渗碳淬火齿轮有效硬化层深度
重载齿轮渗碳质量检验标准
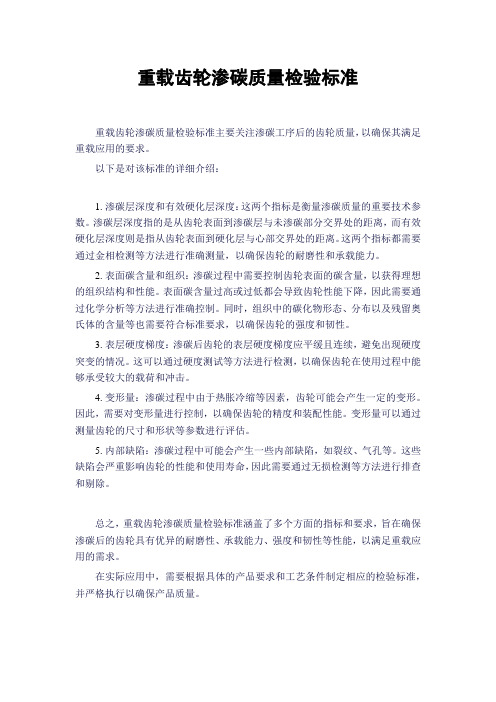
重载齿轮渗碳质量检验标准重载齿轮渗碳质量检验标准主要关注渗碳工序后的齿轮质量,以确保其满足重载应用的要求。
以下是对该标准的详细介绍:1.渗碳层深度和有效硬化层深度:这两个指标是衡量渗碳质量的重要技术参数。
渗碳层深度指的是从齿轮表面到渗碳层与未渗碳部分交界处的距离,而有效硬化层深度则是指从齿轮表面到硬化层与心部交界处的距离。
这两个指标都需要通过金相检测等方法进行准确测量,以确保齿轮的耐磨性和承载能力。
2.表面碳含量和组织:渗碳过程中需要控制齿轮表面的碳含量,以获得理想的组织结构和性能。
表面碳含量过高或过低都会导致齿轮性能下降,因此需要通过化学分析等方法进行准确控制。
同时,组织中的碳化物形态、分布以及残留奥氏体的含量等也需要符合标准要求,以确保齿轮的强度和韧性。
3.表层硬度梯度:渗碳后齿轮的表层硬度梯度应平缓且连续,避免出现硬度突变的情况。
这可以通过硬度测试等方法进行检测,以确保齿轮在使用过程中能够承受较大的载荷和冲击。
4.变形量:渗碳过程中由于热胀冷缩等因素,齿轮可能会产生一定的变形。
因此,需要对变形量进行控制,以确保齿轮的精度和装配性能。
变形量可以通过测量齿轮的尺寸和形状等参数进行评估。
5.内部缺陷:渗碳过程中可能会产生一些内部缺陷,如裂纹、气孔等。
这些缺陷会严重影响齿轮的性能和使用寿命,因此需要通过无损检测等方法进行排查和剔除。
总之,重载齿轮渗碳质量检验标准涵盖了多个方面的指标和要求,旨在确保渗碳后的齿轮具有优异的耐磨性、承载能力、强度和韧性等性能,以满足重载应用的需求。
在实际应用中,需要根据具体的产品要求和工艺条件制定相应的检验标准,并严格执行以确保产品质量。
渗碳淬硬层有效深度名词解释
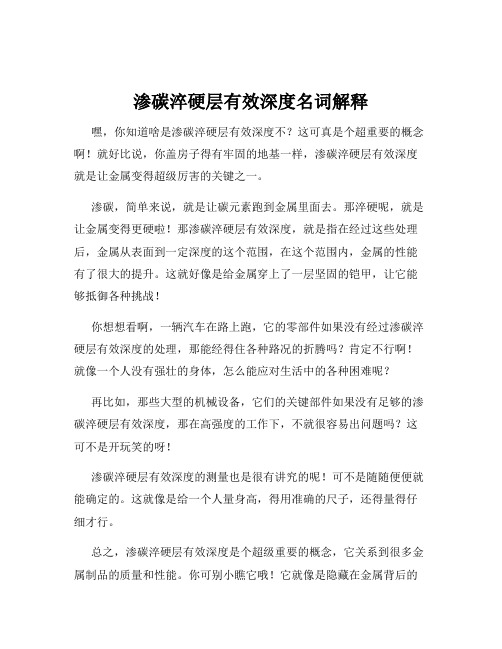
渗碳淬硬层有效深度名词解释嘿,你知道啥是渗碳淬硬层有效深度不?这可真是个超重要的概念啊!就好比说,你盖房子得有牢固的地基一样,渗碳淬硬层有效深度就是让金属变得超级厉害的关键之一。
渗碳,简单来说,就是让碳元素跑到金属里面去。
那淬硬呢,就是让金属变得更硬啦!那渗碳淬硬层有效深度,就是指在经过这些处理后,金属从表面到一定深度的这个范围,在这个范围内,金属的性能有了很大的提升。
这就好像是给金属穿上了一层坚固的铠甲,让它能够抵御各种挑战!
你想想看啊,一辆汽车在路上跑,它的零部件如果没有经过渗碳淬硬层有效深度的处理,那能经得住各种路况的折腾吗?肯定不行啊!就像一个人没有强壮的身体,怎么能应对生活中的各种困难呢?
