硫磺回收装置工艺原理
硫磺回收系统的操作要求和工艺指标

一、制硫工艺原理硫磺回收系统的操作要求和工艺指标Claus制硫总的反应可以表示为:2H2S+02/X S x+2H20在反应炉内,上述反应是部分燃烧法的主要反应,反应比率随炉温变化而变化,炉温越高平衡转化率越高;除上述反应外,还进行以下主反应:2H2S+3O2=2SO2+2H2O在转化器中发生以下主反应:2H2S+SO23/XS x+2H2O由于复杂的酸性气组成,反应炉内可能发生以下副反应:2S+2CO2COS+CO+SO22CO2+3S=2COS+SO2CO+S=COS在转化器中,在300摄氏度以上还发生CS2和COS的水解反应:COS+H2O=H2S+CO2二、流程描述来自上游的酸性气进入制硫燃烧炉的火嘴;根据制硫反应需氧量,通过比值调节严格控制进炉空气量,经燃烧,在制硫燃烧炉内约65%(v)的H2S进行高温克劳斯反应转化为硫,余下的H2S中有1/3转化为SO2燃烧时所需空气由制硫炉鼓风机供给。
制硫燃烧炉的配风量是关键,并根据分析数据调节供风管道上的调节阀,使过程气中的H2S/SO2比率始终趋近2:1,从而获得最高的Claus转化率。
自制硫炉排出的高温过程气,小部分通过高温掺合阀调节一、二级转化器的入口温度,其余部分进入一级冷凝冷却器冷至160℃,在一级冷凝冷却器管程出口,冷凝下来的液体硫磺与过程气分离,自底部流出进入硫封罐。
一级冷凝冷却器管程出口160℃的过程气,通过高温掺合阀与高温过程气混合后,温度达到261℃进入一级转化器,在催化剂的作用下,过程气中的H2S和SO2转化为元素硫。
反应后的气体温度为323℃,进入二级冷凝冷却器;过程气冷却至160℃,二级冷凝冷却器冷凝下来的液体硫磺,在管程出口与过程气分离,自底部流出进入硫封罐。
分离后的过程气通过高温掺合阀与高温过程气混合后温度达到225℃进入二级转化器。
在催化剂作用下,过程气中剩余的H2S和SO2进一步转化为元素硫。
反应后的过程气进入三级冷凝冷却器,温度从246℃被冷却至1.60~C。
第十四章硫磺回收装置

第⼗四章硫磺回收装置第⼗四章硫磺回收装置第⼀节装置概况及特点⼀、装置概况硫磺回收装置是环保装置,它是洛阳分公司500万吨/年炼油⼯程主体⽣产装置之⼀。
该装置主要处理液态烃、⼲⽓脱硫酸性⽓及含硫污⽔汽提酸性⽓等,其产品是国标优等品⼯业硫磺。
⼆、装置组成及规模硫磺回收(Ⅰ)设计⽣产能⼒为3000t/a,1987年8⽉开⼯,2001年4⽉扩能改造⾄1.0×104t/a;硫磺回收(Ⅱ)设计⽣产能⼒为5650t/a,1997年9⽉开⼯,2000年3⽉扩能⾄1.0×104t/a。
三、⼯艺流程特点两套硫磺回收装置均采⽤常规克劳斯⼯艺,采⽤部分燃烧法,即将全部酸性⽓引⼊酸性⽓燃烧炉,按烃类完全燃烧和1/3硫化氢完全燃烧⽣成⼆氧化硫进⾏配风。
过程⽓采⽤⾼温外掺合、⼆级转化、三级冷凝、三级捕集,最终硫回收率达到93%以上。
尾⽓中硫化物及硫经尾⽓焚烧炉焚烧,70m烟囱排放。
第⼆节⼯艺原理及流程说明⼀、⼯艺原理常⽤制硫⽅法中根据酸性⽓浓度不同,分别采⽤直接氧化法、分流法和部分燃烧法。
本装置采⽤的是部分燃烧法,即将全部酸性⽓引⼊燃烧炉,按烃类完全燃烧和1/3硫化氢完全燃烧⽣成⼆氧化硫进⾏配风。
对于硫化氢来说,反应结果炉内约有65%的硫化氢转化为硫,余下35%的硫化氢中有1/3燃烧⽣成⼆氧化硫,2/3保持不变。
炉内反应剩余的硫化氢、⼆氧化硫在转化器内催化剂作⽤下发⽣反应,进⼀步⽣成硫,其主要反应如下:主要反应:燃烧炉内:H2S+3/2O2=H2O+SO2+Q 2H2S+ SO2= 2H2O+3/2S2+QH2S+CO2=COS+ H2O+Q 2H2S+CO2=CS2+2 H2O+Q反应器内:2H2S+SO2=H2O+3/nSOn+Q COS+ H2O = H2S+CO2-QCS2+ 2H2O=2H2S+CO2-Q为获得最⼤转化率,必须严格控制转化后过程⽓中硫化氢与⼆氧化硫的摩尔⽐为2:1。
