互换性表面粗糙度
互换性表面粗糙度实验
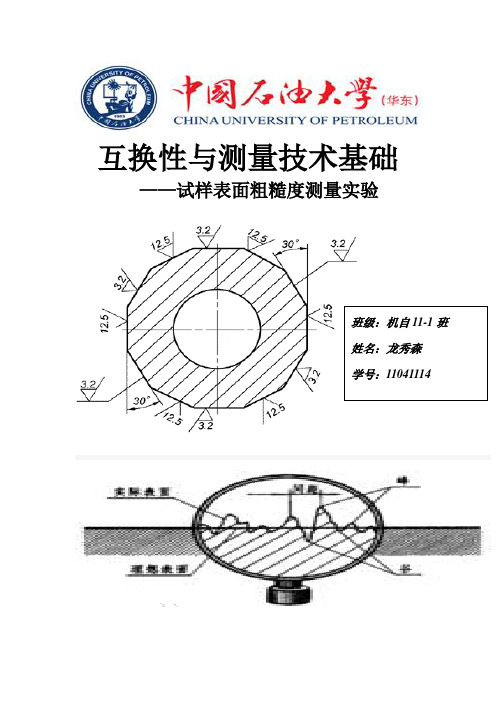
互换性与测量技术基础——试样表面粗糙度测量实验班级:机自11-1班姓名:龙秀森学号:11041114一、实验目的1. 了解表面粗糙度的测量原理、常用方法以及需要测定的参量;2. 学习掌握TR220手持式粗糙度仪、RM—20袖珍式粗糙度仪的使用方法;3. 测定待测物件的轮廓算术平均偏差Ra等参量。
二、实验仪器粗糙度比较样板、TR220手持式粗糙度仪、RM—20袖珍式粗糙度仪。
三、实验内容内容I:表一、比较法测量表面粗糙度编号名称材料Ra(μm)加工方法2 矩形块45#钢 3.2 车床1 小圆柱体45#钢 6.3 立铣内容II:用RM-20袖珍式表面粗糙度仪检测材料:碳化硅加工方法:电火花注意:指定样件,指定表面才能使用该仪器,粗糙面严紧使用,否则损坏一起。
Ra最大只能测15um。
RM-20袖珍型表面粗糙度仪RM-20袖珍型表面粗糙度仪的使用:a、开机打开电源开关,电源接通。
b、功能选择如果需要选择测量参数Ra,将手指轻触图1中3键,如果需要选择测量参数Rz,将手指轻触图1中3键,屏幕将显示Rz值,再直接按3键,屏幕将回到Ra值。
如果需要选择取样长度,将手指轻触图1中4键,若此时的取样长度为0.25mm,再次按此功能键,长度变为0.8mm,再一次则为2.5mm,然后再回到0.25mm。
取样长度的选择根据工件表面质量来选取相应的取样长度。
各取样长度对应的范围如下:0.25mm Ra 0.05-0.15(um)0.8mm Ra 0.1-2.5(um)2.5mm Ra 6.0-15.0(um)c、启动、运行和运行结束将仪器▼||▼对准被测工件表面,用说指轻按1键,传感器开始移动,屏幕自动记录表面粗糙度的数值,待传感器返回开始位置,运行结束,即可开始下次测量。
注:运行结束前,仪器不会响应再次测量的命令,完整的测量结束后,才允许进行下次操作。
d、充电当开机后或测量过程中,液晶屏出现闪烁现象,说明电池电压低于工作电压下限,应予充电。
《互换性与测量技术基础》用光切显微镜测量表面粗糙度实验

《互换性与测量技术基础》用光切显微镜测量表面粗糙度实验一、实验目的1.掌握用光切显微镜评定工件表面粗糙度的方法。
2.加深对表面粗糙度评定参数的理解。
二、实验仪器和工具光切显微镜、被测工件三、实验原理光切显微镜是以光切法原理,测量和观察机械零件加工表面的微观几何形状误差的,又称表面粗糙度显微镜。
在不破坏零件表面的条件下测出工件截面轮廓最大高度和沟糟宽度的实际尺寸。
此外,还可测量零件表面上个别位置的加工痕迹和破损情况。
该仪器用于测量零件表面轮廓最大高度Rz值,其测量范围取决于选用的物镜的放大倍数,通常适用于测量Rz等于 0.8—63 微米的表面粗糙度。
此种仪器只能对外表面进行测量,除对金属进行测量外,也可对纸张、木材和人工材料进行测量。
光切显微镜的外形及成像原理图如图 2-1和图 2-2所示。
图 2-1 光切显微镜外形图图 2-2 光切显微镜成像原理图由光源1发出的光,穿过夹缝2,形成带状光束,经物镜组O1O1′,斜向45°射向工件,凹凸不平的表面上呈现出曲折光带,再以45°反射,经物镜组O2O2′,到达分划板3上。
人眼通过目镜可以看到如图2-3所示。
图 2-3 光切显微镜的目镜视野四、测量步骤1、根据被测工件表面粗糙度的要求,选择合适的物镜组,分别安装在投射光管和观察光管的下端。
2、接通电源。
3、擦净被测工件,把它安放在工作台上,并使被测表面的切削痕迹的方向与光带垂直。
当测量圆柱形工件时,应将工件置于V形块上。
4、粗调节:用手托住支臂,松开锁紧螺钉,缓慢旋转支臂调节螺母,使支臂上下移动,直到目镜中观察到绿色光带和表面轮廓不平度的影象。
然后,将螺钉固紧。
要注意防止物镜与工件表面相碰,以免损坏物镜组。
5、细调节:缓慢而往复转动调节手轮,调焦环和调节螺钉,使目镜中光带最狭窄,轮廓影象最清晰并位于视场的中央。
6、松开螺钉,转动目镜测微器,使目镜中十字线的一根线与光带轮廓中心线大致平行(此线代替平行于轮廓中线的直线)。
