第七章_内轮廓加工
项目三内轮廓的加工

3.内圆锥的检测方法
图3.18 内圆锥加工的轨迹示意图
任务实施 ◆ 工艺分析
1.零件几何特点
零件加工面主要为端面、内台阶、内 圆锥面和倒角。 尺寸如图3.17所示,棒料伸出卡盘长 度为10mm。
2.选择工具、量具和刀具
(1)工具选择。 (2)量具选择。 (3)刀具选择。 (4)粗、精车内圆锥面至尺寸。
4.常见的内圆检测方法
可采用内卡钳、游标卡尺、塞规和内 径百分表检测内圆,如图3.13所示。
图3.13 内圆的检测方法
用内径表测量时,要注意以下两方面。
(1)长指针和短指针应结合观察, 以防指针多转一圈。 (2)短指针位置基本符合,长指针 转动至“零”位线附近时,应防止 “+”、“−”数值搞错。
3.程序模拟加工 4.自动加工及尺寸控制
◆ 检测评分 零件加工结束后,检测结果按表3.5要 求填写。
◆ 任务反馈
(1)装夹钻头时,钻头轴心线和工 件轴心线要一致,否则钻头容易折断。 (2)在装夹钻头锪锥形套前,必须 把钻头锥柄、尾座套筒和锥形套擦拭 干净。否则会由于锥面接触不好,使 钻头在尾座锥孔内打滑旋转。
4.切削用量选择
内圆的加工工艺分析如表3.1所示。
◆ 加工操作
1.加工准备
(1)检查毛坯尺寸。 (2)开机、回参考点。 (3)装夹工件和刀具。 (4)程序输入。
2.对刀
(1)X方向对刀。 (2)Z方向对刀。
图3.15 内圆车刀对刀示意图
3.程序模拟加工 4.自动加工及尺寸控制
◆ 检测评分 零件加工结束后,检测结果按表3.2要 求填写。
图3.23 主偏角不同内圆弧面加工刀具示意图
2.内圆弧加工工艺设计技巧
图3.24 内腔轴向进刀加工示意图
内轮廓零件加工资料

教学
过程
1、通孔车刀
为了减小径向切削力,防止振动,通孔车刀的主偏角一般为60—75度,副偏角为15—30度。
为了防止内孔车刀后刀面和孔壁摩擦又不使后角磨
得太大,一般磨成两个后角。
2、、盲孔车刀
盲孔车刀是用来车盲孔或台阶孔的,主偏角为90—93度,刀尖在刀杆最
前端,刀尖与刀杆外端的距离小于内孔半径。
结合学生普车实习过程讲解
教学过程工艺分析与安排
内孔加工工艺与外轮廓加工基本相同,分析零件图纸—确定装甲方案
---确定加工顺序与走刀路线----刀具选择---确定切削用量---编制加工
程序
为了增加车削刚醒,防止产生振动,要尽量选择粗的刀杆,装夹时刀
杆伸出长度尽可能短,只要略大于孔深即可。
刀尖要对准工件中心,刀杆
与轴心线平行。
为了确保安全,可在车孔前,先用内孔刀在孔内试走一遍。
精车内孔时,应保持刀刃锋利,否则容易产生让刀,把孔车程锥形。
内孔加工质量分析
1、内孔尺寸精度超差:
主要由于没有仔细测量或测量方法有误造成。
2、孔有锥度:
可能是由于切削用量选择不当,车刀磨损,刀刃不够锋利,刀杆刚性
差而产生让刀等原因造成,车床主轴轴线歪斜,床身导轨严重磨损也是造
成所加工孔有锥度的原因。
3、孔表面粗糙度超差:
可能是由于切削用量选择不当,产生积屑瘤;或车刀磨损,刀刃不够
结合
学生
普车
实习
过程
讲解。
单元07内轮廓铣削加工零件的工艺分析.doc

单元04外轮廓铣削加工零件的工艺分析一、加工任务引入编写如图1所示外轮廓零件的加工程序,并在数控铣床上进行加工。
毛坯为125mm×125mm×25 mm,材料为45钢,小批量生产。
图1内轮廓铣削加工任务图任务要求:1、零件图工艺分析2、装夹方案的确定3、加工顺序的确定4、刀具、量具的确定5、切削用量的确定6、工艺卡片的制定二、立铣刀的介绍1.数控铣床常用刀具材料常用的数控刀具材料有高速钢、硬质合金、涂层硬质合金、陶瓷、立方氮化硼、金刚石等.其中,高速钢、硬质合金和涂层硬质合金在数控铣削刀具中应用最广。
2。
常用轮廓铣削刀具常用轮廓铣削刀具主要有面铣刀、立铣刀、键槽铣刀、模具铣刀和成形铣刀等。
(1)面铣刀如图2所示,面铣刀的圆周表面和端面上都有切削刃,圆周表面的切削刃为主切削刃,端面上的切削刃为副切削刃。
面铣刀多为套式镶齿结构,刀齿为高速钢或硬质合金,刀体为40Cr。
刀片和刀齿与刀体的安装方式有整体焊接式、机夹焊接式和可转位式三种,其中可转位式是当前最常用的一种夹紧方式.根据面铣刀刀具型号的不同,面铣刀直径可取d=40~400mm,螺旋角β=10°,刀齿数取z=4~20。