⼆、⼯艺流程说明来⾃液态烃、⼲⽓脱硫装置酸性⽓及含硫污⽔汽提酸性⽓,压⼒0.05Mpa(表),温度40℃左右,硫化氢浓度30~90%(V),烃含量⼩于4%(V),在酸性⽓分液罐V101分液后进⾏⼊酸性⽓焚烧炉F101,所需空⽓由风机C101供给。
硫磺装置新职工培训课件

三、装置简介:
硫磺回收部分采用一级高温转化、两级催化转化的常规 克劳斯工艺。制硫燃烧炉采用烧氨火嘴,在1300℃左 右的温度下,将污水酸性气中的NH3全部转化为N2和 H2O,以达到污水汽提装置停开侧线、节能降耗的目 的。尾气处理部分的还原吸收工艺采用三维设计院开发 的 “SSR”工艺。设计硫磺回收部分的单程转化率为 95%,单程收率为97%,装置总硫收率为99.94%,焚 烧后尾气中SO2的浓度为486mg/m3。完全可以满足 大气污染物综合排放标准(GB16297-1996)的要求。
新职工培训教材
目 录:
一、硫磺车间简介 二、硫磺回收装置的作用 三、装置工艺简介及产品用途 四、物料性质 五、各装置的工艺原理及流程简述
一、硫磺车间简介:
硫磺回收装置是一套联合装置,包括:两套硫磺装 置(1万吨/年硫磺回收装置与2万吨/年硫磺回收装 置各一套)、两套60吨/小时的污水单塔低压汽提 装置、与2万吨/年的制硫相配套的尾气处理和溶剂 再生部分及100吨/小时胺液再生装置。
四氯化碳和苯 主要用途:用于制造染料、农药、火柴、火药、橡胶、
人造丝、医药等
4、催化剂:
项目 特性
外观形状 化学组成 堆密度 比表面积 抗压强度
磨耗 装填位置 装填量
LS-971 1、抗硫酸盐化中毒 2、高克劳斯活性和脱 “漏O”保护型双功能
催化剂
Φ4—6mm红褐色球形 AL2O3>80%、活性组
≤0.3 第二反应器 (AL2O3)10.3m3
五、工艺原理及流程简述:
1、硫磺装置工艺原理: Claus工艺的实质是部分氧化还原反应,其化
学反应式为: (1)2H2S+3O2=2H2S+2SO2+Q (2)2H2S+SO2=3/x Sx+2H2O+Q (1)与(2)又可写为: (3)2H2S+O2=2/x Sx+2H2O+Q
硫磺回收工艺
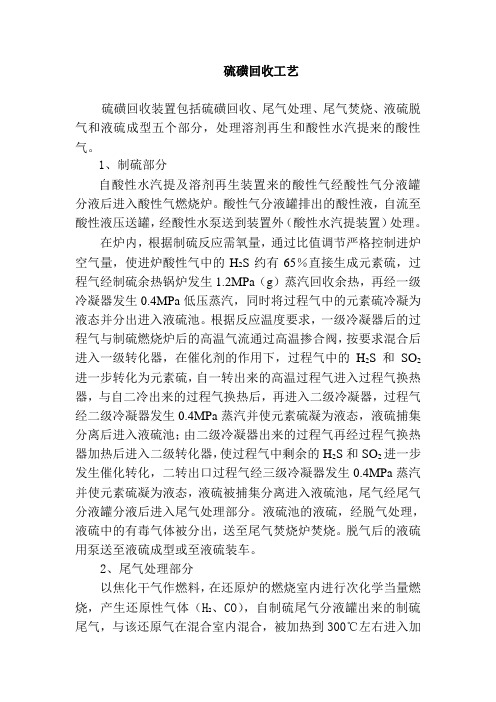
硫磺回收工艺硫磺回收装置包括硫磺回收、尾气处理、尾气焚烧、液硫脱气和液硫成型五个部分,处理溶剂再生和酸性水汽提来的酸性气。
1、制硫部分自酸性水汽提及溶剂再生装置来的酸性气经酸性气分液罐分液后进入酸性气燃烧炉。
酸性气分液罐排出的酸性液,自流至酸性液压送罐,经酸性水泵送到装置外(酸性水汽提装置)处理。
在炉内,根据制硫反应需氧量,通过比值调节严格控制进炉空气量,使进炉酸性气中的H2S约有65%直接生成元素硫,过程气经制硫余热锅炉发生1.2MPa(g)蒸汽回收余热,再经一级冷凝器发生0.4MPa低压蒸汽,同时将过程气中的元素硫冷凝为液态并分出进入液硫池。
根据反应温度要求,一级冷凝器后的过程气与制硫燃烧炉后的高温气流通过高温掺合阀,按要求混合后进入一级转化器,在催化剂的作用下,过程气中的H2S和SO2进一步转化为元素硫,自一转出来的高温过程气进入过程气换热器,与自二冷出来的过程气换热后,再进入二级冷凝器,过程气经二级冷凝器发生0.4MPa蒸汽并使元素硫凝为液态,液硫捕集分离后进入液硫池;由二级冷凝器出来的过程气再经过程气换热器加热后进入二级转化器,使过程气中剩余的H2S和SO2进一步发生催化转化,二转出口过程气经三级冷凝器发生0.4MPa蒸汽并使元素硫凝为液态,液硫被捕集分离进入液硫池,尾气经尾气分液罐分液后进入尾气处理部分。
液硫池的液硫,经脱气处理,液硫中的有毒气体被分出,送至尾气焚烧炉焚烧。
脱气后的液硫用泵送至液硫成型或至液硫装车。
2、尾气处理部分以焦化干气作燃料,在还原炉的燃烧室内进行次化学当量燃烧,产生还原性气体(H2、CO),自制硫尾气分液罐出来的制硫尾气,与该还原气在混合室内混合,被加热到300℃左右进入加氢反应器,在加氢催化剂的作用下进行加氢水解反应,将SO2、S X、CS2、COS等还原为H2S。
