分解炉改造
工业炉窑淘汰改造方案

工业炉窑淘汰改造方案在工业生产中,炉窑设备广泛应用于各个行业,如冶金、化工、玻璃、陶瓷等。
然而,随着社会经济的发展和环境保护的要求提高,传统的工业炉窑面临着淘汰和改造的需求。
本文将以炉窑淘汰改造为主题,侧重探讨减少污染排放、提高能源利用率、提升生产效率等方面的技术方案和措施。
一、炉窑淘汰原因分析1.1 环境污染:传统工业炉窑在燃烧过程中产生的废气排放和固体废弃物处理问题成为重要环境问题,如二氧化硫、氮氧化物、固体颗粒物、重金属等污染物的排放。
1.2 能源浪费:传统工业炉窑采用传统的燃烧方式,能源利用效率低下,无法充分利用废热和余热资源。
1.3 生产效率低:传统工业炉窑的设备老化,存在生产效率低、产品质量不稳定等问题,无法满足现代工业生产需求。
1.4 安全隐患:传统工业炉窑的自动化程度低,操作人员的长期接触高温环境容易引发事故,存在较大的安全隐患。
二、炉窑淘汰改造技术方案2.1 废气处理技术废气处理是炉窑淘汰改造的重要环节,其核心内容是减少污染物的排放。
常见的废气处理技术包括:2.1.1 脱硫技术:采用吸收法、氧化法、还原法等脱硫工艺降低二氧化硫排放量。
2.1.2 脱硝技术:采用选择性催化还原法、选择性催化氧化法等脱硝工艺降低氮氧化物排放量。
2.1.3 循环流化床技术:通过改变燃烧方式和燃料性质,减少固体颗粒物的排放。
2.1.4 烟气净化技术:采用静电除尘、湿式电除尘、布袋除尘等技术降低固体颗粒物排放量。
2.2 能源利用技术能源利用是炉窑淘汰改造的另一个关键领域,其目标是提高能源的利用效率和减少能源的浪费。
常见的能源利用技术包括:2.2.1 高效燃烧技术:采用预混燃烧、分级燃烧、燃烧控制等技术提高燃烧效率。
2.2.2 余热回收技术:通过余热锅炉、余热汽轮机等设备收集和利用工艺炉窑产生的余热。
2.2.3 生物质能利用技术:将生物质能源作为工业炉窑的替代燃料,提高燃烧效率和减少碳排放。
2.2.4 富燃技术:通过添加富燃燃料改善燃烧条件,提高燃烧效率。
七里岗水泥厂分解炉串联改造技术

・!"・#$$%&’(&%七里岗水泥厂现有!$$$)*+和,$$)*+预分解干法线各!条,年产水泥-$万)。
!烧成系统主机设备烧成系统主机设备见表!。
表!烧成系统主机设备设备名称!$$$)*+.二线/,$$)*+.一线/预热器0!#1!%%!#22#1!%$$$220#!1!34!#22!1!3"$$220%!1!"!!-22!1!3"$$2203!1!"!!-22!1!34$$220"!1!"3!-22!1!34$$22分解炉55炉!34!#’67炉!33$$22篦冷机-$8914#"9#:!%2;!%:"2高温风机5<==#3,##$$$2%*>,,?@A6<==##,!4$$$2%*>B,?@A 窑头排风机C31,%D!-5技改后同左回转窑!%:#2;3-2!%2;342"分解炉改造前状况!)预热器的堵塞经常发生,严重时!星期停窑处理%次,预热器的堵塞一般采用人工捅堵的方法,危险性大,处理时间长;0"出口温度经常高于分解炉出口,03、0"内套筒几乎全部烧掉。
#)分解炉不适应烧低挥发分煤。
!88,年添加本地低挥发分煤后,分解炉、竖直烟道结皮较多,需要经常处理。
#原分解炉的技术分析一线分解炉采用E01’67,二线为E0155炉,均是由天津水泥工业设计院设计的,预热器为五级旋风低压损结构。
’67炉具有喷腾和旋流效应,物料滞留时间为!$F左右;55炉具有单纯喷腾效应,物料滞留时间8F左右。
我厂因原燃料成分波动大,又采用人工定时取料进行化验分析,存在时间滞后、数值偏差大、指标调整慢的缺点。
$分解炉技术改造方案选择及实施方案!:扩大55、’67炉容,采用直径加大或顶端加高以及出口加鹅颈管的方式,延长物料停留时间。
但此方案受预热器结构限制,安装时间长。
NC_SST_I分解炉锥部结皮的处理

2006.No.1我公司2号熟料生产线采用NC-SST-I管道式分解炉,规格为Φ3.9m×24m,设计生产能力为1300t/d,2004年10月投产。
进入2005年后,分解炉锥部结皮十分严重,每次点火投料三四天后,分解炉出口压力就从-0.60kPa上升到-1.8kPa以上,系统风量和窑炉用风比例无法稳定,熟料产质量波动较大,窑内结球、结圈等工艺事故较多。
为了维持生产,在分解炉锥部增设捅灰孔,班班清理,仍多次出现大块结皮垮落,堵住分解炉下缩口,被迫停窑处理的事故。
该分解炉两煤粉喷嘴对称布置在锥部两侧,C4下料管布置在三次风入炉口一侧煤粉喷嘴的偏上方。
现场观察,三次风管入炉口一侧存在明火,另一侧煤粉喷嘴入口忽明忽暗。
因煤粉喷嘴入口位置在三次风管入炉口的中部,入炉煤粉与含有大量新鲜氧气的高温三次风直接接触,迅速燃烧,放出大量的热量,而受入炉三次风和下料点的影响,在此一侧形成料的稀相区,放出的热量无物料来吸收,同时部分正在燃烧的煤粉在切向入炉三次风的作用下,被抛向炉壁,黏附到炉壁上,继续燃烧,在锥部形成局部高温,黏附未燃尽的煤粉及生料粉,使结皮逐渐增厚。
