热处理基本原理.
热处理原理与工艺

热处理原理与工艺热处理是一种通过加热和冷却来改变材料性能的工艺。
它可以使金属材料获得所需的力学性能、物理性能和化学性能,从而满足不同工程要求。
热处理工艺包括退火、正火、淬火、回火等,不同的工艺可以实现不同的效果。
下面将详细介绍热处理的原理和工艺。
首先,我们来介绍退火工艺。
退火是将金属材料加热到一定温度,保持一定时间后,再以适当速度冷却到室温。
退火的目的是消除材料内部的应力,改善塑性和韧性,降低硬度。
这种工艺适用于大多数金属材料,尤其是碳钢和合金钢。
其次,正火工艺是将金属材料加热到临界温度以上,保持一定时间后,再冷却到室温。
正火可以提高金属的硬度和强度,同时保持一定的韧性。
这种工艺适用于低碳钢、合金钢和工具钢等材料。
淬火是将金属材料加热到临界温度以上,然后迅速冷却到室温。
淬火可以使金属材料获得高硬度和高强度,但同时会降低其韧性。
这种工艺适用于合金钢、高速钢和不锈钢等材料。
最后,回火是将经过淬火处理的金属材料加热到一定温度,然后保持一定时间后冷却。
回火可以降低金属的脆性,提高韧性和塑性。
这种工艺适用于经过淬火处理的合金钢和工具钢等材料。
在进行热处理工艺时,需要注意控制加热温度、保温时间和冷却速度,以确保获得所需的材料性能。
同时,还需要考虑材料的化学成分、组织结构和形状等因素,综合运用各种热处理工艺,以达到最佳的效果。
总之,热处理是一种重要的金属材料加工工艺,通过改变材料的组织结构和性能,可以满足不同工程要求。
各种热处理工艺都有其特定的原理和适用范围,只有深入理解这些原理,才能正确地选择和应用热处理工艺,从而获得优质的金属材料。
化学热处理的基本原理

5.1 化学热处理基本原理化学热处理过程是一个比较复杂的过程。
一般常把它看成由渗剂中的反应。
渗剂中的扩散,渗剂与被渗金属表面的界面反应,被渗元素原子的扩散和扩散过程中相变等过程所构成。
如气体渗氮时,通人氨气与钢表面产生相界面反应2NH3=3H2十2[N]产生活性氮原子,渗入钢件表面进行渗氮。
渗金属时也可以类似反应表示。
扩散是相界面反应产生的原子渗入金属表面后向钢件内部的迁移过程。
化学热处理过程有时可以只有扩散过程.例如用热浸法渗金属时,就是把工件浸在熔融的金属中,直接吸附金属原子并向内部扩散。
二:化学热处理渗剂及其在化学热处理过程中的化学反应机制化学热处理的渗剂一般由含有欲渗元素的物质组成,有时还须按一定比例加入一种催渗剂,以便从渗剂中分解出含有被渗元素的活性物质。
但不是所有含有被渗元素的物质均可作为渗剂,而作为渗剂的物质应该具有一定的活性。
所谓渗剂的活性就是在相界面反应中易于分解出被渗元素原子的能力。
例如普通气体渗氮就不能用N2作为渗氮剂,因为N2在普通渗氮温度不能分解出活性氮原子。
催化剂是促进含有被渗元素的物质分解或产生出活性原子的物质,它仅是一种中间介质,本身不产生被渗无素的活性原子.例如因体渗碳时,除了炭粒以外,还尚须加碳酸钡和碳酸钠,这碳酸钡和碳酸钠就是催渗剂,碳酸钡和碳酸钠在渗碳前后没有变化,仅在渗碳过程中把炭粒变成活性物质CO.化学热处理时分解出被渗元素的活性原子的化学反应有如下几类:1.分解反应普通气体渗碳及气体渗氮都属于这一类。
例如用甲烷渗碳CH4=2H2十[C]2.置换反应例如渗金属时,常按下列反应进行MeCIx+Fe—→FeCl3+Me 在钢表面沉积出金属。
3.还原反应例如渗金属时有时按下列反应进行MeCIx+H2—→FeCl3+Me不论何种反应,其分解出被渗元素的能力均可根据质量作用定律确定。
根据质量作用定律,每一反应的平衡常数,在常压下,取决于温度。
而当温度一定时,平衡常数也一定,则主要取决于参加反应物质的浓度(液态反应)或分压(气态反应)。
热处理基本原理
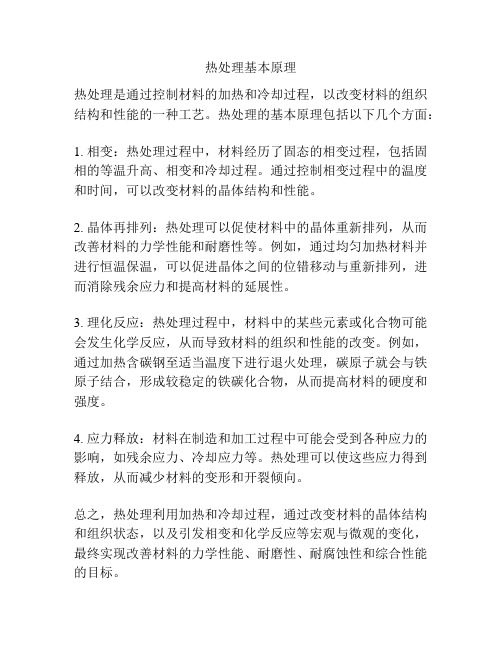
热处理基本原理
热处理是通过控制材料的加热和冷却过程,以改变材料的组织结构和性能的一种工艺。
热处理的基本原理包括以下几个方面:
1. 相变:热处理过程中,材料经历了固态的相变过程,包括固相的等温升高、相变和冷却过程。
通过控制相变过程中的温度和时间,可以改变材料的晶体结构和性能。
2. 晶体再排列:热处理可以促使材料中的晶体重新排列,从而改善材料的力学性能和耐磨性等。
例如,通过均匀加热材料并进行恒温保温,可以促进晶体之间的位错移动与重新排列,进而消除残余应力和提高材料的延展性。
3. 理化反应:热处理过程中,材料中的某些元素或化合物可能会发生化学反应,从而导致材料的组织和性能的改变。
例如,通过加热含碳钢至适当温度下进行退火处理,碳原子就会与铁原子结合,形成较稳定的铁碳化合物,从而提高材料的硬度和强度。
4. 应力释放:材料在制造和加工过程中可能会受到各种应力的影响,如残余应力、冷却应力等。
热处理可以使这些应力得到释放,从而减少材料的变形和开裂倾向。
总之,热处理利用加热和冷却过程,通过改变材料的晶体结构和组织状态,以及引发相变和化学反应等宏观与微观的变化,最终实现改善材料的力学性能、耐磨性、耐腐蚀性和综合性能的目标。