从尾气加氢反应器出来的气流经蒸汽发生器发生0.4MPa蒸汽回收热量后进入尾气急冷塔,与急冷水直接接触降温。
硫磺回收工艺原理
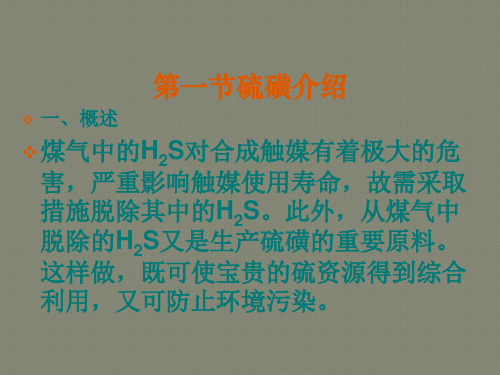
(四)硫循环法
当进料气中H2S含量在5%-10%甚至更低时可考虑采 用此法。它是将一部分液硫产品返回反应炉内,在另 一个专门的燃烧器中使其燃烧生成SO2,并使过程气 中H2S与SO2摩尔比为2。除此之外,流程中其它部 分均与分流法相似。
第一节硫磺介绍
❖ 一、概述
❖ 煤气中的H2S对合成触媒有着极大的危 害,严重影响触媒使用寿命,故需采取 措施脱除其中的H2S。此外,从煤气中 脱除的H2S又是生产硫磺的重要原料。 这样做,既可使宝贵的硫资源得到综合 利用,又可防止环境污染。
大约直到70年代初,主要只是从经济上 考虑是否需要进行硫磺回收。如果在经济上 可行,那就建设硫磺回收装置;如果在经济 上不可行,就把脱除的酸气燃烧后放空。但 是随着世界各国对环境保护的要求日益严格, 当前把煤气中脱除下来的H2S转化成硫磺, 不只是从经济上考虑,更重要的是出于环境 保护的需要。
第三节 工艺方法及流程
一、工艺方法选择 通常,克劳斯装置包括热反应、余热回收、硫冷凝、再 热及催化反应等部分。由这些部分可以组成各种不同的 克劳斯硫磺回收工艺,从而处理不同H2S含量的进料气。 目前,常用的工艺方法有直流法(部分燃烧法)、分流 法、硫循环法及直接氧化法等。不同工艺方法的区别在 于保持热平衡的方法不同。在这几种工艺方法的基础上, 又根据预热、补充燃料气等措施不同,派生出各种不同 的变型工艺方法,其适用范围见表3-1。
脱硫溶液再生所析出的含H2S酸气,大多进入克劳斯装置 回收硫磺。在酸气H2S浓度较低且硫量不大的情况下,也 可采用直接转化法在液相中将H2S氧化为元素硫。除此之 外,还可利用其生产一些硫的化工产品;将H2S转化为元 素硫及氢气具有更高的技术经济价值,因此其研究开发颇
硫磺回收工艺原理PDF

S2H S2H
�
述概、一 �
。要需的护保 境环于出 是的要重更 �虑考上济 经从是只不 �磺硫成化转S2H的来下除脱中气煤把前当
� 格 严 益 日 求要 的 护 保 境 环 对国 各 界 世 着 随 是 但。空放后烧燃气酸的除脱把就�行可不上 济经在果如�置装收回磺硫设建就那�行可 上济经在果如。收回磺硫行进要需否是虑考 上 济 经 从 是 只 要 主 � 初 代 年 07 到 直 约 大
�1-2�
氧S2H了发开sualC.F.C家学化国英年3881
:即,法方的硫制化
应反斯劳克、一
�2-2� lom/JK 9.815 + O2H+2OS== 2O+S2H �应反主下如有
)3-2(
lom/JK1.24 – O2H+2S== 2OS+S2H
�2OS成化氧S2H的3/1内炉烧燃即段应反热在
化催化氧是就来说单简法斯劳克谓所,�ssecorP
用应法斯劳克的后良改经。法方艺工种一的硫制
sualC�法斯劳克用采遍普磺硫收回中气酸从 �
理原本基收回磺硫法斯劳克 节二第 �
处制限于助借能只,度温应反的适合持维难很而热 放的强于由应反的典经一这,应反斯劳克称习式上
。率化转的%09�%08得获来量理 lom/JK502+O2H+NS== 2O+S2H
�应反多许�下况工�℃729于大�温高的内炉烧燃在 降下度温随则侧左�%07过超不常通但�高升步同度 。应反动推剂化催有需�升上率化转衡平而
。态状衡平于处已上际实应反的硫成生是其尤
温随率化转衡平�区应反温高为侧右的图�图意示衡 平的硫为化转S2H为1-2图�应反逆可为应反斯劳克
硫磺回收工艺原理

硫磺回收工艺原理
嘿,朋友们!今天咱们来聊聊硫磺回收工艺原理。
想象一下,这就好像是一场奇妙的化学魔术表演。
简单来说,硫磺回收工艺就像是一个精细的分拣过程。
在这个过程中,含有硫的气体就像是一群混杂的“小伙伴”。
我们要做的呢,就是把硫这个“调皮的家伙”给找出来,让它乖乖地变成硫磺。
首先,这些含硫的气体会进入一个特别的“魔法盒子”,也就是反应装置。
