现场改善方案及几点建议
现场改善的技巧

现场改善的技巧
现场改善是指在实际工作场景中进行的改善工作,旨在提高工作效率、降低成本、提升质量等方面的综合改进。
以下是一些现场改善的技巧:
1. 制定明确的目标:在开始改善之前,需要明确所要解决的问题、目标和预期结果。
这可以帮助团队在改善过程中保持聚焦,并衡量改善的成效。
2. 进行现场观察:在改善之前,对现有的工作场景进行现场观察和调研。
这样可以帮助发现问题、瓶颈和潜在的改进机会。
3. 采用持续改进的方法:现场改善需要持续不断地进行,而不是一次性的改进活动。
可以采用Kaizen(改善)方法,通过持续小步改进来不断优化工作流程。
4. 制定改进计划:根据观察结果和团队的共识,制定具体的改进计划。
计划应该包括具体的行动步骤、责任人和时间表。
5. 培养改进文化:现场改善需要全员参与和支持。
可以通过培训和认识活动来激发员工对改进的热情,并建立一个积极的改进文化。
6. 使用适当的工具和方法:在改进过程中,可以使用一些常见的工具和方法,如5S整理、流程图、因果图、统计分析等,以帮助团队更好地分析问题、找出根本原因和制定解决方案。
7. 进行试点和持续监控:在进行一项改进之前,可以选择一个小范围的试点项目来验证改进效果。
同时,要持续监控改进措施的实施情况和效果,并及时调整。
8. 推广和分享成果:在成功实施改进之后,要及时向整个团队推广和分享改进成果。
通过分享案例和经验,可以激励其他团队成员进行类似的改进工作。
9. 持续学习和改进:现场改善是一个不断学习和改进的过程。
团队成员应该时刻保持学习的心态,并定期进行回顾和反思,以寻找进一步的改进机会。
现场改善方案及几点建议

xx年xx月xx日
目录
• 现场改善方案 • 生产流程优化 • 现场质量与安全管理 • 建议与展望
01
现场改善方案
方案目标与原则
目标
提高现场工作效率,减少浪费,提升产品质量和交货期。
原则
以顾客需求为导向,坚持持续改进和系统化思维,关注成本 效益和安全性。
改善策略与方法
优化生产线布局
根据市场需求、生产能力等因素,合理安排每个月的生产计划,避免生产进度出 现较大波动。
考虑生产资源的匹配
在安排生产计划时,应充分考虑生产资源的匹配情况,避免出现资源浪费或资源 不足的情况。
生产现场改善
优化作业布局
提高员工技能和素质
通过对生产现场的布局进行优化,减少生产 过程中的搬运、等待和空闲时间。
明确改善目标和实施计 划,分解为短期、中期 和长期任务。
成立专门工作 小组
抽调专业人员组成工作 小组,负责现场改善工 作的推进、监督和检查 。
宣传推广
通过内部会议、培训等 形式宣传推广现场改善 的理念和方法,获得员 工的理解和支持。
逐步实施
按照实施计划逐步开展 现场改善工作,过程中 不断总结经验教训,持 续改进。
要点三
培训员工提升信息化 技能
加强员工的信息化技能培训,提高员 工对信息系统的使用熟练度和生产管 理能力。
建议加强供应商合作,提升供应链整体效率,降低成本。
评估现有供应商
对现有供应商进行全面评估,筛选出有潜力的供 应商进行长期合作。
引入新的供应商
积极引入新的供应商,形成竞争机制,降低采购 成本。
建立供应商激励机制
04
建议与展望
建议工厂加强精益生产理念的培训和推广应用
改善现场环境方案
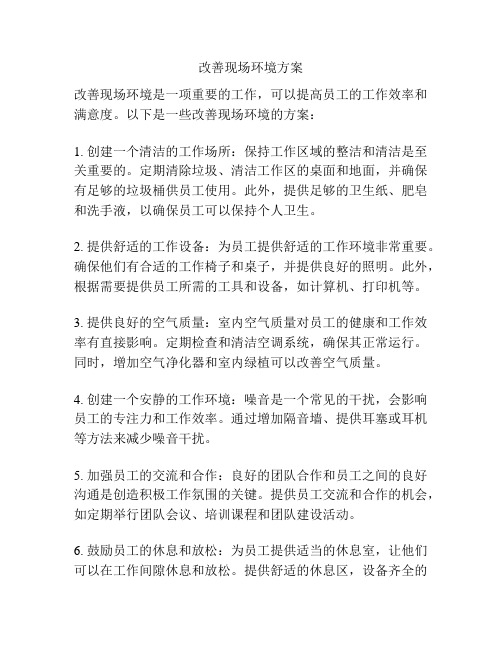
改善现场环境方案改善现场环境是一项重要的工作,可以提高员工的工作效率和满意度。
以下是一些改善现场环境的方案:1. 创建一个清洁的工作场所:保持工作区域的整洁和清洁是至关重要的。
定期清除垃圾、清洁工作区的桌面和地面,并确保有足够的垃圾桶供员工使用。
此外,提供足够的卫生纸、肥皂和洗手液,以确保员工可以保持个人卫生。
2. 提供舒适的工作设备:为员工提供舒适的工作环境非常重要。
确保他们有合适的工作椅子和桌子,并提供良好的照明。
此外,根据需要提供员工所需的工具和设备,如计算机、打印机等。
3. 提供良好的空气质量:室内空气质量对员工的健康和工作效率有直接影响。
定期检查和清洁空调系统,确保其正常运行。
同时,增加空气净化器和室内绿植可以改善空气质量。
4. 创建一个安静的工作环境:噪音是一个常见的干扰,会影响员工的专注力和工作效率。
通过增加隔音墙、提供耳塞或耳机等方法来减少噪音干扰。
5. 加强员工的交流和合作:良好的团队合作和员工之间的良好沟通是创造积极工作氛围的关键。
提供员工交流和合作的机会,如定期举行团队会议、培训课程和团队建设活动。
6. 鼓励员工的休息和放松:为员工提供适当的休息室,让他们可以在工作间隙休息和放松。
提供舒适的休息区,设备齐全的厨房和娱乐设施,如电视、游戏机等。
7. 提供员工健康和福利计划:员工的身心健康对于工作场所的改善至关重要。
提供健康保险、健身计划和假期等福利,可以激励员工保持健康的生活方式,提高生产力。
总之,改善现场环境是一项综合性的工作,需要涉及到许多方面。
通过创建一个清洁、舒适、安静的工作环境,加强员工的交流和合作,提供员工健康和福利计划,可以提高员工的工作效率和满意度。
现场存在问题及整改措施
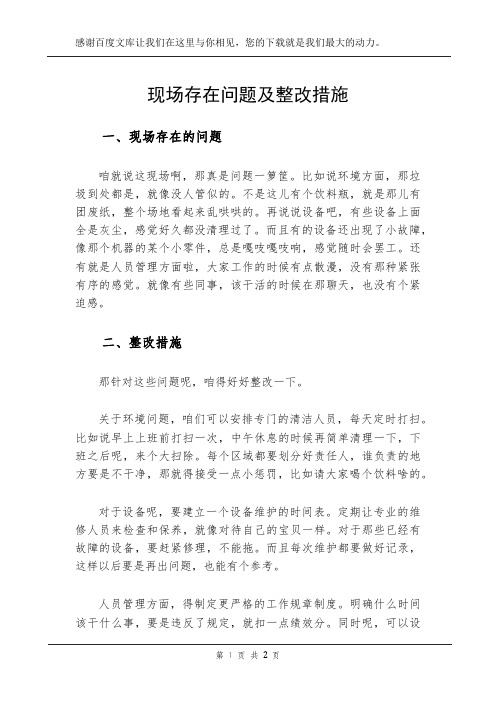
现场存在问题及整改措施一、现场存在的问题咱就说这现场啊,那真是问题一箩筐。
比如说环境方面,那垃圾到处都是,就像没人管似的。
不是这儿有个饮料瓶,就是那儿有团废纸,整个场地看起来乱哄哄的。
再说说设备吧,有些设备上面全是灰尘,感觉好久都没清理过了。
而且有的设备还出现了小故障,像那个机器的某个小零件,总是嘎吱嘎吱响,感觉随时会罢工。
还有就是人员管理方面啦,大家工作的时候有点散漫,没有那种紧张有序的感觉。
就像有些同事,该干活的时候在那聊天,也没有个紧迫感。
二、整改措施那针对这些问题呢,咱得好好整改一下。
关于环境问题,咱们可以安排专门的清洁人员,每天定时打扫。
比如说早上上班前打扫一次,中午休息的时候再简单清理一下,下班之后呢,来个大扫除。
每个区域都要划分好责任人,谁负责的地方要是不干净,那就得接受一点小惩罚,比如请大家喝个饮料啥的。
对于设备呢,要建立一个设备维护的时间表。
定期让专业的维修人员来检查和保养,就像对待自己的宝贝一样。
对于那些已经有故障的设备,要赶紧修理,不能拖。
而且每次维护都要做好记录,这样以后要是再出问题,也能有个参考。
人员管理方面,得制定更严格的工作规章制度。
明确什么时间该干什么事,要是违反了规定,就扣一点绩效分。
同时呢,可以设置一些奖励机制,比如这个月表现最好的员工,可以得到一份小礼物,像一本很有趣的书或者是一张电影票之类的。
然后呢,还可以多组织一些团队建设活动,让大家更有凝聚力,工作的时候就更有干劲了。
三、如何确保整改措施有效实施首先得有个监督小组,这个小组的成员要认真负责。
他们要随时检查整改措施的执行情况,要是发现哪里执行得不好,就得及时指出来。
然后呢,要定期开个会,大家一起讨论整改过程中遇到的问题,然后商量出更好的解决办法。
而且每个阶段都要做个小总结,看看哪些地方做得好,哪些地方还需要改进。
这样一步一步地,就能让现场变得越来越好啦。
反正就是说,咱们要把这个现场整得井井有条,大家工作起来也舒心,效率也能提高不少呢。
现场改善方案及几点建议

