球墨铸铁铸件配料实用技术
铸造球墨铸铁冶炼计算公式

铸造球墨铸铁冶炼计算公式铸造球墨铸铁是一种优质的铸铁材料,具有优良的机械性能和耐磨性能,因此在工程领域得到了广泛的应用。
在球墨铸铁的冶炼过程中,需要进行各种计算,以确保最终产品的质量和性能。
本文将介绍铸造球墨铸铁冶炼过程中的计算公式及其应用。
1. 铸造球墨铸铁的成分计算。
在球墨铸铁的冶炼过程中,需要计算原料的成分比例,以确保最终产品的化学成分符合要求。
通常情况下,球墨铸铁的成分包括碳(C)、硅(Si)、锰(Mn)、磷(P)和硫(S)等元素。
根据产品的要求,可以通过以下公式计算原料的成分比例:\[成分\% = \frac{元素含量}{总重量} \times 100\%\]例如,如果需要生产含有3.5%碳、2.0%硅、0.5%锰、0.1%磷和0.03%硫的球墨铸铁,可以通过上述公式计算出每种元素在原料中的比例,从而确定配料的比例。
2. 铸造球墨铸铁的合金添加量计算。
在球墨铸铁的冶炼过程中,通常需要添加一定量的合金元素,以改善其性能。
常用的合金元素包括铜(Cu)、镍(Ni)、钼(Mo)等。
根据产品的要求,可以通过以下公式计算合金元素的添加量:\[添加量 = \frac{合金元素含量}{总重量} \times 总重量\]例如,如果需要在球墨铸铁中添加0.5%的铜,可以通过上述公式计算出所需的铜的添加量。
3. 铸造球墨铸铁的熔化温度计算。
在球墨铸铁的冶炼过程中,需要计算熔化温度,以确保原料能够完全熔化并得到均匀的液态铁水。
通常情况下,球墨铸铁的熔化温度取决于其成分和合金元素的含量。
可以通过以下公式计算球墨铸铁的熔化温度:\[熔化温度 = aC + bSi + cMn + dP + eS + fCu + gNi + hMo\]其中,a、b、c、d、e、f、g、h分别为碳、硅、锰、磷、硫、铜、镍、钼的系数。
这些系数可以根据实际情况进行调整,以适应不同的产品要求。
4. 铸造球墨铸铁的浇注温度计算。
在球墨铸铁的冶炼过程中,需要计算浇注温度,以确保铁水在浇注时能够达到适当的流动性和润湿性。
探讨高品质球墨铸铁的熔炼技术

探讨高品质球墨铸铁的熔炼技术高品质球墨铸铁是一种具有高强度、高韧性和高耐热性的材料,其广泛应用于机械工程、汽车制造和工程建筑等领域。
而球墨铸铁的熔炼技术对其成品质量有着重要影响,下面将探讨球墨铸铁熔炼技术的关键点。
1. 原材料选择:球墨铸铁的原材料主要包括铸铁砂、钢水和添加剂。
铸铁砂应选择质量稳定、成分均匀的铸铁砂,以确保成品质量的稳定性。
钢水的选择应采用高质量的中频电炉炼钢,以提高球墨铸铁的纯净度和韧性。
添加剂的选择需要根据具体要求决定,常用的添加剂有稀土系元素、合金元素和除硅剂等。
2. 炉型选择:球墨铸铁的熔炼过程需要进行长时间的保温和混炉,所以炉型的选择非常重要。
一般常用的炉型有电炉和电弧炉,其中电炉适用于小批量生产,而电弧炉适用于大批量生产。
炉内的保温材料也需要选用高温耐磨、抗酸碱侵蚀的材料,以保证炉体的稳定性和耐用性。
3. 炉温控制:球墨铸铁的熔炼温度一般在1400℃以上,炉温的控制对成品质量有着重要影响。
一般来说,炉温过高会导致铁水中的碳化物过多,降低球墨铸铁的韧性;而炉温过低则会导致球墨铸铁的强度降低。
需要根据具体的合金配方和成品要求来控制炉温,提高产品的质量和性能。
4. 充气处理:充气处理可以有效地去除球墨铸铁中的气体、夹杂物和氧化物等杂质,提高产品的纯净度和密实度。
充气处理一般采用稀土硅镁合金,通过在铁水中加入稀土硅镁合金后,利用其在高温下的活性作用,吸收氧化铁、硫等杂质,并通过气泡上升到铁液表面。
5. 结晶处理:球墨铸铁的结晶处理是为了促使铸件组织中的碳化物成分尽量为球状分布,从而提高球墨铸铁的韧性和强度。
结晶处理一般采用球化剂,通过在铁液中加入球化剂,使不稳定的碳化物转变为稳定的球状碳化物,从而改善球墨铸铁的组织结构。
高品质球墨铸铁的熔炼技术是一个复杂的过程,需要综合考虑原材料、炉型、炉温控制、充气处理和结晶处理等多个因素。
只有在掌握这些关键点的基础上,才能确保球墨铸铁产品具有高品质、高密实度和高性能。
球墨铸铁炉料配方
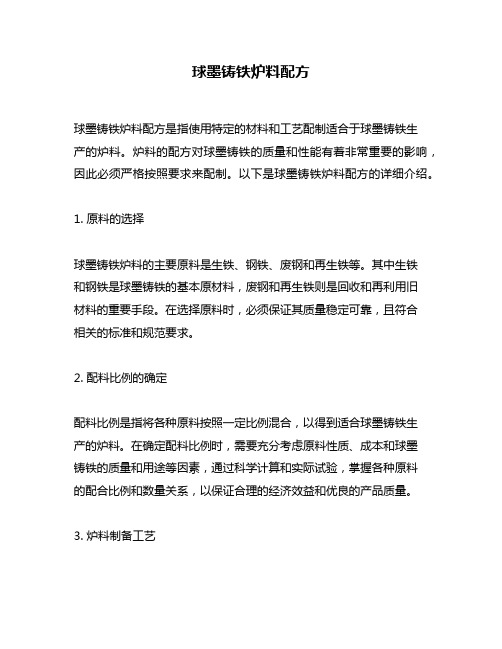
球墨铸铁炉料配方球墨铸铁炉料配方是指使用特定的材料和工艺配制适合于球墨铸铁生产的炉料。
炉料的配方对球墨铸铁的质量和性能有着非常重要的影响,因此必须严格按照要求来配制。
以下是球墨铸铁炉料配方的详细介绍。
1. 原料的选择球墨铸铁炉料的主要原料是生铁、钢铁、废钢和再生铁等。
其中生铁和钢铁是球墨铸铁的基本原材料,废钢和再生铁则是回收和再利用旧材料的重要手段。
在选择原料时,必须保证其质量稳定可靠,且符合相关的标准和规范要求。
2. 配料比例的确定配料比例是指将各种原料按照一定比例混合,以得到适合球墨铸铁生产的炉料。
在确定配料比例时,需要充分考虑原料性质、成本和球墨铸铁的质量和用途等因素,通过科学计算和实际试验,掌握各种原料的配合比例和数量关系,以保证合理的经济效益和优良的产品质量。
3. 炉料制备工艺炉料制备工艺是指将各种原料按照一定流程和方法进行混合、加热、熔化和处理的过程。
这一过程对炉料的品质至关重要,需要严格按照配方和工艺操作,确保每一步都符合要求,避免产生各种不良因素和杂质,炉料的品质和性能才能得到保证。
4. 炉料检验与质量控制炉料检验是指在生产过程中对炉料进行质量检测和控制的过程。
检验的内容包括炉料的外观、成分、组织、硬度、抗拉强度等方面,通过科学的检验方法和手段,及时发现和纠正各种问题,保证炉料的质量和稳定性。
