第七章 加压反应器
史上最全的反应器结构及工作原理图解!
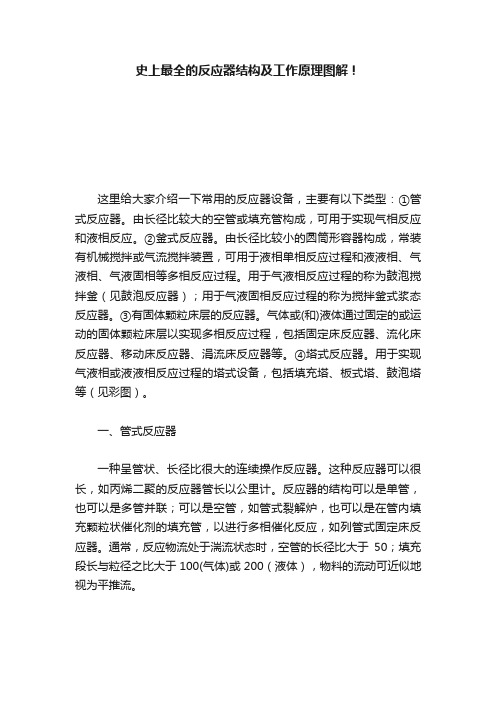
史上最全的反应器结构及工作原理图解!这里给大家介绍一下常用的反应器设备,主要有以下类型:①管式反应器。
由长径比较大的空管或填充管构成,可用于实现气相反应和液相反应。
②釜式反应器。
由长径比较小的圆筒形容器构成,常装有机械搅拌或气流搅拌装置,可用于液相单相反应过程和液液相、气液相、气液固相等多相反应过程。
用于气液相反应过程的称为鼓泡搅拌釜(见鼓泡反应器);用于气液固相反应过程的称为搅拌釜式浆态反应器。
③有固体颗粒床层的反应器。
气体或(和)液体通过固定的或运动的固体颗粒床层以实现多相反应过程,包括固定床反应器、流化床反应器、移动床反应器、涓流床反应器等。
④塔式反应器。
用于实现气液相或液液相反应过程的塔式设备,包括填充塔、板式塔、鼓泡塔等(见彩图)。
一、管式反应器一种呈管状、长径比很大的连续操作反应器。
这种反应器可以很长,如丙烯二聚的反应器管长以公里计。
反应器的结构可以是单管,也可以是多管并联;可以是空管,如管式裂解炉,也可以是在管内填充颗粒状催化剂的填充管,以进行多相催化反应,如列管式固定床反应器。
通常,反应物流处于湍流状态时,空管的长径比大于50;填充段长与粒径之比大于100(气体)或200(液体),物料的流动可近似地视为平推流。
分类:1、水平管式反应器由无缝钢管与U形管连接而成。
这种结构易于加工制造和检修。
高压反应管道的连接采用标准槽对焊钢法兰,可承受1600-10000kPa 压力。
如用透镜面钢法兰,承受压力可达10000-20000kPa。
2、立管式反应器立管式反应器被应用于液相氨化反应、液相加氢反应、液相氧化反应等工艺中。
3、盘管式反应器将管式反应器做成盘管的形式,设备紧凑,节省空间。
但检修和清刷管道比较困难。
4、U形管式反应器U形管式反应器的管内设有多孔挡板或搅拌装置,以强化传热与传质过程。
U形管的直径大,物料停留时间增长,可应用于反应速率较慢的反应。
5、多管并联管式反应器多管并联结构的管式反应器一般用于气固相反应,例如气相氯化氢和乙炔在多管并联装有固相催化剂的反应器中反应制氯乙烯,气相氮和氢混合物在多管并联装有固相铁催化剂的反应器中合成氨。
反应器(化工设备操作维护课件)
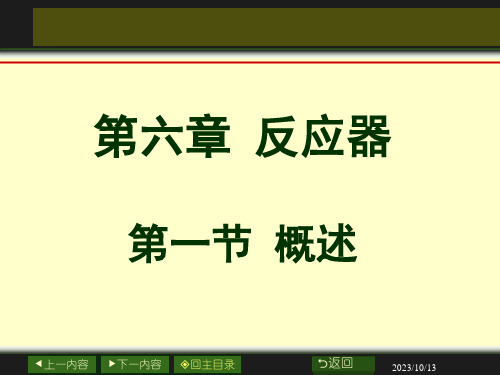
上一内容 下一内容 回主目录
2023/10/13
表 釜式反应器常见故障与处理方法
故障 搅拌轴转数降 低或停止转动
搪瓷搅拌器脱 落 出料不畅
产生原因 皮带打滑 皮带损坏 电机故障 被介质腐蚀
出料管堵塞 压料管损坏
处理方法
调整皮带 更换皮带 修理或更换电机 更换搪瓷轴或修 补 清理出料管 修理或更换配管
2、特点:反应过程伴有传热、传质和反应物的流动过程。 物理与化学过程相互渗透影响,反应过程复杂化。
上一内容 下一内容 回主目录
2023/10/13
§1-2 反应器的类型
• 反应器的类型: 釜式反应器 管式反应器
操作方式 材料 操作压力 绝热管式
换热管式
上一内容 下一内容 回主目录
2023/10/13
2023/10/13
b. 机械密封
机械密封 结构较复 杂,但密 封效果甚 佳。
上一内容 下一内容 回主目录
2023/10/13
4、换热装置
换热装置是用来加热或冷却反应物料,使之符合工艺 要求的温度条件的设备。
其结构型式主要有夹套式、蛇管式、列管式、外部循 环式等,也可用回流冷凝式、直接火焰或电感加热。
上一内容 下一内容 回主目录
2023/10/13
第六章 反应器
第二节 釜式反应器
上一内容 下一内容 回主目录
2023/10/13
§2-1 反应釜基本结构
(一)基本结构:
壳体 密封装置 换热装置 传动装置
上一内容 下一内容 回主目录
2023/10/13
1、搅拌釜式反应器的壳体结构
壳体结构:一般为碳钢材 料,筒体皆为圆筒型。釜 式反应器壳体部分的结构 包括筒体、底、盖(或称 封头)、手孔或人孔、视 镜、安全装置及各种工艺 接管口等。
化学反应工程第二版课后答案第七章
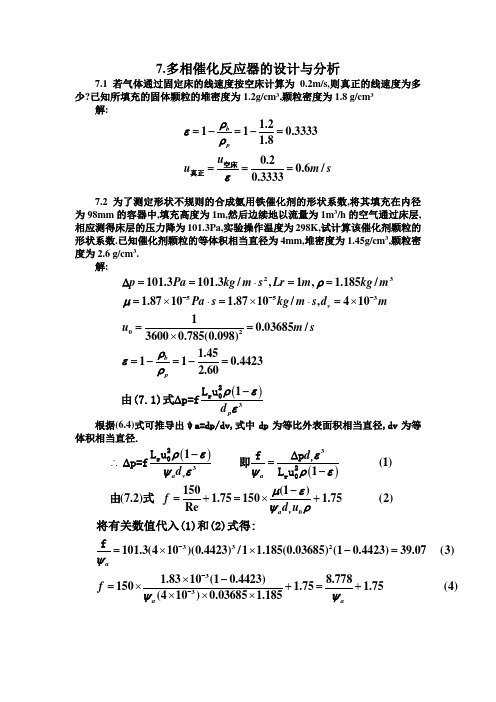
7.多相催化反应器的设计与分析7.1 若气体通过固定床的线速度按空床计算为0.2m/s,则真正的线速度为多少?已知所填充的固体颗粒的堆密度为1.2g/cm 3,颗粒密度为1.8 g/cm 3解:1.2110.33331.80.20.6/0.3333=-=-====空床真正b p u u m s ρερε7.2 为了测定形状不规则的合成氨用铁催化剂的形状系数,将其填充在内径为98mm 的容器中,填充高度为1m,然后边续地以流量为1m 3/h 的空气通过床层,相应测得床层的压力降为101.3Pa,实验操作温度为298K,试计算该催化剂颗粒的形状系数.已知催化剂颗粒的等体积相当直径为4mm,堆密度为1.45g/cm 3,颗粒密度为2.6 g/cm 3.解:()23553023101.3101.3/,1, 1.185/1.8710 1.8710/,41010.03685/36000.785(0.098)1.45110.44232.601---==⋅===⨯⋅=⨯⋅=⨯==⨯=-=-=-2r 0L u 由(7.1)式p=fv b p p p Pa kg m s Lr m kg m Pa s kg m s d mu m s d ρμρερρεε∆∆根据(6.4)式可推导出ψa=dp/dv,式中dp 为等比外表面积相当直径,dv 为等体积相当直径.()()330331(1)1150(1)(7.2) 1.75150 1.75(2)Re 101.3(410)(0.4423)/1 1.185(0.03685)-- ∴ = -- =+=⨯+ =⨯⨯2r 02r 0L u p fp=f即L u 由式将有关数值代入(1)和(2)式得:fv a v a a v ad d f d u ρεεψεψρεμεψρψ∆∆233(10.4423)39.07(3)1.8310(10.4423)8.778150 1.75 1.75(4)(410)0.03685 1.185---= ⨯-=⨯+=+ ⨯⨯⨯a af ψψ(3),(4):8.778/ 1.7539.07,1.758.77800.4969+= --= =2a 式联立将此式变为:39.07解此方程得:a a a a ψψψψψ7.3 由直径为3mm 的多孔球形催化剂组成的等温固定床,在其中进行一级不可逆反应,基于催化剂颗粒体积计算的反应速率常数为0.8s -1,有效扩散系数为0.013cm 2/s,当床层高度为2m 时,可达到所要求的转化率.为了减小床层的压力降,改用直径为6mm 的球形催化剂,其余条件均不变,,流体在床层中流动均为层流,试计算:(1) (1) 催化剂床层高度; (2) (2) 床层压力降减小的百分率.