立铣刀螺旋角大小对切削性能的影响
刀具角度对车削质量的影响
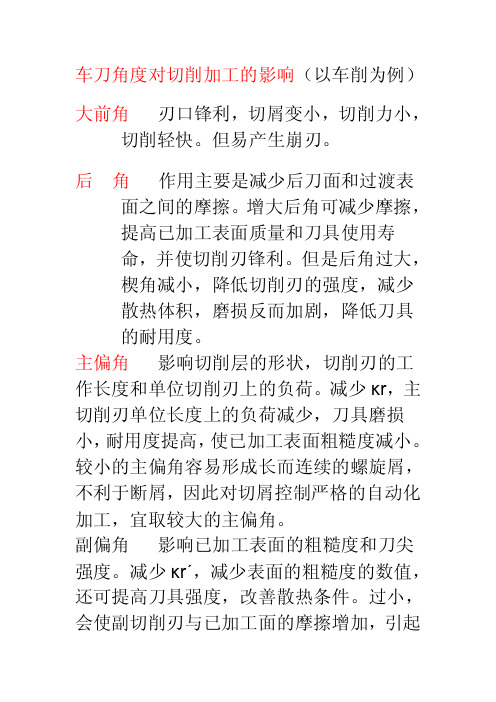
车刀角度对切削加工的影响(以车削为例)大前角刃口锋利,切屑变小,切削力小,切削轻快。
但易产生崩刃。
后角作用主要是减少后刀面和过渡表面之间的摩擦。
增大后角可减少摩擦,提高已加工表面质量和刀具使用寿命,并使切削刃锋利。
但是后角过大,楔角减小,降低切削刃的强度,减少散热体积,磨损反而加剧,降低刀具的耐用度。
主偏角影响切削层的形状,切削刃的工作长度和单位切削刃上的负荷。
减少κr,主切削刃单位长度上的负荷减少,刀具磨损小,耐用度提高,使已加工表面粗糙度减小。
较小的主偏角容易形成长而连续的螺旋屑,不利于断屑,因此对切屑控制严格的自动化加工,宜取较大的主偏角。
副偏角影响已加工表面的粗糙度和刀尖强度。
减少κr´,减少表面的粗糙度的数值,还可提高刀具强度,改善散热条件。
过小,会使副切削刃与已加工面的摩擦增加,引起震动,降低表面质量和刀具耐用度。
副偏角的大小主要根据已加工表面粗糙度要求和刀具强度来选择,不引起振动的情况下,尽量取小值。
车刀的角度对加工质量及效率的影响车刀的主要标注角度有以下5个:1.前角2.主后角3.主偏角4.副偏角5.刃倾角根据经验主偏角和副偏角构成刀尖角度,这个角度要根据粗精加工而定,粗加工时由于主要目的是去除大量的余量,所以这个角度可以适当的大一些,以适应大的进给量;精加工时,余量较少,要保证好的表面质量,所以刀尖角度要小,断屑槽要开的深一些,以免切屑流经已加工表面划伤工件表面。
还有刃倾角,负的刃倾角可以保护切削刃,承受大的进给量,反之则可以提高表面质量。
车刀前角对刀具切削性能影响的研究关于前角大小要根据加工工艺和工件材料来选择!1.前角有正前角和负前角之分(还有一种是0度前角多用于石墨加工)2.取正前角的目的是为了减小切屑被切下时的弹性变形和切屑流出时与前面的摩擦阻力,从而减小切削力和切削热,使切削轻快,提高已加工表面的质量。
3.取负前角的目的是在于改善刃部的受力状况和散热条件,提高切削刃强度和耐冲击能力。
刀具角度对切削的影响

兼具良好的切削性能和抗崩刃性
由于采用深倾角而实现了超群 的切削性能 实现了27°的前角! 超群的低切削抗力!!(使用ML断屑槽时)
其它公司产品
27°
轴向前角
双后角提高了刀尖强度
外圆切削刃设有2段后面, 抗崩刃性实现飞跃性提升
其它公司产品
铣刀旋转方向
外圆切削刃
■抗崩刃性比较表
10 8 6 4 2
■切削抗力比较表
以往产品
其它公司 产品A
其它公司 产品B
0 0 0.05 0.1 0.15 0.2 0.25 0.3 0.35
每齿进给量 fz (mm/t)
Zc
1
加工长度 (m) 100
切削抗力 (N)
型化!
Tungaloy
高效率
●刀体规格设定包括标准刃、多刃、超多刃(订货生产)。 ●CA45°式T/EAW13型设定有大进给专用刀片HJ型。实现了相当于以往产品1.5倍~2倍的进给量。
切 削 宽 度 :ae=80mm
Yc
进给量
Xc
■抗崩刃性
4.5 4.0 3.5 3.0 2.5 2.0 1.5 1.0 0.5
0 TPW13型 (MJ断屑槽)
以往产品 其它公司产品A
被加工材料 :PX5
使 用 机 床 :BT50
切 削 速 度 :Vc=150m/min
每齿进给量 :fz=0.2mm/t
a
b
重量 冷 刀垫固定 (kg) 却孔 螺钉
刀垫
紧固 螺钉
6 10 0.4 有
6 10 0.5 有
6 9.5 1 有
8 12.7 1.5 有
10 15.9 2.8 有 DTS5-3.5SS FSSA1102 CSPB-3.5
铣刀螺旋角对检验铣床工作精度的影响

铣刀螺旋角对检验铣床工作精度的影响Influence of M illing Cu tter s H elix Angle on the Working Accuracy Test of Milling Machine王美印 王秀青(河北师大职技学院)摘 要:分析了铣刀螺旋角对精切试件等高的影响,提出了减小影响的措施。
关键词:铣床 工作精度 铣刀螺旋角万能工具铣床精度标准JB2874 86工作精度检验P1中规定:水平主轴精铣I 面(图1)在规定长度L 内用千分表检验尺寸H 等高允差为0.025mm 。
我们在对X8140工作精度精切攻关过程中发现,铣刀螺旋角对H 等高性的影响在尺寸16mm 方向内竟高达0.006~0.011mm,约占H 允差(0.25m m )的五分之二,这无疑是一个不可忽视的因素。
图1根据铣床工作精度通用标准要求,我们采用套式面铣刀(铣刀直径为 63mm,螺旋角15 ,右旋,齿数12,材料W18Cr4V),与刀杆一起刃磨,安装时符合标准要求,以保证用一把刀一次装夹完成 、 、 、面加工。
验收技术要求规定切削参数为:切深t =0.1~0.3mm,主轴转速为125~210r/min,走刀速度为35~85mm/min,逆铣。
由刀具与切削参数的几何关系(图2)可计算出,切削时一齿切出后下一齿才切入为断续切削。
当刀齿从c 点切入到a 点切出时,由于螺旋角的存在,刀刃与工件表面的接图2 滚切试件触长度在每瞬间是不等的。
因每齿的走刀量很小(当S =40mm/min 、n =180r/min 时,S z =0.0185mm),可认为刀刃上每个切入点c 形成工件表面。
当刀齿从c 点切入到a 点切出时刀刃与工件接触线从c 点(点接触)加长到ac 点,形成工件表面的长度为cc =e 。
由切削力的计算公式知,切削力与切削面积相关。
刀刃在c 点与工件为点接触,面积最小。
切出时刀刃与工件接触线最长,切削面积最大,切削力最大,悬臂刀杆变形也最大。
立铣刀螺旋角

