高锰钢及高铬铸铁热处理工艺曲线
铸钢件常见热处理
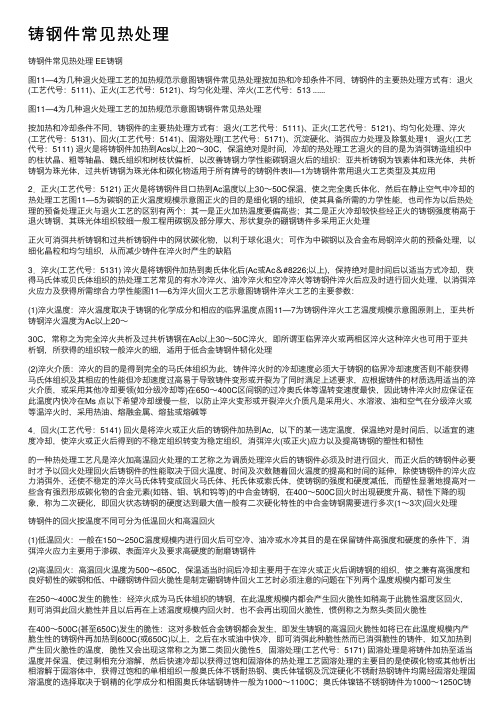
铸钢件常见热处理铸钢件常见热处理 EE铸钢图11—4为⼏种退⽕处理⼯艺的加热规范⽰意图铸钢件常见热处理按加热和冷却条件不同,铸钢件的主要热处理⽅式有:退⽕(⼯艺代号:5111)、正⽕(⼯艺代号:5121)、均匀化处理、淬⽕(⼯艺代号:513 ......图11—4为⼏种退⽕处理⼯艺的加热规范⽰意图铸钢件常见热处理按加热和冷却条件不同,铸钢件的主要热处理⽅式有:退⽕(⼯艺代号:5111)、正⽕(⼯艺代号:5121)、均匀化处理、淬⽕(⼯艺代号:5131)、回⽕(⼯艺代号:5141)、固溶处理(⼯艺代号:5171)、沉淀硬化、消弭应⼒处理及除氢处理1.退⽕(⼯艺代号:5111) 退⽕是将铸钢件加热到Acs以上20~30C,保温绝对是时间,冷却的热处理⼯艺退⽕的⽬的是为消弭铸造组织中的柱状晶、粗等轴晶、魏⽒组织和树枝状偏析,以改善铸钢⼒学性能碳钢退⽕后的组织:亚共析铸钢为铁素体和珠光体,共析铸钢为珠光体,过共析铸钢为珠光体和碳化物适⽤于所有牌号的铸钢件表ll—1为铸钢件常⽤退⽕⼯艺类型及其应⽤2.正⽕(⼯艺代号:5121) 正⽕是将铸钢件⽬⼝热到Ac温度以上30~50C保温,使之完全奥⽒体化,然后在静⽌空⽓中冷却的热处理⼯艺图11—5为碳钢的正⽕温度规模⽰意图正⽕的⽬的是细化钢的组织,使其具备所需的⼒学性能,也司作为以后热处理的预备处理正⽕与退⽕⼯艺的区别有两个:其⼀是正⽕加热温度要偏⾼些;其⼆是正⽕冷却较快些经正⽕的铸钢强度稍⾼于退⽕铸钢,其珠光体组织较细⼀般⼯程⽤碳钢及部分厚⼤、形状复杂的硼钢铸件多采⽤正⽕处理正⽕可消弭共析铸钢和过共析铸钢件中的⽹状碳化物,以利于球化退⽕;可作为中碳钢以及合⾦布局钢淬⽕前的预备处理,以细化晶粒和均匀组织,从⽽减少铸件在淬⽕时产⽣的缺陷3.淬⽕(⼯艺代号:5131) 淬⽕是将铸钢件加热到奥⽒体化后(Ac或Ac•以上),保持绝对是时间后以适当⽅式冷却,获得马⽒体或贝⽒体组织的热处理⼯艺常见的有⽔冷淬⽕、油冷淬⽕和空冷淬⽕等铸钢件淬⽕后应及时进⾏回⽕处理,以消弭淬⽕应⼒及获得所需综合⼒学性能图11—6为淬⽕回⽕⼯艺⽰意图铸钢件淬⽕⼯艺的主要参数:(1)淬⽕温度:淬⽕温度取决于铸钢的化学成分和相应的临界温度点图11—7为铸钢件淬⽕⼯艺温度规模⽰意图原则上,亚共析铸钢淬⽕温度为Ac以上20~30C,常称之为完全淬⽕共析及过共析铸钢在Ac以上30~50C淬⽕,即所谓亚临界淬⽕或两相区淬⽕这种淬⽕也可⽤于亚共析钢,所获得的组织较⼀般淬⽕的细,适⽤于低合⾦铸钢件韧化处理(2)淬⽕介质:淬⽕的⽬的是得到完全的马⽒体组织为此,铸件淬⽕时的冷却速度必须⼤于铸钢的临界冷却速度否则不能获得马⽒体组织及其相应的性能但冷却速度过⾼易于导致铸件变形或开裂为了同时满⾜上述要求,应根据铸件的材质选⽤适当的淬⽕介质,或采⽤其他冷却要领(如分级冷却等)在650~400C区间钢的过冷奥⽒体等温转变速度最快,因此铸件淬⽕时应保证在此温度内快冷在Ms 点以下希望冷却缓慢⼀些,以防⽌淬⽕变形或开裂淬⽕介质凡是采⽤⽕、⽔溶液、油和空⽓在分级淬⽕或等温淬⽕时,采⽤热油、熔融⾦属、熔盐或熔碱等4.回⽕(⼯艺代号:5141) 回⽕是将淬⽕或正⽕后的铸钢件加热到Ac,以下的某⼀选定温度,保温绝对是时间后,以适宜的速度冷却,使淬⽕或正⽕后得到的不稳定组织转变为稳定组织,消弭淬⽕(或正⽕)应⼒以及提⾼铸钢的塑性和韧性的⼀种热处理⼯艺凡是淬⽕加⾼温回⽕处理的⼯艺称之为调质处理淬⽕后的铸钢件必须及时进⾏回⽕,⽽正⽕后的铸钢件必要时才予以回⽕处理回⽕后铸钢件的性能取决于回⽕温度、时间及次数随着回⽕温度的提⾼和时间的延伸,除使铸钢件的淬⽕应⼒消弭外,还使不稳定的淬⽕马⽒体转变成回⽕马⽒体、托⽒体或索⽒体,使铸钢的强度和硬度减低,⽽塑性显著地提⾼对⼀些含有强烈形成碳化物的合⾦元素(如铬、钼、钒和钨等)的中合⾦铸钢,在400~500C回⽕时出现硬度升⾼、韧性下降的现象,称为⼆次硬化,即回⽕状态铸钢的硬度达到最⼤值⼀般有⼆次硬化特性的中合⾦铸钢需要进⾏多次(1~3次)回⽕处理铸钢件的回⽕按温度不同可分为低温回⽕和⾼温回⽕(1)低温回⽕:⼀般在150~250C温度规模内进⾏回⽕后可空冷、油冷或⽔冷其⽬的是在保留铸件⾼强度和硬度的条件下,消弭淬⽕应⼒主要⽤于渗碳、表⾯淬⽕及要求⾼硬度的耐磨铸钢件(2)⾼温回⽕:⾼温回⽕温度为500~650C,保温适当时间后冷却主要⽤于在淬⽕或正⽕后调铸钢的组织,使之兼有⾼强度和良好韧性的碳钢和低、中硼钢铸件回⽕脆性是制定硼钢铸件回⽕⼯艺时必须注意的问题在下列两个温度规模内都可发⽣在250~400C发⽣的脆性:经淬⽕成为马⽒体组织的铸钢,在此温度规模内都会产⽣回⽕脆性如稍⾼于此脆性温度区回⽕,则可消弭此回⽕脆性并且以后再在上述温度规模内回⽕时,也不会再出现回⽕脆性,惯例称之为熬头类回⽕脆性在400~500C(甚⾄650C)发⽣的脆性:这对多数低合⾦铸钢都会发⽣,即发⽣铸钢的⾼温回⽕脆性如将已在此温度规模内产脆⽣性的铸钢件再加热到600C(或650C)以上,之后在⽔或油中快冷,即可消弭此种脆性然⽽已消弭脆性的铸件,如⼜加热到产⽣回⽕脆性的温度,脆性⼜会出现这常称之为第⼆类回⽕脆性5.固溶处理(⼯艺代号:5171) 固溶处理是将铸件加热⾄适当温度并保温,使过剩相充分溶解,然后快速冷却以获得过饱和固溶体的热处理⼯艺固溶处理的主要⽬的是使碳化物或其他析出相溶解于固溶体中,获得过饱和的单相组织⼀般奥⽒体不锈耐热钢、奥⽒体锰钢及沉淀硬化不锈耐热钢铸件均需经固溶处理固溶温度的选择取决于钢精的化学成分和相图奥⽒体锰钢铸件⼀般为1000~1100C;奥⽒体镍铬不锈钢铸件为1000~1250C铸钢中含碳量越⾼,难熔合⾦元素越多,则其固溶温度应越⾼含铜的沉淀硬化铸钢,由于铸态有硬质富铜相在冷却过程中沉淀,致使铸钢件硬度升⾼为软化组织、改善加⼯性能,铸钢件需经固溶处理其固溶温度为900~950C经快冷后可得到铜的质量分数为1.0%~1.5%的过饱和单相组织6.沉淀硬化处理(时效处理) 铸件经固溶处理或淬⽕后,在室温或⾼于室温的适当温度保温,在过饱和固溶体中形成溶质原⼦偏聚区和(或)析出弥散漫衍的强化相⽽使⾦属硬化的处理称为沉淀硬化处理(或时效处理)在⾼于室温下进⾏的称为⼈⼯时效其实质是:在较⾼的温度下,⾃过饱和固溶体中析出碳化物、氮化物、⾦属间化合物及其他不稳定的中间相,并弥散漫衍于基体中,故⽽使铸钢的综合⼒学性能和硬度提⾼时效处理的温度直接影响铸钢件的最终性能时效温度过低,沉淀硬化相析出缓慢;温度过⾼,则因析出相的堆积长⼤导致过时效,⽽得不到最佳的性能所以应根据铸钢件的牌号及规定的性能要求选⽤时效温度奥⽒体耐热铸钢时效温度⼀般为550~850C,⾼强度沉淀硬化铸钢为500C,时间为1~4h 含铜的低硼钢和奥⽒体耐热钢铸件以及低合⾦的奥⽒体锰钢铸件多采⽤时效处理图11-8为截⾯25mm试样的时效效果7.