渐降低。
因当抽提温度增大时,溶剂的密度降低,溶解能力也降低,使得脱沥青油收率降低;(2)当抽提温度为60ħ/77ħ时,所得脱沥青油的残炭值为1.05%,满足加氢试验的进料要求(残炭值<1.2%)。
2.22#减压渣油丙烷脱沥青试验该试验以2#减压渣油为原料,对丙烷脱沥青试验操作参数如剂油体积比、抽提温度等进行考察。
2.2.1剂油比对脱沥青油性质的影响以2#减压渣油为原料,在其他影响因素固定的前提下,进行了剂油体积比的考察试验,试验条件和结果如表5所示。
表52#减压渣油不同剂油比下丙烷脱沥青试验结果(系统压力4MPa,进料量700g/h,抽提温度55ħ/72ħ)项目剂油比6ʒ18ʒ110ʒ1脱沥青油收率/%28.041.442.8脱油沥青收率/%72.058.657.2脱沥青油性质残炭/%0.550.800.88100ħ运动黏度/mm2·s-123.4825.9826.43硫含量/mg·kg-1124013701390氮含量/mg·kg-1790880990由表5可知:(1)在抽提温度等条件固定的前提下,随着剂油比的提高,脱沥青油的收率、硫含量、氮含量和残炭均呈上升趋势。
当剂油比自6ʒ1提升至8ʒ1时,脱沥青油的收率由28.0%增至41.4%,提高约13%;当剂油比由8ʒ1提升至10ʒ1时,脱沥青油的收率趋于稳定;(2)当剂油比为8ʒ1时,残炭值为0.80%,远低于加氢进料要求(残炭值<1.2%),可通过调整抽提温度,在保证残炭指标的前提下,实现收率最大化。
2.2.2抽提温度对脱沥青油性质的影响因2#减压渣油最佳剂油比为8ʒ1,本试验固定该剂油比进行抽提温度的考察,试验条件和结果如表6所示。
表62#减压渣油不同抽提温度下丙烷脱沥青试验结果(系统压力4MPa,剂油比8ʒ1,进料量700g/h)项目抽提温度/ħ50/6555/7057/72脱沥青油收率/%47.544.341.2脱油沥青收率/%52.555.758.8脱沥青油性质残炭/%1.421.150.70100ħ运动黏度/mm2·s-132.6026.1025.36硫含量/mg·kg-1149013901360氮含量/mg·kg-113001200850由表6可知:(1)抽提温度升高,脱沥青油收率降低、残炭值变小;(2)抽提温度为55ħ/70ħ的试验条件所得脱沥青油的残炭值为1.15%,收率为44.3%,满足加氢试验的进料要求(残炭值<1.2%),该条件可用于生产重质润滑油基础油原料。