胶合板工艺缺陷原因及解决方法
影响胶合板质量的因素

阻燃胶合板已经成为了工装不可少的原材料,因此胶合板的质量好坏影响到整体的工装质量,那么,影响胶合板质量的因素有哪些呢?
一,胶粘剂
生产中使用的胶粘剂有足够的胶合强度,胶粘剂分配比合理,调制出的胶粘剂功能安稳,粘度合适,有足够长的活性期才能确保正常操作和成品各项目标符合要求。
二,单板质量
单板质量要在单板旋切工序给与重视,要很好地进行木材软化处理,控制好旋切条件,同时注意单板含水率与平整度。
三,胶合强度
应该注意掌握好施胶量,胶量过大,成本高,胶层过厚,容易投胶,胶量过小,胶层不完整,。
胶合板生产工艺对产品质量的影响

抗拉强度均应符合要求 。但由于各 合理调整 ,如表 1 。
种因素的影响 ,致使每次抽检的旋
通过上述对工艺的合理调整 、
表 1 单板旋切过程中常见的缺陷产生原因和改进方法
缺陷名称
产生原因
改进方法
11 装刀高度过高 。
21 后角过大 ,对木段发生“切入”作
用。
单板厚度超出误差规 31 辅助滑道倾斜度不当 。 定 (外圈单板厚 ,里圈 41 主滑道磨损呈马鞍形 。 变薄)
5
林业科技通讯 FOREST SCIENCE AND TECHNOLO GY 2000·6
Acade mic Field 学术园地
缺陷名称
表 3 胶合过程中产生的缺陷和改进方法 产生原因
改进方法
大开胶边角脱胶
11 胶合剂变质 。 21 胶层的固化不足 。 31 胶料的水分太多 。 41 边角上的胶已干固 。 51 边角缺胶 。 61 单板含水率太高 。 71 每格合板坯边角未对齐或板坯装压机时歪斜 ,
缝 ,缝隙不严等缺陷 ,尚待改进 。现 根据实际工作经验 ,提出一些改进 方法 ,见表 2 。
3 涂胶 、热压
40 %) 。这不仅降低了半成品质量 ,
合板的胶合 ,是把单板涂胶组
又直接影响了合板质量 ,因为单板 成的板坯在一定温度 ,一定压力下
含水率偏高 ,导致合板开胶 、鼓泡 。 使胶层凝固胶粘 ,牢固地把单板胶
61 油刀后产生紧边 。 11 木段外圆粘附泥沙 、崩伤 、刀刃
有细小崩口或卷刃 。
21 刀不锋利 ,油刀不够 。 31 压尺安装不正确 、压榨程度不
够。
41 木段软化程度不够 。 11 旋切软材树种刀钝 、刃口不锋
利 、油刀不够 。
胶合板常见质量缺陷分析与控制
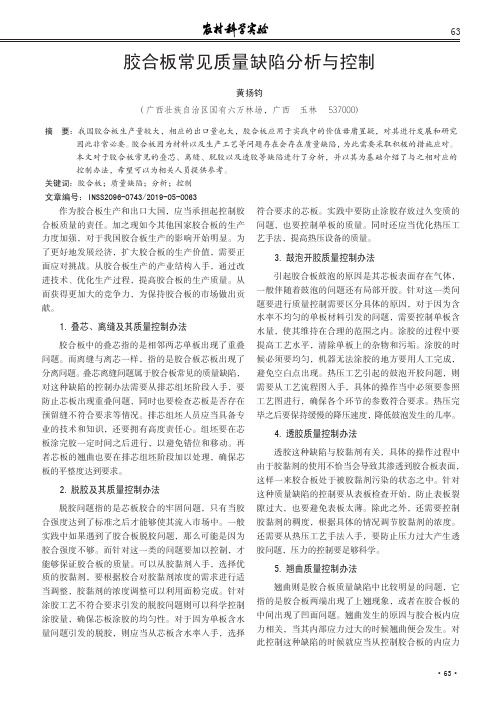
·63·作为胶合板生产和出口大国,应当承担起控制胶合板质量的责任。
加之现如今其他国家胶合板的生产力度加强,对于我国胶合板生产的影响开始明显。
为了更好地发展经济,扩大胶合板的生产价值,需要正面应对挑战。
从胶合板生产的产业结构入手,通过改进技术、优化生产过程,提高胶合板的生产质量。
从而获得更加大的竞争力,为保持胶合板的市场做出贡献。
1.叠芯、离缝及其质量控制办法胶合板中的叠芯指的是相邻两芯单板出现了重叠问题。
而离缝与离芯一样,指的是胶合板芯板出现了分离问题。
叠芯离缝问题属于胶合板常见的质量缺陷,对这种缺陷的控制办法需要从排芯组坯阶段入手,要防止芯板出现重叠问题,同时也要检查芯板是否存在预留缝不符合要求等情况。
排芯组坯人员应当具备专业的技术和知识,还要拥有高度责任心。
组坯要在芯板涂完胶一定时间之后进行,以避免错位和移动。
再者芯板的翘曲也要在排芯组坯阶段加以处理,确保芯板的平整度达到要求。
2.脱胶及其质量控制办法脱胶问题指的是芯板胶合的牢固问题,只有当胶合强度达到了标准之后才能够使其流入市场中。
一般实践中如果遇到了胶合板脱胶问题,那么可能是因为胶合强度不够。
而针对这一类的问题要加以控制,才能够保证胶合板的质量。
可以从胶黏剂入手,选择优质的胶黏剂,要根据胶合对胶黏剂浓度的需求进行适当调整,胶黏剂的浓度调整可以利用面粉完成。
针对涂胶工艺不符合要求引发的脱胶问题则可以科学控制涂胶量,确保芯板涂胶的均匀性。
对于因为单板含水量问题引发的脱胶,则应当从芯板含水率入手,选择符合要求的芯板。
实践中要防止涂胶存放过久变质的问题,也要控制单板的质量。
同时还应当优化热压工艺手法,提高热压设备的质量。
3.鼓泡开胶质量控制办法引起胶合板鼓泡的原因是其芯板表面存在气体,一般伴随着鼓泡的问题还有局部开胶。
针对这一类问题要进行质量控制需要区分具体的原因,对于因为含水率不均匀的单板材料引发的问题,需要控制单板含水量,使其维持在合理的范围之内。
竹帘胶合板表面质量缺陷及影响因素的分析
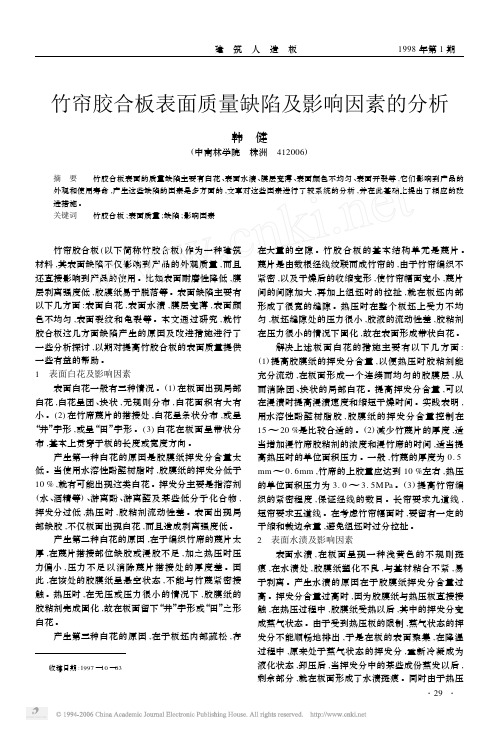
收稿日期:1997—10—03竹帘胶合板表面质量缺陷及影响因素的分析韩 健(中南林学院 株洲 412006)摘 要 竹胶合板表面的质量缺陷主要有白花、表面水渍、膜层变薄、表面颜色不均匀、表面开裂等,它们影响到产品的外观和使用寿命,产生这些缺陷的因素是多方面的,文章对这些因素进行了较系统的分析,并在此基础上提出了相应的改进措施。
关键词 竹胶合板;表面质量;缺陷;影响因素 竹帘胶合板(以下简称竹胶合板)作为一种建筑材料,其表面缺陷不仅影响到产品的外观质量,而且还直接影响到产品的使用。
比如表面耐磨性降低,膜层剥离强度低,胶膜纸易于脱落等。
表面缺陷主要有以下几方面:表面白花,表面水渍,膜层变薄,表面颜色不均匀,表面裂纹和龟裂等。
本文通过研究,就竹胶合板这几方面缺陷产生的原因及改进措施进行了一些分析探讨,以期对提高竹胶合板的表面质量提供一些有益的帮助。
1 表面白花及影响因素表面白花一般有三种情况。
(1)在板面出现局部白花,白花呈团、块状,无规则分布,白花面积有大有小。
(2)在竹席蔑片的搭接处,白花呈条状分布,或呈“井”字形,或呈“田”字形。
(3)白花在板面呈带状分布,基本上贯穿于板的长度或宽度方向。
产生第一种白花的原因是胶膜纸挥发分含量太低。
当使用水溶性酚醛树脂时,胶膜纸的挥发分低于10%,就有可能出现这类白花。
挥发分主要是指溶剂(水、酒精等)、游离酚、游离醛及某些低分子化合物,挥发分过低,热压时,胶粘剂流动性差。
表面出现局部缺胶,不仅板面出现白花,而且造成剥离强度低。
产生第二种白花的原因,在于编织竹席的蔑片太厚,在蔑片搭接部位缺胶或浸胶不足,加之热压时压力偏小,压力不足以消除蔑片搭接处的厚度差。
因此,在该处的胶膜纸呈悬空状态,不能与竹蔑紧密接触。
热压时,在无压或压力很小的情况下,胶膜纸的胶粘剂完成固化,故在板面留下“井”字形或“田”之形白花。
产生第三种白花的原因,在于板坯内部疏松,存在大量的空隙。
竹胶合板的基本结构单元是蔑片。
胶合板来料改善报告

