型钢轧制缺陷及调整
轧制缺陷及质量控制
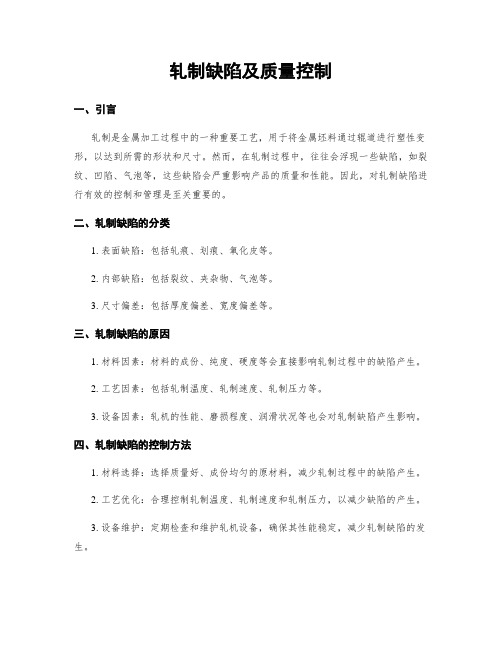
轧制缺陷及质量控制一、引言轧制是金属加工过程中的一种重要工艺,用于将金属坯料通过辊道进行塑性变形,以达到所需的形状和尺寸。
然而,在轧制过程中,往往会浮现一些缺陷,如裂纹、凹陷、气泡等,这些缺陷会严重影响产品的质量和性能。
因此,对轧制缺陷进行有效的控制和管理是至关重要的。
二、轧制缺陷的分类1. 表面缺陷:包括轧痕、划痕、氧化皮等。
2. 内部缺陷:包括裂纹、夹杂物、气泡等。
3. 尺寸偏差:包括厚度偏差、宽度偏差等。
三、轧制缺陷的原因1. 材料因素:材料的成份、纯度、硬度等会直接影响轧制过程中的缺陷产生。
2. 工艺因素:包括轧制温度、轧制速度、轧制压力等。
3. 设备因素:轧机的性能、磨损程度、润滑状况等也会对轧制缺陷产生影响。
四、轧制缺陷的控制方法1. 材料选择:选择质量好、成份均匀的原材料,减少轧制过程中的缺陷产生。
2. 工艺优化:合理控制轧制温度、轧制速度和轧制压力,以减少缺陷的产生。
3. 设备维护:定期检查和维护轧机设备,确保其性能稳定,减少轧制缺陷的发生。
4. 润滑控制:选择合适的润滑剂,保证轧制过程中的润滑效果,减少磨擦和磨损,降低缺陷产生的可能性。
五、质量控制措施1. 检测方法:采用超声波、X射线、磁粉探伤等非破坏性检测方法,及时发现和排除轧制缺陷。
2. 检测设备:使用高精度的检测设备,确保对轧制缺陷的检测准确性和可靠性。
3. 检测标准:制定严格的轧制缺陷检测标准,明确缺陷的类型、数量和尺寸要求。
4. 检测频率:根据产品的重要性和应用领域,确定合理的检测频率,确保产品质量的稳定性和可靠性。
六、案例分析以某钢铁公司为例,该公司采用了先进的轧制设备和严格的质量控制措施,成功地控制了轧制缺陷的发生。
通过优化工艺参数,选择高质量的原材料,并定期进行设备维护和润滑控制,该公司的产品质量得到了有效提升。
同时,该公司还建立了完善的质量检测体系,采用先进的检测设备和严格的检测标准,确保产品质量的稳定性和可靠性。
轧制缺陷及质量控制
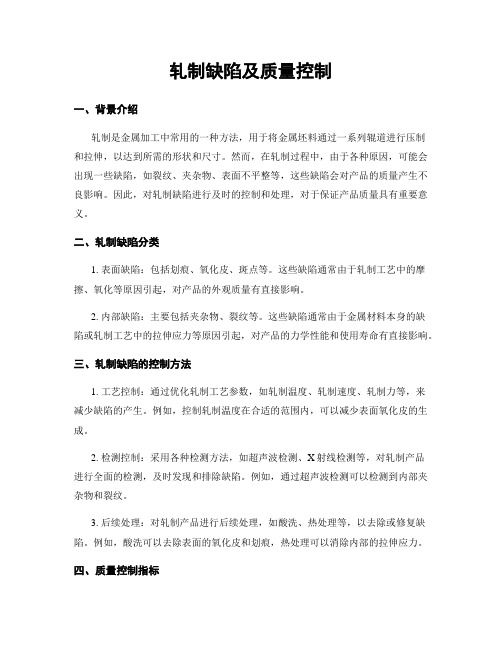
轧制缺陷及质量控制一、背景介绍轧制是金属加工中常用的一种方法,用于将金属坯料通过一系列辊道进行压制和拉伸,以达到所需的形状和尺寸。
然而,在轧制过程中,由于各种原因,可能会出现一些缺陷,如裂纹、夹杂物、表面不平整等,这些缺陷会对产品的质量产生不良影响。
因此,对轧制缺陷进行及时的控制和处理,对于保证产品质量具有重要意义。
二、轧制缺陷分类1. 表面缺陷:包括划痕、氧化皮、斑点等。
这些缺陷通常由于轧制工艺中的摩擦、氧化等原因引起,对产品的外观质量有直接影响。
2. 内部缺陷:主要包括夹杂物、裂纹等。
这些缺陷通常由于金属材料本身的缺陷或轧制工艺中的拉伸应力等原因引起,对产品的力学性能和使用寿命有直接影响。
三、轧制缺陷的控制方法1. 工艺控制:通过优化轧制工艺参数,如轧制温度、轧制速度、轧制力等,来减少缺陷的产生。
例如,控制轧制温度在合适的范围内,可以减少表面氧化皮的生成。
2. 检测控制:采用各种检测方法,如超声波检测、X射线检测等,对轧制产品进行全面的检测,及时发现和排除缺陷。
例如,通过超声波检测可以检测到内部夹杂物和裂纹。
3. 后续处理:对轧制产品进行后续处理,如酸洗、热处理等,以去除或修复缺陷。
例如,酸洗可以去除表面的氧化皮和划痕,热处理可以消除内部的拉伸应力。
四、质量控制指标1. 表面质量:通过目视检查或光学显微镜观察,评估产品表面的缺陷情况,如划痕、氧化皮等。
2. 内部质量:通过超声波检测、X射线检测等非破坏性检测方法,评估产品内部的缺陷情况,如夹杂物、裂纹等。
3. 力学性能:通过拉伸试验、冲击试验等方法,评估产品的力学性能,如强度、韧性等。
五、质量控制流程1. 前期准备:制定轧制工艺参数和质量控制指标,准备好检测设备和试验样品。
2. 轧制过程控制:根据工艺参数进行轧制,定期对轧制产品进行表面质量检查,及时调整工艺参数。
3. 检测控制:对轧制产品进行全面的内部质量检测,如超声波检测、X射线检测等。
4. 后续处理:对有缺陷的产品进行后续处理,如酸洗、热处理等。
轧钢常见缺陷
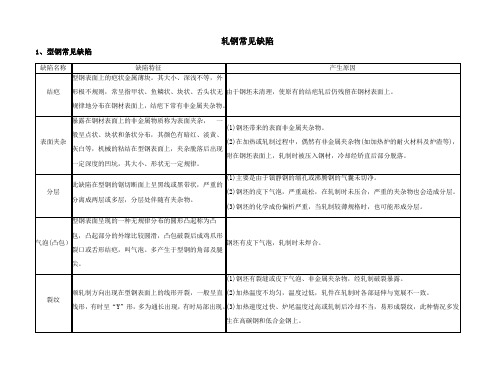
2)腰厚、腰薄产生的主要原因是:如按孔型设计头部压下量为77—=6.7mm;腰部压下量为16一=1.5mm,如果六孔压下量加大l.5mm,则头部尺寸为75.5mm压下量由6.7mm减少到5.2mm,腰部压下量由1.5mm减少到0,自然头部对腰部有拉伸加之腰部无压下而宽展,所以腰变薄,反之腰部变厚。
(1)因辊式或立式矫直机调整操作不当,将钢轨矫断。
(2)钢质不好,如局部夹杂、偏析,在矫直过程中被矫(压)裂(断)。
3、线材常见缺陷
缺陷名称
缺陷特征
产生原因
耳子
盘条表面沿轧制方向的条状凸起称为耳子,有单边耳子,也有双边耳子。在高速线材轧机(连轧)生产中,最终产品头尾两端很难避免耳子的产生。