互换性与技术测量(第六版)第一章
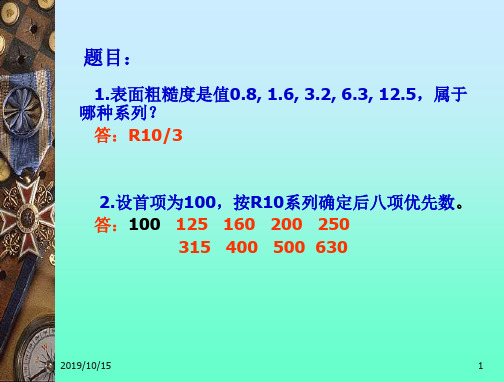
Y av =(Y max +Y min)/2
例题2
计算:孔
50
0.025 0
与轴
50 0.059 0.043
配合的极限间隙或极限过盈、 配合公差并画出公
差带图,说明配合类别。
解:
+0.059 +0.043
0.020 0.033
表示基本尺寸为25,上偏差
为-0.020,下偏差为-0.033。
二、 有关“公差与偏差”的术语与定义
1. 尺寸偏差(简称偏差): (2) 实际偏差 实际偏差Ea=实际尺寸Da—基本尺寸D
注意:由于零件同一表面上不同位置的 实际尺寸往往不同。
偏差是以基本尺寸为基数,从偏离基本 尺寸的角度来表述有关尺寸的术语。
注意:公差值无正负含义。它表示尺寸变动 范围的大小。不应出现“+”“—”号。
加工误差不可避免T≠0
二、 有关“公差与偏差”的术语与定义
公差与偏差的特点比较:
1)“偏差”是代数差,可以为正,负或零; “公差”是绝对值,无正、负可言且不能为零。
2)“极限偏差”限制“实际偏差”;“公差” 限制实际尺寸的变动量。
二、 有关“公差与偏差”的术语与定义
2.尺寸公差(简称公差) 公差:允许尺寸的变动量。等于最大极限尺
寸与最小极限尺寸之代数差的绝对值。孔、轴的
公差分别用Th(hole)和Ts (shaft) 表示。
Th =︱ Dmax- Dmin ︱= ︱ ES-EI︱ Ts =︱ dmax- dmin ︱= ︱ es- ei︱
X max= D max— dmin=ES – ei 孔的最小极限尺寸减去轴的最大极限尺寸所得的代 数差称为最大过盈,用Y max表示。
互换性与测量技术基础表面粗糙度的含义和评定参数
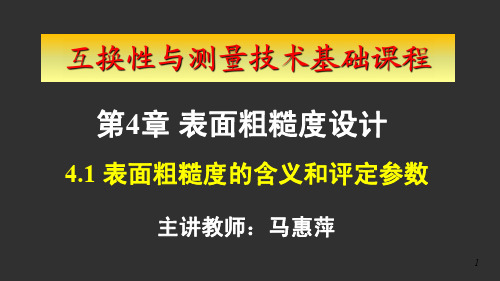
14.1表面粗糙度的含义和评定参数主讲教师:马惠萍第4章 表面粗糙度设计1.问题的提出?(含义及为什么对零件提出表面精度要求?)2.用什么评定?(评定基准及其评定参数)3.如何选用或设计表面粗糙度?4.在零件图上如何标注?第4章 表面粗糙度设计的学习内容why what how how表面粗糙度的产生:(3) 以及机床等工装系统的振动等。
(2) 切削过程中切屑分离时的塑性变形;(1) 切削后遗留的刀痕;微小峰谷的高低程度和间距状况称为表面粗糙度,它是一种微观几何形状误差,也称微观不平度。
4.1.1表面粗糙度的含义一般按S 分:S <1mm 为表面粗糙度1≤S ≤10mm 为波纹度S >10mm 为 f 形状表面粗糙度是指加工后零件表面的微小峰谷(Z )高低程度和间距(S )状况。
间距S高低ZS<1mm短波滤波器滤波后:1≤S≤10mm带通滤波器滤波后:S>10mm长波滤波器滤波后:(1)影响零件的耐磨性;(2)影响配合性质的稳定性;(3)影响抗疲劳强度;(4)影响抗腐蚀性;表面不是越光越好。
4.1.2 表面粗糙度对机械零件使用性能的影响4.1.3 表面粗糙度评定的基本术语1. 取样长度lr---基准线长度。
至少含5个波峰和波谷2.评定长度ln-- --最小的测量长度。
一般包括5个取样长度lr图5.4 取样长度和评定长度3. 中线—指具有几何轮廓形状并划分轮廓的基准线图4-5 轮廓中线轮廓算术平均中线:在取样长度内lr ,划分实际轮廓为上、下两部分面积相等的线轮廓算术平均中线dxx Z lrRa rl ⎰= 0)(1(1)轮廓的算术平均偏差Ra (触针式电感轮廓仪测量0.025-6.3)在取样长度lr 内,纵坐标值Z (x )的绝对值的算术平均值∑=≈ni iZnRa 11Z iZ (x )xlrRa算术平均偏差Ra4.1.4 表面粗糙度的评定参数—幅度(高度)参数(2)轮廓的最大高度Rz minV max P Z Z Rz +=在取样长度lr 内maxP Z 1P Z 1v Z 2v Z Rz最大高度Rz中线maxv Z图4.9 微观形状对质量的影响幅度参数评定?4.1.4 表面粗糙度的评定参数—附加参数(3)间距参数RSm(反映间距特性)轮廓单元:一个轮廓峰和相邻轮廓谷的组合。