热处理基本知识及工艺原理
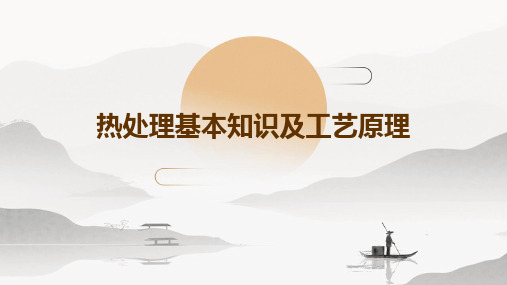
将淬火后的金属材料加热到适当温度,保温一定时间后冷 却至室温。回火可以消除淬火产生的内应力,提高金属材 料的韧性和塑性。
02
热处理工艺原理
加热与冷却
加热
热处理过程中,将金属材料加热至所 需温度,以实现所需的相变和组织转 变。加热方式包括电热、燃气热、微 波加热等。
冷却
热处理过程中,金属材料在加热后需 进行冷却,以控制相变和组织转变的 过程。根据冷却速度的不同,可分为 缓慢冷却和快速冷却。
感谢您的观看
THANKS
热处理的分类
1. 退火
将金属材料加热到适当温度,保温一定时间后缓慢冷却至 室温。退火可以提高金属材料的塑性和韧性,消除内应力 。
3. 淬火
将金属材料加热到适当温度,保温一定时间后快速冷却至 室温。淬火可以提高金属材料的硬度和耐磨性,但可能导 致内应力增大。
2. 正火
将金属材料加热到适当温度,保温一定时间后在空气中自 然冷却。正火可以提高金属材料的强度和韧性,细化组织 结构。
离子注入技术
将具有特定能量的离子注 入材料表面,改变其物理 和化学性质,提高耐磨、 耐腐蚀等性能。
提高热处理效率与节能减排
高效加热方式
采用电磁感应、微波加热 等高效加热方式,缩短加 热时间,提高热处理效率。
余热回收利用
对热处理过程中的余热进 行回收和再利用,减少能 源浪费,降低碳排放。
环保材料与工艺
热处理基本知识及工艺艺原理 • 常见热处理工艺 • 热处理的应用 • 热处理的发展趋势与挑战
01
热处理基本概念
热处理的定义
热处理:通过加热、保温和冷却等工 艺手段,改变金属材料的内部组织结 构,以达到改善其性能、满足使用要 求的一种工艺方法。
热处理的基本知识
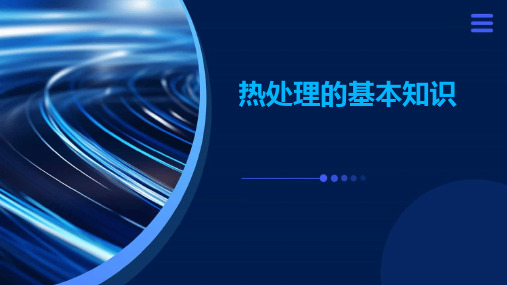
过烧与欠烧的预防与控制
总结词
过烧和欠烧是热处理中常见的问题,它们会 影响材料的性能和热处理的可靠性。
详细描述
过烧是指加热温度过高或保温时间过长,导 致材料内部晶粒长大、氧化或融化。欠烧则 是加热温度或保温时间不足,导致材料未完 全奥氏体化或淬火不完全。为了预防和控制 过烧和欠烧,需要精确控制加热温度和时间 ,以及选择适当的加热和冷却速度。
气氛
热处理过程中所选择的气氛(如空 气、保护气体等)会影响金属的氧 化、脱碳等化学变化。
03
CATALOGUE
热处理工艺分类
退火
退火是将金属加热到适当温度,保持一定时 间,然后缓慢冷却的过程。其目的是消除内 应力、降低硬度、提高塑性和韧性。
退火工艺可分为完全退火、等温退火和球化 退火等。完全退火是将金属加热到临界点以 上,使组织完全奥氏体化,然后随炉缓慢冷 却;等温退火是将金属加热到临界点以上某 一温度,保持一定时间后快速冷却至室温; 球化退火则是将金属加热到略低于临界点温
05
CATALOGUE
热处理中的问题与解决方案
裂纹的产生与预防
总结词
裂纹是热处理中常见的问题,其产生与 多种因素有关,如冷却速度、加热温度 等。
VS
详细描述
裂纹的产生通常是由于热处理过程中材料 内部应力的集中和超过材料的断裂强度所 引起的。为了预防裂纹的产生,需要控制 加热和冷却速度,选择适当的加热温度和 时间,以及采用适当的热处理工艺。
THANKS
感谢观看
04
CATALOGUE
热处理的应用
钢铁工业
01
钢铁是热处理应用最广泛的材料 之一,通过不同的热处理工艺, 可以改变钢铁的内部结构和性能 ,以满足各种不同的需求。
热处理原理与工艺ppt

1 2
空气冷却器
利用空气作为冷却介质,通过换热器将热量带 走。
水冷装置
利用水作为冷却介质,通过循环水将热量带走 。
3
油冷装置
利用油作为冷却介质,通过油循环将热量带走 。
辅助设备
输送装置
包括输送带、辊道等, 用于工件的输送和定位 。
装料装置
包括料仓、料斗、抓斗 等,用于工件的装料和 卸料。
加热元件
包括电热丝、硅碳棒等 ,用于加热设备中的加 热元件。
热处理质量控制
为了保证热处理效果的一致性和可靠性,需要对热处理过 程进行严格的质量控制,包括温度控制、时间控制和气氛 控制等。
展望
01
新技术的发展
随着科技的不断进步,新的热处理技术也不断涌现。例如,真空热处
理、保护气氛热处理和激光热处理等新技术的应用,将进一步提高热
处理质量和效率。
02
节能减排的需求
Байду номын сангаас
04
热处理的应用
工业应用
航空航天领域
为了提高航空航天构件的强度、硬度、韧性和疲劳性能,通常 需要进行热处理。
汽车工业
汽车零部件如齿轮、轴、弹簧等需要进行热处理,以提高其耐 磨性和抗疲劳性能。
机械制造
在机械制造过程中,对金属材料进行热处理可以改变其内部结 构,提高材料的使用性能。
日常生活应用
餐具
THANKS
热处理原理应用
广泛应用于机械制造业、 冶金工业、电子工业等领 域。
热处理的过程
加热
将金属材料加热到一定温 度,使其发生相变或奥氏 体化。
