变速器壳体强度分析
变速器壳体的检验与修理

变速器壳体的检验与修理摘要变速器壳体是变速器的基础件。
变速器壳体的质量决定着变速器总成的工作性能、换挡灵活性、挡位噪声、密封性能和使用寿命。
本文讲述了变速器壳体在大修时所要进行的检查与修理工作。
关键词变速器壳体检验修理变速器壳体是变速器重要零件之一。
变速器壳体是变速器的基础件,它将变速器中的输入轴总成、输出轴总成、换挡机构总成等零部件,按一定的相互位置关系装配成一个整体,并支撑输出轴按一定的传动比关系输出转矩。
它上面有轴承座孔,承载着变速轴、变速齿轮,如果轴承座孔磨损,将影响变速器的工作。
变速器壳体采用整体式壳体,与上盖成一体,以保证变速器前后轴承孔的同心度。
变速器壳体有足够的刚度,以防止壳体的变形,保证轴和轴承工作时不会倾斜。
另外,壳体上还设有注油孔和放油孔,为了保持变速器内部为大气压力,在顶部开有通气孔,壳体设有动力输出孔、倒挡检查孔。
变速器壳体的质量决定着变速器总成的工作性能、换挡灵活性、挡位噪声、密封性能和使用寿命。
在变速器大修时要对变速器壳体进行如下检查与修理,以保证变速器工作正常。
1. 壳体螺纹孔的检验与修理壳体零件材料因强度较低、长期使用、频繁拆装或紧固不当、局部受力过大等原因,易造成壳体螺纹孔损坏。
变速器壳体螺纹孔损伤有注油螺塞孔、放油螺塞孔的螺纹损伤,以及壳体之间连接螺栓螺纹孔的损伤。
螺纹孔的损坏与滑牙,可采用扩孔攻丝或焊补后重新钻孔攻丝的方法修复。
2. 壳体裂纹的检验与修理变速器壳体不得有裂纹。
壳体裂纹的检验,一般采用磁力探伤机进行,或外部检视与轻轻敲击检验。
对未延伸到轴承座孔处不重要部位的裂纹,可用粘接剂粘接、螺钉填补法修复。
对重要部位的裂纹,则应进行焊接修复。
焊接时,必须先对壳体加温后再焊,防止局部内应力过大而再裂或变形。
如轴承座孔、定位销孔、螺纹孔等重要部位出现裂纹时必须更换壳体。
3.轴承座孔的检验与修理轴承座孔的磨损,将使齿轮轴线偏移和两轴线不平行,会破坏壳体与各轴承的配合关系,直接影响变速器输入、输出轴的相对位置,影响齿轮的正常工作,造成齿轮发响、跳挡等一系列故障。
镁合金汽车变速箱壳体强度分析_张少睿
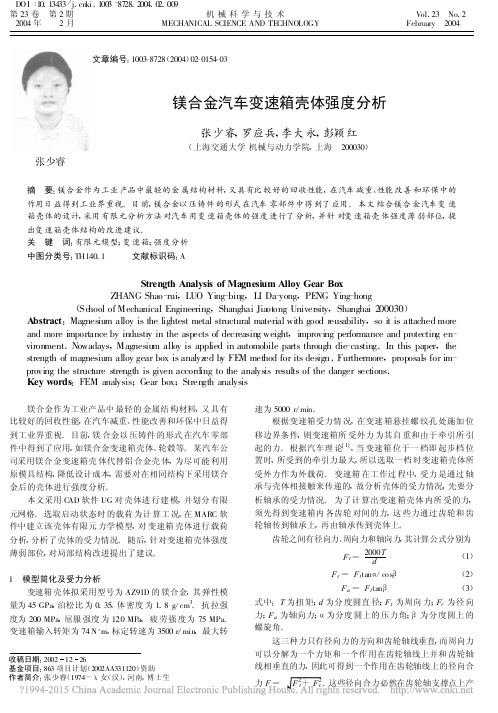
2004 年 2 月 MECHANICAL SCIENCE AND TECHNOLOGY February 2004
看出 , 壳体轴承位置处与 齿轮轴 相接触 部位及其 附近的 应 力值普遍比其他部 位偏高 , 因此 我们针 对放置 轴承 的 3 个 高应 力面进 行了 剖面处 理 , 剖面 位置 如图 1 中 A 、B 、C 所 示 。 各截面处的应力分 布分 别如图 3 ~ 5 所示 。 最大主 应 力位于一档齿轮轴与轴 承相接触部位(见 图 4), 其 值为 29. 83 MPa , 所在节点 编号 为 12522 , 此处 也即变 速箱 最易发 生 开裂的地 方 。 而 最 小 主 应力 也 在 此 截面 上 , 节点 编 号 为 11344 , 其值为 -17.85 MPa 。
15 5
生支反力 。 由于轴承采用向 心球轴承 , 主要承受径 向载荷 , 可忽略轴向因素的影响 , 因此只分析径向力的影响 。
变速箱一轴和二轴及中间轴的轴承支反力根据材料力 学不难求出 , 6 个 轴承孔处的支撑反力结果如表 1 所示 。
表 1 轴承孔处支反力作源自点ABCD
E
F
支反力(N) 3455 .7 5760.7 705.4 3470 .2 6466 .1 127 .1
本文采用 CAD 软件 UG 对 壳体进 行建 模 , 并划分 有限 元网格 。 选取启动 状态时 的载荷 为计 算工 况 , 在 MARC 软 件中建立该 壳体有限元 力学模型 , 对 变速箱 壳体进行 载荷 分析 , 分析了壳体的受力情况 。 随后 , 针对变速箱壳体强度 薄弱部位 , 对局部结构改进提出了建议 。
例析主减速器及差速器总成壳体强度

例析主减速器及差速器总成壳体强度1.引言主减速器及差速器总成、整体式车桥作为车辆传动系统关键零部件,对保证发动机动力顺利传输起到关键作用。
其壳体起到支撑、保护内部零件、承载动力及保存润滑油等作用,一旦壳体开裂,将严重影响主减速器及差速器总成的工作,甚至导致车辆的基本行驶功能丧失。
故其壳体强度尤为重要。
以某款SUV车型主减速器及差速器总成壳体为例,在产品设计阶段应用ABAQUS有限元分析软件对其强度进行分析,识别应力集中部位,为其设计开发提供参考,避免后期产品因强度问题产生失效。
有限元分析法是一种运用各种数值计算方法在计算机上对产品结构的原理、功能、性能等进行前期预测或改进的一种仿真分析技术,在缩短产品开发周期,降低产品开发成本,提高产品的性能品质,提升企业的竞争力等方面起着非常重要的作用。
2.几何模型及有限元模型运用三维设计软件CATIA建立后主减速器及差速器总成壳体三维模型,如图一所示。
为方便有限元模型建立,对三维模型进行局部简化处理[1-2]:省略局部细小特征及花键、螺纹、部分倒角、圆角。
完成后的有限元网格模型如图二所示。
其中壳体采用四面体单元,轴承、主齿等机构采用六面体单元。
最终得到体单元328924个。
3.边界条件及模型载荷加载3.1边界条件对于整体式后桥,约束安装螺栓孔及主齿螺母安装处的三向平移自由度,如图三所示。
3.2模型载荷加载3.2.1后主减速及差速器总成输入扭矩计算此款SUV车型由发动机计算的后主减速器及差速器总成最大输入扭矩为4911N·m,由单边车轮打滑计算的后主减速器及差速器总成打滑输入扭矩为1261.4N·m。
两者取小值作为模型的输入计算扭矩。
3.2.2模型载荷加载[3-4]由打滑扭矩计算出主、被齿受力,作为模型的载荷进行加载。
主齿旋向为左旋,齿轮旋转方向为顺时针(从汽车前部向后看)。
其中主齿受力如图四所示:首先确定齿轮啮合点圆周力F:式中T为被齿转矩;为被齿齿面宽中点处分度圆直径。