1)轧槽导卫安装不正及放偏过钢,使轧件产生耳子。
(1)卫板安装不良,使钢轨产生力偶,形成扭转。
(2)轧件温度不均或压下量不均,造成各部延伸不一致。
(3)矫直机调整不当,钢轨受力偶作用。
(4)在冷却台架上翻钢时因温度较高也会出现扭转。
弯曲
钢轨沿垂直或水平方向呈现不平直的现象叫弯曲,一般呈镰刀形或波浪形,仅在端部的弯曲又叫弯头。
(1)由于重轨的头、腰、底面积相差较大,使轧制、冷却等工序操作易产生弯曲。
(1)钢坯带来的表面非金属夹杂物。
(2)在加热或轧制过程中,偶然有非金属夹杂物(如加热炉的耐火材料及炉渣等),附在钢坯表面上,轧制时被压入钢材,冷却经矫直后部分脱落。
分层
此缺陷在型钢的锯切断面上呈黑线或黑带状,严重的分离成两层或多层,分层处伴随有夹杂物。
(1)主要是由于镇静钢的缩孔或沸腾钢的气囊未切净。
(1)主要因钢坯缩孔部分未切净。
轧制缺陷及质量控制

轧制缺陷及质量控制一、引言轧制是金属加工中常见的一种工艺,用于将金属坯料通过辊轧机进行塑性变形,以达到所需的形状和尺寸。
然而,在轧制过程中,由于材料特性、设备磨损、操作不当等原因,常常会出现一些缺陷,如表面裂纹、气泡、夹杂物等,这些缺陷会对材料的性能和质量产生不利影响。
因此,对轧制缺陷进行有效的控制和管理是至关重要的。
二、轧制缺陷分类1. 表面缺陷:包括轧痕、划伤、氧化皮等。
这些缺陷通常由于辊轧机表面不平整、杂质污染等原因导致。
2. 内部缺陷:包括夹杂物、气泡、裂纹等。
这些缺陷通常由于材料内部的杂质、气体等引起。
三、轧制缺陷控制方法1. 设备维护与管理:定期检查辊轧机的磨损情况,及时更换损坏的辊子,保持辊轧机表面的平整度。
同时,定期清洗设备,防止杂质污染。
2. 材料质量控制:严格控制原材料的质量,检测材料中的夹杂物、气泡等缺陷。
采用先进的材料检测设备,如超声波探伤仪、X射线探伤仪等,对原材料进行全面检测。
3. 工艺参数控制:合理调整轧制工艺参数,如轧制温度、压下量、轧制速度等,以减少缺陷的产生。
通过优化工艺参数,可以改善材料的微观组织,提高材料的性能。
4. 检测与分析:建立完善的缺陷检测与分析体系,及时发现和排查缺陷。
采用先进的无损检测技术,如磁粉探伤、涡流检测等,对轧制材料进行全面检测。
5. 员工培训与管理:加强员工的培训与管理,提高员工的技术水平和质量意识。
定期组织培训,加强对轧制缺陷的认识和理解,提高员工对缺陷的检测和处理能力。
四、轧制缺陷质量控制实施效果评估1. 缺陷检出率:通过对轧制材料进行缺陷检测,统计出缺陷的数量和类型,计算缺陷检出率。
检出率的提高表明缺陷控制措施的有效性。
2. 产品合格率:通过对轧制产品进行质量检测,统计出合格产品的数量和比例,计算产品合格率。
合格率的提高表明缺陷控制措施的有效性。
3. 客户满意度:通过客户反馈和调查问卷等方式,评估客户对轧制产品质量的满意程度。
客户满意度的提高表明缺陷控制措施的有效性。
轧制缺陷及质量控制
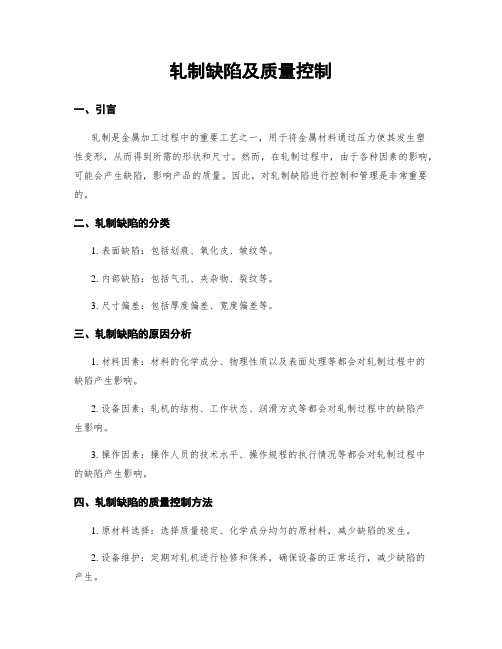
轧制缺陷及质量控制一、引言轧制是金属加工过程中的重要工艺之一,用于将金属材料通过压力使其发生塑性变形,从而得到所需的形状和尺寸。
然而,在轧制过程中,由于各种因素的影响,可能会产生缺陷,影响产品的质量。
因此,对轧制缺陷进行控制和管理是非常重要的。
二、轧制缺陷的分类1. 表面缺陷:包括划痕、氧化皮、皱纹等。
2. 内部缺陷:包括气孔、夹杂物、裂纹等。
3. 尺寸偏差:包括厚度偏差、宽度偏差等。
三、轧制缺陷的原因分析1. 材料因素:材料的化学成分、物理性质以及表面处理等都会对轧制过程中的缺陷产生影响。
2. 设备因素:轧机的结构、工作状态、润滑方式等都会对轧制过程中的缺陷产生影响。
3. 操作因素:操作人员的技术水平、操作规程的执行情况等都会对轧制过程中的缺陷产生影响。
四、轧制缺陷的质量控制方法1. 原材料选择:选择质量稳定、化学成分均匀的原材料,减少缺陷的发生。
2. 设备维护:定期对轧机进行检修和保养,确保设备的正常运行,减少缺陷的产生。
3. 工艺控制:严格控制轧制工艺参数,如轧制温度、轧制速度等,以减少缺陷的发生。
4. 检测手段:采用先进的无损检测技术,如超声波检测、X射线检测等,及时发现并排除缺陷。
5. 操作培训:加强操作人员的培训,提高其技术水平和操作规范性,减少人为因素对缺陷的影响。
五、轧制缺陷的质量控制效果评估1. 缺陷检测率:通过统计检测到的缺陷数量和总产量,计算缺陷检测率,以评估质量控制的效果。
2. 缺陷修复率:通过统计修复的缺陷数量和检测到的缺陷数量,计算缺陷修复率,以评估质量控制的效果。
3. 产品合格率:通过统计合格产品的数量和总产量,计算产品合格率,以评估质量控制的效果。
六、案例分析以某钢铁公司的轧制生产线为例,该公司采用了上述的质量控制方法,并进行了持续的改进。
经过一段时间的实践,缺陷检测率从原来的10%降低到了5%,缺陷修复率从原来的50%提高到了80%,产品合格率从原来的80%提高到了95%。
