CA6140车床的拨叉夹具毕业设计论文
毕业设计论文CA6140车床拨叉(0408)零件的机械加工夹具设计
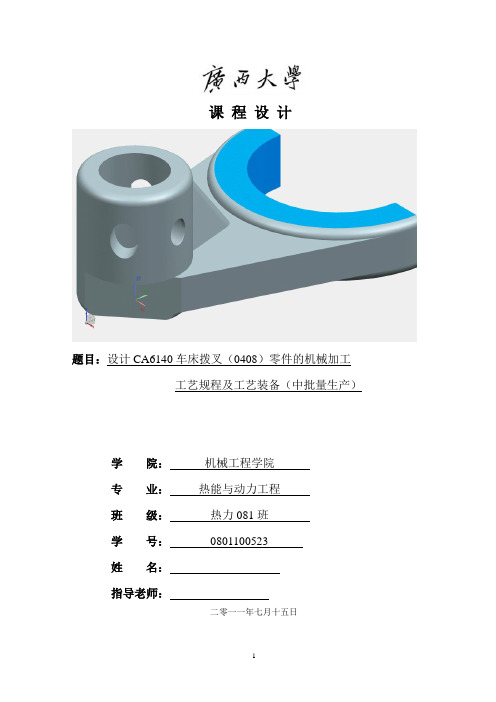
课程设计题目:设计CA6140车床拨叉(0408)零件的机械加工工艺规程及工艺装备(中批量生产)学院:机械工程学院专业:热能与动力工程班级:热力081班学号:0801100523姓名:指导老师:二零一一年七月十五日课程设计任务书题目:设计CA6140车床拨叉零件的机械加工工艺规程及工艺设备(中批量生产)院系、专业班级名称:学生姓名:指导教师:教研室主任:院长(系主任):2011年7月15日目录序言 (4)一.设计内容 (5)二.零件的分析 (5)(一)零件的作用 (5)(二)零件的工艺分析 (5)三、确定生产类型 (6)四、确定毛坯 (6)(一)确定毛坯种类 (6)(二)确定铸件加工余量及形状 (6)(三)绘制铸件毛坯图 (6)五、工艺规程设计 (6)(一)选择定位基准 (6)(二)制定工艺路线 (6)(三)机械加工余量、工序尺寸及公差的确定 (8)(四)确定切削用量及时间定额 (10)工序一 (10)工序二 (12)工序三 (19)工序四 (20)工序五 (23)工序六 (24)工序七 (26)工序八 (27)工序九 (27)工序十 (29)工序十一 (29)工序十二 (29)六.夹具的设计 (31)七、设计感言 (34)参考文献 (35)序言课程设计是我们机械学院学生进入大二下学期以后每个学期都必须要做的一节设计课程,虽然我们是热能与动力工程方向的专业,但是作为机械行业的学生,设计是必不可少的。
自进入大三专业分流以来,整个大三学年里面按照学院的教学要求我们的主要是学习任务是学习与汽车发动机及底盘相关方面的知识。
学校为了让我们懂得在学习的基础上更应该学会如何设计,并巩固大一大二所学的知识,加强基础知识的了解以及团队合作的能力,也为了让我们进行毕业设计之前对所学的各课程的知识进行一次深入性综合性的复习、总结和归纳,让我们有一次比较正规点的理论联系实际的训练,所以学院以我们学过的《机械制造技术基础》课为设计基础,并结合我们所有学过的知识开展了本次课程设计。
CA6140车床拨叉831006加工工艺规程及夹具设计毕业设计
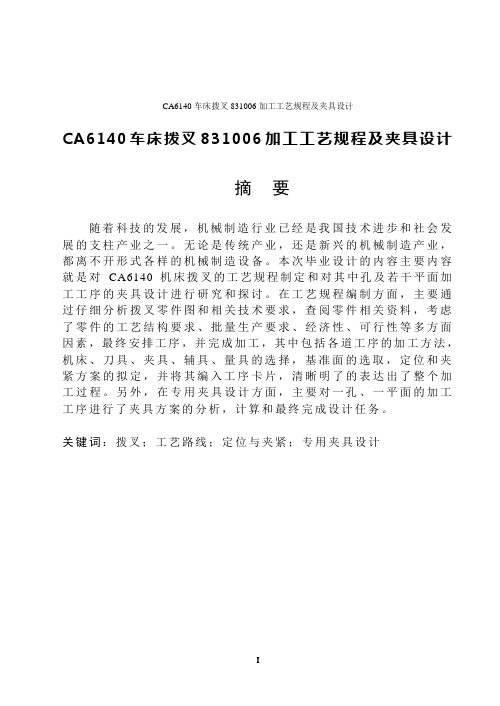
CA6140车床拨叉831006加工工艺规程及夹具设计CA6140车床拨叉831006加工工艺规程及夹具设计摘要随着科技的发展,机械制造行业已经是我国技术进步和社会发展的支柱产业之一。
无论是传统产业,还是新兴的机械制造产业,都离不开形式各样的机械制造设备。
本次毕业设计的内容主要内容就是对CA6140机床拨叉的工艺规程制定和对其中孔及若干平面加工工序的夹具设计进行研究和探讨。
在工艺规程编制方面,主要通过仔细分析拨叉零件图和相关技术要求,查阅零件相关资料,考虑了零件的工艺结构要求、批量生产要求、经济性、可行性等多方面因素,最终安排工序,并完成加工,其中包括各道工序的加工方法,机床、刀具、夹具、辅具、量具的选择,基准面的选取,定位和夹紧方案的拟定,并将其编入工序卡片,清晰明了的表达出了整个加工过程。
另外,在专用夹具设计方面,主要对一孔、一平面的加工工序进行了夹具方案的分析,计算和最终完成设计任务。
关键词:拨叉;工艺路线;定位与夹紧;专用夹具设计CA6140车床拨叉831006加工工艺规程及夹具设计AbstractWith the development of science and te chnology, machinery manufacturing industry of China has been technological progress and social development of pillar industries. Whether in traditional industries or new industries, it is inseparable from a wide range of machinery and equipment. This graduation of content which is the study about the protocol development process and the fixture design of the hole and some plane processing procedure. In terms of process rules, primarily through a careful analysis of the product parts and related technical requirements, check the parts relevant information considered part of the process of structural requirements, batch,and economics, feasibility, and more factors. The final arrangements for the operations to finish processing, includi ng the operations of processing method, machine tools, tooling, fixtures, assistive devices, measurement apparatus selection, select datum, positioning and clamp authoring, and process card, clarity of expression out the whole processing procedure. In addition, in fixture design, the main design about a hole, a flat and a groove machining process has been analysised, computation and finally to complete the design task.Key words: Plectrum; process route; positioning and clamping;dedicated fixture designCA6140车床拨叉831006加工工艺规程及夹具设计目录摘要 (I)Abstract (II)第1章绪论 (1)1.1 夹具设计的意义 (1)1.2 夹具设计研究概述 (2)1.2.1 夹具的定义 (2)1.2.2 夹具发展概况 (2)1.2.3 夹具设计要解决的主要问题 (3)1.3 夹具的功能 (4)1.4 夹具组成 (4)1.4.1 夹具的基本组成部分 (4)1.4.2 夹具的其他组成部分 (5)1.5 夹具的分类 (5)1.5.1 按夹具的通用特性分类 (5)1.5.2 按夹具使用的机床分类 (5)1.6 夹具使用优点 (7)1.7 夹具设计要求 (7)1.7.1 夹具设计基本要求 (7)1.7.2 生产对其提出的新要求 (8)1.8 夹具设计特点 (8)1.9 现代夹具的发展发向 (9)第2章工艺规程的编制 (10)2.1 零件的分析 (10)2.1.1 零件的作用 (10)2.1.2 零件的工艺分析 (11)2.2 确定毛坯的制造形式 (12)2.3 基面的选择 (13)CA6140车床拨叉831006加工工艺规程及夹具设计2.4 制定工艺路 (14)2.5 选择加工设备及刀具、夹具、量具 (15)2.6 机械加工余量、工序尺寸及毛坯尺寸的确定 (16)2.7 确立切削用量及基本工时 (19)第3章夹具设计 (37)3.1 工序30的夹具设计 (37)3.1.1 问题的提出 (37)3.1.2 夹具设计 (37)3.1.3 