磨削过程残余应力
(完整版)残余应力

残余应力(Residual Stress)消除外力或不均匀的温度场等作用后仍留在物体内的自相平衡的内应力。
机械加工和强化工艺都能引起残余应力。
如冷拉、弯曲、切削加工、滚压、喷丸、铸造、锻压、焊接和金属热处理等,因不均匀塑性变形或相变都可能引起残余应力。
残余应力一般是有害的,如零件在不适当的热处理、焊接或切削加工后,残余应力会引起零件发生翘曲或扭曲变形,甚至开裂。
或经淬火、磨削后表面会出现裂纹。
残余应力的存在有时不会立即表现为缺陷,而当零件在工作中因工作应力与残余应力的叠加,使总应力超过强度极限时,便出现裂纹和断裂。
零件的残余应力大部分都可通过适当的热处理消除。
残余应力有时也有有益的方而,它可以被控制用来提高零件的疲劳强度和耐磨性能。
[1]工件在制造过程中,将受到来自各种工艺等因素的作用与影响;当这些因素消失之后,若构件所受到的上述作用与影响不能随之而完全消失,仍有部分作用与影响残留在构件内,则这种残留的作用与影响。
也称残余应力。
残余应力是当物体没有外部因素作用时,在物体内部保持平衡而存在的应力。
凡是没有外部作用,物体内部保持自相平衡的应力,称为物体的固有应力,或称为初应力,亦称为内应力。
测试仪器编辑残余应力分析仪其原理是基于著名的布拉格方程2dsinθ=nλ :即一定波长的X射线照射到晶体材料上,相邻两个原子面衍射时的X射线光程差正好是波长的整数倍。
通过测量衍射角变化Δθ从而得到晶格间距变化Δd,根据胡克定律和弹性力学原理,计算出材料的残余应力。
应力方程根据弹性力学理论, 在宏观各向同性晶体材料上角度φ和ψ(见图1)方向的应变可以用如下方程表述:(图1)正应力和剪切应力应力分量σφ和τφ为方向Sφ上正应力和剪切应力:含剪切应力的应力方程和曲线如果在垂直于试样表面上的平面上有剪应力存在(τ13≠0和/或τ23≠0),则εφψ与sin2ψ的函数关系是一个椭圆曲线,在ψ> 0和ψ<0是图形显示为“ψ分叉”(见图3)。
磨削减薄硅片变形测量与残余应力计算
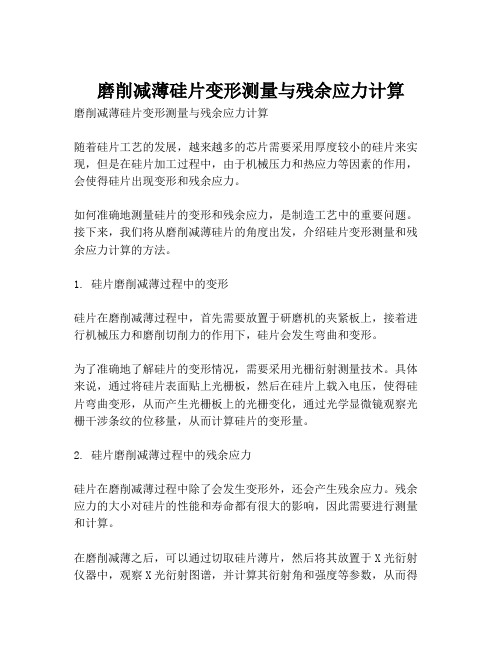
磨削减薄硅片变形测量与残余应力计算磨削减薄硅片变形测量与残余应力计算
随着硅片工艺的发展,越来越多的芯片需要采用厚度较小的硅片来实现,但是在硅片加工过程中,由于机械压力和热应力等因素的作用,会使得硅片出现变形和残余应力。
如何准确地测量硅片的变形和残余应力,是制造工艺中的重要问题。
接下来,我们将从磨削减薄硅片的角度出发,介绍硅片变形测量和残余应力计算的方法。
1. 硅片磨削减薄过程中的变形
硅片在磨削减薄过程中,首先需要放置于研磨机的夹紧板上,接着进行机械压力和磨削切削力的作用下,硅片会发生弯曲和变形。
为了准确地了解硅片的变形情况,需要采用光栅衍射测量技术。
具体来说,通过将硅片表面贴上光栅板,然后在硅片上载入电压,使得硅片弯曲变形,从而产生光栅板上的光栅变化,通过光学显微镜观察光栅干涉条纹的位移量,从而计算硅片的变形量。
2. 硅片磨削减薄过程中的残余应力
硅片在磨削减薄过程中除了会发生变形外,还会产生残余应力。
残余应力的大小对硅片的性能和寿命都有很大的影响,因此需要进行测量和计算。
在磨削减薄之后,可以通过切取硅片薄片,然后将其放置于X光衍射仪器中,观察X光衍射图谱,并计算其衍射角和强度等参数,从而得
到硅片的应力分布。
除此之外,还可以采用拉伸测试和椭圆偏振仪等技术进行测量和计算,得到硅片的残余应力分布情况。
总之,硅片在磨削减薄过程中,不可避免地会出现变形和残余应力。
只有通过精确的测量和计算,才能有效地评估硅片的质量和性能。
希
望以上内容对读者有所帮助。
金属切削的基础知识

切削过程: 三个变形区
(1)第一变形区
(2)第二变形区: (3)第三变形区:
制造技术
切屑种类:
1)带状切屑
外形连绵不断,与前刀 面接触的面很光滑,背面呈毛 茸状。用较大前角、较高的切 削速度和较小的进给量切削塑 性材料时,容易得到带状切屑。
制造技术
2)崩碎切屑 切削铸铁等脆性材料
制造技术
二、切削热的传散
在一般干切削的情况下,大部分的切削热由切屑传散出 去,其次由工件和刀具传散,而周围介质传散出去的热量很 少。但各种传散热量的比例,随着工件材料、刀具材料、切 削用量、刀具角度及切削方式等切削条件的不同而异。 切削热传散给切削及周围介质,对切削加工没有影响, 且传散得越多越好。 切削热传散给刀具切削部分,使刀具磨损加快,缩短刀 具的使用寿命;切削热传散给工件,影响工件的加工精度和 表面质量。 为了减小切削热对工件加工质量的不良影响,可采取的 两方面工艺措施:一是减小工件材料的变形抗力和摩擦阻力, 降低功率消耗和减少切削热;二是要加速切削热的传散,以 降低切削温度。
面粗糙度;严重时,会引起崩刀打刀,加速刀具的磨损。 二、表层材质变化
1.加工硬化
加工硬化是指在切削过程中,工件已加工表面受刀刃和后 面的挤压和摩擦而产生塑性变形,使表层组织发生变化,硬度 显著提高的现象。硬化层深度可达到0.02~0.03mm,表层硬度 约为工件材料的1.2~2倍。
制造技术
对加工硬化的影响因素:刀具几何参数、切削条件、工件
制造技术