解(1)求dp 为6mm 的床层高度L 2,已知数据:dp 1=3mm=0.3cm,dp 2=0.6cm,L 1=2m, kp=0.8s -1,De=0.013cm 2/s00111222100211221110.392230.9210.784530.756===========⎰⎰求得求得AfAf x A Ar A x r A AA F dx L V R L V F dx R ηηηηϕηϕη12120.922 2.430.756∴==⨯=L L m ηη(2)求床层压力降减小的百分率:()()2210201122331211,--= =p p L u L u p f p f d d ρερεεε∆∆假定床层的空隙率不变,则有:11212221= (1)p p f L d p p f L d ∆∆层流流动时:012121501150Re /(2)-==⨯∴= p p p f d u f d d f εμρ(1),(2)式联立:2212221122112120.6/2 3.2252.430.3/2⎛⎫⎛⎫==== ⎪ ⎪ ⎪⎝⎭⎝⎭p p p p p p L d d d p L p L d d L d ∆∆床层压力降减少的百分率为:121 3.22510.689968.99%3.225--===p p p ∆∆∆7.4 拟设计一多段间接换热式二氧化硫催化氧化反应器,每小时处理原料气35000m 3(标准状况下),组成为SO 2:7.5%;O 2:10.5%;N 2:82%.采用直径5mm 高10mm 的圆柱形催化剂共80m 3,取平均操作压力为0.1216Mpa,平均操作温度为733K,混合气体的粘度等于3.4×10-5Pa.s,密度按空气计算.解:由(7.1)式()31-2r 0L u p=fp d ρεε∆根据题给条件有:107330.1013350002730.121321.75/3600-⨯⨯==u A m s A上式中A —床层截面积,m 2.12121/31/32380/80660.785(0.005)0.01 6.0051020.785(0.005) 4.140.0050.01660.785(0.005)0.017.215103.142---==⨯⨯===⨯⨯+⨯⨯⎡⎤⎛⎫⨯⨯===⨯ ⎪⎢⎥⎝⎭⎣⎦p p pp v L A A m V d m a V d mπ在题(7.1)中已推导出/=ap v d d ψ,因此有:336.005100.83237.21510--⨯==⨯a ψ查”无机化工反应工程”P108图4-1得ε=0.45,混合气的物性数据按空气计算误差不大,733K 下,ρ=0.4832kg/m 3,μ=0.034厘泊=3.4×10-5Pa.s,因此有:5310150(1)150 3.410(10.45)1.75150 1.75 1.75Re 6.00510(21.75)0.48320.04444 1.75----⨯⨯-=+=⨯+=+⨯⨯ =+p f d u A A μερ112333800.4832(21.75)(10.45)(0.04444 1.75) 1.8386.005100.45(0.04444 1.75)----⨯-∴=+=⨯⨯ ⨯+ A A p A A A Pa ∆要求△P<4052Pa 则有4052>1.838×107A -3(0.0444A+1.75)80 3.43123.32==L m7.5 多段冷激式氨合成塔的进塔原料气组如下:组分 NH 3 N 2 H 2 Ar CH 4 % 2.09 21.82 66.00 2.45 7.63 (1) (1) 计算氨分解基(或称无氨基)进塔原料气组成:(2) (2) 若进第一段的原料气温度为407℃,求第一段的绝热操作线方程,方程中的组成分别用氨的转化率及氨含量来表示.反应气体的平均热容按33.08 J/molK 计算.反应热△Hr=-5358J/molNH 3(3) (3) 计算出口氨含量为10%时的床层出口温度,按考虑反应过程总摩尔数变化与忽略反应过程总摩尔数变化两种情况分别计算,并比较计算结果.解:(1)计算氨分解基气体组成:100mol 原料气中含NH 32.09mol,相当于2.09/2molN 2及(1.5×2.09)molH 2,因此,(A) (A) 考虑反应过程中气体总摩尔数的变化.以y 代表氨基气体mol%,Ft 表示混合气体总摩尔流量,由2231322+ N H NH 可以看出,每生成1摩尔NH 3,混合气体总摩尔数减少1,所以生成氨的摩尔数=00-t A t A F y F y ,(下标A 代表NH 3,0代表进口处,y A0和y A 均指有氨基的mol%)因此有:()000001:(1)1--=+= +化简得t t A t A tA t t AF F y F y F y F F y(a) (a) 以N 2的转化率表示组成时的绝热操作线方程:()220,0-=N N r T P T F x H F C T∆∆∆上式中(-△Hr)以反应每kmol 的N 2计.()()22220,000,00001111+∴-=+-+=+A N N r t p T AN r T AN t p A y F x H F C T y F H y T x F C y ∆∆∆∆∆∆以进口处N 2的转化率为0作基准计算,则有:()()22,000211253581/-⎛⎫+=+ ⎪+⎝⎭-=⨯N r A N p A r y H y T T x C y H kJ kmolN ∆∆代入有关数据:20.2182535812168033.0810.0209⨯⨯+=++AN y T x化简得:2680692.4(1)=++A N T y x (2)又,生成的NH 3mol 数为:0000011+-=-+A A t A t A t A t Ay y F y F y F y F y反应消耗N 2的mol 数为:000001121⎛⎫+- ⎪+⎝⎭A A t A t A y y F y F y ∴ N 2的转化率:2000011210.2182⎛⎫+- ⎪+⎝⎭=A t A A A N t y F y y y x F代入数据:2110.02090.0209210.2182⎛⎫+- ⎪+⎝⎭=AA N y y x化简得:220.047882.291+=-N A N x y x (3)(3)代入(2)式得:2220.0478*******.41 2.291⎛⎫+=++ ⎪⎪-⎝⎭N N N x T x x 化简后得到以2N x 表示组成的绝热方程为:221620680 2.291=+-N N x T x(b) (b) 以NH 3含量表示组成的绝热操作线方程: ()()00--=t A t A r t p F y F y H F C T ∆∆式中(-△Hr)以每生成1kmolNH 3计,()()()()0000000031111111153581/0.0209(1)10.0209⎛⎫+--= ⎪+⎝⎭⎛⎫--+⎛⎫++∴=-=- ⎪⎪+++⎝⎭⎝⎭-= +⎡⎤-⎢⎥+⎣⎦53581代入数据:T=680+33.08A t A t A r t p A r r A A A A A A A p A A p A r A Ay F y F y H F C T y H H y y y y T y y y C y y C y H kJ kmolNH y y ∆∆∆∆∆∆化简得到以y A 表示组成的绝热操作线方程如下:6801620[0.02047(1)]=+-+A A T y y(B) (B) 忽略反应过程中气体总摩尔数的变化(a)以N 2转化率表示组成时的绝热操作线方程:22,0()-=N r N t p F H x F C T∆∆∆式中-△Hr 以每反应1kmolN 2计.