中国水泥窑余热发电技术(新编版)
水泥窑纯低温余热发电技术与装备简介_百度文库

水泥窑纯低温余热发电技术与装备简介、刖言水泥生产过程需要消耗大量的能源和天然矿物,而这些资源是不可再生的,因此制约了水泥工业的可持续发展,降低水泥生产过程中原燃料的消耗是保证水泥工业可持续发展的最有效措施。
水泥熟料煅烧过程需要较高的煅烧温度,消耗大量的天然矿石能源一一煤炭,以目前先进的新型干法水泥窑为例,其单位熟料烧成热耗在2900~3300kJ/kg但同时约占熟料烧成热耗30--40%的热量随废气从窑尾和窑头排入大气,而采用余热发电技术将这部分热量回收是一种非常有效的办法----、华效公司在低温余热发电方面的技术保障能力及业绩公司简介协作单位公司技术力量及外聘技术顾问相关工作业绩三、水泥低温余热发电技术和装备:设计思想A冷却机中部开口,抽取较高温度的废气以提高发电能力。
(由用户选择目前,?窑外分解窑所配套的篦式冷却机出口废气温度多在200r左右,在这种温度下的热量品位较低,?很难进行动力回收,除非窑尾废气温度相当高的特殊情况,一般情况下要对冷却机进行相应的改造。
由于从冷却机各段篦床上逸出的温度是不一样的,可以将这股废气人为地分为两部分,一部分是从冷却机中部逸出的,温度在300C 以上的中温废气,?利用这股废气进行余热动力回收是可行的;另一部分是从冷却机后部逸出的120 C左右的废气,这股废气基本上没有动力回收价值,而且与前一部分废气混合时降低了其热能的品位,使系统的可用能遭受很大的损失。
因此,在冷却机原有废气出口前新开一抽气口,用以抽取冷却机中部逸出的气体进行余热动力回收,原有抽气口抽取冷却机后部废气,两抽气口之间用挡墙相隔,压力的平衡用挡板实现。
设置锅炉旁通烟道,以便锅炉停运时不影响水泥生产。
锅炉出口废气与原抽气口的废气混合后进入电收尘,汇入水泥工艺流程。
B对预热器进行相应改造,由五级换热改为四级换热。
经过认真核算,可实施预热器的改造以提高发电能力,从而提高全厂整体的热利用效率(由用户选择。
水泥企业余热发电技术简介

水泥企业余热发电技术简介
P=1.0MPa时,水加热至Tb=179.9℃才形成蒸汽 P=1.27MPa时,水加热至Tb=191.6℃才形成蒸汽 P=2.45MPa时,水加热至Tb=216.7℃才形成蒸汽 P=0.1MPa时,水加热至Tb=100℃才形成蒸汽 P=0.007MPa时,水加热至Tb=39.2℃才形成蒸汽
水泥企业余热发电技术简介
锅炉
主蒸汽压力 主蒸汽温度 锅炉入口废气量 锅炉入口废气温度 饱和蒸汽焓 饱和水焓 过热器传热面积 蒸发器传热面积 省煤器段给水温度 省煤器出口进汽压力 进汽温度 高压缸效率 排汽压力 排汽温度 实际排汽焓 排汽干度 发电量 汽轮机汽耗 标准煤耗
国内目前的高压火电厂(单机为25~100MW的中型火电厂),发电用蒸汽参 数一般为9.81MPa—550℃,其发电标准煤耗为380~420g/Kwh,转换效率约 为29~33%(反映在汽轮机汽耗率上为:每KWh发电量消耗蒸汽为4.3Kg—汽 机叶片为老红旗叶片);
国内目前的超高压、亚临界火电厂(单机为200~600MW的大型火电厂),发 电用蒸汽参数一般为16~18MPa—555~575℃,其发电标准煤耗为300~ 330g/Kwh,转换效率约为37~41%(反映在汽轮机汽耗率上为:每KWh发电 量消耗蒸汽为3.45Kg—汽机叶片为老红旗叶片);
80年代水泥生产发展新型干法窑为主,由于水泥窑增加了预热器 及分解炉,窑尾烟气温度大幅度降低,对余热发电系统提出了一 个难题,1995年带补燃锅炉余热发电系统在鲁南投入生产,1997 年日本赠送了全套的纯中低温余热发电系统,中国进入了纯低温 余热发电系统时代。
水泥企业余热发电技术简介
1水及水蒸汽的基本知识
水泥企业余热发电技术简介
中国水泥窑余热发电技术
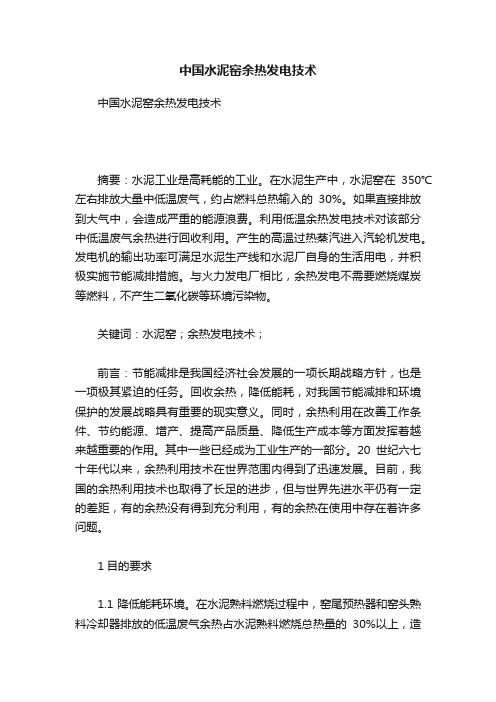
中国水泥窑余热发电技术中国水泥窑余热发电技术摘要:水泥工业是高耗能的工业。
在水泥生产中,水泥窑在350℃左右排放大量中低温废气,约占燃料总热输入的30%。
如果直接排放到大气中,会造成严重的能源浪费。
利用低温余热发电技术对该部分中低温废气余热进行回收利用。
产生的高温过热蒸汽进入汽轮机发电。
发电机的输出功率可满足水泥生产线和水泥厂自身的生活用电,并积极实施节能减排措施。
与火力发电厂相比,余热发电不需要燃烧煤炭等燃料,不产生二氧化碳等环境污染物。
关键词:水泥窑;余热发电技术;前言:节能减排是我国经济社会发展的一项长期战略方针,也是一项极其紧迫的任务。
回收余热,降低能耗,对我国节能减排和环境保护的发展战略具有重要的现实意义。
同时,余热利用在改善工作条件、节约能源、增产、提高产品质量、降低生产成本等方面发挥着越来越重要的作用。
其中一些已经成为工业生产的一部分。
20世纪六七十年代以来,余热利用技术在世界范围内得到了迅速发展。
目前,我国的余热利用技术也取得了长足的进步,但与世界先进水平仍有一定的差距,有的余热没有得到充分利用,有的余热在使用中存在着许多问题。