互换性复习题

互换性复习题一、问答题1.什么叫互换性?互换性在机械制造中的作用是什么?从一批相同规格的零件(或部件)中任意拿出一个,不需任何修配就能装到所属的部件(或机器)中去,达到预定的配合要求,并能满足技术要求及保证良好的使用性能,这就是互换性。
零、部件的互换性为生产的专业化创造了条件,促进了自动化生产的发展,有利于降低产品成本,缩短设计和生产周期,从而提高生产率,提高产品质量,保证机器工作的连续性和持久性,同时给机器的维修带来极大的方便。
2.公差、配合、互换性三者的关系是什么?零件几何参数允许的变动量称为公差。
它包括尺寸公差、形状公差、位置公差等。
公差用来控制加工中的误差,以保证必要的配合性质。
因此,建立各种几何参数的公差标准是实现对零件误差的控制和保证互换性的基础。
3.公称尺寸,实际尺寸,极限尺寸之间有何区别。
公称尺寸是指设计给定的尺寸。
实际尺寸是指通过测量得到的尺寸。
极限尺寸是指允许尺寸变化的两个界限值。
4.公差、偏差有何区别?尺寸公差是指尺寸允许的变动量。
公差等于上极限尺寸与下极限尺寸之代数差的绝对值,也等于上极限偏差与下极限偏差之代数差的绝对值。
公差的数值只能为正值。
偏差是指某一尺寸减其公称尺寸所得的代数差。
偏差分为极限偏差和实际偏差,而极限偏差又分为上极限偏差和下极限偏差。
偏差的数值可以是正值、负值或为零。
5.配合有几种类型?间隙配合、过盈配合、过渡配合。
6. 为什么进行公称尺寸分段?公称尺寸分段后,对同一公称尺寸段内的所有公称尺寸,在相同标准公差等级情况下,规定相同的标准公差,减少了标准公差数目、统一了公差值、简化了公差表格以及便于生产实际应用。
7. 千分尺(又名螺旋测微计)是如何提高测量精度的?其最小分度值为多少?其意义是什么?千分尺的核心部分主要由测微螺杆和螺母套管所组成,是利用螺旋推进原理而提高测量精度的。
其最小分度值为0.01mm,表示其测量准确度为0.01mm。
8. 为什么规定安全裕度和验收极限?通过安全裕度和验收极限来防止因测量不确定度的影响而造成工件“误收”和“误废”。
互换性与技术测量第四章--表面粗糙度及检测概要

Ra
1 lr
lr
Z ( x) dx
0
或
Ra
1 n
n i1
Zi
Z(x)
Zi
lr
Ra
算术平均 偏差Ra
X
2. 轮廓的最大高度 Rz(幅度参数或高度参数)
指在一个取样长度lr内,最大轮廓峰高Zp和最大轮廓谷深Zv 之和的高度。
Z(x)
Z P1
Z Pmax
中线 Rz Zpmax Zvmax
Rz
Z v1
用一条平行于X轴的线与轮廓单元相截所获得的各段截线长度
Mli 之和。
Ml(c) Ml1 Ml2 b1 b2
C是轮廓截面高度(即距峰顶线的距离),用微米或轮廓的 最大高度Rz的百分数表示。
C = Rz %
三、评定参数的数值 在幅度参数常用的范围内,优先选用Ra,Rz用于目前公厂仪 器。 各参数均分别由优先数系中的派生数系确定,见表4-1到4-5。
Rsm
1 m
m i 1
Xsi
中线
l
7r轮
廓 宽 度
4. 轮廓的支承长度率Rmr(c)
指在给定的水平位置c上,轮廓的实体材料长度Ml(c)与评定 长度ln的比率。
n
Rmr (c) bi / ln
i1
Ml(c) 100% ln
轮廓的支承长度率
轮廓的实体材料长度 Ml(c) 是指在一个给定水平位置c上,
6. 粗糙度轮廓中线 用标称形式的线穿过粗糙度轮廓,按最小二乘法拟合所确 定的线。即粗糙度轮廓上的点至中线的距离 Z(x) 的平方和为最
小(即 Z(x)2 min )。
7. 取样长度lr
用于评定轮廓粗糙度在X轴向上的一段长度,数值上它与轮 廓滤波器λc的标志波长相等。
互换性与测量技术基础表面粗糙度的标注和设计

