钢铁生产流程详解图
炼钢生产过程以及流程图详解(全)
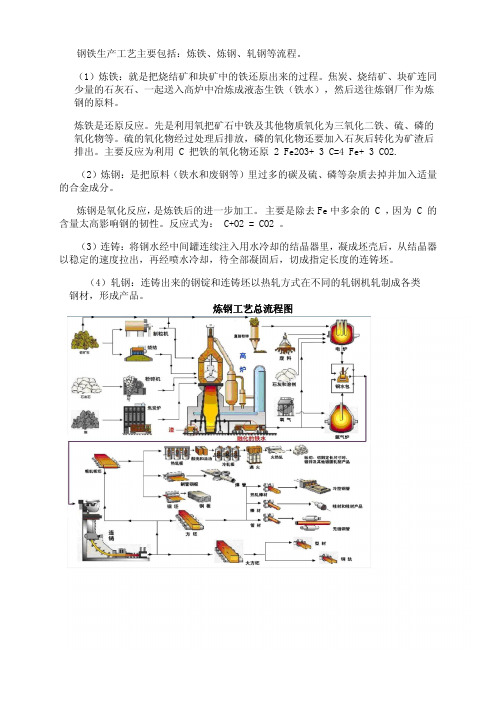
钢铁生产工艺主要包括:炼铁、炼钢、轧钢等流程。
(1)炼铁:就是把烧结矿和块矿中的铁还原出来的过程。
焦炭、烧结矿、块矿连同少量的石灰石、一起送入高炉中冶炼成液态生铁(铁水),然后送往炼钢厂作为炼钢的原料。
炼铁是还原反应。
先是利用氧把矿石中铁及其他物质氧化为三氧化二铁、硫、磷的氧化物等。
硫的氧化物经过处理后排放,磷的氧化物还要加入石灰后转化为矿渣后排出。
主要反应为利用 C 把铁的氧化物还原 2 Fe2O3+ 3 C=4 Fe+ 3 CO2.(2)炼钢:是把原料(铁水和废钢等)里过多的碳及硫、磷等杂质去掉并加入适量的合金成分。
炼钢是氧化反应,是炼铁后的进一步加工。
主要是除去Fe中多余的 C ,因为 C 的含量太高影响钢的韧性。
反应式为: C+O2 = CO2 。
(3)连铸:将钢水经中间罐连续注入用水冷却的结晶器里,凝成坯壳后,从结晶器以稳定的速度拉出,再经喷水冷却,待全部凝固后,切成指定长度的连铸坯。
(4)轧钢:连铸出来的钢锭和连铸坯以热轧方式在不同的轧钢机轧制成各类 钢材,形成产品。
炼钢工艺总流程图炼焦生产流程:炼焦作业是将焦煤经混合,破碎后加入炼焦炉内经干馏后产生热焦碳及粗焦炉气之制程。
烧结生产流程:烧结作业系将粉铁矿,各类助熔剂及细焦炭经由混拌、造粒后,经由布料系统加入烧结机,由点火炉点燃细焦炭,经由抽气风车抽风完成烧结反应,高热之烧结矿经破碎冷却、筛选后,送往高炉作为冶炼铁水之主要原料。
还原气体,还原铁矿石,产生熔融铁水与熔渣之炼铁制程。
转炉生产流程:炼钢厂先将熔铣送前处理站作脱硫脱磷处理,经转炉吹炼后,再依订单钢种特性及品质需求,送二次精炼处理站(RH真空脱气处理站、Ladle Injection盛桶吹射处理站、VOD真空吹氧脱碳处理站、STN搅拌站等)进行各种处理,调整钢液成份,最后送大钢胚及扁钢胚连续铸造机,浇铸成红热钢胚半成品,经检验、研磨或烧除表面缺陷,或直接送下游轧制成条钢、线材、钢板、钢卷及钢片等成品。
钢铁企业生产流程ppt课件
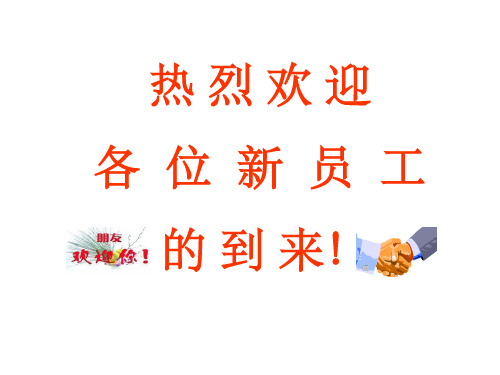
14个泊位:其中25万吨矿 石泊位2个、10万吨级煤 炭泊位1个、5万吨级废钢 泊位1个、2万吨级件杂货 泊位2个、1万吨级件杂货 泊位6个、1万吨级散货出 口泊位2个。
1、2万吨成品泊位
10万吨矿石泊位
转运站
带式输送机 25万吨矿石泊位
5.1 码头工序流程
桥式抓斗卸船机
门机方案
装卸桥方案
组综
成合
总体布置
确定建设项目各场地的配置及各场地交通和能 源综合连接的设计。
主要工序
指钢铁企业内的主体生产厂,如:综合原料场、 焦化、烧结、炼铁、炼钢、轧钢等。
公辅设施
指钢铁企业内的公用辅助设施,如:氧气站、 自备电厂、变电站、煤气站、水处理、空压站等。
2. 钢铁冶金简况
1)矿山的选择,矿山选定后开始是采矿,粉碎,选矿。 2)采掘铁矿石,用粉碎机粉碎,用磁力选矿或浮力选矿选出含铁量高的矿石 制成矿粉。然后制料; 3)通过烧结法或者球团法制成烧结料或者球团料。 4)将制成的烧结矿、球团矿输送到炼铁,也就是把料加入高炉炼成铁水; 5)采用铁水罐或混铁车运送铁水送入炼钢,进行铁水预处理脱硫,再注入转 炉进行吹炼,之后对钢水进行钢水精炼处理。然后进入连铸,用连铸机把钢水铸 成合格钢坯; 6)最后进行轧制。如果是板坯。钢轧机把钢坯轧成一定厚度的钢板或是方坯 ,制成线材或棒材。 简称:采矿-选矿-人造富矿(烧结、球团)-炼铁-炼钢-轧制-冷轧(线棒)