1目的要求1.1降低能耗环境。
在水泥熟料燃烧过程中,窑尾预热器和窑头熟料冷却器排放的低温废气余热占水泥熟料燃烧总热量的30%以上,造成严重的能源浪费。
一方面,水泥生产消耗大量热能,另一方面,水泥生产也需要大量电力。
将400℃以下低温废气余热转化为电能用于水泥生产,可使水泥熟料生产综合电耗降低60%或30%以上。
对于水泥生产企业来说,可以大大减少从社会发电厂购买的电力,或者大大减少水泥生产企业燃烧的燃料。
自备电厂发电可以大大降低水泥生产的能耗;避免了水泥窑余热直接排入大气的热岛现象;同时可以降低社会发电厂或水泥生产企业自用电厂的燃料消耗,减少CO2等燃烧废弃物的排放,有利于环境保护。
1.2政策的推行提供技术支持。
自然资源如能源、原材料、水、土地等,随着经济的发展,资源有限之间的矛盾越来越明显。
新型干法水泥窑纯低温余热发电技术推广实施方案

新型干法水泥窑纯低温余热发电技术推广实施方案根据新型干法水泥窑纯低温余热发电技术的特点和推广目标,提出以下实施方案:一、技术研发1.成立专业团队:组建由水泥生产技术、热能利用技术、电力工程等方面的专家和研究人员组成的团队,负责相关技术的研发和改进。
2.确定研发目标:明确开发新型干法水泥窑纯低温余热发电技术的核心问题,确定研发目标和技术指标。
3.技术改进和创新:结合国内外先进技术和经验,对传统水泥窑低温余热发电技术进行改进和创新,提高发电效率和能源利用率。
4.试验和验证:在实际水泥生产中建立试验装置,进行试验验证和数据收集,评估新技术在不同情况下的适用性和可行性。
二、示范工程建设1.确定示范项目:选择具备一定规模和条件的水泥生产企业作为示范项目,推广新型干法水泥窑纯低温余热发电技术。
2.设计和建设:由专业设计机构进行整体设计,确保发电系统与水泥生产系统的协同运行,确保发电设施的安全、稳定和高效运行。
3.技术指导和培训:提供相应的技术指导和培训,确保施工人员的技术水平,保证示范工程建设的顺利进行。
4.运行和监控:配备专业的运行和监控人员,确保示范工程的正常运行和设备的安全可靠性。
三、政策支持1.优惠政策:制定相关优惠政策,给予示范项目税收减免、贷款支持和高额补贴等政策支持,降低企业推广新技术的经济负担。
2.奖励措施:对于推广应用新型干法水泥窑纯低温余热发电技术的企业,给予一定的奖励措施,鼓励更多的企业积极参与推广。
3.法律法规:加强相关法律法规的制定和完善,保障新技术推广应用的合法权益,减少推广过程中的法律风险。
四、宣传推广1.宣传活动:通过举办专题研讨会、技术交流会和经验分享会等形式,宣传新型干法水泥窑纯低温余热发电技术的特点和优势,号召更多的企业参与推广。
2.宣传材料:编写相关宣传材料,包括宣传手册、技术指南和案例分析等,向水泥生产企业传播新技术的理念和实践经验。
3.媒体宣传:通过互联网、电视、广播等媒体宣传新技术的推广成果和相关的政策支持,提高新技术的知名度和影响力。
纯低温水泥窑余热发电技术
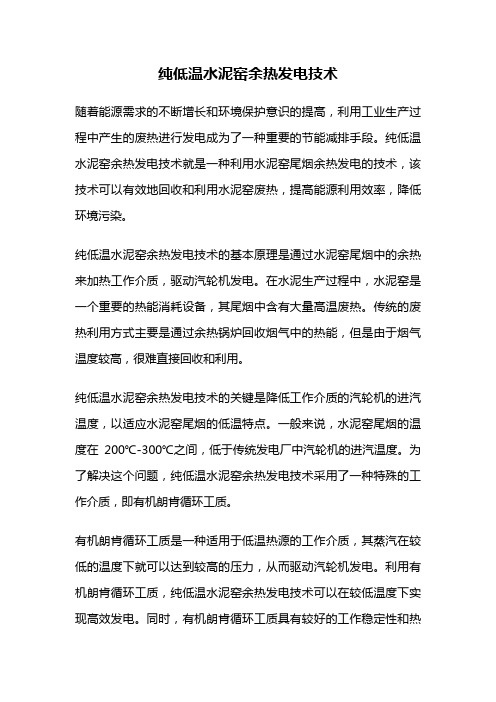
纯低温水泥窑余热发电技术随着能源需求的不断增长和环境保护意识的提高,利用工业生产过程中产生的废热进行发电成为了一种重要的节能减排手段。
纯低温水泥窑余热发电技术就是一种利用水泥窑尾烟余热发电的技术,该技术可以有效地回收和利用水泥窑废热,提高能源利用效率,降低环境污染。
纯低温水泥窑余热发电技术的基本原理是通过水泥窑尾烟中的余热来加热工作介质,驱动汽轮机发电。
在水泥生产过程中,水泥窑是一个重要的热能消耗设备,其尾烟中含有大量高温废热。
传统的废热利用方式主要是通过余热锅炉回收烟气中的热能,但是由于烟气温度较高,很难直接回收和利用。
纯低温水泥窑余热发电技术的关键是降低工作介质的汽轮机的进汽温度,以适应水泥窑尾烟的低温特点。
一般来说,水泥窑尾烟的温度在200℃-300℃之间,低于传统发电厂中汽轮机的进汽温度。
为了解决这个问题,纯低温水泥窑余热发电技术采用了一种特殊的工作介质,即有机朗肯循环工质。
有机朗肯循环工质是一种适用于低温热源的工作介质,其蒸汽在较低的温度下就可以达到较高的压力,从而驱动汽轮机发电。
利用有机朗肯循环工质,纯低温水泥窑余热发电技术可以在较低温度下实现高效发电。
同时,有机朗肯循环工质具有较好的工作稳定性和热传导性能,能够适应水泥窑尾烟的特殊工作环境。
纯低温水泥窑余热发电技术的优势主要体现在以下几个方面:1. 节能减排:利用水泥窑废热发电可以有效地回收和利用废热资源,实现能源的高效利用。
同时,该技术可以减少水泥生产过程中的二氧化碳等污染物的排放,降低环境污染。
2. 经济效益:纯低温水泥窑余热发电技术可以将水泥生产过程中的废热转化为电能,实现了能源的自给自足。
通过发电销售,可以带来可观的经济效益。
3. 应用广泛:纯低温水泥窑余热发电技术具有较好的适应性,可以适用于不同规模的水泥生产线。
同时,该技术还可以与其他余热发电技术相结合,实现多能互补发电。
4. 环保可持续:纯低温水泥窑余热发电技术可以有效地降低水泥生产过程中的能耗和污染物排放,为可持续发展做出贡献。
利用水泥窑余热的多级发电系统的制作技术