14.2表面粗糙度的标注和设计主讲教师:马惠萍第4章 表面粗糙度设计1. 表面粗糙度的参数数值—标准值表4-1 Ra的数值(GB/T1031-2009)0.120.20 3.2500.0250.40 6.30.0500.8012.50.100 1.6025表4-2 Rz的数值(GB/T1031-2009)0.0250.40 6.310010000.0500.8012.52000.100 1.60254000.20 3.2508001. 表面粗糙度的参数数值—标准值表4-4 Rmr (c) 的数值(GB/T1031-2009)Rsm (c ) /%1015202530405060708090表4-3 Rsm 的数值(GB/T1031-2009)Rsm /mm0.0060.1 1.60.01250.2 3.20.0250.4 6.30.050.812.5评定参数选用幅度参数R a、R z附加参数---有特殊要求选用RSm , Rmr(c)优先选R a:粗糙度参数值在(0.025~6.3)μ m;电动轮廓仪(测量范围0.02-8 μ m )选R z:粗糙度参数值在(6.3~100)μm ,(0.008~0.020 )μm;采用光学仪器测量,特高或特低2. 表面粗糙度评定参数(4个)的选用评定参数选用幅度参数R a、R z附加参数---有特殊要求选用RSm , Rmr(c)RSm(轮廓单元平均宽度)(反映间距特性)——导轨、法兰—用于对密封性、涂漆性能、抗裂纹和抗腐蚀等有要求时;Rmr(c) (轮廓的支承长度率)(反映形状特性)—轴承、轴瓦—用于对耐磨性和接触刚度等有要求时,但同时要给出C值2. 表面粗糙度参数的选用6满足功能要求的前提下--值尽量大,表面粗糙(Rmr (c ) 值小 )(标准化)参数值的选用考虑(类比法)参考表4-5~4-7工作面比非工作面值小(同一个零件);摩擦面比非摩擦面值小;配合稳定、尺寸(几何)公差值小、密封性好等值小;满足功能要求的前提下--值尽量大,表面粗糙(Rmr (c ) 值小 )(标准化)参数值的选用考虑(类比法)参考表4-5~4-7小间隙配合和重载过盈配合值小相同公差等级:轴比孔小,小尺寸比大尺寸小特殊应按标准规定确定粗糙度值4-54-64-7一.表面粗糙度的符号4.2.2 表面粗糙度的标注二. 表面粗糙度要求标注的内容及其注法1. 表面粗糙度要求标注的内容表面粗糙度要求标注的内容:表面粗糙度单一要求(不可省略)取样长度传输带加工工艺加工余量等补充要求1. 表面粗糙度要求标注的内容b图粗糙度要求的注写的位置a —第一个表面粗糙度(单一)要求(μm);b — 第二个表面粗糙度要求(μm);c — 加工方法(车,铣,磨,镀等);d — 表面纹理和纹理方向;e — 加工余量(单位:mm)。
表面粗糙度的评定
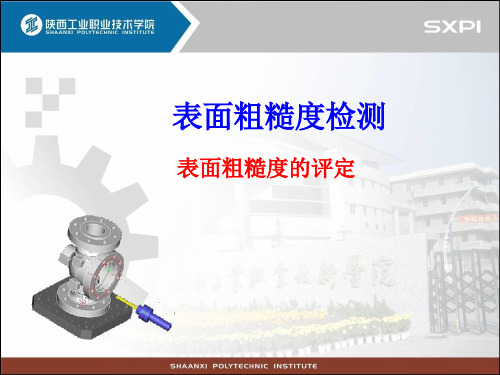
表面粗糙度的评定参数
1.基本术语及定义(GB/T 3505-2000) 轮廓中线 具有几何轮廓形状并划分轮廓的基准线
轮 廓 中 线
轮廓的最小二乘中线 轮廓的算术平均中线
表面粗糙度的评定参数
1.基本术语及定义(GB/T 3505-2000) 轮廓中线
轮廓偏距z是指测量方 向上,轮廓线上的点与 基准线之间的距离 1)轮廓的最小二乘中线
表面粗糙度的评定参数
1.基本术语及定义(GB/T 3505-2000)
表面粗糙度的评定参数
表5-1 轮廓算术平均偏差Ra、轮廓最大高度Rz和轮廓单元的 平均宽度Rz,标准取样长度和标准评定长度(摘自GB/T 1301 -2009、 GB/T 10610-2009)、 表示滤波器传输带λs ~λc 这两个极限值标准化值取自GB/T 6062-2002。
度ln的比率。
给出Rmr(c)参数时,必须同时给出轮廓水平截距c值。
表面粗糙度的评定参数
2.评定参数(GB/T 3505-2000) 国家标准GB/T1031-1995规定: 基本评定参数:幅度参数
附加评定参数:间距和形状特性参数
在取样长度内,使轮廓线上各点轮廓偏距zi的平方和 最小的线。即表面Fra bibliotek糙度的评定参数
1.基本术语及定义(GB/T 3505-2000) 轮廓中线
2)轮廓算术平均中线
轮廓算术平均中线是指在取样长度内划分实际轮廓为 上、下两部分,且使两部分面积相等的基准线。 即