主要工艺及设备配置
年产500万吨/a规模链篦机回转窑生产 线的工艺配置如下 ; 主要包括煤破碎筛分室、煤粉制备、 原、燃料缓冲槽、精矿细磨、浓缩池、 过滤、精矿干燥、高压辊磨、添加剂 配料、混合、造球、生球筛分及布料、 生球干燥及预热、氧化焙烧、冷却、 成品球团矿输出.粉尘处理等主要工序。
钢铁生产流程课堂PPT
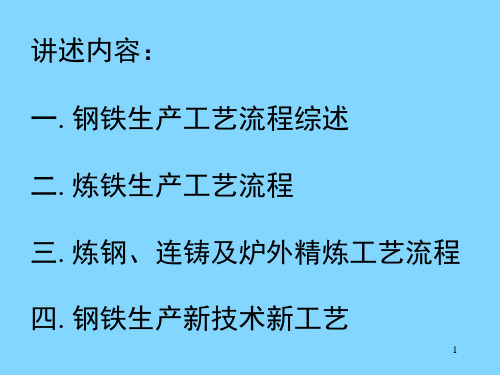
(6)切割装置 ·作用:定尺、切割。 ·方式:火焰、机械 ·火焰切割 -设备轻,不受断面限制,切口齐,
有金属损耗; ·机械切割: - 切割速度快 -无金属损耗 -操作安全可靠 -设备投资大,重量较大。
53
连铸机的生产能力
1)连铸机的作业率 指一年的生产时间(含准备时间)占 一年的日历时间的百分数。 y = (C+P)/ D ×100% 其中:y:作业率 C:年浇铸时间 P:年准备时间 D:年日历时间
6.渣铁处理系统 出铁场、渣铁沟、泥炮、开口机、炉前天车、水渣池、渣铁罐车
16
17
7.喷吹系统 煤粉制备、储煤罐、喷吹罐、混合器、喷枪
18
高炉生产技术经济指标
19
20
21
三、炼钢生产工艺流程 •转炉炼钢工艺; •铁水预处理工艺; •钢水炉外精炼处理工艺。
22
钢与生铁的区别:
首先是碳的含量,理论上一般把碳含量 小于2.11%称之钢,它的熔点在14501500℃,而生铁的熔点在1100-1200℃。
31
32
连铸机的种类
连铸机的机型及其特点 2.1.1 连铸机的机型 (1) 按外形分类;
33
(2)按铸坯断面分类:
机型
最大断面 mm×mm
最小断面 mm×mm
经常浇注断面 mm×mm
板坯
300×2640 310×2500
130×250
180×700~ 300×200
大方坯 小方坯
圆坯
600×600 160×160
·要求全凝固矫直,限制了生产率。
37
(3)多点弯曲立弯式连铸机
- 有垂直段,夹杂物容易上浮,具有立
弯
式连铸机的优点;
钢铁生产流程详解图
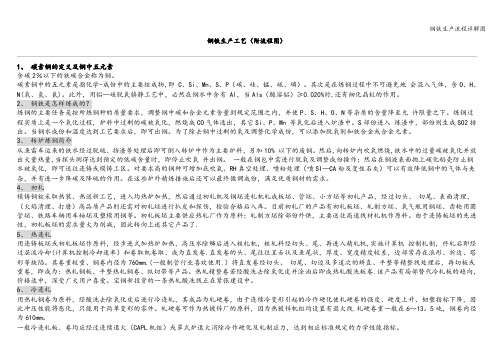
钢铁生产工艺(附流程图)1、碳素钢的定义及钢中五元素含碳2%以下的铁碳合金称为钢。
碳素钢中的五元素是指化学-成份中的主要组成物,即 C、Si、Mn、S、P(碳、硅、锰、硫、磷)。
其次是在炼钢过程中不可避免地会混入气体,含O、H、N(氧、氢、氮)。
此外,用铝—硅脱氧镇静工艺中,必然在钢水中含有 Al,当Als(酸溶铝)≥0.020%时,还有细化晶粒的作用。
2、钢铁是怎样炼成的?炼钢的主要任务是按所炼钢种的质量要求,调整钢中碳和合金元素含量到规定范围之内,并使P、S、H、O、N等杂质的含量降至允许限量之下。
炼钢过程实质上是一个氧化过程,炉料中过剩的碳被氧化,燃烧成CO气体逸出,其它Si、P、Mn 等氧化后进入炉渣中。
S部份进入炼渣中,部份则生成SO2排出。
当钢水成份和温度达到工艺要求后,即可出钢。
为了除去钢中过剩的氧及调整化学成份,可以添加脱氧剂和铁合金或合金元素。
3、转炉炼钢简介从鱼雷车运来的铁水经过脱硫、挡渣等处理后即可倒入转炉中作为主要炉料,另加10% 以下的废钢。
然后,向转炉内吹氧燃烧,铁水中的过量碳被氧化并放出大量热量,当探头测得达到预定的低碳含量时,即停止吹氧并出钢。
一般在钢包中需进行脱氧及调整成份操作;然后在钢液表面抛上碳化稻壳防止钢水被氧化,即可送往连铸或模铸工区。