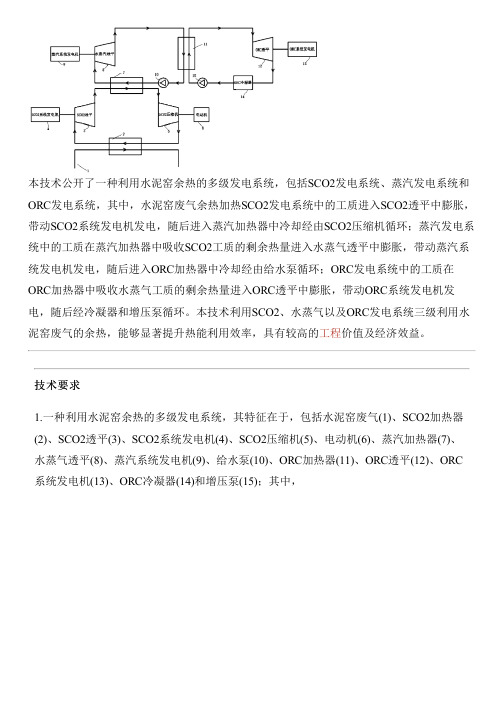
本技术公开了一种利用水泥窑余热的多级发电系统,包括SCO2发电系统、蒸汽发电系统和ORC发电系统,其中,水泥窑废气余热加热SCO2发电系统中的工质进入SCO2透平中膨胀,带动SCO2系统发电机发电,随后进入蒸汽加热器中冷却经由SCO2压缩机循环;蒸汽发电系统中的工质在蒸汽加热器中吸收SCO2工质的剩余热量进入水蒸气透平中膨胀,带动蒸汽系统发电机发电,随后进入ORC加热器中冷却经由给水泵循环;ORC发电系统中的工质在ORC加热器中吸收水蒸气工质的剩余热量进入ORC透平中膨胀,带动ORC系统发电机发电,随后经冷凝器和增压泵循环。
本技术利用SCO2、水蒸气以及ORC发电系统三级利用水泥窑废气的余热,能够显著提升热能利用效率,具有较高的工程价值及经济效益。
技术要求1.一种利用水泥窑余热的多级发电系统,其特征在于,包括水泥窑废气(1)、SCO2加热器(2)、SCO2透平(3)、SCO2系统发电机(4)、SCO2压缩机(5)、电动机(6)、蒸汽加热器(7)、水蒸气透平(8)、蒸汽系统发电机(9)、给水泵(10)、ORC加热器(11)、ORC透平(12)、ORC 系统发电机(13)、ORC冷凝器(14)和增压泵(15);其中,SCO2透平(3)采用向心式透平;水蒸气透平(8)采用向心式透平;ORC透平(12)采用向心式透平;SCO2压缩机(5)采用离心式压缩机;ORC发电系统采用的工质为R134a、R290、R601a以及戊烷低沸点工质;利用水泥窑余热的多级发电系统包含SCO2发电系统、水蒸汽发电系统及ORC发电系统;SCO2发电系统作业时,水泥窑废气(1)加热SCO2加热器(2)中的SCO2工质,随后进入SCO2透平(3)中膨胀,带动SCO2系统发电机(4)转动发电,SCO2工质随后进入蒸汽加热器(7)中与蒸汽发电系统中的工质进行换热得到冷却,进入SCO2压缩机(5)提升压力,其中压缩机所需的电能由电动机(6)提供,如此循环;蒸汽发电系统作业时,蒸汽工质在蒸汽加热器(7)中吸收SCO2工质的剩余热量,随后进入水蒸气透平(8)中膨胀,带动蒸汽系统发电机(9)转动发电,蒸汽工质随后进入ORC加热器(11)中与ORC发电系统中的工质进行换热得到冷却,最后由给水泵(10)重新泵入蒸汽加热器(7)中进行循环;ORC发电系统作业时,ORC工质在ORC加热器(11)中吸收水蒸气工质的剩余热量,随后进入ORC透平(12)中膨胀,带动ORC系统发电机(13)转动发电,随后进入ORC冷凝器(14)中凝结回收,经由增压泵(15)重新泵入ORC加热器(11)中循环。
水泥窑余热发电技术

目录水泥窑纯低温余热发电技术及发展目标水泥余热发电项目CDM的监测及相关要求水泥窑第一代、第二代纯低温余热发电技术的定义及特征水泥窑第一代、第二代纯低温余热发电技术的构成几个主要问题的研究余热电站对水泥窑的影响关于水泥窑纯低温余热发电技术的发展目标对于余热发电量的监测CDM项目监测管理组织机构设置监测设备安装要求及保证办法数据管理系统水泥窑纯低温余热发电技术及发展目标水泥窑第一代、第二代纯低温余热发电技术的定义及特征水泥窑第一代、第二代纯低温余热发电技术的构成几个主要问题的研究余热电站对水泥窑的影响关于水泥窑纯低温余热发电技术的发展目标水泥窑第一代纯低温余热发电技术的定义及特征定义:水泥窑第一代纯低温余热发电技术是指在不影响水泥熟料产量、质量,不降低水泥窑运转率,不改变水泥生产工艺流程、设备,不增加熟料电耗和热耗的前提下,采用0.69~1.27MPa-280~330℃蒸汽将新型干法水泥窑窑尾预热器排出的废气余热、窑头熟料冷却机排出的废气余热转化为电能的技术。
特征:1)冷却机仅设一个用于发电的抽废气口;2)汽轮机主蒸汽温度不可调整,随水泥窑废气温度的变化而变化。
水泥窑第二代纯低温余热发电技术的定义及特征在不影响水泥熟料产量、质量,不降低水泥窑运转率,不改变水泥生产工艺流程、设备,不增加熟料电耗和热耗的前提下,采用1.57~3.43MPa-340~435℃蒸汽将水泥窑窑尾预热器排出的废气余热、窑头熟料冷却机排出的废气余热转化为电能的技术。
定义:两个或两个以上用于发电的抽废气口设置独立过热器汽机主蒸汽温度参数不随废气温度变化独立的蒸汽过热器,提高电站运转率和稳定性出口废气温度可调整装置可满足不同季节、湿度物料烘干需求循环风特征:水泥窑纯低温余热发电技术及发展目标水泥窑第一代、第二代纯低温余热发电技术的定义及特征水泥窑第一代、第二代纯低温余热发电技术的构成几个主要问题的研究余热电站对水泥窑的影响关于水泥窑纯低温余热发电技术的发展目标水泥窑第一代纯低温余热发电技术的构成技术要点热力系统构成模式(1)单压不补汽式纯低温余热发电技术热力系统热力系统构成模式(2)复合闪蒸补汽纯低温余热发电技术热力系统热力系统构成模式(3)双压补汽式纯低温余热发电技术热力系统上述三种模式共同的特点:1)将窑头熟料冷却机排出的总废气分为两个部分自冷却机中抽出。
中国水泥窑余热发电技术3
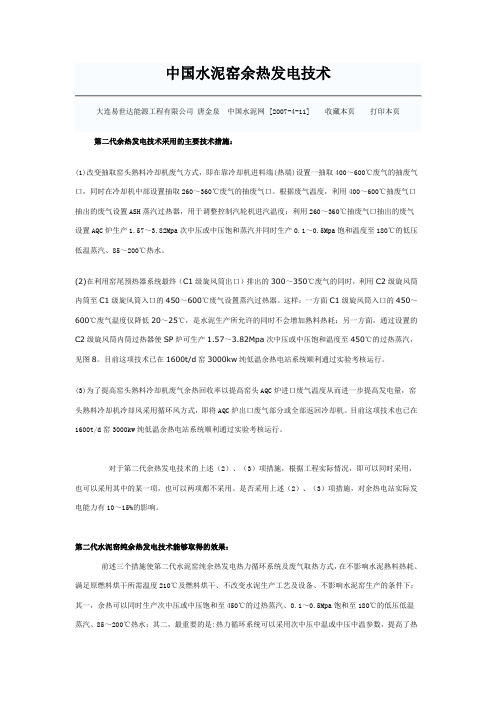