胶合板来料改善报告以胶合板来料改善报告为题,本文将对胶合板来料进行改善分析,并提出相应的建议。
一、胶合板的重要性胶合板是一种由多层木材胶合而成的板材,具有高强度、耐湿性和稳定性等优点,被广泛应用于家具、建筑和装饰等领域。
胶合板来料的质量和性能直接影响到最终产品的质量和使用寿命。
二、胶合板来料存在的问题1. 尺寸不准确:部分胶合板来料尺寸不准确,导致安装困难,影响最终产品的外观和稳定性。
2. 质量不稳定:胶合板来料的质量波动较大,有些板材存在开裂、脱胶等问题,给生产过程带来一定的风险。
3. 粘结强度不足:部分胶合板来料的胶水粘结强度不足,容易出现脱胶现象,影响产品的使用寿命。
三、改善措施及建议1. 优化供应链管理:与供应商建立长期稳定的合作关系,并要求供应商提供高质量的胶合板来料。
加强对供应商的质量监控,确保胶合板来料符合标准要求。
2. 严格质量检验:建立完善的质量检验流程,对胶合板来料进行全面的尺寸和质量检测。
对不合格的来料进行退货或返工处理,确保只有合格的胶合板进入生产环节。
3. 强化工艺控制:优化生产工艺,提高胶合板的粘结强度。
控制好胶水的使用量和涂布均匀度,确保每块胶合板的质量一致。
4. 加强员工培训:提高员工对胶合板来料质量的认知和重视程度,加强对质量检验标准的培训,提高员工的技术水平和质量意识。
5. 建立反馈机制:与客户建立良好的沟通渠道,及时了解客户的需求和反馈,根据客户的反馈及时调整和改进胶合板来料的质量和性能。
四、改善效果评估通过以上改善措施的实施,可以预期以下效果:1. 胶合板来料的尺寸精度得到提高,有利于产品的加工和安装,提高产品的外观和稳定性。
2. 胶合板来料的质量稳定性得到保障,减少了生产过程中的风险和损失。
3. 胶合板的粘结强度得到提高,减少了脱胶现象的发生,延长了产品的使用寿命。
4. 客户满意度得到提升,建立了良好的合作关系,为企业带来更多的业务机会和口碑宣传。
通过对胶合板来料的改善分析和相应的改善措施,可以提高胶合板来料的质量和性能,进一步提升产品的质量和竞争力。
竹胶板模板存在的主要问题及解决方法