持续推进5S管理及现场改善活动
总结词
提高现场管理水平,优化生产环境。
详细描述
制定5S推行计划,明确责任人和实施步骤 。定期组织5S检查和评估,及时发现和整 改问题。同时,鼓励员工参与现场改善活动 ,提出改进建议,持续优化生产环境。
建立完善的质量管理体系并持续改进
总结词
详细描述
提升产品质量,提高客户满意度。
02
问题分析与定位
对反馈的问题进行深入分析,找 出问题的根本原因,为制定改进 措施提供依据。
03
改进措施实施与跟 踪
制定具体的改进措施并加以实施 ,同时对实施效果进行跟踪和评 估,确保问题得到有效解决。
质量成本的核算与控制
核算质量成本
将质量成本进行分类和核算,包括预防成本、鉴定成本、内部故障 成本和外部故障成本等,以全面了解产品质量对企业运营的影响。
配送计划制定
根据订单信息和库存状况 ,制定合理的配送计划, 确保订单及时送达的同时 避免库存积压。
配送技术升级
采用先进的配送技术,如 智能配送系统、无人机配 送等,提高配送效率和准 确性。
05
CATALOGUE
建议与展望
加强员工培训与团队建设
总结词
提升员工技能和素质,增强团队协作能力。
详细描述
制定定期的员工培训计划,包括技能培训、安全培训、质量意识培训等,提高员 工的专业技能和安全意识。同时,加强团队建设,提高员工的归属感和团队协作 能力。
供应商分级管理
根据供应商的综合能力,将供应商进行分级管理,对关键 供应商进行重点监控和合作,以实现供应链的稳定和高效 。
供应商绩效评估
定期对供应商的绩效进行评估,包括交货准时率、质量合 格率、服务响应速度等指标,以便及时调整供应商选择策 略。
现场改善方案及几点建议ppt