对要求高的钢种可增加底吹氩、RH真空处理、喷粉处理(喷SI—CA粉及变性石灰)可以有效降低钢中的气体与夹杂,并有进一步降碳及降硫的作用。
在这些炉外精炼措施后还可以最终微调成份,满足优质钢材的需求。
4、初轧模铸钢锭采取热装、热送新工艺,进入均热炉加热,然后通过初轧机及钢坯连轧机轧成板坯、管坯、小方坯等初轧产品,经过切头、切尾、表面清理,(火焰清理、打磨)高品质产品则还需对初轧坯进行扒皮和探伤,检验合格后入库。
目前初轧厂的产品有初轧板坯、轧制方坯、氧气瓶用钢坯、齿轮用圆管坯、铁路车辆用车轴坯及塑模用钢等。
初轧板坯主要供应热轧厂作为原料;轧制方坯除部份外供,主要送往高速线材轧机作原料。
钢铁工艺流程图(采矿-选矿-冶炼-连铸-环保
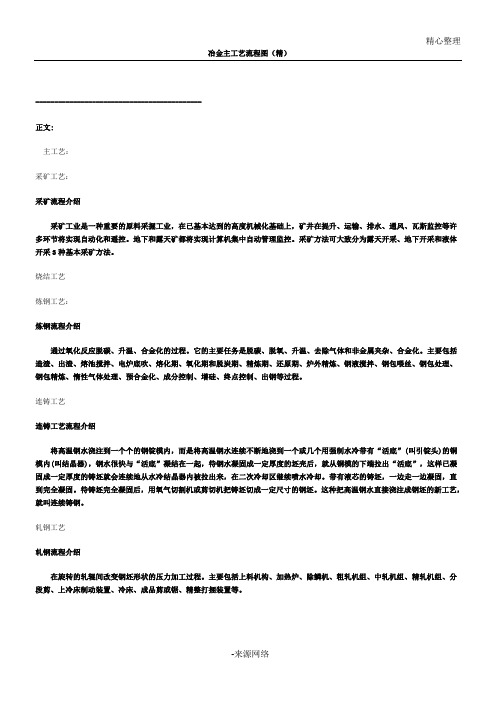
炼钢工艺:
炼钢流程介绍
通过氧化反应脱碳、升温、合金化的过程。它的主要任务是脱碳、脱氧、升温、去除气体和非金属夹杂、合金化。主要包括造渣、出渣、熔池搅拌、电炉底吹、熔化期、氧化期和脱炭期、精炼期、还原期、炉外精炼、钢液搅拌、钢包喂丝、钢包处理、钢包精炼、惰性气体处理、预合金化、成分控制、增硅、终点控制、出钢等过程。
连铸工艺
连铸工艺流程介绍
将高温钢水浇注到一个个的钢锭模内,而是将高温钢水连续不断地浇到一个或几个用强制水冷带有“活底”(叫引锭头)的铜模内(叫结晶器),钢水很快与“活底”凝结在一起,待钢水凝固成一定厚度的坯壳后,就从铜模的下端拉出“活底”,这样已凝固成一定厚度的铸坯就会连续地从水冷结晶器内被拉出来,在二次冷却区继续喷水冷却。带有液芯的铸坯,一边走一边凝固,直到完全凝固。待铸坯完全凝固后,用氧气切割机或剪切机把铸坯切成一定尺寸的钢坯。这种把高温钢水直接浇注成钢坯的新工艺,就叫连续铸钢。
轧钢工艺
轧钢流程绍
在旋转的轧辊间改变钢坯形状的压力加工过程。主要包括上料机构、加热炉、除鳞机、粗轧机组、中轧机组、精轧机组、分段剪、上冷床制动装置、冷床、成品剪或锯、精整打捆装置等。
冶金主工艺流程图(精)
--------------------------------------------
正文:
主工艺:
采矿工艺:
采矿流程介绍
采矿工业是一种重要的原料采掘工业,在已基本达到的高度机械化基础上,矿井在提升、运输、排水、通风、瓦斯监控等许多环节将实现自动化和遥控。地下和露天矿都将实现计算机集中自动管理监控。采矿方法可大致分为露天开采、地下开采和液体开采3种基本采矿方法。
钢铁生产工业流程简图
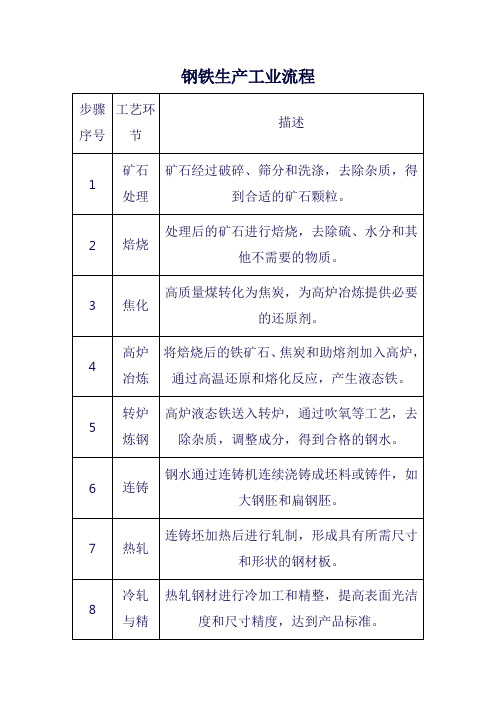
转炉炼钢
高炉液态铁送入转炉,通过吹氧等工艺,去除杂质,调整成分,得到合格的钢水。
6
连铸
钢水通过连铸机连续浇铸成坯料或铸件,如大钢胚和扁钢胚。
7
热轧
连铸坯加热后进行轧制,形成具有所需尺寸整,提高表面光洁度和尺寸精度,达到产品标准。
9
质量检测
对成品钢材进行质量检测,确保符合相关标准和客户要求。
钢铁生产工业流程
步骤序号
工艺环节
描述
1
矿石处理
矿石经过破碎、筛分和洗涤,去除杂质,得到合适的矿石颗粒。
2
焙烧
处理后的矿石进行焙烧,去除硫、水分和其他不需要的物质。
3
焦化
高质量煤转化为焦炭,为高炉冶炼提供必要的还原剂。
4
高炉冶炼
将焙烧后的铁矿石、焦炭和助熔剂加入高炉,通过高温还原和熔化反应,产生液态铁。
10
包装与发货
检测合格的钢材进行包装,并安排发货,送达客户或仓储地点。
钢铁生产流程PPT演示课件

200×200 55×55 φ 100