总之,球墨铸铁炉料配方是球墨铸铁生产的关键之一,其对炉料质量和成本都有着直接的影响。
在配制炉料时,必须严格遵守标准和规范要求,科学计算、精细操作、质量检验是确保球墨铸铁炉料配方的高质量和稳定性的重要手段。
球墨铸铁铸件的铸造过程及要点注意

球墨铸铁铸件的铸造过程及要点注意球墨铸铁铸件是一种使用球墨铸铁材料制造的重要铸件,广泛应用于工程机械、汽车及石油天然气等行业。
为了保证球墨铸铁铸件的质量和性能,铸造过程中需遵循一定的要点和注意事项。
本文将详细介绍球墨铸铁铸件的铸造过程及要点注意。
一、球墨铸铁铸件的铸造过程1. 原料配制:球墨铸铁的主要原材料包括铁水、石墨、球墨化剂等。
在铸造过程中,按照一定比例将这些原料进行配制,以确保最终产品的质量。
2. 铸型制作:根据铸件的形状和尺寸要求,采用砂型铸造或金属型铸造的方式制作铸型。
其中,砂型铸造是最常用的方法,通过将铁水注入砂型中,使其在砂型中凝固形成铸件。
3. 浇注:在铸造过程中,通过将预热后的铁水倒入铸型中,使铁水充分充塞铸型的腔体,并保证铸件的内部结构均匀。
4. 固化:在浇注完成后,铁水逐渐冷却凝固形成球墨铸铁铸件。
在固化过程中,需要确保铸件充分冷却,以避免产生缺陷和应力集中。
5. 毛坯处理:将固化成型的球墨铸铁铸件进行下线、分条、去砂等处理,得到初步的球墨铸铁毛坯。
6. 热处理:对球墨铸铁毛坯进行正火或表面淬火等热处理,以改善其组织和性能,并消除内部应力。
7. 机械加工:对热处理后的球墨铸铁铸件进行车削、铣削、钻孔等机械加工工艺,使其达到最终的尺寸和形状要求。
8. 表面处理:球墨铸铁铸件表面通常需要进行喷砂、研磨或喷漆等处理,以提高其外观质量和耐腐蚀性能。
9. 检验及修磨:通过对球墨铸铁铸件进行尺寸、硬度、力学性能等多项检测,确保其符合设计要求。
如有不合格的铸件,需要进行修磨或返工处理。
二、球墨铸铁铸件铸造的要点注意1. 熔炼与浇注温度控制:在整个铸造过程中,熔炼温度和浇注温度的控制至关重要。
熔炼温度过高会导致铸件孔洞增加,熔炼温度过低则容易形成夹杂物,浇注温度过高会导致铸件变形,浇注温度过低则容易导致铸件凝固不完全。
2. 浇注方式:合理选择适当的浇注方式对于球墨铸铁铸件的质量具有重要影响。
铸铁件配料方法

铸铁件配料方法,及锰铁铬铁加入量配比HT250是珠光体灰铸铁。
化学成分:碳C :3.16~3.30硅Si:1.79~1.93锰Mn:0.89~1.04硫S :0.094~0.125磷P :0.120~0.170根据化学成分考虑原料的成分及烧损就可以知道配料了影响铸铁、铸钢件组织和性能的因素,有化学成分、孕育(变质)处理、冷却速度、炉料的“遗传性”、铁水过热温度等,在这几个因素中,化学成分含量的高低对铸件物理性能的影响相对更大些,而且是第一因素。
所以在生产过程中,根据铸件物理性能的要求,正确的配料或调料,严格控制材质的各化学成分含量尤为重要。
在生产实践中,作为冶炼技术人员和炉工来说,配料和调料应该是熟练掌握的一般性技术问题。
但是对予刚毕业的学生和大多数炉工来说,欲能系统、灵活的掌握,也确非易事。
要想控制铸件的化学成分与配料,必须事先了解以下几下问题:1、铸件的目标化学成分。
2、库存各种金属炉料的化学成分。
3、各种炉料在冶炼过程中化学成分的增减变化率。
4、配料方法。
一、目标化学成分现在大部分铸件,根据其牌号要求的不同,国标中已做出了相应的要求,从铸造手册中即可查到。
但是随着科技的进步,根据铸件的服役状况,市场需要更多物理性能各不相同的铸件,并对铸件的综合性能质量提出了更高的要求,科研单位也不断研究出新材质而取代旧材质,例如某水泥研究设计院研究的“中碳多元合金钢”,成功的代替了原需进口的球磨机衬板,代替了高锰钢,用该材质生产直径φ2.4甚至直径φ4.2的中大型球磨机衬板上,降低了生产成本,取得了良好的经济效益。
另外,如某厂生产出口国外石油钻井用的泥浆泵高铬双金属缸套及采石场600×900破碎机用的锤头,都是超高铬铸铁,这些材质的详细化学成分要求,在铸造手册中是查不到的。
在接受生产绪如上述产品时,如果自己没有完全掌握铸件化学成分要求,以及没有详细了解铸件的服役状况时,应让用户提供尽可能详细的化学成分要求范围及热处理工艺。
机车车辆用球墨铸铁件通用技术条件
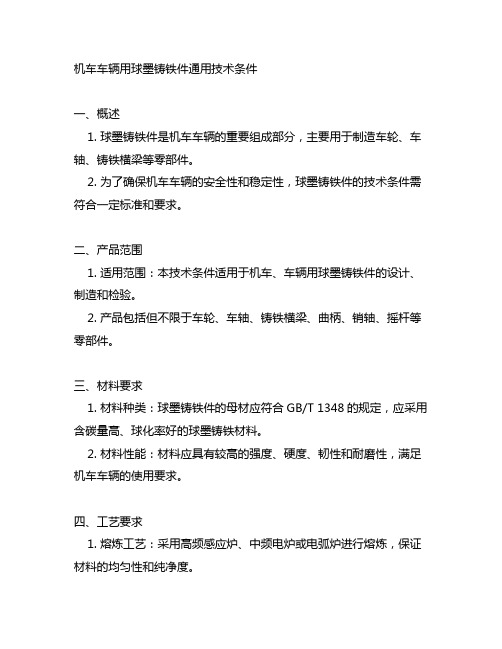
机车车辆用球墨铸铁件通用技术条件一、概述1. 球墨铸铁件是机车车辆的重要组成部分,主要用于制造车轮、车轴、铸铁横梁等零部件。
2. 为了确保机车车辆的安全性和稳定性,球墨铸铁件的技术条件需符合一定标准和要求。
二、产品范围1. 适用范围:本技术条件适用于机车、车辆用球墨铸铁件的设计、制造和检验。
2. 产品包括但不限于车轮、车轴、铸铁横梁、曲柄、销轴、摇杆等零部件。
三、材料要求1. 材料种类:球墨铸铁件的母材应符合GB/T 1348的规定,应采用含碳量高、球化率好的球墨铸铁材料。
2. 材料性能:材料应具有较高的强度、硬度、韧性和耐磨性,满足机车车辆的使用要求。
四、工艺要求1. 熔炼工艺:采用高频感应炉、中频电炉或电弧炉进行熔炼,保证材料的均匀性和纯净度。
2. 浇注工艺:采用自动化、精密化的浇注设备进行铸造,保证铸件的密度和无气孔、夹渣等缺陷。
五、外观要求1. 表面平整度:表面不得有明显的凹凸、裂纹等缺陷,保证外观质量。
2. 表面清洁度:表面不得沾有铁屑、油污等杂质,保证铸件的清洁度。
六、尺寸要求1. 全尺寸精度:按照设计要求进行尺寸检验,保证球墨铸铁件的准确性和稳定性。
2. 重量要求:球墨铸铁件的重量应符合设计要求,不得超过或低于标准重量。