消弭应⼒处理其⽬的是消弭铸造应⼒、淬⽕应⼒和机械加⼯形成的应⼒,稳定尺⼨⼀般加热到Ac,以下100~200C保温绝对是时间,随炉慢冷铸件的组织没有变化碳钢、低硼钢或⾼硼钢铸件都可以进⾏处理8.除氢处理⽬的是去除氢⽓,提⾼铸钢的塑性加热到l70~200C或280~320C,长时间保温进⾏处理没有组织变化主要⽤于易于产⽣氢脆倾向的低硼钢铸件⼆、钢的整体热处理整体热处理是对⼯件整体进⾏穿透加热常⽤的要领有退⽕、正⽕、淬⽕和回⽕1.钢的退⽕与正⽕(1)退⽕与正⽕的⽬的在呆板零件和⼯⽣产模型等⼯件的加⼯制造过程中,退⽕和正⽕经常作为预备热处理⼯序,安排在铸、锻、焊⼯序之后、切削(粗)加⼯之前,⽤以消弭前⼀⼯序所带来的某些缺陷,为随后的⼯序做筹办例如,在铸造或锻造等热加⼯以后,钢件中不但存在残存应⼒,并且组织粗⼤不均匀,成分也有偏析,这样的钢件⼒学性能差劲,淬⽕时也容易造成变形和开裂⼜如,在铸造或锻造等热加⼯以后,钢件硬度经常偏低或偏⾼,并且不均匀,严重影响切削加⼯性能退⽕和正⽕的主要⽬的有:①调整硬度以便进⾏切削加⼯;②消弭残存应⼒,防⽌钢件的变形、开裂;③细化晶粒,改善组织以提⾼钢的⼒学性能;④为最终热处理作好组织筹办(2)退⽕⼯艺及应⽤钢的退⽕是将钢件加热到适当温度,保温绝对是时间,然后缓慢冷却,以获得接近均衡组织状态的热处理⼯艺①完全退⽕与等温退⽕完全退⽕是指将钢件完全奥⽒体化(加热⾄Ac3以上30~50℃)后,随之缓慢冷却,获得接近均衡组织的退⽕⼯艺出产中为提⾼出产率,⼀般随炉冷⾄600℃摆布,将⼯件出炉空冷完全退⽕的主要缺点:完全退⽕主要⽤于:图 3-15 ⾼速⼯具钢的完全退⽕与等温退⽕⼯艺曲线为缩短完全退⽕时间,出产中常采⽤等温退⽕⼯艺,⾏将钢件加热到Ac3以上30~50℃(亚共析钢)或Acl 以上10~20℃(共析钢、过共析钢),保温适当时间后,较快冷却到珠光体转变温度区间的适当温度并保持等温,使奥⽒体转变为珠光体类组织,然后在空⽓中冷却的退⽕⼯艺等温退⽕与完全退⽕⽬的不异,但转变较易节制,所⽤时间⽐完全退⽕缩短约1/3,并可获得均匀的组织和性能特别是对某些硼钢,出产中常⽤等温退⽕来代替完全退⽕或球化退⽕图3-15为⾼速⼯具钢完全退⽕与等温退⽕的⽐较②球化退⽕是指将共析钢或过共析钢加热到Ac1点以上10~20℃,保温绝对是时间后,随炉缓冷⾄室温,或快冷到略低于Arl 温度,保温⼀段时间,然后炉空⾄600℃摆布空冷,使钢中碳化物球状化的退⽕⼯艺,如图3-16所⽰图 3-16 T10钢的球化退⽕⼯艺曲线图 3-17 粒状珠光体显微组织过共析钢及合⾦⼯具钢热加⼯后,组织中常出现粗⽚状珠光体和⽹状⼆次渗碳体,钢的硬度和脆性不仅增长,钢的切削性变差,且淬⽕时易产⽣变形和开裂为消弭上述缺陷,可采⽤球化退⽕,使珠光体中的⽚状渗碳体和钢中⽹状⼆次渗碳体均呈球(粒)状,这种在铁素体基体上弥散漫衍着球状渗碳体的复相组织,称为“球化体”,如图3-17所⽰对于存在有严重⽹状⼆次渗碳体的钢,可在球化退⽕前,进步前辈⾏⼀次正⽕近些年球化退⽕的发展与应⽤(⾃阅)③去应⼒退⽕(见书)若采⽤⾼温退⽕(如完全退⽕),也能够更彻底地消弭应⼒,但会使氧化、脱碳严重,还会产⽣⾼温变形,故为了消弭应⼒,通常为采⽤低温退⽕④廓张退⽕(均匀化退⽕)(见书)(3)正⽕⼯艺及应⽤正⽕是指将钢件加热到Ac3(亚共析钢)或Accm(过共析钢)以上30~50℃,经保温后在空⽓中冷却的热处理⼯艺正⽕与退⽕的主要区别是正⽕冷却速度稍快,得到的组织较藐⼩,强度和硬度有所提⾼,操作简便,出产周期短,成本较低低碳钢和低碳硼钢经正⽕后,可提⾼硬度,改善切削加⼯性能(170~230HBS规模内⾦属切削加⼯性较好);对于中碳布局钢制作的较重要件,可作为预先热处理,为最终热处理作好组织筹办;对于过共析钢,可消弭⽹状⼆次渗碳体为球化退⽕作好组织筹办对于使⽤性能要求不⾼的零件,以及某些⼤型或形状复杂的零件,当淬⽕有开裂危险时,可采⽤正⽕作为最终热处理⼏种退⽕与正⽕的加热温度规模及热处理⼯艺曲线,如图3-18所⽰(a)加热温度规模(b)热处理⼯艺曲线图 3-18 ⼏种退⽕与正⽕⼯艺⽰意图2.钢的淬⽕与回⽕(1)淬⽕是将钢加热⾄临界点(Ac3 或Ac1)以上,保温后以⼤于VK的速度冷却,使奥⽒体转变成马⽒体(或下贝⽒体)的热处理⼯艺淬⽕的⽬的:为了得到马⽒体组织,是钢的最主要的强化⽅式1)淬⽕⼯艺①淬⽕加热温度在选择淬⽕加热温度时,应尽量使获得的组织硬度越⼤越好;获得的晶粒越⼩越好图3-19 碳钢淬⽕加热温度规模⽰意图对于亚共析钢,淬⽕温度⼀般为Ac3以上30~50℃,淬⽕后得到均匀藐⼩的M 和少数残存奥⽒体,若淬⽕温度过低,则淬⽕后组织中将会有F,使钢的强度、硬度减低;若加热温度跨越 Ac3以上(30~50℃),奥⽒体晶粒粗化,淬⽕后得到粗⼤的M,钢的⼒学性能变差,且淬⽕应⼒增⼤,易导致变形和开裂对于共析钢或过共析钢,淬⽕加热温度为Ac1以上30~50℃,淬⽕后得到藐⼩的马⽒体和少数残留奥⽒体(共析钢),或藐⼩的马⽒体、少数渗碳体和残留奥⽒体(过共析钢),由于渗碳体的存在,钢硬度和耐磨性提⾼若温度过⾼,如过共析钢加热到Accm以上温度,由于渗碳体全部溶⼊奥⽒体中,奥⽒体的碳的质量分数提⾼,Ms温度减低,淬⽕后残留奥⽒体量增多,钢的硬度和耐磨性减低此外,因温度⾼,奥⽒体晶粒粗化,淬⽕后得到粗⼤的马⽒体,脆性增⼤若加热温度低于Acl点,组织没发⽣相变,达不到淬⽕⽬的碳钢淬⽕加热温度规模如图3-19所⽰对于硼钢,由于⼤多数合⾦元素有阻碍奥⽒体晶粒长⼤的作⽤,故⽽淬⽕加热温度⽐碳钢⾼,使合⾦元素在奥⽒体中充分溶解和均匀化,以获得较好的淬⽕效果实际出产中,淬⽕加热温度的确定,尚需思量⼯件形状尺⼨、淬⽕冷却介质和技术要求等因素②淬⽕加热时间加热时间包孕升温⽂保温时间凡是以装炉后温度达到淬⽕加热温度所需时间为升温时间,并以此作为保温时间的开始;保温时间是指钢件烧透并完成奥⽒体均匀化所需时间加热时间受钢件成分、形状、尺⼨、装炉⽅式、装炉量、加热炉类型、炉温⽂加热介质等影响经验公式(见书)③淬⽕冷却介质钢进⾏淬⽕时冷却是最关键的⼯序,淬⽕的冷却速度必须⼤于临界冷却速度,快冷才能得到马⽒体,但快冷总会带来内应⼒,往往会导致⼯件的变形和开裂那么,怎样才能既得到马⽒体⽽⼜减⼩变形和开裂呢?