从铜镉渣酸浸后废渣中提取粗铅
从冶锌工业废渣中提取铅、锌、铜、镉

锌渣中铜的提取先用碱洗球磨,以水淘洗晾干 后结成团块,压碎后筛分其粒级,即可满足浸出需 要。湿磨的主要目的不是磨碎,故磨的时间不必太
长。用1 mol/L的NaOH溶液洗后滤渣进一步进行
含量还要除铁。利用铁的电极电位较铜为负,废铁 来源广泛,价格低等,再用废铁置换母液中的铜离子 而生成海绵铜,从而使铜离子达到微量标准而排放。 1.4锌渣中铅的提取
关键词锌渣铅铜镉分离
1堡孽三竺篓妻中回收邢、zn、cu、ca的国喜毳券鬻嚣翟嚣翁蔫篙嘉翥鬻毒篙 内外研究现状
当前锌的生产一般采用两种方法:一是火法冶 质量比在5.O×10q~1.0×10_3的范围内测定其 除砷率。结果发现质量比约为8.0×10叫时,除砷 率达96%以上,在质量比约为4.0×10_4时,除砷
广州化工
・95・
镉常与锌矿伴生,含量较低,一般在湿法炼锌流 程中采用锌粉置换提取镉,并净化炼锌浸出液。这 种方法存在着锌粉消耗大,流程过长、污染大等缺 点,直接影响操作成本和工作环境,因而研究和开发 消耗低、效率高、无污染的提镉新技术是一种极为迫 切的课题。本文根据近几年来的研究进展,对冶锌 工业废渣中提取Pb、Zn、Cu、Cd等作一综合评述。 1.1锌渣中镉的提取【卜4J 金属镉的用途广泛,在电镀、油漆、电器制造以 及航空材料等行业均有着重要的作用,由于水溶性 镉离子的毒性很大,出于环保方面的考虑,近年电镀 用镉量呈逐年下降的趋势。但随着性能优越的镉镍 电池的开发并广泛地应用于高科技生活领域,近十 几年来,电池用镉量显著增大,极大地刺激了对镉的
镉的分离。
nd几的KI溶液后,Cd2+定量地被甲基异丁酮
萃取。也可用N一十二烯胺或N一月桂胺等为萃取 液对Cd2+进行定量萃取,然后镉可用0.5 nlol几的 硝酸,pH=10的氨一氯化铵缓冲液后萃取,或用1
冶锌工业废渣中铅、锌、铜、镉提取工艺的研究
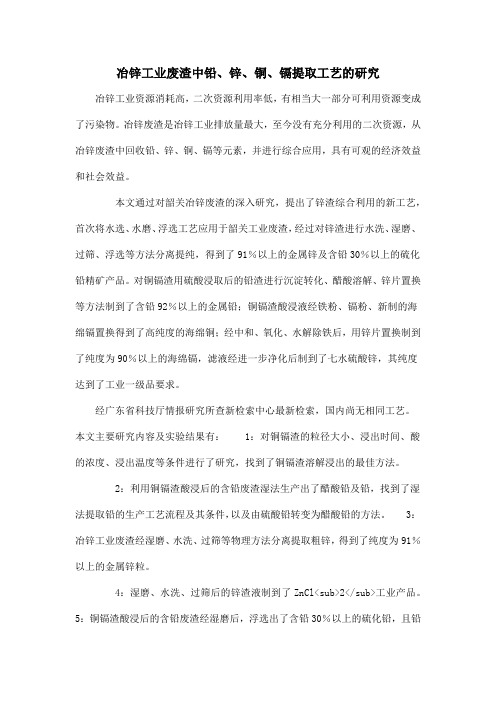
冶锌工业废渣中铅、锌、铜、镉提取工艺的研究冶锌工业资源消耗高,二次资源利用率低,有相当大一部分可利用资源变成了污染物。
冶锌废渣是冶锌工业排放量最大,至今没有充分利用的二次资源,从冶锌废渣中回收铅、锌、铜、镉等元素,并进行综合应用,具有可观的经济效益和社会效益。
本文通过对韶关冶锌废渣的深入研究,提出了锌渣综合利用的新工艺,首次将水选、水磨、浮选工艺应用于韶关工业废渣,经过对锌渣进行水洗、湿磨、过筛、浮选等方法分离提纯,得到了91%以上的金属锌及含铅30%以上的硫化铅精矿产品。
对铜镉渣用硫酸浸取后的铅渣进行沉淀转化、醋酸溶解、锌片置换等方法制到了含铅92%以上的金属铅;铜镉渣酸浸液经铁粉、镉粉、新制的海绵镉置换得到了高纯度的海绵铜;经中和、氧化、水解除铁后,用锌片置换制到了纯度为90%以上的海绵镉,滤液经进一步净化后制到了七水硫酸锌,其纯度达到了工业一级品要求。
经广东省科技厅情报研究所查新检索中心最新检索,国内尚无相同工艺。
本文主要研究内容及实验结果有: 1:对铜镉渣的粒径大小、浸出时间、酸的浓度、浸出温度等条件进行了研究,找到了铜镉渣溶解浸出的最佳方法。
2:利用铜镉渣酸浸后的含铅废渣湿法生产出了醋酸铅及铅,找到了湿法提取铅的生产工艺流程及其条件,以及由硫酸铅转变为醋酸铅的方法。
3:冶锌工业废渣经湿磨、水洗、过筛等物理方法分离提取粗锌,得到了纯度为91%以上的金属锌粒。
4:湿磨、水洗、过筛后的锌渣液制到了ZnCl<sub>2</sub>工业产品。
5:铜镉渣酸浸后的含铅废渣经湿磨后,浮选出了含铅30%以上的硫化铅,且铅的回收率达到96%以上。
6:通过对冶锌废渣中铜的回收方法研究,找到了最佳工艺流程和条件,并制得了纯度较高的海绵铜。
7:对铜镉渣浸出液中铜提取后的溶液成分研究,找到了加入中和试剂来降低酸度、调整PH值以促进水解除铁的方法、氧化剂的选择和用量。
广东工业大学工程硕士学位论文8:经过冶锌工业废渣中锅的提取工艺流程、条件、试剂对铜的置换率影响的研究,找到了最佳工艺条件。
从酸浸渣中综合回收金银铁铅的试验研究

从酸浸渣中综合回收金银铁铅的试验研究
薛元昕;薛光
【期刊名称】《黄金》
【年(卷),期】2011(032)002
【摘要】对从酸浸渣中综合回收金银铁铅进行了试验研究.试验结果表明,采用试验确定的工艺方法,不但可回收酸浸渣中铁铅,还可提高金银的氰化浸出率,分别可达98 %和70 %以上,能获得较好的经济效益和社会效益.