变速器壳体强度有限元分析与试验验证
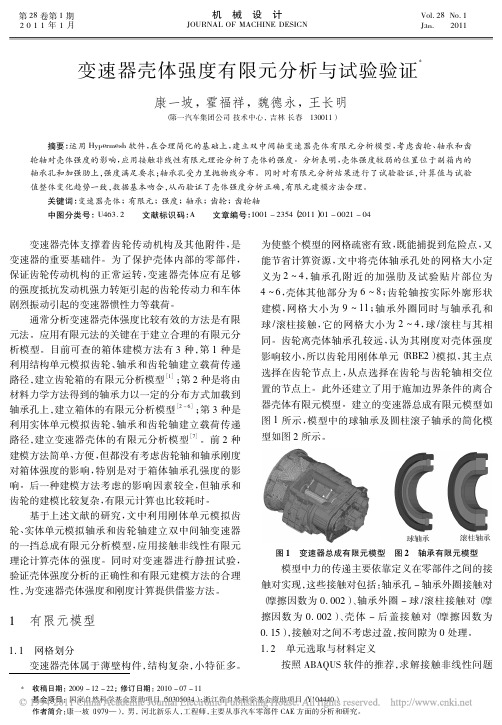
Principal) 查看。 图 4 是壳体的位移变形图,从壳体后端向前看,整
个壳体有顺时针旋转变形的趋势,相对于离合器壳体 前端固定位置的最大位移为 0. 388 mm,发生在后盖的 右上部位的固定销销孔附近,位移较小。图 5 ~ 图 7 是壳体的应力云图,最大应力值为 198. 6 MPa,发生在 壳体副箱支撑第 2 轴后轴承孔的加强肋上,靠近后盖 一侧。支撑第 2 轴后轴承孔的加强肋共有 3 条,按顺 时针排列,其他 2 条应力依次减小,最大相差 90 MPa, 可以考虑在不增加加强肋数量的同时将这 3 条加强肋 绕逆时针旋 转 一 定 角 度,使 它 们 能 比 较 均 匀 地 受 力。 副箱中的第 2 轴后轴承孔最大应力值为 96. 1 MPa,主 要是由副箱常啮合主动齿轮的轴向力引起的,可以将 放置定位盘的凹槽填平,以增加该位置的强度和刚度。 后盖轴承孔最大应力值为 152. 3 MPa,发生在后盖的 右下轴承孔上,此轴承孔的变形较大,建议布置加强肋 增加刚度。壳体主箱中的常啮合齿轮传动速比较小及 离合器壳体对主箱前端面具有支撑作用,所以计算出 的一轴前轴承孔应力和中间轴前轴承孔的应力均比较 小。主箱中间主体部分有较大的抗扭截面模量,应力 值不大,可以将主箱中间主体部位进行减薄以减小质 量,同时要注意刚度变化。
验值对比情况如图 11 所示。
图 11 计算值与试验值对比
在图 11 中,应力相对误差位于 20. 0% 以内的测 点有 8 个,其中 9 号测点的误差最小,为 2. 6% ; 误差 位于 20. 0% ~ 30. 0% 的测点有 2 个,它们是 5 号和 10 号测点,其 误 差 分 别 为 27. 8% 和 20. 8% ,5 号 测
按照 ABAQUS 软件的推荐,求解接触非线性问题
变速器壳体强度有限元仿真分析
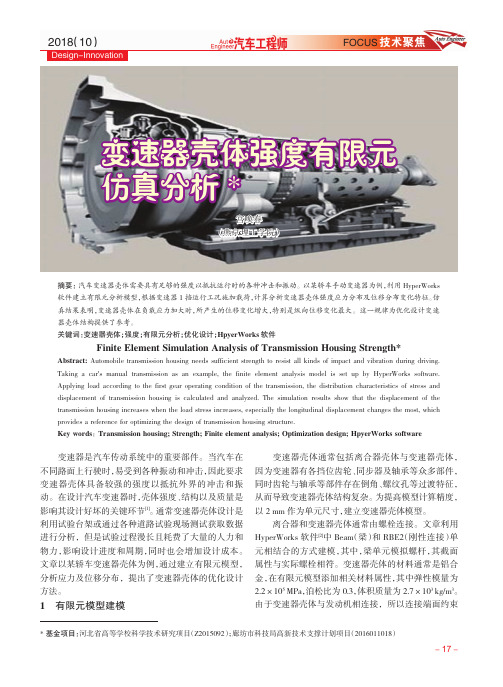
某双离合自动变速器箱体强度分析和轻量化设计
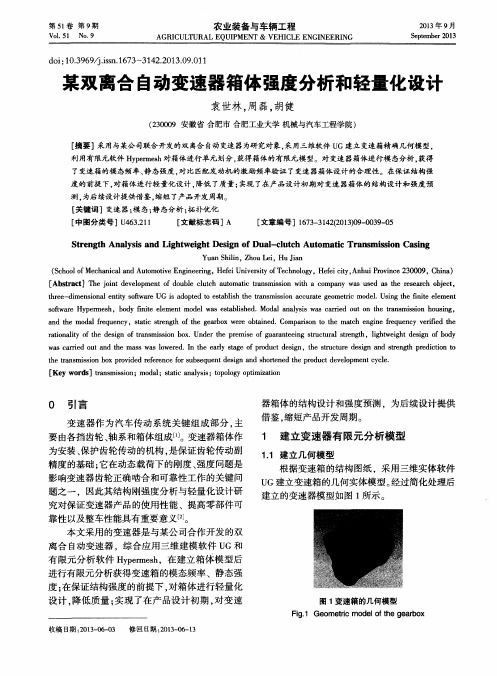
wa s c a r r i e d o u t a n d t h e ma s s wa s l o w e r e d .I n he t e a r l y s t a g e o f p r o d u c t d e s i g n,t h e s t uc r t u r e d e s i g n a n d s t r e n th g p r e d i c t i o n t o
t h r e e — — d i me n s i o n a l e n t i t y s o f t w a r e UG i s a d o p t e d t o e s t a b l i s h t h e t r a n s mi s s i o n a c c u r a t e g e o me t i r c mo d e 1 . Us i n g t h e i f n i t e e l e me n t s o f t wa r e Hy p e r me s h,b o d y i f n i t e e l e me n t mo d e l wa s e s t a b l i s h e d .Mo d a l a n ly a s i s w a s c a r r i e d o u t o n t h e t r a n s mi s s i o n h o u s i n g ,
测, 为后 续设 计 提供 借 鉴 。 缩短 了产 品 开发 周期 。
[ 关键词 ]变速器 ; 模 态; 静 态分析 ; 拓4 1 - /  ̄ 4  ̄
[ 中图分类号】U 4 6 3 . 2 1 1
[ 文献标 志码 ] A
[ 文章编号 ]1 6 7 3 — 3 1 4 2 ( 2 0 1 3 ) 0 9 — 0 0 3 9 — 0 5
变速箱壳体强度和模态分析

变速器的有限元分析变速箱壳体静力学分析本文所研究的变速箱壳体结构的几何模型如下图所示,其中变速箱壳体结构的材料为ADC12,ADC12是日本牌号,又称12号铝料,Al-Si-Cu系合金,是一种压铸铝合金,适合气缸盖罩盖、传感器支架、缸体类等,执行标准为:JIS H5302-2006《铝合金压铸件》,具体材料参数如表2.5所示。
图2.5 变速箱壳体结构几何模型表2.5 ADC12材料参数表采用ansys自带网格划分功能对变速箱壳体结构进行网格划分,在ansys中采用四面体单元进行网格划分,单元类型为solid187,该单元为高阶单元,即带有中间节点,单元的形函数为二次函数,可以更好的模拟不规则的模型。
一般来说,形函数阶次越高,计算结果越精确,因而,同线性单元相比,采用高阶的单元类型可以得到相对较好的计算结果。
Solid187单元共有10个节点,每个节点具有三个平动自由度。
,图2.6 solid187单元类型最终划分完整的有限元网格模型如下图所示,其中网格总数为1555702,节点总数为3395130,网格尺寸为3mm。
图2.7 变速箱壳体结构有限元模型变速箱壳体结构的安装孔位置施加固定约束,变速箱壳体上下盖之间通过绑定接触连接,一档和倒挡工况的轴承支反力施加在变速箱壳体结构的轴承配合面上。
一档和倒挡工况下变速箱壳体结构的载荷边界条件条件如下所示。
图2.8 一档工况下变速箱壳体结构载荷边界条件图2.9 倒挡工况下变速箱壳体结构载荷边界条件一档工况下变速箱壳体结构的等效应力云图和位移云图如下所示,其中变速箱壳体结构最大变形为0.13mm,最大值位置如图2.10所示的max标志位置处。
变速箱壳体结构最大等效应力为108.3Mpa, 最大值位置如图2.11所示的max标志位置处,位移上盖内部,如图2.12所示。