保温
保持一定时间,使金属材 料充分吸收热量,达到预 期的组织结构。
冷却
热处理工艺的原理和应用
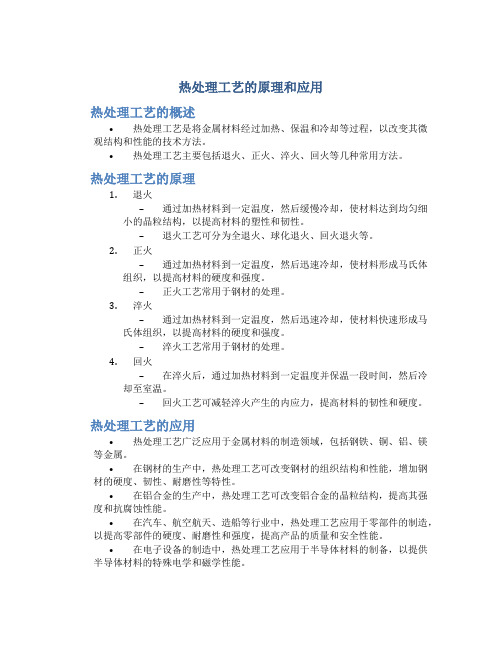
热处理工艺的原理和应用热处理工艺的概述•热处理工艺是将金属材料经过加热、保温和冷却等过程,以改变其微观结构和性能的技术方法。
•热处理工艺主要包括退火、正火、淬火、回火等几种常用方法。
热处理工艺的原理1.退火–通过加热材料到一定温度,然后缓慢冷却,使材料达到均匀细小的晶粒结构,以提高材料的塑性和韧性。
–退火工艺可分为全退火、球化退火、回火退火等。
2.正火–通过加热材料到一定温度,然后迅速冷却,使材料形成马氏体组织,以提高材料的硬度和强度。
–正火工艺常用于钢材的处理。
3.淬火–通过加热材料到一定温度,然后迅速冷却,使材料快速形成马氏体组织,以提高材料的硬度和强度。
–淬火工艺常用于钢材的处理。
4.回火–在淬火后,通过加热材料到一定温度并保温一段时间,然后冷却至室温。
–回火工艺可减轻淬火产生的内应力,提高材料的韧性和硬度。
热处理工艺的应用•热处理工艺广泛应用于金属材料的制造领域,包括钢铁、铜、铝、镁等金属。
•在钢材的生产中,热处理工艺可改变钢材的组织结构和性能,增加钢材的硬度、韧性、耐磨性等特性。
•在铝合金的生产中,热处理工艺可改变铝合金的晶粒结构,提高其强度和抗腐蚀性能。
•在汽车、航空航天、造船等行业中,热处理工艺应用于零部件的制造,以提高零部件的硬度、耐磨性和强度,提高产品的质量和安全性能。
•在电子设备的制造中,热处理工艺应用于半导体材料的制备,以提供半导体材料的特殊电学和磁学性能。
热处理工艺的优点•可改善金属材料的物理性能,提高材料的硬度、韧性、强度等。
•可改变材料的晶粒结构和组织,提供特定的材料性能。
•可改善材料的表面质量,提高耐磨性和耐腐蚀性。
•可通过控制热处理工艺参数,实现材料性能的调控和优化。
热处理工艺的注意事项•热处理工艺的参数,包括加热温度、保温时间、冷却速度等,需要根据材料的类型和要求进行合理选择,以避免材料的过热或过冷现象。
•热处理工艺需要严格控制各个环节的温度和时间,以保证工艺的有效性和一致性。
热处理培训资料

热处理培训资料
热处理是一种重要的金属加工工艺,通过控制金属材料的加热、保
温和冷却过程,改变其晶体结构和性能,从而使其具有更好的强度、
硬度、韧性等特性。
为了帮助大家更好地了解热处理技术,以下是一
些关于热处理的培训资料:
一、热处理的基本原理
1. 热处理的定义:热处理是通过加热、保温和冷却等工艺对金属材
料进行控制,使其获得一定的组织结构和性能。
2. 热处理的分类:热处理可以分为退火、正火、淬火、回火等不同
类型,每种类型的热处理都有其特定的工艺条件和效果。
二、热处理的步骤和工艺
1. 加热:将金属材料置于炉内或其他加热设备中,加热至一定温度,使其达到所需要的状态。
2. 保温:在达到所需温度后,保持一定时间,使金属材料的温度均
匀分布和晶粒重新组织。
3. 冷却:将金属材料迅速冷却至室温,以实现所需的组织结构和性能。
三、热处理的影响因素
1. 温度:加热和保温过程中的温度对金属材料的热处理效果有着重
要影响,温度过高或过低都可能导致热处理效果不理想。
2. 时间:保温时间的长短决定了金属材料晶粒的再结晶和再结晶的程度,影响其力学性能等方面。
3. 冷却速度:冷却速度快慢直接影响金属材料的组织结构和性能,过快或过慢都可能导致不良影响。
四、热处理的应用领域
1. 通用机械制造业:汽车、机床、航空航天等领域都广泛应用热处理技术,以提高产品的性能和寿命。
2. 金属材料加工业:钢铁、铝合金、铜合金等金属材料在生产加工过程中常常需要进行热处理,以改善其物理、化学性能。
3. 工具制造业:刀具、模具等工具制造业中的工件经过适当的热处理,可以提高其耐磨性、硬度等性能。
热处理培训资料
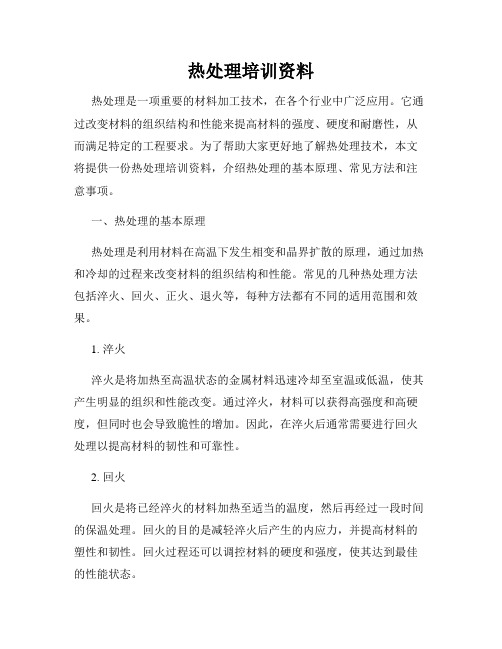
热处理培训资料热处理是一项重要的材料加工技术,在各个行业中广泛应用。
它通过改变材料的组织结构和性能来提高材料的强度、硬度和耐磨性,从而满足特定的工程要求。
为了帮助大家更好地了解热处理技术,本文将提供一份热处理培训资料,介绍热处理的基本原理、常见方法和注意事项。
一、热处理的基本原理热处理是利用材料在高温下发生相变和晶界扩散的原理,通过加热和冷却的过程来改变材料的组织结构和性能。
常见的几种热处理方法包括淬火、回火、正火、退火等,每种方法都有不同的适用范围和效果。
1. 淬火淬火是将加热至高温状态的金属材料迅速冷却至室温或低温,使其产生明显的组织和性能改变。
通过淬火,材料可以获得高强度和高硬度,但同时也会导致脆性的增加。
因此,在淬火后通常需要进行回火处理以提高材料的韧性和可靠性。
2. 回火回火是将已经淬火的材料加热至适当的温度,然后再经过一段时间的保温处理。
回火的目的是减轻淬火后产生的内应力,并提高材料的塑性和韧性。
回火过程还可以调控材料的硬度和强度,使其达到最佳的性能状态。