【总页数】2页(P51-52)
【作者】薛元昕;薛光
【作者单位】烟台职业学院;中国人民武装警察部队黄金第七支队
【正文语种】中文
【中图分类】TD953
【相关文献】
1.选冶联合综合回收铅银渣中金银试验研究 [J], 郭艳华;杨俊龙;廖雪珍;彭建城;彭贵熊
2.从锌渣浸渣中综合回收铟锗铅银的试验研究 [J], 郑顺德;陈世民;林兴铭;李裕后;李俊红
3.氧化铜精矿酸浸渣综合回收银铅试验研究 [J], 叶富兴;李秀娟;邹坚坚;王成行;宋宝旭
4.酸浸渣综合回收浸铅工艺研究 [J], 彭国敏;俎小凤;张福元
5.沉淀转化法综合回收酸浸渣中铅的工艺研究 [J], 张福元;俎小凤;彭国敏
因版权原因,仅展示原文概要,查看原文内容请购买。
一种铜冶炼酸泥中铅、汞、硒综合回收的方法[发明专利]
![一种铜冶炼酸泥中铅、汞、硒综合回收的方法[发明专利]](https://img.taocdn.com/s3/m/99f3b7efcc175527072208f3.png)
专利名称:一种铜冶炼酸泥中铅、汞、硒综合回收的方法专利类型:发明专利
发明人:黄凯,孙科源,胡若鹏,李贞,邢杰,王晓丽,何宗良,杨雪申请号:CN201810121491.3
申请日:20180207
公开号:CN108220606A
公开日:
20180629
专利内容由知识产权出版社提供
摘要:本发明涉及一种铜冶炼酸泥中铅、汞、硒综合回收的方法,属于固体废物综合利用技术领域,本发明具体包括以下步骤:将铜冶炼酸泥与硝酸溶液按液固比为5:1进行混合,搅拌速率为500 r/min,逐渐加入次氯酸钠在常温下反应60min,得到含有氯化汞和硒酸的混合溶液;分离后的滤渣送往铅冶炼系统循环利用,滤液加入次亚磷酸钠,将溶液中离子态汞还原为可沉降的单质汞,絮凝沉淀后采用微孔过滤方式分离含汞渣,经连续精馏提纯获得精制汞;滤液加入亚硫酸钠还原制取粗硒,废水经中和反应,可返回浸出工序循环利用;本发明采用浸出、分段还原实现汞和硒的有效分离,硒回收率达98.7%,汞回收率高达98.9%,操作简单,成本低;浸出后的含铅滤渣返回流程,实现资源的综合利用。
申请人:云南省固体废物管理中心
地址:650034 云南省昆明市西园南路27号
国籍:CN
代理机构:北京名华博信知识产权代理有限公司
代理人:李中强
更多信息请下载全文后查看。
用氧压酸浸法从铜冶炼电尘灰中回收铜锌砷

用氧压酸浸法从铜冶炼电尘灰中回收铜锌砷摘要:本论文研究了一种用氧压酸浸法从铜冶炼电尘灰中回收铜锌砷的方法。
通过实验和分析,发现在一定的氧压条件下,可以有效地溶解电尘灰中的铜、锌和砷元素。
随后,通过调节浸出液的pH值和温度,成功地实现了铜、锌和砷的分离和回收。
实验结果表明,该方法具有高效、环保、经济的特点,为电尘灰资源化利用提供了一种可行的途径。
关键词:氧压酸浸法;氧压条件;铜锌砷引言本论文旨在研究一种利用氧压酸浸法从铜冶炼电尘灰中回收铜锌砷的方法。
电尘灰是铜冶炼过程中产生的废弃物,其中含有大量有价值的金属元素。
目前,存在着高效、环保、经济的回收方法的需求。
因此,本研究通过实验和分析,探讨了氧压酸浸法的可行性,并研究了影响回收效果的关键因素。
结果表明,该方法具有潜力成为电尘灰资源化利用的有效途径。
本研究对于提高铜冶炼废弃物的回收利用效率,推动可持续发展具有重要意义。
1.文献综述铜冶炼电尘灰是铜冶炼过程中产生的废弃物,其中富含铜、锌和砷等有价值的金属元素。
目前,常见的回收方法包括浸出法、熔炼法和氧压酸浸法等。
然而,传统方法存在着效率低、环境污染和资源浪费等问题。
因此,近年来,研究人员开始关注氧压酸浸法。
该方法利用氧压条件下的酸性溶液,能够有效溶解电尘灰中的金属元素。
此外,通过调节溶液的pH值和温度,可以实现铜、锌和砷的分离和回收。
研究表明,氧压酸浸法具有高效、环保和经济的特点,逐渐成为电尘灰资源化利用的一种重要方法。
然而,目前对于该方法的研究还相对较少,有待进一步深入探究其机理和优化条件,以提高回收效率和降低成本。
2.实验方法本论文采用氧压酸浸法从铜冶炼电尘灰中回收铜锌砷。
收集并分析电尘灰的化学成分和物理性质。
将电尘灰样品粉碎并筛选得到目标颗粒大小的样品。
在实验设备中加入一定量的电尘灰样品和酸性溶液,并进行氧压处理。
在一定温度和压力条件下,溶液中的氧气能够与酸性溶液反应,形成含氧的酸性介质。
通过调节溶液的pH值和温度,控制金属元素的溶解率和选择性沉淀。
从酸浸渣中综合回收金银铁铅的试验研究

摘要: 对从酸浸渣中综合回收金银铁铅进行了试验研究。试验结果表明,采用试验确定的工艺
方法,不但可回收酸浸渣中铁铅,还可提高金银的氰化浸出率,分别可达 98 % 和 70 % 以上,能获得
较好的经济效益和社会效益。
关键词: 酸浸渣; 浸铁; 浸铅; 氰化浸出; 金; 银
从表 4 可见,未除铅的氰化浸出率较低,主要原 因是硫酸浸渣中的铅含量较高( 4. 74 % ) ,氰化浸出 液中加入 Na2 CO3 调整剂不足,未能使渣中的 PbSO4 全部转化为 PbCO3 ,使包裹的金未能暴露,影响金银 的氰化浸出。为此,必须加大 Na2 CO3 用量,但增加氰 化浸出成本,影响企业的经济效益。
1 酸浸渣的化学组成
试验采用的酸浸渣由某黄金冶炼厂提供,是金精 矿经沸腾焙烧、稀硫酸浸铜后产物,呈褐红色,显弱酸 性( pH≈2) ,粒度 - 160 目 80 % 。酸浸渣成分主要 是铁的氧化物,含有 Au、Ag,并含有少量的 Cu、Pb、 Zn、As 等金属元素,大都呈硫酸盐的形式存在。酸浸 渣的化学组成见表 1。
3) 酸浸渣经除杂和盐浸除铅后,渣中的杂质元 素大部分除去。采用 NH4 HCO3 - CaO 和 NH4 HCO3 - NaOH 为 pH 调整剂进行氰化浸出,Au、Ag 的氰化 浸出率分别达到 98 % 和 70 % 以上。有价元素 Pb、 Cu 可以回收,而盐浸液可循环利用。该工艺与现行 工艺方法相比,具有较好的经济效益和社会效益。