立铣刀螺旋角大小对切削性能的影响1螺旋刃立铣刀的基本特性与问题的提出立铣刀的基本刃口形状(螺旋槽形状)有直形和螺旋形两种.由于螺旋刃立铣刀相对于直刃具有切削轻快、平稳、效率高和使用范围广等优点,因此在铣削加工中得到了广泛应用.根据加工设备和加工对象的不同要求,螺旋刃立铣刀有左刃、右刃和左螺旋、右螺旋之分的4种不同组合〔1〕,其中左刃左螺旋和右刃右螺旋在加工中的轴向切削阻力有把立铣刀从刀夹中拔出的趋势,需采用拉紧螺栓克服轴向切削阻力.而左刃右螺旋和右刃左螺旋的轴向切削阻力刚好把立铣刀压向夹头方,故多采用锥柄加扁尾,以适应大功率切削.因为右刃右螺旋立铣刀可让切屑沿排屑槽向柄部排出,易保证切削的平稳进行,符合机床主轴旋向标准,在高性能夹头的支持下装卸方便,所以,其使用范围最广,使用量最大.实际应用中的螺旋刃立铣刀,其螺旋角通常在30°~45°.在刀具原理、设计和应用技术领域,根据工件材料、刀具材料及切削加工诸参数的不同,有关螺旋刃立铣刀的切削力、扭矩、切削功率及前角、后角等主要刀具角度的设计计算公式、实验数据与使用经验等资料很多,但有关螺旋角大小与立铣刀加工性能的讨论和资料介绍很少.一般认为,螺旋刃立铣刀的螺旋角β就是刃倾角λs,但有关刃倾角的介绍和讨论主要以车削加工为主线展开,而铣削和车削毕竟有许多不同之处,因此不可能完全适用.对铣削而言,通常认为较大的螺旋角可以增加同时工作的齿数,减少铣削过程中的冲击和增加其平稳性〔2〕,并使立铣刀刀刃锋利、实际前角增大.除此之外,螺旋角的大小对立铣刀的性能究竟还会产生什么样的影响呢?刀具角度之间是相互联系和影响的.不妨首先通过实验和实际加工例,取得初步认识和相关知识,为进一步的深入探讨做准备.2螺旋角与2刃立铣刀铣槽实验实验在立式加工中心上进行.采用直径 12mm的不同螺旋角的2刃立铣刀,铣宽度×高度为12mm×12mm的槽,并以加工后槽的底面为基准,测量槽的两侧面的垂直度误差(侧面最大变形量ΔX),通过比较误差值的大小来评价螺旋角大小对立铣刀铣槽时加工精度的影响.被切削材料为硬度28HRC的碳素钢.实验中各刀具的切削参数统一为:进给速度50mm/min,切削速度29m/min,吃刀深度12mm.切削中冷却液选用油性.实验结果如图1所示.图1螺旋角与铣槽时的加工精度图2铣侧面时的螺旋角与加工精度从实验结果可以看出:(1)逆铣侧总是出现过切,而与之相反,顺铣侧总是出现漏切,且过切量和漏切量的最大点在立铣刀伸出最远处.这一点符合逆铣、顺铣时的刀具变形规律和刀具伸出长度的变形规律.(2)立铣刀的螺旋角小于30°前,不管是顺铣侧还是逆铣侧,垂直度误差值都随螺旋角的增大而增大.螺旋角大于40°以后,又随螺旋角的增大而变小.因此,可以认为立铣刀有较小的螺旋角或有较大的螺旋角时,其铣槽加工的形状精度高.(3)从加工精度看,在螺旋角为0,即切削刃为直刃时精度最高.但从立铣刀螺旋角的基本特性可知,这时完全呈断续切削,切削冲击力大,对刀具本身的制作精度要求高,加工精度对刀具本身精度的依赖性很强,刀具的使用寿命短.所以,实际应用中应根据具体情况辩证地考虑.3螺旋角与4刃立铣刀铣侧面实验在立式加工中心上,用螺旋角分别为30°和55°度的4刃立铣刀铣侧面,比较两种立铣刀随切削宽度(径向吃刀量)的变化对加工精度的影响.立铣刀直径为 25mm,被切削材料为硬度94HRB的45号钢.切削全部采用顺铣方式和干式切削.切削参数统一为:进给速度100mm/min,切削速度26m/min,切削深度38mm.加工后所测得的垂直度误差、平面度误差和表面粗糙度值如图2所示.可以看出,在切削宽度不是特别大时,55°的大螺旋角立铣刀比30°螺旋角立铣刀的加工精度高.这一点与图1的铣槽实验结果相吻合.分析其原因,可以认为这是由于当切削宽度较小时,螺旋角较大的立铣刀实际前角大,刃口锋利,切入性好;切向切削阻力小,减小能量消耗和刀具变形,切削轻快;切削刃与被切削面的接触点多,使立铣刀切入和切出时比较平稳,切削阻力的波动小,减弱了加工中对立铣刀的振动激励等因素的综合效应所致.4螺旋角特性的归纳(1)螺旋角与切削阻力:切向切削阻力随螺旋角的增大而减小,轴向切削阻力随螺旋角的增大而增大.(2)螺旋角与前角:螺旋角的增大使立铣刀实际前角增大,刃口更加锋利.(3)螺旋角与被加工面精度:一般被加工面的垂直度和平面度公差值随螺旋角的增大而增加,但螺旋角大于40°以后反而随螺旋角的增大而呈减小趋势.(4)螺旋角与刀具寿命:圆周刃刃带的磨损速度与螺旋角大小基本成正比;另一方面,当螺旋角很小时,轻微的刀具磨损也将明显降低刀具的切削性能,引起振动,使刀具无法继续使用.当螺旋角过大时,刀具刚性变差,寿命减低.(5)螺旋角与被切削材料:加工硬度低的软质材料时,用大螺旋角,以增大前角,提高刃口的锋利性;加工硬度高的硬质材料时,用小螺旋角,以减小前角,提高刃口的刚性.5结束语螺旋角是螺旋刃立铣刀的主要参数之一,螺旋角大小的改变对刀具的切削加工性能有很大影响.随着数控加工技术和柔性制造技术的发展,在刀具制造工艺上改变螺旋角的大小已成为可能和非常简便.如果进一步深入研究螺旋角大小对螺旋刃立铣刀切削性能的各种影响,在制造和选用螺旋刃立铣刀时,结合机床和工装卡具的性能,根据被加工材料的性能及加工精度、加工效率以及刀具材料和刀具寿命等因素综合考虑,优化螺旋角的大小,无疑会对促进高效、高精铣削加工起重要作用.。
铣削过程中不同铣刀螺旋角对切削力系数影响研究

第1"期2017年12月组合机床与自动化加工技术Modular Machine Tool & Automatic Manufacturing TechnitjueNo. 12Dec. 2017文章编号:1001 -2265 (2017) 12 -01)3-04D01:10. 13462/j. c n k i. m m tam t. 2017. 12.033铣削过程中不同铣刀螺旋角对切削力系数影响研究#毕馨文,王立国(北华大学信息技术与传媒学院,吉林吉林132013)摘要:铣削加工中,铣刀螺旋角的大小对切削力系数具有决定性影响,进而影响整个铣削过程中的稳定性。
为了实现正确计算不同螺旋角铣刀铣削过程中对切削力大小的影响,文章提出两种切削力系数计算方法,分别是基于传统实验测量和正交斜变换的混合计算方法以及泰勒级数法。
首先根据现有知识和相关理论建立了混合计算方法和泰勒级数法的数学模型;然后利用a f a q u s软件对五种不同螺旋角铣刀进行铣削仿真实验得到混合计算方法所需要的切削角和剪切力,用提出的两种方法分别计算铣削过程中的三向切削力;最后通过仿真实验获得的三向切削力值对比证明了混合计算方法和泰勒级数法计算螺旋角对切削力系数影响的准确性。
