硫磺回收尾气处理工艺技术措施
硫磺回收装置尾气处理

:
。
。
其 总 反
10
后
3
,
全 厂 的 H S 排放 量将 逐 年 增 高
。
Z
S夕
量
.
:
S
+
=
25 +
在 克劳 斯催化 %
。
也 势必 增 加
到 了1
987
.
年
,
5 0
:
排 放量 增 加
3 66 魂
。
反应 器中
12 5
℃ 时 H 声转化 率接 近
,
。
倍多
,
1 9 9 0 年 将到 6
,
6 6倍 ,
.
硫收率 最高 也
处 理 技术 已 有 几 十种
以下三 类
1
. 。
,
按其原 理大 致 可 分 为
0 ~
9了 5
,
.
%
。
其 放空 尾 气中仍有
,
写的硫化 物 % 的硫以
,
即 相 当 于装置 处 理 量 的
:
低 温克劳 斯 反应 法
,
50
等 形 态排 入 大 气
。
损失
在低 于 硫 的露点 温 度 下
50
境 续表
2
保
护
,
2
9
为50
酸
、
2
,
然 后 分离 5 0
。
转化 为 元 素 硫
硫
、
.1Βιβλιοθήκη ’亚 硫 酸 盐 等 这 类 方 法基本 上 不 受 C O S
Z
Cs 以及 H s
Z
/ S
0 比 例 的限 制 也 能 达 到 很 高 的
硫回收尾气处理技术及超级克劳斯工艺
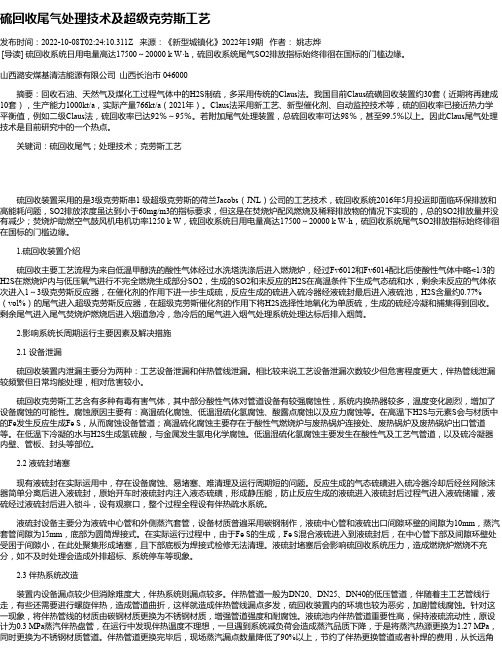
硫回收尾气处理技术及超级克劳斯工艺发布时间:2022-10-08T02:24:10.311Z 来源:《新型城镇化》2022年19期作者:姚志烨[导读] 硫回收系统日用电量高达17500~20000 k W·h,硫回收系统尾气SO2排放指标始终徘徊在国标的门槛边缘。
山西潞安煤基清洁能源有限公司山西长治市 046000摘要:回收石油、天然气及煤化工过程气体中的H2S制硫,多采用传统的Claus法。
我国目前Claus硫磺回收装置约30套(近期将再建成10套),生产能力1000kt/a,实际产量766kt/a(2021年)。
Claus法采用新工艺、新型催化剂、自动监控技术等,硫的回收率已接近热力学平衡值,例如二级Claus法,硫回收率已达92%~95%。
若附加尾气处理装置,总硫回收率可达98%,甚至99.5%以上。
因此Claus尾气处理技术是目前研究中的一个热点。
关键词:硫回收尾气;处理技术;克劳斯工艺硫回收装置采用的是3级克劳斯串1 级超级克劳斯的荷兰Jacobs(JNL)公司的工艺技术,硫回收系统2016年5月投运即面临环保排放和高能耗问题,SO2排放浓度虽达到小于60mg/m3的指标要求,但这是在焚烧炉配风燃烧及稀释排放物的情况下实现的,总的SO2排放量并没有减少;焚烧炉助燃空气鼓风机电机功率1250 k W,硫回收系统日用电量高达17500~20000 k W·h,硫回收系统尾气SO2排放指标始终徘徊在国标的门槛边缘。
1.硫回收装置介绍硫回收主要工艺流程为来自低温甲醇洗的酸性气体经过水洗塔洗涤后进入燃烧炉,经过Fv6012和Fv6014配比后使酸性气体中略<1/3的H2S在燃烧炉内与低压氧气进行不完全燃烧生成部分SO2,生成的SO2和未反应的H2S在高温条件下生成气态硫和水,剩余未反应的气体依次进入1~3级克劳斯反应器,在催化剂的作用下进一步生成硫,反应生成的硫进入硫冷器经液硫封最后进入液硫池,H2S含量约0.77%(vol%)的尾气进入超级克劳斯反应器,在超级克劳斯催化剂的作用下将H2S选择性地氧化为单质硫,生成的硫经冷凝和捕集得到回收。
硫磺回收装置尾气处理工艺探讨
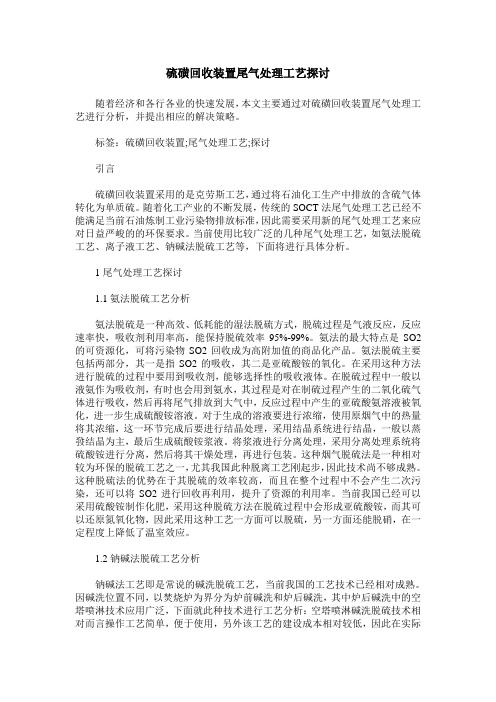
硫磺回收装置尾气处理工艺探讨随着经济和各行各业的快速发展,本文主要通过对硫磺回收装置尾气处理工艺进行分析,并提出相应的解决策略。
标签:硫磺回收装置;尾气处理工艺;探讨引言硫磺回收装置采用的是克劳斯工艺,通过将石油化工生产中排放的含硫气体转化为单质硫。
随着化工产业的不断发展,传统的SOCT法尾气处理工艺已经不能满足当前石油炼制工业污染物排放标准,因此需要采用新的尾气处理工艺来应对日益严峻的的环保要求。
当前使用比较广泛的几种尾气处理工艺,如氨法脱硫工艺、离子液工艺、钠碱法脱硫工艺等,下面将进行具体分析。
1尾气处理工艺探讨1.1氨法脱硫工艺分析氨法脱硫是一种高效、低耗能的湿法脱硫方式,脱硫过程是气液反应,反应速率快,吸收剂利用率高,能保持脱硫效率95%-99%。
氨法的最大特点是SO2的可资源化,可将污染物SO2回收成为高附加值的商品化产品。
氨法脱硫主要包括两部分,其一是指SO2的吸收,其二是亚硫酸铵的氧化。
在采用这种方法进行脱硫的过程中要用到吸收剂,能够选择性的吸收液体。
在脱硫过程中一般以液氨作为吸收剂,有时也会用到氨水,其过程是对在制硫过程产生的二氧化硫气体进行吸收,然后再将尾气排放到大气中,反应过程中产生的亚硫酸氨溶液被氧化,进一步生成硫酸铵溶液。
