高速铁路刹车片的研究与展望
2024年动车组制动闸片市场环境分析

2024年动车组制动闸片市场环境分析引言动车组制动闸片是动车制动系统中的重要组成部分,对于保障列车安全行驶具有至关重要的作用。
随着我国高铁网络的不断扩大和动车组列车的日益增多,动车组制动闸片市场需求也在不断增加。
本文将对动车组制动闸片市场环境进行分析,以期为相关企业和投资者提供参考。
市场规模目前,我国高铁网络已成为世界上最大的高速铁路网络,动车组列车成为主要的运输工具。
据统计,2019年我国动车组列车累计运输量达到XX亿人次,相较于2018年的XX亿人次有显著增长。
随着高铁线路的拓展和客运需求不断增加,预计动车组制动闸片市场规模将继续扩大。
技术发展趋势1.制动性能要求更高:随着高速动车组列车的发展,制动系统对于制动闸片的性能要求也越来越高,包括制动力度、制动平稳性等方面要有更好的表现。
2.材料创新:新型材料的研发和应用,可以提高制动闸片的热稳定性、摩擦系数和耐磨性,提高制动系统效率和寿命。
3.自动化技术:自动化制动系统的引入将提高列车的制动响应速度和准确性,对制动闸片的性能和可靠性提出了更高的要求。
市场竞争格局目前,动车组制动闸片市场上存在着多家重要的供应商。
主要的竞争企业包括:1. X公司:作为行业领先企业之一,X公司具有先进的制造工艺和强大的研发实力,产品质量和性能得到市场的一致认可。
2. Y公司:Y公司作为新兴企业,凭借其创新的技术和灵活的市场策略,逐渐在市场上崭露头角。
3. Z公司:作为传统制造商,Z 公司在市场上拥有一定的份额,但受制于研发能力和技术水平的限制,竞争压力逐渐增大。
市场机遇与挑战机遇1.市场需求增加:随着高铁网络的不断扩大和动车组列车运输量的增加,动车组制动闸片市场需求将持续增长。
2.技术进步的推动:新材料、自动化技术等技术的应用将提高制动闸片的性能,为企业获取更多市场份额提供机遇。
挑战1.技术壁垒:制造高性能的动车组制动闸片需要具备独特的技术和专业的知识,新进入者面临技术壁垒的挑战。
中国铁路设备制动闸片行业研究-行业发展态势及挑战

中国铁路设备制动闸片行业研究-行业发展态势、挑战行业发展态势1、国产化趋势中国动车组用粉末冶金闸片发展起步较晚,2012年以前处于技术保护期,基本被国外产品垄断。
2012年以来,在国家建设“创新型国家”战略的推动下,在中国铁路总公司主导下,中国铁道科学研究院技术牵头,集合中国中车及相关企业的力量,开展中国标准动车组设计研制工作,动车组相关核心零部件国产化进程加速。
随着中国具有完全自主知识产权的中国标准动车组“复兴号”的成功研制生产及运行,中国动车组牵引、制动、网络控制系统实现全面自主化,动车组零部件国产化程度大幅提高,开启动车组零部件的国产替代的新时代。
2、新产品、新技术趋势中国高铁的快速发展对制动装置中刹车材料的性能提出了更高的要求,行驶速度的提升要求摩擦材料能够在较宽的速度、温度范围内具有稳定的摩擦性能。
从制动系统刹车材料发展现状和近几年的研发方向可看出,制动系统刹车材料的主要发展趋势是开发集优良导热性、稳定摩擦系数、耐高温抗冲击、耐磨减磨的闸片材料。
铁路车辆刹车片材料的发展主要经历了铸铁材料、合成材料、粉末冶金材料等,近年来行业内新开发的高性能制动材料有碳陶复合材料。
合成材料是将金属粉末、黏合剂(酚醛树脂、合成橡胶、酚醛树脂和合成橡胶混合物等)和摩擦调节剂等经充分混炼后加热压制而成。
合成材料可通过改变配方和工艺在一定范围内调整其物理机械性能,耐磨性好,使用寿命可达铸铁闸片的四倍以上,制动时无火花,重量轻,摩擦系数稳定性较好。
但是合成材料导热性差,制动热量难以散发。
耐热性差,摩擦系数下降,产生热衰退,其磨损率急剧增加,甚至导致热裂;其次,在潮湿状态下,其摩擦系数大幅下降,因此受雨雪天气等影响较大,无法在工况复杂恶劣的高速动车组上使用。
碳陶复合材料通过引入了具有优异抗氧化性能的碳化硅硬质材料,其具有抗高温氧化、干燥和潮湿状态摩擦系数均非常稳定等优点。
但在现有技术条件下,存在大批量生产工艺复杂、难度大、周期长、成本高等问题,限制了在高速动车组上的推广使用。
2024年高速列车刹车盘市场前景分析

2024年高速列车刹车盘市场前景分析1. 引言随着高速列车的快速发展,刹车盘作为关键部件之一,在高速列车运行过程中起到了至关重要的作用。
本文将对高速列车刹车盘市场前景进行分析,以揭示该市场的发展趋势和商机。
2. 高速列车刹车盘市场概述目前,随着高速列车的不断发展壮大,刹车盘市场也呈现出稳步增长的势头。
高速列车刹车盘主要用于提供刹车力量,在列车运行过程中对列车进行安全、可靠的刹车。
刹车盘是高速列车刹车系统的重要组成部分,其质量和性能直接影响列车刹车效果和乘客的乘坐体验。
3. 高速列车刹车盘市场发展趋势3.1 技术创新驱动市场发展随着科技的不断进步和创新,高速列车刹车盘技术也在不断改进和更新。