定位误差的分析 (40)3.1.4 夹具设计及操作的简要说明 (40)3.2 工序50的夹具设计 (40)3.2.1 问题的提出 (40)3.2.2 夹具设计 (41)3.2.3 定位误差的分析 (43)3.2.4 夹具设计及操作的简要说明 (43)3.3 工序70的夹具设计 (44)3.3.1 问题的提出 (44)3.3.2 夹具设计 (44)3.3.3 定位误差的分析 (47)3.3.4 夹具设计及操作的简要说明 (47)第4章机床夹具优化设计及经济效益 (48)4.1 优化设计分析 (48)4.1.1成组夹具成本 (48)4.1.2 优化设计的现实意义 (49)4.2 机床夹具柔性化 (49)4.3 机床夹具经济效益分析 (50)结论 (52)致谢 (53)参考文献 (1)CA6140车床拨叉831006加工工艺规程及夹具设计ContentsAbstract (Ⅰ)Chapter 1 Introduction (1)1.1 The significance of the fixture design (1)1.2 Fixture design research overview (2)1.2.1 The definition of a fixture (2)1.2.2 Fixture development (2)1.2.3 Design of jigs and fixtures to solve the mainproblems (3)1.3 Functions of fixtures (3)1.4 Fixture composition (4)1.4.1 The basic components of fixtures (4)1.4.2 The other component of the fixtures (4)1.5 Fixture of classification (5)1.5.1 According to the common characteristics ofclassification fixtures (5)1.5.2 The machine tool used by fixture classification (5)1.6 Use the advantages of fixtures (6)1.7 Design of machine-tool fixtures (7)1.7.1 Basic requirements for the design of fixtures (7)1.7.2 Production on his proposed new requirements (7)1.8 Fixture design characteristics (8)1.9 Development of modern fixtures sent to (9)Chapter 2 The compilation of procedures (10)2.1 Part of the analysis (10)2.1.1 Part of the role (10)2.1.2 Parts of the Process Analysis (11)2.2 Determine the form of blank manufacturing (12)CA6140车床拨叉831006加工工艺规程及夹具设计2.3 The choice of base level (13)2.4 Develop route (14)2.5 Select the processing equipment and tooling, fixtures,measuring tools (15)2.6 Allowance, dimensions and fur dimension (16)2.7 Establishment of cutting and basic work (19)Chapter 3 Fixture design (36)3.1 Fixture design of the third working procedure (37)3.1.1 Problem (37)3.1.2 Fixture design (40)3.1.3 The analysis of positioning error (40)3.1.4 Fixture design and a brief description of the operation (40)3.2 Fixture design of the fifth working procedure (40)3.2.1 Problem (40)3.2.2 Fixture design (41)3.2.3 The analysis of positioning error (43)3.2.4 Fixture design and a brief description of the operation (43)3.3 Fixture design of the seventh working procedure (44)3.3.1 Problem (44)3.3.2 Fixture design (44)3.3.3 The analysis of positioning error (47)3.3.4 Fixture design and a brief description of the operation . 47 Chapter 4 Fixture design optimization and economic benefits (48)4.1 Optimal Design and Analysis (48)4.1.1 Group fixture costs (48)4.1.2 The practical significance of design optimization (49)4.2 Flexible Machine Tool Fixture (49)4.3 Economic Analysis of jigs and fixtures (50)Conclusion (52)Thanks (53)References (54)CA6140车床拨叉831006加工工艺规程及夹具设计第1章绪论随着科学技术的高速发展,机械产品不断更新换代,其产品型号越来越多,质量要求越来越高,更新周期越来越短,使机械制造工程飞速的发展。
CA6140车床拨叉831007”零件的机械加工工艺规则及专用夹具设计
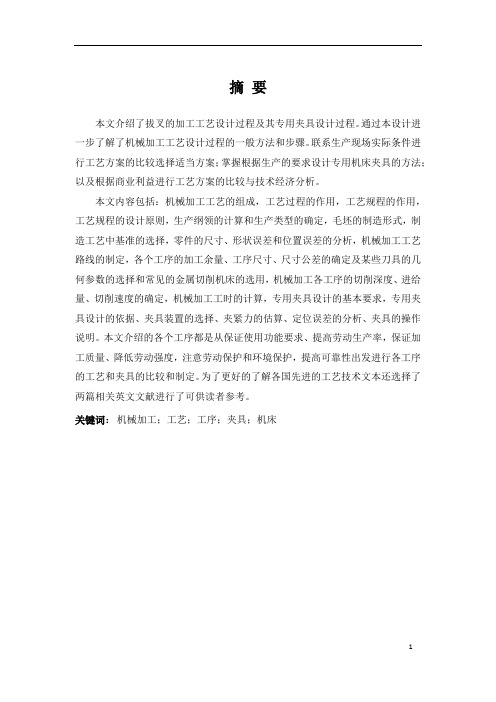
摘要本文介绍了拔叉的加工工艺设计过程及其专用夹具设计过程。
通过本设计进一步了解了机械加工工艺设计过程的一般方法和步骤。
联系生产现场实际条件进行工艺方案的比较选择适当方案;掌握根据生产的要求设计专用机床夹具的方法;以及根据商业利益进行工艺方案的比较与技术经济分析。
本文内容包括:机械加工工艺的组成,工艺过程的作用,工艺规程的作用,工艺规程的设计原则,生产纲领的计算和生产类型的确定,毛坯的制造形式,制造工艺中基准的选择,零件的尺寸、形状误差和位置误差的分析,机械加工工艺路线的制定,各个工序的加工余量、工序尺寸、尺寸公差的确定及某些刀具的几何参数的选择和常见的金属切削机床的选用,机械加工各工序的切削深度、进给量、切削速度的确定,机械加工工时的计算,专用夹具设计的基本要求,专用夹具设计的依据、夹具装置的选择、夹紧力的估算、定位误差的分析、夹具的操作说明。
本文介绍的各个工序都是从保证使用功能要求、提高劳动生产率,保证加工质量、降低劳动强度,注意劳动保护和环境保护,提高可靠性出发进行各工序的工艺和夹具的比较和制定。
为了更好的了解各国先进的工艺技术文本还选择了两篇相关英文文献进行了可供读者参考。
