硫磺回收装置尾气处理技术比选
新标准下硫磺回收装置尾气排放处理技术探讨

现象 。减少 氨 的挥 发 ,防止 氨 随脱 硫 尾 气 逸 出 损失
2NH3+H2O+SO2_÷(NH4)2S03
是 氨法 脱硫 需要 解决 的问题 。
(NH4)2SO3+SO2+H20—}2NH4HSO3
1.4.2 气 溶 胶 风险 气 溶 胶 是指 以亚硫 酸 铵 、亚硫
NH4HSO3+NH3一 (NH4)2SO3
此 ,本 文探 讨 了几 种 可 用 于 尾 气 处 理 的工 艺 技 术 ,
(3)氨 法 脱 硫 在 锅 炉 烟 气 脱 硫 中得 到 广 泛 应
以满 足新 的标 准要 求 。
用 ,国 内氨 法 脱 硫 工 程 投 运 超 过 40项 J。在 硫 磺
1 氨 法脱 硫 工艺 1.1 氨 法脱硫 基本 原理
焚烧 炉焚 烧后 的烟 气经 烟 气 一净 化气 换 热 器 换
理 是 NaOH溶 液 与 烟 气 中 的 SO,接 触 后 反 应 生 成 热 降温后 进入 尾气脱 硫塔 (见 图 2)。在脱 硫塔 人 口 Na:S0。,Na SO3继续 与 S0:反 应 生 成 NaHSO3,在 整 设 置喷 嘴对烟 气急冷 降温 (~60 ̄C)。烟 气经 急冷 段
2018年第 18卷 第 4期
气体净化
·29 ·
新 标 准 下 硫 磺 回收 装 置 尾 气 排 放 处 理 技 术 探 讨
刘 帅 ,杨 彬 ,文增坤
(海 工英 派尔工程有限公 司,山东青岛 266100)
摘要 :针对硫磺 回收装 置尾气 s0 排放标准升级 ,本文介绍和分析 了氨法 ,钠碱 ,络合铁几种可用于 尾气处理的工艺技术 ,以满足新的标准要求 。
限值 为 50 me,/m 。 由此 可见 ,s0:控 制要 求 将 会 越 液结 晶干 燥工 产 出商 品硫酸 铵 。
硫磺回收装置尾气处理

:
。
。
其 总 反
10
后
3
,
全 厂 的 H S 排放 量将 逐 年 增 高
。
Z
S夕
量
.
:
S
+
=
25 +
在 克劳 斯催化 %
。
也 势必 增 加
到 了1
987
.
年
,
5 0
:
排 放量 增 加
3 66 魂
。
反应 器中
12 5
℃ 时 H 声转化 率接 近
,
。
倍多
,
1 9 9 0 年 将到 6
,
6 6倍 ,
.
硫收率 最高 也
处 理 技术 已 有 几 十种
以下三 类
1
. 。
,
按其原 理大 致 可 分 为
0 ~
9了 5
,
.
%
。
其 放空 尾 气中仍有
,
写的硫化 物 % 的硫以
,
即 相 当 于装置 处 理 量 的
:
低 温克劳 斯 反应 法
,
50
等 形 态排 入 大 气
。
损失
在低 于 硫 的露点 温 度 下
50
境 续表
2
保
护
,
2
9
为50
酸
、
2
,
然 后 分离 5 0
。
转化 为 元 素 硫
硫
、
.1Βιβλιοθήκη ’亚 硫 酸 盐 等 这 类 方 法基本 上 不 受 C O S
Z
Cs 以及 H s
Z
/ S
0 比 例 的限 制 也 能 达 到 很 高 的
硫回收尾气处理技术及超级克劳斯工艺
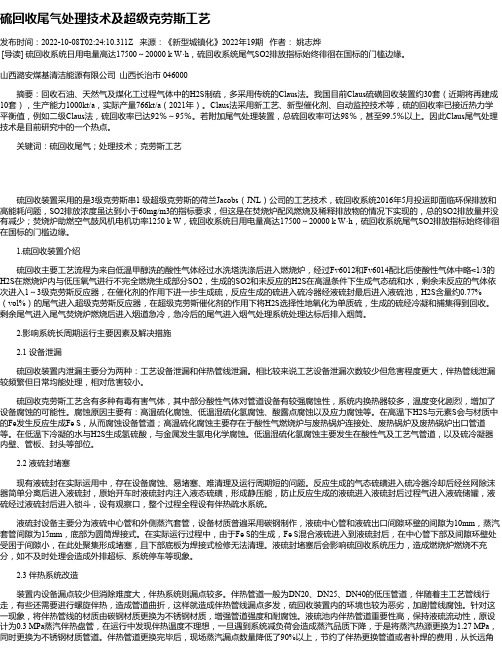
硫回收尾气处理技术及超级克劳斯工艺发布时间:2022-10-08T02:24:10.311Z 来源:《新型城镇化》2022年19期作者:姚志烨[导读] 硫回收系统日用电量高达17500~20000 k W·h,硫回收系统尾气SO2排放指标始终徘徊在国标的门槛边缘。
山西潞安煤基清洁能源有限公司山西长治市 046000摘要:回收石油、天然气及煤化工过程气体中的H2S制硫,多采用传统的Claus法。
我国目前Claus硫磺回收装置约30套(近期将再建成10套),生产能力1000kt/a,实际产量766kt/a(2021年)。
Claus法采用新工艺、新型催化剂、自动监控技术等,硫的回收率已接近热力学平衡值,例如二级Claus法,硫回收率已达92%~95%。
若附加尾气处理装置,总硫回收率可达98%,甚至99.5%以上。
因此Claus尾气处理技术是目前研究中的一个热点。
关键词:硫回收尾气;处理技术;克劳斯工艺硫回收装置采用的是3级克劳斯串1 级超级克劳斯的荷兰Jacobs(JNL)公司的工艺技术,硫回收系统2016年5月投运即面临环保排放和高能耗问题,SO2排放浓度虽达到小于60mg/m3的指标要求,但这是在焚烧炉配风燃烧及稀释排放物的情况下实现的,总的SO2排放量并没有减少;焚烧炉助燃空气鼓风机电机功率1250 k W,硫回收系统日用电量高达17500~20000 k W·h,硫回收系统尾气SO2排放指标始终徘徊在国标的门槛边缘。
1.硫回收装置介绍硫回收主要工艺流程为来自低温甲醇洗的酸性气体经过水洗塔洗涤后进入燃烧炉,经过Fv6012和Fv6014配比后使酸性气体中略<1/3的H2S在燃烧炉内与低压氧气进行不完全燃烧生成部分SO2,生成的SO2和未反应的H2S在高温条件下生成气态硫和水,剩余未反应的气体依次进入1~3级克劳斯反应器,在催化剂的作用下进一步生成硫,反应生成的硫进入硫冷器经液硫封最后进入液硫池,H2S含量约0.77%(vol%)的尾气进入超级克劳斯反应器,在超级克劳斯催化剂的作用下将H2S选择性地氧化为单质硫,生成的硫经冷凝和捕集得到回收。
硫磺回收装置尾气环保达标技术研究