250×250~ 450×450 240×280~ 400×560
90×90~ 150×150
φ 200~φ 300
异性坯
工字型 460×460×120
中空坯 φ 450/6100
椭圆型 120×140
35
(3)按钢液压头分类
表2-2各种机型按钢水静压头分类特征
高炉一代寿命——炉龄 (10~15年,现要求20年以上)
11
2.高炉上料系统
上料系统——炉料料仓 筛分
称量
料罐 皮带机 ( 斜桥料车)
12
3.装料系统
装料系统: 受料斗 布料装置
探尺 均压、 放散阀
钟式炉顶
无料钟炉顶
13
4.送风系统
高炉鼓风机、热风炉、热风总管、热风支管、风口设备 国内热风炉有三种形式:内燃式、外燃式、顶燃式
26
铁水预处理与 钢水炉外精炼处理工艺
27
连铸工艺与设备
1 现代炼钢技术的发展(连铸技术的作用) (1) 1947年-1974年: 技术特点:转炉、高炉的大型化;以模铸-初 轧为核心,生产外延扩大。 (2) 1974年-1989年: 技术特点:全连铸工艺,以连铸机为核心。 (3) 1989年-现在:
技术特点:连铸-连轧工艺,以薄板 坯,连铸-连轧为代表,钢厂向紧凑化发展。
28
连续铸钢的技术特点
· 高效凝固 · 优化成型 · 化学冶金 · 物理冶金 · 节能
29
凝固理论
30
31
连续铸钢的工艺特点 (1)提高综合成材率:模铸从钢水到成坯的收 得 率大约84~88%,连铸为95~96%; (2)降低能耗:连铸节能主要是省去了开坯工序, 以及提高成材率。生产一吨钢坯比模铸可以节能 627~1046kJ,相当于21.4~35.7kg标准煤。加上综 合成材率的提高, 可以节能约130kg标准煤; (3)连铸产品的均一性好,质量好; (4)易于实现机械化和自动化。
51钢铁PPT-钢铁生产流程
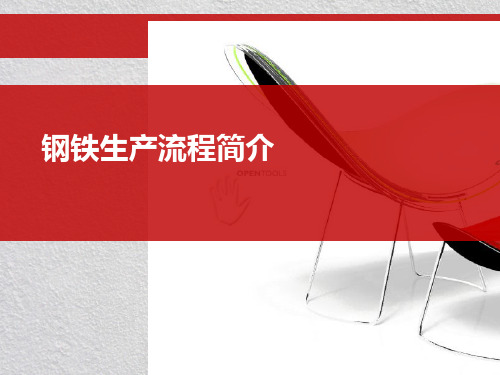
炼铁和炼钢
(2)基本反应原理:
氧化还原反应,在高温下,用氧化剂(纯氧气)把生铁中过多的碳和其 它杂质氧化除去。 (3)炼钢设备: 转炉,电炉,平炉(基本淘汰) (4)炼钢的原料:生铁,氧气,生石灰,硅铁和锰铁;(废钢)
炼铁和炼钢
转炉(氧气顶吹、底吹、顶底复合吹炼)炼钢,是利用吹入炉内
的氧与铁水中的元素碳、硅、锰、磷反应放出的热量来进行冶炼的。我 国转炉炼钢钢总产量的比重已接近70%。在世界上,转炉炼钢也仍然占 据着主要份额。转炉有着铁源来自矿石、钢质纯净等优势,目前世界上 每年约有60%的钢是用转炉生产的。
炼铁和炼钢
氧气顶吹转炉主要的优点是:
(l)生产效率高、生产能力大。一座300吨的炉子吹炼时间不到 20分 钟,包括辅助时间的冶炼时间不超过一小时。一座 30吨氧气顶吹转炉 的年产能力超过一座500吨平炉。
(2)基建投资相当于同样生产能力的平炉车间的70%,冶炼生产费用 相当于平炉的50%。
二次炼铁冶和金炼钢
炼铁和炼钢
氧气顶吹转炉
氧气转炉的主要形式是氧气顶吹转炉,冶炼时炉子保持不动,从上部 吹氧,但在装料和出钢时可以前后转动。氧气顶吹转炉的形状如圆筒,外 部是用钢板制成的炉壳,里面砌有耐火砖。炼钢的原料主要是铁水、废钢 和造渣剂(石灰石等)。
炼铁和炼钢
转炉的结构图
120吨转炉炼钢时的情景
炼铁和炼钢
连铸 连 铸
钢水连续浇铸是20世纪60年代开始大规模工业生产的一项新技术。浇 铸时把盛钢桶内的钢水通过中间包连续地注入结晶器中,钢液的热量被 流经结晶器,器壁的冷却介质迅速带走,形成具有一定厚度的坯壳,接 着通过拉坯机拉出结晶器.
