SPC控制图异常判定资料
SPC控制图表格(自动判别异常点)
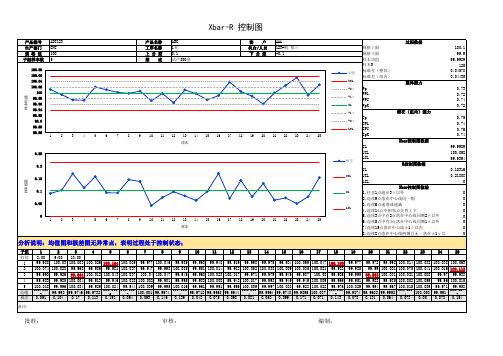
产品编号 生产部门 规 格 值 子组样本数 ABC123 CNC 100 5 产品名称 工序名称 上 公 差 描 述 ABC 1夹 0.1 试产300套 客 户 机台/人员 下 公 差 AAA 123#机 张三 -0.1 过程数据 规格上限 规格下限 样本均值 样本N 标准差(整体) 标准差(组内) 整体能力 Pp PPL PPU PpK 潜在(组内)能力 Cp CPL CPU CpK Xbar控制图数据 CL UCL LCL R控制图数据 CL UCL LCL Xbar控制图检验 1.任意1点超出3σ 以外 2.连续9点落在中心线同一侧 3.连续6点递增或递减 4.连续14点中相邻点交替上下 5.连续3点中有2点落在中心线同侧2σ 以外 6.连续5点中有4点落在中心线同侧1σ 以外 7.连续15点落在中心线±1σ 以内 8.连续8点落在中心线两侧且无一落在±1σ 以内 0.10316 0.21808 0 0 0 0 0 0 0 0 0 99.9989 100.058 99.9394 0.75 0.74 0.76 0.74 0.73 0.72 0.74 0.72 100.1 99.9 99.9989 125 0.04578 0.04435
0.154
批准:
审核:
编制:
子组 时间 1 2 3 4 5 均值 极差 备注: 1 2 3 4 5 6 7 8 9 10 8:00 9:00 10:00 99.988 100.03 100.003 100.026 100.104 100.005 99.977 100.046 99.985 99.993 100.074 100.028 99.968 99.986 99.981 100.027 99.947 99.998 100.085 99.951 99.993 99.926 99.864 100.012 100.043 100.037 100.04 100.047 99.946 99.968 99.983 99.985 100.004 99.913 99.946 100.038 100.002 99.901 99.995 99.983 100.018 99.996 100.034 99.929 100.024 99.944 100.039 99.995 100.016 99.961 100.0112 99.993 99.9746 99.9732 100.0196 100.0102 100.001 99.9974 100.0054 99.9712 0.091 0.104 0.17 0.113 0.158 0.094 0.093 0.146 0.139 0.042 11 12 13 14 15 16 17 18 19 20 21 22 23 24 25 100.063 100.112 99.988 100.015 99.958
SPC控制图判异标准及异常处理方法
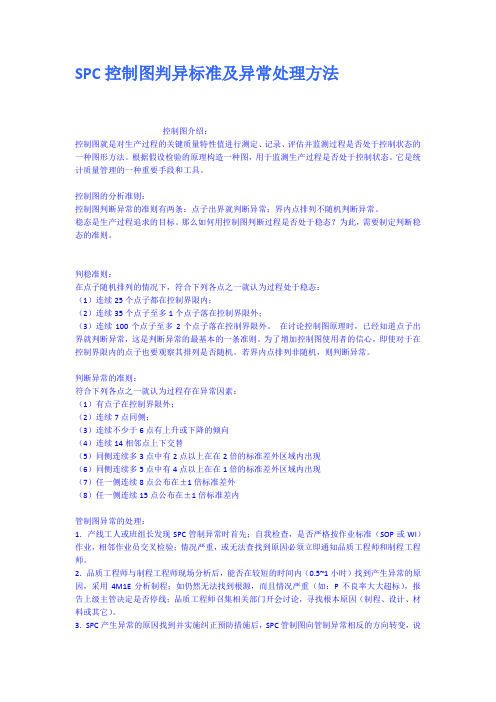
SPC控制图判异标准及异常处理方法控制图介绍:控制图就是对生产过程的关键质量特性值进行测定、记录、评估并监测过程是否处于控制状态的一种图形方法。
根据假设检验的原理构造一种图,用于监测生产过程是否处于控制状态。
它是统计质量管理的一种重要手段和工具。
控制图的分析准则:控制图判断异常的准则有两条:点子出界就判断异常;界内点排列不随机判断异常。
稳态是生产过程追求的目标。
那么如何用控制图判断过程是否处于稳态?为此,需要制定判断稳态的准则。
判稳准则:在点子随机排列的情况下,符合下列各点之一就认为过程处于稳态:(1)连续25个点子都在控制界限内;(2)连续35个点子至多1个点子落在控制界限外;(3)连续100个点子至多2个点子落在控制界限外。
在讨论控制图原理时,已经知道点子出界就判断异常,这是判断异常的最基本的一条准则。