在这里,通过一系列化学反应,硫开始慢慢聚集起来。
这就好比大家在一个混乱的房间里,慢慢找到自己的队伍一样。
然后呢,聚集起来的硫就像小水滴汇聚成大水珠一样,逐渐形成硫磺。
这时候,我们就可以把这些硫磺收集起来啦,就像是把珍贵的宝贝放进小盒子里。
这个工艺原理虽然听起来有点复杂,但其实就是这么一回事。
它的作用可大啦,既可以减少硫对环境的污染,又能把硫变废为宝。
就好像我们把垃圾变成了有用的东西,多棒呀!所以说,硫磺回收工艺原理虽然有点神秘,但真的很有趣也很重要哦!大家这下是不是对它有了更清楚的了解呢?。
硫磺回收工艺原理

还原反应原理
在硫磺回收工艺中,还原反应是将硫 化氢转化为单质硫的过程,通常采用 铁、钴、镍等金属作为催化剂。
还原反应需要在低温、高压条件下进 行,同时需要控制反应温度和压力, 以实现最佳的还原效果。
排放标准来确定。
尾气处理设备应具备高效、低 能耗、环保等特点,同时要能
适应各种工况条件。
06
硫磺回收的优化与改进
提高硫磺回收率的方法
优化反应条件
通过调整反应温度、压力、气体组成等参数,提 高硫磺的回收率。
采用高效催化剂
选用高活性、高选择性的催化剂,降低副反应的 发生,提高硫磺的回收率。
优化工艺流程
2
该设备通常包含催化剂床层、加热器和冷却器等 部分,催化剂是其中的核心组件。
3
选择性催化还原设备应具备高效、低能耗、长寿 命等特点,同时要能适应各种工况条件。
尾气处理设备
尾气处理设备用于对硫磺回收 工艺中产生的尾气进行处理,
以符合环保要求。
常见的尾气处理方法包括脱 硫、除尘、脱硝等,具体处 理工艺应根据尾气的成分和
05
硫磺回收的设备与材料
燃烧炉设备
01
燃烧炉是硫磺回收工艺中的重要设备,用于将含硫气体中的硫 元素燃烧成硫磺。
02
燃烧炉通常采用高温燃烧技术,温度可达到1200℃左右,确保
含硫气体充分燃烧。
燃烧炉的设计应具备高效、稳定、安全等特点,同时要易于操
03
作和维护。
选择性催化还原设备
1
选择性催化还原设备是硫磺回收工艺中的关键设 备,用于在催化剂的作用下将含硫气体中的硫元 素还原成硫磺。
低浓度酸性气下硫磺回收装置存在的问题及对策

护,确保设备正常运行。ຫໍສະໝຸດ 腐蚀监测和防护02
采用在线腐蚀监测技术,对装置中的易腐蚀部位进行实时监测
,及时发现并处理腐蚀问题。
选择耐腐蚀材料
03
在装置设计和制造过程中,选择耐腐蚀性能好的材料,提高设
备的耐腐蚀性能。
04
案例分析
低浓度酸性气下硫磺回收装置的应用实例
某石化企业硫磺回收装置
该装置采用常规的克劳斯工艺,处理低浓度酸性气时存在硫回收率低、尾气排放 不达标等问题。
设备腐蚀和堵塞问题
酸性气体腐蚀设备
低浓度酸性气中的硫化氢等组分具有腐蚀性,会对设备造成腐蚀。
堵塞问题
酸性气中的杂质和反应产物可能导致设备堵塞,影响装置正常运行。
03
对策和建议
优化酸性气处理工艺
01
优化酸性气原料预处理
加强原料酸性气的脱水、脱重烃和脱有机硫等预处理,降低原料酸性气
中的水分、重烃和有机硫含量,提高硫磺回收装置的硫磺回收率。
02
改进酸性气燃烧炉技术
采用新型燃烧炉技术,提高酸性气的燃烧效率,降低燃烧过程产生的污
染物排放。
03
强化酸性气中硫化氢的提取
采用高效吸附剂或化学吸收剂,从酸性气中提取硫化氢,为硫磺回收装
置提供高浓度的硫化氢原料。
提高硫磺回收率的技术改进
优化硫磺冷凝器设计
改进硫磺冷凝器的换热面积和冷却水设计,提高硫磺的冷凝效率 和回收率。
能耗高
环保问题
为了提高硫磺回收效率,需要提高装置的 运行温度和压力,导致装置能耗增加,运 行成本上升。
在硫磺回收过程中,会产生大量的酸性废 水,处理难度较大,对环境造成一定的污 染。
未来硫磺回收装置的发展方向和趋势
硫磺回收工艺原理(原创)

硫磺回收工艺原理1、硫磺回收的原料是来自溶剂再生和酸性水汽提来的酸性气,其目标组分是其中的H2S。
2、在酸性气燃烧炉中,H2S燃烧生成SO2,H2S与SO2反应生成S。