关键词:机械加工;工艺;工序;夹具;机床AbstractIn this paper, the fork off the design process and its dedicated fixture design process. Through the design of a better understanding of the engine machining process of the general process design methods and steps. Contact production at the scene of the actual conditions of the program compared select the appropriate programs; master in accordance with the requirements of the production design for the machine tool fixture methods and in accordance with commercial interests of the program compared with the technical and economic analysis.This article includes: the composition of mechanical processing technology, the role of process, the role of a point of order, the order of the design principles, the calculation of the Program of production and production types of identification, the rough form of manufacturing, manufacturing process in the choice of benchmarks, spare parts The size, shape and location of error of error, mechanical processing line of development, the various processes a gong , process size, Tolerance and the determination of certain tools and geometric parameters of common metal-cutting machine tools of choice , the basis for fixture design, the choice of fixture installation, the clamping force estimates, positioning error The analysis, fixture instructions. This paper describes the various processes are guaranteed from the use of functional requirements, raising labor productivity, and ensure processing quality, reduce labor intensity and attention to labor protection and environmental protection, to improve the reliability of the process and the process of comparison and the development of fixture. In order to better understand the countries of advanced technology has also selected the two texts related to English literature a reference for readers.Key words: Engine machining; process; processes; fixture; Machine目录摘要 (1)ABSTRACT (2)目录 (3)第一章绪论 (1)第二章概述 (2)2.1夹具夹紧装置及夹具体的基本要求 (2)2.2机床夹具功用 (3)2.3机床夹具在机械加工中的作用 (3)2.4机床夹具组成 (4)2.5机床夹具分类 (5)2.6机床夹具的设计要求 (7)第3章零件的分析 (8)3.1零件的作用 (9)3.2零件的工艺分析 (9)第4章工艺规程设计 (10)4.1确定毛坯的制造形式 (10)4.2基准的选择............................................................................... 错误!未定义书签。
河南工学院2007级毕业论文-C6140拨叉加工工艺及其夹具设计
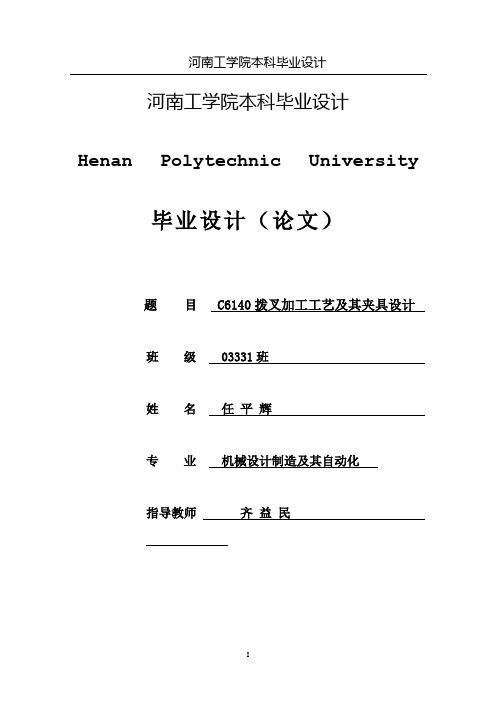
河南工学院本科毕业设计Henan Polytechnic University 毕业设计(论文)题目 C6140拨叉加工工艺及其夹具设计班级 03331班姓名任平辉专业机械设计制造及其自动化指导教师齐益民河南工学院机械工程系2007届毕业生毕业设计任务书二零零七年十月姓名:任平辉班级:03331班专业:机械设计制造及其自动化学号:0703331设计题目: C6140拨叉加工工艺及其夹具设计进度安排:摘要此次设计任务是对拔叉零件的加工工艺、夹具以及拉刀设计,该工件由于上端面和底槽均与花键孔中心有位置关系,因此在工序安排上,先加工花键孔,再通过花键孔定位加工底槽和上端面,最后攻螺纹孔,其中各种夹具均采用专用夹具,由于该零件的尺寸小,所需的夹紧力不大,因此都采用手动夹紧,它的机构设计简单、方便,且满足夹紧要求。
在设计拉刀时,根据零件材料、切削余量等,选择并计算拉刀的各种参数,如拉刀的容屑槽、拉刀齿升量、拉刀齿型及齿数等并根据这些参数画出拉刀工作图。
关键词拔叉,加工工艺,定位,夹紧,拉刀车床河南工学院本科毕业设计 1 绪论1 绪论夹具设计作为高等工科院校教学的基本训练科目,在毕业设计中占极其重要的位置。
夹具结构设计在加深对课程基本理论的理解和加强对解决工程实际问题能力的培养方面发挥着极其重要的作用。
因此,选择拨叉的夹具设计能很好的综合考查我们大学四年来所学知识。
本次所选拔叉的工艺分析及夹具设计内容主要包括:拔叉工艺路线的确定,夹具方案的优选,装配图、零件图的绘制以及拉刀设计,设计说明书的编写等。
夹具是工艺装备的主要组合部分,在机械制造中占有重要地位,夹具对保证产品质量,提高生产率,减轻劳动强度,缩短产品生产周期等都具有重要意义。
随着先进制造技术的发展和市场竞争的加剧,传统的夹具设计方式已成为企业中产品快速上市的瓶颈,各企业迫切需要提高夹具设计的效率。
刀具行业是一个比较特殊的行业,肩负着为制造业提供关键装备、数控刀具的重任,制造业的水平如何往往会受刀具行业整体水平的较大影响,而制造业的发展也会促进刀具行业的发展,两者可以说是相互影响相互制约。
CA6140车床拨叉(831003)零件的机械加工工艺规程及夹具毕业设计论文
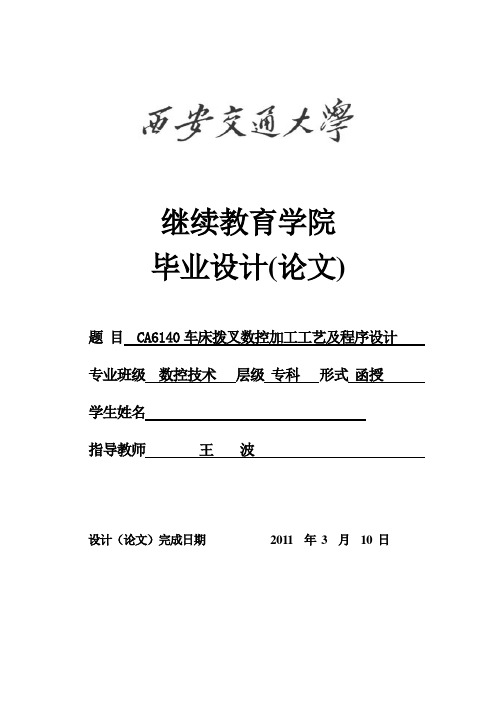
继续教育学院毕业设计(论文)题目 CA6140车床拨叉数控加工工艺及程序设计专业班级数控技术层级专科形式函授学生姓名指导教师王波设计(论文)完成日期2011 年3 月10 日继续教育学院毕业设计︵论文︶学生姓名:日期: 2011年3月27日摘要CA6140车床拨叉它位于车床变速机构中主要起换档,和其他零件配合,在改变转速的时候承受轻微的载荷,所以加工时应该保证本零件的重要工作表面符合技术要求。
对于零件而言,尽可能选择不加工表面作为粗基准。
而对有若干个不加工表面的工件,则应以加工表面要求相对位置精度较高的不加工表面作粗基准。