()()()2222,02222,0,0000.218225358168033.08-- ∴==-⨯⨯=+=+即化简之T=680+707.1NN r N r N N t p t pr N N pN F H F H T x x F C F C y H T T x x C x ∆∆∆∆∆∆∆(b)以NH 3含量表示组成的绝热操作线方程: ()()0--=t A A r t p F y y H F C T ∆∆式中-△Hr 以每反应1kmolN 2计:()0-=-rA A pH T y y C ∆∆353581/-= r H kJ mol NH ∆()()05358168068016200.020933.08=+- =+- A A A T y y T y(3)计算出口氨含量为10%的床层出口温度,考虑反应总摩尔数变化时:6801620[0.02047(1)]6801620[0.10.02047(10.1)]805.5=+-+=+-+ =A A T y y K忽略反应总摩尔变化时:6801620(0.0209)6801620(0.10.0209)808.1=+-=+-=A T y K808.1-805.5=2.6K,温度相差并不大,这是由于合成氨反应体系总转化率不高的缘故,若转化率高则两种方法计算出来的床层出口温度将会有较大的差别.7.6 在绝热催化反应器中进行二氧化硫氧化反应,入口温度为420℃,入口气体中SO 2浓度为7%(mol);出口温度为590℃,出口气体中SO 2含量为2.1%(mol) ,在催化剂床层内A,B,C 三点进行测定.(1) (1) 测得A 点的温度为620℃,你认为正确吗?为什么? (2) (2) 测得B 点的转化率为80%,你认为正确吗?为什么?(3) (3) 测得C 点的转化率为50%,经再三检验结果正确无误,估计一下C 点的温度.解(1)绝热床内的温度是呈线性上升的,出口处温度最高,床内任一点温度不可能高于出口温度,故620℃是不可能的.(2)出口处SO 2的转化率为(0.07-0.021)×100%/0.07=70%.床层内部任一点处转化率不可能高于70%,故转化率为80%是不可能的.(3)△t=λ△X A , 590-420=λ×0.7 λ=(590-420)/0.7=242.86 故C 点温度为:t=t0+λ△X A =420+242.86×0.5=541.4℃7.7 乙炔水合生产丙酮的反应式为:2223322232+→++C H H O CH COCH CO H在ZnO-Fe 2O 3催化剂上乙炔水合反应的速率方程为:737.0610exp(7413/)/=⨯- ⋅床层A A r T C kmol m h式中C A 为乙炔的浓度,拟在绝热固定床反应器中处理含量为3%C 2H 2(mol)的气体1000m 3(STP)/h,要求乙炔转化68%,若入口气体温度为380℃,假定扩散影响可忽略,试计算所需催化剂量.反应热效应为-178kJ/mol,气体的平均恒压热容按36.4J/molK 计算.解:原料气中乙炔浓度很低,可忽略反应过程总摩尔数的变化.()000(1)(1)273273--==+A A A A A F x x C F Q Q t式中Q 0为以标准状态计的体积流量,Q 为温度t 时垢体积流量.()()()()77000.6800070000.64070273(1)7.0610exp(7413/)7.0610exp(7413/)(273)273112737.0610exp(7413/)2737.06101273exp(7413/)-=⨯-=⨯-++==-⨯⨯-+ =⨯--⎰⎰⎰Af A A A A x A r A A A A A A A A x r T C T F Q t Q t dx V F dx F r F x T t dx Q x T550:178/ 1.7810/36.4/()0.03 1.7810146.536.4-==⨯ =⋅-⨯⨯===已知p A r p H kJ mol J mol C J mol K y H KC λ∆∆绝热操作线方程为:()()007()380146.52737.06101273exp(7413/)=+-=++=⨯--令:f A A A A A t t x x x tx x T λ()0.683331.5101000 1.510 1.5--=⨯ =⨯⨯=⎰所以A A r f x dx V m7.8 题7.7所述乙炔水合反应,在绝热条件下进行,并利用反应后的气体预热原料,其流程如图7A 所示.所用预热器换热面积50m 2,乙炔浓度为3%的原料气以1000m 3(STP)/h 的流量首先进入预热器预热,使其温度从100℃升到某一定值后进入体积为1m 3的催化剂床层中绝热反应,反应速率方程见题7.7,预热器总传质系数为17.5w/m 2K,反应气体热容按36.4J/molK 计算,试求:(1) (1) 绝热温升(可不考虑反应过程中反应气体总摩尔数的变化).(2) (2) 计算反应器出口可能达到的乙炔转化率(列出方程式,并用文字说明求解过程).解:(1)绝热温升.按题意,在计算绝热温升时可忽略反应过程总摩尔数的变化.50500.03, 1.7810/,36.4/()0.03 1.7810146.536.4=-=⨯=⋅-⨯⨯===A r p A r p y H J mol C J mol K y H KC λ∆∆(2)列方程求解转化率:(A)由绝热床热量衡算得:T f =T 0+146.5X Af (1) (B)由预热器热量衡算得: T 0-373= T f -T 2 (2) (C) (C) 预热器中,传热的对数平均温度差为:()()2020373373ln ---=--fm f T T T T T T T ∆传热速率方程:()253335232222/, 1.01310,273,1000/,8.31410/1.01310100044.63/ 1.2410/8.3141027317.5/17.5/17.5501.2--= ==⨯== =⨯⋅⋅⨯⨯===⨯⨯⨯=⋅=⋅⋅ A =50⨯-=而又t p f mt t mf F C T T UA T F PQ RT P Pa T K Q m h R Pa m kmol KF kmol h kmol s U w m K J s m K m T T T ∆∆()()2023203731.938 1.938(3)411036.410ln 373----== -⨯⨯⨯-f m f T T T T T T T ∆(D)绝热床反应体积:()00000011211230.50.0321=-++--==- = =+⎰Afx