核电厂稳压器电加热器技术综述
核电厂稳压器电加热器自动控制研究
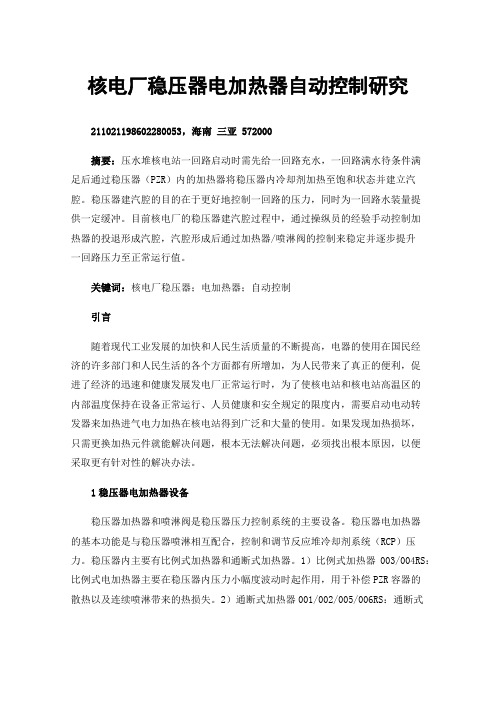
核电厂稳压器电加热器自动控制研究******************,海南三亚572000摘要:压水堆核电站一回路启动时需先给一回路充水,一回路满水待条件满足后通过稳压器(PZR)内的加热器将稳压器内冷却剂加热至饱和状态并建立汽腔。
稳压器建汽腔的目的在于更好地控制一回路的压力,同时为一回路水装量提供一定缓冲。
目前核电厂的稳压器建汽腔过程中,通过操纵员的经验手动控制加热器的投退形成汽腔,汽腔形成后通过加热器/喷淋阀的控制来稳定并逐步提升一回路压力至正常运行值。
关键词:核电厂稳压器;电加热器;自动控制引言随着现代工业发展的加快和人民生活质量的不断提高,电器的使用在国民经济的许多部门和人民生活的各个方面都有所增加,为人民带来了真正的便利,促进了经济的迅速和健康发展发电厂正常运行时,为了使核电站和核电站高温区的内部温度保持在设备正常运行、人员健康和安全规定的限度内,需要启动电动转发器来加热进气电力加热在核电站得到广泛和大量的使用。
如果发现加热损坏,只需更换加热元件就能解决问题,根本无法解决问题,必须找出根本原因,以便采取更有针对性的解决办法。
1稳压器电加热器设备稳压器加热器和喷淋阀是稳压器压力控制系统的主要设备。
稳压器电加热器的基本功能是与稳压器喷淋相互配合,控制和调节反应堆冷却剂系统(RCP)压力。
稳压器内主要有比例式加热器和通断式加热器。
1)比例式加热器003/004RS:比例式电加热器主要在稳压器内压力小幅度波动时起作用,用于补偿PZR容器的散热以及连续喷淋带来的热损失。
2)通断式加热器001/002/005/006RS:通断式加热器用于反应堆启动或瞬态过程,主要考虑在机组各种瞬态扰动下对一回路压力进行补偿和调节。
2温度控制系统设计分析(1)工艺控制系统的基本要求:工艺控制系统(称为设定值)的输入保持不变时,整个系统应处于相对平衡状态,调整后的参数应保持在允许的设定值或偏差范围内。
当所有内部和外部生产因素和条件都发生变化时,需要对正常生产进行干扰,调整后的参数将与原始参数发生变化,工艺控制系统是不断克服不同类型干扰的影响,以便调整后的参数能够恢复到原始参数主要操作方法如下:风机从进气管中抽出空气,分别通过冷却器和电流器获得压力和温度符合技术要求的空气。
核电厂稳压器电加热器典型故障及应对措施

图 1 稳 压 器 电加 热 器 布 置 图
波纹 管 保 温盒 与 电加 热 器接 线 柱 距 离 过 近 ,热 空 气 自
然对流将导致加热器接线柱密封材料过热破裂 ,潮气入侵
将 造成 加 热 器绝 缘 性 能下 降 ;机 组 功 率 运 行 期 间 ,波 纹 管
1稳压器 电加热器简 介
2 3 防火包 裹 中 B列稳压 器 电加热 器 电缆 高 温烧毁
.
温度低于 5 0 ( 、 。
稳压 器 电加 热 器 存 渊 试期 间 ,B列 稳 压 器 电 加热 器 电 缆 存 防火 包 裹 内过 热烧 毁 ,致 使加 热 器 电 缆 出 现 村 { I ' H J 短路
引起 上 游抽 屉 过 流跳 闸缺 陷 。
原 因及 应 对 措 施 。
关键 词 核 电厂 稳 压 器 电加 热 器 绝 缘 高 温
中图分 类 号
TM6 2 3 . 1
0 引言
稳 压 器 是将 核 电厂反 应 堆 一 回路 ( R C P系 统 ) 压 力 维 持
2 典 型 故 障 分 析及 应 对 措 施
2 . 1 稳压 器 波纹管 保温 盒与 电加 热器接 线柱 过近
依靠喷淋阀和稳压器加热器进行适时动态调节的。
如果反应堆功率超过汽轮机 负荷 ,那么水容积膨胀并
压 缩 蒸 汽 ,引起 的 波动 将 由冷 管段 引来 的喷 淋 水 通 过 喷 淋
使蒸汽凝结 ,达到降压 目的 容 积收 缩 且稳 压器 蒸 汽 空 间扩 大 , 引起 的
通 断 式 电加热 器 主 要用 在 反 应 堆 启 动 或 瞬 态 过 程 ; 比 例 可 调式 电加 热器 每 组 有 9根 电 加热 元 件 ,在 稳 压 器 内压
核反应堆-核电-核技术-核工程-3.5 稳压器 (1)

9
10
安全阀组
每个先导式安全阀组由串联的两台阀门组
成。每个阀设置了开启和关闭压力阈值。
一台提供卸压功能的上端阀门,称为保护
阀;另一台下端阀门,其隔离作用,称作隔 离阀。
在正常运行期间,保护阀关闭,隔离阀开
启。如果保护阀在开启之后再关闭失效时, 则隔离阀关闭,防止反应堆冷却剂系统进一 步卸压。
却卸压箱;
疏水管:接RPE系统,用来水位高时排水。
卸压箱的降温:一方面是依靠来自硼和补
给水系统的除盐水喷淋,另一方面依靠箱内 蛇形冷却管,它由设备冷却水系统不间断地 提供冷却水。
卸压箱内充有氮气,箱内压力(额定压力
0.12 MPa)稍高于大气压,可以阻止空气的进 入,氮气气压可以阻止一回路冷却剂所含有 的氢与空气中的氧形成易爆混合物。如果箱 内压力小于0.12 MPa,由氮气分配系统充氮; 如果箱内压力高于0.12 MPa,就释放蒸汽。
一个环路的热管段相连,波动管接在下 封头最低点,其正上方设有挡板式滤网, 使水流进、出稳压器,并防止杂物进入 反应堆冷却剂系统的其他地方。
5
稳压器喷淋系统
根据喷淋水的来源不同,可以分为主喷
淋系统和辅助喷淋系统。
1、主喷淋
主喷淋由连至两个环路的冷管段的管线组成 。喷淋管线上游接在RCP系统主泵的出口 管线上。喷淋的驱动力是反应堆冷却剂 泵出口与喷头出口间的压差。主管线上 安装了喷淋阀,最大流量72m3/h,喷淋压 降速率为1.3MPa/min
卸压能力:卸压箱按照能接收110%
的稳压器蒸汽空间的蒸汽设计。但 不能连续接受稳压器的蒸汽排放。 超量的蒸汽排放会导致泄压箱内压 力上升,压力达到一定值,顶部的 爆破膜破裂,蒸汽排放到安全壳内 。
核电厂稳压器电加热器在役更换自动焊接技术