再比如,那些大型的机械设备,它们的关键部件如果没有足够的渗碳淬硬层有效深度,那在高强度的工作下,不就很容易出问题吗?这可不是开玩笑的呀!
渗碳淬硬层有效深度的测量也是很有讲究的呢!可不是随随便便就能确定的。
这就像是给一个人量身高,得用准确的尺子,还得量得仔细才行。
总之,渗碳淬硬层有效深度是个超级重要的概念,它关系到很多金属制品的质量和性能。
你可别小瞧它哦!它就像是隐藏在金属背后的
魔法,让金属变得无比强大。
所以啊,一定要重视这个渗碳淬硬层有效深度啊!。
硬化层深度测定1
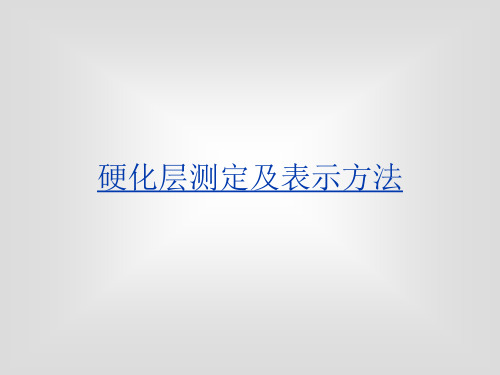
45
49
83
85
64
68
49
54
硬化层深度表示方法
(一).硬化层深度单位以mm表示,小数点第一位以下采四舍五入. (二).硬化层深度的表示符号,如表所示. 测 硬化层深度 微小维克氏硬度 定 方 法 巨观检视 腐蚀试验法
硬 度 试 验 测 定 方 法 洛氏硬度
高调波淬火 有效硬化层深度
火焰淬火 有效硬化层深度 高调波淬火 有效硬化层深度 火焰淬火 有效硬化层深度
氮化层深度及实用氮化层深度的表示方法: 1.1-氮化层深度及实用氮化层深度,单位以mm表示,取至小数点以下第二位. 1.2-氮化层深度较浅时,也可使用µm表示,但须于数字尾端加上单位. 备注: 1.ND:表示氮化层深度.参考(Nitrided case depth) 2.△:表示硬度测试的荷重,其单位为kgf. 3.M :表示金属显微组织(Microstructure). 4.T :表示全氮化层深度(Total Depth). 5.P :表示实用氮化层深度(Practical Depth).
表面硬度HMV(0.5)872 心部硬度HMV(0.3)126 0.1mm 800 0.2mm 846 0.3mm 761 0.4mm 621 0.5mm 400 0.6mm 309 0.7mm 201
硬化层深度表示方法
(一).硬化层深度单位以mm表示,小数点第二位以下采四舍五入. (二).硬化层深度的表示符号,如下表所示.
43.6 53.0 55.9 58.5 62.5 63.6 37.1 46.4 53.7 53.6 61.4 60.9
61.2 68.7 71.4 71.6 73.6 72.3 55.1 64.2 69.9 69.1 62.6 71.1
渗碳淬火组织评级

生产过程中酸洗法进行磨削烧伤的控制,当出现争议时可再用金相组织 法进行最终的判断
30g/L的硝酸水溶液
酸洗法介绍
溶液配比: 配好三种溶液 1、30g/L 的硝酸水溶液 2、50g/L 的盐酸酒精溶液 3、 50g/L 的氢氧化钠水溶液
酸洗法介绍
• 在酸洗前一定要用酒精或洗洁精去处零件表面的 油污和脏物,并用清水冲洗,确保零件表面非常
干净,这个清洗步骤非常重要,零件表面清洗不 干净会引起误判。
• 根据清水冲洗
水溶液
干净
50g/L 的盐酸 25秒 清水冲洗
酒精溶液
干净
吹干
清水冲洗 30秒 50g/L 的氢氧
况确定;常啮合齿轮1-5级,换档齿轮1-4级。
碳化物评级图
钢件渗碳金相检验
抛光态下的内氧化
腐蚀态下的内氧化
钢件渗碳金相检验
• 非马氏体组织:渗碳淬火件表面层中经常出现连续或不连续的 网状或块状黑色组织,主要由于内氧化而贫合金化元素导致形 成屈氏体类组织,一般规定不超过0.02mm.