r A AAA A A A A A A A V F dx kC C x T y C y x T δδ式中C A0为床层进口处浓度,而C A0=P A0/RT 0=0.03×1.013×105/(8.314×103T 0) =0.36655/T 0 kmol/m 3()()030010.3655/10.0150.0344.67 1.34/-= -=⨯=A A A A x T C kmol m T x T F kmol h故有:()7001.341(4)(1)0.36557.0610exp 7413/10.015== -⨯--⎰Afx Ar A A dx V T x T x T T联立解方程(1)-(4)便可解出T 0,T f ,T 2,X Af7.9 某合氨厂采用二段间接换热式绝热反应器在常压下进行如下反应:222+→+CO H O CO H热效应△Hr=-41030J/mol,进入预热器的半水煤气与水蒸汽之摩尔比1:1.4,而半水煤气组成(干基)为:组成 CO H 2 CO 2 N 2 CH 4 其他 ∑ mol% 30.4 37.8 9.46 21.3 0.79 0.25 100图7b 为流程示意图,图上给定了部分操作条件,假定各股气体的热容均可按33.51J/molK 计算,试求Ⅱ段绝热床层的进出口温度和一氧化碳转化率,设系统对环境的热损失为零.解:(1)预热器热量衡算:0222300105250300445'+=+⨯''+=+ = p p p f p FC t FC t FC T FC t t C (2)第一段绝热床热量衡算:()()1110010110.304141030155.21 1.433.490.8155.20.8124.1'-==--⨯===+'-= -=⨯= A A r pt t x x x y H C x x t t C λλλ∆∆ (3)由Ⅰ,Ⅱ段绝热床的中间换热器热量衡算得:1121121122300300124.1,300124.1,:124.1300424.1'+=+'-=-'-= -==+= 上面已算出所以,故有p p p p FC FC t FC t FC t t t t t t C t t C(4)列第二段绝热床热量衡算:()()2221222122122,,:445424.1155.2(0.8):0.9347''=+- -=-'-=-=把的值代入上式解得t t x x t t x x t t x x x λλ7.10在氧化铝催化剂上进行乙腈的合成反应:2233292.2/+→+ =-r C H NH CH CN H H kJ mol ∆设原料气的摩尔比为C 2H 2:NH 3:H 2=1:2.2:1,采用三段绝热式反应器,段间间接冷却,使每段出口温度均为550℃,而每段入口温度亦相同,已知反应速率式可近似地表示为:()4221/ 3.0810exp(7960/)=- ⋅ =⨯-A A r k x kmolC H kg h k T式中A x 为乙炔的转化率,液体的平均热容为128/=⋅pC J mol K ,如要求乙炔转化率达到92%,并且日产乙腈20吨,问需催化剂量多少?解:以A 表示乙炔,3020********.09/240.9224410.92⨯⨯===⨯⨯⨯⨯乙腈A F kmol hM在热衡算中忽略反应过程总摩尔数的变化,并把各段的p C 视为相等,对每一段均有:()()()()0000044:92.2/9.2210/19.2210171.51 2.21128=----===-==⨯⨯==++则有t p r A A r A r r A A AAAt ppt pr A AF C T H F x H F H H y F T xxxF C C F C H kJ mol J molT x x ∆∆∆∆∆∆∆∆∆∆∆∆∆∆依题意,各段进出口温度相等即各段△T 相等,所以各段转化率差△X A 亦相等,因此有:△X A =1/3×0.92=0.3067各段△T 为: △T=171.5△X A =171.5×0.3067=52.59K 因而各段进口温度=823-52.59=770.4KA()0.30670.306710001122.091==-⎰⎰A A Aw F dx dx r k x0.30670.2576(1)=-⎰AA dx k x因此,w 1=22.09×0.2576=5.690 Kg0.61340.306710.4212(1)=-⎰A A dx k x故有:w 2=22.09×0.4212=9.304 Kg0.920.613411.04(1)=-⎰A A dx k xw 3=22.09×1.04=22.96 Kg催化剂总重量=5.69+9.304+22.96=37.95 Kg7.11 例7.3所述的两段绝热式水煤气变换反应器,若第一段出口一氧化碳的转化率为84%,为使该段的催化剂用量最少,则第一段进口气体的温度应为多少?试利用题7.3所给的数据计算并与该题给定的第一段入口温度值相比较.解:用T 0表示第一段入口温度,第一段绝热操作线方程为: T=T 0+155.2X A (1) 例7.3中(G)式:()()()()2*20165421.674111⎡⎤⎛⎫∂⎢⎥ ⎪ ⎪--⎢⎥⎝⎭=⎢⎥∂--⎢⎥⎢⎥⎣⎦AA A A x R T k p x T ββ例7.3中(B)式:()*42.17210exp 6542//min -=⨯- ⋅⋅k T mol g Pa将(B)式代入(G)式得:()()()()()2420165421.6741(2)2.17210exp 6542/11-⎡⎤⎛⎫∂⎢⎥ ⎪ ⎪--⎢⎥⎝⎭= ⎢⎥∂⨯---⎢⎥⎢⎥⎣⎦AA A A x R T T P x T ββ将(1)式代入(2)式得:()()()()()()224000165421.6741(3)2.17210exp 6542/155.211155.2-⎡⎤⎛⎫∂⎢⎥⎪ ⎪-⎢⎥⎝⎭⎢⎥∂⎢⎥⎢⎥⎣⎦-=⎡⎤⨯-+--+⎣⎦A A x A A A A R T T x P x T x ββ而P A0=03.1267P t =0.1267×101325=1.284×104Pa 代入(3)式得:()()()()()()()()22440032200165421.674165422.17210 1.2841011155.2exp 155.21.67412.34610(4)654211155.2exp 155.2-⎡⎤⎛⎫∂⎢⎥⎪ ⎪-⎢⎥⎝⎭⎢⎥∂⎢⎥⎢⎥⎣⎦-=⎛⎫-⨯⨯⨯--+ ⎪+⎝⎭-=⨯ ⎛⎫---+ ⎪+⎝⎭A A x A A A A A A R T x T x T x x T x T x ββββ为使第一段催化剂用量最小,需符合(7.30)所表示的最佳化条件:()11,[]0;1,2,(7.30)+⎛⎫∂ ⎪ ⎪⎝⎭==⋅⋅⋅ ∂⎰A i AAx A A A x x R x T dx i N T(4)式代入(7.30)式得:()()()()30.840220065422.34610 1.6741exp 155.2011155.2⎛⎫-⨯- ⎪+⎝⎭=--+⎰A A A A T x dx x T x ββ()()()()()02065421.6741exp 155.2(5)11155.2⎛⎫-- ⎪+⎝⎭ = --+令A A A A T x f x x T x ββ上式变为:()()0.8430.8402.3461000(6)⨯= = ⎰⎰即A A A A f x dx f x dx符合(6)式的T 0即为所求的最佳第一段入口温度.