新材料的应用、刹车盘制造工艺的创新以及模拟仿真技术的发展,将推动高速列车刹车盘市场的健康成长。
3.2 舒适安全需求促使刹车盘市场增长乘客对高速列车的舒适性和安全性要求越来越高。
高速列车刹车盘的质量和性能直接关系到列车的刹车效果和乘客的乘坐体验。
为了满足乘客需求,高速列车刹车盘市场将持续增长。
3.3 市场竞争加剧随着高速列车刹车盘市场的发展,市场上涌现出了众多的刹车盘生产厂家。
市场竞争激烈,厂家之间的技术创新和产品差异化将成为市场竞争的重要因素。
4. 高速列车刹车盘市场商机分析4.1 需求增长驱动市场扩大随着高速列车运营线路的不断增加和运营里程的增长,对高速列车刹车盘的需求也在不断增加。
市场的扩大将为刹车盘生产厂家带来更多商机。
4.2 环保要求带动新材料市场需求高速列车刹车盘的制造过程中,材料的选择对环境产生重要影响。
因此,随着环保意识的增强,对刹车盘新材料的需求将逐渐增加。
4.3 趋势性升级带来市场机遇随着高速列车技术的不断提升和改进,刹车盘的需求也将逐步发展。
“智能化刹车盘”和“高效能刹车盘”等新型刹车盘的涌现将为市场带来新的商机。
5. 高速列车刹车盘市场挑战与对策5.1 质量和性能的要求提高高速列车的发展对刹车盘提出了更高的质量和性能要求。
高铁刹车片行业分析报告

高铁刹车片行业分析报告高铁刹车片是指用于高速列车的刹车装置,具有高速、高温等特点。
目前,中国高铁刹车片行业处于快速发展阶段,但也存在一些瓶颈和挑战。
本文将对高铁刹车片行业进行全面分析,包括定义、分类特点、产业链、发展历程、行业政策文件、经济环境、社会环境、技术环境、发展驱动因素、行业现状、行业痛点、行业发展建议、行业发展趋势前景、竞争格局、代表企业、产业链描述、SWTO分析、行业集中度等方面。
定义高铁刹车片是指用于高速列车的刹车装置,具有高速、高温等特点。
高速列车运行过程中,刹车片需要对车轮进行摩擦,将动能转换为热能并散发出去,以减速列车行驶速度。
分类特点高铁刹车片按材料分为有机刹车片和陶瓷刹车片。
有机刹车片通常采用复合材料,具有良好的弹性和稳定性,但使用寿命相对较短,需要经常更换。
陶瓷刹车片采用高温陶瓷材料制成,具有较高的耐磨性、耐高温性和耐腐蚀性,使用寿命较长,但价格较高,制造工艺复杂。
产业链高铁刹车片产业链主要包括原材料供应商、刹车片生产商、高铁运营商和维修保养服务提供商等环节。
原材料供应商从事供应有机材料、陶瓷材料、金属材料等刹车片制造所需的原材料。
刹车片生产商将原材料进行制造加工,生产出刹车片产品。
高铁运营商购买刹车片进行列车维护和更新。
维修保养服务提供商为高铁运营商提供刹车片的更换、维护和保养等服务。
发展历程我国高铁刹车片产业起步较晚,主要依靠进口产品满足市场需求。
2008年“和谐号”列车试运行期间,因进口刹车片不符合中国国情,出现严重故障。
此后,我国开始加强高铁刹车片研发和生产制造,大力发展该产业。
目前,国内高铁刹车片生产技术逐渐成熟,产品技术水平和质量稳步提升,市场占有率逐步扩大。
行业政策文件高铁刹车片行业相关政策主要包括《铁路客车车辆技术条件》、《高速铁路运行车辆设备技术条件》、《高速铁路动车组车辆设备技术条件》等。
这些政策规定了高铁刹车片的技术标准、安全要求、检测评估、环保要求等方面的要求。
高速列车车辆制动系统的刹车片材料磨损分析与预测
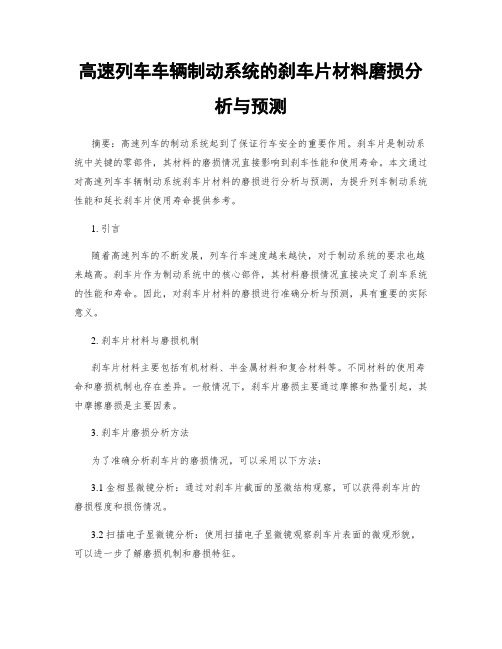
高速列车车辆制动系统的刹车片材料磨损分析与预测摘要:高速列车的制动系统起到了保证行车安全的重要作用。
刹车片是制动系统中关键的零部件,其材料的磨损情况直接影响到刹车性能和使用寿命。
本文通过对高速列车车辆制动系统刹车片材料的磨损进行分析与预测,为提升列车制动系统性能和延长刹车片使用寿命提供参考。
1. 引言随着高速列车的不断发展,列车行车速度越来越快,对于制动系统的要求也越来越高。
刹车片作为制动系统中的核心部件,其材料磨损情况直接决定了刹车系统的性能和寿命。
因此,对刹车片材料的磨损进行准确分析与预测,具有重要的实际意义。
2. 刹车片材料与磨损机制刹车片材料主要包括有机材料、半金属材料和复合材料等。
不同材料的使用寿命和磨损机制也存在差异。
一般情况下,刹车片磨损主要通过摩擦和热量引起,其中摩擦磨损是主要因素。
3. 刹车片磨损分析方法为了准确分析刹车片的磨损情况,可以采用以下方法:3.1 金相显微镜分析:通过对刹车片截面的显微结构观察,可以获得刹车片的磨损程度和损伤情况。
3.2 扫描电子显微镜分析:使用扫描电子显微镜观察刹车片表面的微观形貌,可以进一步了解磨损机制和磨损特征。
3.3 磨损试验:通过设计磨损试验台架,模拟实际行车过程中的工况,对刹车片进行磨损实验,并通过获得的数据进行分析。
4. 刹车片磨损预测模型为了预测刹车片的磨损情况,可以建立基于实验数据和数学模型的磨损预测模型。
常用的磨损预测模型包括:4.1 质量损失模型:根据实验数据建立刹车片质量损失与摩擦片累积摩擦能量之间的关系,通过知道摩擦片摩擦能量的大小,可以预测刹车片的质量损失程度。