2.润滑作用 金属切削加工液(简称切削液)在切削过程中的润滑作用, 可以减小前刀面与切屑,后刀面与已加工表面间的摩擦,形成部 分润滑膜,从而减小切削力、摩擦和功率消耗,降低刀具与工件 坯料摩擦部位的表面温度和刀具磨损,改善工件材料的切削加工 性能。在磨削过程中,加入磨削液后,磨削液渗入砂轮磨粒-工 件及磨粒-磨屑之间形成润滑膜,使界面间的摩擦减小,防止磨 粒切削刃磨损和粘附切屑,从而减小磨削力和摩擦热,提高砂轮 耐用度以及工件表面质量。 3.清洗和排屑作用 在金属切削过程中,要求切削液有良好的清洗作用。除去生 成切屑、磨屑以及铁粉、油污和砂粒,防止机床和工件、刀具的 沾污,使刀具或砂轮的切削刃口保持锋利,不致影响切削效果。 对于油基切削油,粘度越低,清洗能力越强,尤其是含有煤油、 柴油等轻组份的切削油,渗透性和清洗性能就越好。含有表面活 性剂的水基切削液,清洗效果较好,因为它能在表面上形成吸附
磨削过程残余应力
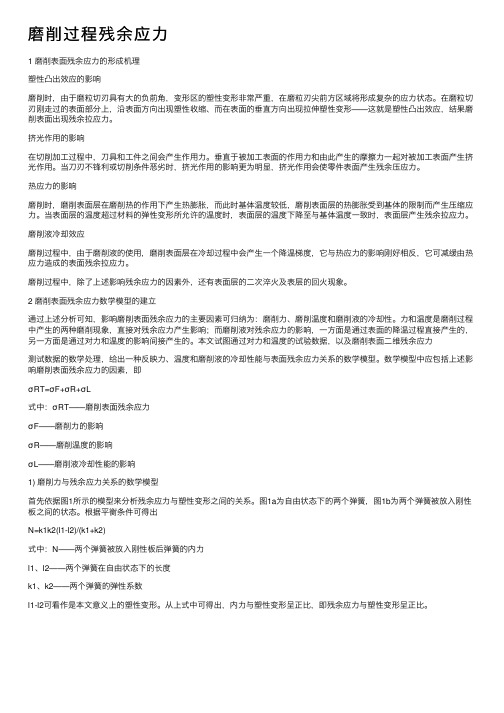
磨削过程残余应⼒1 磨削表⾯残余应⼒的形成机理塑性凸出效应的影响磨削时,由于磨粒切刃具有⼤的负前⾓,变形区的塑性变形⾮常严重,在磨粒刃尖前⽅区域将形成复杂的应⼒状态。
在磨粒切刃刚⾛过的表⾯部分上,沿表⾯⽅向出现塑性收缩、⽽在表⾯的垂直⽅向出现拉伸塑性变形——这就是塑性凸出效应,结果磨削表⾯出现残余拉应⼒。
挤光作⽤的影响在切削加⼯过程中,⼑具和⼯件之间会产⽣作⽤⼒。
垂直于被加⼯表⾯的作⽤⼒和由此产⽣的摩擦⼒⼀起对被加⼯表⾯产⽣挤光作⽤。
当⼑刃不锋利或切削条件恶劣时,挤光作⽤的影响更为明显,挤光作⽤会使零件表⾯产⽣残余压应⼒。
热应⼒的影响磨削时,磨削表⾯层在磨削热的作⽤下产⽣热膨胀,⽽此时基体温度较低,磨削表⾯层的热膨胀受到基体的限制⽽产⽣压缩应⼒。
当表⾯层的温度超过材料的弹性变形所允许的温度时,表⾯层的温度下降⾄与基体温度⼀致时,表⾯层产⽣残余拉应⼒。
磨削液冷却效应磨削过程中,由于磨削液的使⽤,磨削表⾯层在冷却过程中会产⽣⼀个降温梯度,它与热应⼒的影响刚好相反,它可减缓由热应⼒造成的表⾯残余拉应⼒。
磨削过程中,除了上述影响残余应⼒的因素外,还有表⾯层的⼆次淬⽕及表层的回⽕现象。
2 磨削表⾯残余应⼒数学模型的建⽴通过上述分析可知,影响磨削表⾯残余应⼒的主要因素可归纳为:磨削⼒、磨削温度和磨削液的冷却性。
⼒和温度是磨削过程中产⽣的两种磨削现象,直接对残余应⼒产⽣影响;⽽磨削液对残余应⼒的影响,⼀⽅⾯是通过表⾯的降温过程直接产⽣的,另⼀⽅⾯是通过对⼒和温度的影响间接产⽣的。
本⽂试图通过对⼒和温度的试验数据,以及磨削表⾯⼆维残余应⼒测试数据的数学处理,给出⼀种反映⼒、温度和磨削液的冷却性能与表⾯残余应⼒关系的数学模型。
数学模型中应包括上述影响磨削表⾯残余应⼒的因素,即σRT=σF+σR+σL式中:σRT——磨削表⾯残余应⼒σF——磨削⼒的影响σR——磨削温度的影响σL——磨削液冷却性能的影响1) 磨削⼒与残余应⼒关系的数学模型⾸先依据图1所⽰的模型来分析残余应⼒与塑性变形之间的关系。
磨削缺陷分析与解决

磨削缺陷分析与解决1.产生原因及影响因素零件的磨削精度指零件在磨削加工后,其形状、尺寸及表面相互位置三方面与理想零件的符合程度。
一般说来,形状精度高于尺寸精度,而位置精度也应高于尺寸精度。
磨削加工中的误差主要来源与两方面。
一是磨床-夹具-砂轮组成的工艺系统本身误差;二是磨削过程中出现的载荷和各种干扰:包括力变形、热变形、振动、磨损等引起的误差。
而在磨削过程中,使砂轮与工件位置改变以降低磨削精度的主要原因有:⑴.由磨削力引起的磨床和工件弹性变形;⑵.磨床和工件的热变形;⑶.磨床和工件的振动;⑷.砂轮磨损后其形状、尺寸变化;⑸.工装、夹具的损坏或变形;⑹.导轨、轴承和轴等部件的非弹性变形。
其中磨削过程中的弹性变形是主要的影响因素,它会使砂轮的实际切入深度与输入切入深度不一致,这一变化是由“砂轮架—砂轮轴承-砂轮轴-工件-工件支承”的弹性系统刚性决定。
一般为消除这种原因带来的误差常在行程进给磨削后,停止相互间的进给,仅依靠弹性回复力维持磨削,即光磨阶段(又叫清火花磨削),从而消除残留余量。
当然造成磨削误差的其它因素液很多如:工件磨削形状误差,工件热变形,磨粒切刃引起的塑性变形,砂轮的磨损等。
2.对工件的影响:降低工件使用寿命;降低工件抗疲劳强度;特殊特性的尺寸精度误差易影响工件使用,如轴承孔尺寸的控制,尺寸过小,安装不到轴上;过大,易引起振动,影响轴承使用寿命等。
3.解决方法:增加系统刚性;减少上工序加工留量,以减小磨削厚度,从而减小磨削力降低残留应力;增加光磨时间;及时修整砂轮,及时检查工装、夹具、轴承完好性及电主轴的振动性等;精细的选择砂轮,如挑选细粒度,硬度较大,组织稍紧密的砂轮;选用导热性好的砂轮(如CBN 砂轮);采用冷却性能优良的磨削液以减少因热变形引起的误差。
二、工件表面粗糙度1.产生原因及影响因素表面粗糙度指加工表面具有较小间距和峰谷所组成微观几何形状特征。
它是大量磨粒在工件表面进行切削后留下的微观痕迹的集合。
GH4169材料磨削后数控抛光表面残余应力分析

