钻削镗削铰削与削
孔加工方法有哪些

孔加工方法有哪些孔加工是制造业中常见的加工工艺之一,它在各种机械零部件的制造中起着至关重要的作用。
孔加工的质量和效率直接影响着整个产品的性能和生产效率。
那么,孔加工方法有哪些呢?接下来我们将一一介绍。
首先,最常见的孔加工方法之一是钻削。
钻削是利用钻头在工件上旋转并向下推进的方式来形成孔洞的加工方法。
它可以分为手动钻削和机械钻削两种方式。
手动钻削一般用于小批量生产或修补加工,而机械钻削则适用于大批量生产,具有高效率和一致性的优点。
其次,还有铰削这种孔加工方法。
铰削是利用铰刀在工件上旋转并向下推进的方式来形成孔洞的加工方法。
它一般适用于孔的加工深度较大的情况,能够快速、高效地完成孔的加工。
除了钻削和铰削,还有镗削这种孔加工方法。
镗削是利用镗刀在工件上旋转并在径向移动的方式来形成孔洞的加工方法。
它适用于孔的精度要求较高的情况,能够获得较高的加工精度和表面质量。
此外,还有冲剪这种孔加工方法。
冲剪是利用冲头在工件上冲击的方式来形成孔洞的加工方法。
它适用于对工件表面要求较高的情况,能够快速、高效地完成孔的加工。
最后,还有激光加工这种孔加工方法。
激光加工是利用激光束对工件进行照射的方式来形成孔洞的加工方法。
它适用于对孔的形状和尺寸要求较为复杂的情况,能够实现非常精细的加工。
综上所述,孔加工方法有很多种,每种方法都有其适用的场合和优势。
在实际生产中,我们需要根据工件的具体要求和加工条件来选择合适的孔加工方法,以确保产品质量和生产效率。
希望本文所介绍的内容能够对大家有所帮助,谢谢阅读!。
机械制造技术基础4.3钻、铰、镗和拉削加工

6.2 钻削加工
(2)标准高速钢麻花钻的修磨改进方法 1)修磨横刃
6.2 钻削加工
2)修磨前面
3)修磨切削刃
6.2 钻削加工
4)磨出分屑槽
6.2 钻削加工
5)综合修磨
6.2 钻削加工
2.深孔钻 深孔一般指深径比L/d>5~10的孔,必须使用特殊结构的深 孔钻才能进行加工。深孔加工相对普通孔来说,加工难度更 大,技术要求更高,这是深孔加工的特点决定的。其特点如 下:第一、孔的深径比大,钻杆细长,刚性差,工作时易产 生偏斜和振动,因此孔的精度和表面质量难以控制;第二、 排屑通道长,若断屑不好,排屑不畅,可能由于切屑堵塞而 导致钻头破坏;第三、钻头在接近封闭的状态下工作,而且 时间较长,热量大且不易散出,钻头极易磨损。 基于深孔加工的上述特点,设计和使用深孔钻时应注意钻 头的导向、防止偏斜;保证可靠的断屑和排屑;采取有效 的冷却和润滑措施。
6.2 钻削加工
钻削加工是用钻头或扩孔钻在工件上加工孔的方法。其 中用钻头在实体材料上加工孔的方法称为钻孔。钻孔在机械 制造中占有较大的比重,因受钻头结构和切削条件的限制, 加工孔的质量不高,故用于孔的粗加工。
一、钻床
钻床主要是用钻头在实体材料上钻孔,还可以进行扩孔、 铰孔、攻螺纹、锪沉头孔、锪端面等,如图6-1所示。
第六章 钻、铰、镗和拉削加工
本章要点
钻削加工 铰削加工 镗削加工 拉削加工
6.1 概述
钻削、铰削、镗削和拉削加工在机械加工中主要用来进 行孔的加工。它是用相应机床在加工实体材料上钻孔和扩大 已有的孔,并达到一定技术要求的加工方法。
一、孔的类型
按照孔与其他零件的相对连接关系的不同,可分为配合 孔与非配合孔; 按其几何特征的不同,可分为通孔、盲孔、阶梯孔、锥孔 等; 按其几何形状不同,可分为圆孔、非圆孔等。
钻削、铰削、镗削和拉削加工共79页PPT

钻削、铰削、镗削和拉削有价值。—— 希腊
12、法律是无私的,对谁都一视同仁。在每件事上,她都不徇私情。—— 托马斯
13、公正的法律限制不了好的自由,因为好人不会去做法律不允许的事 情。——弗劳德
14、法律是为了保护无辜而制定的。——爱略特 15、像房子一样,法律和法律都是相互依存的。——伯克
31、只有永远躺在泥坑里的人,才不会再掉进坑里。——黑格尔 32、希望的灯一旦熄灭,生活刹那间变成了一片黑暗。——普列姆昌德 33、希望是人生的乳母。——科策布 34、形成天才的决定因素应该是勤奋。——郭沫若 35、学到很多东西的诀窍,就是一下子不要学很多。——洛克
(课件) 钻削、铰削和镗削加工
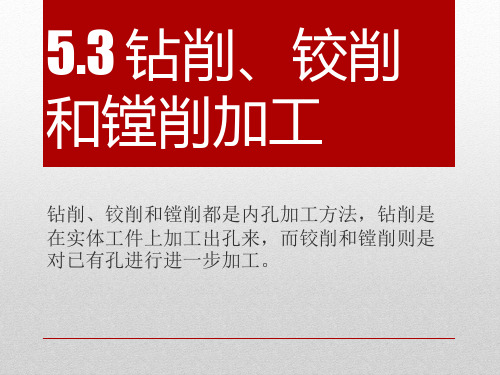
钻套 钻模板
工件
钻头切 削部分
5个刀刃 6个刀面
两条主切削刃 两条副切削刃 一条横刃
两个螺旋形前刀面 两个经刃磨获得的后刀面 两个圆弧段的副后刀面
钻削要素
• 切削速度:钻头外圆处的线速度。vc=πd0n/1000 • 进给量f:钻头或工件每转一转,它们之间的轴向相
5.3 钻削、铰削 和镗削加工
钻削、铰削和镗削都是内孔加工方法,钻削是 在实体工件上加工出孔来,而铰削和镗削则是 对已有孔进行进一步加工。
孔加工的不同方法和特点
• 孔: 连接关系:配合孔、非配合孔 几何特征:通孔、盲孔、阶梯孔、锥孔 几何形状:圆孔、非圆孔 • 孔加工方法: 从实体上加工出孔; 对已有孔进行半精或精加工; • 非配合孔用钻削加工,需要精加工的孔一般在钻削后
多刃镗刀(定尺寸刀具)