硫磺回收装置尾气环保达标技术研究摘要:本文将从当前硫磺回收装置尾气排放的概况出发,阐述硫磺回收装置尾气环保达标的影响因素,对硫磺回收装置尾气环保达标的主要技术进行分析与探究,希望为相关人员提供一些帮助和建议,更好地解决硫磺回收装置尾气不达标问题,实现尾气环保达标排放。
关键词:尾气达标;回收装置;环保目标引言:伴随国内工业水平的不断提高,化工原料深加工、煤化工、开采天然气、原油加工等工业产业都得到了飞速发展,硫磺回收装置在我国的数量逐年增多,然而,部分硫磺回收装置在使用过程中出现了尾气排放不达标的问题,无法满足环境保护的要求。
因此,研究硫磺回收装置尾气环保达标技术具有一定现实意义。
一、当前硫磺回收装置尾气排放的概况硫燃烧炉的反应类型为高温放热反应,二氧化硫在高温下会有三分之一发生转化。
一般来讲,燃烧炉达到1100摄氏度至1400摄氏度时,硫化氢转化成单质硫的比率可高达百分之七十,且转化比例伴随工业水平的提升和转化装置的更新换代而逐渐提升,同时硫磺回收装置尾气也能得到更好的转化。
目前,我国回收技术取得了长足的发展,在实际应用中效果颇丰,大大提高了转化率。
从工作原理上看,硫磺回收装置主要通过汽提来处理污水,处理过程中,酸性气体会投放到高温燃烧炉中用于促进溶剂的再生,随后调节配风量,使酸性气体得到完全燃烧,按照特定配比,三分之二成分的二氧化硫、硫化氢会进行理想转化,另外三分之一为酸性气体,在完全燃烧后也将转化为二氧化硫,这样一来,硫磺回收装置转化尾气二氧化硫的整体效率就会更高。
二、硫磺回收装置尾气环保达标技术(一)硫磺回收装置尾气环保达标的影响因素1.配风比的影响对于硫磺回收装置尾气环保达标来讲,配风比是最直接的影响因素,同时也是合理控制和操作硫磺回收装置的重点,硫磺回收装置的工艺操作、技术控制都离不开配风比控制。
由于控制配风比存在较大难度,因此,二氧化硫物很难达到二级物质量比,从而在未产生反应的状况下与气体一同进入焚烧炉和吸收塔。
硫磺回收中的尾气处理技术

硫磺回收中的尾气处理技术摘要:SO2 是严重的环境污染物,我国实施的环保标准《大气污染物综合排放标准》中严格规定了SO2 的排放浓度和排放总量,要求硫磺回收装置的总硫回收率不断提高,也推动着尾气处理技术不断发展。
关键词:硫磺回收;尾气处理;SCOT 工艺1 概述硫磺回收是一项将含H2S 等有毒含硫气体中的硫化物转变为单质硫,从而变废为宝,保护环境的化工工程。
通常采用克劳斯工艺来实现。
回收原理为:H2S+1.5O2=SO2+H2O+518.9kJ/molH2S+0.5SO2=0.75S2+H2O-4.75kJ/molH2S+0.5SO2=1.5n·Sn+H2O+48.05kJ/mol一般硫磺回收率可达95~98%。
如果需要进一步提高硫磺回收率,则需在硫磺回收装置后附加尾气处理装置。
2 硫磺回收工艺技术2.1 工艺技术含H2S 酸性气体的处理,工业生产中多采用固定床催化氧化工艺、液相直接氧化工艺和生物脱硫及硫回收工艺。
2.1.1 固定床催化氧化工艺代表性的工艺是Claus 工艺。
常规Claus 工艺的特点是流程简单、设备少、占地面积小、投资省、回收硫磺纯度高。
在常规的Claus 硫磺回收工艺基础上又发展为多种工艺,主要有:SCOT 工艺、Super-Claus 工艺、CLINSULF 工艺、MCRC 工艺等。
2.1.2 液相直接氧化工艺有代表性的液相直接氧化工艺主要有:ADA法和改良ADA法脱硫、栲胶法脱硫、氨水液相催化法脱硫等。
液相直接氧化工艺适用于硫磺的“粗脱”,如果要求高的硫回收率和达到排放标准的尾气,宜采用固定床催化氧化工艺或生物法硫回收工艺。
2.1.3 生物脱硫及硫回收工艺有代表性的工艺是Shell-Paques 工艺。
该工艺具有流程简单,操作弹性大,占地面积小,安全可靠等特点,对于低浓度低总硫的装置,由于其一次投入、操作成本和能耗都比较低,不失为一种非常好的选择。
2.2 选择工艺技术的原则硫磺回收装置作为大型化工生产装置的环保治理装置,在选择工艺技术时必须考虑:(1)采用该技术处理后的气体完全满足国家和地方相应排放标准;(2)装置运行必须可靠(包括稳定性、可操作性、安全性);(3)装置投资、运行综合费用低。
炼厂硫磺回收装置尾气处理技术分析