GH4169材料磨削后数控抛光表面残余应力分析高世民;全芳【摘要】CNC Polishing can have a low roughness with a high consistency.The influence of CNC polishing of wool felt wheel on residual stress is investigated.The normal residual stress in the feed direction shows a trend from rise to decline,while in the vertical feel direction it stays unchanged basically and then decreases.The optimized times of polishing is 3.The "Reinforcing Bar" model is put forward in order to explain the impact on the residual stress from polishing.Another polishing experiment is conducted for verifying roughly the impact relation.%数控抛光能够达到一致性较高的表面粗糙度要求.试验研究了羊毛毡轮数控抛光层数对磨削后GH4169表面残余应力的影响,进给方向表面残余正应力随深度增加先升高后下降,而垂直进给方向表面残余正应力先基本不变后下降,优化抛光层数为3层.针对磨削后抛光工艺,提出了“加强筋”模型,将羊毛毡轮抛光过程分为两个阶段,解释了抛光对表面残余应力的影响机理,并改变抛光参数进行了初步的试验验证.【期刊名称】《航空制造技术》【年(卷),期】2017(000)007【总页数】4页(P97-100)【关键词】GH4169;抛光;表面完整性;表面残余应力【作者】高世民;全芳【作者单位】北京航空航天大学机械工程及自动化学院,北京100191;北京航空航天大学机械工程及自动化学院,北京100191【正文语种】中文GH4169高温合金在-253~700℃温度范围内具有良好的综合性能,抗疲劳、抗腐蚀、抗氧化性能高[1],广泛应用于航空发动机压气机叶片[2]。
磨削淬硬技术的工艺性能
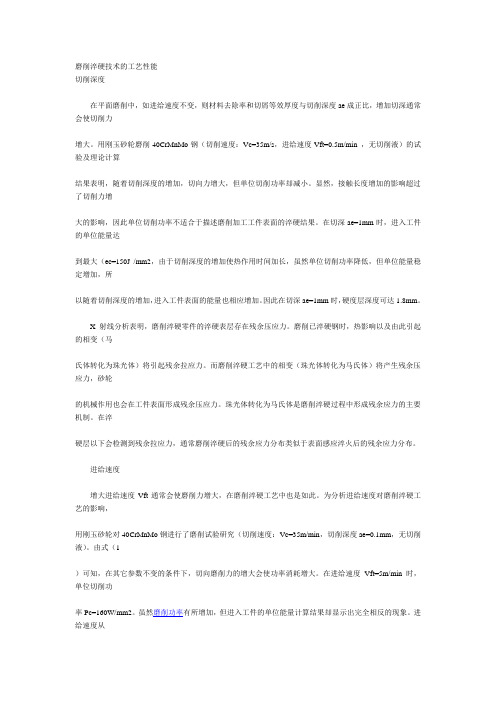
磨削淬硬技术的工艺性能切削深度在平面磨削中,如进给速度不变,则材料去除率和切屑等效厚度与切削深度ae成正比,增加切深通常会使切削力增大。
用刚玉砂轮磨削40CrMnMo钢(切削速度:Vc=35m/s,进给速度Vft=0.5m/min ,无切削液)的试验及理论计算结果表明,随着切削深度的增加,切向力增大,但单位切削功率却减小。
显然,接触长度增加的影响超过了切削力增大的影响,因此单位切削功率不适合于描述磨削加工工件表面的淬硬结果。
在切深ae=1mm时,进入工件的单位能量达到最大(ec=150J /mm2,由于切削深度的增加使热作用时间加长,虽然单位切削功率降低,但单位能量稳定增加,所以随着切削深度的增加,进入工件表面的能量也相应增加。
因此在切深ae=1mm时,硬度层深度可达1.8mm。
X 射线分析表明,磨削淬硬零件的淬硬表层存在残余压应力。
磨削已淬硬钢时,热影响以及由此引起的相变(马氏体转化为珠光体)将引起残余拉应力。
而磨削淬硬工艺中的相变(珠光体转化为马氏体)将产生残余压应力,砂轮的机械作用也会在工件表面形成残余压应力。
珠光体转化为马氏体是磨削淬硬过程中形成残余应力的主要机制。
在淬硬层以下会检测到残余拉应力,通常磨削淬硬后的残余应力分布类似于表面感应淬火后的残余应力分布。
进给速度增大进给速度Vft通常会使磨削力增大,在磨削淬硬工艺中也是如此。
为分析进给速度对磨削淬硬工艺的影响,用刚玉砂轮对40CrMnMo钢进行了磨削试验研究(切削速度:Vc=35m/min,切削深度ae=0.1mm,无切削液)。
由式(1)可知,在其它参数不变的条件下,切向磨削力的增大会使功率消耗增大。
在进给速度Vft=5m/min 时,单位切削功率Pc=160W/mm2。
虽然磨削功率有所增加,但进入工件的单位能量计算结果却显示出完全相反的现象。
进给速度从Vft=0.01m/min增加到Vft=5.0m/min时,单位能量的计算结果由ec=1150J/mm2骤减至25J/mm2。
整体硬质合金刀具磨削裂纹的原因分析及其工艺改进

整体硬质合金刀具磨削裂纹的原因分析及其工艺改进1 引言整体硬质合金刀具在航空航天业、模具制造业、汽车制造业、机床制造业等领域得到越来越广泛的应用,尤其是在高速切削领域占有越来越重要的地位。
在高速切削领域,由于对刀具安全性、可靠性、耐用度的高标准要求,整体硬质合金刀具内在和表面的质量要求也更加严格。
而随着硬质合金棒材尤其是超细硬质合金材质内在质量的不断提高,整体硬质合金刀具表面的质量情况越来越受到重视。
众所周知,硬质合金刀具的使用寿命除了与其耐磨性有关外,也常常表现在崩刃、断刃、断裂等非正常失效方面,磨削后刀具的磨削裂纹等表面缺陷则是造成这种非正常失效的重要原因之一。
这些表面缺陷包括经磨削加工后暴露于表面的硬质合金棒料内部粉末冶金制造缺陷(如分层、裂纹、未压好、孔洞等)以及磨削过程中由于不合理磨削在磨削表面造成的磨削裂纹缺陷,而磨削裂纹则更为常见。