3. 正火正火是将材料加热至适当的温度,保温一定时间后进行冷却。
正火的目的是通过控制组织形态和材料的相变来调整材料的性能,以满足特定的工程要求。
正火适用于一些对硬度、强度和韧性要求均有的工件。
4. 退火退火是将已经加工或者变形的材料加热至一定温度,然后经过一定时间的保温处理,最后缓慢冷却。
退火的目的是通过晶界扩散来恢复材料的塑性和韧性,减少材料的内应力和变形。
退火可以改善材料的加工性能,提高材料的韧性和可塑性。
二、热处理的常见方法热处理有许多不同的方法和工艺,下面介绍几种常见的热处理方法:1. 淬火和回火工艺淬火和回火是最常用的热处理方法之一。
淬火可以通过控制冷却速度和介质的选择来改变材料的结构和性能,而回火则可以通过加热和保温的方式来调节材料的硬度和韧性。
2. 预淬火和再回火工艺预淬火和再回火是为了进一步改善材料的组织和性能而进行的热处理工艺。
热处理原理及工艺

热处理原理及工艺热处理是一种用于改善材料性能的重要工艺。
通过控制材料的加热和冷却过程,可以改变材料的晶体结构、力学性能和化学性能,从而提高材料的强度、硬度、耐腐蚀性等。
热处理的原理是基于固体材料的晶体结构与物理性能之间的关系。
晶体结构是由原子或分子的周期性排列所组成,不同的结构会导致不同的物理性能。
在加热过程中,材料中的原子或分子会随着温度的升高而具有更高的热运动能力,从而使晶体结构发生变化。
通过控制加热温度和时间,可以实现晶体结构的改变。
常见的热处理工艺包括退火、淬火、回火、表面处理等。
退火是将材料加热到特定温度,然后缓慢冷却至室温,目的是消除内部应力和改善材料的韧性。
淬火是在材料加热到高温后,迅速冷却至室温,通过快速冷却可以使材料形成硬脆结构,提高材料的硬度和强度,但也会导致内部应力增大,需要进行回火处理来消除应力。
回火是将淬火后的材料加热到适当温度,然后保温一段时间,最后缓慢冷却,目的是降低材料的硬度,提高韧性。
表面处理是在材料表面形成一层特定的化合物或合金层,用于改善材料的耐磨性、耐腐蚀性等。
热处理工艺的选择要根据材料的组成和应用要求进行。
不同材料具有不同的热处理敏感性和适用温度范围。
合理选择热处理工艺可以使材料在满足力学性能和物理性能要求的同时,减少成本和能源消耗。
总之,热处理是一种通过控制材料的加热和冷却过程,改善材料性能的重要工艺。
通过热处理可以改变材料的晶体结构和物理性能,提高材料的强度、硬度、韧性和耐腐蚀性等。
选择合适的热处理工艺对于提高材料的性能和使用寿命至关重要。
热处理是一种将金属或合金材料通过加热和冷却处理来改变其物理和机械性能的工艺。
它是材料加工中非常重要的一部分,因为可以通过控制热处理工艺,使材料的硬度、强度、韧性、耐腐蚀性等性能得到改善。
热处理的核心原理是通过控制材料的加热温度和冷却速度,使材料的晶体结构发生变化。
材料的晶体结构决定了其宏观性能。
例如,在晶体结构较均匀的钢中,碳原子分布均匀,这样就有利于提高钢材的硬度和强度。
热处理原理

70~80% ➢ 模具、滚动轴承100%需经过热处理 ——总之,重要零件都需适当热处理后才能使用。
3
热处理的基本要素
热处理工艺的三大基本要素:加热、保温、冷却
——这三大基本要素决定了材料热处理后的组织和 性能。
45钢正常淬火组织
41
3. 马氏体的性能
高硬度是马氏体性能 的主要特点
马氏体的硬度主要取 决于其含碳量
含碳量增加,其硬度 增加
马氏体硬度、韧性与含碳量的关系
当含碳量大于0.6%时,其硬度趋于平缓
合金元素对马氏体硬度的影响不大
42
马氏体强化的主要原因是过饱和碳引起的固溶强化, 此外,马氏体转变产生的组织细化也有强化作用
的范围,碳在铁素体的一定晶面上以断续碳化物小 片的形式析出
34
(三)马氏体转变
当奥氏体过冷到Ms以下将转 变为马氏体类型组织
马氏体转变是强化钢的重要 途径之一
1. 马氏体的晶体结构
马氏体组织
碳在-Fe中的过饱和固溶体 称马氏体,用M表示
马氏体转变时,奥氏体中的碳全部保留到马氏体中
35
马氏体具有体心四方晶格(a = b ≠ c) 轴比c/a称为四方度 C%越高,四方度越大,四方畸变越严重 当<0.25%C时,c/a=1,此时马氏体为体心立方晶格
材料的热处理
Heat Treatment of Steel
1
热处理指将钢在固态下加热、保温和冷却,以 改变钢的组织结构,获得所需要性能的工艺
包含热处理原理和热处理工艺两部分内容:
➢ 描述热处理时钢中组织转变的规律称为热处理 原理
➢ 根据热处理原理制定的温度、时间、介质等参 数称为热处理工艺
热处理学基本知识培训学习PPT课件
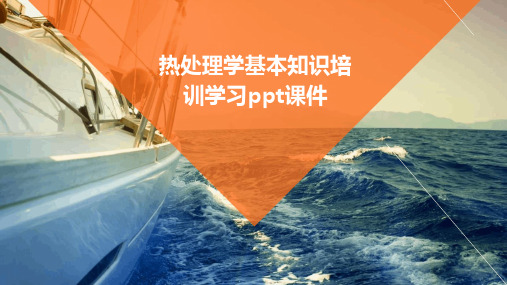
淬火工艺
总结词
淬火是热处理中重要的硬化工艺,通过快速冷却使金属材料硬化,提高其耐磨性和强度。
详细描述
淬火是将金属加热到高温后迅速冷却的过程。通过快速冷却,金属内部的晶体结构发生改变,产生硬 化效果。淬火后金属通常呈现高硬度和高强度,但同时也可能变得脆硬。因此,淬火后通常需要进行 回火处理。