基于材料力学第四强度理论,无论什么应力状态,只要构件内一点处的形变改变比能达到单向应力下的极限值,材料就要发生屈服破坏,其中等效应力可以标准形变改变比能,材料屈服极限为180MPa,变速箱壳体结构在一档工况下最大等效应力为108.3MPa,最大值小于材料屈服极限,可以认为变速箱壳体结构在一档工况下满足强度要求,其安全系数为1.66。
某新能源汽车变速器箱体强度分析
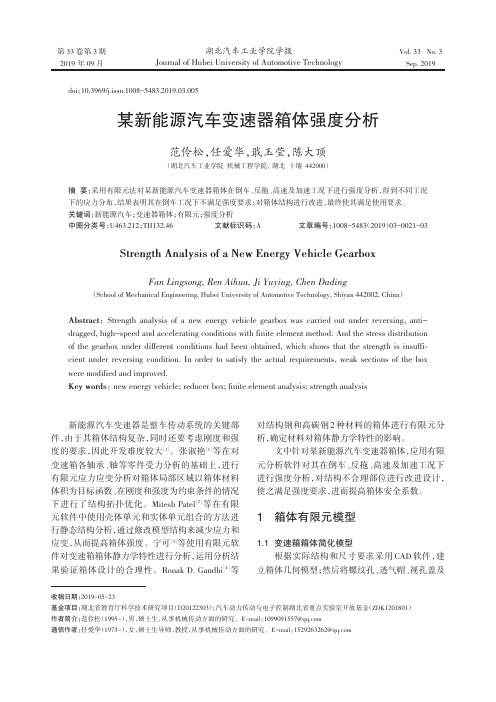
图 1 简化后的箱体 表 1 材料属性
参数 弹性模量/GPa
泊松比
数值 71 0.36
参数 密度(/ kg·m-3) 屈服强度/MPa
数值 2 700 170
到 3 912 843 个单元和 876 134 个节点。 1.2 施加载荷与约束
变速箱结构如图 2 所示,变速器右箱体与驱动 电机外壳采用螺栓固定,在分析过程中,对右箱体 输入端螺栓孔施加固定约束。通过固定螺栓孔处 节点 6 个方向的自由度,来实现对螺栓孔的完全约 束,如图 3a 所示。文中使用 Hypermesh 的 RIGIDS 刚性连接,添加至合箱螺栓座孔处,模拟左右 2 个 箱体的螺栓连接,如图 3b 所示。
立箱体几何模型;然后将螺纹孔、透气帽、视孔盖及
收稿日期:2019-05-23 基金项目:湖北省教育厅科学技术研究项目(D20122303);汽车动力传动与电子控制湖北省重点实验室开放基金(ZDK1201801) 作者简介:范伶松(1995-),男,硕士生,从事机械传动方面的研究。E-mail:1099091557@ 通信作者:任爱华(1973-),女,硕士生导师,教授,从事机械传动方面的研究。E-mail:1529263262@
新能源汽车变速器是整车传动系统的关键部 件,由于其箱体结构复杂,同时还要考虑刚度和强 度的要求,因此开发难度较大[1]。张淑艳[1]等在对 变速箱各轴承、轴等零件受力分析的基础上,进行 有限元应力应变分析对箱体局部区域以箱体材料 体积为目标函数、在刚度和强度为约束条件的情况 下进行了结构拓扑优化。Mitesh Patel[2]等在有限 元软件中使用壳体单元和实体单元组合的方法进 行静态结构分析,通过修改模型结构来减少应力和 应变,从而提高箱体强度。宁可[3]等使用有限元软 件对变速箱箱体静力学特性进行分析,运用分析结 果验证箱体设计的合理性。Ronak D. Gandhi[4]等
电动汽车用变速器壳体的模态研究

电动汽车用变速器壳体的模态研究随着电动汽车的普及,电动汽车的变速器壳体的模态研究日益成为研究热点。
变速器壳体是传递动力和支撑变速器组件的重要零部件,其结构设计对整车性能和使用寿命至关重要。
本文将从变速器壳体的结构分析、模态分析和结论分析三个方面进行研究。
首先,对电动汽车用变速器壳体的结构进行分析。
变速器壳体主要由上下盖板、固定板、中间板和侧板等组成。
其结构呈长方形,尺寸基本相同。
设计时需要考虑壳体在整个使用过程中受到的载荷、热应力和腐蚀等因素的影响,以确保其强度、刚度和密封性。
其次,进行电动汽车用变速器壳体的模态分析。
利用有限元分析软件对变速器壳体进行模态分析,求出壳体在不同频率下的振动模式和振幅。
通过对模态结果的分析,可以有效地评估变速器壳体在工作状态下的振动情况和结构强度。
最后,根据模态分析结果进行结论分析。
分析结果表明,变速器壳体在低频和中频区间振动特点较明显,而高频振动的情况较少。
变速器壳体在主要节点处的振幅较大,需要注意这些节点的防振措施。
在整个结构中,侧板的密封性较高,需要进行更加精细的加工和检测,以确保其密封性。
综上所述,电动汽车用变速器壳体的模态研究旨在评估其在工程实践中的振动特性和结构强度,为进一步完善变速器壳体的设计提供参考。
通过对电动汽车用变速器壳体的结构分析、模态分析和结论分析,可以为变速器壳体的优化设计和生产提供有力的支持。
除了结构和模态分析之外,对于电动汽车用变速器壳体的研究,还需要考虑其材料和加工工艺。
首先,材料方面的选择很关键。
由于电动汽车的操作和环境相对较为温和,传统机械传动的变速器壳体通常采用铸铁或铝合金材料。
而对于电动汽车用变速器壳体的材料,则需要更加注重其轻量化和环保性能。
目前,常用的材料包括铝合金、CFRP(碳纤维增强塑料)和镁合金。
铝合金具有较高的强度和刚度,同时重量轻、耐腐蚀性好,是广泛运用的一种材料。
CFRP 具有轻量化的优势,但是成本较高。
镁合金具有密度低、刚性好和机械性能优异等优点,但是加工难度较大。
部分变速器壳体模态试验分析与验证
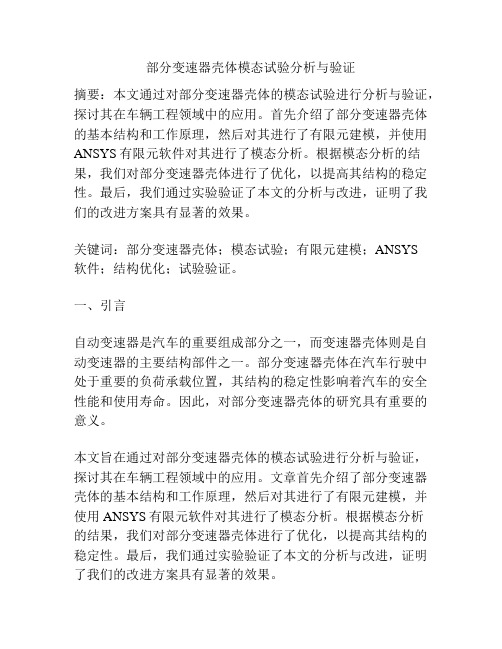
部分变速器壳体模态试验分析与验证摘要:本文通过对部分变速器壳体的模态试验进行分析与验证,探讨其在车辆工程领域中的应用。
首先介绍了部分变速器壳体的基本结构和工作原理,然后对其进行了有限元建模,并使用ANSYS有限元软件对其进行了模态分析。
根据模态分析的结果,我们对部分变速器壳体进行了优化,以提高其结构的稳定性。
最后,我们通过实验验证了本文的分析与改进,证明了我们的改进方案具有显著的效果。
关键词:部分变速器壳体;模态试验;有限元建模;ANSYS软件;结构优化;试验验证。
一、引言自动变速器是汽车的重要组成部分之一,而变速器壳体则是自动变速器的主要结构部件之一。
部分变速器壳体在汽车行驶中处于重要的负荷承载位置,其结构的稳定性影响着汽车的安全性能和使用寿命。
因此,对部分变速器壳体的研究具有重要的意义。
本文旨在通过对部分变速器壳体的模态试验进行分析与验证,探讨其在车辆工程领域中的应用。
文章首先介绍了部分变速器壳体的基本结构和工作原理,然后对其进行了有限元建模,并使用ANSYS有限元软件对其进行了模态分析。
根据模态分析的结果,我们对部分变速器壳体进行了优化,以提高其结构的稳定性。
最后,我们通过实验验证了本文的分析与改进,证明了我们的改进方案具有显著的效果。