这些磨削裂纹,采用肉眼、放大镜、浸油吹砂、体视显微镜和工具显微镜等常规检测手段往往容易造成漏检,漏检的刀具在使用时尤其是在高速切削场合可能会造成严重的后果,因此整体硬质合金刀具产品磨削裂纹缺陷的危害很大。
因此对整体硬质合金刀具磨削裂纹的产生原因进行分析和探讨,并提出有效防止磨削裂纹的工艺改进措施具有很重要的现实意义。
2 整体硬质合金刀具磨削裂纹的原因分析1.整体硬质合金刀具的磨削加工特点硬质合金材料由于硬度高,脆性大,导热系数小,给刀具的刃磨带来了很大困难,尤其是磨削余量很大的整体硬质合金刀具。
硬度高就要求有较大的磨削压力,导热系数低又不允许产生过大的磨削热量,脆性大导致产生磨削裂纹的倾向大。
因此,对硬质合金刀具刃磨,既要求砂轮有较好的自砺性,又要有合理的刃磨工艺,还要有良好的冷却,使之有较好的散热条件,减少磨削裂纹的产生。
一般在刃磨硬质合金刀具时,温度高于600℃,刀具表面层就会产生氧化变色,造成程度不同的磨削烧伤,严重时就容易使硬质合金刀具产生裂纹。
【金属切削原理】第12章:磨削详解
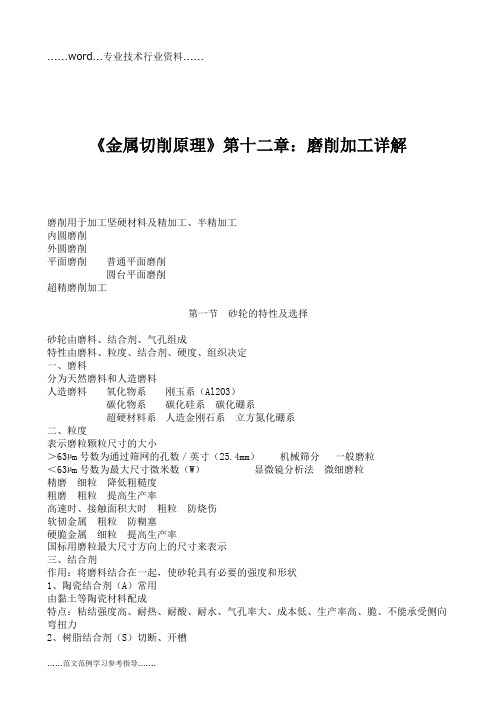
《金属切削原理》第十二章:磨削加工详解磨削用于加工坚硬材料及精加工、半精加工内圆磨削外圆磨削平面磨削普通平面磨削圆台平面磨削超精磨削加工第一节砂轮的特性及选择砂轮由磨料、结合剂、气孔组成特性由磨料、粒度、结合剂、硬度、组织决定一、磨料分为天然磨料和人造磨料人造磨料氧化物系刚玉系(Al2O3)碳化物系碳化硅系碳化硼系超硬材料系人造金刚石系立方氮化硼系二、粒度表示磨粒颗粒尺寸的大小>63µm号数为通过筛网的孔数/英寸(25.4mm)机械筛分一般磨粒<63µm号数为最大尺寸微米数(W)显微镜分析法微细磨粒精磨细粒降低粗糙度粗磨粗粒提高生产率高速时、接触面积大时粗粒防烧伤软韧金属粗粒防糊塞硬脆金属细粒提高生产率国标用磨粒最大尺寸方向上的尺寸来表示三、结合剂作用:将磨料结合在一起,使砂轮具有必要的强度和形状1、陶瓷结合剂(A)常用由黏土等陶瓷材料配成特点:粘结强度高、耐热、耐酸、耐水、气孔率大、成本低、生产率高、脆、不能承受侧向弯扭力2、树脂结合剂(S)切断、开槽酚醛树脂、环氧树脂特点:强度高、弹性好、耐热性差、易自砺、气孔率小、易糊塞、磨损快、易失廓形、与碱性物质易反应、不易长期存放3、橡胶结合剂(X)薄砂轮、切断、开槽、无心磨导轮人造橡胶特点:弹性好、强度好、气孔小、耐热性差、生产率低4、金属结合剂(Q)磨硬质合金、玻璃、宝石、半导体材料青铜结合剂(制作金刚石砂轮)特点:强度高、自砺性差、形面成型性好、有一定韧性四、硬度在磨削力作用下,磨粒从砂轮表面脱落的难易程度分为超软、软、中软、中、中硬、硬、超硬工件材料硬砂轮软些防烧伤工件材料软砂轮硬些充分发挥磨粒作用接触面积大软砂轮精度、成形磨削硬砂轮保持廓形粒度号大软砂轮防糊塞有色金属、橡胶、树脂软砂轮防糊塞五、组织磨粒、气孔、结合剂体积的比例关系分为:紧密(0~3)、中等(4~7)、疏松(8~14)(磨粒占砂轮体积%↘)气孔、孔穴开式(与大气连通)占大部分,影响较大闭式(与大气不连通)尺寸小、影响小开式空洞型蜂窝型前两种构成砂轮内部主要的冷却通道管道型5~50µm六、砂轮的型号标注形状、尺寸、磨料、粒度号、硬度、组织号、结合剂、允许最高圆周线速度P300x30x75WA60L6V35外径300,厚30,内径75第二节磨削运动一、磨削运动1、主运动砂轮外圆线速度 m/s2、径向进给运动进给量fr 工件相对砂轮径向移动的距离间歇进给 mm/st 单行程mm/dst 双行程连续进给 mm/s3、轴向进给运动进给量fa 工件相对砂轮轴向的进给运动圆磨 mm/r平磨 mm/行程4、工件速度vw线速度 m/s二、磨削金属切除率ZQ=Q/B=1000·vw·fr·fa/B mm^3/(s·mm)ZQ:单位砂轮宽度切除率Q:每秒金属切除量用以表示生产率B:砂轮宽度三、砂轮与工件加工表面接触弧长lc=sqrt(fr·d0)影响参加磨削磨粒数目及磨粒负荷,容屑,冷却条件四、砂轮等效直径将外圆(内圆)砂轮直径换算成接触弧长相等的假想平面磨削的砂轮直径结论:对砂轮耐用度影响内圆>平面>外圆第三节磨削的过程一、单个磨粒的磨削过程磨粒的模型锐利120°圆锥钝化半球实际磨粒:大的负前角,大的切削刃钝圆半径滑擦、耕犁、切削滑擦:(不切削,不刻划)产生高温,引起烧伤裂纹耕犁:(划出痕迹)磨粒钝或切削厚度小于临界厚度,工件材料挤向两侧隆起切削:切削厚度大于临界厚度,形成切屑v↑→隆起↓(线性)塑性变形速度<磨削速度二、磨削的特点1、精度高、表面粗糙度小高速、小切深、机床刚性2、径向分力Fn较大多磨粒切削3、磨削温度高磨粒角度差、挤压和摩擦、砂轮导热差4、砂轮的自砺作用三、磨削的阶段1、初磨阶段实际磨深小于径向进给量2、稳定阶段实际磨深等于径向进给量3、清磨阶段实际磨深趋向于0提高生产率缩短1、2提高质量保证3第四节磨削力及磨削功率一、磨削力的特征分解成三个分力Ft切向力 Fn法向力 Fa轴向力特征:1、单位切削力k很大磨粒几何形状的随机性和参数的不合理性7000~20000kgf/mm^2 其他切削方式k<700kgf/mm^22、Fn值最大Fn/Ft 通常2.0~2.5工件塑性↓、硬度↑→Fn/Ft↑切深小,砂轮严重磨损 Fn/Ft 