关键词:螺旋角;稳定性;混合计算方法;泰勒级数法中图分类号:T H162 ;TG506 文献标识码:AStudy on the Influence of Different Helix Angle on Cutting ForceCoefficient during Milling ProcessB I X in-w e n,W A N G L i-g u o(School o f In fo rm a tio n T e c h n o lo g y a nd M e d ia,B e iliu a U n iv e r s ity,J ilin J ilin 132013 ,C h in a) Abstract:D u rin g th e m illin g p ro c e s s,th e size o f th e h e lix a n g le o f th e c u tte r has a d e c is iv e in flu e n c e o n thec u ttin g fo rc e c o e ffic ie n t,w h ic h a ffe c ts th e s ta b ility o f th e w h o le m illin g p ro c e s s.In o rde r to a d iie v e th e c o rre c t c a lc u la tio n o f tlie e ffe c t o f d if e r e n t heli^x a n g le m illin g o n th e c u ttin g f o r c e,tw o k in d s o f c u ttin g fo rc ec o e ffic ie n t c a lc u la tio n m e th od s are p ro p o s e d,w h ic h are based o n th e tr a d itio n a l e x p e rim e n ta l m e a s u re m e n ta nd o rth o g o n a l ob liq u e tra n s fo rm a tio n o f th e h y b ridc a lc u la tio n m e th od a nd the T a y lo r series m e thl y,th e m a th e m a tic a l m o d e l o f th e h y b rid m e th o d an d th e T a y lo r series m e th o d is e s ta b lis h e d a c c o rd in g to thee x is tin g k n o w le d g e a n d re la te d th e o rie s.T h e n,th e s o ftw a re of A B A Q U S is used to s im u la te th e m illing e xp e rim e n t o f fiv e d iffe re n t s p ira l a n g le m illin g to o ls.T h e c u ttin g a n g le a n d shear A n d th e th re e-w a y c u ttin gfo rc e in th e m illin g p rocess is c a lc u la te d b y th e tw o m e th o d s.F i n H y,th e c o m p a is o n o f tlie th re e-w a y c u ttin g fo rc e o b ta in e d b y t h e s im u la tio n e x p e rim e n t s lio w s th a t tlie m ix e d c a lc u la tio n m e tlio d a nd th e T a y lo r serie s m e tlio d h a v e th e e ffe c t o f c a lc u la tin g th e heli^x a n g le o n th e c u ttin g fo rc e c o e f ic ie n t a c c u ra c y.Key words:h e lix a n g le;s ta b ility;h y b rid c a lc u la tio n m e th o d;ta y lo r series m e th o d〇引言近年来,机械加工行业竞争愈加激烈。
立铣刀基础知识PPT课件
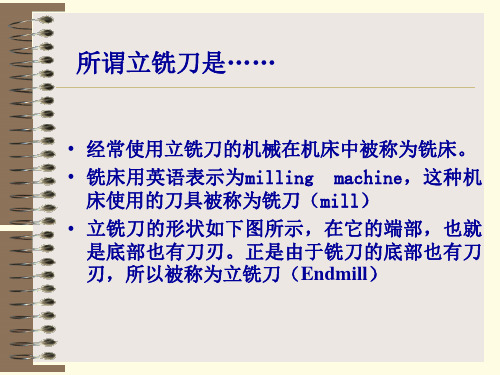
螺旋方向与切刃的方向
1、定义
螺旋方向
从立铣刀的正面看,容屑槽 朝刀柄方向伸延时是向左倾 的就叫左螺旋,向右倾的就 叫右螺旋。
切刃的方向
• 切削刃的朝向因立铣刀工作 时的回转方向而异。把立铣 刀的底刃朝上摆放并从立铣 刀的正面看,切削刃的刃口 朝左边的就叫左刃,朝右边 的就叫右刃。
右螺旋 右刃
左螺旋 左刃
切削中会被切屑塞满。
7、底刃…………指刀具端面的切削刃。 8、底刃前角…………底刃前刀面与轴线的夹角。 9、底刃后角…………指在底刃上的第一后角。 10、底刃第二后角…………指在底刃上的第二后角。 11、底刃后角宽…………底刃后角具有的宽度。 12、底刃容屑槽…………在底刃上的容屑槽。 13、螺旋角…………螺旋切削刃与轴线的夹角。 14、圆周刃倒锥…………立铣刀从刀尖到刀柄侧的直径略微减小。像这 样带有向后的锥度称为倒锥。 15、底刃倒锥…………在底刃面,从刀尖向中心有微微的中凹,这个角
所谓立铣刀是……
• 经常使用立铣刀的机械在机床中被称为铣床。 • 铣床用英语表示为milling machine,这种机
