石墨加工工艺
石墨造粒工艺

石墨造粒工艺石墨造粒工艺是一种将石墨材料加工成颗粒状的工艺过程。
石墨是一种特殊的非金属材料,具有良好的导电性、导热性和耐高温性能,因此在许多领域有着广泛的应用。
石墨造粒工艺可以改善石墨材料的使用性能和加工工艺,并扩大其应用范围。
石墨造粒工艺的目的是将石墨材料加工成具有一定形状和尺寸的颗粒。
首先,需要选择合适的石墨原料。
石墨可以分为天然石墨和人工石墨两种类型,根据不同的需求选择合适的石墨原料。
然后,将石墨材料进行破碎和研磨,使其变成一定粒度的石墨粉末。
研磨过程中需要注意控制研磨时间和研磨介质的选择,以保证石墨粉末的质量和粒度分布。
接下来,通过造粒机将石墨粉末进行造粒。
造粒机主要有压力造粒机和挤压造粒机两种类型。
压力造粒机通过一定的压力将石墨粉末压制成颗粒状,该方法适用于较细的石墨粉末。
挤压造粒机则利用挤压力将石墨粉末挤压成颗粒状,该方法适用于较粗的石墨粉末。
在造粒过程中,需要控制造粒机的参数,如压力、温度和速度,以获得理想的造粒效果。
完成造粒后,还需要进行干燥和筛分处理。
干燥过程可以去除石墨颗粒中的水分,提高石墨颗粒的质量。
筛分过程可以分离出不同粒度的石墨颗粒,以满足不同应用的需求。
干燥和筛分的参数需要根据具体情况进行调整,以获得理想的处理效果。
石墨造粒工艺的优点在于可以改善石墨材料的使用性能和加工工艺。
通过造粒,可以提高石墨材料的流动性和均匀性,便于在生产过程中的加工和使用。
此外,石墨颗粒还可以通过配方设计和表面处理等方法进行功能改性,以满足不同行业和领域的需求。
石墨颗粒的应用范围广泛,包括电池、涂料、橡胶、塑料、涂料、摩擦材料等领域。
石墨造粒工艺是一种重要的石墨加工方法,可以改善石墨材料的使用性能和加工工艺。
通过选择合适的石墨原料、破碎研磨、造粒、干燥和筛分等工艺步骤,可以获得具有一定形状和尺寸的石墨颗粒。
石墨颗粒的应用范围广泛,可以满足不同行业和领域的需求,具有很高的经济和社会价值。
石墨造粒工艺的发展将进一步推动石墨材料的应用和推广,为相关行业的发展做出积极贡献。
高纯石墨提炼工艺流程
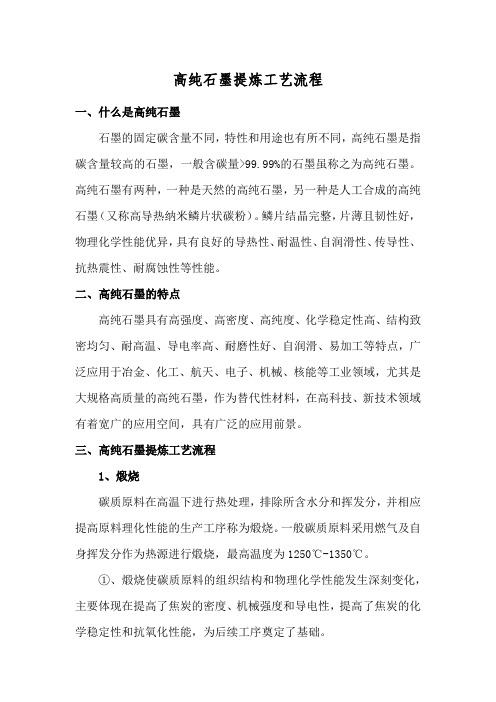
高纯石墨提炼工艺流程一、什么是高纯石墨石墨的固定碳含量不同,特性和用途也有所不同,高纯石墨是指碳含量较高的石墨,一般含碳量>99.99%的石墨虽称之为高纯石墨。
高纯石墨有两种,一种是天然的高纯石墨,另一种是人工合成的高纯石墨(又称高导热纳米鳞片状碳粉)。
鳞片结晶完整,片薄且韧性好,物理化学性能优异,具有良好的导热性、耐温性、自润滑性、传导性、抗热震性、耐腐蚀性等性能。
二、高纯石墨的特点高纯石墨具有高强度、高密度、高纯度、化学稳定性高、结构致密均匀、耐高温、导电率高、耐磨性好、自润滑、易加工等特点,广泛应用于冶金、化工、航天、电子、机械、核能等工业领域,尤其是大规格高质量的高纯石墨,作为替代性材料,在高科技、新技术领域有着宽广的应用空间,具有广泛的应用前景。
三、高纯石墨提炼工艺流程1、煅烧碳质原料在高温下进行热处理,排除所含水分和挥发分,并相应提高原料理化性能的生产工序称为煅烧。
一般碳质原料采用燃气及自身挥发分作为热源进行煅烧,最高温度为1250℃-1350℃。
①、煅烧使碳质原料的组织结构和物理化学性能发生深刻变化,主要体现在提高了焦炭的密度、机械强度和导电性,提高了焦炭的化学稳定性和抗氧化性能,为后续工序奠定了基础。
煅烧设备主要有罐式煅烧炉、回转窑和电煅烧炉。
煅烧质量控制指标是石油焦真密度不小于cm3,电阻率不大于550μΩ.m,针状焦真密度不小于cm3,电阻率不大于500μΩ.m。
②、原料的破碎处理和配料在配料之前,须对大块煅后石油焦和针状焦进行中碎、磨粉、筛分处理中碎:通常是将50mm左右的物料通过颚式破碎机、锤式破碎机等破碎设备进一步破碎到配料所需的磨粉:通过磨粉机(球磨机、环棍式环辊磨粉机)将碳质原料磨细到粒径以下的粉末状小颗粒的过程。
筛分:通过具有均匀开孔的一系列筛子,将破碎后尺寸范围较宽的物料分成尺寸范围较窄的几种颗粒粒级的过程。
配料:是按配方要求,对各种粒度的骨料和粉料、粘结剂分别计算、称量、聚焦的生产过程。
石墨管的加工工艺流程

石墨管的加工工艺流程石墨管是一种具有出色导电、导热性能的材料,通常用于电子元件、热管理、化学工程等领域。
为了制造出高质量的石墨管产品,需要经过多道工艺流程。
首先,原料的准备是制造石墨管的关键。
