辽河油田稠油地面集输技术现状及攻关方向
202辽河油田公司集输系统工作会议

202辽河油田公司集输系统工作会议202*辽河油田公司集输系统工作会议202*辽河油田公司集输系统工作会议12月16日上午,油田公司集输系统工作会议在高升采油厂会议中心三楼召开。
油田公司采油工艺处处长孙守国、副处长刘勇、谢加才、高升采油厂厂长陈保钢,以及18家二级单位集输系统主管领导、集输大队长联合站站长共计120余人参加会议。
会议由采油工艺处副处长刘勇主持。
会上,金马、冷家、高采以多媒体的形式,分别做了“落实对标管理强化基础工作全面提升联合站管理水平”“冷家油田稠油处理工艺技术改造工程”“推行精细化管理促进集输系统工作上水平”的典型发言报告。
油气集输科科长王宝峰宣读了第十次“优质低耗联合站”检查情况通报。
采油工艺处长孙守国、厂长陈保钢、采油工艺副处长谢加才采油工艺副处长刘对勇为获得集输系统管理先进单位、优质低耗联合站、优质低耗注水站等获奖单位颁奖。
谢家才副处长提出了202*年的工作思路和工作重点。
202*年污水处理系统主的工作重点就是“2321”。
就是两个零排放,三个重点工程、2两项重点科研项目、推广一项技术应用。
两个零排放:今天我们采油工艺处组织编制了辽河油田整个的水调基本方案。
同是也把曙光和特油两个采油厂的污水平衡方案也已经做完。
明年我们的重点工作就是污水尽量减少排放三项重点工程:1、锦采、华油的外排工程2、曙光地区污水达标外排工程3、欢采低渗透注水工程。
两项科研重点项目:就是低碳专项股份公司重大科技专项。
第二项就是含油污泥资源化处理。
就后一个就是推广应用,就是污水回收技术应用,我们已经研究两年在欢采用两台锅炉实验我们通过注气量的对比实验。
并且在欢采实验获得成功而且这项技术还通过了集团公司的验收。
今年已经开始推广已经见到了效果。
刘勇副处长首先对今年集输系统工作做了简要回顾对明年工作提出具体工作要求:着重讲一下这次专项检查的情况,做一下讲评这次专项检查有几方面的突出,一个是今年注水站是普察的第二个就是污水罐是现场抽检这是过去没有的。
浅析我国稠油开发的技术现状及发展趋势

1741 稠油资源开发概况稠油属于非常规石油资源,是石油中相对分子质量最大、组成和结构最为复杂的部分,但没有严格的范畴,在不同的研究领域含义不同,其主要特点是高黏度、高密度,一般含有沥青质等成分。
我国稠油主要分布在准格尔盆地、松辽盆地、渤海湾盆地等,它们大部分分布在盆地斜坡上,以地层型油藏为主,如富拉尔基、曙光、单家寺、井楼等。
由于稠油粘度高、密度高,所以在开采过程中阻力大,驱动效率低,体积扫油效率也低,因此,常规的石油开采方法不适用于稠油的开采,应采取一些特殊的工艺技术[1]。
我国自20世纪60年代开始开采稠油以来,稠油开采技术有了突飞猛进的发展,目前的稠油开采技术大致可分为热采和冷采两大类。
稠油热采的开采原理在于稠油黏度虽高,但对温度极为敏感,随着温度的增加,稠油的黏度也会下降,大大降低原油渗流阻力;而稠油的“冷采”是则是在稠油油藏开发过程中,针对油藏的特性,通过其它不升温的方法,如加入适当的化学试剂、微生物采油等技术方法,达到降黏的目的,全文对目前稠油热采技术及冷采技术做了详细的阐述,并对未来稠油开发技术趋势做了简单概述。
2 稠油开采的技术现状2.1 稠油热采技术的现状2.1.1 蒸汽吞吐采油技术蒸汽吞吐采油是一种相对简单而成熟的注蒸汽开采稠油的技术,向采油井中注入一定量的蒸汽,随后关井,让蒸汽与油藏进行热交换,然后再开井采油,一般分为三个步骤:注蒸汽、焖井、开井生产,此过程可循环往复进行,这一采油技术的主要原理是用蒸汽加热近井地带原油,使之黏度降低,是我国稠油开发最常见的开发方式之一。
2.1.2 蒸汽驱采油技术蒸汽驱采油,就是由注入井连续不断地往油层中注入高干度的蒸汽,不断加热油层,降低地层原油黏度,将原油驱赶到生产井的周围,并被采到地面上来的一种普通稠油开发方式。
目前普通稠油油藏蒸汽驱开发大多数采用面积井网(反九点井网),虽然取得了较好的开发效果,但在实际开发过程中,常规面积井网也暴露出许多共性问题:平面驱替不均匀,存在死油带,难以动用;由于蒸汽超覆作用,上部油层吸汽好,下部油层吸汽差,导致油气储量动用程度低;蒸汽调控不灵活,蒸汽驱波及体积受限,导致采收率的提高幅度也受到限制。
辽河油田稠油地面集输技术
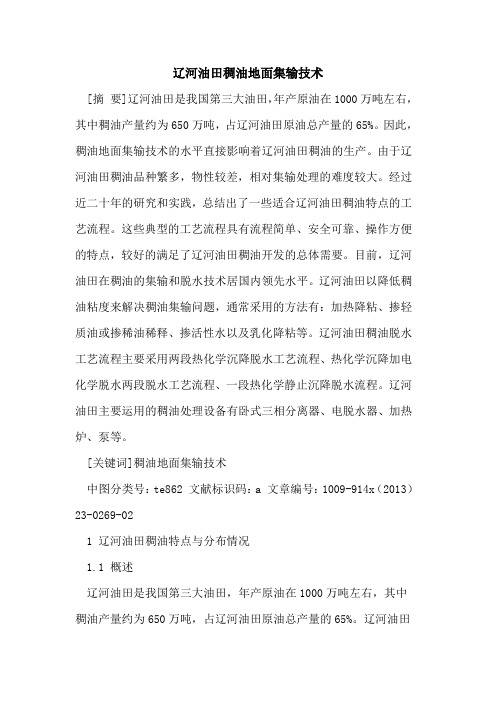
辽河油田稠油地面集输技术[摘要]辽河油田是我国第三大油田,年产原油在1000万吨左右,其中稠油产量约为650万吨,占辽河油田原油总产量的65%。
因此,稠油地面集输技术的水平直接影响着辽河油田稠油的生产。
由于辽河油田稠油品种繁多,物性较差,相对集输处理的难度较大。
经过近二十年的研究和实践,总结出了一些适合辽河油田稠油特点的工艺流程。
这些典型的工艺流程具有流程简单、安全可靠、操作方便的特点,较好的满足了辽河油田稠油开发的总体需要。
目前,辽河油田在稠油的集输和脱水技术居国内领先水平。
辽河油田以降低稠油粘度来解决稠油集输问题,通常采用的方法有:加热降粘、掺轻质油或掺稀油稀释、掺活性水以及乳化降粘等。
辽河油田稠油脱水工艺流程主要采用两段热化学沉降脱水工艺流程、热化学沉降加电化学脱水两段脱水工艺流程、一段热化学静止沉降脱水流程。
辽河油田主要运用的稠油处理设备有卧式三相分离器、电脱水器、加热炉、泵等。
[关键词]稠油地面集输技术中图分类号:te862 文献标识码:a 文章编号:1009-914x(2013)23-0269-021 辽河油田稠油特点与分布情况1.1 概述辽河油田是我国第三大油田,年产原油在1000万吨左右,其中稠油产量约为650万吨,占辽河油田原油总产量的65%。
辽河油田稠油资源主要分布在高升油田、曙光油田、欢喜岭油田、兴隆台油田以及冷家油田等地区。
1.2 稠油分类辽河油田稠油物性差异较大,根据辽河油田目前稠油的生产情况,稠油可分为普通稠油、特稠油和超稠油三类。
1、普通稠油普通稠油粘度大部分在200mpa.s~5000mpa.s之间,这部分稠油约占稠油总产量的70%左右。
2、特稠油特稠油粘度大部分在5000mpa.s~50000mpa.s之间,生产难度较大,这部分稠油约占稠油总产量的15%左右。
3、超稠油超稠油粘度大部分在5×104 mpa.s~20×104mpa.s,这类稠油是近几年才开始规模开采的。
稠油开采技术现状与发展方向采油院.pptx

胜利油田稠油热采产量
探明储量 13.83×108t
已动用 12.63×108t
热采开发3.55×108t 水驱开发9.13×108t
未动用 1.15×108t
特超稠油及薄层稠油油藏
蒸汽吞吐及水驱是稠油油藏的主要开发方式
第2页/共89页
一、前言
胜利油田油藏特点
国内四大主力稠油油田不同深度储量比例对比
Pb/MPa
70 65 60 55 50 45
0
8
6
4
