高速大功率镗铣类加工中心电主轴开发
高档数控机床高速精密电主 轴关键技术及应用 公告

高档数控机床高速精密电主轴关键技术及应用公告全文共四篇示例,供读者参考第一篇示例:高档数控机床高速精密电主轴关键技术及应用随着科技的不断发展,数控机床作为制造业的重要装备之一,正逐渐成为制造业的主力军。
而高档数控机床的核心部件之一——高速精密电主轴,更是决定了整个机床性能和加工质量的关键部件。
本文将重点介绍高档数控机床高速精密电主轴的关键技术及应用。
一、高速精密电主轴的定义和特点高速精密电主轴是数控机床上用于驱动刀具旋转的核心部件,它直接影响了机床的加工精度、效率和稳定性。
一般来说,高速精密电主轴具有以下几个特点:1. 高速转速:高速精密电主轴的工作转速通常在10000rpm以上,甚至可以达到50000rpm以上。
高转速可以提高加工效率,缩短加工周期。
2. 高精度:高速精密电主轴需要具有极高的旋转精度和稳定性,以保证加工的精度和表面质量。
4. 高功率密度:高速精密电主轴需要具有高功率密度,以满足大功率输出的要求,同时尽可能减小轴体体积和重量。
1. 轴承技术:高速精密电主轴的轴承是其最关键的部件之一,直接影响轴的精度、稳定性和寿命。
目前主要采用陶瓷球轴承、陶瓷滚珠轴承和气体轴承等高速轴承技术。
2. 动平衡技术:高速精密电主轴在旋转时会产生不小的离心力,需要采用动平衡技术来消除不平衡导致的振动和噪音。
3. 冷却技术:高速精密电主轴在高速运转时会产生大量热量,需要采用有效的冷却技术来保持轴的温度稳定,避免发热过高导致零部件热变形。
4. 控制技术:高速精密电主轴需要配备精密的控制系统,以实现精准的转速控制、负载检测和自适应控制等功能。
5. 结构设计:高速精密电主轴的结构设计需要考虑到刚性和轻量化的平衡,同时保证轴体的稳定性和可靠性。
高速精密电主轴广泛应用于汽车、航空航天、铁路、军工等领域,主要用于高精度、高效率的加工。
具体应用包括精密零件加工、高速铣削、高速车削、高速钻孔等领域。
目前国内外一些知名数控机床制造商,如哈斯、西铁城、FANUC 等,都大量采用了高速精密电主轴技术,使其生产的数控机床具有更高的加工精度和效率,受到了市场的广泛认可。
国内外高速电主轴技术的现状与发展趋势

高速电主轴技术的现状与发展趋势高速数控机床(CNC)是装备制造业的技术基础和发展方向之一,是装备制造业的战略性产业。
高速数控机床的工作性能,首先取决于高速主轴的性能。
数控机床高速电主轴单元影响加工系统的精度、稳定性及应用范围,其动力性能及稳定性对高速加工起着关键的作用。
1、高速电主轴对数控机床的发展以及金属切削技术的影响对于数控机床模块化设计、简化机床结构、提高机床性能方面的作用:(1)简化结构,促进机床结构模块化电主轴可以根据用途、结构、性能参数等特征形成标准化、系列化产品,供主机选用,从而促进机床结构模块化。
(2)降低机床成本,缩短机床研制周期一方面,标准化、系列化的电主轴产品易于形成专业化、规模化生产,实现功能部件的低成本制造;另一方面,采用电主轴后,机床结构的简单化和模块化,也有利于降低机床成本。
此外,还可以缩短机床研制周期,适应目前快速多变的市场趋势。
(3)改善机床性能,提高可靠性采用电主轴结构的数控机床,由于结构简化,传动、连接环节减少,因此提高了机床的可靠性;技术成熟、功能完善、性能优良、质量可靠的电主轴功能部件使机床的性能更加完善,可靠性得以进一步提高。
(4)实现某些高档数控机床的特殊要求有些高档数控机床,如并联运动机床、五面体加工中心、小孔和超小孔加工机床等,必须采用电主轴,方能满足完善的功能要求。
2、促进了高速切削技术在机械加工领域的广泛应用电主轴系由内装式电机直接驱动,以满足高速切削对机床“高速度、高精度、高可靠性及小振动”的要求,与机床高速进给系统、高速刀具系统一起组成高速切削所需要的必备条件。
电主轴技术与电机变频、闭环矢量控制、交流伺服控制等技术相结合,可以满足车削、铣削、镗削、钻削、磨削等金属切削加工的需要。
采用高速加工技术可以解决机械产品制造中的诸多难题,取得特殊的加工精度和表面质量,因此这项技术在各类装备制造业中得到越来越广泛的应用,正在成为当今金切加工的主流技术。
高速铣削机床电主轴使用的建议
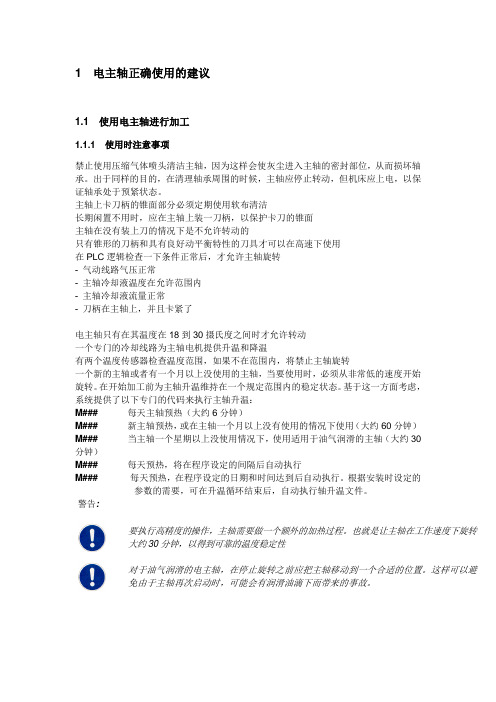
1 电主轴正确使用的建议1.1 使用电主轴进行加工1.1.1 使用时注意事项禁止使用压缩气体喷头清洁主轴,因为这样会使灰尘进入主轴的密封部位,从而损坏轴承。
出于同样的目的,在清理轴承周围的时候,主轴应停止转动,但机床应上电,以保证轴承处于预紧状态。
主轴上卡刀柄的锥面部分必须定期使用软布清洁长期闲置不用时,应在主轴上装一刀柄,以保护卡刀的锥面 主轴在没有装上刀的情况下是不允许转动的只有锥形的刀柄和具有良好动平衡特性的刀具才可以在高速下使用 在PLC 逻辑检查一下条件正常后,才允许主轴旋转 - 气动线路气压正常- 主轴冷却液温度在允许范围内 - 主轴冷却液流量正常- 刀柄在主轴上,并且卡紧了电主轴只有在其温度在18到30摄氏度之间时才允许转动 一个专门的冷却线路为主轴电机提供升温和降温有两个温度传感器检查温度范围,如果不在范围内,将禁止主轴旋转一个新的主轴或者有一个月以上没使用的主轴,当要使用时,必须从非常低的速度开始旋转。
在开始加工前为主轴升温维持在一个规定范围内的稳定状态。
基于这一方面考虑,系统提供了以下专门的代码来执行主轴升温: M### 每天主轴预热(大约6分钟) M### 新主轴预热,或在主轴一个月以上没有使用的情况下使用(大约60分钟) M### 当主轴一个星期以上没使用情况下,使用适用于油气润滑的主轴(大约30分钟) M### 每天预热,将在程序设定的间隔后自动执行M### 每天预热,在程序设定的日期和时间达到后自动执行。
