环氧丙烷生产方法与工艺
环氧丙烷氯化法、共氧化法和直接氧化法技术路线解析
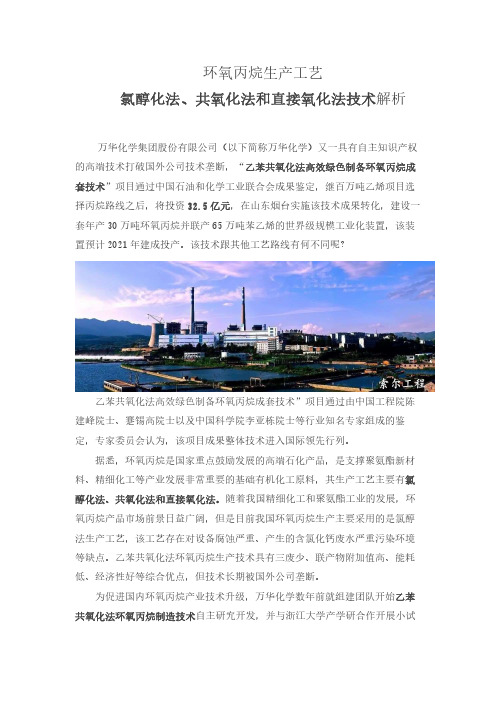
环氧丙烷生产工艺氯醇化法、共氧化法和直接氧化法技术解析万华化学集团股份有限公司(以下简称万华化学)又一具有自主知识产权的高端技术打破国外公司技术垄断,“乙苯共氧化法高效绿色制备环氧丙烷成套技术”项目通过中国石油和化学工业联合会成果鉴定,继百万吨乙烯项目选择丙烷路线之后,将投资32.5亿元,在山东烟台实施该技术成果转化,建设一套年产30万吨环氧丙烷并联产65万吨苯乙烯的世界级规模工业化装置,该装置预计2021年建成投产。
该技术跟其他工艺路线有何不同呢?乙苯共氧化法高效绿色制备环氧丙烷成套技术”项目通过由中国工程院陈建峰院士、蹇锡高院士以及中国科学院李亚栋院士等行业知名专家组成的鉴定,专家委员会认为,该项目成果整体技术进入国际领先行列。
据悉,环氧丙烷是国家重点鼓励发展的高端石化产品,是支撑聚氨酯新材料、精细化工等产业发展非常重要的基础有机化工原料,其生产工艺主要有氯醇化法、共氧化法和直接氧化法。
随着我国精细化工和聚氨酯工业的发展,环氧丙烷产品市场前景日益广阔,但是目前我国环氧丙烷生产主要采用的是氯醇法生产工艺,该工艺存在对设备腐蚀严重、产生的含氯化钙废水严重污染环境等缺点。
乙苯共氧化法环氧丙烷生产技术具有三废少、联产物附加值高、能耗低、经济性好等综合优点,但技术长期被国外公司垄断。
为促进国内环氧丙烷产业技术升级,万华化学数年前就组建团队开始乙苯共氧化法环氧丙烷制造技术自主研究开发,并与浙江大学产学研合作开展小试工艺技术研究。
为突破技术封锁,万华化学的近百名科技人员参与了该项目的研发,并在核心催化剂、反应器关键装备及相关工艺上申请国内外发明专利18件,形成了自主知识产权保护。
同时,万华化学自主设计建成的年产500吨环氧丙烷并联产1100吨苯乙烯工业化试验装置,也一次投料试车成功,并累计实现稳定运行超过90天。
未来,万华化学将投资32.5亿元,在山东烟台实施该技术成果转化,建设一套年产30万吨环氧丙烷并联产65万吨苯乙烯的世界级规模工业化装置,该装置预计2021年建成投产。
环氧丙烷工艺技术概况

环氧丙烷工艺技术概况a)氯醇法氯醇法是传统的环氧丙烷工业生产路线,该法自20世纪30年代由美国UCC公司开发并进行工业生产以来,一直是生产环氧丙烷的主要方法。
截止到2009年6月,全球环氧丙烷的总生产能力约810万吨/年,其中氯醇法占33.58%。
氯醇法分为以石灰为皂化原料的传统氯醇法和以电解液(NaOH)为皂化原料的改良氯醇法。
1)传统氯醇法主要专利商:美国Dow Chemical、日本Asahi glass公司、Mitsui Chemicals和Showa denko 公司、意大利Enichem公司等。
主要工艺过程:丙烯、氯气和水按一定配比送入氯醇化反应器中进行反应,未反应的丙烯与反应中产生的HCl及部分的二氯丙烷等自反应器顶部排出,经冷凝除去氯化氢和有机氯化物,丙烯循环回用。
反应器底部得到氯丙醇质量分数为4~5%的盐酸溶液。
将该溶液与过量约10%的石灰乳混合后送入皂化塔中皂化,再经精馏即可得到环氧丙烷。
优点:传统氯醇法具有流程比较短,工艺成熟,操作负荷弹性大,产品选择性好、收率高,生产比较安全,对原料丙烯纯度的要求不高,投资少,无引起市场干扰的联产产品,其产品具有较强的低成本竞争力等优点。
缺点:传统氯醇法存在的最大问题是设备易于腐蚀,在生产过程中产生大量含氯污水(每吨产品约产生45~60吨废水和2.1吨氯化钙)废渣,该废水具有温度、pH值、氯根含量、COD含量和悬浮物含量“五高”的特点,处理成本高,造成严重的环境污染。
世界上大多数发展中国家和地区采用传统氯醇法技术,装置规模都比较小。
例如:俄罗斯、东欧、巴西、印度和中国。
少数发达国家的老装置也在使用该技术(如日本、德国),面临被淘汰。
2)改良氯醇法主要专利商:美国Dow Chemical和意大利Enichem公司。
主要工艺过程:改良氯醇法是用烧碱代替石灰乳,在常压或减压条件下于80~130℃与氯丙醇发生皂化反应。
该法提高了氯丙醇的转化率和环氧丙烷的收率,同时抑制了皂化副反应的发生,提高了环氧丙烷的选择性。
环氧丙烷

编辑本词条缺少信息栏,补充相关内容使词条更完整,还能快速升级,赶紧来编辑吧!环氧丙烷,又名氧化丙烯、甲基环氧乙烷,是非常重要的有机化合物原料,是仅次于聚丙烯和丙烯腈的第三大丙烯类衍生物。
环氧丙烷为无色醚味液体,低沸点、易燃。
有手性,工业品一般为两种对映体的外消旋混合物。
与水部分混溶,与乙醇、乙醚混溶。
与戊烷、戊烯、环戊烷、环戊烯、二氯甲烷形成二元共沸混合物。
有毒,对粘膜和皮肤有刺激性,可损伤眼角膜和结膜,引起呼吸系统疼痛,皮肤灼伤和肿胀,甚至组织坏死。
目录1基本信息2安全术语3风险术语4制备5应用6理化性质7四氯化碳8运作流程9安全毒性10主要用途11生产方法▪简介▪⑴氯醇法▪⑵共氧化法▪⑶异丙苯氧化法▪⑷(HPPO法)▪⑸氧气直接氧化法12行业发展▪发展历程▪市场需求层次▪存在的问题▪未来发展前景13安全信息1基本信息编辑中文名称环氧丙烷[1]中文别名氧化丙烯;PO;甲基环氧乙烷;(±)-环氧丙烷英文名称:Propylene oxide;简称:PO英文别名1,2-Epoxypropane; Methyloxirane; Propyleneoxide,99%CAS RN:75-56-9EINECS:200-879-2[1]分子式:C3H6O分子量:58.08摩尔质量:58.08 g/mol密度:0.830 g/cm3 (20 °C)熔点:-112 °C危险品标志: F+:Highly flammable;T:Toxic;风险术语:R12:;R20/21/22:;R36/37/38:;R45:;R46:;安全术语:S45:;S53:;在水中的溶解度:易溶(405 g/L,20 °C)折射率(nD):1.3664 (20 °C)2安全术语编辑S45In case of accident or if you feel unwell, seek medical advice immediately (show the label whenever possible.)若发生事故或感不适,立即就医(可能的话,出示其标签)。
