从冶炼铜渣回收铜铁的试验研究_匡敬忠
典型铜熔炼渣铜铁元素分布特征及回收技术研究现状
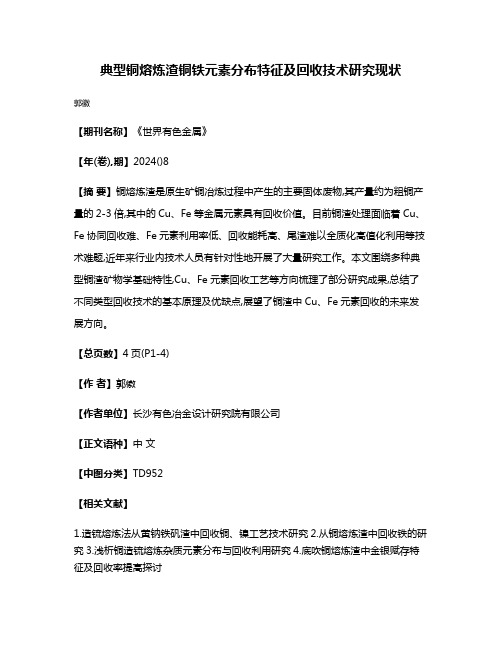
典型铜熔炼渣铜铁元素分布特征及回收技术研究现状
郭徽
【期刊名称】《世界有色金属》
【年(卷),期】2024()8
【摘要】铜熔炼渣是原生矿铜冶炼过程中产生的主要固体废物,其产量约为粗铜产量的2-3倍,其中的Cu、Fe等金属元素具有回收价值。
目前铜渣处理面临着Cu、Fe协同回收难、Fe元素利用率低、回收能耗高、尾渣难以全质化高值化利用等技术难题,近年来行业内技术人员有针对性地开展了大量研究工作。
本文围绕多种典型铜渣矿物学基础特性,Cu、Fe元素回收工艺等方向梳理了部分研究成果,总结了不同类型回收技术的基本原理及优缺点,展望了铜渣中Cu、Fe元素回收的未来发展方向。
【总页数】4页(P1-4)
【作者】郭徽
【作者单位】长沙有色冶金设计研究院有限公司
【正文语种】中文
【中图分类】TD952
【相关文献】
1.造锍熔炼法从黄钠铁矾渣中回收铜、镍工艺技术研究
2.从铜熔炼渣中回收铁的研究
3.浅析铜造锍熔炼杂质元素分布与回收利用研究
4.底吹铜熔炼渣中金银赋存特征及回收率提高探讨
因版权原因,仅展示原文概要,查看原文内容请购买。
云南某冶炼铜炉渣回收铜的试验研究

云南某冶炼铜炉渣回收铜的试验研究一、研究背景和意义铜炉渣是冶炼铜时产生的废弃物,具有较高的含铜量,回收渣中的铜可有效地减少环境污染,降低生产成本。
因此研究铜炉渣回收铜的方法具有重要的理论和应用价值。
二、研究现状和发展趋势目前,铜炉渣回收铜的方法主要有浸出法、融炼法、氧化铃法等。
另外,纳米材料在铜炉渣回收铜中也有较大的应用潜力。
三、试验方法和方案本试验采用浸出法回收含铜铜炉渣,并比较不同浸出剂对回收效率的影响。
选定一定条件下的最优方案进行铜炉渣中铜的回收,并对其物理化学性质进行分析。
四、数据结果和分析试验结果表明,采用某种浸出剂可高效地回收铜炉渣中的铜,回收率达到了较高水平。
在最优方案下,回收效率更高。
对回收铜的物理化学性质分析表明,回收的铜熔点和电导率等性质均符合国家标准。
五、结论和展望本试验成功地将铜炉渣中的铜回收,证明了浸出法是一种可行的、高效的铜炉渣回收方法。
未来可以进一步研究纳米材料在铜炉渣回收铜中的应用,探索更优的回收方法。
第一章:研究背景和意义随着人口的增加和经济的发展,铜的需求量逐年增加,而且伴随着铜的开采和冶炼而产生的废弃物和污染物也越来越多。
其中,铜炉渣一直是铜冶炼中产生的大量废弃物之一。
铜炉渣含有一定量的有价金属铜,回收渣中的铜是可行的,有助于保护环境和资源利用。
铜炉渣是指冶炼铜的过程中,废弃物质中的渣,其中含有很高的金属铜含量。
传统的处理方法是浸出,但浸出过程中有很多环境污染因素,随着各项环境法律政策的不断更新,新技术的出现开始越来越多的受到人们的关注与研究,令这一领域的研究变得富有前瞻和深入。
回收铜炉渣中的铜不仅能减少环境的污染,而且降低生产成本。
传统的浸出法操作比较复杂,需要大量的设备和环境保护措施,不仅耗时费力而且牵涉到较多的环境化学物质,使得一些复杂持久有机污染物和有毒物质悬而未决,回收效率也有很大的局限性。
因此,研究铜炉渣回收铜的方法具有重要的理论和应用价值。
铜炉渣回收铜技术不仅能减轻环境负担,而且能够利用废弃物产生经济效益。
云南某铜冶炼渣浮铜试验
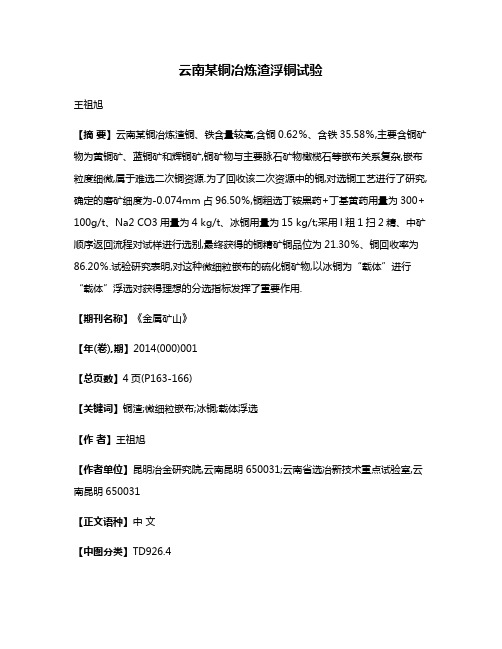