表面粗糙度的评定参数
1.基本术语及定义(GB/T 3505-2000) 轮廓峰顶线 轮廓峰顶线是指在取样长度内,平行于基准线并通 过轮廓最高点的线。
表面粗糙度零件的图纸
零件三维图纸
第1章互换性原理_C粗糙度_

y
y
返回
(5) 螺纹与圆柱齿轮的精度标注
1 螺纹的公差等级及标记
A A 放大
中径(d 2 ) 小径( d1 ) 大径(d )
螺纹构成要素
①牙型(牙型角和牙型 半角/2) ②中径D2(d2) ③螺距P(多螺纹线时为 导程L) ④线数n ⑤旋向(左或右)
α α α 2 2
L (= P )
图 1- 53 组成螺纹的五个要素
(2)表面粗糙度的评定
基本术语及定义
表面轮廓
一个指定平面与实际表面相交所得的轮廓线
•通常按横向实际轮廓, 即与加工纹理方向垂直 的截面上的轮廓
Z
横 向轮廓
实际表面
坐标规定 (新标准)
Y X(轮廓总 走向)
加 工纹理方 向 平面
图 1 -4 1 实际轮 廓线
取样长度
在X轴方向判别被评定轮廓不规则特征的长度,lr ,在轮廓总走向(X轴向)量取
表面粗糙度选用实例
见教材表1-31(以下请记住) Ra值 6.3:机械加工非配合面。 3.2:基本加工方法可达的经济值。 1.6:次要配合中的一般配合面。 0.8:配合面常用值,广泛应用。 0.4:重要工作表面。 0.2:精密机床,气密要求
返回
(4)表面粗糙度的标注
表面粗糙度的符号
符 号 意 义 及 说 明
表面粗糙度的标注实例
表面粗糙度一般标注
总原则是使表面结构的注写和读取方 向与尺寸的注写和读取方向一致。
符号应从材料外指向并接触表面。
可标注在轮廓线上、给定的尺寸线上、 几何公差框格上方,还可用带箭头或黑 点的指引线引出标注,
表面粗糙度的简化注法
如果在工件的多数(包括全部)表面有相同的表面结构要求,则 其表面结构要求可统一标注在图样的标题栏附近(旧标准规定标注 在图样的右上角)。此时除全部表面有相同要求的情况外,还应在 表面粗糙度符号后面的圆括号中给出无任何其它标注的基本符号; 或者在圆括号内给出图形中已标注的不同的表面结构要求
《互换性》 第4章 表面粗糙度
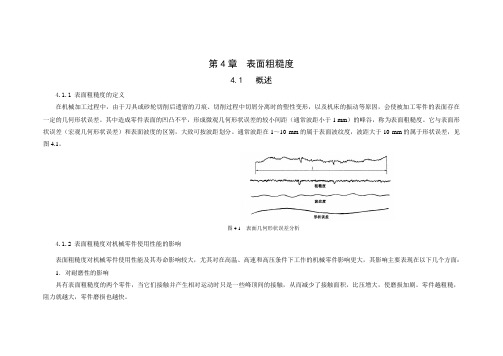
第4章表面粗糙度4.1 概述4.1.1 表面粗糙度的定义在机械加工过程中,由于刀具或砂轮切削后遗留的刀痕、切削过程中切屑分离时的塑性变形,以及机床的振动等原因,会使被加工零件的表面存在一定的几何形状误差。
其中造成零件表面的凹凸不平,形成微观几何形状误差的较小间距(通常波距小于1 mm)的峰谷,称为表面粗糙度。
它与表面形状误差(宏观几何形状误差)和表面波度的区别,大致可按波距划分。
通常波距在1~10 mm的属于表面波纹度,波距大于10 mm的属于形状误差,见图4.1。
图4.1 表面几何形状误差分析4.1.2 表面粗糙度对机械零件使用性能的影响表面粗糙度对机械零件使用性能及其寿命影响较大,尤其对在高温、高速和高压条件下工作的机械零件影响更大,其影响主要表现在以下几个方面:1.对耐磨性的影响具有表面粗糙度的两个零件,当它们接触并产生相对运动时只是一些峰顶间的接触,从而减少了接触面积,比压增大,使磨损加剧。
零件越粗糙,阻力就越大,零件磨损也越快。
但需指出,零件表面越光滑,磨损量不一定越小。
因为零件的耐磨性除受表面粗糙度影响外,还与磨损下来的金属微粒的刻划,以及润滑油被挤出和分子间的吸附作用等因素有关。
所以,过于光滑表面的耐磨性不一定好。
2.对配合性质的影响对于间隙配合,相对运动的表面因其粗糙不平而迅速磨损,致使间隙增大;对于过盈配合,表面轮廓峰顶在装配时易被挤平,实际有效过盈减小,致使连接强度降低。
因此,表面粗糙度影响配合性质的可靠性和稳定性。
3.对抗疲劳强度的影响零件表面越粗糙,凹痕越深,波谷的曲率半径也越小,对应力集中越敏感。
特别是当零件承受交变载荷时,由于应力集中的影响,使疲劳强度降低,导致零件表面产生裂纹而损坏。
4.对接触刚度的影响由于两表面接触时,实际接触面仅为理想接触面积的一部分。