环氧丙烷的工艺流程

环氧丙烷的工艺流程
环氧丙烷是一种重要的有机化工产品,广泛应用于涂料、粘合剂、染料和树脂等领域。
下面将介绍环氧丙烷的工艺流程。
环氧丙烷的主要生产工艺是通过乙基氯和氢氧化钠反应得到丙烯醇,然后将丙烯醇进行环氧化反应得到环氧丙烷。
首先,将乙烯经过乙烯裂解装置进行裂解,裂解出的乙烯和氯气在催化剂的作用下进行氯化反应,得到乙基氯。
然后,将乙基氯和氢氧化钠在反应釜中进行反应,得到丙烯醇。
该反应为乙基氯和氢氧化钠的醇化反应。
反应后,产物经过中间处理,得到较高纯度的丙烯醇。
接下来,将丙烯醇与过氧化苯甲酰在一定温度下进行环氧化反应,得到环氧丙烷。
该反应为丙烯醇与过氧化苯甲酰的氧化反应。
反应后,产物经过过滤、脱色、蒸馏等处理步骤,得到纯度较高的环氧丙烷。
在环氧丙烷的生产过程中,需要进行反应温度、反应时间、反应压力等参数的控制。
同时,还需要对反应中的中间产物进行中间处理,以保证最终产品的纯度。
环氧丙烷的工艺流程中,还涉及到废气处理和废水处理等环保措施。
废气处理是通过收集和处理生产过程中产生的废气,将其中的有害物质净化,达到排放标准。
废水处理是指对生产过程中产生的废水进行处理,去除其中的有害物质,降低对环境的影响。
总结起来,环氧丙烷的工艺流程包括乙基氯和氢氧化钠的醇化反应和丙烯醇与过氧化苯甲酰的环氧化反应。
在生产过程中需要对反应参数进行控制,同时实施废气处理和废水处理等环保措施。
通过这些工艺步骤和控制措施,可以生产出优质的环氧丙烷产品。
(完整版)环氧丙烷工业应用和生产工艺(更新至2017年)

环氧丙烷应用和生产主要工艺路线一、环氧丙烷基础性质中文别称:氧化丙烯英文名称:Propylene Oxide(简称PO)分子式:C3H6O分子量:58.08相对密度:0.859 g/cm3(20℃)熔点:-112℃沸点:34℃环氧丙烷易溶于水,是无色透明的低沸易燃液体,具有类似醚类气味。
环氧丙烷在铁、锌等碱金属存在下易引起自聚反应,所以必须用干氮或者其他惰性气体贮存在容器内加以保护,使用不锈钢洁净容器进行贮存,不适宜长距离运输。
二、环氧丙烷的应用领域环氧丙烷(PO)是一种重要的有机化工原料,是除了聚丙烯和丙烯腈之外的第三大丙烯衍生物。
环氧丙烷主要用于聚醚多元醇以及丙二醇及丙二醇醚等的生产。
聚醚多元醇(PPG)主要用于生产聚氨酯塑料,其次用作表面活性剂(如泡沫稳定性、造纸工业消泡剂和原油破乳剂等),也可用作润滑剂和专用溶剂等。
丙二醇(PG)主要用作抗冻剂、有机溶剂等,也用于生产环氧树脂、不饱和聚酯树脂等,还用于生产医药等的重要中间体。
丙二醇醚是用途广泛的低毒性有机溶剂。
全球环氧市场主要是生产聚醚多元醇,约占70%;其次是生产丙二醇。
在我国约85%的环氧丙烷用于生产聚醚多元醇,约8%用于生产丙二醇,其次是生产丙烯酸酯(2%)和醚类(2%)。
因国内聚醚多元醇的厂家主要集中在山东、上海、江苏等地区,所以这些地区也是环氧丙烷最大的消费地。
二、环氧丙烷主要生产工艺1、氯醇法,(1931实现工业化)主要反应式:⏹氯醇化反应⏹皂化反应皂化是氯醇与碱反应制取环氧化物的过程。
氯醇法制环氧丙烷的原料消耗80年代,我国引进了日本旭硝子、日本三井、美国陶氏等公司的氯醇法技术,我国的生产企业不断对氯醇法工艺装置进行改扩建,使我国环氧丙烷的产能得到了较大的突破;但氯醇法工艺每生产1t环氧丙烷大约有40~60t含氯化物的废水和2~4t的废渣产生,这种工艺生产的废水处理非常困难,污染严重。
此外,氯醇法生产过程中产生的次氯酸也对设备有很大的腐蚀,因此,不管是从经济方面,还是环境保护方面,氯醇法生产工艺都已经不适应现代社会的发展。
环氧丙烷苯乙烯联产装置生产工艺
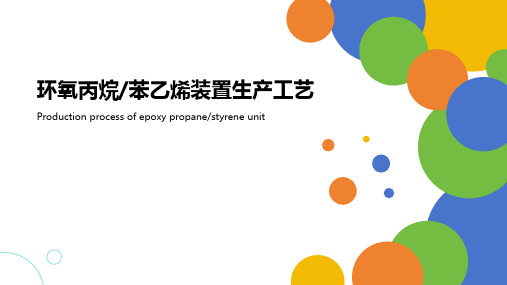
环氧丙烷/苯乙烯装置生产工艺: 原料选择与预处理是环氧丙烷/苯乙烯装置生产工艺的关 键步骤
在环氧丙烷/苯乙烯装置生产工艺中,原料选择与预处理 是至关重要的步骤。以下是该步骤的详细说明。 高品质原料,确保产品质量
环氧丙烷和苯乙烯是主要的生产原料。这两种原料应具 有高质量和低杂质,以确保最终产品的质量。在选择原 料时,应考虑其来源的稳定性、价格和供应能力。 进入生产装置前,原料需预处理,包括脱水、脱硫醇,
料
--------->
原料预处理与混合
环氧丙烷/苯乙烯装置生产工艺
1.原料预处理与混合
在环氧丙烷/苯乙烯装置的生产工艺中,原料预处理与混合 是至关重要的步骤。原料包括苯乙烯和环氧丙烷,它们在 进入反应器之前需要进行必要的处理和混合,以确保反应 的顺利进行。
苯乙烯需要经过脱水处理,以去除其中的水分和硫化氢等 杂质。通常采用沸点石脱水和冷冻干燥法进行预处理。此 外,苯乙烯还需要进行精馏操作,以去除其中的重组分和 轻组分,提高产品的纯度。
催化剂控制
环氧丙烷/苯乙烯装置生产工艺:混合与分离
环氧丙烷/苯乙烯装置生产工艺 环氧丙烷/苯乙烯生产重要化工原料
环氧丙烷(propene oxide)和苯乙烯(styrene)是两 种重要的有机化工原料,广泛应用于塑料、橡胶、涂料 、制药等行业。环氧丙烷/苯乙烯装置是一种生产这两种 原料的化工装置,其生产工艺主要包括原料预处理、环 氧丙烷合成和苯乙烯聚合等步骤。 催化剂在环氧丙烷/苯乙烯装置生产工艺中发挥关键作用
在环氧丙烷/苯乙烯装置的生产过程中,温度控制是一个关键的环节。这种工艺涉及将苯乙烯和环氧丙烷混合,然后进行反应以生成最终的产品。 为了确保反应的顺利进行,温度控制至关重要。 在反应过程中,温度的微小变化都可能导致反应速率和产品纯度的显著变化。因此,工艺工程师需要精确地控制反应温度。这通常是通过使用 热敏电阻、温度控制器和循环冷却水系统来实现的。 在反应开始之前,温度控制器会设置一个预设的温度目标值。一旦反应开始,热敏电阻会开始测量反应釜内的温度,并将数据传输到温度控制 器。如果实际温度超过了预设的限制,温度控制器会启动冷却系统,通过循环冷却水系统将热量带走,从而将温度降低到预设的目标值。