• 减少非马氏体组织的措施: • 1)尽可能用低碳烃和高纯度气体做制备渗碳气体的原料气; • 2)尽可能选用含Cr、Ti、V、B元素的钢; • 3)从工艺和设备上采取措施,保证炉气不受空气污染; • 4)尽可能采用快速的淬火冷却介质和冷却方式。
钢件渗碳金相检验
钢件渗碳金相检验
钢件渗碳金相检验
• 适用于渗碳淬硬层有效深度大于0.3mm的汽车齿轮。 • 放大倍数:400X • 检验部位: 同芯部硬度 • 铁素体:1-3级
金相法测量渗碳(碳氮共渗)齿轮的有效硬化层深度
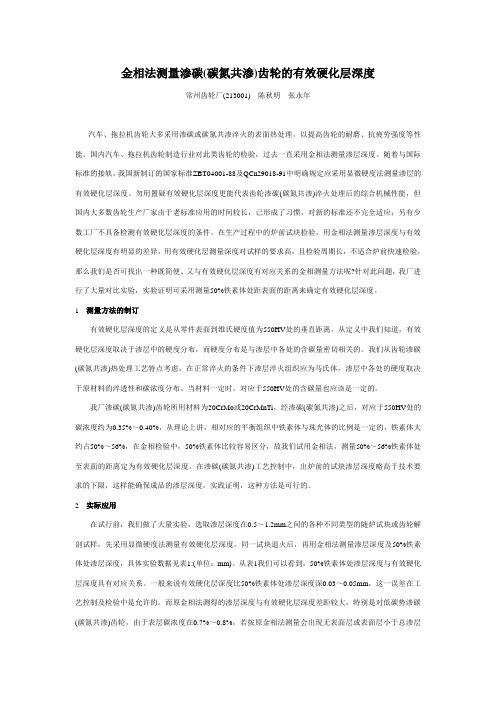
金相法测量渗碳(碳氮共渗)齿轮的有效硬化层深度常州齿轮厂(213001)陈秋明张永年汽车、拖拉机齿轮大多采用渗碳或碳氮共渗淬火的表面热处理,以提高齿轮的耐磨、抗疲劳强度等性能。
国内汽车、拖拉机齿轮制造行业对此类齿轮的检验,过去一直采用金相法测量渗层深度。
随着与国际标准的接轨,我国新制订的国家标准ZBT04001-88及QCn29018-91中明确规定应采用显微硬度法测量渗层的有效硬化层深度。
勿用置疑有效硬化层深度更能代表齿轮渗碳(碳氮共渗)淬火处理后的综合机械性能,但国内大多数齿轮生产厂家由于老标准应用的时间较长,已形成了习惯,对新的标准还不完全适应;另有少数工厂不具备检测有效硬化层深度的条件。
在生产过程中的炉前试块检验,用金相法测量渗层深度与有效硬化层深度有明显的差异,用有效硬化层测量深度对试样的要求高,且检验周期长,不适合炉前快速检验,那么我们是否可找出一种既简便、又与有效硬化层深度有对应关系的金相测量方法呢?针对此问题,我厂进行了大量对比实验,实验证明可采用测量50%铁素体处距表面的距离来确定有效硬化层深度。
1测量方法的制订有效硬化层深度的定义是从零件表面到维氏硬度值为550HV处的垂直距离。
从定义中我们知道,有效硬化层深度取决于渗层中的硬度分布,而硬度分布是与渗层中各处的含碳量密切相关的。
我们从齿轮渗碳(碳氮共渗)热处理工艺特点考虑,在正常淬火的条件下渗层淬火组织应为马氏体,渗层中各处的硬度取决于原材料的淬透性和碳浓度分布。
当材料一定时,对应于550HV处的含碳量也应该是一定的。
我厂渗碳(碳氮共渗)齿轮所用材料为20CrMo或20CrMnTi,经渗碳(碳氮共渗)之后,对应于550HV处的碳浓度约为0.35%~0.40%,从理论上讲,相对应的平衡组织中铁素体与珠光体的比例是一定的,铁素体大约占50%~56%,在金相检验中,50%铁素体比较容易区分,故我们试用金相法,测量50%~56%铁素体处至表面的距离定为有效硬化层深度。
谈齿轮渗碳淬火有效硬化层及硬度梯度

浅谈齿轮渗碳淬火有效硬化层及硬度梯度随着机械工业的发展,对齿轮的质量要求日益提高,而齿轮的强度寿命和制造精度与热处理质量有很大关系。
为了检验齿轮材料热处理质量,在1987年以前,我国的齿轮渗碳淬火内在质量检验标准多为终态金相检验标准。
由于检测仪器的精度、分辨率等因素以及检验人员的经验参差不齐,造成检验结果有很大差异和争议。
为了解决金相法内在检验存在的弊端,机械部在1987年借鉴了DIN.ISO等标准中有关内容,修订了我国现行齿轮渗碳淬火内在质量检验标准。
此检验标准中,其金相组织检验标准基本与原标准相似,主要是对渗碳层深度及碳浓度梯度的测定作了较大的修改。
下面就渗碳层深度和碳浓度梯度分别采用金相法与硬度法测定进行简述。
一、渗碳层深度的检测1.1、金相法1.1.1、取本体或与零件材料成分相同,预先热处理状态基本相似的圆试样或齿形试样进行检测。
1.1.2、送检试样热处理状态为平衡状态,即退火状态。
1.1.3、低碳钢渗层深度为:过共析层+共析层+1/2亚共析层。
1.1.4、低碳合金钢渗层深度为:过共析层+共析层+亚共析层。
1.2、硬度法1.2.1、取样方法同金相法取样方法一致。
1.2.2、送检试样状态为淬火+回火状态。
1.2.3、渗碳深度用有效硬化层来表示,其极限硬度根据不同要求进行选择。
1.2.4、有效硬化层深度(DCp):从试样表面测至极限硬度(如HV550)之间垂直距离。