理想的淬⽕冷却介质如图3-20所⽰出产中,常⽤的冷却介质是⽔、油、碱或盐类⽔溶液⽔是最常⽤的冷却介质,它有较强的冷却能⼒,且成本低,但其缺点是在650~400℃规模内冷却能⼒不敷强,⽽在300~200℃规模内冷却能⼒⼜很⼤,因此常会导致淬⽕钢的内应⼒增⼤,导致⼯件变形开裂,因此,⽔在出产中主要⽤于形状简略、截⾯较⼤的碳钢零件的淬⽕图3-20 理想淬⽕冷却速度曲线如在⽔中加⼊盐或碱类物质,能增长在650~400℃规模内的冷却能⼒,这对保证⼯件,特别是碳钢的淬硬是⾮常有利的,但盐⽔仍具备清⽔的缺点,即在300~200℃规模内冷却能⼒很⼤,⼯件变形开裂倾向很⼤常⽤的盐⽔液体浓度为10%~15%,盐⽔对⼯件有锈蚀作⽤,淬⽕后的⼯件应仔细清洗盐⽔⽐较适⽤于形状简略、硬度要求⾼⽽均匀、表⾯要求光洁、变形要求不严格的碳钢零件淬⽕常⽤的油有机油、变压器油、柴油等油在300~200℃规模内的冷却速度⽐⽔⼩,有利于减⼩⼯件变形和开裂,但油在650~400℃规模内冷却速度也⽐⽔⼩,不利于⼯件淬硬,因此只能⽤于低硼钢与硼钢的淬⽕,使⽤时油温应节制在40~100℃内为了减少⼯件淬⽕时的变形,可采⽤盐浴作为淬⽕介质,如熔化的NaN03、KN03等主要⽤于贝⽒体等温淬⽕,马⽒体分级淬⽕其特点是沸点⾼,冷却能⼒介于⽔于油之间,常⽤于处理形状复杂、尺⼨较⼩和变形要求严格的⼯件2)淬⽕要领由于⽬前还没有理想的淬⽕介质,故⽽在实际出产中应根据淬⽕件的详细情况采⽤不同的淬⽕要领,⼒求达到较好的效果常⽤的淬⽕要领如图3-21所⽰①单液淬⽕这种要领操作简略,易实现机械化凡是形状简略、尺⼨较⼤的碳钢件在⽔中淬⽕,硼钢件及尺⼨很⼩的碳钢件在油中淬⽕图 3-21 常⽤淬⽕要领⽰意图②双液淬⽕先浸⼊冷却能⼒强的介质中,在组织将要发⽣马⽒体转变时当即转⼊冷却能⼒弱的介质中冷却的淬⽕⼯艺常⽤的有先⽔后油,先⽔后空⽓等此种要领操作时,如能节制好⼯件在⽔中停留的时间,就可有效的防⽌淬⽕变形和开裂,但要求有较⾼的操作技术主要⽤于形状复杂的⾼碳钢件和尺⼨较⼤的硼钢件③马⽒体分级淬⽕是将钢件浸⼊温度稍⾼或稍低于Ms点的盐浴或碱浴中,保持适当时间,待⼯件整体达到介质温度后掏出空冷,以获得马⽒体组织的淬⽕⼯艺,此法操作⽐双介质淬⽕容易节制,能减⼩热应⼒、相变应⼒和变形,防⽌开裂主要⽤于截⾯尺⼨较⼩(直径或厚度<12mm、形状较复杂⼯件的淬⽕④等温淬⽕是将钢件加热到奥⽒体化后,随之快冷到贝⽒体转变温度区间保持等温,使奥⽒体转变为贝⽒体的淬⽕⼯艺此法淬⽕后应⼒和变形很⼩,但出产周期长,效率低主要⽤于形状复杂、尺⼨要求精确,并要求有较⾼强韧性的⼩型⼯、⽣产模型及弹簧的淬⽕⑤冷处理为了尽量减少钢中残存奥⽒体,以获得最⼤数⽬的马⽒体,可采⽤冷处理,即把钢淬冷⾄室温后,继续冷却⾄-70~-80℃(或更低温度),保持绝对是时间,使残存奥⽒体在继续冷却过程中转变为M,这样可提⾼钢的硬度和耐磨性,并稳定钢件尺⼨获得低温的办法是采⽤⼲冰(固态CO2)和酒精的混合剂或冷冻机冷却只有特殊的冷处理才置于-103℃的液化⼄烯或-192℃的液态氮中进⾏(2)淬⽕缺陷(见书)①变形与开裂;②氧化和脱碳;③过热和过烧很抱歉,因为您在⽹易相簿发布了违规信息,账号被屏蔽被屏蔽时期他⼈没有办法访问您的相簿去帮忙中⼼,了解如何重新恢复服务更多信息咨询:137********。
钢的热处理工艺和化处理

钢的热处理及金属的表面处理
( b ).固体渗碳 设备 箱式电阻炉 渗碳气氛 木炭+碳酸钠 加热温度 930 ℃±10 ℃ 加热时间 3-7h 渗层深度 0.4-1.6mm 表面碳浓度: 0.85-1.05% 渗后不能直接淬火 适合小件和单件
钢的热处理及金属的表面处理
5. 去应力退火
去应力退火
为消除铸造、锻造、焊接和机加工、冷变形等冷热加工 在工件中造成的残留内应力而进行的低温退火,称为去应力 退火。
作用和目的
减少和消除工件在铸造、锻造、焊接、切削、热处理等 加工过程中产生的残余内应力,稳定工件的尺寸,防止工件
的变形。
钢的热处理及金属的表面处理
正火的目的是使钢的组织正常化,亦称常化处理,一般用 于以下方面:
1. 改善钢的切削加工性能;
2. 消除工件的热加工缺陷; 3. 消除过共析钢的网状渗碳体,便于球化退火; 4. 代替调质处理作为最终热处理,提高加工效率。
三、淬火
速冷却至室温的热处理工艺。
钢的热处理及金属的表面处理
淬火就是把钢件加热到Ac3或Ac1以上温度,经过保温后
钢的热处理及金属的表面处理
二、正火
正火
钢材或钢件加热到Ac3(对于亚共析钢)和Accm(对于过共析
钢)以上30 ℃~50 ℃, 保温适当时间后, 在自由流动的空气 中均匀冷却的热处理称为正火。
正火后的组织
亚共析钢为F+S
共析钢为S
过共析钢为S+Fe3CII
钢的热处理及金属的表面处理
正火的目的:
钢的热处理及金属的表面处理
(一)等温冷却组织转变(以共析钢为例)
钢的热处理及金属的表面处理
1. 高温组织转变 2. 中温组织转变 3. 低温组织转变
热处理工艺卡
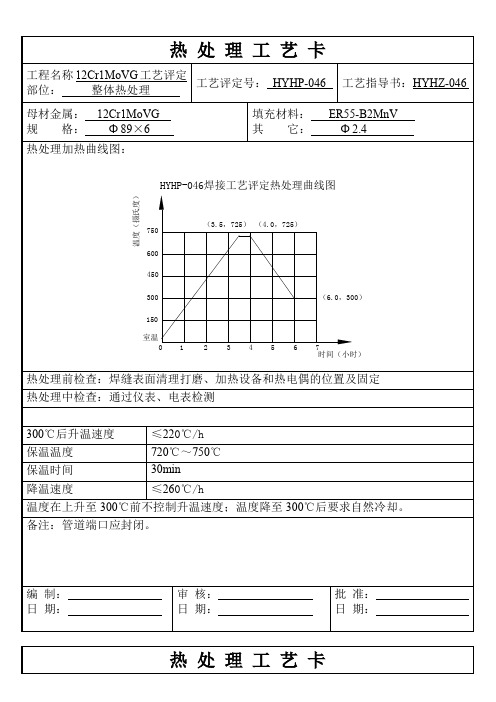
母材金属:12Cr1MoVG
厚度:Φ219×22
填充材料:ER55-B2MnV/E5515-B2-V
其它:Φ2.4 /Φ3.2
热处理加热曲线图:
热处理前检查:焊缝表面清理打磨、加热设备和热电偶的位置及固定
热处理中检查:通过仪表、电表检测
300℃后升温速度
≤220℃/h
保温温度
300℃后升温速度
≤220℃/h
保温温度
720℃~750℃
保温时间
30min
降温速度
≤260℃/h
温度在上升至300℃前不控制升温速度;温度降至300℃后要求自然冷却。:
审核:
日期:
批准:
日期:
热处理工艺卡
工程名称12Cr1MoVG工艺评定
部位:整体热处理
工艺评定号:HYHP-047
720℃~750℃
保温时间
80min
降温速度
≤260℃/h
温度在上升至300℃前不控制升温速度;温度降至300℃后要求自然冷却。
备注:管道端口应封闭。
编制:
日期:
审核:
日期:
批准:
日期:
热处理工艺卡
工程名称12Cr1MoVG工艺评定
部位:整体热处理
工艺评定号:HYHP-046
工艺指导书:HYHZ-046
母材金属:12Cr1MoVG
规格:Φ89×6
填充材料:ER55-B2MnV
其它:Φ2.4
热处理加热曲线图:
热处理前检查:焊缝表面清理打磨、加热设备和热电偶的位置及固定
热处理中检查:通过仪表、电表检测
合金高铬铸铁的热处理

摘要本文以合金高铬铸铁(KMTBCr8)板材(5.6mm5.6mm53mm)为试验材料,进行不同热处理后不同腐蚀介质、不同ph、不同砂浆配比、不同转速下的腐蚀磨损试验。
利用光学显微镜对试样进行基体组织分析、显微组织分析。
研究不同热处理工艺及不同腐蚀磨损条件对KMT BCr8腐蚀磨损性能的影响,并分析不同热处理工艺及腐蚀条件下KMTBCr8腐蚀磨损的规律[1]。
研究发现,KMTBCr8的热处理工艺对其腐蚀磨损性能有影响,铸态的KMTBCr8耐腐蚀磨损性能最好;相同回火温度下,淬火热处理温度越高,KMTBCr8耐腐蚀性越差;相同淬火温度下,KMTBCr8试样低温回火的耐腐蚀磨损性能优于三次高温回火。