零件表面越粗糙,实际接触面积就愈小,单位面积压力增大,零件表面局部变形必然增大,接触刚度降低,影响零件的工作精度和抗振性。
精选互换性与技术测量表面粗糙度公差与配合形状与位置公差

用去除材料的方法获得的表面, Ra的上限值为3.2m,加工方法为铣制。
用去除材料的方法获得的表面, Ra的最大值为3.2m,最小值为1.6m。
四、表面粗糙度代号在图样上的标注
★ 在同一图样上每一表面只注一次粗糙度代号,且应注在可见轮廓线、尺寸界线、引出线或它们的延长线上,并尽可能靠近有关尺寸线。
形状公差和位置公差简称形位公差,是指零件的实际形状和实际位置对理想形状和理想位置的允许变动量。 对一般零件来说,它的形状和位置公差,可由尺寸公差、加工机床的精度等加以保证。而对精度较高的零件,则根据设计要求,需在零件图上注出有关的形状和位置公差。
一、形位公差代号、基准代号
轴与孔的基本偏差代号用拉丁字母表示,大写为孔,小写为轴,各有28个。其中H(h)的基本偏差为零,常作为基准孔或基准轴的偏差代号。
A~H(a~h)的基本偏差用于间隙配合;P~ZC(p~zc)用于过盈配合;J(j)~N(n)用于过渡配合。
5、配合制度1)、基孔制 基本偏差为一定的孔的公差带,与不同基本偏 差的轴的公差带形成各种配合的一种制度。
★ 当零件所有表面都有相同表面粗糙度要求时,可在图样右上角统一标注代号。
★ 对不连续的同一表面,可用细实线相连,其表面粗糙度代号可注一次。
★ 零件上连续要素及重复要素(孔、槽、齿等)的表面,其表面粗糙度代号只注一次。
★ 齿轮、渐开线花键的工作表面,在图中没有表示出齿形时,其粗糙度代号可注在分度线上。螺纹表面需要标注表面粗糙度时,标注在螺纹尺寸线上。
例2 查表写出Φ80R7/h6的极限偏差值。 解:从配合表可知Φ80R7/h6是基轴制常用过盈配合。
(2) Φ80R7配合孔的极限偏差,则由附录表的基本尺寸大于50至80的行与公差等级IT7的列相交处查得Φ80R7的标准公差是30μm。由附表的基本尺寸大于65至80的行与基本偏差代号为R的列相交处查得Φ80R7的上偏差(ES)为-43μm。从而由计算公式EI=ES-IT可得到下偏差为(EI)= - 43 - 30= -73 μm,所以可写成
互换性与测量技术基础-chap5

部分纹理代号
加工纹理
加工纹理示例
粗糙度标注示例
粗糙度标注示例
粗糙度标注示例
粗糙度标注示例
表面结构参数文本书写代号与含义
1983标准与2009标准参数的比较
Ry Ra Sm tp Rz 取消
Rz Ra Rsm Rmr
表面结构要求的图形标注的演变
r (c)的选用 能直观反映实际接触面积的大小,它综合反映 了峰高和间距的影响,而摩擦、磨损、接触变 形都与实际接触面积有关,故此时适宜选用参 数Rmr (c)。 必须同时给出水平截距c 值,R 的5%、10%、 15%、20%、25%、30%、40%、50%、60%、 70%、80%、90%。
5.3 表面粗糙度的选用
原则:在满足功能要求的前提下,尽量选用较大的表 面粗糙度参数值,以便于加工,降低生产成本,获得 较好的经济效益。 表面粗糙度评定参数值选用通常采用类比法。 ① 同一零件上,工作表面的粗糙度应比非工作表面要 求严, Rmr(c)值应大,其余评定参数值应小。 ② 对于摩擦表面,速度愈高,单位面积压力愈大,则 表面粗糙度值应越小,尤其是对滚动摩擦表面应更小。
表面评定的流程
5.1 概述
有关的评定依据 1 取样长度lp、lr、lw
在轮廓的X 轴方向上量取的用于判别轮廓不规 则特征的一段基准线长度。 2 评定长度ln 用于判别被评定轮廓的X 轴方向上的长度,包 含有一个或几个取样长度的长度。
取样长度与评定长度
5.1 概述 3 中线
具有几何轮廓形状并划分轮廓的中线。 1)用cλ 滤波器抑制长波轮廓成分后对应的中线称 为粗糙度轮廓中线(mean line for the roughness profile); 2) 用fλ 滤波器抑制长波轮廓成分后对应的中线称 为波纹度轮廓中线(mean line for the aviness profile); 3) 对原始轮廓进行最小二乘拟合,按标称形状所 获得的中线称为原始轮廓中线(mean line for the primary profile)。