4.2 温度场模型:根据刹车片表面温度分布规律,通过数学模型计算刹车片表面温度,从而预测刹车片的热磨损情况。
4.3 磨损耗能模型:根据刹车片的磨损机理和公式,建立磨损量与刹车片损失能量之间的关系,通过计算损失能量可以预测刹车片的磨损程度。
5. 刹车片材料磨损预测实例分析通过实例分析,可以更具体地了解刹车片材料的磨损预测方法和应用。
2023年高铁刹车片行业市场研究报告
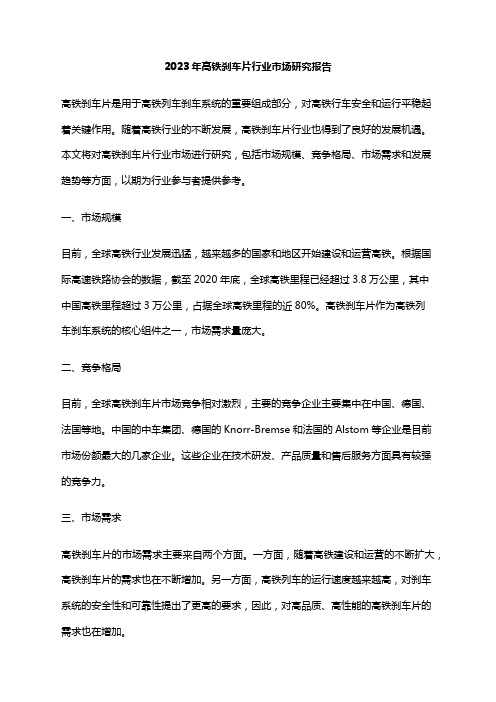
2023年高铁刹车片行业市场研究报告高铁刹车片是用于高铁列车刹车系统的重要组成部分,对高铁行车安全和运行平稳起着关键作用。
随着高铁行业的不断发展,高铁刹车片行业也得到了良好的发展机遇。
本文将对高铁刹车片行业市场进行研究,包括市场规模、竞争格局、市场需求和发展趋势等方面,以期为行业参与者提供参考。
一、市场规模目前,全球高铁行业发展迅猛,越来越多的国家和地区开始建设和运营高铁。
根据国际高速铁路协会的数据,截至2020年底,全球高铁里程已经超过3.8万公里,其中中国高铁里程超过3万公里,占据全球高铁里程的近80%。
高铁刹车片作为高铁列车刹车系统的核心组件之一,市场需求量庞大。
二、竞争格局目前,全球高铁刹车片市场竞争相对激烈,主要的竞争企业主要集中在中国、德国、法国等地。
中国的中车集团、德国的Knorr-Bremse和法国的Alstom等企业是目前市场份额最大的几家企业。
这些企业在技术研发、产品质量和售后服务方面具有较强的竞争力。
三、市场需求高铁刹车片的市场需求主要来自两个方面。
一方面,随着高铁建设和运营的不断扩大,高铁刹车片的需求也在不断增加。
另一方面,高铁列车的运行速度越来越高,对刹车系统的安全性和可靠性提出了更高的要求,因此,对高品质、高性能的高铁刹车片的需求也在增加。
四、发展趋势高铁刹车片行业的发展趋势主要包括以下几个方面:1. 技术创新:随着高铁行业的快速发展,对高铁刹车片的性能要求越来越高。
未来,行业内将更加重视技术创新,开发出更具竞争力的产品。
2. 环保可持续发展:在全球环保意识的提升下,高铁刹车片行业也将朝着环保可持续方向发展。
研发和推广环保型刹车片,减少对环境的影响。
3. 国际市场开拓:目前,中国高铁刹车片行业在国内市场占据主导地位,但在国际市场上还有较大的发展空间。
未来,中国高铁刹车片企业将加大对国际市场的开拓力度。
4. 智能化发展:在高铁行业进一步智能化的背景下,高铁刹车片行业也将逐步发展智能化产品。
2024年高铁刹车片市场分析报告
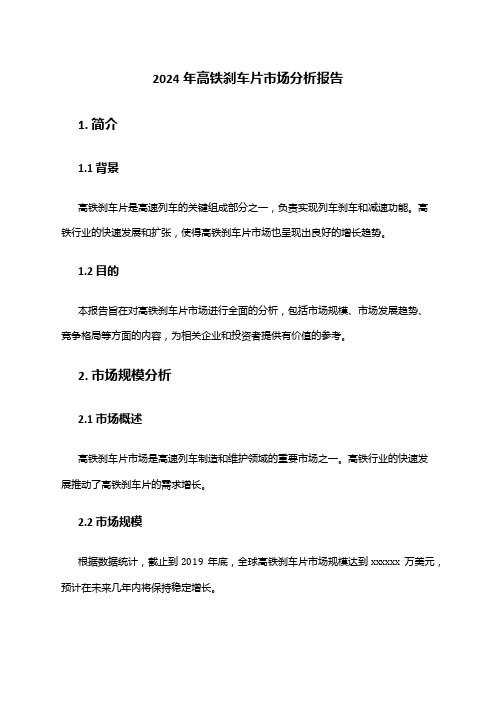
2024年高铁刹车片市场分析报告1. 简介1.1 背景高铁刹车片是高速列车的关键组成部分之一,负责实现列车刹车和减速功能。
高铁行业的快速发展和扩张,使得高铁刹车片市场也呈现出良好的增长趋势。
1.2 目的本报告旨在对高铁刹车片市场进行全面的分析,包括市场规模、市场发展趋势、竞争格局等方面的内容,为相关企业和投资者提供有价值的参考。
2. 市场规模分析2.1 市场概述高铁刹车片市场是高速列车制造和维护领域的重要市场之一。
高铁行业的快速发展推动了高铁刹车片的需求增长。
2.2 市场规模根据数据统计,截止到2019年底,全球高铁刹车片市场规模达到xxxxxx万美元,预计在未来几年内将保持稳定增长。
3. 市场发展趋势分析3.1 技术创新推动市场发展随着高铁技术的不断创新,高铁刹车片也在不断更新换代。
新材料和新工艺的应用,使得高铁刹车片的性能得到显著提升,同时也推动了市场的发展。
3.2 市场竞争格局高铁刹车片市场存在较为激烈的竞争,市场上有多家知名企业提供高铁刹车片产品。
这些企业通过不断提高产品质量和性能,加强研发能力,争夺市场份额。
3.3 区域市场分析高铁刹车片市场分布广泛,不同地区的市场规模和发展程度存在差异。
目前,亚太地区是全球高铁刹车片市场的主要消费地区,其市场规模占据全球市场的大部分份额。
4. 市场机遇与挑战分析4.1 市场机遇随着全球高铁建设的不断推进,高铁刹车片市场将迎来新的发展机遇。
机会主要体现在需求的增长和市场的扩大。
4.2 市场挑战虽然高铁刹车片市场有着广阔的发展前景,但也面临一些挑战。
技术创新和市场需求变化加剧了竞争,企业需要不断提升自身实力以应对挑战。
5. 市场前景展望5.1 市场预测基于目前市场趋势和发展动态,预计未来几年高铁刹车片市场将保持稳定增长。
特别是在高铁技术不断进步和全球高铁建设推进的背景下,市场规模有望进一步扩大。
5.2 市场投资建议对于相关企业和投资者而言,高铁刹车片市场具备较高的投资价值。
高铁刹车片简介演示
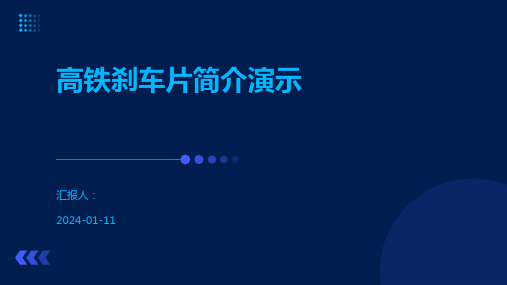
刹车片的摩擦材料是直接与刹车盘接触产生摩擦 力,从而实现车辆减速的材料。
粘合剂