连铸
然后进入二次冷却区直接喷水快速冷却,使坯壳内的钢液全部凝固 而成钢坯,经矫直后由切割机切成一定的长度,最后由输送辊道将其 输送到下道工序或铸坯场地。这种工艺方法有成材率和机械化程度高、 铸坯质量好、操作方便、劳动强度低、生产率高等优点。
13张动图,清晰的告诉你钢铁是怎么造出来的
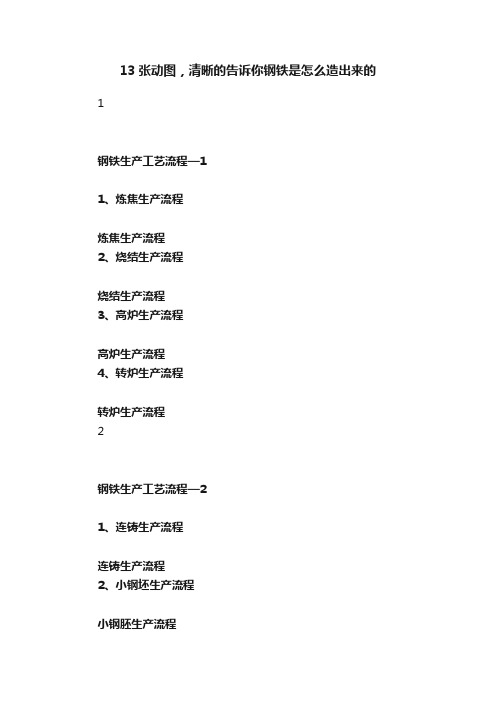
热轧
3
钢铁生产工艺流程—长材
线材生产流程
线材生产流程
4
钢铁生产工艺流程—板材
钢板生产工艺流程
钢板生产流程
End
来源:材易通(ID:matlinkcn)供稿,感谢
请注意甄别内容中的联系方式诱导购买等信息谨防诈骗
13张动图,清晰的告诉你钢铁是怎么造出来的
1
钢铁生产工艺流程—1
1、炼焦生产流程
炼焦生产流程
2、烧结生产流程
烧结生产流程
3、高炉生产流程
高炉生产流程
4、转炉生产流程
转炉生产流程
2
钢铁生产工艺流程—2
1、连铸生产流程
产流程
钢厂各个车间生产工艺(图片)
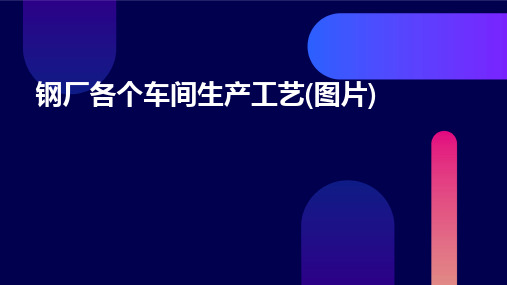
转炉炼钢工艺
总结词
环保、高效、低成本
详细描述
转炉炼钢工艺是一种利用氧气和铁水反应来生产钢的工艺。它具有环保、高效和低成本等优点,是目 前应用最广泛的炼钢工艺之一。转炉炼钢工艺流程包括铁水预处理、转炉炼钢和精炼等环节,最终得 到不同品质和规格的钢材。
电弧炉炼钢工艺
总结词
灵活性、小规模、高合金钢
详细描述
直接还原铁工艺
总结词
直接还原铁工艺是一种将铁矿石直接还原成海绵铁的工艺,通常在较低温度下 进行,以避免产生铁水。
详细描述
直接还原铁工艺通常使用天然气或煤作为还原剂,将铁矿石在较低温度下进行 还原,得到海绵铁。该工艺具有能耗低、污染小等优点,但同时也存在生产效 率较低、成本较高等问题。
熔融还原铁工艺
THANK YOU
球团车间生产工艺
总结词
球团是将细磨物料通过造球机制成球形团块,再经过 高温焙烧,使物料发生固结的工艺过程。
详细描述
球团车间的主要设备包括造球机、焙烧设备、冷却设 备等。造球机用于将细磨物料制成一定粒度和形状的 球形团块,焙烧设备用于提供高温环境,使球团内部 的矿物发生固结。冷却设备用于将焙烧后的球团快速 冷却,以避免其内部的晶体结构发生改变。
炭,以便后续的运输和使用。
烧结车间生产工艺
总结词
烧结是通过加热粉状物料,使其发生物理和化学变化, 最终形成致密块状物料的工艺过程。
详细描述
烧结车间的主要设备包括烧结机、燃烧器、除尘设施等 。烧结机是烧结过程中的核心设备,铁矿粉、溶剂、燃 料等原料在烧结机上经过点火、烧结、冷却等工序,最 终得到烧结矿。燃烧器用于提供烧结所需的热量,除尘 设施用于收集烧结过程中产生的烟尘,以减少对环境的 污染。
钢铁工业生产工艺流程图(可修改版)

生产用水
新水泵站
格栅 调节池 调节池
回用水
斜板沉淀池
排入大气 脱硫 静电除尘 废气 混料 制粒 烧结
配料
铁精粉、煤粉、焦
焦炭
石灰石
煤粉
喷煤 热风
配料
风机
石灰
回转窑焙
石灰 合金 VD炉、精炼炉 圆坯外 圆坯连铸 钢水
钢铁工业生产工艺流程图
排入大气 静电除尘 废气 烧结矿 球团矿 筛分粉 铁口粉 喷煤 高炉 热风 TRT 竖炉焙烧 造球 润磨 反 洗
静电除尘
脱硫
焦炭
炼铁配料
布袋除尘
布袋除尘
排入 排入 大气 大气
烘干
配料 布袋除尘 铁粉 膨润土
生产用水
重力除尘
铁水
氧气 汽轮机组 高炉煤气 发电及其 他用户 一次干法除尘 布袋除尘 排入大 轧机组轧 棒材外销回用水合金 炉源自精炼炉炼钢转炉转炉煤气
一次烟 二次粉
钢水
方坯连铸
加热炉
柳河水