直接氧化法生产环氧丙烷工艺流程简述
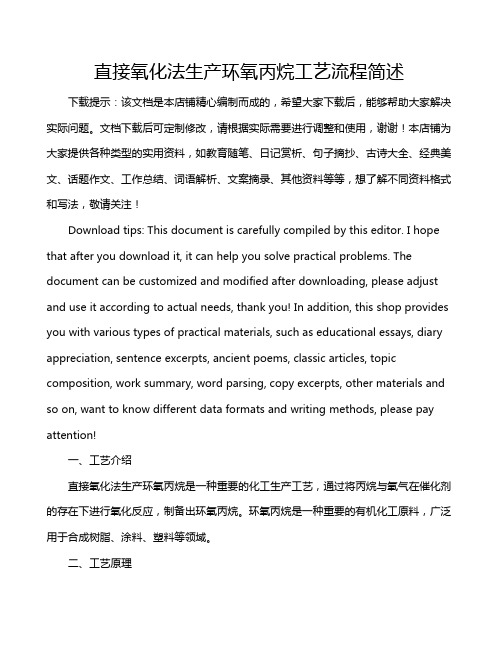
直接氧化法生产环氧丙烷工艺流程简述下载提示:该文档是本店铺精心编制而成的,希望大家下载后,能够帮助大家解决实际问题。
文档下载后可定制修改,请根据实际需要进行调整和使用,谢谢!本店铺为大家提供各种类型的实用资料,如教育随笔、日记赏析、句子摘抄、古诗大全、经典美文、话题作文、工作总结、词语解析、文案摘录、其他资料等等,想了解不同资料格式和写法,敬请关注!Download tips: This document is carefully compiled by this editor. I hope that after you download it, it can help you solve practical problems. The document can be customized and modified after downloading, please adjust and use it according to actual needs, thank you! In addition, this shop provides you with various types of practical materials, such as educational essays, diary appreciation, sentence excerpts, ancient poems, classic articles, topic composition, work summary, word parsing, copy excerpts, other materials and so on, want to know different data formats and writing methods, please pay attention!一、工艺介绍直接氧化法生产环氧丙烷是一种重要的化工生产工艺,通过将丙烷与氧气在催化剂的存在下进行氧化反应,制备出环氧丙烷。
环氧丙烷生产方法与工艺

一.环氧丙烷的简介:环氧丙烷,又名氧化丙烯、甲基环氧乙烷,是非常重要的有机化合物原料,是仅次于聚丙烯和丙烯腈的第三大丙烯类衍生物。
其结构式为:环氧丙烷在常温常压下为无色透明低沸易燃液体,具有类似醚类气味;环氧丙烷工业产品为两种旋光异构体的外消旋混合物。
凝固点-112.13℃,沸点34.24℃,相对密度(20/20℃)0.859,折射率(nD)1.3664,粘度(25℃)0.28 mPa?S。
与水部分混溶[20℃时水中溶解度40.5%(重量);水在环氧丙烷中的溶解度12.8%(重量)],与乙醇、乙醚混溶,并与二氯甲烷、戊烷、戊烯、环戊烷、环戊烯等形成二元共沸物。
有毒,对粘膜和皮肤有刺激性,可损伤眼角膜和结膜,引起呼吸系统疼痛,皮肤灼伤和肿胀,甚至组织坏死。
环氧丙烷主要用于生产聚醚多元醇、丙二醇和各类非离子表面活性剂等,其中聚醚多元醇是生产聚氨酯泡沫、保温材料、弹性体、胶粘剂和涂料等的重要原料,各类非离子型表面活性剂在石油、化工、农药、纺织、日化等行业得到广泛应用。
同时,环氧丙烷也是重要的基础化工原料。
我国环氧丙烷(PO)产业发展受技术水平、环保因素、原料供应等三方面影响,部分装置一直难以满负荷生产,2001年以后,国内PO产能、产量增幅均不是很大,而同期聚氨酯等下游消费领域需求则保持高速增长,国内供需缺口进一步拉大,见表1、表2。
表1 2005年我国PO消费结构%消费领域比例消费领域比例聚醚多元醇84.76醇醚1.87PG/DM C7.78表面活性剂等3.27碳酸丙烯酯2.33表2 2001-2005年我国PO市场供需状况统计万t/a年份产能/万t.a-1产量进口量出口量表观消费量自给率/%20 01 47.633.03.6忽略36.6 90.220 02 49.032.05.3忽略37.3 85.820 03 49.041.411.6 0.1 52.9 78.320 04 55.543.019.10.1 62.0 69.420 05 55.551.315.11.0 65.4 78.420 06E 95.569.012.1.0 80.0 85.0随着中海壳牌25万t/a装置、山东石大胜华4万t/a、天津大沽6万t/a扩建装置、山东东大3万t/a等装置的投产,截至2006年末我国PO产能已增长至95.5万t/a,同比增长72%。
环氧丙烷生产方法与工艺

环氧丙烷生产方法与工艺环氧丙烷是一种重要的有机合成原料,广泛应用于涂料、塑料、胶粘剂等化工领域。
下面将介绍环氧丙烷的生产方法和工艺。
环氧丙烷的生产方法主要有环氧化法和氯氧化法两种。
其中,环氧化法是目前应用最广泛的一种方法。
环氧化法的工艺流程如下:1.原料准备:将丙烷加入反应器中,并加入过量的过氧化氢作为氧化剂。
同时,加入催化剂,常用的催化剂有过硫酸铵或过硫酸钠。
2.氧化反应:在适宜的温度和压力下,将反应器中的丙烷和氧化剂反应,生成环氧丙烷。
3.分离纯化:将反应混合物通过蒸馏或吸附等方法进行分离纯化,得到高纯度的环氧丙烷。
环氧化法的反应条件需要控制得当。
适宜的反应温度通常在40-60℃范围内,较高的温度会导致副反应的发生,影响环氧丙烷的产率和纯度。
反应压力一般在1-2MPa之间,过高的压力会使反应剧烈,过低则会影响反应速率。
在环氧化法中,催化剂的选择也十分重要。
催化剂可以提高反应速率和环氧丙烷的产率。
目前,过硫酸铵或过硫酸钠是最常用的催化剂,在反应中起到氧化剂活化的作用。
相比之下,氯氧化法工艺相对较少应用。
该方法通过将丙烷和氯气反应,生成1,2-二氯丙烷,再经过脱氯反应生成环氧丙烷。
虽然氯氧化法原料较为简单,但由于氯气具有较高的毒性和危险性,操作风险较大,且生成的1,2-二氯丙烷需要通过脱氯反应去除氯原子,工艺相对繁琐,因此应用较少。
环氧丙烷的生产过程中有一些关键点需要注意。
首先是原料的选择和储存,丙烷的纯度和质量对于反应效果和产物纯度有很大影响。