因此φ60孔端面与φ25H7孔垂直度公差为0.1mm,所以先把加工φ25孔的表面和孔精加工出来,再以它为精基准加工别的面,例如铣φ60孔和端面、铣槽等。
同时,在设计夹具时候要考虑定位基准和加紧机构。
在设计中长销限制4个自由度、支撑钉限制1个和侧板限制1个;螺母和心轴配合用来加紧零件,开口垫片可以实现大批量和中批量的生产。
关键词:定位元件加紧机构定为基准自由度CA6140车床拨叉数控加工工艺及程序设计目录1前言……………………………………………………………………………2. 设计的目的……………………………………………………………3. 零件的分析……………………………………………………………3.1 零件的作用…………………………………………………………3.2 零件的工艺分析……………………………………………………4. 工艺规程设计…………………………………………………………4.1 确定毛坯的制造形式…………………………………………4.1.1 铸铁……………………………………………………………4.2 基准的选择………………………………………………………4.3 制造工艺路线……………………………………………………4.3.1 切削力…………………………………………………………4.3.2 刀具磨损与刀具的耐用度………………………………4.3.3 切削用量……………………………………………………5. 箱体的技术要求……………………………………………………6. 夹具设计………………………………………………………………6.1 夹具的作用…………………………………………………………6.2 问题的提出………………………………………………………6.3 夹具的设计……………………………………………………… 7小结…………………………………………………………………………致谢………………………………………………………………………………参考文献………………………………………………………………………1前言通过机床工艺及程序设计,汇总所学专业知识如一体(如《公差于配合》、《机械零件设计》、《金属切削机床》、《机械制造工艺》、《机械制造基础》、《数控加工工艺》、《机械制图》等)。
CA6140开合螺母加工工艺及夹具设计毕业设计论文

CA6140开合螺母加工工艺及夹具设计毕业设计论文标题:CA6140开合螺母加工工艺及夹具设计摘要:本论文以CA6140型车床加工开合螺母为研究对象,通过对该螺母的工艺流程进行分析,设计了相应的夹具,提出了一种适用于该螺母加工的高效、稳定的方法。
通过实验验证,该工艺和夹具设计方案在加工效率、精度和质量方面有良好的表现。
关键词:开合螺母;加工工艺;夹具设计;CA6140;车床一、引言开合螺母在现代制造业中起着重要的作用,广泛应用于航空航天、机械制造、汽车工业等领域。
然而,由于其结构特殊,加工过程对设备和工艺要求较高,因此需要针对其特点进行有效的加工工艺和夹具设计。
二、CA6140开合螺母加工工艺分析1.加工工艺流程分析2.设备选择与调整3.切削参数的确定4.冷却液的选择与使用三、CA6140开合螺母夹具设计1.夹具种类选择2.夹具结构设计3.夹具材料选择4.夹具加工工艺四、CA6140开合螺母加工工艺与夹具设计实验验证1.实验目的2.实验装置与工艺条件3.实验结果与分析4.实验结论五、总结与展望通过对CA6140开合螺母加工工艺和夹具设计的研究,本论文提出了一种高效、稳定的加工方法和相应夹具设计方案。
通过实验验证,该方法在加工效率、精度和质量方面均有较好的表现。
但与现有技术相比,仍需要进一步研究和改进。
未来的研究可以在加工工艺和夹具设计方面进行更深入的探索,以提高加工效率和质量。
[1]XXX.螺纹车削技术与应用[M].北京:机械工业出版社。
[2]XXX.工程制图与CAD[M].北京:中国冶金工业出版社。
[3]XXX.螺纹加工工艺与技术[M].北京:机械工业出版社。
CA6140数控机床毕业设计论文

目录摘要 .............................................................................................................. 错误!未定义书签。
Abstract (2)第1章绪论 (3)1.1 工程背景与意义 (3)1.2 国内外的应用现状及发展趋势 (3)1.3 本课题研究内容 (4)1.3.1 CA6140普通卧式车床知识简介 (4)1.3.2 设计重点 (6)第2章传动方案设计 (7)2.1 确定结构方案 (7)2.2 确定基本参数 (7)2.3 主运动链转速图的拟定 (8)2.3.1 传动组和传动副数目得确定 (8)2.3.2 结构网各种方案的选择 (8)2.3.3 绘制转速图 (9)2.4 齿轮齿数的确定 (11)2.5 绘制传动系统图 (12)2.6 确定各轴转速 (12)2.6.1 确定主轴计算转速 (12)2.6.2 各传动轴的计算转速 (13)2.6.3 各齿轮的计算转速 (13)2.7 验算主轴转速误差 (13)第3章传动原件设计 (14)3.1 带传动设计 (14)3.2 齿轮设计 (15)3.2.1 齿轮材料选择 (15)3.2.2 模数计算 (16)3.2.3 齿轮的几何尺寸 (17)3.2.4 齿轮的结构设计和布局 (18)3.3 各轴径的设计 (19)3.3.1 选材 (19)3.3.2 轴上零件的定位 (19)3.3.3 各轴最小直径 (19)3.3.4 各轴几何尺寸的确定 (20)3.4 键的设计 (20)3.5 其他零部件的选取 (21)第4章结构设计 (22)第5章传动件的校核 (23)5.1 齿轮的校核 (23)5.2 轴承的校核 (25)5.3 键的校核 (25)5.4 轴的校核 (26)5.4.1 传动轴的校核 (26)5.4.2 主轴的校核 (26)第6章结论 (28)总结 (29)致谢 (30)参考文献 (31)附录 (32)摘要作为主要的车削加工机床,CA6140机床广泛应用于机械加工行业中,适用于车削内外圆柱面,圆锥面及其它旋转面,车削各种公制、英制、模数和径节螺纹,并能进行钻孔,铰孔和拉油槽等工作。
CA6140杠杆加工工艺及夹具设计本科毕业设计论文
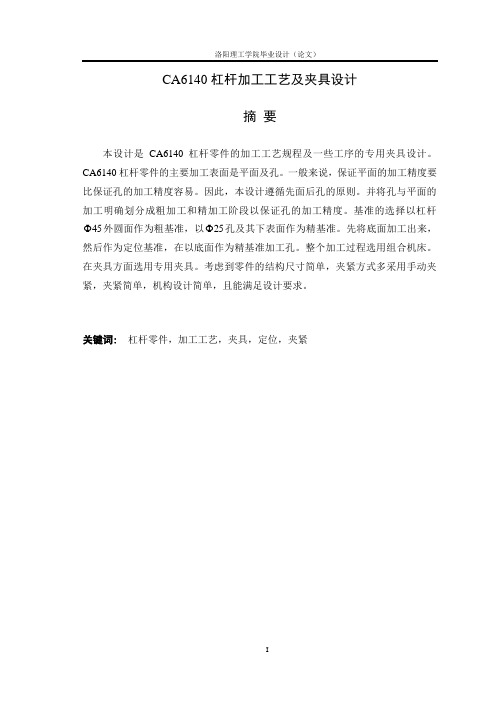
CA6140杠杆加工工艺及夹具设计摘要本设计是CA6140杠杆零件的加工工艺规程及一些工序的专用夹具设计。
CA6140杠杆零件的主要加工表面是平面及孔。
一般来说,保证平面的加工精度要比保证孔的加工精度容易。
因此,本设计遵循先面后孔的原则。
并将孔与平面的加工明确划分成粗加工和精加工阶段以保证孔的加工精度。
基准的选择以杠杆Φ孔及其下表面作为精基准。
先将底面加工出来,45Φ外圆面作为粗基准,以25然后作为定位基准,在以底面作为精基准加工孔。
整个加工过程选用组合机床。
在夹具方面选用专用夹具。
考虑到零件的结构尺寸简单,夹紧方式多采用手动夹紧,夹紧简单,机构设计简单,且能满足设计要求。