2
界面张力 300
粘弹模量
弹性模量
600
900
时间/(s)
0 粘性模量
-2 1200
模量/(mN/m)
二氧化碳改善热采开发效果机理
✓地层条件下稠油体积膨胀(>15%) ✓降粘作用(>90%) ✓降低油水界面张力
第17页/共89页
表面张力/(mN/m)
波及效率 %
68 80.7 62.6 81.3
驱替效率,%
100.00 80.00 60.00 40.00 20.00 0.00 0.00
2.00
热水驱 热水伴N2驱
4.00 6.00 8.00 10.00
注入体积,PV
热水伴CO2驱 热水伴CO2和薄膜扩展剂驱
二氧化碳同薄膜扩展剂相结 合大幅度提高驱替效率;驱替 效率由30%提高到90%;波及 系数由68%提高到81%,大大 改善热采开发效果。
(1) (2) (3)
普亚超
通 锅 炉
临 界 锅 炉
临 界 锅 炉
(1) (2) (3)
高注全
真 空 隔 热
采 一 体 化 管
密 闭 注 汽 管
国内外稠油开发现状及稠油开发技术发展趋势

Xnag ay fl iC i ad hay rsr i i U id t , ii h v o id n n n t ev o ee os ne S e jn e i e s h a h l e i l v r n t t s a
C n d , V nz e e . h p p r a a a a d eu l t ite e n e a n a . c o e ie p nae r u A p s n, po ut n h o g s sd h ay d v l me t H f& t e tte d ci tcn l i ue fr v ol eo r e h r o e o e d Pr du t 。S GD I su o ut n a d e o ci on A , i C mb si , n t - o n t h P f Se m o dn ,Col u , a f o i t l g e ri tc n l i ae P X T A, ro tl la d w h l St megn eh oo e r V E , I oi n Wel n D noe eam g g s A H H z a , o Ge eao ec T e p lain e h n m n cn i n o al t es n r r . t t h a pct i o m ca i a d o d i s s t o f o h e l f tc n l i h v b e d c se ite p r eh o g s e n u sd h p e. o e a e i s n a T e p r ilfcs te r n d v l m n s ts La h ad na g h p e ma y u o h c r t eo e t u o i e X j n a n o n u e e p t a f o n ii
辽河油田超稠油地面工艺技术的应用与进展
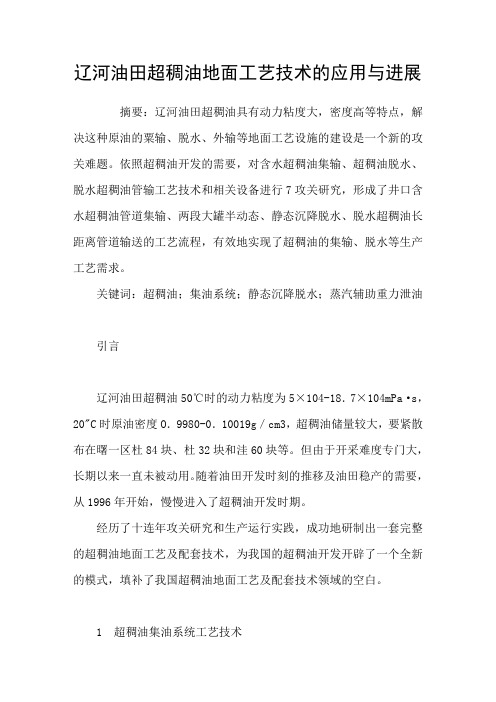
辽河油田超稠油地面工艺技术的应用与进展摘要:辽河油田超稠油具有动力粘度大,密度高等特点,解决这种原油的粟输、脱水、外输等地面工艺设施的建设是一个新的攻关难题。
依照超稠油开发的需要,对含水超稠油集输、超稠油脱水、脱水超稠油管输工艺技术和相关设备进行7攻关研究,形成了井口含水超稠油管道集输、两段大罐半动态、静态沉降脱水、脱水超稠油长距离管道输送的工艺流程,有效地实现了超稠油的集输、脱水等生产工艺需求。
关键词:超稠油;集油系统;静态沉降脱水;蒸汽辅助重力泄油引言辽河油田超稠油50℃时的动力粘度为5×104-18.7×104mPa·s,20"C时原油密度O.9980-0.10019g/cm3,超稠油储量较大,要紧散布在曙一区杜84块、杜32块和洼60块等。
但由于开采难度专门大,长期以来一直未被动用。
随着油田开发时刻的推移及油田稳产的需要,从1996年开始,慢慢进入了超稠油开发时期。
经历了十连年攻关研究和生产运行实践,成功地研制出一套完整的超稠油地面工艺及配套技术,为我国的超稠油开发开辟了一个全新的模式,填补了我国超稠油地面工艺及配套技术领域的空白。
1 超稠油集油系统工艺技术1.1 低含水期集油系统超稠油特点是密度大,粘度高,含胶质、沥青质高,流动性差。
因此,不易输送、脱水。
开采低含水期集油系统采取井口拉油方式,其条件及特点为:产液量小,含水少,管道集输热力、水力条件差,管输温降大、摩阻损失大;适于车运,建设速度快捷。
1.2 高含水期集油系统1.2.1油井平台技术1997年实现了油井平台集油生产工艺,所谓油井平台,是利用丛式井组和水平井组的采油平台。
依照工艺需要,井站集输系统设自压平台、泵平台.中心平台。
自压平台靠井口回压将单井超稠油输送至泵平台或中心平台,泵平台将所辖井和自压平台的超稠油通过提升泵输至中心平台或集输干线。
中心平台所辖井和泵平台的超稠油通过提升泵输至集输干线。
辽河油田典型稠油集输工艺及其优化简化

辽河油田典型稠油集输工艺及其优化简化摘要:辽河油田稠油具有粘度大、密度高、油气比低等特点,在40多年的开发建设过程中,逐渐形成了独具特色的地面集输工艺技术体系,但随着油田开发的深入,开发初期形成的成熟技术与油田生产实际情况不相适应的矛盾日益突出。
本文对辽河油田稠油集输典型流程进行了分析、整理,并提出了如何对现有成熟稠油集输工艺进行优化简化,同时展望了稠油集输工艺技术发展方向。
关键词:稠油粘度集输优化。
1 稠油、超稠油集输工艺1.1 单管加热集输工艺井口来液经加热炉加热后,输往计量站或计量接转站,该工艺集油管线流速通常低于0.5m/s,适用于稠油粘度不大于3000mPa·s(50℃)、单井产液量较高(不小于30t/d)、井口出油温度较高(40℃以上)的稠油集输。
具有流程简单,方便管理,投资少的特点。
1.2 双管掺水集输工艺所谓掺水集输流程即在采油井口加入活性水溶液,达到利用化学药剂降粘、利用水溶液润湿边壁,降阻输送的目的,多用于粘度不大于10000mPa·s的稠油。
回掺水主要利用联合站原油脱出的污水,需建立掺水分输站,掺水比为1.8~2:1(水:油),掺水温度一般在60~65℃。
双管掺水工艺采用集中建站分配水量,减少了掺水泵数量,节约投资和减少耗电量,但掺液量较大,增加集输负荷,油水混合不均,在输送中,当流速较低时,易出现油水分层现象。
1.3 双管掺稀油集输工艺稠油掺稀油是利用两种物性、粘度差别较大,但互溶性好的原油,将其按一定比例互溶在一起,使其具有新的粘度和物性,达到稠油降粘的目的。
稠油掺稀油降粘工艺技术,可以满足任何粘度稠油降粘要求。
应用此工艺需在计量接转站和集中处理站设掺稀油系统,包括稀油的计量、储存、升压、加热、分配等功能。