二、部分变速器壳体的基本结构和工作原理部分变速器壳体是自动变速器中的一个组成部分,其作用是承担变速器内部传递动力的职责。
部分变速器壳体通常由铸件或冷镦加工而成,其底部一般采用多边形的形式,以适应变速器的各种形式和尺寸。
下图是部分变速器壳体的示意图。
部分变速器壳体中包含了多个部件,包括油泵、制动器和离合器等组件。
这些组件的工作往往会对部分变速器壳体的结构造成一定的冲击负荷,因此,部分变速器壳体需要具有足够的强度和刚度来承担这些负荷。
三、有限元建模和模态分析为了对部分变速器壳体的结构进行分析,我们采用了有限元建模的方法。
根据部分变速器壳体的外形和内部结构,我们进行了三维模型的建模,并在模型中添加了油泵、制动器和离合器等部件。
自动变速箱壳体强度研究
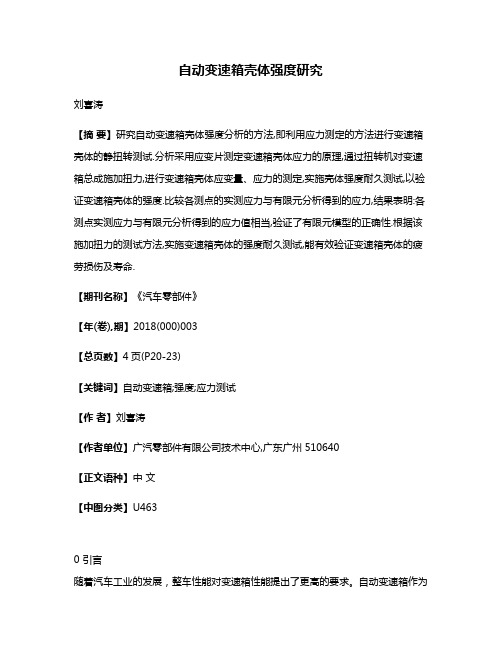
自动变速箱壳体强度研究刘喜涛【摘要】研究自动变速箱壳体强度分析的方法,即利用应力测定的方法进行变速箱壳体的静扭转测试.分析采用应变片测定变速箱壳体应力的原理,通过扭转机对变速箱总成施加扭力,进行变速箱壳体应变量、应力的测定,实施壳体强度耐久测试,以验证变速箱壳体的强度.比较各测点的实测应力与有限元分析得到的应力,结果表明:各测点实测应力与有限元分析得到的应力值相当,验证了有限元模型的正确性.根据该施加扭力的测试方法,实施变速箱壳体的强度耐久测试,能有效验证变速箱壳体的疲劳损伤及寿命.【期刊名称】《汽车零部件》【年(卷),期】2018(000)003【总页数】4页(P20-23)【关键词】自动变速箱;强度;应力测试【作者】刘喜涛【作者单位】广汽零部件有限公司技术中心,广东广州510640【正文语种】中文【中图分类】U4630 引言随着汽车工业的发展,整车性能对变速箱性能提出了更高的要求。
自动变速箱作为汽车传动系统的核心零部件,其性能对整车的安全性、燃油经济性、动力性、乘坐舒适性等有重大影响。
因此,开展对自动变速箱的研究显得尤为重要。
汽车变速箱用于改变发动机传递到驱动轮上的转矩和转速,其功用主要有:改变传动比,拓宽驱动轮转矩和转速的变化范围,从而适应不同的汽车行驶条件,如原地起步、爬坡、加速等,使得发动机在有利的工况下工作;在不改变发动机转速的前提下,设置倒挡,使汽车倒退行驶;设置空挡,切断动力传递,以便发动机能够实现起动、怠速,便于变速箱进行换挡操作。
目前,主流汽车采用的自动变速箱主要分为4类:液力自动变速箱(Automatic Transmission,AT)、电控机械式自动变速箱(Automated Transmission,AMT)、双离合器自动变速箱(Dual Clutch Transmission,DCT)和无级自动变速箱(Continuously Variable Transmission,CVT)[1]。
汽车变速器壳体悬置连接处静强度分析与设计改进

图1 变速器壳体裂纹部位示意图速、急减速以及急转弯等工况时,由于惯性作用,变速器悬置承车辆在颠簸路面行驶时,悬置受到路面冲击力的影响。
因此,变速器壳体悬置部位受力状态极为复杂。
为了进一步确定壳体悬置结构的薄弱点,项目组对发生故障的壳体进静态拉伸试验装置主要由变速器壳体、液压缸和测试工装等组成。
其中拉伸载荷来自液压油缸的压力,油缸通过液压顶杠作用在测试工装上的环形面上。
为分析悬置部位在不同方向的静强X、Y、Z三个方向(图2a)。
根据变速器壳体拉伸方向安装好试验台,分别对X、Y、Z三个方向进行拉伸试验,调节液压控制旋钮,逐渐增加液压压强,观察前壳体悬置直至壳体出现裂纹。
试验过程如图2b~图2d所示。
置与端面连接处。
试验过程中,图3中红圈标记的某处最先产生裂纹。
随着拉伸力的增大,裂纹沿着悬置结构与壳体下端面连接面扩展,最终造成壳体破坏。
这与图2 变速器壳体拉伸试验图4 网格模型图表1 接触关系表图3 Z方向拉伸试验壳体破坏图接触对接触方式接触描述螺栓头与测试工装内表面No Separation允许接触表面之间发生微小的切向移动螺栓头与测试工装内表面No Separation允许接触表面之间发生微小的切向移动螺栓头与测试工装内表面No Separation允许接触表面之间发生微小的切向移动螺栓与螺孔Bonded绑定,不允许有相对移动螺栓与螺孔Bonded绑定,不允许有相对移动螺栓与螺孔Bonded绑定,不允许有相对移动测试工装外表面与前壳体悬置结构表面Rough允许接触表面之间发生法向移动之前壳体故障的部位是一致的。
因此,可认为该悬置部位在Z方向的承载能力最差,是结构的薄弱点。
因此,项目组接下来主要针对变速器Z方向拉伸强度进行分析。
3 壳体静强度CAE分析上述拉伸试验为变速器悬置部位的静强度设计提供了一个参考基准,接下来项目组通过CAE方法进行建模。
首先建立变速器壳体几何模型,壳体内部的油道、定位销孔和倒角等细小结图5 接触关系示意图模型载荷根据拉伸试验断裂时的加载力进行加载,将拉伸载荷加载在测试工装上,方向沿Z方向垂直向上,加载力为41 376 N。
变速器后轴承盖强度分析及结构改进
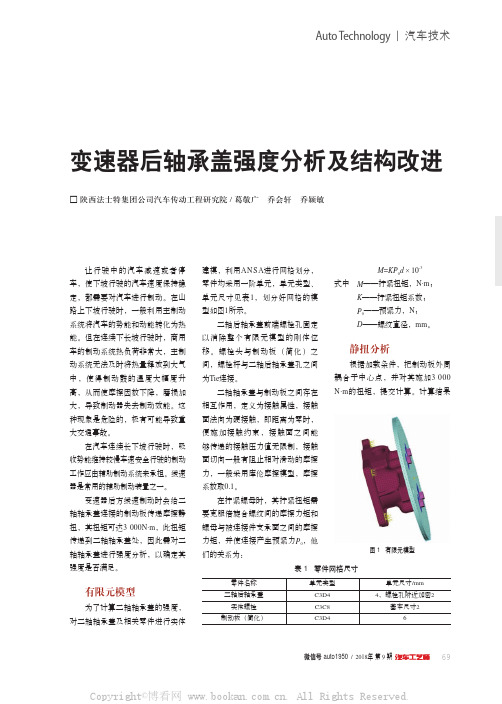
让行驶中的汽车减速或者停车,使下坡行驶的汽车速度保持稳定,都需要对汽车进行制动。
在山路上下坡行驶时,一般利用主制动系统将汽车的势能和动能转化为热能。
但在连续下长坡行驶时,商用车的制动系统热负荷非常大,主制动系统无法及时将热量释放到大气中,使得制动鼓的温度大幅度升高,从而使摩擦因数下降,磨损加大,导致制动器失去制动效能。
这种现象是危险的,极有可能导致重大交通事故。
在汽车连续长下坡行驶时,吸收势能维持较慢车速安全行驶的制动工作应由辅助制动系统来承担。
缓速器是常用的辅助制动装置之一。
变速器后方缓速制动时会给二轴轴承盖连接的制动板传递摩擦静扭,其扭矩可达3 000N·m ,此扭矩传递到二轴轴承盖处,因此需对二轴轴承盖进行强度分析,以确定其强度是否满足。
