减速机马达的选型计算
马达选型计算,丝杆选型计算

皮带轮连续运动选型计算表
说明:由于是连续运动,所以在计算牛矩时只需考虑负载牛矩,启动牛矩忽略,但必须考虑到机械结构参数:
皮带速度:V=2m/min
皮带与工作物总质量m L= 1.5kg*
滑动面摩擦系数μ=0.3*
滚筒直径D=0.023m*
滚筒质量m2=2kg*
传送带和滚筒的机械效率η=0.9*
减速机机械效率ηG=0.7
减速比i=15*
外力FA=0N*
移动方向与水平轴夹角 a =0°
1)电机转速
减速机输出轴转速N=27.67906rpm
电机输出轴转速N M=N*i
=415.1858rpm
2)计算负载转矩
减速机轴向负载F=
=
减速机轴负载转矩T L
=0.05635Nm Array电机轴负载转矩T LM=
=0.005367Nm
4)计算折算到电机轴的惯量
=0.000198kgm2
滚筒的惯量
J M2=
=0.000132kgm 2
J M1+2J M2
=0.000463kgm 2
5)必须转矩
必须转矩
T M =T LM *S =0.010733Nm
6)负荷与电机惯量比
惯量比
=
0.00187
折算到减速机轴的负载惯量 J L =
计算表格
,启动牛矩忽略,但必须考虑到惯量的匹配
其他常数
G=9.8m/s
pi= 3.1416
电机惯量J M=0.0011kgm2安全系数S=2。
回转减速电机选型计算公式
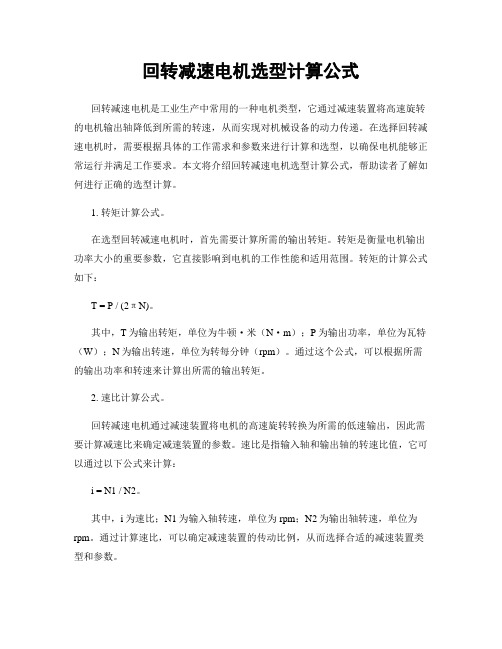
回转减速电机选型计算公式回转减速电机是工业生产中常用的一种电机类型,它通过减速装置将高速旋转的电机输出轴降低到所需的转速,从而实现对机械设备的动力传递。
在选择回转减速电机时,需要根据具体的工作需求和参数来进行计算和选型,以确保电机能够正常运行并满足工作要求。
本文将介绍回转减速电机选型计算公式,帮助读者了解如何进行正确的选型计算。
1. 转矩计算公式。
在选型回转减速电机时,首先需要计算所需的输出转矩。
转矩是衡量电机输出功率大小的重要参数,它直接影响到电机的工作性能和适用范围。
转矩的计算公式如下:T = P / (2πN)。
其中,T为输出转矩,单位为牛顿·米(N·m);P为输出功率,单位为瓦特(W);N为输出转速,单位为转每分钟(rpm)。
通过这个公式,可以根据所需的输出功率和转速来计算出所需的输出转矩。
2. 速比计算公式。
回转减速电机通过减速装置将电机的高速旋转转换为所需的低速输出,因此需要计算减速比来确定减速装置的参数。
速比是指输入轴和输出轴的转速比值,它可以通过以下公式来计算:i = N1 / N2。
其中,i为速比;N1为输入轴转速,单位为rpm;N2为输出轴转速,单位为rpm。
通过计算速比,可以确定减速装置的传动比例,从而选择合适的减速装置类型和参数。
3. 功率计算公式。
在选型回转减速电机时,还需要计算所需的输入功率。
输入功率是指电机需要输入的功率大小,它可以通过以下公式来计算:P = Tω。
其中,P为输入功率,单位为瓦特(W);T为输出转矩,单位为牛顿·米(N·m);ω为输出轴角速度,单位为弧度每秒(rad/s)。
通过计算输入功率,可以确定所需的电机功率大小,从而选择合适的电机型号和参数。
4. 效率计算公式。
在实际工作中,回转减速电机的效率也是一个重要的考量因素。
效率是指电机输出功率与输入功率之比,它可以通过以下公式来计算:η = Pout / Pin。
马达选型与计算
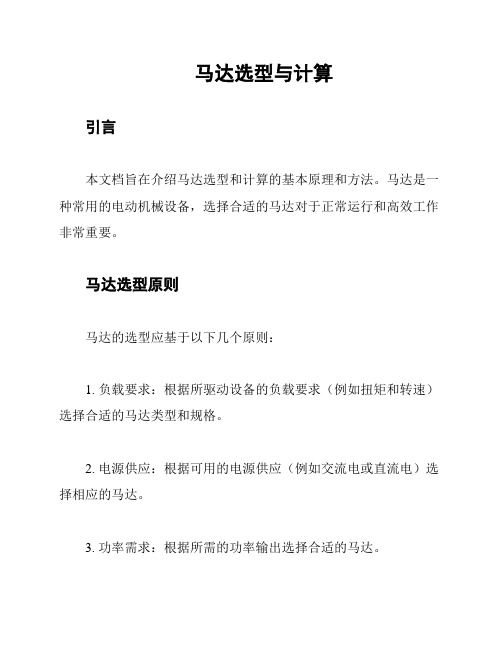
马达选型与计算引言本文档旨在介绍马达选型和计算的基本原理和方法。
马达是一种常用的电动机械设备,选择合适的马达对于正常运行和高效工作非常重要。
马达选型原则马达的选型应基于以下几个原则:1. 负载要求:根据所驱动设备的负载要求(例如扭矩和转速)选择合适的马达类型和规格。
2. 电源供应:根据可用的电源供应(例如交流电或直流电)选择相应的马达。
3. 功率需求:根据所需的功率输出选择合适的马达。
4. 空间限制:考虑到安装空间的限制,选择体积适合的马达。
5. 可靠性和维护要求:根据马达的可靠性和维护要求选择合适的型号和品牌。
马达计算方法马达计算是确定适合的马达规格的关键步骤。
以下是基本的马达计算方法:1. 确定负载参数:首先,准确测量所驱动设备的负载参数,例如扭矩和转速。
2. 计算所需的功率输出:根据负载参数和工作条件计算所需马达的功率输出。
功率(P)的计算公式为:P = 扭矩(T) ×转速(N)其中,扭矩的单位为牛顿·米(Nm),转速的单位为转每分钟(rpm)。
3. 确定额定功率:根据所选马达的额定功率(通常可从马达技术参数手册中获取),确保所需功率输出不超过马达的额定功率。
4. 选择马达类型和规格:基于马达技术参数手册中的相关信息,选择合适的马达类型和规格,以满足所需功率输出。
5. 验证选择的马达:根据所选马达的技术参数验证其是否满足其他要求,例如运行效率、启动和制动特性等。
结论本文档介绍了马达选型和计算的基本原理和方法。
在选择马达时,请根据负载要求、电源供应、功率需求、空间限制、可靠性和维护要求等因素进行综合考虑。
马达计算则指导了确定适合的马达规格的步骤。
通过合理的马达选型和计算,能够提高马达系统的性能和效率,实现良好的运行和工作效果。
电机减速机选型计算

F1 F2 F2 mg (a )
F1 T2 D/2
其中a是设备运行加速度,μ是 摩擦因数。(因为加速时力矩最大 所以此处,仅考虑加速时候的情况)
齿轮齿条受力计算
• 从上面的公式中可以得出: 2mg (a )
其中:J1为减速机转动惯量。 • 查看J与J0的比值是否在正常范围内,若比值太高,需要选用更大惯 量的电机。