轧制缺陷及质量控制
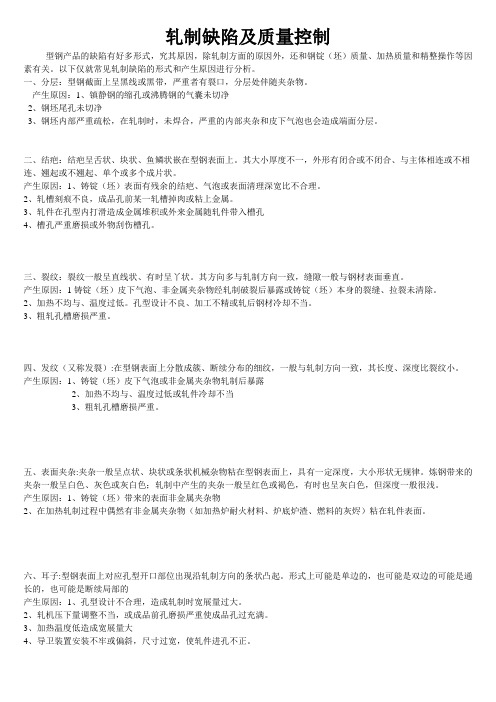
轧制缺陷及质量控制型钢产品的缺陷有好多形式,究其原因,除轧制方面的原因外,还和钢锭(坯)质量、加热质量和精整操作等因素有关。
以下仅就常见轧制缺陷的形式和产生原因进行分析。
一、分层:型钢截面上呈黑线或黑带,严重者有裂口,分层处伴随夹杂物。
产生原因:1、镇静钢的缩孔或沸腾钢的气囊未切净2、钢坯尾孔未切净3、钢坯内部严重疏松,在轧制时,未焊合,严重的内部夹杂和皮下气泡也会造成端面分层。
二、结疤:结疤呈舌状、块状、鱼鳞状嵌在型钢表面上。
其大小厚度不一,外形有闭合或不闭合、与主体相连或不相连、翘起或不翘起、单个或多个成片状。
产生原因:1、铸锭(坯)表面有残余的结疤、气泡或表面清理深宽比不合理。
2、轧槽刻痕不良,成品孔前某一轧槽掉肉或粘上金属。
3、轧件在孔型内打滑造成金属堆积或外来金属随轧件带入槽孔4、槽孔严重磨损或外物刮伤槽孔。
三、裂纹:裂纹一般呈直线状、有时呈丫状。
其方向多与轧制方向一致,缝隙一般与钢材表面垂直。
产生原因:1铸锭(坯)皮下气泡、非金属夹杂物经轧制破裂后暴露或铸锭(坯)本身的裂缝、拉裂未清除。
2、加热不均与、温度过低。
孔型设计不良、加工不精或轧后钢材冷却不当。
3、粗轧孔槽磨损严重。
四、发纹(又称发裂):在型钢表面上分散成簇、断续分布的细纹,一般与轧制方向一致,其长度、深度比裂纹小。
产生原因:1、铸锭(坯)皮下气泡或非金属夹杂物轧制后暴露2、加热不均与、温度过低或轧件冷却不当3、粗轧孔槽磨损严重。
五、表面夹杂:夹杂一般呈点状、块状或条状机械杂物粘在型钢表面上,具有一定深度,大小形状无规律。
炼钢带来的夹杂一般呈白色、灰色或灰白色;轧制中产生的夹杂一般呈红色或褐色,有时也呈灰白色,但深度一般很浅。
产生原因:1、铸锭(坯)带来的表面非金属夹杂物2、在加热轧制过程中偶然有非金属夹杂物(如加热炉耐火材料、炉底炉渣、燃料的灰烬)粘在轧件表面。
六、耳子:型钢表面上对应孔型开口部位出现沿轧制方向的条状凸起。
轧制缺陷及质量控制
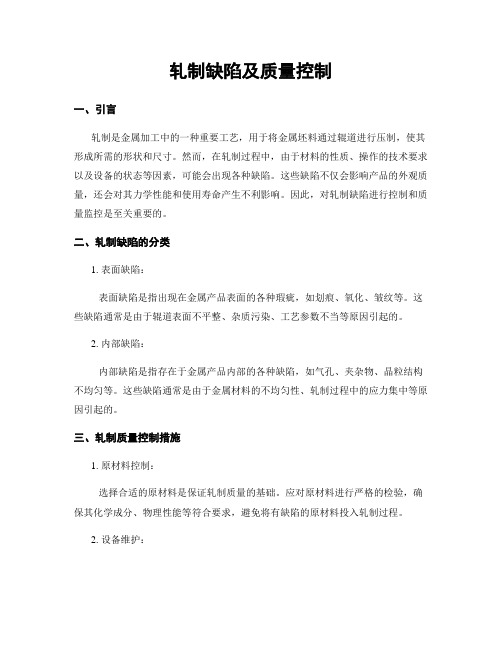
轧制缺陷及质量控制一、引言轧制是金属加工中的一种重要工艺,用于将金属坯料通过辊道进行压制,使其形成所需的形状和尺寸。
然而,在轧制过程中,由于材料的性质、操作的技术要求以及设备的状态等因素,可能会出现各种缺陷。
这些缺陷不仅会影响产品的外观质量,还会对其力学性能和使用寿命产生不利影响。
因此,对轧制缺陷进行控制和质量监控是至关重要的。
二、轧制缺陷的分类1. 表面缺陷:表面缺陷是指出现在金属产品表面的各种瑕疵,如划痕、氧化、皱纹等。
这些缺陷通常是由于辊道表面不平整、杂质污染、工艺参数不当等原因引起的。
2. 内部缺陷:内部缺陷是指存在于金属产品内部的各种缺陷,如气孔、夹杂物、晶粒结构不均匀等。
这些缺陷通常是由于金属材料的不均匀性、轧制过程中的应力集中等原因引起的。
三、轧制质量控制措施1. 原材料控制:选择合适的原材料是保证轧制质量的基础。
应对原材料进行严格的检验,确保其化学成分、物理性能等符合要求,避免将有缺陷的原材料投入轧制过程。
2. 设备维护:定期对轧机设备进行维护和保养,确保其正常运行。
特别是对辊道表面进行修磨,以保证其光滑度和平整度,减少表面缺陷的产生。
3. 工艺参数控制:在轧制过程中,控制好工艺参数对于减少缺陷的产生至关重要。
例如,通过控制轧制温度、轧制速度、轧制力度等参数,可以减少内部缺陷的产生,并提高产品的力学性能。
4. 检测和分析:建立完善的检测体系,对轧制产品进行全面的检测和分析。
可以采用无损检测技术,如超声波检测、射线检测等,对内部缺陷进行检测和评估。
同时,还可以利用光学显微镜、扫描电子显微镜等设备对表面缺陷进行观察和分析。
5. 质量记录和追溯:对轧制产品的质量记录和追溯是确保产品质量的重要手段。
应建立健全的质量管理体系,对每批产品进行标识和记录,以便追溯质量问题的原因和责任。
四、案例分析以某轧钢厂为例,该厂采取了一系列的轧制缺陷控制措施,取得了显著的成效。
通过对原材料的严格筛选和检验,确保了原材料的质量;定期对轧机设备进行维护和保养,减少了设备故障的发生;同时,通过优化工艺参数,控制了轧制过程中的温度和力度,有效降低了内部缺陷的产生。
轧制缺陷及质量控制
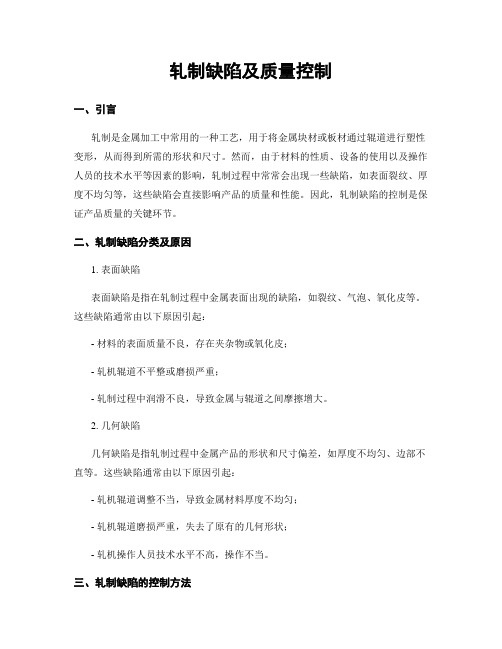
轧制缺陷及质量控制一、引言轧制是金属加工中常用的一种工艺,用于将金属块材或板材通过辊道进行塑性变形,从而得到所需的形状和尺寸。
然而,由于材料的性质、设备的使用以及操作人员的技术水平等因素的影响,轧制过程中常常会出现一些缺陷,如表面裂纹、厚度不均匀等,这些缺陷会直接影响产品的质量和性能。
因此,轧制缺陷的控制是保证产品质量的关键环节。
二、轧制缺陷分类及原因1. 表面缺陷表面缺陷是指在轧制过程中金属表面出现的缺陷,如裂纹、气泡、氧化皮等。