回火工艺
表面热处理
总结词
表面热处理是针对金属表面进行的热处理工 艺,通过改变金属表面的组织结构,提高其 耐磨性、耐腐蚀性和抗氧化性。
详细描述
表面热处理是通过将金属表面局部或全部加 热到高温,然后迅速冷却或保温一定时间后 冷却的过程。常见的表面热处理方法包括渗 碳、渗氮、碳氮共渗等。这些方法可以在不 改变金属整体性能的情况下,提高其表面的 硬度和耐腐蚀性等性能指标。
汽车零部件的热处理
汽车制造业中,许多零部件需要进行热处理以提高其机械性能和耐腐蚀性。例如,发动 机活塞、曲轴、气瓶等都需要经过适当的热处理工艺。
轻量化设计
为了提高燃油效率和降低排放,汽车制造业正在推动轻量化设计。热处理技术在此过程 中发挥了重要作用,例如使用高强度钢材进行热处理,以实现部件的轻量化和高性能。
02 热处理的基本原理
热传导与热对流
热传导
热量通过物体内部微观粒子的相互作 用从高温区域传递到低温区域的过程。
热对流
由于流体各部分之间的相对运动或温 差而引起的热能传递过程,主要发生 在流体与固体接触的界面上。
热辐射与相变
热辐射
物体通过电磁波的形式释放和吸收热能的过程,是热量传递 的三种方式之一。
04 热处理设备与工具
加热设备
电阻炉
利用电阻加热原理,通过电流在电热元件上 产生热量来加热工件。
热处理的原理是什么
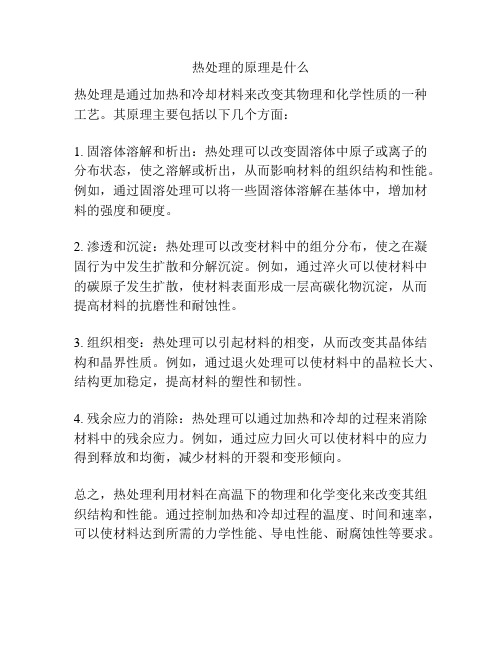
热处理的原理是什么
热处理是通过加热和冷却材料来改变其物理和化学性质的一种工艺。
其原理主要包括以下几个方面:
1. 固溶体溶解和析出:热处理可以改变固溶体中原子或离子的分布状态,使之溶解或析出,从而影响材料的组织结构和性能。
例如,通过固溶处理可以将一些固溶体溶解在基体中,增加材料的强度和硬度。
2. 渗透和沉淀:热处理可以改变材料中的组分分布,使之在凝固行为中发生扩散和分解沉淀。
例如,通过淬火可以使材料中的碳原子发生扩散,使材料表面形成一层高碳化物沉淀,从而提高材料的抗磨性和耐蚀性。
3. 组织相变:热处理可以引起材料的相变,从而改变其晶体结构和晶界性质。
例如,通过退火处理可以使材料中的晶粒长大、结构更加稳定,提高材料的塑性和韧性。
4. 残余应力的消除:热处理可以通过加热和冷却的过程来消除材料中的残余应力。
例如,通过应力回火可以使材料中的应力得到释放和均衡,减少材料的开裂和变形倾向。
总之,热处理利用材料在高温下的物理和化学变化来改变其组织结构和性能。
通过控制加热和冷却过程的温度、时间和速率,可以使材料达到所需的力学性能、导电性能、耐腐蚀性等要求。
热处理基础知识

热处理基础知识热处理基础知识热处理的原理热处理就是通过将⼯件放于⼀定的⽓氛中进⾏适当的加热、保温及冷却,以改变⼯件的性能的过程。
热处理术语整体热处理:把⾦属或⼯件进⾏穿透加热的热处理⼯艺。
本车间使⽤的热处理⼯艺均为整体热处理,包括:渗碳、淬(回)⽕、调质、正⽕、渗碳直接淬⽕等。
局部热处理:仅对⼯件的某个部件或⼏个部位进⾏热处理的⼯艺,常⽤的有⾼频淬⽕、激光表⾯处理等。
化学热处理:把⾦属材料或⼯件放在适当的活性介质中加热、保持,使⼀种或⼏种化学元素渗⼊其表层,以改变其化学成分、组织和性能的热处理⼯艺,渗碳是其中的⼀种。
可控⽓氛热处理:为达到⽆氧化、⽆脱碳、按要求增碳的⽬的,在成分可以控制的炉⽓中进⾏加热和冷却的热处理⼯艺。
本车间⽤的UBE渗碳⾃动⽣产线就是可控⽓氛热处理的⼀种。
真空热处理:在⼀定的真空度的加热炉中,可实现⼯件⽆氧化的热处理⼯艺。
热处理术语滴注式⽓氛:把含碳有机液体(⼀般⽤甲醇)定量滴⼊加热到⼀定温度(700℃以上)、密封良好的炉内,在炉内裂解形成的⽓氛。
甲醇裂解⽓可以⽤作渗碳载⽓、添加丙酮、异丙醇、煤油等可提⾼碳势,作为渗碳⽓氛。
淬⽕冷却介质:⼯件冷却淬⽕时使⽤的介质。
常⽤的有⽔,盐、碱、有机聚合物⽔溶液。
油、熔盐、流态床、空⽓、氢⽓、氮⽓和惰性⽓体等。
淬透性:以在规定条件下淬⽕所能达到的硬度分布表征的材料特性。
淬硬性:以钢在理想条件下所能达到的最⾼硬度表征的材料特性。
端淬试验:将标准端淬试样(φ25x100mm)奥⽒体化后,在专⽤的试验机上对其下端平⾯喷⽔冷却,然后沿试样圆柱表⾯轴向磨平带上测出硬度和⽔冷端距离的关系曲线。
此曲线被称为端淬曲线。
该试验⽅法被称做端淬试验,通过端淬试验可以⼤致确定⾦属材料的淬透性。
热处理术语奥⽒体化:将钢铁加热到Ac3或Ac1以上,使原始组织全部或部分转变为奥⽒体的⼯艺等温转变:钢和铸铁奥⽒体化后,冷却到Ar1或Ar3以下温度保持时的过冷奥⽒体发⽣的转变。
4140热处理工艺

4140热处理工艺引言:4140钢是一种常用的合金钢材料,具有良好的强度和耐磨性。
为了进一步提高其力学性能和耐磨性,常常需要对4140钢进行热处理。
本文将介绍4140热处理工艺的基本原理、工艺流程和工艺参数。
一、基本原理:热处理是通过加热和冷却的方式改变材料的组织结构和性能,使其达到所需的力学性能和耐磨性。