第二代余热发电技术采用的主要技术措施:(1)改变抽取窑头熟料冷却机废气方式,即在靠冷却机进料端(热端)设置一抽取400~600℃废气的抽废气口,同时在冷却机中部设置抽取260~360℃废气的抽废气口。
根据废气温度,利用400~600℃抽废气口抽出的废气设置ASH蒸汽过热器,用于调整控制汽轮机进汽温度;利用260~360℃抽废气口抽出的废气设置AQC炉生产1.57~3.82Mpa次中压或中压饱和蒸汽并同时生产0.1~0.5Mpa饱和温度至180℃的低压低温蒸汽、85~200℃热水。
(2)在利用窑尾预热器系统最终(C1级旋风筒出口)排出的300~350℃废气的同时,利用C2级旋风筒内筒至C1级旋风筒入口的450~600℃废气设置蒸汽过热器。
这样:一方面C1级旋风筒入口的450~600℃废气温度仅降低20~25℃,是水泥生产所允许的同时不会增加熟料热耗;另一方面,通过设置的C2级旋风筒内筒过热器使SP炉可生产1.57~3.82Mpa次中压或中压饱和温度至450℃的过热蒸汽,见图8。
目前这项技术已在1600t/d窑3000kw纯低温余热电站系统顺利通过实验考核运行。
(3)为了提高窑头熟料冷却机废气余热回收率以提高窑头AQC炉进口废气温度从而进一步提高发电量,窑头熟料冷却机冷却风采用循环风方式,即将AQC炉出口废气部分或全部返回冷却机。
目前这项技术也已在1600t/d窑3000kw纯低温余热电站系统顺利通过实验考核运行。
对于第二代余热发电技术的上述(2)、(3)项措施,根据工程实际情况,即可以同时采用,也可以采用其中的某一项,也可以两项都不采用。
是否采用上述(2)、(3)项措施,对余热电站实际发电能力有10~15%的影响。
第二代水泥窑纯余热发电技术能够取得的效果:前述三个措施使第二代水泥窑纯余热发电热力循环系统及废气取热方式,在不影响水泥熟料热耗、满足原燃料烘干所需温度210℃及燃料烘干、不改变水泥生产工艺及设备、不影响水泥窑生产的条件下:其一,余热可以同时生产次中压或中压饱和至450℃的过热蒸汽、0.1~0.5Mpa饱和至180℃的低压低温蒸汽、85~200℃热水;其二,最重要的是:热力循环系统可以采用次中压中温或中压中温参数,提高了热力循环系统效率,在充分利用水泥窑不同废气温度的余热的同时,实现了热量根据其温度进行梯级利用的原理;其三,第二代水泥窑纯余热发电热力循环系统、循环参数及废气取热方式使水泥窑废气余热按其质量最大限度地转换为了电能,从而使余热发电能力比目前普遍采用的第一代水泥窑纯余热发电技术得以大幅提高,吨熟料发电能力实际可达到750Kcal/Kg---38~42kwh/t。
中国水泥窑余热发电技术

中国水泥窑余热发电技术【中国水泥网】【2007-4-11】一、中国发展水泥窑余热发电技术的目的1.1 降低能耗、保护环境水泥熟料锻烧过程中,由窑尾预热器、窑头熟料冷却机等排出的400℃以下废气,其热量约占水泥熟料烧成总耗热量30%以上,造成严重的能源浪费。
水泥生产,一方面消耗大量的热能(每吨水泥熟料消耗燃料折标准煤为100~115kg),另一方面消耗大量的电能(每吨水泥消耗90~115kWh)。
如果将排出的400℃以下废气余热转换为电能并回用于水泥生产,可使水泥熟料生产综合电耗降低60%或水泥生产综合电耗降低30%以上,对于水泥生产企业:可以大幅度减少向社会发电厂的购电量或大幅度减少水泥生产企业燃烧燃料的自备电厂的发电量以大大降低水泥生产能耗;可避免水泥窑废气余热直接排入大气造成的热岛现象,可减少CO2等燃烧废物的排放而有利于保护环境。
1.2 为“建设节约型社会、推进资源综合利用”政策的推行提供技术支持能源、原材料、水、土地等自然资源是人类赖以生存和发展的基础,是经济社会可持续发展的重要的物质保证。
随着经济的发展,资源约束的矛盾日益凸显。
为此中国政府在为贯彻实施《节能中长期专项规划》而编制的《中国节能技术政策大纲》(2005年修订稿)中明确支持“大中型新型干法水泥窑余热发电技术”的研究、开发、推广工作。
1.3 符合清洁发展机制(CDM)项目的要求清洁发展机制是《京都议定书》第12条确定的一个基于市场的灵活机制,其核心内容是允许附件一缔约方(即发达国家)与非附件一国家(即发展中国家)合作,在发展中国家实施温室气体减排项目。
清洁发展机制的设立具有双重目的:促进发展中国家的可持续发展和为实现公约的最终目标做出贡献;协助发达国家缔约方实现其在《京都议定书》第三条之下量化的温室气体减限排承诺。
通过参与清洁发展机制项目,发达国家的政府可以获得项目产生的全部或者部分经核证的减排量,并用于履行其在《京都议定书》下的温室气体减限排义务。
水泥预分解窑余热中温发电技术

2006年第 3 期
孙义焱 木:水泥预分解窑余热中温发电技术
综合利用·环境工程
例如, 烟气温度为 850 ℃( 1 123 K) , 得 Exm /△Hm= 0.52, 烟 气 温 度 为 380 ℃(653 K)时 , Exm /△Hm=0.34, 这说明单位热能的最大作功能力前者约是后者的
1.5 倍。 1.2 锅炉热效率的不同