这些缺陷通常由以下原因引起:- 材料的表面质量不良,存在夹杂物或氧化皮;- 轧机辊道不平整或磨损严重;- 轧制过程中润滑不良,导致金属与辊道之间摩擦增大。
2. 几何缺陷几何缺陷是指轧制过程中金属产品的形状和尺寸偏差,如厚度不均匀、边部不直等。
这些缺陷通常由以下原因引起:- 轧机辊道调整不当,导致金属材料厚度不均匀;- 轧机辊道磨损严重,失去了原有的几何形状;- 轧机操作人员技术水平不高,操作不当。
三、轧制缺陷的控制方法为了控制轧制过程中的缺陷,提高产品的质量和性能,可以采取以下措施:1. 材料预处理在轧制之前,对原材料进行预处理是非常重要的。
首先,对材料的表面进行清洁,去除氧化皮和夹杂物。
其次,对材料进行退火处理,以提高其塑性和可加工性。
最后,对材料进行表面润滑处理,减少与辊道的摩擦。
2. 轧机设备维护保持轧机设备的良好状态对于控制缺陷至关重要。
定期检查和维护轧机辊道,确保其平整度和几何形状的精确性。
同时,及时更换磨损严重的辊道,以保证轧制过程的稳定性和一致性。
3. 润滑控制在轧制过程中,适当的润滑是减少摩擦、防止表面缺陷的关键。
选择合适的润滑剂,并确保润滑剂的供应充足、均匀。
同时,及时清洗辊道和润滑系统,避免杂质对产品质量的影响。
4. 操作人员培训轧制过程需要经验丰富的操作人员进行操作和监控。
因此,对轧机操作人员进行培训,提高其技术水平和操作规范性是非常重要的。
操作人员应熟悉轧机设备的使用方法和调整技巧,能够及时发现和解决轧制过程中的问题。
轧制缺陷及质量控制

轧制缺陷及质量控制一、引言轧制是金属加工过程中的重要环节,对于金属产品的质量和性能具有重要影响。
轧制缺陷是指在轧制过程中产生的各种不良现象,如裂纹、夹杂物、不均匀变形等。
为了保证轧制产品的质量,需要进行有效的质量控制和缺陷检测。
本文将详细介绍轧制缺陷的分类、检测方法以及质量控制措施。
二、轧制缺陷的分类1. 表面缺陷:包括划痕、氧化皮、凹陷等。
2. 内部缺陷:包括夹杂物、气泡、裂纹等。
3. 形状缺陷:包括厚度不均匀、宽度不均匀、边缘不平整等。
三、轧制缺陷的检测方法1. 目视检测:通过人眼观察轧制产品的表面和断面,判断是否存在明显的缺陷。
2. 磁粉检测:利用磁性粉末吸附在轧制产品表面的磁性缺陷上,通过观察磁粉的分布情况来判断是否存在缺陷。
3. 超声波检测:利用超声波的传播特性,通过检测超声波的反射和传播时间来判断轧制产品内部是否存在缺陷。
4. X射线检测:利用X射线的穿透性,通过观察X射线照片来判断轧制产品内部是否存在缺陷。
5. 红外热像检测:利用红外热像仪记录轧制产品表面的热分布情况,通过观察热图来判断是否存在缺陷。
四、轧制缺陷的质量控制措施1. 原材料控制:选择质量良好的原材料,确保原材料的化学成份和物理性能符合要求。
2. 轧制工艺控制:合理控制轧制温度、轧制速度和轧制压力,避免轧制过程中的过热和过冷现象。
3. 设备维护控制:定期对轧机设备进行检修和维护,确保设备的正常运行和精确度。
4. 操作工艺控制:培训操作人员,提高其对轧制工艺的理解和操作技能,减少人为操作引起的缺陷。
5. 缺陷修复控制:对于轧制产品中的一些小缺陷,可以采取修复措施,如打磨、热处理等,以提高产品的外观和性能。
五、案例分析以某钢厂的冷轧钢板生产线为例,该生产线采用磁粉检测和超声波检测相结合的方式进行轧制缺陷的检测。
经过对轧制产品的检测分析,发现存在少量的夹杂物和裂纹缺陷。
针对这些缺陷,钢厂采取了以下措施:首先,加强原材料的筛选和质量控制,确保原材料的纯净度和均匀性;其次,优化轧制工艺参数,减少轧制过程中的应力和变形;最后,对于存在的缺陷,进行修复处理,并进行再次检测,确保产品的质量符合要求。
轧制缺陷及质量控制

轧制缺陷及质量控制一、引言轧制是金属加工中的一种常见工艺,用于将金属坯料通过连续压制和拉伸的方式减小其截面积,从而获得所需的形状和尺寸。
然而,在轧制过程中,由于各种因素的影响,可能会浮现一些缺陷,如表面裂纹、内部气孔、夹杂物等,这些缺陷会对产品的质量和性能产生不利影响。
因此,对轧制缺陷进行有效的控制和管理是至关重要的。
二、轧制缺陷分类1. 表面缺陷:包括轧制印记、划伤、氧化皮、烧伤等。
这些缺陷通常是由于轧制辊或者其他设备的不良状况导致的,可以通过定期检查和维护设备来减少这些缺陷的发生。
2. 内部缺陷:包括气孔、夹杂物、晶界偏差等。
这些缺陷通常是由于原材料的质量问题或者轧制过程中的温度、压力等参数控制不当导致的。
通过优化原材料选择和精确控制轧制工艺参数,可以最大程度地减少内部缺陷的发生。
三、轧制缺陷的检测方法1. 目视检测:通过肉眼观察产品表面,检查是否存在明显的缺陷。
这种方法简单直观,但对于一些弱小的缺陷可能无法有效检测。
2. 超声波检测:利用超声波的传播特性,检测产品内部的缺陷。
通过超声波的反射和散射情况,可以确定缺陷的位置和大小。
这种方法对于检测内部缺陷非常有效,但需要专业的设备和技术人员进行操作。
3. X射线检测:利用X射线的穿透性,检测产品内部的缺陷。
通过检测X射线透射的强度和散射情况,可以确定缺陷的位置和性质。