图2 面铣刀(2)平底立铣刀如图3所示,立铣刀是数控机床上用得最多的一种铣刀。
立铣刀的圆柱表面和端面上都有切削刃,圆柱表面的切削刃为主切削刃,端面上的切削刃为副切削刃,它们可同时进行切削,也可单独进行切削。
主切削刃一般为螺旋齿,这样可以增加切削平稳性,提高加工精度。
由于普通立铣刀端面中心处无切削刃,所以立铣刀不能进行轴向进给,端面刃主要用来加工与侧面相垂直的底平面.图3 平底立铣刀图4 键槽铣刀(3)键槽铣刀如图4所示,键槽铣刀一般只有两个刀齿,圆柱面和端面都有切削刃,端面刃延伸至中心,既像立铣刀,又像钻头。
加工时先轴向进给达到槽深,然后沿键槽方向铣出键槽全长。
按国家标准规定,直柄键槽铣刀直径d=2~22mm,锥柄键槽铣刀直径d=14~50mm。
项目七 轮廓零件的加工
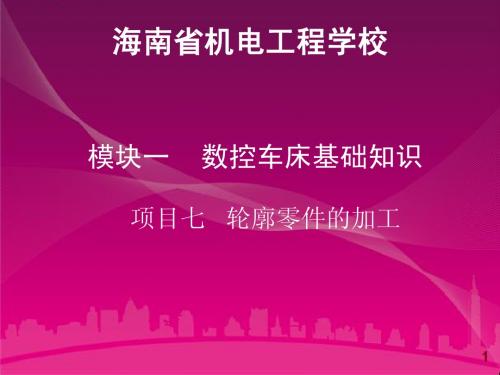
【任务实施】 4. 加工工艺 如表7-1所示
表7-1 加工工艺表 切削用量
工步号 1 2 工步内容 车端面 粗车外轮廓 刀具 T0101 T0101 刀 具 名 称 及 规 主轴转速 格 (r /min) 进给速度 (mm /min)
93° 外圆粗车
刀
93° 外圆粗车
刀
500
100
3
4
精车外轮廓
切断工件
【任务实施】 4. 加工工艺 如表7-3所示
表7-3 加工工艺表 切削用量 工步号 工步内容 刀具 刀具名称及规格 主轴转速 (r /min) 进给速度 ( mm /min )
1 2 3 4
车端面 粗车外轮廓 精车外轮廓 切断工件
T0101 T0101 T0202 T0303
93 ° 外 圆 粗 车
【任务实施】 4. 加工工艺 如表7-4所示
表7-4 加工工艺表 切削用量 工步号 工步内容 刀具 刀具名称及规格 主轴转速 (r /min) 1 2 3 车端面 粗车外轮廓 精车外轮廓 T0101 T0101 T0202 进给速度 (mm /min)
93 ° 外 圆 粗 车
刀
93 ° 外 圆 粗 车
【任务实施】 4. 加工工艺 如表7-2所示
表7-2 加工工艺表 切削用量 工步号 工步内容 刀具 刀具名称及规格
主轴转速 (r /min)
进给速度 ( mm /min )
1 2 3 4
车端面 粗车外轮廓 精车外轮廓 切断工件
T0101 T0101 T0202 T0303
93 ° 外 圆 粗 车
刀
93 ° 外 圆 粗 车
刀
500 1000 350
100 50 20
内轮廓加工
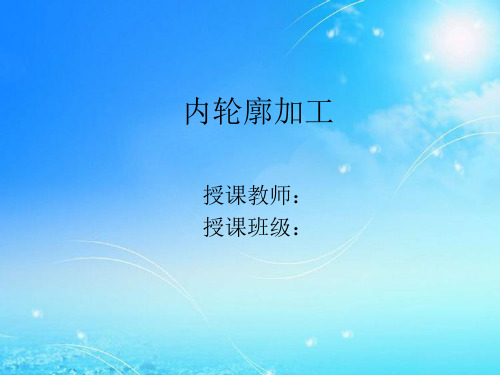
• (2)C点为粗车循环的起点。 • (3)在G71指令的程序段内,要指定精加工工件时程序 段的顺序号、精加工留量、粗加工的每次切深以及F、S 和T功能等。ns→nf程序段中的F、S、T功能,即使被指 定也对粗车循环无效。 • (4)零件轮廓必须符合X轴、Z轴方向同时单调增大或单 调减少。
内轮廓加工
授课教师: 授课班级:
复合固定循环指令
• • • • • • • • • • • • 外圆/内径粗切循环G71 编程格式: G71 U(△d) R(e) G71 P(ns) Q(nf) U(△u 说明:(1)程序段中各地址符的含义: △d-背吃刀量(切削深度),半径值,无正负号; e--退刀量,半径值; ns--精加工轮廓程序段中开始程序段的段号; nf--精加工轮廓程序段中结束程序段的段号; △u--X轴方向精加工余量,直径值; △w--Z轴方向精加工余量; f、s、t--F、S、T代码。
加工中心内轮廓加工编程PPT

Y D
B · ·
程序:
O0001;
G90G80G40;(程序初始化) G91G28Z0;(换刀点) M6T1;(键槽铣刀) M03S600M08;(主轴、冷却液) G54G90G0Z100;(坐标系安全) X0Y0;(检验)
X19.4; Z2; G1Z-18F50;(分层切削) G41D1Y-6F100(建刀补) G3X25.4Y0R6;(切入A) G3X23.36Y9.97R25.4;(B)
【引申】怎么用子程序呢
【旋转变换编程】 ☆子程序调用