石墨是石墨管的主要材料,其纯度和微观结构对产品质量有很大影响。
通常采用高纯度天然石墨作为原料,经过研磨、筛分等步骤,得到适合石墨管制造的粉末。
接下来,石墨粉末被加入到粘结剂中,形成可以被挤压和成型的石墨糊。
常用的粘结剂包括聚合物、树脂等,其作用是增加石墨糊的可塑性和粘结力。
为了获得均匀的石墨糊,需要对粉末和粘结剂进行混合搅拌并控制搅拌时间。
随后,石墨糊被注入到金属模具中,进行挤压成型。
挤压过程中,石墨糊会通过模具的孔道形成圆形或方形的石墨坯。
挤压过程需要控制挤压速度和压力,以确保石墨坯的形状和尺寸的一致性。
经过成型后,石墨坯需要经过高温烘烤和高温处理来去除粘结剂。
首先进行烘烤,将石墨坯置于烘炉中,在逐渐升高的温度下,粘结剂会被蒸发和分解,石墨坯逐渐变得坚硬。
接下来进行高温处理,将石墨坯置于高温炉中进行石墨化。
高温处理温度通常在2000°C以上,石墨坯在高温下逐渐结晶成石墨,形成完整的石墨管结构。
高温处理时间和温度的控制非常重要,这将影响石墨管的结晶度和导电性能。
最后一道工艺是石墨管的表面处理。
石墨管的表面处理可以选择涂覆保护层,增加抗氧化、耐腐蚀性能,也可以进行喷砂、抛光等工艺,提高外观光洁度。
表面处理的选择和工艺对石墨管的使用寿命和性能有重要影响。
总而言之,制造石墨管需要经过原料准备、石墨糊制备、挤压成型、烘烤处理、高温处理和表面处理等多道工艺流程。
每个环节都需要严格控制工艺参数,以确保石墨管的质量。
同时,了解石墨管的加工工艺流程,对于生产石墨管产品的厂商和相关行业的从业人员具有重要的指导意义。
石墨化工艺
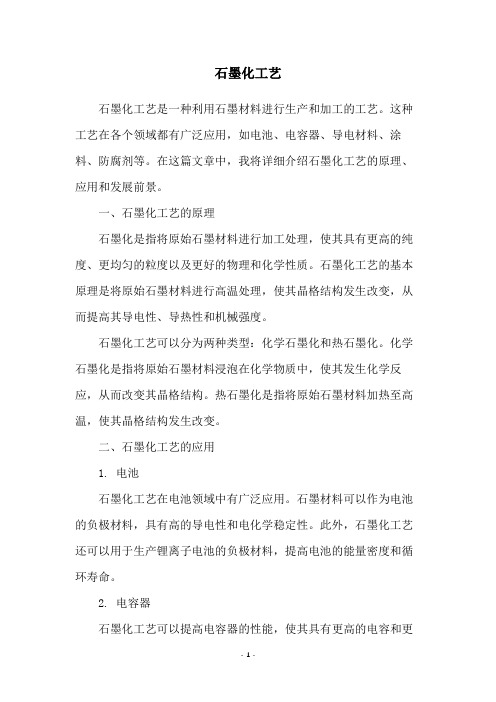
石墨化工艺石墨化工艺是一种利用石墨材料进行生产和加工的工艺。
这种工艺在各个领域都有广泛应用,如电池、电容器、导电材料、涂料、防腐剂等。
在这篇文章中,我将详细介绍石墨化工艺的原理、应用和发展前景。
一、石墨化工艺的原理石墨化是指将原始石墨材料进行加工处理,使其具有更高的纯度、更均匀的粒度以及更好的物理和化学性质。
石墨化工艺的基本原理是将原始石墨材料进行高温处理,使其晶格结构发生改变,从而提高其导电性、导热性和机械强度。
石墨化工艺可以分为两种类型:化学石墨化和热石墨化。
化学石墨化是指将原始石墨材料浸泡在化学物质中,使其发生化学反应,从而改变其晶格结构。
热石墨化是指将原始石墨材料加热至高温,使其晶格结构发生改变。
二、石墨化工艺的应用1. 电池石墨化工艺在电池领域中有广泛应用。
石墨材料可以作为电池的负极材料,具有高的导电性和电化学稳定性。
此外,石墨化工艺还可以用于生产锂离子电池的负极材料,提高电池的能量密度和循环寿命。
2. 电容器石墨化工艺可以提高电容器的性能,使其具有更高的电容和更低的内阻。
石墨材料可以作为电容器的电极材料,具有良好的导电性和化学稳定性。
3. 导电材料石墨化工艺可以生产高纯度的石墨粉末,用于制造导电材料。
石墨材料具有良好的导电性和导热性,可以用于制造电线、电缆等导电材料。
4. 涂料石墨化工艺可以将石墨材料制成涂料,用于防腐、防水、隔热等领域。
石墨涂料具有良好的耐腐蚀性和耐高温性,可以用于制造船舶、化工设备等防腐涂料。
三、石墨化工艺的发展前景随着科技的不断发展,石墨化工艺在各个领域都有广泛的应用和发展前景。
未来,随着人们对环境保护的关注和对新能源的需求,石墨化工艺将会在电池、电容器、导电材料等领域发挥更加重要的作用。
此外,随着人工智能、5G等新兴技术的发展,对高性能材料的需求不断增加,石墨化工艺也将有更广泛的应用。
未来,石墨化工艺将会在更多领域发挥作用,为人类的生产和生活带来更多的便利和效益。
石墨板的生产工艺

石墨板的生产工艺石墨板是一种由石墨粉和树脂组成的复合材料,常用于电子元件、热传导、电磁屏蔽等领域。
下面将介绍石墨板的生产工艺。
首先,石墨板的生产过程主要包括原材料准备、混合、成型、固化和加工五个步骤。
原材料准备阶段,需要准备石墨粉和树脂,其中石墨粉是石墨板的主要成分,树脂则用来起到粘合和固化的作用。
石墨粉通常使用高纯度的天然石墨经过粉碎、筛分等工艺得到,而树脂则选择适合石墨粉的树脂进行配制。
混合阶段,将事先确定好比例的石墨粉和树脂加入混合机中进行充分搅拌。
这个过程中需要控制好搅拌时间和搅拌速度,以保证石墨粉和树脂能够均匀混合,形成均匀分散的石墨/树脂混合体。
成型阶段,将混合好的石墨/树脂混合体放入模具中进行成型。