云南某铜冶炼渣浮铜试验王祖旭【摘要】云南某铜冶炼渣铜、铁含量较高,含铜0.62%、含铁35.58%,主要含铜矿物为黄铜矿、蓝铜矿和辉铜矿,铜矿物与主要脉石矿物橄榄石等嵌布关系复杂,嵌布粒度细微,属于难选二次铜资源.为了回收该二次资源中的铜,对选铜工艺进行了研究,确定的磨矿细度为-0.074mm占96.50%,铜粗选丁铵黑药+丁基黄药用量为300+ 100g/t、Na2 CO3用量为4 kg/t、冰铜用量为15 kg/t;采用l粗1扫2精、中矿顺序返回流程对试样进行选别,最终获得的铜精矿铜品位为21.30%、铜回收率为86.20%.试验研究表明,对这种微细粒嵌布的硫化铜矿物,以冰铜为“载体”进行“载体”浮选对获得理想的分选指标发挥了重要作用.【期刊名称】《金属矿山》【年(卷),期】2014(000)001【总页数】4页(P163-166)【关键词】铜渣;微细粒嵌布;冰铜;载体浮选【作者】王祖旭【作者单位】昆明冶金研究院,云南昆明650031;云南省选冶新技术重点试验室,云南昆明650031【正文语种】中文【中图分类】TD926.4铜是一种重要的有色金属原料,随着我国国民经济的飞速发展,其需求量增加显著。
因此,资源日渐枯竭与需求日渐增长的矛盾日益凸显。
为满足国内的巨大需求,我国每年需从国外进口大量的铜精矿和金属铜。
高昂的进口成本和大量的含铜固体废渣(选铜尾矿和铜冶炼渣等)对堆存地周边环境的危害,让业界开始将目光集聚在一些含铜较高的固体废渣的再利用上[1-6]。
我国每年约产生500万t火法炼铜渣,这些冶炼渣普遍含有较高的铜、铁、金和银等有价金属,是重要的二次资源。
对这种铜渣的提铜,较常见的方法有炭热法、烟化法、电炉贫化法和浮选法,其中,浮选法在处理低铜炉渣方面具有不可替代的效益优势[7-11]。
云南某铜冶炼厂采用火法工艺,造锍熔炼在艾萨炉中进行,所产出的铜锍和炉渣由放出口排放到沉降炉进行分离,铜锍进入转炉吹炼,高温炉渣经水淬成为固体废弃物(艾萨炉渣)。
铜渣浮选尾料中回收铜铁的研究

从图 4 中可以看出,随着焦炭加入量的增加,熔炼炉渣含铁 逐渐降低,当焦炭加入量达到 9% 以上时,熔炼炉渣中含铁不再 发生大幅降低,说明在焦炭加入量达到 9% 时,铜渣浮选尾料中 的铁基本被还原完全,同时考虑到生产实际中成本,选择焦炭的 加入量为 9% 为宜。 3.2 氧化钙加入量对熔炼炉渣含铁的影响
将铜渣浮选尾料磨碎至粒度为 200 目时,做扫描电镜分析, 结果如图 2 所示。
图 1 金川铜渣浮选尾料的 XRD 分析
收稿日期 :2020-05 作者简介 :刘瑜,女,生于 1976 年,汉族,四川邻水人,本科,副教授,研究方向 : 冶金工程、教育教学管理。
图 2 金川铜渣浮选尾料 SEM 照片
对 a、b、c、d、e 五点进行能谱分析,结果见表 2 所示。
金川铜渣浮选尾料中含铜 0.24%、含铁 42.58%、含二氧化硅 30.89%。 1.2 铜渣浮选尾料的晶相结构
通过 XRD 分析可知金川铜渣浮选尾料主要成分为 Fe2SiO4 和 Fe3O4。 1.2.1 铁橄榄石 Fe2SiO4
铁橄榄石属于斜方晶系,硬度为 6.5,比重为 4.32,熔点为 1205℃,颜色深灰。铁橄榄石是铜渣中的主要脉石矿物,含量较 高,结晶粒度较粗,形状较为规则。 1.2.2 磁铁矿相 Fe3O4
表 2 能谱分析结果
Fe
O
Si
Al Cu Zn Ca Mg
S
a 83.8 13.457 1.092 1.651 — — — — —
用氧压酸浸法从铜冶炼电尘灰中回收铜锌砷

用氧压酸浸法从铜冶炼电尘灰中回收铜锌砷摘要:本论文研究了一种用氧压酸浸法从铜冶炼电尘灰中回收铜锌砷的方法。
通过实验和分析,发现在一定的氧压条件下,可以有效地溶解电尘灰中的铜、锌和砷元素。
随后,通过调节浸出液的pH值和温度,成功地实现了铜、锌和砷的分离和回收。
实验结果表明,该方法具有高效、环保、经济的特点,为电尘灰资源化利用提供了一种可行的途径。
关键词:氧压酸浸法;氧压条件;铜锌砷引言本论文旨在研究一种利用氧压酸浸法从铜冶炼电尘灰中回收铜锌砷的方法。