【格式1】M98 P××××L××××; 示例: M98 P100 L5 ;表示调用O0100子程序5次 M98 P100;表示调用O0100子程序1次 【格式2】 M98 P××××(调用次数)××××(子程序号) 示例: M98 P50010;表示调用O0010子程序5次 M98 P5010;表示调用O5010子程序1次
·
·
B
D O
· E · · F G·
X
A ·
H·
·I
内轮廓编程
4、编程
C
A (25.4,0) B (23.36,9.97) C (18.02,11.35) D (10.37,3.66) E (9.46,1.07) F ((9.46,-1.07) G (10.37,-3.66) H (18.02,-11.35) I (23.36,-9.97)
O0111; G91G1Z-2F50; G90G41D1Y-6F100; G3X25.4Y0R6; ...... G3X25.4Y0R25.4; G3X19.4Y6R6; G1G40Y0; M99;
放仿真加工视频 学生进行仿真训练 学生实际制作零件
内轮廓零件加工2
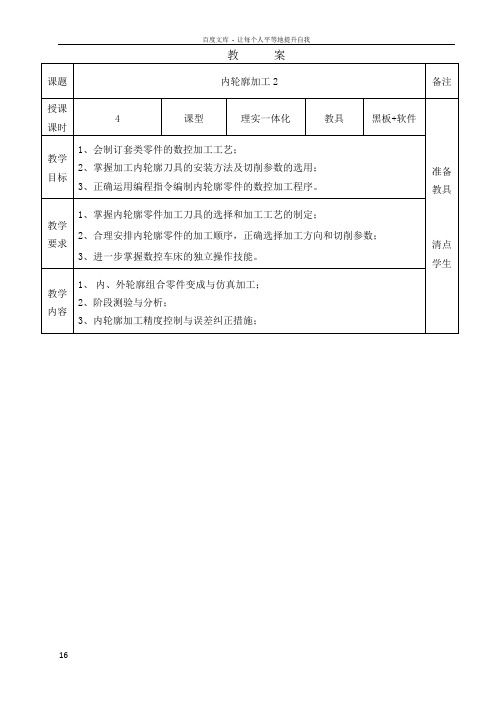
教学过程导入新课:在数控车床经常遇到套类零件的加工。
通过钻、铰、镗、扩等可以加工出不同精度的工件,其加工方法简单,加工精度也比普通机床要高,因此,镗孔、内沟槽和内三角螺纹是套类零件常见的加工要素。
一、内沟槽:1、内沟槽种类:退刀槽、密封槽、轴向定位槽、储油槽、油气通道槽等。
种类作用示图退刀槽车内螺纹、车孔和磨孔时作退刀用或为了拉油槽方便,两端开有退刀槽。
密封槽在T形槽中嵌入油毛毡,防止轴上的润滑剂溢出。
轴向定位槽在轴承座内孔中的适当位置开槽放人孔用弹性挡圈.以实现滚动轴承的轴向定位。
油气通道槽在各种液压和气压滑阀中开内沟槽以通油或通气这类沟槽要求有较高的轴向位置。
画图讲解教学过程2、内沟槽车刀内沟槽车刀与切断刀的几何形状相似,只是装夹方向相反,且在内孔中车槽。
加工小孔中的内沟槽车刀做成整体式内沟槽车刀,如图7-2和图7-3所示。
图7-2 图7-33、车内沟槽方法宽度较小和要求不高的内沟槽,可以用主切削刃宽度等于槽宽的内沟槽刀,采用直进法一次车出。
画图讲解较高或较宽的内沟槽,可采用直进法分几次车出。
粗车时,槽侧和槽底应留精车余量,然后根据槽宽、槽深要求进行精车。
深度浅、宽度大的内沟槽,可采用特殊角度的镗孔刀先车出内凹槽,再用内沟槽刀车出两侧面。
教学过程4、例如:毛坯为φ45mm×45mm的45钢,用FANUC 0i系统编程加工该零件。
一、工艺分析1. 夹毛坯φ45mm,伸出长度30mm,加工φ40mm外圆粗、精镗孔。
2. 加工内沟槽。
3. 调头夹φ40mm外圆,校正→孔口倒角,φ40mm加工至接刀处。
二、选择刀具及确定切削用量1. 刀具选择机夹内孔车刀和内沟槽刀,机夹内孔刀型号为S16R-PCLNR09,内沟槽刀型号为A16Q-CGER1303。
画图讲解+仿真演示教学过程2. 确定切削用量数控加工刀具及切削用量选三、程序编制画图讲解+仿真演示教学过程四、内沟槽加工误差分析二、内三角螺纹加工1、相关工艺知识:刀具选择:在数控车床上车削普通三角螺纹一般选用精密级机夹可转位不重磨螺纹车刀,使用时要根据螺纹的螺距选择刀片的型号。
数控铣床编程模块3 内轮廓零件加工

4 内轮廓加工工艺分析举例 (3)切入方法及切入点
切入点
4 内轮廓加工工艺分析举例
(4)Z形刀路间距值
型腔粗加工中的间距就是刀具切入材料的宽度。刀路间距通常为刀具直径的70%~ 90%左右,相邻两刀应有一定的重叠部分。
Y向以Z形刀路间距Q为单位进行N 次数进给,最终型腔粗加工区域被 切除,则有:Q×N=38-2×4=30
立铣刀斜线下刀
(1)深度方向刀具切入方法
方法三 斜线式进刀方式
①斜线下刀的角度
斜线下刀的刀轨与工件上表面的 夹角的极限(如右图所示)的计算公 式为:
arctan(h / d )
进一步考虑到斜线下刀为往返切削运 动下刀角度应调整为:
arctan(h / 2d)
(1)深度方向刀具切入方法
动,加速切削刃的磨损。
使
用 需 注
当刀具在一个连续的轮廓上切削时使用一次刀具半径补偿,
3