这种方法对于检测较小的内部缺陷非常有效,但需要专业的设备和防护措施。
四、轧制缺陷的质量控制1. 原材料控制:选择高质量的原材料,确保其化学成份和物理性能符合要求。
通过与供应商建立稳定的合作关系,进行原材料的定期检验和评估,以确保产品质量的稳定性。
2. 工艺参数控制:根据产品要求和原材料特性,合理确定轧制过程中的温度、压力、速度等参数。
通过实时监测和调整这些参数,确保产品在轧制过程中获得良好的塑性变形和细化晶粒,减少缺陷的发生。
3. 设备维护管理:定期检查和维护轧制设备,确保其正常运行和性能稳定。
轧制缺陷及质量控制

轧制缺陷及质量控制一、介绍轧制是金属加工的一种常用方法,用于制造各种形状的金属产品。
然而,在轧制过程中,由于材料的物理性质和工艺参数的变化,可能会导致一些缺陷的产生。
为了保证轧制产品的质量,需要进行缺陷控制和质量控制。
本文将介绍轧制缺陷的常见类型以及相应的质量控制方法。
二、轧制缺陷的常见类型1. 表面缺陷表面缺陷是指轧制产品表面出现的不良状况,如划痕、氧化、斑点等。
这些缺陷可能会降低产品的外观质量,甚至影响其使用寿命。
2. 内部缺陷内部缺陷是指轧制产品内部存在的不良状况,如气孔、夹杂物、晶粒结构不均匀等。
这些缺陷可能会降低产品的强度和韧性,从而影响其机械性能。
三、质量控制方法1. 原材料选择选择高质量的原材料是保证轧制产品质量的关键。
原材料应具有良好的化学成分和物理性能,以确保轧制过程中的缺陷最小化。
2. 工艺参数控制控制轧制过程中的工艺参数对于减少缺陷的产生至关重要。
例如,控制轧制温度、轧制速度和轧制力度等参数,可以有效地减少表面缺陷和内部缺陷的产生。
3. 检测技术应用应用先进的检测技术对轧制产品进行质量检测是必不可少的。
常用的检测技术包括超声波检测、X射线检测和磁粉检测等。
这些技术可以有效地检测出轧制产品中的缺陷,并及时采取措施进行修复或淘汰。
4. 质量控制流程建立建立完善的质量控制流程是确保轧制产品质量的重要保障。
流程中应包括原材料检验、工艺参数控制、产品检测和质量记录等环节,以确保每个环节都能得到有效的控制和监督。
5. 员工培训和意识提升员工的素质和技能对于质量控制至关重要。
因此,对轧制工人进行培训,提高他们的专业知识和技能,增强他们的质量意识,可以有效地提高轧制产品的质量。
四、总结轧制缺陷及质量控制是保证轧制产品质量的重要环节。
通过选择优质原材料、控制工艺参数、应用先进的检测技术、建立质量控制流程以及提升员工的素质和意识,可以有效地减少轧制产品的缺陷,提高产品的质量和竞争力。
在今后的轧制过程中,应不断改进和完善质量控制方法,以适应市场的需求和发展。
轧制缺陷及质量控制

轧制缺陷及质量控制一、引言轧制是金属加工中常见的一种方法,用于将金属块或板材通过辊轧机进行塑性变形,以获得所需的形状和尺寸。
然而,在轧制过程中,由于材料的物理特性和加工条件的变化,可能会产生各种缺陷,如裂纹、疲劳、气泡等。
因此,实施有效的质量控制措施对于确保轧制产品的质量至关重要。
二、轧制缺陷的分类及原因1. 表面缺陷:包括划痕、氧化皮、锈蚀等。
这些缺陷可能由于材料表面的污染、辊轧机的磨损或加工条件的不当而产生。
2. 内部缺陷:包括气孔、夹杂物、裂纹等。
这些缺陷可能由于材料的不均匀性、热处理不当或轧制过程中的应力积累而产生。
三、质量控制措施1. 原材料选择:选择高质量的原材料,并进行严格的质量检查,以确保材料的均匀性和无明显缺陷。
2. 加热控制:控制轧制前的加热温度和时间,以确保材料的均匀加热,降低内部应力。
3. 辊轧机调整:定期检查和调整辊轧机的辊面形状和间隙,以确保均匀的轧制压力和变形。
4. 冷却控制:控制轧制后的冷却速度和方式,以避免快速冷却引起的应力和变形。
5. 检测技术:使用先进的检测技术,如超声波检测、X射线检测等,对轧制产品进行无损检测,及时发现和修复缺陷。
6. 质量记录和分析:建立完善的质量记录系统,记录每批轧制产品的质量数据,并进行分析,以识别潜在的质量问题和改进措施。
四、质量控制的效益1. 提高产品质量:通过有效的质量控制措施,可以减少轧制缺陷的发生,提高产品的表面光洁度和内部质量。
2. 降低生产成本:及早发现和修复轧制缺陷,可以减少废品率,降低生产成本。
3. 提高客户满意度:提供高质量的轧制产品,可以满足客户对产品质量的需求,提高客户满意度。
4. 保护品牌形象:通过实施有效的质量控制措施,可以保护企业的品牌形象,树立良好的企业信誉。
五、结论轧制缺陷及质量控制是轧制过程中不可忽视的重要环节。
通过选择优质原材料、控制加工条件、使用先进的检测技术和建立完善的质量记录系统,可以有效减少轧制缺陷的发生,提高产品质量,降低生产成本,提高客户满意度,保护企业品牌形象。
钢在轧制中常见的缺陷总结
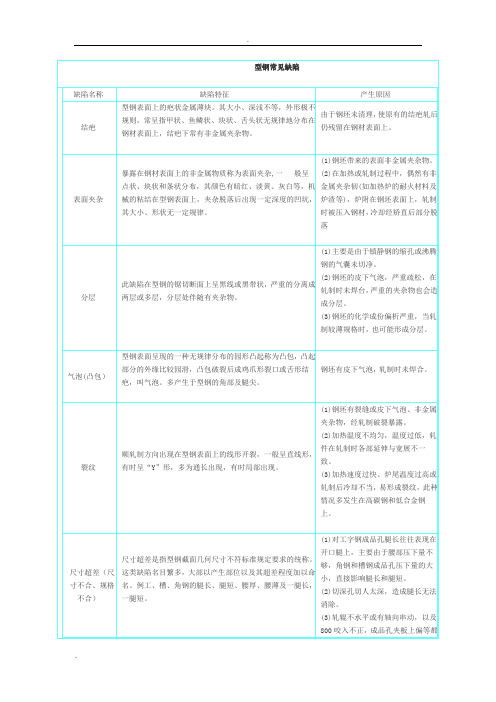
(2)钢坯温度低,造成轧制过程中的宽展大。Ow__v}l_J_
(3)入口导板安装偏斜、松动,轧件进孔不正。l7_Wdbx5x0
zh_Y]__!