七、机械性能要求1. 强度:球墨铸铁件的抗拉强度、屈服强度、延伸率等机械性能指标应符合相关标准。
2. 硬度:表面硬度和心部硬度应符合设计要求,保证零部件的使用寿命和稳定性。
八、表面质量检验1. 表面检验:采用目视、手感和放大镜等工具对球墨铸铁件的表面质量进行检验。
2. 探伤检验:采用超声波、X射线或磁粉探伤等技术对铸件进行内部缺陷检测。
九、检验方法1. 检验设备:应配备齐全的检测设备,包括硬度计、三坐标测量仪、金相显微镜等。
2. 检验程序:按照相关标准和规定执行检验程序,确保球墨铸铁件的质量可控。
十、贮存和包装要求1. 贮存条件:球墨铸铁件应存放在干燥、通风、无腐蚀性气体的仓库中。
球墨铸铁生产要点(精)

球墨铸铁生产要点关键字:球墨铸铁一、原材料:1.球墨铸铁用生铁,Q16或Q12。
2.硅铁:75%硅铁。
3.球化剂:稀土镁硅铁合金,FeSiMg10RE7或FeSiMg9RE9。
4.优质低硫焦炭。
二、配料:废钢0~20%、球墨铸铁用生铁80~95%、回炉料0~10%应使化学成分在:3.3~3.8%C;2.5~3.0%Si; Mn≤0.40%; P≤0.07%;S≤0.03%范围。
三、关键点:1.铁水包:冲入法采用的球化处理包应搪成上下直径相同的圆桶形,并使其深度H与内径D之比H/D=1.5~2,在局部适当地方修出包嘴。
包底可修成堤坝式或凹坑式。
普通浇包不宜使用。
2.球化处理:(1)加入量为1.0~2.2%,原铁液硫含量为0.04%时取下限;硫含量为0.08%时取上限。
应保证沸腾反应持续1~2分钟,时间短则可以肯定球化不良。
(2)加入方法:球化剂不可松散地放在包底或放在铁液冲得着的地方。
球化剂应集中地放在包底紧靠出铁口的一例,并用砂冲子(平头)适度地将其上表面舂平,覆盖一层无油、无锈的球铁屑或孕育剂再撒上适量的珍珠岩,或者盖以红热的带有铸造小孔的铁板。
(3)出铁后,应扒除球化处理残渣,撒上足够厚的一层珍珠岩或草灰。
3.孕育处理:球化处理后的铁液需加0.8~1.6%的75%硅铁,粒度10~20mm,最终应使碳当量在4.6~4.7%为好。
附注:球化剂:包钢产XtMg8-7 球化工艺:冲入法、堤坝式加入顺序:脱硫剂——XtMg 合金——硅铁——草灰(珍珠岩),然后在其上盖4~5mm铁板,冲入包内的铁水达2/3时,暂停冲入,待球化反应渐趋平稳时,再补充另1/3铁水,同时将孕育剂加入。
脱硫剂为Na2CO3,加入量0.2~0.3%. 孕育剂SiFe75:块度10~20mm,加入前150~200℃预热1h,1.2~1.3%以三种方式加入:(1)包内孕育:加入0.6~0.65%;(2)随流孕育:加入0.55~0.65% ;(3)为防止孕育衰退,在浇注过程中,在包内进行浮硅孕育,0.05~0.10%;根据生产实践的总结,Mg和Xt的衰退速度为0.001~0.004%/分;0.0006~0.001%/分。
铸件配料实用技术(生铁锭与废钢铁)

一、生铁锭生铁锭是熔制铸铁和铸钢的最主要金属炉料,约占配料重量的20%~100%,它的化学成分是否稳定、硫磷含量和有害杂质含量是否低,直接关系到所熔制铸铁和铸钢的质量。
合理的选用生铁锭也是获得低成本配料的有效方法之一。
生铁锭可分为铸造生铁、球墨铸铁专用生铁、炼钢生铁、高纯生铁和特种生铁等,均有标准,见表2-1-1至表2-1-7。
生产上常用生铁的化学成分和微量元素含量,见表2-1-8至表2-1-13。
通常:熔制灰铸铁时,应选用铸造生铁。
硅的质量分数为2.0%~3.0%的铸造生铁可用于熔制低牌号灰铸铁;硅的质量分数为1.2%~2.0%的铸造生铁可用于熔制高牌号灰铸铁。
熔制球墨铸铁时,应选用球墨铸铁专用生铁,但也可选用低硅、低锰和低磷硫的铸造生铁或炼钢生铁。
对于要求特别高的球墨铸铁也可选用高纯生铁。
球墨铸铁所用新生铁的硅的质量分数一般在0.8%~1.75%的范围内选择。
熔制大断面球墨铸铁件或铸态铁索体球墨铸铁件时,生铁的锰含量希望低于0.3%,不应超过0.5%,越低越好;熔制珠光体、贝氏体、退火铁索体球墨铸铁体时,生铁的锰的质量分数应小于0.6%;熔制正火珠光体球墨铸铁的中小型铸件时,生铁的锰的质量分数可适当放宽,一般也不要超过0.8%。
对于低温下工作的铁素体韧性球墨铸铁件和其他要求韧性较高的球墨铸铁件,应选用磷的质量分数小于0.07%的生铁。
一般球墨铸铁件用生铁磷的质量分数不应大于0.1%;硫的质量分数应限制在0.05以下;反球化元素不得过量ωTe<0.01%、ωTi<0.3%、ωSn<0.09%、ωSb<0.2%、ωPb<0.2%、ωBi<0.05%。
熔制蠕墨铸铁时,应参照熔制球墨铸铁的要求选用生铁。
熔制可锻铸铁时,一般只加入10%左右的生铁量,主要是为了提高碳含量,因此含磷、硫和铬低的铸造生铁、炼钢生铁和再生铁均能使用。
熔制特种铸铁时,应尽量选用含相应元素高的铸造生铁或特种生铁。
怎样控制好球墨铸铁中碳和硅配料指数
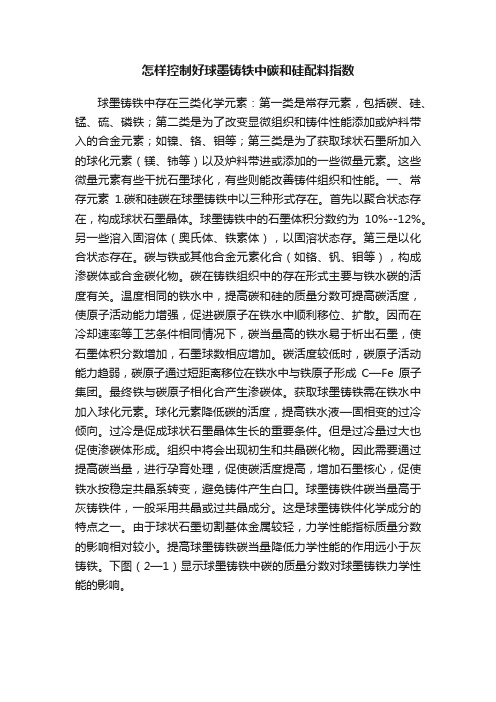
怎样控制好球墨铸铁中碳和硅配料指数球墨铸铁中存在三类化学元素:第一类是常存元素,包括碳、硅、锰、硫、磷铁;第二类是为了改变显微组织和铸件性能添加或炉料带入的合金元素;如镍、铬、钼等;第三类是为了获取球状石墨所加入的球化元素(镁、铈等)以及炉料带进或添加的一些微量元素。
这些微量元素有些干扰石墨球化,有些则能改善铸件组织和性能。
一、常存元素1.碳和硅碳在球墨铸铁中以三种形式存在。
首先以聚合状态存在,构成球状石墨晶体。
球墨铸铁中的石墨体积分数约为10%--12%。
另一些溶入固溶体(奥氏体、铁素体),以固溶状态存。
第三是以化合状态存在。