固定式:用于粗镗或半精镗 直径大于40mm的孔。 可调浮动式:采用一定结构 可以调整两刀刃之间的距离, 从而是一把刀具可以加工不 同直径的孔。加工质量高、 生产效率高成本高,适用于 批量生产、精加工箱体类零 件上直径加大的孔。
钻床
• 一般用于加工尺寸比较小、精度要求不太高的孔。它 可以进行钻孔、扩孔、铰孔及攻螺纹等加工。
铰刀的主要几何参数
• 前角:加工余量小,前角基本不起作用,一般等于 0°,韧性较大的材料,为了减小变形可取5°~10°
• 后角:为了避免重磨后刀面导致直径尺寸变化,后角 尽量取小。
• 主偏角:过大→切削部分短,定位精度差。过小→铰 韧性材料时产生过大的切屑变形。
• 手用铰刀→较小的主偏角,机用铰刀→大主偏角。 • 铰韧性材料→kr=12~15°,铰脆性材料→kr=3~5° • 粗铰→kr=45°
钻削、铰削与镗削加工
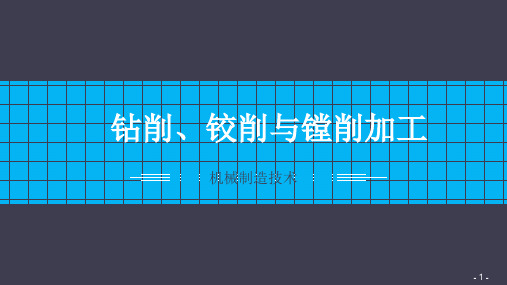
- 17 -
6.2 铰削加工与铰刀
二、铰刀的结构
铰刀由柄部、颈部和工作部组成。工作部包括切削部分和校准部分。切削部分担任主要的切削工作,校准部分起导向、 校准和修光作用。为减少校准部分刀齿与已加工孔壁的摩擦,并防止孔径扩大,校准部分的后端为倒锥形状。
- 26 -
6.4 钻床与镗床
2. 摇臂钻床 摇臂钻床是摇臂绕立柱回转和升降、主轴箱在摇臂上作水平移动的钻床。
其结构如图6.17 所示,大、中型工件上的孔通常采用摇臂钻床加工。在加工时, 工件在底座(或工作台)上安装固定,通过调整摇臂和主轴箱的位置来对正被 加工孔的中心。摇臂钻床广泛用于大、中型零件的加工。
- 11 -
6.1 钻削加工与钻头
- 12 -
6.1 钻削加工与钻头
2. 可转位浅孔钻 图6.5 所示为硬质合金可转位浅孔钻。它是20 世纪70 年代末出现的新型钻头,适合在车床上加工 d = 17.5 ~ 80 mm、l / d
≤ 3 的中等直径浅孔。
- 13 -
6.1 钻削加工与钻头
3. 错齿内排屑深孔钻 错齿内排屑深孔钻是常用的深孔加工钻头。工作时钻头与钻杆连接,通过刀架带动经液封头钻入工件。通过刀齿的交错排
切削部分的刀齿没有刃带,校准部分刀齿则留有0.05 ~ 0.3 mm 宽的刃带,以起修光和导向作用,也便于铰刀制造和检验。 (2)切削锥角2Φ
主要影响进给抗力的大小、孔的加工精度和表面粗糙度以及刀具耐用度。2Φ 取得小时,进给力小,切入时的导向性好; 但由于切削厚度过小产生较大的切削变形,同时切削宽度增大使卷屑、排屑产生困难,并且切入切出时间增长。
钻削、铰削、镗削和拉削加工
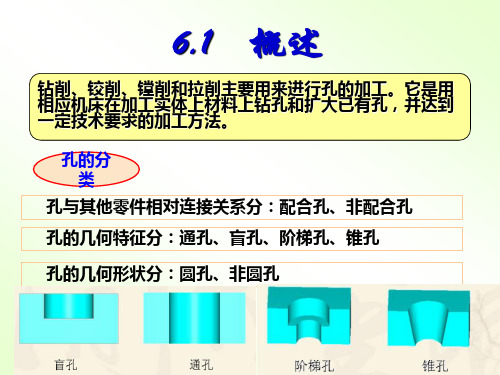
β
γ
f
轴向力和扭矩
切削刃强度和散热条件 一般麻花钻的螺旋角β=25°~ 32°。 黄铜、软青铜: β=10°~ 17° 轻合金、紫铜: β=35°~ 40° 高强度钢、铸铁:β=10°~ 15°
17
麻花钻的主要参数
(2)顶角2φ
指两主切削刃在与它们 平行的平面上投影的夹角
2φ
主切削刃长度
单位切削刃上的负荷及轴向力
21
6.2 钻削加工
6.2.2 钻削工艺特点
由于钻头的强度、刚度有限。容屑、排屑、导向、冷却和润滑 都困难,因此钻削的加工困难,质量不高。
钻孔时钻头易产生“引偏”
引偏概念 由于钻头弯曲而引起孔径扩大, 孔不圆; 孔的轴线歪斜。 “引偏”原因 ① 横刃的存在 ② 钻头的刚性和导向性差
6.2 钻削加工
6.2.1 钻床
钻床上可完成钻孔、扩孔、铰孔、攻丝、钻沉头孔、锪平面
刀具作旋转主运动同时沿轴向移动作进给运动。
6.2 钻削加工
6.2.1 钻床
立式钻床
立式钻床是应用较广的一种机床,其主参数是最大钻孔直径, 常用的有25mm、35பைடு நூலகம்m、40mm和50mm等几种。 特点是主轴轴线是垂直布臵, 而且位臵是固定的。加工时, 为使刀具旋转中心线与被加工 孔的中心线重合,必须移动工 件,因此立式钻床只适用于加 工中小工件上直径d≤50mm的孔。
6.2 钻削加工
用钻头在实体材料上加工孔的方法称为钻孔;用扩孔钻对已 有孔进行扩大再加工方法称为扩孔。它们统称为钻削加工。 钻床主要是用钻头钻削直径不大,精度要求较低的孔,此外 还可以进行扩孔、铰孔、攻螺纹等加工。加工时,工件固定 不动,刀具旋转形成主运动,同时沿轴向移动完成进给运动。 钻床的应用很广,如下图所示。
钻削与镗削加工钻削运动与加工范围

图 6.4 标准型群钻结构
返回目录
其修磨主要特征为: ( 1 )将横刃磨短、磨低,改善横刃处切削条件。 ( 2 )将靠近钻心附近主刃修磨成一段顶角较大的 折线刃和一段圆弧刃 , 以增大该段切削刃前角。同时 ,对称的圆弧刃在钻削过程中起到定心及分屑作用。 ( 3 )在外直刃上磨出分屑槽,改善断屑、排屑情 况。 经过综合修磨而成的群钻 , 切削性能显著 提高。钻削时轴向力下降 35% ~ 50%, 扭矩降低 10% ~ 30% ,刀具使用寿命提高 3 ~ 5 倍 , 生产 率、加工精度都有显著提高 。
两条主切削刃 5 个刀刃 、
两个刀尖
钻头 切削 部分
两条副切削刃 一条横刃、两个刀尖 两个螺旋形前刀面
6 个刀面
Hale Waihona Puke 两个后刀面 两个副后刀面思考题: 1 、麻花钻切削部分的组成如何 ?