炼厂硫磺回收装置尾气处理技术分析摘要:随着工业化进程的不断推进,炼厂所产生的硫磺尾气成为了严重的环境污染源。
为了解决这一问题,炼厂硫磺回收装置尾气处理技术应运而生。
本文以炼厂硫磺回收装置尾气处理技术为研究对象,对其进行了全面的分析和探讨。
一是介绍了硫磺回收装置的工作原理和组成部分,然后分析了尾气处理技术的发展现状和存在的问题,最后提出了进一步研究和改进的方向。
通过本文的研究,可以为炼厂硫磺回收装置尾气处理技术的发展和应用提供一定的参考和借鉴。
关键词:炼厂;硫磺回收装置;尾气处理技术;环境污染引言:随着我国工业化进程的不断推进,社会经济得到了飞速发展。
同时,人们对环境保护意识的增强,对生产过程中产生的尾气进行妥善处理已成为必然趋势。
但是,我国对尾气处理技术的研究起步较晚,在实际应用中存在着诸多问题。
为了解决这一问题,炼厂硫磺回收装置尾气处理技术应运而生。
随着炼厂硫磺回收装置的不断完善和发展,其尾气处理技术也得到了较大程度的改进和优化。
一、硫磺回收装置的工作原理和组成部分1.1硫磺回收装置的概述随着工业化进程的不断推进,硫磺回收装置也在不断地发展和进步,尤其是随着新技术的不断出现,硫磺回收装置也在朝着高效率、高质量以及低消耗的方向发展。
目前,炼厂硫磺回收装置的种类和结构越来越多样化,这主要是因为不同类型的硫磺回收装置具有不同的特点和优势。
常见的硫磺回收装置主要包括四大类:第一,吸收法;第二,催化燃烧法;第三,还原法;第四,加氢处理法。
从结构上来看,这四种类型的硫磺回收装置都是由两个部分构成的,分别是吸收和催化燃烧系统。
其中,吸收部分主要是由吸收塔、再生塔、脱硫塔和水洗塔组成。
催化燃烧部分则主要由燃烧系统和催化燃烧系统两大部分组成。
从工作原理上来看,硫磺回收装置主要是将炼油厂中所产生的硫黄经过吸收、净化和燃烧等过程之后转化成液体硫磺或固体硫磺。
这也是炼厂硫磺回收装置尾气处理技术中最为核心和关键的一环。
硫磺回收装置尾气处理工艺探讨
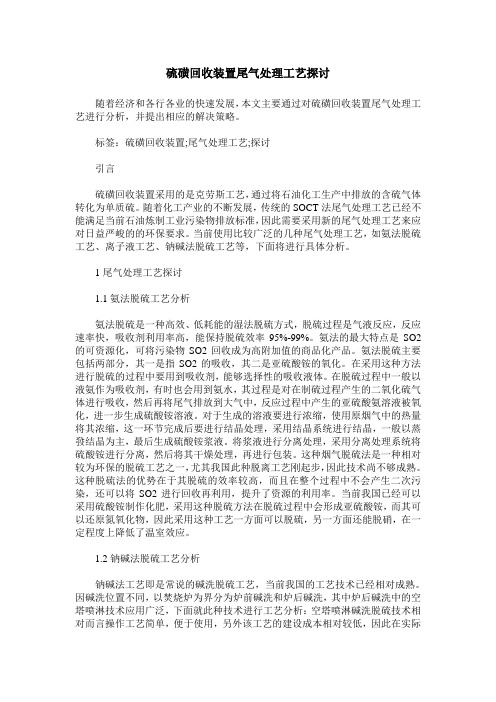
硫磺回收装置尾气处理工艺探讨随着经济和各行各业的快速发展,本文主要通过对硫磺回收装置尾气处理工艺进行分析,并提出相应的解决策略。
标签:硫磺回收装置;尾气处理工艺;探讨引言硫磺回收装置采用的是克劳斯工艺,通过将石油化工生产中排放的含硫气体转化为单质硫。
随着化工产业的不断发展,传统的SOCT法尾气处理工艺已经不能满足当前石油炼制工业污染物排放标准,因此需要采用新的尾气处理工艺来应对日益严峻的的环保要求。
当前使用比较广泛的几种尾气处理工艺,如氨法脱硫工艺、离子液工艺、钠碱法脱硫工艺等,下面将进行具体分析。
1尾气处理工艺探讨1.1氨法脱硫工艺分析氨法脱硫是一种高效、低耗能的湿法脱硫方式,脱硫过程是气液反应,反应速率快,吸收剂利用率高,能保持脱硫效率95%-99%。
氨法的最大特点是SO2的可资源化,可将污染物SO2回收成为高附加值的商品化产品。
氨法脱硫主要包括两部分,其一是指SO2的吸收,其二是亚硫酸铵的氧化。
在采用这种方法进行脱硫的过程中要用到吸收剂,能够选择性的吸收液体。
在脱硫过程中一般以液氨作为吸收剂,有时也会用到氨水,其过程是对在制硫过程产生的二氧化硫气体进行吸收,然后再将尾气排放到大气中,反应过程中产生的亚硫酸氨溶液被氧化,进一步生成硫酸铵溶液。
对于生成的溶液要进行浓缩,使用原烟气中的热量将其浓缩,这一环节完成后要进行结晶处理,采用结晶系统进行结晶,一般以蒸發结晶为主,最后生成硫酸铵浆液。
将浆液进行分离处理,采用分离处理系统将硫酸铵进行分离,然后将其干燥处理,再进行包装。
这种烟气脱硫法是一种相对较为环保的脱硫工艺之一,尤其我国此种脱离工艺刚起步,因此技术尚不够成熟。
这种脱硫法的优势在于其脱硫的效率较高,而且在整个过程中不会产生二次污染,还可以将SO2进行回收再利用,提升了资源的利用率。
当前我国已经可以采用硫酸铵制作化肥,采用这种脱硫方法在脱硫过程中会形成亚硫酸铵,而其可以还原氮氧化物,因此采用这种工艺一方面可以脱硫,另一方面还能脱硝,在一定程度上降低了温室效应。
硫磺回收烟气超低排放工艺技术比较

46能源环保与安全笔者参与了镇海炼化分公司目15万吨/年钠法脱硫硫磺回收装置、中科3×13万吨/年氨法脱硫硫磺回收装置、茂名石化15万吨/年SO2回收硫磺回收联合装置的设计工作,对钠法脱硫、氨法脱硫、SO2回收工艺的有一定的了解,情况介绍如下:一、尾气达标的必要性2015年4月16日颁布的《石油炼制工业污染物排放标准》GB31570-2015要求环境敏感地区新建硫磺回收装置的烟气中SO2排放浓度执行≯100mg/Nm3的特别排放限值。
《燃煤电厂超低排放烟气治理工程技术规范》HJ2053-2018中规定在基准氧含量6%条件下,燃煤电厂标态干烟气中颗粒物、SO2、NOX排放质量浓度分别不高于10mg/m3、35mg/m3、50mg/m3。
目前,常规采用二级Claus+加氢还原吸收焚烧的硫磺回收装置很难长期、稳定维持在SO2排放浓度≯100mg/Nm3。
因此,需要对硫磺回收工艺进行改进,满足环保排放指标要求。
二、硫磺回收装置不同净化工艺概述普通二级Claus过程总硫回收率一般在95%左右,需要增加尾气净化工艺,以满足硫磺回收尾气达标排放的要求。
1.二级Claus工艺简介酸性气进入主烧嘴内进行燃烧反应,生成的过程气发生4.0MPa蒸汽后进入第一硫冷凝器发0.3MPa蒸汽后分离硫磺。
分离硫磺后的过程气进入第一再热器加热后进入一级Claus反应器,反应后的过程气进入第二硫冷凝器发0.3MPa蒸汽后分离硫磺。
分离硫磺后的过程气进入第二再热器加热后进入二级Claus反应器,反应后的过程气进入第三硫冷凝器发0.3MPa蒸汽后分离硫磺,分离硫磺后的过程气至尾气净化单元。
Claus工艺简图见图2.1。
图2.1 Claus工艺简图2.加氢还原吸收焚烧工艺简介目前硫磺回收的尾气净化工艺普遍采用加氢还原吸收焚烧工艺。
自Claus单元经分离硫磺后的尾气经过再热和加入还原气体后进入加氢还原反应器,尾气中的各种硫化物水解、加氢还原为H2S,加氢尾气进入蒸汽发生器回收热量后进入急冷塔冷却,急冷后尾气进入吸收塔,尾气中的H2S被溶剂吸收。
硫磺回收装置液硫池废气回收处理技术应用