对于生成的溶液要进行浓缩,使用原烟气中的热量将其浓缩,这一环节完成后要进行结晶处理,采用结晶系统进行结晶,一般以蒸發结晶为主,最后生成硫酸铵浆液。
将浆液进行分离处理,采用分离处理系统将硫酸铵进行分离,然后将其干燥处理,再进行包装。
这种烟气脱硫法是一种相对较为环保的脱硫工艺之一,尤其我国此种脱离工艺刚起步,因此技术尚不够成熟。
这种脱硫法的优势在于其脱硫的效率较高,而且在整个过程中不会产生二次污染,还可以将SO2进行回收再利用,提升了资源的利用率。
当前我国已经可以采用硫酸铵制作化肥,采用这种脱硫方法在脱硫过程中会形成亚硫酸铵,而其可以还原氮氧化物,因此采用这种工艺一方面可以脱硫,另一方面还能脱硝,在一定程度上降低了温室效应。
硫磺回收工艺流程

硫磺回收工艺流程硫磺回收工艺流程主要是将含有硫磺的废气或废水进行处理,将其中的硫磺分离出来,以减少环境污染并实现资源的回收利用。
下面是一个具体的硫磺回收工艺流程的简要介绍。
首先,硫磺回收工艺的第一步是收集含有硫磺的废气或废水。
这些废气通常是工业生产过程中产生的尾气,而废水则是工厂或化工厂排放出来的废水。
这些废气或废水经过合适的收集系统进行收集,并送入下一步的处理过程。
第二步是对废气或废水进行预处理。
预处理的目的是去除废气或废水中的杂质和污染物,使其更适合后续的硫磺分离过程。
预处理可以采用各种方法,如过滤、沉淀、吸附等。
接下来的第三步是硫磺分离。
这一步通常采用蒸馏或溶剂萃取的方法。
在蒸馏过程中,废气或废水中的硫磺在高温下蒸发,然后通过冷凝,使其凝结回到液体状态。
而溶剂萃取则是用一种溶剂将硫磺从废气或废水中提取出来。
第四步是对硫磺进行精制处理。
在这一步中,硫磺经过过滤、洗涤等处理,去除其中的杂质,得到纯净的硫磺。
这些纯净的硫磺可以用于再生利用或者销售给其他行业。
最后一步是对废气或废水进行尾气处理。
在处理完硫磺后,剩下的废气或废水中可能还存在一些有害污染物,需要进行进一步的处理以符合环保标准。
尾气处理可以采用各种方法,如吸附、催化、洗涤等,以去除废气或废水中的有害物质,使其达到环保要求。
以上就是一个典型的硫磺回收工艺流程的简要介绍。
在实际应用中,硫磺回收工艺可以根据具体情况进行调整和优化,以提高回收效率和降低成本。
硫磺回收工艺的应用可以减少硫磺资源的浪费,减轻环境污染,同时也有经济效益和社会效益。
SCOT硫回收尾气处理技术进展
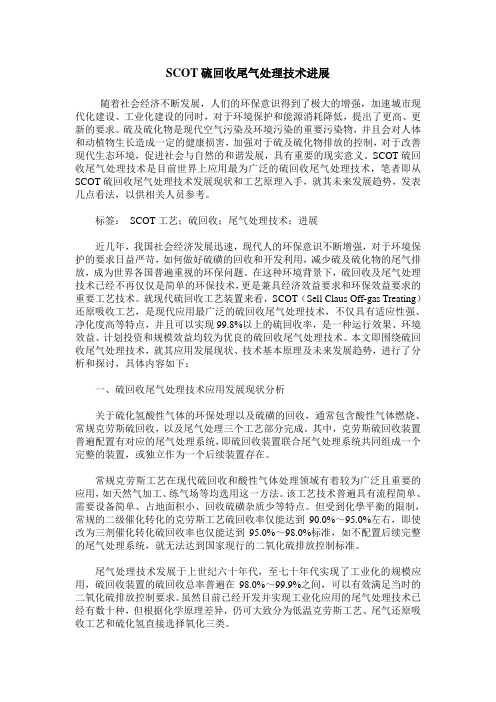
SCOT硫回收尾气处理技术进展随着社会经济不断发展,人们的环保意识得到了极大的增强,加速城市现代化建设、工业化建设的同时,对于环境保护和能源消耗降低,提出了更高、更新的要求。
硫及硫化物是现代空气污染及环境污染的重要污染物,并且会对人体和动植物生长造成一定的健康损害,加强对于硫及硫化物排放的控制,对于改善现代生态环境,促进社会与自然的和谐发展,具有重要的现实意义。
SCOT硫回收尾气处理技术是目前世界上应用最为广泛的硫回收尾气处理技术,笔者即从SCOT硫回收尾气处理技术发展现状和工艺原理入手,就其未来发展趋势,发表几点看法,以供相关人员参考。
标签:SCOT工艺;硫回收;尾气处理技术;进展近几年,我国社会经济发展迅速,现代人的环保意识不断增强,对于环境保护的要求日益严苛,如何做好硫磺的回收和开发利用,减少硫及硫化物的尾气排放,成为世界各国普遍重视的环保问题。
在这种环境背景下,硫回收及尾气处理技术已经不再仅仅是简单的环保技术,更是兼具经济效益要求和环保效益要求的重要工艺技术。
就现代硫回收工艺装置来看,SCOT(Sell Claus Off-gas Treating)还原吸收工艺,是现代应用最广泛的硫回收尾气处理技术,不仅具有适应性强、净化度高等特点,并且可以实现99.8%以上的硫回收率,是一种运行效果、环境效益、计划投资和规模效益均较为优良的硫回收尾气处理技术。
本文即围绕硫回收尾气处理技术,就其应用发展现状、技术基本原理及未来发展趋势,进行了分析和探讨,具体内容如下:一、硫回收尾气处理技术应用发展现状分析关于硫化氢酸性气体的环保处理以及硫磺的回收,通常包含酸性气体燃烧、常规克劳斯硫回收,以及尾气处理三个工艺部分完成。
其中,克劳斯硫回收装置普遍配置有对应的尾气处理系统,即硫回收装置联合尾气处理系统共同组成一个完整的装置,或独立作为一个后续装置存在。
常规克劳斯工艺在现代硫回收和酸性气体处理领域有着较为广泛且重要的应用,如天然气加工、练气场等均选用这一方法。
SCOT法尾气处理工艺技术进展
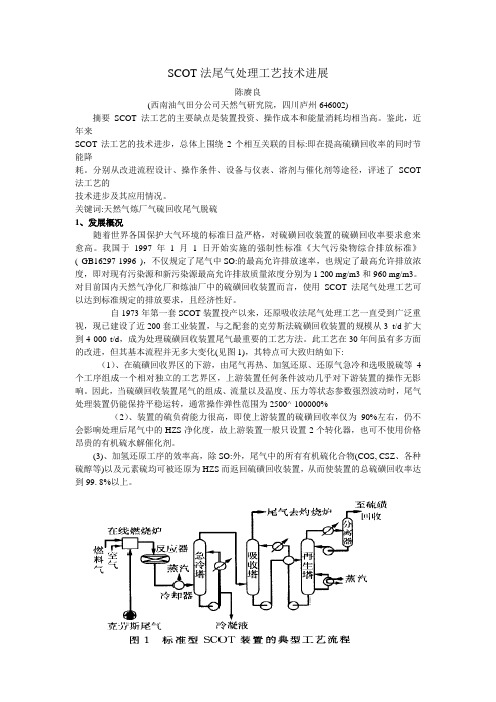
SCOT法尾气处理工艺技术进展陈赓良(西南油气田分公司天然气研究院,四川庐州646002)摘要SCOT法工艺的主要缺点是装置投资、操作成本和能量消耗均相当高。
鉴此,近年来SCOT法工艺的技术进步,总体上围绕2个相互关联的目标:即在提高硫磺回收率的同时节能降耗。