2 、麻花钻的主要几何参数。有:
螺旋角 β 、顶角 2Ф 、前角 γo 、后角 α 。和横刃斜角 ψ 等 。
麻花钻的规格:直柄麻花钻( φ0.5~φ20 )
1 、钻削加工的主要问题
1 )导向定心问题:钻头刚性差,易引偏。 采取的措施: P122-123 (例) 2 )排屑问题: 钻孔排屑困难,切屑挤压、摩擦 已加工表面,表面质量差。 采取的措施: P123 3 )冷却问题:冷却困难。 采取的措施:加冷却液,分段钻削,定时 推出的方法来冷却钻头。 故钻孔加工生产效率低。
麻花钻的两个刃瓣可以看作两把对称的车刀。
图
标准高速钢麻花钻
其切削部分的组成为:
前刀面 ---- 螺旋槽的两螺旋面; 主后刀面 ---- 与工件过渡表面(孔底)相对的端部两曲面; 副后刀面 ---- 与工件的加工表面(孔壁)相对的两条棱边; 主切削刃 ---- 螺旋槽与主后刀面的两条交线; 副切削刃 ---- 棱边与螺旋槽的两条交线; 横刃 ---- 两后刀面在钻芯处的交线。 刀尖 ---- 主切削刃与副切削刃的交点(两个)。
切削的基本类型
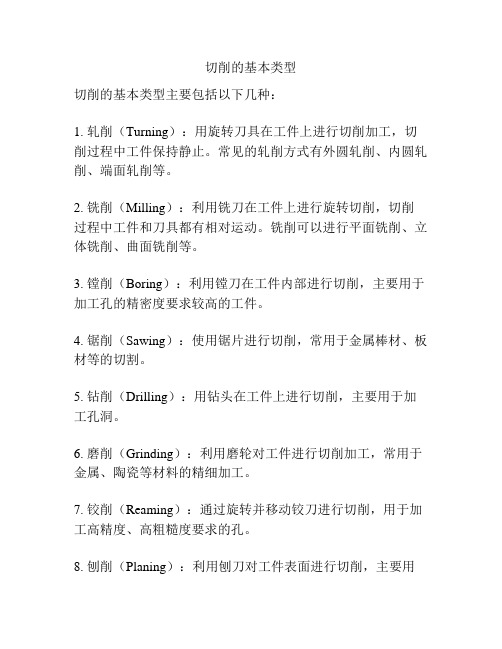
切削的基本类型
切削的基本类型主要包括以下几种:
1. 轧削(Turning):用旋转刀具在工件上进行切削加工,切削过程中工件保持静止。
常见的轧削方式有外圆轧削、内圆轧削、端面轧削等。
2. 铣削(Milling):利用铣刀在工件上进行旋转切削,切削过程中工件和刀具都有相对运动。
铣削可以进行平面铣削、立体铣削、曲面铣削等。
3. 镗削(Boring):利用镗刀在工件内部进行切削,主要用于加工孔的精密度要求较高的工件。
4. 锯削(Sawing):使用锯片进行切削,常用于金属棒材、板材等的切割。
5. 钻削(Drilling):用钻头在工件上进行切削,主要用于加工孔洞。
6. 磨削(Grinding):利用磨轮对工件进行切削加工,常用于金属、陶瓷等材料的精细加工。
7. 铰削(Reaming):通过旋转并移动铰刀进行切削,用于加工高精度、高粗糙度要求的孔。
8. 刨削(Planing):利用刨刀对工件表面进行切削,主要用
于平面的加工。
9. 拉削(Broaching):利用拉刀对工件进行切削,适用于加工孔洞的内轮廓形状。
10. 推削(Pushing):利用推刀对工件进行切削,常用于加工板材、管材等。
这些切削基本类型可以结合使用,互相补充,在不同工件和加工要求下选择合适的切削方法。
第六章-钻削、铰削与镗削加工

应用
下列加工方法中,工件做主运动的是 ( ) (A)铣削加工 (B)车削加工 (C)钻削加工
钻削加工中,刀具作旋转主运动,工件作进给 运动。 ( )
镗削
1、应用:镗床是一种主要用镗刀在工件上加 工孔的机床。通常用于加工尺寸较大,精度 要求较高的孔,特别是分布在不同表面上, 孔距和位置精度要求较高的孔。 2、运动分析:主运动为镗刀的旋转运动,进 给运动为镗刀或工件的移动。 3.镗削加工特点: 刀具结构简单,加工灵活性大、通用性强, 可粗加工也可半精加工和精加工,适用批量较 小的加工,镗孔质量取决于机床精度。
平面磨削
磨削加工的特点
磨削加工是应用较为广泛的切削加工方法之一。 与其他切削加工方式,如车削、铣削、刨削等比 较,具有以下特点: (1)磨削速度高,磨削温度高,将产生大量的 热,需要大量的冷却润滑液。 (2)磨削加工可以获得较高的加工精度和较低 的表面粗糙度。 (3)磨削不但可以加工软材料,而且还可以加 工淬火钢及其他刀具不能加工的硬质材料。 (4)磨削加工的切削深度很小,在一次行程中 所能切除的金属层很薄。 (5)加工范围广。
内、外圆磨削
2、平面磨削 平面磨床用于磨削工件上的各种平面。磨削时 , 砂轮的工作表面可以是圆周表面,也可以是端面。 (1)周边磨削 以砂轮的圆周表面进行磨削时, 砂轮与工件的接触面积小,发热少,磨削力引起的 工艺系统变形也小,加工表面的精度和质量较高, 但生产率较低。以这种方式工作的平面磨床,砂轮 主轴为水平(卧式)布置。 (2)端面磨削 用砂轮(或多块扇形的砂瓦)的 端面进行磨削时,砂轮与工件的接触面积较大,切 削力增加,发热量也大,而冷却,排屑条件较差, 加工表面的精度及质量比前一种方式的稍低,但生 产率较高。以此方式加工的平面磨床,砂轮主轴为 垂直(立式)布置。
钻、扩、铰削
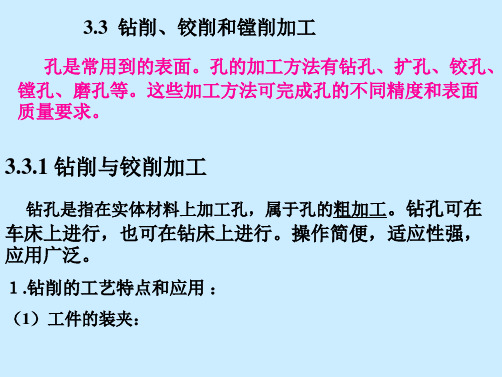
孔是常用到的表面。孔的加工方法有钻孔、扩孔、铰孔、 镗孔、磨孔等。这些加工方法可完成孔的不同精度和表面 质量要求。
3.3.1 钻削与铰削加工