电尘灰是铜冶炼过程中产生的废弃物,其中含有大量有价值的金属元素。
目前,存在着高效、环保、经济的回收方法的需求。
因此,本研究通过实验和分析,探讨了氧压酸浸法的可行性,并研究了影响回收效果的关键因素。
结果表明,该方法具有潜力成为电尘灰资源化利用的有效途径。
本研究对于提高铜冶炼废弃物的回收利用效率,推动可持续发展具有重要意义。
1.文献综述铜冶炼电尘灰是铜冶炼过程中产生的废弃物,其中富含铜、锌和砷等有价值的金属元素。
目前,常见的回收方法包括浸出法、熔炼法和氧压酸浸法等。
然而,传统方法存在着效率低、环境污染和资源浪费等问题。
因此,近年来,研究人员开始关注氧压酸浸法。
该方法利用氧压条件下的酸性溶液,能够有效溶解电尘灰中的金属元素。
此外,通过调节溶液的pH值和温度,可以实现铜、锌和砷的分离和回收。
研究表明,氧压酸浸法具有高效、环保和经济的特点,逐渐成为电尘灰资源化利用的一种重要方法。
然而,目前对于该方法的研究还相对较少,有待进一步深入探究其机理和优化条件,以提高回收效率和降低成本。
2.实验方法本论文采用氧压酸浸法从铜冶炼电尘灰中回收铜锌砷。
收集并分析电尘灰的化学成分和物理性质。
将电尘灰样品粉碎并筛选得到目标颗粒大小的样品。
在实验设备中加入一定量的电尘灰样品和酸性溶液,并进行氧压处理。
在一定温度和压力条件下,溶液中的氧气能够与酸性溶液反应,形成含氧的酸性介质。
通过调节溶液的pH值和温度,控制金属元素的溶解率和选择性沉淀。
熔融铜渣回收铜及铜铁合金工艺研究

目前 铜渣 的贫化 形式 比较单 一 ,主要集 中在单 纯地 回收铜或 铁 的技术方 面 ,而作 为耐 候钢
原料的铜铁合金 ,相关回收技术却鲜见报道。耐候
・
2 6・ 3
干 燥 技 术 与 设 备 D y n e ho o & E up e t r ig T c n l g y q i m n
回收铜炉用铜冷却壁冷却,散热较快,为了保持温
度恒 定 ,将来 自高温 回转煅 烧机 的一 部分高温 烟气 引入 提铜 炉 中来补 给热 量 的损失 。提铜 炉产 生的烟 气直接 排放 。在提铜 炉下 部 的高温 熔池 中,热态 铜
熔池 中 ,对熔 池产 生搅拌 作用 。辅料 首先 由输送 绞 龙送至 高温 回转煅烧 机 ,与来 自提铜 铁合金 炉 的高 温烟气 (60 逆流 运行 ,在 高温 回转 煅烧机 内进 10 ℃) 行 热 交换 ,预 热 好 的辅料 (5℃) 60 由卸 料 阀排 出进 入 下面 的料罐 。同时煅烧 机排气 所夹带 的较细 辅料
中主 要 研 究 路 线 是 向装 有 液 态 铜 渣 的 渣 包 中鼓 吹
炉渣 物质 组成及 嵌布 关系 比较 复杂 ,含铜矿 物大 部 分 以硫化铜 形 式存在 ,有 部分 金属铜 和少量 的氧 化
富氧,使渣 中的氧化亚铁氧化成四氧化三铁 ,然后
通过磁 选方式 进行 回收 ,但铁 的 回收率及 品位 均不
费比较严重等 问题。该熔融铜渣回收铜及铜铁合金
工艺 具有 回收 率高 、成本低 、节约 能源等特 点 。该
工 艺分 两个阶 段进行 ,低温阶 段 回收铜 ,高温 阶段
回收铜铁 合金 。其工 艺流程 图如 图 l 示 。 所
从铜浸出渣中回收铜的试验研究

中图分类号 :TF111
文献标识码 :A
文章编号 :11-5004(2020)01-0100-2