核电厂稳压器电加热器在役更换自动焊接技术陈英杰;颜少华;王松;陈忠兵;刘超;成鹏;冯兴旺【摘要】In order to fill the domestic technology gaps and improve the capability of self-maintenance of main equipment in nuclear power plants,the automatic welding technology for replacing in-service heater elements of voltage stabilizer is researched.According to the characteristics of replacing in-service electric heater and the shortcomings of existing technology,the closed welding head is developed,which improves the stability of welding arc and gas shielded effect.Through a large number of automatic welding technology tests,the influence of protective atmosphere,specimen size and the chemical composition of base metal on the appearance of weld are discussed,and the welding parameters are determined.The results show that the use of argon backside protection and helium front protection welding can ensure complete penetration and protective effect on backing pass;the deviation of specimen structure size can affect the appearance of weld due to different heat dissipation;and the higher the content of S in the base metal chemical composition,the easier it is to penetrate.%为填补国内技术空白,提高核电厂主设备的自主维修能力,研究稳压器电加热器在役更换自动焊接成套技术.根据电加热器在役更换的特点及现有技术缺点,研发封闭式机头,提高焊接电弧的稳定性及气体保护效果.通过大量的自动焊接工艺试验,探讨保护气体、试件尺寸、母材化学成分等对焊缝成形的影响,确定焊接工艺参数.试验结果表明,采用氩气背面保护、氦气正面保护焊接既能保证焊透,又能保证背部保护效果;试件结构尺寸的偏差会因散热不同而影响焊缝成形;母材化学成分中w(S)越高则越容易焊透.【期刊名称】《电焊机》【年(卷),期】2018(048)001【总页数】7页(P63-69)【关键词】稳压器;电加热器;焊接电源;自动焊;焊接机头【作者】陈英杰;颜少华;王松;陈忠兵;刘超;成鹏;冯兴旺【作者单位】中广核核电运营有限公司,广东深圳518124;中广核核电运营有限公司,广东深圳518124;中广核核电运营有限公司,广东深圳518124;苏州热工研究院有限公司,江苏苏州215004;中广核核电运营有限公司,广东深圳518124;苏州热工研究院有限公司,江苏苏州215004;中广核核电运营有限公司,广东深圳518124【正文语种】中文【中图分类】TG4091 研究背景根据世界核电运营者协会(WANO)经验反馈,英国Sizewell B核电厂曾因稳压器电加热器包壳破损导致一回路冷却剂泄漏,反应堆强制停堆。
在役核电厂稳压器电加热器更换技术的工艺改进与应用

在役核电厂稳压器电加热器更换技术的工艺改进与应用作者:闫永巍郑孝纲来源:《中小企业管理与科技·上旬刊》2018年第07期【摘要】论文对近期稳压器电加热器典型故障案例进行了分析,对常用电加热器更换工艺进行了概述,并对电加热器更换工艺的改进及其应用进行了综述。
【Abstract】This article mainly analyzes the typical fault cases of electric heater of the voltage regulator, summarizes the replacement technology of the ordinary electric heater, and reviews the improvement of the replacement technology of electric heater and its application.【关键词】核电厂;稳压器电加热器;工艺改进;应用【Keywords】nuclear power plant; electric heater of the voltage regulator; process improvement; application【中图分类号】TM623 【文献标志码】A 【文章编号】1673-1069(2018)07-0175-021 引言稳压器是压水堆核电站的关键设备之一,主要起维持系统压力的作用。
目前,多数压水堆核电站稳定运行的系统压力在1 5.4MPa左右,一旦偏离设计压力就可能导致严重的事故。
目前,核电厂稳压器电加热器的寿命普遍要低于反应堆的设计寿命,这意味着在反应堆运行的寿期内,会出现稳压器电加热器故障的问题,必然会对故障电加热器进行更换检修[1]。
本文简要介绍近期电加热器故障的案例,列举出目前加热器更换的检修工艺及不足,提出了工艺改进措施,顺利完成在役核电厂电加热器的更换工作,希望有一定的借鉴意义。
cpr1000核电站稳压器电加热器绝缘电阻失效分析及优化研究
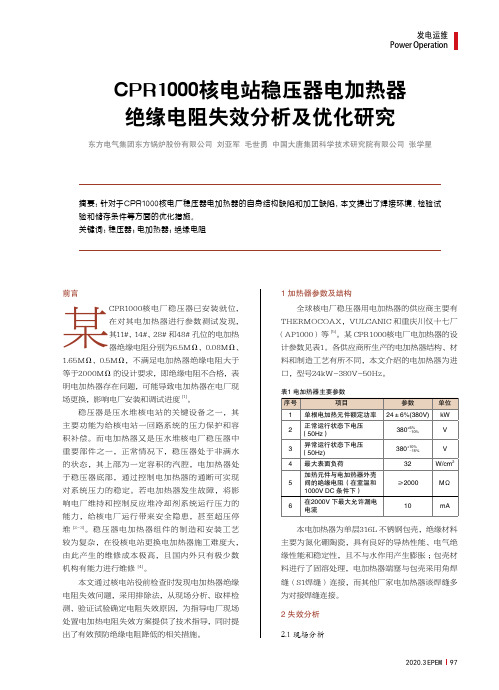
