摩托车发动机曲轴机械加工技术
曲轴的机械加工工艺

曲轴的机械加工工艺
曲轴的机械加工工艺一般包括以下几个步骤:
1. 钢材修整:使用机械设备将原材料钢坯进行切割、锯割等操作,使得其与曲轴的设计尺寸接近。
同时,还需要进行热处理,使得钢材达到所需的力学性能。
2. 钢材粗加工:通过车床、铣床等机械设备,对钢材进行车削、铣削等操作,使其形成初步的几何轮廓。
3. 曲轴片的制造:将钢材分成若干段,每段分别进行车削、铣削等操作,使得每个曲轴片的几何形状和尺寸符合要求。
4. 吊挂:将曲轴片的上下端面加工成平行和垂直的状态,然后进行悬挂,使得曲轴片的主轴中心线和整体曲轴的主轴中心线重合。
5. 精加工:使用磨床等设备,对曲轴片进行磨削,使其达到设计要求的尺寸和表面粗糙度。
6. 装配:将精加工好的曲轴片进行组装,根据设计要求将各段曲轴片组合在一起,形成完整的曲轴。
7. 检测:对制造好的曲轴进行质量检测,包括尺寸精度、加工粗糙度、内外表
面质量等方面的检查,以确保曲轴符合设计要求。
8. 表面处理:对曲轴进行表面处理,包括防腐蚀处理、表面涂层等,以提高曲轴的耐用性和使用寿命。
以上是曲轴的一般机械加工工艺,具体步骤和操作方式可能会因不同的曲轴类型和加工要求而有所不同。
发动机曲轴生产工艺

发动机曲轴生产工艺
发动机曲轴是发动机的关键部件之一,其生产工艺对于发动机性能的提升具有重要意义。
以下是发动机曲轴的生产工艺过程。
首先,曲轴的生产工艺从原材料的选择开始。
一般情况下,曲轴的原材料选用高强度的合金钢,如40Cr、35CrMo等。
这些
合金钢具有良好的耐磨性和高强度,能够满足曲轴在高速旋转时的强度要求。
接下来,曲轴的生产过程分为锻造和加工两个阶段。
锻造阶段是将所选的原材料加热至适宜温度,然后通过锻压机械进行锻造成型。
锻造的目的是使曲轴在结构上具有更好的连续性和均匀性,提高其强度和耐磨性。
锻造完成后,曲轴进入加工阶段。
加工阶段主要包括车削、磨削和检验等步骤。
在车削过程中,曲轴将被加工成所需的基本形状,并进行精确的外轮廓车削;在磨削过程中,曲轴将通过磨床进行细致的加工,确保其尺寸精度和表面质量;在检验中,曲轴将被进行各项性能测试,包括尺寸测量、硬度测试和磁粉探伤等。
最后,曲轴经过喷丸清洗和表面处理后,就可以进入组装阶段。
在组装过程中,曲轴将与其他发动机部件进行配合,形成完整的发动机装置。
组装完成后,曲轴还需要进行平衡修整,以确保其在旋转时的平衡性和稳定性。
总之,发动机曲轴的生产工艺包括原材料选择、锻造、加工和
组装几个关键阶段。
通过精细的生产工艺,可以生产出高质量的发动机曲轴,提高发动机性能和可靠性。
谈发动机曲轴加工工艺技术

关键词:发动机;曲轴加工;工艺技术1曲轴的加工工艺技术设计原则与加工工艺特点首先,是曲轴的加工工艺技术设计原则。
一方面,优化切削刃布置,提高切削面精度以及光滑程度。
发动机在运行过程中,会给曲轴带来巨大的冲击力,由于曲轴还要承担动力传递的任务,加大了曲轴加工的难度。
所以,要保证曲轴部件的稳定性,保证曲轴加工的质量与一致性。
另一方面,曲轴的技术人员要加强对曲轴技术与设计的深入研究,完善曲轴加工的各项技术标准,提高曲轴加工的整体效率与质量。
其次,是曲轴的加工工艺特点。
第一,曲轴的形状复杂。
曲轴的不同中心线不在同一水平线上,具有一定的偏心距离。
由于曲轴轴颈对平衡感以及设计基准位置的要求,在曲轴加工工艺的设计中,针对连杆轴颈,在进行偏心夹具的规划时,要尽量使中心线重合,再连接其他轴颈。
第二,曲轴的刚性差。
曲轴具有较大的长直径和复杂的曲柄结构,导致曲轴的刚性较差。
为了尽量减少曲轴在切削力下的变形,曲轴的加工工艺设计中,合理安排工序,针对粗加工中的变形,一步步地提高加工的精度。
粗加工具有更大的切削力,必须提高曲轴加工的刚性,尽量减少部件的变形。
第三,曲轴加工的技术要求较高。
曲轴在加工过程中对尺寸、形状、位置等具有较高的要求,加工工艺技术较复杂,要充分考虑不同加工方式的配置情况,合理配置粗加工、半精加工以及精加工的技术,在两侧确定中心孔时,尽量选择精加工,降低粗加工的精度误差。
2曲轴的加工工艺技术2.1中心孔技术、粗加工技术首先,是两端中心孔的加工技术。
定位基准中心孔是曲轴加工过程的重要环节,也是影响曲轴加工质量的重要因素。
曲轴中心孔的加工方式主要有两种选择,毛坯几何确定中心孔与质量确定中心孔,两者加工方式的选择具有异质性。
在选择具体的加工方式确定中心孔时,技术人员要对曲轴的具体情况进行综合的考察分析,做出科学的选择。
当前,国内曲轴的中心孔的确定多选择毛坯几何的方式,在确定中心孔时,要对毛坯的质量进行综合的评估分析,当能够有效的控制毛坯的质量处于稳定的较高水平状态,出于控制曲轴加工设备成本的角度,可以采取毛坯几何确定中心孔的方法。
摩托车曲轴加工工艺流程

摩托车曲轴加工工艺流程一、摩托车曲轴加工工艺流程的准备工作1.1研磨机和车床的准备在进行摩托车曲轴的加工之前,需要先准备好研磨机和车床等加工设备。
检查设备是否正常运转,保证设备的工作状态良好。
1.2准备工艺文件准备摩托车曲轴的加工工艺文件,包括加工工艺流程图、工艺卡片、加工工艺规范等文件,以指导后续的加工工艺流程。
1.3准备加工原材料准备摩托车曲轴的加工原材料,一般为优质的合金钢材料。
1.4准备检测设备准备好检测设备,用于对摩托车曲轴进行加工过程中的尺寸和质量进行检测和测量。
1.5对加工环境进行准备为了保证加工的准确性和质量,需要对加工环境进行准备,包括对加工场地的清洁和通风等方面进行安排。
二、摩托车曲轴加工工艺流程的车、铣、镗、磨工序2.1车削工序摩托车曲轴的车削工序是将加工原材料进行车削加工,首先是对加工原材料进行粗车,然后再进行精车。
在车削加工中需要注意保证车刀的刀具刚性和工件的精度,以及切削速度和进给量的选择。