碳与铁或其他合金元素化合(如铬、钒、钼等),构成渗碳体或合金碳化物。
碳在铸铁组织中的存在形式主要与铁水碳的活度有关。
温度相同的铁水中,提高碳和硅的质量分数可提高碳活度,使原子活动能力增强,促进碳原子在铁水中顺利移位、扩散。
因而在冷却速率等工艺条件相同情况下,碳当量高的铁水易于析出石墨,使石墨体积分数增加,石墨球数相应增加。
碳活度较低时,碳原子活动能力趋弱,碳原子通过短距离移位在铁水中与铁原子形成C—Fe原子集团。
最终铁与碳原子相化合产生渗碳体。
获取球墨铸铁需在铁水中加入球化元素。
球化元素降低碳的活度,提高铁水液—固相变的过冷倾向。
过冷是促成球状石墨晶体生长的重要条件。
但是过冷量过大也促使渗碳体形成。
组织中将会出现初生和共晶碳化物。
因此需要通过提高碳当量,进行孕育处理,促使碳活度提高,增加石墨核心,促使铁水按稳定共晶系转变,避免铸件产生白口。
球墨铸铁件碳当量高于灰铸铁件,一般采用共晶或过共晶成分。
这是球墨铸铁件化学成分的特点之一。
由于球状石墨切割基体金属较轻,力学性能指标质量分数的影响相对较小。
提高球墨铸铁碳当量降低力学性能的作用远小于灰铸铁。
下图(2—1)显示球墨铸铁中碳的质量分数对球墨铸铁力学性能的影响。
适当提高碳量,还能提高铁水流动性,减少铸件发生缩孔、缩松倾向和缩松分布面积,改善球墨铸铁铸造性能。
铸铁件配料方法,及锰铁铬铁加入量配比
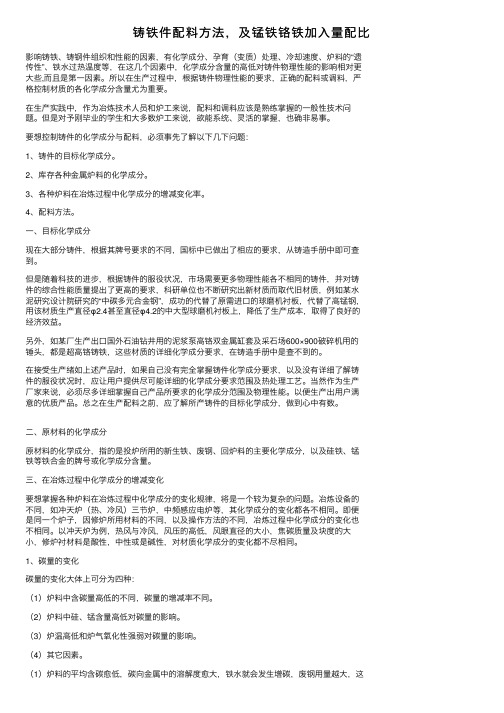
铸铁件配料⽅法,及锰铁铬铁加⼊量配⽐影响铸铁、铸钢件组织和性能的因素,有化学成分、孕育(变质)处理、冷却速度、炉料的“遗传性”、铁⽔过热温度等,在这⼏个因素中,化学成分含量的⾼低对铸件物理性能的影响相对更⼤些,⽽且是第⼀因素。
所以在⽣产过程中,根据铸件物理性能的要求,正确的配料或调料,严格控制材质的各化学成分含量尤为重要。
在⽣产实践中,作为冶炼技术⼈员和炉⼯来说,配料和调料应该是熟练掌握的⼀般性技术问题。
但是对予刚毕业的学⽣和⼤多数炉⼯来说,欲能系统、灵活的掌握,也确⾮易事。
要想控制铸件的化学成分与配料,必须事先了解以下⼏下问题:1、铸件的⽬标化学成分。
2、库存各种⾦属炉料的化学成分。
3、各种炉料在冶炼过程中化学成分的增减变化率。
4、配料⽅法。
⼀、⽬标化学成分现在⼤部分铸件,根据其牌号要求的不同,国标中已做出了相应的要求,从铸造⼿册中即可查到。
但是随着科技的进步,根据铸件的服役状况,市场需要更多物理性能各不相同的铸件,并对铸件的综合性能质量提出了更⾼的要求,科研单位也不断研究出新材质⽽取代旧材质,例如某⽔泥研究设计院研究的“中碳多元合⾦钢”,成功的代替了原需进⼝的球磨机衬板,代替了⾼锰钢,⽤该材质⽣产直径φ2.4甚⾄直径φ4.2的中⼤型球磨机衬板上,降低了⽣产成本,取得了良好的经济效益。
另外,如某⼚⽣产出⼝国外⽯油钻井⽤的泥浆泵⾼铬双⾦属缸套及采⽯场600×900破碎机⽤的锤头,都是超⾼铬铸铁,这些材质的详细化学成分要求,在铸造⼿册中是查不到的。
在接受⽣产绪如上述产品时,如果⾃⼰没有完全掌握铸件化学成分要求,以及没有详细了解铸件的服役状况时,应让⽤户提供尽可能详细的化学成分要求范围及热处理⼯艺。
当然作为⽣产⼚家来说,必须尽多详细掌握⾃⼰产品所要求的化学成分范围及物理性能。
以便⽣产出⽤户满意的优质产品。
总之在⽣产配料之前,应了解所产铸件的⽬标化学成分,做到⼼中有数。
⼆、原材料的化学成分原材料的化学成分,指的是投炉所⽤的新⽣铁、废钢、回炉料的主要化学成分,以及硅铁、锰铁等铁合⾦的牌号或化学成分含量。
铸造球铁熔铁配料规范
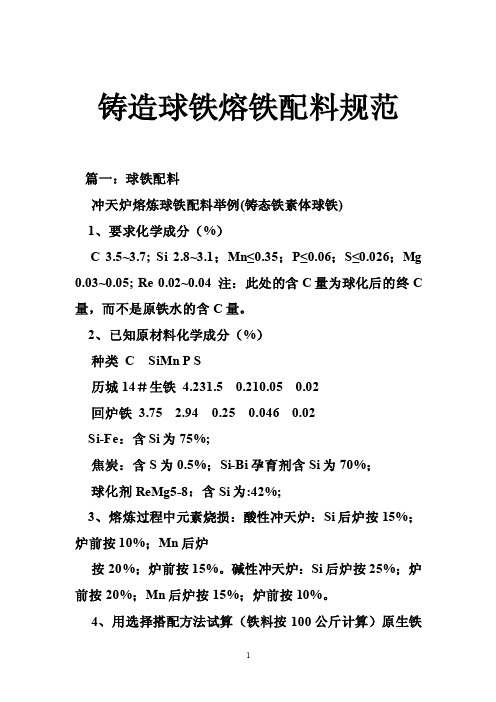
铸造球铁熔铁配料规范篇一:球铁配料冲天炉熔炼球铁配料举例(铸态铁素体球铁)1、要求化学成分(%)C 3.5~3.7; Si 2.8~3.1;Mn≤0.35;P≤0.06;S≤0.026;Mg0.03~0.05; Re 0.02~0.04 注:此处的含C量为球化后的终C 量,而不是原铁水的含C量。
2、已知原材料化学成分(%)种类C SiMn P S历城14#生铁4.231.5 0.210.05 0.02回炉铁3.75 2.94 0.25 0.046 0.02Si-Fe:含Si为75%;焦炭:含S为0.5%;Si-Bi孕育剂含Si为70%;球化剂ReMg5-8:含Si为:42%;3、熔炼过程中元素烧损:酸性冲天炉:Si后炉按15%;炉前按10%;Mn后炉按20%;炉前按15%。
碱性冲天炉:Si后炉按25%;炉前按20%;Mn后炉按15%;炉前按10%。
4、用选择搭配方法试算(铁料按100公斤计算)原生铁65%;回炉铁35%。
5、核算炉料中的含C量C炉料=4.23%×65%+3.75×35%=4.06%由于球铁中碳当量比较高,在冲天炉熔炼条件下要减碳(当碳当量>3.6%时一般要减碳3~8%),如按5.5%计算,则从炉内出来的铁水含C量为:4.06%1×(1-5.5%)=3.84%;同时在球化处理过程中还要降碳0.1~0.2%(原因:○2一部分过饱和C以石墨形式析出,上浮进入熔渣)如球化反应使碳烧损;○按0.15%计算,则铁水最终含C量为:3.84%—0.15%=3.69%(符合3.5~3.7%的要求)6、含Si量的计算铁水最终含Si量包括以下几个部分:1)炉料中的含Si量Si炉料:Si炉料=1.5%×65%+2.94×35%=2.0%,烧损按15%计算,则从炉内出来的铁水含Si量为:2.0%×(1-15%)=1.7%; 2)一次孕育按0.2% 75 Si-Fe(覆盖在球化剂上),进入铁水的硅量Si孕育Ⅰ=0.2%×75%×(1-10%)=0.14%;3)二次孕育按0.4% 