通过采用精益生产理念和工具,加强 现场管理和人员培训,提高员工素质 和技能水平,实现生产过程的可控和 稳定,提高生产效率和产品质量。
实施改善方案后,生产效率和产品质 量得到了显著提升,缩短了产品交货 期,提高了客户满意度,为公司创造 了更大的经济效益和社会效益。
对未来工作的展望
进一步完善生产流程和设备布局,持续优化生产计划 和物料管理,实现生产过程的进一步优化和提升。
03
提高生产安全性
自动化设备可以提高生产安全性,减 少工伤和职业病的发生率。
改善方案三:优化现场布局
提高空间利用率
通过合理的现场布局设计,可以提高空间利用率 ,降低生产成本。
提高物流效率
通过合理的现场布局设计,可以提高物流效率, 降低物流成本。
提高员工工作效率
通过合理的现场布局设计,可以提高员工工作效 率,提高生产效益。
03
对改善方案的几点建议
加强员工培训和意识教育
总结词
详细描述
提升员工技能与素质
总结词
通过定期的内部培训、外部培训以及在线学 习,提高员工的专业技能和综合素质,增强 员工的生产效率意识。
详细描述
培养自主管理意识
推行员工自主管理,培养员工的主人翁意识 ,提高员工发现问题、解决问题的能力,降 低生产事故发生率。
深入推进精益生产理念和工具的应用,扩大精益管理 的覆盖面,提高公司的整体精益管理水平。
加强与供应商的合作与协调,推动供应商参与改善, 降低采购成本和库存成本。
加强员工的培训和教育,提高员工的素质和技能水平 ,培养一支高素质、高效率的优秀员工队伍。
THANK YOU.
2023
现场改善方案及几点建议
目录
• 引言 • 现场改善方案 • 对改善方案的几点建议 • 结论
现场改善方案及几点建议

减少不良品率
加强原材料质量控制
01
严格把控原材料质量,从源头控制产品质量。
引入精益生产理念
02
通过引入精益生产理念,优化生产工艺,减少生产过程中的浪
费。
加强员工技能培训
03
定期对员工进行技能培训,提高员工技能水平,降低操作失误
率。
提升员工技能和素质
制定完善的培训计划
根据员工岗位需求,制定完善的培训计划,提高员工技能水平。
定期组织班组长培训学习,提高 班组长的管理能力和技能水平。
实践锻炼
让班组长参与实际管理工作,通过 实践锻炼提高管理能力。
经验交流
组织班组长之间进行经验交流,分 享管理经验和方法,共同提高。
03
员工培训与激励
加强员工技能培训
岗前培训
在新员工入职时,提供岗位技能、职责等方面的 培训,确保员工具备基本的业务能力和知识。
THANKS
感谢观看
整理
定期清理现场,去除不必要的 物品,保证现场空间的有效利 用。
清扫
保持工作区域的清洁卫生,为 员工创造良好的工作环境。
素养
提高员工素质,培养良好习惯 ,形成积极向上的工作氛围。
定期检查设备维护情况
定期检查
对设备进行定期检查,及 时发现并解决潜在问题。
维护保养
按照设备保养规范进行保 养,延长设备使用寿命。
04
结论与展望
总结现场改善方案及建议
总结方案
通过对现场进行全面细致的观察和分析,我们提出以下几项 改善方案:改进生产流程、优化设备布局、提高员工技能和 意识、加强质量控制等。这些方案旨在提高生产效率、减少 浪费、降低成本并提高产品质量。
建议
现场改善方案及几点建议通用课件

05 现场改善的挑战与解决方 案
员工参与度低
总结词
详细描述
解决方案
实施步骤
缺乏员工参与,现场改善难以 实现。
员工参与是现场改善的关键因 素,缺乏员工参与可能导致改 善措施无法有效实施。
建立员工参与的机制,鼓励员 工提出改进建议,并提供相应 的奖励和激励措施。
1. 建立员工参与的机制,包括 定期的员工大会、改善提案制 度等;2. 鼓励员工提出改进建 议,通过奖励和激励措施激发 员工的积极性;3. 定期评估员 工参与的情况,及时调整和优 化机制。
鼓励员工参与
建立良好的沟通机制
鼓励员工提出自己的意见和建议,促进信息的交流和共享,提高 决策的民主性和科学性。
激励员工创新
鼓励员工进行创新和改进,提供必要的资源和支持,为员工提供展 示自己才能的平台。
建立奖励机制
对积极参与的员工给予适当的奖励,激发员工的积极性和创造力。
定期评估与改进
制定评估标准
优化人员配置,避免人力资源的浪费。
02 现场改善建议
培训员工
01
02
03
明确培训目标
针对员工的弱项进行培训 ,提高其技能水平,使其 能够更好地应对工作中的 挑战。
制定培训计划
根据员工的实际情况和公 司需求,制定合理的培训 计划,确保培训内容的针 对性和实用性。
实施培训
通过内部培训、外部培训 、在线培训等多种形式, 让员工能够方便地接受培 训。
绿色生产
强化环保意识,推广绿色生产模 式,降低能源消耗和环境污染。
清洁能源
利用太阳能、风能等可再生能源 ,替代传统能源,减少碳排放。
循环经济
通过废物分类、回收和再利用, 实现资源的高效利用,降低对环
现场改善所存在的主要问题及建议