丝杆选型
• 丝杆一般用在运行速度较慢的设备上,即 需要的总减速比较高的情况。 因为丝杆本身就带有一定的减速比。而设 备运行速度确定后与电机之间的总减速比 一定,预留给减速机的减速比与齿轮齿条 相比,就少了很多,如果设备运行速度快, 可能减速机的减速比还不足3,这情况无法 选出合适的减速机。
2
选型核算
• 所以负载折算到丝杆(即减速机输出轴) 的转动惯量J2为:
d 2 J 2 m( ) 2
• 折算到电机轴上的惯量J为: • 计算出来后查看J与J0的比值。若太大,请 选择更高惯量电机。
J2 J J1 2 i
纯转动选型
• 纯转动时力矩大小与转动加速度,和负载 转动惯量有关系。
减速机选型计算从输出端来判断减速机的型号需求输出端传动方式减速机输出端主要应用方式有以下三种?齿轮齿条?丝杆导轨?纯转动齿轮齿条受力分析与计算?齿轮齿条传动时
减速机选型计算
从输出端来判断减速机的型号需求
输出端传动方式
减速机输出端主要应用方式有以下三种 • 齿轮齿条 • 丝杆导轨 • 纯转动
齿轮齿条受力分析与计算
F2 mg (a ) T2 F1 R d F1 mg (a ) 2 2 d • 公式中 2 可视为丝杆传动的有效半径。
直流减速电机选型计算公式【秘籍】

直流减速电机,即齿轮减速电机,是在普通直流电机的基础上,加上配套齿轮减速箱。
齿轮减速箱的作用是,提供较低的转速,较大的力矩。
同时,齿轮箱不同的减速比可以提供不同的转速和力矩。
这大大提高了,直流电机在自动化行业中的使用率;在选择直流减速电机型号是要做如下的参数计算(传动比、功率)和注意选型要点。
直流减速电机参数计算:传动比计算:一级传动比理论范围,n电机=(6-20)*n输出=(6-20)*360r/min 二级传动比理论范围,n电机=(8-40)*n输出=(8-40)*360r/min电动机功率和转速已经算出,如果需要看转矩,转矩也可以算出T=9550P/n或T=973P/n,这样就可以选电机型号了。
功率的计算:静功率计算线性运动P=F*V /1000η(P-w,计算静功率,F-N,运行阻力,V-m/s运行速度)旋转运动P=M*N/9550η(p-w,计算静态功率,M-N.m 扭矩,n-rpm转速)动态功率计算旋转运动P=Jt*Nt/91200*tA*η(P-w,计算动功率,Jt-Kg.m 转动惯量nT-rpm转动速度,tA-S启动时间)线性运动:惯性力F=ma;m-kg;,a-m/s启动加速度直流减速电机选型要素:1、选购前确定直流减速电机的使用途径,应用场景,列出环境要求等因素;2、首先确定需要什么样的直流减速机,比如小功率、扭矩大、转速低、噪音、耗能、参数等功率、性能要求;3、确定直直流减速电机输出轴扭矩、安转方式、维护保养方式;4、确定输入传动轴转速和减速比;5、根据机法兰大小选直流减速电机,如输出轴扭矩不足回到2重新匹配;6、工作温度、背隙等是否满足(也可放在步);7、计算负载的扭力大小;对电机的寿命而言,扭力计算十分重要,而且要注意加速度的大转矩值(TP),是否超过电机之大负载扭力。
扩展资料:直流减速电机作用:直流减速电机,即齿轮减速电机,是在普通直流电机的基础上,加上配套齿轮减速箱。
马达选型计算V0.00
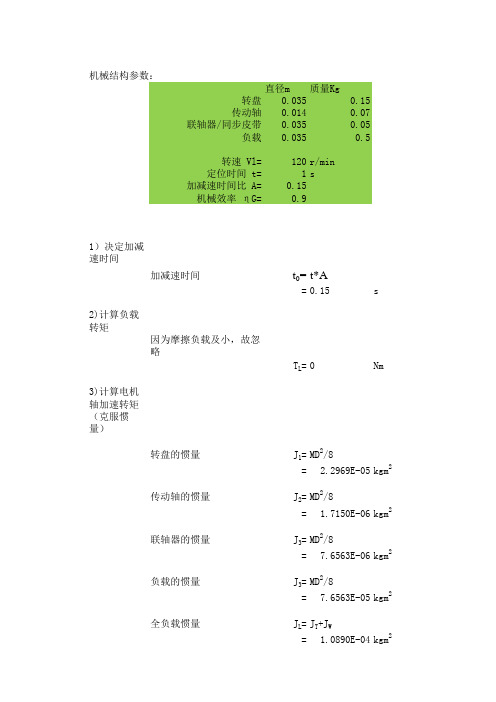
直径m 质量Kg转盘0.0350.15传动轴0.0140.07联轴器/同步皮带0.0350.05负载0.0350.5转速 Vl=120r/min 定位时间 t=1s 加减速时间比 A=0.15机械效率 ηG=0.91)决定加减速时间加减速时间t 0=t*A=0.15s2)计算负载转矩因为摩擦负载及小,故忽略T L =0Nm3)计算电机轴加速转矩(克服惯量)转盘的惯量J 1=MD 2/8=2.2969E-05kgm 2传动轴的惯量J 2=MD 2/8=1.7150E-06kgm 2联轴器的惯量J 3=MD 2/8=7.6563E-06kgm 2负载的惯量J 3=MD 2/8=7.6563E-05kgm 2全负载惯量J L =J T +J W =1.0890E-04kgm 2负载加速转矩T s ==0.009575784Nm4)必须转矩机械结构参数:必须转矩T=(T S+T L)*S=0.019151567Nm5)电机选择根据计算,初步确定电机型号,然后输入转子惯量,确认T M6)负荷与电机惯量比I1=20.167129637)负荷与减速机惯量比当负荷与电机惯量比>5时,考虑采用减速装置,提高惯量匹配I2=20.167129632.2969E-05 1.7150E-06 7.6563E-06 7.6563E-05 1.0890E-04安全系数S=2*电机惯量J M=0.0000054kgm2转矩T M=0.3Nm转速V=120r/mini=1减速机减速比。
马达选型计算方法
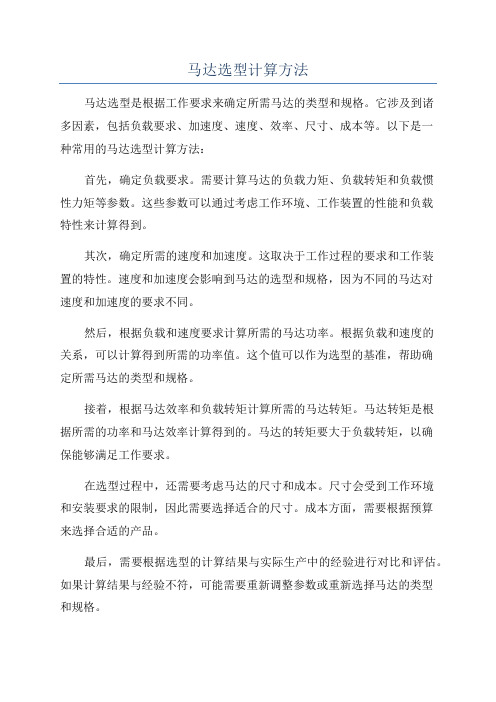
马达选型计算方法
马达选型是根据工作要求来确定所需马达的类型和规格。
它涉及到诸
多因素,包括负载要求、加速度、速度、效率、尺寸、成本等。
以下是一
种常用的马达选型计算方法:
首先,确定负载要求。
需要计算马达的负载力矩、负载转矩和负载惯
性力矩等参数。
这些参数可以通过考虑工作环境、工作装置的性能和负载
特性来计算得到。
其次,确定所需的速度和加速度。
这取决于工作过程的要求和工作装
置的特性。
速度和加速度会影响到马达的选型和规格,因为不同的马达对
速度和加速度的要求不同。
然后,根据负载和速度要求计算所需的马达功率。
根据负载和速度的
关系,可以计算得到所需的功率值。