75 Si-Fe(在出铁槽加入),进入铁水的硅量Si孕育Ⅱ=0.4%×75%×(1-10%)=0.27%;4)三次孕育按0.2% Si-Bi(浇包孕育),进入铁水的硅量Si孕育Ⅲ=0.2%×70%×(1-10%)=0.13%;5)球化剂加入量按 1.7%,则球化剂进入铁水的硅量Si 球化=1.7%×42%×(1-10%)=0.64%;6)铁水终Si含量为上述1)~5)之和(如果生产管卡,还要计入0.1~0.2%的小颗粒75 Si-Fe浇包四次孕育)即Si 终=1.7%+0.14%+0.27%+0.13%+0.64%=2.88%(符合2.8~3.1%的要求)7、含Mn量的计算炉料中的含Mn量Mn炉料:Mn炉料=0.21%×65%+0.25×35%=0.224%,去掉烧损,则从炉内出来的铁水含Mn量为:0.224%×(1-20%)=0.18%;另外,稀土镁合金中一般允许含Mn≤4%,若以4%计(实际应根据验收化验的具体含量计算),并去掉烧损,则进入铁水的Mn量为:1.7%×4%×(1-15%)=0.058%,铁水中的总Mn量为两者之和即0.18%+0.058%=0.238%,在球化处理过程中由于Mn与S作用和Mn夹渣上浮,一般Mn含量要下降3%~5%,若以4%计算,则铁水的终Mn量Mn 终=0.238%×(1-4%)=0.228%(符合终Mn≤0.35的要求)。
固溶强化球墨铸铁生产工艺

固溶强化球墨铸铁生产工艺固溶强化是一种常用的球墨铸铁生产工艺,通过固溶处理可以显著提高球墨铸铁的力学性能和耐磨性能。
本文将介绍球墨铸铁的生产流程和固溶强化工艺,并探讨其影响因素和优缺点。
一、球墨铸铁的生产流程球墨铸铁是一种具有高强度、高韧性和良好的耐磨性能的铸铁材料,广泛应用于机械制造、汽车制造、工程机械等领域。
其生产流程主要包括原料配料、熔炼、浇注、固化和热处理等。
1. 原料配料:球墨铸铁的主要原料是铸铁母合金、石墨球和球化剂。
合理的原料配比可以保证球墨铸铁的化学成分和力学性能符合要求。
2. 熔炼:将原料放入炉中进行熔炼,控制炉温和保持一定时间,使合金中的元素充分溶解和混合,得到均匀的熔体。
3. 浇注:将熔体倒入铸型中,通过重力或压力使熔体充满整个铸型,形成铸件的初形。
4. 固化:待熔体冷却后,固化成为铸件。
在固化过程中,合金中的碳以球状石墨的形式析出,使铸件具有球墨铸铁的特性。
5. 热处理:对固化后的铸件进行热处理,包括固溶处理和淬火处理。
其中,固溶处理是球墨铸铁固溶强化的关键工艺。
二、固溶强化工艺固溶强化是指在一定温度下将球墨铸铁加热至固溶温度,保持一定时间后迅速冷却。
固溶处理过程中,合金中的碳、硅等元素会溶解在铁基体中,形成固溶体。
固溶体具有高硬度和高强度,可以显著提高球墨铸铁的力学性能和耐磨性能。
固溶强化工艺的主要影响因素包括固溶温度、保温时间和冷却速率。
固溶温度应根据球墨铸铁的化学成分和力学性能要求进行选择,一般在800~950℃之间。
保温时间应足够长,以保证合金中的碳、硅等元素充分溶解在铁基体中。
冷却速率应尽量快,以避免固溶体析出过多的晶间碳化物,影响球墨铸铁的力学性能。
固溶强化的优点在于能够显著提高球墨铸铁的综合性能,包括抗拉强度、屈服强度、冲击韧性和耐磨性等。
通过固溶强化,球墨铸铁的性能可以接近或甚至超过一些铸钢材料。
此外,固溶强化工艺简单,操作方便,成本相对较低。
然而,固溶强化也存在一些缺点。
球墨铸铁国家实用标准(摘要)
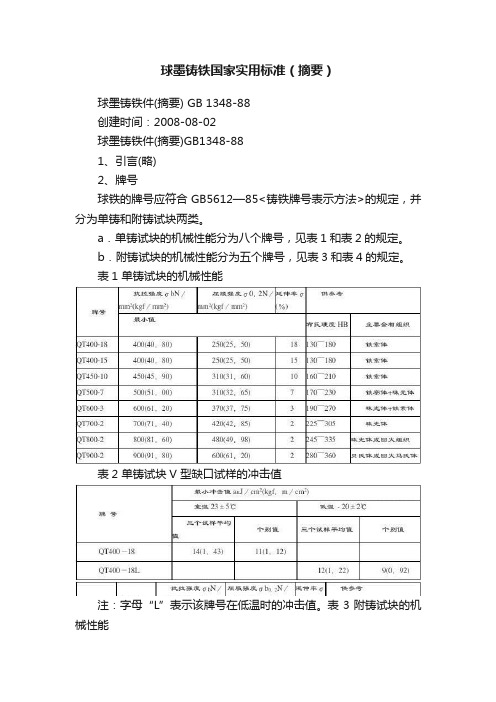
球墨铸铁国家实用标准(摘要)球墨铸铁件(摘要) GB 1348-88创建时间:2008-08-02球墨铸铁件(摘要)GB1348-881、引言(略)2、牌号球铁的牌号应符合GB5612—85<铸铁牌号表示方法>的规定,并分为单铸和附铸试块两类。
a.单铸试块的机械性能分为八个牌号,见表1和表2的规定。
b.附铸试块的机械性能分为五个牌号,见表3和表4的规定。
表1 单铸试块的机械性能表2 单铸试块V 型缺口试样的冲击值注:字母“L”表示该牌号在低温时的冲击值。
表3附铸试块的机械性能表3 附铸试块的机械性能注:牌号后面的字母A系表示该牌号在附铸试块上测定的机械性能,以区别表1的单铸试块测定的性能。
表4 附铸试块V型缺口试样的冲击值3技术要求3.1生产方法、化学成分和热处理生产方法、化学成分和热处理工艺,可由供方自行决定。
但必须保证协议书、技术条件上所规定的球铁牌号或达到本标准规定的机械性能指标。
对于化学成分,热处理方法有特殊要求的球铁件由供需双方商定。
3.2机械性能3.2.1球铁件的机械性能以抗拉强度和延伸率两个指标作为验收依据。
3.2.2冲击试验只适用于表2和表4所规定的牌号,并且仅在需方要求做冲击试验时,冲击值才作为验收依据。
3.2.3对屈服强度、硬度有要求时,经供需双方商定,可作为验收依据。
3.2.4如果以硬度作为验收指标时,按附录A的规定进行。
3.2.5如果是在铸件本体上取样时,取样部位及要达到的性能指标,由供需双方规定。
3.3金相组织如果需方要求进行金相组织检验时,可按GB9441—88《球墨铸铁金相检验》的规定进行,球化级别_般不得低于4级,其检验次数和取样位置由供需双方商定。
球化级别和基体组织,可用无损检测方法进行检验,如有争议时,应用金相检验法裁决。
3.4球铁件的几何形状及其尺寸公差3.4.1球铁件的几何形状及其尺寸应符合球铁件图样的规定。
3.4.2球铁件的尺寸公差应按GB 6414 - 86<铸件尺寸公差>的规定执行。
铸造厂都在使用废钢熔炼球墨铸铁,这三点一定要知道!