中图分类号: TD 953
文献标志码: B
文章编号: 1001 - 1277( 2011) 02 - 0051 - 02
酸浸渣是焙烧—氰化浸金工艺中的中间产物。 金精矿经沸腾炉焙烧后制得焙砂,然后采用 2 % 的硫 酸溶液浸铜后得到的棕红色物料即为酸浸渣。酸浸 渣中除含有 Au、Ag 外,还含有大量的 Fe、Pb 及少量 的 Cu、As。由于物料中含有大量的三氧化铁,对金产 生二次包裹,且在金表面生成一层氧化铁的钝化膜, 影响金的氰化浸出,金的氰化浸出率通常在90 % ~ 95 % 之间。为此,综合回收酸浸渣中的有价元素,提 高酸浸 渣 的 金 银 氰 化 浸 出 率,是 目 前 亟 待 解 决 的 问题。
沉淀转化法回收酸浸渣中铅的酸溶工艺研究

沉淀转化法回收酸浸渣中铅的酸溶工艺研究张福元;卓俭进;张玉明;彭国敏【摘要】以金精矿焙烧-酸浸除杂后的酸浸渣与碳酸氢铵反应生成的转化渣为原料,进行酸溶浸铅工艺研究.通过正交实验考察了液固质量比、浸出pH和浸出时间等因素对铅浸出率的影响,得到最佳工艺条件:浸出液固质量比为2∶1、浸出液pH=0.5、浸出时间为2h.在此条件下,金属铅浸出率可达83%.【期刊名称】《无机盐工业》【年(卷),期】2013(045)011【总页数】3页(P47-49)【关键词】酸浸渣;沉淀转化;铅;硝酸;浸出【作者】张福元;卓俭进;张玉明;彭国敏【作者单位】河南中原黄金冶炼厂有限责任公司,河南省黄金资源综合利用重点实验室,河南三门峡472000;河南中原黄金冶炼厂有限责任公司,河南省黄金资源综合利用重点实验室,河南三门峡472000;河南中原黄金冶炼厂有限责任公司,河南省黄金资源综合利用重点实验室,河南三门峡472000;河南中原黄金冶炼厂有限责任公司,河南省黄金资源综合利用重点实验室,河南三门峡472000【正文语种】中文【中图分类】TQ134.33目前,在中国金精矿湿法冶金的提金工艺过程中,会产生大量含铅酸浸渣,铅品位一般为1%~3%,一定程度上会影响金、银浸出率[1],并易造成铅环境污染。
文献[2-3]对铅锌冶炼渣综合回收有价金属做了相关报道。
笔者曾针对黄金冶炼酸浸渣进行了回收工艺研究[4],采用一种沉淀转化法对酸浸渣中的铅进行综合回收[5],可有效回收低品位的金属铅,增加企业经济效益且避免环境污染。
在之前研究的基础上,笔者针对转化渣,对酸溶浸出工艺继续研究,通过正交实验进一步考察浸出液固质量比、浸出液pH和浸出时间等主要因素对铅浸出率的影响。
1 实验部分1.1 原料以金精矿焙烧-酸浸除杂后的酸浸渣与碳酸氢铵反应生成的沉淀转化渣为原料,其主要组成:w(Au)=3.838×10-5、w(Ag)=1.32×10-4、w(Cu)=0.28%、w(Pb)=2.06%、w(Fe)=33.17%、w(Zn)=0.07%。
铅提炼与回收——D0108

铅提炼与回收——D01081.彩钼铅矿的化学分选方法2.从电解生产双氧水的阳极泥回收铂和铅的方法3.从方铅矿中直接提取铅的方法及设备4.从粉状金属物料直接电解回收锡铅合金的方法5.从炼铜废渣中回收锡、铜、铅、锌等金属的方法6.从硫化铅精矿冶炼金属铅的设备7.从氯化渣中综合回收金银及铅锡等有价金属的方法8.从铅锑粗合金中分离铅锑的方法9.从铅阳极泥提取金、银及回收锑、铋、铜、铅的方法10.从铅阳极泥中回收银、金、锑、铜、铅的方法11.从铅阳极泥中回收银、金、锑、铜、铅的方法212.从碳酸中除去铅和镉的方法13.从钨酸盐溶液中沉淀除钼、砷、锑、锡的方法14.脆硫铅锑矿铅锑直接分离新工艺15.脆硫铅锑尾矿的处理方法16.底吹炉高铅渣液态直接还原炼铅的方法17.电解法制备高纯度活性二氧化铅的方法18.废旧蓄电池铅清洁回收方法19.废旧蓄电池铅清洁回收技术20.废铅酸蓄电池生产再生铅、红丹和硝酸铅21.废铅蓄电池回收铅技术22.分离回收镀白铜针铜锡的方法及其阳极滚筒装置23.分离冶金炉尘中锌铅的新工艺24.高活性微米纯铅粉制造技术25.高铅锑分离法26.含铁、锰、锌、铅的烟尘回收铅、锌的方法27.降铅液及其制备方法28.利用含铅废渣生产铅盐的方法29.铅炉渣磁选富集有价金属及其冶炼方法30.铅锑冶炼废渣处理方法31.铅锌矿的全湿法预处理方法32.一种无污染含铅废弃物再生纯铅冶炼工艺33.铅冶炼工艺34.生铅和精铅的除铊方法35.湿法炼铅的一种工艺36.水口山炼铅法37.碳酸钠转化处理铅基金矿或铅矿工艺38.锑火法精炼除铅法及其液态除铅剂39.锑铅合金用硫除铅的方法40.脱铋浮渣的脱铅方法41.无污染炼铅方法42.新式铅冶炼反射炉43.一种从废蓄电池回收铅的方法44.一种火法处理锑贵铅工艺45.一种铅锌多金属硫化矿的分离方法46.一种锑的熔融萃取精炼除铅剂47.一种无污染含铅废弃物再生纯铅冶炼工艺448.一种由方铅矿制备铅盐新工艺49.以废蓄电池渣泥生产活性铅粉的方法50.用反射炉复合法炼铅的方法51.用硅氟酸从硫化铅精矿浸取铅的工艺52.用硫化铅矿直接提炼金属铅的方法53.用于铅锌矿选择浮选的捕集剂及其制备方法54.用于铅锌矿选择浮选的捕集剂用途55.用于选择性浮选铅锌矿的促集剂56.由铅阳极泥制取硝酸银、回收铜、铅、锑的方法57.由铜合金制成的自来水管件的选择性除铅的工艺及除铅液58.再生铅的冶炼方法59.在中性介质中用电解还原回收废蓄电池中的铅方法60.重选用于选别细粒浸染状构造低品位铅锌矿61.从含氧化铅和或金属铅的材料提取金属铅的湿冶法62.废旧电池铅回收的方法63.废铅熔炼回转炉64.铅-锑粗合金离心偏析分离法65.一种铜转炉烟灰矿渣成团冶炼铅的新工艺及其成团配方66.应用混合捕集剂作为非硫化物矿,特别是锡石的浮选助剂67.直接铅熔炼生产金属铅的一种方法68.[ 200410021325 ]- 废旧蓄电池绿色提铅方法69.[ 02132647 ]- 废铅蓄电池回收铅技术70.[ 00100337 ]- 废铅酸蓄电池生产再生铅、红丹和硝酸铅71.[ 99113219 ]- 废旧蓄电池铅清洁回收技术72.