2.2铣削工序摩托车曲轴的铣削工序是将经过车削的工件进行铣削加工,主要是加工曲轴的曲柄和连杆等部位。
在铣削加工中需要注意保证铣刀的刀具刚性和工件的平整度和表面粗糙度。
2.3镗削工序摩托车曲轴的镗削工序是将经过铣削的工件进行镗削加工,主要是加工曲轴的曲柄孔和连杆孔等部位。
在镗削加工中需要注意保证镗刀的刚性和工件的尺寸和形状精度。
2.4磨削工序摩托车曲轴的磨削工序是将经过镗削的工件进行磨削加工,主要是对曲轴的曲柄和连杆等部位进行精密磨削。
在磨削加工中需要注意保证磨轮的刚性和工件的尺寸和表面粗糙度。
三、摩托车曲轴加工工艺流程的装配和调试工序3.1装配工序将各个加工好的零部件进行装配,组装成成品曲轴。
3.2调试工序将装配好的摩托车曲轴进行调试,包括对曲轴的转动平衡性和动平衡性进行检测和调整,确保最终产品的质量和性能。
四、摩托车曲轴加工工艺流程的检测和质量控制工序4.1检测工序对加工好的摩托车曲轴进行尺寸和质量的检测,包括对曲轴的直径、长度、圆度、曲度和表面粗糙度等进行检测和测量。
发动机曲轴加工工艺及其夹具设计
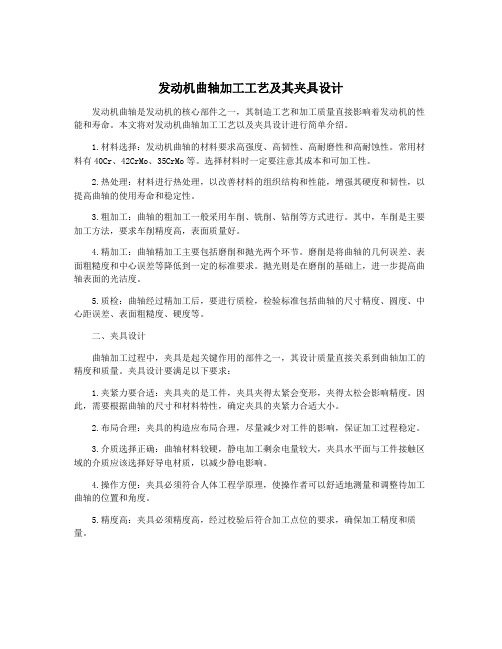
发动机曲轴加工工艺及其夹具设计发动机曲轴是发动机的核心部件之一,其制造工艺和加工质量直接影响着发动机的性能和寿命。
本文将对发动机曲轴加工工艺以及夹具设计进行简单介绍。
1.材料选择:发动机曲轴的材料要求高强度、高韧性、高耐磨性和高耐蚀性。
常用材料有40Cr、42CrMo、35CrMo等。
选择材料时一定要注意其成本和可加工性。
2.热处理:材料进行热处理,以改善材料的组织结构和性能,增强其硬度和韧性,以提高曲轴的使用寿命和稳定性。
3.粗加工:曲轴的粗加工一般采用车削、铣削、钻削等方式进行。
其中,车削是主要加工方法,要求车削精度高,表面质量好。
4.精加工:曲轴精加工主要包括磨削和抛光两个环节。
磨削是将曲轴的几何误差、表面粗糙度和中心误差等降低到一定的标准要求。
抛光则是在磨削的基础上,进一步提高曲轴表面的光洁度。
5.质检:曲轴经过精加工后,要进行质检,检验标准包括曲轴的尺寸精度、圆度、中心距误差、表面粗糙度、硬度等。
二、夹具设计曲轴加工过程中,夹具是起关键作用的部件之一,其设计质量直接关系到曲轴加工的精度和质量。
夹具设计要满足以下要求:1.夹紧力要合适:夹具夹的是工件,夹具夹得太紧会变形,夹得太松会影响精度。
因此,需要根据曲轴的尺寸和材料特性,确定夹具的夹紧力合适大小。
2.布局合理:夹具的构造应布局合理,尽量减少对工件的影响,保证加工过程稳定。
3.介质选择正确:曲轴材料较硬,静电加工剩余电量较大,夹具水平面与工件接触区域的介质应该选择好导电材质,以减少静电影响。
4.操作方便:夹具必须符合人体工程学原理,使操作者可以舒适地测量和调整待加工曲轴的位置和角度。
5.精度高:夹具必须精度高,经过校验后符合加工点位的要求,确保加工精度和质量。
摩托车曲轴加工工艺流程

摩托车曲轴加工工艺流程英文回答:The process of manufacturing a motorcycle crankshaft involves several steps. First, the raw material, usually a steel alloy, is selected and prepared for machining. This may involve cutting the material into appropriate lengths and removing any impurities or defects.Next, the rough machining of the crankshaft is performed. This involves using a lathe or milling machine to shape the crankshaft to its approximate dimensions. The rough machining process removes excess material and creates the basic shape of the crankshaft.After rough machining, the crankshaft undergoes heat treatment. This process involves heating the crankshaft to a specific temperature and then cooling it rapidly to improve its strength and durability. Heat treatment can help to reduce the risk of cracking or failure during use.Once the crankshaft has been heat treated, it undergoes final machining. This involves using precision tools and machines to refine the dimensions and finish of the crankshaft. The final machining process ensures that the crankshaft meets the required tolerances and surface finish.After final machining, the crankshaft may undergo additional processes such