1.3、两种关于渗碳深度检测的方法存在着一定的对应关系,下面用图形来描述。
从图中可看出:DCp(芯部)>DCp(HV500)>DCp(HV550)DCp(HV550)对应渗碳层中碳含量约为0.35~0.38%,此界限处即为金相法中1/2亚共析层处。
DCp(HV500)对应渗碳层中碳含量约为0.31~0.33%,此界限处为金相法中1/2亚共析层处。
DCp(芯部)对应渗碳层中碳含量为基体碳含量,一般为0.17~0.23%,此界限处为金相法中基体组织。
齿轮渗碳厚度范围
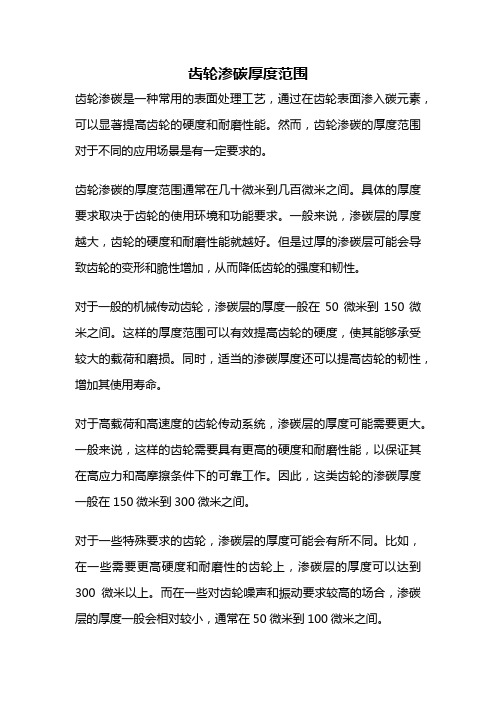
齿轮渗碳厚度范围
齿轮渗碳是一种常用的表面处理工艺,通过在齿轮表面渗入碳元素,可以显著提高齿轮的硬度和耐磨性能。
然而,齿轮渗碳的厚度范围对于不同的应用场景是有一定要求的。
齿轮渗碳的厚度范围通常在几十微米到几百微米之间。
具体的厚度要求取决于齿轮的使用环境和功能要求。
一般来说,渗碳层的厚度越大,齿轮的硬度和耐磨性能就越好。
但是过厚的渗碳层可能会导致齿轮的变形和脆性增加,从而降低齿轮的强度和韧性。
对于一般的机械传动齿轮,渗碳层的厚度一般在50微米到150微米之间。
这样的厚度范围可以有效提高齿轮的硬度,使其能够承受较大的载荷和磨损。
同时,适当的渗碳厚度还可以提高齿轮的韧性,增加其使用寿命。
对于高载荷和高速度的齿轮传动系统,渗碳层的厚度可能需要更大。
一般来说,这样的齿轮需要具有更高的硬度和耐磨性能,以保证其在高应力和高摩擦条件下的可靠工作。
因此,这类齿轮的渗碳厚度一般在150微米到300微米之间。
对于一些特殊要求的齿轮,渗碳层的厚度可能会有所不同。
比如,在一些需要更高硬度和耐磨性的齿轮上,渗碳层的厚度可以达到300微米以上。
而在一些对齿轮噪声和振动要求较高的场合,渗碳层的厚度一般会相对较小,通常在50微米到100微米之间。
齿轮渗碳的厚度范围是根据齿轮的使用环境和功能要求来确定的。
在实际应用中,需要根据具体情况选择合适的渗碳厚度,以保证齿轮的性能和可靠性。
同时,在进行齿轮渗碳处理时,还需要注意控制渗碳的工艺参数,以确保渗碳层的均匀性和一致性,从而提高齿轮的质量和使用寿命。
渗碳淬火硬化层深度检测标准

渗碳淬火硬化层深度检测标准渗碳淬火是一种常用的表面处理方法,用于提高金属材料的硬度和耐磨性。
在渗碳淬火过程中,碳原子会渗透到金属表面,并与金属原子结合形成碳化物,从而形成硬化层。
硬化层的深度是评估渗碳淬火质量的重要指标之一。
渗碳淬火硬化层深度的检测标准主要有以下几种方法:1. 金相显微镜观察法:这是一种常用的检测方法,通过金相显微镜观察样品的横截面,可以清晰地看到硬化层的深度。
通常,硬化层的深度应符合相关标准要求。
2. 显微硬度计测量法:显微硬度计是一种常用的硬度测试仪器,可以测量材料的硬度。
通过在硬化层上进行一系列硬度测试,可以确定硬化层的深度。
通常,硬化层的深度应达到一定的数值范围。
3. 金相腐蚀法:金相腐蚀是一种将试样浸泡在特定腐蚀液中,以观察和测量试样表面的腐蚀情况的方法。
通过在硬化层上进行金相腐蚀实验,可以确定硬化层的深度。
通常,硬化层的深度应达到一定的腐蚀程度。
4. 电子显微镜观察法:电子显微镜是一种高分辨率的显微镜,可以观察到非常细小的结构。
通过在硬化层上使用电子显微镜观察,可以清晰地看到硬化层的深度。
通常,硬化层的深度应达到一定的微米级别。
以上是常用的渗碳淬火硬化层深度检测标准方法。
在实际应用中,可以根据具体情况选择合适的检测方法。
同时,还需要注意以下几点:1. 检测设备的准确性和精度:选择合适的检测设备,并确保其准确性和精度。
只有准确的检测结果才能有效评估渗碳淬火的质量。
2. 标准要求的合理性:检测标准应该合理,符合实际应用需求。
标准要求过高或过低都会影响渗碳淬火的质量评估。
3. 检测结果的可靠性:在进行检测时,需要保证样品的代表性和一致性。
只有可靠的检测结果才能准确评估渗碳淬火的质量。
总之,渗碳淬火硬化层深度的检测标准是评估渗碳淬火质量的重要指标之一。
通过选择合适的检测方法,并注意检测设备的准确性和精度,以及标准要求的合理性和检测结果的可靠性,可以有效评估渗碳淬火的质量。