这个值可以作为选型的基准,帮助确
定所需马达的类型和规格。
接着,根据马达效率和负载转矩计算所需的马达转矩。
马达转矩是根
据所需的功率和马达效率计算得到的。
马达的转矩要大于负载转矩,以确
保能够满足工作要求。
在选型过程中,还需要考虑马达的尺寸和成本。
尺寸会受到工作环境
和安装要求的限制,因此需要选择适合的尺寸。
成本方面,需要根据预算
来选择合适的产品。
最后,需要根据选型的计算结果与实际生产中的经验进行对比和评估。
如果计算结果与经验不符,可能需要重新调整参数或重新选择马达的类型
和规格。
减速机选型计算实例
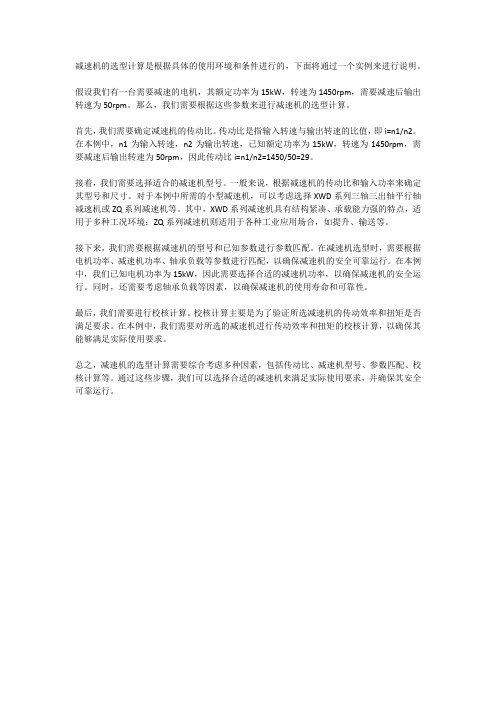
减速机的选型计算是根据具体的使用环境和条件进行的,下面将通过一个实例来进行说明。
假设我们有一台需要减速的电机,其额定功率为15kW,转速为1450rpm,需要减速后输出转速为50rpm。
那么,我们需要根据这些参数来进行减速机的选型计算。
首先,我们需要确定减速机的传动比。
传动比是指输入转速与输出转速的比值,即i=n1/n2。
在本例中,n1为输入转速,n2为输出转速,已知额定功率为15kW,转速为1450rpm,需要减速后输出转速为50rpm,因此传动比i=n1/n2=1450/50=29。
接着,我们需要选择适合的减速机型号。
一般来说,根据减速机的传动比和输入功率来确定其型号和尺寸。
对于本例中所需的小型减速机,可以考虑选择XWD系列三轴三出轴平行轴减速机或ZQ系列减速机等。
其中,XWD系列减速机具有结构紧凑、承载能力强的特点,适用于多种工况环境;ZQ系列减速机则适用于各种工业应用场合,如提升、输送等。
接下来,我们需要根据减速机的型号和已知参数进行参数匹配。
在减速机选型时,需要根据电机功率、减速机功率、轴承负载等参数进行匹配,以确保减速机的安全可靠运行。
在本例中,我们已知电机功率为15kW,因此需要选择合适的减速机功率,以确保减速机的安全运行。
同时,还需要考虑轴承负载等因素,以确保减速机的使用寿命和可靠性。
最后,我们需要进行校核计算。
校核计算主要是为了验证所选减速机的传动效率和扭矩是否满足要求。
在本例中,我们需要对所选的减速机进行传动效率和扭矩的校核计算,以确保其能够满足实际使用要求。
总之,减速机的选型计算需要综合考虑多种因素,包括传动比、减速机型号、参数匹配、校核计算等。
通过这些步骤,我们可以选择合适的减速机来满足实际使用要求,并确保其安全可靠运行。
马达选型计算[指南]
![马达选型计算[指南]](https://img.taocdn.com/s3/m/94950b3bec630b1c59eef8c75fbfc77da26997c5.png)
已知條件:1).每迷鏈條的重量:5kg/米2).一次吊具+二次吊具的重量3kg/米3).工件的重量10kg/件4).工件的間距450mm5).鏈條的節距p=150mm,鏈條的破壞強度為T=5000kg≒50000 N6).上升,下降以30°計算7).受中等載荷,潤滑良好之下8).軌道彎頭採用Φ1200彎頭.2.所求的參數:1).在哪一點處鏈條所受的張力最大T n解:第一步:計算調整裝置作用於鏈條的張力T0因為一般對單個調整裝置的垂直板有12塊,每塊有12kg,取T0=68.2kg第二步:對於第1點處張力T1(屬於水平轉彎段),通過以上計算查表2,公式(2-1)可以知(假設整個鏈條的潤滑狀況良好的情況之下f k=0.03)T1=T0*1.185+f1f1=f k GG=(0.6*3.14)*(5+3+10/0.45)=56.9=57kgT1=68.2*1.185+0.03*57=82.5kg第三步:對於第2點(屬於水平直軌段),由公式(1-1)可知:T2=T1+f k G f k=0.03 l=44米G=G*lG=(5+3+10/0.45)*44=1330kgT2=82.5+0.03*1330=122.4=123kg第四步:對於第3處張力(屬於水平轉彎段),由公式可知(查表2對180°的情況之下):T3=1.185T2+f f=f k GG=(0.6*3.14)*(5+3+10/0.45)=56.9=57kgT3=(123*1.185+0.03*57)kg=147.4kg第五步:從“3~4” 點第4點的張力T4,由公式(1-1)可知:T4=T3+f k G=147.4+0.03*(5+3+10/0.045)*46米=189.1kg第六步:第5點的張力T5(屬於水平轉彎段),由公式可知(查表2對180°的情況之下):T5=1.185T4+f f=f k GG=(0.6*3.14)*(5+3+10/0.45)=56.9=57kgT5=(189.1*1.185+0.03*57)kg=225.8kg第七步:第6點的張力T6,由公式(1-1)可知:T6=T5+f k G=225.8+0.03*(5+3+10/0.045)*46米=267.5kg第八步:對於第7點張力T7(屬於水平轉彎段),由公式可知(查表2對180°的情況之下):T7=1.185T6+f f=f k GG=(0.6*3.14)*(5+3+10/0.45)=56.9=57kgT7=(267.5*1.185+0.03*57)kg=318.7kg第九步:對於第8點張力T8由公式(1-1)可知:T8=T7+f k G=318.7+0.03*(5+3+10/0.045)*46米=360.4kg第十步:對於第9點的張力T9(屬於水平轉彎段)T9= =1.185T8+f=(360.4*1.185+0.03*57)kg=428.8 kg第十一步:對第10點產生張力T10, 由公式(1-1)可知T10=T9+f k G=428.8+0.03*(5+3+10/0.045)*46米=470.5kg第十二步:對第11點產生張力T11(屬於水平轉彎段)T11= =1.185T10+f=(470.5*1.185+0.03*57)kg=559.3 kg第十三步:對第12點產生張力T12由公式(1-1)可知T12=T10+f k G=559.3+0.03*(5+3+10/0.045)*44米=599.2kg綜上所述,在T12處所受張力最大,參考馬達樣本,應選馬達功率為3HP,參照圖如附圖.。