钻孔是指在实体材料上加工孔,属于孔的粗加工。钻孔可在 车床上进行,也可在钻床上进行。操作简便,适应性强, 应用广泛。
1.钻削的工艺特点和应用 :
1.扩孔 使用的刀具:直径较大的麻花钻;扩孔钻。前者用于单件小批生 产中,后者用于精度要求较高或批量较大的生产。
与麻花钻相比扩孔钻的结构特点:
1) 无横刃。 2)切削深度小,容屑槽较浅,刀体强度 高,刚性好,能采用较大的进给量和切 削速度。 3)有3~4个刀齿,导向性好,切削过程 平稳。
扩孔质量好,尺寸精度IT10~IT9,Ra6.3~3.2μm。生产率 高。
2)铰刀齿数多,导向好,芯部直径大,刚性好,修光刃具有 导向、修光、校准孔的作用,刀具的制造精度高。
铰孔不能加工淬硬的孔,也不用于加工段续孔如:阶梯孔、
花键孔以及盲孔、短孔等。实际生产中,钻-扩-饺是加工较精 密中小孔的典型加工工艺
3.3.3 镗削加工
利用钻、扩、铰以及在车床上镗等加工孔的方法只能保证孔本
钻削过程
1 钻削要素
(1)υ(m/s)
v
Dn
1000 60
(2)进给量f(mm/r)
(3)钻----钻头或工件的转速r/min
4.其他钻头
(1)群钻 (2)错齿内排屑深孔钻 (3)单刃外排屑深孔钻
3.3.2 扩孔与铰孔 扩孔和铰孔主要用于对中、小孔的半精加工和精加工。
身的形状尺寸精度,不能保证孔与孔之间的位置精度要求。而 在镗床上镗孔可以保证孔系的位置精度要求(如箱体、支 架等工件上的孔)。
机械加工的工艺流程
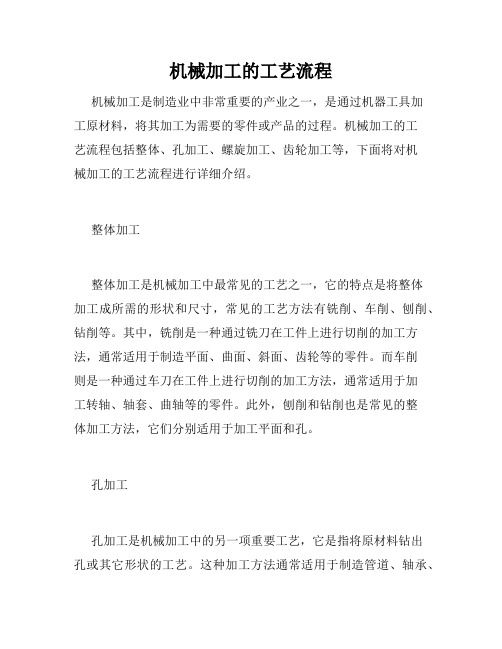
机械加工的工艺流程机械加工是制造业中非常重要的产业之一,是通过机器工具加工原材料,将其加工为需要的零件或产品的过程。
机械加工的工艺流程包括整体、孔加工、螺旋加工、齿轮加工等,下面将对机械加工的工艺流程进行详细介绍。
整体加工整体加工是机械加工中最常见的工艺之一,它的特点是将整体加工成所需的形状和尺寸,常见的工艺方法有铣削、车削、刨削、钻削等。
其中,铣削是一种通过铣刀在工件上进行切削的加工方法,通常适用于制造平面、曲面、斜面、齿轮等的零件。
而车削则是一种通过车刀在工件上进行切削的加工方法,通常适用于加工转轴、轴套、曲轴等的零件。
此外,刨削和钻削也是常见的整体加工方法,它们分别适用于加工平面和孔。
孔加工孔加工是机械加工中的另一项重要工艺,它是指将原材料钻出孔或其它形状的工艺。
这种加工方法通常适用于制造管道、轴承、齿轮、离合器等的零件。
主要的孔加工方法包括钻削、铰削和镗削。
其中,钻削是一种通过钻头在工件上进行切削的加工方法,可以加工直孔、斜孔等不同形状的孔。
铰削是一种通过铰刀在工件上进行切削的加工方法,适用于钻孔后的螺纹加工。
而镗削是一种通过镗头在工件中旋转而切削的加工方法,适用于加工大孔和不规则形状的孔。
螺旋加工螺旋加工是机械加工中的一种特殊的加工方法,它是指通过特殊的机床和刀具,将工件加工成各种形状的螺旋零件。
通常应用在机械传动中,例如蜗杆、升降丝杆、涡轮叶片等。
常见的螺旋加工方法包括螺旋车削、螺旋铣削和螺旋滚压。
齿轮加工齿轮加工也是机械加工中非常重要的一个部分,它的主要目的是将原材料加工成需要的齿轮零件。
加工齿轮有多种方法,包括铣削齿轮、滚齿轮、切齿轮和锲齿轮等,其中滚齿轮是最常用的方法之一。
滚齿轮分为滾削和滚弧两种加工方法,它可以在精度和加工效率方面达到较好的平衡。
总结机械加工的工艺流程包括整体、孔加工、螺旋加工、齿轮加工等多个方面。
不同的加工方法都有其独特的特点和加工适用范围,因此在选择加工方法时需要根据具体的零部件要求来选择。
深孔加工方法

深孔加工方法深孔加工是一种用于加工深孔的特殊加工方法,它广泛应用于模具、汽车零部件、航空航天等领域。
深孔加工方法的选择对加工效率和加工质量有着重要影响。
下面我们将介绍几种常见的深孔加工方法。
首先,钻削是深孔加工中常用的方法之一。
钻削是利用钻头在工件上旋转并向下推进,形成深孔的一种加工方法。
钻削加工简单、效率高,适用于加工直径较小的深孔。
但是,由于切削力和切削温度的积累,钻削加工容易导致刀具磨损和工件表面质量下降。
其次,镗削是另一种常见的深孔加工方法。
镗削是利用镗刀在工件上旋转并移动,形成深孔的加工方法。
相比钻削,镗削可以获得更高的加工质量和更好的表面粗糙度。
同时,镗削还可以加工大直径的深孔,具有很好的加工适应性。
但是,镗削加工的加工效率较低,成本较高。
另外,铰削也是一种常用的深孔加工方法。
铰削是利用铰刀在工件上旋转并移动,形成深孔的加工方法。
铰削加工适用于加工薄壁工件和薄壁孔的深孔加工,具有较好的加工稳定性和表面质量。
但是,铰削加工的切削力较大,加工深度有限。