[质量]竹胶板模板存在的主要问题及解决方法竹胶板, 模板, 解决竹胶板模板由于具有幅面大、强度高、防水、耐磨、表面光滑、易脱模、拆模快、混凝土表面平整、反复使用率高、成本低等优点,被列入建筑业重点推广的10项新技术中。
它又是实行以竹代木的重要环节,它的发展有利于我国森林资源的保护,符合我国森林资源可持续发展的战略。
近几年,竹胶板模板生产线虽在不断增加,但由于种种原因,其销售量及应用范围都一直未能扩大。
1、竹胶板模板生产的现状由于竹胶合板模板有巨大的市场潜力,各地纷纷上马竹胶板生产线。
目前国内竹胶板生产线达70多条,实际年产量已超过2000万m2,不少生产厂还在准备扩建生产线。
福建、浙江、安徽、四川、重庆等地也在新建生产线,加上国家禁伐天然林政策的实施,原来的木胶合板生产企业很多可能转产竹胶板。
国外的木胶合板已开始输入中国;国内新型模板材料的出现将与竹胶板争夺市场,因此,竹胶板模板面临的竞争压力越来越大。
为降低成本,许多厂不惜以牺牲质量为代价,盲目改变生产工艺,使近几年竹胶板模板的质量急剧下降。
由于竹胶板质量无法满足钢框竹胶板模板对周转次数和厚度公差的要求,许多原来生产钢框竹胶合板模板的企业,不得不重新采用钢板作面板。
这是竹胶板模板的倒退,也使新型模板的推广应用再次面临挑战。
2、当前竹胶板模板存在的主要问题及原因(1)厚度公差问题无论是作为钢框竹胶板的面板,还是作为无框胶合板模板直接使用,用户对于竹胶板的厚度公差都有相应的要求。
根据建设部1995年发布的行业标准《竹胶合板模板标准》(JG/T3026-1995)的规定,竹胶合板厚度允许公差为:9~12mm厚板,优等品±0.5mm,一等品±0.8mm,合格品±1.2mm;13~15mm厚板,优等品±0.6mm,一等品±1.0mm,合格品±1.4mm。
其测量方法一般为板四周测8个点,这8个点所测数据如果达到相应要求,则这块板的厚度即按相应的等级认定。
胶合板模板质量问题对策措施表
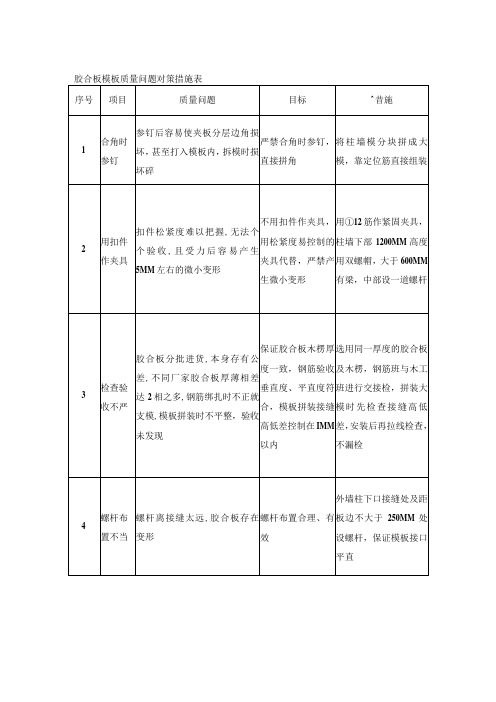
3
检查验收不严
胶合板分批进货,本身存有公差,不同厂家胶合板厚薄相差达2相之多,钢筋绑扎时不正就支模,模板拼装时不平整,验收未发现
保证胶合板木楞厚度一致,钢筋验收垂直度、平直度符合,模板拼装接缝高低差控制在IMM以内
选用同一厚度的胶合板及木楞,钢筋班与木工班进行交接检,拼装大模时先检查接缝高低差,安装后再拉线检查,不漏检
4
螺杆布置不当
螺杆离接缝太远,胶合板存在变形
螺杆布置合理、有效
外墙柱下口接缝处及距板边不大于250MM处设螺杆,保证模板接口平直
胶合板模板质量问题对策措施表
序号
项目
质量问题
目标
^昔施
1
合角时参钉
参钉后容易使夹板分层边角损坏,甚至打入模板内,拆模时损坏碎
严禁合角时参钉,直接拼角
将柱墙模分块拼成大模,靠定位筋直接组装
2
用扣件作夹具
扣件松紧度难以把握,无法个个验收,且受力后容易产生5MM左右的微小变形
不用扣件作夹具,用松紧度易控制的夹Байду номын сангаас代替,严禁产生微小变形
胶合板不合格整改措施

胶合板不合格整改措施胶合板是一种常用的建筑材料,它具有较好的强度和耐久性。
然而,胶合板在生产过程中可能会出现一些质量问题,导致产品不合格。
针对这些问题,可以采取以下整改措施:1. 质检流程优化:对胶合板生产过程中的每个环节进行严格的质量检查,包括原材料的检测、贴合层压工艺的控制、成品的抽检等。
确保每一批次的产品都符合相关的质量标准。
2. 增加原材料检测频次:胶合板的质量受到原材料的影响较大,特别是胶合板的胶粘剂部分。
因此,在生产过程中增加原材料的检测频次,确保每一批次的原材料都符合质量要求。
3. 严格控制压机参数:胶合板的胶粘剂在压合过程中需要达到一定的温度和压力,才能保证产品的质量。
因此,生产中需要对压机参数进行严格控制,确保每一批次的胶合板都可以达到标准的胶合效果。
4. 强化员工培训:提高员工的专业知识和技能,让他们能够准确理解和执行相关的质量控制标准。
通过培训,增强员工的责任心和工作积极性,降低产品因操作不当而引起的质量问题。
5. 建立质量管理体系:建立完善的质量管理体系,包括质量控制标准、质量检测流程、责任分工等。
通过质量管理体系,确保生产过程中每一个环节都受到有效的监控和管理。
6. 客户投诉及时处理:对于出现质量问题的胶合板,及时收集客户的投诉和意见,并进行分析和处理。
通过了解客户对产品的需求和反馈,不断改进产品的质量,提高客户满意度。
总之,胶合板的质量问题需要重视,并采取相应的整改措施。
通过优化质检流程、加强员工培训、建立质量管理体系等方法,可以不断提高胶合板的质量,并满足客户的需求。
作者则基于上述介绍进一步展开探讨。
7. 强化原材料供应链管理:在胶合板的生产过程中,原材料的质量直接影响到最终产品的质量。
因此,建立健全的原材料供应链管理体系,与信誉可靠的供应商合作,进行长期稳定的采购合作,确保原材料的质量稳定可靠。
8. 增加质量监测设备的投入:通过引入先进的质量监测设备,提高产品的质量管控精度。
塑胶件常见缺陷产生的原因及解决方法