床使用的刀具被称为铣刀(mill) • 立铣刀的形状如下图所示,在它的端部,也就
是底部也有刀刃。正是由于铣刀的底部也有刀 刃,所以被称为立铣刀(Endmill)
底部带刃(END)+铣床(Milling Machine)上 使用的刀具(MILL)
1、圆周刃前角…………圆周刃的前刀面与刀尖与中心的连线形成的角度, 它是影响立铣刀切削性能的重要因素。 2、圆周刃后角…………称作圆周刃第一后角,是与圆周刃前角同样重要 的要素。 3、圆周刃第二后角……圆周刃的第二后角立铣刀切削时保证工件与立铣 刀之间有充分的间隙。 4、圆周第一刃刃带宽…………圆周刃后角具有的宽度。 5、圆周总刃带宽…………带有圆周刃后角与圆周刃第二后角的总宽度 6、容屑槽…………容纳切屑的地方,也叫作排屑槽。如果切屑槽小的话,
立铣刀螺旋角大小对切削性能的影响

立铣刀螺旋角大小对切削性能的影响1螺旋刃立铣刀的基本特性与问题的提出立铣刀的基本刃口形状(螺旋槽形状)有直形和螺旋形两种.由于螺旋刃立铣刀相对于直刃具有切削轻快、平稳、效率高和使用范围广等优点,因此在铣削加工中得到了广泛应用.根据加工设备和加工对象的不同要求,螺旋刃立铣刀有左刃、右刃和左螺旋、右螺旋之分的4种不同组合〔1〕,其中左刃左螺旋和右刃右螺旋在加工中的轴向切削阻力有把立铣刀从刀夹中拔出的趋势,需采用拉紧螺栓克服轴向切削阻力.而左刃右螺旋和右刃左螺旋的轴向切削阻力刚好把立铣刀压向夹头方,故多采用锥柄加扁尾,以适应大功率切削.因为右刃右螺旋立铣刀可让切屑沿排屑槽向柄部排出,易保证切削的平稳进行,符合机床主轴旋向标准,在高性能夹头的支持下装卸方便,所以,其使用范围最广,使用量最大.实际应用中的螺旋刃立铣刀,其螺旋角通常在30°~45°.在刀具原理、设计和应用技术领域,根据工件材料、刀具材料及切削加工诸参数的不同,有关螺旋刃立铣刀的切削力、扭矩、切削功率及前角、后角等主要刀具角度的设计计算公式、实验数据与使用经验等资料很多,但有关螺旋角大小与立铣刀加工性能的讨论和资料介绍很少.一般认为,螺旋刃立铣刀的螺旋角β就是刃倾角λs,但有关刃倾角的介绍和讨论主要以车削加工为主线展开,而铣削和车削毕竟有许多不同之处,因此不可能完全适用.对铣削而言,通常认为较大的螺旋角可以增加同时工作的齿数,减少铣削过程中的冲击和增加其平稳性〔2〕,并使立铣刀刀刃锋利、实际前角增大.除此之外,螺旋角的大小对立铣刀的性能究竟还会产生什么样的影响呢?刀具角度之间是相互联系和影响的.不妨首先通过实验和实际加工例,取得初步认识和相关知识,为进一步的深入探讨做准备.2螺旋角与2刃立铣刀铣槽实验实验在立式加工中心上进行.采用直径12mm的不同螺旋角的2刃立铣刀,铣宽度×高度为12mm×12mm的槽,并以加工后槽的底面为基准,测量槽的两侧面的垂直度误差(侧面最大变形量ΔX),通过比较误差值的大小来评价螺旋角大小对立铣刀铣槽时加工精度的影响.被切削材料为硬度28HRC的碳素钢.实验中各刀具的切削参数统一为:进给速度50mm/min,切削速度29m/min,吃刀深度12mm.切削中冷却液选用油性.实验结果如图1所示.图1螺旋角与铣槽时的加工精度图2铣侧面时的螺旋角与加工精度从实验结果可以看出:(1)逆铣侧总是出现过切,而与之相反,顺铣侧总是出现漏切,且过切量和漏切量的最大点在立铣刀伸出最远处.这一点符合逆铣、顺铣时的刀具变形规律和刀具伸出长度的变形规律.(2)立铣刀的螺旋角小于30°前,不管是顺铣侧还是逆铣侧,垂直度误差值都随螺旋角的增大而增大.螺旋角大于40°以后,又随螺旋角的增大而变小.因此,可以认为立铣刀有较小的螺旋角或有较大的螺旋角时,其铣槽加工的形状精度高.(3)从加工精度看,在螺旋角为0,即切削刃为直刃时精度最高.但从立铣刀螺旋角的基本特性可知,这时完全呈断续切削,切削冲击力大,对刀具本身的制作精度要求高,加工精度对刀具本身精度的依赖性很强,刀具的使用寿命短.所以,实际应用中应根据具体情况辩证地考虑.3螺旋角与4刃立铣刀铣侧面实验在立式加工中心上,用螺旋角分别为30°和55°度的4刃立铣刀铣侧面,比较两种立铣刀随切削宽度(径向吃刀量)的变化对加工精度的影响.立铣刀直径为25mm,被切削材料为硬度94HRB的45号钢.切削全部采用顺铣方式和干式切削.切削参数统一为:进给速度100mm/min,切削速度26m/min,切削深度38mm.加工后所测得的垂直度误差、平面度误差和表面粗糙度值如图2所示.可以看出,在切削宽度不是特别大时,55°的大螺旋角立铣刀比30°螺旋角立铣刀的加工精度高.这一点与图1的铣槽实验结果相吻合.分析其原因,可以认为这是由于当切削宽度较小时,螺旋角较大的立铣刀实际前角大,刃口锋利,切入性好;切向切削阻力小,减小能量消耗和刀具变形,切削轻快;切削刃与被切削面的接触点多,使立铣刀切入和切出时比较平稳,切削阻力的波动小,减弱了加工中对立铣刀的振动激励等因素的综合效应所致.4螺旋角特性的归纳(1)螺旋角与切削阻力:切向切削阻力随螺旋角的增大而减小,轴向切削阻力随螺旋角的增大而增大.(2)螺旋角与前角:螺旋角的增大使立铣刀实际前角增大,刃口更加锋利.(3)螺旋角与被加工面精度:一般被加工面的垂直度和平面度公差值随螺旋角的增大而增加,但螺旋角大于40°以后反而随螺旋角的增大而呈减小趋势.(4)螺旋角与刀具寿命:圆周刃刃带的磨损速度与螺旋角大小基本成正比;另一方面,当螺旋角很小时,轻微的刀具磨损也将明显降低刀具的切削性能,引起振动,使刀具无法继续使用.当螺旋角过大时,刀具刚性变差,寿命减低.(5)螺旋角与被切削材料:加工硬度低的软质材料时,用大螺旋角,以增大前角,提高刃口的锋利性;加工硬度高的硬质材料时,用小螺旋角,以减小前角,提高刃口的刚性.5结束语螺旋角是螺旋刃立铣刀的主要参数之一,螺旋角大小的改变对刀具的切削加工性能有很大影响.随着数控加工技术和柔性制造技术的发展,在刀具制造工艺上改变螺旋角的大小已成为可能和非常简便.如果进一步深入研究螺旋角大小对螺旋刃立铣刀切削性能的各种影响,在制造和选用螺旋刃立铣刀时,结合机床和工装卡具的性能,根据被加工材料的性能及加工精度、加工效率以及刀具材料和刀具寿命等因素综合考虑,优化螺旋角的大小,无疑会对促进高效、高精铣削加工起重要作用.(注:文档可能无法思考全面,请浏览后下载,供参考。