最后,激光加工是近年来发展起来的一种新型深孔加工方法。
激光加工利用高能激光束对工件进行加工,可以实现对各种材料的深孔加工。
激光加工具有非常高的加工精度和加工效率,适用于加工高难度、高精度的深孔。
但是,激光加工设备成本较高,对操作人员的要求也较高。
综上所述,深孔加工方法的选择应根据工件材料、工件形状、加工精度等因素进行综合考虑。
在实际应用中,可以根据具体情况选择合适的深孔加工方法,以实现高效、高质量的深孔加工。
希望本文对您有所帮助。
钻削铰削与镗削与拉削
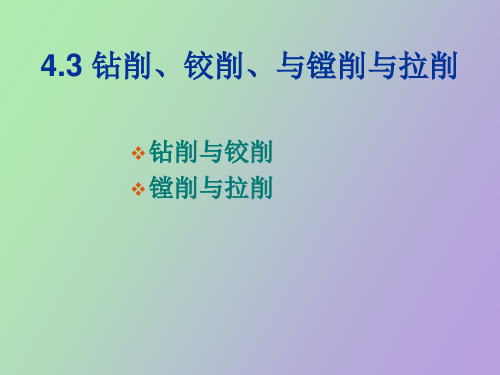
有单刃外排屑深孔钻、错齿内排屑深孔钻和喷 吸钻
六、 铰削
1)铰削的加工特点:
铰孔是利用铰刀从工件孔壁切除微量金属层,以 提高其尺寸精度和减小表面粗糙度值的方法。
它适用于孔的半精加工及精加工,也可用于磨孔 或研孔前的预加工。铰孔精度一般为IT9~IT7,表面
3.常用镗刀分类、特点及要求:
1)要求:镗刀和刀杆应有足够刚度,安装方便, 便于调整,具有良好的排屑和断屑功能。
2)分类:
按结构分:整体式镗刀,装配式镗刀,可调式 镗刀。
按刀刃数量分:单刃镗刀,双刃镗刀,多刃镗 刀。
按加工表面分:内孔镗刀和端面镗刀。
3)单刃镗刀
(1)适应性强 单刃镗刀是结构最简单的刀具之一, 使用和刃磨方便;一把刀具可以加工不同直径的 孔,各种结构类型的孔均能镗削;镗削加工可在 钻孔、铸孔和锻孔的基础上进行,既可以粗加工,
双刃镗刀
(1)加工质量高 由于镗刀片在加工过程中的浮 动,可以补偿镗刀安装误差及镗刀刀杆偏 摆所引起的不良影响,提高孔的精度。又 由于镗刀的修光刃比较宽,因而对孔壁的 修光效果好,减小了表面粗糙度值。但由 于镗刀是浮动的,故不能校正原有孔的轴 线偏斜或位置误差。
(2)生产率较高 浮动刀片有两个主切削刃同时切削, 并且操作简便,所以可提高生产率。
4)标准麻花钻头的缺陷 a.钻头的外缘处易磨损、中心切削困难。 b.切削条件较差、横刃长度大、轴向力大。 c.主切削刃长、排屑困难、切削液不易注入。 d.棱带与孔壁易摩擦、工作表面粗糙。
五、深孔加工(D/L=5~10)
1)深孔加工的特点(D/L=20以上的孔) 刚性差,易振动,中心线易偏斜,排屑困难,散热
❖ 圆弧刃切出的过渡表面有凸起的圆环筋,可 以防止钻孔偏斜,减少了孔径的扩大,加强 了定心导向作用,
第六章机械制造基础钻削铰削镗削和拉削加工

第五节
第六章 钻削、铰削、镗削和拉削加工
图6-37 拉削过程
2021/9/23
返回目录
37
第五节
第六章 钻削、铰削、镗削和拉削加工
图6-38 同廓式拉削图形
2021/9/23
返回目录
38
第五节
第六章 钻削、铰削、镗削和拉削加工
图6-39 渐成式拉削图形
2021/9/23
返回目录
39
第五节
第六章 钻削、铰削、镗削和拉削加工
第三节 铰削加工
图6-27 铰刀的刃倾角
2021/9/23
返回目录
27
第六章 钻削、铰削、镗削和拉削加工
第三节 铰削加工
图6-28 铰刀的浮动连接
2021/9/23
返回目录
28
第四节
第六章 钻削、铰削、镗削和拉削加工
图6-29
2021/9/23
返回目录
29
第四节
第六章 钻削、铰削、镗削和拉削加工
第六章 钻削、铰削、镗削和拉削加工
第二节 钻 削 加 工
图6-1 钻床上能完成的典型加工
2021/9/23
返回目录
1
第六章 钻削、铰削、镗削和拉削加工
第二节 钻 削 加 工
图6-2
2021/9/23
返回目录
2
第六章 钻削、铰削、镗削和拉削加工
第二节 钻 削 加 工
图6-3
2021/9/23
返回目录
图6-30 固定式双刃镗刀
2021/9/23
返回目录
30
第四节
第六章 钻削、铰削、镗削和拉削加工
图6-31
2021/9/23
返回目录
钻、扩、铰、研的特点

钻、扩、铰、研的特点用标准麻花钻钻削的特点1)切削刃上各点的切屑流出方向不同;主切削刃上各点的切屑流出方向和切屑速度均不相同,这造成切削刃上各点切屑卷曲的差异,增加了切屑上各点间的相互牵制和切屑的附加变形。
2)切削刃上各点前角不同,标准麻花钻切削刃上各点静态前角均不同,而且相差悬殊,造成切削条件上的差别。
工作时,因为各点切屑流出方向的不同,实际工作前角也发生了不同的变化。
实际工作前角不仅与半径有关,而且与钻头转速有关。
3)横刃切削条件极差,因横刃前角为极大的负值,切屑变形十分剧烈,形成很大的轴向力,使钻头工作不稳定。
4)切削刃上各点切屑变形不同,标准麻花钻钻削碳钢时切削刃上各点的变形系数切点半径及钻深有关。
5)为半封闭式切削,钻削时,切屑和切削液只能沿钻头螺旋沟进出,是半封闭式切削。