上面有关式子中的β,可用例7.3中(C)式求得:()()()()34444443.99110 1.28310 1.59410 1.283101.283101 5.90910 1.283100.0165exp(4408/)7.3⨯+⨯⨯+⨯=⨯-⨯-⨯= 例中(A)式A AA A x x x x KpKp T β将(1)式代入例7.3(A)式得:Kp=0.0165exp[4408/(T 0+155.2X A )] (7) 将(7)式代入例7.3中(C)式得:()()()()()()()()34444443。
化学工程反应器知识点

化学工程反应器是化学工程领域中的重要组成部分。
反应器是用来进行化学反应的装置,它可以控制反应条件,实现化学反应的高效进行。
在化学工程反应器中,有许多重要的知识点需要了解和掌握。
本文将从基本概念、分类、设计和操作等方面,逐步介绍化学工程反应器的知识点。
一、基本概念 1. 反应器定义:反应器是用来进行化学反应的设备,它可以控制反应条件,包括温度、压力、物料进出等。
2. 反应器的作用:反应器可以实现化学反应的高效进行,提高反应速率和产物纯度。
3. 反应器的组成:反应器由反应容器、加热/冷却设备、搅拌装置、进出料口等组成。
二、分类 1. 反应器按照物料状态分类: - 气相反应器:适用于气体反应体系,如氧化反应。
- 液相反应器:适用于液体反应体系,如酯化反应。
- 固相反应器:适用于固体反应体系,如催化剂反应。
- 气-液相反应器:适用于气体与液体相间的反应体系,如气液萃取。
2. 反应器按照反应类型分类: - 批量反应器:适用于小规模生产和实验室研究。
- 连续流动反应器:适用于大规模生产,可以连续输入原料和产出产物。
- 微型反应器:适用于微量反应体系,可以实现高通量实验。
- 等温反应器:反应温度保持恒定。
- 非等温反应器:反应温度随时间变化。
三、设计 1. 反应器设计的目标:反应器设计需要满足反应速率、产物纯度、安全性等要求。
2. 反应器设计要考虑的因素: - 反应动力学:了解反应速率方程和反应机理,确定反应条件。
- 热力学:了解反应热效应,设计适当的冷却/加热设备。
- 流体力学:考虑反应物料在反应器内的流动情况,设计合适的搅拌装置。
- 安全性:考虑反应器内部的压力、温度等参数,设计安全措施。
3. 反应器设计的方法:- 经验法:根据类似反应器的经验数据进行设计。
- 数值模拟:利用计算流体力学(CFD)软件进行反应器内部流动和传热的模拟,优化设计。
- 实验方法:通过实验研究确定反应器设计参数。
加压帕尔反应器

加压帕尔反应器是一种常用于化学反应和热力学实验的重要设备,可以用来测量温度、压力、容积和物料的组分等参数。
本文将从以下三个方面介绍加压帕尔反应器的结构和功能:一、加压帕尔反应器的结构加压帕尔反应器通常由主体、密封系统、温度控制系统、压力控制系统和取样系统等部分组成。
主体通常采用不锈钢材料制成,内部设有隔板或搅拌装置,以增加传热和传质的效率。
密封系统是反应器的关键部分,要求能够承受较高的压力,并且保持较高的密封性能,以防止物料泄漏。
温度控制系统通过加热和冷却装置来控制反应器的温度,以保证反应的顺利进行。
压力控制系统通过压力传感器和调节阀等设备来实时监测和控制反应器的压力,以确保安全和准确测量。
取样系统则用于从反应器中取出样品,以便进行后续的分析和检测。
二、加压帕尔反应器的功能加压帕尔反应器的主要功能是进行化学反应和热力学实验。
通过在高压下进行反应,可以加快反应速率,缩短实验时间。
同时,加压反应器还能提高化学反应的平衡转化率,为研究化工过程提供有力的工具。
此外,加压帕尔反应器还可以用于热力学实验,如焓变、熵变等参数的测量,为热力学研究提供准确的数据支持。
三、使用加压帕尔反应器的注意事项在使用加压帕尔反应器时,需要注意以下几点:1. 操作前应仔细检查设备各部件是否完好无损,特别是密封系统和压力控制系统。
2. 在加压操作前,应确保物料已经完全混合均匀,以免影响实验结果的准确性。
3. 在进行实验时,应严格按照操作规程进行操作,避免因操作不当导致设备损坏或实验数据失真。
4. 实验结束后,应及时清洗设备,并确保设备内无残留物,以防止设备腐蚀和堵塞。
5. 定期对设备进行维护和保养,确保设备的正常运行和使用寿命。
总之,加压帕尔反应器是一种重要的实验设备,使用时需要严格按照操作规程进行,并注意设备的维护和保养。
通过正确的使用和维护,可以延长设备的使用寿命,提高实验的准确性和可靠性。
反应器基本理论课件
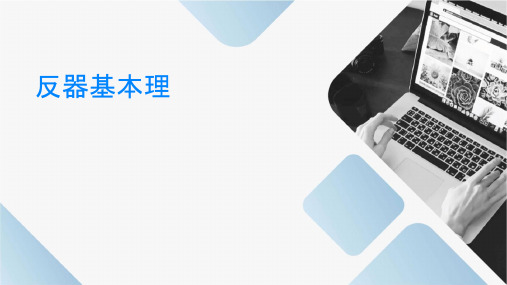
• 反应器概述 • 反应器的基础理论 • 反应器的类型与选择 • 反应器的操作与优化
反器概述
01
反应器的定义和分类
分类
连续反应器(Continuous Reactor):反应物以稳定流速连 续加入,产物也连续流出。
定义:反应器是一种用于进行化 学反应的设备或系统,通过控制 反应条件来促进化学反应的进行, 并获取所需的产物。
批式反应器(Batch Reactor): 反应物一次性加入,反应完成后 产物一次性取出。
半连续反应器(Semi-Batch Reactor):反应物一部分连续加 入,一部分批次加入。
反应器在化工流程中的地位
01
02
03
核心设备
反应器是化工流程中的核 心设备之一,直接影响产 品质量和生产效率。
反应条件控制
评估指标
评估反应器性能的主要指标包括反应器的转化率、选择性、产率等。此外,还需关注反应器的能耗、设备寿命、 操作稳定性等方面的指标。在实际应用中,需根据具体反应体系和需求,综合权衡各方面因素,选择最适合的反 应器类型和设计参数。
04
反器的操作
化
反应器的稳态操作
稳态操作定义
指的是反应器在连续、稳 定的状态下进行操作,各 参数不随时间变化。
适用场景
非均相反应器适用于涉及固-液、固气等反应体系的反应过程,如催化裂 化、气体吸附等。
反应器的选择与评估
选择因素
在选择反应器时,需要考虑反应物的性质、反应条件、产物要求等因素。例如,对于快速反应,宜选择均相反应 器;对于慢反应,宜选择非均相反应器。同时,还需考虑反应器的传热、传质性能,设备的投资与运行成本等因 素。
非理想流动模型
分析实际反应器中可能出现的非理想流动现象,如返混、死区等, 以及这些现象对反应器性能的影响。
加压反应式-概述说明以及解释

加压反应式-概述说明以及解释1.引言1.1 概述概述:加压反应式在化学工程领域中扮演着重要的角色,它是一种通过增加反应系统中的压力来促进反应进行的技术。