有限元模型为了计算二轴轴承盖的强度,对二轴轴承盖及相关零件进行实体变速器后轴承盖强度分析及结构改进□陕西法士特集团公司汽车传动工程研究院 / 葛敬广 乔会轩 乔颖敏建模,利用ANSA 进行网格划分,零件均采用一阶单元,单元类型、单元尺寸见表1,划分好网格的模型如图1所示。
二轴后轴承盖前端螺栓孔固定以消除整个有限元模型的刚体位移。
螺栓头与制动板(简化)之间,螺栓杆与二轴后轴承盖孔之间为Tie 连接。
二轴轴承盖与制动板之间存在相互作用,定义为接触属性,接触面法向为硬接触,即距离为零时,便施加接触约束,接触面之间能够传递的接触压力值无限制,接触面切向一般有阻止相对滑动的摩擦力,一般采用库伦摩擦模型,摩擦系数取0.1。
在拧紧螺母时,其拧紧扭矩需要克服倍旋合螺纹间的摩擦力矩和螺母与被连接件支承面之间的摩擦力矩,并使连接产生预紧力P 0,他们的关系为:M =KP 0d ×10-3式中 M ——拧紧扭矩,N·m ;K ——拧紧扭矩系数; P 0——预紧力,N ; D ——螺纹直径,mm 。
静扭分析根据加载条件,把制动板外周耦合于中心点,并对其施加3 000 N·m 的扭矩,提交计算。
变速器壳体强度分析

1变速器壳体强度分析4.1变速器箱体的有限元结构强度计算分析变速器箱体是变速器系统的主要组成部分,在齿轮传动过程中,箱体承受较大的载荷并产生较大的变形和应力。
变速器的各轴均通过轴承支撑在箱体上,因此箱体的受力变形对变速器工作的可靠性和寿命有较大的影响。
本节着重研究了变速器箱体的实体建模及有限元结构强度分析。
4.1.1变速器箱体三维实体模型的建立M5ZRI的箱体分为前箱体后箱体两个部分由8个螺栓连接,为铸铝件,其结构非常复杂,外形不规则,尤其是前箱体的钟型罩部分是由大量的曲面构成。
建模工作中使用大型CA D软件uG进行了箱体的三维实体建模,分别建立了前后两个箱体后再将其装配到一起。
建立的箱体实体模型如图4一l:图4一l变速器箱体的实体模型从上图可以看出该实体模型十分复杂,直接导入AN SYS并划分网格十分困难,并且由于铸造结构的大量小过渡圆角等结构的存在将使有限元分析的规模过大以至计算机难以承受。
因此在不影响分析精度的前提下,必须对这个实体进行简化,得到的简化模型参见图3—9。
4.1.2变速器箱体结构强度分析有限元模型的建立变速器箱体的有限元分析使用了通用有限元分析软件ANS YS。
箱体有限元强度分析采用与了上文有限元模态分析同样的方法建立有限元模型,即在0G的结构分析St ructu re模块中进行有限元模型的分网加载等前处理,利用inp命令流文件导入ANSY S,使用ANSY S的求解器求解并进行后处理。
一、网格划分单元类型及材料属性的确定在UG的St ructu re结构分析模块中首先设定有限元模型使用A NSYS格式,设定网格划分类型为自动四面体网格划分。
对于比较复杂的模型,使用二次单元通常会比线性单元的求解效率高且产生良好的效果,因此单元类型使用了SO LID92,为3-D固体结构二次单元,每个单元有l O个节点,每个节点上有x,Y,zZ个方向上的平移自由度,此单元可以应用于弹塑性、大变形及大应变分析,与线性的实体单元SOL ID45相比,SOLl992更适用于不规则的实体模型网格划分。
汽车变速器轴类零件疲劳强度分析
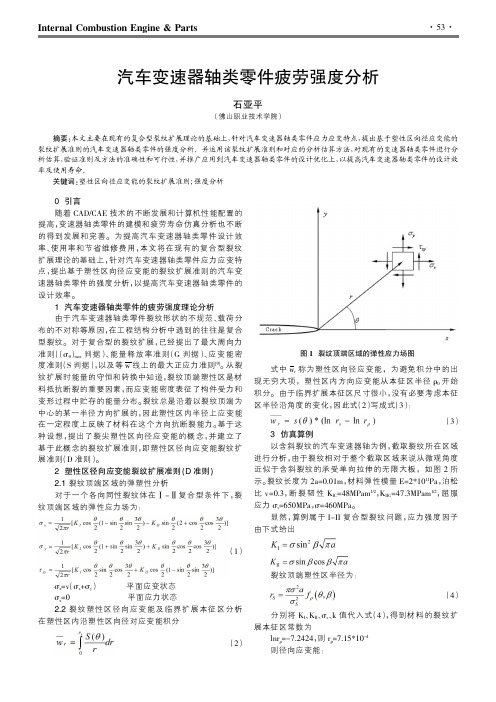
Internal Combustion Engine &Parts0引言随着CAD/CAE 技术的不断发展和计算机性能配置的提高,变速器轴类零件的建模和疲劳寿命仿真分析也不断的得到发展和完善。
为提高汽车变速器轴类零件设计效率、使用率和节省维修费用,本文将在现有的复合型裂纹扩展理论的基础上,针对汽车变速器轴类零件应力应变特点,提出基于塑性区向径应变能的裂纹扩展准则的汽车变速器轴类零件的强度分析,以提高汽车变速器轴类零件的设计效率。
1汽车变速器轴类零件的疲劳强度理论分析由于汽车变速器轴类零件裂纹形状的不规范、载荷分布的不对称等原因,在工程结构分析中遇到的往往是复合型裂纹。
对于复合型的裂纹扩展,已经提出了最大周向力准则((σθ)max 判据)、能量释放率准则(G 判据)、应变能密度准则(S 判据),以及等w 线上的最大正应力准则[9]。
从裂纹扩展时能量的守恒和转换中知道,裂纹顶端塑性区是材料抵抗断裂的重要因素,而应变能密度表征了构件受力和变形过程中贮存的能量分布。
裂纹总是沿着以裂纹顶端为中心的某一半径方向扩展的,因此塑性区内半径上应变能在一定程度上反映了材料在这个方向抗断裂能力。
基于这种设想,提出了裂尖塑性区向径应变能的概念,并建立了基于此概念的裂纹扩展准则,即塑性区径向应变能裂纹扩展准则(D 准则)。
2塑性区径向应变能裂纹扩展准则(D 准则)2.1裂纹顶端区域的弹塑性分析对于一个各向同性裂纹体在Ⅰ-Ⅱ复合型条件下,裂纹顶端区域的弹性应力场为:(1)σz =v (σx +σy)平面应变状态σz =0平面应力状态2.2裂纹塑性区径向应变能及临界扩展本征区分析在塑性区内沿塑性区向径对应变能积分(2)式中w r 称为塑性区向径应变能,为避免积分中的出现无穷大项,塑性区内方向应变能从本征区半径ρ0开始积分。
由于临界扩展本征区尺寸很小,没有必要考虑本征区半径沿角度的变化,因此式(2)写成式(3):(3)3仿真算例以含斜裂纹的汽车变速器轴为例,截取裂纹所在区域进行分析,由于裂纹相对于整个截取区域来说从微观角度近似于含斜裂纹的承受单向拉伸的无限大板,如图2所示。
HEV_变速器壳体开裂失效分析

MANUFACTURING AND PROCESS | 制造与工艺近年来,随着国家战略的引导和人们生活品质提高的需要,纯电动汽车和混动汽车获得了快速发展。
而汽车重量对混动汽车燃油经济性和纯电动汽车的续航里程起着决定性作用,车重每降低100kg,油耗可减少0.7L/100km[1]。
根据业内的共识,簧下质量减重降油耗效果显著优于簧上质量,在动力底盘零件设计过程中,为了降油耗产品工程师会依据CAE分析结果,将零件尽可能减薄,譬如文中提到的将某混动车型变速器壳体的壁厚减薄,这往往带来一些新的问题。