掺液比为1:0.3~0.7(稠油:稀油),与掺活性水相比,液量减少40%以上,大大减少了集输、脱水、污水处理等工序的负荷,亦相对地减少了设备数量和动力消耗。
从辽河油田高升采油厂看稠油的形成及开采中常见问题1(合集)

从辽河油田高升采油厂看稠油的形成及开采中常见问题1(合集)第一篇:从辽河油田高升采油厂看稠油的形成及开采中常见问题1 从辽河油田高升采油厂看稠油的形成及开采中常见问题作者:孙铭辽河油田公司高升采油厂座落于绕阳河畔的盘山和台安两县交界处。
沈盘公路横穿油区.京沈高速公路、京(秦)沈电气化铁路与厂区擦肩而过。
辖区面积近1000km2,1978年建厂,现有员12551人。
管理着1468口油水井、2座联合站、2座注水站、37座转油站、6座注汽站。
是辽河油田集稀油、稠油和高凝油于一身的多种类油品生产基地。
曾被誉为“出稠油、出经验、出人才”的摇篮。
是中国最早正规开发的稠油油田,自1994年以来已连续15年稳产70×10^4t原油生产规模,创造了辽河油田稠油开发史上稳产时间最长的纪录。
稠油油藏分类稠油油藏的形成主要受地层盆地后期抬升活动细菌生物降解作用,地层水洗和氧化作用,以及烃类轻质分散失等诸因素影响。
而晚期构造运动是主导因素,其他因素是在这一地质背景下的地化过程,按上述因素可将超稠油油藏分为风化削蚀、边缘氧化、次生云移和底水稠度等四种成因。
一、风化削蚀成因超稠油油藏主要分布在后期构造抬升活动强烈发育,盆地具有早期沉陷,后期衰退的特点,早期形成的古油藏抬升而接近地表,或者古油藏盖层封堵条件遭受不同程度破坏,天然气和轻质组分大量溢散,液态烃经受地层水的洗作用成地表风化作用,形成重质油或软沥青。
二、边缘氧化成因超稠油油藏主要分布在盆地和凹陷斜坡边缘,油藏类型以地层型或地层岩性封闭为主,在盆地后期构造运动抬升过程中,盆地边缘急剧上升,边缘斜坡带或为油气大规模运移和聚集的指向,油源主要来自盆地内部重油区,油气沿地层不整合面稳定砂体向上倾方向运移,进入盆地边缘地层水交替带,原油发生严重生物降解程度和物理性质有一个明显的变化规律,下倾部位原油具有原生性,上倾部位原油均发生不同程度生物降解作用,油质变重变稠,甚至在盆地边缘部位形成软沥青,有利于超稠油油藏形成,这类油藏一般规模较大,广泛分布在盆地或凹陷边缘。
辽河稠油火驱开发地面工艺关键技术

0前言
火驱是以空气作为助燃剂,采取电点火或化学点火 等方式,持续燃烧地下原油中的重组分产生热能使重组 分在高温下(600 ~ 700 t)发生裂解,注入的高压空气、 燃烧产生的气体和水蒸气,以及裂解产生的轻质油驱动 原油流向采油井采出,火驱采收率可高达70%。
1辽河油田火驱发展历程
2005年起,辽河油田陆续在杜66块、高3块、锦91 块等区块实施火驱开发m。以辽河油田曙光地区杜66 块火驱为例,2005年首先进行2个井组单层火驱开采现 场试验,2006年增加5个井组进行火驱开采试验,2008 年调整为上层系多层火驱开采现场试验,2010至2012 年外扩20井组,2014年扩大实施火驱,新增114井组,共 进行141井组火驱生产。实际生产表明,对比蒸汽吞吐、 蒸汽驱、热水驱等传统开采方式,杜66块火驱具有较好 增油效果。同时其他火驱区块均实现产量上升,充分证 明火驱开发方式接替的有效性[21。
关键词:火驱;组合增压;系统优化;预脱水;尾气处理;高效溶气浮选 DOI:10. 3969 /j. issn. 1006 -5539. 2019. 04. 005
Key Technology of Fire-Flooding Development of Liaohe Heavy Oil
Lu Hongyuan China Liaoቤተ መጻሕፍቲ ባይዱe Petroleum Engineering Company Ltd, Paxrjin, Liaoning, 124010, China
2火驱地面关键技术
2.1火驱配套注空气技术 2.1.1空气增压技术
往复式压缩机适用于小排量、高压力工况,螺杆机 适用于中低压力、中小排气量工况,为满足现场高压力、 大流量空气注入的需求,创新采用螺杆空压机与往复空 压机组合增压技术,如杜66块火驱注空气站工艺流 程见图1。螺杆压缩机和往复压缩机自动关联启停,结 合杜66块现场运行调试指标,研究最优出口压力配比, 最终确定螺杆压缩机出口压力0. 95 MPa,往复压缩机出 口压力10 MPa,注气量可达到20 x 104 m3 /d,满足空压
稠油目前开采技术与下步技术攻关
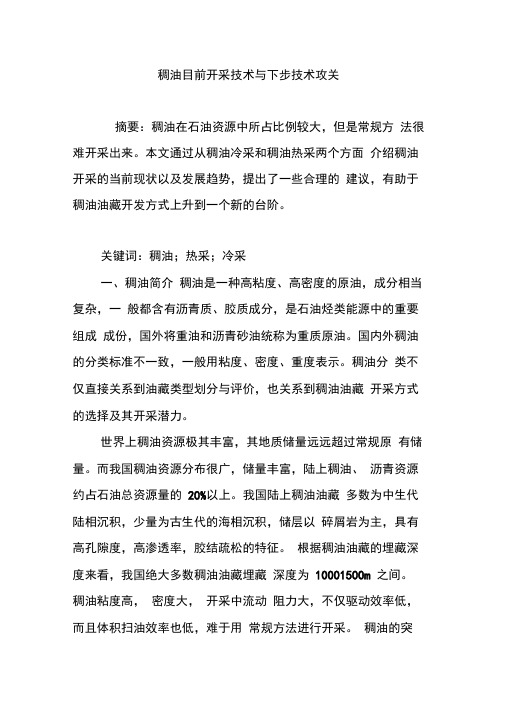
稠油目前开采技术与下步技术攻关摘要:稠油在石油资源中所占比例较大,但是常规方法很难开采出来。
本文通过从稠油冷采和稠油热采两个方面介绍稠油开采的当前现状以及发展趋势,提出了一些合理的建议,有助于稠油油藏开发方式上升到一个新的台阶。
关键词:稠油;热采;冷采一、稠油简介稠油是一种高粘度、高密度的原油,成分相当复杂,一般都含有沥青质、胶质成分,是石油烃类能源中的重要组成成份,国外将重油和沥青砂油统称为重质原油。
国内外稠油的分类标准不一致,一般用粘度、密度、重度表示。
稠油分类不仅直接关系到油藏类型划分与评价,也关系到稠油油藏开采方式的选择及其开采潜力。
世界上稠油资源极其丰富,其地质储量远远超过常规原有储量。
而我国稠油资源分布很广,储量丰富,陆上稠油、沥青资源约占石油总资源量的20%以上。
我国陆上稠油油藏多数为中生代陆相沉积,少量为古生代的海相沉积,储层以碎屑岩为主,具有高孔隙度,高渗透率,胶结疏松的特征。
根据稠油油藏的埋藏深度来看,我国绝大多数稠油油藏埋藏深度为10001500m 之间。
稠油粘度高,密度大,开采中流动阻力大,不仅驱动效率低,而且体积扫油效率也低,难于用常规方法进行开采。
稠油的突出特点是含沥青质、胶质较高我国胶质、沥青质含量较高的稠油产量约占原油总产量的70%。
因此,稠油开采具有很大的潜力。
对于稠油油藏,常规方法很难开采,采取一些特殊的工艺措施加强稠油开采很有必要。
二、稠油开采技术稠油开采一般可分为热采和冷采两大类。
稠油粘度虽然高,但对温度极为敏感,每增加10 度,粘度下降约一半。
加热过程中,水、轻质油和稠油粘度的变化表明,增加相同的温度,稠油的粘度比水和轻质油降低的多得多。
热力采油作为目前稠油开发的主要手段,能够有效升高油层温度,降低稠油粘度,使稠油易于流动,从而将稠油采出。
稠油“冷采”是相对“热采”而言的,即在稠油油藏开发中,不是通过升温方式来降低油品的粘度,提高油品的流动性能,而是通过其它不涉及升温的方法,利用油藏特性,采取适当的工艺达到降粘开采的目的。
辽河油田超稠油地面集输工艺技术

可 以在 油井平 台上直接 布置 加热和 提升 装置 , 实 现 井 台合 一 , 省 了大量 集输 管线 ,解决 了集输 :
工 艺 中冈井 口回压低 、出井 油温低 、难于 输送 的
难题。
22 油井平 台 .