伺服电机及减速机选型计算

伺服电机及减速机选型计算1)关于负载条件①基本负载2000kg(⼯件+夹具+回转变位器+配重)②负载重⼼位置0.1m(假定为0.1m,设计时务必⼩于这个值)③负载系数×1.2Motor减速机 减速⽐=1712)电机规格(a12/3000i)项⽬额定输出额定转数最⾼转数3)减速机RV320E-1714) 【关于电机扭矩】负载扭矩[N?m] ……⽤于回转的扭矩选择电机规格时,乘以负载系数。
T L=∑mgr×Z TL=∑mgr×Z=2000×1.2×9.8×0.1×1/342≒6.877 <12 电机的额定扭矩(Z:确认减速⽐、输出轴的转数有⽆问题。
)(重⼒平均负载扭矩=最⼤负载扭矩/2^0.5/综合减速⽐=2000×1.2×9.8×0.1/2^0.5/342=4.86) ?慣性⼒矩[kg?m2] :向电机轴(输⼊轴)的换算。
I=∑mr2×Z2I=mr2×Z 2=2000×1.2×0.12×(1/342)2≒0.36×10-4I=m(D 2+d 2)÷8×Z 2=I=∑mr2×Z 2⾓加速度 [rad/s^2] :最⼤加速时的负载 dω/dt=(2π/60) N/⊿tdω/dt=(2π/60) N/⊿t=(2π/60)×3000/0.2≒1570.8(N:电机额定转数rpm、⊿t:加速时间sec) ?加速扭矩[kg ?m^2/s^2=N ?m] ……⽤于加速的扭矩 Ta=I ?dω/dt Ta=I ?dω/dt=74×10-4×1570.8≒11.62瞬时最⼤扭矩[kg ?m^2/s^2=N ?m] Tmax=TL+ Ta <电机的最⼤扭矩Tmax=TL+ Ta=6.877+11.62=18.5 <35 电机的最⼤扭矩 变位器最⾼⾓速度ωpmax=额定转数÷综合减速⽐×360°÷60sec=3000÷342×360÷60 ≒52.63°/sec 加減速时间tA=t1=设计值=0.2sec⾓加速度dωp/dt=ωpmax/tA =263.15°/sec2停⽌时间t4=1.0sec以内。
减速机选型计算公式
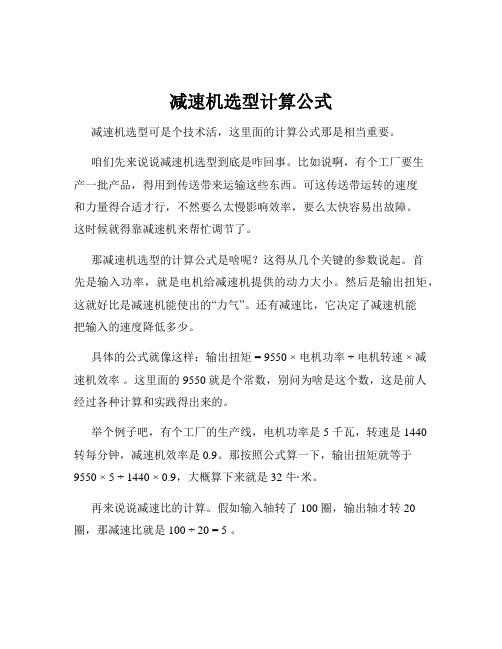
减速机选型计算公式减速机选型可是个技术活,这里面的计算公式那是相当重要。
咱们先来说说减速机选型到底是咋回事。
比如说啊,有个工厂要生产一批产品,得用到传送带来运输这些东西。
可这传送带运转的速度和力量得合适才行,不然要么太慢影响效率,要么太快容易出故障。
这时候就得靠减速机来帮忙调节了。
那减速机选型的计算公式是啥呢?这得从几个关键的参数说起。
首先是输入功率,就是电机给减速机提供的动力大小。
然后是输出扭矩,这就好比是减速机能使出的“力气”。
还有减速比,它决定了减速机能把输入的速度降低多少。
具体的公式就像这样:输出扭矩 = 9550 ×电机功率 ÷电机转速 ×减速机效率。
这里面的 9550 就是个常数,别问为啥是这个数,这是前人经过各种计算和实践得出来的。
举个例子吧,有个工厂的生产线,电机功率是 5 千瓦,转速是 1440 转每分钟,减速机效率是 0.9。
那按照公式算一下,输出扭矩就等于9550 × 5 ÷ 1440 × 0.9,大概算下来就是 32 牛·米。
再来说说减速比的计算。
假如输入轴转了 100 圈,输出轴才转 20 圈,那减速比就是 100 ÷ 20 = 5 。
不过,在实际选型的时候,可不能光盯着这些公式。
还得考虑工作环境,是高温、潮湿还是有灰尘啥的。
还有负载的特性,是平稳运行还是有冲击负载。
我记得之前去一个工厂帮忙选型,那场面真是让人头疼。
工厂里的设备又老又旧,运行起来嘎吱嘎吱响。
我就拿着本子和笔,在那一个个测量数据,计算选型。
结果算出来的减速机安装上去,一开始还挺好,没过几天就出问题了。
后来一检查,发现是因为设备老化,实际的负载比我计算的大多了。
没办法,只能重新选型,费了好大的劲。
所以啊,减速机选型可不能马虎,得综合考虑各种因素,反复计算和验证,才能选出最合适的减速机,让生产顺利进行。
总之,减速机选型的计算公式是基础,但实际应用中还得灵活多变,多观察多思考,这样才能选对减速机,让机器高效稳定地运转,为生产助力。
减速机选型实例计算公式

减速机选型实例计算公式减速机是一种广泛应用于机械传动系统中的重要设备,通常用于降低高速旋转的输入轴输出的速度,并提供更大的扭矩。
由于减速机在工业生产中的重要性,正确选型对于机械传动系统的正常运行至关重要。
本文将介绍减速机选型的具体计算公式,并通过一个实例来演示如何进行准确的选型。
首先,进行减速机选型之前,需了解减速机所需的基本参数,包括输入转速、输出转速、传动功率和传动比。
通过这些参数,可以计算出减速机的额定扭矩和类型。
计算减速机的额定扭矩公式如下:额定扭矩 = 传动功率× 60 ÷ (2π ×输出转速)例如,某台机械设备传动功率为10千瓦,输出转速为1500转/分钟。
代入上述公式,得到额定扭矩:额定扭矩= 10 × 1000 × 60 ÷ (2π × 1500) ≈ 637 Nm接下来,根据减速机的额定扭矩选取合适的传动比。
传动比即输入转速与输出转速的比值。