2020.3 EPEM97发电运维Power Operation前言某CPR1000核电厂稳压器已安装就位, 在对其电加热器进行参数测试发现, 其11#、14#、28#和48#孔位的电加热 器绝缘电阻分别为6.5MΩ、0.08MΩ、1.65MΩ、0.5MΩ,不满足电加热器绝缘电阻大于等于2000MΩ的设计要求,即绝缘电阻不合格,表明电加热器存在问题,可能导致电加热器在电厂现场更换,影响电厂安装和调试进度[1]。
稳压器是压水堆核电站的关键设备之一,其主要功能为给核电站一回路系统的压力保护和容积补偿。
而电加热器又是压水堆核电厂稳压器中重要部件之一,正常情况下,稳压器处于非满水的状态,其上部为一定容积的汽腔,电加热器处于稳压器底部,通过控制电加热器的通断可实现对系统压力的稳定。
若电加热器发生故障,将影响电厂维持和控制反应堆冷却剂系统运行压力的能力,给核电厂运行带来安全隐患,甚至超压停堆[2-3]。
稳压器电加热器组件的制造和安装工艺较为复杂,在役核电站更换电加热器施工难度大,由此产生的维修成本极高,且国内外只有极少数机构有能力进行维修[4]。
本文通过核电站役前检查时发现电加热器绝缘电阻失效问题,采用排除法,从现场分析、取样检测、验证试验确定电阻失效原因,为指导电厂现场处置电加热电阻失效方案提供了技术指导,同时提出了有效预防绝缘电阻降低的相关措施。
CPR1000核电站稳压器电加热器 绝缘电阻失效分析及优化研究东方电气集团东方锅炉股份有限公司 刘亚军 毛世勇 中国大唐集团科学技术研究院有限公司 张学星摘要:针对于CPR1000核电厂稳压器电加热器的自身结构缺陷和加工缺陷,本文提出了焊接环境、检验试验和储存条件等方面的优化措施。
关键词:稳压器;电加热器;绝缘电阻1 加热器参数及结构全球核电厂稳压器用电加热器的供应商主要有tHERMoCoAX,VULCANIC 和重庆川仪十七厂(AP1000)等[5]。
某CPR1000核电厂电加热器的设计参数见表1。
浅谈核岛稳压器

浅谈核岛稳压器文章对稳压器的主要功能、工作原理和结构特点做了简单的介绍,并着重分析了其制造过程中的关键点、难点。
标签:稳压器;结构;制造稳压器是核电站核岛一回路冷却剂系统核安全一级主设备,其制造质量对核反应堆的安全运行有着重大意义。
1 稳压器的主要功能和工作原理1.1 主要功能稳压器用于稳定和调节一回路主系统的工作压力,避免一回路主系统压力过高或过低,以防止一回路主系统及设备超压或压力过低出现沸腾现象,避免堆芯燃料元件棒过热烧毁事故。
1.2 工作原理稳压器与一回路通过波动接管连接,因此稳压器内的蒸汽压力与一回路水的压力是相等的。
因此,通过控制稳压器内的压力可以调节一回路中水的压力,其具体是通过喷雾器和电加热器实现的。
正常情况下,稳压器内的冷却剂处于汽液平衡状态,当需要降低系统压力时,冷却水从喷雾器喷出使其上部空间的蒸汽冷凝,使压力降低;当需要提高系统压力时,稳压器底部的电加热器启动,稳压器底部的部分水形成水蒸汽,从稳压器底部上升到上部的蒸汽空间,使压力升高[1]。
2 某项目稳压器的结构介绍某项目稳压器是一个立式圆柱结构的高温高压设备(见图1)。
该设备主体是由上、中、下三段筒体与上、下封头组焊而成。
设备主体材料为508-Ⅲ钢锻件,各接管安全端材料为F316不锈钢锻件,总容积35m3。
2.1 上封头组件上封头设有一个喷雾接管,三个安全阀接管和一个人孔。
喷雾接管下端装有喷雾器以伸入到稳压器的上部蒸汽空间内。
喷雾接管内部焊接有防热冲击套管,用于降低因冷水喷入温度变化所产生的热应力。
安全阀接管连接安全阀,用于提供超压保护。
上封头还装有三个压力水位计接管和一个温度计接管。
2.2 筒体组件及其附件筒体的下部设有上、下电加热元件支撑板,对电加热元件起支撑作用,并可以抑制其横向振动。
此外,该支撑板促进了波动水流与稳压器内水的混合,而不影响稳压器内水的自然循环。
上支撑板中间也开有提供人员检查通道的人孔。
上、下电加热元件支撑板分别与四个焊在壳体内表面的支撑座相连接,保证支撑板水平定位。
百万千瓦级核电厂稳压器自主化结构设计主要技术分析
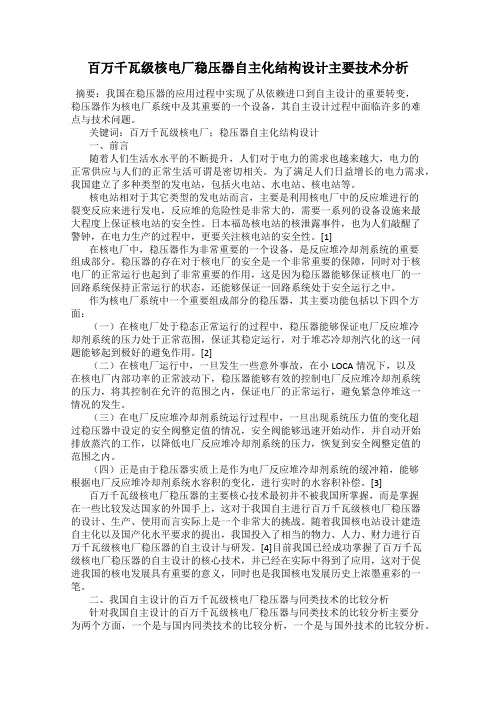
百万千瓦级核电厂稳压器自主化结构设计主要技术分析摘要:我国在稳压器的应用过程中实现了从依赖进口到自主设计的重要转变,稳压器作为核电厂系统中及其重要的一个设备,其自主设计过程中面临许多的难点与技术问题。
关键词:百万千瓦级核电厂;稳压器自主化结构设计一、前言随着人们生活水水平的不断提升,人们对于电力的需求也越来越大,电力的正常供应与人们的正常生活可谓是密切相关。
为了满足人们日益增长的电力需求,我国建立了多种类型的发电站,包括火电站、水电站、核电站等。
核电站相对于其它类型的发电站而言,主要是利用核电厂中的反应堆进行的裂变反应来进行发电,反应堆的危险性是非常大的,需要一系列的设备设施来最大程度上保证核电站的安全性。
日本福岛核电站的核泄露事件,也为人们敲醒了警钟,在电力生产的过程中,更要关注核电站的安全性。
[1]在核电厂中,稳压器作为非常重要的一个设备,是反应堆冷却剂系统的重要组成部分。
稳压器的存在对于核电厂的安全是一个非常重要的保障,同时对于核电厂的正常运行也起到了非常重要的作用,这是因为稳压器能够保证核电厂的一回路系统保持正常运行的状态,还能够保证一回路系统处于安全运行之中。
作为核电厂系统中一个重要组成部分的稳压器,其主要功能包括以下四个方面:(一)在核电厂处于稳态正常运行的过程中,稳压器能够保证电厂反应堆冷却剂系统的压力处于正常范围,保证其稳定运行,对于堆芯冷却剂汽化的这一问题能够起到极好的避免作用。
[2](二)在核电厂运行中,一旦发生一些意外事故,在小LOCA情况下,以及在核电厂内部功率的正常波动下,稳压器能够有效的控制电厂反应堆冷却剂系统的压力,将其控制在允许的范围之内,保证电厂的正常运行,避免紧急停堆这一情况的发生。
(三)在电厂反应堆冷却剂系统运行过程中,一旦出现系统压力值的变化超过稳压器中设定的安全阀整定值的情况,安全阀能够迅速开始动作,并自动开始排放蒸汽的工作,以降低电厂反应堆冷却剂系统的压力,恢复到安全阀整定值的范围之内。
稳压器电加热器更换技术研究