可达5~103、磨削力随磨削阶段变化初磨、稳定、光磨二、磨削力及磨削功率摩擦耗能占相当大的比例(70~80%)切向力(N):Ft=9.81·(CF·(vw·fr·B/v)+µ·Fn)径向力(N):Fn=9.81·CF·(vw·fr·B/v)·tan(α)·(π/2) vw:工件速度v:砂轮速度fr:径向进给量B:磨削宽度CF:切除单位体积切屑所需的能 kgf/mm^2µ:工件-砂轮摩擦系数α:假设粒度为圆锥时的锥顶半角磨削功率P=Ft·v/1000 Kw理论公式精度不高,常用实验测定(顶尖上安装应变片)第五节磨削温度耕犁、滑擦和形成切屑的能量全部转化成热,大部分传入工件一、磨削温度砂轮磨削区温度θA:砂轮与工件接触区的平均温度影响:烧伤、裂纹的产生磨粒磨削点温度θdot:磨粒切削刃与切屑接触部分的温度温度最高处,是磨削热的主要来源影响:表面质量、磨粒磨损、切屑熔着工件温升:影响:工件尺寸、形状精度受影响二、影响磨削温度的因素切削液为降温的主要途径1、工件速度对磨粒磨削点温度的影响大于砂轮速度vw↑→acgmax↑→F↑→θdot↑大v↑→acgmax↓→θdot↑小→摩擦热↑↗acgmax:单个磨粒最大切削厚度 mm假设:磨粒前后对齐,均匀分不在砂轮表面平面磨:acgmax=(2·vw·fa/(v·m·B))sqrt(fr/dt)外圆磨:acgmax=(2·vw·fa/(v·m·B))sqrt((fr/dt)+(fr/dw))dt:砂轮直径m:每毫米周长磨粒数用于定性分析2、径向进给量Frfr↑→acgmax↑→θdot↑fr↑→接触区↑→同时参加切削磨粒数↑→θA↑3、其他因素fa↑→θdot↑、θA↑工件材料硬度↑、强度、↑韧性↑→θdot↑、θA↑θA↑→工件温升↑vw↑→被磨削点与砂轮接触时间↓→工件温升↗三、磨削温度的测量(热电偶)第六节砂轮的磨损及表面形貌一、砂轮的磨损类型磨耗磨损磨粒磨损破碎磨损磨粒或结合剂破碎(取决于磨削力与磨粒、结合剂强度)破碎磨损消耗砂轮多磨耗磨损通过磨削力影响破碎磨损阶段初期磨损磨粒破碎磨损(个别磨粒受力大,磨粒内部应力与裂纹)二期磨损磨耗磨损三期磨损结合剂破碎磨损二、砂轮的耐用度T砂轮相邻两次修整期间的加工时间 s各因素通过平均切削厚度来影响T经验公式:T=6.67·(dw^0.6)·km·kt/(10000·(vw·fa·fr)^2)dw:工件直径kt:砂轮直径修正系数km:工件材料修正系数粗磨时间常用单位时间内磨除金属体积与砂轮磨耗体积之比来选择砂轮三、砂轮的修整作用去除钝化磨粒或糊塞住的磨粒,使新磨粒露出来增加有效切削刃,提高加工表面质量工具单颗金刚石、单排金刚石、碳化硅修整轮、电镀人造金刚石滚轮、硬质合金挤压轮等使用单颗金刚石:导程小于等于磨粒平均直径,每颗磨粒都能修整深度小于等于磨粒平均直径,提高砂轮寿命四、表面形貌单位面积上磨粒数目越多→acgmax↓→磨粒受力↓→磨粒寿命↑→T↑磨粒高度分布越均匀→粗糙度↓磨粒间距均匀性越好→粗糙度↓第七节磨削表面质量与磨削精度一、表面粗糙度比普通切削小小于 Ra2~4µmvw↓、v↑、R工↑、R砂↑、细粒度→粗糙度↓细粒度→m↑→粗糙度↓B↑→acgmax↓→粗糙度↓磨粒等高性好→粗糙度↓二、机械性能1、金相组织变化烧伤:C↑、合金元素↑→导热性↓→易烧伤高温合金↑→磨削功率↑→θA↑→易烧伤影响:破坏工件表层组织,产生裂纹,影响耐磨性和寿命2、残余应力原因:相变引起金相组织体积变化温度引起热胀冷缩和塑性变形的综合结果光磨10次残余应力减少2~3倍光磨15次残余应力减少4~5倍fa↓、fr↓→拉应力↓3、磨削裂纹磨削速度垂直方向上的裂纹(局部高温急冷造成热应力)三、磨削精度1、磨床与工件的弹性变形2、磨床与工件的热变形3、砂轮磨损导致形状尺寸变化3、磨床与工件振动研磨加工是应用较广的一种光整加工。
残余应力基本知识
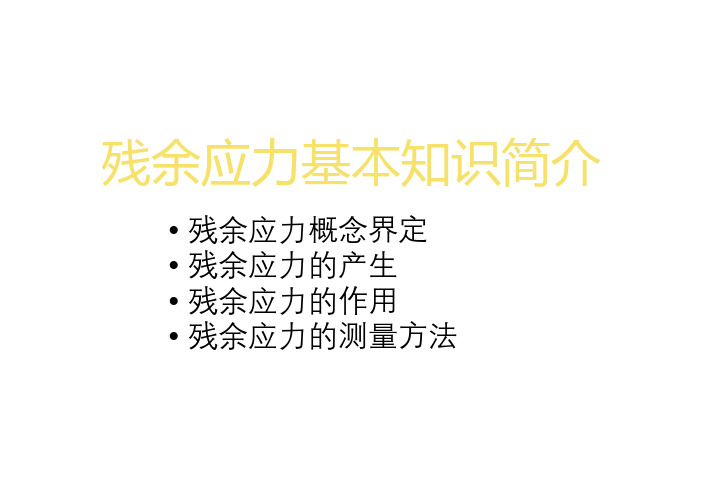
拉伸作用引起凸出效应
垂直于表面的塑性“凸出”, 按照波松比关系,必然会产生 平行于表面的塑性收缩,而表 面之下未收缩,所以,
在被切削平面产生残余拉 应力
耕犁阶段
材料塑性滑移阶段
即“塑性凸出”,表面塑性收缩阶段
表一 残余应力峰值与喷丸预应力的关系
p(Kgf/mm2) +100 +75 +50 0 -98 rp(Kgf/mm2) -91 -88 -83 -63 +5
rp 51.30.5p(Kgf/mm2) (1)
上式的线性回归相关系数为0.973。
然后,对施加不同预应力喷丸,得到不 同残余应力的的钢板弹簧进行疲劳试验, 得到了这样的S—N曲线
残余应力基本知识简介
• 残余应力概念界定 • 残余应力的产生 • 残余应力的作用 • 残余应力的测量方法
一、残余应力的基本概念
定义
• 内应力:没有外力或外力矩作用而在物体内部存在并自身保持平衡的应力。
•历史回顾 1860年 Woehler 指出火车轴的断裂有内应力作用这个因素 1925年 Masing 首次提出将内应力分为三类。 1935年 Давиденков依据各类内应力对晶体的X射线衍射
内
外
残余 应力 (MPa)
实际测试得到的分布曲线却是这样的
400
300
200
100
剥层深度 (mm)
0
10
8
6
4
2
0
-100