as balancing and surface treatment. Balancing involves adding or removing weightfrom the crankshaft to ensure that it rotates smoothly and evenly. Surface treatment, such as polishing or coating,can improve the crankshaft's resistance to wear and corrosion.Finally, the finished crankshaft is inspected forquality and then prepared for assembly. It may be packaged and shipped to a motorcycle manufacturer for installationin their vehicles.中文回答:摩托车曲轴的加工工艺流程包括几个步骤。
发动机曲轴加工工艺及其夹具设计

发动机曲轴加工工艺及其夹具设计发动机曲轴是发动机的核心部件之一,它的加工工艺和夹具设计对于发动机的性能和寿命有着至关重要的影响。
本文将从这两个方面进行探讨。
一、发动机曲轴加工工艺发动机曲轴的加工工艺主要包括以下几个步骤:1. 材料准备:选择合适的材料,如高强度合金钢、铸铁等。
2. 粗加工:采用车床、铣床等机床进行粗加工,将材料切削成初步形状。
3. 热处理:对粗加工后的曲轴进行热处理,以提高其硬度和强度。
4. 精加工:采用磨床等高精度机床进行精加工,将曲轴的各个部位加工到规定的尺寸和形状。
5. 表面处理:对曲轴进行表面处理,如抛光、喷涂等,以提高其表面光洁度和耐腐蚀性。
以上步骤中,精加工是最为关键的一步,它直接影响到曲轴的精度和平衡性。
因此,在精加工过程中,需要采用高精度的机床和刀具,并严格控制加工参数,以确保曲轴的精度和平衡性符合要求。
二、发动机曲轴夹具设计曲轴夹具是曲轴加工过程中不可或缺的工具,它的设计直接影响到曲轴的加工精度和效率。
一般来说,曲轴夹具应具备以下几个特点: 1. 稳定性好:曲轴夹具应能够稳定地夹紧曲轴,避免在加工过程中出现晃动或偏移。
2. 精度高:曲轴夹具应具备高精度的定位和夹紧功能,以确保曲轴的加工精度。
3. 适应性强:曲轴夹具应能够适应不同类型和尺寸的曲轴,以满足不同的加工需求。
4. 操作简便:曲轴夹具应具备简单易用的操作方式,以提高加工效率和安全性。
在曲轴夹具的设计中,需要考虑到曲轴的形状、尺寸和加工要求等因素,以确定夹具的结构和参数。
同时,还需要进行严格的试验和验证,以确保夹具的性能和可靠性。
发动机曲轴的加工工艺和夹具设计是发动机制造中非常重要的环节,需要采用高精度的机床和夹具,并严格控制加工参数和夹具结构,以确保曲轴的精度和平衡性符合要求。
发动机曲轴加工工艺
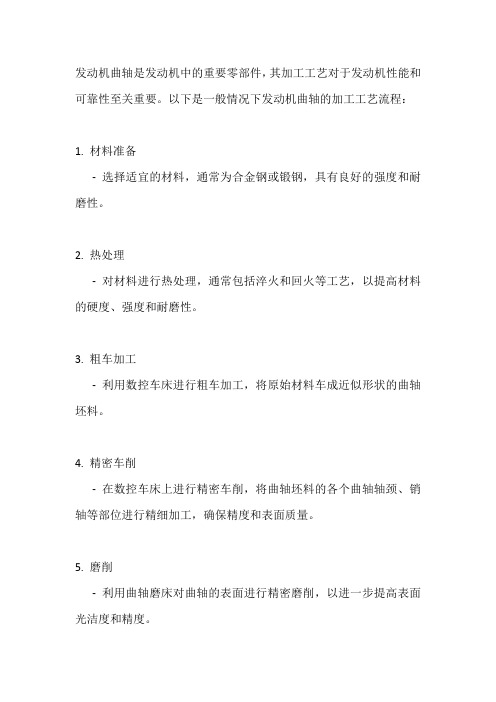
发动机曲轴是发动机中的重要零部件,其加工工艺对于发动机性能和可靠性至关重要。
以下是一般情况下发动机曲轴的加工工艺流程:
1. 材料准备
-选择适宜的材料,通常为合金钢或锻钢,具有良好的强度和耐磨性。
2. 热处理
-对材料进行热处理,通常包括淬火和回火等工艺,以提高材料的硬度、强度和耐磨性。
3. 粗车加工
-利用数控车床进行粗车加工,将原始材料车成近似形状的曲轴坯料。
4. 精密车削
-在数控车床上进行精密车削,将曲轴坯料的各个曲轴轴颈、销轴等部位进行精细加工,确保精度和表面质量。
5. 磨削
-利用曲轴磨床对曲轴的表面进行精密磨削,以进一步提高表面光洁度和精度。
6. 平衡
-对加工好的曲轴进行动平衡或静平衡处理,以保证曲轴在高速旋转时的平衡性能,减少振动和噪音。
7. 检测与检验
-对加工完成的曲轴进行尺寸检测、硬度检测、表面质量检测等全面检验,确保符合设计要求。
8. 表面处理
-进行表面镀铬等处理,提高曲轴的表面硬度和耐磨性。
值得注意的是,整个加工工艺需要严格控制加工精度和表面质量,以确保曲轴在发动机运行时能够承受高速旋转和周期性负载,并保持稳定性和耐久性。
同时,还需严格遵循相关的质量管理体系和安全操作规程,确保曲轴的工艺质量和安全性。
曲轴零件的机械加工工艺及夹具设计
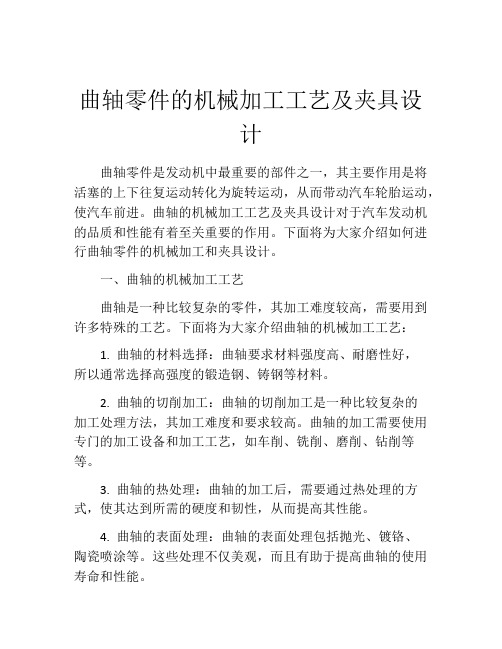
曲轴零件的机械加工工艺及夹具设计曲轴零件是发动机中最重要的部件之一,其主要作用是将活塞的上下往复运动转化为旋转运动,从而带动汽车轮胎运动,使汽车前进。
曲轴的机械加工工艺及夹具设计对于汽车发动机的品质和性能有着至关重要的作用。
下面将为大家介绍如何进行曲轴零件的机械加工和夹具设计。
一、曲轴的机械加工工艺曲轴是一种比较复杂的零件,其加工难度较高,需要用到许多特殊的工艺。
下面将为大家介绍曲轴的机械加工工艺:1. 曲轴的材料选择:曲轴要求材料强度高、耐磨性好,所以通常选择高强度的锻造钢、铸钢等材料。
2. 曲轴的切削加工:曲轴的切削加工是一种比较复杂的加工处理方法,其加工难度和要求较高。
曲轴的加工需要使用专门的加工设备和加工工艺,如车削、铣削、磨削、钻削等等。
3. 曲轴的热处理:曲轴的加工后,需要通过热处理的方式,使其达到所需的硬度和韧性,从而提高其性能。
4. 曲轴的表面处理:曲轴的表面处理包括抛光、镀铬、陶瓷喷涂等。
这些处理不仅美观,而且有助于提高曲轴的使用寿命和性能。
二、曲轴的夹具设计曲轴的夹具是曲轴机械加工的重要工具,它们可以确保曲轴在加工过程中的稳定性和精度。
夹具的设计应该考虑以下几个因素:1. 加工特性:不同的加工方式对夹具的要求不同,应根据加工特性设计夹具。
2. 工件材质:工件的材质对夹具设计产生很大的影响。