根据安装时设定的参数的需要,可在升温循环结束后,自动执行轴升温文件。
警告:要执行高精度的操作,主轴需要做一个额外的加热过程。
也就是让主轴在工作速度下旋转大约30分钟,以得到可靠的温度稳定性对于油气润滑的电主轴,在停止旋转之前应把主轴移动到一个合适的位置。
这样可以避免由于主轴再次启动时,可能会有润滑油滴下而带来的事故。
1.1.2 加工条件高速铣削加工中心可理解为刀具和工件之间有很高的相对速度。
简述电主轴技术发展前景

简述电主轴技术发展前景引言近年来,随着制造业的不断发展和技术的进步,电主轴技术作为一种新兴的切削加工技术正迅速崛起。
电主轴技术通过将电动机与主轴直接连接,实现高速、高精度的加工,具有较大的发展潜力。
本文将简要阐述电主轴技术的发展前景,包括其应用领域、技术优势以及面临的挑战。
应用领域电主轴技术的广泛应用领域是其发展的重要驱动力之一。
目前,电主轴技术已经广泛应用于机床、数控机床、汽车制造、航空航天等领域。
在机床领域,电主轴技术可以提供更高的切削力和速度,使得加工效率大大提高。
在汽车制造领域,电主轴技术可以实现更高精度的零部件加工,提高汽车的质量和性能。
在航空航天领域,电主轴技术可以实现更高的机械部件加工精度,提高飞机的安全性和可靠性。
技术优势电主轴技术的发展前景可从其技术优势方面来看。
首先,电主轴技术具有较高的切削速度和切削力。
相比传统的机械主轴,电主轴技术可以实现更高的转速和更大的切削力,使得加工效率更高。
其次,电主轴技术具有较高的精度和稳定性。
通过电主轴技术,可以实现更高的定位精度和加工精度,提高零部件的质量和精度。
此外,电主轴技术还具有较低的振动和噪音水平,使得工作环境更加安静和舒适。
面临的挑战电主轴技术发展的前景不仅有技术优势,还面临一些挑战。
首先,电主轴技术的成本较高。
相比传统的机械主轴,电主轴技术需要更多的电气设备和控制系统,成本较高。
其次,电主轴技术在超高速加工和超高精度加工方面仍存在一些技术难题。
目前,电主轴技术的切削速度和切削力还无法满足某些特殊需求。
此外,电主轴技术的维护和维修也需要专业知识和技能,提高了运维成本。
未来发展趋势虽然电主轴技术面临一些挑战,但其发展前景仍然十分广阔。
未来,电主轴技术将继续在制造业中发挥重要作用,并不断推动行业的发展。
随着相关技术的不断改进和创新,电主轴技术的性能将不断提升,成本将逐渐降低。
预计在不久的将来,电主轴技术将实现更高的切削速度和切削力,提供更高的加工效率和精度。
高速立式加工中心电主轴的振动测试及频谱分析

动 分 量 转 变 成 电信 号 并 将 电 信 号 输 入 到 测 量 放 大 系 统 中. 之 后 再 对 其 进 行 信 号 处 理
1 . 2 电 主 轴 测 试 系 统 的 组 成
电主轴 在 高速运 转 时 . 电 主 轴 系 统 会 发 生 振 动 通 过 在 电 主 轴 前 端 与 后 端 贴 装 加 速 度 传 感 器 采 集 加 速 度 信 号 .之 后 对 加 速 度 信 号 进 行 处 理 得 到 电 主 轴 的 振 动 信号。
随着 社会 的发 展 以及科 技水 平 的提高 .高速 数控
机 床 作 为 装 备 制 造 业 的 战 略 性 产 业 . 是 装 备 制 造 业 的 技 术 基 础 和 主 要 发 展 方 向 高 速 立 式 加 工 中 心 的 主 要 特 点 为高速 、 高精 度 、 高 稳定 性 。 电主轴 作 为 高速 立式
要 求 的 运 动 以 外 .其 它 一 切 偏 离 理 想 位 置 的 运 动 为 主 轴振 动 。 电主 轴端 部 的振 动量 , 主 要 应 用 加 速 度 传 感 器
2 电主 轴 的频 谱 分 析
加 速 度 传 感 器 安 装 在 主 轴 端 部 .传 感 器 拾 取 振 动 信号 , 并将 此振 动信 号 通过 电缆传 人 到振 动分 析 仪 . 在 电 脑 屏 幕 上 显 示 一 条 幅 值 随 时 间 变 化 的 曲 线 在 时 域
及 实 际 的生 产 加 工 过 程 提 供 依 据
1 电主 轴 的基 本 结构 及 振 动 测 试
如 图 1所 示 . 为 高 速 立 式 加 工 中 心 电 主 轴 的 基 本 结 构 图 。其 额 定 功 率 为 2 2 k W, 额 定 扭矩 为 3 4 N・ n l 。 最
电主轴助力高精高速高效加工——我国高性能机床主轴技术现状分析
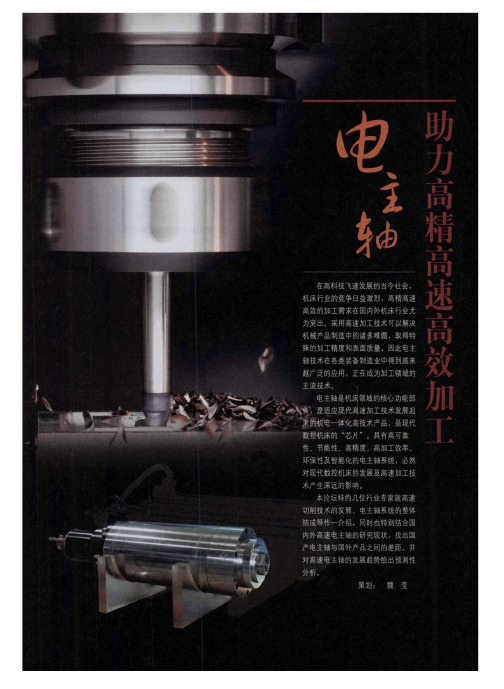
径向刚度> 0 i。湖南大学针对超高速外圆/ 50N・ n 凸
轮轴 磨 床 开 发 了 电动机 内 置式 液 体 ( )静 压 电主 动 轴 ,额 定 功率 和 最 高 转 速 达 3 k 、 1 0 r n 5W 0O 0/ , mi
国际先进水平 :在P B C 板高速钻削用电主轴领 域 ,已大面积推广应用1000 8 0 r n 2 ~1000/ 气静压 0 mi
现代工业对机床加工精度和加工效率要求的不断提
高 ,机 床 对 主轴 性 能 的要 求 也 越 来越 高 ,传统 的 高 速主 轴 概 念 已难 以 充分 描 述 机 床 主轴 的 技 术 内涵 。
磨损小 ,寿命长 ,在精密超精密机床上获得 了广泛
应 用 ,其 主 要技 术 难 点 在于 控 制 高 速 时主 轴 的 温 升 和 热变 形 。气体 轴 承 电主轴 以 “ 膜 ”作 为 支 撑 , 气
O 6 ,
参磊‘ ‘ 加 ,两 I 朋 I 。 冷 工 。— 冲 ,
E
用 油 气 润 滑 和 强 制 水 冷 方 式 。 沈 阳 建 筑 大 学 开 发 限 公 司开 发 了系 列 ( )静 压 主 轴产 品 ,额 定 功率 动