刀具在另一个连续的轮廓上切削时应重新使用一次刀具半 径补偿,以避免过切或留下多余的凸台。
意
的
问
题3 Biblioteka 腔铣削用量粗加工时,为了得到较高的切削效率,选择较大的
粗
切削用量,但刀具的切削深度与宽度应与加工条件 (机床、工件、装夹、刀具)相适应。
3 型腔铣削用量
精加工时,为了保证加工质量,就避免工艺系统
受力变形和减小震动,精加工切深应小,数控机床
精
的精加工余量可略小于普通机床,一般在深度、宽
加 工
度方向留0.2~0.5mm余量进行精加工。精加工时, 进给量大小主要受表面粗糙度要求限制,切削速度 大小主要取决于刀具耐用度。
4 内轮廓加工工艺分析举例
1 通用铣削夹具
内轮廓零件加工

2)常用的夬固式车刀3)內孔车刀的刀杆*:•內孔车刀的刀杆有圆刀杆和方刀杆.根据加工内孔 大小不同,有圖刀杆彌方刀杆1、 通孔车刀为了减小径向切削力,防止振动,通孔车刀的主偏角一般为60— 75度, 副偏角为15— 30度。
为了防止内孔车刀后刀面和孔壁摩擦又不使后角磨 得太大,一般磨成两个后角。
2、 、盲孔车刀盲孔车刀是用来车盲孔或台阶孔的,主偏角为 90— 93度,刀尖在刀杆最 前端,刀尖与刀杆外端的距离小于内孔半径。
教学过程结合 学生普车实习 过程 讲解工艺分析与安排内孔加工工艺与外轮廓加工基本相同,分析零件图纸一确定装甲方案---确定加工顺序与走刀路线----刀具选择---确定切削用量---编制加工程序为了增加车削刚醒,防止产生振动,要尽量选择粗的刀杆,装夹时刀杆伸出长度尽可能短,只要略大于孔深即可。
刀尖要对准工件中心,刀杆与轴心线平行。
为了确保安全,可在车孔前,先用内孔刀在孔内试走一遍。
精车内孔时,应保持刀刃锋利,否则容易产生让刀,把孔车程锥形。
内孔加工质量分析1、内孔尺寸精度超差:主要由于没有仔细测量或测量方法有误造成。
2、孔有锥度:可能是由于切削用量选择不当,车刀磨损,刀刃不够锋利,刀杆刚性差而产生让刀等原因造成,车床主轴轴线歪斜,床身导轨严重磨损也是造成所加工孔有锥度的原因。
3、孔表面粗糙度超差:可能是由于切削用量选择不当,产生积屑瘤;或车刀磨损,刀刃不够锋利,切削时刀杆振动造成。
结合学生普车实习过程讲解教学过程在数控车床上加工孔,无论是钻孔还是镗孔,都可以用G01来直接完成;而对于较深的孔,则最好采用深孔钻削循环指令G74来进行加工。
孔加工G01例1:如图1-54所示通孔,利用G01编制精加工程序。
70 -0-0530*03分析:分析控的类型特点,确定加工工艺与刀具00021 ;N10 G00 X150. Z100. T0101 N20 MO3 S400 ;N30 G00 X59.98 Z2.;N40 G01 Z0 F0.2 ;N50 X39.98 Z-29.99 F0.08 N60 Z-73. ;N70 G00 X35.;N80 Z2. ;N90 G00 X150. Z100.;N100 T0100 ;程序名程序起点,换1号镗刀主轴正转,转速为400r/min快速运动至程序起点靠近工件; 镗锥孔镗①40mm勺孔让刀退刀快速返回换刀点教学过程锥形通孔工件编程实例画图讲解取消刀补N110 M30 ;程序结束并返回程序开始例2:如图所示盲孔,毛坯内孔直径为①16mm,外圆已加工至合格尺寸,利用G01编制孔加工程序。
03课件-单元三——零件的内轮廓加工

程序号 公制单位设定\设定G54作为加工坐标 工作平面设定\取消半径补偿\取消长度补偿\取消
固定循环\绝对坐标设定 直线快速移动\主轴正转 Z轴直线快速移动至安全平面 \开启切削液 变量初始值 WHILE循环语句条件设置
建立半径补偿D01=4.5 轮廓起始
N130 G2 X30. Y-5. R5.; N132 G3 X5. Y-30. R25.; N134 G2 X-5. Y-30. R5.; N136 G3 X-12.322 Y-12.322 R25.;
(1)、分析图纸,指导制订加工工艺;
(2)、根据工艺编写加工程序;
(3)、指导工件、刀具的装夹、对刀和工件坐标系的 确定;
(4)、程序的输入、调试;
(5)、指导零件的检验,评价方法。
(1) 分析图纸,指导制订加工工艺;