成型有两种常用的方法,一种是压制成型,另一种是浇注成型。
在压制成型中,将混合体放入压制机中进行压制,压力和时间需要根据具体情况来确定。
而在浇注成型中,则是将混合体倒入已经设计好形状的模具中,然后通过振动和震动等加工方式来排除气泡,使混合体充分填充到模具中。
固化阶段,成型好的石墨板需要经过固化过程。
固化的目的是让树脂起到粘合的作用,并形成结构稳定的石墨板。
固化的方式有很多种,可以是自然固化,也可以是通过加热、加压等方法来加快固化过程。
最后,经过固化的石墨板需要进行加工和磨光。
加工过程包括切割、打孔等工艺,以得到符合要求的石墨板尺寸。
磨光过程则是将石墨板表面进行抛光,使其得到更好的光洁度和平整度。
综上所述,石墨板的生产工艺包括原材料准备、混合、成型、固化和加工五个步骤。
通过控制好每个步骤的工艺参数,可以制造出具有良好性能的石墨板产品。
石墨生产工艺介绍

石墨生产工艺介绍石墨,又称为石墨材料,是一种具有良好导电、导热和润滑性能的材料,广泛应用于电子、冶金、化工等领域。
石墨的生产工艺分为自然生石墨和人工合成石墨两种。
自然生石墨的生产工艺主要分为开采、研磨和加工三个步骤。
首先,需要选取含有较高石墨矿物质的岩石,通常选取石英岩或者云母岩。
然后,通过开采方法将石墨矿石从矿脉中提取出来,常用的开采方法有露天开采和井下开采。
露天开采适用于矿脉露头较大的情况,通过爆破和拆卸等手段将矿石提取出来;井下开采适用于矿脉露头较小或者埋深较大的情况,需要通过井下隧道或者井筒将矿石运出地下。
提取出的石墨矿石经过研磨处理,主要目的是将石墨矿石的杂质去除,获得纯净的石墨粉末。
通常采用湿法研磨的方法,将石墨矿石与水混合并添加一定的研磨介质,通过摩擦和冲击的作用将矿石粉破碎为粉末。
研磨过程中需要控制研磨时间和研磨介质的大小,以获取合适的石墨粒度。
最后,经过研磨处理后的石墨粉末可以进行加工,常见的加工方法包括压制、烧结和石墨化处理。
压制是将石墨粉末放入模具中,在高温高压的条件下进行压制,使石墨粉末紧密结合成坚硬的石墨块状。
烧结是将压制成型的石墨块放入烧结炉中,在高温下进行烧结,使石墨块的颗粒间相互融合,形成致密的结构。
石墨化处理是在高温高压的环境中,通过化学反应或者物理变化将石墨块进行改性处理,以提高其性能。
人工合成石墨的生产工艺主要有化学气相沉积法和高温焙烧法两种。
化学气相沉积法是利用气相化学反应使石墨材料在衬底上沉积形成,可以控制石墨材料的形貌和结构。
高温焙烧法是将石墨材料的前驱体经过高温热处理,使其发生结构变化,形成石墨结构。
总之,石墨的生产工艺主要分为自然生石墨和人工合成石墨两种。
自然生石墨主要通过开采、研磨和加工三个步骤,而人工合成石墨主要通过化学气相沉积法和高温焙烧法进行。
随着技术的不断进步,石墨的生产工艺也在不断发展和改进,以满足不同领域对石墨材料性能和品质的要求。
石墨生产工艺(3篇)
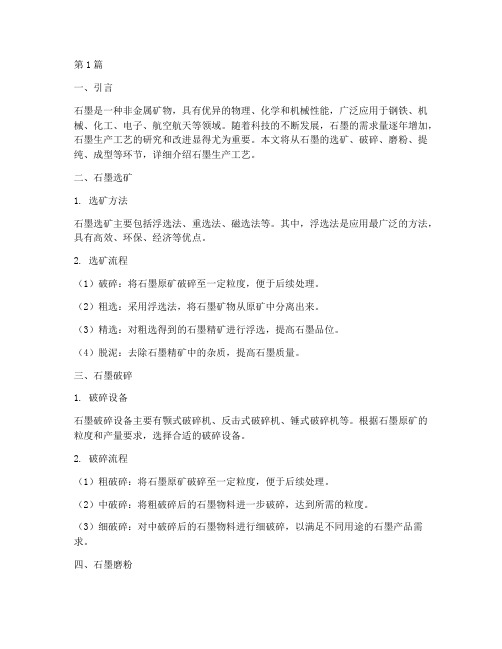
第1篇一、引言石墨是一种非金属矿物,具有优异的物理、化学和机械性能,广泛应用于钢铁、机械、化工、电子、航空航天等领域。
随着科技的不断发展,石墨的需求量逐年增加,石墨生产工艺的研究和改进显得尤为重要。
本文将从石墨的选矿、破碎、磨粉、提纯、成型等环节,详细介绍石墨生产工艺。
二、石墨选矿1. 选矿方法石墨选矿主要包括浮选法、重选法、磁选法等。
其中,浮选法是应用最广泛的方法,具有高效、环保、经济等优点。
2. 选矿流程(1)破碎:将石墨原矿破碎至一定粒度,便于后续处理。
(2)粗选:采用浮选法,将石墨矿物从原矿中分离出来。
(3)精选:对粗选得到的石墨精矿进行浮选,提高石墨品位。
(4)脱泥:去除石墨精矿中的杂质,提高石墨质量。
三、石墨破碎1. 破碎设备石墨破碎设备主要有颚式破碎机、反击式破碎机、锤式破碎机等。
根据石墨原矿的粒度和产量要求,选择合适的破碎设备。
2. 破碎流程(1)粗破碎:将石墨原矿破碎至一定粒度,便于后续处理。
(2)中破碎:将粗破碎后的石墨物料进一步破碎,达到所需的粒度。
(3)细破碎:对中破碎后的石墨物料进行细破碎,以满足不同用途的石墨产品需求。
四、石墨磨粉1. 磨粉设备石墨磨粉设备主要有球磨机、 Raymond 磨、雷蒙磨等。
根据石墨物料的粒度和产量要求,选择合适的磨粉设备。
2. 磨粉流程(1)粗磨:将破碎后的石墨物料进行粗磨,达到一定的粒度。
(2)细磨:对粗磨后的石墨物料进行细磨,以满足不同用途的石墨产品需求。