机械搅拌澄
V型滤池 反 洗 蓄水池 反 洗 污 水
- 1、下载文档前请自行甄别文档内容的完整性,平台不提供额外的编辑、内容补充、找答案等附加服务。
- 2、"仅部分预览"的文档,不可在线预览部分如存在完整性等问题,可反馈申请退款(可完整预览的文档不适用该条件!)。
- 3、如文档侵犯您的权益,请联系客服反馈,我们会尽快为您处理(人工客服工作时间:9:00-18:30)。
钢铁生产工艺(附流程图)1、碳素钢的定义及钢中五元素含碳2%以下的铁碳合金称为钢。
碳素钢中的五元素是指化学-成份中的主要组成物,即 C、Si、Mn、S、P(碳、硅、锰、硫、磷)。
其次是在炼钢过程中不可避免地会混入气体,含O、H、N(氧、氢、氮)。
此外,用铝—硅脱氧镇静工艺中,必然在钢水中含有 Al,当Als(酸溶铝)≥0。
020%时,还有细化晶粒的作用。
2、钢铁是怎样炼成的?炼钢的主要任务是按所炼钢种的质量要求,调整钢中碳和合金元素含量到规定范围之内,并使P、S、H、O、N等杂质的含量降至允许限量之下。
炼钢过程实质上是一个氧化过程,炉料中过剩的碳被氧化,燃烧成CO气体逸出,其它Si、P、Mn 等氧化后进入炉渣中。
S部份进入炼渣中,部份则生成SO2排出。
当钢水成份和温度达到工艺要求后,即可出钢。
为了除去钢中过剩的氧及调整化学成份,可以添加脱氧剂和铁合金或合金元素。
3、转炉炼钢简介从鱼雷车运来的铁水经过脱硫、挡渣等处理后即可倒入转炉中作为主要炉料,另加10% 以下的废钢。
然后,向转炉内吹氧燃烧,铁水中的过量碳被氧化并放出大量热量,当探头测得达到预定的低碳含量时,即停止吹氧并出钢。
一般在钢包中需进行脱氧及调整成份操作;然后在钢液表面抛上碳化稻壳防止钢水被氧化,即可送往连铸或模铸工区。
对要求高的钢种可增加底吹氩、RH真空处理、喷粉处理(喷SI—CA粉及变性石灰)可以有效降低钢中的气体与夹杂,并有进一步降碳及降硫的作用。
在这些炉外精炼措施后还可以最终微调成份,满足优质钢材的需求。
4、初轧模铸钢锭采取热装、热送新工艺,进入均热炉加热,然后通过初轧机及钢坯连轧机轧成板坯、管坯、小方坯等初轧产品,经过切头、切尾、表面清理,(火焰清理、打磨)高品质产品则还需对初轧坯进行扒皮和探伤,检验合格后入库。
目前初轧厂的产品有初轧板坯、轧制方坯、氧气瓶用钢坯、齿轮用圆管坯、铁路车辆用车轴坯及塑模用钢等。
初轧板坯主要供应热轧厂作为原料;轧制方坯除部份外供,主要送往高速线材轧机作原料。
由于连铸板坯的先进性,初轧板坯的需求量大为削减,因此转向上述其它产品了。
5、热连轧用连铸板坯或初轧板坯作原料,经步进式加热炉加热,高压水除鳞后进入粗轧机,粗轧料经切头、尾、再进入精轧机,实施计算机控制轧制,终轧后即经过层流冷却(计算机控制冷却速率)和卷取机卷取、成为直发卷。
直发卷的头、尾往往呈舌状及鱼尾状,厚度、宽度精度较差,边部常存在浪形、折边、塔形等缺陷。
其卷重较重、钢卷内径为760mm。
(一般制管行业喜欢使用。
)将直发卷经切头、切尾、切边及多道次的矫直、平整等精整线处理后,再切板或重卷,即成为:热轧钢板、平整热轧钢卷、纵切带等产品。
热轧精整卷若经酸洗去除氧化皮并涂油后即成热轧酸洗板卷。
该产品有局部替代冷轧板的趋向,价格适中,深受广大用户喜爱。
宝钢新投资的一条热轧酸洗线正在紧张建设中。
6、冷连轧用热轧钢卷为原料,经酸洗去除氧化皮后进行冷连轧,其成品为轧硬卷,由于连续冷变形引起的冷作硬化使轧硬卷的强度、硬度上升、韧塑指标下降,因此冲压性能将恶化,只能用于简单变形的零件。
轧硬卷可作为热镀锌厂的原料,因为热镀锌机组均设置有退火线。
轧硬卷重一般在6~13.5吨,钢卷内径为610mm。