应该选择合适的材料和加工工艺,确保夹具的刚性和精度。
3. 加工精度:曲轴是一个高精度零件,夹具设计时应该注意加工精度的要求,保证夹具的精度和稳定性。
4. 生产效率:合理的夹具设计应该能够提高生产效率,降低成本,从而提高企业的竞争力。
总之,曲轴零件的机械加工和夹具设计对于汽车发动机的性能和品质有着至关重要的作用。
只有通过正确的加工工艺和夹具设计,才能制造出质量更高、性能更优的曲轴,满足汽车发动机的需求。
摩托车发动机曲轴结构、材料、加工工艺

一、曲轴材料汽车和摩托车曲轴连杆是发动机的关键零件,一般用40铬合金钢,或45号优质碳素钢制作,还需调制处理。
曲轴一般是用45号锻钢或者球墨铸铁来制作。
现在有国家标准可以参考GB/T23339-2009(曲轴)和GB/T23340-2009 (连杆)。
你好!发动机曲轴的材料性能要求有较高的强度、冲击韧性、耐磨性。
一般采用锻造钢和球墨铸铁,锻钢需要进行热处理采用调质,就是淬火后高温回火,使材料具有较高的综合机械性能,轴径表面再进行表面淬火,提高表面硬度及耐磨性。
球墨铸铁曲轴采取等温回火、中频淬火、激光淬火等热处理工艺。
我给你提供一些标准,在标准分享网下载,这些都是GB标准和曲轴的相关资料。
请下载研究,可以详细了解曲轴的材料和相应的技术性能要求和热处理方法及要求,这样我们就找到了我们的目标,有了目标,然后我们才好进行下一步的研究,这样形成了一个良好的开端,就是成功的一半了。
我认为很多标准是经过各方面的考虑和很多专家的意见的综合得来的。
是一个非常重要的要求。
这些标准或资料可以在(标准分享网)上下载,在其搜索输入例如“曲轴”或“曲轴热处理”或“曲轴工艺”或者直接输入下面的资料的关键词就可以免费、免注册快速下载相关标准和曲轴相关的资料。
1 GB/T23339-2009《内燃机曲轴技术条件》2 GB/T 24595-2009 《调质汽车曲轴用钢棒》3 GB/T 15712-2008 《非调质机械结构钢》4 《铸造缺陷和热处理工艺对球墨铸铁曲轴疲劳强度的影响》5 见参考网址:6其他要求根据你详细的情况在谷哥中搜索“曲轴热处理”等下面介绍下GB/T23339-2009《内燃机曲轴技术条件》相对于原JB/T6727-2000《内燃机曲轴技术条件》的主要变化。
GB/T23339-2009《内燃机曲轴技术条件》相对于原JB/T6727-2000《内燃机曲轴技术条件》的主要变化有两个方面。
一是材质方面,首次增加了采用非调质钢的规定。
曲轴零件的机械加工工艺及夹具设计概述
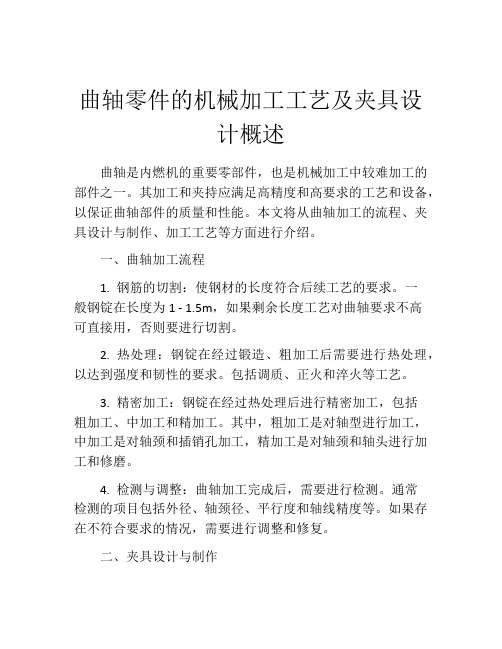
曲轴零件的机械加工工艺及夹具设计概述曲轴是内燃机的重要零部件,也是机械加工中较难加工的部件之一。
其加工和夹持应满足高精度和高要求的工艺和设备,以保证曲轴部件的质量和性能。
本文将从曲轴加工的流程、夹具设计与制作、加工工艺等方面进行介绍。
一、曲轴加工流程1. 钢筋的切割:使钢材的长度符合后续工艺的要求。
一般钢锭在长度为1 - 1.5m,如果剩余长度工艺对曲轴要求不高可直接用,否则要进行切割。
2. 热处理:钢锭在经过锻造、粗加工后需要进行热处理,以达到强度和韧性的要求。
包括调质、正火和淬火等工艺。
3. 精密加工:钢锭在经过热处理后进行精密加工,包括粗加工、中加工和精加工。
其中,粗加工是对轴型进行加工,中加工是对轴颈和插销孔加工,精加工是对轴颈和轴头进行加工和修磨。
4. 检测与调整:曲轴加工完成后,需要进行检测。
通常检测的项目包括外径、轴颈径、平行度和轴线精度等。
如果存在不符合要求的情况,需要进行调整和修复。
二、夹具设计与制作夹具的主要功能是稳定固定加工零件,使加工达到精确度和稳定性,提高加工效率和质量。
对于曲轴的加工中,常用的夹具有中心孔夹具、两端夹具和平行四边形夹具等。
对于中心孔夹具,其最主要的作用在于在加工过程中保持轴心不动,通过将曲轴的中心孔安装于夹具上,进行加工和旋转。
对于两端夹具,常常用于精密加工中,通过夹紧曲轴的两端进行加工和调整。
但使用两端夹具时应注意不要夹断轴颈。
平行四边形夹具则能够将曲轴固定,并确保平行度,是一个既简单,又有效的加工曲轴的夹具。
三、加工工艺1. 粗加工:曲轴的粗加工主要是对轴型进行加工。
首先,通过车削机将钢锭加工成符合直径要求的高度,并根据轴型图削出外形。
然后采用龙门铣床加工出内凸辊、凸轮和法块孔等。
2. 中加工:轴盖用旋花车进行加工,使其内直径和曲轴颈外径一致。
通过铣床将轴颈进行精密加工和修磨,以达到加工轴颈直径精度和表面粗糙度的要求。
此时需注意切削液的多次换换或循环过滤,防止不规则颗粒对轴颈的损伤。
发动机曲轴的加工工艺

发动机曲轴的加工工艺1. 引言发动机曲轴是发动机的重要组成部分,负责将活塞运动转换为旋转运动,并驱动其他附件工作。
发动机曲轴的加工工艺对于发动机性能和寿命有着重要的影响。
本文将详细介绍发动机曲轴的加工工艺。
2. 曲轴的材料选择发动机曲轴通常采用高强度合金钢制造,如40Cr、42CrMo等。
这些材料具有较高的强度和硬度,能够承受较大的载荷和磨损。
3. 曲轴的加工过程3.1 粗加工粗加工是指通过车削等方法将原始材料加工成近似形状的曲轴毛坯。
粗加工主要包括以下几个步骤:•材料切削:根据曲轴设计图纸,将原始材料切削成适当尺寸的毛坯。
•中心定位:使用中心定位装置将毛坯固定在车床上,确保其几何形状与设计要求一致。
•车削:通过车床进行车削加工,将毛坯的外形和尺寸加工到接近最终要求。
•钻孔:根据设计要求,在毛坯上进行钻孔,用于安装连杆和其他附件。
3.2 精加工精加工是指对粗加工后的曲轴进行细致的加工,以获得更高的精度和表面质量。
精加工主要包括以下几个步骤:•磨削:使用磨床进行磨削加工,将曲轴表面的不平整和余量去除,同时提高其圆度和表面光洁度。