为了增加控制图使用者的信心,即使对于在控制界限内的点子也要观察其排列是否随机。
若界内点排列非随机,则判断异常。
判断异常的准则:符合下列各点之一就认为过程存在异常因素:(1)有点子在控制界限外;(2)连续7点同侧;(3)连续不少于6点有上升或下降的倾向(4)连续14相邻点上下交替(5)同侧连续多3点中有2点以上在在2倍的标准差外区域内出现(6)同侧连续多5点中有4点以上在在1倍的标准差外区域内出现(7)任一侧连续8点公布在±1倍标准差外(8)任一侧连续15点公布在±1倍标准差内管制图异常的处理:1.产线工人或班组长发现SPC管制异常时首先;自我检查,是否严格按作业标准(SOP或WI)作业,相邻作业员交叉检验;情况严重,或无法查找到原因必须立即通知品质工程师和制程工程师。
2.品质工程师与制程工程师现场分析后,能否在较短的时间内(0.5~1小时)找到产生异常的原因,采用4M1E分析制程;如仍然无法找到根源,而且情况严重(如:P不良率大大超标),报告上级主管决定是否停线;品质工程师召集相关部门开会讨论,寻找根本原因(制程、设计、材料或其它)。
SPC控制图的种类及判异方法48页

控制图的种类及判异方法
SPC统计过程控制
依管理特性值分类
计 x R 均值和极差图
x 量
-s均值和标准差图
型
数 X med -R 中位值极差图
据
X-MR 单值移动极差图
一、控制图的种类
P chart 不良率控制图
计 数 nP chart不良数控制图 型 数 C chart 缺点数控制图 据
SPC统计过程控制
五、计数型数据控制图
1、P图/不良率控制图 -1
◆ P图是用来测量在一批检验项目中不合格品(缺陷)项目的百分数。 ◆ 步骤:
1>收集数据,选择子组容量、频率 和数量: -子组容量:需足够大(最好能恒定),并有包含几个不合格品。 -分组频率:根据实际情况,兼容量大和信息反馈快的要求。 -子组数量:收集的时间需足够长,使得可以找到所有可能影响到过程 变差源,一般为25组
SPC统计过程控制
一、控制图的种类
SPC统计过程控制
一、控制图的种类
SPC统计过程控制
二、控制图的选择方法
计量值
控制图的选择
数据性质
计数值
N≧2 X
样本大小 N=1
N=? _ X
CL性质?
N=2-5
N≧10
N=?
不良数
数据系不良数 缺点数 或缺点数
是
不是
N是否相等?
是 单位大小 是否相同?
X~ R X R
A2 3 3 0.577 n d2 5 2.326
D4 1 3 d3 1 3 0.864 2.114
d2
2.326
D3 1 3 d3 1 3 0.864 ( 0)0
SPC控制图判异准则制定依据判异准则顺口溜精选文档

S P C控制图判异准则制定依据判异准则顺口溜精选文档TTMS system office room 【TTMS16H-TTMS2A-TTMS8Q8-SPC控制图判异准则制定依据过程控制图包含2种,一种是“分析用控制图”,另一种是“控制用控制图”。
分析用控制图,主要作以下2点用途:①所分析的过程是否为稳态;②过程能力指数是否满足要求。
这种把能力指数满足要求称作技术稳态。
分析用控制图的调整过程即质量不断改进的过程。
控制用控制图,当过程达到我们所确定的“统计稳态“和技术稳态”后,才能将分析用控制图的控制线延长作为控制用控制图。
这种延长的控制线相当于生产立法,便进入日常管理。
故从数理统计的角度来看,分析用控制图阶级就是过程参数未知阶段,而控制用控制图阶段则是过程参数已知阶段。
在由分析用控制图向控制用控图转化前,需要对过程判读,这时就需要用到:判稳准则和判异原则。
1)判稳准则的思路对于判异来说,“点出界就判异”。
虽不百发百中,也是千发九九七中,很可靠,但在控制图上有一点未出界,可否判稳?这可能存在2种可能:①过程本来就稳定;②异常漏报。
故出现一点未出界不能立即判稳。
但接连出现m (m>>1)个点子未出界,则情况大不相同。