铸造厂都在使用废钢熔炼球墨铸铁,这三点一定要知道!在球墨铸铁的传统生产工艺中,一般使用10%左右的碳素废钢进行配料。
本文只涉及在感应电炉内生产球墨铸铁时,提高碳素废钢使用比例后,生产过程中特别应注意的一些问题。
根据生产实践,笔者提出了自己的看法,供同行参考。
1.炉料的选择(1)废钢生产球墨铸铁使用的废钢应为碳素废钢。
其中不应含有阻碍石墨化的元素,如铬。
更不应含有反球化合金元素。
废钢的块度应有30%左右呈厚片状,可以平放于炉内。
(2)增碳剂①优质焦炭。
含硫量要低,块度60~80mm,具有较高的强度,烧红后不能一捣即碎。
②废电极块。
最好有一定长度,便于扦入铁液中。
(3)生铁主要用来调整铁液含碳量。
希望使用wC>4%的高碳低硫生铁。
生铁中的硅含量适当高一些较好,生产球墨铸铁可以少加硅铁。
(4)球化剂、孕育剂按传统工艺使用,遵从各厂实际情况而定。
2.熔炼熔炼工艺流程:焦炭块+废钢→电极块→提温→扒出焦炭块和电极块→取样分析含碳量→生铁→回炉料→取样分析Si、Mn→提温→锰铁+硅铁→出炉→孕育+球化→浇注。
熔炼过程中的注意事项如下:(1)焦炭块装于炉底,目的是要创造较长的焦炭块在铁液中的浸泡时间。
焦炭块用量是废钢的5%左右。
废钢熔化50%左右,焦炭上边应用厚片状废钢遮盖。
也可以用60~80 mm的废电极块代替焦炭装于炉底作增炭剂,含硫量更低,对获得优质球墨铸铁更有利。
(2)废钢使用比例主要决定于增炭效率。
开始使用此法生产球墨铸铁的厂家,以30%左右为好。
提高了增炭效率之后,逐步提高废钢使用比例。
过多的使用废钢,如果增炭效率不高,则影响最终产品的碳硅当量。
(3)废钢熔毕,扦入电极棒,适当提高炉内温度,提高增炭效率。
但是,炉温过高,增加电耗,对炉衬也不利。
(4)预估含炭量够高后,扒出焦炭块和电极棒,取样分析含炭量。
(5)根据分析结果,计算生铁加入量和回炉球墨铸铁使用量。
(6)根据含硅量估算,决定是否可用回炉料补足铁液总量。
球墨铸铁管件技术

球墨铸铁管件技术
1.球墨铸铁管件的概述
2.制作球墨铸铁管件的工艺流程
(1)前期准备:将球墨铸铁管件的性能参数确定,分析并设定制造
要求,收集有关设计技术参数,确定原料、变形规格及要求。
(2)熔炼:下料配料,用熔铁炉作成型、熔炼铁水,熔炼时间长度
和温度波动均匀,铁水的成分也要合格。
(3)浇口:保温模型、料池中加入熔铁。
料池速度控制恰当,以保
证铁水浇口流利。
(4)球冷:加强铸件外表面的热处理过程,使铸件外表面的温度可
以迅速降低到接近室温,在此过程中,熔炼的球墨在表面形成一层结晶状
态的铁包铬碳合金,即熔炼球墨件。
(5)检验:检验熔炼的球墨铸铁管件的外观尺寸,以及材质,抗拉
强度,抗压强度等性能参数。
(6)整形:将球墨铸铁管件变形成所需的实用型式,并做表面处理,以提高其性能。
(7)包装:将生产完成的熔炼球墨铸铁管件分批装箱,并标明特性
指标。
球墨铸铁铸件配料实用技术

残余镁量大致为 ! " !2$ 1 ! " !6$ ;在有稀土的情况下,残余镁量也大致为 ! " !2$ 1 ! > !!6$ 、残余稀土量为 ! " !/#$ 1 ! " !#$ 。几种常用球化剂的加入量可参见表 : ? 2 ? /#。
线
利用不同球化级别
的球墨铸铁在凝固过
比
电
程中比电阻一定的原 将所测的电流变化值与各种球化级别的标准变化值相比较,确定所测试样的
包内冲入法 密流处理法 型内球化法
:! 1 #! *! 1 0! #! 1 6!
!>5 1 /"6 !"# 1 /"* !"* 1 /"!
镁硅铁合金
包内冲入法
:! 1 2!
@ :"!
注:原铁液中硫含量高时,球化剂加入量取大值,反之取小值。
孕育剂的加入量(质量分数)应当保证消除球化元素所造成的白口倾向,如果想获得 铁素体球墨铸铁,其孕育增硅量应大于 ! " 5$ ;如果想获得珠光体球墨铸铁,其孕育增硅 量也不应小于 ! " *$ 。硅铁(硅 0#)孕育的加入量可参见表 : ? 2 ? /5。
由于加镁处理后,铁液温度下降和搅拌作 用,促进了锰的脱硫作用和锰夹渣的上浮
锰
增加
球化剂中锰几乎全 当生产珠光体球铁时,有时球化剂中配有
部转入铁液
! .2$%’ ( !%’
硅
增加
qt600球墨铸铁铸造技术条件

qt600球墨铸铁铸造技术条件摘要:1.QT600 球墨铸铁概述2.QT600 球墨铸铁的技术要求3.QT600 球墨铸铁的铸造工艺4.QT600 球墨铸铁的应用领域5.结论正文:一、QT600 球墨铸铁概述QT600 球墨铸铁是一种高强度、高韧性的球墨铸铁材料,其主要成分为碳(C)2.5-3.0%,硅(Si)2.3-2.7%,锰(Mn)0.2-0.4%,硫(S)小于0.02%,磷(P)小于0.08%,镁(Mg)小于0.09%。
QT600 球墨铸铁具有良好的铸造性能、抗震性能和耐磨性能,广泛应用于汽车、机械、建筑等领域。
二、QT600 球墨铸铁的技术要求为确保QT600 球墨铸铁件的质量,对其技术要求如下:1.化学成分:C:2.5-3.0、Si:2.3-2.7、Mn:0.2-0.4、S<0.02、P<0.08、Mg<0.09,残存稀土氧化物:0.04~0.05,Cu:0.35~0.40(都是%)。
2.力学性能:抗拉强度≥600MPa,伸长率≥10%,硬度达到HRC50-55,甚至更高,但为了避免硬脆现象,常用硬度在HRC38-45 之间。
3.铸造工艺:采用热模法、冷模法或壳型法等铸造工艺,确保铸件表面光洁,内部质量良好。
三、QT600 球墨铸铁的铸造工艺1.熔炼:选用高质量的生铁作为原料,严格控制化学成分,进行熔炼。
2.球化处理:在铸铁熔液中加入适量的球化剂,使铸铁中的石墨球化,提高铸铁的韧性。
3.孕育处理:在铸铁熔液中加入适量的孕育剂,促进铸铁中的石墨细化,提高铸铁的抗拉强度。
4.浇注:将处理后的铸铁熔液倒入预先准备好的模具中,进行浇注。
5.凝固:铸件在模具中逐渐冷却,凝固成型。
6.清理:将凝固后的铸件从模具中取出,清理表面的砂粒、气泡等缺陷。
四、QT600 球墨铸铁的应用领域QT600 球墨铸铁件因其高强度、高韧性和耐磨性能,广泛应用于汽车发动机、变速器、汽车轮毂、机械传动部件等领域。
珠光体球墨铸铁熔炼配方

珠光体型球墨铸铁熔炼配方及注意事项一、化学成份C Si Mn P S Mg RE原铁液 3.6-3.7 1.2-1.3 0.3-0.4 <0.06 <0.06 0.03-0.04 0.02-0.03 球化后 3.6-3.7 2.0-2.1 0.3-0.4 <0.06 <0.06 0.03-0.04 0.02-0.03二、合金加入量:1、QT600-3 Cu:0.3-0.4%2、QT700-2 Cu:0.4-0.5% Sn:0.03-0.03%三、球化剂加入量及放臵方法:1、加入量:1.3%左右,用前烘烤预热。