其中, △Hm=Cp(T- T0), T0 为热力学规定环境温度, 一
般为 298.15 K, T 为烟气热力学温度, Cp 为定压平均
比热容, C 为定比热容( Cp≈C) 。单位热能的火用值可
以用火用焓比“Exm /△Hm”来表示。
ln T
即:
Exm △Hm
=1-
T0
T0 T- T0
风中的热焓约 1 200 kJ/kg, 两者比约 3 倍。这说明两 者余热的单位热能发电量约差一倍, 其差异是可观
- 81 -
综合利用·环境工程
孙义焱:水泥预分解窑余热中温发电技术 木
方法的技术核心。
热能转移的具体方法是将预热器系统进气
端或中部的气体予以分流。一部分气体入预热
器系统以预热物料, 由于气固比的降低, 提高了
该部分气体在预热系统内的热效率, 降低了预
我国新型干法水泥窑纯低温余热发电技术现状

实际设 计计算 指标 要求 。
术 中“ 第一 代技 术 ” “ 及 第二 代技 术 ” 区分如 下 : 第 一 代 技 术 :无 论 是 单 压 循 环 系 统 还 是 双 压 循 环 系统 或 复 合 闪蒸 系 统 .凡 是 汽 轮 机 主 进 汽 压
力 ≤1 7 P 、 . M a 主进 汽温度  ̄3 0C 2 < 3  ̄ 的水 泥窑 纯低 温余 热发 电技 术 , 称为第 一代 技术 。 均
度波动 范围远远超 出保 证汽轮 机寿命所允 许的波动范 围. 因此 汽轮机 寿命 ( 主要是 叶片寿命 ) 到影 响 。 受
() 3 由于汽 轮机采用低 压低温 主蒸 汽参数 , 使汽轮 机不具 备采用 滑参数 运行 的条件 ( 当设 计采 用主蒸 如:
汽压力 和温度 为 06 9 a 3 7 . MP 一 1℃时 , 际运行 变化范 8 实
合 闪蒸 系统 。 是 汽 轮机 主进 汽 压 力> . MP 、 凡 1 7 a 主进 5
汽 温度 > 4  ̄ 的水泥 窑纯 低温 余热 发 电技术 , 3 0C 均称 为 第二 代技 术 。
达到 :当窑 尾预 热器废 气温 度为 3 0( 3 0C 2  ̄ 3  ̄ 时吨熟 2
料发 电量 为 2 ~ 5 Wht( 目前 实 际 只 达 到 了2 — 8 3k / 而 2
1 已投 产 余 热 电站 实 际发 电情 况
至 20 0 8年底 .全 国水 泥行 业有 2 3条 水泥 窑 已 6 投产 或 即将 投产 纯低 温余 热 电站 ,在这 些 电站 中 :5 8 条窑 采用 的是第 二代 水泥 窑纯低 温 余热 发 电技术 ( 以
没有达 到 :当窑 尾 预热器 废气 温度 为 3 0C 3 0 时 “ 2  ̄ 3  ̄ C
水泥窑纯低温余热发电技术特点

浅析水泥窑纯低温余热发电技术特点摘要:本文将对水泥窑纯低温余热发电技术的特点进行浅析,主要讨论了水泥窑窑内余热资源的利用,技术的应用及其优缺点。
以传统的热能发电技术为基础,水泥窑纯低温余热发电技术能够大大降低发电成本,更有效地利用热能资源,保护环境。
总之,水泥窑纯低温余热发电技术是一种有效的、可靠的发电技术,值得购买及使用。
关键词:水泥窑,纯低温余热发电技术,余热资源正文:随着工业生产的发展,发电技术的升级也推动了工厂热能利用的有效发展。
在传统的热能发电技术的基础上,水泥窑纯低温余热发电技术应运而生。
它利用窑内产生的余热,通过换热器和余热发电机将热能转化为电能,被广泛用于工业生产中。
水泥窑纯低温余热发电技术具有3个主要特点:1. 热能利用率高:水泥窑纯低温余热发电技术把熔下的熔铝吸收的热量有效转化为电能,具有较高的热能利用率。
2. 发电成本低:这种技术不需要外来能源,只需要利用窑内产生的余热,可以节省与外来能源的开支,降低发电成本。
3. 环境友好:水泥窑纯低温余热发电技术可以有效地利用热能资源,减少对环境的污染。
总之,水泥窑纯低温余热发电技术具有发电成本低、热能利用率高、环境友好等优点,在工业生产中有着重要作用。
然而,也存在一些缺点,例如发电效率低,余热发电机处理过程繁琐、容易出现故障等缺点,因此在运用时要注意问题,及早发现和纠正缺陷。
总的来说,水泥窑纯低温余热发电技术是一种有效的、可靠的发电技术,值得购买及使用。
在工业生产中,水泥窑纯低温余热发电技术的应用一直受到广泛关注。
它可以大大降低发电成本,提高发电效率,保护环境,更有效地利用热能资源,减少能源消耗。
然而,在运用水泥窑纯低温余热发电技术时也应注意一些问题,如合理设计、窑头温度控制、余热发电机处理过程及窑内烟气排放控制等。
为此,应采取适当措施来保证水泥窑纯低温余热发电技术的安全运行。
首先,在设计阶段应当严格遵守相关标准,合理配置系统组成部分,提高水泥窑纯低温余热发电技术的可靠性。
水泥窑纯低温余热发电技术

水泥窑纯低温余热发电技术一、所属行业:建材行业二、技术名称:水泥窑纯低温余热发电技术三、适用范围:大中型水泥窑余热的回收和利用四、技术内容:1.技术原理利用水泥窑低于350℃的废气的余热生产0.8~2.5MPa的低压蒸汽,推动汽轮机做功发电。
2.关键技术热力系统配置,以及相关主机设备效率的提高。