铜元素作为金属市场内的主要构成元素,在促进市场的发 展方面有着十分重要的作用,随着经济的快速发展,人们对金属 制品的要求越来越高,高品质铜出现供不应求的现象,造成铜金 属制品的价格呈现逐年阶梯式递增的状况,提升了人们对铜浸 出渣中回收铜的重视程度 [1]。分析金属市场内铜元素的发展趋 势,作为铜金属主要生产国家,目前产铜的关键方法为火法炼 铜,该种工艺手法下每产出 1t 的纯铜,即会产生对应的 3t ~ 4t 铜渣,随着市场对铜金属需求量的提升,对应存储的铜渣也越来 越多,一方面浪费了大量的占地面积,违背了资源可持续发展战 略的实施,另一方面,铜渣铜含有部分放射性元素,堆积在土壤 或河流中造成环境的污染,因此有关人员对于从铜浸出渣中回 收铜的试验研究势在必行。由于传统的回收铜方法存在能耗大、 成本高、渣料中仍存在大量铜元素为析出等缺陷,以下将结合产 铜方法存在的缺陷,开展从铜浸出渣中回收铜试验的研究,为铜 金属的回收提供正确的技术指导。
100
S 科学技术 cience and technology
3 实验结论分析 结合上述表 2 电解后阴极的金属元素含量的分析。可得知对
其进行电解后,电解后铜元素含量存在明显提升,约 99.98g/L。经 检测,浸出后的混合溶液中铜元素的含量为 32.47g/L,此时状态 下的溶液中电流密度为 350A/dm2,电流流经效率为 95.23%,电压 为额定标准电压 220V,电能消耗约为 1500(kW)h/t。随着混合溶 液的反复循环电解,溶液中最终铜元素的含量为 0.025g/L,从铜 浸出液中对于铜元素的回收率高达 99.78%。
S 科学技术 cience and technology 从铜浸出渣中回收铜的试验研究
某堆存铜渣中回收铜金属的选矿试验研究及生产应用
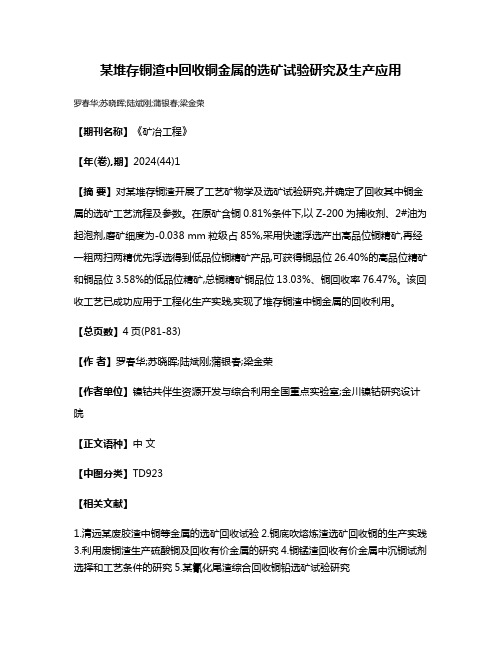
某堆存铜渣中回收铜金属的选矿试验研究及生产应用
罗春华;苏晓晖;陆斌刚;蒲银春;梁金荣
【期刊名称】《矿冶工程》
【年(卷),期】2024(44)1
【摘要】对某堆存铜渣开展了工艺矿物学及选矿试验研究,并确定了回收其中铜金属的选矿工艺流程及参数。
在原矿含铜0.81%条件下,以Z-200为捕收剂、2#油为起泡剂,磨矿细度为-0.038 mm粒级占85%,采用快速浮选产出高品位铜精矿,再经一粗两扫两精优先浮选得到低品位铜精矿产品,可获得铜品位26.40%的高品位精矿和铜品位3.58%的低品位精矿,总铜精矿铜品位13.03%、铜回收率76.47%。
该回收工艺已成功应用于工程化生产实践,实现了堆存铜渣中铜金属的回收利用。
【总页数】4页(P81-83)
【作者】罗春华;苏晓晖;陆斌刚;蒲银春;梁金荣
【作者单位】镍钴共伴生资源开发与综合利用全国重点实验室;金川镍钴研究设计院
【正文语种】中文
【中图分类】TD923
【相关文献】
1.清远某废胶渣中铜等金属的选矿回收试验
2.铜底吹熔炼渣选矿回收铜的生产实践
3.利用废铜渣生产硫酸铜及回收有价金属的研究
4.铜锰渣回收有价金属中沉铜试剂选择和工艺条件的研究
5.某氰化尾渣综合回收铜铅选矿试验研究
因版权原因,仅展示原文概要,查看原文内容请购买。
铜冶炼渣浮选回收铜的研究现状

铜冶炼渣浮选回收铜的研究现状摘要:我国国土面积辽阔,但铜资源却比较稀缺。
硫化铜矿物提铜是我国铜资源获取的一个重要方式。
在实际开展硫化铜矿石铜硫浮选分离工作过程中,涉及了较多类型的铜矿分离。
矿石性质具有较强的复杂性,不同类型矿石之间的性质也存在相应差异,本文主要围绕铜冶炼渣浮选回收铜进行分析和探讨,以供参考。
关键词:铜渣;回收铜;研究引言:铜渣作为一种副产品,其主要产生于火法炼铜熔硫以及转炉这一过程,所包含类型较多。
现阶段我国大部分铜企业对铜渣都会采用渣场堆放或者直接丢弃方式,采用此种铜渣处理方法除了会占用较多土地之外,同样会对环境产生相应污染。
一些铜渣也会应用在铺路工作中,或者是对其进行处理将其转化成混凝土应用在建筑建设过程中,该方法虽避免了铜渣的大面积堆存,但其中的有价金属却没有得到回收,导致被浪费。
所以,怎样实现铜渣的高效利用是现阶段我国铜冶炼领域重点研究的一项课题。