粘合剂用于将摩擦材料与基体牢固地粘合在一起 ,使其成为一个整体。
刹车片的工作过程
制动时,刹车片受到来自制动器的压力,摩擦材料与刹车盘接触并产生摩擦力。 随着制动力的增加,摩擦力逐渐增大,使高铁减速。
当制动器松开时,摩擦力消失,高铁逐渐恢复到正常速度。
刹车片的性能直接关系到列车的制动效果 ,保养良好的刹车片能够提供更加稳定和 可靠的制动性能。
提高行车安全性
降低运营成本
刹车片的良好状态是保证列车安全运行的 重要因素之一,保养得当可以降低因刹车 系统故障引发的安全风险。
及时维护和更换刹车片可以避免因严重磨 损或故障导致的意外维修和更换成本,从 而降低运营成本。
市场发展前景与趋势
市场需求增长
随着高铁网络的不断扩展和运营里程的增加,对高质量刹车片的需求将持续增长。
市场竞争格局变化
随着技术的进步和市场的扩大,将吸引更多企业进入高铁刹车片市场,推动竞争格局的 变化。
环保和可持续发展要求
随着社会对环保和可持续发展的关注度提高,对高铁刹车片生产过程中的环保要求也将 更加严格,推动相关技术的绿色化发展。
经济性
优质的刹车片能够延长刹车盘的使用寿命,降低维修和更换成本,提高高铁的运行效率和 经济效益。
技术发展
随着科技的不断进步,高铁刹车片在材料、工艺、设计等方面也在不断创新和发展,推动 了整个高铁技术的进步。
02
高铁刹车片的工作原理
刹车片的基本结构
基体
刹车片的基体是用来支撑摩擦材料和传递制动力 矩的结构,通常由金属材料制成。
THANKS
谢谢您的观看
高速列车车辆制动系统的刹车片磨损检测与预警技术研究
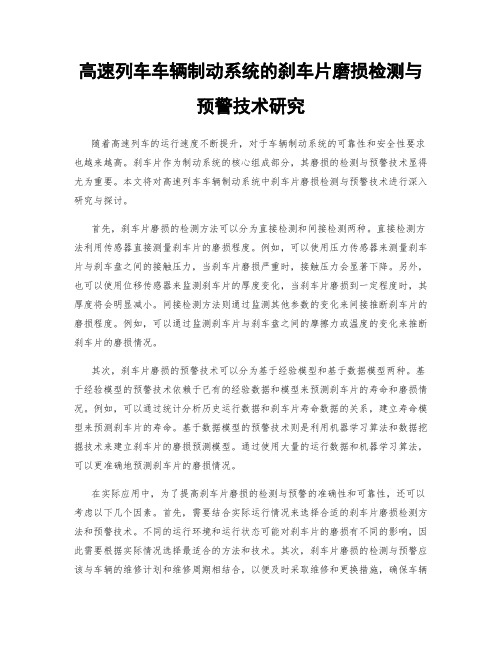
高速列车车辆制动系统的刹车片磨损检测与预警技术研究随着高速列车的运行速度不断提升,对于车辆制动系统的可靠性和安全性要求也越来越高。
刹车片作为制动系统的核心组成部分,其磨损的检测与预警技术显得尤为重要。
本文将对高速列车车辆制动系统中刹车片磨损检测与预警技术进行深入研究与探讨。
首先,刹车片磨损的检测方法可以分为直接检测和间接检测两种。
直接检测方法利用传感器直接测量刹车片的磨损程度。
例如,可以使用压力传感器来测量刹车片与刹车盘之间的接触压力,当刹车片磨损严重时,接触压力会显著下降。
另外,也可以使用位移传感器来监测刹车片的厚度变化,当刹车片磨损到一定程度时,其厚度将会明显减小。
间接检测方法则通过监测其他参数的变化来间接推断刹车片的磨损程度。
例如,可以通过监测刹车片与刹车盘之间的摩擦力或温度的变化来推断刹车片的磨损情况。
其次,刹车片磨损的预警技术可以分为基于经验模型和基于数据模型两种。
基于经验模型的预警技术依赖于已有的经验数据和模型来预测刹车片的寿命和磨损情况。
例如,可以通过统计分析历史运行数据和刹车片寿命数据的关系,建立寿命模型来预测刹车片的寿命。
基于数据模型的预警技术则是利用机器学习算法和数据挖掘技术来建立刹车片的磨损预测模型。
通过使用大量的运行数据和机器学习算法,可以更准确地预测刹车片的磨损情况。
在实际应用中,为了提高刹车片磨损的检测与预警的准确性和可靠性,还可以考虑以下几个因素。
首先,需要结合实际运行情况来选择合适的刹车片磨损检测方法和预警技术。
不同的运行环境和运行状态可能对刹车片的磨损有不同的影响,因此需要根据实际情况选择最适合的方法和技术。
其次,刹车片磨损的检测与预警应该与车辆的维修计划和维修周期相结合,以便及时采取维修和更换措施,确保车辆的安全性和可靠性。
最后,还可以考虑引入智能故障诊断系统和远程监控技术,实时监测和分析刹车片的磨损情况,提前预警并指导维修操作。
总结而言,高速列车车辆制动系统的刹车片磨损检测与预警技术是确保列车运行安全和可靠的重要手段。
2024年动车组制动闸片市场发展现状

动车组制动闸片市场发展现状引言动车组是一种高速铁路车型,为了保证其行车安全和稳定性,制动系统起着至关重要的作用。
而制动闸片作为制动系统的核心部件,在动车组的运行中起着关键作用。
本文将对动车组制动闸片市场的发展现状进行分析和总结。
1. 动车组制动闸片的定义与功能动车组制动闸片是指用于动车组制动系统中的摩擦制动部件,通过与制动盘接触产生摩擦力,实现制动效果。
其主要功能包括:•提供稳定的制动效果,确保动车组行车安全;•承受高速运行中的高温和高压力,保证制动系统的可靠性;•具有较好的耐磨性和耐久性,延长制动闸片的使用寿命;•保证制动闸片的制动力平衡,避免制动不匀、侧滑等问题。
2. 动车组制动闸片市场规模与趋势动车组制动闸片市场规模随着动车组运营里程的增加而不断扩大。
目前,中国动车组制动闸片市场已经成为全球最大的市场之一。
根据统计数据显示,2019年中国动车组制动闸片市场规模达到XX亿元,预计未来几年将保持较高的增长速度。
市场趋势方面,随着动车组技术的不断进步和应用领域的扩展,动车组制动闸片市场呈现以下趋势:•制动闸片材料升级:为了提高制动闸片的制动效果和耐久性,制动闸片材料正向高温耐磨的方向发展。