螺旋角对切削过程的影响

螺旋角对切削过程的影响
螺旋角是指切削工具前沿与刀具轴线的夹角,通常在金属切削加工中,通过改变螺旋角的大小来影响切削力、切削温度、表面质量等切削性能参数。
具体来说,对于切削角度相同的刀具,在其他条件不变的情况下,螺旋角越小,切削力将会越小,切屑排出也更加容易。
而螺旋角过小则易引起装夹力损伤和表面质量的下降。
此外,螺旋角的大小也会对刀具的刃磨和寿命产生影响。
一般来说,螺旋角较大时,切削刃更容易被磨损,因为采取过多的磨削会使螺旋角过小,进而导致质量下降。
因此,在实际加工中,需要根据具体材料、加工要求和刀具材质等因素,综合考虑选择适合的螺旋角。
切削参数对切屑变形的影响
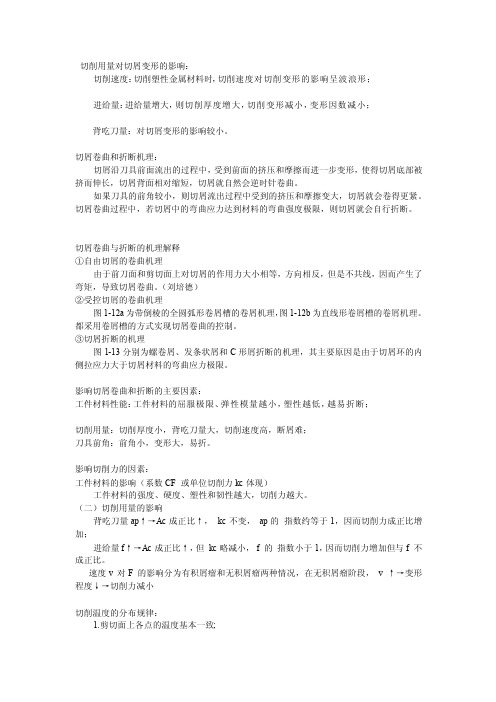
切削用量对切屑变形的影响:切削速度:切削塑性金属材料时,切削速度对切削变形的影响呈波浪形;进给量:进给量增大,则切削厚度增大,切削变形减小,变形因数减小;背吃刀量:对切屑变形的影响较小。
切屑卷曲和折断机理:切屑沿刀具前面流出的过程中,受到前面的挤压和摩擦而进一步变形,使得切屑底部被挤而伸长,切屑背面相对缩短,切屑就自然会逆时针卷曲。
如果刀具的前角较小,则切屑流出过程中受到的挤压和摩擦变大,切屑就会卷得更紧。
切屑卷曲过程中,若切屑中的弯曲应力达到材料的弯曲强度极限,则切屑就会自行折断。
切屑卷曲与折断的机理解释①自由切屑的卷曲机理由于前刀面和剪切面上对切屑的作用力大小相等,方向相反,但是不共线,因而产生了弯矩,导致切屑卷曲。
(刘培德)②受控切屑的卷曲机理图1-12a为带倒棱的全圆弧形卷屑槽的卷屑机理,图1-12b为直线形卷屑槽的卷屑机理。
都采用卷屑槽的方式实现切屑卷曲的控制。
③切屑折断的机理图1-13分别为螺卷屑、发条状屑和C形屑折断的机理,其主要原因是由于切屑环的内侧拉应力大于切屑材料的弯曲应力极限。
影响切屑卷曲和折断的主要因素:工件材料性能:工件材料的屈服极限、弹性模量越小,塑性越低,越易折断;切削用量:切削厚度小,背吃刀量大,切削速度高,断屑难;刀具前角:前角小,变形大,易折。
影响切削力的因素:工件材料的影响(系数CF 或单位切削力kc体现)工件材料的强度、硬度、塑性和韧性越大,切削力越大。
(二)切削用量的影响背吃刀量ap↑→Ac成正比↑,kc不变,ap的指数约等于1,因而切削力成正比增加;进给量f↑→Ac成正比↑,但kc略减小,f 的指数小于1,因而切削力增加但与f 不成正比。
速度v 对F 的影响分为有积屑瘤和无积屑瘤两种情况,在无积屑瘤阶段,v ↑→变形程度↓→切削力减小切削温度的分布规律:1.剪切面上各点的温度基本一致;2.前、后刀面上的最高温度都处于离刀刃一定距离的地方;后刀面的温度降低和升高在极短时间内完成;3.在剪切区域内,垂直于剪切方向上的温度梯度较大;垂直于前刀面的切屑底层的温度梯度较大;4.工件材料塑性越大,前刀面与切屑的接触长度越长,温度分布越均匀;工件材料脆性越大,最高温度所在的点离刀刃越近;工件材料导热系数越低,前、后刀面上的温度越高。
铣刀的几何参数

铣刀的分类
可转位铣刀的四种分类 Milling cutters categorization
面铣刀
可ห้องสมุดไป่ตู้位槽铣刀(如三面刃 铣刀)
立铣刀
圆柱铣刀的几何角度
螺旋角——螺旋切削刃展开成直线后,与铣刀轴线内的夹角。ω=λ s 1) 它能使刀齿逐渐切入和切离工件。 2) 能增加实际前角,使切削轻快平稳,同时形成螺旋形切屑,排屑易、可防止切屑堵塞 现象。 3) 一般 [ 细齿圆柱形铣刀:ω= 30 ° ~35 °; 粗齿圆柱形铣刀:ω= 40 °~45 ° ]
面上,故适当增大后角 a 0 于减少磨损通常:
a 0 = 12 ° ~16 °(粗铣取小值,精铣取大值)。
面铣刀的几何角度
机夹面铣刀每个刀齿安装在刀上之前,相当于一把车刀。
2. 前角:
γ 1) 通常:图样标注 n (以便于制造);
γ γ γ 2) 检验时测量 0tg n = tg 0cos ω
γ 3) 按被加工材料选择:铣削钢时取 n = 10 °~20 °
γ 4) 铣削铸铁时取 n =5 ° ~15 °
3. 后角: 圆柱形铣刀后角规定 P 0 平面内变量,磨损主要发生在后
刀具几何参数与切削用量的合理选择

切削热
合理的刀具几何参数和切 削用量可以降低切削热, 减少因热变形对加工精度 的影响,提高加工效率。
04 实际应用案例分析
案例一
总结词
根据工件材料和加工要求,选择合适的刀具几何参数和切削用量,提高加工效率和表面 质量。
详细描述
在车削加工中,刀具的几何参数如前角、后角和刃倾角对切削力和切削热有显著影响。 前角增大,切削力减小,切削热增加;后角增大,切削热减少,但切削力可能增大。选 择合适的切削用量,如切削速度、进给量和切削深度,可以优化加工效率和表面质量。
刀具主副偏角
主副偏角的大小影响切削层的形状和切削宽度。减小主副 偏角,可减小切削层的截面积,降低切削力,但刀尖强度 减弱。
切削用量对加工质量的影响
1 2
切削速度
切削速度过高可能导致工件表面粗糙度增加或产 生积屑瘤;切削速度过低则可能使切削力增大, 导致刀具磨损。
进给量
进给量过大会导致切削力增大,工件表面粗糙度 增加;进给量过小则可能影响加工效率。
案例四
总结词
根据工件材料、磨料和加工要求,选择合适的刀具几何参数和切削用量,以提高磨削效率和表面质量。
详细描述
在磨削加工中,刀具的几何参数如磨料粒度、结合剂硬度对磨削效率和表面质量有重要影响。磨料粒度越细,表 面粗糙度越低;结合剂硬度越高,磨粒越稳定。选择合适的切削用量,如磨削深度、磨削速度和进给速度,可以 优化磨削效率和表面质量。
谢谢聆听
进给量过小可能导致加 工效率低下,过大则可 能导致加工表面质量下 降。
切削深度的合理选择
01
切削深度影响切削力、切削热和 刀具寿命。
02
选择合适的切削深度可以降低切 削力,减少热量产生,提高刀具
立铣刀讲义
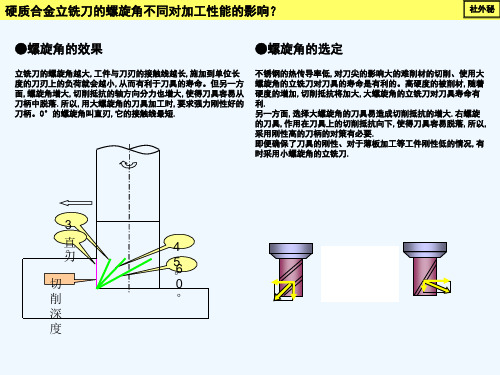
问题
侧面加工的加工面精度改善?