其次是反应器的设计和选择,反应器需要耐压、抗腐蚀和优良的热传导性能。
最后是分离纯化工艺,通常采用蒸馏或吸附等方法进行分离纯化,以获取高纯度的环氧丙烷。
综上所述,环氧丙烷的生产方法主要有环氧化法和氯氧化法。
其中,环氧化法是目前应用较广泛的一种方法,具有工艺简便、原料易得等优点。
随着化工技术的不断发展,环氧丙烷的生产工艺也在不断改进,以提高产率和纯度,并减少对环境的影响。
环氧丙烷生产工艺
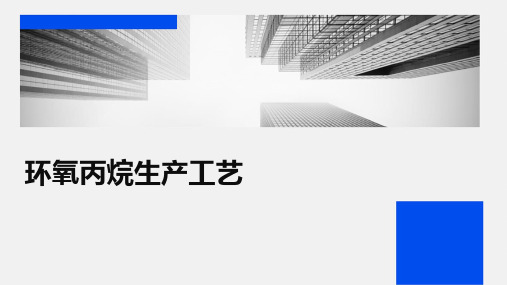
智能化
借助智能化技术实现生产过程 的自动化和信息化,提高生产 管理的效率和精度。
高效化
通过技术进步和设备更新,提 高生产效率和产品质量,降低 能耗和物耗。
多元化原料
开发利用多种原料来源,如生 物质、二氧化碳等,以降低对
传统化石资源的依赖。
THANK YOU
直接氧化法生产工艺
直接氧化法的原理
01
直接氧化法是一种通过直接将丙烯和氧气反应生成环氧丙烷的 方法。
02
该反应通常在高温和催化剂存在的条件下进行,通过自由基反
应机制,丙烯分子被氧气氧化,生成环氧丙烷和水。
催化剂在此过程中起着关键作用,它能降低反应活化能,提高
03
反应速率,并选择性地将丙烯转化为环氧丙烷。
环氧丙烷的沸点为34.2℃,凝 固点为-160.8℃,相对密度为
0.82。
它易溶于水和有机溶剂,具有 较低的蒸气压,因此在大气中
较难挥发。
环氧丙烷的应用
作为生产聚醚和聚氨酯的重要原料,用于制造泡沫塑料 、保温材料、胶粘剂等。
可用于生产润滑油添加剂、表面活性剂等。
在医药、农药、染料等精细化学品合成中用作中间体。 在石油工业中用作萃取剂和溶剂。
缺点
产生大量含盐废水,对环境造成一定 影响;同时,该方法需要使用大量酸 碱,对设备腐蚀严重,维护成本较高 。
03
共氧化法生产工艺
共氧化法的原理
共氧化法是一种利用丙烯和氧气在催化剂存在下,通过氧化反应生成环氧丙烷的方 法。
该反应过程中,丙烯首先被氧化成过氧化氢,然后过氧化氢再与丙烯反应生成环氧 丙烷和水。
环氧丙烷的生产方法
丙烯直接氧化法
01
将丙烯和氧气在催化剂的作用下直接氧化生成环氧丙烷,是最
环氧丙烷生产介绍
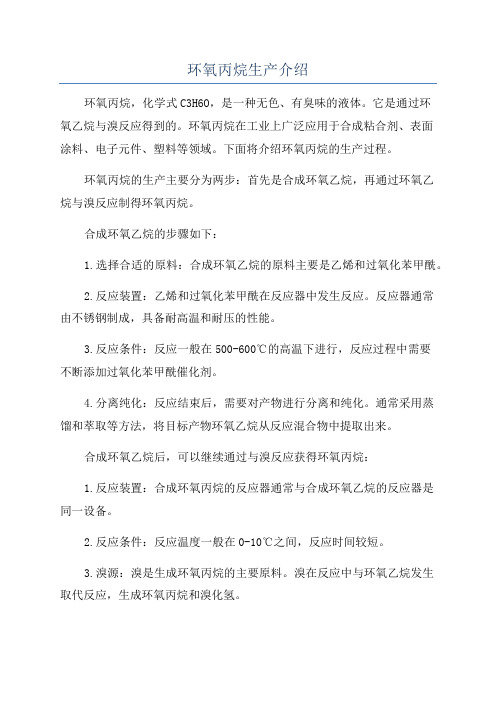
环氧丙烷生产介绍环氧丙烷,化学式C3H6O,是一种无色、有臭味的液体。
它是通过环氧乙烷与溴反应得到的。
环氧丙烷在工业上广泛应用于合成粘合剂、表面涂料、电子元件、塑料等领域。
下面将介绍环氧丙烷的生产过程。
环氧丙烷的生产主要分为两步:首先是合成环氧乙烷,再通过环氧乙烷与溴反应制得环氧丙烷。
合成环氧乙烷的步骤如下:1.选择合适的原料:合成环氧乙烷的原料主要是乙烯和过氧化苯甲酰。
2.反应装置:乙烯和过氧化苯甲酰在反应器中发生反应。
反应器通常由不锈钢制成,具备耐高温和耐压的性能。
3.反应条件:反应一般在500-600℃的高温下进行,反应过程中需要不断添加过氧化苯甲酰催化剂。
4.分离纯化:反应结束后,需要对产物进行分离和纯化。
通常采用蒸馏和萃取等方法,将目标产物环氧乙烷从反应混合物中提取出来。
合成环氧乙烷后,可以继续通过与溴反应获得环氧丙烷:1.反应装置:合成环氧丙烷的反应器通常与合成环氧乙烷的反应器是同一设备。
2.反应条件:反应温度一般在0-10℃之间,反应时间较短。
3.溴源:溴是生成环氧丙烷的主要原料。
溴在反应中与环氧乙烷发生取代反应,生成环氧丙烷和溴化氢。
4.分离纯化:类似合成环氧乙烷的分离纯化步骤,需要将环氧丙烷从反应混合物中提取出来,以获得纯净的环氧丙烷。
总结起来,环氧丙烷的生产包括合成环氧乙烷和合成环氧丙烷两个步骤。
首先,选择适当的原料,将乙烯和过氧化苯甲酰反应生成环氧乙烷。
然后,将环氧乙烷与溴反应,获得环氧丙烷。
整个过程需要合适的反应装置和条件,以及分离纯化步骤,以得到高纯度的环氧丙烷。
环氧丙烷的生产技术经过多年的发展,工艺逐渐成熟。
生产过程中需要注意安全性,确保反应装置和条件的稳定性。
环氧丙烷的广泛应用为其生产带来了巨大的发展空间,同时也推动了相关技术的创新和提高。
3万吨环氧丙烷生产工艺设计论文
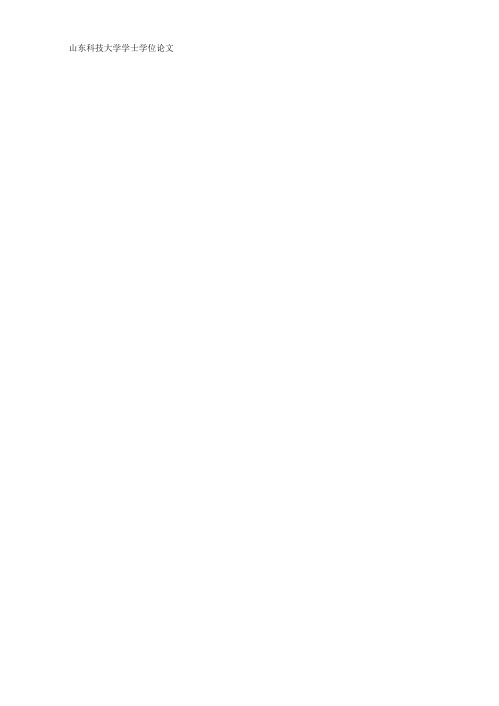
摘要设计是年产3万吨环氧丙烷的工艺设计。
设计采用了氯醇法进行环氧丙烷的生产。
主要是利用氯气和水反应生成次氯酸,然后利用次氯酸与丙烯反应生成氯丙醇,氯丙醇再进入皂化塔与氢氧化钙反应生成产品环氧丙烷。
主要模拟了反应过程的物料与热量衡算,主要精馏塔的设计,三废处理以及经济合算等问题。
设计说明书共有八章。
介绍了环氧丙烷生产工艺流程的选择和论证,对整个工艺装置进行了物料和能量衡算,对非标准设备和主要管道进行了计算和选型,最后对该工艺流程的安全生产和三废处理作了相关说明。
关键词:环氧丙烷;工艺设计;工艺流程;氯醇法ABSTRACTChlorohydrination method was adopted for the process design of the production of propylene oxide.Propylene and chlorine reacted in the presence of water to form the intermediate. and propylene chlorohydrin was dehydrochlorinated by a calcium hydroxide solution to form propylene oxide. Mainly to simulate the reaction process of the material and heat balance, the design of the main column, "three wastes" treatment and economical problems.This design contains eight paragraphs. This document is mainly to introduce the demonstration and choosing