从废铅蓄电池中湿法回收铅的技术进展73.天津建废铅酸蓄电池处理中心74.废铅蓄电池回收铅与开发黄丹、红丹以及净化铅蒸汽新工艺研究75.用废铅蓄电池制备黄丹和红丹76.废铅酸蓄电池回收处置现状与再生铅清洁生产工艺77.废旧铅酸蓄电池清洁拆解工艺探索78.废铅蓄电池的处理及资源化——黄丹红丹生产新工艺79.整顿废铅蓄电池回收和再生铅行业势在必行80.中国废铅酸蓄电池回收和再生铅生产81.中国废铅蓄电池回收和再生铅生产82.废旧铅蓄电池中铅的湿法回收83.废铅蓄电池回收铅锑新工艺研究84.从废铅蓄电池回收铅生产与研究85.从蓄电池糊膏回收铅的RSR法86.从废蓄电池中回收铅的方法87.国外废铅蓄电池回收利用技术简介88.从废铅酸蓄电池中回收有价金属89.[ 200510056582 ]- 氰化钠脱硫废渣制取选金氰化钠和硫化铅的方法90.[ 200310106645 ]- 无污染的炼铅方法91.[ 200410060803 ]- 生物浸出——萃取法分选彩钼铅矿的方法92.[ 200510094077 ]- 使受铅污染的土壤和含铅废水可以除铅及回收铅的装置93.[ 200410023072 ]- 一种锡铅锌硫化矿分步浮选技术94.[ 200310122475 ]- 吸附、离子交换联用除蜂胶中的铅95.[ 200410014573 ]- 铅锌硫化矿快速选铅选锌工艺96.大气颗粒物中铅的序列提取与分析表征97.原子荧光光谱法测定淫羊藿提取物中的铅98.湿法从氰化金泥中提取金、银、铜、铅工艺试验研究99.平衡时间及含水量对红壤有效态铅提取量的影响100.土壤中铅镉有效态提取剂的选择101.超声波提取-DPV溶出伏安法快速测定白菜中铜、铅、锌102.从铜镉渣酸浸后废渣中提取粗铅103.某含银高铅复杂多金属矿的分离提取104.阳极溶出方波伏安法同时测定竹叶提取物中的铜、铅和镉105.十二烷基苯磺酰胺喹啉作载体的液膜法提取水中铅的研究106.从烟灰铅渣中提取三盐基硫酸铅的实践107.西部氧化铅锌资源提取基本思路探讨108.从冶锌工业废渣中提取铅、锌、铜、镉109.从烟灰铅渣中提取三盐基硫酸铅的生产实践110.土壤中铅镉的化学形态和有效态的提取与分离研究111.黑白显像管玻壳铅尘中铅的提取方法112.显像管玻壳含铅粉尘中铅形态及提取方法研究113.用液态阴离子交换剂提取分离铀和铅114.从高银铅阳极泥中提取金银并综合回收铅锑等有价金属115.黄河口及其附近海域沉积物中可提取的铅和镍116.湿法氯化方铅矿提取铅盐和单质硫的研究117.提取和回收土壤中的铅类118.用亚硫酸钠从高铅氯化渣中提取119.从炼铜烟尘中提取三盐基硫酸铅的生产实践120.索氏提取-石墨炉原子吸收光度法测定大气飘尘中痕量铅121.含铜,铅等杂物粗银的湿法提纯方法122.胭脂河矿区含金黄铁矿方铅矿的分选提纯实验123.应用内标的APDC-Cu(Ⅱ)快速共沉淀分离富集和原子吸收光谱测定食盐中的铅124.磷酸钕共沉淀选择性分离富集-原子吸收测定环境水样中痕量铅125.豫光金铅10万t再生铅分离工程奠基126.某选矿厂矿泥系统铅锌分离工艺的探索127.某选矿厂矿泥系统铅锌分离探索研究128.CL-7402萃淋树脂分离富集铅的研究及其应用129.铜铅分离试验研究130.分离冶金炉尘中锌铅的新工艺131.组合抑制剂在铜铅分离浮选中应用的试验研究132.锡铁山含银铅锌硫化物矿石浮选分离研究133.脆硫铅锑矿铅锑分离新工艺研究134.钢铁厂含锌铅粉尘中锌铅分离的半工业试验135.岩石中微量铅分离方法的实验研究136.从铟锗酸浸尾渣中浮选分离铅锌金属137.某低品位铅锌分离无氰工艺的研究138.岩石中铅和锌的分离与测定139.铅锑合金火法分离工艺探讨140.多金属硫化矿石中低品位铅锌分离无氰工艺研究141.硫酸铵-二溴对甲基偶氮羧磺-聚乙二醇-水体系浮选分离铅(Ⅱ)142.硝酸钠-硫氰酸铵-十六烷基三甲基氯化铵-水体系浮选分离铅(Ⅱ)143.硝酸钠-碘化钾-氯化十六烷基吡啶体系浮选分离铅(Ⅱ)的研究144.硝酸钠存在下碘化钾—十六烷基三甲基氯化铵—水体系浮选分离铅(Ⅱ)的研究145.光度法研究聚乙二醇—硫酸铵—邻苯三酚红体系中铋(Ⅲ),铁(Ⅲ),铜(Ⅱ),镍(Ⅱ),钴(Ⅱ),铅(Ⅱ)的萃取分离146.混合粗精矿铅锌分离抑制剂研究147.缅甸铅锌混合粗精矿铅锌分离试验研究148.某难选铅锌矿石浮选分离新工艺试验研究149.PbS—Sb2S3二元系在水蒸气气氛下的铅锑分离研究150.PbS—Sb2S3—FeS三元系在水蒸气气氛下的铅锑分离151.钢铁厂含锌铅粉尘中锌铅分离理论及实践152.秘鲁劳拉选矿厂新铜铅分离法的研究和应用153.难选硫化铜与硫化铅的浮选分离工艺154.会理锌矿铅锌浮选分离新工艺研究155.铜铅锌银多金属矿湿法分离新工艺156.沉淀法、溶剂萃取法分离铅与稀土的探讨157.用铁浴法分离离炉炉尘中的铅和锌158.乳状液膜法分离水中铅的研究159.会理锌矿铅锌分离试验研究160.硫酸铵-碘化钾-溴化十六烷基吡啶体系浮选分离铅161.硫化物沉淀法选择性分离碱性锌溶液中的铅162.含金多金属硫化矿酮铅分离的研究163.内蒙古某铅锌矿铅锌分离的研究与实践164.锌冶炼中酸浸渣的锌铅分离165.微细粒氧化铅锌矿复合活化疏水聚团浮选分离新工艺166.利用组合抑制剂进行铜铅分离的试验研究167.铜铅分离无铬浮选168.铜铅混合精矿无氰无铬法分离工艺综述169.乐昌铅锌矿铅锌流浮选分离新工艺研究170.三盐基硫酸铅连续分离和干燥工艺简介171.人发及废水中痕量铅的液膜分离与测定172.用液膜分离技术处理含铅废水173.豫灵金矿铜铅硫分离工艺的探索174.金同铅锌矿化的分离及共生175.乙硫氮浮选铅及铅锌分离的研究176.低空白分离岩石中微量铅177.混合精矿体系中方铅矿与黄铁矿浮选分离的矿浆电化学(Ⅰ)- 178.混合精矿体系中方铅矿与黄铁矿浮选分离的矿浆电化学(Ⅱ):--…179.方铅矿与黄铁矿浮选分离的矿浆电化学研究:Ⅲ.