互换性与测量技术 表面粗糙度-题-整理

表面粗糙度一、判断题〔正确的打“A”,错误的打“B”〕1.确定表面粗糙度时,通常可在两项高度特性方面的参数中选取。
()2.评定表面轮廓粗糙度所必需的一段长度称取样长度,它可以包含几个评定长度。
()3.一个取样长度至少包含5个微峰和5个微谷()4.一般加工表面选取评定长度为几个连续的取样长度()5.Rz参数由于测量点不多,因此在反映微观几何形状高度方面的特性不如Ra参数充分。
()6.Rz参数对某些表面上不允许出现较深的加工痕迹和小零件的表面质量有实用意义。
()7.Rz不能较准确地反映表面轮廓的微观几何特征,所以不能单独使用。
()8.选择表面粗糙度评定参数值应尽量小好。
()9.在保证满足技术要求的前提下,选用较小的表面粗糙度数值。
()10.零件的尺寸精度越高,通常表面粗糙度参数值相应取得越小。
()11.零件的表面粗糙度值越小,则零件的尺寸精度应越高。
()12.摩擦表面比非摩擦表面的表面粗糙度数值小。
滚动摩擦表面比滑动摩擦表面的表面粗糙度值小()13.要求配合精度高的零件,其表面粗糙度数值应大。
()14.运动速度高;受交变载荷、冲击载荷的零件,其表面粗糙度值要求高。
()15.同一零件,配合表面、工作表面的粗糙度数值小于非配合表面、非工作表面的数值。
()16.摩擦表面、承受重载荷和交变载荷表面的粗糙度数值应选较小值。
()17.配合精度要求高的结合面、尺寸公差和形位公差精度要求高的表面,粗糙度选较小值。
()18.同一公差等级的零件,小尺寸比大尺寸,轴比孔的粗糙度值要小。
()19.工作表面比非工作表面的粗糙度数值要求高。
()20.要求耐腐蚀的表面,粗糙度值应选较小值。
()21.有关标准已对表面粗糙度要求作出规定的应按相应标准确定表面粗糙度数值。
()22.接触刚度是零件结合面在外力作用下,抵抗接触变形的能力。
机器的刚度在很大程度上取决于各零件之间的接触刚度。
表面粗糙度影响零件的接触刚度。
()23.零件被测表面和测量工具测量面的表面粗糙度都会直接影响测量的精度,尤其是在精密测量时。
互换性第5章表面粗糙度(新标准讲稿)

2019/12/21
17/51
取样长度 lr 和评定长度 ln
第5章 表面粗糙度及检测
2019/12/21
18/51
第5章 表面粗糙度及检测
5.2.4 中线(mean line)
具有几何轮廓形状并划分轮廓的基准线。
中线穿过粗糙度轮廓,是用来确定粗糙度参数的基准线。它是用λc 轮廓滤波器抑制长波成分后形成的轮廓的中线——最小二乘中线。
11/51
第5章 表面粗糙度及检测
5.2.1 轮廓滤波器(profile filter)
用轮廓法测量表面粗轮粗廓粗 时粗 粗,把轮粗廓粗分粗为粗长粗波和短波的滤波器。
传输系数/%
λs
λc
λf 波长
■ λs 轮廓滤波器
确定存在于表面上的粗糙度与比它更短的波的成分之间相交界限的滤波器。
■ λc 轮廓滤波器
13/51
第5章 表面粗糙度及检测
5.2.2 表面轮廓与轮廓参数
■ 原始轮廓(primary profile)——P轮廓
经过λs 轮廓滤波器后的总轮廓。
在原始轮廓上计算得到 的参数称为P参数。
■ 粗糙度轮廓(roughness profile)——R轮廓
对原始轮廓采用λc 轮廓滤波器抑制长波成分以后形成的轮廓。 在粗糙度轮廓上计算得 到的参数称为R参数。
6.3
100
1600
Rz
0.05 0.1
0.8 1.6
12.5 25
200 400
0.2
3.2
50
800
2019/12/21
28/51
第5章 表面粗糙度及检测
轮廓的单元平均间距Rsm的数值 (mm)
0.006
互换性与技术测量 第五章_表面粗糙度轮廓及其监测

第五章表面粗糙度轮廓及其监测一、判断题1.Rz参数由于测量点不多,因此在反映微观几何形状高度方面的特性不如Ra参数充分。