塑胶件常见缺陷产生的原因及解决方法一、材料问题1.材料选择不当:选择不适合的塑胶材料或材料质量不达标,容易导致塑胶件的缺陷。
解决方法是根据具体要求选择合适的塑胶材料,并进行必要的材料测试和质量控制。
2.材料批次差异:不同批次的塑胶材料可能存在差异,如流动性、收缩率等,导致成型件的缺陷。
解决方法是进行材料测试和合理的材料配方设计,确保不同批次的材料性能稳定一致。
二、工艺问题1.注塑工艺参数不合理:注塑工艺参数(如注射速度、保压时间等)不合理会导致成型件的缺陷,如短流、气泡等。
解决方法是通过优化注塑工艺参数,使之更加合理和稳定。
2.注塑模具设计和制造问题:模具结构不合理、尺寸精度不达标等问题会导致成型件的缺陷,如模具表面瑕疵、尺寸偏差等。
解决方法是进行合理的模具设计和制造,并进行必要的模具修整和维护。
3.注塑材料温度控制不当:材料温度过高或过低都会导致成型件的缺陷,如熔接线、气泡等。
解决方法是通过调整料筒温度、模具温度等进行合理的温度控制。
4.模具开合不良:模具开合不良或夹模力不足会导致成型件的缺陷,如模具压痕、塌陷等。
解决方法是保持模具开合顺畅,并确保夹模力适当。
三、设计问题1.设计尺寸不合理:设计尺寸过大或过小、壁厚不均匀等问题会导致成型件的缺陷,如尺寸偏差、变形等。
解决方法是根据塑胶件的使用要求和成型工艺特点进行合理的尺寸设计,并进行必要的尺寸优化。
2.设计结构不合理:设计结构复杂、壁薄部位过多等问题容易导致成型件的缺陷,如留痕、焊痕等。
解决方法是简化设计结构、增加加强筋等措施,提高塑胶件的强度和表面质量。
3.装配接口设计不当:塑胶件的装配接口设计不当会导致装配困难、配套件脱落等问题,影响整体使用效果。
解决方法是合理设计装配接口,确保装配紧固可靠。
以上是塑胶件常见缺陷产生的原因及解决方法的概述。
在实际生产中,还需要根据具体情况进行详细分析和解决。
为了确保塑胶件的质量,需要在材料选择、工艺控制和设计优化等方面进行全面的控制和改进。
浅析江西胶合板生产存在的问题及改进建议

引进
,
原木上机 下 机 无 专 用 设 单板 剪切 由 于 木
原木 定 心 上木装 置 题
。
才 能从根本 上 解 决 问
单板 干 燥机热 效率差
。
如较先 进的为计 算机控 制 的 光 学 扫 描
,
材材质下降无 法 用 电动剪 切单板 整理工艺 均 采用手工操作 相 当多 的压机无 自动 装卸板
光 学摄象 检测
1 989
所 以 旋切 前 煮
、
由 于 原材料 的缺 陷
。
给 原木 蒸
。
省 胶合板 总 产量 为 省 胶合 板总 产量达 胶 合板需 2 平
。 .
1
6
.
万 M 左右
5万 M
3,
3
年全
。
剥皮
、
足 心 带 来不 少 困 难
, ,
旋 切 出来的 而且
,
发展 迅 猛
,
许 多单板 需 较多 的补洞
。
拼 缝处 理
一
,
外的劳动 率水平
提高产 品质量 及提 高劳动 生产率
当前 存在 的 几个 主 要问 题
,
( 二 ) 对 合理 利 用 木材 重 视 不 够
、
首先采 用人 工定 心 误 差 较大 材质 下 降
,
,
由 于木 材
, ,
( 一 ) 工 人 的 劳动 强度 大
劳 动生产 率
,
径 级 减小
,
,
公 心精 度 很低 人 工乡
,
超 声 波 扫描及 接触传感 器等定心
,
大大 提高 了定 心 精度
。
提 高了 出材率
装置
胶合板模板质量通病分析与防治

胶合板模板质量通病分析与防治胶合板模板与传统的钢模板和木模板相比,由于具有质量轻、强度高、韧性好、可以节约大量钢材和木材、周转次数多、较其经济,一投入市场即受到欢迎,在建筑领域中无论多层住宅,还是高层住宅、商业楼、桥梁等工程都在广泛使用。
通过多年的施工实践证明,胶合板模板可大大降低工人劳动强度,便于施工,易于组合拼接,成本较低等优点,其使用量越来越大,但其施工质量好坏在很大程度上取决于工人技术水平、质量意识,若拼模不认真也容易产生跑模,涨模、漏浆,接口不平,接缝错位等通病。
如何有效的防治上述质量通病的产生,是保证工程主体质量的关键。
一、通病产生的原因(1)对模板制作组装方案重视不够,未认真编制组装方案;或虽编制了切实可行的组装方案,但在实际施工时,模板工为省工少时而打了折扣;或所选择的组装方案不符合工程实际情况。
(2)采购时未把握好胶合板及其辅助材料的质量关,或为节约成本而购买劣质材料,使用过程中过早地扭曲变形开裂。
(3)为节约成本,盲目增加模板周转次数,致使模板损坏严重,无法保证混凝土浇筑质量。
(4)施工前未进行有效的技术交底或交底不到位,施工中质检技术人员缺乏检查或检查流于形式,特别是缺乏对模板拼接、支撑架和紧固件的检查。
(5)起吊安装过程中工人野蛮施工,未采取有效的防碰撞措施,导致模板变形,棱角受损。
(6)拆除时未按照拆除方案或操作规程进行,强行硬撬致使出现人为损坏。
(7)对再次使用的模板未进行有效防护。
(8)监理人员没有认真审查模板组装方案,隐蔽验收时对模板检查流于形式,忽视了对模板强度、拼缝、标高、支撑系统、紧固件等的检查。
二、预防措施为减少上述质量通病的发生,提高工程质量,针对其产生的原因,根据施工经验,在施工中采取了以下几方面措施,大大提高了工程质量,还增加了模板周转次数,降低了工程成本;(1)施工前应认真熟悉施工图纸,结合工程实际,根据工程结构形式、荷载大小、地基土类别、施工设备、和材料供应等条件进行编制设计切实可行的模板及支架安装和拆除方案。
胶合板工艺缺陷原因及解决方法