方铅矿与黄铁180.砂金中微量铅的分离与富集181.全岩中微量铅分离方法的实验研究182.湿法回收废铅蓄电池制备三碱式硫酸铅183.用碱法从电弧炉烟尘中回收铅和锌184.提高铅锌选矿回收率的生产实践185.碳黑泥对废水中铅(Ⅱ)的吸附和回收利用186.提高含银铅铜金矿石金回收率的研究与生产实践187.铅矾浮选:从锌浸出渣中回收铅的研究188.从锌浸出渣中回收铅的研究189.从锌厂废渣中回收锌和铅190.从云南边境某选矿尾矿中回收铅锌的工艺试验研究191.含砷铅铋渣综合回收铅铋的研究192.氰化尾渣回收铅锌混合精矿过程清洁生产技术的研究与应用193.废旧铅酸蓄电池的回收利用与环保194.提高某铅矿金铅回收率的选矿试验研究195.废铅酸蓄电池铅回收清洁生产工艺196.健康教育在防治废旧蓄电池回收人员铅中毒中的作用197.车用废旧铅酸电池回收再生市场商机无限198.提高云南某铅锌矿回收率的选矿工艺研究199.锡阳极泥中回收锡铋铜铅的工业试验200.提高七宝山铅锌矿铅锌回收率的措施201.无锡市出台电动车废铅蓄电池回收新规202.复杂多金属物料综合回收铜铅锌锡试验研究203.提高凡口选矿厂矿泥系列铅锌回收率的研究204.用AC法从高锑低银类铅阳极泥中回收银和铅205.铅鼓风炉渣中铅锌等有价金属回收的设计和生产实践206.报废铅酸蓄电池的回收利用研究207.三山岛金矿从氰渣中回收铅金属的生产实践208.三盐基硫酸铅废渣回收生产工艺研究209.西南稀土矿黑色风化矿泥中铅的回收210.陶瓷测铅、镉废酸液的回收利用研究211.凡口铅锌矿资源的综合回收与利用212.火法-湿法联合工艺处理铅铋银硫化矿综合回收有价金属213.电子信息产品无铅技术及回收利用国际研讨会214.凡口铅锌矿锗和镓资源与回收215.凡口铅锌矿稀散金属选矿回收实践216.冶金含锌铅炉尘回收处理新方法217.废旧铅酸电池的回收和再利用218.从氰化尾矿中浮选回收铅、锌的生产实践219.废旧电池铅回收法220.干法消化对铅回收率影响的探讨221.乡镇废旧蓄电池回收对环境和儿童血铅的影响222.:从锌渣浸渣中综合回收铟锗铅银的试验研究223.磺酰胺萃取回收水中的铅224.中国废铅蓄电池回收利用现状及管理对策225.回收上规模市场待规范:评我国再生铅行业的发展226.我国废铅蓄电池回收处理现状及对策227.我国废铅蓄电池回收处理环境现状及对策228.用湿法冶金法从黄铜熔渣中回收铜,镜和铅229.提高云南昭通地区铅锌矿铅锌回收率的工艺技术研究230.从合金丝废料回收铅,锡和铟231.天水金精矿氰化尾渣综合回收铜铅的试验研究232.自多金属精矿中综合回收金银铜铅的清洁工艺233.小高炉回收铅的生产实践234.高硫铅锌矿石部氧化铅中回收技术研究235.浅析从废蓄电池中回收铅直收率的提高236.银洞坡金矿氰化尾矿直接浮选回收铅,金,银的工艺研究和生产实践237.火湿法冶金并用从工业废料中回收高铅锡青铜238.提高金家河选矿厂铅锌产品质量和回收率的生产实践234.从多金属精矿中湿法综合回收金银铜铅的研究235.欧洲的蓄电池回收和再生铅工业236.我国含铅蓄电池回收利用的现状与对策237.小高炉回收铅银生产实践238.低品位铅锌精矿回收铅锌的研究239.混合浮选--从印度一种复杂多金属硫化矿床中回收铅锌有价成…240.从含铜锌铅矿氧压酸浸渣中回收铅和硫的研究241.从氯化铅渣中回收铅铋的研究242.中国铅的消费及回收243.小口金精矿氰化尾渣综合回收铅的试验研究244.一种湿法回收废铅蓄电池填料的新技术245.电化学法从废料中回收金银和铅的工艺研究246.电化学法处理有毒废料回收金银和铅247.改进选矿流程提高铅银回收率248.用立式熔炼炉回收转炉烟尘中铜,铅,锌的方法249.氯盐法从含硫铅渣中回收铅250.株冶铜铅锌生产的综合回收251.铅酸蓄电池综合回收法:CX-EW技术252.铅渣回收新工艺253.从废铅蓄电池中湿法回收铅技术的述评254.发达国家废铅蓄电池的回收政策及我国的对策255.改变加药地点提高铅精矿质量和回收率256.铁闪锌矿浮选中铅的回收257.从铅电解阳极泥回收铅锑合金258.铁置换法从多金属硫化物浸渣中回收铅259.小高炉冶炼复合锰矿时铅的回收260.提高张全庄金矿选厂金回收率和综回收铅的生产实践261.从氯化废渣中综合回收银,铅262.铅酸蓄电池综合回收法:CX-EW技术263.从分金炉渣中回收金,银,锡,铅的工艺研究264.高品位载金多金属硫化矿提金及综合回收铅锌265.从电解铅阳极泥中回收铅锑合金266.梭梭井银铅矿床银的赋存状志及其与回收率的关系267.从浮选粗精矿氰化炭浆法提金尾渣中综合回收铜铅金银的试验268.热浸镀锌回收液中钢铜镍锰镉铅的原子吸收光谱分析269.回收金属铅与延长富锰渣电炉炉龄270.铜阳极泥湿法工艺过程中铅铋的分布及回收方案271.由锌钡白酸浸废渣回收铅制取三盐基硫酸铅的研究272.提高反射炉熔铅的回收率273.回收铅的短回转窑274.用硫化-浮选法从锌渣中回收铅,银,金275.含金灰及含银铅物料的综合回收利用276.西德布劳巴赫炼铅厂废旧蓄电池的回收利用277.Metaleurope在奥卡炼铅厂的二次铅回收278.氧化锑中金铅的综合回收279.从铜转炉烟尘中回收铅与铋280.用鼓风炉处理转炉烟灰回收铜,铅,锌的方法281.推动再生铅产业健康发展需要解决的问题282.新再生铅生产技术已在生产中应用283.厦门兴建亚太最大再生铅企业将于今年8月投产284.新的再生铅生产技术285.新技术促使更好地利用再生铅286.上海飞轮研发出新再生铅生科技术287.含铅危险固废物的保再生处理方法288.再生铅新技术问世289.中国再生铅产业可持续发展的必然选择290.我看废旧铅蓄电池的再生利用流程291.再生铅引进项目的设备电气调试292.含铅危险固体废物的环保再生处理方法293.固相电解法——一种再生铅的新技术394.重视铅锌再生,发展循环经济295.失效铅酸蓄电池可以再生修复296.