高温耐磨材料的使用将提升制动闸片在高速运行中的性能表现。
•制动闸片结构创新:传统的制动闸片结构存在制动力分布不均和制动盘磨损加剧等问题。
新一代制动闸片结构通过优化设计,实现制动力的均衡分配,减少制动系统的磨损。
•智能监测与维护:为了提高动车组制动系统的安全性和可靠性,智能监测与维护技术逐渐应用于制动闸片市场。
通过传感器和数据分析技术,实现对制动闸片性能的实时监测与预测维护。
3. 动车组制动闸片市场竞争格局与主要厂商动车组制动闸片市场竞争格局逐渐形成,主要厂商涉及制动系统、制动闸片等相关领域。
目前,全球动车组制动闸片市场的主要厂商有:•英菲尼迪国际公司(Brembo):作为全球领先的汽车制动系统制造商,Brembo在动车组制动闸片市场具有较强竞争力。
高铁刹车片行业分析报告
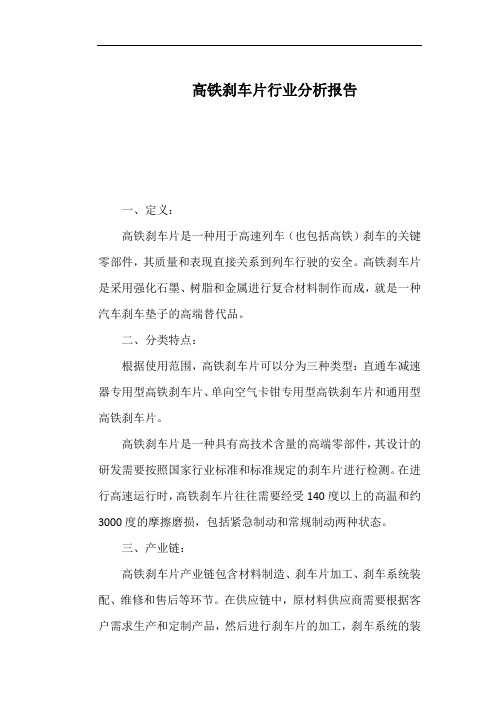
高铁刹车片行业分析报告一、定义:高铁刹车片是一种用于高速列车(也包括高铁)刹车的关键零部件,其质量和表现直接关系到列车行驶的安全。
高铁刹车片是采用强化石墨、树脂和金属进行复合材料制作而成,就是一种汽车刹车垫子的高端替代品。
二、分类特点:根据使用范围,高铁刹车片可以分为三种类型:直通车减速器专用型高铁刹车片、单向空气卡钳专用型高铁刹车片和通用型高铁刹车片。
高铁刹车片是一种具有高技术含量的高端零部件,其设计的研发需要按照国家行业标准和标准规定的刹车片进行检测。
在进行高速运行时,高铁刹车片往往需要经受140度以上的高温和约3000度的摩擦磨损,包括紧急制动和常规制动两种状态。
三、产业链:高铁刹车片产业链包含材料制造、刹车片加工、刹车系统装配、维修和售后等环节。
在供应链中,原材料供应商需要根据客户需求生产和定制产品,然后进行刹车片的加工,刹车系统的装配和产品的销售和维修。
四、发展历程:在中国,高铁刹车片技术的发展可以追溯到20世纪60年代,当时吸收了日本和德国的相关技术。
20世纪90年代,中国开始推行高速铁路建设,使用高速列车,高铁刹车片逐渐从进口转为本土生产。
目前,在中国,市场上有较多应用于高速列车的高铁刹车片制造商。
五、行业政策文件及其主要内容:1.《中华人民共和国铁路法》2.《中华人民共和国公路运输管理条例》3.《中华人民共和国工业生产许可证管理办法》4.《中华人民共和国自然资源部关于加强矿业领域环境保护的通知》六、经济环境:我国高铁行业建设早期投资较大,高端核心零部件依赖进口,但随着近年来自主创新取得的成果,中国高铁零部件制造商已经有一定的市场份额和规模优势。
目前,中国的高速铁路运营里程和对外贸易增长,为高铁刹车片行业提供了良好的发展环境。
七、社会环境:随着我国城市化程度和出行人数的不断增加,铁路运输出现了迅猛发展,相当一部分人群开始关注交通安全问题,高铁行业的技术和安全性被认为是保障人民两会出行安全的重要环节。
2024年高铁刹车片市场前景分析
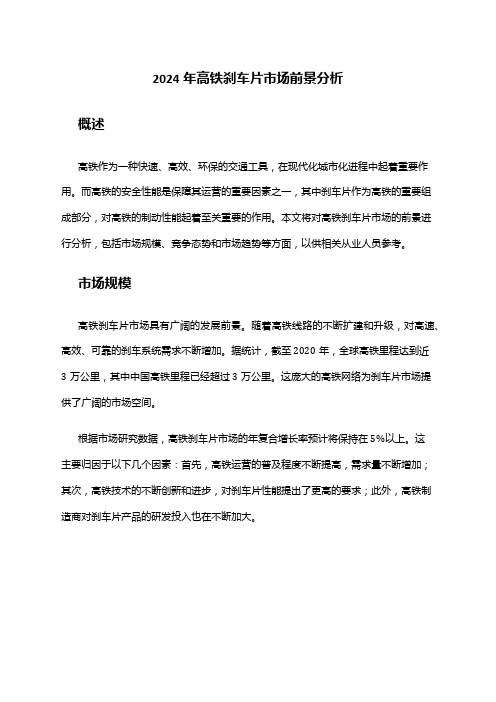
2024年高铁刹车片市场前景分析概述高铁作为一种快速、高效、环保的交通工具,在现代化城市化进程中起着重要作用。
而高铁的安全性能是保障其运营的重要因素之一,其中刹车片作为高铁的重要组成部分,对高铁的制动性能起着至关重要的作用。
本文将对高铁刹车片市场的前景进行分析,包括市场规模、竞争态势和市场趋势等方面,以供相关从业人员参考。
市场规模高铁刹车片市场具有广阔的发展前景。
随着高铁线路的不断扩建和升级,对高速、高效、可靠的刹车系统需求不断增加。
据统计,截至2020年,全球高铁里程达到近3万公里,其中中国高铁里程已经超过3万公里。
这庞大的高铁网络为刹车片市场提供了广阔的市场空间。
根据市场研究数据,高铁刹车片市场的年复合增长率预计将保持在5%以上。
这主要归因于以下几个因素:首先,高铁运营的普及程度不断提高,需求量不断增加;其次,高铁技术的不断创新和进步,对刹车片性能提出了更高的要求;此外,高铁制造商对刹车片产品的研发投入也在不断加大。
竞争态势高铁刹车片市场竞争激烈,主要的竞争对手包括国内外的刹车片制造商和供应商。
国内市场上,一些知名的高铁刹车片制造商已经形成了一定的市场份额,具有较强的竞争力。
而国外市场上,一些刹车片巨头也在积极进入中国市场,试图分一杯羹。
在竞争中,产品质量、性能和可靠性是消费者选择刹车片的重要因素。
因此,高铁刹车片制造商应注重提高产品的质量和性能,同时减少成本,提高竞争力。
市场趋势高铁刹车片市场的发展趋势主要包括以下几个方面:1.技术创新和产品升级:随着高铁技术和制造工艺的不断进步,对刹车片的性能和质量提出了更高的要求。
刹车片制造商应积极进行技术创新和产品升级,以适应市场需求。
2.环保性能要求的提高:在应对气候变化和环境保护的背景下,对高铁刹车片的环保性能要求也在不断提高。
刹车片制造商应注重研发环保型产品,减少对环境的影响。