在许多工业生产过程中,加压反应式被广泛应用,以提高反应速率,提高产率和改善产品纯度。
本文旨在探讨加压反应式的定义、应用及其优势,以及展望未来在这一领域的发展方向。
通过深入了解和研究加压反应式,我们可以更好地了解其在化学工程领域中的重要性,并为未来的研究和应用提供有益的参考和借鉴。
1.2 文章结构文章结构部分的内容应当包括对整篇文章的框架和组织进行说明,介绍各个部分的内容和关联,帮助读者更好地理解文章的结构和主题。
文章结构是为了更好地组织和表达作者的观点和论据,一般包括引言、正文和结论三个主要部分。
在本篇文章中,我们将按照这个结构进行论述和展开。
具体而言,在引言部分,我们会简要介绍加压反应式的概念和重要性,引导读者进入主题。
在正文部分,我们将详细探讨加压反应式的定义、应用领域和优势,以及相关的研究和案例分析。
最后,在结论部分,我们将对加压反应式的重要性进行总结,展望未来可能的发展方向,并得出结论。
通过文章结构的明确和清晰,读者可以更加系统地了解加压反应式的概念和意义,帮助他们更好地理解和应用这一概念。
1.3 目的:本文的目的是探讨加压反应式在化学工业中的重要性和应用。
通过分析加压反应式的定义、应用和优势,我们将揭示其在提高反应效率、加速反应速率、改善反应产物纯度等方面的作用。
此外,我们还将展望加压反应式在未来的发展趋势,为读者提供对这一领域更深入的了解和认识。
通过本文的阐述,旨在引起读者对加压反应式的关注,促进该领域的研究与应用。
2.正文2.1 加压反应式的定义:加压反应式是一种特殊的化学反应方式,即在高压条件下进行的化学反应。
通常情况下,在常压下进行的化学反应可能受到限制,因为在常压条件下,一些反应可能无法进行或进行速度较慢。
而通过加压的方式,可以提高反应物之间的碰撞频率,从而加快反应速率,促进反应的进行。
化学第七章 化学反应速率和化学平衡 微专题 24 含答案

微专题化学反应原理在物质制备中的调控作用1.化学反应方向的判定(1)自发反应在一定条件下无需外界帮助就能自发进行的反应称为自发反应.(2)熵和熵变的含义①熵的含义熵是衡量一个体系混乱度的物理量。
用符号S表示.同一条件下,不同物质有不同的熵值,同一物质在不同状态下熵值也不同,一般规律是S(g)>S(l)〉S(s)。
②熵变的含义熵变是反应前后体系熵的变化,用ΔS表示,化学反应的ΔS越大,越有利于反应自发进行。
(3)判断化学反应方向的判据ΔG=ΔH-TΔSΔG<0时,反应能自发进行;ΔG=0时,反应达到平衡状态;ΔG>0时,反应不能自发进行。
2.化工生产适宜条件选择的一般原则(1)从化学反应速率分析,既不能过快,又不能太慢。
(2)从化学平衡移动分析,既要注意外界条件对速率和平衡影响的一致性,又要注意二者影响的矛盾性。
(3)从原料的利用率分析,增加易得廉价原料,提高难得高价原料的利用率,从而降低生产成本。
(4)从实际生产能力分析,如设备承受高温、高压能力等.(5)注意催化剂的活性对温度的限制。
3.平衡类问题需综合考虑的几个方面(1)原料的来源、除杂,尤其考虑杂质对平衡的影响。
(2)原料的循环利用。
(3)产物的污染处理。
(4)产物的酸碱性对反应的影响.(5)气体产物的压强对平衡造成的影响。
(6)改变外界条件对多平衡体系的影响。
专题训练1.(2017·四川资阳诊断)无机盐储氢是目前科学家正在研究的储氢新技术,其原理如下:NaHCO3(s)+H2(g),Pd或PdO70 ℃,0.1 MPa HCOONa(s)+H2O(l)在2 L恒容密闭容器中加入足量碳酸氢钠固体并充入一定量的H2(g),在上述条件下发生反应,体系中H2的物质的量与反应时间的关系如表所示:下列推断正确的是()A.当容器内气体的相对分子质量不再变化时,反应达到平衡状态B.0~4 min内H2的平均反应速率v(H2)=0。
生物选矿技术第七章

• 浸出过程操作温度40℃左右,使用插入式螺旋冷 却管。 • 矿浆pH控制在1.6-1.8之间。 • 浸出槽都采用机械搅拌并充入空气。 • 充气充足以保持溶液中足够的二氧化碳及氧,溶 液中氧含量不低于1.5ppm。 • 按负荷要求,能够设计充分充气搅拌的最大槽尺 寸为士880m3。 • 采用轴流型搅拌器,耗能低。 • 整个生产过程采用计算机控制,所有装臵露天。
• 金的表面在氰化物溶液中逐渐地由表及里地溶解。 溶液中氧的浓度与金的溶解速度有关。金的溶解 速度随氧浓度上升而增大,采用富氧溶液或高压 充气氰化可以强化金的溶解。 • 氰化试剂溶解金银的能力为:氰化铵>氰化钙> 氰化钠>氰化钾。氰化钾的价格最贵,目前多数 使用氰化钠。氰化物的耗量取决于物料性质和操 作因素,常为理论量的20-200倍.
七、硫脲法浸金
• 硫脲又名硫化尿素,分子式为SCN2H4,白色具光泽 菱形六面体,味苦,密度为1.405克/厘米,易溶 于水,水溶液呈中性。硫脲毒性小。无腐蚀性对人 体无损害。结构式为: • NH2 • S=C <
• NH2
• 在氧化剂存在下,金呈Au(SCN2H4)2+络合阳离子形 态转入硫脲酸性液中。 • 硫脲溶金是电化学腐蚀过程,其他化学方程式可以 用下式表示: • Au+2SCN2H4 = Au(SCN2H4)2++e
• 此法虽是一种成熟的工业方法,但是焙烧过程 生成As2O3和S02,造成严重的环境污染。而且, 焙烧还生成不挥发的砷酸盐及砷化物,使As不 能完全脱除。Au被易熔的Fe和As的化合物包裹 而钝化,氰化处理含Fe焙砂时也达不到高的回 收率,要溶解钝化膜需要进行碱性或酸性浸出, 再磨碎、浮选等附加作业。
• 在南非,Getunin集团公司经过20余年努力,研究 开发了Genmin BI0X工艺,1984年开始中试,1986 年成功应用于南非菲尔维(Fairview)金矿山细菌 处理厂,实现了难处理金矿石细菌氧化预处理方 法在世界上的首次工业应用。 • 随后,巴西的桑本托(SaoBento)、澳大利亚的维 鲁纳(Wiluna)、澳大利亚的哈伯拉兹 (HarbourLights)、澳大利亚的犹安米和肯尼亚加 纳的阿散蒂(Ashanti)等十几家金矿山开始了生物 浸出方法的中试或投产,其中加纳的阿散蒂规模 最大。它处理的矿石是含碳质的硫化物金矿石, 直接氰化金浸出率仅5%-40%,细菌氧化预处理后 的氰化金浸出率可提高到94%以上。
反应器PPT课件
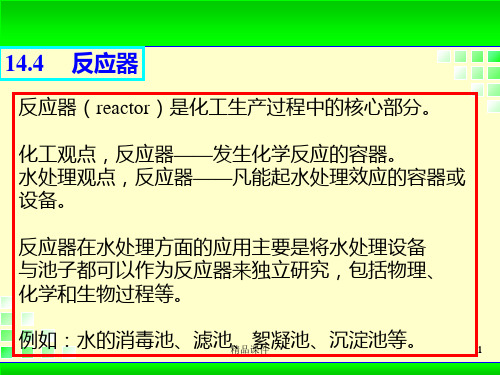
此类反应器需有投料和卸料的时间,通 常用于实验室实验或少量水处理中。
精品课件
10
物料衡算式为:
dCi dt
r(Ci )
t=0,Ci=C0;t=t,C=Ci,积分上式得:
t
ccoi
dCi r (Ci )
设为一级反应,r(Ci)=-kCi,则
t
ccoi
dCi kCi
1 C0 k lnCi
精品课件
11
理想反应 器分类
完全混合间歇式反应器(CMB型,completely mixed batch)
完全混合,间歇操作,封闭系统
完全混合连续式反应器(CSTR型,continous flow stirred tank reactor) 完全混合,连续操作,不封闭系统