(3)分级:对磨粉后的石墨物料进行分级,去除不合格的物料。
五、石墨提纯1. 提纯方法石墨提纯方法主要有酸洗法、碱洗法、氯化法等。
其中,酸洗法和碱洗法应用较为广泛。
2. 提纯流程(1)酸洗:将石墨物料放入酸洗槽中,进行酸洗处理,去除杂质。
(2)碱洗:将酸洗后的石墨物料放入碱洗槽中,进行碱洗处理,进一步去除杂质。
(3)过滤:将碱洗后的石墨物料进行过滤,得到纯净的石墨。
六、石墨成型1. 成型方法石墨成型方法主要有挤压法、压制法、烧结法等。
高纯石墨加工工艺

高纯石墨加工工艺主要包括以下几个步骤:
1.原料准备:选用高纯度的天然石墨或人工合成的石墨粉末作为
原料。
2.石墨烘干:将原料石墨粉末进行烘干,以去除其中的水分。
3.石墨压制:将烘干后的石墨粉末放入压制机中,在高压下进行
压制成块状或板状。
4.石墨烧结:经过压制后的石墨块或板放入石墨烧结炉中,在高
温条件下进行烧结,使其颗粒之间相互结合。
5.石墨加工:经过烧结的石墨块或板进行机械加工,如铣削、车
削、磨削等,以获得所需的形状和尺寸。
6.表面处理:对石墨制品进行表面处理,如抛光、清洁等,以提
高其光洁度和表面质量。
7.检测和质量控制:对加工后的石墨制品进行检测,如密度、硬
度、导电性等参数的测量,以确保产品质量。
8.最终产品包装:将加工好的高纯石墨制品进行适当的包装,以
保护产品免受外界环境的影响。
石墨填料压制工艺

石墨填料压制工艺
石墨填料压制工艺是一种重要的石墨材料加工工艺,其主要是通过压制成型的方法将石墨粉末压制成具有特定形状和尺寸的石墨制品。
这种工艺具有操作简便、生产效率高、产品质量稳定等优点,在石墨材料加工领域得到了广泛应用。
石墨填料压制工艺主要包括以下几个步骤:首先是石墨粉末的制备。
石墨粉末是压制工艺的基础,其质量和粒度对最终产品的性能有着重要影响。
石墨粉末的制备一般通过天然石墨的破碎、磨矿等工序完成,制备过程中需要控制石墨粉末的粒度和纯度,以满足不同应用领域的需求。
接下来是石墨填料的混合与搅拌。
将石墨粉末与其他填料改性剂按照一定比例混合,并进行充分的搅拌,以提高填料的性能。
混合和搅拌的均匀性对最终产品的性能有着重要影响。
然后是压制成型。
将混合好的石墨填料放入模具中,通过施加一定的压力,使石墨填料在模具中成型。
压制过程中需要控制压力的大小和压制时间,以确保产品的密度和尺寸精度。
最后是脱模与后处理。
待石墨材料固化之后,从模具中取出,进行脱模和清理。
根据需要,还可以进行烘烤等后处理,以提高产品的稳定性和性能。
总之,石墨填料压制工艺是一种重要的石墨材料加工工艺,其操作简便、生产效率
高、产品质量稳定等优点使得其在石墨材料加工领域得到了广泛应用。
通过不断优化工艺参数和控制产品质量,可以进一步提高石墨填料的性能和应用范围。
石墨制作工艺

石墨制作工艺嘿,朋友们,咱今天来聊聊石墨制作工艺这事儿。
说起石墨,这东西在咱们生活中还真挺常见,可你知道它是咋被制作出来的不?我记得有一次去一个工厂参观,那真是让我大开眼界。
一进去,就听到各种机器轰鸣的声音,那场面,别提多热闹了。
先来说说石墨的原材料,一般是天然石墨矿石或者人造石墨前驱体。
就像做菜得先有好食材一样,这原材料的质量可是关键。
然后就是粉碎环节啦。
把大块的矿石或者前驱体弄碎成小颗粒,这就好比把一个大西瓜切成小块儿,方便后续加工。
机器咔咔咔地响,那些大块头瞬间就变得服服帖帖。
接着是提纯。
这一步就像是给石墨“洗澡”,把里面的杂质都洗掉,让石墨变得更纯净。
工厂里的师傅们可是一丝不苟,严格把控着每一个环节,眼睛紧紧盯着仪表上的数字,生怕出一点差错。
再往后就是成型啦。
把处理好的石墨材料按照需要做成各种形状,有的像圆柱体,有的像长方体。
这过程就像是捏橡皮泥,不过可比那复杂多了。
在高温处理环节,石墨被放进高温炉里,就像被放进了一个大火炉里烤。
那温度高得吓人,感觉能把一切都融化掉。
但神奇的是,经过这一遭,石墨的性能反而变得更好了。
还有石墨化过程,这可是个关键步骤。
在特定的条件下,石墨的结构会发生变化,变得更加稳定和有序。
最后就是加工和质检啦。
把石墨产品打磨得光滑平整,再仔细检查有没有瑕疵。
就像我们考试交卷前要反复检查一样,一点儿都不能马虎。
经过这么多复杂的工序,石墨才能最终变成我们需要的样子。
你看,小小的石墨,从不起眼的矿石或者前驱体,经过这么多道精心的制作工艺,才得以在各个领域发挥重要作用。