4140钢的主要成分是铁、碳、铬和锰,通过合理的热处理工艺,可以使其获得良好的硬度和韧性。
二、工艺流程:1. 预处理:将初始材料进行清洗和去除表面氧化物,以确保后续热处理的效果。
2. 加热:将4140钢材料加热到适当的温度,通常为800-850℃。
加热过程中要保持均匀加热,避免过热或不均匀加热导致材料变形或渗碳不均匀。
3. 保温:将加热到适当温度的4140钢材料保持一定时间,使其达到均匀的温度分布和相变。
4. 冷却:将保温后的4140钢材料迅速冷却,通常采用水淬或油淬的方式。
冷却速度的控制对最终材料的性能有重要影响,过快或过慢的冷却速度都会导致材料性能下降。
5. 回火:将淬火后的4140钢材料加热至适当温度,通常为150-300℃,保温一段时间后再进行冷却。
回火的目的是消除冷却过程中产生的内应力和脆性,并提高材料的韧性。
三、工艺参数:1. 加热温度:通常为800-850℃,根据具体要求可进行调整。
2. 保温时间:根据材料的尺寸和要求的硬度,保温时间一般为1-2小时。
3. 冷却介质:常用的冷却介质有水和油。
水淬可以获得更高的硬度,但会增加材料的脆性;油淬可以获得较好的韧性和耐磨性。
4. 回火温度:通常为150-300℃,根据要求的性能可进行调整。
5. 回火时间:根据材料的尺寸和要求的性能,回火时间一般为1-2小时。
四、工艺特点:1. 热处理可以提高4140钢的硬度和韧性,使其具有良好的综合力学性能。
2. 4140热处理工艺具有可控性好、适应性广的特点,能够满足不同应用领域的需求。
3. 4140热处理过程中需要注意加热温度、保温时间和冷却速度的控制,以避免产生过热或过冷的现象。
热处理原理和工艺培训课件
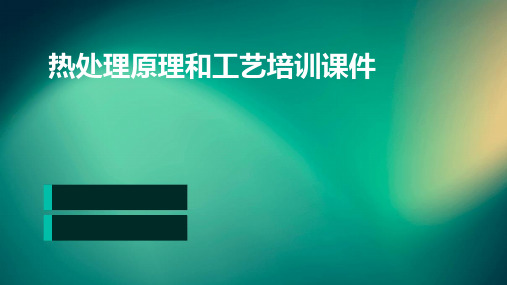
刀具热处理
刀具热处理
01
刀具的热处理可以提高其硬度和耐磨性,从而提高切削效率和
刀具寿命。
高速钢刀具
02
高速钢刀具在热处理后具有较高的硬度和良好的耐磨性,适用
于加工硬度较高的材料。
硬质合金刀具
03
硬质合金刀具的热处理可以进一步提高其硬度和耐热性,适用
于高速切削和加工高温合金等难加工材料。
模具热处理
模具热处理
模具的热处理可以提高其硬度和耐磨性,延长模具使用寿命,保 证产品质量。
冷冲模具
冷冲模具需要进行表面强化处理,以提高其耐磨性和抗冲击性。
塑料模具
塑料模具需要进行适当的热处理,以提高其抗腐蚀性和耐热性。
精密零件热处理
精密零件热处理
精密零件的热处理可以提高其尺寸稳定性和机械性能,保证产品 质量和精度。
热处理质量检测与评估
硬度检测
采用硬度计对热处理后 的产品进行硬度检测,
以评估热处理效果。
金相组织分析
通过金相显微镜观察热 处理后的产品组织结构, 分析热处理对组织的影
响。
力学性能测试
对热处理后的产品进行 拉伸、冲击、弯曲等力 学性能测试,以评估其
机械性能。
不合格品处理
对不合格的热处理产品 进行追溯和处理,分析 原因并采取相应的纠正
工艺中具有重要意义。
03
应力与应变原理
金属材料在加热和冷却过程中会产生热应力、组织应力和相变应力等。
这些应力会导致材料变形和开裂。因此,在热处理过程中需要采取措施
控制应力与应变,以获得良好的热处理效果。
02 热处理工艺
预处理工艺
01
02
03
清理
去除工件表面的油污、锈 迹和氧化皮,确保工件表 面干净,以便进行后续的 热处理工艺。
常见的热处理方法及其原理解析

常见的热处理方法及其原理解析热处理是通过加热和冷却金属材料来改变其物理和化学性质的方法。
它在金属加工和制造行业中具有重要地位,可以改善材料的硬度、韧性、强度和耐腐蚀性能。
本文将介绍几种常见的热处理方法,并分析其原理。
1. 硬化(Quenching)硬化是一种常用的热处理方法,通过快速冷却材料来增加其硬度和强度。
通常,将材料加热到临界温度(也称为临界点),然后迅速将其冷却到室温,以实现硬化作用。
快速冷却的方法包括浸泡在油中(油淬硬化)或水中(水淬硬化),或采用其他冷却介质如盐水。
这种快速冷却过程会导致材料内部组织发生相变和晶粒细化,从而提高了硬度和强度。
2. 淬火(Tempering)淬火是硬化后对材料进行回火处理的方法,目的是调整其硬度和韧性的比例。
淬火是通过加热材料到较高温度,然后迅速从空气中冷却,以减少硬化后的脆性。
这个过程会改变材料内部的晶粒结构,使之重新组合并形成一种更均匀的组织。
通过控制回火温度和时间,可以调整材料的硬度和韧性,以满足特定的使用要求。
3. 固溶处理(Solutionizing)固溶处理是一种将固体溶解在熔融金属中的方法,用于改善金属的强度和耐腐蚀性。
该方法通常应用于合金材料,因为合金材料的组织中含有多种元素。
固溶处理涉及将材料加热到足够高的温度使其熔化,然后冷却以形成均匀的固溶体。
这个过程可以去除合金材料中的析出相并使其均匀溶解。
在固溶处理后,材料通常会进行进一步的冷却和固化,以稳定其组织。
4. 马氏体转变(Martensitic Transformation)马氏体转变是一种通过快速冷却使材料发生固态相变的方法。