这对于提高金属材料的硬度和耐磨性具有重要意义。
齿轮轴渗碳热处理工艺研究

齿轮轴渗碳热处理工艺研究电圆锯主要用于切割钢件,渗碳齿形轴是电圆锯中的重要零件。
由于渗碳齿轮轴在工作中需承受转矩、冲击及磨损,因此要求具有较高的硬度、耐磨性和疲劳强度极限,一般采用低碳合金钢制造。
经实际验证,20CrMnTi材料热处理性能优于20CrMo,但存在着变形现象,为此进行分析变形产生的根本原因,并采取控制措施,为解决其它渗碳淬火零件的变形提供参考。
1 材料选用电圆锯齿轮轴最初选用20CrMo材料,技术要求为表面硬度HV(10)680~820,有效硬化层深0.2~0.5。
实际经热处理加工后表层至芯部过渡区及芯部硬度偏低,检测芯部硬度为296HV(1),低于JB/T7516—1994标准规定的心部硬度值为30—45HRC要求。
用户经耐久试验测试,轮齿有早期磨损现象,齿面呈剥落状裂纹。
分析认为心部硬度低是由于心部未淬透,心部组织中铁素体量太多,使得表面渗碳硬化层与心部的过渡区太陡。
在高的交变应力作用下,表面与心部交界处产生裂纹,逐渐扩展,容易产生深层剥落现象。
因此20CrMo材料渗碳淬火处理无法满足性能要求。
为改进淬透性,材料变更为20CrMnTi,热处理工艺采用原20CrMo材料使用的工艺。
经实际热处理加工后验证各项指标均符合要求。
总体反映20CrMnTi 材料热处理性能优于20CrMo。
2 变形形式及原因2.1 变形形式渗碳齿轮轴的热处理指标均合格,但在啮合检测时径向综合总偏差Fi″严重超差,结合齿圈径向跳动Fr检测得出:热处理过程存在严重变形,通过100件试验件热处理前后数据收集的状态分析,其变化趋势无规律可循。
2.2 原因分析渗碳齿轮轴经渗碳淬火后的变形是齿轮在热处理过程中产生的,但变形产生的根本原因,主要取决于材料、形状及整个工艺过程的质量。
因此要控制好热处理变形,不仅要在热处理时控制,而且要在齿轮的结构设计、材料的选用以及热前热后的制造过程都需要采取有效措施才能较理想的控制齿轮轴变形。
浅谈齿轮渗碳淬火有效硬化层及硬度梯度

浅谈齿轮渗碳淬火有效硬化层及硬度梯度随着机械工业的发展,对齿轮的质量要求日益提高,而齿轮的强度寿命和制造精度与热处理质量有很大关系。
为了检验齿轮材料热处理质量,在1987年以前,我国的齿轮渗碳淬火内在质量检验标准多为终态金相检验标准。
由于检测仪器的精度、分辨率等因素以及检验人员的经验参差不齐,造成检验结果有很大差异和争议。
为了解决金相法内在检验存在的弊端,机械部在1987年借鉴了DIN.ISO等标准中有关内容,修订了我国现行齿轮渗碳淬火内在质量检验标准。
此检验标准中,其金相组织检验标准基本与原标准相似,主要是对渗碳层深度及碳浓度梯度的测定作了较大的修改。
下面就渗碳层深度和碳浓度梯度分别采用金相法与硬度法测定进行简述。
一、渗碳层深度的检测1.1、金相法1.1.1、取本体或与零件材料成分相同,预先热处理状态基本相似的圆试样或齿形试样进行检测。
1.1.2、送检试样热处理状态为平衡状态,即退火状态。
1.1.3、低碳钢渗层深度为:过共析层+共析层+1/2亚共析层。
1.1.4、低碳合金钢渗层深度为:过共析层+共析层+亚共析层。
1.2、硬度法1.2.1、取样方法同金相法取样方法一致。
1.2.2、送检试样状态为淬火+回火状态。
1.2.3、渗碳深度用有效硬化层来表示,其极限硬度根据不同要求进行选择。
1.2.4、有效硬化层深度(DCp):从试样表面测至极限硬度(如HV550)之间垂直距离。
1.3、两种关于渗碳深度检测的方法存在着一定的对应关系,下面用图形来描述。
从图中可看出:DCp(芯部)>DCp(HV500)>DCp(HV550)DCp(HV550)对应渗碳层中碳含量约为0.35~0.38%,此界限处即为金相法中1/2亚共析层处。
DCp(HV500)对应渗碳层中碳含量约为0.31~0.33%,此界限处为金相法中1/2亚共析层处。
DCp(芯部)对应渗碳层中碳含量为基体碳含量,一般为0.17~0.23%,此界限处为金相法中基体组织。
渗碳齿轮最佳有效硬化层深度