分别从改进流程设计、操作条件、设备与仪表、溶剂与催化剂等途径,评述了SCOT 法工艺的技术进步及其应用情况。
关键词:天然气炼厂气硫回收尾气脱硫1、发展概况随着世界各国保护大气环境的标准日益严格,对硫磺回收装置的硫磺回收率要求愈来愈高。
我国于1997年1月1日开始实施的强制性标准《大气污染物综合排放标准》( GB16297-1996 ),不仅规定了尾气中SO:的最高允许排放速率,也规定了最高允许排放浓度,即对现有污染源和新污染源最高允许排放质量浓度分别为1 200 mg/m3和960 mg/m3。
对目前国内天然气净化厂和炼油厂中的硫磺回收装置而言,使用SCOT法尾气处理工艺可以达到标准规定的排放要求,且经济性好。
自1973年第一套SCOT装置投产以来,还原吸收法尾气处理工艺一直受到广泛重视,现已建设了近200套工业装置,与之配套的克劳斯法硫磺回收装置的规模从3 t/d扩大到4 000 t/d,成为处理硫磺回收装置尾气最重要的工艺方法。
此工艺在30年间虽有多方面的改进,但其基本流程并无多大变化(见图1),其特点可大致归纳如下:(1)、在硫磺回收界区的下游,由尾气再热、加氢还原、还原气急冷和选吸脱硫等4个工序组成一个相对独立的工艺界区,上游装置任何条件波动几乎对下游装置的操作无影响。
因此,当硫磺回收装置尾气的组成、流量以及温度、压力等状态参数强烈波动时,尾气处理装置仍能保持平稳运转,通常操作弹性范围为2500^-100000%(2)、装置的硫负荷能力很高,即使上游装置的硫磺回收率仅为90%左右,仍不会影响处理后尾气中的HZS净化度,故上游装置一般只设置2个转化器,也可不使用价格昂贵的有机硫水解催化剂。
硫磺工艺

国内硫磺回收及尾气处理工艺已成熟工艺:•SSR---齐鲁•ZHSR---镇海•LQSR---洛阳、齐鲁正在开发工艺:•16万吨/年---镇海、齐鲁•20万吨/年---SEI、齐鲁•超级Claus---齐鲁一.SSR---齐鲁(1)15%低负荷运行。
(2)制硫燃烧炉和尾气焚烧炉,无在线加热炉设备台数、控制回路数少,投资省、能耗低、占地少。
(3)无在线加热炉,避免了惰性气体进入系统,过程气总量少5-15%,工艺设备规格和工艺管道规格较小;在同等尾气净化度时,尾气排放量和污染物(SO2)绝对排放量相对较少。
硫回收工艺描述“SSR”工艺特点:(4)“SSR”工艺的主要设备均使用碳钢制造,且都可国内制造,从而形成了投资低、国产化率高的特点。
(5)一级转化器入口过程气再热采用高温掺合,控制简单、灵活、投资省。
二.ZHSR工艺•1996年镇海炼化引进引进荷兰Comprimo Comprimo公司公司7万万吨吨//年装臵年装臵•消化、吸收、再创新--10万吨万吨/年装臵年装臵•镇海工程公司、齐鲁研究院合作开发16万吨/年大型硫回收装臵工艺包ZHSR工艺流程ZHSR技术的特点(1)在线加热炉--成熟、可靠、升温快,负荷波动适应性强。
(2)尾气净化采用溶剂两级吸收、两段再生技术。
(3)尾气加氢开停工循环--蒸汽抽射器比循环风机投资低、操作简单、维护方便(4)反应炉、锅炉、硫冷器、加热器、反应器、硫封罐、液硫池采用特殊的布臵方式,使生成的液硫自动全部流入液硫池,全装臵无低点积硫。
三.LQSR节能型工艺•齐鲁研究院与洛阳石化工程公司合作开发•基于LSH-02低温加氢催化剂的开发成功,入口温度可降至220℃LQSR工艺特点(1)取消在线加热设备。
过程气采用自产中压蒸汽加热方式;Claus尾气采用自产中压蒸汽,辅助二级过热蒸汽加热,在催化剂硫化、开停工、运行末期及催化剂再生时使用;(2)尾气处理催化剂采用LSH-02低温型Claus尾气加氢催化剂,入口温度降至220℃,节能效果显著;(3)总硫回收率达到99.9%以上;(4)烟气中SO2量为15.4kg/h、浓度为435.5mg/Nm3。
液相氧化催化硫磺回收技术
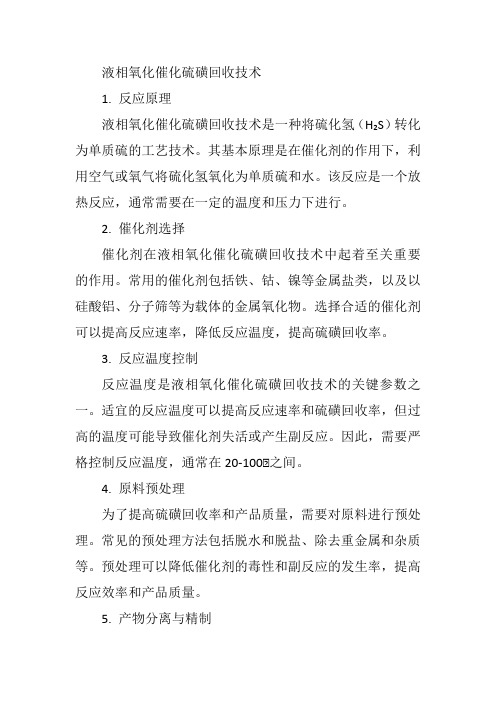
液相氧化催化硫磺回收技术1. 反应原理液相氧化催化硫磺回收技术是一种将硫化氢(H₂S)转化为单质硫的工艺技术。
其基本原理是在催化剂的作用下,利用空气或氧气将硫化氢氧化为单质硫和水。
该反应是一个放热反应,通常需要在一定的温度和压力下进行。
2. 催化剂选择催化剂在液相氧化催化硫磺回收技术中起着至关重要的作用。
常用的催化剂包括铁、钴、镍等金属盐类,以及以硅酸铝、分子筛等为载体的金属氧化物。
选择合适的催化剂可以提高反应速率,降低反应温度,提高硫磺回收率。
3. 反应温度控制反应温度是液相氧化催化硫磺回收技术的关键参数之一。
适宜的反应温度可以提高反应速率和硫磺回收率,但过高的温度可能导致催化剂失活或产生副反应。
因此,需要严格控制反应温度,通常在20-100℃之间。
4. 原料预处理为了提高硫磺回收率和产品质量,需要对原料进行预处理。
常见的预处理方法包括脱水和脱盐、除去重金属和杂质等。
预处理可以降低催化剂的毒性和副反应的发生率,提高反应效率和产品质量。