一、前言某石化公司4万吨/年硫磺回收装置于2012年10月30日建成投产。
该装置由山东三维设计院设计,由制硫、尾气处理、液硫脱气、尾气焚烧及液硫成型5部分组成,尾气处理与制硫部分相配套。
其中制硫部分采用部分氧化还原的Claus 制硫工艺,尾气处理采用SSR工艺。
酸性气主要来源于干气脱硫溶剂再生装置及污水汽提装置,酸性气中H2S体积分数为55%~65%。
通过控制合适的燃烧炉配风比、优化尾气吸收塔操作、对尾气吸收脱硫剂进行专供专用等措施,将尾气SO2质量浓度降至130-180 mg/m3左右,实现了达标排放。
随着环保要求日益严格,为进一步节能减排,对液硫池废气回收处理部分进行了改造。
二、工艺现状介绍自一、二、三级硫冷凝器冷凝的液硫随重力自流汇集液硫池,H2S溶解于液硫时不仅有物理溶解,还会生成多硫化氢(H2Sx,x通常为2~8),反应式如下:H2S+(x-1)S→H2Sx。
当温度升高,化学平衡向右移动,多硫化氢的溶解度随温度升高迅速增加。
虽然H2S在液硫中溶解度随温度升高略有下降,但H2S和H2Sx的总溶解量仍随温度升高而增加。
溶解在液硫中的H2S会对硫磺储存、成型和运输等过程造成设备腐蚀、人员中毒、发生爆炸等危害。
为了保证安全的加工或运输,必须先脱除液硫中溶解的H2S,使其浓度降低到10μg/g以内。
三、液流废气处理工艺该硫磺回收装置采用液硫循环机械搅动式脱气工艺,液硫池外部设液硫循环泵,介质通过循环泵输送至液硫冷却器,液硫与低温除氧水换热,温度降至约138℃后进入液硫池内部脱气区。
分别在液硫池脱气Ⅰ区、Ⅱ区设置2组液硫蒸汽喷射器,脱气区内液硫处于搅动状态,通过机械搅动达到脱气的目的。
该脱气工艺液硫池内硫蒸气量大,出现硫雾夹杂于H2S气体通过蒸汽喷射器进入尾气焚烧炉焚烧处理,硫元素全部转化为SO2随尾气排放至大气,主要工艺流程见图1。
该工艺主要问题在于液硫池废气被蒸汽喷射器送至尾气焚烧炉焚烧,会增加烟道气中SO2排放浓度。
硫磺回收装置尾气S02超低排放技术改造措施

硫磺回收装置尾气 S02超低排放技术改造措施在炼油厂中,用于硫磺回收的主要装置就是硫磺回收装置,在石化企业中也是较为环保的一种的装置。
硫磺尾气产量也是银川集团公司和环保局的主要监管对象之一。
硫磺回收装置自2013年开工以来,由于上游装置酸气量和酸气中H2S含量波动较大,硫磺炉送风调整滞后,尾气管脱硫效果不佳,含硫气体排放量较高(500mg/m3~700mg/m3),波动频繁,有时超标。
为降低尾气SO2排放浓度,减少含硫尾气振荡超标次数。
1技术改造前装置存在的主要问题(1)硫磺装置的进料为清洁酸性气和含氨酸性气,其中清洁酸性气来源于溶剂再生装置,溶剂再生装置溶剂供全厂相关装置使用,循环量90t/h,供催化、柴加、汽加等上游装置的干气和氢气的硫化氢脱除,上游装置干气中CO2含量较高,特别是催化装置干气CO2含量达5.2%(体积分数),溶剂系统使用的溶剂为星光宝亿公司生产的XG-04脱硫溶剂,主要成分MDEA,此溶剂的选择性较差,在吸收H2S的同时,CO2的共吸率高达80%。
大量的CO2吸入溶剂后,经溶剂再生装置汽提后通过清洁酸性气进入硫磺装置,在制硫炉焚烧过程中,生成羰基硫,经两级制硫反应器和加氢反应器后部分羰基硫无法水解为H2S,无法通过尾气吸收塔和超重力装置吸收处理,有机硫在硫磺尾气SO2排放中的贡献率达到60%以上,造成尾气SO2偏高。
(2)尾气吸收塔和硫磺超重力系统与全厂溶剂系统共用溶剂,此溶剂选择性相对较差,且因上游装置来富溶剂易带油及其他杂质,对溶剂造成污染,长期运行过程中溶剂品质逐渐变差。
硫磺超重力系统尾气进气H2S含量低,系统压力15~20kPa,在超重力系统低压力运行环境下,溶剂对低浓度H2S的吸收明显变差,因此全厂溶剂系统提供的溶剂无法满足硫磺尾气超低排放的需求。
2主要技术改造措施2.1增设先进控制系统根据硫生产中的闭合反应原理,由于硫化氢与二氧化硫的摩尔比为2:1,所以元素硫的转化率最高的是生产。
第四章 硫磺回收及尾气处理
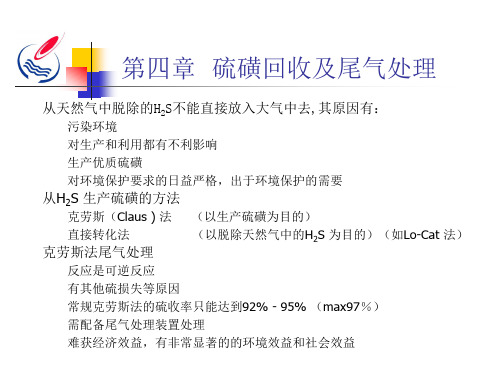
1.直流法 ①反应炉内H2S转化率一般可达 60%~70%; ②原料气中的H2S含量应大于50%。 其原因是应保证酸气与空气燃烧的反
应热足以维持反应炉内温度不低于
980℃ ; ③设置了三级或四级催化反应器, 其主要目的是:a.由转化器出来的过
2. 各国从自身国情出发,其标准差别很大。例如,加拿大因地广人稀故其标准
较美国要宽,而日本由于是人口密集岛国,故其标准最严; 3. 随着经济发展和环保意识的增强,这些国家所要求的硫收率也在不断提高。 (二)我国标准 我国在1997年执行的GB16297—1996《大气污染物综合排放标准》中对SO2 的排放不仅有严格的总量控制(即最高允许排放速率),而且同时有非常严格的 SO2排放浓度控制(即最高允许排放浓度),见表4-2。
程气温度应高于其硫露点温度,以防
液硫凝结在催化剂上而使之失去活性; b较低的温度可获得较高的转化率。
2.分流法
当H2S含量15~30%时,用直流法难以使反应炉内燃烧稳定,应用分流法。
常规分流法的特点是将原料气(酸气)分为两股,其中1/3原料气与按照化学计 量配给的空气进入反应炉内,使原料气中H2S及全部烃类、硫醇燃烧,H2S按反应 (4-2)生成SO2,然后与剩余原料气混合进入催化转化段。因此,常规分流法中生 成的元素硫完全是在催化反应段中获得的。 当原料气H2S含量在30~55%,采用直流法则反应炉内火焰难以稳定,采用常 规分流法将1/3的H2S燃烧生成SO2时,炉温又过高使炉壁耐火材料难以适应。可 采用非常规分流法,即将进入反应炉的原料气量提高至1/3以上来控制炉温。以 后的工艺流程则与直流法相同。
(4-2)
(4-3)
(4-4)
=
(二)克劳斯法平衡转化率Kp 以反应(4-3)为例,该反应是可逆反应,低压下此气相反应的平衡常数Kp 可表示为:
新标准下硫磺回收装置尾气排放处理技术探讨