3、因为H2S的燃点为260℃,因此,酸性气进火焰正常)允许,酸性气完全可以不用预热。
燃烧炉之前有必要进行预热,但当燃烧炉热量过剩(温度偏高)或工况允许(火焰正常)。
4、H2S在燃烧炉内400℃时可以正常燃烧,H2S和SO2在燃烧炉内高于630℃时就可以顺利反应;由于NH3的分解温度要求较高,在1100℃时分解90%,在1200℃时分解100%,但在实际工业炉内,因为其它介质的影响,燃烧炉温度要控制在1250℃才能使NH3完全分解,所以燃烧炉的温度比较高。
5、在燃烧炉出口的过程气,经过余热锅炉、三级冷凝器后,在转化反应器内继续反应,但是因为温度有所降低,所有必须在有催化剂的条件下进行,H2S 与SO2反应生成S。
6、液硫在130~160℃的流动性最好,因此各级冷凝器的冷后温度尽量控制在这个范围。
但为了满足一二级反应器的温度要求,工艺中设置了高温掺合阀,用来控制反应器的入口温度。
7、制硫部分回收了原料气中大约95%的S,尾气中除含部分H2S或SO2外,还有一部分COS,CS2等组分。
加氢反应的作用就是将SO2、COS、CS2等转化为H2S。
经过冷却、吸收,H2S被循环胺液吸收送回溶剂再生系统. 8、被吸收的尾气中残留的S则进入尾气焚烧炉(炉膛温度650~700℃),以SO2的形式,最后排入烟囱。
排放指标为SO2≯960mg/m3(或270kg/h)。
9、制硫转化反应器和尾气加氢反应器的反应温度到底控多少,一般要有催化剂的性能来确定。
超级克劳斯硫磺回收工艺
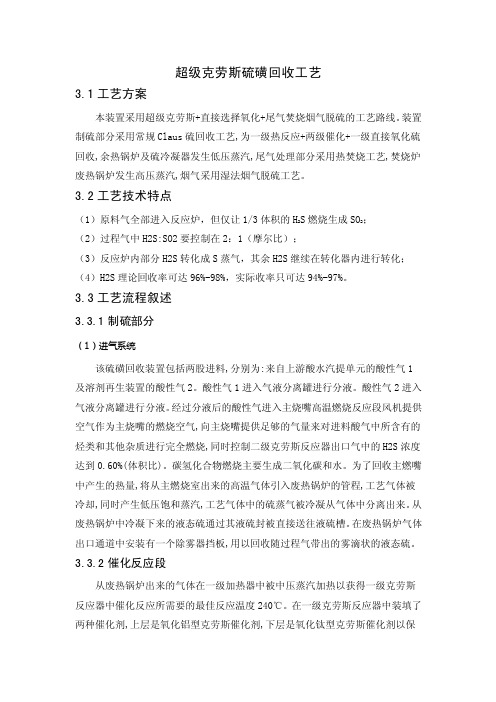
超级克劳斯硫磺回收工艺3.1工艺方案本装置采用超级克劳斯+直接选择氧化+尾气焚烧烟气脱硫的工艺路线。
装置制硫部分采用常规Claus硫回收工艺,为一级热反应+两级催化+一级直接氧化硫回收,余热锅炉及硫冷凝器发生低压蒸汽,尾气处理部分采用热焚烧工艺,焚烧炉废热锅炉发生高压蒸汽,烟气采用湿法烟气脱硫工艺。
3.2工艺技术特点(1)原料气全部进入反应炉,但仅让1/3体积的H2S燃烧生成SO2;(2)过程气中H2S:SO2要控制在2:1(摩尔比);(3)反应炉内部分H2S转化成S蒸气,其余H2S继续在转化器内进行转化;(4)H2S理论回收率可达96%-98%,实际收率只可达94%-97%。
3.3工艺流程叙述3.3.1制硫部分(1)进气系统该硫磺回收装置包括两股进料,分别为:来自上游酸水汽提单元的酸性气1及溶剂再生装置的酸性气2。
酸性气1进入气液分离罐进行分液。
酸性气2进入气液分离罐进行分液。
经过分液后的酸性气进入主烧嘴高温燃烧反应段风机提供空气作为主烧嘴的燃烧空气,向主烧嘴提供足够的气量来对进料酸气中所含有的烃类和其他杂质进行完全燃烧,同时控制二级克劳斯反应器出口气中的H2S浓度达到0.60%(体积比)。
碳氢化合物燃烧主要生成二氧化碳和水。
为了回收主燃嘴中产生的热量,将从主燃烧室出来的高温气体引入废热锅炉的管程,工艺气体被冷却,同时产生低压饱和蒸汽,工艺气体中的硫蒸气被冷凝从气体中分离出来。
从废热锅炉中冷凝下来的液态硫通过其液硫封被直接送往液硫槽。
在废热锅炉气体出口通道中安装有一个除雾器挡板,用以回收随过程气带出的雾滴状的液态硫。
3.3.2催化反应段从废热锅炉出来的气体在一级加热器中被中压蒸汽加热以获得一级克劳斯反应器中催化反应所需要的最佳反应温度240℃。
在一级克劳斯反应器中装填了两种催化剂,上层是氧化铝型克劳斯催化剂,下层是氧化钛型克劳斯催化剂以保证COS和CS2在催化床层下部进行水解反应。
一级克劳斯反应器入口温度通过进入一级加热器的中压蒸汽流量来进行调节控制。
硫磺回收装置尾气吸收单元运行总结

硫磺回收装置尾气吸收单元运行总结硫磺回收装置尾气吸收单元是工业生产中用来收集和处理硫磺尾气的重要设备。
其主要功能是通过吸收、净化和回收处理,将含硫废气中的硫元素分离提纯,以达到环境保护、资源回收和减少对大气污染的效果。
在企业生产中,为了确保尾气吸收单元的正常运行,提高硫磺回收效率,提升工作效益,我们对尾气吸收单元的运行情况进行了总结。