5. 产物分离与精制反应生成的硫磺和水需要进行分离和精制。
常用的分离方法包括过滤、离心分离和蒸馏等。
精制过程通常包括加热熔融、离心分离、干燥和成型等工序,以获得高纯度、高质量的硫磺产品。
6. 尾气处理液相氧化催化硫磺回收技术中产生的尾气需要进行处理,以防止对环境和人体造成危害。
常见的尾气处理方法包括燃烧、吸收、吸附和生物处理等。
处理后的尾气应符合国家和地方环境保护标准的要求。
7. 能耗与资源利用液相氧化催化硫磺回收技术的能耗较高,需要合理利用资源,降低能耗。
可以通过优化工艺参数、采用节能设备和技术、提高设备能效等措施来降低能耗和提高资源利用率。
8. 安全与环保液相氧化催化硫磺回收技术涉及易燃易爆、腐蚀性和有毒物质,需要采取安全措施,确保生产安全和员工健康。
同时,应加强环保意识,采用环保技术和设备,减少污染物排放,保护环境。
高含硫天然气硫磺回收及尾气处理工艺技术

高含硫天然气硫磺回收及尾气处理工艺技术摘要:我国的四川储藏着丰富的高含硫天然气,高含硫天然气的开发必须要配套建设大型的天然气净化厂,高含硫天然气中硫化氢以及二氧化硫的含硫都比较高,一些情况下甚至能达到10%左右,产硫量也比较高。
在我国环保要求不断提升的前提下,高含硫天然气气田必须要实现99.7%以上的硫回收才能最终达到尾气排放标准要求,因此对整个处理过程中硫磺回收以及尾气处理工艺设计提出更高要求。
本文主要针对目前国内外大型硫磺回收和尾气处理技术的发展状况进行了分析,以现场生产实践为基本出发点,对硫磺回收和尾气处理工艺流程的简化、操作稳定性等进行了探讨;关键词:高含硫天然气;硫磺回收;尾气处理;优化引言高含硫天然气在处理过程中如果不经过硫的有效回收,不仅会导致出现大量的资源浪费,而且也会对环境造成严重污染,因此,在当今绿色环保生产不断深化的前提下,整个天然气生产处理领域中硫磺回收和尾气处理工艺都得到了高度重视。
1 硫磺回收及尾气处理技术发展现状Claus制硫技术目前已经经过了100多年的发展历史,是当前整个化工处理领域中最为成熟的一种含硫酸气处理工艺。
三级 Claus硫收率由于会受到各种化学反应平衡的限制,导致其实际的收率仅仅能够达到97%。
鉴于此,国内外已经针对 Claus制硫技术开展了大量的研究,进一步开发出了多种尾气处理工艺,以此来有效提升硫收率。
1.1富氧 Claus技术该技术最早是应用在硫回收装置方面,其主要的应用目的是进一步扩大企业的产能。
例如,充分利用50%的富氧空气,在整个工艺处理过程中单位体积氧气消耗仅仅会代入等量的氮气,能够将过程气量进行明显的控制,也能够有效减少工艺处理过程中对惰性气体的反复加热冷却,从而有效的起到了节能降耗的目的。
另外,通过应用50%的富氧空气,能够将总硫的实际收率进一步提升0.5%~1.0%,从而使得整个工艺过程中硫的夹带损失得到了有效缩减。
富氧 Claus工艺在上世纪80年代出现之后,在整个工业生产领域得到了广泛的关注,在旧装置改造、产能扩充、新装置建设、控制硫回收及尾气处理成本等各个方面都实现了广泛应用。
浅谈克劳斯法硫磺回收的工艺与技术

浅谈克劳斯法硫磺回收的工艺与技术发布时间:2021-11-11T07:22:25.299Z 来源:《中国科技人才》2021年第22期作者:薛媛媛1 吴蕊宁2 张伟3 [导读] 在煤化工生产中采用合适的硫磺回收工艺非常必要。
文章对克劳斯法在硫磺回收中的工艺与技术展开了分析,旨在进一步提升煤化工企业生产中硫磺回收技术水平,降低对环境的污染。
同时给行业工作人员提供有益参考。
薛媛媛1 吴蕊宁2 张伟31,3 蒲城清洁能源化工有限责任公司陕西蒲城 7155012陕西煤业化工技术研究院有限责任公司陕西西安 71000摘要:在煤化工生产中采用合适的硫磺回收工艺非常必要。
文章对克劳斯法在硫磺回收中的工艺与技术展开了分析,旨在进一步提升煤化工企业生产中硫磺回收技术水平,降低对环境的污染。
同时给行业工作人员提供有益参考。
关键词:硫磺回收;尾气处理;克劳斯法;煤化工1克劳斯硫回收工艺特点目前,在我国很多化工厂都会运用克劳斯法来进行酸性气体的处理以及硫的回收。
与其它硫回收方法相比,该方法具有成本低廉、流程简便、占地面积小等优点。
所以,克劳斯法在我国化工生产中应用非常广泛。
但是近些年随着我国对环保重视程度的不断提升,传统的克劳斯法即便经过三级转化,其硫回收率也只能达到95%-98%,这已经无法满足我国环保新标准的要求,所以,如何提升硫回收率已经成为整个行业所重点关注和必须要解决的一个关键问题。
2克劳斯法硫磺回收工艺的优势(1)在煤化工生产硫回收过程中,克劳斯法硫磺回收工艺具有工艺简便、操作简单、成本较低等优势,且该反应的化学稳定性相对较高。
该方法所使用的装置复杂度也相对较低,维修较为方便,其催化剂的使用寿命能够高达10年,寿命比较长;(2)克劳斯法硫磺回收工艺对于硫磺的回收以及转化效率非常高,能够满足当前越来越严格的环保标准;同时通过对克劳斯法进行优化和改良之后,其硫磺回收率能够达到99.4%以上,极大的降低了向大气中排放的硫化物;(3)克劳斯法硫磺回收工艺对化工生产中酸性气浓度的适应范围较广,能够针对不同浓度的酸性气选择不同的工艺和技术。