现场改善所存在的主要问题及建议现场改善是指针对现场实际情况进行的改善措施,旨在提高生产效率、降低成本、优化工作流程等方面。
虽然现场改善可以为企业带来巨大的好处,但要充分发挥其效果,必须认真面对其中存在的主要问题,并提出相应的建议。
问题一:沟通不畅现场改善需要多个部门的协作和沟通。
然而,现实中往往存在沟通不畅的问题。
部门之间缺乏有效的沟通渠道和回应机制,导致信息传递不及时,工作任务分配不清楚,误解和矛盾频发。
这严重影响了现场改善的推进和效果。
建议:建立有效的沟通机制是解决这个问题的关键。
可以通过定期的会议、沟通平台和信息共享等方式,促进各部门之间的信息交流和协作。
同时,需要制定明确的工作责任分工和沟通流程,以提高沟通效率和减少误解。
问题二:缺乏员工参与和反馈现场改善必须依靠员工的参与和反馈,他们深知现场的情况,可以提供宝贵的意见和建议。
然而,在实际操作中,许多员工没有得到发言的机会,或者他们的意见没有得到重视。
这不仅令员工感到被忽视,也忽略了他们在改善过程中的重要作用。
建议:鼓励员工参与现场改善,提供主动发言和建议的机会。
可以设立员工建议箱、组织员工座谈会、开展员工培训等方式,激发员工积极性,使他们能够真正参与到现场改善中。
同时,要充分重视员工的反馈意见,认真评估并适时采纳合理建议。
问题三:缺乏有效的改善指标和监控机制现场改善需要有明确的目标和衡量指标,以便对改善措施进行评估和监控。
然而,目前许多企业在这方面存在问题。
一方面,没有明确的改善目标,难以衡量改善的实际效果;另一方面,缺乏有效的监控机制,导致改善效果无法及时发现和纠正。
建议:制定明确的改善目标和指标是解决这个问题的关键。
要确立具体的目标,如提高产能、降低不良率等,并将其与实际操作相结合,制定切实可行的改善措施。
同时,建立有效的监控机制,如设置关键点检查、引入现场数据采集系统等,实时掌握改善效果,及时调整和改进。
问题四:改善成果未得到长期维持现场改善往往是一个长期的过程,需要不断跟进和维持。
现场改善解决方案(3篇)

第1篇一、引言随着我国经济的快速发展,各行各业对生产效率和产品质量的要求越来越高。
现场改善作为一种提升企业竞争力的有效手段,已经成为企业持续发展的关键。
本文将从现场改善的背景、意义、原则和方法等方面,详细阐述现场改善的解决方案。
二、现场改善的背景与意义1. 背景(1)市场竞争加剧:随着全球化的推进,国内外市场竞争日益激烈,企业需要不断提高自身竞争力。
(2)劳动力成本上升:我国劳动力成本逐年上升,企业面临成本压力,需要通过改善现场来降低成本。
(3)安全生产要求:现场改善有助于提高安全生产水平,降低安全事故发生率。
2. 意义(1)提高生产效率:通过现场改善,优化生产流程,减少浪费,提高生产效率。
(2)降低生产成本:现场改善有助于降低生产成本,提高企业盈利能力。
(3)提升产品质量:改善现场环境,提高员工操作技能,确保产品质量。
(4)增强企业竞争力:通过现场改善,提高企业整体实力,增强市场竞争力。
三、现场改善的原则1. 以人为本:关注员工需求,提高员工工作满意度,激发员工潜能。
2. 预防为主:注重预防,将安全隐患消灭在萌芽状态。
3. 系统思维:从全局出发,综合考虑各个方面的因素,实现系统优化。
4. 持续改进:不断优化现场,追求卓越,实现可持续发展。
四、现场改善的方法1. 5S管理5S管理是指整理(Seiri)、整顿(Seiton)、清扫(Seiso)、清洁(Seiketsu)和素养(Shitsuke)五个方面的管理。
通过5S管理,可以改善现场环境,提高工作效率。
(1)整理:对现场物品进行分类,将无用、废弃物品清除,确保现场整洁。
(2)整顿:对现场物品进行标识、分类,确保物品摆放有序,方便取用。
(3)清扫:定期对现场进行清扫,保持现场清洁。
(4)清洁:制定清洁制度,确保现场清洁。
(5)素养:培养员工良好的工作习惯,提高员工素质。
2. 6W2H分析法6W2H分析法是一种系统分析方法,通过对问题的深入剖析,找出问题的根本原因。
现场管理不足及改进措施

现场管理不足及改进措施1. 现场管理的现状大家好,今天我们来聊聊现场管理这个话题。
说实话,现场管理这事儿,有点像家里的卫生,明明知道应该保持干净,但一忙起来,就容易变成“乱糟糟”的一团。
你瞧,很多时候现场管理就像一只没绳子的狗,想跑哪儿就跑哪儿,根本不受控制。
你可能在想,现场管理不就是个流程、一个制度吗?可不是那么简单呀,很多小细节总是被忽视掉,比如物品摆放、人员安排等等,结果一场忙碌下来,真是“乱七八糟”!其实,现场管理的不足有时候真的是“无形中”的,大家忙着各自的工作,谁又能留意到那角落里的杂物呢?还有,沟通也很重要哦。
大家在一起干活,可是有时候一句话没说清,事情就可能出现偏差,真是“说得好不如做得好”。
再说了,有些时候,大家忙得不可开交,想要把事情做好,但如果没有好的管理,结果往往是“劳而无功”。
所以,咱们得认真思考一下,现场管理的短板到底在哪里。
2. 现场管理不足的表现2.1 物品管理混乱说到物品管理,真是让人心累。
一大堆工具、材料,真是应有尽有,可是找起来就像大海捞针,费劲得要命。
你想想,有时候一个小工具搞不清楚放哪儿,结果整个团队得停下来等,那真是“抓瞎”啊!而且,物品如果放错地方了,不仅浪费时间,还可能造成安全隐患,这可不是开玩笑的。
2.2 人员安排不合理再来聊聊人员安排,很多时候大家都是各干各的,有时候一个人干得快,可是另一个人就慢得像蜗牛。
这样的安排,肯定会造成资源的浪费,简直是“火上浇油”。
要是能够合理调配,发挥每个人的特长,事情做起来就能事半功倍。
想象一下,大家都是“鸡犬升天”的样子,干劲十足,结果自然好得不得了。
3. 改进措施3.1 加强沟通那么,既然问题这么多,我们该怎么解决呢?首先,加强沟通绝对是个好主意。
定期召开团队会议,让每个人都有机会发言,把自己的想法提出来,大家一起brainstorm,真的是“众人拾柴火焰高”。
这样,不仅能够增进感情,还能提高工作效率,双赢嘛!3.2 制定标准流程另外,制定标准流程也是必须的。
现场改善方案及几点建议
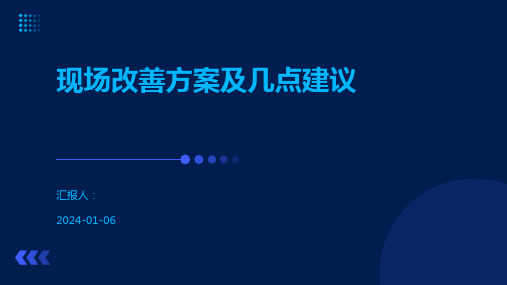
持续改进
根据评估结果和生产实际情况,对标准作业 指导书进行持续改进。
目视化管理
标识管理
对现场物品、区域、设备等进 行明确标识,方便识别。
颜色管理
利用不同颜色区分物品、区域 或状态,提高视觉效果。
图形管理
利用图表、图示等形式展示数 据、流程等信息,便于理解。
看板管理
设置看板,展示关键指标、目 标、计划等信息,提高管理效
03
设备与工装管理
设备维护保养
定期检查
制定设备检查计划,定期对设备进行全面检查,确保 设备处于良好状态。
预防性维护
实施预防性维护,定期更换易损件,清洗和润滑关键 部位,预防设备故障。
应急维修
建立应急维修机制,对突发故障进行快速响应和处理 ,尽快恢复生产。
工装夹具优化
分析和改进
对现有工装夹具进行分析,找出 存在的问题和改进点,进行优化
率。
02
人员培训与激励
培训计划
01
定期培训
制定定期培训计划,确保员工不 断更新知识和技能,提高工作效 率。
针对性培训
02
03
培训效果评估
根据员工的岗位和职责,提供针 对性的培训课程,以满足工作需 求。
对培训计划进行定期评估,了解 员工的学习成果,以便调整培训 内容和方式。
激励机制
薪酬激励
提供具有竞争力的薪酬福利,激发员工的工作积极性和创造力。
建立应急预案,组织应急演练,提高应对突发事 件的能力。
环境因素控制
识别现场环境因素,评估其对 环境的影响,制定相应的控制
措施。
加强废弃物分类、回收和处 理工作,减少对环境的污染
。
合理利用资源,降低能源消耗 ,提高能源利用效率。
现场改善方案及几点建议