•镗削:使用镗床进行镗削加工,将曲轴上的孔径扩大到设计要求,并提高其位置精度。
•滚压:通过滚压机对曲轴表面进行滚压处理,以提高其抗疲劳性能和表面硬度。
•平衡:对曲轴进行动平衡和静平衡处理,以减小振动和噪音,并确保发动机正常运转。
3.3 热处理热处理是对曲轴进行调质处理,以提高其强度和耐磨性。
常用的热处理方法包括淬火和回火。
淬火可以使曲轴表面形成高硬度的马氏体组织,回火则可以减轻内应力并提高韧性。
3.4 表面处理为了提高曲轴的耐腐蚀性和表面硬度,常常对曲轴进行表面处理。
常用的表面处理方法包括镀铬、喷涂和氮化等。
4. 曲轴加工设备曲轴加工需要使用各种专用设备和工具,包括车床、磨床、镗床、滚压机、热处理设备等。
这些设备和工具需要具备较高的精度和稳定性,以确保加工质量。
5. 质量控制在曲轴加工过程中,质量控制是非常重要的环节。
曲轴零件的机械加工工艺及夹具设计概述

曲轴零件的机械加工工艺及夹具设计概述曲轴是一种常见的发动机零件,它是将活塞通过连杆和拐角转化为旋转力量的重要机械零件。
曲轴旋转时承受着很大的惯性力和工作负荷,要保证曲轴的精度和强度,必须对其进行高精度的机械加工和精心设计的夹具。
本文将对曲轴零件的机械加工工艺及夹具设计进行详细的概述。
一、曲轴零件的机械加工工艺曲轴的机械加工工艺一般有以下步骤:1、毛坯加工:根据设计图纸的要求,选择合适的毛坯材料进行切削加工,制成粗加工后的曲轴毛坯。
2、中心线定位:将曲轴毛坯放在加工中心,通过调整夹具和自动控制系统,确保曲轴旋转轴线与加工中心的旋转轴线一致,保证加工精度。
3、粗加工:采用车床、铣床等机床进行粗加工,主要是将毛坯外形和基准面加工到设计要求的尺寸、形状和位置精度。
4、回火处理:为了提高曲轴的强度和韧性,需要对粗加工后的曲轴进行回火处理,调整材料的组织结构。
5、精加工:采用高精度的数控车床、磨床等机床进行精加工,对曲轴进行外圆、内孔、轴承座和油孔等核心部件的细加工和研磨,使其达到设计和使用要求的加工精度和表面光洁度。
6、表面处理:为了保护曲轴表面和提高其装饰性和耐蚀性,可以在曲轴表面经过电镀、喷涂、镀铬等工艺处理。
二、曲轴零件的夹具设计曲轴是一种中空、复杂零件,加工时不仅要保证零件的精度和表面质量,还要考虑到加工过程中对曲轴的变形、热变形和工艺损伤等因素的影响。
因此,曲轴的夹具设计是影响曲轴加工精度和效率的关键因素之一。
根据曲轴零件的特点,夹具的设计应该遵循以下原则:1、夹紧稳定:夹紧力应均匀分布,避免在加工过程中产生不均匀的受力和变形,损伤曲轴表面。
2、可调性强:夹具应具有可调性,能够适应不同型号和规格的曲轴加工,保证加工精度,提高生产效率。
3、刚性高:夹具应具有高的刚性和稳定性,使曲轴在加工过程中不会产生颤振和爆炸危险,保证加工质量。
4、操作简便:夹具的操作应简单、方便,能够快速装夹和卸夹,提高生产效率。
摩托车曲轴加工工艺流程

摩托车曲轴加工工艺流程下载温馨提示:该文档是我店铺精心编制而成,希望大家下载以后,能够帮助大家解决实际的问题。
文档下载后可定制随意修改,请根据实际需要进行相应的调整和使用,谢谢!并且,本店铺为大家提供各种各样类型的实用资料,如教育随笔、日记赏析、句子摘抄、古诗大全、经典美文、话题作文、工作总结、词语解析、文案摘录、其他资料等等,如想了解不同资料格式和写法,敬请关注!Download tips: This document is carefully compiled by the editor. I hope that after you download them, they can help yousolve practical problems. The document can be customized and modified after downloading, please adjust and use it according to actual needs, thank you!In addition, our shop provides you with various types of practical materials, such as educational essays, diary appreciation, sentence excerpts, ancient poems, classic articles, topic composition, work summary, word parsing, copy excerpts,other materials and so on, want to know different data formats and writing methods, please pay attention!摩托车曲轴是发动机中的重要零部件,其加工工艺直接影响着发动机的性能和稳定性。
摩托车曲轴加工工艺流程

摩托车曲轴加工工艺流程社会的不断进步,使得人们的生活水平在很大程度上得到了提高,摩托车曲轴加工工艺流程就是通过改变室内的热湿环境,为人们的居住生活提供一个舒适健康的环境。
摩托车曲轴加工工艺流程的应用越来越广泛,一个良好的摩托车曲轴加工工艺流程设计,不仅可以提高人们生活舒适度,还可以提高工作学习效率。
随着我国民众环保意识的增强,不再单单一味追求舒适的居住环境,更多的开始关注节能减排、绿色环保、和谐自然的居住环境。
1.1摩托车曲轴加工工艺流程引言概述摩托车曲轴加工工艺流程在最近几十年飞速发展的过程之中,其整体的产业耗能占比已经接近我国社会整体能耗的三分之一,而对于摩托车曲轴加工工艺流程的整体使用来说,其能耗在建筑整体能耗之中的占比达到了40-50%,摩托车曲轴加工工艺流程以其出色的节能性和环保性,受到越来越多的关注,同时也被不断推广。