这就像我们每个人,经过不断地学习和锻炼,才能变得更加出色,实现自己的价值。
好啦,关于石墨制作工艺,今天就先聊到这儿,希望能让你对石墨有更多的了解!。
石墨加工工艺流程
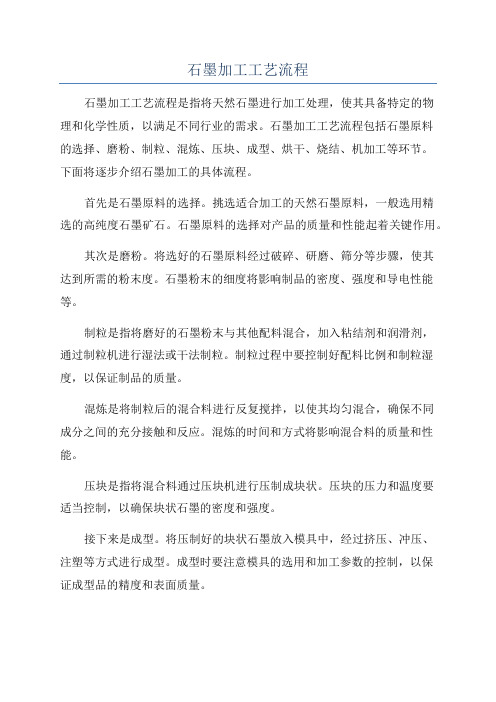
石墨加工工艺流程石墨加工工艺流程是指将天然石墨进行加工处理,使其具备特定的物理和化学性质,以满足不同行业的需求。
石墨加工工艺流程包括石墨原料的选择、磨粉、制粒、混炼、压块、成型、烘干、烧结、机加工等环节。
下面将逐步介绍石墨加工的具体流程。
首先是石墨原料的选择。
挑选适合加工的天然石墨原料,一般选用精选的高纯度石墨矿石。
石墨原料的选择对产品的质量和性能起着关键作用。
其次是磨粉。
将选好的石墨原料经过破碎、研磨、筛分等步骤,使其达到所需的粉末度。
石墨粉末的细度将影响制品的密度、强度和导电性能等。
制粒是指将磨好的石墨粉末与其他配料混合,加入粘结剂和润滑剂,通过制粒机进行湿法或干法制粒。
制粒过程中要控制好配料比例和制粒湿度,以保证制品的质量。
混炼是将制粒后的混合料进行反复搅拌,以使其均匀混合,确保不同成分之间的充分接触和反应。
混炼的时间和方式将影响混合料的质量和性能。
压块是指将混合料通过压块机进行压制成块状。
压块的压力和温度要适当控制,以确保块状石墨的密度和强度。
接下来是成型。
将压制好的块状石墨放入模具中,经过挤压、冲压、注塑等方式进行成型。
成型时要注意模具的选用和加工参数的控制,以保证成型品的精度和表面质量。
烘干是将成型的石墨制品放入烘干设备中进行烘干,以去除水分和挥发物。
烘干的温度和时间要适当控制,以免产生开裂和变形等问题。
烧结是将烘干后的石墨制品放入高温炉中进行烧结处理,使其结晶更加致密。
烧结的温度和时间要根据石墨制品的具体要求进行调整,以提高石墨制品的强度和耐热性。
最后是机加工。
将烧结好的石墨制品根据客户的要求进行切割、镗孔、开槽、抛光、电镀等机械加工,以得到最终产品。
机加工的精度和工艺水平将直接影响到最终石墨制品的质量。
总之,石墨加工工艺流程包括石墨原料的选择、磨粉、制粒、混炼、压块、成型、烘干、烧结、机加工等环节。
这些流程的每一步都需要精心控制和操作,以确保最终产品的质量和性能。
石墨制品广泛应用于电池、电解槽、铜合金等行业,对于提高产品的效率和可靠性具有重要意义。
高纯石墨提炼工艺流程
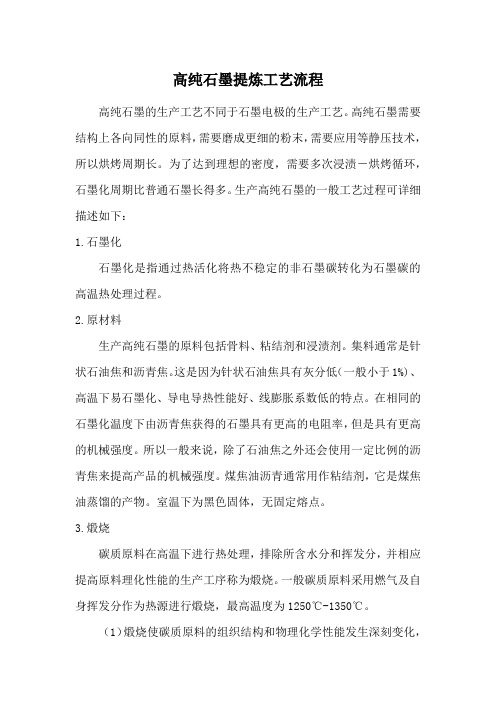
高纯石墨提炼工艺流程高纯石墨的生产工艺不同于石墨电极的生产工艺。
高纯石墨需要结构上各向同性的原料,需要磨成更细的粉末,需要应用等静压技术,所以烘烤周期长。
为了达到理想的密度,需要多次浸渍-烘烤循环,石墨化周期比普通石墨长得多。
生产高纯石墨的一般工艺过程可详细描述如下:1.石墨化石墨化是指通过热活化将热不稳定的非石墨碳转化为石墨碳的高温热处理过程。
2.原材料生产高纯石墨的原料包括骨料、粘结剂和浸渍剂。
集料通常是针状石油焦和沥青焦。
这是因为针状石油焦具有灰分低(一般小于1%)、高温下易石墨化、导电导热性能好、线膨胀系数低的特点。
在相同的石墨化温度下由沥青焦获得的石墨具有更高的电阻率,但是具有更高的机械强度。
所以一般来说,除了石油焦之外还会使用一定比例的沥青焦来提高产品的机械强度。
煤焦油沥青通常用作粘结剂,它是煤焦油蒸馏的产物。
室温下为黑色固体,无固定熔点。
3.煅烧碳质原料在高温下进行热处理,排除所含水分和挥发分,并相应提高原料理化性能的生产工序称为煅烧。
一般碳质原料采用燃气及自身挥发分作为热源进行煅烧,最高温度为1250℃-1350℃。
(1)煅烧使碳质原料的组织结构和物理化学性能发生深刻变化,主要体现在提高了焦炭的密度、机械强度和导电性,提高了焦炭的化学稳定性和抗氧化性能,为后续工序奠定了基础。
煅烧设备主要有罐式煅烧炉、回转窑和电煅烧炉。
煅烧质量控制指标是石油焦真密度不小于cm3,电阻率不大于550μΩ.m,针状焦真密度不小于cm3,电阻率不大于500μΩ.m。
(2)原料的破碎处理和配料在配料之前,须对大块煅后石油焦和针状焦进行粉碎、磨粉、筛分处理。
①中碎:通常是将50mm左右的物料通过颚式破碎机、锤式破碎机等破碎设备进一步破碎到配料所需的大小。
②磨粉:通过磨粉机(球磨机、环棍式环辊磨粉机)将碳质原料磨细到粒径以下的粉末状小颗粒的过程。
③筛分:通过具有均匀开孔的一系列筛子,将破碎后尺寸范围较宽的物料分成尺寸范围较窄的几种颗粒粒级的过程。