合理安排生产设备、物料、工具等的布局,减少员工走动距离和时 间,提高工作效率。
加强现场沟通与协调
加强与员工的沟通与协调,及时解决现场问题,确保生产顺利进行 。
引入先进技术,提升产品质量
采用先进的生产设备和技术
引入先进的生产设备和技术,提高生产效率和 产品质量。
实施质量管理体系
建立完善的质量管理体系,确保产品质量符合 要求,提高客户满意度。
THANKS
谢谢您的观看
04
总结与展望
总结本次改善方案及建议的成果
提升生产效率
通过优化生产流程和减少浪费 ,现场改善方案成功提高了生
产效率。
提高产品质量
通过改进生产工艺和加强质量 控制,现场改善方案有助于提 高产品质量。
降低成本
通过减少原材料浪费和能源消 耗,现场改善方案有效降低了 生产成本。
增强员工参与度
通过员工参与改进过程,现场 改善方案增强了员工的归属感
通过培训和实践,提高员 工的技能水平和操作熟练 度。
培养员工安全意识
加强员工的安全培训,提 高员工的安全意识,减少 事故发生。
建立激励机制
通过建立激励机制,激发 员工的工作积极性和创造 力。
03
几点建议
加强现场管理,提高工作效率
制定合理的生产计划和流程
根据市场需求和产能,制定合理的生产计划和流程,减少生产中 的停顿和等待时间,提高工作效率。
加强质量意识培训
加强员工的质量意识培训,让员工认识到质量的重要性,提高员工对产品质量 的责任心。
加强员工培训,提高员工素质
加强技能培训
加强员工的技能培训,提高员作精神,提高团 队合作效率。
建立激励机制
关于改进生产现场管理的建议

关于改进生产现场管理的建议随着社会经济的发展和企业的不断壮大,生产现场管理的重要性日益凸显。
高效的生产现场管理不仅可以提高生产效率,降低成本,还可以增加员工的工作积极性和满意度,进而提升企业的竞争力。
本文将就改进生产现场管理提出以下几点建议。
一、建立并优化生产流程在生产现场管理中,生产流程是关键环节。
建立明确、流程化的生产流程能够有效提升生产效率。
为此,企业应该对生产流程进行全面审视和优化。
首先,通过分析每个环节的工作内容和时间耗费,找出可能存在的瓶颈和浪费,并加以改进。
其次,合理安排生产任务的先后顺序,确保各个工序之间的衔接协调,避免生产过程中的等待和停顿。
最后,引入先进的生产流程管控技术,如精益生产、六西格玛等,以提高质量和效率。
二、提供必要的设备和工具生产现场管理的另一个重要方面是提供必要的设备和工具。
只有具备适当的设备和工具,员工才能更好地完成工作任务。
因此,企业需要对现有的设备和工具进行全面的调查和评估,确定是否需要进行更新或更换。
此外,对于一些频繁使用的工具,应该提前备好,以避免生产过程中不必要的等待。
另外,还应建立良好的设备维护和保养制度,确保设备的正常运行和寿命。
三、加强员工培训和技能提升员工是企业生产的中流砥柱,加强员工培训和技能提升对于改进生产现场管理至关重要。
企业应该根据员工的工作需求和发展方向,制定全面的培训计划,并通过内外部培训资源,提供必要的培训和学习机会。
培训内容可以包括工作操作技能、质量控制知识、安全意识培养等方面。
此外,建立良好的员工激励机制,鼓励员工参与各种培训和学习活动,提高员工的技能水平和工作积极性。
四、实施现场安全管理生产现场管理中的安全问题不容忽视。
为了保障员工的安全和健康,企业应该制定并严密执行现场安全管理制度。
首先,确保现场设备和工具的安全性,及时修复或更换有问题的设备和工具,避免发生意外伤害。
其次,加强员工的安全意识培养,定期进行安全教育和培训,提高员工识别和应对潜在风险的能力。
操作工现场改善计划方案