轧痕(凸、凹、压印)__t"5ZYa__
在钢轨表面出现的各种不连续的伤痕叫轧痕。各种轧痕都存在热加工的痕迹、般呈周期性出现,有时无规律分布。R{6_M__(!x
(2)切深孔切人太深,造成腿长无法消除。_x^1d9_Z_
(3)轧辊不水平或有轴向串动,以及800咬入不正,成品孔夹板上偏等都会造成一腿长,一腿短等。k!_}(a0h
(4)腰的厚、薄主要是成品孔及成品前孔压下量不合理所造成。miu?X_!
_M_gi~j_.[
划伤(刮伤、擦伤、划痕)p6K___~_b
钢坯有夹杂。$_uRi/%Q9_
@zLyG#kH
Y
分层_5as5{"_l
轨腰断面中心线附近显露的金属分离层叫分层。常呈现黑线或黑带,内有大量非金属夹杂物。x>_T+k8[_n
I_aO&f<^#o
(1)主要因钢坯缩孔部分未切净。_,,M_L^ey_
(2)钢坯中心聚集大量的非金属夹杂物,在轧制中不能使金属焊合。] U }B_~Y_
dx.J_v/Mb
扭转2N.!#~_2D
钢轨上某部分相对另一部分,沿长度方向绕其轴线旋转定角度称扭转,严重时象麻花.扭转分全长和局部扭转两种。Q_{~;_4+ZD
*_#GX_~3_A
(1)卫板安装不良,使钢轨产生力偶,形成扭转。0bu!(Tpg_7
(2)轧件温度不43;Z
#X'_-/q`.
轧制缺陷及质量控制

轧制缺陷及质量控制在金属材料的生产过程中,轧制是一个非常重要的工艺环节。
然而,由于各种因素的影响,轧制过程中常常会出现各种缺陷,影响产品的质量。
因此,对轧制缺陷的控制和质量管理显得尤为重要。
本文将从轧制缺陷的种类和影响、质量控制的重要性、轧制缺陷的检测方法、质量控制的关键技术以及轧制缺陷的预防措施等五个方面进行详细介绍。
一、轧制缺陷的种类和影响1.1 表面缺陷:如划痕、氧化皮等,影响产品的外观美观度。
1.2 内部缺陷:如气孔、夹杂物等,影响产品的力学性能和使用寿命。
1.3 尺寸偏差:如厚度不均匀、宽度误差等,影响产品的加工精度和使用效果。
二、质量控制的重要性2.1 保证产品质量:通过严格的质量控制,可以确保产品达到设计要求。
2.2 提高生产效率:质量控制可以减少废品率,提高生产效率。
2.3 增强市场竞争力:高质量的产品可以提升企业的市场竞争力,赢得客户信赖。
三、轧制缺陷的检测方法3.1 目视检查:通过肉眼观察产品表面和截面,发现明显的缺陷。
3.2 无损检测:如超声波检测、射线检测等,可以检测内部缺陷。
3.3 机械性能测试:通过拉伸、硬度等测试方法,评估产品的力学性能。
四、质量控制的关键技术4.1 温度控制:控制轧制过程中的温度,避免产生过热或过冷导致的缺陷。
4.2 压力控制:调整轧制机的压力,确保产品的尺寸和形状符合要求。
4.3 润滑控制:保证轧制过程中的润滑效果良好,减少摩擦损失和表面缺陷。
五、轧制缺陷的预防措施5.1 定期维护设备:保持轧机设备的良好状态,减少因设备故障引起的缺陷。
5.2 严格控制原材料质量:选择优质原材料,减少夹杂物的含量,降低产品内部缺陷的风险。
5.3 培训员工技能:提高员工的操作技能和质量意识,减少人为因素导致的缺陷。
综上所述,轧制缺陷的控制和质量管理对于金属材料生产至关重要。
只有通过科学的方法和有效的措施,才能确保产品质量达到要求,提升企业的竞争力和市场地位。
希望本文的介绍能够帮助读者更好地了解轧制缺陷及质量控制的相关知识。
轧制缺陷及质量控制
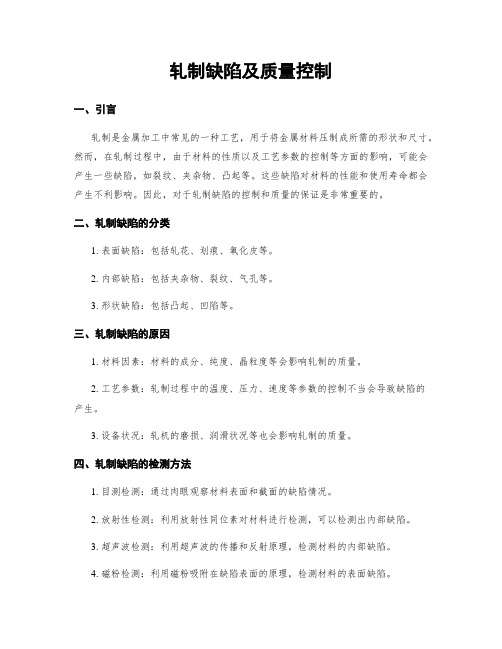
轧制缺陷及质量控制一、引言轧制是金属加工中常见的一种工艺,用于将金属材料压制成所需的形状和尺寸。
然而,在轧制过程中,由于材料的性质以及工艺参数的控制等方面的影响,可能会产生一些缺陷,如裂纹、夹杂物、凸起等。
这些缺陷对材料的性能和使用寿命都会产生不利影响。
因此,对于轧制缺陷的控制和质量的保证是非常重要的。
二、轧制缺陷的分类1. 表面缺陷:包括轧花、划痕、氧化皮等。
2. 内部缺陷:包括夹杂物、裂纹、气孔等。
3. 形状缺陷:包括凸起、凹陷等。
三、轧制缺陷的原因1. 材料因素:材料的成分、纯度、晶粒度等会影响轧制的质量。
2. 工艺参数:轧制过程中的温度、压力、速度等参数的控制不当会导致缺陷的产生。
3. 设备状况:轧机的磨损、润滑状况等也会影响轧制的质量。
四、轧制缺陷的检测方法1. 目测检测:通过肉眼观察材料表面和截面的缺陷情况。
2. 放射性检测:利用放射性同位素对材料进行检测,可以检测出内部缺陷。
3. 超声波检测:利用超声波的传播和反射原理,检测材料的内部缺陷。
4. 磁粉检测:利用磁粉吸附在缺陷表面的原理,检测材料的表面缺陷。
5. 热红外检测:利用红外辐射的原理,检测材料的缺陷情况。
五、轧制缺陷的质量控制1. 优化工艺参数:通过对轧制过程中的温度、压力、速度等参数的调整,减少缺陷的产生。
2. 提高材料质量:选择高纯度、均匀性好的材料,可以降低缺陷的发生率。
3. 定期设备维护:对轧机进行定期的检修和维护,保证设备的正常运行。
4. 强化人员培训:对操作人员进行培训,提高其对轧制缺陷的识别和处理能力。
5. 建立完善的质量管理体系:制定相应的标准和规范,对轧制缺陷进行严格的控制和管理。
六、案例分析以某钢铁公司为例,该公司通过优化工艺参数,提高材料质量,并加强设备维护,成功降低了轧制缺陷的发生率。