关键词:杠杆零件,加工工艺,夹具,定位,夹紧CA6140 Release Lever Processing Craft and Jig DesignABSTRACTThis paper is to design the craft processes of making the CA6140 lever spare parts and some specialized tongs in the process. The CA6140 lever spare part primarily processes the surface and bores. Generally speaking, to guarantee the accuracy of the flat surface process is easier than that of the bore. Therefore, this design follows the principle that surface first and then the bore, and definitely divides the process of flat surface and bore into coarse processes and precise processes to guarantee the bore processes. The basic choice is to consider 45 outside circle as rough basis and to consider 25 bore and its next surface as precise basis. The bottom is first processed out to be fixed position basis, and process the bore using the bottom as the precise basis. The whole processes choose the machine bed. In the aspects of tongs choosing, specialized tongs are used. In consideration of the simple construction size of the spare parts, clipping by hands is adopted. It is simple, and the organization design is simple, and can satisfy the design request.KEY WORDS:Lever spare parts, Craft proces , Tongs, Fixed position, Tight clip毕业设计(论文)原创性声明和使用授权说明原创性声明本人郑重承诺:所呈交的毕业设计(论文),是我个人在指导教师的指导下进行的研究工作及取得的成果。
CA6140车床拨叉加工工艺及铣Φ22孔上端面夹具毕业设计论文
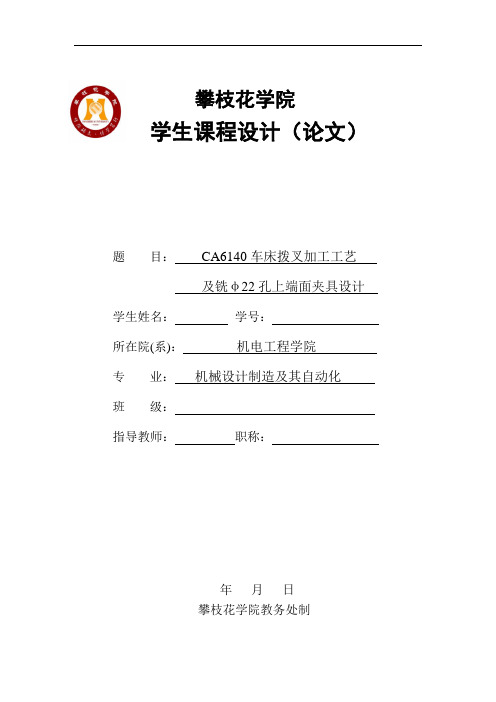
攀枝花学院学生课程设计(论文)题目:CA6140车床拨叉加工工艺及铣φ22孔上端面夹具设计学生姓名:学号:所在院(系):机电工程学院专业:机械设计制造及其自动化班级:指导教师:职称:年月日攀枝花学院教务处制攀枝花学院本科学生课程设计任务书注:任务书由指导教师填写。
课程设计(论文)指导教师成绩评定表目录序言 .................................................................................................................................................. 2 1 零件的分析 (3)1.1零件的作用 ......................................................................................................................... 3 1.2零件的工艺分析 ................................................................................................................. 3 2 工艺规程设计 .. (4)2.1确定毛坯的制造形式 ......................................................................................................... 4 2.2基面的选择 ......................................................................................................................... 4 2.3制定工艺路线 ..................................................................................................................... 4 2.4机械加工余量、工序尺寸及毛坯尺寸的确定 ................................................................. 7 3 切削用量及时间定额 . (9)3.1粗铣φ22孔上端面 ........................................................................................................... 9 3.2扩φ22孔 .......................................................................................................................... 9 3.3精铣φ22孔上端面 ........................................................................................................ 10 3.4精铰φ22孔 .................................................................................................................... 10 3.5粗镗、半精镗φ55孔 ..................................................................................................... 10 3.6粗镗、半精镗73孔 .. (11)3.7 钻8M 螺纹孔、攻8M 螺纹、钻8 锥销孔 .............................................................. 13 3.8铣断 .................................................................................................................................. 14 4 夹具设计. (15)3.1问题的提出 ....................................................................................................................... 15 3.2夹具设计 ........................................................................................................................... 15 设计总结......................................................................................................................................... 17 参考文献.. (18)序言机械制造工艺学课程设计是我们学完了大学的全部基础课、技术基础课以及大部分专业课之后进行的.这是我们在进行毕业设计之前对所学各课程的一次深入的综合性的总复习。
