生产件批准流程图
生产件批准程序PPAP(PPT 64张)

第1部分-总则
下列情况,组织必须获得经授权的顾客代表的
批准:
1. 一种新的零件或产品(即:以前未曾提供给某个 顾客的某种零件、材料、或颜色)。 2. 对以前所提供不符合零件的纠正。 3. 由于设计记录、规范或材料方面的工程变更从而 引起产品的改变。 4. 第3部分要求中的任一种情况。
制方法,并符合顾客规定的要求(例如《先期产品质 量策划和控制计划》参考手册)。 如果组织对新零件的通用性已经过评审,那么相似零 件的“零件家族”控制计划是可以接受的。 考虑设计 FMEA 和制造过程 FMEA 的输出制定试生产和生 产控制计划,控制计划中必须包括对顾客和组织确定 的特殊特性的所采取的监控的方法。 有些顾客可能会要求批准控制计划。
1.0
Re g r e ssio n 9 5 % CI D a ta Avg Bia s
P re dictor C onsta nt S lope S
P 0.000 0.000
0.5 R e fe re nce A v e ra ge 2 4 6 8 10
0.0
0
G a ge B ia s B ia s -0.053333 0.491667 0.125000 0.025000 -0.291667 -0.616667
分析结论: t远大于 2.093,偏 倚明显偏 离0,该 测量系统 不能接收
23
第2部分 2.2.9 全尺寸测量结果
组织必须按设计记录和控制计划的要求,提供尺寸验证
已经完成的证据,且测量结果符合规定的要求。 对于每个独立的加工过程,如:生产单元或生产线,和 所有的多模腔、成型模、模型或冲模,组织都必须有全 尺寸测量结果。必须对设计记录和控制计划中注明的所 有尺寸(参考尺寸除外)、特性和规格等项目,记录实 际测量结果。 组织必须标明设计记录的日期、变更版本,以及任何尚 未包括在设计记录中、但已经过授权而且纳入生产的工 程变更文件。
TS程序文件(配流程图)--生产件批准程序

1.0目的本程序的目的是正确了解顾客的工程设计和标准要求, 以在实际生产过程中按规定的生产要求来生产符合顾客需要的产品。
2.0范围本程序包括了所有生产件批准的一般要求。
生产件包含生产、效劳产品及散装材料。
至于散装材料、原材料或非生产材料是否需要进行生产件批准程序, 那么由顾客决定。
生产件批准程序应在第一批产品发运之前实施。
3.0职责3. 1顾客代表与顾客共同协商确定何时需要进行PPAP提交以及按何种等级提交。
3. 2工程小组负责PPAP的筹划。
4.03.3设计技术科汇总PPAP所需提交的文件和样品, 设计技术科负责人签发零件提交保证书/首批样品检验报告。
5.03.4设计技术科确定供给商PPAP的提交等级并负责批准, 生产供给科负责联系供给商PPAP的提交6.0定义PPAP -- 生产件批准程序。
生产件: 是指在生产现场用正式生产工装、量具、过程、材料、操作者、环境和过程参数〔如: 进给量/速度/循环时间/压力/温度〕制造的零件。
PSW: 零件提交保证书7.0输入顾客代表顾客要求设计技术科工程更改工程组过程确认结果设计技术科供方生产件提交要求6.0 作业流程:责任者/部门 流程 相关文件/表单工程组←APQP工程组N工程组N顾客/工程组→PPAP 提交清单设计技术科→PPAP资料和生产→样件顾客→PPAP文件包N仓库 →检验报告7.1 顾客通知要求必须将以下的任何设计和工程更改通知给顾客质量部门。