在其他热处理工艺及腐蚀条件都相同时,中性砂浆中KMTBCr8的表面锈蚀最严重,碱性砂浆次之,酸性砂浆中KMTBCr8的锈蚀最轻。
在相同腐蚀磨损条件下,高转速比低转速的失重量要多。
关键词:合金高铬铸铁;热处理;腐蚀磨损;组织形貌AbstractThis paper, taking high chromium cast iron alloy plate (5.6mm x 5.6mm x 53mm) as experiment material, respectively in different heat treatment, different corrosive medium, different ph, different cement mortar ratio, different speed of the corrosion wear test . Using Zeiss electron modern analysis methods, the research discusses the heat treatment process and different corrosion wear conditions affect the performance of KMTBCr8 corrosion and wear, and analyze the different heat treatment process and the abrasion performance of the corrosion conditions and corrosion KMTBCr8 relationship; For the material in the actual system theoretical foundation for the safe use. The main research contents include : matrix organization analysis, the morphology and microstructure analysis.On the basis of the successful preparation of sample heat treatment, firstof all the groups were compared before and after heat treatment. Then to study KMTBCr8 by weight-loss method in acid and alkali neutral mortar dynamic law of corrosion wear characteristics. By comparing the samples before and after corrosion wear weight difference, analyzing corrosion wear data record, a series of XY scatterplot smooth.The study found that KMTBCr8 heat treatment process on the corrosion and wear properties of influential, the higher the heat treatment temperature, corrosion resistance, the worse, the more serious the surface rust. In the neutral mortar KMTBCr8 surface corrosion is more serious. Under the same corrosion wear time, high speed than the weightlessness rate of those low speed.In neutral mortar, when KMTBCr8 after heat treatment, the neutral mortar corrosion resistance than the as-cast the most neutral mortar with poor corrosion resistance. Followed by alkaline cement mortar, the poor corrosion resistance than as-cast. Finally is acidic slurry, and its poor corrosion resistance than the as-cast least. You can see that the as-cast KMTBCr8 most resistant to corrosion.Keywords: high chromium cast iron; Heat treatment; Corrosion and wear; The rupture目录摘要 PAGEREF _Toc21099 IAbstract II第1章绪论 11.1引言 11.2铸铁概述 11.2.1 铸铁及其应用 11.2.2 铸铁的金相组织和力学性能的特点 41.3金属的腐蚀磨损 31.3.1 金属的腐蚀磨损概述 41.3.2 腐蚀磨损的试验方法 41.4 铸铁的热处理 51.4.1 铸铁热处理概述 51.4.2 消除内应力处理 61.4.3 石墨化退火 61.4.4 正火 61.4.5 淬火 61.5本课题的研究目的和主要研究内容 71.5.1本课题的研究目的及意义 71.5.2本课题的主要研究内容 7第2章试验材料及具体试验方法 92.1 KMTBCr8的成分 92.2 热处理实验 92.2.1 热处理试样的制备 92.2.2 热处理工艺 92.3 金相观察 122.3.1 金相试样的制备 122.3.2 观察及照相 122.4 硬度的测定 122.5腐蚀磨损试验 132.5.1腐蚀磨损试样的制备 132.5.2腐蚀磨损试验 13第3章组织与硬度分析 143.1 金相组织分析 143.1.1原始试样组织 143.1.2淬火+回火后组织 143.2 硬度值及分析 183.2.1 KMTBCr8不同热处理状态下的硬度值 18 3.2.2 硬度分析 19第4章腐蚀磨损试验结果分析 214.1 酸性环境对高铬铸铁腐蚀性能的影响 214.1.1 腐蚀磨损试验结果 224.1.2 宏观腐蚀形貌分析 234.1.3 试验结论与分析 234.2 碱性环境对高铬铸铁腐蚀磨损性能的影响 24 4.2.1腐蚀磨损试验结果 264.2.2试验结论与分析 26结论 34致谢 35参考文献 36CONTENTSTOC \o "1-3" \h \u Abstrace(Chinese) IAbstract(English) IIChapter 1 Introduction 11.1 Introduction 11.2 Summary of cast iron 11.2.1 Cast iron and its application 11.2.2 The characteristics of the microstructure and mechanical properties of cast iron 21.3 Metal corrosion and wear 31.3.1 The corrosion of the metal wear overview 41.3.2 Corrosion wear test method 41.4 Heat treatment of cast iron 51.4.1 Summary of cast iron heat treatment 51.4.2 Eliminate internal stress 61.4.3 The graphitization annealing 61.4.4 Normalization 61.4.5 Quenching 61.5 The research purpose of this subject and the main research content 7 1.5.1 This topic research purpose and meaning 71.5.2 The main research content of this project 7Chapter 2 The test materials and the concrete testing methods 92.1 The composition of KMTBCr8 92.2 Heat treatment experiment 92.2.1 The preparation of sample heat treatment 92.2.2 Heat treatment process 92.3 Metallographic observation 122.3.1 Preparation of metallographic sample 122.3.2 Observation and photography 122.4 Determination of hardness 122.5 Corrosion wear test 132.5.1 Corrosion wear test specimen preparation 132.5.2 Corrosion wear test 13Chapter 3 Analysis metallographic and hardness 143.1 Analysis metallographic 143.1.1 The original sample organization 143.1.2 After quenching and tempering 143.2 Hardness and analysis hardness 183.2.1 KMTBCr8 hardness value under different heat treatment states 18 3.2.2 Analysis hardness 19Chapter 4 Corrosion wear test results analysis 214.1 Acidic environment impact on the corrosion performance of high chromium cast iron 214.1.1 Corrosion wear test results 234.1.2 Macroscopic corrosion morphology analysis 234.1.3 Test results and analysis 234.2 Alkaline environment effect on the properties of high chromium cast iron corrosion and wear 244.2.1 Corrosion wear test results 264.2.2 Test results and analysis 30Conclusion 34Acknowledgement 35References 36第1章绪论1.1 引言高铬铸铁在现代社会的应用很广,它有高的硬度和耐磨性,但是所有的金属材料都面对腐蚀和磨损两大难题,高铬铸铁也不例外。
高锰钢铁路辙叉热处理工艺的改进

高锰钢铁路辙叉热处理工艺的改进高锰钢铁路辙叉热处理工艺的改进高锰钢辙叉是目前我国铁路运输中的主要工务部件,它型号繁多,铺设遍及全国。
近几年来,铁路的几次大提速,对这种部件的使用性能与寿命提出了更高的要求,各生产厂家也在努力提高质量,以满足更高的要求。
过去某厂在生产高锰钢辙叉过程中,由于没有充分认识到高锰钢的特性,没有真正搞清其导热等性能对这类件热处理过程的影响,长期以来制定的热处理工艺不合理,致使裂纹废品频繁发生,此项废品率达15,左右,给企业带来较大损失。
1.裂纹废品情况及初步分析产生裂纹的高锰钢辙叉数量与其在热处理窑中的摆放位置及排序(见图1)有关。
我们选择有代表的10窑110件辙叉进行热处理后统计的废品情况见表1,共有14件裂纹废品,其废品率为12.7,。
易发生裂纹废品的叉位集中在上部和边缘,因为这些叉位距火口近,受热义急又快,升温较快。
裂纹产生的部位及其特性见表2。
裂纹形状见图2。
可以看出,产生的都是横裂纹。
裂纹多发生在结构上应力集中处,裂纹的宽度和长度都比较接近,属同一类型,应属同一原因所致。
从15,25mm不同的结构厚度中均产生相同裂纹,也可说明这些裂纹基本由同一原因引起。
对产生裂纹的辙叉取样进行金相检验,其组织为奥氏体和极少量的碳化物,碳化物的数量与形状在国标允许的范围内。
这说明裂纹并未产生在水淬阶段,而是产生在热处理的升温阶段。
2.原热处理工艺我厂过去对高锰钢辙叉进行热处理,根据热处理窑的冷热情况及水爆后辙叉的温度高低,同时执行三种工艺,现场操作者依据实际情况选择其中一种工艺来执行。
三种工艺分别是热辙叉热窑(冷窑)工艺、冷辙叉热窑工艺和冷辙叉冷窑工艺。
三种工艺的工艺曲线如图3所示。
表3为原三种热处理工艺的废品分布。
可见,根据炉况及辙叉的残留温度,所选择的热处理工艺应用后都不同程度地产生了裂纹废品,尤其是冷辙叉热窑工艺废品率更高。
3.产生裂纹原因分析与碳钢件相比,高锰钢件的导热能力很差,其导热系数仅为碳钢的1/4,1/6,导致其在热处理的加热或冷却过程中不同部位大的温差,这样会在件内产生巨大的热应力。
图1-34热处理工艺曲线示意图

二、钢的热处理金属材料在固体范围内进行加热、保温和冷却,以改变其内部组织,获得所需性能的一种方法称热处理。
热处理的种类很多,根据其目的、加热和冷却方法的不同,可以分为:普通热处理、表面热处理及其他热处理方法。
普通热处理有退火、正火、淬火、回火;表面热处理有表面淬火(感应加热、火焰加热等)、化学热处理(渗碳、渗氮等);其他热处理有真空热处理、变形热处理和激光热处理等。
热处理方法虽然很多,但都是由加热、保温和冷却三个阶段组成的,通常用热处理工艺曲线表示。
图1-34 热处理工艺曲线示意图一、钢的普通热处理根据加热及冷却的方法不同,获得金属材料的组织及性能也不同。
普通热处理可分为退火、正火、淬火和回火四种。
普通热处理是钢制零件制造过程中非常重要的工序。
退火1.退火工艺及其目的退火是将工件加热到适当温度,保温一定时间,然后缓慢冷却的热处理工艺,实际生产中常采取随炉冷却的方式。
退火的主要目的:①降低硬度,改善钢的成形和切削加工性能;②均匀钢的化学成分和组织;③消除内应力。
2.常用退火工艺方法根据处理的目的和要求的不同,钢的退火可分为完全退火、球化退火和去应力退火等。
表1-4 为主要退火工艺方法及其应用。
表1-4 常用退火方法的工艺、目的与应用名称工艺目的应用完全退火将钢加热至Ac 3 以上30~50℃,保温一定时间,炉冷至室温(或炉冷至600℃以下,出炉空冷)细化晶粒,消除过热组织,降低硬度和改善切削加工性能主要用于亚共析钢的铸、锻件,有时也用于焊接结构球化退火将钢加热至Ac 1 以上20~40℃,保温一定时间,炉冷至室温,或快速冷至略低于Ar 1 温度,保温后出炉空冷,使钢中碳化物球状化的退火工艺使钢中的渗碳体球状化,以降低钢的硬度,改善切削加工性,并为以后的热处理做好组织准备。
若钢的原始组织中有严重的渗碳体网,则在球化退火前应进行正火消除,以保证球化退火效果主要用于共析钢和过共析钢均匀化退火(扩散退火)将钢加热到略低于固相线温度(Ac 3 或Ac cm 以上150~300℃),长时间保温(10~15h),随炉冷却。
高锰钢热处理工艺流程

高锰钢热处理工艺流程《高锰钢热处理工艺流程》嘿,大家好呀!今天咱来聊聊高锰钢热处理工艺流程。
这事儿啊,可有意思着呢!我先给大家讲个小故事哈。
有一次我去一个工厂参观,正好看到他们在对高锰钢进行热处理。
哇塞,那场面,可真是让我大开眼界。
一开始啊,工人们把高锰钢放进一个大大的炉子里面,就像把宝贝小心翼翼地放进保险箱一样。
这个炉子可神奇了,它能把温度升得高高的。
然后呢,就开始加热啦。
我就眼睁睁地看着那温度一点点升上去,心里还想着,这高锰钢在里面会不会热得受不了呀。
在加热的过程中,工人们可紧张啦,眼睛一直盯着各种仪表,就像医生在看着病人的心电图似的。
他们要时刻关注着温度的变化,不能有一丝一毫的差错。
等温度达到要求了,就进入了保温阶段。
这时候啊,就好像让高锰钢在里面好好睡一觉,让它充分吸收热量,发生一些奇妙的变化。
我在旁边都不敢大声说话,生怕吵醒了它似的。
保温一段时间后,重头戏来啦,那就是冷却!工人们把高锰钢从炉子里拿出来,然后用各种方法让它快速冷却。
有的用水浇,那滋滋的声音,就像放鞭炮一样;有的用风冷,呼呼的风声,感觉像是在给高锰钢吹风扇呢。
我在旁边看着,心里那个好奇呀,这高锰钢经过这么一番折腾,到底会变成啥样呢。
等冷却完成后,我一看,哇,和之前完全不一样啦!变得更加坚硬、更加耐磨了。
这就是高锰钢热处理工艺流程的大致过程啦。
从加热到保温再到冷却,每一步都很关键,都需要工人们精心操作。
就像我们做饭一样,火候掌握不好,做出来的菜就不好吃。
其实啊,生活中很多东西都需要经过类似的处理才能变得更好。
就像我们人一样,也要经过各种磨练和考验,才能变得更加坚强、更加优秀。
所以呀,大家可别小看了这高锰钢热处理工艺流程,它里面蕴含着很多道理呢。
下次要是有机会,大家也可以去工厂看看,亲自感受一下这个神奇的过程。
好啦,今天就和大家聊到这里啦,希望你们喜欢我讲的这个小故事和关于高锰钢热处理工艺流程的介绍。
拜拜啦!。
高锰钢的热处理

热处理技术与装备高锰钢的热处理是将高锰钢铸件加热到碳化物固溶的温度,并保温一定时间,然后在水中快速冷却,形成单一的奥氏体组织,使其强度和韧性大大提高,达到可加工硬化的目的。
与普通碳钢不同,高锰钢在水中淬火后不是变硬,而是变软了,因此高锰钢的热处理又叫水韧处理。
在热处理过程中,碳化物是在固溶态下溶解到奥氏体中去的,所以又叫固溶强化处理。
高锰钢固溶理的参数主要有入炉温度、升温速度、保温温度、保温时间、摆放位置等。
1入炉温度和加热速度高锰钢铸件在入炉之前,铸件表面的粘砂、披缝和浇注冒口要清理干净。
粘砂对铸件加热或冷却都有隔热作用,使铸件加热和入水后的冷却不均匀,严重粘砂会降低铸件入水后的冷却速度,造成晶界碳化物重新析出。
披缝较薄,在热处理加热时会脱碳,水淬后会变成马氏体,马氏体相变体积膨胀,可能会使铸件基体受到拉应力而开裂。
高锰钢导热性能低, 100℃以下为碳钢的1/4~1/6倍, 600℃时为碳钢的1/2~5/7倍。
高锰钢热膨胀系数大,为碳钢的2倍, 500℃以上更大。
虽然铸件在低温加热过程中无相变应力发生,但加热到300℃以上,会在晶内和晶界上出现脆性碳化物增多的现象,有时会发生珠光体转变。
高锰钢辙叉结构复杂,同一铸件壁厚相差悬殊,铸件本身存在不小不等的铸造应力。
在热第1期吴霞等:高锰钢的热处理处理的加热或冷却过程中不同部位存在较大的温差,产生热应力。
这样,热应力和铸造应力叠加,会使辙叉产生裂纹。
因此,必须控制高锰钢辙叉的入炉温度和加热速度。
高锰钢辙叉热处理工艺分两种:冷辙叉处理和热辙叉处理。
对于热辙叉,如果装入同一窑的所有辙叉的装窑温度基本和窑温一致,则这种工艺可以节能,提高效率。
但在实际生产中装窑温度很难与窑温一致,且相差较大,主要原因有:不同炉次的辙叉开箱水爆后在同一窑中进行热处理,造成同一窑中辙叉的初始温度不同;由于连续生产,每天窑的温度也不尽相同;季节性的温度变化导致辙叉与窑温的变化较大;辙叉在窑内的排序不同会造成一定的温差。
高锰钢裂纹防治与的热处理工艺

一、高镒钢铸件防止裂纹的产生1、铸件的结构设计铸件的壁厚相差太大、壁厚过渡不当、铸件圆角过渡太小等结构问题均容易产生裂纹。
因此,铸件设计应密切与铸造工艺相结合,尽量避免铸件设计不合理。
例如可以将字断面改为形断面等。
2、铸造工艺设计(包括各种工艺因素及浇注系统)在铸造工艺各因素中最重要的是铸型的退让性,其次是砂箱设计不合理。
例如箱筋阻碍收缩可以产生裂纹,因此,箱筋距铸件及冒口要有一定的距离。
浇注系统设计不当,分散导人的多条内浇道往往因阻碍铸件收缩,而在与内浇道联结处开裂。
应该特别指出,在铸件内浇道导入处,局部温度高而最后凝固,由于得不到足够的补缩,收缩应力使铸件开裂,所以一般在内浇道处要设置冒口补缩。
3、高镒钢铸件的冒口及冷铁设置高镒钢铸件的冒口设置以不用普通顶冒口为原则,因为用乙烘焰切割冒口时容易造成裂纹。
所以最好采用侧冒口及易割冒口,冒□一般用锤打掉。
铸件设置冒口对热节进行补缩,使铸件不产生缩孔及缩松,是防止内裂的有效措施,但冒口设置又产生了接触热节,其它工艺措施要与其配合得当。
如合理地使用冷铁,就可做到既防止内裂又不会产生外裂。
冷铁可以调节铸件各部分凝固速度,可以使铸件的缺陷发生位置迁移,同冒口配合可以扩大冒口的补缩范围。
但是冷铁使用不当,例如使用弯曲变形的冷铁时往往会在不适当的冷铁长度范围内因铸件凝固速度不均衡而造成裂纹。
冷铁之间间隔大也可造成裂纹,高镒钢铸件对此很敏感,所以工艺设计时应特别注意。
4、化学成分及熔炼工艺在高镒钢中,碳和磷对裂纹的产生影响最大。
含碳量越高,铸件越容易产生裂纹。
钢液的还原精炼对高镒钢铸件裂纹的影响也要引起重视。
在高镒钢的冶炼过程中应严格控制炉渣中FeO+MnO之和不大于1.2%,因为随着渣中FeO+MnO之和的提高,钢液中FeO+MnO也必升高,凝固后在晶界上析出,会使钢变脆。
控制浇注温度及开箱温度也是防止高镒钢铸件产生裂纹的有效措施。
随着浇注温度的升高,铸件收缩应力增大,更重要的是晶粒粗大,柱状晶严重,大大削弱了钢的强度。
高铬铸铁的软化退火工艺

高铬铸铁的软化退火工艺高铬铸铁是一种具有高硬度、高耐磨性和高耐热性能的铸铁材料,广泛应用于机械制造、汽车工业和能源领域。
然而,高铬铸铁的硬度和脆性也带来了一些加工和使用上的困难。
为了改善其可加工性和韧性,软化退火工艺成为了一种常用的处理方法。
软化退火是通过加热和冷却的方式来改变材料的组织结构和性能。
对于高铬铸铁来说,软化退火的关键是使其马氏体组织转变为珠光体组织。
马氏体是一种硬脆的组织,而珠光体则是一种较为韧性的组织。
软化退火可以通过以下几个步骤来实现。
将高铬铸铁件放入退火炉中进行加热。
加热温度一般控制在800℃到950℃之间,具体的温度取决于材料的成分和要求的性能。
加热的目的是使材料中的铬元素溶解,并使其与铁形成固溶体。
加热时间要足够长,以保证铬元素完全溶解。
接下来,将加热后的高铬铸铁件从退火炉中取出,迅速进行冷却。
冷却的方式有多种,常见的包括空冷、水淬和油淬等。
冷却的目的是使固溶体中的铬元素重新析出,并形成珠光体组织。
冷却速度的控制非常重要,过快或过慢都会对材料的组织和性能产生不良影响。
软化退火后的高铬铸铁具有较为均匀的珠光体组织,硬度和脆性得到了明显的降低。
这种材料不仅易于加工,而且具有较好的韧性和抗冲击性能。
因此,软化退火工艺在高铬铸铁的制造和加工过程中得到了广泛应用。
软化退火工艺的控制对于高铬铸铁的性能和质量具有重要的影响。
加热温度、加热时间和冷却方式等参数需要严格控制,以确保材料的组织和性能达到要求。
此外,退火后的高铬铸铁需要进行合适的热处理,以进一步调整其组织和性能。
高铬铸铁的软化退火工艺是一种有效的方法,可以改善材料的可加工性和韧性。
通过控制加热和冷却的过程,可以使高铬铸铁从硬脆的马氏体组织转变为韧性较好的珠光体组织。
软化退火后的高铬铸铁在机械制造和其他领域具有广泛的应用前景。
在实际应用中,需要根据具体要求和条件,合理选择软化退火工艺的参数,以获得最佳的性能和质量。
Mn13高锰钢的热处理工艺研究

窑温一致,且相差较大,主要原因有:不同炉次的辙 叉开箱水爆后在同一窑中进行热处理。造成同一窑 中辙叉的初始温度不同;由于连续生产,每天窑的初 始温度也不尽相同;季节性的温度变化导致辙叉与 窑的温度变化较大:辙叉在窑内的排序不同会造成 一定的温差。这样导致辙叉与炉窑存在较大温差,导 致辙叉在水韧处理后开裂。冷辙叉的装窑温度降 到室温。热辙叉的装窑温度降到150℃。两种辙叉入 窑后都均温1.O~1.5 h后再升温。在650℃以下升 温时,由于高锰钢晶界和晶内会析出碳化物,有时还 会发生珠光体转变,因此升温速度要慢。改进后的工 艺(图1)中,冷、热两种辙叉从150℃升温到650℃
41.5 28.2 33.3 3239.42 769.82 751.19
砂(%)
32.4 32.5 34.8 37.4
Otk/(J・cm-2)
263.80 267.72 281.45 232.42
0.5 t.O
2.0
389.32 406.98 394.23 400.1l
1
膨胀系数大.为碳钢的2倍.500℃以上时更大。虽 然铸件在低温加热过程中无相变应力产生,但加热 到300℃以上后会出现晶内和晶界上脆性碳化物增 多的现象。有时会发生珠光体转变。Mnl3高锰钢辙 叉结构复杂.同一铸件壁厚相差悬殊,铸件本身存在 不小的铸造应力。在热处理的加热或冷却过程中不 同部位存在较大的温差。会产生热应力。这样,热应 力和铸造应力叠加。使辙叉产生裂纹。因此,必须控 制Mnl3高锰钢辙叉的入炉温度和加热速度。 Mnl3高锰钢辙叉的热处理分冷辙叉处理和热 辙叉处理。对于热辙叉,如果装入同一窑的所有辙叉 的装窑温度基本和窑温一致.则这种工艺可以节约 能源,提高效率。但在实际生产中装窑温度很难与
and
铸铁的拉伸曲线

铸铁的拉伸曲线
铸铁是一种具有高强度和高耐磨性的铸造材料,在机械制造、汽车
工业、建筑行业等领域得到广泛应用。
在了解铸铁的性能特点时,重
要的一个参数就是其拉伸曲线。
以下是铸铁的拉伸曲线及其相关说明:
1. 拉伸强度
拉伸强度是指在材料拉伸测试中材料断裂前所承受的最大拉力。
铸铁
的拉伸强度通常大于400MPa,但不同国家和地区对铸铁的标准有所不同。
在拉伸测试中,材料的断裂模式包括颈缩断裂和平面疵断裂。
2. 屈服强度
屈服强度是材料开始发生塑性变形时所承受的最大应力。
铸铁的屈服
强度通常在200MPa左右。
但需要注意的是,铸铁的屈服强度随着温度的升高而降低。
3. 伸长率
伸长率是指在材料拉伸测试中,在达到最大拉力之前,材料的长度和
直径发生的相对变化。
铸铁通常具有低的伸长率,不同类型的铸铁其
伸长率也有所不同。
4. 断面收缩率
断面收缩率是指在拉伸测试中材料断裂后,断面收缩的百分比。
这个参数通常用来评估铸件的凝固过程和冷却收缩性能。
铸铁的断面收缩率通常在30%以上。
5. 断裂韧性
断裂韧性是指材料在发生断裂时所吸收的能量。
铸铁的断裂韧性通常比较低,但可以通过添加一些合适的合金元素来提高。
了解铸铁的拉伸曲线及其相关参数可以帮助我们更好地了解铸铁的特性和性能,在使用铸铁制造的产品时有助于选择合适的型号和质量。
高锰钢及高铬铸铁热处理工艺曲线
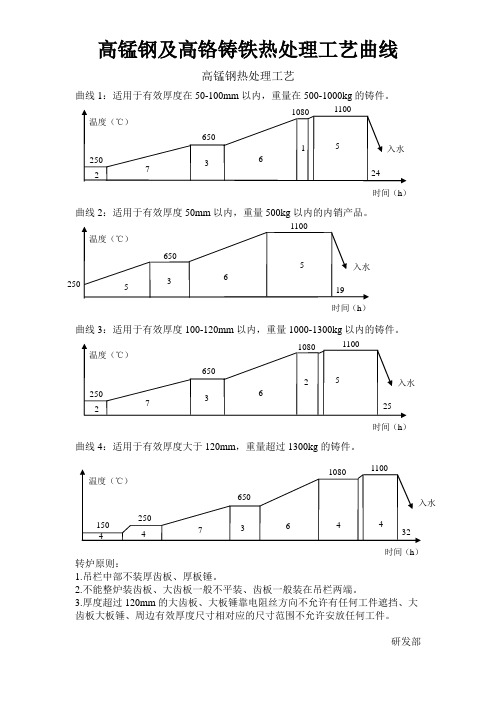
3.厚度超过120mm的大齿板、大板锤靠电阻丝方向不允许有任何工件遮挡、大齿板大板锤、周边有效厚度尺寸相对应的尺寸范围不允许安放任何工件。
研发部
高铬铸铁热处理工艺
一、淬火
二、回火
三、装炉要求:
1.根据电阻炉传热特点、吊栏中部不单独装工件。
2.工件间要留有间隙,尤其是板锤中间间隙要大于板锤厚度。
3.炉门300mm内不放工件。
研发部温度入水10802501100时间h2502432191100650温度1080250时间h入水251100温度入水10802501100时间h温度入水高锰钢及高铬铸铁热处理工艺曲线高铬铸铁热处理工艺一淬火二回火三装炉要求
高锰钢热处理工艺
曲线1:适用于有效厚度在50-100mm以内,重量在500-1000kg的铸件。
曲线2:适用于有效厚度50mm以内,重量500kg以内的内销产品。
曲线3:适用于有效厚度100-120mm以内,重量1000-1300kg以内的铸件。
曲线4:适用于有效厚度大于120mm,重量超过1300kg的铸件。
转炉原则:
1.吊栏中部不装厚齿板、厚板锤。
2.不能整炉装齿板、大齿板一般不平装、齿板一般装在吊栏两端。
超高锰钢热处理工艺及性能研究

Table2
不同热处理工艺条件超高锰钢的力学性能
water
Mechanical properties of super—high manganese steel by the different
toughening treatment
2.2
热处理工艺对超高锰钢组织和力学性能的影响 从表2中比较工艺1和2发现,经回火弥散强化的超高锰钢的强度、冲击韧性、硬度以及延伸率均比
谢敬佩等:
超高锰钢热处理工艺及性能研究
。23‘
力学性能、金相和微观分析试样都从楔形块上制取,试样毛坯在高温箱式电炉中进行热处理。
1.3力学性能测试 在SHIMAD(岛津)ZUAG—1250KV精密万能电子拉伸试验机上进行拉伸试验,改传统圆形拉伸试 样为板条状,利用线切割加工,避免切削加工过程中引起的硬化等问题,性能测试前进行砂纸打磨。金 属拉伸试验试样尺寸按GB2975切取。冲击试验在JB一300A摆锤式冲击试验机上进行,采用标准夏比 u型缺口的冲击试样‘引。硬度测试采用HB一3000布氏硬度试验机。 用配备了EDAX能谱仪的JSM一5610LV型扫描电子显微镜观察超高锰钢的显微组织及冲击断口形貌。
treatment(1 000 X)
・26・
2008全国耐磨材料暨水泥矿山应用技术交流会
3
结论
(1)含合金元素Cr、Mo并经RE—Si—Fe合金变质处理的超高锰钢在1 100。C常规水韧处理后奥氏
体转变完全,晶粒均匀,晶内基本没有碳化物,晶界存在极少量未溶碳化物。冲击断口呈纤维状,综合力 学性能良好。 (2)经600。C×6h保温沉淀强化和回火弥散强化处理的超高锰钢晶粒度基本不变,晶内弥散析出细 小、均匀的颗粒状M,C,型碳化物,这些碳化物符合第二相强化原则,提高了超高锰钢的力学性能。 (3)优化出含合金元素Cr、Mo的超高锰钢最佳热处理工艺为:加热至1100。C×4h,水淬,再经250。C x4h回火处理。经过优化,奥氏体晶粒细小,晶内颗粒状碳化物均匀、弥散分布,力学性能得到显著提 高:orb=994.51Mpa‘,or。=430.98Mpa,dk=260J。em~,HB=227,8=55.03%。与常规水韧处理相比orb 提高了18.2%,or。提高了7%,Otk提高了22%,8提高了30.3%,硬度提高了9.7%。 参考文献
锰钢热处理工艺

锰钢热处理工艺【锰钢热处理工艺】一、锰钢热处理工艺的历史其实啊,锰钢这玩意儿在材料界可是有着不短的历史。
早在很久很久以前,人们就发现了锰这种元素在钢铁中的神奇作用。
在过去,钢铁的性能往往受到很多限制,强度不够、韧性不足等等问题一直困扰着人们。
后来,经过不断地尝试和摸索,发现加入一定量的锰之后,钢铁的性能能得到显著提升。
比如说,在工业革命时期,对于各种机械设备的需求大增,这时候锰钢就开始崭露头角。
它被用在制造蒸汽机的零件、铁路轨道的连接件等等,为当时的工业发展立下了汗马功劳。
随着时间的推移,对于锰钢的研究越来越深入,热处理工艺也在不断地改进和完善。
从最初的简单加热处理,到后来更加精细复杂的工艺,锰钢的性能也变得越来越出色。
二、锰钢热处理工艺的制作过程1. 材料准备说白了就是先把原材料准备好。
锰钢的主要成分除了铁之外,就是锰啦,当然还可能会有一些其他的合金元素。
这些原材料都要按照一定的比例进行调配,就像是做菜时要把各种调料放对量一样。
2. 加热环节这一步可是关键哦!把调配好的锰钢材料放进加热炉中,加热到特定的温度。
这个温度可不是随便定的,那是经过科学家们无数次实验得出的最佳数值。
打个比方,这就好比烤蛋糕,温度太高会烤焦,温度太低又烤不熟。
3. 保温阶段加热到合适温度后,还得让它在这个温度下保持一段时间,确保整个材料都被均匀加热,内部结构也能发生相应的变化。
4. 冷却处理冷却的方式有好几种,比如快速冷却、缓慢冷却等等。
不同的冷却方式会让锰钢获得不同的性能。
这就像人跑步后,有的人马上冲个冷水澡,有的人慢慢散步等自然降温,身体的反应可不一样。
三、锰钢热处理工艺的特点1. 高强度锰钢经过热处理后,强度那是相当高。
想象一下,它就像一个超级大力士,能够承受巨大的压力和拉力,不容易变形和断裂。
比如说在建筑行业中,用锰钢制造的钢梁能够支撑起巨大的建筑物,稳如泰山。
2. 良好的韧性它不仅强度高,韧性也很棒。
这意味着它不容易脆断,具有一定的弹性和延展性。
- 1、下载文档前请自行甄别文档内容的完整性,平台不提供额外的编辑、内容补充、找答案等附加服务。
- 2、"仅部分预览"的文档,不可在线预览部分如存在完整性等问题,可反馈申请退款(可完整预览的文档不适用该条件!)。
- 3、如文档侵犯您的权益,请联系客服反馈,我们会尽快为您处理(人工客服工作时间:9:00-18:30)。
曲线1:适用于有效厚度在50-100mm以内,重量在500-1000kg的铸件。
曲线2:适用于有效厚度50mm以内,重量500kg以内的内销产品。
曲线3:适用于有效厚度100-120mm以内,重量1000-1300kg以内的铸件。
曲线4:适用于有效厚度大于120mm,重量超过1300kg的铸件。
转炉原则:
1.吊栏中部不装厚齿板、厚板锤。
2.不能整炉装齿板、大齿板一般不平装、齿板一般装在吊栏两端。
3.厚度超过120mm的大齿板、大板锤靠电阻丝方向不允许有任何工件遮挡、大齿板大板锤、周边有效厚度尺寸相对应的尺寸范围不允许安放任何工件。
研发部
高铬铸铁热处理工艺
一、淬火
二、回火
三、装炉要求:
1.根据电阻炉传热特点、吊栏中部不单独装工件。
2.工件间要留有间隙,尤其是板锤中间间隙要大于板锤厚度。
3.炉门300mm内不放工件。
研பைடு நூலகம்部