3.市场多元化:随着高铁在全球范围的普及,市场需求也呈现出多元化的趋势。
高速列车车辆制动系统的刹车片材料性能分析与选择

高速列车车辆制动系统的刹车片材料性能分析与选择随着高速列车的迅猛发展,车辆制动系统的性能要求也变得更加严苛。
刹车片作为车辆制动系统中的核心部件之一,其材料性能对整个系统的安全性和性能至关重要。
本文通过对高速列车车辆制动系统的刹车片材料性能进行分析,并根据性能要求选择合适的材料,以提高刹车系统的可靠性和制动效果。
首先,我们需要对高速列车车辆制动系统的工作原理进行了解。
高速列车的制动系统常采用摩擦制动原理,即通过刹车片与车轮的摩擦来实现制动效果。
因此,刹车片的摩擦性能是选择材料时的重要考量因素之一。
摩擦性能主要包括摩擦系数和摩擦温度。
摩擦系数是刹车片与车轮之间的摩擦力与垂直载荷之比,反映了刹车片提供制动力的强度。
摩擦温度则是刹车片在制动过程中产生的摩擦热量,过高的摩擦温度会导致刹车片失效或退化。
因此,在选择刹车片材料时,需要考虑其摩擦系数和耐高温特性。
此外,刹车片材料还应具备良好的磨损性能和耐疲劳性能。
高速列车的运营条件比较苛刻,频繁的制动操作会导致刹车片的磨损,因此,刹车片材料需具备较高的磨损耐久性,以延长其使用寿命。
同时,高速列车运行过程中的振动和冲击也会对刹车片产生影响,因此刹车片材料还需具备较好的抗疲劳性能,以保证在恶劣工况下的可靠性。
在满足以上性能要求的前提下,还需考虑刹车片材料的成本和可用性。
高速列车制动系统的刹车片需求较大,因此材料的成本和供应稳定性也是选择的重要考虑因素之一。
要确保能够满足大规模生产的需求,并在成本可控的前提下提供优质的刹车片材料。
根据以上分析,我们可以选择以下几种材料作为高速列车车辆制动系统刹车片的候选材料:1. 铸铁:铸铁具有良好的耐磨性和耐高温特性,且成本较低,可在大规模生产中得到保障。
然而,铸铁的摩擦系数较低,磨损性能稍逊于其他材料。
2. 有机材料:有机材料如有机纤维复合材料具有较高的摩擦系数和良好的磨损耐久性,且重量较轻。
但有机材料的耐高温性较差,容易在高温下退化。
高铁刹车片调研报告

高铁刹车片调研报告高铁刹车片调研报告一、背景介绍随着高铁建设的不断推进,高铁运行速度越来越快,对刹车片的要求也越来越高。
刹车片是高铁安全运行的重要部件之一,对于保证列车的刹车性能和稳定性具有重要作用。
因此,深入了解刹车片的性能特点和市场需求,对于高铁刹车片的生产和研发具有重要意义。
二、调研目的和方法本次调研的目的是了解高铁刹车片的市场需求和发展趋势,为相关企业的生产和研发提供参考。
本次调研主要通过市场调研、企业访谈和文献分析等方法进行。
三、调研结果1.市场需求:高铁刹车片市场需求旺盛,随着高铁线路的不断建设,对刹车片的需求量也在不断增加。
按照速度等级划分,高铁刹车片主要分为普速铁路用刹车片和高铁用刹车片。
其中,高铁用刹车片的需求量更大,市场潜力更为巨大。
2.发展趋势:高铁刹车片的发展趋势主要集中在以下几个方面: (1) 提高刹车片的耐磨性和热稳定性,以适应高速运行的需求。
(2) 优化刹车片的摩擦特性,提高刹车效果和舒适性。
(3) 探索新材料的应用,如纳米材料、复合材料等,提高刹车片的性能和使用寿命。
(4) 加强刹车片的制造工艺和质量控制,以确保刹车片的可靠性和安全性。
3.关键技术:高铁刹车片的关键技术主要包括材料技术、制造工艺技术和检测技术。
材料技术是高铁刹车片研发的核心,需要开发出具有良好耐磨性、耐高温性和摩擦特性的材料。
制造工艺技术包括模具设计、压制、烧结和磨削等过程,需要保证刹车片的成型精度和表面质量。
检测技术包括刹车片的力学性能测试和磨损状态监测等,需要能够准确评估刹车片的性能指标和使用寿命。
4.现状和存在问题:目前,国内高铁刹车片生产企业众多,但整体水平还存在一些问题。
主要表现在材料品质不稳定、制造工艺落后、技术创新不足等方面。
这些问题制约了高铁刹车片的质量和性能提升,并且使国内企业在市场竞争中处于劣势地位。
四、建议和展望针对上述存在的问题,建议相关企业在以下方面加强努力:1.加大技术研发力度,不断提升高铁刹车片的性能和品质。
高铁刹车片行业发展趋势

02
制造工艺创新
03
智能化技术应用
引入先进的制造工艺,如3D打印 技术、激光熔覆技术等,实现刹 车片的快速制造和个性化定制。
结合物联网、大数据、人工智能 等技术,实现刹车片的智能监测 、预测性维护和远程故障诊断。
产品升级换代方向探讨
01
02
03
轻量化设计
通过优化设计和材料选择 ,降低刹车片的重量,提 高车辆的燃油经济性和操 控性。
国际化合作
加强国际间的技术交流与合作,推动高铁刹车片行业 的全球化发展。
04
政策法规与标准规范影响分析
政策法规对行业发展的影响
促进产业升级
随着国家对高铁刹车片行业的政策支持力度不断加大,特 别是鼓励创新、优化升级等相关政策的出台,为行业的技 术进步和高质量发展提供了有力保障。
规范市场竞争