一、工作原理尾气吸收单元是硫磺回收装置的核心部件,主要包括吸收塔、冷凝器、分离器、废水处理系统等组成。
其工作原理是将含硫废气引入吸收塔中,通过底部的吸收液喷淋,使硫化氢、二硫化碳等硫化物溶解在吸收液中,再通过冷凝器对含硫吸收液进行冷却升华再结晶,分离出硫磺,最后进行干燥处理,回收产出硫磺。
吸收过程中所产生的废水也需要通过后续的废水处理系统进行处理达标排放。
二、运行总结1.设备状态监测尾气吸收单元的运行状态直接影响硫磺回收效率和安全生产,所以设备状态监测是非常重要的。
通过设备在线监测系统,及时了解吸收塔、冷凝器、废水处理系统等组件的运行情况,确保单元设备运行稳定可靠。
2.操作维护管理为了确保尾气吸收单元的长期稳定运行,必须进行科学的操作维护管理。
对吸收液的浓度、温度、压力等参数进行监测和调节,及时对设备进行清洗、维护保养以确保设备的正常运行。
3.安全生产管理硫磺回收装置尾气吸收单元在运行中需要严格遵守安全操作规程,对设备进行定期检查、维护,及时排除设备隐患,及时处理设备故障和事故,确保安全生产。
对操作人员进行安全培训,提高操作技能,增强安全生产意识。
4.环境保护管理尾气吸收单元在运行中会产生大量的废水,对排放废水进行处理是非常重要的。
需要对废水进行脱硫脱硝处理,达到排放监测标准。
并且要将硫磺回收后产出的硫磺进行综合利用,达到资源回收和环境保护的目的。
5.技术改进随着科技的不断发展,对尾气吸收单元进行技术改进是提高硫磺回收效率和降低生产成本的重要手段。
可以通过优化设计、更新设备和工艺,提高设备的吸收效率和废水处理效果。
天然气净化硫磺回收原理

天然气净化硫磺回收原理
天然气净化硫磺回收的原理主要包括以下步骤:
1. 硫磺回收装置尾气中的非H2S的含硫化合物如SO2、COS、CS2、S等被还原性气体(如氢气)还原为H2S。
2. 通过MDEA溶液将H2S吸收并解吸,最后返回到硫磺回收装置的酸性气燃烧炉,进一步回收硫磺。
3. 从吸收塔顶排出的尾气仅含有微量的硫化物,通过焚烧炉高温焚烧后排入大气。
烟气中SO2的排放量及排放浓度满足《大气污染物综合排放标准》以及《恶臭污染物综合排放标准》的排放要求。
此外,为了降低有机硫的生成量,可以采取一些措施,如减少酸气中烃类含量、提高燃烧炉温度、选择合适催化剂类型以及保持较高的加氢水解反应温度等。
以上信息仅供参考,如有需要,建议您咨询化学领域专业人士或查阅化学相关书籍。
- 1、下载文档前请自行甄别文档内容的完整性,平台不提供额外的编辑、内容补充、找答案等附加服务。
- 2、"仅部分预览"的文档,不可在线预览部分如存在完整性等问题,可反馈申请退款(可完整预览的文档不适用该条件!)。
- 3、如文档侵犯您的权益,请联系客服反馈,我们会尽快为您处理(人工客服工作时间:9:00-18:30)。
第二节 相关物质性质及危害
毒性危害
硫化氢
是一种强烈的神经毒物,无色、
影
响
有臭鸡蛋味,高浓度或低浓度 可察觉气味的最低浓度
下长期接触往往会硫化氢使人
难以觉察的微弱气味 可觉察气味
失去嗅觉,属高度危险物质,
气味难闻 8小时最大允许浓度
空气中最高允许浓度10mg/m3。
工作天数 1小时后眼睛和呼吸系统
H2S属于极毒物。用象臭鸡蛋味
Байду номын сангаас
第四节 CLAUS法工艺的热力学基础
低温催化反应 •在燃烧炉后续的(多级)转化反应器内,按下式所示在催化剂 床层中进行低温催化反应。
•从理论上讲,反应温度愈低则转化率愈高。 •实际上由于受单质硫露点温度的影响,催化转化反应的温 度一般控制在170~350℃之间。使用一个转化器(一级转化) 时,硫的总回收率只能局限在75%~ 90%的范围内。 •工业上一般采用增加转化器数目,并在两级转化器之间设 置硫冷凝器分离液硫,以及逐级降低转化器温度等措施,促 使此反应的平衡尽可能向右移动而使总硫回收率提高至97% 以上。
第四节 CLAUS法工艺的热力学基础
2.基本CLAUS反应
理论计算
A条件:纯O2+纯H2S
最终温度:4760℃