基于以上的分析,2005年5月6日,利用停窑的机会,将三次风管入炉口一侧的煤粉喷嘴向上抬高500mm左右,高于三次风管入炉口位置(见图1),一方面,使煤粉着火点靠近下料点,使燃烧能受到物料的抑制,减缓了煤粉的燃烧速度;另一方,避免高速切向入炉的三次风中携带过多未燃尽的煤粉,增加锥部结皮的几率。
改造后,虽三次风入炉口一侧仍存在明火,但温度明显下降,分解炉锥部结皮的情况大为改观,再未发生因锥部结皮严重停窑的事故。
NC-SST-I型分解炉具有炉容大、煤粉及物料在炉内停留时间长的特点,火嘴位置的上移,并未造成入窑物料分解率的下降,而分解炉锥部结皮的减少,保证了系统风量的稳定,为窑系统实现稳产、高产创造良好的条件。
图1分解炉喷煤嘴改造前后位置(编辑顾志玲)中图分类号:TQ172.622.26文献标识码:B文章编号:1002-9877(2006)01-0053-01NC-SST-I分解炉锥部结皮的处理赵来山,倪宏山,尚国辉(中宁赛马水泥有限公司,宁夏中宁755100)动。
鲁南中联1号、2号窑节能减排技术改造

根据 回转窑设备本身 的一些 条件 . 以及 用户所要
达 到 的使 用 目标 . 们 对 回转 窑 的 以 下 几 个 方 面 进 行 我
更新设计 :
( ) 动 装 置 。原 主传 动 为两 台 1 5W 的 电动机 , I 十六排 充气篦 床 由箱式篦 板梁 ( 1传 2k 包括 活动 梁和 固定
的优 化结 构 , 对于 低热 值 、 挥 发分 , 低 高灰 分 的低 品 位燃煤也 有很好 的适应性
拟 定 的 改 造 . 分 利 用 原 框 架 的 结 构 . 可 能 减 充 尽
少原框 架 的拆 除 和改建 。 降低 改造 费用 , 缩短 改造 时
间 与 来 生 线 比结 将 加 凑 。 原 的 产 相 ,构 更 紧 。
来 的钢结 构 。 建新 的钢结构 系统 , 框架 体 系为钢 管混
凝 土 和 型 钢钢 梁 结 构 。 高 温 风 机 的 流 量 将 放 大 到 4 0O 0 3 . 压 力 8 0 m/ 全 h
8 3P . 0a 电机功率 l 0k 满足改造后的窑系统通 3 0W, 6
风要求 将原来 的液力耦合器调速改为变频调速。
热 器 规 格 为 C : 一 0 0 m, 21 4 0mm, 3 I2 0 m C : — , 7 0 6 C:
1 一 90 m ,4 1 5 r a C:一 90 5 mm , 5 1 C:一 20 5 mm , 预
不提 高五级 旋风 筒空 间高度 的前提下 .进 一步增 加
积小, 篦床 名义面 积 5 .m . 床有效 面积仅 4 . O 2篦 4 6 m。 8 熟 料冷却效果不好 , 料 出料温度 高 。 回收效率低 。 熟 热 改 造 的新 型高效 篦冷 机不仅 其篦 床有 效面积 将增 大
分解炉喷煤管的改造优化

35
本次对分解炉喷煤管优化改造的成功,消除
图5改造后分解炉送煤压力曲线
了窑系统的顽疾之症,树立了工艺优化的信心。当 然,本次改造虽然取得了良好的效果,却也带来一 些负面作用,比如分解炉腰部温度偏高,可能会影 响分解炉耐火材料的使用寿命,下一步还需继续摸 索改善之路。
参考文献
[1] 张薇,简森夫,胡道和.分解炉内煤粉燃烧特性的研究[J]. 水泥技术,1996(1):16-18.
改造后煤管(改造后)
新世他水泥專报
Cement Guide for New Epoch
表2改造后喷煤管尺寸与主管道比例关系
内径/mm
面积/mn?
307
73 985
232
84 504
160
80384
136
58 077
备注 主管道截面积的79.5%
旦巌mu* 同**
____ CSh e .
图4改造前分解炉送煤压力曲线
表1改造前喷煤管尺寸与主管道比例关系
内径/mm
面积/mn?
307
73 985
232
84 504
200
62 800
备注
占主管道截面积的84.9%
图2改造后分解炉喷煤管位置
的热空气相遇燃烧,再与C4撒料箱进入的生料粉 混合,以提高煤粉入炉后的燃烧速度,同时延长生 料粉与热空气融合的时间。
(2)改造分解炉喷煤管分管方式及管径,如 图3。缩小分解炉喷煤管管口截面面积至主管道截 面积的80%以下,见表2。缩小入炉煤管截面积是 利用“消防栓效应”,就像在消防水管端部加上喷 嘴一样,提高喷嘴处喷出压力,可有效减小送煤压
预热器分解炉技改施工方案
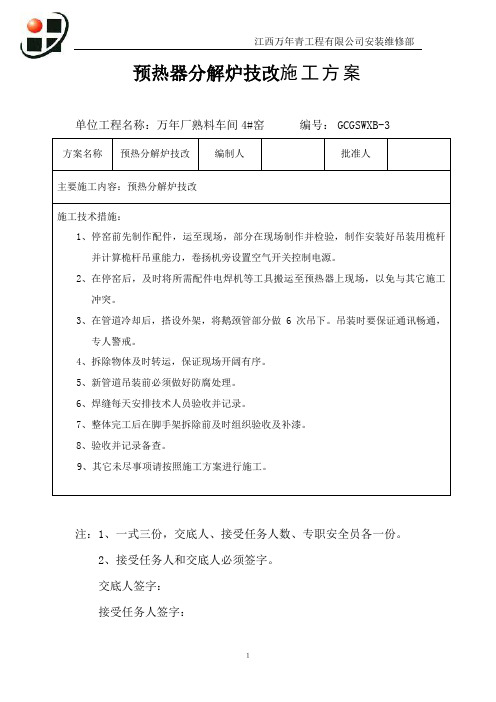
单位工程名称:万年厂熟料车间4#窑编号:GCGSWXB-3
方案名称
预热分解炉技改
编制人
批准人
主要施工内容:预热分解炉技改
施工技术措施:
1、停窑前先制作配件,运至现场,部分在现场制作并检验,制作安装好吊装用桅杆并计算桅杆吊重能力,卷扬机旁设置空气开关控制电源。