Instrumentation and Equipments 仪器与设备, 2017, 5(4), 83-86Published Online December 2017 in Hans. /journal/iaehttps:///10.12677/iae.2017.54012Study on the Technology of PressurizerImmersion Heaters ReplacementZhenfeng Wang, Xiong Cao, Yu Li, Zhiwei Ding, Xiang ZhouShanghai Nuclear Engineering Research & Design Institute Co. LTD, ShanghaiReceived: Dec. 10th, 2017; accepted: Dec. 20th, 2017; published: Dec. 27th, 2017AbstractPressurizer immersion heaters are the important functional part in pressurizer. The normal op-eration of heaters plays a key role in the pressure fluctuation of control and regulation of the reactor coolant system. Therefore, replacing failure heaters and the end service of heaters timely is very necessary. This paper analyzed the failure reasons of heaters and researched the replace-ment technology of heaters.KeywordsPressurizer, Electric Heater, Technology of Heaters Replacement稳压器电加热器更换技术研究王振锋,曹雄,李煜,丁志伟,周响上海核工程研究设计院有限公司,上海收稿日期:2017年12月10日;录用日期:2017年12月20日;发布日期:2017年12月27日摘要电加热器是稳压器中的重要功能性部件之一,电加热器的正常运行对控制及调节反应堆冷却剂系统的压力波动起着关键作用。
核电厂稳压器加热器开关频繁跳闸的原因分析及防控措施

1引言核电厂稳压器是对一回路压力进行控制和超压保护的重要设备,通过4组通断式加热器和2组比例式加热器来调节稳压器中水的温度,从而参与对一回路压力的控制。
然而阳江、红沿河等核电厂的加热器开关均多次发生了误动跳闸的问题,其中阳江核电厂在2018年就发生了3起,严重影响了稳压器加热器的可用性。
本文针对阳江核电厂其中一起加热器开关跳闸的原因进行了深入剖析,找到了该共模缺陷的根治措施。
2事件描述2018年6月10日,Y4RCP021RS稳压器加热器上游开关Y4RCP002RS-01D1跳闸,检查为断路器过载保护动作。
6月11日上午,电气人员出票对开关跳闸原因进行检查,下游加热器负荷的直阻及绝缘检查无异常;将开关推入合闸,用钳形电流表测量开关三相电流均在111.6A左右,与额定电流相仿,无异常;用热成像仪对抽屉开关内部元器件进行测温,发现断路器本体表面温度持续上涨,在运行4小时后达到77.1℃,且有继续上涨的趋势,存在温度过高的明显异常。
3断路器频繁跳闸的原因分析3.1对断路器定值的合理性分析Y4RCP002RS-01D1断路器型号为T3N250TMD125,过载保护定值设置为125A,本次开关运行电流108.5A左右,过载保护定值配置符合要求。
而且一般加热器负荷为恒流负载,无过载的工况。
因此排除定值整定不合理导致开关误动的可能。
3.2温度对断路器过载特性的影响分析①热脱扣器的原理断路器的过载保护通过热脱扣器实现,其利用的是双金属片原理,双金属片通常由两层热膨胀系数不同的合金叠合而成。
其中,膨胀系数较大的称为主动层,膨胀系数较小的称为被动层。
由于金属膨胀系数的差异,在温度发生变化时,主动层的形变要大于被动层的形变,从而双金属片的整体就会向被动层一侧弯曲,产生形变。
当形变角度达到一定程度的时候,双金属片推动限位螺栓运动,进而推动传动连杆运动,导致断路器脱扣跳闸,断开主回路,实现过载保护。
双金属片上缠绕着电热丝,电热丝的电流是从主回路分流过来的,主回路电流越大,电热丝的发热量也就越大,双金属片的变形度也就越快。
核电厂稳压器电加热器在役更换自动焊接技术

第 48卷 第 1期 2018年 1月
雹晖梭
Electric W elding Machine
Vo1.48 No.1 Jan.2018
本 文 参 考 文 献 引 用 格 式 : 焚杰 .颜 少 毕 . 松 , 骸 电 厂 器 IU/Jt J ̄:!v, 他 蜓换 I:t-,0j't 刊妾般 … fU 机 .201 8.48(OI):63—69
1 研 究背景
根据 世 界 核 电运 营 者 协 会(WANO)经 验 反 髋 ,
核 iI电厂稳压器 电加热器在i役更换 自动焊 接 技术
陈 英 杰 , 颜 少 华 ,王 松 ,陈 忠兵 2,刘 超 ,成 鹏 ,冯 兴 旺 l
(1.中广核核 电运 营有 限公 司,广 东 深圳 5 l 8l 24;2.苏州热工研 究院有限公 司,江 要 :为填补 国内技术空 白,提 高核电厂主设备的 自主维修能力,研究稳压器电加热 器在役更换 自动 焊接 成套技 术。根 据 电加热 器在 役更 换 的特 点及现 有技 术缺 点 ,研发封 闭式机头 ,提 高焊接 电弧 的稳 定
关 键 词 :稳压器;电加热器;焊接 电源 ;自动焊;焊接机 头 中图分 类号 :TG409 文献标志码 :A 文章编号 :1001—2303(2018)01—0063—07 DOI:10.75t2 ̄.issn.1001-2303.2018.01.15
核电厂稳压器电加热器典型故障分析及改进措施
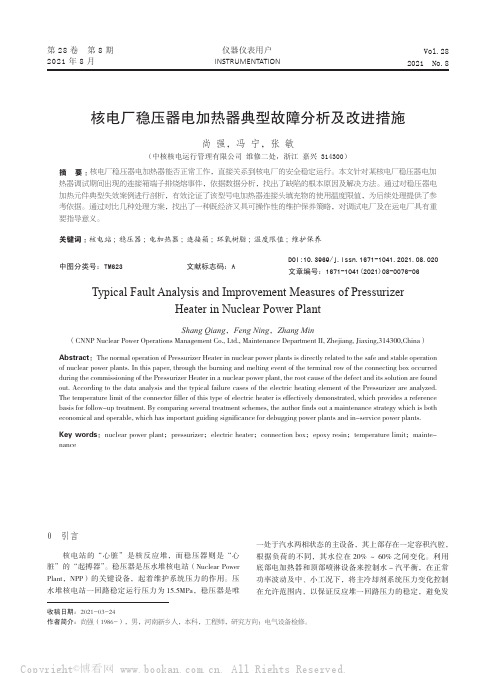