但是,摩托车曲轴加工工艺流程在施工中往往不受重视,导致发生了很多问题,而且我国的摩托车曲轴加工工艺流程的设计和施工往往由不同单位承包,其对于问题的理解方式不同,相对应的利益关系也存在很大区别,导致很难有完美的配合。
加之,设计人员和施工人员的素质不同,摩托车曲轴加工工艺流程可能由于缺乏施工经验而凭空想象,造成设计不合理;施工人员对设计理解度不够,达不到设计要求,造成设计效果大打折扣等。
摩托车曲轴加工工艺流程的施工质量好坏直接和影响了建筑物的使用质量好坏,加强摩托车曲轴加工工艺流程的施工摩托车曲轴加工工艺流程管理,有利于提高摩托车曲轴加工工艺流程质量。
因此,对摩托车曲轴加工工艺流程进行工程摩托车曲轴加工工艺流程管理是非常有意义的,也是非常重要的。
由于社会的发展,人们的生活水平得到了大大提高,在这种大形势下,相应的物质需求也就急速膨胀,而摩托车曲轴加工工艺流程基本的居住工程也成了社会最为关注的重点摩托车曲轴加工工艺流程之一。
作为摩托车曲轴加工工艺流程中重要组成部分之一的摩托车曲轴加工工艺流程,其设施好坏还会对用户日常生活产生直接影响,因此摩托车曲轴加工工艺流程的质量是否过关直接影响到用户对于住房的选择,也是考察整个摩托车曲轴加工工艺流程的质量是否达标的重要参考条件之一。
曲轴零件的机械加工工艺及夹具设计
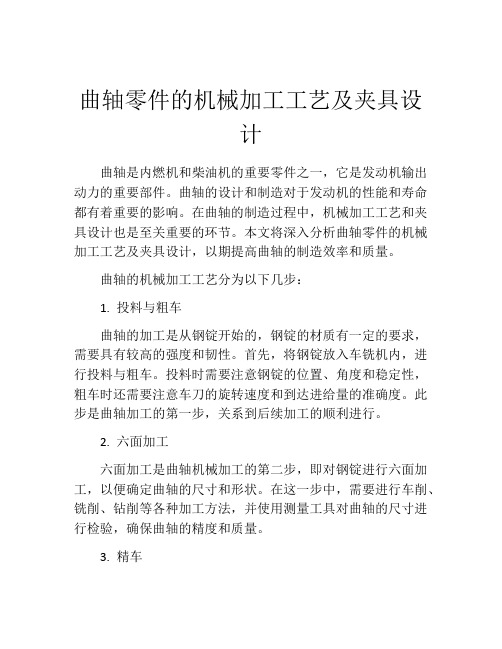
曲轴零件的机械加工工艺及夹具设计曲轴是内燃机和柴油机的重要零件之一,它是发动机输出动力的重要部件。
曲轴的设计和制造对于发动机的性能和寿命都有着重要的影响。
在曲轴的制造过程中,机械加工工艺和夹具设计也是至关重要的环节。
本文将深入分析曲轴零件的机械加工工艺及夹具设计,以期提高曲轴的制造效率和质量。
曲轴的机械加工工艺分为以下几步:1. 投料与粗车曲轴的加工是从钢锭开始的,钢锭的材质有一定的要求,需要具有较高的强度和韧性。
首先,将钢锭放入车铣机内,进行投料与粗车。
投料时需要注意钢锭的位置、角度和稳定性,粗车时还需要注意车刀的旋转速度和到达进给量的准确度。
此步是曲轴加工的第一步,关系到后续加工的顺利进行。
2. 六面加工六面加工是曲轴机械加工的第二步,即对钢锭进行六面加工,以便确定曲轴的尺寸和形状。
在这一步中,需要进行车削、铣削、钻削等各种加工方法,并使用测量工具对曲轴的尺寸进行检验,确保曲轴的精度和质量。
3. 精车曲轴的精车是机械加工中非常关键的一步,它可以提高曲轴的表面质量和尺寸精度。
在曲轴的精车过程中,需要使用砂轮进行加工,尤其需要注意砂轮的质量和尺寸的准确度。
曲轴的精车需要连续处理,以确保曲轴的表面光滑度和精度。
4. 钻削孔钻削孔是曲轴机械加工工艺的最后一步,它用于形成曲轴主轴承和连杆小头的孔洞。
在钻削孔的过程中,需要注意孔洞的直径和深度的准确度,孔洞的位置和角度的准确度,以及孔洞的表面光滑度。
曲轴的机械加工工艺需要设计合理的夹具,以确保曲轴的准确度、精度和表面质量。
在夹具设计过程中,需要考虑以下几个方面:1. 夹具的稳定性需要确保曲轴在加工的过程中不会发生晃动、掉落和变形等情况,以保证加工的精确性和安全性。
2. 夹具的垂直度夹具的垂直度需要保证在加工过程中曲轴的定位准确度和孔洞的位置和角度的准确度。
3. 夹具的尺寸精度夹具的尺寸需要与曲轴的尺寸相对应,在加工过程中确保曲轴的精确度和表面质量。
4. 夹具的耐磨性曲轴加工是连续进行的,需要保证夹具的寿命和使用效果,需要选择具有耐磨性的材料。
曲轴加工工艺(整理打印)

3.4 曲轴的机械加工工艺过程曲轴的机械加工工艺过程在很大程度上取决于生产批量、加工要求、毛坯种类和热处理安排等。
典型加工顺序为:铣两端面→钻中心孔→粗车→精车→铣削→热处理→磨削加工等。
曲轴机械加工过程大致可分为以下几个阶段:①加工定位基面→粗、精车主轴颈→中间检查;②粗磨主轴颈→铣定位面→车连杆轴颈→加工定位销孔、油道孔等次要表面→中间检查;③中频淬火→半精磨主轴颈→中间检查;④精磨连杆轴颈→中间检查;⑤精磨主轴颈→铣键糟→中间检查;⑥两端孔加工、动平衡→超精加工主轴颈及连杆轴颈→最终检查。
CA6102发动机曲轴生产线共有64道工序,72台设备,其中23台进口设备。
其主要工序见表3.1.3。
工序1、铸造工序2、热处理,正火工序3、粗车两侧面,划左端顶尖孔线工序4、粗车主轴颈两端工序5、半精车主轴颈两端和1:10锥体工序6、粗车连杆轴颈工序7、精车主轴颈两端和锥体工序8、精车连杆轴颈工序9、精车两侧面工序10、攻M36螺纹工序11、在主轴颈右端钻8Φ的小孔工序12、在主轴颈右端铣键槽工序13、终检加工表面工序(或工步)名称工序(或工步)余量工序(或工步)基本尺寸工序(或工步)经济精度工序(或工步)尺寸及其偏差表面粗糙度公差等级公差曲轴两端面粗车 2 717 IT11 0.220 721 12.5 精车0.5 715 IT8 0.054 716 1.6 毛坯 5 721 - - 716 -曲轴右端80Φ粗车 2 81 IT11 0.220 83 12.5 半精车0.6 80.4 IT9 0.087 81 3.2 精车0.4 80 IT8 0.054 80 1.6 毛坯 3 83 - - 83 -曲轴右端65Φ粗车 2 66 IT11 0.220 66 12.5 半精车0.6 65.4 IT9 0.087 65.4 3.2 精车0.4 65 IT7 0.035 65 1.6 毛坯 3 68 - - 68 -曲轴右端65Φ粗车 2 66 IT11 0.220 66 12.5 半精车0.6 65.4 IT9 0.087 65.4 3.2 精车0.4 65 IT8 0.054 65 1.6 毛坯 3 68 - - 80 -曲轴锥面部分粗车 