这时整个点子系列的β总=βm要比个别点子的β小得多,可以忽略不计。
那么仅有一种可能,即过程稳定。
如果接连在控制界内的点子更多,即使有个别个点子偶然出界,过程仍可看作是稳态的。
这就是判稳准则的思路。
判稳准则,在点子随机排列的情况下,符合下列各原则之一就判稳:连续25个点,界外点数d=0;其概率P = α1连续35个点,界外点数d≤1; 其概率P = α2连续100个点,界外点数d≤2; 其概率P = α3尽管在上述判稳原则下,对于出界点也应当加以排查。
用概率统计如下,假设过程正常:P(连续35点,d≤1)=(0.9973)35(0.0027)0+(0.9973)34(0.0027)1= 0.9959 =α2故, P(连续35点,d>1)= 1 - 0.9959 = 0.0041 =α2同理,α1 = 0.0654;α2 = 0.0041;α3 = 0.0026,可见α1 与α2 和α3明显不相称。
SPC控制图异常判定资料

UCL 長 さ8の 連 CL 長 さ7の 連
LCL
●此时可预想的异常原因有:1.材料Lot(新品,原料)的变更.2.机械 装置异常(设备异常或工装松动),引发的平均值的变化。 ●另外,还有测量系统变化(新检查员或量具)或计测方法的异常。
4-3
7点连续上升或下降的倾向
有7点连续上升或下降倾向时可判定为异常。 (JIS Z 9021:1998年新规定由7点→6点。 但因为SPC参考手册尚未有变动因此继续适用7连异常判定)
4-6
有周期性时
有周期性时
UCL
CL
L CL
此时,需要技术性追究发生周期的原因,有必要慎重判断是否 处在管理状态下。 掌握周期原因,但工程能力充分,而且为排除异常原因所需的费用 较多时也可以判定为处在管理状态下。 可能的原因:1.操作人员疲劳;2. 原材料发送有问题;3.热积累或 应力积累。
U傾 向 連 続 7点 下 降 傾 向
●此时可预想的原因有,发生某种劣化或消耗,平均值逐渐 上升,下降。
4-4
接近管理界限
若把中心线(CL)与管理界限间的宽幅3等分时,处在最外侧的 范围内若有3点中的2点时可判为异常。 3点中2点处在外侧的情况很多。图上所示的情况都可判定 为异常。
4-1
点子越出管理界限时(管理out)
点子处在管理上限(UCL)的上面,或处在管理下限(LCL)的下面时。 正处在管理界限上时可判定为异常(out)。
UCL
CL
L CL
●此时可预想的异常原因: 机器发生了突发异常或者机器磨损严重导致机器装置失灵等
4-2
出现7点以上的连
点子连续排列在中心线的(CL:严密讲应利用上下同数的中央值, 但实际上用CL判定也可)排列在中心线的上方或下方时称为连。 若出现7点以上的连时可判定为异常 (JIS Z 9021:1998新规定连的异常判定7连→9连。 但因为SPC参考手册尚未有变动因此继续适用7连异常判定)
SPC控制图的判定方法
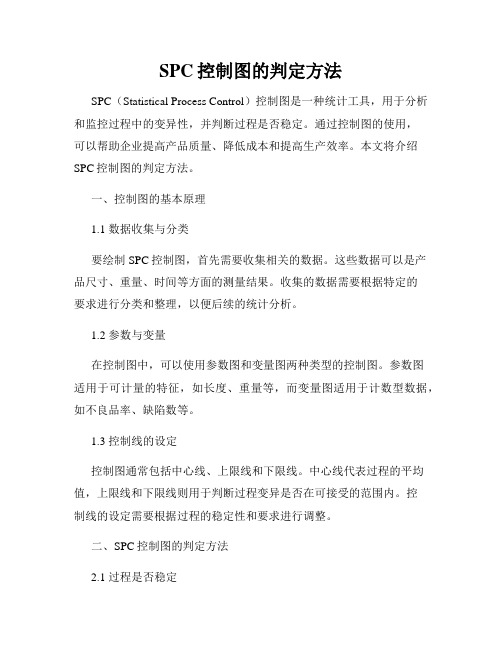
SPC控制图的判定方法SPC(Statistical Process Control)控制图是一种统计工具,用于分析和监控过程中的变异性,并判断过程是否稳定。
通过控制图的使用,可以帮助企业提高产品质量、降低成本和提高生产效率。
本文将介绍SPC控制图的判定方法。
一、控制图的基本原理1.1 数据收集与分类要绘制SPC控制图,首先需要收集相关的数据。
这些数据可以是产品尺寸、重量、时间等方面的测量结果。
收集的数据需要根据特定的要求进行分类和整理,以便后续的统计分析。
1.2 参数与变量在控制图中,可以使用参数图和变量图两种类型的控制图。
参数图适用于可计量的特征,如长度、重量等,而变量图适用于计数型数据,如不良品率、缺陷数等。
1.3 控制线的设定控制图通常包括中心线、上限线和下限线。
中心线代表过程的平均值,上限线和下限线则用于判断过程变异是否在可接受的范围内。
控制线的设定需要根据过程的稳定性和要求进行调整。
二、SPC控制图的判定方法2.1 过程是否稳定在绘制控制图之前,首先需要判断过程是否稳定。
稳定的过程指的是过程产生的变异性仅来自于随机误差,而不是系统性的因素。
判断过程是否稳定可以通过以下几种方式进行:(1)过程能否满足规范要求:通过对过程数据进行规范性能指标的计算与分析,判断过程是否满足要求。
(2)过程的输入是否稳定:观察过程的输入数据,如材料的质量、设备的稳定性等,判断输入是否稳定。
(3)过程是否存在特殊因素:通过了解和分析过程中的特殊因素,如人为因素、设备故障等,判断过程是否稳定。
2.2 控制图的规则绘制了控制图后,可以通过判断数据点的分布情况,在控制图上标示出不同的规则。
常用的规则有以下几种:(1)单点超出控制限:单个数据点超出上限线或下限线。
(2)连续点在中心线同一侧:三个或更多连续的数据点在中心线的同一侧。
(3)多点连续递增或递减:连续五个或更多数据点递增或递减。
(4)趋势:六个或更多连续递增或递减的数据点。
SPC控制图8种不良模式

4
潘帅杰 <常规控制图>
国家标准GB/T4091-2001
5
异常4:连续14点中相邻点交替上下
例1:
A B C C B A
异常5:连续3点有2点落在中心线同一侧的B区外(2σ外)
例1:
A B C C B A A B C C B A
异常6:连续5点中有4点落在中心线同一侧的C区外(1σ 外) 例1:
异常1:点落在控制限外
例1:
A B C C B A A B C C B A
异常2:连续9点落在中心线同一侧
例1:
A B C C B A
异常3:连续6点递增或递减
例1:
例2:
A B C C B A A B C C B A
例2:
A B C C B A
例2:
潘帅杰 <常规控制图>
国家标准GB/T4091-2001
例1:
A B C C B A A B C C B A
异常8:连续8点落在中心线两侧且无1点在C区内
例1:
例2:
A B C C B A A B C C B A
例2:
潘帅杰 <常规控制图>
国家标准GB/T4091-2001
9
潘帅杰 <常规控制图>
国家标准GB/T4091-2001
10
例2:
A B C C B A A B C C B A
例2:
A B C C B A
例2:
潘帅杰 <常规控制图>
国家标准GB/T4091-2001
6
潘帅杰 <常规控制图>
国家标准GB/T4091-2001
SPC控制图判异准则解读

理论基础:正态分布原理及中心极限定理。
不論總體分佈是否正態分佈,若抽取樣本,而個別 樣本的數目愈多,樣本的平均數愈趨向正態分佈 ------中心趋向定理
·
·
·
·
·
·
· ·
·
UCL
·
CL
·
LCL
两类错误 1.第一类错误:虚发警报(false alarm) 过程正常,由于点子偶然超出界一
• 20 世纪 20 年代美国贝尔电话实验室成立了两个研究质量的课题组,一为 过程控制组,学术 领导人为为休哈特(Walter A.Shewhart);另一为产品控制组, 学术领导人为道奇(Harold F.Dodge)。其后,休哈特提出了过程控制理论以及 控制过程的具体工具——控制图(control chart)。道奇与罗米格(H.G.Romig)则提 出了抽样检验理论和抽样检验表。
准则 7:连续 15 点在 C 区中心线上下(图 4.3-7)。 出现本准则的现象是由于参数σ变小。对于 这种现象不要被它的良好“外貌”所迷惑 ,而应该注意到它的非随机性。造成这种现象的原因可能 有数据虚假或数据分层不 够等。在排除了上述两种可能性之后才能总结现场减少标准差σ的先进经 验。
α0=0.682715=0.0033
判异准则 小概率事件原理:小概率事件在一次试验中几乎不可能发生,若发生即判断 异常.国标 GB/T4091—2001《常规控制图》中规定了 8 种判异准则 准则 1:一点落在 A 区以外(图 4.3-1)。 在 3σ原则下,准则 1 犯第一类错误的概率为α0=0.0027。
准则 2:连续 9 点落在中心线同一侧(图 4.3-2)。 此准则是为了补充准则 1而设计的,以改进控制图的灵敏度。 选择 9 点是为了使其犯第一类错误的概率α与准则 1 的α0=0.0027 大体相仿。
8张图直观讲解SPC八大判异原则(燃爆质量圈)

8张图直观讲解SPC八大判异原则(燃爆质量圈)当我们要求供应商使用SPC进行过程控制的时候,必然会涉及到的一个问题就是8大判异原则。
也就是说,管制图中出现下面的8种点位分布的时候,我们就认为过程出现了特殊原因,我们必须找出点位分布异常的特殊原因,将其消除,从而提前遏制不良品的产生。
作为SQE,你有没有被供应商问及,为啥这8种分布叫做异常分布?今天就从统计学角度,跟大家解释一下,我们通常所说的8大判异原则为啥能够判异,其暗示的潜在异常原因是什么!首先所有SQE必须要清醒地认识:异常的出现就是小概率事件产生了!首先给大家解释下正态分布的概率比例,见下图:在这张图上,请大家忽略SQE供应商质量平台的logo和名称,专注地记住左A,左B,左C,右C,右B,右A这6个分区;同时在ABC分区的下方都有一个相同颜色的小数:0.023,0.136,0.341(这是样本点出现在相应分区的概率,查表可得,有兴趣,大家可以自己去查表,我们在本文结束的时候有表哦)好,接下来,我给大家一一解释8大判异入选异常判断准则的缘由:2/3A(连续3点中有2点在中心线同一侧的B区外<即A区内>)解释:0.023的平方=0.00529,就是说抽1000数据,才会出现6次这样的情况,小概率事件产生了,肯定有特殊原因导致!原因:一般认为是新员工,工艺方法错误,机器故障,原材料不合格,测量错误,计算错误,检验方法或标准变化。
4/5C(连续5点中有4点在中心线同一侧的C区以外)解释:(0.136 0.023)的4次方=0.000639,就是说这种情况出现的概率是千分之六,小概率事件产生了,肯定有特殊原因导致!原因:一般认为是新员工,工艺方法错误,机器故障,原材料不合格,测量错误,计算错误,检验方法或标准变化。
6连串(连续6点递增或递减,即连成一串)解释:规律分布,必有异因!原因:刀具模具等工具的磨损,维护保养水平降低,操作工的技能越来越熟练。
如何从SPC控制图判断过程是否稳定

如何从SPC控制图判断过程是否稳定
1 判稳准则(只存在普通原因)
1)连续25点,无界外点;
2)连续35点,界外点数d≤1;
3)连续100点,界外点数d≤2。
2 判异准则(存在特殊原因)
常见的异常情况与模式有如下八种:
1)一点落在A区以外;
2)连续9点落在中心线的同侧;
3)连续6点递增或递减;
4)连续14点中相邻点上下交替;
5)连续3点中有2点落在中心线同侧的B区以外;
6)连续5点中有4点落在中心线同一侧的C区以外;
7)连续15点在C区中心线上下;
8)连续8点在中心线两侧而无一点在C区。
其中第1点表示点出界就判异——3σ方式,确定α0=0.27%,在实际使用中第1点一定要考虑到。
其余7点表示界内点排列不随机——第二类判异准则,在实际使用中可以考虑选取其中几个做为判异准则。
SPC统计常用控制图评价

SPC统计常用控制图评价引言SPC〔Statistical Process Control,统计过程控制〕是一种通过采集和分析过程数据,以便实时监控和控制过程稳定性的方法。
常用的SPC工具之一是控制图,它能够帮助我们识别过程中的特殊因素和常见问题,并实施相应的改良措施。
本文将介绍SPC常用控制图,并对其评价方法进行讨论。
一、SPC常用控制图1.1 均值图均值图〔X-Bar图〕是一种常用的控制图,用于监控连续型数据的均值是否稳定。
它通过绘制样本均值的变化情况,以及控制限的设置,来判断过程是否受到特殊因素的影响。
如果样本均值超出控制限范围,就说明过程出现了问题。
1.2 极差图极差图〔R图〕是另一种常用的控制图,用于监控连续型数据的变异性是否稳定。
它通过绘制样本极差的变化情况,以及控制限的设置,来判断过程是否存在异常变异。
如果样本极差超出控制限范围,就说明过程出现了问题。
1.3 标准差图标准差图〔S图〕是控制图中另一种用于监控连续型数据变异性的工具,它通过绘制样本标准差的变化情况,以及控制限的设置,来判断过程的稳定性。
如果样本标准差超出控制限范围,就说明过程存在异常变异。
1.4 化验图化验图〔C图〕是一种用于检测离散型数据的控制图。
它通过绘制样本中不良品的数量或比例的变化情况,以及控制限的设置,来判断过程是否稳定。
如果样本不良品数量或比例超出控制限范围,就说明过程存在问题。
二、控制图的评价方法控制图的评价方法主要包括特殊因素的判断和过程能力的评估。
2.1 特殊因素的判断特殊因素指的是导致过程异常的特殊因素,比方机器故障、操作失误、原材料问题等。
通过控制图的帮助,我们可以判断特殊因素是否存在。
一般来说,如果样本点落在控制限之外,或出现非随机的趋势、扰动或周期性变化,就可能是由特殊因素引起的。
在判断特殊因素的时候,还需要考虑其实质性和重复性,以防止过度反响。
2.2 过程能力的评估过程能力是指过程的稳定性和可控性。
SPC判定原则
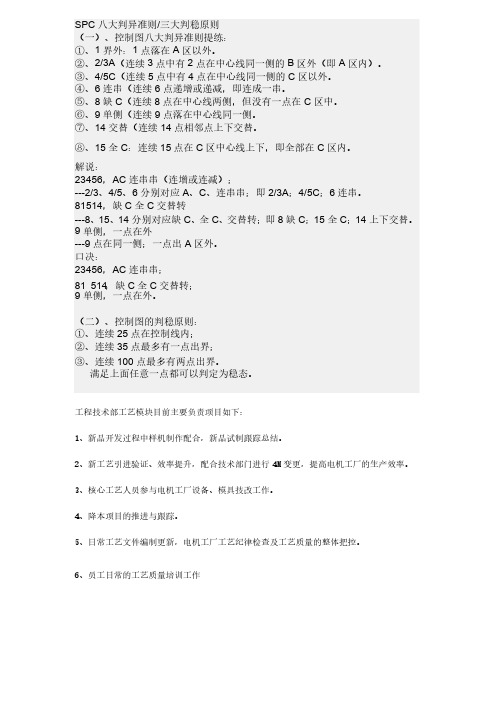
SPC八大判异准则/三大判稳原则(一)、控制图八大判异准则提练:①、1界外:1点落在A区以外。
②、2/3A(连续3点中有2点在中心线同一侧的B区外(即A区内)。
③、4/5C(连续5点中有4点在中心线同一侧的C区以外。
④、6连串(连续6点递增或递减,即连成一串。
⑤、8缺C(连续8点在中心线两侧,但没有一点在C区中。
⑥、9单侧(连续9点落在中心线同一侧。
⑦、14交替(连续14点相邻点上下交替。
⑧、15全C:连续15点在C区中心线上下,即全部在C区内。
解说:23456,AC连串串(连增或连减);---2/3、4/5、6分别对应A、C、连串串;即2/3A;4/5C;6连串。
81514,缺C全C交替转---8、15、14分别对应缺C、全C、交替转;即8缺C;15全C;14上下交替。
9单侧,一点在外---9点在同一侧;一点出A区外。
口决:23456,AC连串串;81 514,缺C全C交替转;9单侧,一点在外。
(二)、控制图的判稳原则:①、连续25点在控制线内;②、连续35点最多有一点出界;③、连续100点最多有两点出界。
满足上面任意一点都可以判定为稳态。
工程技术部工艺模块目前主要负责项目如下:1、新品开发过程中样机制作配合,新品试制跟踪总结。
2、新工艺引进验证、效率提升,配合技术部门进行4M变更,提高电机工厂的生产效率。
3、核心工艺人员参与电机工厂设备、模具技改工作。
4、降本项目的推进与跟踪。
5、日常工艺文件编制更新,电机工厂工艺纪律检查及工艺质量的整体把控。
6、员工日常的工艺质量培训工作7、车间提交的工艺难点问题解决。
质量隐患的排查、判定及跟踪。
、车间提交的工艺难点 问题解决。
质量隐患的排查、判定及跟踪。
、变频电机检测失效的攻关8、变频电机检测失效的攻关目前存在的难点:在电机工厂现有规模的情况下,工程技术模块还缺乏1-2名弱电和控制方向的人员。
向的人员。
1-2名设备模具的方向型人才。
在现有电机工厂核心工艺人员逐步成长的情况下,应该在不久的将来久的将来足以承担电机工厂的发展需求。
SPC控制图异常判定资料

01 SPC控制图概述
SPC控制图定义
定义
SPC控制图是一种用于监控、分析和 控制生产过程的工具,通过收集数据 并在控制图上绘制点来评估过程的稳 定性。
THANKS FOR WATCHING
感谢您的观看
如何选择合适的控制图?
不同的控制图适用于不同类型的数据和过程。在选择控制图 时,需要考虑数据的分布、过程的特性以及要监控的过程参 数。常见的控制图包括均值-极差控制图、均值-标准差控制 图、不合格品率控制图等。
选择依据:根据数据类型和过程特性选择合适的控制图,确 保能够有效地监测和控制过程。
如何解读控制图的异常信息?
总结词
累积和控制图通过计算累积和来评估过程的稳定性,适用于监测生产过程的关键特性。
详细描述
当控制图上的点超出上控制限或下控制限,或者点在控制限内但呈持续上升或下降趋势 时,可以判定为异常。此外,如果点在控制限内但出现周期性波动,也可能是异常。
移动极差控制图异常判定实例
总结词
移动极差控制图通过计算移动极差来评 估过程的稳定性,适用于监测数据分布 较为稳定的过程。
目的
控制图用于检测生产过程中的异常波 动,预防不良品产生,并保持产品质 量稳定。
SPC控制图原理
中心线(CL)
控制图的中心线表示过程的预期平均值。
控制上限(UCL)和控制下限(LCL)
这两个界限用于判断数据点是否超出可接受的范围。
判定原则
当数据点超出UCL、LCL或连续7点上升或下降时,判定为异常。
累积和控制图异常判定标准
(超经典)SPC控制图+判异8准则

OK
0.6
0.5
0.4
0.3
0.2
0.1
0
0
0
0
0
0
0
1、0T.0h00e0proces0s.0a00r0e within0.s0t0a0t0istical c0o.0n0t0r0ol, plea0s.e00k00eep it. 0.0000
Re
ma
0 0.0000
0 0.0000
0 0.0000
0 0.0000
SPC控制图
(表格编号:***************)
规格
尺寸数
机台编号
地点/时间 产品信息 测量仪器
特性
工序 产品型号
名称 中值 下限
测量地点 料号 编号
上公差 中值
质检室
时间 制程 单位 下公差 上限
测 量 者
审 核
Data Time
6月22 日 8:30
1
2
3
4
特5 性6
7
8
X-bar
R
6月22 日 9:30
Lower Control Limit(LCLx) Upper Control Limit(UCLR)
Control Limit(CLR) Lower Control Limit(LCLR)
The capability for a stable process
K Cp Cpk The Grade of the capability
Performance index
Fraction defective
Pp Ppk Estimate Fraction Defective
Value 0.000 0.000 0.000
SPC判异规则范文

SPC判异规则范文SPC(Statistical Process Control,统计过程控制)是一种管理和监控过程稳定性的质量管理方法。
SPC判异规则是用来识别过程中出现异常或超出控制限的模式或点。
这些规则可帮助管理者及时发现和纠正过程中的问题,确保产品质量符合标准要求。
以下是常见的SPC判异规则。
1. 单点超出控制限规则(One-point beyond control limits rule)这是最简单的判异规则,当一个点超出控制限时,即可认为过程出现异常。
此判异规则适用于稳定性较高的过程。
但需要注意的是,有时候一个点的超出可能是由于随机因素导致的,因此需要进一步确认。
2. 连续点落在同一侧规则(Runs beyond limits rule)连续点落在同一侧超出控制限,可能表明过程中存在系统性的偏移或变化。
这种情况下,应该检查系统是否需要进行调整或改进。
3. 趋势规则(Trends rule)趋势规则用于检测过程中的递增或递减趋势。
当连续的点呈现递增或递减的趋势时,即使点本身没有超出控制限,也应该引起关注。
此时可能需要对过程进行调整或修复。
4. 非随机分布规则(Non-random pattern rule)当点的分布不随机时,即存在特殊的模式,可能表明过程中存在系统性的偏离。
例如,在控制图中出现串珠、波浪、周期性等模式,都可能表明过程中存在问题。
5. 突变规则(Shifts rule)突变规则用于检测过程中的突然变化。
当连续的点突然出现跳跃或突变时,可能表明过程发生了突发事件或变化。
突变的原因可能是由于设备故障、材料变化或操作员失误等。
6. 相关性规则(Lack of correlation rule)相关性规则用于检测不同变量之间的相关性是否符合预期。
当两个或多个变量之间的相关性不符合以往的经验或理论预期时,可能表明存在未知的因素影响了过程。
以上是常见的SPC判异规则,这些规则可以根据具体的过程和需求进行调整和定制。
SPC控制图判异准则最新版

本人将国标中的控制图的8条判异准则,每条总结成2到5个字,总共二十多个 字,可以像背诗一样,很容易记住: 一外、九同、六递、十四交 三二同B外、五四同C外、十五C内、八C外 详细解读及图表可参考下文,图表均摘自国标。
精选2021版课件
1
8条判异准则详解
故障,原料不合格 ➢ 检验方法或标准变化 ➢ 计算错误,测量误差
精选2021版课件
4
六递:连续6点递增或递减
异常原因: 工具逐渐磨损,维护水平逐渐降 低,操作人员技能逐渐提高
精选2021版课件
5
十四交:连续14点中 相邻点交替上下
异常原因: 白夜班交替,交替使用两不同机 台,两个不同供应商查明原因,采取措施,加以消除,不再出现,纳入标准
精选2021版课件
2
一外:一个点落在A区以外
异常原因: ➢ 新操作人员,方法不对,机器
故障,原料不合格 ➢ 检验方法或标准变化 ➢ 计算错误,测量误差
精选2021版课件
3
九同:连续9点落在中心线同一侧
异常原因: ➢ 新操作人员,方法不对,机器
➢一外:1个点落在A区以外 ➢九同:连续9点落在中心线同一侧 ➢六递:连续6点递增或递减 ➢十四交:连续14点中相邻点交替上下 ➢三二同B外:连续3点中有2点落在中心线同一侧的B区外 ➢五四同C外:连续5点中有4点落在中心线同一侧的C区外 ➢十五C内:连续15点落在中心线两侧的C区以内 ➢八C外: 连续8点落在中心线两侧且无一在C区以内(即在C区以外)
精选2021版课件
6
三二同B外:连续3点中有2点 落在中心线同一侧的B区以外
异常原因: ➢ 新操作人员,方法不对,机器
- 1、下载文档前请自行甄别文档内容的完整性,平台不提供额外的编辑、内容补充、找答案等附加服务。
- 2、"仅部分预览"的文档,不可在线预览部分如存在完整性等问题,可反馈申请退款(可完整预览的文档不适用该条件!)。
- 3、如文档侵犯您的权益,请联系客服反馈,我们会尽快为您处理(人工客服工作时间:9:00-18:30)。
UCL
CL
LCL
4-5
中心化倾向
把中心线(CL)与管理界限间的宽幅3等分,若大部分点子处在 中央2个宽幅内时,通常15点连续时可判定为异常。
UCL
CL
LCL
●此时,与其说工程异常,群构成上存在的问题更多。 ●特别是,群内混在平均值明显不同的数据,或者群内变动明显比 群间变动大的情况会出现此样现象。 ●再者,测试异常或有意识的修改数据时也会有此现象。 ●此时,需要修改群构成。
4-1
点子越出管理界限时(管理out)
点子处在管理上限(UCL)的上面,或处在管理下限(LCL)的下面时。 正处在管理界限上时可判定为异常(out)。
UCL
CL
LCL
●此时可预想的异常原因: 机器发生了突发异常或者机器磨损严重导致机器装置失灵等
4-2
出现7点以上的连
点子连续排列在中心线的(CL:严密讲应利用上下同数的中央值, 但实际上用CL判定也可)排列在中心线的上方或下方时称为连。 若出现7点以上的连时可判定为异常 (JIS Z 9021:1998新规定连的异常判定7连→9连。 但因为SPC参考手册尚未有变动因此继续适用7连异常判定)
UCL 長 さ8の 連 CL 長 さ7の 連
LCL
●此时可预想的异常原因有:1.材料Lot(新品,原料)的变更.2.机械 装置异常(设备异常或工装松动),引发的平均值的变化。 ●另外,还有测量系统变化(新检查员或量具)或计测方法的异常。
4-3
7点连续上升或下降的倾向
有7点连续上升或下降倾向时可判定为异常。 (JIS Z 9021:1998年新规定由7点→6点。 但因为SPC参考手册尚未有变动因此继续适用7连异常判定)
4-6
有周期性时
有周期性时
UCL
CL
LCL
此时,需要技术性追究发生周期的原因,有必要慎重判断是否 处在管理状态下。 掌握周期原因,但工程能力充分,而且为排除异常原因所需的费用 较多时也可以判定为处在管理状态下。 可能的原因:1.操作人员疲劳;2. 原材料发送有问题;3.热积累或 应力积累。
UCL
CL
LCL 連 続 7点 上 昇 傾 向 連 続 7点 下 降 傾 向
●此时可预想的原因有,发生某种劣化或消耗,平均值理界限
若把中心线(CL)与管理界限间的宽幅3等分时,处在最外侧的 范围内若有3点中的2点时可判为异常。 3点中2点处在外侧的情况很多。图上所示的情况都可判定 为异常。
为了对工程进行及时有效的控制,各位工程担当 一定要清楚控制图的判定标准,有异常发生后一定要 注明发生的原因以及对策!切记!切记! (12月份公司内审,SPC就是不符合项目) 控制图符合下列各点之一判稳定: (1)连续 25 个点,界外点数 d = 0, (2)连续 35 个点,界外点数 d ≤ 1, (3)连续 100 个点,界外点数 d ≤2。