一、铜渣组成分析铜渣的组成具有较强复杂性,所包含的硫化物与氧化物较多,另外还掺杂着一定数量的微量成分。
铜渣从表面上看呈黑绿色或者是黑色,硬度和密度都相对较高,比重在4左右。
铁与硅在铜渣中的占比相对较高,铁榄石与磁铁矿是其中的主要矿物。
而硅主要包括硅酸盐以及一些硅灰石等,另外还含有一定数量的不具有透明性的玻璃体;其次,铜的硫化物也是铜渣的组成部分,比如掺杂了一定数量的金属铜与氧化铜。
除此之外,铜渣中还包含了一定的金、银、镍、钴等元素。
炉渣中所包含的铜元素更多的表现是硫化物形态,比如金属铜、黄铜矿等。
铜矿物在铜渣当中一般会与铁橄榄石基体以及铁矿聚集,也有可能表现为球状,在磁铁矿的包裹状态下存在。
一些铜渣则会表现为斑状结构,也有可能是多种不同的铜矿物之间镶嵌共同存在。
炉渣所拥有的冷却条件以及炉渣组分会对铜渣所包含铜矿物以及铁矿物的粒度产生较大影响,进而会引起铜矿物以及铁矿物之间的差异。
二、选矿法进行铜渣含有铜的回收分析在铜渣处理工作中对于选矿法的应用,明确来说就是对铜渣进行磨细,使其粒度达到一定程度,以此来实现铜渣所包含有价金属与脉石的分离,在此基础上对其采用浮选以及磁选工艺进行铜渣中铜以及其它一些有价金属的回收。
铜冶炼废渣综合回收研究

铜冶炼废渣综合回收研究随着社会经济的发展和工业化进程的加快,铜的需求量不断增加,铜冶炼产生的废渣问题也日益突出。
传统的废渣处理方式仅仅是简单地堆放或填埋,无法有效回收其中有价值的物质,同时也给环境带来了巨大的压力。
因此,针对铜冶炼废渣的综合回收研究具有重要的意义。
物理分选技术是指通过磁选、重选、浮选等物理方法,将废渣中的有价值金属从无价值金属中分离出来。
这种方法具有操作简单、成本低廉的特点,但回收率通常较低。
矿化回收技术是将废渣中的有价值金属通过化学反应转化为易于回收的矿石,再进行冶炼提取的方法。
这种方法可以提高回收率,但处理过程复杂且成本较高。
冶炼回收技术是将废渣直接进行冶炼,将其中的有价值金属提取出来。
这种方法回收率较高,但对设备要求较高,而且会产生大量的二次污染物。
综合考虑以上各种方法的优缺点,可以采用物理分选和矿化回收相结合的方式进行废渣的综合回收。
具体实施方法包括以下几个步骤:首先,将废渣进行物理分选,利用磁选、重选等方法将其中的有价值金属从无价值金属中分离出来。
采用磁选技术分离铁和钢水,并进行烧结处理,产生铁矿石。
重选技术可以分离出含铜、镍、锌等元素的精矿。
然后,将重选得到的精矿进行化学反应,将其中的有价值金属转化为易于回收的矿石。
最后,将转化后的矿石进行冶炼提取,得到高纯度的有价值金属。
此外,为了进一步提高废渣的回收率,还可以探索采用新型的废渣回收技术。
例如,可以采用生物技术将废渣中的有价值金属转化为生物质,然后通过生物浸出将其提取出来。
此外,还可以探索采用微生物降解废渣中的有机物质,促进有价值金属的提取。
综上所述,铜冶炼废渣的综合回收研究具有重要的意义。
采用物理分选和矿化回收相结合的方式可以提高回收率,同时也需要探索新型的废渣回收技术,以进一步提高回收效果。
只有加强对废渣综合回收技术的研究,才能最大程度地回收有价值金属,减少环境污染,实现可持续发展的目标。
从废铜渣中回收铜的研究
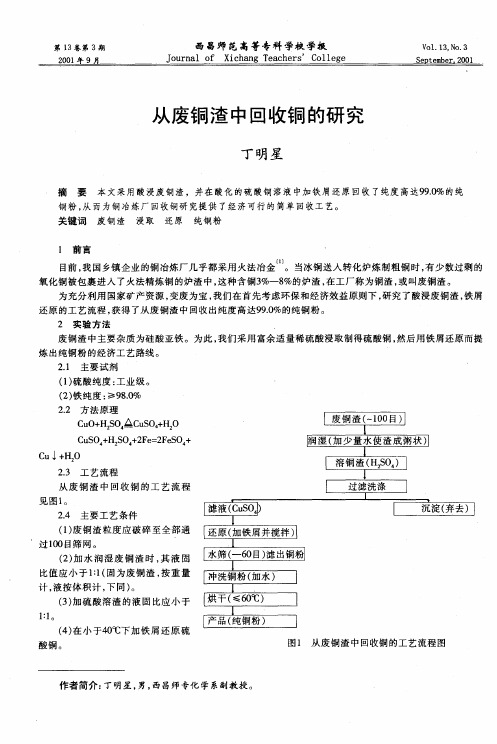
废铜渣( -100 目) 润湿( 加少量水使渣成粥状)
Cu工 0 +H2
2.3 工艺流程 从废铜渣中回收铜的工艺流程
见 图t o
溶铜渣(H2 S04)
2.4 主要工艺条件 ( 1)废铜渣粒度应破碎至全部通 ’ 过100 目 筛网。 (2 ) 加水润湿废铜渣时, 其液固
比值应小于1:1( 固为废铜渣 , 按重量 计, 液按体积计, 下同) 。 (3 )加硫酸溶渣的液固比应小于
1 前言