石墨化工艺流程

石墨化工艺流程石墨化工艺流程是将石墨矿石经过一系列的处理工艺,使其转变成可用于不同领域的石墨产品的过程。
下面将以石墨电极的生产为例,介绍石墨化工艺流程。
首先,原始的石墨矿石需要经过破碎和磨矿的工序,将矿石破碎成较小的颗粒并磨细,以提高其可操作性。
然后,将破碎和磨细后的石墨矿石混合在一起,并与一定比例的粘结剂进行搅拌,使其成为一个均匀的石墨矿浆。
这个石墨矿浆将用作制备石墨电极的原料。
接下来,将石墨矿浆倒入模具中,并经过振实和压制的工序,将矿浆中的空气排出,使其形成致密的物体。
经过一段时间的固化,模具中的石墨坯体将变得更加坚固。
然后,将石墨坯体进行高温烧结。
在烧结炉的高温环境中,石墨坯体中的粘结剂将烧结掉,石墨晶体结构得到改善,使其具备更好的导电性和机械强度。
烧结炉内的温度需要精确控制,以确保石墨电极能够达到所需的物理和化学特性。
烧结后的石墨坯体经过进一步的加工,包括机械加工、磨削和抛光,以达到所需的尺寸和表面粗糙度。
这些加工工序需要高精度的设备和工艺控制,以确保石墨电极的高质量。
最后,经过严格的质量检查和测试,合格的石墨电极将被包装和交付给客户。
在包装过程中,还需要注意防止石墨电极的表面受到污染和损坏。
需要指出的是,石墨化工艺流程不仅适用于石墨电极的生产,还可以用于其他石墨制品的制造,如石墨垫片、石墨锅、石墨阴极等。
总结来说,石墨化工艺流程是一个复杂的过程,需要多个环节的协调和控制。
从原始石墨矿石到最终的石墨产品,经历了破碎、混合、压制、烧结、加工和包装等工序。
只有经过严格的质量控制和测试,才能生产出高质量的石墨产品。
石墨产品在电力、冶金、化工等领域有着广泛的应用,对促进工业发展起到了重要的作用。
石墨加工工艺流程
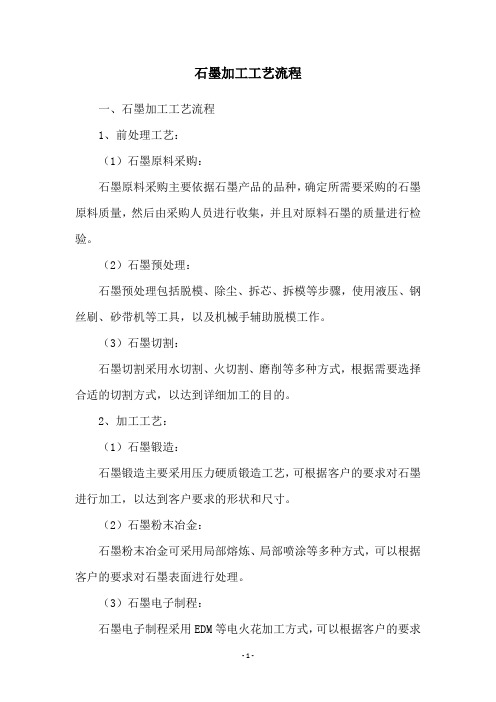
石墨加工工艺流程
一、石墨加工工艺流程
1、前处理工艺:
(1)石墨原料采购:
石墨原料采购主要依据石墨产品的品种,确定所需要采购的石墨原料质量,然后由采购人员进行收集,并且对原料石墨的质量进行检验。
(2)石墨预处理:
石墨预处理包括脱模、除尘、拆芯、拆模等步骤,使用液压、钢丝刷、砂带机等工具,以及机械手辅助脱模工作。
(3)石墨切割:
石墨切割采用水切割、火切割、磨削等多种方式,根据需要选择合适的切割方式,以达到详细加工的目的。
2、加工工艺:
(1)石墨锻造:
石墨锻造主要采用压力硬质锻造工艺,可根据客户的要求对石墨进行加工,以达到客户要求的形状和尺寸。
(2)石墨粉末冶金:
石墨粉末冶金可采用局部熔炼、局部喷涂等多种方式,可以根据客户的要求对石墨表面进行处理。
(3)石墨电子制程:
石墨电子制程采用EDM等电火花加工方式,可以根据客户的要求
对石墨形状进行加工,以达到客户的要求。
3、后处理工艺:
(1)石墨热处理:
石墨热处理一般采用氩弧焊接,以改善石墨加工过程中出现的热变形,提高石墨的加工精度和耐磨性。
(2)石墨表面处理:
石墨表面处理一般采用热处理、电镀、抛光等处理工艺,以达到改善表面性能和防锈的目的。
(3)石墨测试:
石墨测试一般采用粉末X射线检测、维氏硬度测试等方式,以确保石墨加工后的产品质量。
石墨产品加工工艺技术研究

石墨产品加工工艺技术研究摘要:目前国内对石墨加工的研究还不充分,当石墨加工时刀具磨损严重,工件容易出现裂纹、断裂、塌陷等现象。
石墨切削中产生的切屑容易附着在刀具面和加工面上,产生剧烈的摩擦和冲击,在切削中引起非常严重的刀具磨损。
石墨粉尘不仅污染环境,还对机床零件造成一定的磨损。
因此石墨产品加工工艺技术研究直接影响产品性能,加工工艺的不同直接影响石墨产品的质量。
研究合理的模具结构,选择合理的工艺参数非常重要。
本文从加工性能、切削技术、深加工等方面研究石墨加工工艺技术,促进石墨产品的制造。
关键词:石墨;加工工艺;技术引言:石墨是一种常见的非金属材料。
切削时,石墨材料在施加的局部应力的作用下膨胀,材料破碎,石墨工件在与刀尖接触的位置被压溃破裂,产生裂纹,产生块状切屑,使刀具磨损,在石墨工件的加工表面留下凹坑。
在加工中,需要选择合适的加工工艺,除了确保刀具本身的属性外,需要按照标准持续调整切削参数。
否则随着刀具磨损的增加,在生产工艺标准下产品质量下降严重,影响石墨产品的质量。
一、石墨加工性能分析石墨是一种脆性材料,切割的石墨碎片为粉状,因此在加工过程中需要开发特殊的加工工艺和方法。