操作工现场改善计划方案一、现状分析。
咱操作工在现场干活儿,就像在一个大迷宫里找出口,有些地方特别绕,效率不高。
比如说,工具摆放那叫一个乱,每次找个工具都得翻箱倒柜,跟寻宝似的,这就浪费了好多时间。
还有啊,操作流程有时候不太顺溜,就像走路的时候突然有个坑,得绕一下才能继续走,这也影响咱的工作速度。
再加上现场有时候有点脏和乱,让人看着就心烦,干活儿都没劲儿。
二、改善目标。
1. 提高工作效率,就像给咱自己的工作按上加速器,让每个操作环节都能像行云流水一样顺畅。
目标是在[具体时间段]内,整体工作效率提升[X]%。
2. 把现场整理得干干净净、井井有条,就像家里刚被老妈收拾完一样,让人一进去就觉得舒坦,而且工具啥的一眼就能看到,拿取方便。
3. 降低出错率,咱不能老是在工作里犯错,就像打球老是投不进篮筐一样丢人。
要把出错率在[具体时间段]内降低[X]%。
三、具体改善措施。
# (一)工具管理。
1. 定制工具架。
咱得弄一个专门的工具架,每个工具都有自己的小窝。
就像每个小朋友都有自己的座位一样,这样找工具的时候,眼睛一扫就知道在哪儿了。
给工具架分好区,按照使用频率来放工具。
常用的工具就放在最顺手的地方,不常用的就放在稍微靠里一点的地方。
这就好比把常用的筷子放在饭桌上最容易拿到的地方,不常用的特殊餐具就放在橱柜靠里的地方。
2. 工具标识。
给每个工具的小窝都贴上标签,上面画着工具的样子或者写上工具的名字。
这样,哪怕是刚来的小菜鸟,也能一下子找到想要的工具。
就像去超市找东西,看了标签就知道在哪儿。
# (二)操作流程优化。
1. 流程梳理。
大家一起坐下来,好好把现在的操作流程捋一捋。
就像拆一个机器一样,把每个步骤都拆出来看看,哪些是可以简化的,哪些是可以合并的。
比如说,原来要先做A 再做B,但是仔细想想,其实可以同时做,那就改过来。
2. 操作指南制作。
弄一个简单易懂的操作指南,就像做菜谱一样。
把每个操作步骤都写得清清楚楚,最好还配上一些小图片。
现场工作改进计划和建议

现场工作改进计划和建议干这行这么久,今天分享点现场工作改进的经验。
我觉得现场工作那是相当复杂的,就像一团乱麻,你得一点点梳理。
首先就是工作流程这块,我之前总是按照老的流程走,也没觉得有啥不对。
可有一次啊,因为一个小环节的延误,整个项目都被拖了后腿。
我感觉这就是缺乏对流程的重新审视。
我后来就花了不少时间把整个流程画出来,每个环节都细细研究,就像给一个机器拆零件一样,然后发现好多可以合并或者精简的部分。
比如说,以前资料传递要经过三个人,其实完全可以简化为两个人传递就行。
这一下效率就提高了很多。
还有现场的人员安排。
我参与的一次活动,安排了好多人在一个区域,结果人挤人,工作还进展不顺利。
我感觉在人员分布之前,一定要先对工作区域有个清晰的划分。
就像在家里打扫卫生,你得先规划哪个房间先打扫,几个人打扫。
现场也是一样,根据具体的工作内容和工作量来精确分配人员。
别一股脑的把人都堆在一块。
哦对了还有,人员之间的沟通也很重要。
我之前参加一个工程建设的现场工作,施工人员和设计人员沟通不畅,施工的按照自己的想法来,设计的又觉得没按照设计方案,结果就产生了很多返工的情况。
我觉得可以建立一个专门的沟通小组,或者用可视化的东西来呈现工作要求,像在墙上挂个大的设计图啥的,让所有人都看得明白。
不过我也知道,这种办法可能在一些大型复杂的项目上就比较难做到全覆盖。
那替代方案就是每个小组安排一个专门的联络人员呗,再定期开沟通会。
我想说的是,现场工作环境千变万化,有时候计划赶不上变化快。
就像天气突然变坏影响工作一样,你就得有些临时的应变方案。
比如说材料堆放,如果快要下雨了,要有个快速遮盖的方案。
我感觉要在日常工作里就养成观察环境和考虑突发情况的习惯,这样才能在问题出现时不至于手忙脚乱。
我现在也还在摸索学习,这些经验只是我自己的一些拙见。
大家要是有其他好的想法或者资源,也欢迎分享。
对了,有一本书叫《现场管理的改善》,我觉得挺不错的,有空可以看看,里面一些工业现场的案例感觉能给我们现场工作改进不少启发呢。
现场管理不足及改进措施

现场管理不足及改进措施一、现场管理不足及改进措施在当今社会,随着企业规模的不断扩大和市场竞争的日益激烈,现场管理的重要性日益凸显。
许多企业在实际操作中,现场管理往往存在诸多不足之处,这些问题不仅影响了企业的生产效率,还可能导致安全事故的发生。
因此,针对现场管理中的不足,采取有效措施进行改进,对于提高企业的整体竞争力具有重要意义。
本文将从以下几个方面对现场管理的不足进行分析,并提出相应的改进措施。
1.1 现场管理的目标不明确许多企业在实施现场管理时,往往没有明确的管理目标,导致管理过程中缺乏方向性。
为了解决这一问题,企业应该明确现场管理的目标,将其与企业的整体战略相结合,确保现场管理与企业的发展目标保持一致。
企业还应制定具体的管理目标,如提高生产效率、降低成本、保证产品质量等,以便在实际操作中有所依据。
1.2 现场管理的组织结构不合理现场管理的组织结构对于企业的管理效果至关重要。
如果组织结构不合理,可能会导致管理层级过低,信息传递不畅;或者组织结构过高,导致决策迟缓,影响企业的执行力。
因此,企业应根据自身的实际情况,合理设计现场管理的组织结构,确保各级管理人员能够有效地协同工作,提高管理效果。
1.3 现场管理的制度不健全现场管理制度是规范企业管理行为的重要手段。
许多企业在实际操作中,现场管理制度往往不健全,导致管理过程中出现混乱。
为了解决这一问题,企业应建立健全现场管理制度,明确各项管理规定和操作流程,确保员工在实际工作中有章可循。
企业还应定期对现场管理制度进行审查和更新,以适应企业发展的需要。
二、现场管理的改进措施针对上述现场管理中的不足,企业可以采取以下措施进行改进:2.1 加强现场管理培训企业应加强对员工的现场管理培训,提高员工的管理意识和能力。
培训内容应包括现场管理的基本理论、方法和技巧,以及企业的具体管理要求和标准。
通过培训,使员工充分认识到现场管理的重要性,增强他们参与现场管理的积极性。
现场管理不足及改进措施