(对)2.零件的尺寸精度越高,通常表面粗糙度参数值相应取得越小。
(对)3.零件的表面粗糙度值越小,则零件的尺寸精度应越高。
(错)4.利用摩擦原理工作的表面应比非摩擦表面的表面粗糙度数值小。
(错)5.确定表面粗糙度时,通常必须三项高度特性方面的参数中选取。
(对)6.对过盈配合来说,表面粗糙会减小实际有效过盈,降低连接强度。
(对)7.轮廓的算术平均偏差最客观全面的反映了零件表面的粗糙程度。
(对)8.评定表面粗糙度时,规定取样长度是为了使测量方便。
(错)9.轮廓支撑长度率越大,则轮廓承受载荷的面积越大,所以就越耐磨。
(对)10.表面越粗糙,取样长度应越长。
(对)11.轮廓微观不平度的平均间距和轮廓支撑长度率主要用于控制表面加工痕迹的细密度。
(对)13.要求配合精度高的零件,其表面粗糙度数值应大。
(错)14.在加工过程中,刀具进给不规则或回转质量不平衡会形成工件表面波纹度。
(对)15.受交变载荷的零件,其表面粗糙度值应小。
(对)16.符号代表用任何方法获得的表面粗糙度,Ra的上限值为3.2。
(错)17.同一加工表面的值肯定大于值。
(对)18.评定表面轮廓粗糙度所必需的一段长度称评定长度,它可以包含几个取样长度。
(对)19.选择表面粗糙度参数值应尽量小。
(错)20.评定表面粗糙度时,规定评定长度是为了减少表面波度的影响。
(错)21.工件表面越粗糙,摩擦系数越大;工件表面越光洁,摩擦系数越小(错)22.国家标准规定经常采用的表面粗糙度幅度参数为轮廓算术平均偏差和轮廓的均方根偏差。
(错)二、填空题1.在同一水平位置上,轮廓支撑长度率数值越大,表示实体材料的长度占评定长度的比率越( ),( )和( )越好。
[答案]大;支撑刚度;耐磨性2.选择表面粗糙度轮廓的评定参数时,应优先使用( )。
[答案]轮廓的算术平均偏差3.用去除材料的方法获得的表面Ra的最大值为3.2,Ra的最小值为1.6,则该表面的粗糙度轮廓应标注为( )。
互换性A 5 表面粗糙度
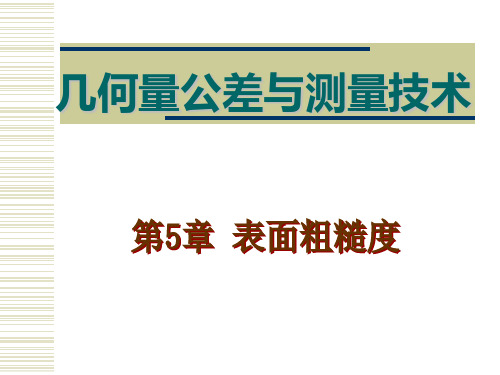
§5.4 表面粗糙度在零件图上的标注
二、表面粗糙度要求在完整图形符号上的标注 3、极限值判断规则的标注
表面粗糙度要求中给定极限值判断规则有两种: 16﹪规则是指在同一评定长度范围内评定参数所有 实测值中,大于上限值的个数少于总数的16﹪,小于下 限值的个数少于总数的16﹪ ,则认为合格。 16﹪规则 是表面粗糙度要求标注中的默认规则。 最大规则是指整个被测表面上评定参数所有的实测 值皆不大于上限值,才认为合格。标注时,在评定参数 代号的后面加注一个“max”标记。
F S
i 1 i i 1
n
m
i
将实际轮廓划分为面积相等的 ②轮廓的算术平均中线:上、下两部分的线。
§5.2 表面粗糙度的评定
二、基本术语和定义
2、取样长度(lr):是指在测量方向判别被评定 轮廓不规则特征的长度。它至少包含5个以上的 轮廓峰和谷,取样长度的方向与轮廓走向一致。
注意:规定取样长度的目的在于限制和减弱其他形状 误差,特别是表面波纹度对测量结果的影响。 粗糙度参数值是在一个取样长度上评定出来的。
二、表面粗糙度要求在完整图形符号上的标注
2、表面粗糙度极限值的标注 在完整图形符号上标注评定参数及其数值,其数值 分为单向极限值和双向极限值。 ①单向极限值:当只标注某个评定参数代号及其一个数 值时为单向极限值。默认它是评定参数的上限值。 ②双向极限值:同时标注评定参数的上下限值时为双向 极限值。双向极限值应分成两行标注,上限值标注在上 方,并在传输带前加注代号“U”;下限值标注在下方, 并 在传输带前加注代号“L”。一般在不会引起歧义的情况 下,可以不加“U” “L”。
位置b,注写第二个表面粗糙度要求。有更多要求,图形符号应 在垂直方向扩大,以空出足够空间。 位置c,注写加工方法、表面处理、涂层和其他加工工艺要求等。 如车、磨、镀等。 位置d,注写所要求的表面纹理和纹理方向,如“=”“⊥”“×” 等。 位置e,注写所要求的加工余量,以mm为单位给出数值。