目 ,国 镇 业 铜 炼 几 都 用 法 金’ 当 铜 人 化 炼 粗 时有 数 剩 前 我 乡 企 的 冶 厂 乎 采 火 冶 ‘ 冰 送 转 炉 制 铜 ,少 过 的 〕 。
氧化铜被包裹进人了火法精炼铜的炉渣中, 这种含铜3%- 8%的炉渣, 在工厂称为铜渣, 或叫废铜渣。 为充分利用国家矿产资源, 变废为宝, 我们在首先考虑环保和经济效益原则下, 研究了酸浸废铜渣, 铁屑 还原的工艺流程 , 获得了从废铜渣中回收出纯度高达99.0%的纯铜粉。
注释及参考文献: ( 1〕 赵景员, 王淑贤.力学.人民教育出 版社(1979) 0 (2〕 周衍柏.理论力学.高等教育出版社( 1984 ) a
(3〕 梁昆森.数学物理方法, 人民教育出版社( 1976 ) 0 (责任编辑 :任学藻)
第 13 卷第 3 期
丙昌师范高等专科学校学报
J our na l of Xi chang Teacher s' Col l ege
Vo l . 13, No . 3
从废铜渣中回收铜的研 究
丁明星
摘 要 本文采用酸浸废铜渣,并在酸化的硫酸铜溶液中加铁屑还原回收了纯度高达99.0% 的纯 铜粉, 从而为铜冶炼厂回收铜研究提供了经济可行的简单回收工艺。 关键词 废铜渣 浸取 还原 纯铜粉1:1。Biblioteka 水筛(- 60 目)滤出铜粉
- 1、下载文档前请自行甄别文档内容的完整性,平台不提供额外的编辑、内容补充、找答案等附加服务。
- 2、"仅部分预览"的文档,不可在线预览部分如存在完整性等问题,可反馈申请退款(可完整预览的文档不适用该条件!)。
- 3、如文档侵犯您的权益,请联系客服反馈,我们会尽快为您处理(人工客服工作时间:9:00-18:30)。
现今我国的铜产量位居全世界第一,据统计估 算,1949 ~ 2010 年我国产出的冶炼铜渣达到 5000
万 t 左右。随着各铜冶炼企业的产能提高,冶炼铜 渣量不断增多,铜渣的有效综合利用显得十分重要。 目前我国铜渣处理仅用于建筑材料,造成了资源浪 费[1 - 3],因为铜 渣 中 存 在 大 量 的 有 价 金 属,如 Cu、 Fe、Au、Ag、Ni 等,其中铜品位在 0. 5% ~ 8% ,铁的 品位在 40% 左右,而我国开采铜矿石品位大部分都 在 1% 以下,铁矿的平均品位只有 29. 3% ,可见铜渣 中有 价 元 素 有 巨 大 的 开 发 潜 力[4]。 作 者 采 用 浮 选 - 磁选流程,对从冶炼铜渣中回收铜和铁的工艺 流程和药剂制度进行了研究。
铜冶炼造锍过程中,冰铜中要有适当的硅酸盐 成分,此时冶炼吹入的空气速度要稳定,使得炉内铁 先被氧化成 FeO ( Fe2 + ) ,FeO 与 SiO2 形 成 铁 橄 榄 石,其反应式如下:
2FeO + SiO2 = Fe2[SiO4 ]( 铁橄榄石) FeO 将进一步被氧化成为 Fe2 O3 ,FeO 与 Fe2 O3 将按一定比例结晶析出形成磁铁矿 ( Fe3 O4 ) , [5 - 6] 它是铁回收的主要矿物,而在造渣过程中,如果磁铁 矿含量过高将导致熔体粘度增大,从而使得铜锍与 炉渣分离困难,导致炉渣中铜的机械夹杂严重,并且 部分铜将呈细微颗粒被其他矿物包裹,被包裹的铜
ISSN 1005 - 2763 CN 43 - 1215 / TD
矿业研究与开发 第 32 卷 第 4 期 MINING R & D,Vol. 32,No. 4
2012 年 8 月 Aug. 2012
*
从冶炼铜渣回收铜铁的试验研究
匡敬忠,曾军龙,肖坤明
( 江西理工大学 资源与环境工程学院, 江西 赣州市 341000)
摘 要: 介绍了铜渣中铜和铁的赋存状态,分析了影响铜渣
中铜、铁回收的主要因素。对某铜业公司冶炼炉渣采用浮选
与磁选综合回收铜、铁的工艺流程进行了试验,并取得了较