除了优化产品结构,汽车降低能耗的途径主要是使用新型轻量化材料。
压铸铝合金因为优异的材料性能、加工的稳定性和比强度高等优点,成为汽车轻量化的热门材料。
高强韧铝合金压铸件从上世纪90年代起开始批量应用,近年来铝合金压铸件逐步替代铸铁,用量逐年增加,并广泛应用于汽车变速器壳体、发动机部件和汽车轮毂等等。
随着汽车工业技术的进步,大部分铝合金制造的汽车零部件向壁薄、高强度、高质量、高可靠性方向发展。
德国莱茵铝合金公司研究的新型压铸铝合金:Magsimal-59、Silafont-36与Castasil-37,通过控制Fe元素的含量,实现标准圆棒试样在铸态下断后延伸率达到17%,并成功应用于汽车车门制造。
王海东等对Al-Si-Mg系合金中添加微量元素Ti时,能有效细化晶粒,显著提供铝合金的抗拉强度和屈服强度,添加微量Zr或Sr元素,铝合金的力学性能显著改善,为制造铝合金汽车车身、吸能件提供了解决方案[2-3]。
目前研究和应用最广的铝合金主要是Al-Mg系、Al-Si系、Al-Si-Cu系和Al-Si-Mg四个系列。
我司的某变速器壳体属于Al-Si-Cu系的压铸铝合金,牌号是ADC12。
1 故障描述某混动车型变速器在路试测试时,壳体安装螺栓处开裂,断裂情况如下图1所示。
壳体开裂的裂纹源位于螺栓安装面下第三螺纹根部(图1,Ⅰ区箭头指向位置;CAE仿真分析显示,该处属于应力集中部位)。
金属带式无级变速器壳体的强度和刚度分析
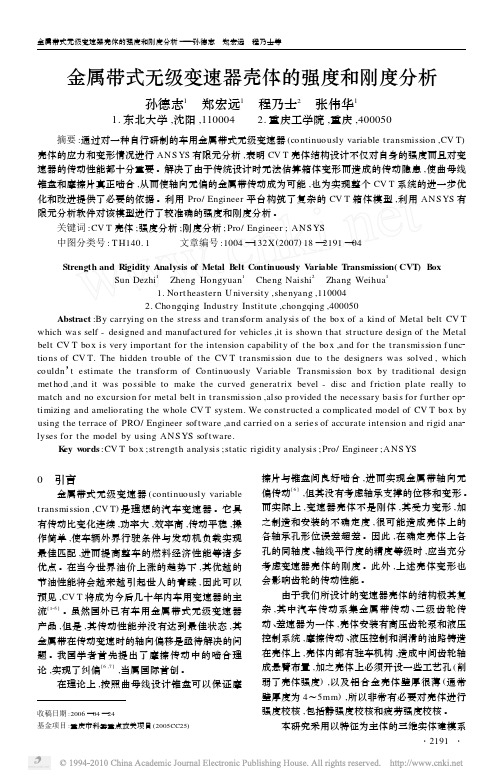
金属带式无级变速器壳体的强度和刚度分析孙德志1 郑宏远1 程乃士2 张伟华11.东北大学,沈阳,1100042.重庆工学院,重庆,400050摘要:通过对一种自行研制的车用金属带式无级变速器(co ntinuously variable t ransmission ,CV T )壳体的应力和变形情况进行ANS YS 有限元分析,表明CV T 壳体结构设计不仅对自身的强度而且对变速器的传动性能都十分重要。
解决了由于传统设计时无法估算箱体变形而造成的传动隐患,使曲母线锥盘和摩擦片真正啮合,从而使轴向无偏的金属带传动成为可能,也为实现整个CV T 系统的进一步优化和改进提供了必要的依据。
利用Pro/Engineer 平台构筑了复杂的CV T 箱体模型,利用ANS YS 有限元分析软件对该模型进行了较准确的强度和刚度分析。
关键词:CV T 壳体;强度分析;刚度分析;Pro/Engineer ;ANS YS 中图分类号:T H140.1 文章编号:1004—132X (2007)18—2191—04Strength and Rigidity Analysis of Metal B elt Continuously V ariable T ransmission(CVT)BoxSun Dezhi 1 Zheng Hongyuan 1 Cheng Naishi 2 Zhang Weihua 11.Nort heastern U niversity ,shenyang ,1100042.Chongqing Indust ry Instit ute ,chongqing ,400050Abstract :By carrying on t he stress and t ransform analysis of t he box of a kind of Metal belt CV T which was self -designed and manufact ured for vehicles ,it is shown t hat st ruct ure design of t he Metal belt CV T box is very important for t he intension capability of t he box ,and for t he t ransmission f unc 2tions of CV T.The hidden t rouble of t he CV T transmission due to t he designers was solved ,which couldn ’t estimate t he t ransform of Continuously Variable Transmission box by t raditional design met hod ,and it was po ssible to make t he curved generat rix bevel -disc and friction plate really to match and no excursion for metal belt in t ransmission ,also p rovided t he necessary basis for f urt her op 2timizing and ameliorating t he whole CV T system.We const ructed a complicated model of CV T box by using t he terrace of PRO/Engineer software ,and carried on a series of accurate intension and rigid ana 2lyses for t he model by using ANS YS software.K ey w ords :CV T bo x ;st rengt h analysis ;static rigidity analysis ;Pro/Engineer ;ANS YS收稿日期:2006—04—24基金项目:重庆市科委重点攻关项目(2005CC25)0 引言金属带式无级变速器(continuously variable t ransmission ,CV T )是理想的汽车变速器。