立铣刀进行侧面切削加工时,加工面变粗糙、无法加工出直角等,达到所定的加工面精度困难.选 用何种刀具、采用什么方法加工才能解决这方面的问题?
无法得到所要加工精度的原因
即便高刚性的硬质合金立铣刀,刃长以及颈长尺寸过度的情况,刀刃(长)部分的退 让、振颤容易发生,造成加工精度、工具寿命低下.刀刃(长)部分的退让在加工被 削材的过程中,刀具先端发生扰曲(弯曲)现象,加工面变成弓形 其他的原因,刀具的保持刚性以及跳动精度低的情况也有可能是切削条件不合理造 成的.
影响切削的因素
材料
材质
精度
铣刀
材质
种类
刀柄
夹持方式
保持精度
CNC机床
主轴特性
驱动特性
加工形状
尺寸精度
主轴连接方式
问题
侧面加工、槽加工、底面加工使用同一刀具(不分别使用)
按加工种类刀具备齐,刀具管理会变得繁杂,有没有可能用1支刀具就可进行多种工程的加工?
螺旋角、刃数不同刀具的特征
一般来说市场上广泛流通的螺旋角30° 的2刃,4刃刀具也可侧面、槽和底面加工.不过2刃的立铣刀进行侧面加工. 若进给不提高,不能成为有效的加工.同时4刃的立铣刀进行槽加工,排屑槽太窄,容易发生切屑堆积,无法排出. 3刃立铣刀兼具2刃4刃中间的特长,侧面、槽加工两方面都可对应
不是进给而是切削量调整
如果刀具非正常磨损、崩刃而造成的急剧磨损的情况有必要进行刀具的选定、
切削条件的修正.为了提高刀刃强度,用负前角形状会有效,同时选择硬度 高的细小的超超微粒硬质合金材料.另外高硬度的CBN也将会增加.而切削 条件的修正不是进给速度大幅下调,而是首先下调切削量.为了保持刀具的 耐磨性,实现良好的加工面,切削速度方面选择高速要比低速有利(重要).切 削量下调以便在高速领域可实现稳定的加工.
不同形状钻头的切削特征
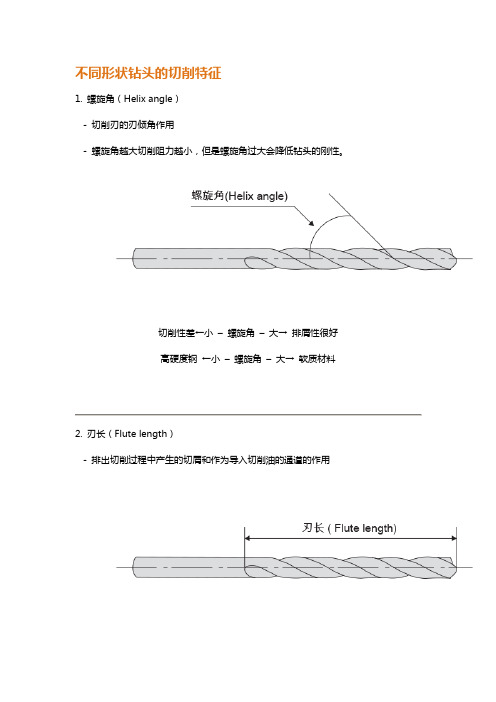
不同形状钻头的切削特征
1. 螺旋角(Helix angle)
- 切削刃的刃倾角作用
- 螺旋角越大切削阻力越小,但是螺旋角过大会降低钻头的刚性。
切削性差←小–螺旋角–大→排屑性很好
高硬度钢←小–螺旋角–大→软质材料
2. 刃长(Flute length)
- 排出切削过程中产生的切屑和作为导入切削油的通道的作用
排屑性能低←小–刃长–大→刚性差
3. 钻顶角(Point angle)
- 影响到切削性能,由工件决定角度
扭矩增加←小–钻顶角–大→扭矩减小
毛刺增多←小–钻顶角–大→毛刺减小
软质材料←小–钻顶角–大→高硬度钢
4. 钻边宽度(Margin width)
- 钻头外径与工件内径接触的部分,起到防止弯曲和引导作用。
- 主要由钻头的大小决定。
切削阻力减少←小–钻边宽度–大→切削阻力增加
引导性不够←小–钻边宽度–大→引导性良好
5. 钻腹厚度(Web)
- 形成钻头的轴心部,赋有刚性。
- 钻腹厚度较大时为降低阻力需做修磨。
切削阻力减小←小–钻腹厚度–大→切削阻力增加
刚性减小←小–钻腹厚度–大→刚性增加
排屑性良好←小–钻腹厚度–大→排屑性降低
软质材料←小–钻腹厚度–大→ 高硬度钢。
铣刀参数及涂层对0Cr18Ni9不锈钢铣削性能的影响
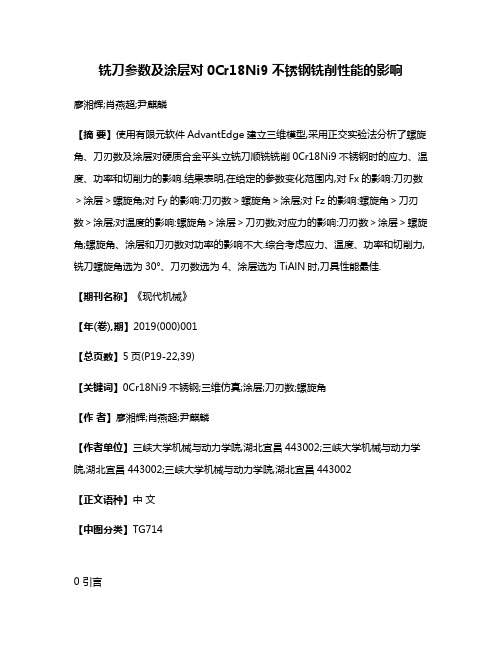
铣刀参数及涂层对0Cr18Ni9不锈钢铣削性能的影响廖湘辉;肖燕超;尹麒麟【摘要】使用有限元软件AdvantEdge建立三维模型,采用正交实验法分析了螺旋角、刀刃数及涂层对硬质合金平头立铣刀顺铣铣削0Cr18Ni9不锈钢时的应力、温度、功率和切削力的影响.结果表明,在给定的参数变化范围内,对Fx的影响:刀刃数>涂层>螺旋角;对Fy的影响:刀刃数>螺旋角>涂层;对Fz的影响:螺旋角>刀刃数>涂层;对温度的影响:螺旋角>涂层>刀刃数;对应力的影响:刀刃数>涂层>螺旋角;螺旋角、涂层和刀刃数对功率的影响不大.综合考虑应力、温度、功率和切削力,铣刀螺旋角选为30°、刀刃数选为4、涂层选为TiAlN时,刀具性能最佳.【期刊名称】《现代机械》【年(卷),期】2019(000)001【总页数】5页(P19-22,39)【关键词】0Cr18Ni9不锈钢;三维仿真;涂层;刀刃数;螺旋角【作者】廖湘辉;肖燕超;尹麒麟【作者单位】三峡大学机械与动力学院,湖北宜昌443002;三峡大学机械与动力学院,湖北宜昌443002;三峡大学机械与动力学院,湖北宜昌443002【正文语种】中文【中图分类】TG7140 引言0Cr18Ni9不锈钢因其良好的无磁性、耐高温、耐蚀性、机械性能和无热处理硬化现象等,被广泛用于医疗、核工、航天航空、一般化工设备和食品用设备中,在不锈钢总产量中其占比在30%以上。
但0Cr18Ni9不锈钢塑性大、韧性高、切削力大、切削加工温度高、表面硬化严重,使得加工效率低,刀具磨损快,刀具寿命低[1-2]。
选择合理的刀具几何参数及涂层可以有效改善0Cr18Ni9不锈钢切削加工性能,从而延长刀具寿命,提高加工效率。