新标准下硫磺回收装置尾气排放处理技术探讨发布时间:2022-10-17T08:48:44.035Z 来源:《科技新时代》2022年4月8期作者:张永福[导读] 随着时代的进步发展,在社会经济稳步提升的同时,张永福陕西神木化学工业有限公司陕西神木 719319摘要:随着时代的进步发展,在社会经济稳步提升的同时,工业污染问题也日益加重。
在这样的背景下,国家针对炼制工业污染排放出台了新的标准,其中对硫磺装置尾气的排放处理提出了新的要求。
为强化硫磺回收装置尾气排放处理的效果,本文通过文献法和经验法,对二氧化硫的排放回收展开了研究,首先分析了目前较为常见的尾气排放处理技术,然后分析了影响二氧化硫排放的因素,最后提出了尾气排放处理的优化措施,以供参考。
关键词:硫磺回收装置;尾气排放;处理引言:当今社会可持续发展理念深入人心,国家越来越重视环境保护,人们的环保意识也在不断增强,希望能够生活中健康干净的环境中。
为此国家制定了《石油炼制工业污染排放标准》,对二氧化硫的排放进行了规定,要求控制在400mg/m3。
基于此相关企业应该注重多硫磺回收装置的创新,深入分析当前的尾气排放处理技术,对其进行优化,保证二氧化硫的排放能够达到相关标准,为环境保护做出贡献,推动炼制工业的可持续发展。
一、新标准下硫磺回收装置尾气排放处理技术(一)碱法洗涤脱硫技术在化学中,去除二氧化硫的试剂有很多。
由于二氧化硫具有一定的酸性,因此常见的脱硫方式为碱法脱硫,主要应用的试剂为氢氧化钠,俗称钠碱法脱硫[1]。
主要原理为让二氧化硫气体融入到氢氧化钠溶液中,让二者发生反应,形成新物质亚硫酸钠,此时反应没有结束,亚硫酸钠也会和二氧化硫气体进行反应,生成亚硫酸氢钠。
在整个脱硫的过程中,氢氧化钠起到的是吸收剂的作用,在反应之前需要先和水反应进行分解,形成钠离子和氢氧根离子。
亚硫酸钠进行吸收,与氧气发生反应,从而实现脱硫。
具体的工艺流程如下:二氧化硫通过焚烧炉进入到净化器中,在经过降温处理后,二氧化硫气体进入到硫磺回收装置中。
硫磺回收装置尾气净化系统高效脱硫剂招标技术要求

硫磺回收装置尾气净化系统高效脱硫剂
招标技术要求
投标人必须承诺投标的高效脱硫剂满足招标人各使用企业装置的操作条件,以中标方与招标人使用企业签订的技术协议为准。
3.性能保证
在装置正常运行条件下,包括:原料性质、流量稳定,操作压力、温度等参数符合工艺要求,设备运行正常,投标人提供的高效脱硫剂应满足下列要求:
⑴净化尾气H2S含量<20mg∕Nm3;(如有更高要求,由甲乙双方根据具体情况另签补充协议约束);
⑵再生性能好,再生后贫液的H2S+CO2含量≤0∙5g/1;
⑶具有较好的脱硫选择性,降低CO?的共吸率;
⑷使用浓度高,可配置35%〜45%的水溶液;
⑸稳定性好,不易降解;
⑹保证系统内不会因脱硫剂产品质量造成胺液发泡问题;
⑺对装置无腐蚀;
⑻硫磺回收装置排放尾气二氧化硫含量以中标方与招标人使用企业签订的技术协议为准;
⑼使用寿命为3年以上;
⑩单耗小于O.15kg∕t净化尾气;
四、消泡剂用量
投标人根据招标人各使用企业装置规模以及运行周期用量,免费提供一周期对应的消泡剂(消泡剂数量在报价书中必须明确),消泡剂的报价包含在高效脱硫剂报价内,并包含提供消泡剂的投加指导服务费用。
投标人提供的高效脱硫溶剂需避免溶剂发泡。
若因溶剂发泡引起质量下降,投标人负责提供消泡剂以确保脱硫效果,消泡剂的数量不限于投标人报价书内填报的数量。
高含硫天然气硫磺回收及尾气处理工艺技术

高含硫天然气硫磺回收及尾气处理工艺技术摘要:我国的四川储藏着丰富的高含硫天然气,高含硫天然气的开发必须要配套建设大型的天然气净化厂,高含硫天然气中硫化氢以及二氧化硫的含硫都比较高,一些情况下甚至能达到10%左右,产硫量也比较高。
在我国环保要求不断提升的前提下,高含硫天然气气田必须要实现99.7%以上的硫回收才能最终达到尾气排放标准要求,因此对整个处理过程中硫磺回收以及尾气处理工艺设计提出更高要求。
本文主要针对目前国内外大型硫磺回收和尾气处理技术的发展状况进行了分析,以现场生产实践为基本出发点,对硫磺回收和尾气处理工艺流程的简化、操作稳定性等进行了探讨;关键词:高含硫天然气;硫磺回收;尾气处理;优化引言高含硫天然气在处理过程中如果不经过硫的有效回收,不仅会导致出现大量的资源浪费,而且也会对环境造成严重污染,因此,在当今绿色环保生产不断深化的前提下,整个天然气生产处理领域中硫磺回收和尾气处理工艺都得到了高度重视。
1 硫磺回收及尾气处理技术发展现状Claus制硫技术目前已经经过了100多年的发展历史,是当前整个化工处理领域中最为成熟的一种含硫酸气处理工艺。
三级 Claus硫收率由于会受到各种化学反应平衡的限制,导致其实际的收率仅仅能够达到97%。
鉴于此,国内外已经针对 Claus制硫技术开展了大量的研究,进一步开发出了多种尾气处理工艺,以此来有效提升硫收率。
1.1富氧 Claus技术该技术最早是应用在硫回收装置方面,其主要的应用目的是进一步扩大企业的产能。
例如,充分利用50%的富氧空气,在整个工艺处理过程中单位体积氧气消耗仅仅会代入等量的氮气,能够将过程气量进行明显的控制,也能够有效减少工艺处理过程中对惰性气体的反复加热冷却,从而有效的起到了节能降耗的目的。
另外,通过应用50%的富氧空气,能够将总硫的实际收率进一步提升0.5%~1.0%,从而使得整个工艺过程中硫的夹带损失得到了有效缩减。
富氧 Claus工艺在上世纪80年代出现之后,在整个工业生产领域得到了广泛的关注,在旧装置改造、产能扩充、新装置建设、控制硫回收及尾气处理成本等各个方面都实现了广泛应用。
新规下的硫回收尾气处理技术分析与对比