根据内轮廓1的零件特点,外轮廓使用¢20平铣刀进行 加工,内轮廓使用¢8平铣刀进行加工。粗加工需要分 层铣削,并且在零件轮廓的周边及底面留有精加工余量 。精加工在提高切削进给速度的同时,根据实际测量值 确定精加工的刀具半径补偿。在刀具的切削过程中,注 意首切时降低刀具进给速度。
O0004; N100 G21 G54; N102 G17 G40 G49 G80 G90;
N104 G00 X0 Y0.S1000 M03; N106 Z20.; N108 M08; N110 #1=1; N112 WHILE [#1 LE 3] DO1; N114 G1 Z-#1 F150; N116 G42 G1 Y-13.74 F200 D1; N118 G02 X-12.322 Y-12.322 R10.; N120 G03 X-30. Y-5. R25.; N122 G02 X-30. Y5. R5.; N124 G3 X-5. Y30. R25.; N126 G2 X5. Y30. R5.; N128 G3 X30. Y5. R25.;
最新《数控车床编程与操作》精品课件 内轮廓仿真加工

任务二
二、内轮廓精加工实例
内轮廓精加工
单击菜单中的“ 数控车”菜单项,在 下拉菜单中选择“轮 廓精车”,如图1612所示。
图16-12 轮廓精车
任务二
内轮廓精加工
单击“轮廓精车”项,弹出 “精车参数表”对话框, 设置各参数内容。
(1)加工参数的设置。在“加工参数”选项卡中设置加工表面类型 为内轮廓;加工精度为0.01,切削行数为2,干涉前角(度)为10,加工 余量为0,切削行距为0.3,干涉后角(度)为10;最后一行加工次数为1; 拐角过渡方式为尖角;反向走刀为否;详细干涉检查为是;刀尖半径补 16-13所示。
任务一
内轮廓粗加工
图16-3 设置“加工参数”选项卡(粗车)
任务一
内轮廓粗加工
(2)进退刀方式的设置。在“进退刀方式”选项卡中设置每行相对 毛坯进刀方式为与加工表面成定角[长度l为1,角度A(度)为45];每行 相对加工表面进刀方式为与加工表面成定角[长度L为1,角度A(度)为 45];每行相对毛坯退刀方式为垂直;每行相对加工表面退刀方式为垂 直,快速退刀距离为2,如图16-4所示。 (3)切削用量的设置。在“切削用量”选项卡中设置进退刀时快速 走刀为是,进刀量为0.15,单位为mm/rev;主轴转速选项为恒转速,主 轴转速为500;样条拟合方式为圆弧拟合,拟合圆弧最大半径为 9 999 如图16-5所示。
任务二
内轮廓精加工
图16-13 设置“加工参数”选项卡(精车)
任务二
内轮廓精加工
(2)进退刀方式的设置。在“进退刀方式”选项卡中设置每行相对 加工表面进刀方式为与加工表面成定角(长度l为1,角度A(度)为45), 快速退刀距离为2;每行相对加工表面退刀方式为垂直,如图16-14所示。 (3)切削用量的设置。在“切削用量”选项卡中设置进退刀时快速 走刀为是,进刀量为 0.15,单位为mm/rev;主轴转速选项为恒转速,主 轴转速为800;样条拟合方式为圆弧拟合,拟合圆弧最大半径为9 999, 如图16-15所示。
第07章 轮廓

第七章轮廓表示把边缘连接起来就成为轮廓(contour).轮廓可以是断开的,也可以是封闭的.封闭轮廓对应于区域的边界,而区域内的像素可以通过填充算法来填满.断开的轮廓可能是区域边界的一部分,也可能是图像线条特征,如手写体笔画、图画中的线条等.区域之间的对比度太弱或边缘检测阈值设置太高都有可能产生间断的轮廓.轮廓可以用边缘序列表或曲线来表示.曲线通常称为轮廓的数学模型.曲线表示包括线段、二次曲线、三次样条曲线等.下面是几种轮廓表示的评价标准:高效:轮廓应该是一种简单和紧凑的表示.精确:轮廓应能精确地逼近图像特征.有效:轮廓应适合于后处理阶段的计算.轮廓表示的精确性由以下三个方面因素决定:①用于轮廓建模的曲线形式;②曲线拟合算法的性能;③边缘位置估计的精确度.轮廓的最简单表示形式是边缘有序表.这种表示的精确度就是边缘估计的精确度,但其表示的紧凑性是最差的,因此不是一种有效的后续图像分析表示方法.用适当的曲线模型来拟合边缘会提高精确度,这是因为曲线模型拟合边缘时往往具有均值化效应,因而可以减少边缘位置误差.