胶合板工艺缺陷原因及解决方法-标准化文件发布号:(9456-EUATWK-MWUB-WUNN-INNUL-DDQTY-KII胶合板工艺缺陷原因及解决方法一、鼓泡和局部脱胶产生的原因:1、单板含水率太高或干燥不均匀2、涂胶量过大3、降压速度过快或热压温度过高4、树脂缩合程度不够5、热压时间不足解决的方法:1、控制单板含水率在8~12%的范围内2、控制涂胶量符合工艺要求3、降压第二阶段速度应缓慢,热压温度应适当降低4、检查树脂质量5、适当延长热压时间二、胶合强度低或脱胶产生的原因:1、胶液质量差2、涂胶量不足或涂胶不均匀3、陈化时间过长,胶液已干或陈化时间太短,胶未形成连续的胶膜4、压力不足,或温度过低,或热压时间太短5、单板毛刺沟痕太深,旋切质量差6、单板含水率太高解决的方法:1、检查胶液质量2、注意涂胶量适中而均匀3、主要控制陈化时间4、适当提高压力含温度,或延长热压时间5、提高单板旋切质量6、控制单板含水率不超过规定的范围三、透胶产生的原因:1、单板质量太差,背面裂隙过大2、胶液太稀或涂胶量过大,陈化时间过短3、热压的温度过高或压力过大解决的方法:1、提高单板质量,减小背面裂隙深度2、提高胶液浓度,减少涂胶量,延长陈化时间3、降低热压温度或降低热压的单位压力四、芯板叠层离缝产生的原因:1、芯板未整张化,手工排芯间隙掌握不准2、装板时芯板移动错位3、芯板边部不齐4、芯板边部有荷叶边或裂口解决的办法:1、芯板整张化或涂胶陈化后再排芯2、装板时防止芯板错位3、芯板边部剪切齐直4、提高芯板旋切和干燥质量,防止荷叶边和裂口五、翘曲产生的原因:1、胶合板结构和加工工艺不符合对称原则2、单板含水率不均匀3、温度、压力过高解决的方法:1、注意遵守对称原则2、提高单板干燥质量3、适当降低温度和压力六、胶合板厚薄不一或超出允许的公差范围产生的原因:1、每个间隔中热压张数过大2、单板厚薄不一3、压板倾斜或柱塞倾斜4、胶合板板胚厚度计算不正确或热压工艺中压力过大,温度过高解决的方法:1、尽可能采用一张一压的热压工艺2、提高单板质量3、压机安装校正成水平4、调整板胚搭配厚度,调整压力和温度七、板面压痕产生的原因:1、垫板表明凹凸不平2、垫板表面粘有胶块或杂物3、单板碎片或杂物夹入板层间解决的办法:1、检查、更换垫板2、检查垫板、清理干净3、配胚时注意清楚。
胶合板问题汇总
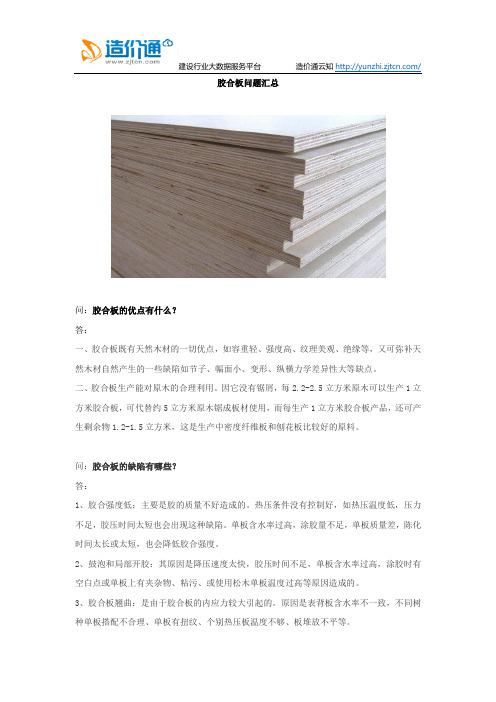
胶合板问题汇总问:胶合板的优点有什么?答:一、胶合板既有天然木材的一切优点,如容重轻、强度高、纹理美观、绝缘等,又可弥补天然木材自然产生的一些缺陷如节子、幅面小、变形、纵横力学差异性大等缺点。
二、胶合板生产能对原木的合理利用。
因它没有锯屑,每2.2-2.5立方米原木可以生产1立方米胶合板,可代替约5立方米原木锯成板材使用,而每生产1立方米胶合板产品,还可产生剩余物1.2-1.5立方米,这是生产中密度纤维板和刨花板比较好的原料。
问:胶合板的缺陷有哪些?答:1、胶合强度低:主要是胶的质量不好造成的。
热压条件没有控制好,如热压温度低,压力不足,胶压时间太短也会出现这种缺陷。
单板含水率过高,涂胶量不足,单板质量差,陈化时间太长或太短,也会降低胶合强度。
2、鼓泡和局部开胶:其原因是降压速度太快,胶压时间不足,单板含水率过高,涂胶时有空白点或单板上有夹杂物、粘污、或使用松木单板温度过高等原因造成的。
3、胶合板翘曲:是由于胶合板的内应力较大引起的。
原因是表背板含水率不一致,不同树种单板搭配不合理、单板有扭纹、个别热压板温度不够、板堆放不平等。
4、边角开胶:造成这种缺陷原因是压板边角磨损造成压力不足,每个间隔里的板坯边角未对齐,装板时板坯放得歪斜受压力不均,单板边部旋切时压榨程度不足,胶接力弱,边角缺胶,胶过早干涸,压板局部地方温度低等。
5、透胶:原因是胶液太稀、胶量过大、单板背面裂缝太深、单板含水率过高、陈化时间和压力过大。
6、芯板叠层和离缝:其原因是人工用零片排芯时预留缝隙过大或过小,装板时芯板错位或重叠,零片边部不齐等。
问:胶合板分成几类?答:一类胶合板为耐气候、耐沸水胶合板,由此及彼有耐久、耐高温,能蒸汽处理的优点;二类胶合板为耐水胶合板,能在冷水中浸渍和短时间热水浸渍;三类胶合板为耐潮胶合板,能在冷水中短时间浸渍,适于室内常温下使用。
用于家具和一般建筑用途;四类胶合板为不耐潮胶合板,在室内常态下使用,一般用途胶合板用材有榉木、椴木、水曲柳、桦木、榆木、杨木等。
胶合板生产工艺对产品质量的影响