新规下的硫回收尾气处理技术分析与对比作者:汪月秋来源:《科学与技术》2018年第07期摘要:目前国内含硫酸性气主要处理路线为制取单质硫磺,产生附加值较高的硫磺产品后尾气高空排放,然而,对于大型工业园区或重化工基地尾气排放必然要面临尾气排放指标与环境容量的问题。
本文介绍了几种能够满足新规排放标准的硫回收尾气处理技术,简要比较并分析了不同各技术的特点,作为硫回收尾气处理技术选择时参考。
关键词:新规;硫回收;尾气处理引言根据相关法规,国内硫回收装置大气排放口现阶段执行GB31570-2015石油炼制化工污染物排放标准,同时结合企业全厂其他污染物大气排放因素以及项目环境大气容量,局部地区硫回收装置排放尾气SO2组分浓度限值最低要求为100mg/Nm3。
1、硫磺回收装置工艺流程硫磺回收单元主要处理来自低温甲醇洗含硫化氢30%左右的富硫酸性气,采用部分燃烧Claus工艺,包括三级冷凝和两级催化转化。
未反应的Claus尾气通过加氢还原—吸收工艺进一步降低尾气中硫组分含量,经处理后的尾气排入尾气焚烧炉进行焚烧。
将低温甲醇洗来的主酸性气、预洗酸性气和博元公司酸性气在燃烧炉内部分燃烧,控制过程气中H2S/SO2比值为2,提高硫磺回收率。
气化来煤气水分离和酚氨回收酸性气与过程气一起进入尾气焚烧炉,通过废锅回收热量后进入氨法脱硫系统进一步吸收SO2,最后使二氧化硫排放达到国家标准。
通过此法可使H2S的总转化率98-99%;三期年产硫磺16万吨,不仅经济效益可观,还可以消除污染,保护环境。
2、硫磺回收工艺和尾气处理工艺2.1、硫磺回收工艺本公司硫磺回收装置是由山东三维石化工程股份有限公司设计,中石化十建承建,每套装置双脱和硫磺单元两部分,设计H2S的总转化率98-99%;三期年产硫磺16万吨。
进入反应炉燃烧器的空气量需将酸性气中的烃类完全氧化,同时满足装置尾气中SO2/H2S比率为1∶2所要求的部分H2S燃烧所需的空气量。
硫磺回收装置尾气处理工艺探讨

硫磺回收装置尾气处理工艺探讨引言:硫磺回收装置是用于回收工业生产过程中产生的硫磺尾气的设备,对于减少硫磺的浪费和对环境的污染有重要意义。
在设计硫磺回收装置的尾气处理工艺时,需要考虑到各种因素,如硫磺尾气的成分、处理效率、能耗等。
本文将对硫磺回收装置尾气处理的工艺进行探讨,并提出一种可行的工艺方案。
一、硫磺尾气的成分分析二、工艺方案探讨1.常规吸收法常规吸收法是处理硫磺尾气的常用方法之一、通过将尾气中的SO2与吸收液中的反应剂(如氨水)进行吸收反应,将SO2转化为硫酸铵或硫代硫酸铵等形式,然后通过后续的脱硫和硫酸铵的分离工艺,将硫酸铵回收。
这种方法的优点是工艺成熟、可靠性高,但存在反应速度慢、能耗大的问题。
2.燃烧法燃烧法是将硫磺尾气中的硫化物直接燃烧为二氧化硫,然后对二氧化硫进行进一步处理。
这种方法的优点是处理效率高,但存在能耗大、二氧化硫气体排放的问题。
3.催化氧化法催化氧化法是利用催化剂促使硫磺尾气中的硫化物氧化为SO2的方法。
催化氧化法具有反应速度快、处理效率高的特点,但对于硫磺尾气中的其他成分如CS2的处理效果较差。
三、可行的工艺方案根据硫磺回收装置尾气的成分分析和各种工艺方案的优缺点1.组合工艺方案:将常规吸收法和催化氧化法结合,先采用常规吸收法将硫磺尾气中的SO2吸收成硫酸铵或硫代硫酸铵,然后采用催化氧化法将残留的硫化物氧化为SO2、这样可以充分利用常规吸收法的成熟工艺和催化氧化法的高效率。
2.能耗优化方案:在硫磺回收装置中引入能耗优化技术,如换热器和废热利用设备,以减少处理过程中的能耗。
同时,对反应器设计进行优化,提高反应速度和效率,降低硫磺尾气处理过程中的能耗。
3.二次处理方案:对除去SO2之外的其他成分,如CS2等,采用其他合适的工艺进行处理,以降低硫磺尾气的综合污染。
结论:硫磺回收装置尾气处理的工艺方案需要考虑到硫磺尾气的成分、处理效率和能耗等因素。
通过组合多种工艺方案、优化能耗和引入二次处理等手段,可以实现硫磺尾气的高效处理和回收。
硫磺回收及尾气处理装置优化运行技术分析