of the process design for the production of propylene oxide. The calculation of material and energy balance of propylene oxide were carried out based on the technological equipments. The non-standard equipment equipments and main pipe lines were calculated and choosed. Finally, the work safety and three industrial wastes disposal was also introduced.Keywords: propylene oxide;technological planning;process flow;chlorohydrination method目录第一章绪论 (2)1.1环氧丙烷的实际意义 (2)1.2 原料的性质 (2)1.2.1丙烯 (2)1.2.2氯气 (2)1.2.3石灰 (3)1.3环氧丙烷性质及性能 (3)1.3.1产品名称与结构式 (3)1.3.2理化性质 (3)1.3.3环氧丙烷安全与毒性 (4)1.4国内外环氧丙烷工业发展史 (4)1.4.2中国环氧丙烷工业发展史 (5)1.6技术发展趋势 (8)第二章环氧丙烷工艺的选择 (9)2.1.1氯醇法 (9)2.1.2共氧化法 (10)2.1.3 异丙苯氧化法 (10)2.1.4过氧化氢直接氧化法(HPPO法) (11)2.1.5氧气直接氧化法 (12)2.1.6电化学法 (12)2.2工艺方法的选择 (12)第三章工艺流程说明 (15)第四章物料衡算部分 (21)皂化塔的物料衡算 (25)第五章热量衡算 (30)5.1 皂化第一冷凝器 (30)5.2 皂化第二冷凝器 (31)5.3 皂化第三冷凝器 (32)5.4 工艺水加热器 (33)5.5 皂化塔热量衡算 (33)5.6 成品塔的热量衡算 (35)5.7 回收塔的热量衡算 (36)5.8 蒸汽耗量总表 (37)蒸汽的耗量见表5.3。
环氧丙烷工艺流程

环氧丙烷工艺流程
《环氧丙烷工艺流程》
环氧丙烷是一种重要的有机化工产品,广泛应用于涂料、粘合剂、塑料、橡胶和电子材料等领域。
环氧丙烷的生产工艺流程主要包括原料准备、反应釜反应、脱水、分离、精馏和产品收集等步骤。
首先是原料准备,环氧丙烷的主要原料是丙烯和氯化氢,需要通过丙烯裂解和氯化氢氧化等反应得到。
接下来是反应釜反应,将丙烯和氯化氢混合后送入反应釜进行环氧化反应,生成环氧丙烷和盐酸。
这是环氧丙烷生产的关键步骤,需要控制反应温度、压力和反应时间,以确保产品质量和产率。
然后是脱水,通过蒸馏等方式将反应产物中的水分去除,以提高产品纯度。
接着是分离,将产物中的环氧丙烷和盐酸进行分离,得到纯净的环氧丙烷产品。
然后是精馏,对环氧丙烷进行精馏,以提高产品的纯度和稳定性。
最后是产品收集,将精馏后的环氧丙烷产品进行包装、贮存和运输。
整个环氧丙烷生产工艺流程需要严格控制反应条件、分离操作和产品质量,以确保产品符合工业标准和客户需求。
同时,还需要考虑能源消耗、环境保护和安全生产等方面的因素,以促进工艺流程的可持续发展。
氯醇法制环氧丙烷精制工业流程

氯醇法制环氧丙烷精制工业流程下载温馨提示:该文档是我店铺精心编制而成,希望大家下载以后,能够帮助大家解决实际的问题。
文档下载后可定制随意修改,请根据实际需要进行相应的调整和使用,谢谢!并且,本店铺为大家提供各种各样类型的实用资料,如教育随笔、日记赏析、句子摘抄、古诗大全、经典美文、话题作文、工作总结、词语解析、文案摘录、其他资料等等,如想了解不同资料格式和写法,敬请关注!Download tips: This document is carefully compiled by theeditor. I hope that after you download them,they can help yousolve practical problems. The document can be customized andmodified after downloading,please adjust and use it according toactual needs, thank you!In addition, our shop provides you with various types ofpractical materials,such as educational essays, diaryappreciation,sentence excerpts,ancient poems,classic articles,topic composition,work summary,word parsing,copy excerpts,other materials and so on,want to know different data formats andwriting methods,please pay attention!1. 原料准备:首先,需要准备氯醇法生产环氧丙烷所需的原料,主要包括丙烯、氯气和氢气。
环氧丙烷装置生产工艺知识

环氧丙烷装置生产工艺知识环氧丙烷是一种重要的有机化工原料,广泛应用于树脂、涂料、粘合剂、电气绝缘材料等领域。
环氧丙烷的生产工艺主要包括氯丙烷法和环氧化法两种,其中环氧化法生产工艺是目前主流的生产工艺之一。
本文将介绍环氧丙烷装置生产工艺的基本原理、工艺流程和关键技术参数。
一、基本原理环氧化法是将丙烯与过氧化氢在酸性催化剂存在下进行反应,生成环氧丙烷的生产工艺。
反应方程式如下:CH2=CHCH3 + H2O2 - CH2OCHCH3 + H20反应过程中,过氧化氢起到氧化剂的作用,酸性催化剂促进了反应的进行。
反应中生成的环氧丙烷可以通过蒸镭等方法进行分离和纯化。