好的指标。在磨矿细度为 - 0. 037 mm 占 95. 27% ,通过一粗
二扫 再 精 选 闭 路 流 程,获 得 了 铜 品 位 46. 36% 、回 收 率
KUANG Jingzhong,ZENG Junlong,XIAO Kunming ( School of Resources and Environmental Engineering,
Jiangxi University of Science and Technology, Ganzhou,Jiangxi 341000,China)
表 1 混合渣试样多元素分析结果 w /%
Fe 42. 58 SiO2 18. 3
Cu 2. 25 MgO 0. 119
Zn 1. 41 Al2 O3 0. 928
As 0. 126 CaO 1. 32
Pb 0. 512
Mo 0. 178
S 0. 498
Mn 0. 031
3 试验流程及条件
3. 1 试验流程 考虑到铜渣质地致密、硬度高、嵌布粒度细且不
2 铜渣组成及成分
2. 1 铜渣的来源 试样来自国内某大型铜业公司,试验用的铜渣
样品由电炉渣和铸渣机炉渣两部分混合而成,电炉 渣是直接水淬急速冷却得到的铜渣,难以破碎; 而铸 渣机炉渣是缓冷得到的铜渣,保温时间长,有利于铜 相和铁相迁移、聚集、长大、结晶,硅的含量更低。 2. 2 铜渣的化学和矿物组成
83. 63% 的铜精矿; 通过二段磨矿加入分散剂,获得了铁品位
51. 81% 、回收率为 30. 88% 的铁精矿。
关键词: 冶炼铜渣; 铜矿物; 铁矿物; 浮选; 磁选
中图分类号: TD952
文献标识码: A
文章编号: 1005 - 2763( 2012) 04 - 0054 - 04
Experimental Study on the Copper and Iron Recovery from Smelting Copper Slag
Cu 回收率 /%
68. 54 81. 37 73. 86 56. 1 78. 76
3. 3 磨矿细度试验 由于铜渣 难 磨、嵌 布 粒 度 细、莫 氏 硬 度 高 的 原
因,磨矿细度对铜、铁回收指标的影响非常明显。在 自然 pH 值、捕收剂丁基黄药 180 g / t、分 散 剂 600 g / t的条件下,进行了磨矿细度对铜品位和回收率影 响的对比试验,结果见图 2。从图 2 可以看出,随着 磨矿细度的增加,粗选铜的品位逐渐减少,而回收率 逐渐增大; 但是,当磨矿细度 - 0. 037mm 占 97. 21% 时,铜的回收率反而降低,认为可能是炉渣性质使得 矿物在磨矿过程中产生次生细泥而影响铜矿的品位 和回收率。所 以 磨 矿 细 度 确 定 为 - 0. 037 mm 占 95. 27% ,在 此 条 件 下,可 以 获 得 铜 的 品 位 为 13. 05% 、回收率为 81. 37% 的铜精矿。
对于浮铜捕收剂,进行了乙基黄药、丁基黄药、 酯 - 105、LP - 01、Z - 200 的对比试验,铜粗选试验 流程如 图 1 所 示。在 磨 矿 细 度 为 - 0. 037 mm 占 95. 27% ,分散剂用量为 600 g / t,流程为一粗二扫, 上述 5 种捕收剂的对比试验结果见表 2。试验结果 表明,综合考虑铜品位和回收率,铜粗选捕收剂采用 丁黄更合适。
均匀及有塑性的特性,采用一段磨矿浮选铜,浮铜尾 矿磁选铁,得到的粗铁精矿二段再磨磁选得铁精矿。 磨矿流程对比试验发现二段磨矿回收铁的效果更 好。考虑到嵌布粒度细及夹杂严重,试验考察了一 段磨矿加入分散剂与不加分散剂对选铜及选铁的影 响,发现加入分散剂对提高浮铜的效果不明显,而对 提高铁品位效果较好。通过分散剂的用量实验发 现,无论在一段磨矿还是二段磨矿时加入分散剂,对 铁 的 品 位 提 高 较 明 显,一 段 磨 矿 磁 选 铁 的 品 位 47. 58% ,回收率为 34. 45% ,二段磨矿加分散剂得 到铁的品位为 51. 81% ,回收率为 30. 88% 。所以试 验流程确定采用一段磨矿浮铜,浮铜尾矿得铁粗精 矿再磨磁选铁流程。 3. 2 捕收剂对比试验