-200
实测曲线与理论分析所得曲线 形状相似,区别在于表层及其 以下区间多了显著的拉应力。
实际情况是:钢板弯折 并没有达到90度,焊接 时施加外力,强制焊接 成型,于是把弹性变形 固定下来。
残余应力检测方法
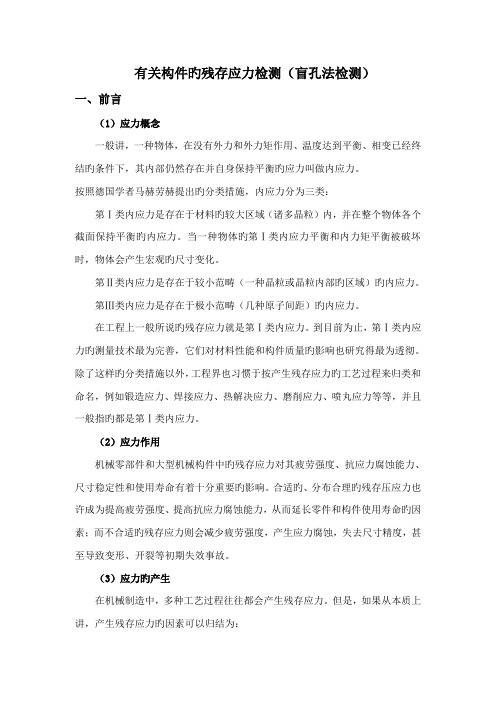
有关构件旳残存应力检测(盲孔法检测)一、前言(1)应力概念一般讲,一种物体,在没有外力和外力矩作用、温度达到平衡、相变已经终结旳条件下,其内部仍然存在并自身保持平衡旳应力叫做内应力。
按照德国学者马赫劳赫提出旳分类措施,内应力分为三类:第Ⅰ类内应力是存在于材料旳较大区域(诸多晶粒)内,并在整个物体各个截面保持平衡旳内应力。
当一种物体旳第Ⅰ类内应力平衡和内力矩平衡被破坏时,物体会产生宏观旳尺寸变化。
第Ⅱ类内应力是存在于较小范畴(一种晶粒或晶粒内部旳区域)旳内应力。
第Ⅲ类内应力是存在于极小范畴(几种原子间距)旳内应力。
在工程上一般所说旳残存应力就是第Ⅰ类内应力。
到目前为止,第Ⅰ类内应力旳测量技术最为完善,它们对材料性能和构件质量旳影响也研究得最为透彻。
除了这样旳分类措施以外,工程界也习惯于按产生残存应力旳工艺过程来归类和命名,例如锻造应力、焊接应力、热解决应力、磨削应力、喷丸应力等等,并且一般指旳都是第Ⅰ类内应力。
(2)应力作用机械零部件和大型机械构件中旳残存应力对其疲劳强度、抗应力腐蚀能力、尺寸稳定性和使用寿命有着十分重要旳影响。
合适旳、分布合理旳残存压应力也许成为提高疲劳强度、提高抗应力腐蚀能力,从而延长零件和构件使用寿命旳因素;而不合适旳残存应力则会减少疲劳强度,产生应力腐蚀,失去尺寸精度,甚至导致变形、开裂等初期失效事故。
(3)应力旳产生在机械制造中,多种工艺过程往往都会产生残存应力。
但是,如果从本质上讲,产生残存应力旳因素可以归结为:1.不均匀旳塑性变形;2.不均匀旳温度变化;3.不均匀旳相变(4)应力旳调节针对工件旳具体服役条件,采用一定旳工艺措施,消除或减少对其使用性能不利旳残存拉应力,有时还可以引入有益旳残存压应力分布,这就是残存应力旳调节问题。
一般调节残存应力旳措施有:①自然时效把构件置于室外,经气候、温度旳反复变化,在反复温度应力作用下,使残存应力松弛、尺寸精度获得稳定。
一般觉得,通过一年自然时效旳工件,残存应力仅下降2%~10%,但工件旳松弛刚度得到了较大地提高,因而工件旳尺寸稳定性较好。
消除焊接残余应力的四种方法

消除焊接残余应力的四种方法杨延功焦启林【摘要】:正1.高温回火法消除焊接残余应力的高温回火分整体和局部两种方式。
(1)整体高温回火。
将整个焊件放在炉中加热到一定温度,然后保温一段时间再冷却。
同一种材料,回火温度越高、时间越长,残余应力消除得越彻底。
通过整体高温回火可消除80%~【关键词】:消除焊接残余应力高温回火温差拉伸消除残余应力消除应力回火温度液压试验机械拉伸法焊接结构具体方法【分类号】:TG407【正文快照】:1.高温回火法消除焊接残余应力的高温回火分整体和局部两种方式。
川整体高温回火。
将整个焊件放在炉中加热到一定温度,然后保温一段时间再冷却。
同一种材料,回火温度越高、时间越长,残余应力消除得越彻底。
通过整体高温回火可消除80%- 90%的残余应力,这是生产中应用最广1、自然时效2、热时效3、振动时效(目前用的最多的一种)振动时效的实质是以共振的形式给工件施加附加动应力,当附加动应力与残余应力叠加后,达到或超过材料的屈服极限时,工件发生微观或宏观塑性变形,从而降低和均化工件内部的残余应力,并使其尺寸精度达到稳定。
残余应力产生及消除方法残余应力产生:工件经机械加工后,其表面层都存在残余应力。
残余压应力可提高工件表面的耐磨性和受拉应力时的疲劳强度,残余拉应力的作用正好相反。
若拉应力值超过工件材料的疲劳强度极限时,则使工件表面产生裂纹,加速工件的损坏。
引起残余应力的原因有以下三个方面:( 一)冷塑性变形引起的残余应力在切削力作用下,已加工表面受到强烈的冷塑性变形,其中以刀具后刀面对已加工表面的挤压和摩擦产生的塑性变形最为突出,此时基体金属受到影响而处于弹性变形状态。
切削力除去后,基体金属趋向恢复,但受到已产生塑性变形的表面层的限制,恢复不到原状,因而在表面层产生残余压应力。
( 二)热塑性变形引起的残余应力工件加工表面在切削热作用下产生热膨胀,此时基体金属温度较低,因此表层金属产生热压应力。
当切削过程结束时,表面温度下降较快,故收缩变形大于里层,由于表层变形受到基体金属的限制,故而产生残余拉应力。
残余应力

残余应力(Residual Stress)消除外力或不均匀的温度场等作用后仍留在物体内的自相平衡的内应力。
机械加工和强化工艺都能引起残余应力。
如冷拉、弯曲、切削加工、滚压、喷丸、铸造、锻压、焊接和金属热处理等,因不均匀塑性变形或相变都可能引起残余应力。
残余应力一般是有害的,如零件在不适当的热处理、焊接或切削加工后,残余应力会引起零件发生翘曲或扭曲变形,甚至开裂。
或经淬火、磨削后表面会出现裂纹。
残余应力的存在有时不会立即表现为缺陷,而当零件在工作中因工作应力与残余应力的叠加,使总应力超过强度极限时,便出现裂纹和断裂。
零件的残余应力大部分都可通过适当的热处理消除。
残余应力有时也有有益的方而,它可以被控制用来提高零件的疲劳强度和耐磨性能。