齿轮淬火深度

图片:齿轮淬火的“最佳”硬化层深与“适当”硬化层深戴忠森众所周知,齿轮的淬硬层深“过浅”,对接触和弯曲承载能力都不利。
但淬硬层也不是越深越好,最佳或适当的硬化层深度,可使齿面和齿根都具有较高的强度(承载能力)。
另外,不同的热处理方法,其“最佳”值也不是一样的。
二十世纪七、八十年代,随着齿轮强度计算方法ISO标准的公布,以及国内GB/3480“圆柱齿轮承载能力计算方法”标准的实施,特别是工业硬齿面齿轮的广泛采用,国内外齿轮工作者(专家、学者),就热处理硬化层深问题,进行了大量的试验研究和理论分析。
其实质都是基于接触(弯曲)疲劳强度,其核心问题是:疲劳裂纹发生(萌生)在何处?破坏后的形状是点蚀(pitting贝壳状),还是片蚀(剥落spalling)?研究表明,一般软齿面大多是点蚀,而硬齿面大齿轮大多是剥落(片蚀)。
疲劳裂纹的萌生,有可能在表面,也有可能在表层。
至今,有关硬齿面齿轮接触疲劳强度(剥落)计算的理论和方法,主要有:最大剪切应力τmax (τ45°);正交剪切应力(τyz);当量剪切应力(τeffa);深部接触应力;最大剪切应力/剪切强度的峰值;正交剪切应力/强度(硬度)(τyz/HV)max;当量剪切应力/强度的峰值等,通过理论计算可以确定接触疲劳强度(安全系数);或者确定最佳淬硬层深度。
这些理论和方法一直都有争议,因此至今也没有一个权威的理论和方法被大家所能完全接受。
所谓“最佳硬化层深”,其说法也是较含糊的,而且众说不一,以渗碳淬火齿轮为例,德国DIN3990,硬化(渗碳)层深度,给出一个经验公式:(推荐)Eht= 0.15mn(mn——法面模数)(1)。
该经验公式,有一个突出的问题,就是未考虑实际载荷的情况。
所以,对于轻载齿轮,允许比经验公式稍浅的硬化层深度。
Thomas Tobie近年来提出在用ISO/DIN 进行标准化承载能力计算时,考虑硬化层深度对承载能力的影响,引入了影响系数ZEht(接触承载能力影响系数);УEht(弯曲承载能力影响系数)。
渗碳齿轮最佳有效硬化层深度
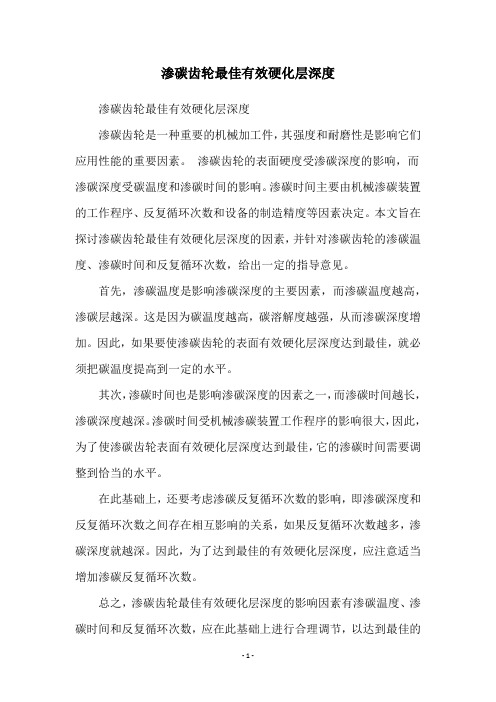
渗碳齿轮最佳有效硬化层深度
渗碳齿轮最佳有效硬化层深度
渗碳齿轮是一种重要的机械加工件,其强度和耐磨性是影响它们应用性能的重要因素。
渗碳齿轮的表面硬度受渗碳深度的影响,而渗碳深度受碳温度和渗碳时间的影响。
渗碳时间主要由机械渗碳装置的工作程序、反复循环次数和设备的制造精度等因素决定。
本文旨在探讨渗碳齿轮最佳有效硬化层深度的因素,并针对渗碳齿轮的渗碳温度、渗碳时间和反复循环次数,给出一定的指导意见。
首先,渗碳温度是影响渗碳深度的主要因素,而渗碳温度越高,渗碳层越深。
这是因为碳温度越高,碳溶解度越强,从而渗碳深度增加。
因此,如果要使渗碳齿轮的表面有效硬化层深度达到最佳,就必须把碳温度提高到一定的水平。
其次,渗碳时间也是影响渗碳深度的因素之一,而渗碳时间越长,渗碳深度越深。
渗碳时间受机械渗碳装置工作程序的影响很大,因此,为了使渗碳齿轮表面有效硬化层深度达到最佳,它的渗碳时间需要调整到恰当的水平。
在此基础上,还要考虑渗碳反复循环次数的影响,即渗碳深度和反复循环次数之间存在相互影响的关系,如果反复循环次数越多,渗碳深度就越深。
因此,为了达到最佳的有效硬化层深度,应注意适当增加渗碳反复循环次数。
总之,渗碳齿轮最佳有效硬化层深度的影响因素有渗碳温度、渗碳时间和反复循环次数,应在此基础上进行合理调节,以达到最佳的
有效硬化层深度。
硬化层深度测定
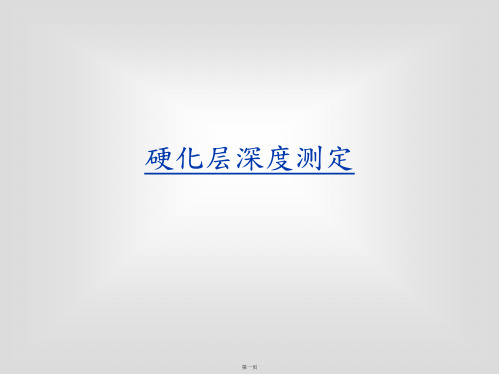
第十八页
钢的脱碳层深度测定及表示方法
定义:
1.脱碳层:钢料经加热或热处理后,表层含碳量减少的部份. 2.全脱碳层深度:从脱碳层表面到脱碳层心部的物理与化学性质的差异, 以无法区別的位置为止的深度. 3.肥粒铁脱碳层深度:自表层到脱碳层完全肥粒铁的深度. 4.实用脱碳层深度:自表层到实用上容许的硬度处的深度. 5.特定残脱碳率脱碳层深度:自脱碳层表面到某一定的残碳率(残留含碳量 与无脱碳处的含碳量的比率).