胶合板生产工艺对产品质量的影响..r6]厶,e胶合板生产工艺对产品质量的影响螋了/;;(黑龙江省哈尔滨市方林人造板厂150080)摘要本文就本厂的胶合板生产工艺中存在的问题进行了分析,简要说明了生产工艺与胶合板质量的密切联系,找出了生产工艺中影响产品质量的有关因素,为尽?提高产品质量,结合本厂的条件厦特点,提出了几点建议.关键词垦全壑生圭苎!量质量加强和改善工艺管理,全面掌握生产过程.保证产品质量的能力,是胶合板翻造过程质量管理的一个重要环节.合理改善生产工艺,可以直接影响产品质量.在认真抓好影响质量因素的各个环节的同时,充分重视生产工艺对产品质量的影响,保证产品质量的提高.胶台板生产是用旋切单板生产的肢台板.其工艺过程包括原木蒸煮,剥皮,锯断,木段定中心,上木与单板旋切,干燥,剪切,单板整理和分等,涂腔,组坯,预压,热压,锯边砂光,分等检验和包装等工序.各道工序都有严格的工艺要求,是否按工艺要求进行生产对产品质量有直接影响,以下仅就生产工艺过程中出现的主要问题谈一谈粗浅的认识.1旋切为了不给产品质量留下隐患,必须严格控制不合格产品流人下道工序.单板旋切要求单板厚度均收藕日期*’2000-01—15匀,两边及中间三点的厚度差不超过?o.5lqoJr~l,且表面光洁度及横纹抗拉强度均应符合要求.但由于各种因索的影响,致使每次抽检的旋切台格率只能达到70%,85%.为提高产品质量,对有关工艺应进行合理调整,如表1.通过上述对工艺的台理调整,寰1单板旋切过程中常见的缺陷产生藤目和改进方软化单扳光洁度差.背面不够.裂琼度大(单扳松软)3.刀门太大.超过单板厚度.4旋刀研唐不崔利,或油刀不够5.压尺棱磨损严重.不起压榨作1降低使辞于刀门的l『4一l,3.2延长木段薰煮时向,使术芯选4EC以上.3凋小刀门,使等于单板厚度蕊定压榨事.4勤换刀,勤油刀.5.更换压尺.新挟压尺棱要磨圆.单槿表面出现凹凸棱刀门破碎屑堵塞.消除刀『]碎属4FORESTSO雁lNijEAND”FEOHNOLOGY2000?6改进,使旋出单板的质量大大提高.2干燥旋切后的单板含有大量水分,需要干燥到一定含水率,才能适合胶合板的胶合或贮存.根据胶合的需要,干燥后单板含水率应为8%,12%,并且要注意干燥机干燥过程中的工艺条件,适当调整工艺操作,避免因工艺原因造成的板子降等如板边翘曲,板端裂缝,含水率不均等等.干燥后的单板应按一定规格进行合理剪切,剪切偏斜度不得超过15rllr1.但在抽检时发现工人为了抢产量,人为加快干燥速度,造成单板含水率偏高(有时达到加%, 40%).这不仅降低了半成品质量, 又直接影响了合板质量,因为单板含水率偏高,导致合板开胶,鼓泡. 而剪切不合理,降低了一,=等品率,以至产生等外品及废品.单板分选工序,是关键的一道工序.应严格按照国家标准进行分选,并保证优材优用,劣材劣用,从而才能保证工厂的经济效益获得最大提高,但在实际操作中,有部分工人工作马马虎虎,对国标掌握不全面.从而出现与标准要求不符的等级板.这不仅造成了材质浪费,而且影响合板质量.所以必须严格执行工艺标准.在分选时发现无纸拼缝机拼出的单板存在一些问题,如:端头离缝,缝隙不严等缺陷,尚待改进.现根据实际工作经验,提出一些改进方法.见表2.3涂胶,热压合板的胶合,是把单板涂胶组成的板坯在一定温度,一定压力下使胶层凝固胶粘,牢固地把单板胶合起来.影响胶合质量的主要因素,除裹2无纸拼蕾机操作常见缺陷和改进方法了单板旋切质量外,胶的质量和掌握合理的胶合工艺条件是很重要的一环.在胶压前影响胶合质量的因素是:(1)单板含水率和涂胶后板坯的含水率,直接影响板坯热传导速度,胶液的渗透程度和胶压需要的时间.过多的水分,不利于胶合质量的提高,延长热压需要的时间,并且容易产生”鼓泡”,”透胶”等缺陷.(2)胶料的可使用时间超过允许范围时,胶已变质,就会使胶合质量降低.(3)涂胶量均匀适当,陈化时间则受室温的影响,在操作上应适当控制.在胶压过程中,影响胶合质量的条件主要是温度,压力和胶压时间.压机达到一定的温度,才能使胶层固化,我厂生产的三层?类胶合板一般热压温度在110,120”C. 并且在一定的压力(10,18吲?) 和适当时间作用下,使合板达到工艺要求,如果操作工在操作中违反工艺规程,往往会造成许多质量后果.如大开胶和局部开胶,鼓泡及胶着力达不到规定标准等,在生产中必须克服掉随意违返操作规程的习惯,确保产品质量.合板的缺陷,就其性质和对产品质量影响大小,分为下述几类:胶合强度上的缺陷,结构上的缺陷,外观上的缺陷,非永久性缺陷.下面简要谈一下胶合过程产生的缺陷和改进方法,见表3.总之,影响胶合板质量的因素多种多样,即有管理人员方面,也有职工素质方面,原材料质量及机械设备状态等均对产品质量有较大影响.FOREST8CIENCEANDTECHNOLOGY2000?6 衰3胶合过程中产生的缺陷和改进方法6 FORESTSCIENCEANDTEOHNOLOGY2000~6。
胶合板模板质量通病控制措施