3 - IT11 0.220 - 12.5 半精车0.6 - IT9 0.087 - 3.2 精车0.4 - IT8 0.054 - 1.6曲轴左端68Φ粗车 3 69 IT11 0.220 69 12.5 半精车0.6 68.4 IT9 0.087 68.4 3.2 精车0.4 68 IT8 0.054 68 1.6 毛坯 5 80 - - 80 -曲轴左端65Φ粗车 2 66 IT11 0.220 66 12.5 半精车0.6 65.4 IT9 0.087 65.4 3.2 精车0.4 65 IT7 0.035 65 1.6 毛坯 3 68 - - 68 -曲轴左端65Φ粗车 2 66 IT11 0.220 66 12.5 半精车0.6 65.4 IT9 0.087 65.4 3.2 精车0.4 65 IT8 0.054 65 1.6 毛坯 3 68 - - 80 -曲轴粗车 2 61 IT11 0.220 61 12.5工序3:粗车两侧面1加工条件工件材料:QT60-2,190—270HB ,铸造.加工要求:粗车左右侧面,留加工余量5mm.机 床:CW6180B 卧式车床.刀 具:YG6工序4 粗车主轴颈两端工件材料:QT60-2, 600b a M P σ=,铸件。
- 1、下载文档前请自行甄别文档内容的完整性,平台不提供额外的编辑、内容补充、找答案等附加服务。
- 2、"仅部分预览"的文档,不可在线预览部分如存在完整性等问题,可反馈申请退款(可完整预览的文档不适用该条件!)。
- 3、如文档侵犯您的权益,请联系客服反馈,我们会尽快为您处理(人工客服工作时间:9:00-18:30)。
摩托车曲轴一.关键词:摩托车曲轴性能要求制造工艺热处理二.摘要:本文介绍了摩托车曲轴的结构,结构简图,基本制造方法,工作条件,使用性能,毛胚材料,毛胚成型以及热处理工艺等,在尽量保证摩托车正常工作的前提下选择性能符合要求且成本低的材料。
三.摩托车曲轴的结构简介:曲轴是发动机的主要零件之一。
它将活塞的往复运动转换为曲轴的旋转运动,并在作功行程中,连续承受活塞连杆组传来的力,即周期变化的气体压力、往复和旋转运动质量的惯性力并输出转矩。
因此,曲轴在工作中既承受转矩又承受弯矩,这就要求曲轴有足够的强度和刚度。
曲轴由主轴颈、连杆轴颈、前端轴、飞轮组合和平衡块等组成,发动机曲轴为整体铸造,采用全支承结构,大大提高曲轴的抗弯强度。
为防止曲轴的轴向位移,该曲轴采用中间止推结构,如图所示。
为防止机油从曲轴后端沿轴向泄漏,在轴颈上设置了甩油盘及回油螺纹,在缸体上还装有分开式橡胶油封、密封回油螺纹后的轴颈,这些措施大大提高了封油效果。
曲轴后端凸缘通过6个螺栓与飞轮连接,其中有两个螺栓的导颈部分是定位用的,分别装在两个特定的定位孔中,以保证曲轴与飞轮相互间的准确位置。
这两个螺栓不能错装在其它螺栓孔中,螺母全部为槽式自锁螺母,曲轴飞轮螺栓的紧固次序如图所示。
曲轴前端轴颈装有正时齿轮和V带轮(减振器),并装有甩油盘和起动爪,甩油盘将把沿V带轮轴颈外泄的机油甩回正时齿轮室内。
飞轮安装在曲轴的后端上,是一个质量大的铸铁圆盘。
它储存能量,带动整个曲柄连杆机构越过上止点,保证发动机曲轴旋转的均匀性和输出转矩的均匀性。
它借助本身旋转的惯性力,帮助克服起动时气缸中的压缩阻力和维持短期超载时发动机的继续运转。
飞轮前端面外缘上有一个圆柱销,这是发动机活塞上止点的标记。
只要飞轮上的这一标记对准飞轮壳右前端面观察孔边缘上的径向刻线,即是一、六缸活塞处于上止点位置。
四.工作条件:1.在工作过程中,曲轴收到很大的交变扭力,弯曲力,压力,离心力和拉力的共同作用。
同时,曲轴的各轴颈要在很高的比压下作高速转动,使轴颈和轴承收到高强度的磨损。
这就要求曲轴的材料必须有足够的强度和刚度,还具备搞疲劳强度高,轴颈表面的耐磨性强和平衡性好等特点。
2.主轴颈、连杆轴颈本身的精度,即尺寸公关等级IT6,表面粗糙度Ra值为 1.25~0.63μm。
轴颈长度公差等级为IT9~IT10。
轴颈的形状公差,如圆度、圆柱度控制在尺寸公差之半。
3.位置精度,包括主轴颈与连杆轴颈的平行度:一般为100mm之内不大于0.02mm;曲轴各主轴颈的同轴度:小型高速曲轴为0.025mm,中大型低速曲轴为0.03~0.08mm。
4.各连杆轴颈的位置度不大于±20′。
五.使用性能要求:根据工作条件和失效形式分析,可以对曲轴用材提出如下性能要求:1.高的疲劳强度,防止轴疲劳断裂;2.良好的综合力学性能,即强度与塑性,韧性有良好的配合,防止过载和冲击断裂;3.高的硬度,热硬性,热强度和良好的耐磨性,以增加抗咬死能力,防止轴颈等局部承受摩擦的部位过度磨损或咬死。
六.曲轴的一般制造方法:1铣曲轴两端面,钻中心孔本工序在钻铣车组合车床上完成,主要保证曲轴总长及中心孔的质量,若端面不平则中心钻上的两切削刃的受力不均,钻头可能引偏而折断,因此采用先面后孔的原则。
中心孔除影响曲轴质量分布外,它还是曲轴加工的重要基准贯穿整个曲轴加工始终。
因而直接影响曲轴加工精度。
打中心孔在本次工艺设计中因考虑设备因素,采用找出曲轴的几何中心代替质量中心。
打中心孔以毛坯的外表面作为基准,因而毛坯外表面质量好坏直接影响孔的位置误差。
2曲轴主轴颈的车削由于曲轴年产量不大,主轴颈加工采用车削,在刚度较强的普通车床上进行。
曲轴安装在前、后顶尖上线一端用大盘夹住而另一端用顶尖顶住,用硬质合金车几道工序上完成主轴颈的车削。
由于加工余大且不均匀,旋转不平衡,加工时产生冲击,因此工件要夹牢固。
车床、刀具、夹具要有足够的刚性。
主轴颈车削顺序是先精车一端主轴颈及轴肩,然后以车好的主轴颈定位。
另一侧用顶尖以中心孔定位。
车另一端主轴颈、肩及各个轴颈,半精度及精车都按此顺序进行,逐渐提高主轴颈及其他轴颈的加工精度。