第28卷 第8期2021年8月仪器仪表用户INSTRUMENTATIONVol.282021 No.8核电厂稳压器电加热器典型故障分析及改进措施尚 强,冯 宁,张 敏(中核核电运行管理有限公司 维修二处,浙江 嘉兴 314300)摘 要:核电厂稳压器电加热器能否正常工作,直接关系到核电厂的安全稳定运行。
本文针对某核电厂稳压器电加热器调试期间出现的连接箱端子排烧熔事件,依据数据分析,找出了缺陷的根本原因及解决方法。
通过对稳压器电加热元件典型失效案例进行剖析,有效论证了该型号电加热器连接头填充物的使用温度限值,为后续处理提供了参考依据。
通过对比几种处理方案,找出了一种既经济又具可操作性的维护保养策略,对调试电厂及在运电厂具有重要指导意义。
关键词:核电站;稳压器;电加热器;连接箱;环氧树脂;温度限值;维护保养中图分类号:TM623 文献标志码:ATypical Fault Analysis and Improvement Measures of PressurizerHeater in Nuclear Power PlantShang Qiang ,Feng Ning ,Zhang Min(CNNP Nuclear Power Operations Management Co., Ltd., Maintenance Department II, Zhejiang, Jiaxing,314300,China)Abstract:The normal operation of Pressurizer Heater in nuclear power plants is directly related to the safe and stable operation of nuclear power plants. In this paper, through the burning and melting event of the terminal row of the connecting box occurred during the commissioning of the Pressurizer Heater in a nuclear power plant, the root cause of the defect and its solution are found out. According to the data analysis and the typical failure cases of the electric heating element of the Pressurizer are analyzed. The temperature limit of the connector filler of this type of electric heater is effectively demonstrated, which provides a reference basis for follow-up treatment. By comparing several treatment schemes, the author finds out a maintenance strategy which is both economical and operable, which has important guiding significance for debugging power plants and in-service power plants.Key words:nuclear power plant;pressurizer;electric heater;connection box;epoxy resin;temperature limit;mainte-nanceDOI:10.3969/j.issn.1671-1041.2021.08.020文章编号:1671-1041(2021)08-0076-06收稿日期:2021-03-24作者简介:尚强(1986-),男,河南新乡人,本科,工程师,研究方向:电气设备检修。
核电厂稳压器电加热器技术综述
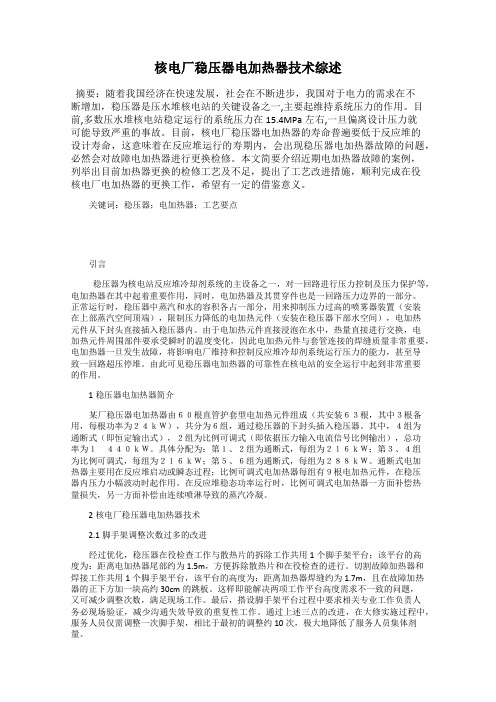
核电厂稳压器电加热器技术综述摘要:随着我国经济在快速发展,社会在不断进步,我国对于电力的需求在不断增加,稳压器是压水堆核电站的关键设备之一,主要起维持系统压力的作用。
目前,多数压水堆核电站稳定运行的系统压力在15.4MPa左右,一旦偏离设计压力就可能导致严重的事故。
目前,核电厂稳压器电加热器的寿命普遍要低于反应堆的设计寿命,这意味着在反应堆运行的寿期内,会出现稳压器电加热器故障的问题,必然会对故障电加热器进行更换检修。
本文简要介绍近期电加热器故障的案例,列举出目前加热器更换的检修工艺及不足,提出了工艺改进措施,顺利完成在役核电厂电加热器的更换工作,希望有一定的借鉴意义。
关键词:稳压器;电加热器;工艺要点引言稳压器为核电站反应堆冷却剂系统的主设备之一,对一回路进行压力控制及压力保护等,电加热器在其中起着重要作用,同时,电加热器及其贯穿件也是一回路压力边界的一部分。
正常运行时,稳压器中蒸汽和水的容积各占一部分,用来抑制压力过高的喷雾器装置(安装在上部蒸汽空间顶端),限制压力降低的电加热元件(安装在稳压器下部水空间),电加热元件从下封头直接插入稳压器内。
由于电加热元件直接浸泡在水中,热量直接进行交换,电加热元件周围部件要承受瞬时的温度变化,因此电加热元件与套管连接的焊缝质量非常重要,电加热器一旦发生故障,将影响电厂维持和控制反应堆冷却剂系统运行压力的能力,甚至导致一回路超压停堆。
由此可见稳压器电加热器的可靠性在核电站的安全运行中起到非常重要的作用。
1稳压器电加热器简介某厂稳压器电加热器由60根直管护套型电加热元件组成(共安装63根,其中3根备用,每根功率为24kW),共分为6组,通过稳压器的下封头插入稳压器。
其中,4组为通断式(即恒定输出式),2组为比例可调式(即依据压力输入电流信号比例输出),总功率为1440kW。
具体分配为:第1、2组为通断式,每组为216kW;第3、4组为比例可调式,每组为216kW;第5、6组为通断式,每组为288kW。