利 删钻井 平台作 为采油 平 台。主要包 括 自压 平 台、 平 台和 中心 平 台,习惯上 称之 为油井 平 泵
台。
根 据超稠 油 的物 性 、井 口运 行 参数 、单 井产
量 、集 油管线 管径 、集 中处理站 布置位 置不 同,
油井平 台的布置类型也不同, 布置何种类型的油
井平 台 , 还要考 虑平 台至接转 站利 集 中处理站 距 离。
13 超 稠油 的特 点 . 23接转 站 .
42 泵平 台 .
这 种布 局 主 要 应 用 在 油 井 平 台距 集 中处 理
沥青质含量高; ⑨密度高; ④气油比极低 ; ⑤凝
固点较低 ,但粘度 较大 ;⑥ 粘温敏 感性 强 :⑦ 呈
含水油特性;⑧与轻质油、稀原油互溶性好。
多年 的生产 实践 , 累 了一 套适合超 稠油采 、 、 积 集 输 的生产 经验 。 为稠 油中一 种特殊 品种 , 河 作 辽
油 田从 1 9 9 7年 开始 , 对杜 8 、 3 4 杜 2区块等 5 ℃ 0
超 稠 油 的特 点如 下 :① 粘度极 人 :② 胶质 、
接转 站 主 要 考 虑 采 油 区 域 内不 设集 中 处理
第 3期
臧秀萍: 辽河油 田超稠油地面集输工艺技术
站 ,需要 输送 至其 它 区域集 中处理 站进 行处理 。 与集 中处 理站 距离 较远 ,平 台输送 管 线摩 阻 较大 , 单独 输送 不 经济 时 , 在采 油 区域 内集 中输
辽河油田难采储量开采技术发展状况及应用

辽河油区难采储量开采技术发展状况及应用王旭贾海燕(辽河石油勘探局工程技术研究院辽宁盘锦 124010)摘要:随着辽河油区勘探开发程度的不断加深,难采、难动用区块的开发已成为油田稳产中不容忽视的问题,实际情况表明,这些难采区块分别存在着高凝、低渗、出砂、海上稠油开采等技术困难,具有低产能、投资高、风险大的特点。
经过多年的持续技术攻关和实践,辽河油区目前已经陆续开发了侧钻井、水平井、分支井等特殊工艺井钻完井技术及配套技术,广泛应用于超稠油油藏、低渗透油藏、薄层稠油油藏开发,极大提高了难采储量动用程度,降低吨油生产成本,取得良好的效果。
此外,在油井增油技术方面也取得突破,防砂、高温调剖、找堵水、气体采油技术等都进一步完善和应用。
本文重点介绍了特殊工艺井技术和油井增油技术在难采油藏开发中的发展状况及应用,希望对其它油区类似油藏的开发起到借鉴作用。
关键词:辽河油区;难采储量;特殊工艺井;油井增产技术;应用中图分类号:TE353 文献标识码:ADevelopments and Applications of Oil Production Technology for Difficult-to-ProduceReserve in Liaohe OilfieldWang Xu, Jia Haiyan(Engineering Technical Research Institute of Liaohe Petroleum Exploration Bureau, Liaoning , Panjin, 124010, China)Abstract: The development of Liaohe oilfield has come into mid-late period, troubles of sustainning production appear gradually obvious. For this reason,the studies concerning the effective and economic oil production technology for difficult-to-produce reserve are gradual emphasized. As compared with the conventional reserve, difficult-to-produce reserve has high pour-point, low permeability, sand inflow, offshore heavy oil, etc, so its production always leads to low yield, high cost, high risk. In resent years, complicated structural wells, including side-tracking wells, horizontal wells, branched wells, etc., have been studied and developed in Liaohe oilfield. Through the application of these complicated structural wells in super heavy oil reservoir, low permeability reservoir, thin heavy reservoir, a very good result was obtained, improving oil recovery effectively, reducing running cost per ton. In addition, some stimulation treatment technologies have also been developed and adopted, such as sand control, high temperature injection profile modification, water finding and block off, oil production by using gases. In this paper, the developments and applications of the complicated structural wells and the stimulation treatment technologies for difficult-to-produce reserve are presented, and these research results will have some effects on the production of other similar difficult-to-produce reserve.Keywords: Liaohe oilfield; difficult-to-produce reserve; complicated structural wells; stimulation treatment technologies;application 引言辽河油区油气勘探开发的区域包括辽河盆地陆上、辽河滩海和外围盆地三部分,是一个地质条件十分复杂的复式油气区,勘探开发进入中后期以来,后备资源日渐匮乏,难采储量开发成为当务之急。
油气田地面工程面临的形势及攻关方向
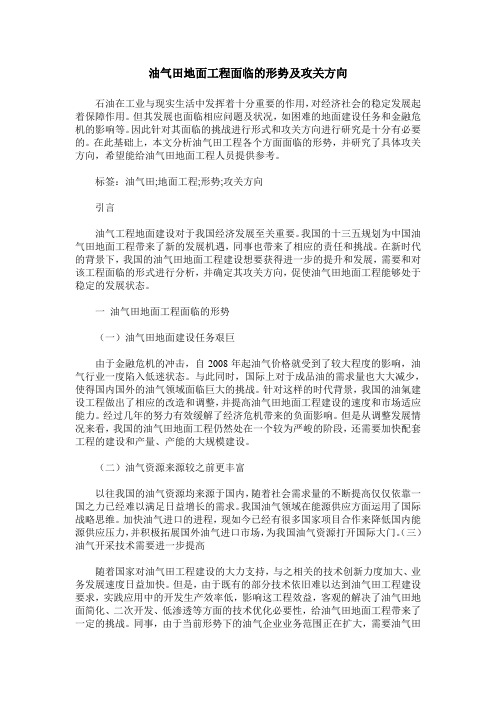
油气田地面工程面临的形势及攻关方向石油在工业与现实生活中发挥着十分重要的作用,对经济社会的稳定发展起着保障作用。
但其发展也面临相应问题及状况,如困难的地面建设任务和金融危机的影响等。
因此针对其面临的挑战进行形式和攻关方向进行研究是十分有必要的。
在此基础上,本文分析油气田工程各个方面面临的形势,并研究了具体攻关方向,希望能给油气田地面工程人员提供参考。
标签:油气田;地面工程;形势;攻关方向引言油气工程地面建设对于我国经济发展至关重要。
我国的十三五规划为中国油气田地面工程带来了新的发展机遇,同事也带来了相应的责任和挑战。
在新时代的背景下,我国的油气田地面工程建设想要获得进一步的提升和发展,需要和对该工程面临的形式进行分析,并确定其攻关方向,促使油气田地面工程能够处于稳定的发展状态。
一油气田地面工程面临的形势(一)油气田地面建设任务艰巨由于金融危机的冲击,自2008年起油气价格就受到了较大程度的影响,油气行业一度陷入低迷状态。
与此同时,国际上对于成品油的需求量也大大减少,使得国内国外的油气领域面临巨大的挑战。
针对这样的时代背景,我国的油氣建设工程做出了相应的改造和调整,并提高油气田地面工程建设的速度和市场适应能力。
经过几年的努力有效缓解了经济危机带来的负面影响。
但是从调整发展情况来看,我国的油气田地面工程仍然处在一个较为严峻的阶段,还需要加快配套工程的建设和产量、产能的大规模建设。
(二)油气资源来源较之前更丰富以往我国的油气资源均来源于国内,随着社会需求量的不断提高仅仅依靠一国之力已经难以满足日益增长的需求。
我国油气领域在能源供应方面运用了国际战略思维。
加快油气进口的进程,现如今已经有很多国家项目合作来降低国内能源供应压力,并积极拓展国外油气进口市场,为我国油气资源打开国际大门。
(三)油气开采技术需要进一步提高随着国家对油气田工程建设的大力支持,与之相关的技术创新力度加大、业务发展速度日益加快。
但是,由于既有的部分技术依旧难以达到油气田工程建设要求,实践应用中的开发生产效率低,影响这工程效益,客观的解决了油气田地面简化、二次开发、低渗透等方面的技术优化必要性,给油气田地面工程带来了一定的挑战。
稠油开采现状与相关技术研究

国石 油总 产量 的 1 / 1 0 。各 大稠 油开采 油 田针 对 其 自身特 点 , 通过 引进 、 消化 、 吸收 和技 术创 新 , 形成 了各 具特 色的开采 技 术 ,
取 得 新的进 展 和 突破 。 关键词 : 稠油; 开采 ; 热采技 术 中图分 类 号 : T E 3 7
的影 响 , 递 减较 快 外 , 二、 三周 期均 缓 慢递 减, 直至周期结束 。 二是第 四周期 以后 , 日 产 油上升 阶段逐渐 变缓 ,产量 高峰值 逐渐 降 低、 滞后 , 甚 至峰值产量 消失 , 缓慢进入递减 期。 这 两种开发模式 , 生产 6 0 d以后 , 单井周 期内产量变化规律驱 于一致 。 2 - 3采注 比、 回采水率 、 油汽 比变化趋势 蒸汽吞吐是一个降压开采 的过程 , 采出 液量 大于注入 蒸汽 量才能保 证下 一轮 注汽 质量 。采注 比的大小 与注汽干度 密切相关 , 同时 中周期 以后采 注 比下 降快 也反 映地 层 能量 降低过 快 , 周期 递减 过大 , 因此采 注与 周期吞 吐效果有 直接影响 , 控制合 理的采注 比对于稳定区块产量起到重要作 用。 超稠油 的这种变化规律 与其特殊 的原 油性质 、 储层 条件 、 举 升工艺有着直 接关系。 3稠油开采现状 我 国上世纪 8 0 年代就着 眼对 稠油 的研 究 和开发 , 按稠 油油藏 的特点 , 其开采 方式 也各 有所 异 ,但 总是沿 着降黏 和使分 子变 小、 变轻的方向发展努力着。目前 , 提 高采 收 率最成 功的开采方法分两 大类 : 一是注入 流 体热采 或驱替型方法 , 如热水驱 、 蒸气吞 吐 、 蒸气 驱 、 火 驱等 ; 另一类是 增产型开采方 式 , 包 括水 平 井 、 复合 分支 井 、 水力 压 裂 、 电加 热、 化学 降黏等 , 这两类技 术的结合使用 , 已 成为当今稠油开发 的主要手段 。其 中 , 胜 利 油 田采用 热采 、 注 蒸气 、 电加 温 、 化学 降 黏 ( 注 聚合 物驱 ) 等技术 ; 辽河 油 田的 中深层 热 采稠油技 术 ;大港油 田的化 学辅助 吞吐 技 术; 新疆 油 田的浅层 稠油 面积驱技 术 ; 河 南 油 田的稠油热采技术 等 , 均处于 国内领先水 平。尤其是河南油 田 原 油 的黏度特 高( 普 通 稠油为 1 0 0 0 0 M p a . s ,特 稠 油 为 1 0 0 0 0 — 5 0 0 0 0 M p a . s , 超稠 油为 5 0 0 0 0 M p a . s 以上 ) , 热 采需要的参数很大 , 需要 注气 压力 7 s . Mp a , 注气速度为 l O 0  ̄ d , 蒸气 干度为 7 5 %, 蒸气温 度为 2 9 0  ̄ C , 油层 深度 为 3 0 0 m , 放 喷时地 层 温度为 1 4 0  ̄ C , 压力 为 5 s . M p a , 优选好合理参 数, 是有效开发稠 油的关键 。人们 为了节能 降耗 , 特研制成功一 种将饱和 的尿 素溶液注 入被蒸气加热 的地层 ,使尿素 在高温下 , 分 解成 氨和 C O 对地 层进行 注蒸气 、 碱和 C O 驱 的综合处理方 法 , 已在俄罗斯 的部分稠油 油 藏试验 结果表 明 , 该方 法是 高效 的 , 有广 泛 的适用性和 良好 的发展前景 。 4稠油 开采技术 问题 我 国 目前高 度重视 稠油 开采 中的有关
油田集输工艺存在的问题与解决对策

油田集输工艺存在的问题与解决对策摘要:在石油开采过程中,油气集输承担的任务主要是初步加工、采集、运输以及存储开采出的天然气以及原油。
现有的集输工艺能够实现原油和天然气的分开处理,将检验合格的原油送到油库进行储存,而天然气则被输送至天然气处理厂进行深加工。
其实在这个过程中本身存在着一定的危险性,因此其安全生产的问题也就成为了社会关注的焦点。
关键词:油田;集输工艺;问题与对策油田集输工艺的发展艰巨而长远,但该技术的主旨是既定的,即根据油田环境和实际情况的不同,选择最为合适的先进集输技术,并以此为基础进行优化和完善,才能真正使得油田生产获得最大的经济效益。
国的油田集输工艺很不够完善,还存在着一部分问题,但是可以通过后期的不断完善,可以让石油更加充分的开采和利用。
一、油气集输工艺的流程我国在油气技术方面的工艺流程主要有以下几个方面:计量产物、油和气体的分离,接转技术、原油的脱水和存储技术等等。
该工艺流程十分复杂,它是可以将石油的处理、运输等过程综合在一起的完整的工艺系统。
对油田产物进行计量,主要是通过操作专业的计量分离器来进行。
通过这一方式,可以将其分成三相和两相这两大类。
分离后,再通过流量仪表,将两相、三相的产物分别进行计量。
然后接下来是根据油气水这三种产物特性的不同,通过重力或者是离心的技术将三者分离开来,这一步主要是在油气分离器中进行的。
接下来的接转工作,其目的是为了给油气施加动力。
由于油气之间分离后,自身的动力无法维持油气的运输,因此需要进行增压。
对于油气需要分别进行增压工作,其中对于油主要是用油泵,而气体可以利用压缩机进行。
后面原油的脱水工作,根据原油不同的物理和化学性质,通过电化学法等技术将游离水、乳化水从原油中脱离。
而后续的原油稳定和油田气的处理工作,是为了保证原油可以更加顺利地运输和储存的后续收尾工作。
油井产物的计量是通过计量分离器把油井的产物分成两相和三相的两类。
两相的产物是气体和液体,三相的产物是气体、游离水和乳化油。
辽河油田稠油开发技术介绍

全国稠油总储量20.6亿吨
全国稠油年产量1510万吨
10.8亿吨
746万吨
其它油田
辽河油田
全国稠油储量分布图
其它油田
辽河油田
全国稠油产量分布图
2. 稠油油藏地质特点
(1)构造复杂、断块多
发育三级断层100多条,四级断层300余条、四级断块450多个。
辽河盆地西部凹陷稠油分布图
下,埋藏深度从600m到2300m。
463
685
677
680
26 1 2 2 150 1 6 9
555 485
超稠油 开发
737
703
682
60
177
215 155
137
489 424
117 350
方式 转换
热采稠油合计
661 260 114 287
647 657
564
281 286
506
239
超稠油
206
100 97
265 277
6 3 特稠油
中深层:500-900 (m)
深层:900-1300 (m)
特、超深层:1300-2600 (m)
储量
24%
比例
35%
41%
储量 比例
储量 比例
(3)油藏类型多,油水关系复杂
根据油水关系划分,主要有六种油藏类型。
纯油藏(曙一区杜家台油层)
块状底水油藏(冷41块沙三段)
块状气顶油气藏(高2、3区莲花油层)
以上隔热技术难以满足中深层稠油蒸汽驱和SAGD高干度的需要。
隔热系数 0.07w/m.oC
光光油油管管条条件 件下下
蒸汽干度随深度变化曲线
当前稠油采油新技术的应用研究与分析

当前稠油采油新技术的应用研究与分析摘要:本文主要针对当今油田采油新技术的应用,在油田不同开发阶段,不断加强科研攻关与技术配套提高采收效果。
辽河油田经过40多年的开发建设,大部分油藏区块都已进入开发中后期,由于油区的层间、层内的非均质性较为突出,注水死角在纵向和横向的面上都存在,采油技术的创新需求不断提高。
特别是对高渗水驱油藏集成配套新技术、稠油油藏开采新技术、掺稀降粘采油技术、烧油层驱油技术、潜山油藏开采新技术等创新技术领域取得的新进展进行分析和研究,以便在实际工作中加以推广,提高采收率及效果。
采油工程技术系统是油田开发链条中的重要环节之一。
关键词:油田采油新技术应用分析一、关于稠油油藏的开采技术分析当前,辽河油田还开展火烧驱油配套技术研究和试验,以物理模拟、烧驱油方案设计、火烧驱油点火、注气动态实时监控、产井动态监测、全注气和生产等为主体内容的系列技术得到成功应用,取得了初步效果。
在高升区块进行的部分油井进行系列火驱试验。
火驱井组位于区块内采出程度最高、压力水平最低的区块中部。
目前有火驱点火井8口,开井8口;火驱一线井组共有油井30口,开井27口;二线井组共有油井14口,开井10口。
日产液由驱前的64.1吨上升至115.3吨,日产油由驱前的23.9吨上升至40.3吨。
目前整个井组的火驱效果较为明显。
通过系统研究高温多效泡沫驱的机理、油藏适应性、采收参数等的系统研究,在热力采油数学模型的基础上建立了多相态、多组分高温多效泡沫驱油数学模型,可为现场实施方案的优化提供技术支持。
所以说,经过多年蒸汽吞吐,辽河油田的主力老区块的周期产油量在后期均出现下降,油井的汽比降低、合含水不断上升、采用蒸汽注入吞吐时,吞吐的效果已经不能和开始初期相比,从而在一定程度上,会导致开发难度不断增大的难题,.在这种情况下,有关技术人员对多效泡沫辅助热采技术研究开展试验和研究是非常有战略意义的选择。
二、高渗水油藏的驱油技术高渗水油藏的驱油技术是根据地质的特殊情况,按照不同的油藏的性质、地域分布等综合情况,将油田划分为不同的油藏类别,分别包含整装构造类油藏、高渗透断块油藏、低渗透油藏、殊岩性油藏、稠油断块油藏等。
辽河油田地面工程技术进展及发展方向
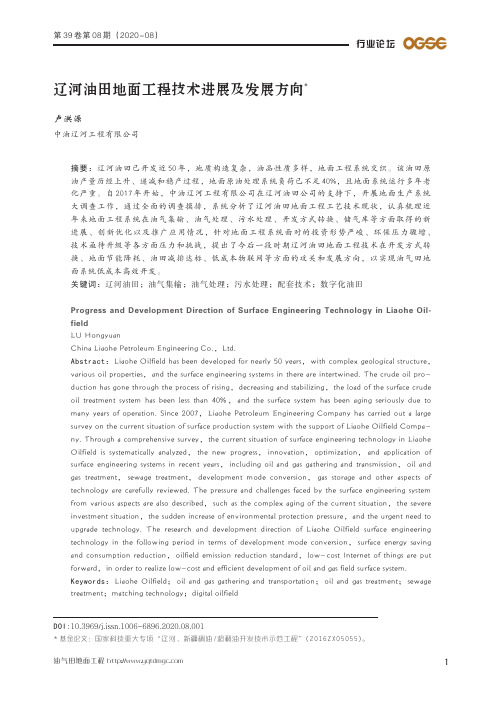
辽河油田地面工程技术进展及发展方向*卢洪源中油辽河工程有限公司摘要:辽河油田已开发近50年,地质构造复杂,油品性质多样,地面工程系统交织。
该油田原油产量历经上升、递减和稳产过程,地面原油处理系统负荷已不足40%,且地面系统运行多年老化严重。
自2017年开始,中油辽河工程有限公司在辽河油田公司的支持下,开展地面生产系统大调查工作,通过全面的调查摸排,系统分析了辽河油田地面工程工艺技术现状,认真梳理近年来地面工程系统在油气集输、油气处理、污水处理、开发方式转换、储气库等方面取得的新进展、创新优化以及推广应用情况,针对地面工程系统面对的投资形势严峻、环保压力骤增、技术亟待升级等各方面压力和挑战,提出了今后一段时期辽河油田地面工程技术在开发方式转换、地面节能降耗、油田减排达标、低成本物联网等方面的攻关和发展方向,以实现油气田地面系统低成本高效开发。
关键词:辽河油田;油气集输;油气处理;污水处理;配套技术;数字化油田Progress and Development Direction of Surface Engineering Technology in Liaohe Oil⁃fieldLU HongyuanChina Liaohe Petroleum Engineering Co.,Ltd.Abstract:Liaohe Oilfield has been developed for nearly50years,with complex geological structure,various oil properties,and the surface engineering systems in there are intertwined.The crude oil pro-duction has gone through the process of rising,decreasing and stabilizing,the load of the surface crude oil treatment system has been less than40%,and the surface system has been aging seriously due to many years of operation.Since2007,Liaohe Petroleum Engineering Company has carried out a large survey on the current situation of surface production system with the support of Liaohe Oilfield Compa-ny.Through a comprehensive survey,the current situation of surface engineering technology in Liaohe Oilfield is systematically analyzed,the new progress,innovation,optimization,and application of surface engineering systems in recent years,including oil and gas gathering and transmission,oil and gas treatment,sewage treatment,development mode conversion,gas storage and other aspects of technology are carefully reviewed.The pressure and challenges faced by the surface engineering system from various aspects are also described,such as the complex aging of the current situation,the severe investment situation,the sudden increase of environmental protection pressure,and the urgent need to upgrade technology.The research and development direction of Liaohe Oilfield surface engineering technology in the following period in terms of development mode conversion,surface energy saving and consumption reduction,oilfield emission reduction standard,low-cost Internet of things are put forward,in order to realize low-cost and efficient development of oil and gas field surface system.Keywords:Liaohe Oilfield;oil and gas gathering and transportation;oil and gas treatment;sewage treatment;matching technology;digital oilfieldDOI:10.3969/j.issn.1006-6896.2020.08.001*基金论文:国家科技重大专项“辽河、新疆稠油/超稠油开发技术示范工程”(2016ZX05055)。
辽河油田某稠油产区地质开发经验浅谈
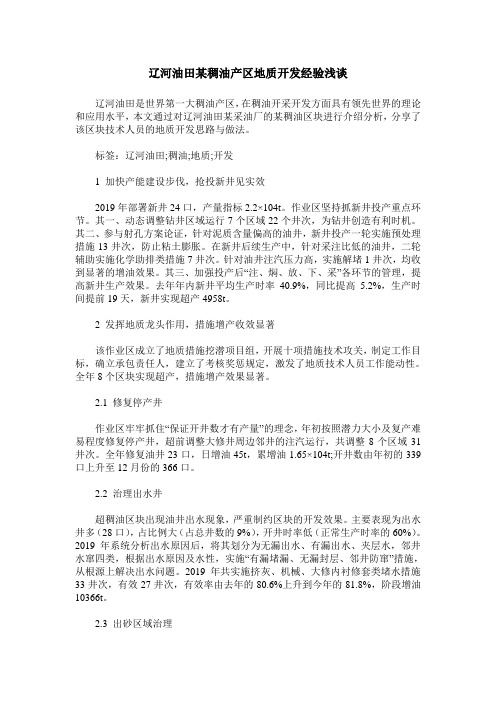
辽河油田某稠油产区地质开发经验浅谈辽河油田是世界第一大稠油产区,在稠油开采开发方面具有领先世界的理论和应用水平,本文通过对辽河油田某采油厂的某稠油区块进行介绍分析,分享了该区块技术人员的地质开发思路与做法。
标签:辽河油田;稠油;地质;开发1 加快产能建设步伐,抢投新井见实效2019年部署新井24口,产量指标2.2×104t。
作业区坚持抓新井投产重点环节。
其一、动态调整钻井区域运行7个区域22个井次,为钻井创造有利时机。
其二、参与射孔方案论证,针对泥质含量偏高的油井,新井投产一轮实施预处理措施13井次,防止粘土膨胀。
在新井后续生产中,针对采注比低的油井,二轮辅助实施化学助排类措施7井次。
针对油井注汽压力高,实施解堵1井次,均收到显著的增油效果。
其三、加强投产后“注、焖、放、下、采”各环节的管理,提高新井生产效果。
去年年内新井平均生产时率40.9%,同比提高5.2%,生产时间提前19天,新井实现超产4958t。
2 发挥地质龙头作用,措施增产收效显著该作业区成立了地质措施挖潜项目组,开展十项措施技术攻关,制定工作目标,确立承包责任人,建立了考核奖惩规定,激发了地质技术人员工作能动性。
全年8个区块实现超产,措施增产效果显著。
2.1 修复停产井作业区牢牢抓住“保证开井数才有产量”的理念,年初按照潜力大小及复产难易程度修复停产井,超前调整大修井周边邻井的注汽运行,共调整8个区域31井次。
全年修复油井23口,日增油45t,累增油1.65×104t;开井数由年初的339口上升至12月份的366口。
2.2 治理出水井超稠油区块出现油井出水现象,严重制约区块的开发效果。
主要表现为出水井多(28口),占比例大(占总井数的9%),开井时率低(正常生产时率的60%)。
2019年系统分析出水原因后,将其划分为无漏出水、有漏出水、夹层水,邻井水窜四类,根据出水原因及水性,实施“有漏堵漏、无漏封层、邻井防窜”措施,从根源上解决出水问题。
国内外稠油开发现状及稠油开发技术发展趋势

国内外稠油开发现状及稠油开发技术发展趋势随着全球经济的日益发展,世界对石油的需求量迅猛增长,经过上个世纪对常规油资源的大规模的开发后,稠油资源以其丰富的储量吸引了世人的注意。
本文概述了各种稠油开采技术的特点、机理、和适用条件。
标签:稠油油藏;稠油开发技术;热力采油;热力化学采油;微生物采油辽河和新疆油田,其生产开发受到技术的制约,尚未找到适合的吞吐后接替技术,使目前蒸汽吞吐后期产量递减很快的生产矛盾日益突出,这两个油田的稠油未动用储量总共约有4亿t,其中超稠油未动用储量占了一半以上,约有2.2亿t。
1 概述1.1 研究的意义稠油在世界油气资源中占有较大的比例。
稠油资源丰富的国家有加拿大、委内瑞拉、美国、前苏联、中国、印度尼西亚等。
中国重油沥青资源分布广泛,已在12个盆地发现了70多个重质油田,预计中国重油沥青资源量可达300×108t 以上。
1.2 稠油的定义及分布我国陆上稠油资源约占石油总资源量的20%以上,目前在12个盆地发现了70多个稠油油田,探明与控制储量约为40亿t。
我国陆上稠油油藏多为中新生代陆相沉积,少量为古生代海相沉积。
储层具有高孔隙、高渗透、胶结疏松的特征。
1.3 稠油开发技术常规稠油开采技术的发展。
常规的热力采油技术将会被热力化学采油技术取代。
热力化学采油技术会有很大的发展,其中的水裂解技术会有更大的发展。
微生物采油技术发展,分子生物技术,示踪剂技术,可视化技术等。
2 稠油开发技术热力采油主要是通过一些工艺措施使油层温度升高,降低稠油粘度,使稠油易于流动,从而将稠油采出。
其主要方法有蒸汽吞吐、蒸汽驱等。
蒸汽吞吐通常只能采出井点周围油层中有限区域内的原油,井间存在大量蒸汽难以波及到的死油区,蒸汽吞吐的原油采收率一般由于蒸汽吞吐以消耗弹性能量降压开采为驱动条件,基于单井操作,油层的受热范围受到限制,井间储量动用程度差,采出程度低;国内外蒸汽吞吐开采实践表明,蒸汽吞吐的采收率一般为20%左右,因此单纯依靠蒸汽吞吐增加最终采收率的程度是有限的。
- 1、下载文档前请自行甄别文档内容的完整性,平台不提供额外的编辑、内容补充、找答案等附加服务。
- 2、"仅部分预览"的文档,不可在线预览部分如存在完整性等问题,可反馈申请退款(可完整预览的文档不适用该条件!)。
- 3、如文档侵犯您的权益,请联系客服反馈,我们会尽快为您处理(人工客服工作时间:9:00-18:30)。
辽河油田稠油地面集输技术现状及攻关方向 齐建华* 张春光 辽宁辽河石油工程有限公司 齐建华等. 辽河油田稠油地面集输技术现状及攻关方向. 石油规划设计,2002,13(6):54~57 摘 要 由于辽河油田稠油品种繁多,物性较差,相对集输处理的难度较大。
辽河油田以降低稠油粘度来解决稠油集输问题,通常采用的方法有:加热降粘、掺轻质油或掺稀油稀释、掺活性水以及乳化降粘等。
稠油脱水工艺流程主要采用两段热化学沉降脱水工艺流程;热化学沉降加电化学脱水两段脱水工艺流程;一段热化学静止沉降脱水流程。
主要运用的稠油处理设备有卧式三相分离器、电脱水器、加热炉、泵等。
主题词 稠油 物理性质 集输 加热 脱水 降粘 工艺流程 设备 稠油分类 辽河油田是我国第三大油田,年产原油约1 400万t,其中稠油产量约为900万t,占辽河油田原油总产量的65%。
辽河油田稠油资源主要分布在高升油田、曙光油田、欢喜岭油田、兴隆台油田以及冷家油田等地区。
辽河油田稠油物性差异较大,根据辽河油田目前稠油的生产情况,稠油可分为普通稠油、特稠油和超稠油3类。
1 普通稠油 普通稠油粘度大部分在200~5 000 mPa・s之间,这部分稠油约占稠油总产量的70%。
2 特稠油 特稠油粘度大部分在5 000~50 000 mPa・s之间,生产难度较大,这部分稠油约占稠油总产量的15%。
3 超稠油 超稠油粘度大部分在5×104~20×104 mPa・s,这类稠油是近几年才开始规模开采的。
这部分稠油约占稠油总产量的15%。
辽河油田超稠油的储量较大,埋深较浅,约在700~800 m之间。
表1 辽河油田稠油的一般性质 项 目 20℃的密度(g/cm3) 粘度50℃(mPa・s) 凝点(℃) 含蜡量(%) 沥青质+胶质(%) 杜32块 1.0019 58191~168700 30 4.07 41.99 冷家油田 0.979 10538~54800 18 9.8 11.2 小洼油田 0.950~1.019 813~6853 3~24 1.5~4 27~40 目前,辽河油田已建成的稠油集中处理站有特油公司杜84块1#集中处理站、特油公司杜32块2#集中处理站、冷一稠油集中处理站、曙光油田曙五联合站、兴隆台油田海一联合站、兴隆台油田洼一联合站、锦州油田锦一联合站等。
* 齐建华,男,1966生,高级工程师,1988年毕业于石油大学(华东)石油储运专业。
现在辽宁辽河石油工程有限公司从事油气储运专业设计。
通信地址:辽宁省盘锦市辽宁辽河石油工程有限公司,124010 稠油地面集输工艺流程 1 单管加热集输流程 该工艺流程只有一条管线,流程比较简单。