如果所需的传动比不在标准传动比范围内,可以通过综合考虑使用多台减速机进行级联传动,以满足需要的传动比。
例如,假设我们需要的传动比为5:1。
此时,可以通过选择合适的齿轮来实现传动比。
在实际选型中,还需考虑到齿轮的尺寸、耐用性等因素,以确保选用的齿轮能够满足实际工作条件的要求。
除了以上所述的参数和计算公式外,减速机的选型还需考虑其他因素,如额定转速、工作环境、轴向和径向载荷,以及减速机的型号和品牌等。
选型时,可以参考相关减速机厂家提供的技术手册和产品目录,以获取更详细的信息和指导。
综上所述,减速机选型是一项综合考虑多种因素的工作。
只有准确选型,才能保证减速机在机械传动系统中的正常运行,提高设备的可靠性和工作效率。
因此,在选型过程中,必须充分了解减速机的基本参数和计算公式,并综合考虑各种因素,从而选取合适的减速机型号和配置。
通过正确的选型,减速机能够更好地满足工业生产的需求,为生产效益的提升和设备维护的便利性带来显著的优势。
马达选型计算方法

马达选型计算方法1. 常用马达特点1.1. 交流马达:最常用。
转矩大,转速一般在1500转/分左右。
1.2. 直流马达:1.3. 步进马达:如东方。
扭矩大。
不能扭矩过载,否则会丢步。
选型计算一般留100—200%的转矩余量。
1.3.1. 从静止到额定转速(1000转/分左右)要约0.2—0.4秒。
1.4. 数字伺服马达:如松下。
功率大。
高速时扭矩稳定,扭矩过载能力强,一般为额定的3倍。
可以长时间工作的额定转矩的2倍。
1.4.1. 从静止到额定转速(3000转/分左右)要约60毫秒。
2. 选型计算例子:使用状况描述2.1. 控制:使用三菱PLC FX1S-20MT-001,最大脉冲速度100K Pulse/sec3. 马达种类的选择:3.1. 有定位需要。
因此:需要采用有定位功能的步进或伺服马达。
3.2. 步进与伺服的选择。
3.2.1. 一般步进便宜。
优先选择步进。
3.2.2. 要求在0.1秒内急加速,达到600转/左右。
反应速度是步进马达无法达到的,因此选择伺服。
4. 伺服马达的选型计算:主要是转速、扭矩、制动等问题。
4.1. 动作过程说明:在此起停频繁,仅仅最大允许0.15秒,采用三角型运行模式。
4.1.1. 梯形运行过程4.1.2. 三角形运动过程(适合频繁启停),此时T2=0。
4.2. 计算过程4.2.1. 考虑点:4.2.1.1. 启动:机构负载、摩擦力/阻力f、直线加速v、角加速度θ4.2.1.2. 平稳运行:机构负载、摩擦力/阻力f4.2.1.3. 制动时:机构负载、摩擦力/阻力f、直线减速(惯性)、负角加速度(惯量)4.2.2. 直线机构负载、摩擦力/阻力的计算4.2.2.1. 直线机构1:平台根据:·s = v(t2) +[ ½ x a (t1)2 ] x 2·v = at1·F1=ma(F1为负载力,m为质量,a为加速度)·F2=F1 + f(F2为总负载力,f为阻力/摩擦力)已知:·加速时间=减速时间=t1=总时间0.15s / 2=0.075s·匀速运行时间t2=0s(三角启停)·行程s=120mm=0.12m·质量m=3Kg·阻力f=10N计算得:·加速度a=21.4m/s2·最大速度V max=at=21.4 x 0.075=1.605m/s·运动动作克服力F1=3Kg x 21.4m/s2 = 64.2N·运动总力F2=64.2 + 10=74.2N假设:使用r=0.02m(Φ40mm)齿轮·需要转矩为M=F2 x r =74.2N x 0.02m = 1.484Nm·需要最大转速V max = V max / 2πr = 1.605 / (2π0.02) = 12.78转/秒 = 766.8转/分·需要最大角速度:ω=V max / π=12.78转/秒 / π=4.07rad/s(弧度/秒)预选型:·根据松下马达选型目录。
电机减速器的选型计算实例
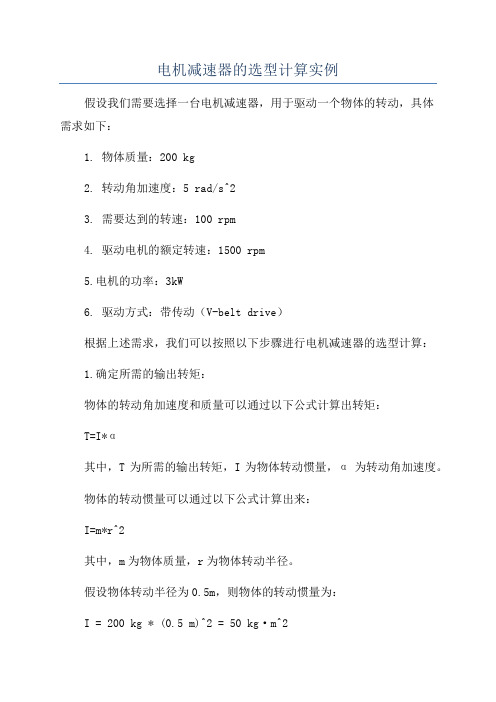
电机减速器的选型计算实例假设我们需要选择一台电机减速器,用于驱动一个物体的转动,具体需求如下:1. 物体质量:200 kg2. 转动角加速度:5 rad/s^23. 需要达到的转速:100 rpm4. 驱动电机的额定转速:1500 rpm5.电机的功率:3kW6. 驱动方式:带传动(V-belt drive)根据上述需求,我们可以按照以下步骤进行电机减速器的选型计算:1.确定所需的输出转矩:物体的转动角加速度和质量可以通过以下公式计算出转矩:T=I*α其中,T为所需的输出转矩,I为物体转动惯量,α为转动角加速度。
物体的转动惯量可以通过以下公式计算出来:I=m*r^2其中,m为物体质量,r为物体转动半径。
假设物体转动半径为0.5m,则物体的转动惯量为:I = 200 kg * (0.5 m)^2 = 50 kg·m^2将转矩和转速代入转矩-转速关系曲线,可以计算出所需的输出转矩。
2.确定所需的减速比:减速比由所需的输出转速和驱动电机的额定转速决定。
减速比=驱动电机的额定转速/所需的输出转速减速比 = 1500 rpm / (100 rpm / 60) = 9003.确定所需的传动类型:根据驱动方式为带传动(V-belt drive),可以选择使用皮带轮和皮带进行传动。
根据所需的减速比和驱动电机的额定转速,可以选择适当的皮带轮组合来实现所需的减速效果。
4.确定减速器的类型和规格:5.确定减速器的效率和功率:根据电机的功率和减速器的效率,可以计算出减速器的实际输出功率和所需的电机输入功率。
减速器的效率一般在90%左右,可以通过实际测试或者厂商提供的性能曲线来获取准确值。
减速机在选型时如何套用公式计算?10点妙招!