18mm 厚胶合板模板是目前我国建造界使用最广泛的现浇混凝土结构模板,其主要优点是可随意制作拼装,施工速度快,尤合用于浇筑外形变化复杂的混凝土结构或者构件;其次是因木材导热系数低,混凝土冬期施工时,木模板有一定的保温养护作用。
但是胶合板模板重复利用率低,损耗大,重复使用几次后就会有缺角、变形、圆边等,导致模板与模板之间的接缝不严密,容易产生漏检浆现象;此外胶合板模板还有容易受水浸泡变形损坏等缺陷。
为节约为了消除胶合板模板在现浇混凝土结构中的诸多不利因素,我们采取了一系列措施防止质量通病的产生。
一、在施工现场严格按规范要求施工1、模板的强度、刚度、稳定性应满足施工荷载作用要求。
同一构件的模板支撑严禁采用不同类型(或者不同工艺)材料支撑。
2、模板支设前先进行修整,将表面杂物清理干净并涂刷隔离剂。
已变形、破损模板经修整后再使用或者作废处理。
模板瓶装前涂刷,严禁采用废机油替代隔离剂。
3、当砼梁、板的跨度较大时,应考虑模板起拱,以消除因结构自重、设备自重及施工人员、机具等施工荷载作用引起挠度变形。
如设计无规定,起拱高度应为全跨长的 1/1000~1/3000。
首层顶板模板支设时,其钢、木支撑下必须垫设木板。
木板长度不宜小于 2.0m,宽度不应小于 200mm,厚度不得小于 50mm,严禁垫砖或者短木。
4、首层模板浇水湿润或者楼板养护期内,应采取可靠措施防止水通过预留洞口及各种缝隙渗至填土地面,导致支撑失稳;雨季期间应采取防止雨水倒灌措施。
5、砼浇筑前,应认真复核模板轴线位置是否正确、支撑是否坚固,发现问题应及时进行处理。
6、结构构件底模拆除前,应对与结构同条件养护的砼试块进行试验,当试块强度达到规定要求且不少于 15 天时方可拆模。
其中板须达到设计强度标准值的 75%,且不少于两周;梁底模及悬臂构件须达到设计强度标准值的 100%,且不得少于 28 天。
楼板模板在支设前应先在墙体上弹线,不得一边支模一边引线,保证周边标高一致。
胶合木板制造工艺优化

胶合木板制造工艺优化胶合木板制造工艺优化胶合木板是一种应用广泛的木材制品,用于家具、装饰材料等领域。
优化胶合木板的制造工艺可以提高产品的质量和生产效率。
以下是一种步骤思维的优化工艺:第一步:原材料选择优质的原材料是制造高质量胶合木板的基础。
选择具有均匀纹理、无明显疵点和虫眼的木材。
通过优化原材料的选择,可以减少生产过程中的缺陷和浪费。
第二步:预处理在将木材进行胶合之前,需要对其进行一些预处理。
首先,将原木切割成所需尺寸的木块。
然后,通过蒸汽处理或浸泡木材,使其含水率适当,以提高胶合效果。
此外,可以对木材进行表面处理,如去除树皮和修整边缘,以确保最终产品的外观质量。
第三步:胶粘剂选择胶粘剂在胶合木板的制造过程中起着至关重要的作用。
选择适合的胶粘剂类型和配方,使其具有良好的粘合强度和耐久性。
常用的胶粘剂包括尿素醛树脂、酚醛树脂和酚醛酚醛树脂。
第四步:胶合工艺胶合工艺是胶合木板制造过程中最关键的环节。
首先,在木材表面涂覆胶粘剂,然后将木块按照设计要求堆叠在一起。
在堆叠过程中,可以使用夹具或压力机施加压力,以确保木材之间的紧密贴合。
最后,将堆叠好的木块进行加热,以促进胶粘剂的固化。
第五步:修整和加工胶合完成后,需要对胶合木板进行修整和加工。
首先,将胶合板的边缘修整,以确保其平整度和直角度。
然后,可以根据需要对胶合板进行切割、打孔、雕刻等加工工艺,以满足不同的应用需求。
第六步:质量控制质量控制是优化胶合木板制造工艺的重要环节。
通过引入严格的质量检查标准和流程控制,可以确保胶合木板的质量稳定性和一致性。
例如,对胶合板的厚度、强度、平整度等进行检测,并记录和分析生产过程中的关键参数。
通过以上的步骤思维优化胶合木板的制造工艺,可以提高产品的质量和生产效率,满足市场需求,并为企业带来更多的竞争优势。
胶合板不合格整改措施

胶合板不合格整改措施第1篇:不合格产品整改措施关于XXXXXXXX衣服不合格的整改措施尊敬的北京市消费者协会领导:首先xxx集团公司感谢北京市消费者协会本着以对消费者负责的工作理念开展商品比较试验,促进对我们商品质量的提高,使我们更好地为消费者提供高品质的羽绒制品。
本公司于2013年12月16日收到贵协会的通知后,得知xxx的Q-1881款纤维含量指标不符合国家标准,XXX公司给予了高度重视,立即通知各门店对不合格商品进行了下架,返回厂家,召开中层质量管理人员会议,分析原因,查找不足,并按照协会的通知精神制定了整改措施:一、每批次商品在进入市场后先进行商品质量检测,对不合格商品决不投放市场。
二、加大服装面料自检的管理力度,调整并提升更高水平的业务管理人员进行商品质量把关。
三、加强业务培训,聘请专业人员讲解、学习有关国家标准,进一步提高我公司管理人员的业务水平。
通过北京市消费者协会对本公司的监督,使我们对羽绒制品的标准知识有了新的认识。
本公司诚恳接受此次教训,确保以后以维护消费者利益为宗旨,企业产品严格执行国家标准,并且进一步加强对商品质量和服务的监督,保护消费者的合法权益,为促进国民经济又好又快发展和构建社会主义和谐社会服务。
最后我们衷心的感谢北京市消费者协会敦促我们加强企业自律,促进商品质量提高,为消费者提供放心安全的高品质服装,希望您们今后给予我们更多地指导与帮助。
常熟市XXX制衣有限公司2013-x-x第2篇:考核不合格整改措施考核不合格整改措施篇1:考核整改报告整改情况报告根据省局晋安监规字(20XX)336号文件有关要求,按照省局考核组对我公司下达的20XX年度考核意见,对照《安全评价机构管理规定》、《安全评价机构考核管理规则》、《安全评价机构管理办法》和质量标准化标准及考核评级办法等有关规定,我们认真做了如下整改:一、管理方面:对照考核组提出的意见,我们已制定了人员培训制度及培训档案,在下一步的工作中我们将认真落实。
胶合板常见质量缺陷分析与控制