近年来许多学者对0Cr18Ni9不锈钢进行大量的实验和仿真研究,这些研究大多是从铣削参数和冷却方式这两方面进行,较少研究铣刀几何参数及涂层对铣削性能的影响。
P Chockalingam等研究了合成油、水基乳液和压缩冷空气对铣削加工0Cr18Ni9不锈钢表面粗糙度和切削力的影响[3]。
钨钢铣刀的使用技巧

30°螺旋角 2刃 30°螺旋角 4刃 45°螺旋角 3刃
3刃立铣刀下记理由使它的形状能抑制振颤与刚性同时兼有、侧面加工和槽加工同时可对应 第一:不同于偶数刃,切削刃没有处在对角线上,具有振颤不易发生的特点 第二:衡量刚性的指标有刃径的芯厚与维持刚性的形状等. 30°平刀芯厚占65%;45°平刀芯厚占70%; 15°的芯厚以上的随形状可实现刚性
●螺旋角的选定
不锈钢的热传导率低,对刀尖的影响大的难削材的切削、使用大 螺旋角的立铣刀对刀具的寿命是有利的。高硬度的被削材,随着 硬度的增加,切削抵抗将加大,大螺旋角的立铣刀对刀具寿命有 利. 另一方面,选择大螺旋角的刀具易造成切削抵抗的增大.右螺旋 的刀具,作用在刀具上的切削抵抗向下,使得刀具容易脱落,所以, 采用刚性高的刀柄的对策有必要. 即便确保了刀具的刚性、对于薄板加工等工件刚性低的情况,有 时采用小螺旋角的立铣刀.
切削路径对刀具的影响 ●高速加工首选等高切削
等高切削
仿形切削
为了得到最长的刀具寿命,在铣削过程中应使切削刃尽可能长时间地保持连续切削, 最好是顺铣.在这方面采用等高线铣削是最好方法,它能让刀具始终沿着一个方向切削, 受力变化是最小的. 而仿形铣削路径常常是逆铣和顺铣的混合(之字形),这意味切削中会频繁地吃刀和 退刀,切削刃和切削过程便更容易受到工作负载和方向改变的不利影响,工作负载和方 向的变会引起切削力和刀具弯曲的变化,使刀具产生崩刃或异刚性刀具切削刃部的退让可以抑制.短刃长、大直径、多刃数是保持高刚性 的刀具
多段加工的有效性
短刃刀具具有高刚性,侧面加工时柄部易发生干涉.为了避免干涉,(避空)比刀具刃 径小、设定颈长的细长刀具使用是非常有必要的. 若有这类刀具,Z方向的多段加工成为可能.同时切削速度、进给速度可以实现高速, 实现加工时间缩短.
高速铣削刀具及切削参数的选择

高速铣削刀具及切削参数的选择摘要:通过等效类比的方法研究了高速铣削刀具选择的一般原则。
推导了球头铣刀的有效直径和有效线速度的计算公式,以此进一步确定转速,通过试验的方法测定了径向铣削深度和每齿进给量对表面粗糙度的影响。
关键词:高速铣削刀具;有效直径;有效线速度;切削参数;表面粗糙度作者:宋志国,宋艳,常州信息职业技术学院0 引言传统意义上的高速切削是以切削速度的高低来进行分类的,而铣削机床则是以转速的高低进行分类。
如果从切削变形的机理来看高速切削,则前一种分类比较合适;但是若从切削工艺的角度出发,则后一种更恰当。
这是因为随着主轴转速的提高,机床的结构、刀具结构、刀具装夹和机床特性都有本质上的改变。
高转速意味着高离心力,传统的7∶24锥柄,弹簧夹头、液压夹头在离心力的作用下,难以提供足够的夹持力;同时为避免切削振动要求刀具系统具有更高的动平衡精度。
高速切削的最大优势并不在于速度、进给速度提高所导致的效率提高;而是由于采用了更高的切削速度和进给速度,允许采用较小的切削用量进行切削加工。
由于切削用量的降低,切削力和切削热随之下降,工艺系统变形减小,可以避免铣削颤振。
1 刀具的选择通常选用图1所示的3种立铣刀进行铣削加工,在高速铣削中一般不推荐使用平底立铣刀。
平底立铣刀在切削时刀尖部位由于流屑干涉,切屑变形大,同时有效切削刃长度最短,导致刀尖受力大、切削温度高,导致快速磨损。
在工艺允许的条件下,尽量采用刀尖圆弧半径较大的刀具进行高速铣削。
图1 立铣刀示意图随着立铣刀刀尖圆弧半径的增加,平均切削厚度和主偏角均下降,同时刀具轴向受力增加可以充分利用机床的轴向刚度,减小刀具变形和切削振动(图2)。
图2 立铣刀受力示意图图3为高速铣削铝合金时,等铣削面积时两种刀具的铣削力对比。
刀具为直径Φ10mm的2齿整体硬质合金立铣刀,螺旋角30度。
刀尖圆弧半径为1.5mm和无刀尖圆弧的两种刀具。
图3 刀尖圆弧半径对铣削力的影响铣削面积同定为a,a p·a e=2.Omm2。
- 1、下载文档前请自行甄别文档内容的完整性,平台不提供额外的编辑、内容补充、找答案等附加服务。
- 2、"仅部分预览"的文档,不可在线预览部分如存在完整性等问题,可反馈申请退款(可完整预览的文档不适用该条件!)。
- 3、如文档侵犯您的权益,请联系客服反馈,我们会尽快为您处理(人工客服工作时间:9:00-18:30)。
立铣刀螺旋角大小对切削性能的影响