由顾客决定是否要求提交PPAP和以前批准的零件或产品相比, 使用了其它不同的加工方法或材料;使用新的或改良的工装〔不包括易损工装〕、模具、铸模、模型等, 包括附加的或换用的工装;对现有工装及设备进行翻新或重新布置之后进行生产;生产是在工装和设备转移到不同的企业或一个新增的厂址进行的;供方对零件、非等效材料、或效劳〔如: 热处理、电镀〕的更改, 从而影响顾客的装配、成型、功能、耐久性或性能的要求;在工装停止批量生产到达或超过12个月以后重新启用而生产的产品;涉及由内部制造的, 或由供方制造的产品和过程更改。
质量管理体系过程程序图(1
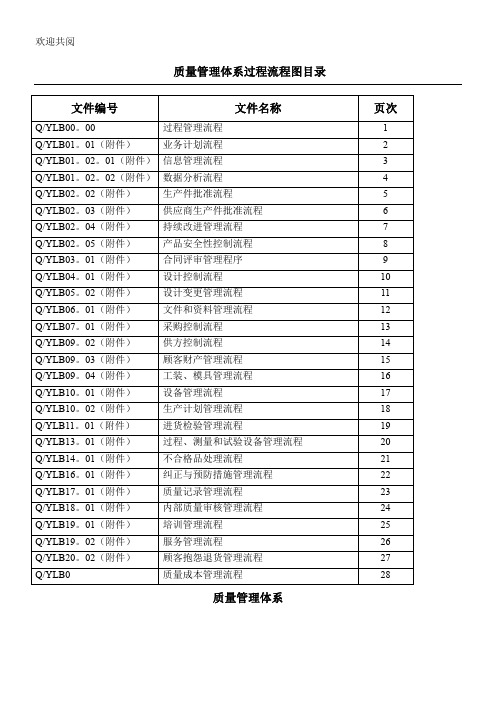
质量管理体系过程流程图目录
质量管理体系
数据分析流程
供应商生产件批准流程
设计变更管理程序
文件和资料管理流程
采购控制流程
供方控制流程
顾客财产管理流程
工装、模具管理流程
设备管理流程
生产计划管理流程
进货检验管理流程
过程、成品检验管理流程
检验、测量和试验设备管理流程
不合格品处理程序
纠正和预防措施管理流程
质量记录管理流程
内部质量审核管理流程
培训管理流程
服务管理流程
顾客报怨退货管理程序
质量成本管理流程。
生产件批准程序

力。
注2:本要求的目的是為了確定生產過程是否能生產出滿足要求的產
品。初始過程研究關注的重點是計量型數據而不是計數型數據。裝配錯誤、
試驗失敗、表面缺陷是“計數型數據”的例子。了解這部分內容很重要,但
不包括在本手冊的初始研究中。用計數型數據對特性實施監測,需要相當長
的時間收集更多的數據。計數型數據不適用於PPAP提交,除非有經授權的顧
組織必須確定其中一個被測零件為標准樣件。(2.2.15) 注:通常全尺寸測量結果不適用於散裝材料。
24
2.2.10 材料/性能試驗結果的記錄
對於設計記錄或控制計劃中規定的材料和/或性能試驗,組織必須有試驗結 果記錄。 2.2.10.1材料試驗結果 當設計記錄或控制計劃中規定有化學、物理或金屬的要求時,組織必須對 所有這些零件和產品材料進行試驗。 材料試驗結果必須說明以下內容: A/試驗零件的設計變更等級; B/任何尚未納入設計記錄,但經過授權的工程變更文件; C/試驗零件的材料規范編號、發佈日期和變更等級; D/進行試驗的日期; E/試驗零件的數量; F/實際試驗結果; G/材料供方的名稱,當顧客要求時,注明顧客指定的供方/供貨商代碼。 對於顧客開的材料規范並有顧客批准的供方名單的產品,組織必須從該名 單上的供方處采購材料和/或服務(如:油漆、電鍍和熱處理、焊接)。 25
的一個支架可以有不同的用途。
注3:對於定義為黑盒子的零件(見術語表),設計記錄要規定和其它件
的配合關係和性能要求。
注4:對於標准目錄零件,設計記錄可能只包含功能規格或者認可的行
業標准的參考要求。
注5:對於散裝材料,設計記錄可以包括原材料的標識、配方、加工步
驟和參數,以及最終的產品規范和接受准則。如果度量結果不適用,那麼
生产件批准程序(PPAP)
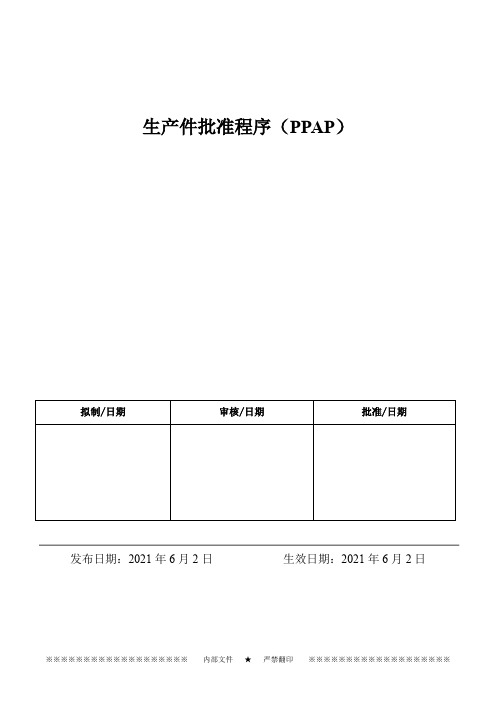
4.1市场部:负责零件送样及资讯回馈;
4.2工程部:负责送样产品之检测、送样资料准备及承认资料归档以及受控;
4.3跨功能小组:审查PPAP文件(包括供应商及外包商提交之PPAP文件)。
5. 程序内容:
5.1PPAP策划时须整理的文件(提交的等级见5.6要求,或依客户要求进行提交)
(1)设计记录
-:不适用。
5.12.供应商提供的材质证明书确认内容如下:
1).材质证明母材厂家和要求一致。
2).材料规格、材质和要求一致。
3).材料化学成分含量标和设计要求(JIS要求或客户要求)一致,且实绩含量的标准范围内。
6.相关文件:
6.1《文件控制程序》;
6.2《记录控制程序》;
6.3 PPAP参考手册。
5.7.1客人回签之标准标品,由品质部保管其样品,工程部保管其相关资料.
5.7.2如客户不能将认可样品回签,则由工程部根据客户认可资料进行检样,品质部并保管其样品,工程部保管其相关 资料。
5.8所有送样认可相关记录保存期限为产品生产终止之年度再加一日历年。
5.9标准样品(Master sample)需于上面标示认可日期,保存期限为产品生产终止之年度再加一日历年,或新样品制作 出且经过客户认可为止。
(2)任何授权的工程变更文件
(3)需要时工程认可
(4)设计FMEA
(5)制程流程图
(6)制程FMEA
(7)尺寸结果
(8)材料/功能测试结果记录
(9)初期制程研究
(10)量测系统分析研究
(11)认可实验室文件
(12)控制计划
(13)零件送样保证书(Production Part Submission Warrant)
ISO9001体系二级文件—生产件批准控制程序
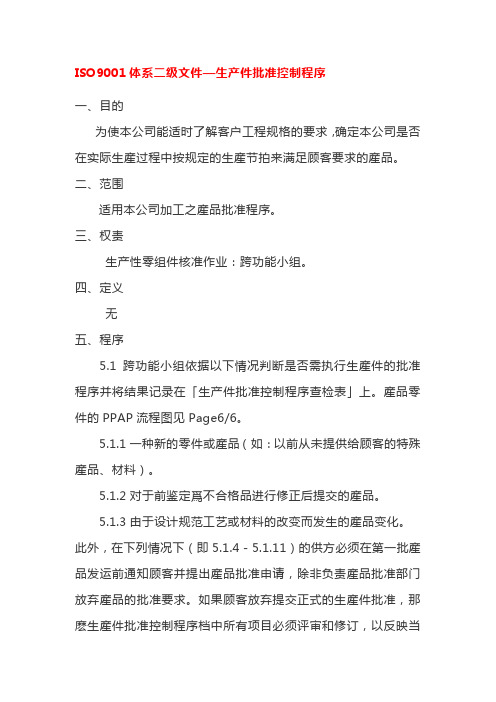
ISO9001体系二级文件—生产件批准控制程序一、目的为使本公司能适时了解客户工程规格的要求,确定本公司是否在实际生産过程中按规定的生産节拍来满足顾客要求的産品。
二、范围适用本公司加工之産品批准程序。
三、权责生产性零组件核准作业:跨功能小组。
四、定义无五、程序5.1跨功能小组依据以下情况判断是否需执行生産件的批准程序并将结果记录在「生产件批准控制程序查检表」上。
産品零件的PPAP流程图见Page6/6。
5.1.1一种新的零件或産品(如:以前从未提供给顾客的特殊産品、材料)。
5.1.2对于前鉴定爲不合格品进行修正后提交的産品。
5.1.3由于设计规范工艺或材料的改变而发生的産品变化。
此外,在下列情况下(即5.1.4-5.1.11)的供方必须在第一批産品发运前通知顾客并提出産品批准申请,除非负责産品批准部门放弃産品的批准要求。
如果顾客放弃提交正式的生産件批准,那麽生産件批准控制程序档中所有项目必须评审和修订,以反映当前有关的过程。
生産件批准控制程序必须包含同意本次放弃的産品批准负责部门人员的签名日期。
5.1.4相对于以前批准过的産品,使用了其他可选择的结构和材料。
5.1.5使用新的或改变的工具(易损工具除外)、模具、夹具、检具等,包括附加的和可替换的工具进行的生産。
5.1.6对现有工装及设备进行重新装备或重新调整后进行的生産。
5.1.7生産过程或生産方法发生了变化后进行的生産。
5.1.8把工装或设备转到其他生産场地或在另一生産场地进行的生産。
5.1.9分包産品、材料或服务的来源发生了变化。
5.1.10工装在停止批量生産达12个月或更长时间后重新投入生産。
5.1.11由于对供方质量的担心,顾客要求推迟供货。
以上这些要求的目的是爲了确定对直按顾客或最终购买者的影响,本公司对分包的材料服务负责。
任何与生産批准程序要求有关的问题,应与顾客産品批准的负责部门联系。
5.2若跨功能小组判定需要做PPAP则营业部通知顾客,由顾客决定是否需要提交本次PPAP给顾客。
生产件批准程序(PPAP)

生产件批准程序(PPAP)文件编号: Q/DCE 01.019版本号: 09E05区分部门姓名签名日期拟制产品与技术中心审核产品与技术中心会签营运部会签质量管理部会签市场营销部会签物资保障部批准副总经理1 目的为得到客户生产件批准的认可,规定在首次批量供货前的准备要求;规定供应商所提供的主要原材料或者外加工服务的生产件批准程序。
2 范围在正式批量生产前,所有生产材料(结构材料)及外包加工的生产件批准活动及提交顾客生产件批准的各项活动。
3 职责3.1 市场营销部(客户代表)负责确定顾客要求,并将顾客要求传达给产品与技术中心;确认产品与技术中心提交的 PPAP 资料,提交客户批准及沟通。
3.2 产品与技术中心负责采集产品 PPAP 相关资料提交市场营销部(客户代表)确认并转交客户进行批准;负责供应商及外加工点提交的 PPAP 资料的确认;负责客户 PPAP 文件的存档;3.3 各部门负责配合产品与技术中心执行客户对生产件批准的各种要求,并提供 PPAP 相关资料。
3.4 物资保障部负责通知供应商 PPAP 提交要求;采集供应商 PPAP 文件并提交产品与技术中心;与供应商的接口包括供应商 PPAP 生产安排;监控供应商的改进行动。
负责供应商 PPAP 文件的存档。
3.5 营运部负责通知外加工点 PPAP 提交要求;采集外加工点 PPAP 文件并提交产品与技术中心;与外加工点的接口包括外加工点 PPAP 生产安排;监控外加工点的改进行动。
3.6 分管领导负责提交顾客的、供应商及外加工点提交的 PPAP 资料的批准。
4 输入客户需求和本公司需要、 HSF 要求。
5 定义PPAP:指 Production Part Approval Process (生产件批准程序)的英文简称。
生产件:在生产现场,用生产工装、量具、工艺过程、材料、操作者、环境和过程设置,如:时间/温度等的过程设置下被创造出来的产品。
6 业务流程图6.1 客户生产件批准流程图 (见附件 1)6.2 供应商生产件批准流程图 (见附件 2)7 控制要求7.1 生产件提交策划7.1.1 当客户或者供应商有需求和要求时,供应商制作 PPAP 资料提交给客户批准,通常生产件批准在第一次产品批量发运前完成,除非客户抛却该生产件的批准要求。
质量管理体系中PPAP生产件批准程序的具体内容
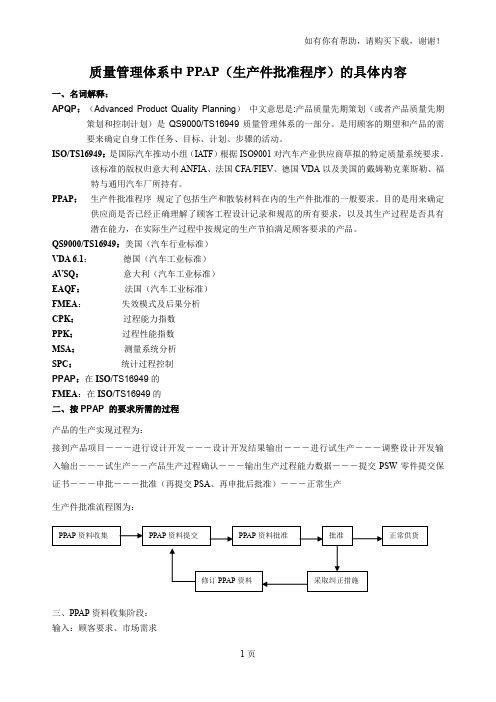
质量管理体系中PPAP(生产件批准程序)的具体内容一、名词解释:APQP:(Advanced Product Quality Planning)中文意思是:产品质量先期策划(或者产品质量先期策划和控制计划)是QS9000/TS16949质量管理体系的一部分。
是用顾客的期望和产品的需要来确定自身工作任务、目标、计划、步骤的活动。
ISO/TS16949:是国际汽车推动小组(IATF)根据ISO9001对汽车产业供应商草拟的特定质量系统要求。
该标准的版权归意大利ANFIA、法国CFA/FIEV、德国VDA以及美国的戴姆勒克莱斯勒、福特与通用汽车厂所持有。
PPAP:生产件批准程序规定了包括生产和散装材料在内的生产件批准的一般要求。
目的是用来确定供应商是否已经正确理解了顾客工程设计记录和规范的所有要求,以及其生产过程是否具有潜在能力,在实际生产过程中按规定的生产节拍满足顾客要求的产品。
QS9000/TS16949:美国(汽车行业标准)VDA 6.1:德国(汽车工业标准)AVSQ:意大利(汽车工业标准)EAQF:法国(汽车工业标准)FMEA:失效模式及后果分析CPK:过程能力指数PPK:过程性能指数MSA:测量系统分析SPC:统计过程控制PPAP:在ISO/TS16949的FMEA:在ISO/TS16949的二、按PPAP 的要求所需的过程产品的生产实现过程为:接到产品项目―――进行设计开发―――设计开发结果输出―――进行试生产―――调整设计开发输入输出―――试生产――产品生产过程确认―――输出生产过程能力数据―――提交PSW零件提交保证书―――申批―――批准(再提交PSA、再申批后批准)―――正常生产生产件批准流程图为:三、PPAP资料收集阶段:输入:顾客要求、市场需求产品技术要求、产品标准、技术标准、产品图与产品有关的法律法规原材料及辅料要求对合格供方要求生产过程所需工艺流程、工序布置产品实现过程所需设备及精度要求产品实现过程所需计量器具及要求设计过程失效模式及后果分析FMEA输出:1.初始产品图纸、初始加工工艺规程及工艺过程图纸2.设计目标;3.识别顾客要求;识别顾客的特殊要求,供方必须有与所有适用的顾客特殊要求相符合的记录。
PPAP生产件批准程序(流程图)

PPAP生产件批准程序(IATF16949-2016/ISO9001-2015)1.0目的按顾客要求进行生产件的批准,以证明本公司能满足顾客所有要求。
对供方提出生产件批准要求,以验证其是否符合我公司要求。
2.0范围适用于顾客提出的生产件批准要求及对供方提出的生产件批准要求。
3.0术语和定义3.1 PPAP(Production Part Approval Process):生产件批准程序。
3.2 生产件:是指在生产现场用正式生产工装、量具、过程、材料、操作者、环境和过程参数(如时间/压力/温度)以及制造所需的零部件。
3.3 PSW:零件提交的保证书。
4.0工作程序责任部门业务流程要点描述及记录工程部生产部物控部4.1 进行生产件批准的时机4.1.1 新的产品4.1.2 已经批准的零件或产品,使用了其它可选择的结构或材料。
4.1.3 使用新的或改进的工装(不包括易损工装)、模具等。
4.1.4 对现有工装及设备进行翻新或重新布置之后进行生产。
4.1.5异地生产(包括转移场地和附加场地)。
4.1.6 供方材料或服务的来源生产变化。
4.1.7 工装在停止批量生产达到或超过12个月以后,重新生产。
4.1.8 制造过程和方法发生了变化。
4.1.9 产品设计图样、规范或材料规范的改变使产品发提出PPAP申请生了变化。
工程部 销售部4.2 判定是否向顾客提交生产件批准及提交等级。
生产部工程部4.3 提交生产件批准的产品和文件。
4.3.1 一般样件数量为3~6件,顾客另有规定的则按顾客要求的数量。
4.3.2 零件提交保证书。
4.3.3 外观件批准报告(如果有)。
4.3.4 设计记录(图纸、技术规范)。
工程部 质管部否否4.3.5 工程更改文件。
4.3.6 DFMEA/PFMEA 。
4.3.7 尺寸检查报告。
4.3.8 材料检查报告。
4.3.9 产品性能检查报告。
4.3.10 过程流程图。
4.3.11 初始过程能力分析。
PPAP生产件批准控制程序(含流程图)
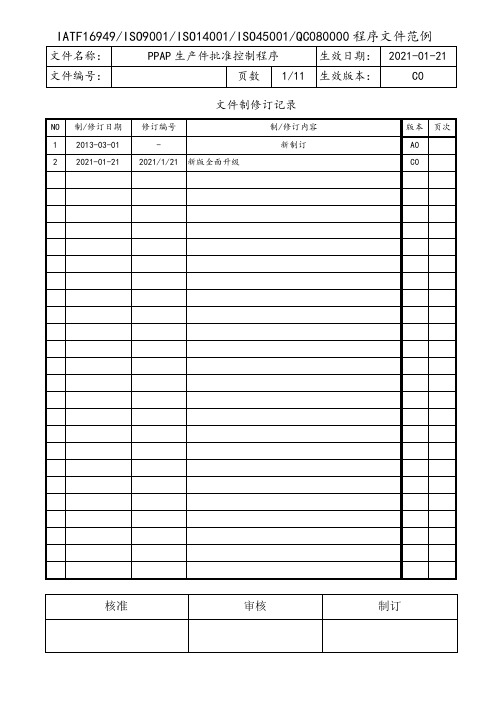
文件制修订记录1.0目的:确定我司是否已经正确理解了顾客工程设计记录和规范的所有要求,并且在执行所要求的生产节拍条件下的实际生产过程中,具有持续满足这些要求的潜能。
2.0范围:本程序适用于有 PPAP 要求或提出其它特殊要求的客户生产认可,要求在第一批产品发运之前,对产品生产进行评审和批准。
3.定义:3.1生产件:在生产现场,使用正式生产工装、量具、材料、操作者、环境和过程参数制造的零件。
3.2批(产品批):由在同样生产条件下生产的产品组成的单元。
3.3 PPAP:为Products Part Approval Process,以下简称PPAP,即生产件批准程序。
3.4 DFMEA:设计潜在失效模式及后果分析。
3.5 PFMEA:过程潜在失效模式及后果分析。
4.0职责:4.1营销部:负责PPAP资料提交客户送审;当顾客没有批准要求或PPAP档放置在公司内待查时,代表顾客行使批准程序。
4.2生产部:负责生产件样品、标准样品所需实物及其相关数据提供;4.3研发部:负责PPAP作业规划、过程流程图、PFMEA、控制计划、零件提交证书、工程变更等数据的收集与提交。
4.4品保部:负责对材料、性能、尺寸等进行检验及报告提供;量测系统分析、制程能力分析、顾客工程核准(如有要求)等及其报告提供。
5.0作业内容及流程:5.1初始过程研究:在提交顾客或组织确定的所有特殊特性之前,必须确定初始过程能力或性能指数的水准是可接受的。
初始过程能力主要对以下两种质量指数进行研究 :1.Cpk-稳定过程的能力指数。
2.Ppk-性能指数。
过程稳定时,可计算Cpk;当过程存在已知的可判断的特殊原因,且输出满足规范要求时,应该使用Ppk。
初始过程能力研究接受准则:5.2PPAP的批准等级说明:当客户要求其产品制作 PPAP 及认可时,营销部应与客户协议后定出接受认可的等级,当客户未提出批准要求或没有指定认可等级时,APQP小组有权决定认可等级。
生产件批准程序PPAP课件PPT(32张)

二、PPAP的过程要求
11.2.质量指数 如果适用,应该使用能力或性能指数对初始过程研究进行总结。
11.3.过程能力研究的接收准则: 若过程稳定,组织在评估初始过程研究结果时,必须采用以下的 接受准则:
3.顾客工程批准
顾客要求时,组织必须具有顾客工程批准的证据。
4.设计失效模式及后果分析(DFMEA):
有产品设计职责的组织,必须按照顾客要求开发设计 FMEA。
5.过程流程图
组织必须使用组织规定的格式绘制过程流程图,清楚的 描述生产过程的步骤和顺序以流程,同时应适当地满足 顾客规定的需要、要求和期望。
组零织件必 图须有在关所的有辅的助辅图助面当文)设件上(记计例录记如变:更录补的或充版的本控全、制尺绘寸图计结日划果期表、规、组定草织图名有、称性扫和描零能图件或、编剖号功面。能图、要C求MM时检查,点组结果织,必几何须尺对寸和公差图、或其它与 所示全部活动不是每次所都有出现这。些零件或产品材料进行试验。性能试验报告必须包括以 当 合设格计实记 验录 室或 必控 须制 定计 义划 实下中验内规 室定 范容有 围:化 ,学 并、 有物 文理 件或 证金 明属 该的 实要 验求 室时 可, 进组 行织 测必 量须 或对 试所 验有 活这 动些 。零件和产品材料进行试验。 一顾旦客完 采全购满订足单所/有顾准客则特,殊试组要织求验则零必须件在的AA设R上计记录变所更要求等的级信息;。 顾客采购订单/顾客特殊任要求何尚未纳入设计记录,但经过授权的工程变更文件; 等合级格1实—验—室仅必向须顾定客义提实交验保试室证范验书围(零,对并件指有定的文的件工外证观程明项该规目实,范验提室编供可一号进份行、外测观发量批或布准试报日验告活期)动。和。 变更的等级; 生 —产对件于必专须利符零合部所件有/详顾细客数进工据程行设试计记验录的和工日程期规范;要求(包括安全性和法规的要求)。
PPAP-生产件批准程序
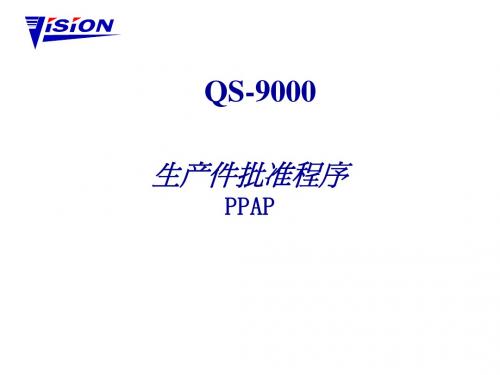
※ ※ ※ ※ ※ S ※ ※
R R R R R R R R
10 Measure. System analysis 測量系統分析表 11 Certified Laboratory Record 具有資格的實驗室文件 12 Control plan 過程質量控制計劃表 13 PSW 提樣保證書 14 AAR (Optional) 外觀件批准報告 (選擇使用) 15 Product sample Parts 產品樣本
1.1
Qualification for production: 產品承制資格: 產品承制資格
• 1.1.1 客戶未批准前不得交貨。 客戶未批准前不得交貨。 • 1.1.2 依客戶承認之規格與要求,可依據客戶交貨日 依客戶承認之規格與要求, 期交貨。 期交貨。 • 1.1.3 正確使用客戶規定的特殊特性符號,以標明其 正確使用客戶規定的特殊特性符號, 重要特性。 重要特性。 • 1.1.4 若客戶要求放棄外觀件批准報告時,須提供書 若客戶要求放棄外觀件批准報告時, 面證明。 面證明。 • 1.1.5 若客戶要求提交的PPAP報告與本程序規定的 若客戶要求提交的 報告與本程序規定的 不一致,以客戶要求的為準。 不一致,以客戶要求的為準 •
QS-9000
生产件批准程序
PPAP
生产件批准程序 PPAP
对所有生产、 对所有生产、服务产品和散装材料都有要求 生产件 生产现场 使用生产条件 提交的部件需取自有效的生产过程 一小时到一个班次的生产 规定的产量至少为300 300件 规定的产量至少为300件 每一腔都应进行
生产件批准程序 PPAP
生产件批准程序 PPAP
若生产涉及以下情况, 若生产涉及以下情况, 除非顾客让步 接受, 须提交: (续) 接受, 须提交: 工具/ 8. 工具/设备转移至不同的生产场所 改变外包加工部件, 材料, 9. 改变外包加工部件, 材料, 服务 的来源 10.停止生产12个月以后再恢复生产 停止生产12 10. 停止生产12个月以后再恢复生产 11.由于对供方质量的担心 由于对供方质量的担心, 11. 由于对供方质量的担心, 顾客要 求停止交货