推流式反应器(PF型,plug flow reactor)
推流式,连续操作,不封闭系统
精品课件
9
完全混合间歇式反应器(CMB型,completely mixed batch)
• 投入反应物,均匀混合,并发生反应, 达到预期反应程度后,排出反应物
特征: 1.反应过程中为封闭系统,无物质输入输 出。 2.反应器中反应物浓度随时间是变化的, 但任一时刻t,反应器中浓度认为是均 匀的。
精品课件
12
完全混合连续式反应器(CSTR型,continous flow stirred tank reactor )
反应物连续输入,一进入反应器即与 反应器内的物料快速混合均匀(瞬间 )。反应器内物料连续流出,且出水 中反应物浓度与反应器内各点处反应 物浓度相同。
• 特征: • 1.连续流入,连续流出; • 2.反应器内各点反应物浓度相同,且
Cn 0.01,n 2,k 0.92 C0
第七章酶反应器酶反应器的特点与类型酶反应器的选择和使用

2)连续流搅拌罐反应器(Continuous Flow Stirred Tank Reactor, CSTR) 适用的酶:固定化酶
2. 适用的操作方式: 分批式、流加分批式、连续式
3.优点:
结构简单,酶与底物混合充分均匀,传质阻力小,反应条件易控 制,能处理胶体状底物、不溶性底物。
方向以恒定速度通过反应床。
在其横截面上液体流动速度完全相同,沿流动方向底物及 产物的浓度逐渐变化,但同一横切面上浓度一致。又称活塞流 反应器(Plug Flow Reactor, PFR) 适用于:固定化酶。
优点:可使用高浓度的催化剂 。 与CSTR相比,可减少产物的抑制作用(产物浓度沿反应器 长度逐渐增高 )。 缺点:①温度和pH难以控制; ②底物和产物会产生轴向浓度分布; ③清洗和更换部分固定化酶较麻烦。 床内压力降大,底物必须在加压下才能进入。
(四)膜式反应器(Membrane Reactor) 将酶催化反应与半透膜的分离作用组合在一起的反应器。 适用于:游离酶、固定化酶。 1. 游离酶膜反应器
2)转盘型反应器 以包埋法为主,制备成固定化酶凝胶薄板(成型
为圆盘状或叶片状),然后装配在转轴上,并把整个 装置浸在底物溶液中,更换催化剂方便。
能处理粉末状底物; 即使应用细颗来自的催化剂,压力降也不会很高。缺点:需保持一定的流速,运转成本高,难于放大; 由于颗粒酶处于流动状态,易导致颗粒的机械破损; 流化床的空隙体积大,酶的浓度不高; 底物高速流动使酶冲出,降低了转化率。 改进:使底物进行循环,避免催化剂。 使用几个流态化床组成的反应器组,或使用锥形流态化床。
第七章酶反应器酶反应器的特 点与类型酶反应器的选择和使
用
第一节 酶反应器的特点与类型
加压器简介介绍

技术发展趋势与展望
技术创新
加压器技术不断发展,未来将 朝着更高效率、更低能耗和更
环保的方向发展。
材料优化
随着材料科学的进步,新型材料将 被广泛应用于加压器的制造,提高 其性能和寿命。
智能化控制
智能化技术将进一步实现加压器的 远程监控、故障诊断和自适应控制 。
行业挑战与对策建议
市场竞争
加压器市场竞争激烈,企业需要 加强技术创新、降低成本、提高
加压器简介介绍
汇报人: 2023-11-16
contents
目录
• 加压器概述 • 加压器的工作原理 • 加压器的性能指标 • 加压器的设计与制造 • 加压器的应用案例 • 加压器的发展趋势与挑战
01
加压器概述
定义与作用
定义
加压器是一种用于增加流体压力的设备,通常用于气体或液体管道系统中。
作用
04
加压器的设计与制造
设计理念与原则
高效性
加压器的设计应遵循高效 性的原则,确保在最小的 能量消耗下实现最佳的加 压效果。
稳定性
加压器的设计应注重稳定 性,确保其在长时间使用 过程中保持稳定,避免出 现波动或故障。
安全性
加压器的设计应充分考虑 安全性,确保在使用过程 中不会对人员和环境造成 伤害。
其他领域的应用案例
在建筑领域中,加压器被用于 输送水泥、沙子等建筑材料, 提高施工效率。
在航空航天领域,加压器则被 用于为各种设备提供稳定的气 源和压力,确保设备的正常运 行。
在医疗器械中,加压器可以用 于为注射器提供稳定且可靠的 压力,确保药物能够顺利地进 入患者体内。
06
加压器的发展趋势与挑战
材料选择与加工工艺
材料选择
- 1、下载文档前请自行甄别文档内容的完整性,平台不提供额外的编辑、内容补充、找答案等附加服务。
- 2、"仅部分预览"的文档,不可在线预览部分如存在完整性等问题,可反馈申请退款(可完整预览的文档不适用该条件!)。
- 3、如文档侵犯您的权益,请联系客服反馈,我们会尽快为您处理(人工客服工作时间:9:00-18:30)。
气三相,又称为三相流化床反
应器 。
34
35
• 两相或多相反应器 • 许多底物不溶于水或微溶于水,如脂肪、类脂肪
或极性较低的物质,进行酶反应时有浓度低,反 应体积大,分离困难、能耗大的缺点。 • 解决办法: • 使酶反应在有机相中进行,可增加反应物浓度, 还可减少底物,特别使产物对酶的抑制作用。
36
•
在其横截面上液体流动速度完全相 同,沿流动方向底物及产物的浓度逐 渐变化,但同一横切面上浓度一致。 又称活塞流反应器(Plug Flow Reactor, PFR)
23
• 适用于:固定化酶。
• 优点:可使用高浓度的催化剂 。
• 与CSTR相比,可减少产物的抑制作用(产物浓
度沿反应器长度逐渐增高 )。
• 缺点:①温度和pH难以控制; • ②底物和产物会产生轴向浓度分布; • ③清洗和更换部分固定化酶较麻烦。 • 床内压力降大,底物必须在加压下才能进入。
•
24
• (三)流化床型(Fludized Bed
Reactor, FBR)
• 装有较小颗粒的垂直塔式反应
器(形状可为柱形、锥形等)。底 物以一定速度由下向上流过, 使固定化酶颗粒在浮动状态下 进行反应。流体的混合程度介
• 4. 缺点:
• 反应效率低,载体易被破坏,搅拌动力消耗大,回收过程 酶易损失。 在反应器出口装上滤器 ,或用尼龙网罩住固定化酶 ,或制 成磁性固定化酶,或多个搅拌罐串联。
22
• 5. 改进:
•
• (二)固定床型(也称填充床, Packed Bed Reactor, PBR )
• 把颗粒状或片状等固定化酶填充于 固定床内,底物按一定方向以恒定速 度通过反应床。
反应器的形状为管式或列管式,中
空纤维可承受较大压力,通过正常 超滤程序将底物压入内壁与海绵状 介质上的酶起反应。
32
33
• (五)鼓泡塔型反应器
• 利用从反应器底部通入的气体产生的大量气泡, 在上升过程中起到提供反应底物和混和这两种作 用的一类反应器。是有气体参与的酶催化反应中 常用的一种反应器。 适用于:游离酶、固定化酶 在使用固定化酶进行催化反应 时,反应系统中存在固、液、
生物功能,在体外进行生化反应的装置系统。
13
根据生物反应过程中所使用的生物催化剂不同可将