ND-HMV△-T
ND-HMK△-T
巨视腐蚀 试验法
ND-M-T
实用氮化层深度 ND-HMV△-P
ND-HMK△-P
﹡
氮化层深度及实用氮化层深度的表示方法:
1.1-氮化层深度及实用氮化层深度,单位以mm表示,取至小数点以下第二位. 1.2-氮化层深度较浅时,也可使用µm表示,但须于数字尾端加上单位.
第十六页
表示方法
例1. ND-HMV0.3-T0.38
表示以微小维克氏硬度试验法测定,试验荷重为0.3kgf,全氮化层深
度0.38mm
例2. ND-HMV0.5-P0.25 表示以微小维克氏硬度试验法测定,试验荷重为0.5kgf,实用氮化层
深度0.25mm
例3. ND-HMK0.1-T0.45 表示以微小诺普氏硬度试验法测定,试验荷重为0.1kgf,实用氮化层深度
约订单标准执行.或经本厂建议及双方共同研讨且必须经 客户同意的协调内容,订为标准合约。
2.全硬化层深度: 判別硬化层表面与心部基地,物理与化学性质的差异,区別其 位置地距离。
第二页
示意图
表 面
1.5MM
L1 L2 L3 L4 L5 L6
注:L n ﹢1- L n ≦ 0.1mm
表面热处理零件有效硬化层、渗层等的有关说明

表面热处理零件有效硬化层、渗层等的有关说明一、常用热处理零件硬化层深度、渗层深度有关术语、定义、代号和适用范围及检测方法1附注:①特殊情况下,经有关方协议,也可采用 4.903N~49.03N(0.5kgf~5kgf)内的某一试验力和其他值的极限硬度值,在特殊情况下要注明,如Dc49.03/515=0.6表示采用试验力49.03N(5kgf),极限硬度值为515HV时的有效硬化层深度等于0.6mm;②特殊情况下,经有关方协议,也可采用4.903N~49.03N(0.5kgf~5kgf)内的某一试验力和其他值的极限硬度值,在特殊情况下要注明,如Ds4.903/0.9=0.6表示采用试验力4.903N(0.5kgf),极限硬度值等于零件表面所要求的最低硬度的0.9倍时的有效硬化层深度等于0.6mm;③测量方法有显微组织测量法和显微硬度测量法,选择的测量方法和它的精度取决于硬化层的性质和估计的深度。
由于测量方法也影响到测量结果,因此选择哪种方法测量及何种试样形式,必须在图纸和工艺上预先规定;④当工艺/图纸没有规定测量方法时,优先采用显微硬度法。
用显微硬度测量法检测时,一般试验力用1.96N(0.2kgf)的界线显微硬度为基体硬度加30HV,除非工艺/图纸另有规定;⑤试验力为0.9807N(0.1kgf)(HV0.1),极限硬度值HG一般规定为基体硬度加30HV。
特殊情况下,经有关方协议,也可采用2其他试验力的显微硬度和极限硬度值;⑥试验力为0.9807(0.1kgf)(HV0.1),特殊情况下,经有关方协议,也可采用其他试验力的显微硬度和极限硬度值;⑦测量方法有硬度法和金相法两种,采用哪种测量方法应预先规定。
硬度法规定采用试验力为2.94N(0.3kgf)的维氏硬度,从试样表面测至比基体硬度高50HV处的垂直距离为渗氮层深度,对于渗氮层硬度变化很平缓的钢件(如碳钢、低碳低合金钢制件)可从试样表面沿垂直方向测至比基体维氏硬度值高30HV处。
汽车齿轮渗碳标准

汽车齿轮渗碳标准中华人民共和国专业标准QC/T 262—1999代替ZB T04 001—88汽车渗碳齿轮金相检验1 主题内容与适用范围1.1 本标准规定了汽车钢制渗碳齿轮金相组织,渗碳层有效层深度的含义及检测方法。
1.2 适用于渗碳淬硬层有效深度大于0.3mm的汽车齿轮。
1.3 用于齿轮在完成所有热处理工序后的质量检查。
2 引用标准GB××××钢件渗碳淬硬层有效深度的测定GB××××齿轮材料热处理后质量检查的一般规定3 术语3.1 表面硬度齿宽中部节圆附近表面的硬度。
3.2 心部硬度在齿宽中部横截面上,轮齿中心线与齿根圆相交处的硬度(见示意图)。
3.3 渗碳淬硬层有效深度从轮齿表面起,在9.81N(1kgf)载荷下测至550HV,也可在49.03N(5kgf)载荷下测至513HV处的垂直距离。