硫磺回收及尾气处理装置优化运行技术分析摘要:目前资源使用量增加,环境污染问题严重。
为减少天然气使用中污染物的排放,硫磺回收及尾气处理受到关注。
该装置的应用效果显著,是天然气处理系统中起到关键性作用的部分。
尾气处理装置运行过程中,可通过硫元素的回收,控制污染物的排放,同时产生巨大经济效益,为保护环境提供支持。
基于此,本文将围绕硫磺回收及尾气处理相关内容,提出处理装置优化措施,为后续工作提供参考。
关键词:运行技术;尾气处理;硫磺回收;装置优化引言:结合现实经验可知,持续完善硫磺回收及尾气处理核心单元,可充分利用硫资源,从而改善大气环境,技术应用效果显著。
某气田建设中应用高含硫净化装置和尾气处理单元,提高了硫磺回收率,解决一系列生产问题的同时,减少了SO2的排放量,达到了环保、高效生产的科学目标。
由此可见,硫磺回收及尾气处理核心单元的合理完善,对企业发展和环境改善有持续的作用。
1 装置工艺流程介绍硫磺回收设备由反应炉等重要构件组成,其中囊括了冷凝器及转化器等。
研究发现,传统硫磺回收装置中,为保障较高的回收效率,会采用直接加热方法,将气体在反应炉内转化,然后对硫化物质吸收,保障硫磺的回收量和效率。
装置运行原理是进入反应炉内的气体(通常指酸性气体)在重要介质的作用下会与空气进行燃烧,生成安全的物质,并有效排放出去。
此阶段提供的空气量并不是随机的,会按照化学计量配给,以保障科学性。
通过稳定的反应机制,达到稳定的硫回收效果。
三级硫冷凝器出口处特意安装了在线分析仪,主要功能是分析HS/SO2,对尾气质量严格把控。
以上设备能准确控制所需燃烧空气流量,从而达2到最佳的硫回收率。
尾气碱洗工艺中,其中逆喷管的核心配件就是喷头。
实践表明,选用耐磨性好的喷头,可减少堵塞的发生。
脱硫设备运行阶段,其中的脱硫碱液将会喷出,如果与烟气逆向而遇(含硫的烟气),就会形成泡沫区,实现二氧化硫的吸收和转化。
与此同时,吸收液水分会蒸发,保障脱硫质量和效率[1]。
硫回收尾气处理技术对比