1螺旋刃立铣刀的基本特性与问题的提出立铣刀的基本刃口形状(螺旋槽形状)有直形和螺旋形两种.由于螺旋刃立铣刀相对于直刃具有切削轻快、平稳、效率高和使用范围广等优点,因此在铣削加工中得到了广泛应用.根据加工设备和加工对象的不同要求,螺旋刃立铣刀有左刃、右刃和左螺旋、右螺旋之分的4种不同组合〔1〕,其中左刃左螺旋和右刃右螺旋在加工中的轴向切削阻力有把立铣刀从刀夹中拔出的趋势,需采用拉紧螺栓克服轴向切削阻力.而左刃右螺旋和右刃左螺旋的轴向切削阻力刚好把立铣刀压向夹头方,故多采用锥柄加扁尾,以适应大功率切削.因为右刃右螺旋立铣刀可让切屑沿排屑槽向柄部排出,易保证切削的平稳进行,符合机床主轴旋向标准,在高性能夹头的支持下装卸方便,所以,其使用范围最广,使用量最大.实际应用中的螺旋刃立铣刀,其螺旋角通常在30°~45°.在刀具原理、设计和应用技术领域,根据工件材料、刀具材料及切削加工诸参数的不同,有关螺旋刃立铣刀的切削力、扭矩、切削功率及前角、后角等主要刀具角度的设计计算公式、实验数据与使用经验等资料很多,但有关螺旋角大小与立铣刀加工性能的讨论和资料介绍很少.一般认为,螺旋刃立铣刀的螺旋角β就是刃倾角λs,但有关刃倾角的介绍和讨论主要以车削加工为主线展开,而铣削和车削毕竟有许多不同之处,因此不可能完全适用.对铣削而言,通常认为较大的螺旋角可以增加同时工作的齿数,减少铣削过程中的冲击和增加其平稳性〔2〕,并使立铣刀刀刃锋利、实际前角增大.除此之外,螺旋角的大小对立铣刀的性能究竟还会产生什么样的影响呢?刀具角度之间是相互联系和影响的.不妨首先通过实验和实际加工例,取得初步认识和相关知识,为进一步的深入探讨做准备.2螺旋角与2刃立铣刀铣槽实验实验在立式加工中心上进行.采用直径12mm的不同螺旋角的2刃立铣刀,铣宽度×高度为12mm×12mm的槽,并以加工后槽的底面为基准,测量槽的两侧面的垂直度误差(侧面最大变形量ΔX),通过比较误差值的大小来评价螺旋角大小对立铣刀铣槽时加工精度的影响.被切削材料为硬度28HRC的碳素钢.实验中各刀具的切削参数统一为:进给速度50mm/min,切削速度29m/min,吃刀深度12mm.切削中冷却液选用油性.实验结果如图1所示.图1螺旋角与铣槽时的加工精度图2铣侧面时的螺旋角与加工精度从实验结果可以看出:(1)逆铣侧总是出现过切,而与之相反,顺铣侧总是出现漏切,且过切量和漏切量的最大点在立铣刀伸出最远处.这一点符合逆铣、顺铣时的刀具变形规律和刀具伸出长度的变形规律.(2)立铣刀的螺旋角小于30°前,不管是顺铣侧还是逆铣侧,垂直度误差值都随螺旋角的增大而增大.螺旋角大于40°以后,又随螺旋角的增大而变小.因此,可以认为立铣刀有较小的螺旋角或有较大的螺旋角时,其铣槽加工的形状精度高.(3)从加工精度看,在螺旋角为0,即切削刃为直刃时精度最高.但从立铣刀螺旋角的基本特性可知,这时完全呈断续切削,切削冲击力大,对刀具本身的制作精度要求高,加工精度对刀具本身精度的依赖性很强,刀具的使用寿命短.所以,实际应用中应根据具体情况辩证地考虑.3螺旋角与4刃立铣刀铣侧面实验在立式加工中心上,用螺旋角分别为30°和55°度的4刃立铣刀铣侧面,比较两种立铣刀随切削宽度(径向吃刀量)的变化对加工精度的影响.立铣刀直径为25mm,被切削材料为硬度94HRB的45号钢.切削全部采用顺铣方式
和干式切削.切削参数统一为:进给速度100mm/min,切削速度26m/min,切削深度38mm.加工后所测得的垂直度误差、平面度误差和表面粗糙度值如图2所示.可以看出,在切削宽度不是特别大时,55°的大螺旋角立铣刀比30°螺旋角立铣刀的加工精度高.这一点与图1的铣槽实验结果相吻合.分析其原因,可以认为这是由于当切削宽度较小时,螺旋角较大的立铣刀实际前角大,刃口锋利,切入性好;切向切削阻力小,减小能量消耗和刀具变形,切削轻快;切削刃与被切削面的接触点多,使立铣刀切入和切出时比较平稳,切削阻力的波动小,减弱了加工中对立铣刀的振动激励等因素的综合效应所致.4螺旋角特性的归纳(1)螺旋角与切削阻力:切向切削阻力随螺旋角的增大而减小,轴向切削阻力随螺旋角的增大而增大.(2)螺旋角与前角:螺旋角的增大使立铣刀实际前角增大,刃口更加锋利.(3)螺旋角与被加工面精度:一般被加工面的垂直度和平面度公差值随螺旋角的增大而增加,但螺旋角大于40°以后反而随螺旋角的增大而呈减小趋势.(4)螺旋角与刀具寿命:圆周刃刃带的磨损速度与螺旋角大小基本成正比;另一方面,当螺旋角很小时,轻微的刀具磨损也将明显降低刀具的切削性能,引起振动,使刀具无法继续使用.当螺旋角过大时,刀具刚性变差,寿命减低.(5)螺旋角与被切削材料:加工硬度低的软质材料时,用大螺旋角,以增大前角,提高刃口的锋利性;加工硬度高的硬质材料时,用小螺旋角,以减小前角,提高刃口的刚性.5结束语螺旋角是螺旋刃立铣刀的主要参数之一,螺旋角大小的改变对刀具的切削加工性能有很大影响.随着数控加工技术和柔性制造技术的发展,在刀具制造工艺上改变螺旋角的大小已成为可能和非常简便.如果进一步深入研究螺旋角大小对螺旋刃立铣刀切削性能的各种影响,在制造和选用螺旋刃立铣刀时,结合机床和工装卡具的性能,根据被加工材料的性能及加工精度、加工效率以及刀具材料和刀具寿命等因素综合考虑,优化螺旋角的大小,无疑会对促进高效、高精铣削加工起重要作用.。