镁合金汽车变速箱壳体强度分析
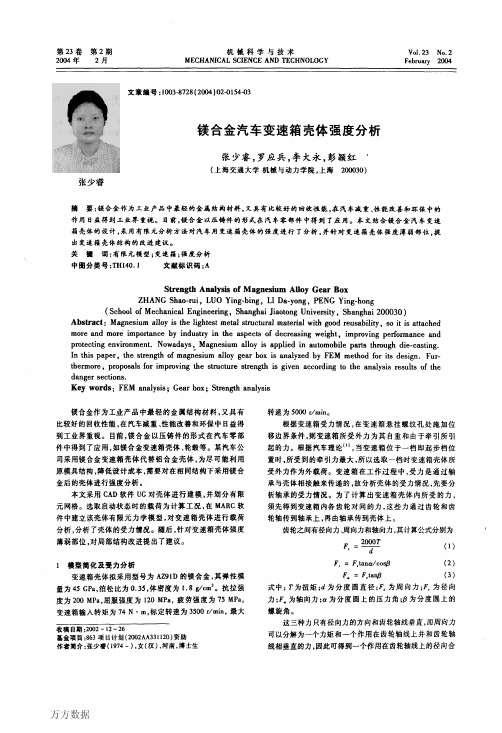
第23卷2004年第2期2月机械科学与技术MECHANICALSCIENCEANDTECHNOLOGYV01.23No.2Febnlary20014张少睿文章编号:1003-8728(2004)02旬154国3镁合金汽车变速箱壳体强度分析张少睿,罗应兵,李大永,彭颖红。
(上海交通大学机械与动力学院,上海200030)摘要:镁舍金作为工业产品中最轻的金属结构材料,又具有比较好的回收性能,在汽车减重、性能改善和环保中的作用日益得到工业界重视。
目前,镁合金以压铸件的形式在汽车零部件中得到了应用。
本文结合镁合金汽车变速箱壳体的设计,采用有限元分析方法对汽车用变速箱壳体的强度进行了分析,并针对变速箱壳体强度薄弱部位,提出变速箱壳体结构的改进建议。
关键词:有限元模型;变速箱;强度分析中圈分类号:THl40.1文献标识码:AStrengthAnalysisofMagn鹤iumAuoyGearBoxZHANGShao—rui,LUOYing-bing,LIDa-yong,PENGYing-hong(SchoolofMechanicalEngineering,ShanghaiJiaotongUniversity,Shangh8i200030)Abstract:Magnesiumalloyis出elightestmetalstructuralmatedalwitllgoodreus8bility,soitisattachedmoreandmoreimponancebyindustryintlleaspectsofdecreasingweight,impmvingperfomanceandpmtectingenVifonment.Nowadays,Magnesiumalloyisappliedinautomobilepartstllroughdie-casting.IntIlispaper,thestrengthofmagnesiumalloyge8rboxisanalyzedbyFEMmemodforitsdesign.Fur.thermore,proposalsforimprovingtllestmcturestrengtllisgivenaccordingtotheanalysisresultsoftIledangersections.Keywords:FEManalysis;Gearbox;Strengthanalysis镁合金作为工业产品中最轻的金属结构材料,又具有比较好的回收性能,在汽车减重、性能改善和环保中日益得到工业界重视。
- 1、下载文档前请自行甄别文档内容的完整性,平台不提供额外的编辑、内容补充、找答案等附加服务。
- 2、"仅部分预览"的文档,不可在线预览部分如存在完整性等问题,可反馈申请退款(可完整预览的文档不适用该条件!)。
- 3、如文档侵犯您的权益,请联系客服反馈,我们会尽快为您处理(人工客服工作时间:9:00-18:30)。
1变速器壳体强度分析
4.1变速器箱体的有限元结构强度计算分析
变速器箱体是变速器系统的主要组成部分,在齿轮传动过程中,箱体承受较大的载荷并产生较大的变形和应力。
变速器的各轴均通过轴承支撑在箱体上,因此箱体的受力变形对变速器工作的可靠性和寿命有较大的影响。
本节着重研究了变速器箱体的实体建模及有限元结构强度分析。
4.1.1变速器箱体三维实体模型的建立
M5ZRI的箱体分为前箱体后箱体两个部分由8个螺栓连接,为铸铝件,其结构非常复杂,外形不规则,尤其是前箱体的钟型罩部分是由大量的曲面构成。
建模工作中使用大型CAD软件uG进行了箱体的三维实体建模,分别建立了前后两个箱体后再将其装配到一起。
建立的箱体实体模型如图4一l:
图4一l变速器箱体的实体模型
从上图可以看出该实体模型十分复杂,直接导入ANSYS并划分网格十分困难,并且由于铸造结构的大量小过渡圆角等结构的存在将使有限元分析的规模过大以至计算机难以承受。
因此在不影响分析精度的前提下,必须对这个实体进行简化,得到的简化模型参见图3—9。
4.1.2变速器箱体结构强度分析有限元模型的建立
变速器箱体的有限元分析使用了通用有限元分析软件ANSYS。
箱体有限元强度分析采用与了上文有限元模态分析同样的方法建立有限元模型,即在0G的结构分析Structure模块中进行有限元模型的分网加载等前处理,利用inp命令流文件导入ANSYS,使用ANSYS的求解器求解并进行后处理。
一、网格划分单元类型及材料属性的确定
在UG的Structure结构分析模块中首先设定有限元模型使用ANSYS格式,设定网格划分类型为自动四面体网格划分。
对于比较复杂的模型,使用二次单元通常会比线性单元的求解效率高且产生良好的效果,因此单元类型使用了SOLID92,为3-D 固体结构二次单元,每个单元有lO个节点,每个节点上有x,Y,zZ个方向上的平移自由度,此单元可以应用于弹塑性、大变形及大应变分析,与线性的实体单元SOLID45相比,SOLl992更适用于不规则的实体模型网格划分。
变速器箱体采用的材料是铸铝ADCl 2,主要用来制造变速器箱体,气缸体缸盖等。
其材料特性为:弹性模量70GPa,泊松比O.32,密度2.8×10 5Kg/m3,抗拉强度a.=329MPa。
根据材料的性能,对材料属性设置项进行了相关的设定。
二、变速器箱体模型的网格划分及加载、约束条件的确定
如上文所述在uG的Structure模块中采用自动四面体网格划分,网格密度的控制根据计算规模的大小及变速箱简化模型的几何尺寸,经过几次试算确定了较为合理的网格密度,确定全局单元尺寸为8.0,网格扩展因子设定为1.0。
变速箱实体模型划分为147639个节点78525个单元,在uG中划分的网格及导XANSYS后的网格模型见下图4—2。