2、放臵方法:将球化剂放在堤坝一侧底层,其上放覆盖剂:硅铁、草灰、球铁铁屑(或废钢碎片)等并分层适度舂紧。
最后用同堤坝上口大小相近的铁板(或薄钢板)覆盖。
四、球化过程及效果观察出铁时铁水应冲至堤坝的另一侧,注意不要让铁水流直接与球化剂接触。
当铁水出至铁水量的三分之二左右时,停止出铁。
出铁半分钟左右球化反映就开始了,产生大量白色镁光和火苗,火苗越多越长则球化越好,反应时间可持续2分钟左右。
反应停止后,立即将铁水表面的渣子扒净,再出另外三分之一的铁水,同时进行第一次孕育。
五、孕育剂加入量及加入方法:1、加入量:0.7—0.8%,用前烘烤预热2、加入方法:第一次加入量:0.5-0.6%;第二次加入量0.2%.六、出炉温度、浇注温度和浇注时间:1、出炉温度:第一次出用于球化的铁水(2/3铁水),出铁温度1480-1500℃;第二次出用于孕育和提高铁水(1/3铁水),出铁温度1560℃。
(这是由于铁水温度高低对球化处理效果有很大关系。
温度过高,不仅反应过早而且强烈,将大大降低球化剂的吸收率,影响球化效果;温度过低,球化剂将“冻死”在堤坝内,不发生反应。
2、浇注温度:1350-1420℃3、从球化开始到浇注结束,13分钟内完成。
七、炉前质量检验1、火苗观察法:经球化处理的铁水,在其表面会冒出白亮色的火苗(似蜡烛火苗),这是镁蒸气逸出发生氧化燃烧的现象。
球墨铸铁生产方法

一.球墨铸铁生产计算方法
1.铸造`球铁用料a生铁:含硫低生铁通常用本溪产地Q10 Q12。
b回炉料:自己家已知成分水冒口。
C废钢。
最好用牌号一直的。
2.球化剂。
一般用7-8XTMg 3-8XtMg(小件多用)
3.孕育剂。
Si75粒度3-5小件硅钡孕育剂2-5粒度(做二次孕育作用)
二.球墨铸铁配料计算法
1.生铁硅的计算方法。
比如配料Q10生铁50% 回炉料40% 废钢10%
已知生铁含硅Si生=0.89%si 回炉料(根据化验或者前一天配料数)si回=2.6% si球化剂中含硅量(大部分含40-45%si)
Si终=si生*50+si回*40%+si球*球化剂用量(根据用包大小加入量1.2-1.4%)
其它成分炉料计算方法大致相同
三.装料方法
1.把称好的炉料按顺序投放依次投放炉中增碳剂-废钢-生铁-回炉料。
2.炉料装入要少100kg.溶化化后浇注碳硅仪浇注调整炉料。
3.炉温升到1530-1580出炉
4.球化包包底要按如图方式(底坑必须大于球化剂堆积体积)
1)装球化剂按比例投入摊平,捣实。
2)盖上球铁铁削(块度越小越好)均与捣实。
3)撒入少许聚渣剂(不要全盖上防止凝死)
2)铁水温度达到要求时开始倾转炉。
按图5方向注入2/3水停住。
球化包开始反应同时盖上铁盖(防止溅出)。
3)待反应接近尾声时倒入剩余铁水同时把孕育剂顺流加到包里,撒上集渣剂搅拌打渣。
4)浇注三角试片,暗红色取出用水极冷。
取出看两边缩凹中间有缩松。
断口银白色为合格。
高质量球墨铸铁微量元素和合金元素的选择与控制

高质量球墨铸铁微量元素和合金元素的选择与控制球墨铸铁是一种高强度、高韧性和耐磨性能优异的材料,广泛应用于汽车、机械、航空航天、建筑等领域。
为了保证球墨铸铁的性能,需要控制微量元素和合金元素的含量。
1. 稀土元素:添加稀土元素可以提高球墨铸铁的强度、韧性和耐磨性能。
稀土元素可以加强球化剂的活性,促进球化反应的进行,并且与碳化物形成化合物,提高石墨颗粒的生长速度和形态。
2. 立方晶增强元素:立方晶增强元素包括Ni、Cu、Mo等,它们可以促进面心立方晶的形成,提高球墨铸铁的强度和硬度。
但是,过量的立方晶增强元素会导致球墨铸铁的韧性下降。
3. 结构调节元素:结构调节元素包括Cr、Mn、Si等,它们可以稳定铸铁组织,提高球墨铸铁的强度和耐磨性,但会影响球化效果。
4. 碳化物形成元素:碳化物形成元素包括Cr、Mo、V等,它们可以与碳形成稳定的碳化物,提高球墨铸铁的硬度和耐磨性。
5. 氧化物形成元素:氧化物形成元素包括Al、Ti等,它们可以与氢氧化物形成氧化物,消除铁水中的气体和杂质,改善球化效果。
在选择球墨铸铁的微量元素和合金元素时,应该根据具体应用场景和材料性能需求进行选择和控制。
同时,还需要优化生产工艺,保证合金元素的均匀分布,并细化铸件组织,以提高球墨铸铁的性能。
- 1、下载文档前请自行甄别文档内容的完整性,平台不提供额外的编辑、内容补充、找答案等附加服务。
- 2、"仅部分预览"的文档,不可在线预览部分如存在完整性等问题,可反馈申请退款(可完整预览的文档不适用该条件!)。
- 3、如文档侵犯您的权益,请联系客服反馈,我们会尽快为您处理(人工客服工作时间:9:00-18:30)。
!>5 1 /"6 !"# 1 /"* !"* 1 /"!
镁硅铁合金
包内冲入法
:! 1 2!
@ :"!
注: 原铁液中硫含量高时, 球化剂加入量取大值, 反之取小值。
孕育剂的加入量 (质量分数) 应当保证消除球化元素所造成的白口倾向, 如果想获得 铁素体球墨铸铁, 其孕育增硅量应大于 ! " 5$ ; 如果想获得珠光体球墨铸铁, 其孕育增硅 量也不应小于 ! " *$ 。硅铁 (硅 0#) 孕育的加入量可参见表 : ? 2 ? /5。
球化剂类型
几种常用球化剂的加入量 (质量分数)
吸收率 ($) 加入量 ($)
球化处理方法
工业纯镁
自建压力加镁法 转动包法
#! 1 6! 5! 1 0!
! " / 1 ! " :: ! " /* 1 ! " :!
包内冲入法 稀土硅铁镁合金 密流处理法 型内球化法
:! 1 #! *! 1 0! #! 1 6!
由球化剂 (一般含硅 4%’ ( 0%’ ) 和孕育 剂 (含硅 50’ ) 中带入
注: 成分含量皆指质量分数。
球墨铸铁原铁液化学成分的特点是高碳、 低硅、 低磷硫, 可参见表 ! " # " $% 进行控 制。 表 ! " # " $%
球墨铸铁 牌号 ’ () *+ , (
球墨铸铁原铁液化学成分的控制
球铁铁液表面有一 铁 液 表 面 膜 观 察 层很 厚 的 氧 化 膜, 因 为球铁的表面张力比 灰铁 大, 净化效果较 大, 铁液表面与灰铸 铁有明显区别 稀土镁球铁的表面 特征较纯镁球铁差 铁液表面平静, 覆盖 一层皱皮, 温度下降 后 会出现五颜六色的浮皮 表面现象介于两者之间 表面翻腾严重, 氧化皮极 少, 并集中在中央
元素名称
球墨铸铁球化孕育处理时五大元素的变化情况
一般增减量 原 因Leabharlann 增减趋向碳降低
一般降低 % & $ ’ ( % & !’