切削热不易传出,主切削刃与棱带交界转角处磨损严重。
6)多刃切削,麻花钻有两个主切削刃、一个横刃。
如果刃磨的不好,切削刃不对称,就会造成孔的偏斜、振动,使加工孔呈多角形(不圆),并使钻头磨损加剧。
深孔钻削的特点1)由于孔的深度与直径的比较大,钻杆细长,刚性差,工作时容易偏斜及产生振动,因此,孔的精度及表面粗糙度较难保证,2)切屑多而排屑通道长,若不采取必要措施,随时可能由于切屑堵塞耐导致个头损坏。
3)钻头在近似封闭的状态下工作,热量不易散出,钻头损严重。
扩孔钻加工的特点1)扩孔钻与麻花钻相比,由于没有横刃,刀体强度及刚性都较好,齿数多,切削平稳;2)加工精度及加工效率均较高。
铰削的特点1)铰削的精度.高。
用于孔的半精加工和精加工,由于加工余量小,齿数多,又有较长的修光刃等原因,铰孔精度可达it6-it11,表面粗糙度可达Ra1.6-0.2。
2)浮动铰孔时不能提高孔的位置精度。
3)铰孔的生产率较高,费用较低,既可铰圆柱孔,亦可铰圆锥孔,因此在孔的精加工中应用广泛。
研磨加工的特点与经济精度1)尺寸精度高。
磨料采用极细的微粉,在低速、低压下,磨除一层极薄的金属。
第六章 钻削、铰削与镗削加工

(1)铰刀的直径及公差
1)加工后孔径扩大时: dmax =Dmax-Pmax dmin =Dmax-Pmax-G
铰 刀 的 结 构
铰刀直径应选小一些
铰刀直径公差分布图
(1)铰刀的直径及公差 2)孔径缩小时:
dmax =Dmax+Pmin
铰 刀 的 结 构 dmin =Dmax+Pmin-G 铰刀直径应选大一些
6)特种钻头
(1)扩孔钻
(2)中心钻
用于孔加工的预制精确定位,引导麻花钻进行孔加工,减少误差 。
(3)枪钻
用于加工 L/D>20~100的深孔加工。
1、钻削加工
钻削运动
回转体零件上的孔——在车床上加工; 箱体类零件上的孔或孔系——在钻床上加工。
主运动:钻头的旋转运动(钻床),或工件的旋转 运动(车床)。 进给运动:钻头沿轴线作直线进给运动(钻床), 或工件沿钻头轴线作直线进给运动(铣床)
上加工出孔的道具,如麻花钻、中心钻及深孔钻等;另一类 是对工件上已有孔进行再加工的道具,如扩孔钻、锪钻、铰 刀及镗刀等。
深孔:孔深与孔径之比大于5~10倍的孔称为深孔。 孔加工刀具的共同特点:刀具工作部分处于加工表面包 围之中,刀具的强度、刚度及导向、容屑及冷却润滑等都比 切削外表面时问题更突出。
二、孔的种类
钻孔
扩孔
铰孔
攻螺纹
锪埋头孔
锪端面
2. 扩孔钻的结构
图 扩孔钻 1) 齿数多(3、4齿); 2)不存在横刃;
3)切削余量小,排屑容易。
锪孔
在已加工的孔上加工圆柱形沉头孔、锥形沉头孔和凸台断面 等。 锪孔的目的是为了保证孔口与孔中心线的垂直度,以便与孔 连接的零件位置正确,连接可靠。在工件的连接孔端锪出柱形或 锥形埋头孔,用埋头螺钉埋入孔内把有关零件连接起来,使外观 整齐,装配位置紧凑。将孔口端面锪平,并与孔中心线垂直,能 使连接螺栓(或螺母)的端面与连接件保持良好接触。
- 1、下载文档前请自行甄别文档内容的完整性,平台不提供额外的编辑、内容补充、找答案等附加服务。
- 2、"仅部分预览"的文档,不可在线预览部分如存在完整性等问题,可反馈申请退款(可完整预览的文档不适用该条件!)。
- 3、如文档侵犯您的权益,请联系客服反馈,我们会尽快为您处理(人工客服工作时间:9:00-18:30)。
钻削镇削較削与削作者:日期:2、引入1、本门课程的总体安排。
2、本篇在这门课中的地位和作用。
二、讲授新课第五章钻削、镗削、铰削与拉削孔是各种机器零件上出现最多的几何表面之一,分为非配合孔和配合孔二大类。
一般孔加工采用钻、扩等加工,有一定要求的孔是在钻、扩基础上进行再进一步的镗、铰等加工。
但不论是何种孔加工都具有以下一些特点:(1)部分孔加工刀具为定尺寸刀具,刀具本身精度会影响孔的加工精度。
(2)孔加工刀具的切削和夹持部分的有关尺寸受被加工孔尺3寸的限制,会使刀具的刚性变差。
(3)孔加工时,刀具一般是封闭或半封闭状态下进行工作,对加工质量和刀具耐用度都会产生不利的影响。
基于以上原因,在机械设计过程中选用孔和轴配合的公差等级时,经常把孔的公差等级定得比轴低一级。
孔加工的方法很多,常用的有钻孔、扩孔、锪孔、铰孔、镗孔、拉孔、磨孔等,还有金刚镗、珩磨、研磨、挤压及特种加工孔等方法。
其加工孔直径Φ 0.01 ~Φ1000mm ,加工精度可达到IT13~IT5,表面粗糙度Ra12.5 ~0.006 μm;可在金属或非金属材料上加工,也可在普通材料或高硬度材料上加工。
在加工中可根据不同要求,合理进行选择最佳的加工方案,达到加工质量能符合要求。