3.工艺流程窑头和窑尾余热锅炉生产的主蒸汽及低压蒸汽,进入汽轮机作功,做功后的蒸汽被冷却凝结成水并除氧,之后由给水泵再输送给窑头和窑尾余热锅炉再生产蒸汽。
汽轮机做功带动发电机发电,最后电量输送到工厂总降压站。
五、主要技术指标:1.与该节能技术相关生产环节的能耗现状:水泥生产中:热耗:3000~3400kJ/t.cl;电耗:95~110kWh/t.cl。
2.主要技术指标:具有约32~40kWh/t.cl的余热发电能力。
六、技术应用情况:该技术获得国家专利,已经有60多座电站投入运行,正在设计和施工的有100多座,目前行业内的推广比例约为8.5%。
七、典型用户及投资效益:典型用户浙江煤山众盛水泥厂,北京水泥厂有限责任公司等。
(1)某5000t/d级水泥生产线,窑头窑尾具有不能被水泥生产系统利用的中低温废气,节能技改投资额5600万元,余热电站建设规模9MW,建设期1年,节能量22000吨标煤/年,水泥厂可少购电:1.2亿kWh/年,投资回收期2.5-3.0年。
(2)某25000t/d级水泥生产线,窑头窑尾具有不能被水泥生产系统利用的中低温废气,节能技改投资额2850万元,余热电站建设规模4.5MW,建设期1年,节能量11000吨标煤/年,水泥厂可少购电:0.6亿kWh/年,投资回收期2.7-3.2年。
八、推广前景和节能潜力:全国生产能力≥1000t/d的新型干法生产线均可应用此技术。
“十一五”期间,该技术在行业内的普及率预计能达到40%,需总投入80亿元,可节能300万吨标煤。
九、推广措施及建议:1.从国家层面上制定强制性法规提倡水泥窑余热电站的建设;2.从国家层面上制定鼓励性政策及切实可行的鼓励性措施;3.从国家层面上制定统一的余热电站并网的政策及要求,解决电力系统对水泥窑余热电站并网壁垒的问题。
水泥窑低温余热发电技术及主要参数

水泥窑低温余热发电技术及主要参数
目前,我国水泥工业低温余热发电技术的核心内容是基于朗肯循环理论的热力循环系
统,热力循环方式主要有单压系统、闪蒸系统、双压系统三种基本模式,以及由此衍生的复
合系统构成。
理论和实践表明,以上三种热力系统的选择,应依据企业的具体情况来选择合
适的系统,采用哪种方式最合理,应依据热平衡计算、生产线规模、企业管理水平、投资额大小等实际情况进行综合比较后确定。
低温余热发电主要设备及主要技术参数,以5000t/d 水泥熟料生产线为例, 5 000t/d 及规模相当的生产线可利用窑头、窑尾余热资源,建设一套装机容量约为9MW 的低温余热电站。
主要设备有凝汽式汽轮机、发电机、SP 余热锅炉和AQC 余热锅炉,其主要技术参数指标见表2、表3。
水泥窑余热发电技术创新

图3 下进风式窑头余热锅炉水泥窑纯低温余热发电系统流程图 水泥窑余热发电技术创新
图4 双侧下进风式窑头余热锅炉水泥窑纯低温余热发电系统流程图 水泥窑余热发电技术创新
窑头余热锅炉的结构优化开发
开发的目的:
• 从机理上解决窑头余热锅炉磨损问题; • 减小窑头余热锅炉系统阻力; • 简化烟风管道系统,降低投资。
窑头余热锅炉的创新点
废气从下往上流动,降低废气在窑头余热锅炉内的流速,废气中携带的 粉尘颗粒在上升的过程,受到惯性力和颗粒自身重力的作用,颗粒速度 逐渐较小,达到了分离粉尘颗粒的效果,有效地减少了窑头余热锅炉受 热面迎风侧的积灰,同时减少粉尘颗粒对锅炉受热面的管束的冲击磨损。 窑头余热锅炉与粉尘颗粒分离装置一体化,取消外置式沉降室,简化了 烟气管道,减少了占地面积,节省了初投资费用。 窑头余热锅炉取消外置式沉降室,改为自带沉降室的窑头余热锅炉,减 少了窑头余热锅炉系统的阻力,系统总阻力小于800Pa,基本上不需要 改造窑头排风机,同时减少了余热发电系统的运行成本。 窑头余热锅炉入口处布置了2-4排“假管”和均流装置,有效防止前几排 受热面因废气的冲刷而造成的磨损。
3. 窑头锅炉换热管束磨损严重。
水泥窑余热发电技术创新
图1 现有水泥窑纯低温余热发电系统流程图
水泥窑余热发电技术创新
图2 带有外置独立沉降室窑头余热锅炉的立面图 水泥窑余热发电技术创新
水泥窑余热发电技术创新
• 水泥窑余热发电热力系统优化 • 窑头余热锅炉的结构优化开发
水泥窑余热发电技术创新
水泥窑余热电站设计原则
水泥窑余热发电技术创 新
2020/11/22
水泥窑余热发电技术创新
第六届余热发电国际峰会报告
- 1、下载文档前请自行甄别文档内容的完整性,平台不提供额外的编辑、内容补充、找答案等附加服务。
- 2、"仅部分预览"的文档,不可在线预览部分如存在完整性等问题,可反馈申请退款(可完整预览的文档不适用该条件!)。
- 3、如文档侵犯您的权益,请联系客服反馈,我们会尽快为您处理(人工客服工作时间:9:00-18:30)。
( 安全论文 )单位:_________________________姓名:_________________________日期:_________________________精品文档 / Word文档 / 文字可改中国水泥窑余热发电技术(新编版)Safety is inseparable from production and efficiency. Only when safety is good can we ensure better production. Pay attention to safety at all times.中国水泥窑余热发电技术(新编版)摘要:水泥工业是高耗能的工业。