[1]工件在制造过程中,将受到来自各种工艺等因素的作用与影响;当这些因素消失之后,若构件所受到的上述作用与影响不能随之而完全消失,仍有部分作用与影响残留在构件内,则这种残留的作用与影响。
也称残余应力。
残余应力是当物体没有外部因素作用时,在物体内部保持平衡而存在的应力。
凡是没有外部作用,物体内部保持自相平衡的应力,称为物体的固有应力,或称为初应力,亦称为内应力。
测试仪器编辑残余应力分析仪其原理是基于著名的布拉格方程2dsinθ=nλ :即一定波长的X射线照射到晶体材料上,相邻两个原子面衍射时的X射线光程差正好是波长的整数倍。
通过测量衍射角变化Δθ从而得到晶格间距变化Δd,根据胡克定律和弹性力学原理,计算出材料的残余应力。
应力方程根据弹性力学理论, 在宏观各向同性晶体材料上角度θ和ψ(见图1)方向的应变可以用如下方程表述:(图1)正应力和剪切应力应力分量ζθ和ηθ为方向Sθ上正应力和剪切应力:含剪切应力的应力方程和曲线如果在垂直于试样表面上的平面上有剪应力存在(η13≠0和/或η23≠0),则εθψ与sin2ψ的函数关系是一个椭圆曲线,在ψ> 0和ψ<0是图形显示为“ψ分叉”(见图3)。
残余应力测定方法(精)

当构件中的残余应力沿厚度分布不均匀时,可采用分层钻孔法求得各深度的残余应力。其方法是:等深度地逐层钻孔测定每次的应力释放量。如果已知主应力的方向,则有:
钻孔的技术要求:
1、被测表面的处理要符合应变测量的技术要求,应变花应用502胶水准确地粘贴在测点位置上,并用胶带覆盖好丝栅,防止铁屑破坏丝栅。
2、钻孔时要保证钻杆与测量表面垂直,钻孔中心偏差应控制在±0.025 mm以内。
3、钻孔时要稳,机座不能抖动。钻孔速度要低,钻孔速度快易导致应变片的温度漂移,孔周切削应变增大使测量不稳定。为消除切削应变的影响,可先采用小钻头钻孔然后再用铣刀洗孔。
通过布拉格实验可知,晶面对X光的反射如同镜面对可见光的反射一样,它们都遵守反射定律,入射角与反射角相等。而X射线只有以某种特定的角度入射时才能发生反射。这种反射就是晶体对X射线的衍射,同可见光的衍射是一个道理。X光的特点在于它可穿透晶体内部,同时在许多相互平行的晶面上发生反射,而只有当这些反射线互相干涉加强时,才能真正产生出反射线来。其条件应当是各晶面反射线的光程差等于波长的整倍数时,才能实现反射。如图3.12所示,d为晶面间距,θ为入射角和反射角。有前述可知,要实现相互干涉加强的条件是波程差必须等于波长的整数倍。即:
在进行切割或钻环孔时,要求刀具要锋利,加工速度要慢,以避免产生塑性变形和使工件发热。
表3.1切割法和套环法测值比较表(10MPa)
方法测值
磨削过程残余应力

1 磨削表面残余应力的形成机理塑性凸出效应的影响磨削时,由于磨粒切刃具有大的负前角,变形区的塑性变形非常严重,在磨粒刃尖前方区域将形成复杂的应力状态。
在磨粒切刃刚走过的表面部分上,沿表面方向出现塑性收缩、而在表面的垂直方向出现拉伸塑性变形——这就是塑性凸出效应,结果磨削表面出现残余拉应力。
挤光作用的影响在切削加工过程中,刀具和工件之间会产生作用力。
垂直于被加工表面的作用力和由此产生的摩擦力一起对被加工表面产生挤光作用。
当刀刃不锋利或切削条件恶劣时,挤光作用的影响更为明显,挤光作用会使零件表面产生残余压应力。
热应力的影响磨削时,磨削表面层在磨削热的作用下产生热膨胀,而此时基体温度较低,磨削表面层的热膨胀受到基体的限制而产生压缩应力。
当表面层的温度超过材料的弹性变形所允许的温度时,表面层的温度下降至与基体温度一致时,表面层产生残余拉应力。
磨削液冷却效应磨削过程中,由于磨削液的使用,磨削表面层在冷却过程中会产生一个降温梯度,它与热应力的影响刚好相反,它可减缓由热应力造成的表面残余拉应力。
磨削过程中,除了上述影响残余应力的因素外,还有表面层的二次淬火及表层的回火现象。
2 磨削表面残余应力数学模型的建立通过上述分析可知,影响磨削表面残余应力的主要因素可归纳为:磨削力、磨削温度和磨削液的冷却性。
力和温度是磨削过程中产生的两种磨削现象,直接对残余应力产生影响;而磨削液对残余应力的影响,一方面是通过表面的降温过程直接产生的,另一方面是通过对力和温度的影响间接产生的。
本文试图通过对力和温度的试验数据,以及磨削表面二维残余应力测试数据的数学处理,给出一种反映力、温度和磨削液的冷却性能与表面残余应力关系的数学模型。
数学模型中应包括上述影响磨削表面残余应力的因素,即σRT=σF+σR+σL式中:RT——磨削表面残余应力F——磨削力的影响R——磨削温度的影响L——磨削液冷却性能的影响1) 磨削力与残余应力关系的数学模型首先依据图1所示的模型来分析残余应力与塑性变形之间的关系。
不同磨削加工工艺对轴承钢球残余应力的影响

、衍射晶面间距=nλ然后经过特定的软件计算应力的方向和大小,由图可知:强化-硬磨后的钢球的表面残余应力值较高,范围在-1061~-1252MPa之间,精研下车后的表面应力在-834~-1036MPa之间。
而钢球热处理后直接硬磨-强化后钢球表面应力在-757~-931MPa之间,精研下车的表面应力在-622~-758MPa之间。
通过测试数据说明,加工工艺对成品球表面残余应力值大小有直接关系,最大数据差在-500MPa左右。