第一节钻削加工(一)一、概述4用钻头作回转运动,并使其与工件作相对轴向进给运动,在实体工件上加工孔的方法称为钻孔;在已有孔的情况下,用扩孔钻对孔径进行再扩大的加工称为扩孔;钻孔与扩孔统称为钻削。
钻削可以在各种钻床上进行,也可以在车床、铣床、镗床和组合机床、加工中心上进行,但大多数情况下,尤其是在大批量下生产时,主要还是在钻床上进行。
二、钻床主要用钻头在工件上加工孔的机床称为钻床。
通常以钻头的回转运动为主运动,钻头的轴向移动为进给运动。
钻床的分类:坐标镗钻床、深孔钻床、摇臂钻床、台式钻床、立式钻床、卧式钻床、铣钻床、中心孔钻床等八大类。
大部分以最5大钻孔直径为主要参数。
钻床的主要功用为钻孔和扩孔,也可以用来铰孔、攻螺纹、锪沉孔及锪凸台端面等。
1、立式钻床特点是主轴是垂直布置且位置固定不动(沿立柱轴线回转)。
因其立轴结构不同可分为圆柱立式钻床、方柱立式钻床和可调多轴立式钻床。
机床的使用:主轴箱和工作台可沿立柱作上下移动以调整工作高度;工件安放于工作台上,通过工件的位置移动来找正;利用主轴箱的功能,可以进行变换主轴转速、主轴进给量等加工参数,主轴的上下移动可实现自动进给或手动进给。
适合于加工单件或小批量的中小型工件加工,钻孔直径为Φ16~Φ80mm ,如Z5132 、Z5140A 等。
62、摇臂钻床特点是主轴能沿立柱的中心轴线进行回转。
机床的使用:将工件放置于工作台上;主轴绕立柱可上下移动和旋转或主轴箱可在摇臂上作横向移动;利用主轴箱的功能,可以进行变换主轴转速、主轴进给量等加工参数,主轴的上下移动可实现自动进给或手动进给。
适合于加工单件或中小批量的大中型工件加工,钻孔直径为Φ25~Φ125mm ,如Z3040 、Z3050A 等。
3、钻削加工中心7般以钻孔、攻螺纹和铣削为主,且刀具在十把以上的加工中心称为钻削加工中心功能:各种直径的孔加工;各种面的铣削加工;多轴(多空间)加工孔或面。
技术性能:主轴转速高,加工孔直径范围大,进给速度大,定位精度高等。
三、麻花钻1、概述是孔加工中应用最广泛的刀具。
主要用来在实体材料上钻削直径在Φ 0.1 ~Φ 80mm ,加工精度为IT12 左右,表面粗糙度在Ra12.5 ~86.3μm 左右的孔或精度要求较高的孔的预加工。
分类:按材料不同可分为高速钢和硬质合金钻头;按柄部不同分为直柄和锥柄钻头;按长度不同分为基本型、短、长、加长和超长型等钻头。
⑴硬质合金麻花钻有整体式、镶片式和可转位式(无横刃式)三种,一般用于加工各类特殊材料的各种孔加工。
用细颗粒钨系材料及YG、YW 、YT 等制作而成,整体式大多采用TiN 涂层(金黄色)或镶片式采用涂层刀片;钻头直径从Φ 0.2 ~Φ60mm ,硬度在58~62HRC 。
⑵高速钢麻花钻是一种标准刀具,由工作部分、柄部和颈部(锥柄钻才有)组成,锥柄还带有扁尾。
整体呈倒锥形。
整个切削部分由前面、后面、副后面、主切削刃、副切削刃和910横刃等组成。
2、切削部分的几何参数⑴螺旋角β螺旋角增大会使钻头锋利和排屑通畅,但使钻尖强度削弱和散tan2 r 0L热条件变差。
⑵顶角2φ顶角大,钻头强度增大;标准麻花钻2φ=118 °;加工钢、铸铁、硬青铜时,2φ=116 ~120°;加工硬铸铁、不锈钢、耐热钢时,2φ =120~150 °。
⑶刃倾角λSX 和端面刃倾角λtx 每一点上的刃倾角和端面刃倾角都不相同,越靠近钻心越大。
⑷主偏角κr每一点上的主偏角也不相同,越靠近外缘处越大。
⑸前角γOX每一点上的前角都不相同且变化较大,如外缘处前角为30 °,钻心处前角为-30 °。
⑹后角αfx 主切削刃上外缘处的点其后角最小,钻心处的点其后角最大。
11⑺横刃角度ψ标准麻花钻的横刃斜角ψ =50 ~55°。
一般后角增大,横刃斜角随之减小,导致横刃长度增大,进给力增大,切削条件变差,对加工质量产生不利影响。
四、钻削原理1、钻削要素d0nc⑴切削速度υC:钻头外缘处的线速度c 1000⑵进给量:每转进给量f,每齿进给量fz,进给速度υ f ;υf=nf=znfz 。
⑶背吃刀量αp:do2h D sin⑷切削厚度hD 和切削宽度bD:D 2bDd2sin⑸切削面积AD :A D h D b Dfd o4122、钻削力和钻削功率在钻削力合成中,有一个总扭矩T 和一个总进给力F。
T T o T o1 T 2F co F co1d o F c bF 2F fo 2F fo1 F f从上式得知:总扭矩T来源于主切削刃,总进给力F来源于横刃。
Pc 2 Tn6切削功率PC 。