3曲轴连杆轴颈的车削主轴颈及其它外圆车好后,以主轴颈作为加工连杆轴颈的基准,采用专用的车夹具、车削连杆轴颈,车削同样在普通车床上进行。
车削连杆轴颈需要解决的是角度定位(两连杆轴颈轴线需要控制在180度+30度或180度—30度)以及曲轴旋转的不平衡问题。
这些都由专用夹具来保证,夹具体为一对用以定位的V型块组成,装在接盘上。
接盘与车床过渡接盘靠中间的定位销定位并连接,接盘在过渡接盘上靠棱形定位销可转180度,依次车削两个连杆轴颈。
V型块中心与车床主轴线距离一个曲轴半径。
车削过程中,一端与曲轴主轴颈定位并夹紧,另一端靠偏中心座夹紧,中心座上钻有中心孔,中心孔偏心距同样为一个曲轴半径。
用顶尖顶紧中心孔,这样就能保证连杆轴颈轴线与车床主轴线一致。
安装夹具体的接盘上有平衡块,消除曲轴旋转时不平衡力矩的生。
曲轴加工时由于受到离心力和两顶尖的轴向压紧偏心力的作用,容易发生弯曲变形,为了加强工件刚度,用撑杆来撑住另一个曲拐的开移。
车削连杆轴颈时为了使切削力不致于太大,每次车削余量控制在1~1.5mm内,同时车床旋转不能太高,刀具采用高速钢。
4键槽加工这个键槽主要用于飞轮,加工此键槽应安排在主轴颈精车工序之后,这样能保证定位精度及控制键槽的深度以及对称度。
键槽加工是以两主轴颈定位,同样用专用夹具在普通铣床上进行。
5轴颈的磨削由于主轴颈及连杆轴颈精度较高,尺寸精度为IT6级,表面粗糙度1.6~0.8μm,并且具有较高的形状精度及位置精度。
因此主轴颈与连杆轴颈精车后要进行磨削,以提高精度表面粗糙度。
在工艺设计中,首先磨主轴颈然后磨连杆轴颈。
中间主轴颈磨好后才能磨其余轴颈,磨主轴颈和连杆轴颈的安装方法基本上与车轴颈相同,磨主轴颈是以中心孔定位,在外圆磨床上进行,磨连杆轴颈则以经过精磨的两端主轴颈定位,以保证与主轴颈的轴线距离及平行度要求,磨连杆轴颈是在曲轴磨床上进行的。
由于轴颈宽度不大,采用横向进给磨削法,生产率较高,磨轮的外形需仔细地修整,因为直接影响轴颈与圆角的形状,磨削余量根据车削后的精度而定,粗磨余量值每边0.2~0.3mm,精磨余量控制在0.1~0.15 mm内。
在横向进给磨削中,磨轮对工件的压力很大,为避免曲轴弯曲,采用可以调节的中心架,否则就不能去掉上道工序留下的弯曲度,最好待这个轴颈的摆差减小才开始使用中心架。
磨削主轴颈时应把两顶尖孔倒角处抹干净,去砂粒及油泥,确保加工基准——中心孔的精度,磨削工序之前必须修研中心孔。
加工时应要解决以下问题:A:正确分配粗加工、半精加工及精加工余量。
B:粗基准选择用曲轴两端的中心孔。
中心孔的加工以主轴颈外圆作为基准,这样能保证曲轴加工径向及轴向加工余量的均匀性。
C:精加工时仍用中心孔作为基准,但要重新修磨中心孔,避免精加工时因中心孔磨损引起加工误差。
也可一端用主轴颈定位,另一端用中心孔定位以提高刚度。
D:曲轴轴向定位以主轴颈轴肩定位,工艺设计时定位基准应尽量与设计基准一致。
七.毛坯材料:锻钢曲轴:优质中碳钢和中碳合金钢,如35、40、45、35Mn2、40Cr, 35CrMo钢等;铸造曲轴:铸钢、球墨铸铁、珠光体可锻铸铁及合金铸铁等, 如ZG25、QT600-3、QT700-2 、KTZ450-5、KTZ500-4等。
八.毛坯制造方法:毛坯制取方法:首先按照图样尺寸、形状要求制造,就是模锻:经过制坯工步、预锻和终锻工步、切锻工步来锻造所需的锻件的。
完善的模锻工艺过程包括下料、毛坯质量检查、加热、模锻、切边冲孔、表面清理、校正、精压、锻件热处理、质量检查、入库等工序。
热处理就是调质处理或正火处理,重复一次,回火,回火次数不限,必要时热矫正,然后消除内应力,空冷,空冷后的金相组织应符合以下要求:不低于GB/T 6394中所规定的4级晶粒度的晶粒至少不小于占每个视场面积的85%以上;金相组织应为珠光体+铁素体,不允许有GB/T 13299-1991中所规定的魏氏组织。
锻件经调质处理后,其基体的金相显微组织为索氏体。
锻件在热处理后,再经喷丸或喷砂处理。
为提高耐磨性和耐疲劳强度,轴颈表面经高频淬火或氮化处理,并经精磨加工,以达到较高的表面硬度和表面粗糙度的要求。
锻件的宏观组织不允许有机加工不可消除的折叠、孔眼(蜂窝孔和缩松孔)、折痕、起鳞、气泡、裂纹、分层、氧化皮及非金属杂质等影响强度的缺陷,不允许用补焊的方法消除曲轴缺陷。
对有平衡块的锻钢曲轴,在平衡块顶部的未填满部分进行补焊,补焊强度不低于曲轴平衡块其他处的强度,补焊后还要经过探伤。
九.制定毛坯零件制造工艺路线:在进行大量的工艺分析之后,制定出大批大量生产曲轴的加工工艺路线:(1)锻造(2)热处理(3)铣两端面(4)车两端工艺搭子外圆(5)钻主轴颈中心孔(6)钻连杆轴颈中心孔(7)检验(8)粗车三个连杆轴颈(9)精车三个连杆轴颈(10)车工艺搭子两端面(11)粗车各处外圆(12)精车各处外圆(13)检验(14)磨削连杆轴颈外圆(15)磨削两主轴颈(16)磨削φ22-00.12mm外圆(17)磨削φ20 0 -00.021mm外圆(18)检验(19)车掉两端工艺搭子(20)车两端面(21)铣键槽(22)倒角(23)去毛刺(24)最后检验十.安排热处理工序:(1)曲轴中频感应淬火曲轴中频感应淬火将采用微机监控闭环中频感应加热装置,具有效率高、质量稳定、运行可控等特点。
(2)曲轴软氮化对于大批量生产的曲轴来说,为了提高产品质量,今后将采用微机控制的氮基气氛气体软氮化生产线。
氮基气氛气体软氮化生产线由前清洗机(清洗干燥)、预热炉、软氮化炉、冷却油槽、后清洗机(清洗干燥)、控制系统及制气配气等系统组成。
(3)曲轴表面强化技术球墨铸铁曲轴圆角滚压强化将广泛应用于曲轴加工中,另外,圆角滚压强化加轴颈表面淬火等复合强化工艺也将大量应用于曲轴加工中,锻钢曲轴强化方式将会更多地采用轴颈加圆角淬火处理。