B条件:纯O2+1/3H2S→H2O、SO2、H2S 最终温度:
2593℃
C条件:纯O2+1/3H2S→H2O、S2
最终温度:2471℃
D条件:空气+纯H2S
最终温度:1860℃
E条件:空气+1/3H2S→H2O、SO2、H2S 最终温度:
1、自由火焰及其周围的高温反应区内,有少量的CH4被氧化 而生成CO和H2,并消耗一定量的O2。与此同时,有部分CH4 也会与H2O反应而生成CO和H2。上述这两个反应是燃烧炉内 生成CO和H2的主要(副)反应。
2、任何在自由火焰区内未被氧化掉的CH4,将在燃烧炉内转 化为CS2、COS、CO、CO2和C(烟炱),这是炉内生成有机硫 化合物的主要(副)反应。研究表明,在燃烧炉的反应条件下由 CO/CO2不可能生成CS2,后者是通过烃类与S2和/或H2S的反 应生成。因此,当原料酸气中烃类含量较高而不能在自由火焰 区内完全被燃烧(或氧化)掉时,过程气中CS2的生成率将增加。
1443℃
F条件:空气+1/3H2S→H2O、S2 最终温度:1349℃
第四节 CLAUS法工艺的热力学基础
由上述反应热力学条件比较分析可以得出: (1)燃烧炉温度超过1500℃后耐火材料的选择非常困难,故 常规克劳斯工艺均选择空气作为氧化剂。 (2)计算结果表明反应条件F此条件下最高可能达到的反应温 度为1349℃。 (3)原料酸气中的H2S浓度(或分压)是决定燃烧炉温度的关键 因素,燃烧炉温度将随原料酸气中H2S浓度的增加而升高。 (4)氧化剂中的O2浓度是影响燃烧炉温度的另一个重要因素, 随着氧气浓度的提高,炉温将急剧上升,从而为贫酸气制硫、 氧基硫磺回收等新工艺的开发奠定了理论基础。
• 硫化氢是一种无机化合物,化学式为H2S。 • 正常情况下是一种无色、易燃的酸性气体,浓度
低时带恶臭,气味如臭蛋;浓度高时反而没有气 味(因为高浓度的硫化氢可以麻痹嗅觉神经)。 • 硫化氢是一种急性剧毒,甚至高于氰化物。吸入 少量高浓度硫化氢可于短时间内致命。低浓度的 硫化氢对眼、呼吸系统及中枢神经都有影响。
ppm(体积)
0.14 0.77 4.6 7.0 10
50~100 70~120 170~255 200~300 350~500 400~600 500~700
700 700~1000 大于1000
第二节 相关物质性质及危害
毒性危害
H2S的局部刺激作用,是由于接触湿润粘膜与钠离子形 成的硫化钠引起的
返回
第五节 硫蒸汽对CLAUS反应的影响
一、反应温度与转化率的关系
1、火焰反应区内H2S的转化率 随温度升高而增加;催化反应 区内H2S的转化率随温度降低 而迅速增加
2、随着温度降低反应速率也 逐渐变慢,温度低于350℃时 的反应速率已不能满足工业要 求,必须使用催化剂加速反应, 以求在尽可能低的温度下达到 尽可能高的转化率
第五节 硫蒸汽对CLAUS反应的影响
一、反应温度与转化率的关系
3、从平衡关系式看,O2的化学当量过剩不能提高转化率, 因为多余的O2将与H2S反应生成SO2。但提高空气中的O2 含量和酸气中的H2S含量则有利于提高转化率。
4、降低过程气中硫蒸气分压有利于平衡向右边移动,且硫 蒸气本身又远比其他组分容易冷凝,这就是在两级转化器之 间设置硫冷凝器的原因。从过程气中分离硫蒸气后也相应地 降低了硫露点,从而使下一级转化器在更低的温度下操作。
4、对反应催化剂的影响。 使催化剂中毒,丧失活性。
第一节 建设硫磺回收装置的意义
三、硫磺回收的意义
• 1、环保意义 我国《大气污染物综合排放标准》(GB 16297-1996)对 新产生污染源SO2的最高允许排放质量浓度为960mg/m3。
• 2、社会效益 对炼油企业来说,减少硫的损失是体现企业提高油品质量后 生产管理水平的一个重要标志
第2阶段:催化反应阶段,即剩余的2/3体积H2S在催化剂 作用下与生成的SO2继续反应生成元素硫。
返回
第三节 CLAUS法工艺的发展过程
酸性气
硫回收单元
尾气加氢单元
尾气焚烧单元
尾气吸收单元
溶剂再生单元