当材料经过快速冷却时,其晶体结构会由面心立方格子(A相)转变为体心立方格子(B相),这个过程被称为马氏体转变。
这种相变导致材料的变硬和变脆,并且产生奥氏体晶粒结构。
马氏体转变广泛应用于钢材的制造中,可以提高材料的硬度和强度。
5. 强化(Precipitation Hardening)强化是一种常见的热处理方法,用于提高合金材料的硬度和强度。
- 1、下载文档前请自行甄别文档内容的完整性,平台不提供额外的编辑、内容补充、找答案等附加服务。
- 2、"仅部分预览"的文档,不可在线预览部分如存在完整性等问题,可反馈申请退款(可完整预览的文档不适用该条件!)。
- 3、如文档侵犯您的权益,请联系客服反馈,我们会尽快为您处理(人工客服工作时间:9:00-18:30)。
细晶强化:
合金的晶粒越细小,内部的晶粒和晶界的数目就越
多。细晶强化利用晶界上原子排列的不规则性,原子能 量高这一特点,对材料进行强化。 双晶粒的拉伸试验说明:晶界对形变有阻碍作用。
双晶粒拉伸示意图
低碳钢的σs 与晶粒大小的关系
在右图中,低碳钢的σs 与晶粒直径平方根的倒数呈线
性关系,可用下式表示:
固态相变的晶体学:
固态相变的晶体学主要描述晶体中原有相与新相之
间的晶体学关系,如晶体结构、点阵常数等,分析新相 形成的原子迁移过程。
第三节
钢的热处理
钢铁材料的强韧化重要有两个途径:一是对钢铁材 料实施热处理;二是通过调整钢的化学成分,加入合金 元素(亦即钢的合金化原理),以改善钢的性能。 钢铁材料热处理是通过加热、保温和冷却方式借以
1863年,英国金相学家和地质学家展示了钢铁在
显微镜下的六种不同的金相组织,证明了钢在加热和冷
却时,内部会发生组织改变,钢中高温时的相在急冷时 转变为一种较硬的相。 法国人奥斯蒙德确立的铁的同素异构理论,以及英 国人奥斯汀最早制定的铁碳相图,为现代热处理工艺初
步奠定了理论基础。与此同时,人们还研究了在金属热
σs= σ0+Kd-1/2 …… Hall-Petch公式
细晶强化理论的提出: (1)针对不同常规材料,探索抑制其晶粒长大的办法。
(2)在世界范围掀起了研究纳米材料的狂潮。
可以实现在提高材料强度的同时,也改善材料的塑性 和韧性,获得最佳的强韧性配合。
加工硬化:
加工硬化是指金属材料随着塑性变形程度的增加,强
度、硬度升高;塑性、韧性下降的现象。加工硬化(冷变 形)是热处理不能强化的金属材料的主要强化方法。 加工硬化曲线:
曲线分为三阶段
1)易滑移阶段(位错少干扰) 2)线性硬化阶段(位错塞积)
3)抛物线硬化阶段(螺旋位错
启动,位错密度下降)
加工硬化的实质:
是金属塑性变形时内部产生滑移,使
晶粒变形和细化亚组织,因而产生大量的位错,晶格严重 畸变,内部应力增加,其宏观效应就是加工硬化。
随着淬火技术的发展,人们逐渐发现淬冷剂对淬火
质量的影响。三国蜀人蒲元曾在今陕西斜谷为诸葛亮打
制3000把刀,相传是派人到成都取水淬火的。这说明中
国在古代就注意到不同水质的冷却能力了,同时也注意
了油和尿的冷却能力。
中国出土的西汉(公元前206~公元24)中山靖王墓中
的宝剑,心部含碳量为0.15~0.4%,而表面含碳量却达 0.6%以上,说明已应用了渗碳工艺。但当时作为个人 “手 艺”的秘密,不肯外传,因而发展很慢。
4)奥氏体均匀化: 渗碳体全部溶解完毕时,奥氏体的 成分是不均匀的,只有延长保温时间,通过碳原子的扩 散才能获得均匀化的奥氏体。 亚共析钢的加热过程:
F P F A A
AC1 AC3
过共析钢的加热过程:
P Fe3CⅡ A Fe3CⅡ A
AC1 ACcm
加工硬化
固溶强化
回火索氏体
固溶强化
第二相强化
细晶强化
固态相变
塑性金属材料的强化机制表明:通过热处理中的加
热和冷却过程使合金产生固态相变,从而合金组织发生 变化,最终导致材料性能产生变化。 固态相变是指固态物质在温度、压力、电场、磁场 改变时,从一种组织结构会转变成另一种组织结构。
材料科学研究中的固态相变主要是指温度改变而产
δ
Cu-Ni固溶体的机械 性能与成分的关系
Al-Mg固溶体的应力-应变曲线
固溶强化的实质:晶体结构中的弹性交互作用、 电 交互作用和化学交互作用。其中最主要的是:溶质 原子与位错的弹性交互作用阻碍了位错的运动。
不同溶质原子在位错周围的分布状态
Cotrell气团模型:溶质原子与位错弹性交互作用的结果, 使溶质原子趋于聚集在位错的周围,以减小点阵畸变, 降低体系的能量。(它对位错有“钉扎”作用)
△G = -V△GV + Sσ+ V△Ge
式中:V为新相体积;S为新、旧相的界面积;△GV
和△Ge分别表示形成单位体积新相时自由能和应变能;
σ表示新、旧相界单位面积的界面能。
固态相变的动力力学条件:
固态相变的动力学主要讨论相变进行的速率问题,
固态相变的速率是形核率和长大速率的函数,即与相变 温度有关的函数。 动力学除了讨论固态相变过程中的形核和晶粒长大 的速率问题,还包括外界条件(温度、压力和磁场)和 组分对相变过程的影响及控制相变产物的组成等内容。