湖北金洋公司年产十万吨再生铅扩建项目正式启动297.处理再生铅原料的生态安全问题298.再生铅生产中含铅废渣处理工艺探讨299.我国再生铅工业发展现状及政策措施300.铅再生方法的实践和探索301.七大问题制约我国再生铅行业健康发展302.大力发展再生铅工业,促进我国铅资源产业持续发展303.清华大学铅酸蓄电池再生液304.废铅酸电池回收再生市场需规范305.再生铅生产306.含铅废弃物无污染再生纯铅及合金307.铅蓄电池再生方法的试验与探讨308.我国再生铅生产及与国外的差距309.增强环保意识发展我国再生铅工业310.从废旧蓄电池中无污染火法冶炼再生铅及合金311.印刷线路板脱铅锡液的再生利用312.再生铅冶炼对土壤环境影响及其评价和环境管理313.关于改变中国再生铅现状和制定有关政策法规的建议314.硫化物矿石的再生(以铅-锌矿床为例)315.国内外再生铅生产现状及发展趋势316.利用再生精铅生产铅钙合金的工艺试验317.国外再生铅工业的发展318.再生铅冶金过程的"三废"及其治理319.我国再生铅资源现状及铅市场预测320.再生铅低锑合金的工艺及应用321.再生铅反向炉改造及炉龄提高322.恩绍芬公司再生铅技术的改进323.废铅蓄电池再生冶炼的工艺探讨324.废铅酸蓄电池的再生修复325.废铅再生新工艺326.用废铅蓄电池湿法再生铅的研试327.用废铅蓄电池极板再生精铅328.再生铅的生产329.[ 200510032520 ]- 用萃取-电解法从冶炼铅锌矿尾渣中提取金属镓的技术330.[ 200610011194 ]- 一种对铅锌尾矿进行铅锌复合提纯的湿化学方法331.[ 200610010909 ]- 低温硫化转化难选复杂氧化铅锌矿的方法332.[ 200610066648 ]- 一种炼铅法以及用于实现该炼铅法的装置333.[ 200610000393 ]- 蓄电池二氧化铅的循环利用方法和装置334.[ 200510137829 ]- 铅粉机335.[ 200510030984 ]- 废旧印刷电路板混合金属中铅元素的真空蒸馏分离方法336.[ 200510092400 ]- 铅蓄电池的铅膏及铅板的脱硫方法337.[ 200510010889 ]- 难选复杂氧化铅锌矿热压转化的方法338.[ 200510075224 ]- 用于机动车的铅酸蓄电池339.[ 200580008153 ]- 回收铅酸电池电极之间的分离器中存在的二氧化硅的方法340.[ 200410155579 ]- 综合回收利用铅锑鼓风炉弃渣的工艺341.[ 200410023272 ]- 一种硫化-氧化混合铅锌矿浮选方法342.[ 200510032037 ]- 从方铅矿精矿直接制备超细氧化铅粉体的方法343.[ 200610048650 ]- 浮-重-浮联合流程回收彩钼铅矿的方法344.[ 200610048548 ]- 废铅酸蓄电池板栅和膏泥的处理工艺345.[ 200610086420 ]- 从金矿氰化尾渣中浮选回收铅锌混合精矿的方法346.[ 200610031387 ]- 利用废铅蓄电池板栅和连接件制备三盐基硫酸铅的方法347.[ 200610038298 ]- 全湿法酸式电解固相原位还原废蓄电池铅清洁回收方法348.[ 200510017760 ]- 一种再生铅加工工艺及装置349.[ 200520031143 ]- 一种再生铅加工装置350.[ 200510077746 ]- 电解液带纳米碳的阀控式密封铅酸蓄电池351.[ 200410060943 ]- 铅酸蓄电池极板生产中废硫酸的回收方法及设备352.[ 200480025066 ]- 从废铅-酸电池中高产率地回收铅并降低相关的矿渣与气态释放物产生的方法353.[ 200410014571 ]- 提高铅中银回收率的分步浮选工艺354.[ 03821761 ]- 金属氧化物或炼铁废弃物的还原处理方法以及锌和/或铅的浓缩回收方法355.从氯化铅水溶液中电解提取铅356.从铅中提取贵重金属的新方法357.粗金除铅提纯的工艺研究358.含铜,铅等杂物粗银的湿法提纯方法359.硫酸盐沉淀分离法测定粗铅中的铅含量360.新型抑制剂RC分离脆硫锑铅矿和磁黄铁矿的研究361.某难选铜铅混合精矿的分离试验研究362.用天然磷酸盐从水溶液中分离铅363.河南豫光金铅10万吨/年再生铅分离工程土建开工364.萃取分离-石墨炉原子吸收光谱法测定铁镍基高温合金中砷、铅、锡、锑、铋365.负载有结晶紫的微晶酚酞分离铅(Ⅱ)366.硝酸-过氧化氢消解试样-MIBK-APDC萃取分离FAAS法测定酱油中铅367.离心分离共沉淀原子吸收光谱法测定饮用水中铅和镉368.基体分离-ICP-AES法测定镀金液中铅、铜、铁、镍的研究369.磷酸铈共沉淀分离富集硫酸钴中痕量铅及铅的原子吸收光谱测定370.浮游球衣菌的分离及其对铅离子的吸附性能371.用电渗析法纯化回用含铅废水372.铜铅锌多金属复杂硫化矿综合回收工艺研究373.从铅阳极泥中回收铋的火法工艺实践374.从铅浮渣反射炉烟灰中回收铟生产实践375.铅膏回收系统设备及应用376.某氰化尾矿综合回收铜铅的试验研究377.全球铅回收发展趋势(上)378.用自吸式充气浮选柱回收铅锌尾矿中锌的试验379.银在ISP铅锌冶炼中的行为分布及回收380.从铅锌选矿厂沉积物中回收金要了解更多详细内容请看网站天农高科。
铜阳极泥脱铜渣中铅的高效浸出试验研究
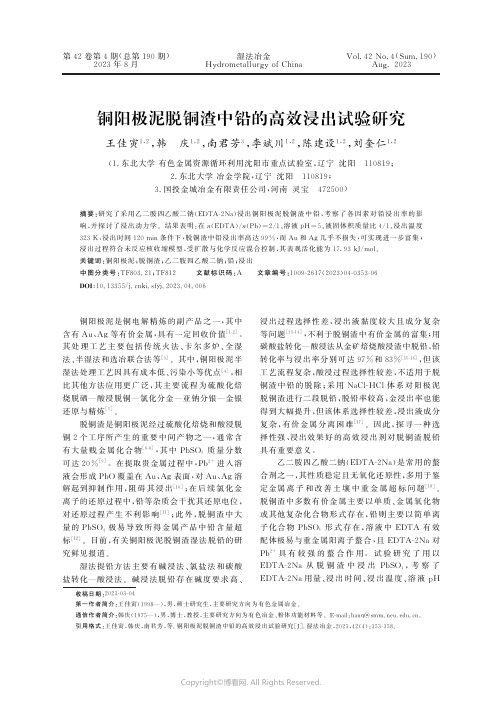
脱铜渣中 Pb 的 主 要 物 相 为 PbSO4 。EDTA
V0
t
(
x =ρ ×100% 。
3)
mw
式中:
x—铅浸出率,% ;
ρt—浸 出t 时 间 时 溶 液 中
铅质量浓 度,
V0 —初 始 溶 液 体 积,
L;
m—脱
g/L;
铜渣质量,
w—脱铜渣中铅质量分数,% 。
g;
2 试验结果与讨论
/n(
2
Copyright©博看网. All Rights Reserved.