曲线模型也会提高轮廓表示的经济性,为后处理提供了一种更适合、更紧凑的表示,例如,一条直线上的边缘集用一直线来拟合是表示这些边缘的最简单和最有效的方法,这一表示也简化了后续处理(如确定线的长度和方向);另外,由于估计直线与真实直线的均值方差小于真实直线与任何其它边缘之间的均值方差,因此可以说这种表示也增加了精确度.轮廓曲线拟合通常采用内插曲线或逼近曲线来实现.已知一组称为控制点的坐标点,内插是指一条曲线拟合这组控制点,使得曲线通过所有的控制点;逼近是指一条曲线拟合这组这组控制点,使得这条曲线非常接近这些控制点而无需一定通过这些点.在下面几节中,假定由边缘检测器得到的边缘十分准确,并使用内插值方法进行边缘曲线拟合.定义7.1边缘表是边缘点或边缘段的有序集合.定义7.2轮廓是边缘表或用于表示边缘表的曲线.定义7.3边界是包围一个区域的封闭轮廓.在无特别说明的情况下,边缘通常是指边缘点.对大多数曲线拟合算法来说,只需要边缘的位置信息。
UG基础-第7章--固定轴曲面轮廓铣

加工思路 (1)定义需要加工的几何体、 所用刀具。 (2)指定合适的驱动方法。 (3)设置合理的投射矢量。 (4)设置必要的加工参数、非 加工参数。 (5)生成刀具轨迹。
2024/3/9
Page 5 【例7-1】用固定轴曲面轮廓铣精加工球形模具型腔
加工步骤 步骤一:打开模型文件,进入加工模块。
启动UG NX 6.0,打开塑料模凹模板的球形型腔模型文 件,其操作过程如图7-2所示。单击【标准】工具栏上的按 钮,弹出【打开】对话框,选择光盘文件 example\chapter7\ 7-1.prt,打开塑料模凹模板的球形型腔 模型文件。 进入加工模块,操作如图7-3所示。单击【应用】工具 栏上的按钮,弹出【加工环境】对话框,在【要创建的 CAM设置】选项组中选择【mill_contour】,单击按钮,进 入加工模块。
2024/3/9
Page 24 例7-2 用曲线/点驱动方法进行零件轮廓的铣削 加工
步骤四:创建几何体—— 加工几何体。操作过程如图722所示。
在【创建几何体】对话框中,在【几何体子类型】选 项组中选择类型为(工件),在【位置】选项组的 【几何体】下拉列表中选择【MCS】,并在【名称】 文本框中输入“Part”,单击按钮,弹出【工件】对话 框。
1. 零件几何 2. 检查几何 3. 切削区域 4. 修剪几何 5. 驱动几何 6. 驱动点 7. 驱动方法 8. 投射矢量 9. 刀轴 10. 驱动方法及驱动几何原理
2024/3/9
Page 16 7.3 常用驱动方法
• NX 6.0提供的驱动方法有曲线/点、螺旋 式、边界、区域铣削、表面积、流线、刀轨、 径向切削、清根和文本等10种。下面重点讨 论曲线/点、边界、区域铣削和表面积等4种驱 动方法。
第七章 内轮廓加工

直进法车内沟槽
·
较高或较宽的内沟槽,可采用直进法分几次车出。粗车 时,槽侧和槽底应留精车余量,然后根据槽宽、槽深要求进 行精车。 深度浅、宽度大的内沟槽,可采用特殊角度的镗孔刀先车 出内凹槽,再用内沟槽刀车出两侧面。
多次直进法车宽内沟槽
纵向进给车宽内沟槽
毛坯为φ45mm×45mm的45钢,用FANUC 0i系统编程加工该 零件。
续表
在FANUC 0i系统加工该零件中M24×1.5-6H的螺纹。
零件加工图
第二节
内沟槽车削加工
1.能根据图样合理选择内沟槽加工刀具。
2.能对内沟槽的径向和轴向尺寸进行测量。
3.能合理进行内沟槽加工的误差分析。
常见的内沟槽:退刀槽、密封槽、轴向定位槽、储油槽、 油气通道槽等。 内沟槽加工难的主要原因:刀具刚性差,切削条件差。 影响内沟槽加工精度的主要因素:刀具的选用。 宽度较小和要求不高的内沟槽, 可以用主切削刃宽度等于槽宽的内 沟槽刀,采用直进法一次车出。
(6)车削薄壁套类零件时,车削刀具应选择较大的主偏角, 以减小背向力,防止加工工件变形。
3.毛坯选择
套类零件的毛坯主要根据零件材料、形状结构、尺寸大 小及生产批量进行选择。
孔径较小时,可选棒料,也可采用实心铸件。 孔径较大时,可选用带预制孔的铸件或锻件。 壁厚较小且较均匀时,还可选用管料。
当生产批量较大时,还可采用挤压和粉末冶金等先进毛坯 制造工艺,可在毛坯精度提高的基础上提高生产率,节约用材。