该工艺流程主要适用于单井产液量高(一般大于20 t/d),出油温度高(一般在40℃以上),原油粘度一般不超过3 000 mPa・s,油井回压一般控制在1~1.2 MPa的稠油区。
2 掺稀油降粘集输流程 掺稀油降粘集输流程经过多年的生产实践,现已形成稠油掺稀油的双管密闭集输、多级分离、大罐热化学沉降脱水、掺稀油定量分配等较为完备的稠油集输工艺。
该工艺对于低产、高稠、井深,周边有稀油资源的油田非常适用。
掺稀油的部位可选择在井下、井口、站内,主要维持地面集油管线的水力条件,提高脱水质量。
稠油掺稀油流程的平面布局主要有3种:小二级布站(计量站→集中处理站);大二级布站(计量接转站→集中处理站);三级布站(计量站→计量接转站→集中处理站)。
3 平台拉油集中处理集输工艺流程 该工艺流程用于环境条件差,矿区无稀油资源,原油粘度高于几万毫帕秒的特稠油、超稠油的集输。
该工艺流程一般以平台为单元,建高架罐,采用导热油集中伴热。
一个导热油站平均管井约50口,集中布站、管线同架,采用导热油伴热或加热与采用电热带和电加热棒加热比较,提高了热能的利用效率。
4 裂化降粘采、集、输一体化工艺流程 裂化降粘就是在高温下将大分子烃类裂解成小分子烃类,使稠油转化为低粘度的原油。
该流程是单井掺柴油采油和集输,原油在处理站预脱水和高温脱水后再经加热进分馏塔回收和分离出柴油,柴油返输到井口回掺,循环使用。
塔底油经加热进入裂化降粘反应塔,然后经过稳定,降粘外输。
该工艺流程解决了稀释剂的来源,使稠油的开采、集输、处理、降粘各环节紧密配合,节约能源,提高了经济效益。
该工艺适用于稠油资源丰富,且周围无稀油源的稠油区块。
5 超稠油乳化降粘工艺流程 该技术是辽河油田为有效利用超稠油资源,解决国内燃料紧张问题而研究开发的一项技术。
目前,辽河油田已建成曙光金宇乳化油厂、井下乳化油厂、热电厂乳化油厂等多个中小型超稠油乳化装置,初步建成超稠油乳化能力近100×104 t/a。
以曙光油田40×104 t/a乳化油处理站为例来叙述超稠油乳化降粘工艺流程。
首先,汽车拉油卸至卸油槽内,超稠油卸车温度为80~90℃;再经卸油泵升压、换热器升温至95℃左右再进入缓冲罐内;然后由乳化泵升压,予混器混相进入换热器升温至约97℃再进入乳化管内进行乳化。
乳化后的乳化油进入储罐储存,再经装车泵装车外运。
乳化剂的加入量为2%(乳化油与纯油重量比),乳化油含水15%~20%,80℃时粘度为250~600 mPa・s。
此工艺流程目的是通过乳化剂将超稠油乳化制成油包水型乳化油,改善油在燃烧时的雾化效果,增加二次雾化,使燃料充分燃烧,从而改善燃烧效果,提高燃烧效率。
稠油脱水工艺流程 1 两段热化学沉降脱水工艺流程 各小站来油一般含水50%~70%,温度50~60℃,经进站计量后加热至约70℃。
进一段热化学沉降脱水罐脱出游离水,使原油含水达到30%以下。
低含水油溢流至缓冲罐,经脱水泵加压、脱水炉加热后,温度达到80~90℃。
然后进二段热化学沉降罐进行二段沉降脱水,合格油溢流进合格油储罐,经外输泵加压后计量外输。
在油田有伴生天然气的情况下,一段脱水可以采用三相分离器,以提高集输系统的密闭程度。
该流程的关键是沉降时间、脱水温度和化学药剂的选择。
其特点是操作简单、可靠,主要应用于曙光油田、高升油田、海外河油田、欢喜岭油田等集中处理站。
2 热化学沉降加电化学脱水两段脱水工艺流程 各小站来油一般含水50%~70%,温度50~60℃,经进站计量后加热至70℃左右。
进一段热化学沉降脱水罐,脱出游离水,使原油含水达到30%以下。
低含水油溢流至缓冲罐,经脱水泵加压、脱水炉加热后,温度达到80~90℃。
然后进二段电脱水器脱水,合格油进合格油储罐,经外输泵加压后计量外输。
在油田有伴生天然气的情况下,一段脱水可以采用三相分离器,以提高集输系统的密闭程度。
该流程的关键是一段脱水位置和二段电脱水器能否建立起稳定的电场。
其特点是脱水精度高,主要应用于曙光油田、兴隆台油田、小洼油田、锦州油田和冷家坨子里等集中处理站。
3 一段热化学静止沉降脱水流程 此工艺流程用于原油的密度和粘度较大,胶质沥青含量高的原油处理。
该工艺流程的要点在于确定出超稠油热化学沉降的合理工艺参数、脱水温度、沉降时间,采用高效破乳剂和适宜的加药量。
采用多个储罐分别交替静止沉降,浮动出油。
完成沉降脱水的罐转作合格油储罐。
脱水后的净化油含水小于2%,污水含油在1 000 mg/L以下。
该工艺流程在曙一区杜84、杜32块运行良好。
主要稠油处理设备 1 卧式三相分离器 卧式三相分离器的分离过程为高压产出液进分离器之后,先通过减速器降低压力和速度,压力降幅大约为0.07~0.14 MPa。
为了防止液流在进入沉降段后产生波动,加装了防浪板(板上有若干小孔)消泡器,液流从防浪板的小孔进入沉降段,使液流比较稳定。
沉降段的主要分离元件是波纹板聚结器,经聚结器后,原油从溢流板流出,这时原油的含水一般约10%;水则从沉降段的下部排出,水中含油小于350 ppm。
分离出的天然气通过捕雾器从分离器的顶部排出,可100%除掉气体中10 μm的液滴。
产生液的脱水时间大约在30~60 min,控制压力在0.4~0.6 MPa。
因稠油含砂较多,故分离器除具有沉降脱水功能之外,一般都具有水力除砂功能,也是采用在三相分离器的底部,用高压水流冲击沉砂,使之悬浮在水中,同时开启排砂阀将砂排出。
2 稠油电脱水器 辽河油田使用的稠油电脱水器基本是在稀油电脱水的基础上,借鉴国外先进经验技术,自己研制开发的。
该脱水器尺寸为∅3800×16000 mm,设计压力为0.6 MPa,采用直流电极,处理量为80~120 m3/h,进口原油含水小于30%,净化油含水率由2%以上降至1%左右。
排放污水含油率由原来的2.5%降至1.4%,耗电量由0.7 kW・h/t(油)降至0.127 kW・h/t(油)。
辽河油田的稠油电脱水器主要针对稠油的特点在以下几个方面进行了调整。
(1)电极板间距由罐内调节改为罐外调节 在稠油的生产过程中,各不同阶段、不同区块的油品性质差异很大,需要根据具体情况对极板间距进行调节。
这是因为聚结力的大小与极板间距的二次方成正比,对极板间距进行调节可以对聚结力的大小进行调节。
而原有的电脱水器必须停产后在罐内进行调节,很不方便,也影响了生产。
进行改进后即方便了生产,也适应了不同的油品性质。
(2)增加了接地电极板 电脱水器下层板与油水界面形成一个弱电场区。
较高含水量的原油进入电脱水器后,先经过这个区域进行预脱水,它可使较大颗粒的游离水聚结、沉降、分离,以保证高强电场深度脱水的稳定。
但由于油水界面自动控制技术还不十分可靠,因此预脱水能力很低,影响了原油的处理质量。
为了解决这一问题,在底层极板的下方适当增设了接地电极,形成了较稳定的弱电场区,对提高稠油的处理质量有一定的作用。
(3)改进油流分配和集水管结构 原油脱水质量的好坏,与脱水器内液流的稳定程度有直接的关系。
新型稠油电脱水器采用了与罐体直筒段同长双列分配管结构,液流在分配管中均匀的流出,避免个别部位呈喷射状。
集水管也是如此,把原来的单列短管及容易造成砂堵的集水管,改为双列的与油分配管同长的结构,还在集水管上方设置了挡砂板,有效地防止了砂堵,减少了污水含油量。
这种稠油电脱水器经过几年的运行,脱水效果比较理想。
3 加热炉 辽河油田根据辽河油田稠油的特点开发了一种热管炉。
其传热方式及结构特点不同于常规的加热炉,与同负荷的水套炉相比热效率提高10%,达到85%。
另外一个主要优点是盘管的压力损失减少60%~80%,这对稠油集输是非常有利的。
该炉采用了热管技术,在加热方式上采用了两极传热。
首先在主附火筒上装有1型、2型热管共计50支,它们将燃料燃烧的高温烟气和低温烟气的热量,通过热管内部工质的相变换热及火筒壁的传热,将热量传递给壳体内的热媒(软化水),从而使热媒加热到设计温度(120℃)。