将有限元网格模型与变速箱简化实体模型对比,可以看出网格模型能准确的反映实体模型的特征,可见划分较为精确。
uG中划分网格的实体模型导入ANSY$获得的有限元模型
图4—2变速器箱体的有限元模型
网格模型建立后进行模型的约束及加载。
由于变速器箱体所受的载荷主要是齿轮传动引起的众多轴承载荷,以及箱体自身的重量,箱体自身的重量ANSYS程序能够自动计算,而各轴承载荷通过轴承外圈作用在箱体上,将其作为箱体轴承支撑圆柱面上的法向均布面载荷来处理。
变速器箱体的边界约束条件则是按变速器的实际安装状态,将后箱体输出端的支撑座处以及前箱体裙部的安装面这两处单元各节点的三个平动自由度U,、U,、u。
约束为O。
由于导入ANSYS后的有限元模型各加载面上单元数量众多,而导入的有限元模型不包含实体的点线面特征,加载比较困难,因此所有的加载与约束均在uG的Structure模块中进行,然后通过in 口命令流文件导入ANSYS。
根据变速器的输入扭矩以及五档传动比和齿轮的基本参数计算得到箱体各轴支撑轴承处所受载荷如下:
一轴支撑轴承处轴向力F。
-3420N;径向力F,=2652N;切向力F:=6433N。
径向力和轴向力均按照各自的方向作用在轴承支撑处相应的半圆柱面上,而轴向力根据实际安装情况,是通过轴承卡环作用在一个圆环面上,该受力面在简化处理模型时己经做出,加载在其上即可。
二轴施加给箱体的力主要是后端的双列角接触球轴承处三个方向的力和后端辅助支撑轴承处的两个方向的力:角接触球轴承处轴向力F,=3379N;径向力F,=1071N;切向力E=3000N。
径向力和轴向力均按照各自的方向作用在轴承支撑处相应的半圆柱面上,而轴向力根据实际安装情况,通过轴承卡环作用在前箱体上轴承安装位置的沉孔圆环面E。
辅助支撑轴承处径向力F,=132lN;切向力F。
=3699N按照各自的方向作用在轴承支撑处相应的半圆柱面上。
中间轴前端支撑轴承处轴向力F,:7941N;径向力F,=2268N;切向力F:=5775N。
径向力和轴向力均按照各自的方向作用在轴承支撑处相应的半圆柱面上,而轴向力根据实际安装情况,通过挡环作用在变速器前端盖上,如上文所述,前端盖简化为局部与前箱体一体,该处的受力面也已做出,加载在其上即可。
中间支撑轴承处轴向力F。
=7900N;径向力F,=1160N;切向力F:=777N,各力均按其实际加载位置施加。
后端轴承支撑处只有两个方向的力,径向力F,=1493N;切向力F。
=5775N均按照各自的方向作用在轴承支撑处相应的半圆柱面上。
下图4—3即为uG中加载的情况,如透视图中所示各加载面所受的面载荷以红色箭头表示,后箱体上支撑处的黄色标志表示约束该处三个平动自由度。
所有的加载信息和约束条件经过格式化为ANSYS命令流文件后,导入ANSYS后自动转换施加到有限元网格模型的各节点上。
图4—3 UG中施加约束及载荷
43导入ANSYS后的加载与约束条件见下图4-4。
各图中的约束i’以浅蓝色的标志表示,而转化到节点上的面载荷则据其大小以不同的颜色表示在各受载面上,如图4—4中红色箭头所指各面,其余各受载面的加载情况大致相同。
约束面载荷
图4—4 ANSYS中施加约束及载荷的箱体模型
完成加载和约束的模型即可进行有限元分析计算。
4.1.3变速器箱体结构强度有限元计算结果
加载及约束设定完成后,即可进入ANSYS的求解器进行计算。
设定分析的类型为静态线性过程(LINEAR STATIC),材料性质为线弹性(LINEAR E1.ASTIC)。
选取直接解法求解方式,不组装整个矩阵,只是在求解器处理每~个单元时,同时进行整个矩阵的组装和求解,也称为波前法,其求解速度快计算精度高,但是需要大容量的硬盘空间储存中间数据。
使用当前载荷步(Current LS)开始求解。
有限元计算完毕以后,使用ANSYS的后处理功能,利用计算出的箱体各个单元的节点位移,来确定各个单元的应力大小,以及整个结构变形情况和应力分布情况。
图4-5是箱体在五档工况下的综合位移(SUMxyz)变形图:
图4—5变速器箱体的综合变形图
从上图可以看出,相对于支座固定位置的最大位移值为0.125mm,发生在变速箱边缘红色区域标有Mx标志处。
可以看到各轴承支撑位置隔板在0,12mm至0.07ram 之间,由于各轴的支撑轴承都有一定的变形间隙,箱体的变形对传动过程影响不大。
针对箱体的铸铝材料,其强度条件采用第一强度(最大拉应力)理论和第二强度(最大拉应变)理论进行判断“”。
在ANSYS的后处理模块中分别导出箱体的第一、第二强度理论的应力分布云图如下图4-6和4—7:
闰4—6变速器箱体的第一强度理论应力云图
从图4—6可以看出变速器箱体外表面的第一强度理论应力较小,大都分布在l 14MPa至010.029MPa之间,后箱体上靠近固定支座位置附近出现应力最大值为77.045MPa,而各轴承支撑处的应力值大约分布在32.368MPa至lJ65.876MPa 之间。
图4—7变速器箱体的第二强度理论应力云图
变速器箱体的第二强度理论应力分布与第一强度理论应力分布基本一致,且其值比较小最大值只有41.488MPa,不再加以分析,以第一强度理论应力值作为强度判据。
根据以上变速器箱体各应力分布云图可知具体数据如下:
第一强度理论应力最大值为: 77.045MPa:箱体内部应力最大值为: 6B.876MPa:第二强度理论应力最大值为:41.488MPa:变速器箱体的材料为ADCl2,其抗拉强度盯。
=329 MPa,,取安全系用应力为b1H 164,5MPa。
从有限元分析的结果可以看出各应力的最大值与许用应力相比较小,说明变速器箱体有一定的强度储备。
而从箱体的综合变形分布图可以看出,变速箱体各部分的变形比较小,最大变形0.125mm并且出现在距离变速器传动关键部件较远的后箱体边缘处,说明变速器箱体的受力变形对变速器的正常工作影响较小。
通过列M5ZRl变速器箱体进行的有限元结构强度计算分析,该变速器箱体的强度及刚度均满足使用要求,安全可靠。