在水泥生产中,水泥窑在350℃左右排放大量中低温废气,约占燃料总热输入的30%。
如果直接排放到大气中,会造成严重的能源浪费。
利用低温余热发电技术对该部分中低温废气余热进行回收利用。
产生的高温过热蒸汽进入汽轮机发电。
发电机的输出功率可满足水泥生产线和水泥厂自身的生活用电,并积极实施节能减排措施。
与火力发电厂相比,余热发电不需要燃烧煤炭等燃料,不产生二氧化碳等环境污染物。
关键词:水泥窑;余热发电技术;前言:节能减排是我国经济社会发展的一项长期战略方针,也是一项极其紧迫的任务。
回收余热,降低能耗,对我国节能减排和环境保护的发展战略具有重要的现实意义。
同时,余热利用在改善工作条件、节约能源、增产、提高产品质量、降低生产成本等方面发挥着越来越重要的作用。
其中一些已经成为工业生产的一部分。
20世纪六七十年代以来,余热利用技术在世界范围内得到了迅速发展。
目前,我国的余热利用技术也取得了长足的进步,但与世界先进水平仍有一定的差距,有的余热没有得到充分利用,有的余热在使用中存在着许多问题。
1目的要求1.1降低能耗环境。
在水泥熟料燃烧过程中,窑尾预热器和窑头熟料冷却器排放的低温废气余热占水泥熟料燃烧总热量的30%以上,造成严重的能源浪费。
一方面,水泥生产消耗大量热能,另一方面,水泥生产也需要大量电力。
将400℃以下低温废气余热转化为电能用于水泥生产,可使水泥熟料生产综合电耗降低60%或30%以上。
对于水泥生产企业来说,可以大大减少从社会发电厂购买的电力,或者大大减少水泥生产企业燃烧的燃料。
自备电厂发电可以大大降低水泥生产的能耗;避免了水泥窑余热直接排入大气的热岛现象;同时可以降低社会发电厂或水泥生产企业自用电厂的燃料消耗,减少CO2等燃烧废弃物的排放,有利于环境保护。
1.2政策的推行提供技术支持。
自然资源如能源、原材料、水、土地等,随着经济的发展,资源有限之间的矛盾越来越明显。
为此目的,中国政府在其节能技术计划中大力支持研究、开发和推广中型和中型干燥热生产新技术。
在国际金融危机的背景下,广泛应用于水泥工业余热生产工艺不仅降低生产成本和改善环境污染,而且市场竞争力大大提高水泥企业,做出了重大贡献,在水泥工业节能减少大量工业。
1.3符合清洁要求。
清洁发展机制是一种灵活的市场机制,其核心要素是向附件一缔约方提供促进发展中国家的可持续发展,促进最终目标;并协助发达国家缔约方履行减少温室气体排放的定量承诺。
参加世贸组织项目使发达国家政府能够获得执行项目所获得的所有或部分经认证的减排,并利用它们履行规定的限制温室气体排放的承诺。
在发达国家企业的情况下,可用于履行其限制温室气体排放的国家义务,或在适当市场上出售经济利益。
发达国家政府和企业可以通过参与项目大幅降低减排承诺的经济成本。
对发展中国家来说,通过额外的资金和/或先进的环境保护技术,参与发展中国家可以促进可持续发展。
因此,清洁发展机制是互惠互利的。
世贸组织的合作也可能降低全球温室气体减排的总体经济成本。
2中国水泥窑余热发电技术2.1水泥余热发电系统。
1)烟气流程出窑尾一级筒的废气(约310℃)经SP炉换热后温度降至208℃左右,经窑尾高温风机送至生料磨烘干原料后,经除尘器净化后达标排放。
取自窑头篦冷机中部的废气(分别约470℃和325℃)进入AQC炉,热交换后温度降至100℃左右后与熟料冷却机尾部的废气会合后进入收尘器净化达标后由引风机经烟囱排入大气。
SP炉的排灰为窑灰,可回到水泥生产工艺流程中,窑尾除尘器收下的窑灰一起用输送装置送到生料均化库。
AQC炉产生的粉尘将和窑头收尘器收下的粉尘一起回到工艺系统。
2)余热锅炉与水泥生产工艺系统的衔接(1)AQC炉为了确保AQC炉出现事故时不影响水泥生产,保留旁路烟道并设置调节型的切换烟风阀门,在必要时解列AQC炉。
保证水泥线的安全稳定运行。
(2)SP炉SP炉设置在窑尾预热器与窑尾高温风机之间,用烟气管道与余热锅炉连接。
SP炉系统的烟气侧阻力≤1100Pa,通过提高高温风机的风压,可使系统完全正常工作。
为保证余热锅炉的启停不影响水泥生产及电站的稳定运行,在SP炉烟气连接管道上设有旁通烟道,可使锅炉在出现故障时或水泥生产不正常时解列,既满足了水泥生产的稳定运行又保证了SP炉的安全。
通过旁通烟道的调节作用还可使水泥生产及余热锅炉的运行均达到理想的运行工况。
2.2水泥生产线对外排放的余热量分析根据水泥生产线工艺流程,生产线废气余热主要来源于窑尾预热器出口烟气,篦冷机尾排烟气。