核岛主设备稳压器加热器全自动焊接工艺

0 前 言
在核 电站核 岛主设 备 中 , 压器 作 为核 I 设 稳 级 备 , 主要 作用 是稳 定 和调 节一 回路 主 系统 冷却 剂 其
1 焊 接 结 构 工 艺 性 分 析
加 热 器 与 加 热 器 套 管 材 料 均 为 Z C D1. N , 2 N 81 S 2
该 材料 为法 国牌 号 , 于含 Mo元 素控 氮 型奥 氏体 属 不 锈钢 , 似 于 3 6 , 货 状 态 为 固溶 处 理 , 处 类 1L 供 热 理 温度 1 5 0℃~ 5 。 0 110o 控氮 型奥 氏体 不锈钢与 一 C
Ke o d : u l r o e ; i al u e a tm t e i ;a k p n t t ; o y es i dg s y w r s n c a w rt nw l tb ;uo ai w l n b c e e a t p he a e p h c d g re w t l
间腐蚀 和 晶间应 力 腐蚀 性 能优 良的特点 , 泛运 用 广
于 核 电 站 核 岛 主 设 备 , 学 成 分 如 表 2所 示 。 化
表 1 Z CND 1 .2 2 81 NS 力 学 性 能
加 热器 套管焊 接 又是其 焊接 制造 的难 点之 一 。 在该 项 目的一 期合 同 中 , 接程 序 和操 作都 是 由外 方负 焊 责 , 没 有 实现 真 正 的 国产 化 , 了打 破 国 外公 司 并 为 的垄 断 , 成稳 压 器 国产化 制 造 的 目标 , 方 锅炉 完 东 股 份公 司技术 人员 经 过反 复调 试 和摸 索 , 功 地调 成 试 出 了一套合 适 的焊接 程 序 和操作 技 术 , 并成 功运
p n t t .rc d r t t n e t eut h w t t on t e w l n t i , e ige up n , r e t e g sw li rga e e a po e u e e d t s l s o h i y , ed g ma r lw l n q ime tpo c v a , e n p orm, re sa sr aj t p i ea d t i d g
核电站稳压器电加热器失效分析及优化措施
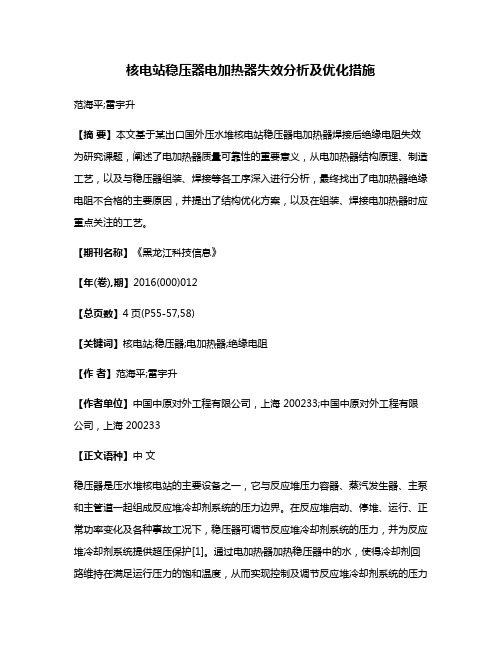
核电站稳压器电加热器失效分析及优化措施范海平;雷宇升【摘要】本文基于某出口国外压水堆核电站稳压器电加热器焊接后绝缘电阻失效为研究课题,阐述了电加热器质量可靠性的重要意义,从电加热器结构原理、制造工艺,以及与稳压器组装、焊接等各工序深入进行分析,最终找出了电加热器绝缘电阻不合格的主要原因,并提出了结构优化方案,以及在组装、焊接电加热器时应重点关注的工艺。
【期刊名称】《黑龙江科技信息》【年(卷),期】2016(000)012【总页数】4页(P55-57,58)【关键词】核电站;稳压器;电加热器;绝缘电阻【作者】范海平;雷宇升【作者单位】中国中原对外工程有限公司,上海 200233;中国中原对外工程有限公司,上海 200233【正文语种】中文稳压器是压水堆核电站的主要设备之一,它与反应堆压力容器、蒸汽发生器、主泵和主管道一起组成反应堆冷却剂系统的压力边界。
在反应堆启动、停堆、运行、正常功率变化及各种事故工况下,稳压器可调节反应堆冷却剂系统的压力,并为反应堆冷却剂系统提供超压保护[1]。
通过电加热器加热稳压器中的水,使得冷却剂回路维持在满足运行压力的饱和温度,从而实现控制及调节反应堆冷却剂系统的压力波动。
可见电加热器是稳压器设备的核心元件,对压水堆核电厂的安全运行起着非常重要的作用。
近几年,国内核电站陆续发生稳压器电加热器失效的案例,包括绝缘电阻不合格、连接电缆脱落、爆管、连接接头烧损等,给核电站运行带了较大的安全隐患。
另外,稳压器电加热器组件的制造和安装工艺较为复杂,在役核电站更换电加热器施工难度大,由此产生的维修成本极高,且国内外只有极少数机构有能力进行维修[2]。
本文通过真实案例,对电加热器绝缘电阻失效进行了原因分析,通过各项试验验证了可能造成绝缘电阻失效,并提出了改进措施,顺利完成电加热器在制造厂的更换工作,希望有一定的借鉴之处。
本案例稳压器电加热器的主要参数见表1[3],主要结构如图1所示。
电加热器制造完毕后进行了出厂试验,各项性能满足要求,运输到制造厂后进行了入厂复验,绝缘电阻满足要求。
核电厂稳压器电加热器典型故障与改进措施

核电厂稳压器电加热器典型故障与改进措施摘要:保持核电厂稳压器电加热器的正常工作,与核电厂的安全、稳定运行息息相关。
本文主要围绕核电厂稳压器电加热器典型故障及改进措施展开论述,首先概述了稳压器电加热器的具体内涵;其次分析了稳压器电加热器的典型故障,并提出了相应的整改措施;最后列举了一项典型故障案例。
关键词:核电厂,稳压器,电加热器对于一个核电厂来说,核反应堆是它的“心脏”,而“心脏”的“起搏器”就是稳压器。
稳压器作为压水堆核电站中的关键性设备,发挥着维护系统压力的重要作用,而且稳压器是处在汽水两相状态下的一项主设备,在上部存有一定的容积汽枪,依据存在的负荷差异,相应的水位会在20%-60%之间进行变动。
主要通过底部电加热器以及顶部的喷淋设备来维持水汽平衡,如果功率波动相对比较正常,将主冷却剂系统控制在规范的压力变化范围内,从而更好保障反应堆一回路的压力稳定,防止出现紧急停堆。
如果多根稳压器电加热器同时出现故障,就容易致使反应堆冷却系统的运行压力产生较大波动,进而导致非计划停堆,严重影响着机组的经济性与安全性。
1、稳压器电加热器的相关概述就国内M310型号的水堆机组稳压器而言,其底部的电加热元件有63根,总共分为6组,每一根电加热元件的功率是24KW,其中3根作为备用,在稳压器下封头处将稳压器插入其中,从而与稳压器内部的水源实施直接的热量传导。
在这6组中,4组属于固定式类型,也就是恒功率输出,剩余2组属于比例式类型,也就是根据压力输入电力信号,再按照一定比例进行输出,整体的功率是1440KW,实际的功率分配为:A、B组是固定式,总功率是432KW;C、D组是比例式,总功率同样是432KW;E、F组是固定式,总功率是572KW。