钻削时的切削用量: 1)背吃刀量(ap)。钻孔 时的背吃刀量是钻头直径的1/2。 2)切削速度(vc)。钻孔 时的切削速度是指麻花钻主切 削刃外缘处的切削速度:
钻孔时的背吃刀量
式中
vc——切削速度,m/min;
内轮廓零件加工

教案教学过程1、通孔车刀为了减小径向切削力,防止振动,通孔车刀得主偏角一般为60—75度,副偏角为15—30度。
为了防止内孔车刀后刀面与孔壁摩擦又不使后角磨得太大,一般磨成两个后角。
2、、盲孔车刀盲孔车刀就是用来车盲孔或台阶孔得,主偏角为90—93度,刀尖在刀杆最前端,刀尖与刀杆外端得距离小于内孔半径。
结合学生普车实习过程讲解教学过程工艺分析与安排内孔加工工艺与外轮廓加工基本相同,分析零件图纸—确定装甲方案---确定加工顺序与走刀路线----刀具选择---确定切削用量---编制加工程序为了增加车削刚醒,防止产生振动,要尽量选择粗得刀杆,装夹时刀杆伸出长度尽可能短,只要略大于孔深即可。
刀尖要对准工件中心,刀杆与轴心线平行。
为了确保安全,可在车孔前,先用内孔刀在孔内试走一遍。
精车内孔时,应保持刀刃锋利,否则容易产生让刀,把孔车程锥形。
内孔加工质量分析1、内孔尺寸精度超差:主要由于没有仔细测量或测量方法有误造成。
2、孔有锥度:可能就是由于切削用量选择不当,车刀磨损,刀刃不够锋利,刀杆刚性差而产生让刀等原因造成,车床主轴轴线歪斜,床身导轨严重磨损也就是造成所加工孔有锥度得原因。
3、孔表面粗糙度超差:可能就是由于切削用量选择不当,产生积屑瘤;或车刀磨损,刀刃不够锋利,切削时刀杆振动造成。
结合学生普车实习过程讲解教学过程在数控车床上加工孔,无论就是钻孔还就是镗孔,都可以用G01来直接完成;而对于较深得孔,则最好采用深孔钻削循环指令G74来进行加工。
孔加工G01例1:如图1-54所示通孔,利用G01编制精加工程序。
画图讲解教学 过程例题2:用G71编制加工程序工艺分析与安排利用G71编制加工内孔程序时,工艺安排与外圆加工雷同,只就是注意:刀具选择;循环起点得设置;孔内退刀方向,指令中Δu 为负值即可。
画图讲解 + 仿真 演示课堂 练习课后 作业查询关于内孔加工种类与加工方式有哪些?授课 心得φ25φ30φ20φ42201552480。
- 1、下载文档前请自行甄别文档内容的完整性,平台不提供额外的编辑、内容补充、找答案等附加服务。
- 2、"仅部分预览"的文档,不可在线预览部分如存在完整性等问题,可反馈申请退款(可完整预览的文档不适用该条件!)。
- 3、如文档侵犯您的权益,请联系客服反馈,我们会尽快为您处理(人工客服工作时间:9:00-18:30)。
3)进给量(f)。在车床上钻孔时,工件转1周,钻头沿轴向
移动的距离为进给量。用手慢慢转动尾座手轮来实现进给运动,
进给量太大会使钻头折断,选f =(0.01~0.02)d,钻铸铁时
(3)注意事项 一般切削螺纹时,从粗车到精车,是按照同样的螺距进行的。 从粗车到精车,主轴的转速必须是一定的,当主轴速度变化时, 螺纹切削会出现乱牙现象。 多线螺纹的导程一般较大,螺纹的升降速度段应取较大的值, 主轴的转速也不宜太高,防止主轴编码器出现过冲现象。 螺纹刀的螺旋升角也要选择合理,避免刀具后角与工件发生干 涉。
进给量略大些。
(2)对已有孔进行再加工的刀具 如扩孔钻、铰刀及镗刀等。 1)扩孔钻用于将现有孔扩大,一般精度可达IT10~IT11,表
面粗糙度可达Ra3.2~12.5μm,通常作为孔的半精加工刀具。
2)镗刀用来扩孔及用于孔的粗、精加工。
适用:能修正钻孔、扩孔等工序所造成的孔轴线歪曲、偏斜等 缺陷,故适用于要求孔距很准确的孔系加工。镗刀可加工不同 直径的孔。
第一节 镗孔及内三角螺纹加工
1.掌握G71、G70指令在内轮廓加工中的应用。2.掌握G74指令在钻孔中的应用。 3.掌握G92、G76指令在内螺纹加工中的应用方法。 4.能准确测量孔的精度。 5.能合理进行内轮廓加工的误差分析
一、内孔加工
1.基本指令介绍
(1)G71——内孔粗车复合循环 指令格式:
种类:根据结构特点及使用方式,可分为单刃镗刀、多刃镗刀 和浮动镗刀等。