生物反应器分为:酶反应器和细胞生物反应器。 生物反应器应具备的条件: 能维持一定的温度、pH、反应物(如营养物质、溶解 氧等)浓度
应具备良好的传质、传热和混合性能,以便为生物反 应的顺利进行提供适宜的环境条件。 细胞生物反应器除具备上述特性外,还要求有一定的 除菌及密封设备,以防止生产过程中因微生物侵入造成 的杂菌污染。 14
• 例如:气液反应、气液固反应、液固反应等。该
反应釜为催化加氢、聚合、酯化、冶金、制药、
化工、树脂合成、橡胶助剂工业的理想选择。
5
催化加氢优点:
• 1. 催化加氢属于绿色还原技术。应用催化加氢技术代替
铁粉、硫化碱、水合肼等传统还原法,不仅可以提高原
料利用率和产品的质量,降低生产成本,增强产品的竞 争力; • 2. 充分利用了氢气资源,又调整了产品结构,提高企业 的经济效益(同时可利用氮肥厂、氯碱厂和炼油厂回收 的氢气生产加氢产品) • 3. 三废能减少90%以上,有效地保护了生态环境。
38
• 底物的物理性质 • 溶解性物质 ——任何类型反应器 • 底物 颗粒物质 CSTR、PBR • 胶体物质
39
• 反应操作要求
• 1.若酶受高浓度底物抑制
• 固定化多酶反应器
• 将多种酶固定化后,制成多酶反应器,模拟微生物细胞 的多酶系统,进行多种酶的顺序反应,来合成各种产物, 目前此技术还处于实验阶段,但发展前景良好。 • 1)可组成高效率,巧妙的多酶反应器。
• 2)构建全新的酶化学合成路线,生产人类所需的、自 然界不存在的物质。 • 3)代替微生物发酵,用小型柱式反应器取代庞大的微 生物发酵罐。
④储存容器
——各种型式的储罐
3
安全附件
• • • • • • 压力表 温度计 安全阀 爆破片 紧急切断装置 安全联锁装置
4
• 高压釜:搅拌转速可控制、运行平稳、噪音小、
适用范围广、使用简单、操作方便等特点,是进
行各种搅拌反应的理想装置。 • 轴套采用自润滑的石墨、陶瓷、聚四氟乙烯填充 碳纤维等材料,适用于各种物料在不同的反应条 件下进行搅拌反应。
• 有立式和卧式两种,卧式适用于需氧反应或产 物有挥发性物,广泛应用于水处理装置。
30
• 3)空心酶管反应器 • 酶固定在细管的内壁上,底物溶液流经细管时,
只有与管壁接触的部分进行酶反应。
• 管内径1mm,管内流动属于层流。多与自动分析
仪等组装在一起,用于定量分析。
31
• 4)中空纤维膜反应器
• 由外壳和数以千计的醋酸纤维制成的中空纤维(内径 200μm -500μm,外径300μm -900μm)。组成。内 层紧密、光滑,具有一定分子量截流值,可截留大 分子物质而允许不同的小分子物质通过。 外层为多孔的海绵状支持层,酶被 固定在海绵状支持层中 。
• (四)膜式反应器(Membrane Reactor)
• 将酶催化反应与半透膜的分离作用组合在一起的 反应器。 • 适用于:游离酶、固定化酶。 • 1. 游离酶膜反应器
27
• 2. 固定化酶膜反应器
• 由膜状或板状固定化酶或固定化微生物组装的反
应器 。
• 分类:
• 1)平板状或螺旋状反应器
• 2)转盘型反应器
4NH 3 6NO 5N2 6H 2O
催化剂200-300℃:Pt (Pd,Fe,Cu,Mn)/Al2O3 (TiO2,V2O5)
11
催化反应器的设计
• 设计基础
– 反应器的流动模型
• 活塞流、混合流
• 实际流态介于两者之间
• 反应器内每一点的流态各不相同,停留时间各异 • 不同停留时间的物料在总量中所占的分率具有相 应的统计分布-停留时间分布函数 • 工业上,连续釜式反应器-理想混合反应器;径
19
• 酶反应器的类型 • 搅拌罐型反应器
• 固定床型反应器
• 流化床型反应器
• 膜式反应器
• 鼓泡塔型反应器
20
• (一)搅拌罐型(Stirred Tank Reacter, STR) • 有搅拌装置的、传统形式的反应器。由反应罐、搅拌器和保温
装置组成。
• 1. 分类: • 1)分批搅拌罐式反应器(Batch Stirred Tank Reactor, BSTR)
第六章 加压反应器与 其它反应器
参考书: 濮存恬编.精细化工过程及设备.北京: 化学工业出版社
1
6.1 加压反应器 基本概念—压力容器是指盛装一定工作介质, 能够承受压力(包括内压和外压)载荷 作用的密闭容器。这是一个泛指的概念。
压力容器的基本构成: 典型的压力容器的基本结构形式比较简单,主要由 壳体、封头、法兰、支座以及接管座等部件构成。
9
催化净化工艺
来自冶炼厂或硫磺 燃 烧 的 富 含 SO2 的 尾气 含有约为初始 进 气 SO2 浓 度 3% 的尾气 水 段间冷却 的四层催 化床 填充床 吸收塔 含有约为初 始 进 气 SO2 浓 度 0.3% 的 尾 气 水
预除尘和 水分
第二级 催化床
填充床 吸收塔
单级吸收工艺 二级吸收工艺
浓度较低,这就产生了一个产物回收工艺及成本
的问题。
16
17
18
• 二、 酶反应器的特点与类型
• 定义:以酶或固定化酶作为催化剂进行酶促反应的装置
称为酶反应器(Enzyme reactor)。
• 特点定的产物。
• 与化学反应器相比:在低温、低压下发挥作用,反应时 的耗能和产能较少。 • 与发酵反应器相比:不表现自催化方式(即细胞的连续 再生)。
SO2 1/ 2O2 Vanadium SO3
SO3 H 2O H 2 SO4
SO2单级和二级净化工艺的流程图 催化反应:420-550℃
10
催化净化工艺
NOx NH3 filter
Combustor Mixer
Reactor
NOx的选择性催化还原(SCR)
8NH 3 6NO2 7 N2 12H 2O
于CSTR和PFR之间。
• 适用于:固定化酶。
25
• 优点:具有良好的传质及传热性能,pH、温度控制 及气体的供给比较容易; • 不易堵塞,可适用于处理黏度高的液体; • 能处理粉末状底物;
• 即使应用细颗粒的催化剂,压力降也不会很高。
• 缺点:需保持一定的流速,运转成本高,难于放大; • 由于颗粒酶处于流动状态,易导致颗粒的机械破损; • 流化床的空隙体积大,酶的浓度不高; • 底物高速流动使酶冲出,降低了转化率。 • 改进:使底物进行循环,避免催化剂损失。 • 使用几个流态化床组成的反应器组,或使用锥形流态 26 化床。
•
适用的酶:游离酶、固定化酶
Reactor, CSTR)
• 2)连续流搅拌罐反应器(Continuous Flow Stirred Tank • 适用的酶:固定化酶
21
• 2. 适用的操作方式:
• 分批式、半分批式、连续式 • 3.优点: • 结构简单,酶与底物混合充分均匀,传质阻力小,反应条件 易控制,能处理胶体状底物、不溶性底物。
2、气体净化和压缩装置:
进入催化反应器的气体为克服阻力,需先经压缩,
气体压缩前先采用过滤器除去其中悬浮状的固体
杂质。 3、液态组分汽化和蒸气混合物制备所用设备
8
气体催化净化
• 含尘气体通过催化床层发生催化反应,使污染物
转化为无害或易于处理的物质 • 应用 – 工业尾气和烟气去除SO2和NOx – 有机挥发性气体(VOCs)和臭气的催化燃烧净化 – 汽车尾气的催化净化