固定式电加热器具体应用于启动或瞬态过程,比例式电加热器实际用在对小范围的稳压器出现的偏差进行补偿。
在反应堆稳态功率的运行过程中,通过比例式电加热器能够在补偿热量损失的同时,对连续喷淋造成的蒸汽冷凝加以补偿。
AP1000 稳压器电加热器控制及其特点

AP1000 稳压器电加热器控制及其特点作者:刘启东来源:《科学与技术》 2019年第3期摘要:AP1000稳压器作为一回路稳压的重要设备,当一回路压力下降时可以提供压力补偿,当一回路压力升高时,可以提供喷淋降低压力。
其中稳压器里的电加热器作为一回路压力补偿的重要手段,其对于系统的安全稳定运行起着至关重要的作用。
关键词:结构;电源;逻辑;控制1概述稳压器电加热器(以下简称电加热器)在反应堆启动和停堆时,投入电加热器来满足反应堆冷却剂的升温和降温速率的要求,主要功能是:在核电厂额定工况和变负荷运行中,加热稳压器中的水,使其维持在满足运行压力的饱和温度,从而控制及调节反应堆冷却剂中的压力波动。
1.1稳压器电加热器的结构电加热器主要由电缆、绝缘隔板、套筒、包壳等构成。
其中电加热器的包壳为A类设备,安全分类为SC-1级,抗震类别1级。
电加热器的设计要求可以满足寿期60年的使用要求。
1.2稳压器电加热器电源稳压器电加热器安装在稳压器底封头的套管内,包括一组比例电加热器(功率370kW),4组备用电加热器(其中A/B组功率为246kW,C/D组功率为370kW),稳压器电加热器共包含78个电加热棒,每个MCC抽屉柜下对应3个电加热棒,所以共对应26个MCC抽屉柜,其中比例电加热器对应6个MCC抽屉柜,备用电加热器A/B组均对应4个MCC抽屉柜,备用电机热器C/D组均对应6个MCC抽屉柜。
每个电加热棒功率为61.67kW,电加热器总功率为1600kW,由核岛1/2号中压母线下的MCC供电。
失去全部厂外交流电源时,操纵员手动带载A、B两组备用电加热器至备用柴油发电机,如有必要可以手动带载C、D两组。
正常运行时,比例电加热器投入运行以补偿喷淋水的持续引入和向周围环境的热量损失,备用电加热器依据一回路压力自动投入运行。
运行原理是依据PHC机柜(稳压器电加热器控制机柜)内SCR(可控硅结构)的调压,从而实现比例电加热器功率的调节。
百万千瓦级核电厂稳压器自主化结构设计主要技术分析
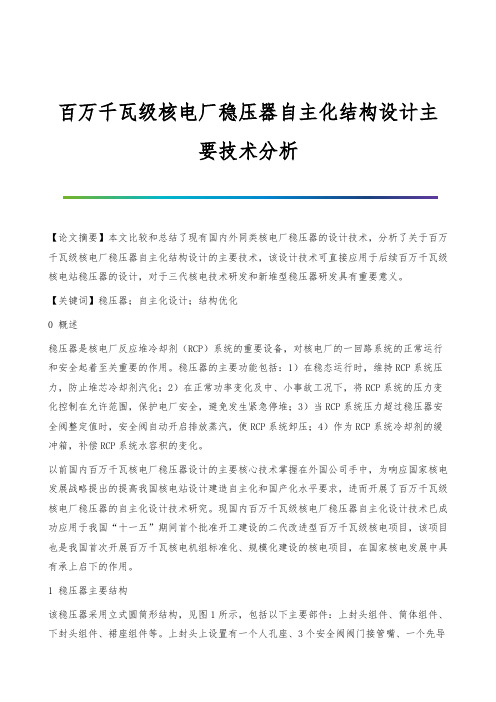
百万千瓦级核电厂稳压器自主化结构设计主要技术分析【论文摘要】本文比较和总结了现有国内外同类核电厂稳压器的设计技术,分析了关于百万千瓦级核电厂稳压器自主化结构设计的主要技术,该设计技术可直接应用于后续百万千瓦级核电站稳压器的设计,对于三代核电技术研发和新堆型稳压器研发具有重要意义。
【关键词】稳压器;自主化设计;结构优化0 概述稳压器是核电厂反应堆冷却剂(RCP)系统的重要设备,对核电厂的一回路系统的正常运行和安全起着至关重要的作用。
稳压器的主要功能包括:1)在稳态运行时,维持RCP系统压力,防止堆芯冷却剂汽化;2)在正常功率变化及中、小事故工况下,将RCP系统的压力变化控制在允许范围,保护电厂安全,避免发生紧急停堆;3)当RCP系统压力超过稳压器安全阀整定值时,安全阀自动开启排放蒸汽,使RCP系统卸压;4)作为RCP系统冷却剂的缓冲箱,补偿RCP系统水容积的变化。
以前国内百万千瓦核电厂稳压器设计的主要核心技术掌握在外国公司手中,为响应国家核电发展战略提出的提高我国核电站设计建造自主化和国产化水平要求,进而开展了百万千瓦级核电厂稳压器的自主化设计技术研究。
现国内百万千瓦级核电厂稳压器自主化设计技术已成功应用于我国“十一五”期间首个批准开工建设的二代改进型百万千瓦级核电项目,该项目也是我国首次开展百万千瓦核电机组标准化、规模化建设的核电项目,在国家核电发展中具有承上启下的作用。
1 稳压器主要结构该稳压器采用立式圆筒形结构,见图1所示,包括以下主要部件:上封头组件、筒体组件、下封头组件、裙座组件等。
上封头上设置有一个人孔座、3个安全阀阀门接管嘴、一个先导式安全阀压力信号箱接管嘴和一个喷雾接管嘴。
筒体组件包括三节筒体(上部筒体、中部筒体和下部筒体)和电加热元件上支撑板及仪表接管等。
下封头中心设置有一个波动接管嘴,接管内装有防热冲击套管,在下封头底部,以同心圆的排列方式、立式安装有三圈直接浸没式的电加热元件,并设置了电加热元件下支撑板。
- 1、下载文档前请自行甄别文档内容的完整性,平台不提供额外的编辑、内容补充、找答案等附加服务。
- 2、"仅部分预览"的文档,不可在线预览部分如存在完整性等问题,可反馈申请退款(可完整预览的文档不适用该条件!)。
- 3、如文档侵犯您的权益,请联系客服反馈,我们会尽快为您处理(人工客服工作时间:9:00-18:30)。
核电厂稳压器电加热器技术综述
摘要:随着我国经济在快速发展,社会在不断进步,我国对于电力的需求在不
断增加,稳压器是压水堆核电站的关键设备之一,主要起维持系统压力的作用。
目前,多数压水堆核电站稳定运行的系统压力在15.4MPa左右,一旦偏离设计压力就
可能导致严重的事故。
目前,核电厂稳压器电加热器的寿命普遍要低于反应堆的
设计寿命,这意味着在反应堆运行的寿期内,会出现稳压器电加热器故障的问题,必然会对故障电加热器进行更换检修。
本文简要介绍近期电加热器故障的案例,
列举出目前加热器更换的检修工艺及不足,提出了工艺改进措施,顺利完成在役
核电厂电加热器的更换工作,希望有一定的借鉴意义。
关键词:稳压器;电加热器;工艺要点
引言
稳压器为核电站反应堆冷却剂系统的主设备之一,对一回路进行压力控制及压力保护等,电加热器在其中起着重要作用,同时,电加热器及其贯穿件也是一回路压力边界的一部分。
正常运行时,稳压器中蒸汽和水的容积各占一部分,用来抑制压力过高的喷雾器装置(安装
在上部蒸汽空间顶端),限制压力降低的电加热元件(安装在稳压器下部水空间),电加热
元件从下封头直接插入稳压器内。
由于电加热元件直接浸泡在水中,热量直接进行交换,电
加热元件周围部件要承受瞬时的温度变化,因此电加热元件与套管连接的焊缝质量非常重要,电加热器一旦发生故障,将影响电厂维持和控制反应堆冷却剂系统运行压力的能力,甚至导