一般冷连轧板、卷均应经过连续退火(CAPL机组)或罩式炉退火消除冷作硬化及轧制应力,达到相应标准规定的力学性能指标。
冷轧钢板的表面质量、外观、尺寸精度均优于热轧板,且其产品厚度右轧薄至0.18mm左右,因此深受广大用户青睐。
以冷轧钢卷为基板进行产品的深加工,成为高附加值产品。
如电镀锌、热镀锌、耐指纹电镀锌、彩涂钢板卷及减振复合钢板、PVC 复膜钢板等,使这些产品具有美观、高抗腐蚀等优良品质,得到了广泛应用。
冷轧钢卷经退火后必须进行精整,包括切头、尾、切边、矫平、平整、重卷、或纵剪切板等。
冷轧产品广泛应用于汽车制造、家电产品、仪表开关、建筑、办公家具等行业。
钢板捆包后的每包重量为3~5吨。
平整分卷重一般为3~10吨/卷。
钢卷内径610mm。
钢铁生产工艺流程钢材知识2010-03-19 15:41:39 阅读241 评论0 字号:大中小热轧生产流程。
资源来源:台湾中钢公司网站。
热轧生产流程>第一热轧钢带生产流程:热轧钢带工场主要制程是将扁钢胚加热后,经粗轧机及精轧机轧延成钢带,并以层流冷却系统喷水冷却至适当温度,再由盘卷机卷成粗钢卷。
资源来源:台湾中钢公司网站。
热轧生产流程>热轧厚板剪切线布置图:主要功能为将原料钢卷上线解卷、切边、切片、整平、堆叠、及包装为成品钢板叠(HR PLATE)。
资源来源:台湾中钢公司网站。
热轧生产流程>热轧薄板剪切线布置图:主要功能为将原料钢卷上线解卷、调质精整、切边、切片、整平、堆叠、及包装为成品钢片叠(H.R. SHEET)。
资源来源:台湾中钢公司网站。
热轧生产流程>一号调质重卷线布置图:主要功能为将原料钢卷上线解卷、调质轧延、分切、重卷及包装为成品H.R COIL 或H.R BAND〔HR BAND 未调质轧延〕。
资源来源:台湾中钢公司网站。
热轧生产流程>二号调质重卷线布置图:主要功能为将原料钢卷上线解卷、调质轧延、分切、重卷及包装为成品H.R COIL 或H.R BAND〔HR BAND 未调质轧延〕。
资源来源:台湾中钢公司网站。
热轧生产流程>酸洗涂油线设备布置图:主要功能为将原料钢卷上线解卷、焊接、整平、酸洗、调质轧延、切边、涂油、分切及包装为成品酸洗钢卷。
资源来源:台湾中钢公司网站。
热轧生产流程>第二热轧钢带生产流程:热轧钢带工场主要制程是将扁钢胚加热后,经粗轧机及精轧机轧延成钢带,并以层流冷却系统喷水冷却至适当温度,再由盘卷机卷成粗钢卷。
资源来源:台湾中钢公司网站。
热轧生产流程>三号调质重卷线布置图:主要功能为将原料钢卷上线解卷、调质轧延、分切、重卷及包装为成品H.R COIL 或H.R BAND〔HR BAND 未调质轧延〕。
资源来源:台湾中钢公司网站。
热轧生产流程>四号调质重卷线布置图:主要功能为将原料钢卷上线解卷、调质轧延、分切、重卷及包装为成品H.R COIL 或H.R BAND〔HR BAND 未调质轧延〕。
资源来源:台湾中钢公司网站。
冶金工业工艺介绍(钢铁工业)北京古大仪表有限公司冶金工业是指对金属矿物的勘探、开采、精选、冶炼、以及轧制成材的工业部门。
包括黑色冶金工业(即钢铁工业)和有色冶金工业两大类。
冶金工业是重要的原材料工业部门,为国民经济各部门提供金属材料,也是经济发展的物质基础。
一条完整的钢铁生产线按工艺可分为:炼焦、高炉、转炉、连铸、热/冷轧、高速线材等部分。
下面是各工序的大致工艺介绍,方便各位了钢铁工业的解整个生产工艺流程。
炼焦(coking )将炉煤经过高温干馏转化为焦炭、焦炉煤气和化学产品的工艺过程。
即煤炭焦化。
指主要从硬煤和褐煤中生产焦炭、煤气、干馏炭及煤焦油或沥青等副产品的炼焦炉的操作活动。