4 试样要求4.1 在制备试样时,不得有因受热而导致组织改变的现象。
4.2 测定渗碳淬硬层有效深度时,被测表面应与硬度机的载物台平行。
5 技术要求5.1 渗碳淬硬层有效深度,由产品图样规定,测试方法按GB××××《钢件渗碳淬硬层有效深度的测定》的规定。
至心部硬度降按GB××××《钢件渗碳淬硬层有效深度的测定》的规定。
5.2 面层含碳量按GB××××《钢件渗碳淬硬层有效深度的测定》的规定。
5.3 碳化物在放大400倍下检查,检查部位以齿顶角及工作面为准,按本标准中碳化物级别图评定。
常啮合齿轮1~5级合格,换档齿轮1~4级合格。
5.4 残余奥氏体及马氏体在放大400倍下检查,检查部位以节圆附近表面及齿根处为准。
按本标准中残余奥氏体马氏体级别图分别评定,1~5级合格。
5.5 表面硬度为HRC~63,心部硬度由产品图样规定。
渗碳齿轮齿根部的硬化层深度分析

3 试验结果分析
齿顶、齿根与 节 圆 硬 化 层 误 差 主 要 产 生 在 渗 碳 和 淬火冷却两个环节,齿顶、齿根硬化层深度与节圆硬化 层深度的偏差百分比见表Байду номын сангаас3。
齿顶硬化层深度偏差百分比齿顶硬化层深度节圆硬化层深度节圆硬化层深度100齿根硬化层深度偏差百分比齿根硬化层深度节圆硬化层深度节圆硬化层深度100齿根和渗碳气氛接触的面积小于扩散路径上的面积而节圆和渗碳气氛接触的面积大于扩散路径上的面积在相同的吸碳面积下齿根处渗碳层的碳浓度低于节圆处的碳浓度在淬火冷却时齿根处和淬火介质接触的面积小于热量传递路径上的面积而节圆处和淬火介质接触的面积大于热量传递路径上的面积在表面换热系数相同的条件下齿根冷却慢节圆冷却快
齿轮渗碳 时 ,除 了 齿 顶 面 的 渗 碳 扩 散 外 ,渐 开 线 齿面也在渗碳扩散,齿顶的渗碳层碳浓度是齿顶和齿 面两个面渗碳扩散的叠加( 图 5) ,再加上齿顶部位在 淬火冷却时冷却速度最快,因此渗碳淬火后齿顶部位 的硬化层深度较深,从表 3 结果可以看出齿顶硬化层 深度比节圆高 12. 9% ~ 21. 0% 。
( a) tooth profile sample; ( b) gear sample
2. 2 硬化层深度 试样渗碳淬火后的硬化层深度见表 1。由表 1 可
以看出,齿顶的硬化层深度最深,齿根最浅; 但齿轮试
第4 期
黎丽君: 渗碳齿轮齿根部的硬化层深度分析
97
样由于质量大,淬火冷却时受淬透性限制,心部硬度较 低,齿根的硬化层深度较浅。
表 1 4820H 钢试样渗碳淬火、回火后的硬化层深度 Table 1 Hardening case depth of the 4820H steel samples after
渗碳淬火齿轮有效硬化层深
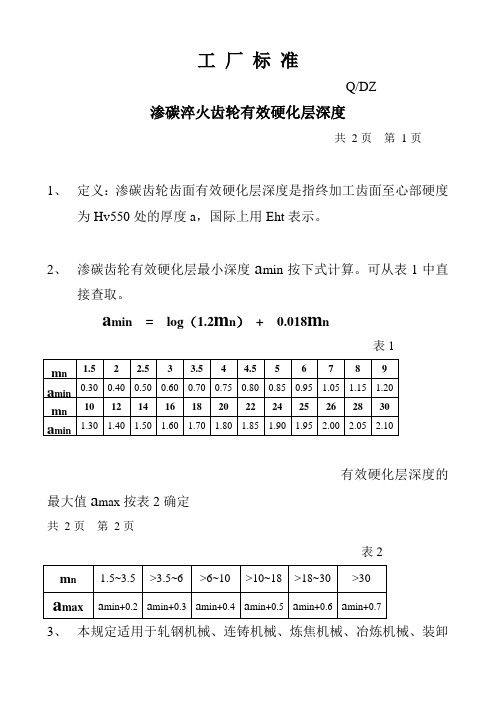
工厂标准
Q/DZ
渗碳淬火齿轮有效硬化层深度
共2页第1页
1、定义:渗碳齿轮齿面有效硬化层深度是指终加工齿面至心部硬度
为Hv550处的厚度a,国际上用Eht表示。
2、渗碳齿轮有效硬化层最小深度a min按下式计算。
可从表1中直
接查取。
a min= log(1.2m n)+ 0.018m n
表1
有效硬化层深度的
最大值a max按表2确定
共2页第2页
表2
3、本规定适用于轧钢机械、连铸机械、炼焦机械、冶炼机械、装卸
机械的传动齿轮。
4、特殊工况用渗碳齿轮的有效硬化层深度,可根据接触剪应力的大
小另行确定。
6.、本表对于Mn≤8的齿轮而言,其推荐的渗碳深度是合理的,但对于Mn>8的齿轮而言,其数据缺乏合理性。
7. 对于合理的渗碳层深度各国、各公司的标准不同,而且差距还比较大。
各国及各行业推荐的渗碳层深度见表3
表3 各国及各行业推荐的渗碳层深度
注:根据JB/T 8853-2001《圆柱齿轮减速机》渗碳层的深度根据模数选择,当Mn=1.5~6时,渗碳层深度ht=(0.2~0.3)Mn;
当Mn=7~18时,渗碳层的深度ht=(0.15~0.25)Mn(小模数取大值,大模数取小值)。