减速机在选型时如何套用公式计算?10点妙招!在您购买减速机的时候您可能不知道如何计算一些相关参数,那下面就看看一些具体的参数如何计算包括已知数据与未知数参数的情况一、减速机选型计算(手算);(已知参数)1. 原动机电机功率:P1 KW电机转速:n1 / min最大起动扭矩:TA Nm2. 工作机工作机轴功率:P2 KW转速:n2 /min每天运行时间:h/day每小时起动次数每小时工作周期:ED =XXX%3. 电动机电机功率:P1 =75KW电机转速:n1=1500/min最大起动扭矩:TA=720 Nm4.皮带机皮带机轴功率:P2=66KW转速:n2=26/min每天运行时间:12h/日每小时起动次数:7次每小时工作周期: ED=100%二、减速机选型计算;(已知参数)环境温度:℃安装位置:室内小空间;室内大空间;室外;海拔高度:m环境温度:30℃安装位置:室内大空间海拔高度:<1000m三、减速机结构选型设计根据皮带机安装位置和空间大小,决定选择直交轴齿轮箱。
安装方式:卧式安装输出轴位置和型状:位于齿轮箱右侧,部置形式C型,实心轴输出轴旋转方向:面对输出轴端看为逆时针(CCW)四、减速机选型(类型和规格的确定)选择减速机规格和类型确定传动比:n1/n2=1500/26=57.7 in=56确定减速机额定功率:P2N≥P2×f1×f2=66×1.3×1=85.8kw从功率表中选择类型B3SH,减速机规格9 号,对应的额定功率P2N=100KWf1:工作机系数; f2:原动机服务系数检查减速机选型是否合适:(计算满足 3.33 ×P2≥P2N)3.33×P2=3.33×66=219.8KW>P2N(100KW) 满足要求。
五、减速机选型(类型和规格的确定)起动扭矩校核:P2N≥(TA×N1/9550) ×f3P2N≥ (720×1500 /9550) ×0.65= 73.5kwf3起动扭矩系数(查表3)六、确定减速机润滑方式确定减速机润滑油供给方式根据减速机安装方式和旋转速度决定;此减速机可采用浸油飞溅润滑,可查表确定是否采用强制润滑或飞溅润滑。
马达选用计算
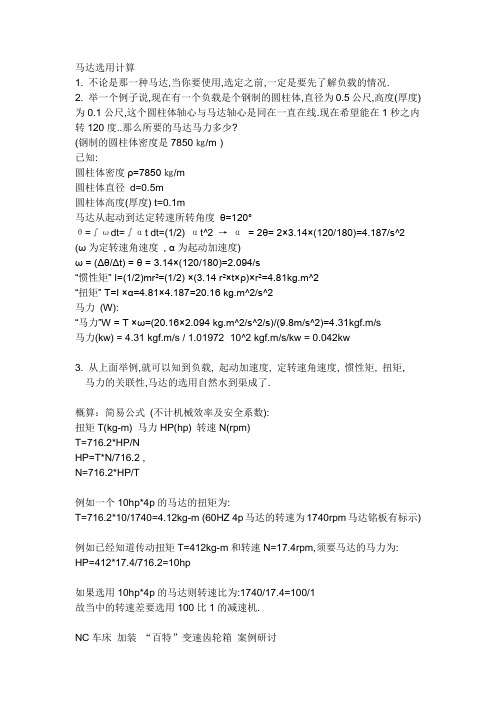
马达选用计算1. 不论是那一种马达,当你要使用,选定之前,一定是要先了解负载的情况.2. 举一个例子说,现在有一个负载是个钢制的圆柱体,直径为0.5公尺,高度(厚度)为0.1公尺,这个圆柱体轴心与马达轴心是同在一直在线.现在希望能在1秒之内转120度..那么所要的马达马力多少?(钢制的圆柱体密度是7850㎏/m³)已知:圆柱体密度ρ=7850㎏/m³圆柱体直径d=0.5m圆柱体高度(厚度) t=0.1m马达从起动到达定转速所转角度θ=120°θ=∫ωdt=∫αt dt=(1/2) αt^2 →α= 2θ= 2×3.14×(120/180)=4.187/s^2 (ω为定转速角速度, α为起动加速度)ω = (Δθ/Δt) = θ = 3.14×(120/180)=2.094/s“惯性矩” I=(1/2)mr²=(1/2) ×(3.14 r²×t×ρ)×r²=4.81kg.m^2“扭矩” T=I ×α=4.81×4.187=20.16 kg.m^2/s^2马力(W):“马力”W = T ×ω=(20.16×2.094 kg.m^2/s^2/s)/(9.8m/s^2)=4.31kgf.m/s马力(kw) = 4.31 kgf.m/s / 1.01972×10^2 kgf.m/s/kw = 0.042kw3. 从上面举例,就可以知到负载, 起动加速度, 定转速角速度, 惯性矩, 扭矩,马力的关联性,马达的选用自然水到渠成了.概算:简易公式(不计机械效率及安全系数):扭矩T(kg-m) 马力HP(hp) 转速N(rpm)T=716.2*HP/NHP=T*N/716.2 ,N=716.2*HP/T例如一个10hp*4p的马达的扭矩为:T=716.2*10/1740=4.12kg-m (60HZ 4p马达的转速为1740rpm马达铭板有标示)例如已经知道传动扭矩T=412kg-m和转速N=17.4rpm,须要马达的马力为:HP=412*17.4/716.2=10hp如果选用10hp*4p的马达则转速比为:1740/17.4=100/1故当中的转速差要选用100比1的减速机.NC车床加装“百特”变速齿轮箱案例研讨已知中碳素钢的切削阻抗应力: P=200 kg/mm2 ,假设切削深度:t= 6 mm, 工具机切削进给率:f= 0.3 mm/rev,则材料的切削力: F=P * t* f=200 * 6 * 0.3 = 360 kg当工具机之最大加工旋转半径R= 315 mm (0.315m)或旋转直径D= 630 mm (0.63m) 时扭力τ= F * R= 360*1.315 = 113.4 kg/m已知中碳素钢的切削最高速度V= 140 m/sec,经由下列公式可以反求得知所需之转速(N/rpm)及马力(HP/kw):∵V=π* D * N ∴140=π* 0.63 * N ∴N= 140 = 70.7 rpm π* 0.63∵扭力τ= 716.2 * HPN∴马力HP= τ* N = 113.4 * 70.7 = 11.2 ≒11.2 * 3/4 kw ≒8.4 kw 716.2 716.2若安全系数设为2时,所需马力为8.4 kw * 2 = 16.8 kw。
减速电机选型计算

减速电机选型计算摘要:减速电机是工业自动化领域中常见的关键设备之一,其主要作用是通过减速装置改变输出轴的转速和扭矩,以满足不同工况下的要求。
因此,在进行减速电机选型时,需要进行一系列的计算,以确定合适的型号和规格。
本文将以此为目标,介绍减速电机选型计算的方法和步骤。
1. 引言减速电机是通过减速装置降低电机的转速,并提高输出轴的扭矩,从而适应不同工况下的需求。
在工业自动化设备中,减速电机广泛应用于各种传动系统中,如:输送机、搅拌机、机械手等。
正确选型的减速电机可以提高设备运行效率,延长设备寿命,降低能源消耗。
2. 减速电机选型计算的基本步骤2.1 确定工作要求在进行减速电机选型计算之前,首先需要明确工作要求,包括输出扭矩、输出转速、工作环境要求等。
这些要求将作为计算的基础。
2.2 计算负载特性根据工作要求和工作环境,确定减速电机的负载特性。
这包括负载扭矩、负载惯量、负载转矩等参数的计算。
2.3 确定减速比根据负载特性和输出要求,计算减速比。
减速比是减速电机选型中的重要参数,它决定了输出轴的转速和扭矩。
2.4 计算电机功率和速度根据负载特性和减速比,计算减速电机所需的功率和速度。
2.5 选择减速电机型号和规格通过对比不同厂家和型号的减速电机,选择满足要求的型号和规格。
3. 减速电机选型计算的具体方法3.1 计算负载扭矩负载扭矩是减速电机选型计算的关键参数之一。
通常,负载扭矩的计算需要考虑工作周期、运行时间和启动瞬间等因素。
3.2 计算负载惯量负载惯量是减速电机能否正常工作的重要参数之一。
负载的惯性矩可以通过测量负载各部分的质量和距离来获得。
3.3 计算负载转矩负载转矩是根据负载惯量和减速比计算得出的。