为了保证镗孔时的加工质量,镗刀应满足下列要求: ①镗刀和镗刀杆要有足够的刚度; ②镗刀在镗刀杆上既要夹持牢固,又要装卸方便,便于调整; ③要有可靠的断屑和排屑措施。 3)铰刀用于中小型的半精加工和精加工,也常用于磨孔或研 孔的预加工。 铰刀的齿数多、导向性好、刚性好、加工余量小、工作平稳,
深孔钻削循环加工
3.孔加工刀具
(1)钻头 用途:主要用于在实心材料上钻孔(有时也用于扩孔)。 种类:根据转头构造及用途不同,可分为麻花钻、扁钻及深孔 钻等。
钻孔的尺寸精度一般可达IT11~IT12,表面粗糙度Ra12.5~
2.5μm。 麻花钻是钻孔最常用的刀具,钻头一般由高速钢制成。
对于精度要求不高的内孔,可用麻花钻直接钻出。 对于精度要求较高的孔,钻孔后还要再经过车削或扩孔、铰孔 才能完成。 麻花钻的选用:应留出下道工序的加工余量;一般应使麻花钻 螺旋槽部分略长于孔深。
麻花钻过长则刚性差,麻花钻过短则排屑困难,也不宜钻穿孔。
由于高速切削的发展,镶硬质合金的钻头也得到了广泛应用。
钻削时的切削用量:
1)背吃刀量(ap)。钻孔时
的背吃刀量是钻头直径的1/2。
2)切削速度(vc)。钻孔时的
切削速度是指麻花钻主切削刃 外缘处的切削速度:
钻孔时的背吃刀量
式中 vc——切削速度,m/min;
说明:G71的切削方式可以是外圆,也可以是内孔,其方式决 定于与Δu的正负号。Δu表示精加工余量和方向。如果该值 是负值,说明余量是留在负方向的,镗孔时刚好符合该要求。
(2)G70——精车循环 指令格式: G70 P(ns) Q(nf);
2.G74——深孔钻削循环
当遇到深孔加工时,如果采用一次钻削将会降低刀具的寿命, 降低工件的加工精度,因此采用深孔钻削循环。 (1)指令格式
一般加工精度可达IT16~IT18,表面粗糙度可达Ra0.4~1.6μm。
4.编程实例
(1)运用G71、G70指令编写圆柱孔的加工程序。
镗直圆柱孔零件图
(下一页续表)
(续表)
(2)加工圆柱孔和圆锥孔,运用G71、G70指令编写加工程序。
镗圆锥孔零件图
(下一页续表)
续表 (下一页续表)
续表 (下一页续表)
续表
二、内三角螺纹加工
1.加工工艺知识
(1)刀具选择与进刀方式 在数控车床上车削普通三角螺纹一般选用精密级机夹可转位不 重磨螺纹车刀,使用时要根据螺纹的螺距选择刀片的型号。 螺纹加工的进刀方式:直进法、斜进法。 当螺纹牙型深度较浅、螺距较小时,可以采用直进法直接加工。 当螺纹牙型深度较深、螺距较大时,可分数次切削进给,一般 采用斜切法加工,避免扎刀现象。 切深的分配方式:常量式、递减式。
(2)切削用量与切削液的选择
1)切削用量的选择。在螺纹加工中,背吃刀量ap等于螺纹车 刀切入工件表面的深度,如果其他刀刃同时参与切削,应为各 刀刃切入深度之和。由此可以看出随着螺纹车刀的每次切入、 背吃刀量在逐变的增加。
2)螺纹加工多为粗、精加工同时完成,要求精度较高,因此, 选用合适的切削液能够进一步提高加工质量,对于一些特殊材 料的加工尤为如此。
2.编程实例
(1)运用G92指令直进法加工内三角螺纹。
小螺距内三角螺纹加工图
(2)运用G76加工内三角螺纹。
大螺距内三角螺纹加工图
(下一页续表)
续表 (下一页续表)
续表
续表
毛坯为φ45mm×45mm的45钢,用FANUC 0i系统进行编程加工 该零件。
套类零件加工实例
一、工艺分析
1.夹住毛坯φ45mm外圆,伸出大于20mm长→车端面→钻孔, 长度大于45mm→粗车左端φ34mm内孔及C1.5mm倒角至 φ34.5mm→精车φ34mm内孔至尺寸要求。
第七章 内轮廓加工
在数控车床经常遇到套类零 件的加工。通过钻、铰、镗、 扩等可以加工出不同精度的工 件,其加工方法简单,加工精 度也比普通机床要高,因此, 镗孔、内沟槽和内三角螺纹是 套类零件常见的加工要素。
典型套类零件图
第一节 镗孔及内三角螺纹加工 第二节 内沟槽车削加工 第三节 复杂套类零件的加工
(2)指令说明 e:回退量 该值为模态值,可由参数5319号指定。由程序指令 修改。
X:最大切深点的X轴坐标,通常不指定。 Z:最大切深点的Z轴坐标。 △i:X方向的进给量(不带符号),通常不指定。
△k:每次加工深度(不带符号)。 △d:刀具在切削底部的退刀量,通常不指定。 F :进给速度。
加工深孔,用深孔钻削循环加工格式,其中e=1,k=20, F=0.1,程序如下: