甲醇回收塔结构设计说明
化工原理课程设计甲醇填料吸收塔设计

投资估算及经济效益分析
投资估算
根据甲醇填料吸收塔的设计方案,对设备、材料、安装、调试等各方面的费用进行详细估算,以确保投资预算的 准确性。
经济效益分析
通过对比不同设计方案的经济效益,包括投资回报率、净现值、内部收益率等指标,评估甲醇填料吸收塔的经济 效益,为决策提供依据。
环保法规遵守情况说明
在甲醇吸收塔周围设置防火墙或 防火带,防止火灾蔓延。同时, 塔体上应设置明显的安全警示标 志和灭火器材。
防爆措施
对于可能存在爆炸危险的区域, 应采取相应的防爆措施,如设置 防爆门、防爆窗等。此外,还应 对塔体进行定期检查和维修,确 保设备完好无损。
防毒措施
甲醇具有一定的毒性,因此在设 计过程中应采取相应的防毒措施 。例如,在塔体上设置排风口和 通风设备,确保空气流通;工作 人员在操作时应佩戴防毒面具和 防护服等个人防护用品。
化工原理课程设计甲 醇填料吸收塔设计
目录
• 课程设计背景与目的 • 甲醇填料吸收塔基本原理 • 设计方案制定与参数选择
目录
• 工艺流程设计与优化 • 设备布置与管道设计 • 控制系统设计与实现 • 经济评价与环保考虑
01
课程设计背景与目的
化工原理课程设计意义
01 02
理论与实践结合
化工原理课程设计是连接化工理论学习与工程实践的重要桥梁,通过课 程设计,学生可以将所学的化工原理知识应用于实际工程问题中,加深 对理论知识的理解和掌握。
塔内件设计与优化
通过对塔内件(如分布器、收集器、再分布器等)的设计和优化,实现气液均匀分布、减少返混和降低压降等目标, 从而提高吸收效率和降低能耗。
操作条件优化
通过对操作条件(如温度、压力、流量等)的优化,使吸收塔在最佳工况下运行,提高吸收效率和产品 质量,降低能耗和废弃物排放。
填料塔毕业设计--甲醇回收填料精馏塔设计(含外文翻译)

目录摘要 (Ⅲ)Abstract (Ⅳ)第1章前言 (1)第2章流程确定和说明 (2)2.1加料方式 (2)2.2进料状况 (2)2.3塔顶冷凝方式 (2)2.4回流方式 (2)2.5加热方式 (2)2.6加热器 (3)第3章精馏塔设计计算 (4)3.1操作条件与基础数据 (4)3.2精馏塔工艺计算 (6)3.3精馏塔主要工艺设计 (11)3.4填料的选择 (15)3.5塔径设计计算 (16)3.6填料层高度计算 (17)第4章塔附件的选型与设计 (19)4.1冷凝器 (19)4.2加热器 (19)4.3塔内管径的计算及选择 (19)4.4液体分布器 (20)4.5填料支承板的选择 (21)4.6塔釜设计 (21)4.7裙座设计 (22)4.8吊柱 (22)4.9人孔 (22)4.10法兰 (22)4.11除沫器 (23)第5章塔总体高度设计 (25)5.1塔顶部空间高度 (25)5.2进料部位空间高度 (25)5.3塔立体高度 (25)第6章塔设备的机械设计 (26)6.1设计条件 (26)6.2按压力计算筒体和封头厚度 (26)6.3塔的质量计算 (27)6.4塔的自振周期计算 (28)6.5地震载荷计算 (29)6.6风载荷计算 (30)6.7各种载荷引起的轴向应力 (32)6.8筒体和裙座危险截面的强度与稳定性校核 (34)6.9筒体和裙座水压试验应力校核 (35)6.10基础环设计 (37)6.11地脚螺栓计算 (38)6.12开孔补强 (40)参考文献 (42)致谢 (43)附录1 (44)附录2 (47)甲醇回收填料精馏塔设计摘要精馏是借助回流技术来实现高纯度和高回收率的分离操作,在抗生素药物生产中,需要用甲醇溶媒洗涤晶体,洗涤过滤后产生废甲醇溶媒,然后对甲醇溶媒进行精馏,从而将甲醇进行回收利用。
精馏操作一般在塔设备中进行,塔设备分为两种,板式塔和填料塔。
填料塔结构简单、装置灵活、压降小、持液量少、生产能力大、分离效率高、耐腐蚀,且易于处理易起泡、易热敏、易结垢物系。
甲醇合成塔介绍

来??源:百川资讯更新时间:2011-09-0116:17【打印】【收藏】
关键字:甲醇?合成塔
摘??要:甲醇合成塔设计的关键技术之一就是要高效移走和利用甲醇合成反应所放出的巨大热量。
甲醇合成塔设计的关键技术之一就是要高效移走和利用甲醇
热性和热稳定性较好,反应温度接近等温,易于控制,一氧化碳与二氧化碳的单程转化率和气相产物中的甲醇百分含量高于传统的气-固相催化法。
及时甲醇市场资讯,欢迎登陆百川资讯甲醇频道。
更多甲醇相关常识,欢迎进入百川资讯甲醇常识中心。
甲醇回收塔设计优化
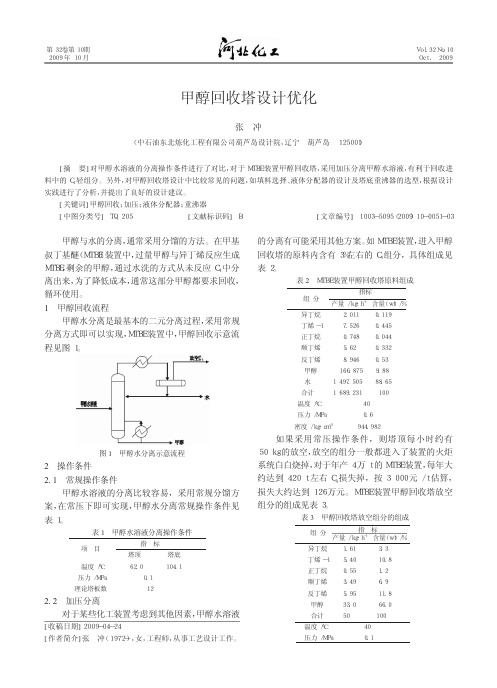
图 2 甲醇回收塔滴盘式分配器
滴盘式分配器在直径较小的塔中经常采用。通过 改变盘内孔径的尺寸和数目,可以适用于不同的液体 流率。该分配器固定在塔壁的支耳上,升气管可以是 圆形的,也可以是矩形的或方形的,气相向上流经立 式的升气管。液相通过盘上的小孔实现均匀的分布。
冲功能有限,而且由于汽液混合返回口朝下,直接冲
再循环式热虹吸重沸器有水平式,也有立式。水 击塔底液面,几方面不利因素综合作用造成液位的波
平式重沸器通常采用壳程沸腾,而立式的通常采用管 动。所以对于小直径分馏塔底的重沸器设计时应优先
程沸腾。在化工生产中,受尺寸限制一般采用水平式 选用一次通过式或其他形式。必须选用水平式再循环
滴盘式分配器从结构上来看,存在一个小的缺 点。滴盘式分配器液体分配的小孔在分配器的最底 端,而且孔径一般都较小,为 2~5 mm 左右,甲醇回收 塔设计时孔径为 3 mm。当处理介质清洁时,该分配器 能实现很好的汽液分配;但当系统中存在污垢时,分 配器底部的小孔非常容易发生堵塞,而引起液体分配 的不均。在某次设计的 MTBE 装置刚开工的过程中,由 于系统吹扫得不彻底,导致管路的部分污垢进入甲醇 回收塔,造成进料及回流入口的分配器堵塞,影响了 装置的开车。所以对于此类填料塔的设计,可以考虑 在进料及回流的管路上,在靠近塔处设置过滤设施, 防止不可预见的污垢进入塔内,影响分配器的正常工 作。
如果采用常压操作条件,则塔顶每小时约有
50 kg 的放空,放空的组分一般都进入了装置的火炬
系统白白烧掉,对于年产 4 万 t 的 MTBE 装置,每年大
约达到 420 t 左右 C4 损失掉,按 3 000 元 /t 估算, 损失大约达到 126 万元。MTBE 装置甲醇回收塔放空
甲醇合成塔介绍
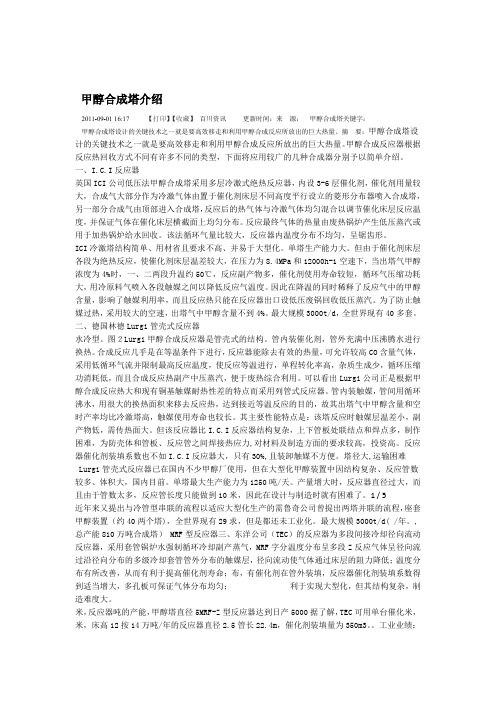
甲醇合成塔介绍2011-09-01 16:17 【打印】【收藏】百川资讯更新时间:来源:甲醇合成塔关键字:甲醇合成塔设计的关键技术之一就是要高效移走和利用甲醇合成反应所放出的巨大热量。
摘要:甲醇合成塔设计的关键技术之一就是要高效移走和利用甲醇合成反应所放出的巨大热量。
甲醇合成反应器根据反应热回收方式不同有许多不同的类型,下面将应用较广的几种合成器分别予以简单介绍。
一、I.C.I反应器英国ICI公司低压法甲醇合成塔采用多层冷激式绝热反应器,内设3-6层催化剂,催化剂用量较大,合成气大部分作为冷激气体由置于催化剂床层不同高度平行设立的菱形分布器喷入合成塔,另一部分合成气由顶部进入合成塔,反应后的热气体与冷激气体均匀混合以调节催化床层反应温度,并保证气体在催化床层横截面上均匀分布。
反应最终气体的热量由废热锅炉产生低压蒸汽或用于加热锅炉给水回收。
该法循环气量比较大,反应器内温度分布不均匀,呈锯齿形。
ICI冷激塔结构简单、用材省且要求不高、并易于大型化。
单塔生产能力大。
但由于催化剂床层各段为绝热反应,使催化剂床层温差较大,在压力为8.4MPa和12000h-1空速下,当出塔气甲醇浓度为4%时,一、二两段升温约50℃,反应副产物多,催化剂使用寿命较短,循环气压缩功耗大,用冷原料气喷入各段触媒之间以降低反应气温度。
因此在降温的同时稀释了反应气中的甲醇含量,影响了触媒利用率,而且反应热只能在反应器出口设低压废锅回收低压蒸汽。
为了防止触媒过热,采用较大的空速,出塔气中甲醇含量不到4%。
最大规模3000t/d,全世界现有40多套。
二、德国林德Lurgi管壳式反应器水冷型。
图2Lurgi甲醇合成反应器是管壳式的结构。
管内装催化剂,管外充满中压沸腾水进行换热。
合成反应几乎是在等温条件下进行,反应器能除去有效的热量,可允许较高CO含量气体,采用低循环气流并限制最高反应温度,使反应等温进行,单程转化率高,杂质生成少,循环压缩功消耗低,而且合成反应热副产中压蒸汽,便于废热综合利用。
合成甲醇回收塔操作规程
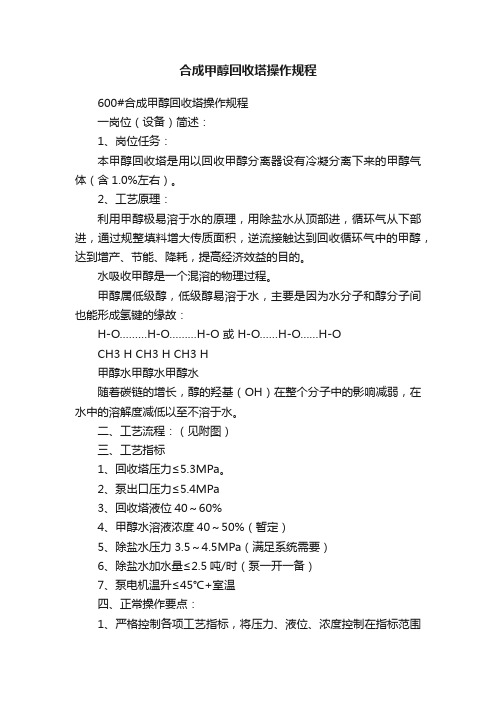
合成甲醇回收塔操作规程600#合成甲醇回收塔操作规程一岗位(设备)简述:1、岗位任务:本甲醇回收塔是用以回收甲醇分离器设有冷凝分离下来的甲醇气体(含1.0%左右)。
2、工艺原理:利用甲醇极易溶于水的原理,用除盐水从顶部进,循环气从下部进,通过规整填料增大传质面积,逆流接触达到回收循环气中的甲醇,达到增产、节能、降耗,提高经济效益的目的。
水吸收甲醇是一个混溶的物理过程。
甲醇属低级醇,低级醇易溶于水,主要是因为水分子和醇分子间也能形成氢键的缘故:H-O………H-O………H-O 或 H-O……H-O……H-OCH3 H CH3 H CH3 H甲醇水甲醇水甲醇水随着碳链的增长,醇的羟基(OH)在整个分子中的影响减弱,在水中的溶解度减低以至不溶于水。
二、工艺流程:(见附图)三、工艺指标1、回收塔压力≤5.3MPa。
2、泵出口压力≤5.4MPa3、回收塔液位40~60%4、甲醇水溶液浓度40~50%(暂定)5、除盐水压力3.5~4.5MPa(满足系统需要)6、除盐水加水量≤2.5吨/时(泵一开一备)7、泵电机温升≤45℃+室温四、正常操作要点:1、严格控制各项工艺指标,将压力、液位、浓度控制在指标范围内。
2、保证往复式水泵的正常运转,用“看、听、摸、闻”的方法,注意电机、机器响声,温度是否正常。
注意克服跑冒滴漏,尤其是柱塞填料的泄漏要经济检查(一小时一次)。
3、注意调节流量:根据负荷的大小,调节甲醇水溶液浓度,如负荷降低,甲分出口气体中CH3OH含量低,回收浓度低,可部份打循环或全打循环。
即关小(或关死)溶液出口调节阀,开(或开大),回收塔出口至泵进口阀门循环,在一般正常生产,为保证足够的喷啉密度,应部份打循环。
即一边进水,一边循环一边放料(甲醇水溶液)入闪蒸槽。
保证水溶液的浓度,保证精馏系统水不过剩(水平衡)。
即回收塔加入水量不得超过(最好相等)在相同负荷下精馏加的萃取水量。
4、注意泵的压力在正常生产中,不必人为控制,泵的压力是随回收塔或系统压力的升降而升降。
MTBE装置甲醇回收塔再沸器出口管系的柔性设计
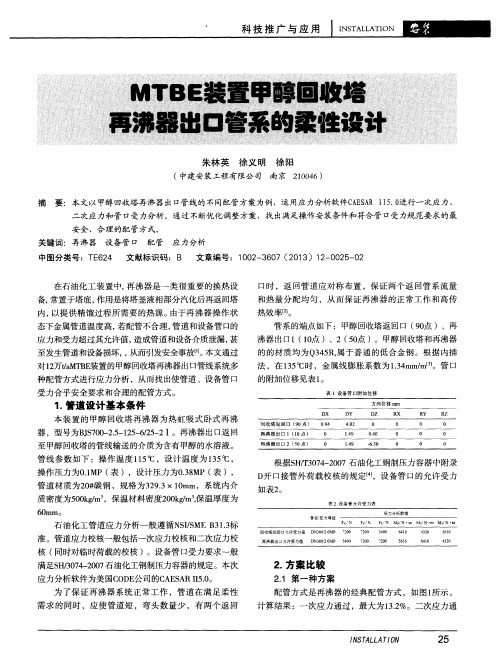
用
l I N S T A L L A T I O N
朱林英
徐义 明
徐 阳
( 中建安装工程有 限公 司 南京 2 1 0 0 4 6)
摘
要 :本文 以 甲醇回收塔 再沸器 出口管线 的不同配管方案 为例 ,运 用应力分析软件C A E S A R I I 5 . 0 进行一次应 力、 二 次应 力和管 1 : 2 受 力分析 。通 过不断优 化调整方案 ,找 出满足操作 安装条件和符合管 口受 力规 范要求 的最
高效工作 。因此决 定修改 再沸器 的设备管 口设计条件 ,
将再沸器管 口法 兰压力等级 由2 . 0 MP 等级提高到5 . 0 MP 等 级 ,其余 均不改变 。通过再沸器设备管 口条件 的改进, 以 满足S H  ̄3 0 7 4 — 2 0 0 7 的规定 ( 管 口允许 受力见表6),同
准 。管道应 力校核一般包 括一次应力校核和二次应力校
核 ( 同时对 临时荷 载的校核 )。设备管 口受力要求一般
满足S H / 3 0 7 4 — 2 0 0 7 石 油化工钢制压力容器 的规定 。本次
应力分析软 件为美国C O D E 公 司的C A E S A R I I 5 . 0 。
的的材质 均为 Q 3 4 5 R , 属 于普通 的低合 金钢 。根据 内插 法 ,在 1 3 5 o C 时 ,金 属线膨胀 系数为 1 . 3 4 m m / m[ 。管 口
的附加位移见表 1 。
表 1设备管 口附加位移
1 . 管道设计基本条件
本 装置 的 甲醇 回收 塔再 沸器 为热 虹 吸式 卧式再 沸
图1再沸器 出口管道配管方案一
甲醇回收成套装置之甲醇填料回收塔设计

甲醇回收成套装置之甲醇填料回收塔设计甲醇回收装置⼯艺流程⽅框图信阳市某制药⼚酸性废⽔回收甲醇之填料精馏塔设计1 设计条件:1.1 设计压⼒: 1.0MPa;1.2 设计温度:200℃;1.3 设计处理能⼒:5000(6000;8000)kg/h;1.4 要求达到技术指标:塔顶产品: 回收甲醇≥99% ,⽔份≤0.4%;塔底稀酸中含甲醇≤100ppm(wt)。
1.6 蒸汽:压⼒0.4~0.7Mpa温度151℃~170℃2 技术要求:2.1 进料量:5000(6000;8000)kg/h2.2 回收甲醇≥99% ,⽔份≤0.4%;稀酸中含甲醇≤100ppm(wt)。
2.3 系统蒸汽消耗保证值:每⼩时处理吨酸性废⽔消耗0.6Mpa压⼒的饱和蒸汽1.28吨。
2.4 装置负荷可调范围为30% 120%,并装置确保蒸汽在0.4Mpa压⼒、151℃的⼯况下,满⾜上述装置能⼒与负荷可调范围。
3 设计内容:3.1.设计⽅案的确定及流程说明3.2.塔的⼯艺计算3.3.塔和填料主要⼯艺尺⼨的设计计算3.4.设计结果概要或设计⼀览表3.5.塔附属设备的选型与计算3.6.图纸及技术资料的提供:带控制节点的⽣产⼯艺流程图、回收塔⼯艺条件图3.7.对设计的评述或有关问题的分析讨论3.8.编制设计说明书信阳市某制药⼚酸性废⽔回收甲醇之板式精馏塔设计。
1 设计条件:1.1 设计压⼒: 1.0MPa;1.2 设计温度:200℃;1.3 设计处理能⼒: 5000(6000;8000)kg/h;1.4 要求达到技术指标:塔顶产品: 回收甲醇≥99% ,⽔份≤0.4%;塔底稀酸中含甲醇≤100ppm(wt)。
1.6 蒸汽:压⼒0.4~0.7Mpa温度151℃~170℃2技术要求:2.1 进料量:5000(6000;8000)kg/h 。
2.2 回收甲醇≥99% ,⽔份≤0.4%;稀酸中含甲醇≤100ppm(wt)。
2.3 系统蒸汽消耗保证值:每⼩时处理吨酸性废⽔消耗0.6Mpa压⼒的饱和蒸汽1.28吨。
- 1、下载文档前请自行甄别文档内容的完整性,平台不提供额外的编辑、内容补充、找答案等附加服务。
- 2、"仅部分预览"的文档,不可在线预览部分如存在完整性等问题,可反馈申请退款(可完整预览的文档不适用该条件!)。
- 3、如文档侵犯您的权益,请联系客服反馈,我们会尽快为您处理(人工客服工作时间:9:00-18:30)。
甲醇回收塔结构设计第一章概述1.1前言在化工、炼油、医药、食品及环境保护等工业部门,塔设备是一种重要的单元操作设备。
它的应用面广、量大。
塔设备广泛用于蒸馏、吸收(气提)、萃取、气体的洗涤、增湿及冷却等单元操作中,它的操作性能好坏,对整个装置生产,产品产量、质量、成本以及环境保护、“三废”处理等都有较大的影响。
因此对塔设备的研究一直是工程界所关注的热点。
塔器按其结构可分为两大类:板式塔和填料塔。
板式塔的研究起步较早,其流体力学和传质模型比较成熟,数据可靠,因而70年代以前的很长一段时间里,板式塔的研究处于领先地位。
70年代,由于性能优良的新型填料相继问世,特别是规整填料及新型塔内件的不断开发应用和基础理论研究的不断深入,使填料塔的放大技术有了新的突破,改变了以板式塔为主的局面,填料塔也进入了一个崭新的时期。
本次设计任务是分离甲醇水的混合液,以回收甲醇,塔径DN400已定,且处理量不算很大,故采用填料塔。
1.2甲醇回收塔的设计背景本次任务设计的甲醇回收塔是针对工厂废液等的进行甲醇提纯回收,不仅能有效的保护环境,还能回收有用产品,节约能源,是一件大有裨益的事。
二十多年来,填料塔以其优良的综合性能不断推广应用于工业生产中,改变了板式塔长期占据统治地位的局面。
与板式塔相比,新型的填料塔性能具有如下特点:(1)生产能力大板式塔与填料塔的流体流动和传质机理不同。
板式塔的传质通过上升的蒸汽穿过板上的液池来实现。
塔板的开孔率一般占塔板截面积的8~15%,其优化设计要考虑塔板面积与降液管面积的平衡,否则即使开孔率大也不会使生产能力提高。
填料塔的传质是通过上升蒸汽的与靠重力沿填料表面下降的液体逆流接触实现。
填料塔的开孔率通常在50%以上,其空隙率则超过90%,一般液泛点都较高,其优化设计主要考虑与塔内件的匹配,若塔设计合理,填料塔的生产能力一般均高于板式塔。
(2)分离效率高塔的分离效率决定于分离物系的性质、操作状态(压力、温度、流量等)以及塔的类型及性能。
一般情况下下,填料塔具有较高的分离效率,但其效率会随着操作状态的变化而变化。
(3)压力降小填料塔由于空隙率较高,故其压降远远小于板式塔。
一般情况下,塔的每个理论级的压降,板式塔为0.4~1.1kPa;散装填料为0.013~0.27kPa;规整填料为0.01~1.07kPa。
压降低,对于新塔可以大幅度降低塔高,减小塔径;对于老他可以减小回流比以求节能或提高产量与产品质量。
(4)操作弹性大操作弹性是指塔对符合的适应性。
塔正常操作负荷的变动范围越宽,则操作弹性越大。
由于填料本身对负荷变化的适应性很大,故填料塔的操作弹性决定于塔内件的设计,特别是液体分布器的设计,因而可以根据实际需要确定填料塔的操作弹性。
而板式塔的操作弹性则受到塔板液泛、雾沫夹带及降液管能力的限制,一般操作弹性较小。
(5)持液量小持液量是指塔在正常操作时填料表面、内件或塔板上所持有的液量,它随操作负荷的变化而有增减。
对于填料塔,持液量一般小于6%,而板式塔则高达8%~12%。
持液量大,会加长开工时间。
填料塔较板式塔优点很多,但造价通常高于板式塔。
1.3回收塔主要工艺流程(1)进料状况进料状况一般有泡点进料、露点进料、气-液混合物进料、过冷液体进料、过热蒸汽进料。
此次设计采用泡点进料。
采用泡点进料,不仅对稳定塔操作较为方便,且不受季节气候温度影响。
泡点进料时基于恒摩尔流假定精馏段和提馏段塔径基本相等,制造上较为方便。
(2)塔顶冷凝方式塔顶冷凝采用全凝器,用水冷凝,甲醇和水不反应,且容易冷凝,故采用全凝器。
塔顶出来的气体温度不高,冷凝后回流液和产品温度不高无需进一步冷却。
此次分离是要得到液体甲醇,故选用全凝器符合要求。
(3)回流方式回流方式可分为重力回流和强制回流。
对于小型塔,回流冷凝器一般安装在塔顶。
其优点是回流冷凝器无需支撑结构,缺点是回流冷凝器回流控制较难。
本次任务是针对小型塔,采用重力回流。
(4)加热方式加热方式可分为直接蒸汽和间接蒸汽加热。
直接蒸汽加热是用蒸汽直接由塔底进入塔内。
由于重组分是水,故省略加热装置。
间接蒸汽加热是通过加热器使釜液部分汽化,上升蒸汽与回流下来的冷液进行传质。
本次任务用间接蒸汽加热,由于塔径较小,采用内置盘管再沸器,用水蒸气作加热介质。
1.4基础数据及设计内容(1)基础数据:进料流量 2500kg/h ; 料液组成含甲醇50%,塔顶组成含甲醇99.5%,残液含甲醇2%;精馏塔直径400Φ,设计压力0.65MPa ,设计温度105℃;再沸器直径1000Φ,管内压力0.6MPa ,设计温度158℃。
(2)设计方案根据设计要求,对精馏装置的流程、操作条件、主要设备及其材料的选取等进行叙述。
(3)精馏塔工艺计算。
物料衡算,能量衡算,理论塔板数的计算,工艺条件和相关物性数据的查阅及计算(4)塔体的主要工艺尺寸的设计计算。
塔径的计算,填料层高度的计算,填料层压降的计算以及塔内件的设计计算,塔的附属设备的计算。
(5)精馏塔设备设计及选型塔体材料材料选取,壁厚计算,封头的选型,精馏塔各部分高度、质量的计算及塔体的连接形式,地震载荷、风载荷的计算校核及应力校核,手孔、接管及开孔补强的计算,裙座和基础环的设计。
第二章 精馏塔工艺计算2.1精馏塔的物料衡算(1)原料液及塔顶、塔底产品的摩尔分率 甲醇的摩尔质量 32.04/A M kg kmol = 水的摩尔质量 18.02/B M kg kmol = 进料含甲醇 50%(w ) 塔顶含甲醇 99.5%(w ) 塔底含甲醇 2%(w ) 摩尔分数:0.5/32.040.3600.5/32.040.5/18.02F x ==+0.995/32.040.9910.995/32.040.005/18.02D x ==+0.02/32.040.0110.02/32.040.98/18.02W x ==+(2)原料液及塔顶、塔底的平均摩尔质量0.36032.04(10.360)18.0223.07/F M kg kmol =⨯+-⨯=0.99132.04(10.991)18.0231.91/D M kg kmol =⨯+-⨯= 0.01132.04(10.011)18.0218.17/W M kg kmol =⨯+-⨯=(3)物料衡算已知进料流量为2500/kg h ,换算成摩尔处理量 2500108.366/23.07F kmol h == 全塔物料衡算:WD F Wx Dx Fx W D F +=+=,38.592/D kmol h =,69.774/W kmol h =2.2理论塔板数2.2.1相对挥发度由()()11A A A A x y x y α-=-,再根据表1[]2数据可得到不同温度下的挥发度,见表2 表2.1 水—甲醇体系的平衡数据表2.2所以 4.20m α==2.2.2最小回流比及操作回流比泡点进料:0.360q F x x == ()()4.200.3600.703111 4.2010.360m F q m F x y x αα⨯===+-+-⨯故最小回流比为 min 0.9910.7030.8400.7030.360D q q qx y R y x --===--取操作回流比为min 220.840 1.680R R ==⨯=2.2.3精馏塔的气、液相负荷精馏段: 1.86038.59271.781/L R kmol h ==⨯= ()1 2.86038.592110.373/V R D kmol h =+=⨯= 提馏段:71.781108.366180.147/L L F kmol h '=+=+= 110.373/V V kmol h '==2.2.4操作线方程精馏段操作线方程:()10.6500.34711D n n n x Ry x x a R R +=+=+++提馏段操作线方程:1 1.6320.007nn m L Wy x x V V +''=-=-''2.2.5逐板法求理论塔板数由()11q q qx y x αα=+-,得()()1yx b y αα=--将 4.20α=代入得相平衡方程:()()1 4.20 3.20yyx c yyαα==---联立(a )、(b )、(c )三式,可至上而下逐板计算所需理论板数。
因为塔顶为全凝,则10.991D y x == 由(c )式求的第一块板下降液体组成1110.9910.9634.20 3.20 4.20 3.200.991y x y ===--⨯同理得表2.3精馏塔理论塔板数: 10T N = (包括再沸器) 进料板位置: 6F N =2.3实际塔板数2.3.1 液相平均粘度(1)进料粘度:根据表1,用内插法求得 79.8F t C =o查手册[]2得 0.278A u mPa s =⋅ 0.365B u mPa s =⋅()()lg 0.251lg 0.2780.749lg 0.365LF u =+ 0.341F u mPa s =⋅(2)塔顶物料粘度:根据表1,用内插法求得 64.6D t C =o查手册得 0.329A u mPa s =⋅ 0.438B u mPa s =⋅()()lg 0.991lg 0.3290.009lg 0.438LD u =+0.330F u mPa s =⋅(3)塔釜物料粘度:根据表1,用内插法求得 98.0W t C =o查手册得 0.233A u mPa s =⋅ 0.289B u mPa s =⋅()()lg 0.011lg 0.2330.989lg 0.289LD u =+0.288F u mPa s =⋅精馏段液相平均粘度:0.3410.3300.33622LD LF u u u mPa s ++===⋅精 提馏段液相平均粘度:0.2880.3300.31522LW LF u u u mPa s ++===⋅提2.3.2 精馏段和提馏段的相对挥发度查表2得: 5.055F α=, 2.397D α=,7.720W α=精馏段的平均挥发度: 3.481α==精精馏段的平均挥发度: 6.247α==提2.3.3 全塔效率T E 和实际塔板数全塔效率可用奥尔康公式:()0.2450.49T L E u α-=精馏段:()0.2450.493.4810.3410.470T E -=⨯= 提馏段:()0.2450.496.2470.3150.415T E -=⨯=精馏段实际板层数:5110.47T T N N E ==≈精块 精馏段实际板层数:5130.415T T N N E '==≈提块2.4精馏塔的工艺条件及物性数据2.4.1 工艺条件塔顶压力:101.3P kPa =操作温度:塔顶 64.6D t C =o塔釜 98.0W t C =o进料 79.8F t C =o精馏段平均温度:64.679.872.222D F t t t C ++===o 精 提馏段平均温度:98.079.888.922W F t t t C ++===o 精2.4.2 平均摩尔质量(1)塔顶平均摩尔质量10.991D x y ==,10.963x =()0.99132.0410.99118.0231.91/VD M kg kmol =⨯+-⨯= ()0.96332.0410.96318.0231.52/LD M kg kmol =⨯+-⨯=(2)进料板层平均摩尔质量0.584F y =,10.251x =()0.58432.0410.58418.0226.21/VF M kg kmol =⨯+-⨯= ()0.25132.0410.25118.0221.54/LF M kg kmol =⨯+-⨯=(3)塔底层平均摩尔质量0.045W y =,0.011W x =()0.04532.0410.04518.0218.65/VW M kg kmol =⨯+-⨯=()0.01132.0410.01118.0218.17/LW M kg kmol =⨯+-⨯=(4)精馏段平均摩尔质量()31.9126.21/229.06/VJ M kg kmol =+= ()31.5221.54/226.53/LJ M kg kmol =+=(5)精馏段平均质量流量/71.78126.531904.35/J LJ A L DRM M kg h ==⨯=()1/110.37329.063207.44/J VJ A G D R M M kg h =+=⨯=(6)提馏段液体平均摩尔组成()()/20.2510.011/20.131T F W x x x =+=+= (7)提馏段中液体平均摩尔质量()(),132.040.13118.0210.13119.86/x T A T B T M M x M x kg kmol=⨯+-=⨯+⨯-=(8)提馏段中液体平均质量流量,,//71.78119.86108.36619.863577.72/T x T A x T BL L M M F M M kg h=⨯+⨯=⨯+⨯= (9)提馏段蒸汽平均摩尔组成()()/20.5840.045/20.3145T F W Y Y Y =+=+= (10)提馏段中液体平均摩尔质量()(),132.040.314518.0210.314522.43/y T A T B T M M y M y kg kmol=⨯+-=⨯+⨯-=(11)提馏段中液体平均质量流量 ,110.37322.432475.67/T y T L V M kg h'=⨯=⨯=2.4.3 平均密度(1)气相平均密度计算72.2t C =oJ 88.9t C =oT(a)精馏段蒸汽密度()(),003/22.4/29.06/22.4273.15/273.1572.21.03/T J J M T T t kg m ρ=⨯+⎡⎤⎣⎦=⨯+=Y,J (b)提馏段的蒸汽密度()(),003/22.4/22.43/22.4273.15/273.1588.90.76/T T T M T T t kg m ρ=⨯+⎡⎤⎣⎦=⨯+=Y,T (2)液相平均密度计算液相平均密度依下列式计算1iLmiαρρ=∑表2.4 不同温度下甲醇和水的密度(3)塔顶液相平均密度计算64.6D t C =o根据表3得,3755.65/A kg m ρ=,3981.41/B kg m ρ=()31/0.991/755.650.009/981.41756.52/LDm kg m ρ=+= (4)进料板液相平均密度计算79.8F t C =o根据表3得,3737.64/A kg m ρ=,3971.91/B kg m ρ=0.25132.040.3730.25132.040.74918.02A α⨯==⨯+⨯()31/0.373/737.640.627/971.91868.97/LFm kg m ρ=+=(5)塔底液相平均密度接近水的密度,98.0W t C =o ,3959.79/B kg m ρ=精馏段液相平均密度:()3756.52868.97/2812.75/LJ kg m ρ=+= 提馏段液相平均密度; ()3868.97959.79/2962.40/LT kg m ρ=+=2.4.4 液体平均表面张力液相平均表面张力依下式计算:Lm i i x δδ=∑ (1) 塔顶液相平均表面张力计算64.6D t C =o查手册[]2得16.803/A mN m δ=,65.361/B mN m δ=0.99116.8030.00965.36117.24/LDm mN m δ=⨯+⨯= (2)进料板液相平均表面张力计算79.8F t C =o查手册[]2得15.063/A mN m δ=,62.636/B mN m δ=0.25115.0630.74962.63650.695/LDm mN m δ=⨯+⨯=(3)釜底液相平均表面张力接近水的表面张力,98.0W t C =o,查得59.270/B mN m δ=精馏段液相平均表面张力:()17.2450.695/233.968/LJ mN m δ=+=提馏段液相平均表面张力; ()59.27050.695/254.983/LT mN m δ=+=2.4.5精馏塔各段物性参数汇总(1)塔顶、进料板、塔釜数据结果汇总: 表2.5 塔顶、进料板、塔釜的物性参数(2)精馏段、提馏段数据结果:表2.6 精馏段、提馏段的物性参数2.5热量衡算2.5.1加热介质和冷却剂 (1)加热介质的选择常用的加热介质有饱和水蒸气和烟道气。