ca6140拨叉夹具设计课程设计
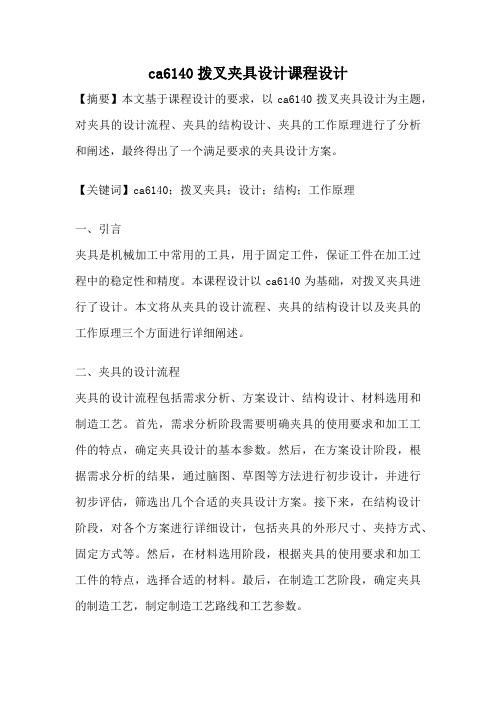
ca6140拨叉夹具设计课程设计【摘要】本文基于课程设计的要求,以ca6140拨叉夹具设计为主题,对夹具的设计流程、夹具的结构设计、夹具的工作原理进行了分析和阐述,最终得出了一个满足要求的夹具设计方案。
【关键词】ca6140;拨叉夹具;设计;结构;工作原理一、引言夹具是机械加工中常用的工具,用于固定工件,保证工件在加工过程中的稳定性和精度。
本课程设计以ca6140为基础,对拨叉夹具进行了设计。
本文将从夹具的设计流程、夹具的结构设计以及夹具的工作原理三个方面进行详细阐述。
二、夹具的设计流程夹具的设计流程包括需求分析、方案设计、结构设计、材料选用和制造工艺。
首先,需求分析阶段需要明确夹具的使用要求和加工工件的特点,确定夹具设计的基本参数。
然后,在方案设计阶段,根据需求分析的结果,通过脑图、草图等方法进行初步设计,并进行初步评估,筛选出几个合适的夹具设计方案。
接下来,在结构设计阶段,对各个方案进行详细设计,包括夹具的外形尺寸、夹持方式、固定方式等。
然后,在材料选用阶段,根据夹具的使用要求和加工工件的特点,选择合适的材料。
最后,在制造工艺阶段,确定夹具的制造工艺,制定制造工艺路线和工艺参数。
三、夹具的结构设计夹具的结构设计是夹具设计的核心环节,直接关系到夹具的使用效果和加工精度。
拨叉夹具是一种常用的夹具类型,适用于固定圆柱形工件。
其结构主要包括底座、定位销、拨叉、夹紧螺杆和夹具座等部分。
底座是夹具的主体部分,用于固定夹具的其他组件。
定位销用于固定工件的位置,保证工件的定位精度。
拨叉是夹具的核心部件,用于夹持工件。
夹紧螺杆用于调整夹具的夹持力,保证工件在加工过程中的稳定性。
夹具座用于固定夹具的位置,保证夹具的稳定性。
四、夹具的工作原理拨叉夹具的工作原理是通过拨叉的运动来实现工件的夹持和释放。
在夹具使用过程中,首先将工件放置在夹具座上,并通过定位销对工件进行定位。
然后,通过调整夹紧螺杆,使得拨叉夹持住工件。
CA6140车床拨叉的加工工艺及夹具毕业设计论文

拨叉(CA6140车床)夹具设计

结合生产实际,备品率a%和废品率b%分别取3%和0.5%,则年产纲领 拨叉重量为1.12kg,查表2-1知,拨叉属轻型零件,生产类型为大批生产。
表2-2不同机械产品的零件质量型别表
表2-3机械加工零件生产类型的划分
表2-3生产类型
三、
(一)
1、求最大轮廓尺寸
根据零件图确定轮廓尺寸:长约为155.5mm,宽为75mm,高位80mm,故最大轮廓尺寸为155.5mm。
5、求RMA(要求的机械加工余量)
对所有加工表面取同一个数值,由表5-4查最大轮廓尺寸为155.5mm、机械加工余量等级为F级,RMA数值为1.5mm。
6、求毛坯基本尺寸
1拨叉头侧面单侧加工由式5-1求出,即
,因为拨叉头外圆半径为
20mm,因此压铸时外圆铸完整,外圆槽完全机加工做出。
2拨叉脚两端面双侧加工由式5-2求出,即
表4-2工艺路线
工序号
工序名称
机床设备
刀具
量具
负责人
1
铸件表面处理
钳工台
锤子、锉刀
卡尺
2
退火
3
扩、铰 孔
立式钻床
扩孔钻、铰刀
卡尺、赛规
汪帅兵
4
粗铣拨叉脚两端面
卧式双面铣床
卧式双面铣床铣刀
游标卡尺
沈博文
5
粗铣拨叉脚顶面、内侧面
铣床
铣刀
游标卡尺、赛规
吴家文
6
粗铣、半精铣拨叉头侧面
立式铣床
立铣刀
游标卡尺
刘露淳
该拨叉在改换档位时要承受弯曲应力和冲击载荷的作用,因此该零件应具有足够的强度、刚度和韧性,以适应拨叉的工作条件。该零件的主要工作表面为拨叉脚两端面、叉轴孔φ250-0.03mm(H7),在设计工艺规程时应重点予以保证。
CA6140主轴加工工艺及夹具毕业设计
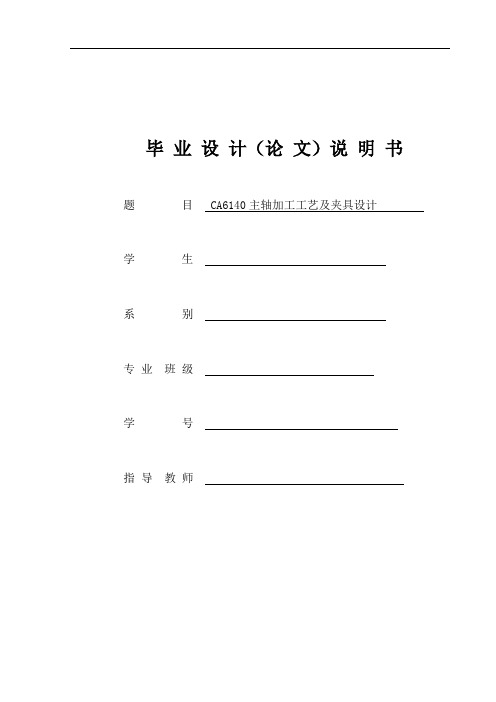
第三阶段:以两端面支承轴颈为基准,钻通孔、车、磨小端面锥孔(配 锥堵),车、磨大端锥孔(配莫氏 号锥堵)。
第二章工艺规程的设计
2.1确定毛坯的制造形式
零件材料为 钢。 主轴在机床运行中要起到传递功率的作用,则其在工作过程中,经常受到扭矩作用,由于零件年生产量为 件,已达到大批量生产的水平,而且零件的轮廓尺寸不太大。故可采用模锻成型,且为胎膜锻。它的毛坯精度较高,加工余量较小,对提高生产率,保证加工质量也是有利的。
2.2基准的选择
2.2.1
为取得两中心孔作为精加工的定位基准,所以机械加工的第一道工序是铣两端面中心孔。为此可选择前、后支承轴颈(或其近处的外圆表面)作为粗基准。这样,当反过来再用中心孔定位,加工支承轴颈时,可以获得均匀的加工余量,有利于保证这两个高精度轴颈的加工精度。
主轴轴颈对支承轴颈的跳动公差,用标准检验棒检查时,在近主轴端处不大于 :在离主轴端 处不大于 。其他定位表面对支承轴颈的同轴度、平行度或垂直度公差一般为 。
1.2.1.3
1.2.2
CA6140车床主轴结构较为复杂,精度要求也较高,在大批量的生产条件下,主轴的机械加工工艺过程有三组加工表面。
第一阶段:以毛坯外圆为基准,车 和 的端面及钻中心孔。
就我个人而言,我希望能通过这次课程设计对自己未来将从事的工作进行一次适应性训练,从中锻炼自己分析问题、解决问题的能力,为今后参加祖国的建设打下一个良好的基础。
由于能力所限,设计尚有许多不足之处,恳请各位老师给予指导。
第一章零件的分析
1.1
本次设位于主轴箱部,主要作用是传递回转和扭矩。电动机的回转运动和扭矩是通过各级变速齿轮等传递到主轴,再通过主轴传递给工件或刀具的。主轴必须具有较高的回转精度,以保证工件几何形状的正确;为机床附件和有关工艺装备提供安装基面,直接或间接地支持和导向作用;当棒料(毛坯)需从主轴中心通孔通过作贯穿送料时,主轴内孔还具有支承作用。
CA6140拨叉加工工艺及夹具设计

摘 要 本设计是车床拨叉零件的加工工艺及专用夹具设计。
从零件的结构外型分析,它的外型复杂,且不易加工,因此该零件选用铸造件。
它的主要加工面是孔、拨叉叉口两端面和槽,在设计中采用先面后孔的原则,先以一个面加工出一个基准面,然后,再以该基准面加工相应的孔。
在后面的工序中,均以该孔为定位基准,加工其他部位,在整个加工过程中,分别采用了铣床、钻床和镗床。
按要求设计了镗孔专用夹具,采用一面两销定位。
由于该零件的尺寸不大,所需的夹紧力不大。
因此,夹紧方式都采用手动夹紧,它的夹紧简单,机构的设计更为方便,满足夹紧要求。
关键词: 拨叉,加工工艺,专用夹具,定位 The plectrum parts processing and special fixtureDesigns to the lathe of CA 6140AbstractThis design is a lather plectrum parts processing and special fixture designs. Appearance from the analysis of the structure of parts, it looks complicated and difficult process, the choice of casting parts. Its main processing side holes at both ends of fork surface and groove, used in the design after the first hole of the principle of surface, first with a surface of a base-level processing, and then base-level processing of the corresponding hole. Behind the processes, are the base of the hole for positioning, processing other parts of the body, in the whole process, namely the use of a milling machine, drilling and boring m achine Required to design a special jig boring, using a two-pin position. Due to the size of the parts do not, the clamping force is not required. Therefore, the clamping means are manually clamping, clamping it simple, more convenient for the design of institutions to meet the requirements clamping.Keywords:Fork,Processing, Technology, Dedicated fixture, Positioning目录1 绪论 (3)2 概述 (3)2.1 选题的目的和意义 (3)2.2 国内外研究现状及发展趋势 (3)3 零件的分析 (4)3.1 零件的作用 (4)3.2 零件的工艺分析 (4)3.3 本章小结 (5)4 工艺规程设计 (5)4.1 确定毛坯的制造形式 (5)4.2 基面的选择 (6)4.2.1 粗基准的选择 (6)4.2.2精基准的选择。
ca6140车床拔叉零件机械加工规程及夹具设计

编号:SMXP-7.5.1-P60-R002 日期:年月日山西机电职业技术学院毕业设计(论文)题目CA6140车床拨叉零件的机械加工工艺规程及夹具设计指导教师。
系部机械工程系专业机械制造及其自动化姓名刘小保学号101103102012年 4 月19 日毕业作品、毕业设计(论文)任务书题目CA6140车床拨叉零件的机械加工工艺规程及夹具设计学生姓名。
学号专业班级机电一体化联系方式指导老师指导老师联系方式一、课题背景:结合我国实际国情,经济型数控车床是我国从普通车床向数控车床发展的及其重要的台阶。
利用现有的普通车床,对其进行机械加工是一条低成本,高效益的途径。
机械车床作为机电一体化的典型产品,在机械制造业中发挥着巨大的作用,很好地解决了现代机械制造中结构复杂、精密、批量小、多变零件的加工问题,且能稳定产品的加工质量,大幅度地提高生产效率。
二、设计要求:论理正确、逻辑性强、文理通顺、层次分明、表达确切,把实践结果上升到理论认识或应用理论的高度,最终解决实际问题,并提出自己的见解和观点;三、计划进度:(按周制订计划,六周完成任务)1.设计的目的2.零件的分析3.工艺规程设计4. 确定切削用量及基本工时5. 夹具设计主要参考文献:[1]孙巳德主编,《机床夹具图册》,机械工业出版社,2002年版[2] 赵家齐主编,《机械制造工艺学课程设计指导书》,哈尔滨工业大学,2000年版[3] 艾兴,肖诗纲主编,《切削用量简明手册》,机械工业出版社,2005年版[4] 李益民主编,《机械制造工艺设计简明手册》,哈尔滨工业大学,2000版[5] 王先逵主编,《机械制造工艺学》,清华大学,2002版等等。
指导教师签名:年月日CA6140车床拨叉零件的机械加工工艺规程及夹具设计【摘要】针对现有常规CA6140普遍车床拔插零件的加工工艺,从而提高加工精度和扩大机床使用范围,并提高生产率。
本论文说明了普通车床的拔插零件的机械加工的设计过程,较详尽地介绍了CA6140车床拨叉零件的机械加工工艺规程及夹具设计。
CA6140拨叉831008零件的夹具设计
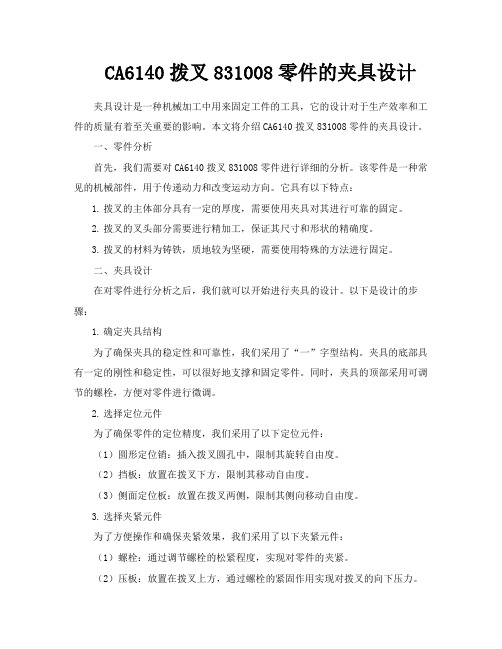
CA6140拨叉831008零件的夹具设计夹具设计是一种机械加工中用来固定工件的工具,它的设计对于生产效率和工件的质量有着至关重要的影响。
本文将介绍CA6140拨叉831008零件的夹具设计。
一、零件分析首先,我们需要对CA6140拨叉831008零件进行详细的分析。
该零件是一种常见的机械部件,用于传递动力和改变运动方向。
它具有以下特点:1.拨叉的主体部分具有一定的厚度,需要使用夹具对其进行可靠的固定。
2.拨叉的叉头部分需要进行精加工,保证其尺寸和形状的精确度。
3.拨叉的材料为铸铁,质地较为坚硬,需要使用特殊的方法进行固定。
二、夹具设计在对零件进行分析之后,我们就可以开始进行夹具的设计。
以下是设计的步骤:1.确定夹具结构为了确保夹具的稳定性和可靠性,我们采用了“一”字型结构。
夹具的底部具有一定的刚性和稳定性,可以很好地支撑和固定零件。
同时,夹具的顶部采用可调节的螺栓,方便对零件进行微调。
2.选择定位元件为了确保零件的定位精度,我们采用了以下定位元件:(1)圆形定位销:插入拨叉圆孔中,限制其旋转自由度。
(2)挡板:放置在拨叉下方,限制其移动自由度。
(3)侧面定位板:放置在拨叉两侧,限制其侧向移动自由度。
3.选择夹紧元件为了方便操作和确保夹紧效果,我们采用了以下夹紧元件:(1)螺栓:通过调节螺栓的松紧程度,实现对零件的夹紧。
(2)压板:放置在拨叉上方,通过螺栓的紧固作用实现对拨叉的向下压力。
4.设计辅助元件为了确保夹具使用的稳定性和方便性,我们设计了以下辅助元件:(1)垫片:放置在夹具和零件之间,增加接触面积,减少压痕。
(2)润滑剂:涂抹在接触表面,减小摩擦阻力,方便零件的移动和旋转。
(3)清洁剂:用来清除零件表面的杂质和污垢,保证夹具和零件的接触面积。
5.校验夹具可靠性夹具设计完成后,我们需要对其进行校验,确保其可靠性。
我们采用了实验的方法,将拨叉放置在夹具中,通过模拟加工过程中的受力情况,对其进行了可靠性验证。
- 1、下载文档前请自行甄别文档内容的完整性,平台不提供额外的编辑、内容补充、找答案等附加服务。
- 2、"仅部分预览"的文档,不可在线预览部分如存在完整性等问题,可反馈申请退款(可完整预览的文档不适用该条件!)。
- 3、如文档侵犯您的权益,请联系客服反馈,我们会尽快为您处理(人工客服工作时间:9:00-18:30)。
2.4机械加工余量、工序尺寸及毛坯尺寸的确定············································································5
1.1零件的作用
题目所给的零件是CA6140车床的拨叉。它位于车床变速机构中,主要起换档,使主轴回转运动按照工作者的要求工作,获得所需的速度和扭矩的作用。零件上方的φ20孔与操纵机构相连,二下方的φ50半孔则是用于与所控制齿轮所在的轴接触。通过上方的力拨动下方的齿轮变速。两件零件铸为一体,加工时分开。
3.1绘制零件图·················································································································பைடு நூலகம்·················11
3. 2编制工艺文件·································································································································11
2.1毛坯的制造形式···························································································································3
2.2基准面的选择································································································································3
2.2.2精基准的选择。主要应该考虑基准重合的问题。当设计基准与工序基准不重合时,应该进行尺寸换算,这在以后还要专门计算,此处不再重复。
2..3制定工艺路线
制定工艺路线的出发点,应当是使零件的几何形状、尺寸精度及位置精度等技术要求能得到合理的保证。在生产纲领已确定为中批生产的条件下,可以考虑采用万能性机床配以专用夹具,并尽量使工序集中来提高生产率。除此以外,还应当考虑经济效果,以便使生产成本尽量下降。
2.5确定切削用量及基本工时············································································································6
3绘制零件图和编制工艺卡············································································································10
工序五:以Ф20 mm的下表面为精基准,粗、半精镗Ф50 mm的孔,保证其内表面粗糙度为3.2 um
工序六;以Ф20 mm的下表面为精基准,粗、精铣Ф50 mm的上表面,保证其与孔的垂直度误差不超过0.07mm,其上、下表面尺寸为12mm
工序七:铣断
工序八:以Ф20 mm的孔为精基准,钻Ф8 mm的锥孔的一半Ф4 mm,装配时钻铰
4.2.4夹具设计及操作的简要说明·····························································································15
5结论·····················································································································································16
这一组加工表面包括:φ50 的孔,以及其上下两个端面。
这两组表面有一定的位置度要求,即φ50 的孔上下两个端面与φ20 的孔有垂直度要求。
由上面分析可知,加工时应先加工一组表面,再以这组加工后表面为基准加工另外一组。
2. 工艺规程设计
2.1毛坯的制造形式
零件材料为HT200,考虑零件在机床运行过程中所受冲击不大,零件结构又比较简单,故选择铸件毛坯。 图一毛坯图
1.2零件的工艺分析····························································································································2
2工艺规程的设计·······························································································································3
4夹具设计···········································································································································13
4.1问题的提出·································································································································13
1.2零件的工艺分析
CA6140车床共有两处加工表面,其间有一定位置要求。分述如下:
1.以φ20为中心的加工表面
这一组加工表面包括:φ20 的孔,以及其上下端面,上端面与孔有位置要求,孔壁上有一个装配时钻铰的锥孔,一个M8的螺纹孔。下端有一个47°的斜凸台。这三个都没有高的位置度要求。
2.以φ50为中心的加工表面
在选择各表面、内花键及槽的加工方法时,要综合考虑以下因素:
(1)要考虑加工表面的精度和表面质量要求,根据各加工表面的技术要求,选择加工方法及分几次加工。
(2)根据生产类型选择,在大批量生产中可专用的高效率的设备。在单件小批量生产中则常用通用设备和一般的加工方法。
(3)考虑被加工材料的性质。
(4)考虑工厂或车间的实际情况,同时也应考虑不断改进现有加工方法和设备,推广新技术,提高工艺水平。
零件材料为HT200。考虑零件在机床运行过程中所受冲击不大,零件结构又比较简单,故选择铸件毛坯。
2.2基准面的选择
一个好的机构不但应该达到设计要求,而且要有好的机械加工工艺性,也就是要有加工的可能性,要便于加工,要能保证加工的质量,同时是加工的劳动量最小。设计和工艺是密切相关的,又是相辅相成的。对于设计拨叉的加工工艺来说,应选择能够满足内花键加工精度要求的加工方法及设备。除了从加工精度和加工效率两方面考虑以外,也要适当考虑经济因素。在满足精度要求及生产率的条件下,应选择价格低的机床。
4.2夹具体设计·································································································································13
4.2.1定位基准的选择·················································································································13
6致谢·····················································································································································16
2.2.1粗基准的选择······················································································································4
2.2.2精基准的选择······················································································································4
4.2.2切削力及夹紧力的计算·····································································································13
4.2.3定位误差分析·····················································································································15
1、工艺路线方案一:
工序一:退火
工序二:粗、精铣Ф20 mm、Ф50 mm的下表面,保证其粗糙度为3.2 um
工序三:以Ф20 mm的下表面为精基准,粗、精铣Ф20 mm的孔的上表面,保证其粗糙度为3.2 um,其上、下表面尺寸为30mm,