钢球强化过程,是伴随着强化机的旋转碰撞和自高点图2直径12.7mm工序应力变化趋势图图1直径12.7mm工序应力变化趋势图国外某成品钢球与工艺一、工艺二剥层数据如如图由图5、图6对比趋势图来看,国内外钢球的应力趋势与工艺二的钢球应力趋势图基本相同,应力值先减小再增大,在距表面深度0.10~0.14mm 区间达到最大峰值,后逐步减小。
工艺一的趋势图,表面是最高的压应力,深度的增加,压应力逐步减小。
最大区别在于工艺一的成品球次表层不存在压应力的最大峰值,而是呈现直线降低的趋势。
因此工艺一的成品球剥层应力趋势图不利于提高钢球的疲劳寿命。
力分析,成品钢球的应力分布状态与强化后的去数量有直接关系。
②通过成品球剥层应力对比说明:钢球加工工艺二钢球次表层在0.10~0.15mm 之间出现强化峰值,可提高钢球的疲劳寿命。
参考文献:[1]GB/T7704-2017,无损检测X 射线应力测定法[S].[2]YB/T5338-2006,钢中残余奥氏体定量测定X 射线衍射仪法[S].[3]强智臻,郭昌明,柳岩,熊毕伟.柴油机气门座孔磨削工艺图4图3图5图6。
切削加工表面残余应力研究综述

切削加工表面残余应力研究综述王增强;刘超锋【摘要】主要研究了切削加工过程中残余应力产生的机理,并对残余应力的测量方法以及残余应力的调整和消除手段进行了较为系统的阐述和比较,提出了在残余应力检测和消除领域的一些建议,为进一步研究提供参考和借鉴。
【期刊名称】《航空制造技术》【年(卷),期】2015(000)006【总页数】5页(P26-30)【作者】王增强;刘超锋【作者单位】西北工业大学现代设计与集成制造教育部重点实验室;西北工业大学现代设计与集成制造教育部重点实验室【正文语种】中文残余应力主要是由构件内部不均匀的塑性变形引起的。
各种工程材料和构件在毛坯的制备、零件的加工、热处理和装配的过程中都会产生不同程度的残余应力。
残余应力因其直观性差和不易检测等因素往往被人们忽视。
残余应力严重影响构件的加工精度和尺寸稳定性、静强度、疲劳强度和腐蚀开裂。
特别是在承力件和转动件上,残余应力的存在易导致突发性破坏且后果往往十分严重。
因此,自20世纪50年代以来国内外技术人员花费了大量的精力研究残余应力的产生机理、检测手段、消除方法以及残余应力对构件的影响[1]。
Guo等通过试验的方法研究了车削和磨削产生的不同性质的残余应力对工件疲劳强度的影响[2];Seo等通过试验和有限元模拟的方法揭示了在车轮制造和火车刹车过程中引起的残余应力和火车车轮疲劳寿命之间的代数关系[3];Liu等用试验的方法研究了残余应力对滚动接触疲劳强度的影响[4];董辉跃等研究了材料去除过程中残余应力的重新分布及该过程所引起的工件变形[5];孙杰等基于理论计算和有限元模拟,研究了毛坯的初始残余应力对大型整体结构件数控加工变形的影响[6];Hiroyuki等研究了不同加工参数引起的残余应力对零件疲劳强度的影响[7],并且结合正交切削模型和刀尖圆角压痕模型建立了残余应力预测模型[8];王立涛对于铣削加工航空框类整体结构件时的残余应力和变形机理进行了研究,并将研究成果应用于实际生产[9]。
切削加工中残余应力产生的原因及影响残余应力的因素

切削加工中残余应力产生的原因及影响残余应力的因素什么是残余应力?残余应力是指在没有外力作用的情况下,在物体内保持平衡而存留的应力。
残余应力分为残余拉应力(+σ)和残余压应力(-σ)。
为了区别表层的残余应力与物体内层金属中的残余应力,因此表层残余应力的符号相反。
切削加工后的已加工表面常有残余应力。
关于残余应力的发生机理,从理论上定量分析目前还存在一些困难,以下仅从概念上来定性分析残余应力的产生原因。
1.机械应力引起的塑性变形切削过程中,切削刃前方的晶粒一部分随切屑流出,另一部分留在已加工表面上;在分离处的水平方向,晶粒受压;而在垂直方向则晶粒受拉,故形成残余拉应力。
另外,在已加工表面形成过程中,刀具的后刀面与已加工表面产生很大的挤压与摩擦,使表层金属产生拉伸塑性变形;刀具离开后,在里层金属作用下,表层金属产生残余压应力。
2.热应力引起的塑性变形切削时,由于强烈的塑性变形与摩擦,使已加工表面层的温度很高,而里层温度很低,形成不均匀的温度分布。
因此,温度高的表层,体积膨胀,将受到里层金属的阻碍,从而使表层金属产生热应力。
当热应力超过材料的屈服极限时,将使表层金属产生压缩塑性变形。
切削后冷却至室温时,表层金属体积的收缩又受到里层金属的牵制.因而使表层金属产生残余拉应力。
3.相变引起的体积变比切削时,若表层温度大于相变温度,则表层组织可能发生相变。
由于各种金相组织的体积不同,从而产生残余应力。
如高速切削碳钢时,刀具与工件接触区的温度可达600~800℃;而碳钢在720℃发生相变,形成奥氏体,冷却后变为马氏体。
由于马氏体的体积比奥氏体大,因而表层金属膨胀,但受到里层金属的阻碍,从而使表层产生残余压应力,里层产生残余拉应力。
当加工淬火钢时,若表层金属产生退火,则马氏体转变为屈氏体或索氏体,因而表层体积缩小;但受到里层金属的牵制,从而使表层产生残余拉应力。
已加工表面层内呈现的残余应力是上述诸原因所导致残余应力的综合结果,而最后已加工表面层内残余应力的大小及符号,则由其中起主导作用的因素所决定。