c 60 1063、切削热与钻头磨损钻头磨损和切削热产生的交汇点在于:切削速度和切削温度最高、刀体强度最薄弱的前面、后面和刃带三者的交汇处五、麻花钻的修磨与群钻131、标准高速钢麻花钻的缺点切削刃上各点前角变化大,横刃较长,主切削刃较长,切削速度高、切削刃强度和散热条件较差。
2、麻花钻的修磨1)修磨主切削刃,形成多段或圆弧形切削刃;2)修磨横刃,使横刃变短和改善横刃处的前角角度;3)修磨前刀面,使前角变大或变小,以适应不同材料的切削加工;(4)修磨刃带,加大刃带上形成的副后角;(5)磨分屑槽,便于排屑和断屑。
143、群钻是在长期的生产实践中,综合了标准麻花钻各种修磨方法的成功经验,而设计出的一种先进钻头。
为了适应不同工件材不同孔径的钻削需要,群钻已形成了多种系列。
图示为标准群钻。
结构上与普通钻头相比:主切削刃由外刃、圆弧刃和内刃所构成;刀尖有三个;顶角有二个(外刃顶角和内刃顶角);在一侧主切削刃后开有分屑槽。
性能上与原来的普通钻头相比:效率提高,切削条件改善,有利于钻头定心,耐用度提高,切削省力,精度与表面质量更好。
15三、新课小结本节主要是使学生掌握钻削的基本知识及钻床、刀具、原理等知识;掌握麻花钻各部分的切削角度和选择方法;了解钻削力的计算方法。
四、布置作业1、孔加工刀具有何特点?2、钻削三要素及计算公式。
3、麻花钻在结构上有那些缺陷?应如何修磨来加以改进?一、引入1、孔加工刀具有何特点?2、钻削三要素及计算公式。
3、麻花钻在结构上有那些缺陷?应如何修磨来加以改进?16二、讲授新课第一节钻削加工(二)六、扩孔与锪削1、扩孔在已有孔的基础上再进行孔加工。
刀具为扩孔钻,一般有3~4 条主切削刃。
按刀具切削部分材料分有高速钢和硬质合金两种;按外形分有整体直柄、整体锥柄、套式和转位形(主要用于大直径)扩孔钻的加工质量比钻孔要好。
因为:无横刃切削阻力小,加工余量小;刀刃多切削力小,导向性好;刀体强度高,刚性好。
17扩孔时进给量可以比钻孔大一倍。
2、锪削在已加工孔的基础上进行圆柱形沉头孔、锥形沉头孔和端面凸台加工。
刀具为锪孔钻,有圆柱沉头锪钻、锥形沉头锪钻、端面锪钻等;一般有3~4 个刀齿。
锥形沉头锪钻角度有60 °、90°、120°三种。
大多数用高速钢制造,大直径采用硬质合金制造。
七、深孔加工1、深孔加工的特点及对刀具的要求18一般把深径比在5~10 以上的孔称为深孔。
直径比在20 以下的通常用加长麻花钻,直径比在20 以上的通常用深孔钻加工。
深孔加工比非深孔加工难度大得多,其主要原因:①刀具细长,刚性很差②排屑困难③冷却、润滑困难。
深孔钻与其他钻头相比有以下特点:足够的刚性和良好的导向功能;有可靠的断屑、排屑功能;有效的冷却、润滑功能2、常用的深孔加工刀具(1)单刃外排屑深孔钻;(2)错齿内排屑深孔钻;(3)喷吸钻。
八、钻孔质量分析主要问题有:孔径扩大和孔轴线偏斜、钻头的崩刃和折断。
1、孔径扩大和孔轴线偏斜(1)产生原因:19①切削刃不对称;②加工面不平;③钻头横刃过长;④钻头与夹具间隙过大;⑤设计或工序不合理2)采取措施:①预加工孔端面;②尽量工件回转;③先钻中心孔;④适当小的进给量;⑤切削刃修磨对称;⑥修磨横刃;⑦调整机床;⑧选用合适钻套;20⑨钻深孔时用支承架。
2、钻头的崩刃和折断(1)产生原因:①进给量、进给力变化大;②切屑缠绕或堵塞;③堵塞冷却不充分;④磨损过大;⑤夹持不稳定;⑥孔将钻通时,力过大。
(2)采取措施:①及时修磨钻头;②及时修磨横刃;③改善断屑、排屑条件;④采用分级进给加工;21⑤减小工艺系统的弹性变形。
三、新课小结本节主要是使学生了解扩孔和锪削的基本知识;的了解深孔加工工艺;掌握钻孔质量分析的基本方法。
22四、布置作业1、深孔加工比一般孔难度大很多,主要原因是什么?2、为防止钻孔时孔径扩大和孔轴线偏斜,一般应采取哪些措施?3、为防止钻孔时钻头折断,一般应采取哪些措施?23、引入1、深孔加工比一般孔难度大很多,主要原因是什么?2、为防止钻孔时孔径扩大和孔轴线偏斜,一般应采取哪些措施?3、为防止钻孔时钻头折断,一般应采取哪些措施?、讲授新课第二节镗削概述镗孔是一种应用非常广泛的孔加工方法。
可以用于孔的粗加工、半精加工、精加工;可以加工通孔和盲孔;可以加工各种工件材料。
镗孔可以在各种镗床上进行加工,也可以在卧式车床、回轮或转塔车床、铣床、数控机床、加工中心上进行。
在镗床上镗孔的突出优点:可以用一种镗刀加工一定范围内各种不同直径的孔,尤其是大直径的孔;可以修正上一工序所产生的孔的相互位24置误差。
但生产率低,适合于单件和中、小批量生产的场合。
镗孔加工精度一般为IT9~IT7,表面粗糙度为Ra6.3 ~0.8um ;高精度镗床可达到精度IT6,表面粗糙度为Ra1.6 ~0.8um ,甚至达到Ra0.2um 。