同时,石墨易碎,抗拉强度低,加工性好,对尺寸精度和表面质量要求高,加工过程中容易产生严重的刀具磨损。
此外,刀具冲击工件,引起零件边缘塌陷和刀具磨损等诸多问题。
当刀具的切削刃与工件接触时,由于刀具的前进,工件的一部分被断裂,成为“屑”。
这些碎片散落在工具表面或沉积在工具表面,大部分沿前刀面滑动,容易造成工具损坏。
此外,石墨材料的致密性和均匀性远远不及金属,石墨工件受到不同程度的冲击,导致石墨工件角脆性断裂,刀具磨损严重,容易产生工件间隙这也是石墨加工的难点。
二、石墨切削加工工艺(一)切削加工工艺措施石墨材料的传统加工方法包括车削、铣削、磨削、锯切等,实现简单的加工。
随着石墨工具及其相关技术的迅速发展和应用,这些传统的加工方法逐渐被新的加工工艺所取代。
石墨加工

6.3切削方式:铣削方式有顺铣和逆铣之分,判断顺铣还是逆铣可根据判断工件的进给方向和刀具的旋转方向是否一致,一致为顺铣,相反则为逆铣。
由于顺铣时的切削震动小于逆铣的切削震动,所以应采用顺铣来加工内外形轮廓。顺铣由于刀具的切入厚度是从最大递减到零的,所以不知处出现由于切不下而导致的弹刀现象;反之,逆铣开始的切入厚度非常小,一旦出现刃口碰到硬质点或者切削颗粒的情况都会产生震颤或者弹刀现象。与此同时,一定要尽量避免大吃量出刀,防止棱边崩角或掉渣的现象。
6、刀具的机械加工条件
选择适当的加工条件对于刀具的寿命以及加工的质量有相当大的影响。
6.1选择合适的转速和进给。一般来说,由于石墨材料易于切削,在加工过程中可以选择高转速、快速进给、大吃刀的切削参数,有效的提高加工效率,但由于石墨在加工中容易产生崩角、掉渣现象、尤其在棱边等位置易形成锯齿,在这些部位应适当降低转1、前言
石墨在生产生活中是非常常见的一种黑色非金属原料,密度比较低还拥有着耐高温性、导电导热性、润滑性、化学稳定性、可塑性、抗热震性等等优秀的性质。并且由于其属于六方晶体,层面间结合力比较弱,内部气孔率大、抗拉强度低等特点,使得石墨的机械加工性能非常好。根据其不同的特性,其用途也非常广泛,例如:根据其化学稳定性可以制作成墨水、铅笔芯等;根据其耐高温性可以制成提炼黄金的磨具;根据其导电、导热性可以制成电加工机床的电极等。
石墨零件的结构比较复杂、精度要求高等,一般都对其质量要求比较高,在由于其上述特性,造成加工中容易出现棱边锯齿化、掉渣以及崩角等质量的不合格现象。
2、刀具的选择
刀具是否正确选择直接决定了加工的效率、质量。因此,我们如果想要对加工的质量进行有效地控制就必须选择合理有效地刀具。例如:石墨材质本身就比较便于切削,所以对于一些表面精度要求不高还要控制成本的产品可以采用高度钢刀具。刀具的切削性能直接决定着加工质量、加工效率、以及刀具耐久度等,因此一定要对刀具的材料进行合理的选择。刀具的硬度和韧性是相矛盾的,硬度越高,耐磨性越好,但同时韧性就越低、质地越脆。同时,石墨是由石墨粉末压制而成,只始于采用干切削方法,但是高速钢的耐磨性很差,在加工中极容易产生严重磨损,因此不能用高速钢刀具加工精度、质量要求比较高的石墨产品,而应该用那些涂层刀具或者耐磨性比较好的刀具。例如:采取硬质合金涂层刀具、硬质合金YG8刀具等。硬质合金主要有TiC、TaC、WC等难熔金属碳化物以及铁粉通过冶金方法提炼出来的。同普通高速钢相比,硬质合金钢具有着硬度高、耐磨性好的优点;同时,与超硬材料相比具有着韧性好的优点。硬质合金钢的涌入非常广泛,不仅提升了生产效率,还提高了石墨产品的质量。因此,在刀具的选择中一定要进行最恰当的选择。
石墨深加工技术概况及应用

石墨深加工技术概况及应用石墨是一种具有特殊结构和优异性能的材料,其在深加工技术中有着广泛的应用。
本文将介绍石墨深加工技术的概况以及其在各个领域的应用。
石墨深加工技术是指通过对石墨进行特殊处理,改变其物理性质和化学性质,使其具备更多的功能和应用价值。
石墨深加工技术主要包括石墨热处理、石墨表面改性、石墨复合材料制备等多个方面。
石墨热处理是指通过高温处理石墨,使其晶格结构发生改变,提高石墨的热导率和耐热性能。
这种技术可以使石墨在高温环境下保持稳定的性能,提高其在高温工艺中的应用价值。
石墨热处理技术在航空航天、电子器件、冶金工业等领域有着广泛的应用。
石墨表面改性是指通过对石墨表面进行物理或化学处理,改变其表面性质,以提高其耐磨性、耐腐蚀性和导电性能等。
常见的石墨表面改性方法包括化学氧化、石墨烯涂覆等。
石墨表面改性技术可以使石墨在电池、电子器件、润滑材料等领域发挥更好的性能。