硫磺尾气焚烧部分工艺介绍
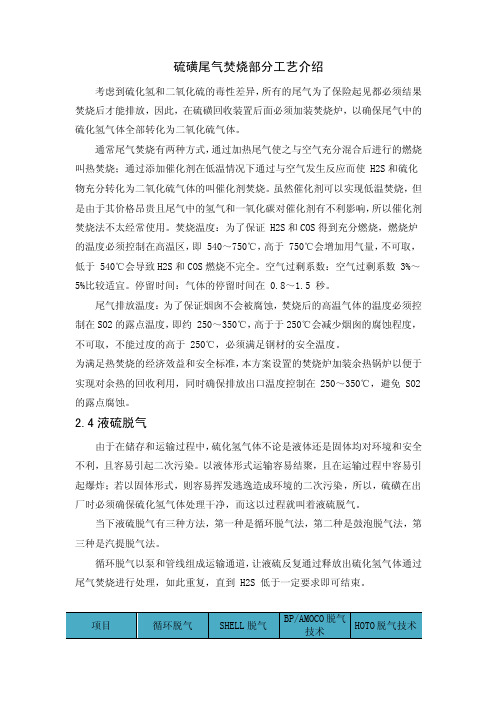
硫磺尾气焚烧部分工艺介绍考虑到硫化氢和二氧化硫的毒性差异,所有的尾气为了保险起见都必须结果焚烧后才能排放,因此,在硫磺回收装置后面必须加装焚烧炉,以确保尾气中的硫化氢气体全部转化为二氧化硫气体。
通常尾气焚烧有两种方式,通过加热尾气使之与空气充分混合后进行的燃烧叫热焚烧;通过添加催化剂在低温情况下通过与空气发生反应而使 H2S和硫化物充分转化为二氧化硫气体的叫催化剂焚烧。
虽然催化剂可以实现低温焚烧,但是由于其价格昂贵且尾气中的氢气和一氧化碳对催化剂有不利影响,所以催化剂焚烧法不太经常使用。
焚烧温度:为了保证 H2S和COS得到充分燃烧,燃烧炉的温度必须控制在高温区,即 540~750℃,高于 750℃会增加用气量,不可取,低于 540℃会导致H2S和COS燃烧不完全。
空气过剩系数:空气过剩系数 3%~5%比较适宜。
停留时间:气体的停留时间在 0.8~1.5 秒。
尾气排放温度:为了保证烟囱不会被腐蚀,焚烧后的高温气体的温度必须控制在SO2的露点温度,即约 250~350℃,高于于250℃会减少烟囱的腐蚀程度,不可取,不能过度的高于 250℃,必须满足钢材的安全温度。
为满足热焚烧的经济效益和安全标准,本方案设置的焚烧炉加装余热锅炉以便于实现对余热的回收利用,同时确保排放出口温度控制在 250~350℃,避免 SO2的露点腐蚀。
2.4液硫脱气由于在储存和运输过程中,硫化氢气体不论是液体还是固体均对环境和安全不利,且容易引起二次污染。
以液体形式运输容易结聚,且在运输过程中容易引起爆炸;若以固体形式,则容易挥发逃逸造成环境的二次污染,所以,硫磺在出厂时必须确保硫化氢气体处理干净,而这以过程就叫着液硫脱气。
当下液硫脱气有三种方法,第一种是循环脱气法,第二种是鼓泡脱气法,第三种是汽提脱气法。
循环脱气以泵和管线组成运输通道,让液硫反复通过释放出硫化氢气体通过尾气焚烧进行处理,如此重复,直到 H2S 低于一定要求即可结束。
硫磺回收尾气处理安稳运行操作指南

硫磺回收尾气处理安稳运行操作指南1 加氢反应器⑴为了使S8和SO2全部进行加氢还原反应为H2S,必须保证工艺过程气进入反应器的温度在280~300℃范围内,这也是COS和CS2全部水解为H2S的必要条件。
⑵反应器出口温度随尾气组成中S8和SO2含量的增加而增加。
每增加1%的SO2相当于温升70℃左右。
⑶如尾气回收部分的H2浓度分析仪和制硫部分的H2S/SO2在线比值分析仪暂未投用,应正确配比克劳斯反应的风与酸性气的比值,控制制硫尾气中的SO2浓度,从而控制催化剂床层温升在允许范围内(<100℃)。
反应器进料中SO2含量极限,由催化剂床层允许最大温升决定,通常床层温度应小于400℃。
在短时间内尾气中SO2的允许最大浓度为1%(V)。
为保持较低的温升,在不降低总硫回收率的条件下,尽可能的降低制硫尾气中SO2浓度,通常保持尾气中H2S/SO2比值在2~4范围内。
可通过定期分析净化气中的氢浓度数据,适时调整混氢阀,控制净化气中氢浓度稍高于正常值,保证制硫尾气中SO2和S2全部还原为H2S。
⑷当H2S/SO2在线分析仪失灵或没有H2S/SO2在线分析仪时,为避免尾气中SO2过量而穿透反应器床层,可以根据反应器温升适时调整制硫炉配风量.反应器温升在正常情况下约为40℃,如温升过高说明配风过量,应适时减少配风;反之则适当加大配风.⑸克劳斯尾气中O2组份与H2还原反应生成水,导致尾气中还原组份减少,并且0.1%(v)的O2可使温升达15℃,在连续操作的过程中O2含量应控制在0.2 %(v)以下。
2 急冷塔⑴急冷塔顶出口气体温度约40℃,并且应尽可能的低,其目的是使气体带入吸收塔的水汽尽可能的少,并且低温有利于吸收。
⑵急冷塔底酸性水中的CO2和H2S含量与急冷水中的NH3含量、塔底温度、CO2和H2S分压有关,通常酸性水中的CO2含量为20~200ppm(wt),H2S含量为20~100ppm(wt)。
⑶急冷塔排出污水的PH值应保持≥7,为了防止设备和管道腐蚀,当PH小于6时,应往急冷水中注NH3。
复合胺法克劳斯尾气脱硫技术

复合胺法烟气脱硫技术
本技术所用的吸收剂是以复合有机胺盐为主,添加少量活化剂、抗氧化剂组
成的水溶液,有机胺盐的蒸汽压极低,无毒、无害、不燃、不爆,在脱除 SO2 的 同时,付产高纯 SO2 气体。
反应方程式:
SO2 + H2O ←→ H+ + HSO3-
(1)
R + H+←→ RH+
(2)
总反应式:
SO2 + H2O + R ←→ RH+ + HSO3-
(3)
上式中 R 代表离子液 SO2 吸收剂,(3)式是可逆反应,低温下反应(3)从左向
右进行,高温下反应(3)从右向左进行。复合胺脱硫技术正是利用此原理,在常
温下吸收二氧化硫,高温下将吸收剂中二氧化硫解吸,从而达到脱除和回收烟气
中 SO2 的目的。 工艺流程
复合胺法克劳斯硫磺回收尾气脱硫技术
背景技术 我国一直倡导节能减排工作,严格控制大气二氧化硫排放量,2012 年以前,
国家标准规定的二氧化硫排放浓度为不高于 960mg/g。目前国家有关部门正在酝 酿修订大气污染物综合排放标准,要求新建硫磺装置二氧化硫排放浓度小于 400mg/Nm3(特定地区排放浓度小于 100mg/Nm3)。2017 年 7 月 1 日以后,国家环 保标准 GB31571-2015 要求执行新的指标,环境要求更加苛刻。
制硫尾气送入制硫尾气焚烧炉进行焚烧,所有含硫介质均转化为 SO2,尾气 进入余热锅炉回收能量。
从余热锅炉出来的烟气,经动力波洗涤装置的逆喷管淬冷后,进入洗涤塔,
2
与洗涤水逆流接触,温度被降低至 40~50℃,经除雾器除雾后,进入吸收塔,与 从吸收塔上部进入的脱硫贫液逆流接触,气体中的 SO2 被吸收,净化气从塔顶引 出,送烟囱放空。
硫磺回收装置尾气处理工艺探讨

硫磺回收装置尾气处理工艺探讨引言:硫磺回收装置是用于回收工业生产过程中产生的硫磺尾气的设备,对于减少硫磺的浪费和对环境的污染有重要意义。
在设计硫磺回收装置的尾气处理工艺时,需要考虑到各种因素,如硫磺尾气的成分、处理效率、能耗等。
本文将对硫磺回收装置尾气处理的工艺进行探讨,并提出一种可行的工艺方案。
一、硫磺尾气的成分分析二、工艺方案探讨1.常规吸收法常规吸收法是处理硫磺尾气的常用方法之一、通过将尾气中的SO2与吸收液中的反应剂(如氨水)进行吸收反应,将SO2转化为硫酸铵或硫代硫酸铵等形式,然后通过后续的脱硫和硫酸铵的分离工艺,将硫酸铵回收。
这种方法的优点是工艺成熟、可靠性高,但存在反应速度慢、能耗大的问题。
2.燃烧法燃烧法是将硫磺尾气中的硫化物直接燃烧为二氧化硫,然后对二氧化硫进行进一步处理。
这种方法的优点是处理效率高,但存在能耗大、二氧化硫气体排放的问题。
3.催化氧化法催化氧化法是利用催化剂促使硫磺尾气中的硫化物氧化为SO2的方法。
催化氧化法具有反应速度快、处理效率高的特点,但对于硫磺尾气中的其他成分如CS2的处理效果较差。
三、可行的工艺方案根据硫磺回收装置尾气的成分分析和各种工艺方案的优缺点1.组合工艺方案:将常规吸收法和催化氧化法结合,先采用常规吸收法将硫磺尾气中的SO2吸收成硫酸铵或硫代硫酸铵,然后采用催化氧化法将残留的硫化物氧化为SO2、这样可以充分利用常规吸收法的成熟工艺和催化氧化法的高效率。
2.能耗优化方案:在硫磺回收装置中引入能耗优化技术,如换热器和废热利用设备,以减少处理过程中的能耗。
同时,对反应器设计进行优化,提高反应速度和效率,降低硫磺尾气处理过程中的能耗。
3.二次处理方案:对除去SO2之外的其他成分,如CS2等,采用其他合适的工艺进行处理,以降低硫磺尾气的综合污染。
结论:硫磺回收装置尾气处理的工艺方案需要考虑到硫磺尾气的成分、处理效率和能耗等因素。
通过组合多种工艺方案、优化能耗和引入二次处理等手段,可以实现硫磺尾气的高效处理和回收。
硫磺回收装置尾气达标排放的优化措施

硫磺回收装置尾气达标排放的优化措施发布时间:2021-07-02T14:14:34.410Z 来源:《中国科技信息》2021年8月作者:王海东[导读] 2020年国家生态环境部、市场监督管理总局联合发布了《陆上石油天然气开采工业大气污染物排放标准》(GB39728-2020),严格了硫磺回收装置尾气排放控制指标,天然气净化厂硫磺回收装置尾气排放达标面临着巨大的压力和严峻的挑战。
陕西延长石油(集团)有限责任公司延长气田采气三厂陕西延安王海东 717500摘要:2020年国家生态环境部、市场监督管理总局联合发布了《陆上石油天然气开采工业大气污染物排放标准》(GB39728-2020),严格了硫磺回收装置尾气排放控制指标,天然气净化厂硫磺回收装置尾气排放达标面临着巨大的压力和严峻的挑战。
为此,本文以延长石油延长气田采气三厂安塞沿河湾净化厂为例,对硫磺回收装置尾气达标排放采用科学合理的方法,优化工艺措施,实现节能环保发展,以期为相关工作起到参考作用。
关键词:硫磺回收装置二氧化硫尾气达标排放优化措施1 天然气净化厂标准排放现状分析1.1 SO排放标准《大气污染物综合排放》(GB 16297-1996)对天然气净化生产装置SO2的排放浓度、排放速率以及无组织排放进行了规定和要求,规定SO2排放浓度限值为1200mg/m3。
2020版国家标准取消排放速率指标,只保留浓度指标。
对于硫磺产量小于200t/d的天然气净化厂,尾气浓度要求低于800mg/m3。
1.2 H2S排放标准《恶臭污染排放标准》(GB14554-1993)规定的H2S不同排气筒高度允许的排放量。
排气筒高度15m允许的H2S排放速率0.33kg/h,排气筒高度20m允许的H2S排放速率0.58kg/h。
《工作场所有害因素职业接触限值第1部分化学有害因素》(GBZ2.1-2007)规定了H2S 最高容许浓度为10 mg/m3。
天然气净化装置尾气H2S排放必须同时满足以上两个标准。
- 1、下载文档前请自行甄别文档内容的完整性,平台不提供额外的编辑、内容补充、找答案等附加服务。
- 2、"仅部分预览"的文档,不可在线预览部分如存在完整性等问题,可反馈申请退款(可完整预览的文档不适用该条件!)。
- 3、如文档侵犯您的权益,请联系客服反馈,我们会尽快为您处理(人工客服工作时间:9:00-18:30)。
分析硫磺回收尾气处理的工艺流程,对生产工艺设备的运行状况进行分析,保证各种硫磺回收设备安全运行,达到设计的作用效果。
同时,设计最佳的尾气处理方案,结合硫磺回收工艺的特点,强化对尾气的处理,使其中的二氧化硫的含量达到环保的标准,促使硫磺回收尾气处理达到更好的效果,满足硫磺回收工艺的技术要求。
1 硫磺回收尾气处理工艺流程
国产装置的应用,直接选择氧化硫磺回收装置进行硫磺回收和尾气的处理,设置具有等温和绝热效果的二级反应器,H2S与O2在催化剂作用下直接反应生成硫磺。
回收更多的硫磺,同时将尾气进行处理,优化尾气处理的生产工艺流程,对各个不同的生产单元进行控制,设计最佳的处理程序,促使尾气处理达到更高的标准。
1.1 氧化焚烧单元的生产工艺流程
硫磺回收装置来的含硫酸性气体进入焚烧炉,与燃料气和空气混合燃烧后,产生的高温烟气进入烟气冷却器冷却,温度达到230℃左右后去碱洗装置。
经碱洗装置脱硫后排入大气。
烟气冷却器产生的1.5MPa饱和蒸汽在空冷器冷凝后,返回烟气冷却器循环利用。
1.2 碱洗单元的生产工艺流程
焚烧后含硫烟气从洗涤塔底部进入,水洗降温除尘后从塔顶出至脱硫塔。
洗涤热水冷却降温后从洗涤塔上部送入,循环使用。
洗涤塔出来的烟气从脱硫塔底部进入,在塔中与从上而下喷淋的NaOH溶液在填料表面接触,将含硫烟气中SO2吸收脱除后,从塔顶直接排放大气。
吸收SO2的富液一部分从脱硫塔顶部返回脱硫塔循环使用,一部分调节塔底液位后送至氧化罐。
脱硫富液与新鲜的N a O H溶液在管道中混合,调节PH值后进入氧化罐,将溶液中的Na2SO3氧化成Na2SO4。
从氧化罐来的硫酸钠溶液直接进中和脱色罐,中和、脱色工作结束后,将溶液送入板框压滤机过滤,除去溶液中的固体杂质,硫酸钠溶液送入产品溶液池。
1.3 蒸发结晶单元的生产工艺流程
硫酸钠溶液经过两级预热器加热后,注入一效蒸发器。
在一效加热室和分离室内循环浓缩。
一部分浓缩液排入二效蒸发器,在二效加热室和分离室中循环,进一步浓缩达到过饱和,从而结晶出硫酸钠。
二效蒸发器的部分浓缩液送入增稠器沉降分离。
上层的清液溢流至母液罐,下层的浆液进入离心机脱水。
脱水后的Na2SO4晶体进入干燥机进行干燥,再由斗提机输送至料仓储存,并根据库存情况定期包装出料。
2 硫磺回收尾气处理工艺技术措施
设计最佳的硫磺回收尾气处理的方案,使其达到尾气处理的指标,并优选最佳的处理设备,加强对尾气处理设备的维护管理,延长硫磺回收工艺中尾气回收设备的安全运行周期,延长设备的检修时间,降低硫磺回收生产工艺尾气回收处理的成本,最大限度地提高硫磺回收系统的效率。
2.1 尾气处理的方案
尾气中需要脱除的酸性组分主要包括H2S、SO2和单质硫等,根据尾气气质情况初步筛选处理方案,将尾气中的部分二氧化硫及单质成分转化为硫化氢气体,经过加氢处理,并对硫磺溶液进行吸收提纯后,进入到硫磺回收装置。
也可以采取另一个处理方案,将尾气中的硫化物及单质硫转化为二氧化硫的焚烧工艺方案,结合湿法脱硫的技术措施,促使烟气的排放达标,碱液废水去下游的处理单元,进一步处理。
还可以选择第三个处理方案,将尾气中的硫化氢及二氧化硫都转换为单质硫,进行回收利用,也实现硫磺回收工艺尾气处理的效果。
通过对不同方案的技术原理、技术特点、应用范围、项目投资、运行情况等方面进行对比分析,并依据尾气特点,确定适合的尾气处理工艺为尾气焚烧,实施热力燃烧与烟气冷却回收中压蒸汽及NaOH碱洗脱硫的工艺技术措施。
对硫磺回收装置的尾气处理的指标进行分析,为了响应国家环保技术要求,履行社会安全环保的责任,提高SO2减排量,参考(GB 16297—1996)《大气污染物综合排放标准中排放浓度的要求,确定尾气处理装置设计SO2排放指标为960mg/m3。
达到尾气排放的标准,才能进行硫磺回收工艺的尾气排放,否则继续进行处理,直至达到排放标准为止。
2.2 尾气处理装置的选择及使用
净化厂尾气处理装置由尾气焚烧、碱洗脱硫装置组成。
为处理碱洗装置脱硫富液,建设蒸发结晶装置一套,集中处理碱洗富液,处理后产品硫酸钠外运,废水回用或回注。
实现尾气处理工艺的生产管理目标,加强对尾气处理装置的选择和使用,促使每个处理装置安全平稳运行,才能达到设计的处理能力,满足硫磺回收工艺尾气处理的需要。
选用30%wt的氢氧化钠溶液作为吸收液,在脱硫塔