现场管理不足及改进措施一、现场管理不足及改进措施在现代社会中,现场管理是企业生产和经营活动中不可或缺的一部分。
许多企业在现场管理方面存在诸多不足,这些问题不仅影响了企业的生产效率,还可能导致安全事故的发生。
本文将从现场管理的角度,分析当前企业在现场管理方面存在的问题,并提出相应的改进措施。
我们来看一下现场管理中存在的一些问题。
在许多企业中,现场管理往往被忽视,导致生产过程中出现了许多不规范的现象。
例如,生产线上的工人在操作机器时,不按照规定的操作流程进行,这不仅会影响生产效率,还可能导致设备损坏或者发生安全事故。
现场的环境卫生也是一个令人关注的问题。
有些企业的生产现场脏乱差,不仅影响了员工的工作环境,还可能对产品质量产生不良影响。
针对以上问题,我们需要采取一系列的改进措施。
加强现场管理的意识。
企业应该认识到现场管理对于提高生产效率和保障生产安全的重要性,将现场管理纳入企业的日常管理工作中。
企业可以通过定期组织现场管理培训,提高员工的现场管理意识和能力。
企业还可以设立专门的现场管理部门,负责现场管理工作的组织实施。
完善现场管理制度。
企业应该根据自身的生产特点和管理要求,制定一套完善的现场管理制度。
这套制度应该包括生产操作规程、设备维护保养规定、环境卫生管理规定等内容。
企业还应该定期对现场管理制度进行检查和修订,确保其与企业的实际情况相适应。
加强现场管理人员的培训和考核。
企业应该定期对现场管理人员进行培训,提高他们的专业素质和管理能力。
企业还应该建立一套有效的考核机制,对现场管理人员的工作进行考核,以激励他们更好地履行职责。
加大现场管理的投入。
企业应该加大对现场管理的投入,提供足够的人力、物力和财力支持。
例如,企业可以引进先进的现场管理设备和技术,提高现场管理水平;还可以加强对现场管理人员的奖励和处罚,激发他们的工作积极性。
现场管理是企业生产和经营活动的重要组成部分。
只有加强现场管理,才能提高企业的生产效率,降低生产成本,保障生产安全。
现场工作改进计划和建议