第 42 卷第 4 期
王佳寅,等:铜阳极泥脱铜渣中铅的高效浸出试验研究
· 355 ·
/n(
浸出效 果。因 此,确 定 适 宜 的n(
EDTA)
Pb)为
体积质量比对脱铜渣中 Pb 浸出率的影响试验结
/n(
图 2 n(
EDTA)
Pb)对脱铜渣中 Pb 浸出率的影响
2+
宜溶液 pH 为 5。
2
.3 液固体积质量比对脱铜渣中 Pb浸出率的影响
/
试 验 条 件:
n(
EDTA)
n(
Pb)=2/1,浸 出 时
间 120mi
n,溶液 pH=5,浸 出 温 度 323 K。 液 固
由图 5 看 出:随 浸 出 时 间 延 长,脱 铜 渣 中 Pb
/mi
热式磁力搅拌 器 内(
400r
n,±0
.1 ℃ )开 始 升
温,用 NaOH 和 HCl调溶液 pH,同时使用 pH 计
进行监测。待 pH 与 温 度 达 到 预 定 值 后,将 脱 铜
渣加入到烧杯中,开启搅拌并计时,搅拌过程中调
- 1、下载文档前请自行甄别文档内容的完整性,平台不提供额外的编辑、内容补充、找答案等附加服务。
- 2、"仅部分预览"的文档,不可在线预览部分如存在完整性等问题,可反馈申请退款(可完整预览的文档不适用该条件!)。
- 3、如文档侵犯您的权益,请联系客服反馈,我们会尽快为您处理(人工客服工作时间:9:00-18:30)。
收稿日期:2002-12-24作者简介:曾懋华(1965-),男,湖南益阳人,韶关学院化学系教师,硕士研究生,主要从事应用化学的研究.从铜镉渣酸浸后废渣中提取粗铅曾懋华1,2,易飞鸿1,彭翠红2,奚长生2(1.广东工业大学轻工化工学院,广东广州510081;2.韶关学院化学系,广东韶关512005)摘要:利用铜镉渣酸浸后的含铅废渣湿法生产醋酸铅及铅,有利于提高经济效益、改善生态环境.通过对铅渣中硫酸铅转变为醋酸铅的方法探讨,以及湿法提取铅的生产工艺流程和条件的研究,制得了纯度达90%以上的粗铅.关键词:环境保护;重金属提炼;铅;铜镉渣中图分类号:X 758 文献标识码:A 文章编号:1007-5348(2003)03-0084-05冶金工业生产中的铜镉渣、锌渣等含铅废渣通过二次利用,以硫酸浸取后的酸浸渣中的铅含量都很高,且主要以硫酸铅的形式存在,其硫酸铅含量一般为30%左右.酸浸渣含有铜、镉、银、铁等杂质,且难以分离,因而大多数的工厂把生产排出的含铅废渣作为废物堆放.铅是一种对人体有毒的重金属,含铅废渣的长期堆放会污染环境,破坏生态平衡,影响人们的生活.因此,从含铅废渣中提取铅,在提高经济效益和二次资源利用方面都有重要的意义,同时,铅的回收也有利于减少环境污染,保护生态环境.国内外从铅盐中提取铅,主要用电解法和置换法,以锌粉置换存在置换率低、生产成本高的缺点[1].本文作者对含铅废渣的综合利用进行了探讨,通过多种方法进行各种试验,研究出以锌粒置换铅以及由硫酸铅转变为醋酸铅的方法,此法具有抗杂质干扰性好、工艺流程简单、生产出的粗铅含铅量高,可以直接应用制取铅制品等优点.1 基本原理以20%~25%的硫酸浸取含铅废渣[2],铅以硫酸铅的形式存在于酸浸渣中,利用碳酸盐与硫酸铅(K sp (PbS O 4)=116×10-8)反应,生成溶度积更小的碳酸铅(K sp (PbCO 3)=714×10-14)沉淀:PbS O 4+Na 2C O 3=PbC O 3+Na 2S O 4PbS O 4+(NH 4)2C O 3=PbC O 3+(NH 4)2S O 4PbS O 4+2NH 4HC O 3=PbC O 3+(NH 4)2S O 4+C O 2↑+H 2O用1ζ1的醋酸溶解碳酸铅,得到醋酸铅工业产品.PbC O 3+2H Ac =Pb (Ac )2+H 2O +C O 2↑由醋酸铅作为中间产品可制取金属铅.调节pH 值后,将锌粒加入到醋酸铅溶液中,将铅置换出来:Pb 2++Zn =Pb +Zn 2+2003年3月韶关学院学报(自然科学版)Mar.2003第24卷 第3期Journal of Shaoguan University (Natural Science )V ol.24 N o.3附在锌粒上的金属铅为海绵状,显淡灰色,容易脱落,经过洗涤压制成块后,低温干燥,即得淡灰色具有金属光泽的铅产品.2 试验工艺流程由含铅废渣提取粗铅的试验工艺流程[3]如图1所示.饱和(NH 4)2C O 3溶液↓含铅废渣硫酸洗涤过滤滤渣沉淀转化后过滤1ζ1的醋酸↓锌粒↓滤渣过滤得醋酸铅溶液海绵铅洗涤干燥产品粗铅图1 试验工艺流程图3 工艺条件311 酸浸渣洗涤除杂酸浸渣的表面常有铜、铁、镉等元素及化合物,它们的存在将影响到产品的质量,需用20%的硫酸再次浸取,并需加入H 2O 2作氧化剂.过滤分离,滤液用作浸取锌渣的原料,酸浸渣用水洗涤干净,以消除可溶性盐类的干扰,特别是铜、铁等杂质离子对醋酸铅产品的影响.酸浸渣的清洗液可并入铜镉渣的酸浸液中用以提取铜、镉、锌.硫酸浸取渣放置过久易结块,给洗涤带来困难,试验中采用新制的硫酸浸取渣提取铅.312 硫酸铅的转型硫酸铅的转型方法有两种,一种是直接转化为可溶于水的盐,另一种方法就是转化为比它更难溶的沉淀[4].第一种方法,本实验中是用高浓度的NaOH 溶液溶解含铅废渣,发现溶解的效果很好,在控制好一定的pH 值后,硫酸铅全部转化为铅酸盐,但滤液中溶解了较多的杂质,难于分离,对产品质量带来严重的影响;如果用NH 4Ac 溶液浸取,则要过量一倍左右的NH 4Ac 才能使PbS O 4全部转化为Pb (Ac )2,并且反应速度比较慢,反应终点难以判断,生产出的Pb (Ac )2产品中混有较多的NH 4Ac 和(NH 4)2S O 4,使产品分离比较困难,这种方法既增加了生产成本,又使所得产品难于分离,不符合工业生产的要求.而将硫酸铅转化为更难溶的碳酸铅沉淀,工艺流程简单,操作方便,转化彻底,且在一般情况下不会使渣中的杂质转化,得到的产品纯度较高.31211 Na 2C O 3转型试剂的研究:在铅渣中加入饱和碳酸钠溶液,常温时反应40min ,在200r/min 的搅拌条件下,对碳酸钠的用量进行了多次实验,结果见表1.表1 Na 2CO 3用量对转化率的影响碳酸钠的量与理论用量的比例时间/min温度/℃搅拌速度/r ・min -1PbS O 4的转化率/%1ζ1104025200891341ζ1114025200951671ζ1124025200991651ζ113402520099187 由表1可知,在其它条件相同的情况下,要达到比较高的转化率,必须使碳酸钠过量・58・第3期曾懋华,等:从铜镉渣酸浸后废渣中提取粗铅112倍以上,这样就使得副产物Na 2S O 4溶液中混有较多过量的Na 2C O 3,不利于副产物的回收和再利用.31212 NH 4HC O 3转型试剂的研究:在铅渣中加入饱和碳酸氢铵溶液,在相同的温度(25℃)和反应时间(60min )内,对碳酸氢铵的用量与硫酸铅的转化率研究结果见表2.表2 NH 4HCO 3用量对转化率的影响碳酸氢铵的量与理论用量的比例时间/min温度/℃搅拌速度/(r ・min -1)PbS O 4的转化率/%1ζ1106025200691161ζ1126025200751621ζ1146025200821481ζ1166025200891351ζ1186025200941571ζ210602520095139 由表2各项数据可知:尽管碳酸氢铵的用量达到理论用量的2倍,硫酸铅的转化率仍然不高,只达到95139%.主要原因是有一半的碳酸根转化为二氧化碳气体放出,另外NH 4HC O 3比较容易分解,当温度达到35℃时即分解,开始产生C O 2和H 2O ,从而使实际消耗的NH 4HC O 3量大大增多,硫酸铅的转化率自然就下降.31213 (NH 4)2C O 3转型试剂的研究:在其它条件不变的情况下,对碳酸铵的用量和硫酸铅的转化率进行了对比实验,实验结果见表3.