硫回收尾气处理技术对比作者:白鹏申凤山来源:《中国化工贸易·下旬刊》2019年第07期摘要:本文介绍了几种硫磺回收尾气处理技术的基本原理和技术特点,对目前常用的技术做了技术经济性比较,对硫磺回收尾气处理技术的选择提出了意见。
关键词:硫回收;尾气处理;克劳斯;SCOT;超级克劳斯近年来随着煤化工的迅速发展,硫回收技术也得到了快速发展,同时,环保法规对于尾气排放要求也日益严格,最新颁布的中华人民共和国《石油炼制工业污染物排放标准》对硫回收装置尾气中SO2的含量要求必须小于400mg/m3,在环境承载能力减弱或大气环境容量较小的区域要求尾气中SO2的含量必须小于100mg/m3,为了达到尾气排放标准,就需要对硫回收装置中尾气处理技术提出更高的要求。
克劳斯法是目前硫磺回收的主流工艺,在不断发展过程中很多方面都有了重大改进,但因限制于化学反应平衡,硫磺回收率一般只能达到97%左右,尾气中仍有约1%的硫化物即相当于原料中3%~4%的硫以SO2的形态排入大气,这样不仅浪费了硫资源,也造成了大气污染[1]。
为此,针对这一问题便产生了硫回收尾气处理技术。
1 克劳斯法硫回收原理克劳斯法硫回收装置一般分为制硫部分和尾气处理部分,制硫部分即发生克劳斯反应制取硫磺,制硫部分主要采用部分燃烧法,将原料气全部送入制硫燃烧炉,严格控制空气或氧气的进气量,使H2S燃烧后生成SO2的量满足H2S/SO2接近于2,H2S与SO2在燃烧炉中的高温下发生反应生成气态硫磺,未完全反应的硫化氢和二氧化硫再经过克劳斯反应器,在催化剂的作用下发生反应生成单质硫。
主要反应如下:O2+H2S→H2O+SO2SO2+2H2S →2H2O+3S同时,克劳斯反应器中还发生氧硫化碳和二硫化碳的水解反应:H2O+COS→CO2+H2S2H2O+CS2→CO2+2H2S经过上述过程反应的酸性气,因限制于化学反应平衡,硫磺回收率一般只能达到97%左右,尾气中含有的各种形态的硫经过焚烧后以二氧化硫的形态排入大气。
- 1、下载文档前请自行甄别文档内容的完整性,平台不提供额外的编辑、内容补充、找答案等附加服务。
- 2、"仅部分预览"的文档,不可在线预览部分如存在完整性等问题,可反馈申请退款(可完整预览的文档不适用该条件!)。
- 3、如文档侵犯您的权益,请联系客服反馈,我们会尽快为您处理(人工客服工作时间:9:00-18:30)。
硫磺回收装置尾气处理技术比选
摘要:当今随环保标准不断提高,对硫磺回收尾气的处理技术不断提出更高的要求。
本文通过归纳总结出硫磺回收装置尾气达标的技术存在的问题,阐述几种硫磺回收装置尾气处理技术,为尾气处理技术比选提供专业合理的思路。
关键词:硫磺回收;尾气处理;工艺技术比选
引言:随全球环保问题不断受到人们关注与重视,各国对二氧化硫的排放标准不断提高,这对硫磺回收装置尾气处理技术提出了更高的要求。
国家环境保护部规定存在硫磺回收装置的每立方米二氧化硫排放值最高为400mg,而对于大气污染较为严重的小容量大气环境和脆弱的生态环境,每立方米二氧化硫排放最高值为100mg。
本文对硫磺回收装置尾气处理技术进行比选,以期实现企业经济效益与环保效益最大化。
1 硫磺回收装置尾气处理技术问题
过去国内主要采用2种工艺技术处理硫磺回收装置的尾气,一种是通过两级克劳斯,经过加氢还原吸收,最后进行尾气焚烧工艺;第二种是在两级克劳斯的基础上用催化氧化代替,再进行尾气焚烧工艺。
但由于新标准对二氧化硫排放限值的要求不断提高,这两种工艺在尾气处理时无法达到新的标准,具体问题如下。
对于加氢还原反应吸收尾气的处理技术而言,是将含硫的物质包括SO2、COS及CS2加氢还原成H2S,然后选择胺液分别吸收,经胺液处理过的硫化氢继续循环进入两级克劳斯的阶段[1]。
该工艺暴露出的问题有:一、催化剂性能严重影响加氢反应器的转化率,工艺过程中仍有因催化剂因素存在部分有机硫没被转化成硫化氢,因此胺液不能完全吸收,而是和尾气一起排放。
二、胺液虽然能吸收尾气中的硫化氢,但受反应平衡理论制约,胺液无法全部吸收硫化氢,导致约0.5%的硫化氢在尾气中排放,不合标准。
对于催化氧化尾气处理技术而言,是指选择性地添加氧化催化剂在催化氧化反应中,将尾气中的硫化氢直接转变成单质硫。
该工艺暴露出的主要问题是指选择性氧化催化剂的性能问题导致转化率提高受限,使得约1%的硫化物进入尾气中一同排放,导致二氧化硫含量超标[2]。
2 满足标准的尾气处理技术介绍
2.1氨法尾气脱硫工艺
氨法尾气脱硫工艺的基本过程包括二氧化硫的吸收及亚硫酸铵的氧化。
大致的工艺流程为:将克劳斯的尾气直接排入焚烧炉里,经过一段时间的焚烧处理后再进入胺法脱硫系统中。
胺法脱硫的核心机制就是脱硫塔,塔内分为两个区域包括吸收区及氧化区。
存在于烟气中的胺液往上或下喷出并发生发生反应,排除二氧化硫和三氧化硫,生成亚硫酸铵和亚硫酸氰铵。
塔顶排出脱硫后的烟气,塔底形成的硫酸铵溶液的结晶以干燥处理的方法产出产出硫酸铵。
该技术削减SCOT 尾气处理的步骤,同时排出的尾气里不存在粉尘,保证硫酸铵的生产。
该技术存在问题:一、工艺开展过程中有少量氨不参加化学反应直接排出,直接从烟囱挥发。
二、此法经常出现气溶胶的现象,即由硫酸铵等多种物质组成的固体液态小质点,随烟气一起排出。
2.2络合铁催化剂处理尾气工艺
络合铁催化剂作为新型脱硫催化剂,在焦炉煤气脱硫系统中广泛的运用。
络合铁脱硫催化剂存在两种不同形式,包括:淡黄色结晶粉末的存在形式和红棕色的液体存在形式。
络合铁同稳定剂组成淡黄色晶体粉末物,同缓蚀剂、吸收剂组
成红棕色液体。
络合铁催化剂处理尾气主要是利用氧气氧化硫化氢转变为单质硫,适用于高含量硫的原料气。
2.3碱法洗涤脱硫工艺
碱法洗涤脱硫工艺基本原理就是利用烧碱溶液与烟气中的二氧化硫接触发生
两次反应,生成亚硫酸氢钠。
大致的工艺技术路线为:经过焚烧阶段后的烟气排
入烟气净化器进行换热降温,最后进入尾气脱硫塔。
工艺要求在脱硫塔入口设置
喷嘴,使烟气经过冷却后能直接进入吸收区;设置喷头将碱溶液喷入吸收层,与
烟气形成逆流,最终实现降温目的。
为控制氢离子浓度指数将循环泵连接喷淋层,增减溶液,以7左右为标准控制氢离子浓度,最大程度上提高脱硫效果且使用最
少的吸收剂[3]。
除雾后的烟气升温处理经烟囱达标排放。
整个流程中,该工艺提
高了尾气二氧化硫的回收率,大大幅度降低了硫磺回收装置尾气二氧化硫的排放量。
与此同时,该工艺也存在脱硫过程中产生大量废水的问题,需要消耗大量碱
液处理废水中的硫酸钠。
2.4低温甲醇洗工艺
低温甲醇洗工艺技术是采用甲醇有机溶剂充当吸收剂,通过利用甲醇在低温
环境下能够对二氧化碳、硫化氢、COS等酸性气体溶解度大的特点,分阶段或同
时进行脱除酸性气体的净化工艺。
由于煤化工硫磺尾气中含有不同形态的硫化物,可以采取加氢还原反应转变硫化物为还原硫化氢,再将其排入低温甲醇洗装置,
以实现脱硫。
改工艺技术基本流程为:从硫磺回收装置收集到的尾气加氢转化成
硫化氢排入激冷塔,用逆流急冷水降温后再进入低温甲醇洗装置。
此时利用低温
甲醇选择性吸收硫化氢形成甲醇富液,再返回再生单元吸收硫化氢循环回硫磺回
收装置,最终实现回收尾气硫的低量排放
3 尾气处理技术选择的思路
通过对以上四种工艺技术的介绍,容易得知四种工艺技术各有长处与短处,
在选择尾气处理技术的时候需要结合自身资金与项目实际内容进行筛选,总结以
下思路作为参考。
3.1碱法洗涤脱硫工艺
该工艺技术系统复杂,流程周期长,投资成本高且工程消耗量巨大。
如前所述,巨大的废水会加重污水处理厂的负担,增加污水处理的成本。
若要回收硫酸
钠以出售获利,势必要设置处理系统,导致投资成本进一步增加。
即选择此工艺
技术时,产生的硫酸钠废水量不多时可以采用,但无法回收硫酸钠。
3.2氨法尾气脱硫工艺
该工艺巨大的优势在于其产生的硫酸铵是实用的农用肥料,经收集出售,收
入可观,尤其对于大多数设置回收系统的煤化工项目而言,完全可以将自产的废
氨水当成脱硫吸收剂使用,以实现废水治理废气。
另外,根据技术专家的经验,
硫磺回收装置与锅炉氨法脱硫装置距离最好小于800米以防止硫酸铵结晶堵住管
道和管道因过长成本增加。
因此,在开展新项目后需要在总图布置时就要严格把
控这两个主要装置的距离。
3.3络合铁催化剂处理尾气工艺
新型络合铁脱硫后生成副盐的概率很低,投入氨和碱的使用的成本和处理副
盐由此降低[4]。
脱硫废液的减少节约了用水量和降低能耗,提高了经济效益和环
保效益。
但是脱硫废液中存在悬浮硫及氨需要加强控制,以促进脱硫工作的稳定
开展。
3.4低温甲醇洗工艺
该工艺因其没有尾气处理装置,建设投资较小。
从理论的角度看,低温甲醇
洗工艺是能实现无废气排放。
但是,若采取改工艺处理废气,要求相关管理者在
工艺包编制时能够详细安排硫磺回收尾气的处理方法和处理量,最大程度避免硫
磺回收尾气时运行不顺畅。
另外,由于该技术装置还是实验阶段,尚未投入运行,存在一定的技术风险。
结语:企业经济的发展和环保压力增减是同向变动的,尾气处理排放的达标是缓
解环保压力的重要一环。
在进行尾气处理技术上的选择时,需要结合企业实际情
况和项目状况,统筹考虑不同工艺的优缺点,帮助企业实现经济和环保效益最大化。
参考文献:
[1]曹东学.硫磺回收装置尾气处理技术比选[J].石油炼制与化工,2019,50(06):64-69.
[2]刘帅,杨彬,文增坤.新标准下硫磺回收装置尾气排放处理技术探讨[J].石油化工应用,2018,37(01):124-127.
[3]韩科,刘春辉.新排放标准下的硫磺回收尾气处理技术选择[J].现代化
工,2017,37(09):159-163.
[4]张迎,赵霞,傅晓乐,李超维.硫磺回收装置尾气处理新技术对比[J].中国石油石
化,2016(23):20-21.。