政策法规的出台和实施,有助于规范市场竞争秩序,打击 假冒伪劣产品,提高市场准入门槛,推动优质企业做大做 强。
挑战应对策略建议
加强技术研发 推进智能化制造
加强国际合作 加强人才培养
加大技术研发力度,提高产品质量和技术水平,满足高铁技术 的不断升级需求。
加快推进智能化制造,提高生产效率和产品质量,降低生产成 本。
积极参与国际合作,学习借鉴国际先进技术和管理经验,提高 自身竞争力。
加强人才培养和引进,建立高素质、专业化的人才队伍,为高 铁刹车片行业的发展提供强有力的人才保障。
根据材质和性能要求不同,高铁刹车片可分为金属类和非金属类两大类,其中金 属类又包括铜基合金、铁基合金等,非金属类则以树脂基、陶瓷基等为主。
发展历程回顾
01
高铁刹车片行业伴随着中国高铁事业的快速发展而 逐步成长起来。
- 1、下载文档前请自行甄别文档内容的完整性,平台不提供额外的编辑、内容补充、找答案等附加服务。
- 2、"仅部分预览"的文档,不可在线预览部分如存在完整性等问题,可反馈申请退款(可完整预览的文档不适用该条件!)。
- 3、如文档侵犯您的权益,请联系客服反馈,我们会尽快为您处理(人工客服工作时间:9:00-18:30)。
高速铁路刹车片的研究与展望
作者:张兴旺刘佳玲梁建全王明智
来源:《中国化工贸易·下旬刊》2017年第01期
摘要:本文介绍了我国高速铁路刹车片的现状及研究方向,探讨了当前刹车材料中存在的问题,并且研究了Ti3SiC2新材料的一些性能,展望了以Ti3SiC2替代片状石墨成为我国高速铁路刹车片新型润滑剂的可能性。
关键词:高速铁路;刹车片;粉末冶金;Ti3SiC2
自从日本建立起世界上第一条高速铁路开始,世界发达国家进入了高速铁路发展的新时期。
1981年法国TGV列车在巴黎东南线、1991年德国的ICE列车都相继投入运行,现在高速铁路已经发展到意大利、西班牙和英国。
在世界高速铁路总里程碑中,日、法、德三国共占84%,是高速铁路技术最先进、运营经验最丰富的国家。
就高速列车的运行速度而言,法国TGV的317.5km/h位列首位,日本希望者号261.8km/h列第二位,德国LCE列第三位。
若就最高速度利用率而言,日本希望者号以87.2%领先,法国第二,德国第三[1]。
进入新世纪之后,我国高速铁路同样取得了突飞猛进的发展。
从引进时速两百公里高速铁路技术,到自主开发时速三百多公里“和谐号”动车组,从京津城际铁路到京沪高速铁路的开通,我国高速铁路的发展震惊了世界,并迅速跨入引领世界的“高铁时代”!从高铁技术性能上,在系统吸收掌握动车组技术之后,全面构建了设计、制造、维修体系。
在这个基础上,结合中国的国情,自主研发了提升到时速350公里的列车。
中国已发展成为世界上高速铁路发展最快、系统技术最全、集成能力之最强、运营里程最长、运营速度最高、在建规模最大的国家[2]。
中国正在引领世界高速铁路的发展。
1 国内刹车片材料的研究
1.1 国内刹车片材料的概述
目前,我国高速铁路刹车片主要采用了粉末冶金摩擦材料。
与其他摩擦材料相比,粉末冶金摩擦材料具有很高的机械强度,能够在工作温度下适应弯、剪等不同性质的载荷;另外,粉末冶金摩擦材料的比热容和密度都比较大,并且基体材料主要采用铜、铁等金属,具有非常好的导热性能,摩擦材料能够在很短的时间内将摩擦产生的热量吸收并且传递出去,摩擦表面的温度能够维持在允许的范围内;最重要的是,粉末冶金摩擦材料具有非常好的摩擦稳定性,当摩擦面温度升高时,摩擦系数和耐磨性都不会明显下降,冷却后再使用时的回复能力强。
基体金属通常采用Cu、Sn、Fe、Ni、Mn、Ti及其合金,由于单一金属基体的强度不高,因此大多数粉末冶金摩擦材料基体金属中都添加有合金元素,用以形成固溶体来强化基体。
在摩擦剂方面,由于摩擦剂参与摩擦表面膜形成时的物理-化学反应,反应生成的表面膜厚度、种类、力学和物理-化学性能在很大程度上决定了粉末冶金摩擦材料的摩擦学行为,因此,摩擦剂的选
择尤为重要。
常用的摩擦剂为SiO2和SiC,并且添加SiO2、SiC、B4C作为摩擦剂的材料比单独添加SiO2、SiC或SiO2+SiC的材料,综合性能更优异[3]。
润滑组分方面,首选材料为石墨、MoS2,其次是氮化硼。
片状石墨是我国高铁刹车片材料中最常用的固体润滑剂,由于其层状结构,在切向摩擦力作用下能获得非常低的摩擦系数(0.015-0.05)。
片状石墨通常在摩擦过程中参与构成表面的工作膜时,其作为固体润滑剂的作用才表现出来。
1.2 当前刹车片材料的研究方向
由于高速铁路速度的不断提很高,高铁巨大的动能转化成制动刹车片的摩擦热能,摩擦副表面温度会急剧上升,对刹车制动装置要求也越加苛刻。
这就需要不断的探讨和开发出高性能的刹车材料。
当前我国刹车材料的主要研究方向是改进材料的高温抗氧化性和提高并稳定摩擦系数两个方面。
在高温下,材料受到强烈氧化时,由于氧化膜通常力学强度比金属基体低,容易破裂和剥落,从而引起材料很快磨损。