根据生产线的运行情况,业主提供废气参数如下:窑尾预热器出口:368000Nm3/h-310℃;窑头冷却机出口:304000Nm3/h-360℃;旁路放风废气:25400Nm3/h-1050℃根据以上资料及烟气流程,水泥窑用于余热发电的废气参数确定如下:SP余热锅炉窑尾SP余热锅炉布置于高温风机正上方,锅炉进风取自窑尾预热器C1筒出风管道,本方案考虑5℃温度损失和1.5%的旁通阀门泄漏,SP余热锅炉废气设计参数确定如下:362480Nm3/h-305℃/208℃AQC余热锅炉对于AQC余热锅炉,由于当地的原料含碱量较高,导致熟料含碱,致使进入AQC锅炉废气含碱,AQC余热锅炉的蒸发受热面比较容易结块堵灰,因此采用传统的工艺流程,废气先经过粉尘分离器,再进入余热锅炉,使碱及早形成固态并沉降下来,减少对受热面的粘附,且加大换热面间距;有效的提高了锅炉的换热效率及防止积灰,以减轻熟料颗粒对窑头余热锅炉的冲刷磨损,但因为冷却机取风口到锅炉进口的距离相对较远,为减少中间环节(主要是废气分离器)漏风及温度损失,本方案将分离器与AQC余热锅炉固化为一体,在锅炉入口处设置降尘室,以达到预除尘的目的。
尽管如此,从冷却机取风点至AQC锅炉入口仍有大约5℃的温度损失。
考虑窑头篦冷机内部温度的分布及工作特性,并为了提高烟气余热品质,采用在窑头冷却机中前部取风的方式,拟采用两个取风口,其中高温风进入锅炉一级进风口,中温风进入锅炉二级进风口,每个取风管道上均设置调节型烟风阀门,便于灵活控制进入余热锅炉的风温。
为了保证一级进风温度,设置自窑头罩至锅炉的烟道并配置调节型烟风阀门。
窑头冷却机废气分配如下:高温一级取风废气参数:64090Nm3/h-470℃中温二级取风废气参数:239910Nm3/h-325℃另外,篦冷机鼓风采用热循环风方式,自窑头排风机回风至篦冷机二段、三段鼓风机入口,在冬季运行时,有效的保证了AQC锅炉的进风温度,大大提高了窑头余热资源的更充分利用。
2.3装机容量充分利用水泥生产线废气余热。
余热电站的生产运行不能影响水泥生产系统的生产运行及热耗指标。
余热电站的系统及设备应以“成熟可靠、技术先进、节省投资、提高效益”为原则,并考虑目前国内余热发电装备的技术水平,最大限度的采用先进的热力系统和技术。
烟气通过AQC和SP余热锅炉沉降下来的粉尘回用窑灰资源综合利用项目以达到节约资源及环境保护的目的。
尽量采用节能型产品,在利用废气余热的前提下进一步提高节能技术水平。
余热电站的建设尽量少的影响水泥生产线的停产时间。
电站控制采用DCS控制系统,提高控制水平和运行稳定性。
根据目前国内余热发电技术及装备现状,结合水泥窑生产线余热资源状况,采用低温低压余热发电技术。
根据目前的余热发电的技术水平,对锅炉出口主蒸汽压力为1.60MPa参数下,需:AQC锅炉:22.5t/h-1.6MPa(a)-440℃过热蒸汽7.45t/h-0.30MPa(a)-170℃过热蒸汽SP锅炉:20.5t/h-1.6MPa(a)-285℃过热蒸汽汽机进汽参数:1.5MPa(a)-360℃;0.20MPa(a)-160℃。
基于汽轮机排汽压力为0.007MPa(a),经计算蒸汽共具有约11275kW的发电能力。
考虑到汽轮机的稳定工作范围为额定功率的40%~110%,配备一台额定发电功率为9000KW的汽轮机和一台9000KW 的发电机及1台窑尾余热锅炉+1台窑头余热锅炉。
2.4热力系统根据上述装机方案,为满足生产运行需要并达到节能、回收余热的目的,结合水泥生产工艺条件,热力系统方案确定如下:1)SP余热锅炉:在窑尾设置SP余热锅炉,余热锅炉设置蒸汽段和省煤器段:蒸汽段生产1.6MPa(a)-285℃的过热蒸汽,锅炉省煤器给水来自AQC余热锅炉热水段。
2)AQC余热锅炉AQC余热锅炉设置主汽过热段,主蒸汽段,低压蒸汽段及热水段。
冷却机中部抽取一级高温废气进入AQC余热锅炉主汽过热段,生产1.6MPa(a)-440℃的过热蒸汽;冷却机中部抽取的二级中温废气进入AQC余热锅炉主蒸汽段,生产主汽饱和蒸汽;低压蒸汽段生产的0.3MPa(a)-170℃的过热蒸汽用于汽轮机补汽;AQC炉热水段生产的130℃热水作为SP、AQC余热锅炉各级蒸汽段的给水,AQC锅炉废气经原有的窑头收尘系统收尘后排入大气。
热力系统构成:汽轮机凝结水经凝结水泵送入真空除氧器,真空除氧器的出水经锅炉给水泵为窑头AQC余热锅炉热水段供水,AQC余热锅炉热水段的出水做为AQC、SP余热锅炉各级蒸汽段的给水。
AQC和SP余热锅炉主蒸汽段生产的过热蒸汽在汽轮发电机房合并后进入汽轮机的主进汽口。
AQC低压蒸汽段生产的0.3MPa(a)-170℃过热蒸汽做为汽轮机的补汽;汽轮机做功后的乏汽通过空气冷凝器冷凝成水,经凝结水泵送入真空除氧器,从而形成完整的热力循环系统。
窑头熟料冷却机余热锅炉采用多段受热面,最大限度地利用了窑头熟料冷却机废气余热。
为了保证电站事故不影响水泥窑生产,余热锅炉设有旁通废气管道,一旦余热锅炉或电站发生事故时,可以将余热锅炉从水泥生产系统中解列,不影响水泥生产的正常运行。
窑头、窑尾余热锅炉均采用立式结构,并采取相应措施解决锅炉的漏风、磨损、堵灰等问题,同时这种结构可减少占地面积。
除氧器采用真空除氧方式,有效的保证了除氧效果。
窑头降尘装置与窑头余热锅炉固化于一体,减少了窑头废气输送过程中的温度损失。
为保证窑尾锅炉下灰顺畅,在SP锅炉内部设置了振打除灰装置,保障清灰效果。