根据牛顿定律,负载转矩可以通过以下公式计算得出:转矩 = 惯性矩× 加速度。
3.4 计算减速比根据工作要求和负载特性,计算减速比。
减速比可以通过公式:减速比 = 输出转速 / 输入转速计算得出。
减速电机选型计算
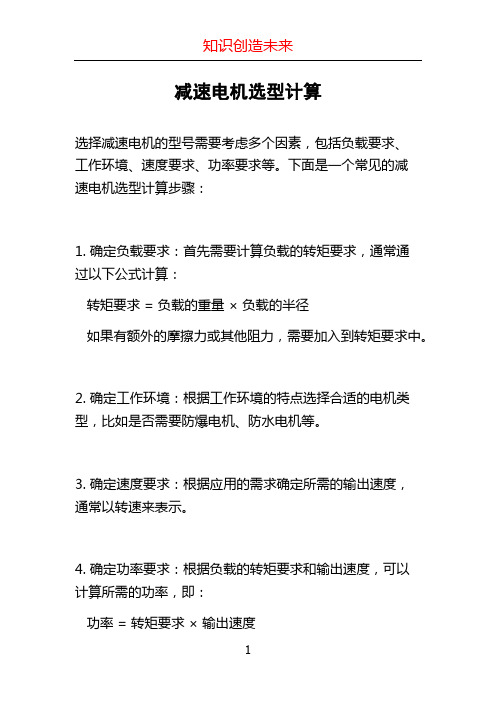
减速电机选型计算
选择减速电机的型号需要考虑多个因素,包括负载要求、
工作环境、速度要求、功率要求等。
下面是一个常见的减
速电机选型计算步骤:
1. 确定负载要求:首先需要计算负载的转矩要求,通常通
过以下公式计算:
转矩要求 = 负载的重量× 负载的半径
如果有额外的摩擦力或其他阻力,需要加入到转矩要求中。
2. 确定工作环境:根据工作环境的特点选择合适的电机类型,比如是否需要防爆电机、防水电机等。
3. 确定速度要求:根据应用的需求确定所需的输出速度,
通常以转速来表示。
4. 确定功率要求:根据负载的转矩要求和输出速度,可以
计算所需的功率,即:
功率 = 转矩要求× 输出速度
需要注意的是,电机的额定功率应大于所需功率。
5. 根据以上参数选择合适的减速电机型号。
需要提醒的是,这只是一个常见的减速电机选型计算步骤,实际选型过程还需要考虑一些其他的因素,比如效率、可
靠性、价格等。
同时,也可以通过咨询相关的电机供应商
或工程师来获取更专业的选型建议。
减速机电机选型方法

减速机,电机选型常用方法
本期内容主要内容是给大家讲一下减速机,电机选型常用方法。
电机选型常用方法:
功率(W)=扭矩(nm)*角速度
角速度=2Pi*转/秒
电机功率:P=T*N/9550*η (其中T为扭矩,N为转速,η为机械效率)9550是转换为角速度
1、电机需要扭矩运动
P—功率,kW;F—牵引力(kN),V—速度(m/min),η—传动机械的效率
2、T=9550 P/N (转动)
n—电机的额定转速 r/min;T—转矩,Nm
实际功率=K*扭矩*转速(K—转换=9550*电机功率(千瓦)/电机转速n
P=F*v÷60÷η(直线系数)
减速机选型常用方法:
1、先选速比:先确定负载所需要转速,即减速机出力轴的输出转速,在用电机的输出转速/减速机轴输出转速=减速比
2、减速机的选型:得上述减速比后,根据电机额定输出扭矩*减速比<减速机额定输出扭矩,根据这个输出扭矩选型,就可以确保减速机不会崩齿了。
3、最后将电机型号或者尺寸报给减速机厂商即可
资料来源——天机传动。
电机、减速器的选型计算实例

电机减速机的选型计算
1参数要求
配重300kg,副屏重量为500kg,初选链轮的分度圆直径为164.09mm,链轮齿数为27,(详见misimi手册P1145。
副屏移动的最大速度为0.5m/s,加速时间为1s。
根据移动屏实际的受力状况,将模型简化为:
物体在竖直方向上受到的合力为:
其中:
所以:
合力产生的力矩:
其中:r为链轮的半径
链轮的转速为:
2减速机的选型
速比的确定:
初选电机的额定转速为3000r/min
初选减速器的速比为50,减速器的输出扭矩由上面计算可知:193.6262Nm 3电机的选型
传动方式为电机—减速机—齿轮-链轮-链条传动,将每一级的效率初定位为0.9,则电机的扭矩为:
初选电机为松下,3000r/min,额定扭矩为:9.55Nm,功率3kw转子转动惯量为7.85X10-4kgm2带制动器编码器,减速器为台湾行星减速器,速比为50,额定扭矩为650NM
4惯量匹配
负载的转动惯量为:
转换到电机轴的转动惯量为:
惯量比为:
电机选型手册要求惯量比小于15,故所选电机减速器满足要求
减速机扭矩计算方法:
式:
减速机扭矩=9550×电机功率÷电机功率输入转数×速比×使用系数
知道扭矩和减速机输出转数及使用系数,求减速机所需配电机功率如下公式:电机功率=扭矩÷9550×电机功率输入转数÷速比÷使用系数。
- 1、下载文档前请自行甄别文档内容的完整性,平台不提供额外的编辑、内容补充、找答案等附加服务。
- 2、"仅部分预览"的文档,不可在线预览部分如存在完整性等问题,可反馈申请退款(可完整预览的文档不适用该条件!)。
- 3、如文档侵犯您的权益,请联系客服反馈,我们会尽快为您处理(人工客服工作时间:9:00-18:30)。
确定升降摆动吊带轮的直径:D(mm)----- 一般要求升降摆动吊带轮(或曲柄)的摆动角度小
于80°(±40°),当升降摆幅为40mm(±20mm)时,采用Φ60mm的SUS304圆支作吊带轮,当升
降摆幅为50mm(±25mm)时,采用Φ75mm的SUS304圆支作吊带轮,则升降摆动所需扭矩: M=Wx9.8xD/2000 (N.M)
深 5.5.1计算所需扭矩: 首先计算交换车在最大負荷状态下工作时的总重量:W(Kg),包括交换车架、随交换车移动的
的水槽及水的重量、飞巴和工件、挂具的重量等;
确定交换车轮的直径:d(mm)----- 交换车轮应设计成一边有导向一边无导向,若两边车轮
均设计为有导向,则万一交换车轨道有变形时,易产生卡滯现象; 交换车应尽量设计成链条拖动
公 技 撐的选较小功率,而负载较重、频率较快、托轮支撐的选较大功率。
科 对于采用龙门式或天井式吊车的大中型设备,水平搖摆频率大多在8±2次/分鐘范圍內。如 图新 果是單槽摆动,一般选用功率0.18KW以下的小型刹车马达; 如果是全面式摆动,一般选用功率 永 0.25KW以上的小型刹车马达,负载较輕、频率较低、吊带懸挂支撐的选较小功率,而负载较重、 圳 频率较快、托轮支撐的选较大功率。
用度,fB数值越大,说明减速机越耐用。一般选择fB≧1.2
料 资
5.5.4确定交换车减速机马达型号:
考
参 根据上述确定的M'、i、fB数值从型录中选择合适的减速机马达型号,一般选用4级刹车马达。 ( 5.6选择减速机马达要考慮的主要因素:
5.6.1 输出扭矩或功率、扭矩储备系数
司
5.6.2输出转速或减速比
5.3水平搖摆减速机马达
) 水平搖摆由于受搖摆频率、摆幅、角度和工件形狀、尺寸以及支撐形式等的影響,负载变化 料 级大,很難估算,一般都是參照以前制作過的、類型与規格相近的设备来比较选取。水平搖摆一 资 般选择带刹车的减速机马达(三相四级),对于有摆动频率调节要求的,应配备变频器调速。
考 参 对于采用侧臂式吊车的小型设备,通常是用挂籃装載PCB作前后處理,這類设备的水平搖摆 ( 频率大多在10±4次/分鐘范圍內。如果是單槽摆动,一般选用功率90W以下的微型刹车马达; 如 司 果是全面式摆动,一般选用功率0.18KW以上的小型刹车马达,负载较輕、频率较低、吊带懸挂支
5.2吊车升降减速机马达
新
5.2.1计算所需扭矩:
图
永 首先计算吊车的最大提升总重量:W(Kg),包括吊车吊臂、飞巴和工件、挂具的重量,以及
圳 所带水份的重量; 深
确定提升皮带轮的最大卷绕直径:D(mm)----- 小型侧臂式吊车一般采用Φ80mm皮带轮,而大
型侧臂式吊车和龙门式吊车一般采用Φ90mm皮带轮,根据提升高度的不同,皮带卷绕层数也不同,
将减速机的输出转速除以马达的同步转速,即是所需要的减速比i.