通常人们采用耐热强度较高的合金作为基体材料,因为耐热强度较高的合金具有较高的抗氧化能力。
目前,为了达到更高的工作温度,已向更难熔的金属和更复杂的合金化过渡,用铝代替锡合金化,提高铜基体的工作温度和力学强度极限。
而要提高和稳定摩擦系数,就需要探讨新的摩擦组元和润滑组元,并处理好二者的配比问题。
在摩擦材料中加入比纯碳化物或纯氮化更为稳定、强度更高的复式化合物,摩擦系数和耐磨性均得到提高。
同时,不稳定的石墨也日益趋向于采用惰性的抗卡剂来代替[4]。
1.3 刹车片材料的问题研究
分析以往我国刹车片材料的研究过程:为了提高摩擦系数,防止金属的转移和镶嵌,往往在闸片中添加不同程度的磨料,但是降低了材料的导热性,产生热衰,造成高速制动摩擦系数降低,产品致密度下降,自身损耗增大,磨损制动盘;磨料的加入和金属粉末的合金化使铜基闸片的硬度较高(HB>40),不但影响产品的摩擦系数,还加大了闸片自身以及制动盘的磨耗,同时产生制动噪声[5]。
高速列车的运行速度高、惯性大,进行有效制动时需要很高的制动能量,闸片温升很高,瞬态温度有时可达1000℃,要求闸片具有更高的力学强度、稳定的摩擦系数、优良的耐磨性和抗高温氧化性[6]。
而传统的铜基摩擦材料,以片状石墨作为润滑剂。
但是片状石墨的高温抗氧化能力较差,在450℃开始氧化,并且随着温度的升高氧化急剧增加。
因此,在这样高的温度下,摩擦材料中石墨的氧化会降低列车制动力、增加闸片的磨损,影响到列车的安全。
同时,石墨和基体的粘结力很小,可以把石墨当作孔隙对待。
在刹车材料中,一定孔隙量的存在有利于改善其磨损性能,特别是在有固体润滑剂存在的条件下,有利于储存固体润滑剂而改善磨损性能;但是过量的孔隙会降低材料的连续性,对摩擦产生不利影响。
2 Ti3SiC2材料的研究
三元层状化合物Ti3SiC2是新型可加工陶瓷材料MAX相的典型代表,具有与石墨类似的层状结构和自润滑性,其导热性能优异,更重要的是它具有优于片状石墨的抗热震性和高温抗氧化性[8]。
刘光明等人[9]研究了Ti3SiC2在1100℃空气中的循环氧化行为,其氧化层主要由TiO2和SiO2组成,氧化产物的外层为较完整致密的TiO2,内层为SiO2和TiO2的混合氧化物,在内层氧化物中存在贯穿性裂纹,显示出了非常好的高温抗氧化能力。
在Ti3SiC2和Cu的研究中,我们发现在二者的烧结中(如图1),850℃时,试样中出现了较多的TiSi2相,900℃时,TiSi2相减少,同时出现了Ti3Cu相,到了950℃则完全变为
Ti3Cu相,另外TiC的量大量增加。
由此可见,Ti3SiC2和Cu在高温下发生了界面反应,金属Cu在高温下局部率先熔融为液态,在850℃时,Cu的扩散会导致Ti3SiC2的分解,生成TiSi2相。
随着温度的提高,高温Cu液作用使得TiSi2晶体结构中的Ti-Si键断裂,Si原子游离出来,扩散到Cu里面,形成Ti(Si)固溶体,Ti3SiC2界面上则剩下更稳定的Ti-C八面体。
这种扩散会增强Cu和Ti3SiC2的界面结合能力,提高Ti3SiC2和Cu的润湿性。
在刹车片材料的研究中(如图2),采用Cu为基体,以Ni、Fe和微量金属作为基体增强相,摩擦剂采用SiO2,同时加入Ti3SiC2颗粒作为润滑剂。
经高温烧结后,试样在高速高比压的条件下进行摩擦磨损试测试,结果在试样的摩擦表面检测到了SiO2、TiO等物质。
这说明,Ti3SiC2参与了试样摩擦过程,磨损产物参与了表面膜的形成,同时当摩擦表面温度达到一定程度后,表面开始氧化。
Ti3SiC2在高温摩擦过程中发生了分解、氧化,生成了Ti和Si 的氧化物,这些氧化物具有一定的黏性和流动性,参与了润滑膜的形成。
同时,SiO2、TiO的产生能够很好的阻断Ti3SiC2和空气的接触,避免更多的Ti3SiC2产生氧化,起到了很好的高温抗氧化的能力。
3 展望
研究发现,Ti3SiC2在高温下和Cu会发生双向的扩散反应,这增强了Ti3SiC2和Cu基体的结合强度,提升了铜基摩擦材料整体的高温抗软化能力。
更重要的是,Ti3SiC2良好的高温抗氧化能力能够保证摩擦材料在很高的温度下摩擦稳定。
因此,在我国高速铁路不断发展的今天,Ti3SiC2有能力替代片状石墨成为新的润滑剂应用到高速铁路刹车材料中,以适应我国刹车材料的研究方向和发展现状。
参考文献:
[1]李世珷.世界高速铁路发展的动向[J].新技术应用,2007,35(1):35.
[2]冯晓芳.中国高速铁路的发展与展望[J].Science&Technology Information, 2009,1(29):129-130.
[3]白新桂,李明,许明等. 金属陶瓷成分对其摩擦磨损性能影响研究[J].机械工程材料,1997,21(4):13-15.
[4]曲在纲,黄月初.粉末冶金摩擦材料[M].北京:冶金工业出版社,2005:24-25.
作者简介:
张兴旺(1987- ),工程师,从事轨道交通车辆制动系统研究。