同时,该公司还建立了完善的质量管理体系,对轧制缺陷进行了严格的控制和管理。
经过一段时间的实施,该公司的产品质量得到了显著提升,客户的满意度也大幅度提高。
轧制缺陷及质量控制

轧制缺陷及质量控制一、引言轧制是金属加工中的一种重要工艺,用于将金属坯料通过辊道压制成所需的形状和尺寸。
然而,在轧制过程中,可能会浮现一些缺陷,如裂纹、夹杂物和凹坑等,这些缺陷会降低产品的质量和性能。
因此,进行轧制缺陷的控制和质量管理是至关重要的。
二、轧制缺陷的分类1. 裂纹:轧制过程中,由于应力集中或者金属内部的缺陷,可能会导致裂纹的产生。
裂纹可以分为表面裂纹和内部裂纹两种类型。
2. 夹杂物:夹杂物是指金属中的非金属杂质,如氧化物、硫化物和氮化物等。
夹杂物会影响金属的强度和韧性。
3. 凹坑:凹坑是指金属表面的凹陷,可能是由于辊道表面的磨损或者金属表面的缺陷导致的。
三、轧制缺陷的原因分析1. 材料因素:材料的成份和内部缺陷会直接影响轧制过程中的缺陷产生。
例如,材料中含有大量夹杂物或者过多的硬质相,会增加裂纹和凹坑的产生风险。
2. 设备因素:轧制设备的质量和性能直接影响轧制过程中的缺陷控制。
例如,辊道的磨损和不平整会导致凹坑的产生,辊道的间隙不合适会增加夹杂物的产生风险。
3. 工艺因素:轧制工艺参数的选择和控制对缺陷的产生和控制起着重要作用。
例如,轧制温度、轧制速度和轧制压力的选择需要根据材料的性质和要求进行合理调整。
四、轧制缺陷的控制措施1. 材料控制:选择合适的原材料,并进行必要的检测和筛选,以确保材料中的夹杂物和缺陷控制在合理范围内。
2. 设备维护:定期检查和维护轧制设备,确保辊道的平整度和间隙的合适性,减少凹坑和夹杂物的产生。
3. 工艺优化:根据不同材料的特性和产品的要求,优化轧制工艺参数,如温度、速度和压力等,以减少裂纹和凹坑的产生。
4. 检测技术:采用先进的无损检测技术,如超声波检测和磁粉探伤等,对轧制产品进行全面的检测,及时发现和排除缺陷。
5. 质量管理:建立完善的质量管理体系,包括质量检验、质量控制和质量反馈等环节,确保轧制产品的质量稳定和持续改进。
五、轧制缺陷的质量控制1. 检测方法:采用适当的检测方法对轧制产品进行质量控制,如外观检查、尺寸测量和物理性能测试等。
钢在轧制中常见的缺陷总结
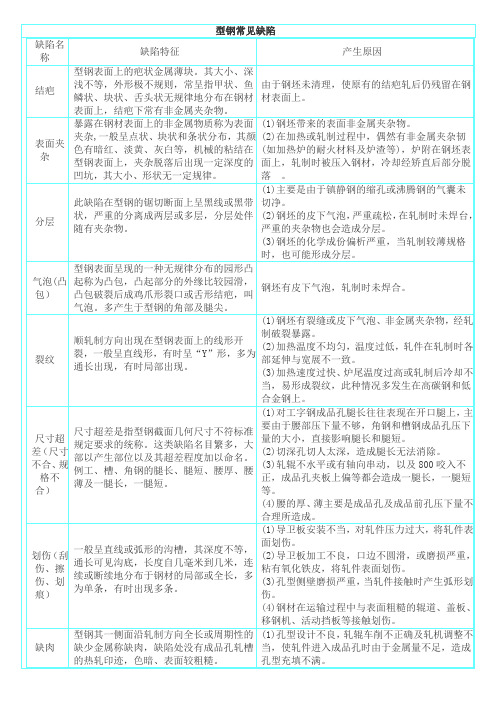
开裂_{V_8uk_ $
钢坯在轧制中,自动裂开称开裂。工业轨尤为多见。_\#_F>_R,
sN_M_F(TY
(1)由于钢锭中心部位集中大量气体和非囊属夹杂物所致。`-?`H>+OG_
(2)由于钢“内裂”或“穿孔”所致。ZQ_-6n1O_
8~B___LT_Z
过烧G_ 6x__N R
因钢坯加热不当,钢轨表面出现的横向粗糙裂口叫“过烧”。裂口多出现在轨头和轨底侧边,金相观察裂口处金属晶粒粗大。7Rc>LI*'
(1)轧机操作调整不当或成品前孔磨损严重,造成成品孔压下量过大。=c%gV]>_G
(2)钢坯温度低,造成轧制过程中的宽展大。Ow__v}l_J_
(3)入口导板安装偏斜、松动,轧件进孔不正。l7_Wdbx5x0
zh_Y]__!
轧痕(凸、凹、压印)__t"5ZYa__
在钢轨表面出现的各种不连续的伤痕叫轧痕。各种轧痕都存在热加工的痕迹、般呈周期性出现,有时无规律分布。R{6_M__(!x
一般呈直线或弧形的沟槽,其深度不等,通长可见沟底,长度自几毫米到几米,连续或断续地分布于钢材的局部或全长,多为单条,有时出现多条。xr7}@rq"U<
)#_cZ_& O_
(1)导卫板安装不当,对轧件压力过大,将轧件表面划伤。F8"J_<_VJ7
(2)导卫板加工不良,口边不圆滑,或磨损严重,粘有氧化铁皮,将轧件表面划伤。!'p
(1)钢坯带来的表面非金属夹杂物。1_vdG \$_
(2)在加热或轧制过程中,偶然有非金属夹杂韧(如加热炉的耐火材料及炉渣等),炉附在钢坯表面上,轧制时被压入钢材,冷却经矫直后部分脱落_U#|6n ,_。cp_6I]#_X
轧制缺陷及质量控制
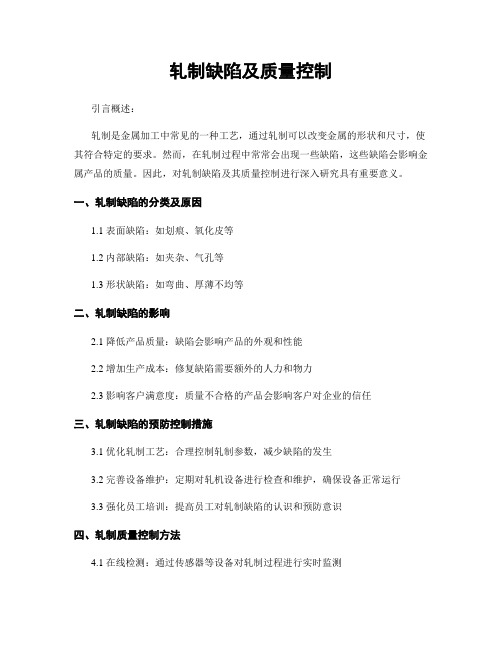
轧制缺陷及质量控制
引言概述:
轧制是金属加工中常见的一种工艺,通过轧制可以改变金属的形状和尺寸,使其符合特定的要求。
然而,在轧制过程中常常会出现一些缺陷,这些缺陷会影响金属产品的质量。
因此,对轧制缺陷及其质量控制进行深入研究具有重要意义。
一、轧制缺陷的分类及原因
1.1 表面缺陷:如划痕、氧化皮等
1.2 内部缺陷:如夹杂、气孔等
1.3 形状缺陷:如弯曲、厚薄不均等
二、轧制缺陷的影响
2.1 降低产品质量:缺陷会影响产品的外观和性能
2.2 增加生产成本:修复缺陷需要额外的人力和物力
2.3 影响客户满意度:质量不合格的产品会影响客户对企业的信任
三、轧制缺陷的预防控制措施
3.1 优化轧制工艺:合理控制轧制参数,减少缺陷的发生
3.2 完善设备维护:定期对轧机设备进行检查和维护,确保设备正常运行
3.3 强化员工培训:提高员工对轧制缺陷的认识和预防意识
四、轧制质量控制方法
4.1 在线检测:通过传感器等设备对轧制过程进行实时监测
4.2 人工检验:对轧制后的产品进行目视检查和尺寸测量