5.4.3确定使用系数fB:
)
资料 使用系数是减速机最大输出功率与所配马达额定功率的比值,亦可以简单地看作是减速机的
耐用度,fB数值越大,说明减速机越耐用。一般选择fB≧1.2
考
5.4.4确定升降搖摆减速机马达型号:
参
(
司 根据上述确定的M'(P)、n(i)、fB数值从型录中选择合适的减速机马达型号,一般选用四级马
速比i=1/30. 5.2.3确定使用系数fB:
使用系数是减速机最大输出功率与所配马达额定功率的比值,亦可以简单地看作是减速机的
耐用度,fB数值越大,说明减速机越耐用,一般选择fB≧1.2。
5.2.4确定升降减速机马达型号:
根据上述确定的M'、i、fB数值从型录中选择合适的减速机马达型号,一般选用4级刹车马 达。
公
5.6.3是否采用刹车马达
技 科
5.6.4使用系数
新
5.6.5电力規格
图
永 5.6.7减速机的出軸形式、方向和安装方式
圳 5.6.8马达接線盒位置
深 5.6.9润滑方式
間(不包括两端等待上下挂时間),确定交换车的运动速度V(M/S),再算出减速机的输出转速
n: n=60V/πd (r.p.m.)
将减速机的输出转速除以马达的同步转速,即是所需要的减速比i.
5.5.3确定使用系数fB:
) 使用系数是减速机最大输出功率与所配马达额定功率的比值,亦可以简单地看作是减速机的耐
因此提升皮带轮的最大卷绕直径也会有较大变化,一般提升皮带轮的最大卷绕直径为100~130mm,
则提升所需扭矩: M=Wx9.8xD/2000 (N.M)
扭矩储备系数(或安全系数)一般选取≧1.3,则减速机马达的输出扭矩:
M'≧1.3M (N.M) 5.2.2确定减速比:
通常吊车升降最高速≦300mm/s,升降低速:65mm/s,依靠变频器调速,选择减速机马达的减
扭矩储备系数(或安全系数)一般选取≧1.3,则减速机马达的输出扭矩: M'≧1.3M (N.M) 5.4.2确定输出转速n或减速比i: 通常升降搖摆减速机马达的输出转速就是升降搖摆的摆动频率,当要求摆动频率可调节时,
应选用最高的摆动频率作计算依据,则升降搖摆减速机马达的功率:P=M'x n / 9550 (KW)
的减速速比i=1/30. 5.1.3 确定使用系数 f :
B
考 参
( 使用系数是减速机最大输出功率与所配马达额定功率的比值,亦可以简单地看作是减速机的
司 耐用度,fB数值越大,说明减速机越耐用,一般选择fB≧1.2。 公 5.1.4确定橫移减速机马达型号:
科技 根据上述确定的M'、i、fB数值从型录中选择合适的减速机马达型号,一般选用4级刹车马达。
公 达。值得特別提出的是,升降搖摆减速机马达千万不要选择刹车马达,因为马达一断电,搖摆装
科技 置就会在其自身重量的作用下,一直降到搖摆最低位!如果采用刹车马达,当断电时搖摆沒有在
新 最低位,则刹车会阻止搖摆机构下降,显得多余。当搖摆频率固定不变时,不要变频器调速,当
图 要求搖摆频率变化时,则要变频器调速。 圳永 5.5交换车用减速机马达
方式,即减速机马达不随交换车移动; 设计交换车时,要尽量降低运动件的重心,以提高运动的
ቤተ መጻሕፍቲ ባይዱ
稳定性,对于质量较重的有水槽交换车,必须有软起动软制动功能,可以采用变频器调速来实现。
一般选择SUS304交换车轮与SUS304路轨的摩擦系数f=0.15,则交换车移动所需扭矩:
M=Wx9.8x0.15x d /2000 (N.M) 扭矩储备系数(或安全系数)一般选取≧1.3,则减速机马达的输出扭矩: M'≧1.3M (N.M) 5.5.2确定减速比: 驱动交换车的减速机马达之减速比,一般是根据交换车往復运动的行程和流程允許的动作时
一般选择PU轮与SUS304路轨的摩擦系数f=0.2,则橫移所需扭矩:
M=Wx9.8x0.2xD/2000 (N.M)
扭矩储备系数(或安全系数)一般选取≧1.3,则减速机马达的输出扭矩:
) M'≧1.3M (N.M) 料 5.1.2确定减速比:
资 通常吊车橫移最高速:≦700mm/s,橫移低速:150mm/s,依靠变频器调速,选择减速器马达
减速机马达的选型计算
5.1吊车横移减速机马达
5.1.1计算所需扭矩: 首先计算吊车在最大负荷状态下工作时的总重量:W(Kg),包括吊车自重、工件、挂具与飞
巴的重量;
确定横移PU轮的直径:D(mm)----- 小型侧臂式吊车一般采用Φ5"(D=127mm)PU轮,而大型 侧臂式吊车和龙门式吊车一般采用Φ6" (D=152mm)PU轮;
深
水平搖摆的频率即是减速机马达的输出转速,根据马达功率和减速机的输出转速,即可确定
减速机马达的型号。当搖摆频率固定不变时,不要变频器调速,当要求搖摆频率变化时,则要变 频器调速。
5.4升降搖摆减速机马达 5.4.1计算所需扭矩:
首先计算某套搖摆装置在最大負荷工作状态下的总重量:W(Kg),包括搖摆框架、搖摆吊臂、