2、在停窑后,及时将所需配件电焊机等工具搬运至预热器上现场,以免与其它施工冲突。
注:1、一式三份,交底人、接受任务人数、专职安全员各一份。
2、接受任务人和交底人必须签字。
交底人签字:
接受任务人签字:
3、在管道冷却后,搭设外架,将鹅颈管部分做6次吊下。吊装时要保证通讯畅通,专人警戒。
4、拆除物体及时转运,保证现场开阔有序。
5、新管道吊装前必须做好防腐处理。
6、焊缝每天安排技术组织验收及补漆。
8、验收并记录备查。
9、其它未尽事项请按照施工方案进行施工。
技术改造总结报告

申报节能量 (吨标煤) 545.4
1537.2 307.2 2398.8
自查节能量 (吨标煤) 197.9
1489.6 615.43 2302.Biblioteka 3SLC-S预分解 系统改造
合计
二、能源工作
1. 分两批申报节能技改项目 两批共计申报节能量5744.8吨标 准煤,可以获得上海市节能技术改造 项目专项扶持奖励170多万元,二批 项目的50%专项扶持奖励款合计86.05 万元已到账。
一、技术改造与进步
4. R1S25生料循环风机节电改造 而内反馈调速技术是针对电机自 动改变电机的电流,也就是改变电机 的转速,风门挡板在全开状态下达到 节能的目的。实际运行中挡板开度由 70%提高到80%,没有达到理想中的 100%,折算年节标煤197.9吨。
一、技术改造与进步
5. 预热器倒U形管改造
为了保证各冷却风室的气密性, 将原气动闸板阀改为电动弧形锁风阀, 用于风室与拉链机之间的密封,较彻 底地解决漏风问题;同时还用优质的 密封材料用于风室与风室之间的密封, 解决了冷却机里面窜风、漏风等致命 问题,以此减少冷却风的泄漏。
一、技术改造与进步 3. 散装发货系统扩能改造
散装发货系统水泥库底分二条不 同水泥品质输送,52.5水泥发货系统 已在2005年4月完成改造,原42.5水 泥发货利用能力为120吨/小时、与 52.5水泥发货系统混用维持日常发货, 在水泥销售旺季上述系统难以满足需 求。
二、能源工作
1. 分两批申报节能技改项目
上半年申报了《冷却机节能技术改造》 作为第一批节能技改项目,改造前的二次 风温900℃,改造后的二次风温1092℃, 改造前的三次风温750℃,改造后的三次 风温906℃。年节能量:按年产熟料68万 吨、并考虑二、三次风传递和使用过程中 的热损失取30%计算,全年可以从冷却机 多回收的有效热量为3346吨标煤。
预分解窑结圈的原因分析及处理

二、结圈的原因分析及处理公司1000t/d 预分解窑从试生产到 炉风量不平衡等原因,造成在距窑口三次风流化风 A 炉,MFC预分解窑结圈的原因分析及处理一、概述公司1000t/d 预分解窑是以窑尾带 TD 分解炉的单系列五级旋风预热器和/3.2 X 46m 回转窑为 核心 配套/ 3.5 X 10m 中卸式烘干生料磨、503H-606H-825H 推动篦式冷却机,设计生产能力920t/d 熟料。
99年8月,因TD 炉炉容偏小,对分解炉进行了改造,在窑尾塔架旁增设一台N — MFC 流态化 分解炉与原TD 炉串联(见图1 )。
改造后,因对预分解窑认识不足,操作、管理水平跟不上,造成 窑内频繁结圈,严重影响回转窑的正常运转(表1为历年结圈的次数和影响时间)。
经过几年的生产, 已摸清了结圈的原因,并基本解决预分解窑结圈的问题。
在此,对公司预分解窑结圈的原因分析及 处理过程做些简单介绍。
表1为历年结圈的次数和影响时间 年份 19992000 2001 2002 2003.1 〜6 影响停窑时间(t )87 322.67 58.67 37.05 停窑次数(次)527 3 4 料 2000年4月期间,因原燃材料成份不稳定,操作不统一、窑12m 至35m 处频繁结圈,引起停窑次数及时间最多的是23 30m 处的后结圈,16〜23m 处结圈造成停窑次数仅有一次, 16m 以内的结圈虽对产质量有一定的影响,但从未引起停窑。
纵观几年的生产过程,虽然引发结圈的因素委多。
但每次都有一、二个主要 原因,每当解决了主要原因,结圈的问题可以得到缓解或消除。
下面主要介绍一下23m 〜30m 处后 结圈的形成原因及处理过程。
1、窑内用风过大,热工制度不稳定( 2000.1〜3)2000年1月至2000年5月,因回转窑25〜30m 处频繁结圈被迫停窑 297小时,尤其2000年3 月,窑内结圈停窑 9次,其中进窑处理 6次,共影响停窑121小时。
窑预分解系统的问题分析及改进措施

窑预分解系统的问题分析及改进措施摘要:我厂1号RSP窑经过6年多的运转,系统耐火材料呈现出不同程度的磨损、烧坏现象。
SB室下部掉砖,进而壳体烧损;SC室用风不良,导致边壁物料保护层不均衡,局部衬砖磨损严重;斜烟道及鹅颈管侧墙衬砖垮落,由于鹅颈管结构缺陷,经常结皮和堆料;MC室断面物料分布不均,物料稀相区炉壁烧损,直至筒体严重变形;因窑尾缩口处风速低,喷腾能力减弱而塌料;高温级旋风筒分离效率低,导致物料大量返回,内循环增加等。
本文依据热工标定结果,对该预分解系统出现的问题进行分析,并提出改进措施。
1 RSP窑系统工况分析热工标定主要参数对比见表1、表2,窑尾高温区工艺流程见图1。
表1 预热预分解系统温度变化℃表2 RSP炉的分解进程变化注:1997年数据为南京化工大学硅酸地方国营工程研究所的热工标定结果,SC 室出口指斜烟道出进口等同于鹅颈管出口。
图1 窑尾高温区工艺流程1.1 三次风温度及其对SC室工况的影响由表1可见,三次风温度和入炉生料温度分别只有600℃和671℃。
入炉生料温度低主要是由于C4锥体及下料管增开人孔门较多,外漏风量和散热损失增加引起的,通过加强管理,隔热堵漏后完全可以解决;三次风温度目前基本稳定在560~580℃,提高的余地很小。
其原因是:我厂采用单筒冷却机,经过多年的运转,内部装置所遭受的磨损和腐蚀不断加剧,而且增加了砌筑耐火砖的长度,熟料停留时间短(约为30min),出机熟料温度高(~290℃),使热效率本身就不高的单筒冷却机热回收率进一步降低(1997年热工标定结果为56.6%)。
三次风温度是影响分解率和燃尽率的重要因素。
较低的三次风温度导致炉内煤粉着火速度减慢,形成滞后燃烧,特别是SC室内煤粉是在纯助燃空气中燃烧,助燃空气的温度在很大程度上决定了煤粉燃尽率,三次风温度低,即使分解炉多加煤,SC室内温度也不会高,反而会加剧煤粉滞后燃烧。
从表1和表2可以看出,SC室生料出口温度和分解率分别是948℃和43.4%,结合入炉生料表观分解率已达22.6%的实际情况,说明SC室内的分解反应极低,煤粉燃烧状况不理想。
简述各设计院的分解炉

分解炉在窑外分解系统起着很重要的作用,自1971年第一台窑外分解系统投产,从而开始水泥工业大规模生产开始,分解炉的形式有很多。
从分解炉内的气流运动来看,可归纳为四种基本型式,即:涡旋式、喷腾式、悬浮式和流化床式。
早期开发的分解炉,多以上述四种运动型式之一为基础,使生料和燃料分别依靠“涡旋效应”、“喷腾效应”、“悬浮效应”和“流态化效应”分散于热气流中,利用物料颗料之间在炉内流场中的相对运动,实现高度分散、均匀混合和分布、迅速换热,以达到提高燃烧效率,传热效率和入窑生料碳酸盐分解率的目的。
分解炉按照设计单位国内有以下常见几种:RSP 来源与日本小野田TDF、TSD、TD、TSD、TWD、TTF、TFD天津院CDC成都院NST-I NC-SST南京院具体形式和特点如下:TDF型分解炉TDF分解炉是天津水泥院在引进日本DD炉技术的基础上,针对中国燃料特点,研制开发的一种双喷腾分解炉(Dual Spout Furnace),如下图1-1所示。
TDF炉技术特点如下:①分解炉坐落窑尾烟室之上,炉与烟室之间缩口在尺寸优化后可不设调节阀板,结构简单;②炉中部设有缩口,保证炉内气固流产生第二次“喷腾效应”;①三次风切线入口设于炉下锥的上部,使三次风涡旋入炉;炉的两个三通道燃烧器分别设于三次风入口上部或侧部,以便入炉燃料斜喷入三次风气流之中迅速起风燃烧;②在炉的下部圆筒体内不同的高度设置四个喂料管入口,以利物料分散均布及炉温控制。
⑤炉的下锥体部位的适当位置设置有脱氮燃料喷嘴,以还原窑气中的氮,满足环保要求;⑥炉的顶部设有气固流反弹室,使气固流产生碰撞反弹效应,延长物料在炉内滞留时间;⑦气固流出口设置在炉上椎体顶部的反弹室下部;⑧由于炉容较DD炉增大,气流、物料在炉内滞留时间增加,有利于燃料完全燃烧和碳酸盐分解。
TSD分解炉TSD型炉是带旁置旋流预燃室的组合式分解炉(Combination Furnace with spin pre-burning Chamber)见图1-2炉TSD炉技术特点如下:①设置了类似RSP型炉的预燃室;②将DD型炉改造为类似MFC型炉的上升烟道或RSP型窑的MC室(混合室),作为TSD型炉炉区的组成部分,并扩大了DD炉型的上升烟道容积,使TSD炉具有更大的适应性;③该炉可用于低挥发分煤及质量较差的燃料。
RSF窑外分解窑的改造与生产操作体会

改造的内容
主要控制点热工参数:
控制点 C1 C2 分解炉 窑尾 窑头竖井
根据设计硅 酸盐 熟料 生产能 力日 产 5 00 吨,台 时产 量 21 吨。进行了 回转窑 2. 5 40 米的 立筒型 F 在线窑 外分解 窑 的技术改造与更换。
� 温度 � � 压力
390 - 410 870 -890 8 80 -900 930 - 96 0 780 - 880 4900 - 5 300 6 00 -800 5 00 -6 00 6 0 -100 -
F窑 外分解 窑生产 中以窑外 分解窑 的基本6 年第 3 期
+
充分发挥预热器预热分解炉作用, 保证入 窑碳酸钙 分解 率达到要求指标, 大于 87% 。 合理控制窑尾温度, 保证熟料预烧效果。 提高烧成带热力强度, 确保熟料优质高产。 强化冷却机熟料冷却效果, 提高熟料质量和易磨性。 根据窑外分解窑的原理制定生产工艺及热工参数如下 :
2
【 文献标识码】 : B
� 装备技术
【 文章编号】 : 16 72 - 4011 (2006 ) 03 - 0033 - 02
《 四川建材》 2006 年第 3 期
窑外 分 解 窑 的 改 造 与 生 产 操 作 体 会
夏 小 楣
(新工建材有限责任公司)
【关键词】 : F 窑外分解窑; 改造; 操作 【中图分类号】 : 172. 6 我公司
产的情形下 完 成施 工 的) ;(2 )� 分解炉 为立 筒 型分 解 炉 � � 经过实践,当分解炉温度控制在 85 0 86 0 2 45 0 + 400 (椭 圆形) , 高 10 � � � 级( C4 ) 预热器入 口温度 只有 820 830
; (� 3) 预热器为四级旋风预热器,型式 2.1. 1. 1。其中: 解率只有 81% 83% 。在实 际操作 中,鉴于 我厂 生料中 碱 级旋风筒( C1 ) :有效内经 2 6 00 —双旋风筒 含量 1. 5% 左右,石灰石 中氯离子 0. 025% ,有 害成分偏 高 级旋风筒( C2 ) :有效内经 级旋风筒( C4 ) :有效内经 窑尾废气处理系统 35 00 3 400 —单旋风筒 —单旋风筒 得状况,要求合 理控制 炉温。实 践证 明,当分 解炉 温度 达 以 上,入窑生料 发 粘,易 粘结 堵塞 四 级旋 风 筒 入窑 下 料管, 级 旋风筒 锥部 物 、870 料粘挂,致使物 料下料 不畅。 经摸 索调 整,将分 解炉、 四 ,调 整后入 窑碳酸 钙分解率 可 级旋风筒( C3 ) :有效内经 � 35 00 —单旋风筒 � � � � 到 930 95 0 ,四级旋风筒温度达到 900 920 � � 经常造成窑内 结皮及 结蛋,并 造成 、
水泥窑协同处置市政污泥的应用实践
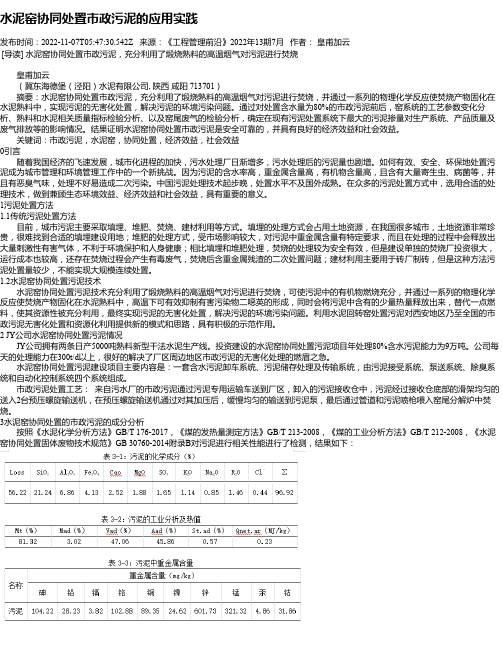
水泥窑协同处置市政污泥的应用实践发布时间:2022-11-07T05:47:30.542Z 来源:《工程管理前沿》2022年13期7月作者:皇甫加云[导读] 水泥窑协同处置市政污泥,充分利用了煅烧熟料的高温烟气对污泥进行焚烧皇甫加云(冀东海德堡(泾阳)水泥有限公司, 陕西咸阳 713701)摘要:水泥窑协同处置市政污泥,充分利用了煅烧熟料的高温烟气对污泥进行焚烧,并通过一系列的物理化学反应使焚烧产物固化在水泥熟料中,实现污泥的无害化处置,解决污泥的环境污染问题。
通过对处置含水量为80%的市政污泥前后,窑系统的工艺参数变化分析、熟料和水泥相关质量指标检验分析、以及窑尾废气的检验分析,确定在现有污泥处置系统下最大的污泥掺量对生产系统、产品质量及废气排放等的影响情况。
结果证明水泥窑协同处置市政污泥是安全可靠的,并具有良好的经济效益和社会效益。
关键词:市政污泥,水泥窑,协同处置,经济效益,社会效益0引言随着我国经济的飞速发展,城市化进程的加快,污水处理厂日渐增多,污水处理后的污泥量也剧增。
如何有效、安全、环保地处置污泥成为城市管理和环境管理工作中的一个新挑战。
因为污泥的含水率高,重金属含量高,有机物含量高,且含有大量寄生虫、病菌等,并且有恶臭气味,处理不好易造成二次污染。
中国污泥处理技术起步晚,处置水平不及国外成熟。
在众多的污泥处置方式中,选用合适的处理技术,做到兼顾生态环境效益、经济效益和社会效益,具有重要的意义。
1污泥处置方法1.1传统污泥处置方法目前,城市污泥主要采取填埋、堆肥、焚烧、建材利用等方式。
填埋的处理方式会占用土地资源,在我国很多城市,土地资源非常珍贵,很难找到合适的填埋建设用地;堆肥的处理方式,受市场影响较大,对污泥中重金属含量有特定要求,而且在处理的过程中会释放出大量刺激性有害气体,不利于环境保护和人身健康;相比填埋和堆肥处理,焚烧的处理较为安全有效,但是建设单独的焚烧厂投资很大,运行成本也较高,还存在焚烧过程会产生有毒废气,焚烧后含重金属残渣的二次处置问题;建材利用主要用于砖厂制砖,但是这种方法污泥处置量较少,不能实现大规模连续处置。
设备技术改造在水泥生产管理中的重要性

设备技术改造在水泥生产管理中的重要性发布时间:2021-10-24T13:41:44.357Z 来源:《基层建设》2021年第20期作者:赵向兵[导读] 摘要:在现代社会科学技术水平不断发展的形势下,在水泥生产过程中越来越多的新技术及新工艺得以应用,在水泥生产管理中设备技术改造至关重要,所谓的设备技术改造,指的是设备技术的优化升级,确保设备在生产的过程中高效健康的运转,助力企业提升效益,本文主要对设备改造进行探究,分析其重要性,希望为广大业内人士带来一定的参考价值。
哈密天山水泥有限责任公司新疆哈密 839000摘要:在现代社会科学技术水平不断发展的形势下,在水泥生产过程中越来越多的新技术及新工艺得以应用,在水泥生产管理中设备技术改造至关重要,所谓的设备技术改造,指的是设备技术的优化升级,确保设备在生产的过程中高效健康的运转,助力企业提升效益,本文主要对设备改造进行探究,分析其重要性,希望为广大业内人士带来一定的参考价值。
关键词:设备技术改造;水泥企业;生产管理引言随着科学技术的日新月异发展,一些新的技术也应用到生产实际中,原有的设备需要及时更新改造,才能更好地满足现代化生产的需求。
因此,要确保企业生产的顺利进行,需要加强对机电设备更新改造技术的探讨与研究。
一、设备升级改造的作用和意义所谓设备升级改造就是指将新的科技成果,新技术、新材料、新装备、新工艺等通过一系列的技术攻关,对现有的老旧设备进行再淘汰和重组。
原则上不破会原有的大型技术装备,在现有的基础上进行再优化。
其主要意义在于:引进新技术、应用新装备,优化新的工艺流程,以此提升生产效率,降低运行成本,实现企业效益与社会效益的双赢。
二、设备改造的科学性论述众所周知,工业生产的基础是设备,而高效、稳定的设备运行则是保障稳定生产的基础。
尤其是如今大型的、精密的的仪器设备,更应该在做好设备保养维护的基础上不断的进行优化,小改小革。
因此,科学的设备改造是提升企业生命力和效益的基础和关键所在!具体在实际改造过程中应注意以下几个问题:(1)预算先行在技术改造前必须进行科学的预算,必须把握“投资最小,效益最大”的原则。
分解炉喂煤系统改造

江西水泥厂 3#窑 2000年 7月份以前一直用 的 是丹麦分解炉喂煤系统,分解炉煤 粉仓 中的煤粉经 螺 旋 闸门 用双 管 喂料 机 卸 出 ,经 固体 流量 计 ,由螺旋 气力输送泵将煤粉送到窑尾分解炉 ,其工艺流程简 单,但使用效果不好 ,存在下煤不均 匀,分解炉温度 难以控制,塌料、窜料频繁等不 良现象。同时,混合 室的温度时高 时低,高时达 1100多度,分解炉 的炉 壁常因高温而烧损 ;低时 830多度,造成煤粉的燃烧 不完全。G 的出 口温度经常在 470℃左右,热效率
1994,9、
2 刘述祖 .水泥悬 浮预热与窑外 预分解技术 、武汉工业 大学出版社 ,
满 足 以下两 点 :
1)必须 保 证 18—40m/s的 风 速 ,确 保 物 料 从 各
排 转子 室 内卸 出。
2)转子 喂料秤 规 定 的散状 物 料 的粒 度 和水 份 必
须符合要求 ,只有采用气力输送 时,才能使用压缩空
气(6bar),且压缩空气必须纯净、干燥 、无油,否则物
料结 块 ,转子 秤 容 易 卡死 或计 量 不 准 。
产、fCaO 的合格率 ,熟料 质量等各项技 术参 数都明
2)预热 器 温 度 波 动 得 到 了改 善 (表 3),给 了方 便 ,也 保 证 了职工 的安全 (塌 料 容 易伤 人 )。
表 3 改造 前后预热 器温度对 比
G 出 口温度 的高 低 ,反 映 携 出 窑 炉 系 统 热 量 的 多少,在整个熟料 热耗 中占有很大 的 比重。出 口废 气温度愈高,熟料热耗愈大。从上表可以看 出,分解 炉喂煤改造后,出 口废气温度下降近 4O℃。
偏低,入窑生料的 CaCO3分解率 也不 稳定,高 时达 95%,低 的在 75%左 右 ,这 种 大 起 大 落 的 分 解 率 对 窑的煅烧极为不利,稳定窑的热工制度相当困难 ,所 以工艺技术参数不够理想(见表 1)。
SLC分解炉及窑头余热风管的技术改造
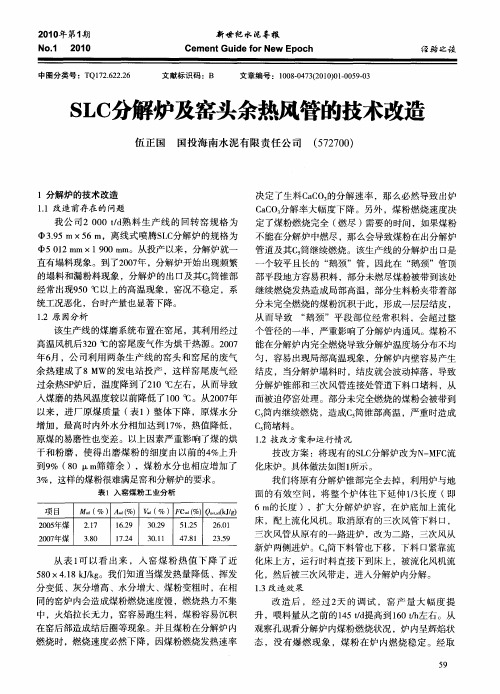
S 分解炉及窑头余热风管的技术改造 L C
伍正 国 国投海南水泥有限责任公 司 (7 7 0 520 )
1分解炉 的技术 改造 1 . 1改造前存 在的 问题
决定 了生料C C a O 的分解速率 ,那么必然导致 出炉 CC a O分解率大幅度下降。另外 ,煤粉燃烧速度决 定了煤粉燃烧完全 ( 燃尽 ) 需要的时间,如果煤粉 不能 在分 解炉 中燃尽 ,那 么会 导致 煤粉 在 出分解炉 管道及 其 C筒 继续 燃烧 。该 生产 线 的分解 炉 出 E是 l
上 。分解 炉 出 口温度 稳定 在8 0℃左 右 。分解炉 内 6
—
煤 粉 的稳 定燃烧 ,避免 了炉 内局部高 温现象 ,炉 内 壁 结皮现 明显减 少 。出分解 炉 “ 颈”管平 段积料 鹅
2 1 年 第1 00 期
No. 1 2 0 01
Hale Waihona Puke 新 世 纪水 泥导报 Ce n i e f w oc me t Gu d orNe Ep h 劈 之谈
中图分类号 :T 7 .2 . Q126 22 6
文献标识码 :B
文章编号 :10 .4 32 1)10 5 .3 0 80 7 (0 00 —0 90
原煤的易磨性也变差 。以上 因素严重影响了煤的烘 干 和粉 磨 ,使 得 出磨煤 粉 的细 度 由 以前 的4 %上 升 到9 ( 0 m % 8 筛筛余 ),煤粉水分也相应增加 了 3 %,这样的煤粉很难满足窑和分解炉的要求。
表 1 入 窑 煤粉 工业 分 析 项目 M ( ) a%) % ( ( ) C d%) d J l % F af .( / Q k g
分未完全燃烧的煤粉沉积于此 ,形成一层层结皮 ,
从而导致 “ 颈 ”平段 部 位 经 常积 料 ,会 超过 整 鹅
某水泥厂窑尾分解炉拆除施工方案
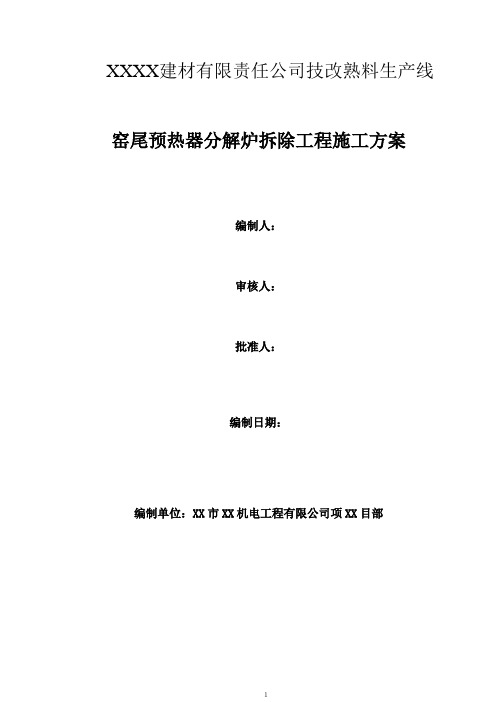
XXXX建材有限责任公司技改熟料生产线窑尾预热器分解炉拆除工程施工方案编制人:审核人:批准人:编制日期:编制单位:XX市XX机电工程有限公司项XX目部第一章工程概况一、总体概况云南XX市XX区XX镇XXXX建材有限责任公司熟料生产线窑尾预热器分解炉更换,拆除及运输的工程慨况及工程特点,窑尾预热器分解炉拆除的分解技术,吊装方法,拆除吊装的安全措施,关键词:高空吊装拆除,防止坠落。
第二章编制依据第一节编制依据1、XXXX建材有限责任公司熟料生产线技改机电设备安装工程施工合同。
2、《建筑拆除工程安全技术规范》(JGJ147-2004)。
3、《建筑机械使用安全技术规程》(JGJ33-2001)。
4、《建筑机械使用安全技术规程》(JGJ33-2001)。
5、《建筑施工高处作业安全技术规范》(JGJ80-91)。
6、《建筑物、构筑物拆除技术规程》(DBJ08-70-98)。
7、公司《质量保证手册》、《管理标准》及各种管理制度。
8、同类工程施工经验。
9、国家及地方相关规范及标准。
第二节编制说明1、XXXX建材有限责任公司熟料生产线实地查看,并结合我公司以往施工经验编制本施工方案。
2、本施工方案,介绍我公司在该工程上投入的主要机械设备、劳动力情况以及施工组织、主要施工工艺方法、技术措施、质量保证体系和措施、安全生产及文明施工保证措施、环境保护措施等。
第三节编制原则1、坚持科学施工顺序,并结合工程特点、现场环境情况、施工条件等具体情况。
2、加强质量管理、确保工程“合格”。
3、高度重视对周边环境卫生、噪声、治安方面的影响,充分利用建设单位可以提供的场地,作好生产、生活和治安方面的安排,配置工作状态良好的设备。
4、从实际出发,在确保人身安全和财产安全的前提下,选择经济、合理的拆除方案,进行科学的组织,以实现安全、经济、速度快的目标。
第三章施工组织第一节技术准备工作1、首先熟悉被拆设备及钢结构建筑物的周边环境状况,清理施工场地,规划施工现场交通道路,保证工程车辆进出畅通。
第四代篦冷机升级改造的应用经验
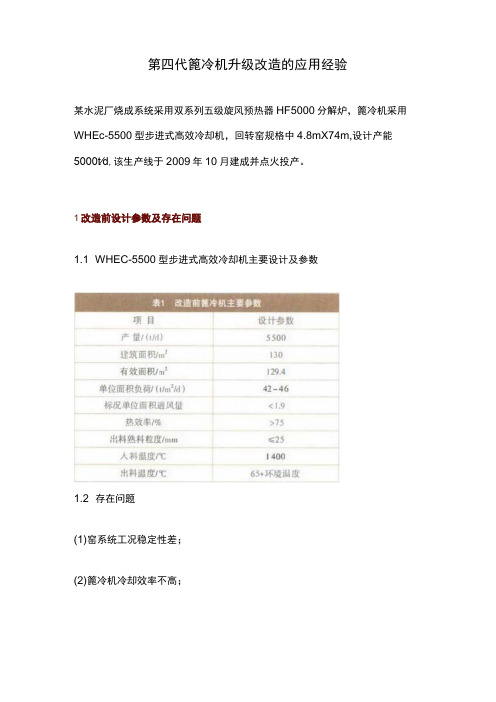
第四代篦冷机升级改造的应用经验某水泥厂烧成系统采用双系列五级旋风预热器HF5000分解炉,篦冷机采用WHEc-5500型步进式高效冷却机,回转窑规格中4.8mX74m,设计产能5000t∕d,该生产线于2009年10月建成并点火投产。
1改造前设计参数及存在问题1.1 WHEC-5500型步进式高效冷却机主要设计及参数1.2 存在问题(1)窑系统工况稳定性差;(2)篦冷机冷却效率不高;(3)熟料易磨性差;(4)风室漏料严重;(5)电气故障,篦床无故停止运行,篦床各列运行不同步,篦床速度调整不灵活;(6)固定斜坡方面的问题,其风机风量与面积不匹配。
固定斜坡具体配置如图1及表2。
图1改造前固定斜坡三台风机分区风机装机风址/(m71)全压/Pa电机功率ZkW工况风速/(m/s)供风区域2M130009OOC550.85周边区域3M20000I110090 3.62中心区域4M3500010300180翻]周边区域2篦冷机升级改造方案及参数2.1 固定床改造方案将固定斜坡整体拆除,更换为TCH新型急冷模块(图2、图3、图4),参数为W9×19,宽3.6m,长2.7m,角度调整为IO o o图2新型急冷模块图3篦板仿真模拟图4科恩达篦板该下料斜坡采用二分区供风形式,将原2M风机停用,仅利用3M和4M风机,根据各区域料层厚度和熟料颗粒的不同调节风门开度,使熟料在下料口得到更好的急冷效果,改造后斜坡冷却风机减少一台,装机功率减少55kW o改造后固定斜坡具体配置如图5、表3。
图5改造后斜坡分区方案图示项目装装机址/(n7h)全压/Pn电机功率ZkW工况风速/(tn∕G供风区域3M200001150090 1.9中心区域4M35OOO9700I8C 1.9周边区域2.2 活动床改造方案水平活动篦床为步进式输送物料,根据现场的篦床结构尺寸,采用SC1W6-6×10(6列10个标准段节),篦床总有效面积为126.36m2,可以满足5500t∕d 产量需求。
分解炉喷煤管改造示意图

项目名称:分解炉喷煤管改造示意图(高硫烟煤、 高硫无烟煤) 设计:张峰(贵州西南水泥) 制表:梁奎虎 日期:2017年4月
900
8~10度
100
1、脱氧煤管在 缩口正上方 500mm~1000mm 2、在三次风管 的对面,水平夹 角为8度。