表3 (NH 4)2CO 3用量对转化率的影响碳酸铵的量与理论用量的比例时间/min温度/℃搅拌速度/(r ・min -1)PbS O 4的转化率/%1ζ1106025200951121ζ1116025200981461ζ1126025200991431ζ113602520099165 由表3可知,用碳酸铵做转型剂,只要过量112倍即可达到99%以上的转化率,完全能满足工业生产的要求[5].主要原因是(NH 4)2C O 3的最低分解温度为60℃,在常温下反应不会使它分解,在反应中没有二氧化碳产生,原材料消耗少,生产成本低,符合工业生产的要求.生成的副产物(NH 4)2S O 4既可以与过量的(NH 4)2C O 3一起作为混合氮肥生产,又可以加热浓缩,使过量的(NH 4)2C O 3分解(用水吸收产生的气体重新用于(NH 4)4C O 3再利用),在加热到100℃时(NH 4)2C O 3几乎全部分解完全,这样就能得到较纯净的固体化肥硫酸铵.由此可见,以碳酸铵作为转型试剂在相同的实验条件下,能较好地使硫酸铅转化为更难溶的碳酸铅.在常温下,采取两次转化的方法,控制碳酸铵的浓度为160~180g/L ,反应时间为1h 以上,即可使99%以上的硫酸铅转化为碳酸铅.313 醋酸铅溶液的制备将上述转化所得的碳酸铅洗涤干净后转入烧杯中,并加入适量的1ζ1的醋酸溶液至沉淀完全溶解后,过滤,得到醋酸铅溶液.由醋酸铅可以转化为其它形式的铅盐或制得金・68・韶关学院学报(自然科学版)2003年属铅.314 金属铅的制备把上述制得的醋酸铅溶液转入烧杯,加热到50℃,在不断搅拌的条件下,加入锌粒(理论质量ζ实际质量=1ζ112)进行反应.置换反应在锌粒的表面进行,生成的铅呈海绵状,附在锌粒的表面,影响锌粒继续反应.搅拌时海绵铅从锌粒的表面脱落,沉积在容器底部.反应1h 后,过滤,用水洗涤海绵铅,洗净后,压制成块,低温干燥即可得到淡蓝灰色有金属光泽的铅.经检测,滤液中铅的含量为1mg/L 左右,铅的置换率达到9916%.得到的海绵铅用原子吸收分光光度法测定,纯度达到95162%.4 从硫酸浸渣中提取铅本实验采用韶关马坝冶炼厂的铜镉渣,以20%的硫酸溶液浸取,过滤干燥后取滤渣实验,经分析含硫酸铅2718%.取干燥后的硫酸浸渣1000g ,按实验步骤操作,制得粗铅14916g ,回收率为9518%,经原子吸收分光光度法及E DT A 滴定法测定,纯度为9214%.5 问题与讨论511 用锌粒代替锌粉由于锌粉置换生成的铅成粉末状,如直接加入干粉或是湿粉会使许多未发生反应的锌粉被裹住,不能完全反应.搅拌会使柔软的粗铅聚集成团,搅拌速度越快,成团越快,这样就会浪费很多锌粉,生成的铅纯度不高.采用锌粒代替锌粉,生成的铅松散,以一定的速度搅拌,可使海绵铅及时脱离锌粒的表面.由于铅的原子量较大,产生的海绵状铅很快下沉,使置换反应顺利进行.512 温度对置换速度的影响用锌粒置换铅,温度太低,反应速度慢,反应时间长,不利于工业生产.温度过高所需的热能多,增加生产成本;醋酸铅中混有的少量醋酸也会将生成的铅部分溶解.实验证明:置换铅的最佳温度为50℃左右.513 溶液pH 值对置换率及粗铅纯度的影响以锌粒理论质量ζ实际质量=1ζ112,加热50℃,不断快速搅拌下加入锌粒,得到的结果如表4所示.由表4可知,如果pH 值太小(如pH 值3~4和pH 值4~5),H +浓度较大,加快了锌与氢离子的反应,产物表面有气泡,根据从酸浸渣中所得含铅液的置换实验可知,控制pH 值为5~6时较为适宜.514 锌粒的用量实验采用普通试剂锌粒,平均粒重012g.置换反应在锌粒表面进行,在搅拌时相互碰撞,生成的铅不断脱落,锌粒呈现新的表面继续反应,颗粒逐渐变小.以所需理论质量与不同的实际用量加入锌粒,得到的实验结果如表5所示.表4 溶液pH 值对置换率及粗铅纯度的影响开始pH 值5~64~53~4反应后pH 值5~664~5置换率/%991739912098138粗铅纯度/%901529110289169表5 锌粒用量试验结果锌粒理论质量ζ实际质量1ζ1111ζ1121ζ113滤液中铅含量/mg ・L -1518111018粗铅纯度/%961269415891133 从表5可知,锌量较少时,粗铅纯度较高,但置换不完全;锌量过多,则其它共存离・78・第3期曾懋华,等:从铜镉渣酸浸后废渣中提取粗铅子同时被置换,粗铅的纯度降低.在其它条件不变的情况下,锌粒的理论质量与实际质量的最佳比例为1ζ112.6 结语铅具有抗酸、抗碱、防潮等优点,大量用于制造铅蓄电池、电缆包衣、铅管和化工设备内衬、轴承合金、低熔合金、活字合金、焊料、放射性和射线的防护层等.从含铅废渣中回收铅有着广阔的应用前景,对于保护生态环境有积极的作用.采用本法从铜镉渣的硫酸浸渣中提取铅,以价格低廉的锌粒替代锌粉,解决了锌粉置换铅时搅拌易成团的问题,回收率高,粗铅纯度最高可达到97%,可以直接应用于某些铅制品,或者进一步电解制得精铅.本法工艺流程简单,只需一般生产设备即可,操作方便.参考文献:[1]东北工学院有色金属冶炼教研室.铅冶金[M].北京:冶金工业出版社,1975.17.[2]奚长生,等.含铅废渣生产硬脂酸铅的研究[J ].广东化工.2001(6):44-46.[3]周连江,乐志强.无机盐工业手册[M].北京:化学工业出版社,2000.[4]华中师范大学,等.分析化学(第三版)[M].北京:高等教育出版社,2001.[5]龚亚军,曹昌琳,龚乾,等.硫化铅在碳酸化转化过程中电化学行为的研究[A].中国有色金属学会.中国有色金属学会首届学术会议论文集[C].北京:冶金工业出版社,1986.85-90.Study on Abstraction of Lead from the Acidized SedimentContaining Copper and C admiumZE NG Mao 2hua 1,2,YI Fei 2hong 1,PE NG Cui 2hong 2,XI Chang 2sheng 2(1.Institute of Light Industry and Chemistry ,G uangdong University of T echnology ,G uangzhou 510081,G uangdong ,China ; 2.Department of Chemistry ,Shaoguan University ,Shaoguan512005,G uangdong ,China )Abstract :T ake use of the sediment containing the lead from the acidized copper and cadmium sedi 2ment to hydro 2metallurgic produce the lead acetate and lead.Which is available to enhance the eco 2nomic values and im prove the environment.By studying the technics of converting the lead sulfate to lead acetate and the technics of hydro 2metallurgic distilling .The lead from the sediment converting the lead which is disposed by acidizing the copper and cadmium sediment .We can distill the lead 90per 2cent.K ey w ords :environment protect ;heavy metal distill ;lead ;copper and cadmium sediment(责任编辑:赵 鸥)・88・韶关学院学报(自然科学版)2003年。