冷却时钢的组织转变
A1
1、钢的冷却方式 热处理时常用的冷却方 式有两种:一是等温冷却 (常用于理论研究);二是
连续冷却(常用于生产)。
2、过冷奥氏体等温冷却曲线的绘制 通常将处于A1以下温度尚未发生转变的奥氏体称为过冷
奥氏体。钢在冷却时的组织转变实质上是过冷奥氏体的组织
转变。
1)等温冷却试验: (a) 首先将若干薄圆片状试样放入锡熔炉中,在高于共 析温度的条件下进行奥氏体化;(b)将上述奥氏体化后 的试样迅速放入另一锡熔炉保温,炉温低于共析温度;
加热速度 加热速度越快,过热度越大,奥氏体实际形成温度 越高,可获得细小的起始晶粒。 钢的化学成分 碳全部溶于奥氏体时,随奥氏体中含碳量的增加, 晶粒长大倾向增大。 合金元素Ti、Zr、V、Nb、Al等,当其形成弥散稳 定的碳化物和氮化物时,由于分布在晶界上,因而阻碍 晶界的迁移,阻止奥氏体晶粒长大,有利于得到细晶粒 钢。Mn和P是促进奥氏体晶粒长大的元素。
改变合金的组织与性能的一种工艺方法,其基本内容包
括热处理原理及热处理工艺两大方面。
钢的热处理原理
钢的热处理相变温度
钢在加热时,实际 转变温度往往要偏离平 衡的临界温度,冷却时
也是如此。随着加热和
冷却速度的增加,滞后 现象将越加严重。通常把加热时的临界温度标以字母 “C”,如AC1、AC3、ACm等;把冷却时的临界温度标以字母 “r”,如Ar1、Ar3、Arm等。
处理的加热过程中对金属的保护方法,以避免加热过程
中金属的氧化和脱碳等。
1850~1880年,对于应用各种气体(诸如氢气、煤 气、一氧化碳等)进行保护加热曾有一系列专利。 1889~1890年英国人莱克获得多种金属光亮热处理的专 利。 1901~1925年,在工业生产中应用转筒炉进行气体
渗碳 ;30年代出现露点电位差计,使炉内气氛的碳势达到 可控,以后又研究出用二氧化碳红外仪、氧探头等进一
存在组织缺陷。对金属材料进行热处理主要源于提高其
综合机械性能,符合材料在设计和制备过程中所遵循的 “成分-组织-性能”的原则。
金属材料的强化机制
结构材料
金属材料
高分子材料
强 度
陶瓷材料
屈服强度
断裂强度
抗拉强度
疲劳强度
材料强度的唯一性判据 导致材料失效 的最大应力
通常研究的结构材料在室温工作条件下,最需要考虑的是屈服 强度和断裂强度。
热处理的发展史
早在公元前770~前222年,中国人在生产实践中就 已发现,铜铁的性能会因温度和加压变形的影响而变化。
白口铸铁的柔化处理就是制造农具的重要工艺。
公元前六世纪,钢铁兵器逐渐被采用,为了提高钢
的硬度,淬火工艺遂得到迅速发展。中国河北省易县燕
下都出土的两把剑和一把戟,其显微组织中都有马氏体 存在,说明是经过淬火的。
加热时钢的组织转变
1、奥氏体的形成过程 钢在加热时奥氏体的形成过程又称为奥氏体化。以
共析钢的奥氏体形成过程为例。
1)奥氏体形核:奥氏体的晶核优先在铁素体与渗碳体 的界面上形成。 2)奥氏体晶核长大: 奥氏体晶核形成以后,依靠铁、
碳原子的扩散,使铁素体不断向奥氏体转变和渗碳体不
断溶入到奥氏体中去而进行的。 3)残留渗碳体的溶解: 铁素体全部消失以后,仍有部 分剩余渗碳体未溶解,随着时间的延长,这些剩余渗碳 体不断地溶入到奥氏体中去,直至全部消失。
晶粒度对加工硬化曲线的影响
晶体结构对加工硬化曲线的影响
时效强化:
时效强化是指获得过饱和固溶体后,在一定温度下
保温析出过渡相、第二相等而实现对材料强化的方法。
第二相强化(弥散强化):
通过各种工艺手段使第二相质点弥散分布,可以阻
碍合金内部的位错运动,从而提高合金强度的方法。 第二相一般指各种化合物质点。 获得第二相的途径: 1)生产中可通过对马氏体进行回火的方法获得弥散分布
组织名称
珠 珠光体 光 索氏体 体 屈氏体
符 号
P S
转变温 度/℃
A1~ 650 650~ 600 600~ 550 550~ 350 350~ 240
屈服强度 σb≥σk
断裂强度 σb≤σk
脆性材料
脆性材料的强度 通常以σk表示
塑性材料
塑性材料的强度 通常以σb表示
大部分金属材料属于塑性材料,其塑性变形是靠位 错的运动而发生的,因此,任何阻止位错运动的因素都 可以成为提高金属材料强度的途径。
固溶强化:
当合金由单相固溶体构成时,随溶质原子含量的增 加,其塑性变形抗力大大提高,表现为强度和硬度上升, 塑性和韧性值下降。 σb δ
生的相变。固态相变主要包括三种基本变化:1)晶体结 构的变化;2)化学成分的变化;3)有序程度的变化。 一种相变可同时包括一种、两种或三种变化。
材料科学遇到的相变习惯上分为扩散型相变和无扩
散型相变两大类。
扩散型相变的特点是通过激活原子运动而产生,要 求温度高,原子活动能力强。纯金属的同素异构转变、 固溶体的多形性转变、以及脱溶转变等均属于此类。 无扩散型相变的特点是相变中原子不发生扩散、原
(c)依据试样保温时间的差异,分别从炉中取出试样,
置于水中快冷; (d)磨制金相试 样,并观察显微 组织。