8~10度 500mm~1000mm 三次风管 烟室缩口定位原则(圆形,不建议使用长方 形): 1、2500t/D:定位有效净空直径1.8米; 2、3200t/D:定位有效净空直径2~2.2米; 3、5000t/D:定位有效净空直径2.5~2.7米; (改造后要计算理论值,确保正常对应三次 风阀门开度下,分解炉出口负压≥负500Par)。
烟室缩口 喷煤管定位原则: 1、喷煤管远离三次风管; 2、喷煤管入口水平夹角:8~10度; 3、C4撒料台与喷煤管垂直距离:800~1600mm; 4、煤管与c4撒料台对称:夹角约10度; 5、脱氧煤管在缩口正上方500mm~1000mm(分解炉炉容偏大的煤管 下移,分解炉炉容偏小煤管上移),用煤量占约5~15%(7立方净 空气量对应1吨煤) 6、送煤风速26米~28米; 7、有空间优化的分解炉二个煤管,最大限度可能移到分解炉直筒 与分解炉锥部交接处。
1、C4下料管与分解炉炉 壁夹角为30度; 2、C4撒料台伸入分解炉 炉壁有效长度为200mm; 3、撒料台端面宽度为 1000mm。 喷煤管中心与C4撒 料台垂直距离 800~1600mm
300
C4撒料台 1000mm源自300900 200mm 入口水平夹角8~10度 100 相对喷煤点对错开, 夹角10度 伸入炉壁有效长 度20mm
- 1、下载文档前请自行甄别文档内容的完整性,平台不提供额外的编辑、内容补充、找答案等附加服务。
- 2、"仅部分预览"的文档,不可在线预览部分如存在完整性等问题,可反馈申请退款(可完整预览的文档不适用该条件!)。
- 3、如文档侵犯您的权益,请联系客服反馈,我们会尽快为您处理(人工客服工作时间:9:00-18:30)。
现状:
一、我厂采用南京凯胜院设计的直筒分解炉,下锥体直接座落在烟室上面,三次风管以“一”字行单管切入炉内,而大多厂采用双管切入,喂煤点分对称两点入炉,设计位置分上中下三个部位,此结构造成较高风速的三次风直接吹扫一侧喂煤点,分解炉锥部靠喂煤点周边结皮严重。
结皮形成期受三个方面影响,一是回转窑初投料时期,一定量的煤灰粘附在分解炉锥部,与料粉一起形成低温熔融液相,粘附在分解炉锥部。
另外三次风温和炉内温度偏低,煤粉燃烧不好,夹裹在料内,与料一起形成低温熔融液相,粘附在分解炉锥部;二是生产期间,不同矿点的石灰石直接入破碎机,预均化效果差,每堆石灰石品质差异比较大,并且同一堆不同点的石灰石品质也有较大的差异,再加上原煤成分波动大,均化效果差,时常出现煤料不对口,分解炉温度控制有一定的滞后,为分解炉锥部结皮创造条件;三是煤粉称频繁跑煤,较大量的煤粉不能完全燃烧,随料粉贴附在炉壁,并且大量的煤粉入炉,会形成局部高温,造成分解炉结皮加重。
二、我厂使用原煤挥发份低,细度控制较细,喂煤点本应放在下部,但由于燃烧比较快,只能提到上部,进入三次风吹扫区,炉内出现偏流,炉内煤粉不能和物料充分的混合,而吹到炉壁燃烧,形成结皮。
三、煤粉输送管道直径227mm,入炉前分两支支管,支管直径为163mm。
原使用煤粉发热量小于5500 kcal/kg,用量比较大,所以管径比较粗。
目前使用煤粉发热量大于6000 kcal/kg,用量比较小,较粗管径的管道内煤粉流动不稳定,造成分解炉煤管火焰不稳定,煤粉燃烧不稳定。
后果:
1、分解炉锥部结皮厚,通风差,窑内出现还原气氛,还原性黄心料比较严重。
窑内通风不好,窑头火焰不顺畅,窑头喷煤管易结焦,火焰分叉,窑皮不稳定,对耐火材料使用寿命影响较大,并且分叉火焰扫料,出现还原性黄心料。
结皮清理过程中可能会有大块结皮垮落,卡在分解炉锥部或者烟室斜坡,瞬间的正压喷火对人员伤害比较大,危险性比较高。
清理过程中检查门开的多,漏入大量的冷风,并且需要使用气管或者水枪清理,对生产稳定性及产质量影响比较大,另外瞬间的正压和喷出的小颗粒,存在对人员造成烧伤、烫伤的危害。
2、结皮垮落,卡在分解炉锥部或缩口。
需要大幅度的减产或者停窑,造成电耗煤耗上升,生产成本增加。
频繁的停窑,对一些主机、辅机设备及耐火材料使用寿命会有一定的影响。
结皮清理过程中使用风镐、压缩空气、水枪或者炸药,人员的危险性比较大,可能会出现正压或者颗粒物喷出伤人,结皮瞬间垮落撞击清理工具,伤害到清理人员,且使用炸药时会有可能震落耐火材料。
改造内容:
1、分解炉煤管上移,定在设计中的最上部位置。
2、煤粉输送管道内径变小,直径由148mm缩小到138mm。
3、撒料台铺耐热钢板,确保生料入炉分散均匀。
4、三次风管与分解炉交接处上顶加厚,靠外壁侧浇筑厚200 mm,宽500 mm,高600 mm的挡风墙,确保三次风上切入点在分解炉煤管的下部。
5、在分解炉喷嘴上方向斜右侧加装空气炮。
改造后效果:
1、结皮少,垮落几率大大下降,停窑次数减少;
2、系统通风好,窑内还原气氛下降,黄心料减少;
3、窑内火焰顺畅,形状良好,窑皮稳定,窑内煅烧稳定,熟料结粒好;
4、分解炉跑煤频率下降,煤粉燃烧效果好,煤料混合充分;
4、煤耗、电耗等生产指标下降,生产成本下降。