二、工艺流程环氧丙烷的生产工艺通常包括前处理、反应、分离和精储等环节,具体流程如下:1.前处理:丙烯和空气混合后进入预处理器,在预处理器中去除杂质和水分,然后进入储气罐。
2.反应:丙烯和过氧化氢在环氧化反应釜中反应,反应过程中加入酸性催化剂,反应结束后生成环氧丙烷。
3.分离:反应结束后,将反应混合物通过分离器进行分离,得到环氧丙烷和未反应的丙烯、过氧化氢等组分。
4.精储:通过精储,将环氧丙烷和其他组分进一步分离和纯化,得到高纯度的环氧丙烷。
三、关键技术参数环氧丙烷的生产过程中,需要注意以下关键技术参数:1.反应温度:反应温度是影响环氧丙烷产率和选择性的关键参数。
通常反应温度在70℃-90℃之间,过高或过低都会影响反应效果。
2.酸性催化剂:酸性催化剂种类和使用量的选择对反应效果有很大影响。
常用的酸性催化剂包括硫酸、磷酸等,使用量通常在0.1%-0.5%之间。
3.过氧化氢浓度:过氧化氢的浓度对反应效果也有重要影响。
通常浓度在30%-50%之间,过高或过低都会影响反应效果。
4.反应时间:反应时间也是影响反应效果的重要参数。
反应时间过短,反应不完全,反应时间过长,则会降低产率。
5.分离和纯化技术:分离和纯化环节是保证产品质量的关键步骤,通常采用蒸储等方法进行分离和纯化,可以得到高纯度的环氧丙烷。
环氧丙烷工业应用和生产工艺(更新至2017年)(最新整理)

环氧丙烷应用和生产主要工艺路线一、环氧丙烷基础性质中文别称:氧化丙烯英文名称:Propylene Oxide(简称PO)分子式:C3H6O分子量:58.08相对密度:0.859 g/cm3(20℃)熔点:-112℃沸点:34℃环氧丙烷易溶于水,是无色透明的低沸易燃液体,具有类似醚类气味。
环氧丙烷在铁、锌等碱金属存在下易引起自聚反应,所以必须用干氮或者其他惰性气体贮存在容器内加以保护,使用不锈钢洁净容器进行贮存,不适宜长距离运输。
二、环氧丙烷的应用领域环氧丙烷(PO)是一种重要的有机化工原料,是除了聚丙烯和丙烯腈之外的第三大丙烯衍生物。
环氧丙烷主要用于聚醚多元醇以及丙二醇及丙二醇醚等的生产。
聚醚多元醇(PPG)主要用于生产聚氨酯塑料,其次用作表面活性剂(如泡沫稳定性、造纸工业消泡剂和原油破乳剂等),也可用作润滑剂和专用溶剂等。
丙二醇(PG)主要用作抗冻剂、有机溶剂等,也用于生产环氧树脂、不饱和聚酯树脂等,还用于生产医药等的重要中间体。
丙二醇醚是用途广泛的低毒性有机溶剂。
全球环氧市场主要是生产聚醚多元醇,约占70%;其次是生产丙二醇。
在我国约85%的环氧丙烷用于生产聚醚多元醇,约8%用于生产丙二醇,其次是生产丙烯酸酯(2%)和醚类(2%)。
因国内聚醚多元醇的厂家主要集中在山东、上海、江苏等地区,所以这些地区也是环氧丙烷最大的消费地。
二、环氧丙烷主要生产工艺1、氯醇法,(1931实现工业化)主要反应式:⏹氯醇化反应⏹皂化反应皂化是氯醇与碱反应制取环氧化物的过程。
氯醇法制环氧丙烷的原料消耗原料规格消耗氯气(吨/吨PO)100% 1.35-1.65丙烯(吨/吨PO)100%0.82-0.86石灰(吨/吨PO)95% 1.0-2.1电(kwh/t)200-300冷却水(吨/吨PO)250-320蒸汽(吨/吨PO) 2.5-6.5工艺水(吨/吨PO)20-100副产物二氯丙烷(吨/吨PO)0.05-0.19二氯二乙丙醚(吨/吨PO)0-0.02氢气(吨/吨PO)0-0.04三废废水(吨/吨PO)40-80废渣(吨/吨PO)280年代,我国引进了日本旭硝子、日本三井、美国陶氏等公司的氯醇法技术,我国的生产企业不断对氯醇法工艺装置进行改扩建,使我国环氧丙烷的产能得到了较大的突破;但氯醇法工艺每生产1t环氧丙烷大约有40~60t含氯化物的废水和2~4t的废渣产生,这种工艺生产的废水处理非常困难,污染严重。
环氧丙烷生产工艺流程

环氧丙烷生产工艺流程
环氧丙烷是一种重要的化工原料,广泛应用于合成聚氨酯、合成洗涤剂、粘合剂、涂料等领域。
以下是环氧丙烷的生产工艺流程。
首先,环氧丙烷的生产原料主要是丙烯和过氧化氢。
丙烯是一种从石油中提取的烃类化合物,通常通过蒸馏和精制过程得到高纯度的丙烯。
而过氧化氢则通过氢气和氧气在催化剂的作用下反应生成。
其次,丙烯与过氧化氢在催化剂的存在下进行环氧化反应。
催化剂通常采用一氧化钙、双函数碱性催化剂等。
反应过程中,丙烯在催化剂的作用下与过氧化氢发生氧化反应,生成环氧丙烷。
然后,环氧丙烷的反应产物经过提纯处理。
首先,通过冷凝和分馏过程,将环氧丙烷与未反应的丙烯分离。
接下来,通过萃取和再结晶等方法,去除杂质,提高产品的纯度。
最后,通过蒸馏和干燥等工艺,得到高纯度的环氧丙烷。
最后,生产的环氧丙烷进行储存和包装。
环氧丙烷在储存过程中需要保持恒定的温度和压力,以确保产品的质量稳定。
在包装过程中,常采用钢瓶、安全桶等容器进行包装,以便运输和使用。
需要注意的是,环氧丙烷的生产过程中涉及到一些安全问题。
由于环氧丙烷易燃、爆炸性质,必须采取严格的安全措施,如
防爆装置、防静电等,确保生产过程中的安全性。
总之,环氧丙烷的生产工艺流程包括原料准备、环氧化反应、提纯处理和储存包装等环节。
通过合理的工艺控制和安全措施,可以获得高质量的环氧丙烷产品。
环氧丙烷生产工艺及市场分析

山东化工SHANDONG CHEMIPAL INDUSTRY・94・2021年第50卷环氧丙烷生产工艺及市场分析夏兵(山东德辰科技有限公司,山东东营257000)摘要:环氧 烷(PO )属 烯衍生物, 化工行业的 有机原料, 仅 聚丙烯和丙烯月青$大产聚醞多元醇(PPG )和 醇(MPG )等,进一步加工制造聚氨酯(PU ) 活性剂、乳化剂、消泡剂等。
环氧 烷的衍生物纺织、日化、防等行业’根据目产环氧丙烷所采用的生产工艺技术,重点从工艺特点、耗、 供需 进行了分析与论述’关键词:环氧丙烷%工艺流程% 析中图分类号:TQ223国+6文献标识码:A文章编号:1008-021X ( 2021) 03-0094-051生产工艺分析,氧烷的主流生产工艺 有三大类,即氯醇法、氧化法(间接氧化法)和双氧水直接氧化法。