现场工作改进计划和建议《现场工作改进计划和建议》咱就说啊,在咱这个工作现场,那真是有不少事儿能说道说道呢。
就拿上次那个项目来说吧,那可真是让我把现场的问题看得透透的。
我记得那是个大夏天,热得人就像在蒸笼里似的。
我们在一个户外的场地搞活动搭建,现场那叫一个混乱啊。
各种工具、材料堆得到处都是,就像刚被龙卷风席卷过一样。
我一到现场,差点被横在地上的一根钢管绊倒,“哎呀妈呀”,当时我心里就想,这可不行啊。
首先呢,这物料的摆放得好好整整。
你看那些个工具啊,大锤子小钉子的,还有那些木板啥的,全都混在一起。
工人师傅们每次找个东西都得翻半天,就像在寻宝似的,嘴里还嘟囔着“这玩意儿放哪儿去了呢”。
我就想啊,咱能不能专门划出几个区域来呢?比如说,这边是工具区,锤子、钉子、螺丝刀啥的,按照大小或者使用频率摆放得整整齐齐的。
那边呢,是材料区,木板按尺寸堆好,钢管也码得规规矩矩的。
这样的话,工人师傅们拿东西多方便啊,就跟去超市拿东西一样,一目了然。
再说说这人员的分工吧。
当时现场啊,就像一锅乱炖,大家都在忙,可又不知道谁具体负责啥。
我看到有个哥们儿,本来是负责搭架子的,结果跑去帮着抬木板了,然后搭架子那边人手不够,进度就慢下来了。
咱得像下棋似的,把每个棋子都放在该放的地方。
在项目开始之前,就得把每个人的任务清清楚楚地列出来,谁负责啥,谁和谁配合,都得明明白白的。
这样大家就不会像没头的苍蝇一样乱转了。
还有哦,现场的安全问题可不能马虎。
那天啊,我看到有个工人师傅在高处作业,可是他的安全带系得那叫一个敷衍啊。
就随便在腰上绕了一圈,那要是不小心掉下来,可就不是闹着玩的了。
咱们得安排专门的人来检查安全设备的使用情况,像安全带啊、安全帽啊,都得仔仔细细地检查。
而且呢,在现场多设置几个安全警示标识,大大的那种,写着“注意安全”“此处危险”啥的。
让大家时时刻刻都能看到,心里就有根弦儿绷着。
另外呢,现场的沟通也很重要。
当时我就发现,很多时候因为沟通不畅,导致工作重复做或者做错了。
- 1、下载文档前请自行甄别文档内容的完整性,平台不提供额外的编辑、内容补充、找答案等附加服务。
- 2、"仅部分预览"的文档,不可在线预览部分如存在完整性等问题,可反馈申请退款(可完整预览的文档不适用该条件!)。
- 3、如文档侵犯您的权益,请联系客服反馈,我们会尽快为您处理(人工客服工作时间:9:00-18:30)。
这只是基于目前的现状所测得的数据,其实一线操作人员的操
优点: 极大的提高员工的工作效率,减少人员配置: 目前的现状洗坯的员工需要40人工作10H才能完成当天2.5W精
坯的目标,现在38人在8H 就能完成。如果将工作时间提高到目前的10H,有效嫁动时间为9.5H
: 修坯体的人员6组即18人就可完成当日产量目标,节约3人; 洗坯的人员由17人减少为14人,节约3人; 综上所述:一共节约6人。这只是基于现状的数据所计算出来,
备折旧)故在采取制程验证改善前五项不良的基础之上,在精坯导入 全检的方式,将不良品
尽可能多的拦截下来,该返修的返修,该送原料车间的送入原料车间 走FA流程,以提高后段
2、流水线的初步评估
其实最有效的工作流程优化是导入流水线作业,故也初步进行了流水 线导入的评估。
1、两条线实际嫁动时间9.5H;两条线最低产能=2*13200=26400;(跑顺后正常产能为27470+) 2、两条线人力需求:24*2=46人;以上岗位车间现有人力56人,节省10人,多余的人力可以进行产线轮
泸州得天陶瓷有 限公司
Luzhou Detian Ceramics Co., Ltd
何志 2016.6.2
7
尊敬的刘总、李总并各位领导: 本人加入得天陶瓷已一个多月的时间。期间耗时半个月对
公司所有车间的生产流程有了一个初步的熟悉,对于公司的工艺流程 及生产管理现状已经有了一个初步的认识。后定职于整个公司最重要 也是最关键的成型车间,在此期间发现了一系列急需改善的问题点。 根据本人以前的工作经验,拟定了部分的改善思路与几点建议。由于 本人以前未接触过陶瓷行业,肯定存在诸多认识不到位之处,还望各 位领导指教。 以上
洗坯
19.9 15.9 27.2 13.7 25.8 16.2 18 15.5 16.1 19.5 18.78 18.78 192
由以上数据可知:
洗坯的标准产能为192个/H,若每日工作7.5H,则全天产能为 192*7.5=1440个。
若需完成25000以上产能,则需要17人。
以上排拉修坯人员总数需求为17+21=38人平均上班8H可完成每 日25000的产能目标。
4、可考虑增设IPQC的岗位,便于进行制程巡检管控,有利于质量的提升。
5、导入流水线可考虑增加气枪吹瓶口的动作,消除瓶底/瓶颈内泥渣(此项已验证可行,可将除多余粘接料外 的所有注浆、粘接掉入的泥渣清除干净)
6、流水线导入可在线尾部增加自动气枪,专门吹除瓶口外部泥渣,效果较好(此项已验证可行,能有效吹除瓶 口外部残余泥渣)
增加IPQC起到过程监督 的作用 厂房改造以降低车间温 员度-工-留正住人激员励机制重新修 订
第一ห้องสมุดไป่ตู้分、成型车间工作改善
一、精益生产推行
1、洗坯工作流程优化 目前整个成型车间全部是分站式作业,比如洗坯的员工,同 一车产品要做四道工序: 修坯体--->磨瓶颈--->洗瓶口、量尺寸,再将已喷釉的产品拉 来进行洗坯。整个流程全 部由一个作业员完成。在不停的从坯架车上取放造成动作浪费。故考 虑将该工序人员重新排 拉组合,以流水方式完成这三道工序,最大程度的减少搬运的距离、 频繁的动作浪费。且让 员工的操作越来越简单,有助于工作效率的提升。
何志 2016.6.27
目录 :
第一部分、成型车间工 作改善
第二部分、公司层面建 议事项
精益生产推行—洗坯流程优化、
流水线导入、 精坯检验导入全检
实行班长巡检工作流程
全制程验证改善不良
车间目视化改善-6S与看板管
理
员工培训改善
技术部增加当站PE--工艺
工程师/技术员
增加每日生产例会-各部门提
高工作效率
以导入,否则员工意见会较大。 3、洗坯处需重新设计水管布线方式,工程量较大,需工程部门评估。
2、缩短成型车间产品生产周期1天左右。(现阶段产品生产周期基本在3天左右,改善后生产周期基本在2天左 右)
3、所有装满产品的坯架车只有4个状态,粘接后待修坯、修坯后待烘烤、烘烤后待投流水线、精坯待转素烧窑。 便于进行区域规划,利于成型车间的6S改善。
3、精坯检验重新排拉布线(导入全检)
从品质部每日数据中选取一周的数据得知成瓷的良率仅 78.34%。个人认为主要的原因为
成型的检验采用抽检的方式,我觉得这是很不合理的。因为在进素烧 窑之前所有的报废品都
是可以走返工流程的,期间的成本损耗相对较少(仅有水电+人工成 本),但素烧成瓷后,所
有的产品只有倒入垃圾堆,变成实实在在的公司成本损失(水电气+ 人工+原料+窑炉等部分设
工序
第1次 第2次 第3次 第4次 第5次 第6次 第7次 第8次 第9次 第10次 T/T N/T 标准工时
修坯
7.6 6.4 7.5 5.9 7.6 9.1 7.2 8.9 6.5 6.9 7.36
磨瓶颈
5.1 5.6 5.3 5.5 8.6 6.3 5.5 5.9 6.3 5.3 5.94 7.36 489
休安排,保证员工休息时间充足。 3、以上排拉布线方法为现阶段的工作效率,随着员工工作熟练度的提升,产能只会越来越高。建议按此
方式进行排拉。 目前的问题点: 1、员工工资的计算方式变更,由于是流水线,无法较好的统计单人产量,建议按照团体完成的产量计算
工资。 2、员工的工资模拟,需拿出一定的数据进行模拟,然后与现在的工资进行对比,若工资更高或持平则可
随着员工动作的单一、效 率会提升得比较明显,后期所需的人力只会更少。 目前的困难点:
由于公司本工序采用的是计件方式,若导入可能工资的计算方式 会进行调整,由个人计
件变更为小组计件。对于各组员工速度的匹配度在管理上增加了一定 的难度。
这只是成本最低的方案,最优化的方案是导入流水线,将烘烤完 毕之后的所有工序导入流
洗瓶口,量尺寸 5.7 6.8 4.9 7.7 5.9 6.1 7.1 5.8 6.9 5.1 6.2
由以上数据可知: 瓶颈岗位为修坯,一组三人每小时标准产能为489个。 若每日工作7.5H,则全天产能为489*7.5=3667个。 若每日完成25000以上,则需要7组人力,共计21人。
工序
第1次 第2次 第3次 第4次 第5次 第6次 第7次 第8次 第9次 第10次 T/T N/T 标准工时