硫磺回收尾气处理工艺技术措施
钟伟 张超 李刚 苏志浩
中国石油长庆油田分公司第一采气厂 陕西 榆林 718500
摘要:对石油化工生产过程中的硫磺回收的尾气处理工艺技术措施进行优化,选择直接氧化的实施工艺措施,结合尾气的单减法回收技术措施,解决硫磺尾气回收的技术难点问题,保证硫磺回收尾气的处理达到环保的标准,避免硫磺回收工艺的尾气导致环境污染事故,影响到石油化工生产的安全环保性能。
关键词:硫磺回收 尾气处理 工艺技术 措施
(下转第269页)
2.1 工程概况
在某地的中拐凸起火山岩油气藏的地质勘探中,勘探人员采用了土壤烃氧化菌检测、土壤吸附烃检测用于化学样品分析。
化学样品采样采用了均匀网格式的布样方式,网格密度为330m×330m,共采集样品1550个(地表约20cm深度土壤样品),单个样品的质量控制在200g及以上,其中土壤烃氧化菌检测负责测定土壤专属烃氧化菌的含量,土壤吸附烃检测则负责测试土壤吸附气的组成,前者可实现气藏的存在与分布判别,后者则能够判断下伏油气藏的性质。
2.2 具体应用
在土壤烃氧化菌检测中,勘探人员将异常门槛值定为50(专属烃氧化菌的含量MV),代表较高微渗漏强度,50以下则为较弱或无微渗漏强度(低异常和背景值),由此可确定全部微生物值的平均值、最大值、最小值、标准偏差分别为51、390、0、63,背景微生物值的平均值与标准偏差则分别为18、15。
微生物异常值分级使用五个颜色表示,分别为红色、橙色、黄色、绿色、蓝色,代表超高异常、高异常、中异常、低异常、无异常,微生物值含量区间分别为95~390、65~94、50~64、14~49、0~23,由此可得出图1所示的中拐凸起MV值平面分布示意图;在土壤吸附烃检测中,共选测SSG样品77个,由此可发现部分样品落在油区、大部分样品落到凝析油气区,因此工区油气藏具备油气并存兼有油的特征,且油气性质无明显差异。
结合检测结果开展综合评价,可完成有利区评价,复杂油气藏勘探、勘探有利区划分由此获得了有力支持,化学样品采集与分析对地质勘探的利用价值
也由此得到了证明。
图1 中拐凸起MV值平面分布示意图
3 结束语
综上所述,化学样品采集与分析对地质勘探具备较高利用价值,在此基础上,本文涉及的化学样品采集价值、化学样品分析价值、地质勘探实例分析等内容,则提供了可行性较高的化学样品采集与分析路径,而为了更好发挥化学样品采集与分析效用,地质、地球物理成果的融入必须得到重点关注。
参考文献
[1]李雪霏.地质勘探中化学样品的采集与分析[J].黑龙江科技信息,2017(7):43.
[2]孙春岩,赵浩,贺会策.海洋底水原位探测技术与中国南海天然气水合物勘探[J].地学前缘,2017,24(06):225-241.
[3]单铭洲.地质勘探中化学样品的采集与分析[J].科技风,2014(13):223.
内,吸收液与含硫尾气充分接触混合,尾气中的二氧化硫与吸收液中的氢氧化钠反应生成亚硫酸钠。
亚硫酸钠再与鼓入的空气进行氧化反应生成硫酸钠。
由于烟气中还含有大量的CO2,用NaOH溶液洗涤气体时,首先发生CO2与NaOH的反应,导致了吸收液pH的降低,且出现脱硫效率很低的现象。
随着时间的延长,pH降至7.6以下时,发生吸收SO2的反应。
随主要吸收剂Na2SO3的不断生成,SO2的脱除效率也不断升高。
当Na2SO3全部转变成NaHSO3时,吸收反应将不再发生,此时PH值降至4.4。
但随SO2通入PH值仍继续下降,此时pH值下降原因是由于SO2在溶液中的物理溶解。
因此,吸收液有效吸收SO2的pH范围必须控制在4.4~7.6之间。
2.2.3 氧化反应的过程
对吸收二氧化硫的过程进行分析,保证吸收塔内的吸收液能够更多地吸收二氧化硫,促使尾气中的二氧化硫的含量下降,才能使尾气达到环保标准的要求。
通过中和反应的过程,保持溶液的酸碱度达标,避免出现酸碱度的不平衡,而影响到酸气的吸收程度,影响到硫磺回收装置的尾气吸收效果。
最后是将烟气中的氧完全氧化处理,除去烟气中的有毒有害的成分,达到硫磺回收装置尾气处理的质量标准,获得更加结晶的尾气资源,达到硫磺回收装置尾气处理的目标。
3 结束语
通过对硫磺回收尾气处理工艺技术措施的探讨,硫磺回收的过程中采取直接氧化的方式,应用尾气回收的单碱法,达到最理想的处理效果。
保证硫磺回收的效率,并对尾气进行处理,满足环保的技术要求。
优化硫磺回收装置尾气处理的方案,选择最佳的处理系统和单元,通过最优的处理工艺流程,加速尾气反应的进行,获得最佳的尾气处理的质量标准,使其达到安全环保的指标。
参考文献
[1]杨叔杰. 降低硫磺回收装置烟气SO2排放浓度的建议[J]. 化工管理,2017(29).
[2]单宝贵,戴学海,衣凤城,等.CT6-4B硫磺回收催化剂的应用探讨[J]. 石油与天然气化工,41(5).
[3]李金金,黄黎明,何金龙,等.亚露点硫磺回收催化剂孔结构分析研究[J]. 石油与天然气化工,2013,42(3):211-215.
(上接第281页)。