致一回路超压停堆。
由此可见稳压器电加热器的可靠性在核电站的安全运行中起到非常重要
的作用。
1稳压器电加热器简介
某厂稳压器电加热器由60根直管护套型电加热元件组成(共安装63根,其中3根备用,每根功率为24kW),共分为6组,通过稳压器的下封头插入稳压器。
其中,4组为
通断式(即恒定输出式),2组为比例可调式(即依据压力输入电流信号比例输出),总功
率为1440kW。
具体分配为:第1、2组为通断式,每组为216kW;第3、4组
为比例可调式,每组为216kW;第5、6组为通断式,每组为288kW。
通断式电加
热器主要用在反应堆启动或瞬态过程;比例可调式电加热器每组有9根电加热元件,在稳压
器内压力小幅波动时起作用。
在反应堆稳态功率运行时,比例可调式电加热器一方面补偿热
量损失,另一方面补偿由连续喷淋导致的蒸汽冷凝。
2核电厂稳压器电加热器技术
2.1脚手架调整次数过多的改进
经过优化,稳压器在役检查工作与散热片的拆除工作共用1个脚手架平台;该平台的高
度为:距离电加热器尾部约为1.5m,方便拆除散热片和在役检查的进行。
切割故障加热器和
焊接工作共用1个脚手架平台,该平台的高度为:距离加热器焊缝约为1.7m,且在故障加热
器的正下方加一块高约30cm的跳板。
这样即能解决两项工作平台高度需求不一致的问题,
又可减少调整次数,满足现场工作。
最后,搭设脚手架平台过程中要求相关专业工作负责人
务必现场验证,减少沟通失效导致的重复性工作。
通过上述三点的改进,在大修实施过程中,服务人员仅需调整一次脚手架,相比于最初的调整约10次,极大地降低了服务人员集体剂量。
2.2电加热套管与连接件的成分及性能分析
稳压器电加热器元件套管及连接件的材料大多采用Z2CND18-12(N)(法国牌号)不锈钢,其中w(Cr)约为18%,w(Ni)约为12%,w(Mo)含量约为2.5%,近似316L不锈钢。
控氮不锈钢一般在钢中加入w(N)0.05%~0.08%,N为强的奥氏体化元素,不锈钢中加入N
可以降低较为昂贵的Ni含量,且可以形成固溶强化作用,在提高不锈钢强度的同时,并不会降低其塑性及韧性,加入N还可提高材料的耐晶间腐蚀性能、耐点蚀及缝隙腐蚀性能。
因此,更换的加热器套管材质仍选用Z2CND18-12(控氮)不锈钢材料。
2.3THERMOCOAX电加热器
THERMOCOAX从1976年开始供应稳压器电加热器,目前全球有5500多根电加热器在运
行川,国内大多数二代加核电厂稳压器,如表1所示。
THERMOCOAX电加热器外部为316L
不锈钢包壳,其外径约22mm,壁厚约2mm。
该电加热器有两道屏障,不锈钢小管中心处装
有镍铬合金电加热丝,之间填充Mg0绝缘材料,此为第一道屏障,然后将小管以双排形式缠
绕在铜棒上,装人电加热器包壳内,此为第二道屏障,经缩管压实,再加人连接头和相关密
封元件完成制造,如图2所示。
THERMOCOAX电加热器主要特征如下:1)绝缘材料Mg0与一
回路水之间设置了双层包壳,减小了Mg0及加热丝与一回路水接触的概率;2)中间设置铜棒,改善了轴向和周向的传热效率,提高了表面功率密度;3)响应时间短,电加热器能在较短时间
内达到额定功率;4)在包壳尺寸相同的情况下,Mg0的用量少,降低了包壳可能因膨胀损害的
程度。
针对缩管操作后电加热器包壳存在残余应力的问题,EDF公司联合THERMOCOAX进行
了研究,制定了采用感应加热热处理工艺进行电加热器包壳退火的处理工艺,处理温度为
900-}-1000℃,经热处理后,包壳的表面硬度从320HVl降到了200HVl,有效地消除了包壳的
残余应力,表面晶粒度约达到了ASTM7-}-8级,经晶间腐蚀试验,无裂纹或其他显示出现。
该热处理工艺于2010年12月通过评定,目前THERMOCOAX公司已应用到电加热器的制造
过程中,EDF公司对其备用的电加热器也采用该方法进行了热处理。
2.4焊接材料及工艺要点
预置熔化环的自熔化焊接所用熔化环通常选用w(Cr)26%左右的铁素体不锈钢。
不锈
钢焊缝的耐晶间腐蚀性能,主要与焊缝化学成分有关,影响最大的是C含量,C含量越低,
其耐蚀性越好;其次,稳定化元素Ti,Nb的加入,也对防止晶间腐蚀有利;最后就是焊缝的组织,焊缝中含有适量的铁素体可以增加其耐晶间腐蚀性能。
但铁素体相的存在也有不利的
影响,铸态焊缝存在过多铁素体相时会有利于σ相的析出,铁素体相越多,越容易析出σ相。
σ相的硬度非常高,不但会降低焊缝塑性和韧性,还会增大晶间腐蚀倾向。
如果单独对电加
热元件套管和连接件进行自熔化焊接,试验结果证明,其焊缝组织几乎为单一的奥氏体组织,基于以上原因,为了避免焊缝产生微裂纹,提高耐蚀性能,并保证焊缝含有一定比例的铁素体,最好是形成铁素体体积分数为5%~12%的双相奥氏体焊缝组织。
选择铁素体不锈钢熔化环,并通过计算得出熔化环的厚度等尺寸,可以解决前述两种接头形式的不足,从而满足稳
压器电加热器的设计要求。
采用预置熔化环的自熔化时,由于氦气具有电离能高、电弧能量
密度大、对母材热输入大、工件熔深大、易于焊透的优点,所以通常采用氦气作为保护气体。
为了保证焊缝全焊透和背面成形良好,焊接时需要熔池深度比较大的规范。
电流主要影响熔
池深度,电弧长度决定电弧电压,选用氦气作为保护气体,电弧电位梯度较大,弧长变化对
电弧电压影响较大,可通过工艺试验获得优化的焊接工艺参数。
结语
目前核电厂稳压器电加热器主体已经实现了国产化,但仍然应该借鉴国内外先进技术和
运行经验进行持续改进,以进一步降低电加热器的失效风险和危害程度,同时应加强配套电
缆的研制。
建议参照EDF的做法对国内核电厂备用的THERMOCOAX电加热器进行热处理,
以消除包壳的残余应力。
应加快电加热器更换技术的研究和更换专用设备的研发,以具备或
进一步提升电加热器的更换和维护能力。
参考文献
[1]RSEM压水堆核电厂核岛机械设备在役检查规则[M].
[2]RCC-M压水堆核岛机械设备设计和建造规则[M].
[3]刘全印.核电站稳压器电热元件与套管焊接技术[J].压力容器,2009,26(1):53-56.。