胶合板常见质量缺陷分析与控制发布时间:2021-06-23T17:33:39.133Z 来源:《基层建设》2021年第9期作者:张正启[导读] 摘要:我国胶合板的生产和出口量十分大。
崇左广林迪芬新材料科技有限公司广西壮族自治区崇左市摘要:我国胶合板的生产和出口量十分大。
胶合板的价值在实践中是分不开的。
因此,有必要进一步发展和研究这些问题。
胶合板由于材料、制造和其他问题而存在不合格物料。
需要采取积极主动的措施来解决这一问题。
常见缺陷例如叠芯、离缝、脱胶以及透胶对胶合板进行了分析,并提供了相应的控制措施。
关键词:胶合板;质量缺陷;分析;控制我国是胶合板的最大生产国。
但是,我们的胶合板产品经常受到外部贸易壁垒的影响,而外部贸易壁垒又受到国际先进生产力的影响,并面临着巨大的外部挑战和威胁。
只有调整和改进胶合板的工业结构,改进制造技术,控制生产过程,升级、改进地生产优质胶合板产品,提高基本竞争力,我们才能有稳定的市场。
本文分析了我国实木生产中胶合板的生产工艺、质量问题和工艺控制,为胶合板的生产和工艺控制提供参考。
一、胶合板的生产过程简述图1胶合板制造工艺流程图。
大多数胶合板生产企业不生产单板和胶黏剂,而是直接采购。
因此,本文中介绍的工艺和制造工艺不包括在截断到旋切单板工艺。
图1显示了胶合板的制造工艺。
图1胶合板的生产工艺流程图二、调胶工序管理现状1.企业领导不了解调胶工艺的重要性,也没有意识到调胶工序的质量会影响胶合板的生产和产品质量。
2.根据辅料、半成品、成品的质量调胶。
如果以原胶的pH值和固化时间作为固化剂种类和使用的依据,则游离甲醛含量是添加甲醛捕捉剂依据。
3.固化剂添加不当。
固化剂的作用是在中性或碱性条件下降低胶凝剂的pH值。
加快脲醛树脂分子链的联速,缩短凝胶的凝固时间,严格控制固化剂的使用,如过量使用,胶黏剂的使用寿命短,甚至热压前固化;如果用得不够,它就不能起到催化剂的作用。
4.调胶质量达不到技术要求。
胶合板用作模板的质量通病及防治措施

! $"!
施工管理措施 胶合板模板必须具有足够的强度、 刚度和
$"*
施工过程中应做到施工前认真准备, 编制
稳定性, 不得产生允许的变形, 应进行观察或 测量检查, 确保模板材质。
质安措施。施工过程中应进行检查和整改, 施 工后检查验收。
$"$
用作底模的地坪, 铺设的底板以及胎模等
不得发生不允许的下沉或起鼓, 确保模板整体 稳定。
广东土木与建筑
&+
模板的缝隙应做到不致漏浆, 预埋件应安 对于清水混凝土的模板质量, 除了比国家
$"& $"’
! 安装完时在边角处安装小块三角形或
长方形模板。当一个开间铺 $ 块大模板, 中间 可有意铺 ! 条小模( 见图 !%) , 拆模时用铁撬先 拆出这个小模, 然后用木楔楔入大块模, 逐块 拆下, 确保混凝土表面不受损坏。
" 在拆除墙、柱或楼板的模板时均应用
木楔先楔入, 使模板与混凝土表面脱离, 再用 铁撬撬模, 尽量少用铁撬与混凝土表面接触。
灌混凝土时, 还应该在现场进行质量监督检查。
$")
进行清水混凝土施工时, 要求工程项目管
理部门加强协调、 检查、 监督, 协调施工, 混凝 土工、 水电工等工种在施工过程中相互配合协 调施工, 共同保护模板, 一切按操作规程精心 施工。
# !"!
质量通病的防治技术措施 垂直度
!"$
阴阳角不方正
! 内墙阴角
-+
朱小华: 胶合板用作模板的质量通病及防治措施
!""# 年第 $ 期
在阴角处 ( 块相互垂直模板上安装 ( 块 角铁, 型号为: 主 角 铁 )%&&’*&&, 且 *-&&’
- 1、下载文档前请自行甄别文档内容的完整性,平台不提供额外的编辑、内容补充、找答案等附加服务。
- 2、"仅部分预览"的文档,不可在线预览部分如存在完整性等问题,可反馈申请退款(可完整预览的文档不适用该条件!)。
- 3、如文档侵犯您的权益,请联系客服反馈,我们会尽快为您处理(人工客服工作时间:9:00-18:30)。
胶合板工艺缺陷原因及解决方法
一、鼓泡和局部脱胶
产生的原因:
1、单板含水率太高或干燥不均匀
2、涂胶量过大
3、降压速度过快或热压温度过高
4、树脂缩合程度不够
5、热压时间不足
解决的方法:
1、控制单板含水率在8~12%的范围内
2、控制涂胶量符合工艺要求
3、降压第二阶段速度应缓慢,热压温度应适当降低
4、检查树脂质量
5、适当延长热压时间
二、胶合强度低或脱胶
产生的原因:
1、胶液质量差
2、涂胶量不足或涂胶不均匀
3、陈化时间过长,胶液已干或陈化时间太短,胶未形成连续的胶膜
4、压力不足,或温度过低,或热压时间太短
5、单板毛刺沟痕太深,旋切质量差
6、单板含水率太高
解决的方法:
1、检查胶液质量
2、注意涂胶量适中而均匀
3、主要控制陈化时间
4、适当提高压力含温度,或延长热压时间
5、提高单板旋切质量
6、控制单板含水率不超过规定的范围
三、透胶
产生的原因:
1、单板质量太差,背面裂隙过大
2、胶液太稀或涂胶量过大,陈化时间过短
3、热压的温度过高或压力过大
解决的方法:
1、提高单板质量,减小背面裂隙深度
2、提高胶液浓度,减少涂胶量,延长陈化时间
3、降低热压温度或降低热压的单位压力
四、芯板叠层离缝
产生的原因:
1、芯板未整张化,手工排芯间隙掌握不准
2、装板时芯板移动错位
3、芯板边部不齐
4、芯板边部有荷叶边或裂口
解决的办法:
1、芯板整张化或涂胶陈化后再排芯
2、装板时防止芯板错位
3、芯板边部剪切齐直
4、提高芯板旋切和干燥质量,防止荷叶边和裂口
五、翘曲
产生的原因:
1、胶合板结构和加工工艺不符合对称原则
2、单板含水率不均匀
3、温度、压力过高
解决的方法:
1、注意遵守对称原则
2、提高单板干燥质量
3、适当降低温度和压力
六、胶合板厚薄不一或超出允许的公差范围
产生的原因:
1、每个间隔中热压张数过大
2、单板厚薄不一
3、压板倾斜或柱塞倾斜
4、胶合板板胚厚度计算不正确或热压工艺中压力过大,温度过高解决的方法:
1、尽可能采用一张一压的热压工艺
2、提高单板质量
3、压机安装校正成水平
4、调整板胚搭配厚度,调整压力和温度
七、板面压痕
产生的原因:
1、垫板表明凹凸不平
2、垫板表面粘有胶块或杂物
3、单板碎片或杂物夹入板层间
解决的办法:
1、检查、更换垫板
2、检查垫板、清理干净
3、配胚时注意清楚。