$ & 球化反应使碳烧损 上浮 ! & 一部分过饱和的碳以石墨形式析出, 进入溶渣
视原铁液硫量而 硫 降低多 定, 一 般 降 )% ’ ( *% ’ 稀土和镁的脱硫作用, 生成 +,! -# , ./-
磷
稍有降低
一般降低 # ’ ( 0 ’
与镁生成 ./# 1!
稍有降低
一般降低 # ’ ( 0 ’
由于加镁处理后, 铁液温度下降和搅拌作 用, 促进了锰的脱硫作用和锰夹渣的上浮
锰 球化剂中锰几乎全 部转入铁液 当生产珠光体球铁时, 有时球化剂中配有 ! .2 $%’ ( !%’
增加
硅
增加
一般增加 % & ) ’ ( % & 3’
一、 球墨铸铁熔炼用炉的选择
熔制灰铸铁的熔炼炉基本上都可用来熔制球墨铸铁。 最广泛采用的还是冲天炉, 碱性冲天炉对获得高温低硫铁液十分有利。 采用感应电炉, 或电弧炉, 或冲天炉 C 电炉双联熔炼炉熔制球墨铸铁, 对保证球墨铸 铁质量较为理想。
二、 球墨铸铁原铁液化学成分的控制
球墨铸铁件的化学成分应根据球墨铸铁件的合金牌号性能要求以及球墨铸铁件的 壁厚状况和热处理工艺等确定。 但确定球墨铸铁的原铁液化学成分 (或配料标准成分) 时, 由于需要进行球化孕育处 理, 因此还应考虑由于球化孕育处理时元素的增减情况 (见表 ! " # " $#) , 并且主要应考 虑由于球化剂和孕育剂所带入的硅元素的增加值。 表 ! " # " $#
原铁液化学成分 (质量分数) (&) 备 注
-.%// " $0 -.%// " $1 -.%1/ " $/
}
#21 3 #24
$51 3 !2/
6 /27
6 / 2 /8
6 / 2 /0
铁素体类型
-.1// " 8 -.7// " #
}
#21 3 #24
$21 3 !2/
/2# 3 /20
6 / 2 /0
6 / 2 /0
铁素体 " 珠光体类型
-.8// " ! -.0// " ! -.4// " !
}
#21 3 #24
$2/ 3 $20
/21 3 /24
6 / 2 $/
6 / 2 /0
珠光体类型
注: 铸态球墨铸铁的锰含量应稍低一些。
三、 球墨铸铁的球化孕育处理
球墨铸铁进行球化孕育处理的目的是通过向具有碳当量在共晶成分附近的球墨铸 铁原铁液中加入一定数量的球化剂和孕育剂, 引起强烈脱氧和去硫, 促使石墨成为球状, 并细化球状石墨和改善球状石墨的分布, 因而可获得较高的强度和冲击韧度等。 球化剂的种类较多, 主要有: 纯镁、 稀土硅铁镁合金、 镁焦、 钇基重稀土硅铁镁合金、 铜镁合金、 镍镁合金、 镁硅铁合金、 镁铁屑压块、 稀土硅铁、 含钡稀土硅铁镁合金等。但使 用最多的稀土硅铁镁合金; 常用球化剂的成分 (质量分数) 如下: 稀土硅铁镁合金 9:/ 2 1& 3 !/& , * ;1& 3 $!& , ()#1& 3 %1& , ’< 6 1& , .) 6
78: " #$ 1 *$ , 94 ’ ! " #$ , %& ’ /$ ; ( ;"== " 6#$ 。 球化剂的加入量应当保证石墨完全球化。在无稀土的情况下, 保证石墨完全球化的 残余镁量大致为 ! " !2$ 1 ! " !6$ ; 在有稀土的情况下, 残余镁量也大致为 ! " !2$ 1 ! > 残余稀土量为 ! " !/#$ 1 ! " !#$ 。几种常用球化剂的加入量可参见表 : ? 2 ? /#。 !!6$ 、 孕育剂的种类也较多, 可参用灰铸铁 (孕育铸铁) 用的孕育剂。 表 : ? 2 ? /#
把 试 片 悬 空 敲 击, 敲击声 检查 利用 球 铁 吸 震 性 差、 传音强的特点进行鉴 别
球化: 尖锐有韵如同钢声 衰球化鉴尖锐有韵但响声不长 不球化: 声音闷哑
・ !## ・
第二篇
方法名称
铸件配料实用技术
方法简述 球 化 鉴 别
球化 情况
火苗特征
火苗等级
良好
大于 !"## 的大火苗三个以上 小火苗多而有力
第二节
球墨铸铁的熔制特点及其配料
球墨铸铁
是铁液经过球化剂处理而不是经过热处理处理, 使石墨大部或全部呈球
状, 有时少量为团絮状的铸铁。但球墨铸铁经过一定的热处理却可改变基体的形式, 球 墨铸铁的基体形式有: 铁素体、 珠光体、 铁素体加珠光体、 贝氏体、 奥氏体加贝氏体。 球化前的铁液 (原铁液) 成分 (质量分数) 一般选择在共晶点附近, 以不出现石墨漂浮 为前提, 通常希望为高碳、 低硅、 低磷硫, 亦即: $- 4 *# 2 - 4 7# , %&3 6 .# 2 / 4 .# , ’(. 4 -# 8 9 . 4 3.# , % 9 . 4 .5# 。 2 . 4 7# , 经球化处理后的铁液还需进行孕育处理, 以消除球化元素所造成的白口倾向, 并同 时细化石墨球。球化孕育处理后的球墨铸铁 (质量分数) , %& 常被调整到 3 4 5# 2 - 4 -# , 控制在 . 4 .-# 2 . 4 .5# , 稀土氧化物残余量 ( ;<= >?残 ) 控制在 . 4 ./# 2 镁残余量 ( ’ :残 ) 都不希望太高。 . 4 .1# , 球墨铸铁除有类似于灰铸铁的良好减震性、 耐磨性、 切削加工性以及铸造工艺性外, 伸长率 还具有比普通灰铸铁高得多的强度、 塑性和韧性, 抗拉强度可达 3/.. 2 31*.’8@, 可达 3)# , 冲击韧度可达 0.A ! B"/ , 因此已用于生产受力复杂, 强度、 韧性和耐磨性等要 求较高的零件, 如汽车、 拖拉机、 内燃机等的曲轴、 凸轮轴, 还有通用机械的中压阀门等。
大火苗
球 化 后 的 铁 液, 在 补加 铁 液 搅 拌、 倒包 火 苗 检 查 法 时, 铁液表面有火苗 窜出, 这是镁蒸气逸 出燃烧的现象。火花 越多、 越 长、 越 有 力, 球化 越 好, 但在铁液 温度偏高时火苗有萎 缩现象 一般 良好
有一、 二个大火苗杂有十个 以上的小火苗产
中火苗
小于 $%## 的小火苗少而无力
小火苗
不球化
看不到火苗
无火苗
火花判别球化的方法
炉 前 快 速 金 相 检 查
以 直 径 !&" ’ &" 或 !(" ’ (" 试棒, 凝 固后 淬 水 冷 却, 在砂 轮上 磨 去 表 面, 经粗 磨和 抛 光, 用显微镜 观察。但 要 注 意, 由 于铸 件 比 试 棒 大, 试 棒球化级别要订的比 铸件高一些 按球化标准评级 此法可在 &#)* 内完成, 比较准确可靠
! " #$ , %& ’ ! " #$ , () ’ *, +, 余量; 稀土硅铁合金 +, 余量; 钇基重稀土硅铁镁合金 镁硅铁合金 含钡稀土 硅 铁 镁 合 金 工业纯镁 (重稀土) , -./5$ 1 :6$ 34*!$ 1 *#$ , 78#$ 1 6$ ; <8/$ 1 2$ , ( ;5$ 1 =$ , -./$ 1 2$ , 34*!$ 1 *#$ , ( ;#$ 1 :!$ , 34*#$ 1 #!$ , 78! " #$ , -.! 1 ! " 5$ ; -./0$ 1 20$ , 342#$ 1 *5$ , ()#$ 1 6$ , 78#$ 1 6$ , 94! 5$ ,