截 2019年 末,全球范围内氯醇法工艺 全球产能的45%%共氧法工艺全球产能的54%,共氧法有 产工艺的 ,其中乙苯共氧法占全球产能的33%、异烷共氧法 全球产能的18%,双氧水直接氧化法约占全球产能的3%[1]o1.1氯醇法工艺该工艺烯和氯气为原料,采用氯醇化、皂化、精憎等工艺。
在水和氯气的混合物 过量的丙烯,经过氯醇化反 氯丙醇,反 的丙烯与反应过程中产生的氯化部分有机氯化物(二氯 烷等)经反 顶部 , 凝脱出氯化 有机氯化物, 烯 利用,反 底部产含含4%盐酸的氯丙醇溶液。
然后添加皂化剂(改良氯醇法 烧 统氯醇法的 皂化剂)对氯丙醇进行皂化粗环氧丙烷,粗氧丙烷送 进行氧丙烷产品。
氯醇法生产工艺分为氯醇单元、皂化单元、精憎 单元三部分,工艺流程如图1 。
工艺特点是技术、流程短、投资 ,反应设备大多采反 ,制造 ,选择性 高,对丙烯 的要求不高,作性大。
但氯气消耗 大,并 产过程中产生的次氯酸对设备的腐蚀严重,同时生产过程 的大量的高温含盐废水 渣(传统氯醇法)严污染 。
改良氯醇法 液 ,在100~105a 、常压条件下与氯丙醇发生皂化反应’该法有效抑制了皂化副反应 的发生、减少 醇的 ,提高了环氧丙烷的选择性和 ’目前该技术专利 美 化学公司(Dow Chemical )和意大利埃尼公司(Emchem ) 掌握。
- 1、下载文档前请自行甄别文档内容的完整性,平台不提供额外的编辑、内容补充、找答案等附加服务。
- 2、"仅部分预览"的文档,不可在线预览部分如存在完整性等问题,可反馈申请退款(可完整预览的文档不适用该条件!)。
- 3、如文档侵犯您的权益,请联系客服反馈,我们会尽快为您处理(人工客服工作时间:9:00-18:30)。
一.环氧丙烷的简介:环氧丙烷,又名氧化丙烯、甲基环氧乙烷,是非常重要的有机化合物原料,是仅次于聚丙烯和丙烯腈的第三大丙烯类衍生物。
其结构式为:环氧丙烷在常温常压下为无色透明低沸易燃液体,具有类似醚类气味;环氧丙烷工业产品为两种旋光异构体的外消旋混合物。
凝固点-112.13℃,沸点34.24℃,相对密度(20/20℃)0.859,折射率(nD)1.3664,粘度(25℃)0.28 mPa?S。
与水部分混溶[20℃时水中溶解度40.5%(重量);水在环氧丙烷中的溶解度12.8%(重量)],与乙醇、乙醚混溶,并与二氯甲烷、戊烷、戊烯、环戊烷、环戊烯等形成二元共沸物。
有毒,对粘膜和皮肤有刺激性,可损伤眼角膜和结膜,引起呼吸系统疼痛,皮肤灼伤和肿胀,甚至组织坏死。
环氧丙烷主要用于生产聚醚多元醇、丙二醇和各类非离子表面活性剂等,其中聚醚多元醇是生产聚氨酯泡沫、保温材料、弹性体、胶粘剂和涂料等的重要原料,各类非离子型表面活性剂在石油、化工、农药、纺织、日化等行业得到广泛应用。
同时,环氧丙烷也是重要的基础化工原料。
我国环氧丙烷(PO)产业发展受技术水平、环保因素、原料供应等三方面影响,部分装置一直难以满负荷生产,2001年以后,国内PO产能、产量增幅均不是很大,而同期聚氨酯等下游消费领域需求则保持高速增长,国内供需缺口进一步拉大,见表1、表2。
表1 2005年我国PO消费结构%消费领域比例消费领域比例聚醚多元醇84.76醇醚1.87PG/DM C7.78表面活性剂等3.27碳酸丙烯酯2.33表2 2001-2005年我国PO市场供需状况统计万t/a年份产能/万t.a-1产量进口量出口量表观消费量自给率/%20 01 47.633.03.6忽略36.6 90.220 02 49.032.05.3忽略37.3 85.820 03 49.041.411.6 0.1 52.9 78.320 04 55.543.019.10.1 62.0 69.420 05 55.551.315.11.0 65.4 78.420 06E 95.569.012.1.0 80.0 85.0随着中海壳牌25万t/a装置、山东石大胜华4万t/a、天津大沽6万t/a扩建装置、山东东大3万t/a等装置的投产,截至2006年末我国PO产能已增长至95.5万t/a,同比增长72%。
中海壳牌25万t/a乙苯共氧化法装置的投产,打破了我国PO生产单纯依赖氯醇法的格局,对于推动我国PO生产技术的提高将产生积极的作用。
2005年我国PO生产企业产能见表3。
表3 2005年我国PO生产企业产能统计万t/a生产企业地址工艺路线产能锦化化工集团氯碱股份有限公司辽宁葫芦岛氯醇法12.5山东滨化集团有限公司山东滨州氯醇法9.中石化上海高桥石化公司上海氯醇法8.天津大沽化工有限责任公司天津氯醇法8.江苏钟山化工有限公司江苏南京氯醇法4.沈阳金碧兰化工有限公司辽宁沈阳氯醇法4.山东东大化学工业有限公司山东淄博氯醇法3.福建湄洲湾氯碱工业有限公司福建泉州氯醇法2.浙江太平洋化学有限公司浙江宁波氯醇法2.江西九江化工厂江西九江氯醇法2.中石化巴陵石油化工有限公司湖南岳阳氯醇法1.总计55.5在我国PO市场中,中海壳牌、锦西化工、天津大沽、上海高化、山东滨化等厂商在市场中占有重要位置。
我国主要PO生产企业多同时生产聚醚,不生产聚醚的PO企业目前仅山东滨化和巴陵石化两家。
在2006年我国的PO市场已经陷入低迷,但未来几年我国新、扩建PO项目依然非常密集。
2007年我国PO产能将至少新增26万t/a,至2009年我国PO产能将达156.5万t/a,由此可能出现严重的供过于求。
未来3年我国新扩产PO项目见表4。
表4未来3年我国投产PO项目统计万t/a公司名称公司地址工艺方法产能投产时间福建湄洲湾氯碱集团(扩产)泉州福建氯醇法5.02007山东东成集团东营山东氯醇法6.02007山东兖矿集团兖州山东氯醇法5.02007江苏钟山化工集团(与锦湖合资)南京江苏氯醇法10.2007山东金岭集团东营山东氯醇法10.200镇海炼化(与莱昂德尔合资)宁波浙江PO/SM法28.20092007年华东、华南地区市场变化主要看福建湄洲湾装置的扩产情况,扩产后其产能将达5万t,但因聚醚产能也相应扩大,故其PO供应仍需要外购。
华东、华北地区,由于PO 需求量较大,一直是各大供应商主要争夺的市场。
随着山东地区东成集团、兖矿集团2套PO 装置的投用,市场竞争将变得更加的激烈。
东北地区由于地理原因,市场变化将不会太大,主要是看锦西化工、沈阳金碧兰的供应情况。