第四节 CLAUS法工艺的热力学基础
一、CLAUS反应与温度的关系 1.高温热反应与低温催化反应 高温热反应 •酸性气体中的硫化氢首先在无催化剂存在的条件下,在反 应炉内与空气进行燃烧反应。 •反应能达到的温度与酸性气体中的硫化氢含量有关,含量 愈高则温度愈高,通常炉温都应保持在920℃以上,否则火 焰不稳定。 •燃烧炉内进行化学反应速度甚快,一般在l s以内即可完成 全部反应,H2S转化为单质硫的理论转化率可达60%~75 %。
第四节 CLAUS法工艺的热力学基础
二、燃烧炉内高温热反应的复杂性
第四节 CLAUS法工艺的热力学基础
三、燃烧炉内的主要反应
第四节 CLAUS法工艺的热力学基础
四、燃烧炉可能发生的副反应
第四节 CLAUS法工艺的热力学基础
四、燃烧炉可能发生的副反应
第四节 CLAUS法工艺的热力学基础
四、燃烧炉可能发生的副反应
第六节 燃烧炉内化学反应的机理
二、CH4的氧化反应与CO、H2及有机硫化合物的生成
第六节 燃烧炉内化学反应的机理
三、燃烧炉温度的主要影响因素
工业装置上燃烧炉(理论上)能达到的最高温度确实与原 料酸气中H2S浓度有关,但更重要的是与炉内过程气的组 成有关。因此,燃烧炉温度首先是取决于过程气中 H2S/O2的比例,从而奠定了富氧克劳斯工艺的理论基础。 同时,也与燃烧器及炉内的H2和CO生成量、H2S/SO2转 化为S2的量以及炉内出现的诸多反应之间的动力学控制因 素有关。
0.23
孤岛
85.12
11.61
2.09
0.43
辽河
85.86
12.65
-
-
伊朗(轻质)
85.14
13.13
-
-
美国(堪萨斯)
84.20
13.00
1.90
0.45
俄罗斯
83.90
12.30
2.67
0.33
墨西哥
84.20
11.40
3.60
-
(C+H)% 99.60 98.46 99.07 96.73 98.51 98.27 97.20 96.20
一、石油中的含硫化合物
1、石油及其馏分中的硫分布 高硫石油 含硫石油 低硫石油
2、硫在石油及其馏分中的存在形态 活性硫化物 非活性硫化物
第一节 建设硫磺回收装置的意义
原油名称
C%
H%
S%
N%
大庆
85.87
13.73
0.1
0.16
胜利
86.26
12.20
0.8
0.41
大港
85.67
13.40
0.12
第五节 硫蒸汽对CLAUS反应的影响
二、不同温度下硫组分的形态分布 1、气相状态的单质硫存在多个形态〔或分子结构),且 在不同温度下气相中平衡的硫组分间的形态分布是不同 的。 2、一般而言,当反应温度高于900K时气相中硫主要是 以S2的形态存在;而当温度低于700K则主要以S6、S8的 形态存在。由此可以看出,克劳斯法工艺过程气的组成 实际上是十分复杂的,一般情况下它将包括H2S、SO2、 CO2、H2O、H2,CO、COS、CS2、S2、S6、S8、N2 组分等。
返回
第六节 燃烧炉内化学反应的机理
一、燃烧炉内氧化反应的次序及历程
克劳斯装置(主)燃烧器及燃烧炉内物质被氧化的次序大致为: H2S是燃烧速度最快的,故首先被烧掉;NH3则是很难被氧 化而分解的物质,燃烧速度较慢,因而最后被烧掉。
第六节 燃烧炉内化学反应的机理
二、CH4的氧化反应与CO、H2及有机硫化合物的生成
第二节 相关物质性质及危害
三、硫磺性质
•硫是一种非常常见的无味无嗅的非金属,纯的硫是黄色的晶 体,又称做硫磺。 •纯的硫呈浅黄色,质地柔软,硫燃烧时的火焰是蓝色的,并 散发出一种特别的硫黄味(二氧化硫的气味)。硫不溶于水但 溶于二硫化碳。 •硫在工业中很重要,比如作为电池中或溶液中的硫酸。硫被 用来制造火药。在橡胶工业中做硫化剂。硫还被用来杀真菌, 用做化肥。硫化物在造纸业中用来漂白。硫酸盐在烟火中也有 用途。硫酸镁可用做润滑剂,被加在肥皂中和轻柔磨砂膏中, 也可以用做肥料。 •在工业中,最重要的硫的化合物是硫酸。硫酸是所有工业过 程中必不可少的一个原材料,因此硫酸的消耗量被看做是一个 国家工业化程度的一个指标。