高 速大功 率 陶瓷 球轴 承 电主轴单元 最高转 速达 到
我国高性能机床主轴技术 现状分析
湖 南大学国家 高效磨 削工程 中心教 授 熊万 里
优 点 ,其 极 限转 速 高 、精 度 高 、刚 度 高 ,在 加 工 中
高性能机床主轴概述
机 床 主 轴是 机 床 的 核 心部 件 ,其 功 能是 带 动 刀 具 ( 轮 )或 工件 旋 转 ,实 现 高 速精 密加 工 。随 着 砂
具 有轴 承动 态 预 紧 调 整 功 能 。 ③平 均 无 故 障运 行 时 间 ≥5O 0 。 ④主 轴 回转 精 度 < 1 m。⑤轴 系统 0h . 0 刚 度 ≥3 0 I。 ⑥动 平 衡 精 度 G .级 。⑦ 恒 功 0 N・ T I O4
数控铣床电主轴系统设计说明书
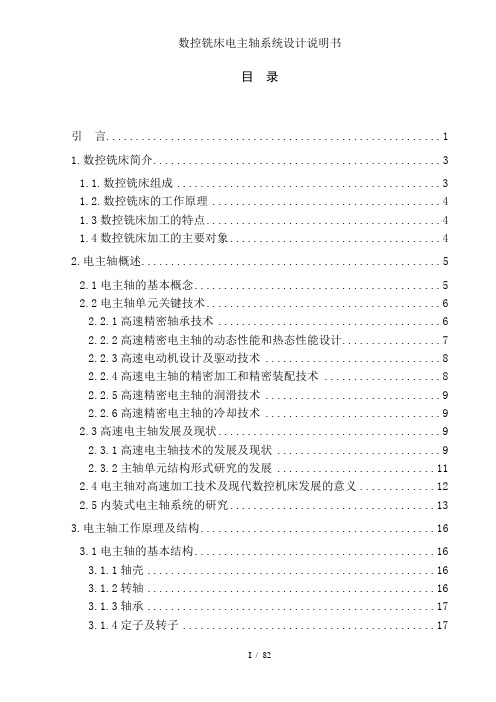
目录引言 (1)1.数控铣床简介 (3)1.1.数控铣床组成 (3)1.2.数控铣床的工作原理 (4)1.3数控铣床加工的特点 (4)1.4数控铣床加工的主要对象 (4)2.电主轴概述 (5)2.1电主轴的基本概念 (5)2.2电主轴单元关键技术 (6)2.2.1高速精密轴承技术 (6)2.2.2高速精密电主轴的动态性能和热态性能设计 (7)2.2.3高速电动机设计及驱动技术 (8)2.2.4高速电主轴的精密加工和精密装配技术 (8)2.2.5高速精密电主轴的润滑技术 (9)2.2.6高速精密电主轴的冷却技术 (9)2.3高速电主轴发展及现状 (9)2.3.1高速电主轴技术的发展及现状 (9)2.3.2主轴单元结构形式研究的发展 (11)2.4电主轴对高速加工技术及现代数控机床发展的意义 (12)2.5内装式电主轴系统的研究 (13)3.电主轴工作原理及结构 (16)3.1电主轴的基本结构 (16)3.1.1轴壳 (16)3.1.2转轴 (16)3.1.3轴承 (17)3.1.4定子及转子 (17)3.2电主轴的工作原理 (17)3.3电主轴的基本参数 (19)3.3.1电主轴的型号 (19)3.3.2转速 (19)3.3.3输出功率 (19)3.3.4 输出转矩 (19)3.3.5电主轴转矩和转速、功率的关系 (20)3.3.6 恒转速调速 (20)3.3.7 恒功率调速 (20)3.3.8 轴承中径 (20)3.4自动换刀装置 (21)4. 电主轴结构设计 (22)4.1主轴的设计 (22)4.1.1.铣削力的计算 (22)4.1.2 主轴当量直径的计算 (23)4.2高速电主轴单元结构参数静态估算 (23)4.2.1 高速电主轴单元结构静态估算的内容及目的 (23)4.2.2轴承的选择和基本参数 (23)4.3轴承的预紧 (24)4.4主轴轴承静刚度的计算 (24)4.4.1 主轴单元主要结构参数确定及刚度验算 (26)4.4.2主轴单元主要结构参数确定 (27)4.4.3主轴强度的校核 (32)4.4.4主轴刚度的校核 (34)4.4.5主轴的精密制造 (35)4.5主轴电机 (36)4.5.1电机选型 (36)4.6主轴轴承 (37)4.6.1轴承简介 (37)4.6.2陶瓷球轴承 (38)4.6.3陶瓷球轴承的典型结构 (40)4.7主轴轴承精度对主轴前端精度影响 (40)4.8拉刀机构设计 (41)4.8.1刀具接口 (41)4.8.2拉刀杆尺寸设计 (42)4.8.3夹具体结构尺寸设计 (43)4.8.4 松、拉刀位移的确定 (45)4.8.5碟型弹簧的设计及计算 (46)4.9HSK工具系统结构特点分析 (48)4.10HSK工具系统的静态刚度 (52)4.10.1 HSK工具系统的变形转角及极限弯矩 (52)5.电主轴的润滑及冷却 (55)5.1润滑介绍 (55)5.1.1润滑的作用和目的 (55)5.1.2 电主轴润滑的主要类型 (55)5.1.3 油气润滑的原理和优点 (57)5.2电主轴的冷却 (58)5.2.1电主轴的热源分析 (58)5.2.2电主轴的冷却方法 (59)5.3电主轴的防尘和密封 (60)6.电主轴的驱动和控制 (61)6.1恒转矩变频驱动和参数设置 (61)6.2恒功率变频驱动和参数设置 (62)6.3矢量控制驱动器的驱动和控制 (64)6.4普通变频器原理 (65)6.5本设计采用的变频器原理 (67)6.6主轴准停 (69)6.6.1主轴的准停功能 (69)6.6.2主轴准停的工作原理 (69)6.6.3主轴准停控制方法 (70)7.主轴动平衡 (72)7.1动平衡介绍 (72)7.2动平衡设计 (73)总结 (75)致谢 (76)参考文献 (77)引言高速机床是实现高速切削加工的前提和条件。
机床高速电主轴原理与应用_杨军
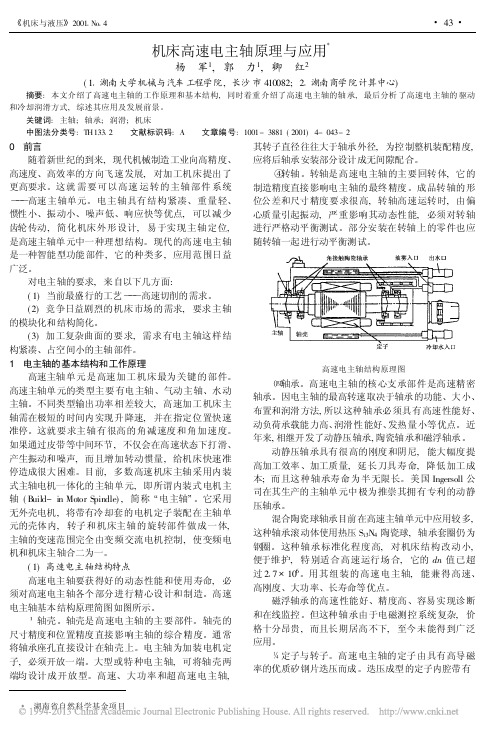
机床高速电主轴原理与应用*杨军1,郭力1,卿红2(11湖南大学机械与汽车工程学院,长沙市410082;21湖南商学院计算中心)摘要:本文介绍了高速电主轴的工作原理和基本结构,同时着重介绍了高速电主轴的轴承,最后分析了高速电主轴的驱动和冷却润滑方式,综述其应用及发展前景。
关键词:主轴;轴承;润滑;机床中图法分类号:TH13312文献标识码:A文章编号:1001-3881(2001)4-043-20前言随着新世纪的到来,现代机械制造工业向高精度、高速度、高效率的方向飞速发展,对加工机床提出了更高要求。
这就需要可以高速运转的主轴部件系统)))高速主轴单元。
电主轴具有结构紧凑、重量轻、惯性小、振动小、噪声低、响应快等优点,可以减少齿轮传动,简化机床外形设计,易于实现主轴定位,是高速主轴单元中一种理想结构。
现代的高速电主轴是一种智能型功能部件,它的种类多,应用范围日益广泛。
对电主轴的要求,来自以下几方面:(1)当前最盛行的工艺)))高速切削的需求。
(2)竞争日益剧烈的机床市场的需求,要求主轴的模块化和结构简化。
(3)加工复杂曲面的要求,需求有电主轴这样结构紧凑、占空间小的主轴部件。
1电主轴的基本结构和工作原理高速主轴单元是高速加工机床最为关键的部件。
高速主轴单元的类型主要有电主轴、气动主轴、水动主轴。
不同类型输出功率相差较大,高速加工机床主轴需在极短的时间内实现升降速,并在指定位置快速准停。
这就要求主轴有很高的角减速度和角加速度。
如果通过皮带等中间环节,不仅会在高速状态下打滑、产生振动和噪声,而且增加转动惯量,给机床快速准停造成很大困难。
目前,多数高速机床主轴采用内装式主轴电机一体化的主轴单元,即所谓内装式电机主轴(B uild-in Motor Spindle),简称/电主轴0。
它采用无外壳电机,将带有冷却套的电机定子装配在主轴单元的壳体内,转子和机床主轴的旋转部件做成一体,主轴的变速范围完全由变频交流电机控制,使变频电机和机床主轴合二为一。
加工中心用电主轴结构设计及其仿真分析

加工中心用电主轴结构设计及其仿真分析一、综述随着科技的不断发展,加工中心在制造业中的地位越来越重要。
加工中心作为一种高效、高精度、高自动化的加工设备,已经成为现代制造业的重要支柱。
然而加工中心在使用过程中,电主轴作为其核心部件,其结构设计和性能对加工中心的整体性能具有重要影响。
因此对加工中心用电主轴的结构设计及其仿真分析进行研究,对于提高加工中心的性能和降低生产成本具有重要意义。
电主轴是一种将交流电源转换为高速旋转并带传动功能的电动机。
它具有结构简单、重量轻、惯性小、响应速度快等优点,广泛应用于数控机床、加工中心等机械设备中。
电主轴的结构设计主要包括电机、减速器、轴承、冷却系统等部分。
其中电机是电主轴的核心部件,其性能直接影响到整个电主轴的性能;减速器用于降低电机转速,提高扭矩;轴承用于支撑转子并实现转动;冷却系统用于降低电机温度,保证电主轴的正常运行。
为了提高加工中心的性能,需要对电主轴的结构进行优化设计。
首先应选择合适的电机类型和参数,以满足加工中心的工作要求。
其次应合理选择减速器类型和参数,以保证电主轴具有较高的转速和扭矩输出。
此外还应考虑轴承的选择和配置,以确保电主轴具有较低的噪声和振动。
冷却系统的设计也至关重要,应根据加工中心的工作环境和工艺要求,选择合适的冷却方式和参数。
为了验证电主轴结构设计的合理性和性能,可以采用仿真分析方法对其进行评估。
通过建立数学模型,对电主轴的结构参数进行优化设计,并利用仿真软件对其进行模拟分析。
仿真分析可以帮助我们了解电主轴在不同工况下的性能表现,为实际应用提供依据。
同时仿真分析还可以发现结构设计中的潜在问题,为改进设计提供参考。
加工中心用电主轴结构设计及其仿真分析是一项重要的研究工作。
通过对电主轴结构的设计优化和仿真分析,可以提高加工中心的性能,降低生产成本,为现代制造业的发展做出贡献。
1.1 研究背景和意义随着现代制造业的飞速发展,加工中心在工业生产中扮演着越来越重要的角色。
应用有限元方法对高速电主轴的优化设计
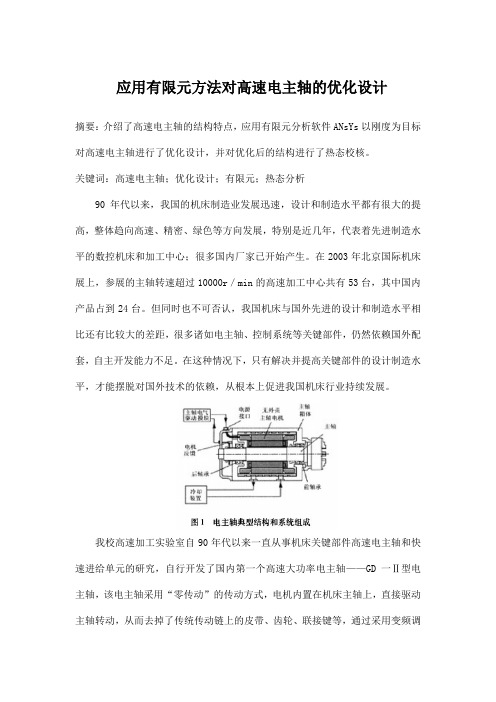
应用有限元方法对高速电主轴的优化设计摘要:介绍了高速电主轴的结构特点,应用有限元分析软件ANsYs以刚度为目标对高速电主轴进行了优化设计,并对优化后的结构进行了热态校核。
关键词:高速电主轴;优化设计;有限元;热态分析90年代以来,我国的机床制造业发展迅速,设计和制造水平都有很大的提高,整体趋向高速、精密、绿色等方向发展,特别是近几年,代表着先进制造水平的数控机床和加工中心;很多国内厂家已开始产生。
在2003年北京国际机床展上,参展的主轴转速超过10000r/min的高速加工中心共有53台,其中国内产品占到24台。
但同时也不可否认,我国机床与国外先进的设计和制造水平相比还有比较大的差距,很多诸如电主轴、控制系统等关键部件,仍然依赖国外配套,自主开发能力不足。
在这种情况下,只有解决并提高关键部件的设计制造水平,才能摆脱对国外技术的依赖,从根本上促进我国机床行业持续发展。
我校高速加工实验室自90年代以来一直从事机床关键部件高速电主轴和快速进给单元的研究,自行开发了国内第一个高速大功率电主轴——GD一Ⅱ型电主轴,该电主轴采用“零传动”的传动方式,电机内置在机床主轴上,直接驱动主轴转动,从而去掉了传统传动链上的皮带、齿轮、联接键等,通过采用变频调速技术使主轴达到很高的转速,它的典型结构和系统组成如图l所示…。
主要具有以下几个特点:(1)结构简单紧凑,能很好地解决传统皮带或齿轮等方式传动在高速运转条件下所引起的振动和噪声问题。
(2)提高生产率,可在最短时间内实现高转速,也即是主轴回转时具有极大的角加速度。
(3)电机内置于主轴两支承之间,可有效地提高主轴系统的刚度,同时也提高了系统的固有频率,从而提高了其临界转速值。
目前,在试验成功的基础上,这种电主轴已经进入产业化,为了达到更高的设计要求和水平,并保证电主轴更高的可靠性,我们采用了有限元分析(Finite Element Analysis)对电主轴进行优化设计。
文献综述模板
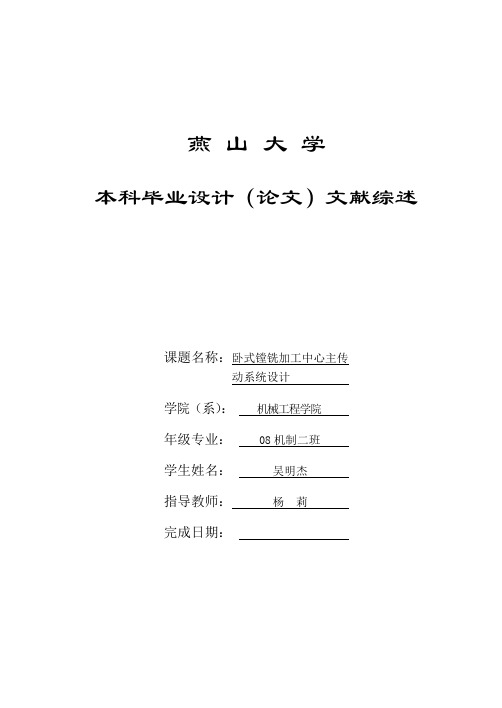
燕山大学本科毕业设计(论文)文献综述课题名称:卧式镗铣加工中心主传动系统设计学院(系):机械工程学院年级专业:08机制二班学生姓名:吴明杰指导教师:杨莉完成日期:一、课题国内外现状加工中心是数控机床各类产品中发展最快、所占比重最大的一类产品,也是制造业应用最广的一类设备。
一些经济发达国家都把发展加工中心作为发展数控机床的首要任务,它的发展直接关系到国家经济建设和国防安全。
目前,我国国产加工中心的市场占有率很低,按台数计不足1/3、按金额计不足1/4,尽快缩小国产加工中心与国际水平的差距,是我国机床工业的当务之急,提高国产加工中心的市场占有率关键在于提高国产加工中心的国际市场综合竞争力。
我国加工中心市场与我国经济发展水平,制造业的水平和企业国际竞争力的提高密切相关。
从八十年代前后开始,北京机床研究所等单位研究开发了立式加工中心,并形成了商品。
九十年代初,我国企业通过引进技术,消化吸收如北京机床所引进美国TK公司立式加工中心技术、北京机电研究院引进美国辛辛那提公司马刀立式加工中心技术等等和自行开发,基本掌握了加工中心的设计和制造技术,为加工中心生产和应用打下了基础。
到九十年代末,国内的加工中心生产数量仍然较少,每年合计仅300台左右。
2000年前后,一批海外大的机床跨国集团公司看好中国市场,开始在中国建立生产数控机床和加工中心独资和合资企业,实现了本地制造和本地销售。
目前形成规模的有台湾杭州友佳机床有限公司、宁夏小巨人机床有限公司、大连忆达日平机床有限公司、北一大隈机床有限公司、德马吉上海机床有限公司等。
步入21世纪,随着我国综合经济实力的快速提高,加工中心市场进入了快速发展期。
汽车及其零部件、通用机械、航空航天、模具等等各行业对加工中心需求的大幅度上升,国产加工中心择优选择国内外数控系统、功能部件等配套件,加快产业化生产步伐,质量、可靠性大幅度提高,据一样性价比优势,逐步得到了国内用户的肯定和认可。
基于敏感度分析的大型数控镗铣中心主轴箱优化设计研究
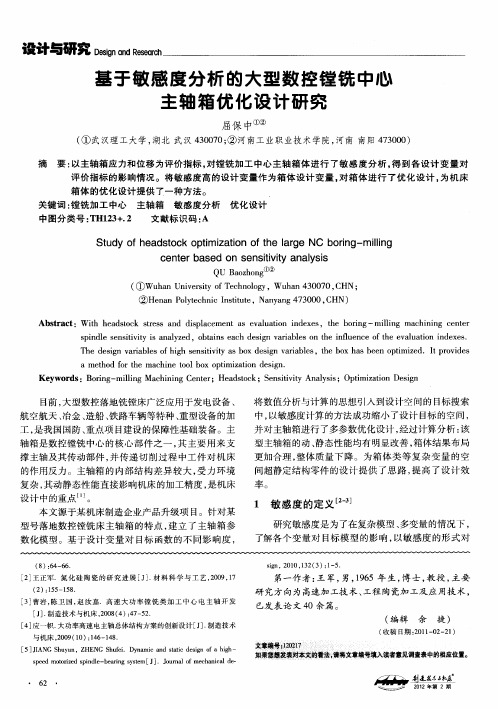
设计与研究 Dia s『 ennRec s dea g h
基 于 敏 感 度分 析 的 大型 数 控 镗 铣 中心 主 轴 箱 优 化 设 计 研 究
屈保 中① ②
( ①武汉理工大学, 湖北 武汉 4 07 ; 河南S 业职业技术学院, 300 ② - 河南 南阳 4 30 ) 70 0
( )15 5. 2 : 5 —1 8
第一作 者 : 军 , ,95年 生 , 士 , 授 , 王 男 16 博 教 主要
研 究 方向 为 高速 加 工技 术 、 工程 陶瓷加 工及应 用技 术 ,
[] 3 曹岩 , 卫 国, 汝嘉.高速 大功 率镗 铣 类加 工 中 心 电主轴 开 发 陈 赵 [ ] 制造技术与机床 ,0 8 4)4 — 2 J. 2 0 ( :7 5 . [ 应一帜. 4] 大功率高速 电主轴总体结构方案 的创新床广 泛应 用于 发 电设备 、 大 航 空 航天 、 金 、 冶 造船 、 铁路 车 辆等 特种 、 型设 备 的加 重 工 , 我 国 国防 、 是 重点 项 目建设 的保 障性 基 础装 备 。主 轴箱 是数 控 镗铣 中心 的核 心 部 件 之 一 , 主 要 用 来 支 其 撑 主轴及 其 传动 部 件 , 传 递切 削过 程 中工 件 对 机 床 并
数控机床高速电主轴技术及应用

数控机床高速电主轴技术及应用一、高速电主轴的发展历程早在 20 世纪 50 年代,就己出现了用于磨削小孔的高频电主轴,当时的变频器采用的是真空电子管,虽然转速高,但传递的功率小,转矩也小。
随着高速切削发展的需要和功率电子器件、微电子器件和计算机技术的发展,产生了全固态元件的变频器和矢量控制驱动器;加上混合陶瓷球轴承的出现,使得在 20 世纪 80 年代末、90 年代初出现了用于铣削、钻削、加工中心及车削等加工的大功率、大转矩、高转速的电主轴。
国外高速电主轴技术发展较快,中等规格的加工中心的主轴转速目前己普遍达到 10000r/min 甚至更高。
1976 年美国的 Vought 公司首次推出一台超高速铣床,采用了 Bryant 内装式电机主轴系统,最高转速达到了20,OOOr/min,功率为 15KW。
到 90 年代末期,电主轴发展的水平是:转速40,000 r/min,功率 40 KW(即所谓的“40-40 水平”)。
但 2001 年美国Cincinnati 公司为宇航工业生产了 SuperMach 大型高速加工中心,其电主轴最高转速达 60,000 r/min,功率为 80 KW。
目前世界各主要工业国家均有装备优良的专业电主轴生产厂,批量生产一系列用于加工中心和高速数控机床的电主轴。
其中最著名的生产厂家有:瑞士的 FISCHER 公司、IBAG 公司和 STEP-TEC 公司,德国的 GMN 公司和FAG 公司,美国的 PRECISE 公司,意大利的 GAMFIOR 公司和 FOEMAT 公司,日本的 NSK公司和 KOYO公司,以及瑞典的 SKF公司等公司。
高速电主轴生产技术的突破,大大推动了世界高速加工技术的发展与应用。
从 80年代中后期以来,商品化的超高速切削机床不断出现,超高速机床从单一的超高速铣床发展成为超高速车铣床、钻铣床乃至各种加工中心等。
德国、美国、瑞士、英国、法国、日本也相继推出了自己的超高速机床。
2024年高速电主轴市场环境分析

2024年高速电主轴市场环境分析引言高速电主轴是一种用于高速切削和镗削的精密机械设备,被广泛应用于机床、线切割、激光加工等行业。
随着制造业的发展,高速电主轴市场呈现出蓬勃的增长态势。
本文将对高速电主轴市场环境进行分析,包括市场规模、竞争状况、发展趋势等方面。
1. 市场规模高速电主轴市场在近年来持续增长,主要由以下几个方面的因素推动:•制造业的发展:随着制造业的不断进步和升级,对高速、高精度加工设备的需求不断增加,推动了高速电主轴市场的发展。
•自动化生产的普及:随着自动化生产技术的不断成熟和应用,对高速电主轴的需求也在不断提高,使得市场规模持续扩大。
•环保需求的增加:高速电主轴由于其高效节能和低噪音的特点,能够满足环保需求,因此在环保政策的推动下,市场需求进一步增长。
据统计,2019年高速电主轴市场规模达到XX亿元,预计在未来几年内将保持持续增长。
2. 竞争状况高速电主轴市场竞争激烈,主要由以下几家企业主导市场:•A公司:作为市场的领导者,A公司具有先进的技术和强大的研发能力,产品质量得到广泛认可。
•B公司:B公司凭借其丰富的市场经验和良好的客户关系,极大地增强了其在市场中的竞争力。
•C公司:C公司通过不断创新和技术提升,逐渐取得了市场份额,并在某些细分领域取得了重要突破。
此外,还有一些新兴企业进入市场,通过低价策略和差异化产品占据一定市场份额。
整体来看,高速电主轴市场竞争激烈,企业需要不断提升产品质量、降低成本以及加强市场营销和服务能力以保持竞争优势。
3. 发展趋势高速电主轴市场在未来呈现出以下几个发展趋势:•高速化与高精度化:随着制造业对产品质量和加工效率要求的提高,高速电主轴需要不断提升转速和加工精度,以满足市场需求。
•智能化与自动化:自动化技术和智能控制系统的发展,使得高速电主轴能够更好地适应自动化生产线的需求,实现智能化操作和监控。
•轻量化与节能环保:轻量化设计和节能环保技术的应用,能够降低产品能耗和环境污染,符合可持续发展的要求。
高速大功率车铣电主轴后置圆锥摩擦锁紧机构设计
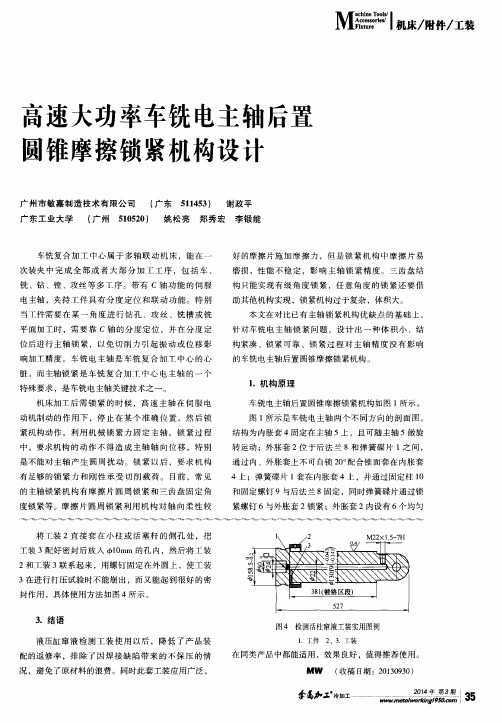
高速大功率车铣电主轴后置 圆锥摩擦锁紧机构设计
广州市敏嘉制造技术有 限公 司 ( 广东 5 1 1 4 5 3 ) 谢政 平 广东工业大学 ( 广州 5 1 0 5 2 0 ) 姚松 亮 郑秀 宏 李锻 能
车铣 复 合 加 工 中 心属 于 多轴 联 动 机 床 ,能在 一 次装 夹 中 完 成 全 部 或 者 大 部 分 加 工 工 序 ,包 括 车 、
3 ・结语
液压 缸窜 液 检 测 工 装 使 用 以后 ,降低 了 产 品装 配 的返修 率 ,排 除 了因 焊 接 缺 陷 带来 的 不保 压 的情
况 ,避免 了原材 料 的浪费 。 同时此套 工装 应用广 泛 ,
图4 检测活柱窜液工装实用图例
1 . 工 件 2 、 3 . 工 装 在 同类产 品 中都能适 用 ,效果 良好 ,值 得推荐 使用 。
1 .机构原 理
车铣 电主轴后 置 圆锥 摩擦 锁 紧机构 如 图 1所示 。 图 1所示 是车铣 电主 轴两 个 不 同方 向的剖 面 图 , 结 构为 内胀套 4固定 在主 轴 5上 ,且 可随 主轴 5做旋 转运 动 ;外胀 套 2位 于后 法 兰 8和 弹簧 碟 片 l之 间 ,
当l T件 需要 在 某一 角 度进 行 钻孔 、攻 丝 、铣 槽 或 铣 平面加 工 时 ,需 要 靠 C轴 的 分度 定 位 ,并 在 分度 定
位 后进 行 主轴 锁 紧 ,以免 切 削 力 引 起 振 动 或 位 移 影 响加 工精度 。车 铣 电 主轴 是 车 铣 复 合 加 T 中心 的心
铣 、钻 、镗 、攻 丝 等多 工 序 。带 有 c轴 功 能 的伺 服 电主轴 ,夹 持 工 件 具 有 分 度 定 位 和 联 动 功 能 。特 别
北京航空航天大学科技成果——机床高速电主轴的扭矩测量装置
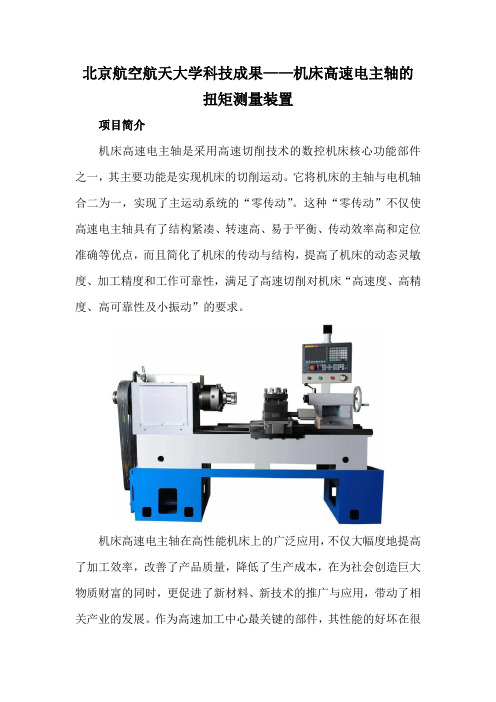
北京航空航天大学科技成果——机床高速电主轴的扭矩测量装置项目简介机床高速电主轴是采用高速切削技术的数控机床核心功能部件之一,其主要功能是实现机床的切削运动。
它将机床的主轴与电机轴合二为一,实现了主运动系统的“零传动”。
这种“零传动”不仅使高速电主轴具有了结构紧凑、转速高、易于平衡、传动效率高和定位准确等优点,而且简化了机床的传动与结构,提高了机床的动态灵敏度、加工精度和工作可靠性,满足了高速切削对机床“高速度、高精度、高可靠性及小振动”的要求。
机床高速电主轴在高性能机床上的广泛应用,不仅大幅度地提高了加工效率,改善了产品质量,降低了生产成本,在为社会创造巨大物质财富的同时,更促进了新材料、新技术的推广与应用,带动了相关产业的发展。
作为高速加工中心最关键的部件,其性能的好坏在很大程度上决定了整台高速机床的加工精度和生产效率,而高速电主轴的可靠性更是体现了整台机床在生产企业的可用性,高速电主轴在高速运转状态下的扭矩输出是高速电主轴的主要性能之一。
因此,需要设计一种扭矩试验装置来测量高速电主轴在高速运转情况下的扭矩输出情况。
目前国内研究机构对高速电主轴扭矩的测量大多是基于独立的电主轴利用测功电机直接加载,并通过扭矩传感器直接测量高速电主轴的输出扭矩和转速,这对同轴度的要求比较高,且很难达到高速的要求。
为解决上述问题,本项目研发了一种用于机床高速电主轴的扭矩测量装置。
技术描述本成果属于测量装置技术领域,具体涉及一种用于机床高速电主轴的扭矩测量装置及测量技术。
用于机床高速电主轴的扭矩测量装置,包括减速器、扭矩转速传感器和电力测功电机,减速器和扭矩转速传感器之间通过第一联轴器相连,以用于传递扭矩,扭矩转速传感器和电力测功电机之间通过第二联轴器相连,以用于扭矩加载,减速器的输入轴上设有第三联轴器,第三联轴器用于将减速器的输入轴与加载杆连接,加载杆能够与机床的电主轴相连。
通过使用本成果的用于机床高速电主轴的扭矩测量装置及测量技术,可以有效的降低机床电主轴的转速并传递转矩,使扭矩的测量更加准确,且易于装配。
高速电主轴

高速电主轴- 介绍高速电主轴是高速加工中心的核心部件。
在模具自由曲面和复杂轮廓的加工中,常常采用2~12mm较小直径的立铣刀,而在加工铜或石墨材料的电火花加工用的电极时,要求很高的切削速度,因此,电主轴必须具有很高的转速。
目前,加工中心的主轴转速大多在18000~42000r/min,瑞士Mikro的高速加工中心XSM400U/XSM600U其主轴转速已达54000r/min。
而对于模具的微细铣削(铣刀直径一般采用0.1~2mm),则需要更高的转速。
横林精工-高速电主轴如德国Kugler公司的五轴高精度铣床,其最高主轴转速达160000r/min(采用空气轴承),这样的高转速,当采用0.3mm直径的铣刀加工钢模时,就可达到150m/min的切削速度。
目前,德国Fraunhofer生产技术研究所正在开发转速为300000r/min的空气轴承支撑的主轴。
加工模具时,总是采用很高的转速,而高转速产生的发热,以及切削时可能产生的振动是影响模具加工精度的重要因素。
为保证高速电主轴工作的稳定性,在主轴上装有用来测量温度、位移和振动的传感器,以便对电机、轴承和主轴的温升、轴向位移和振动进行监控。
由此为高速加工中心的数控系统提供修正数据,以修改主轴转速和进给速度,对加工参数进行优化。
当主轴产生轴向位移,则可通过零点修正或轨迹修正来进行补偿。
高速电主轴- 高速电主轴购买需知关于高速电主轴高速电主轴运转速度是通过变频器的驱动来实现的。
您可以自己选用变频器,当然也可以将这项工作交由我们来为您代劳,我们将为您匹配好变频器的参数和主轴参数,减少您的麻烦。
关于选型选购主轴时,请告知我们:你在我们网上所选用的主轴型号;或者告诉我们主轴的相关参数,比如:主轴工作电压、主轴的外径、主轴的功率、主轴的转速、主轴的轴端连接、主轴的冷却方式(水冷/自冷/风冷)等,我们将为您推荐最合适的产品。
关于包装及运输方式您所选购的主轴将用高密度的泡沫箱及纸箱包装。
- 1、下载文档前请自行甄别文档内容的完整性,平台不提供额外的编辑、内容补充、找答案等附加服务。
- 2、"仅部分预览"的文档,不可在线预览部分如存在完整性等问题,可反馈申请退款(可完整预览的文档不适用该条件!)。
- 3、如文档侵犯您的权益,请联系客服反馈,我们会尽快为您处理(人工客服工作时间:9:00-18:30)。
.
.Q .
高速电主轴的性能要求与设计
主轴部件的基本要求 电主轴通常装备在高速加工中心上, 在设计电主
轴时要根据用户的工艺要求, 采用典型零件统计分析 的方法来确定高速电主轴的基本性能参数。机床厂对 同一尺寸规格的高速机床, 一般会分两大类型, 即 “高 速型” 和 “ 高刚度型” , 分别进行设计。前者主要用于 航空、 航天等工业加工轻合金、 复合材料和铸铁等零
[ ?, 8] 过盈套 作为内装电动机转子与主轴的联结紧固元
与主轴单元合二为一, 电动机置 于 主 轴
前、 后轴承之间的一体化的结构, 采用内装电动机直接 驱动。主轴部件由前后各两套高速精密角接触陶瓷球 轴承
[ %]
支撑于电主轴外壳中, 均分别用串联 安 装 方
式, 前后支承受力为外撑式。前轴承固定, 承受径向载 荷和轴向载荷。后轴承在轴向可有微量位移, 以补偿 主轴工作时的热伸长。主轴支承结构选用接触角为 $%3 的 角 接 触 混 合 陶 瓷 球 轴 承,456 公 司 的 6578&$/69! 和 6578&$$69! 轴承; 采用油 : 气润滑 系统对其润滑; 轴承的配置采用前二后二、 背对背、 定 压预紧的形式, 可以满足高速运转的要求。电动机转 子取消了键联接, 而用压配合方法安装在主轴上, 处于 前后轴承之间, 工作时由压配合产生的摩擦力来传递 转矩。电动机定子通过一个铝质冷却套安装在电主轴 的壳体中。为了有效散热, 在壳体内开设了冷却管路。 主轴系统工作时, 由冷却泵打入冷却液带走主轴单元 内的热量, 以保证电主轴正常工作。主轴为空心结构, 内部安装 ;<< 公司生产的 7=> 拉刀机构, 以实现自 动换刀。主轴后部安装有测速传感器, 可实现 ! 轴控 制。电主轴使用油 : 气润滑系统来对轴承进行润滑和 冷却。对电动机定子则采用冷却系统— — —水冷却机来 冷却。
[ $& , $$ ] 关 。主轴单 元 的 弯 曲 刚 度 $ % @ & % ’ !( 0 ( !) ) 。
一般情况下, 弯曲刚度远比轴向刚度 $ ( 重要, 是衡量 主轴单元刚度的重要指标, 通常用来代指主轴的刚度。 主轴结构如图 $ 所示, 特点如下: ($) 具有结构紧凑、 易 于 平 衡、 传动效率高等优
[ ", B] 高, 回转精度要求高, 故根据 《 机床设计手册》 选用
标准化设计。这样的配置具有: 中等的刚度和承载能 力, 后支撑一组弹簧合理预紧, 且补偿磨损, 极限转速 很高, 发热小, 轴向精度高的特性。 主轴的静刚度简称主轴刚度, 反映主轴单元抵抗 静 态 外 载 荷 的 能 力, 与负荷能力及抗振性密切相
[ $% ]
中质量, 将使主轴部件的固有频率降低, 有可能发生共 振。所以必须研究电主轴单元的动态特性, 分析主轴 单元的各阶固有频率和振型。进行模态分析时, 高阶 模态的固有频率较高, 不会产生共振。因此只分析最 低几阶模态, 然后根据薄弱环节采取措施。 !; " %; $; $ 主轴部件有限元建模 主轴部件的结构简化 加工中心电主轴是一个多阶梯空心的圆柱体, 须 经过一定简化后, 方可进行有限元分析。主轴部件在 以下方面进行简化: ($ ) 各处倒角简化成直角, 忽略空 刀槽; (%) 润滑油孔、 工艺孔、 螺纹孔等均按实体处理; (1) 主轴轴承简化成弹性元件; (!) 主轴上电动机转 子、 锁紧螺母、 中间隔套等零件简化成集中质量。 %; $; % 单元类型的选择及结构剖分 主轴部件几何形状、 约束情况以及所承受的载荷 都对称于主轴, 所以其各点的位移、 应力和应变也都对 称于主轴, 是轴对称问题。在 7<, ) =:469>?49 中将 轴对称问题定义为 %@ 9A’-B((CD<’+ 之后, 就可以将空 间轴对称问题转化为平面问题来处理。常采用轴剖面 等参数建立有限元分析模型。首先对电主轴单元作如 下简化: ($ ) 支承位置简化。将角接触球轴承的串联组配 简化为前后各两个支承, 支点位置在两接触线与主轴 轴线的交点处; (% ) 认为轴承只具有径向刚度, 不具有角刚度, 如 此将支承进一步简化为径向的压缩弹簧。即梁的径向 采用弹性边界元模拟轴承支承; (1) 忽略轴承负荷及转速对轴承刚度的影响, 视 轴承刚度为一个不变的常数; (!) 静态分析时, 转子的重量作为轴上的均布载 荷处理; (0) 动态分析时, 轴上附加的转子质量转化为相 应轴段的密度增加值, 而刚度仍为原轴段刚度。可将 主轴部件离散 %E% 个实体单元, ! 个弹簧元素单元模 型。 %; $; 1 约束条件的建立 合理确定有限元模型约束条件是成功地进行有限 元分析的基本条件。约束条件的确定, 应尽可能符合 原结构的实际情况。对于本结构不考虑主轴部件的轴 向变形, 仅研究其径向变形。该主轴部件是两端定位 方式, 这种定位方式在有限元模型中很难建立, 因此在 前支承处将 + 向约束置于主轴轴肩一点上, 同时限制 该点在 , 向运动; 在后支承处选一点约束主轴 , 向运 动, 由于点约束会引起应力集中, 约束作用点用两个实
################################################ 海交通大学学报Q ’%%! (\) : (%$ [ (%! ( 编辑 汪 艺) # ( 收稿日期: ’%%" ! %^ ! %( ) # # 作者: 俞鸿斌, 男, $("$ 年生, 硕士研究生, 讲师, 文章编号: Z!%( 主要研究方向: 数控技术, 机械 *+X ] *+A ] *+1 等。
・# !" ・
影响主轴组件刚度的主要因素有主轴的结构尺 寸、 轴承类型与配置形式、 轴承间隙的大小、 传动件的
布置方式、 主轴组件的制造和装配质量等。机床主轴 往往有较高的刚度要求, 因此, 轴承直径的尺寸往往较 大。根据这些轴承直径尺寸所选定的滚动轴承, 其疲 劳寿命往往是富裕的, 因此常常不需要作疲劳寿命的 计算。这类轴承的选择主要取决于其精度和刚度 主要对主轴组件的径向刚度进行校核计算。 一般在设计车、 铣、 镗床的主轴组件时, 主轴的结 构尺寸和轴承的刚度、 阻尼, 主要是根据不出现切削自 激振动的条件来确定的。主轴系统的刚度, 也是根据 不出现切削自激振动的条件指定的。工程上常采用根 据自激振动稳定性确定主轴组件刚度要求的近似算法 来确 定 机 床 系 统 的 刚 度: ! , ! "# # &’( [ ) %! ($ * !) +,-"+,-#] 。即只要机床切削点的刚度满足上式要求, 就可以保证机床不产生自振。 根据对电主轴系统精度和刚度的验算, 确定了主 轴前轴颈直径 $ . /0 ((, 主轴内孔直径 % . 10 ((, 选 取前、 后滚动轴承之间的支承距离 & . !20 ((, 轴端的 所选前轴承 45632$147! 的径向跳 悬伸量 ’ . 30 ((, 动量 $$ . ! !(, 后轴承 45632$$47! 的径向跳动量 $% . ! !(, 主轴锥孔对支承轴颈的径向跳动量 $ . ()% * % . 28 22$0 !(, 可以满足主#$ ) %&’’( !"#$ ) &)*’+ ,"--".# ,)/)+"0’( 1&".(-’ 2’3’-)&4’./ 5)+ ,67$".".# 8’./’+%
*+, -./ ! ,*012 345678 " ,90+, :7;5. " ( !<=>88? 8@ A4=>.BC8/5= 1/65/44C5/6 ,D5E./ F4=>/8?865=.? G/5H4CI5BJ,D5E./, "$%%&’ *02; ./ K5.8B8/6 G/5H4CI5BJ,D5’ ./, "$%%!( *02) "<=>88? 8@ A4=>./5=.? 1/65/44C5/6,D5’ !"#$%&’$:+ >56> ) IL44M >56> ) L8N4C O5??5/6 IL5/M?4 @8C O.=>5/5/6 =4/B4CI 5I M4H4?8L4M B8 C4.?5P4 >56> ) IL44M ./M >56> ) .==7C.=J O.=>5/4Q + IL5/M?4 @5/5B4 4?4O4/B O8M4? 5I =8/IBC7=B4M , 5/=?7M5/6 IBC7=B7C.? I5OL?5R @5=.B58/,4?4O4/B BJL4 I4?4=B58/,IBC7=B7C4 I7SM5H5I58/,=8/IBC.5B 4IB.S?5I>O4/B,?8.M M4B4CO5/.B58/, .MM5B58/.? O.II .BB.=>O4/B,4B=Q Q F>4 LC.=B5=.? B4IB5/6 M.B4 I>8N B>.B 5BI IB.B5= C565M5BJ,IB.B5= C4H8?7B58/ .==7C.=J ,./M O.=>5/5/6 .==7C.=J .==8CM N5B> B>4 C4T75C4O4/BIQ ()*+,%-#:U5CB7.? VC8B8BJL5/6 <5O7?.B58/;A5??5/6 A8B8C5P4M <L5/M?4;<B.B5= W4>.H58C;XJ/.O5= W4>.H58C;Y5/5B4 1?4O4/B +/.?JI5I 随着高速切削技术的发展和功率电子器件、 微电 子器件、 计算机技术等的发展, 在 ’% 世纪 Z% 年代末、 (% 年代初出现了用于铣削、 钻削、 车削及加工中心等 加工的大功率、 大转矩、 高转速的电主轴
[ $ [ &]