Abstract: The occurrence states of copper and iron in smelting copper slag are explained,the effect factors of copper and iron recovery from smelting copper slag are analyzed. Experiment was made on a technological process of flotation and magnetic separation to comprehensively recover copper and iron in the smelting slag from a copper company,and good separation indexes were achieved. By a closed circuit consisting of one roughing,two scavenging and re - concentration,at the grinding fineness of - 0. 037 mm fractions taking up 95. 27% ,a copper concentrate grading 46. 36% at a recovery 83. 63% was obtained. An iron concentrate grading 51. 81% at a recovery of 30. 88% was obtained by means of regrinding and adding dispersant. Key Words: Smelting copper slag,Copper minerals,Iron mineral,Flotation,Magnetic separation
1 高效回收铜渣中铜、铁的影响因素分析
铜渣是高温火法冶炼铜的副产物,主要包含冰 铜熔炼渣和粗铜吹炼渣,成分包含硫化铜、氧化铜、 金属铜、磁铁矿、铁橄榄石及玻璃体等非晶质体。铜 的回收对象为 Cu2 S、CuS 及单质 Cu,而 CuO 难以浮 选回收; 目前,大多数采用电炉贫化法和浮选法回收 铜渣中的铜,浮选法因具有成本低、精矿回收率高、 尾矿中铜的品位低等优点而被广泛采用。影响铜的 品位和回收率因素如下。 1. 1 冶炼过程
图 1 铜粗选流程
56
矿业研究与开发
2012,32( 4)
表 2 不同捕收剂粗选铜试验结果
捕收剂
种类 用量 /( g /t)
乙黄
180
丁黄
180
LP - 01
180
酯 - 105
180
Z - 200
180
产率 /%
8. 40 14. 05 10. 36 9. 80 13. 58
Cu 品位 /%
18. 63 13. 03 16. 04 12. 88 13. 05
* 收稿日期: 2011 - 08 - 28 基金项目: 江西省青年科学家培养对象( 井冈之星) 资助项目( 20112BCB23020) . 作者简介: 匡敬忠( 1971 - ) ,男,江西泰和人,博士,教授,主要从事矿物分选理论与工艺研究,Email: kj - zhong@ 126. com。
表 3 捕收剂的用量试验
捕收剂 用量 /( g /t)
丁黄
160
丁黄
180
丁黄
ቤተ መጻሕፍቲ ባይዱ200
丁黄
220
产品 产率 /% 品位 /%