2007年PO市场价格的走势将主要取决于上下游的影响。
由于新增产能较多,PO供应将不再成为影响市场的主要问题,上游丙烯和下游聚醚的市场变化将成为左右市场的主导因素。
但因竞争激烈,所以不大可能达到2005年1.7万元/t的高价,市场预计将以稳为主,而行业利润也不再可能达到以前的水平。
二.环氧丙烷的生产方法环氧丙烷是重要的丙烯衍生物,每年约7%的丙烯用于环氧丙烷生产。
生产工艺主要有氯醇化法、共氧化法(也称间接氧化法)和直接氧化法。
目前世界生产环氧丙烷的主要工业化方法为氯醇化法和共氧化法,其中共氧化法又分为乙苯共氧化法和异丁烷共氧化法。
近几年,异丙苯氧化法和过氧化氢直接氧化法已开发成功并先后实现工业化生产,以氧气作为氧化剂的直接氧化法也在开发中。
(1)氯醇法氯醇法生产历史悠久,工业化已有60多年,以美国陶氏化学(DowChemical)公司的氯醇法为代表。
氯醇法的主要工艺过程为丙烯氯醇化、石灰乳皂化和产品精制,其特点是生产工艺成熟、操作负荷弹性大、选择性好,对原料丙烯的纯度要求不高,从而可提高生产的安全性,建设投资少。
由于固定资产投入少,产品成本较低,其产品具有较强的成本竞争力。
目前世界环氧丙烷约40%的产能为氯醇法。
氯醇法的缺点是水资源消耗大,产生大量废水和废渣,每生产1t环氧丙烷产生40~50t含氯化物的皂化废水和2t以上的废渣,该废水具有温度高、pH值高、氯根含量高、COD含量高和悬浮物含量高的“五高”特点,难以处理。
同时,氯醇法还消耗大量高能耗的氯气和石灰原料,而氯和钙在废水和废渣中排放掉,生产过程中产生的次氯酸对设备的腐蚀也比较严重。
中国环氧丙烷生产始于20世纪60年代,采用自行开发的氯醇法工艺路线。
20世纪80年代末和90年代初,中国先后引进了日本旭硝子公司、三井东压公司、昭和电工公司和美国陶氏公司氯醇法技术,锦化化工、山东滨化、中石化上海高桥石化、天津大沽化工等企业环氧丙烷装置建成投产后取得了较好的经济效益,生产水平得到较大提高。
目前,除中海壳牌25万t/a环氧丙烷装置采用共氧化法外,国内现有80%的环氧丙烷产能使用氯醇法。
(2)共氧化法共氧化法又称哈康法,包括异丁烷共氧化法和乙苯共氧化法2种,分别由异丁烷或乙苯与丙烯进行共氧化反应,生成叔丁醇或苯乙烯,同时联产环氧丙烷。
共氧化法由美国奥克兰公司开发,现为美国莱昂德尔(Lyondell,也译为利安德)公司所有。
共氧化法克服了氯醇法的腐蚀大、污水多等缺点,具有产品成本低(联产品分摊成本)和环境污染较小等优点。
自1969年工业化以来,在世界范围发展迅速,目前,共氧化法环氧丙烷产能已占世界总产能的55%左右。
共氧化法的缺点是工艺流程长,原料品种多,丙烯纯度要求高,工艺操作在较高的压力下进行,设备材质多采用合金钢,设备造价高,建设投资大。
同时,环氧丙烷在共氧化法生产中,只是1个产量较少的联产品,每吨环氧丙烷要联产2.2~2.5t苯乙烯或2.3t叔丁醇,原料来源和产品销售相互制约因素较大,必须加以妥善解决,只有环氧丙烷和联产品市场需求匹配时才能显现出该工艺的优势。
此外,共氧化法产生的污水含COD也比较高,处理费用约占总投资的10%。
国内环氧丙烷生产一直采用氯醇法工艺。
2006年3月,随着中海壳牌年产25万t环氧丙烷装置投产,环氧丙烷生产格局发生一定变化。
中海壳牌项目是目前国内最大的1套环氧丙烷装置,也是唯一采用环氧丙烷/苯乙烯共氧化联产法工艺的环氧丙烷装置。
预计2009年底,Lyondell与中石化合资在镇海建设的28万t/a共氧化法环氧丙烷生产装置将建成投产。
(3)异丙苯氧化法异丙苯氧化法由日本住友(Sumitomo)化学公司开发,采用钛基催化剂的固定床反应器,以过氧化氢异丙苯(CHP)为氧化剂,CHP使丙烯环氧化得到环氧丙烷和二甲基苄醇,后者脱水为α-甲基苯乙烯,然后再加氢生成异丙苯,异丙苯氧化成CHP后循环使用。
异丙苯氧化法实际是共氧化法的1种改进,与共氧化法的主要区别在于使用异丙苯替代了乙苯,并且异丙苯循环使用,不产生联产品。
由于该工艺无需联产苯乙烯所需的辅加设备,装置投资费用比共氧化法约低1/3,也无需使用氯气的氯醇法工艺所需的防腐设备。
2003年5月,住友化学公司投资1亿多美元,在日本千叶建成采用其独有异丙苯氧化法工艺的20万t/a环氧丙烷装置。
此外,住友与沙特阿拉伯-美国石油公司(SaudiAramco)在沙特的合资企业也将采用住友异丙苯氧化法技术建设20万t/a的环氧丙烷装置。
(4)过氧化氢直接氧化法(HPPO法)过氧化氢真接氧化法是由过氧化氢(双氧水)催化环氧化丙烯制环氧丙烷的新工艺,生产过程中只生成环氧丙烷和水,工艺流程简单,产品收率高,没有其他联产品,基本无污染,属于环境友好的清洁生产系统。
目前过氧化氢真接氧化法工艺分别由赢创工业集团(原德固萨,Degussa)与伍德(Uhde)公司、陶氏化学和巴斯夫(BASF)公司联合开发和工业化推广。
2001年,赢创工业集团和伍德公司在德国法兰克福建设了1套过氧化氢法试验性装置,测试最佳催化剂和测定临界参数,并开始对技术进行工业化设计。
2003年,赢创推出该技术的商业化工艺包。
2006年5月,韩国环氧丙烷和聚酯薄膜生产商SKC公司从赢创和伍德购买专利,开始在韩国蔚山建设世界第1套过氧化氢法环氧丙烷装置,该装置生产规模为10万t/a,2008年7月已建成投产,生产运行良好。
赢创工业集团正在与俄罗斯天然气寡头Gazprom的子公司Sibur谈判,计划在俄罗斯建设过氧化氢和环氧丙烷联合生产装置。
2001年,陶氏化学从EniChem公司购买了利用过氧化氢作为氧化剂来生产环氧丙烷的实验室技术,还包括在意大利的1套试验装置。
2003年,陶氏化学和巴斯夫开始合作开发过氧化氢法技术并将其商业化。
2006年,陶氏化学与巴斯夫公司共同宣布在比利时安特卫普合资建设30万t/a过氧化氢法环氧丙烷装置,计划于2009年初建成投产。
2008年6月,陶氏化学与泰国SiamCement集团(SCG)合资建立的SCG-DOW集团在泰国的环氧丙烷装置动工,使用陶氏与巴斯夫联合开发的过氧化氢法工艺,产能为39万t/a,该项目预计将于2011年投入运营。