4.3 抽样检测:定期抽取产品进行全面检验,确保产品质量符合标准
五、轧制缺陷处理方法
5.1 修磨:对表面缺陷进行修磨处理,恢复产品表面光洁度
5.2 热处理:对内部缺陷进行热处理,消除缺陷并提高产品性能
5.3 重新轧制:对形状缺陷的产品进行重新轧制,确保产品尺寸和形状符合要求
总结:
轧制缺陷及质量控制是金属加工中一个重要的环节,只有通过科学的方法对轧制缺陷进行预防和控制,才能生产出高质量的金属产品,提高企业的竞争力和市场占有率。
希望本文的内容能够对相关行业的从业人员有所帮助。
轧制缺陷及质量控制
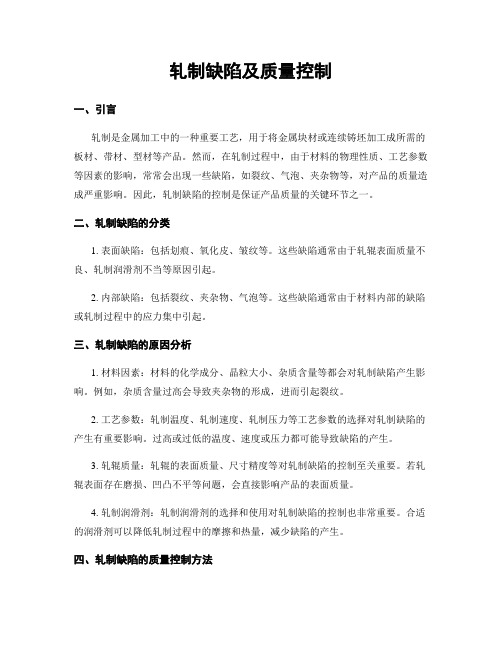
轧制缺陷及质量控制一、引言轧制是金属加工中的一种重要工艺,用于将金属块材或连续铸坯加工成所需的板材、带材、型材等产品。
然而,在轧制过程中,由于材料的物理性质、工艺参数等因素的影响,常常会出现一些缺陷,如裂纹、气泡、夹杂物等,对产品的质量造成严重影响。
因此,轧制缺陷的控制是保证产品质量的关键环节之一。
二、轧制缺陷的分类1. 表面缺陷:包括划痕、氧化皮、皱纹等。
这些缺陷通常由于轧辊表面质量不良、轧制润滑剂不当等原因引起。
2. 内部缺陷:包括裂纹、夹杂物、气泡等。
这些缺陷通常由于材料内部的缺陷或轧制过程中的应力集中引起。
三、轧制缺陷的原因分析1. 材料因素:材料的化学成分、晶粒大小、杂质含量等都会对轧制缺陷产生影响。
例如,杂质含量过高会导致夹杂物的形成,进而引起裂纹。
2. 工艺参数:轧制温度、轧制速度、轧制压力等工艺参数的选择对轧制缺陷的产生有重要影响。
过高或过低的温度、速度或压力都可能导致缺陷的产生。
3. 轧辊质量:轧辊的表面质量、尺寸精度等对轧制缺陷的控制至关重要。
若轧辊表面存在磨损、凹凸不平等问题,会直接影响产品的表面质量。
4. 轧制润滑剂:轧制润滑剂的选择和使用对轧制缺陷的控制也非常重要。
合适的润滑剂可以降低轧制过程中的摩擦和热量,减少缺陷的产生。
四、轧制缺陷的质量控制方法1. 材料筛选:选择质量良好的原材料,确保化学成分均匀、杂质含量低、晶粒细小等,以减少缺陷的产生。
2. 工艺优化:通过合理调整轧制温度、速度、压力等工艺参数,降低应力集中,减少缺陷的产生。
3. 轧辊维护:定期检查和维护轧辊,保证其表面质量和尺寸精度,减少轧制缺陷的发生。
4. 润滑剂选择:选择合适的润滑剂,并根据轧制工艺要求进行正确的使用,以降低摩擦和热量,减少缺陷的产生。
5. 在线监测:利用先进的无损检测技术,对轧制过程进行实时监测,及时发现并修复缺陷,确保产品质量。
五、轧制缺陷的质量控制实践案例一家钢铁企业在轧制过程中,经常出现表面划痕和内部裂纹的问题,严重影响了产品的质量和市场竞争力。
- 1、下载文档前请自行甄别文档内容的完整性,平台不提供额外的编辑、内容补充、找答案等附加服务。
- 2、"仅部分预览"的文档,不可在线预览部分如存在完整性等问题,可反馈申请退款(可完整预览的文档不适用该条件!)。
- 3、如文档侵犯您的权益,请联系客服反馈,我们会尽快为您处理(人工客服工作时间:9:00-18:30)。
型钢轧制故障分析
卡钢是指轧件在正常运行过程中,受周围环境影响卡在轧制线上,而不能向下游方向轧制的一种故障现象。
产生的主要原因有:来料轧件尺寸过大、形状失真;本道次压下量过大;入口导卫装置不正、过紧、过松或滚动体损失;出口导卫歪斜或在导卫内留有异物;轧件温度低;机电设备故障等。
缠辊是指轧件意外地、毫无规则地沿轧制圆周方向缠绕在轧辊身上的一种轧制故障现象。
产生的主要原因是:上下辊的辊径差较大,造成较大的上压力或下压力;出口导卫装置与轧辊接触部位间隙过大;入口与出口导卫装置错位安装;轧件意外进入未安装出口导卫装置的孔型中等。
打滑一般是指轧件头部已接触到轧辊有时甚至已局部进入变形区,但轧件最终未能被咬入轧机形成正常轧制的一种故障现象。
产生的主要原因有:来料过大,造成实际的咬入角超过允许的咬入角;在咬入角偏大的情况下,轧件断面小,轧机间距大,致使轧件无压下量;轧制线不正,对轧件运行产生阻力等。
拉钢是指连续轧制过程中,下游机架的金属秒流量明显大于上游相邻机架的金属秒流量而对轧件产生较大的拉应力,使轧件中部断面积缩小甚至将其拉断的一种故障现象。
堆钢是指连续轧制过程中,下游机架的金属秒流量明显
小于上游相邻机架的金属秒流量而在两机架间产生大量金属堆积,使轧件稳定性遭到破坏,甚至造成轧制废品的一种故障现象。
拉钢与堆钢产生的原因基本相同,主要有以下几个方面:轧制速度设定有误;速度与轧制断面不匹配;电气系统有波动;轧件温度差过大等。
对于以上轧制故障的处理,首先要分析清楚造成故障的具体原因,采取有针对性的措施。
有的时候一种故障的产生,可能同时受到几种因素的影响,要注意综合分析,切忌片面独行、主观臆断。
轧制过程中非扭转翻钢道次的轧件发生扭转是应当尽力避免的,因为它是一种不稳定因素,对轧制工艺和产品质量都有不良影响。
产生这种现象的主要原因有:错辊造成上下轧槽未对正,使轧件自然产生力偶;上一翻钢道次的轧件进入本架轧机时的扭转翻钢角度过大或过小;导卫安装不良,如横梁安装倾斜、与轧辊轴线不平行及滚动导卫的孔型错位等;轧件在孔型内充满度不够或过充满;发生扭转的道次压下量偏小等。