根据最终温度,有高温炼焦(900~1100℃)、中温炼焦(660~750℃)和低温炼焦(500~580℃)。
通常指高温炼焦。
现代炼焦生产在焦化厂炼焦车间进行。
炼焦车间一般由一座或几座焦炉及其辅助设施组成,焦炉的装煤、推焦、熄焦和筛焦组成了焦炉操作的全过程,每个炉组都配备有装煤车、推焦车、拦焦机、熄焦车和电机车,一侧还应设有焦台和筛焦站。
近来开发的炼焦新工艺还有:配入部分型煤炼焦的配型煤工艺、用捣固法装煤的煤捣固工艺、煤预热工艺等。
高炉高炉:炼铁一般是在高炉里连续进行的。
高炉又叫鼓风炉,这是因为要把热空气吹入炉中使原料不断加热而得名的。
这些原料是铁矿石、石灰石及焦炭。
因为碳比铁的性质活泼,所以它能从铁矿石中把氧夺走,而把金属铁留下。
转炉转炉:目前,炼钢的方法主要有转炉、电炉和平炉三种。
大多数铁是在顶吹转炉中炼成钢的,铁与废钢混合在一起倒入炉中,吹入氧气流。
氧与铁中的碳结合成一氧化碳把碳带走。
顶吹转炉用40min就可生产350t钢。
在一定限度内,炉容量越大,经济效益越好,因此氧气顶吹转炉迅速走向大型化。
现在世界上最大的转炉为350t,并且正在研究建造400t-450t转炉。
电炉electric furnace利用电热效应供热的冶金炉。
电炉设备通常是成套的,包括电炉炉体,电力设备(电炉变压器、整流器、变频器等),开闭器,附属辅助电器(阻流器、补偿电容等),真空设备,检测控制仪表(电工仪表、热工仪表等),自动调节系统,炉用机械设备(进出料机械、炉体倾转装置等)。
平炉工艺介绍用于炼钢、配备蓄热室的膛式火焰炉。
平炉由熔炼室、炉头、上升道、沉渣室、蓄热室、换向阀、烟道、烟囱等组成。
熔炼室是平炉的中心部分,前面有装料炉门、后面底部有出钢口。
平炉炼钢是用平炉以煤气或重油为燃料,在燃烧火焰直接加热的状态下,将生铁和废钢等原料熔化并精炼成钢液的炼钢方法。
平炉炼钢自1864年法国人P..马丁利用有蓄热室的火焰炉,用废钢、生铁成功地炼出钢液起,直到1960年一直是世界上的主要炼钢方法,从60年代起平炉逐渐被氧气转炉和电炉炼钢所代替。
轧机是实现金属轧制过程的设备。
泛指完成轧材生产全过程的装备﹐包括有主要设备﹑辅助设备﹑起重运输设备和附属设备等。
但一般所说的轧机往往仅指主要设备。
英国于1766 年有了串行式小型轧机﹐19 世纪中叶﹐第一台可逆式板材轧机在英国投产﹐并轧出了船用铁板。
1848 年德国发明了万能式轧机﹐1853 年美国开始用三辊式的型材轧机﹐并用蒸汽机传动的升降台实现机械化。
接着美国出现了劳特式轧机。
1859 年建造了第一台连轧机。
万能式型材轧机是在1872 年出现的﹔20 世纪初制成半连续式带钢轧机﹐由两架三辊粗轧机和五架四辊精轧机组成。
深冷制氮的工艺流程说明深冷空气分离技术:深度冷冻法分离空气是将空气液化后,再利用氧、氮的沸点不同将它们分离。
即,造成气、液浓度的差异这一性质,来分离空气的一种方法。
因此必须了解气、混合物的一些基本特征:气-液相平衡时浓度间的关系:液态空气蒸发和冷凝的过程及精馏塔的精馏过程。
炼钢工艺过程中的各环节介绍炉外精炼:将炼钢炉(转炉、电炉等)中初炼过的钢液移到另一个容器中进行精炼的炼钢过程,也叫二次冶金。
炼钢过程因此分为初炼和精炼两步进行。
初炼:炉料在氧化性气氛的炉内进行熔化、脱磷、脱碳和主合金化。
精炼:将初炼的钢液在真空、惰性气体或还原性气氛的容器中进行脱气、脱氧、脱硫,去除夹杂物和进行成分微调等。
将炼钢分两步进行的好处是:可提高钢的质量,缩短冶炼时间,简化工艺过程并降低生产成本。
炉外精炼的种类很多,大致可分为常压下炉外精炼和真空下炉外精炼两类。
按处理方式的不同,又可分为钢包处理型炉外精炼及钢包精炼型炉外精炼等。