石墨复合材料制备是指将石墨与其他材料进行混合或复合,以获得具有更好性能和更广应用领域的材料。
石墨复合材料制备技术可以将石墨的导电性能、高温性能和机械强度与其他材料的特性相结合,使得复合材料在航空航天、汽车制造、电子工业等领域有着重要的应用。
除了上述概况外,石墨深加工技术在许多其他领域也有着广泛的应用。
例如,在新能源领域,石墨深加工技术可以用于制备储能材料,提高锂离子电池的性能;在化工工业中,石墨深加工技术可以用于制备催化剂,提高化学反应效率;在环境保护领域,石墨深加工技术可以用于制备吸附材料,去除水污染物等。
石墨深加工技术是一种重要的材料处理技术,通过对石墨的热处理、表面改性和复合材料制备等手段,可以使石墨具备更多的功能和应用价值。
石墨深加工技术在航空航天、电子器件、汽车制造、化工工业、环境保护等多个领域都有着广泛的应用前景。
随着科技的不断进步,石墨深加工技术将会得到更加广泛的发展和应用。
(完整)石墨制作工艺
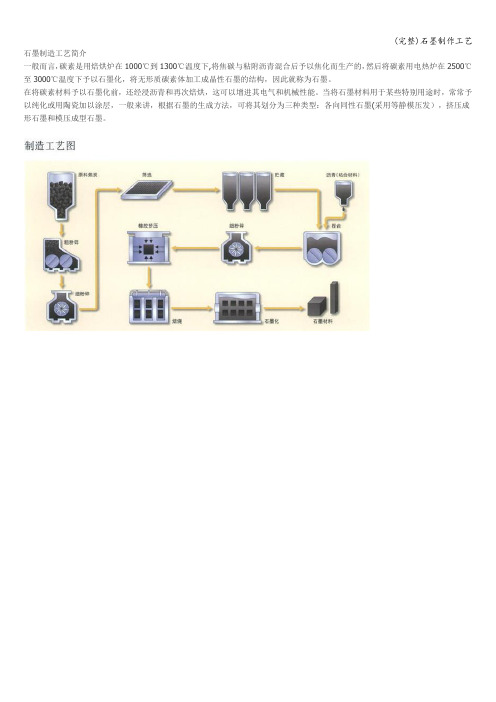
(完整)石墨制作工艺石墨制造工艺简介
一般而言,碳素是用焙烘炉在1000℃到1300℃温度下,将焦碳与粘附沥青混合后予以焦化而生产的,然后将碳素用电热炉在2500℃至3000℃温度下予以石墨化,将无形质碳素体加工成晶性石墨的结构,因此就称为石墨。
在将碳素材料予以石墨化前,还经浸沥青和再次焙烘,这可以增进其电气和机械性能。
当将石墨材料用于某些特别用途时,常常予以纯化或用陶瓷加以涂层,一般来讲,根据石墨的生成方法,可将其划分为三种类型:各向同性石墨(采用等静模压发),挤压成形石墨和模压成型石墨。
人造石墨的原理

人造石墨的原理
人造石墨是通过将天然石墨经过化学处理、高温压缩等工艺加工而成的。
具体来说,制造人造石墨的过程包括以下步骤:
1.选择优质的天然石墨为原料,经过清洗和筛选等处理,去除杂质。
2.将天然石墨进行多道化学处理,包括酸洗、碱洗、高温氧化等,使
其变得更纯净。
3.将处理后的石墨烧结,使其成为一种类似固体的物质,称为焦炭。
4.将焦炭进行高温压缩处理,用特殊的机器将其压缩成坚硬的块状物。
5.将经过压缩的焦炭进行再次热处理,将其升温到接近石墨的熔点,
使其变成人造石墨。
总体来说,制造人造石墨的原理就是通过对天然石墨进行一系列的物理、化学处理,使其变成一种更纯净的物质,然后通过高温、高压等工艺
让其形成一种坚硬、耐磨、导电性能优良的人造石墨。
- 1、下载文档前请自行甄别文档内容的完整性,平台不提供额外的编辑、内容补充、找答案等附加服务。
- 2、"仅部分预览"的文档,不可在线预览部分如存在完整性等问题,可反馈申请退款(可完整预览的文档不适用该条件!)。
- 3、如文档侵犯您的权益,请联系客服反馈,我们会尽快为您处理(人工客服工作时间:9:00-18:30)。
石墨的生产工艺
1、一般碳石墨材料生产程序
碳石墨材料可用普通机床进行干湿加工。
但是为了保持其纯度,高纯石墨通常是用干加工。
磨削和研磨普通石墨,常采用湿加工。
最好避免在同一台机器上进行干、湿加工的转换操作。
除尘
采用干加工时,所有机器上都应加装除尘装置,除了大型石墨加工车间外,不需装中央除尘设备。
如果车间主要用于加工金属,是需在各个机器上安装工具真空吸尘器(真空300mm水头或气流速递为18米/秒)应盖上润滑的抛光面或导向面。
切削
碳可以用青铜基金刚石砂轮进行切削,砂轮粗度为200-300mm,线速度为50-60米/秒。
石墨可用工具钢粗齿带锯进行割据(5个齿/英寸)切割速度为300-600米/分。
车削
工件最好是放在弹簧夹套里或者带一个膨胀环。
以石墨的陶瓷特性来看,应把夹持压力分散在尽可能大的面积上。
原则上可采用KO1、K05以及K10硬质合金刀片,如果要求公差低于1T7,那么建议使用金刚石刀具。
通过采用刀具刀口的圆角或角倒角,以减少共建的崩边角情形。
注:较低数据主要用于碳材料加工面较高数据用于石墨材料加工,而较高数据用于石墨材料加工
铣削
铣削通常使用硬质合金和金刚石刀具。
后角应不小于10度。
使用金刚刀具加工,则切削速度可增加50%
注:较低数据用于碳材料加工,而较高数据用于石墨加工
磨削
碳石墨材料可以进行磨削加工。
砂轮密度应在6-9之间。
当需要进行高精度表面处理时,必须采取珩磨,研磨及抛磨工艺。
石墨是可以进行粘接材料可使用聚酯,双氧树脂,在高温条件下使用的氧化铝合着或者氧化铝或者氧化锆为基体的陶瓷粘洁剂。