STRATCO硫酸烷基化工艺技术特点及影响因素分析_厉建伦
硫酸烷基化工艺腐蚀分析及应对措施研究

硫酸烷基化工艺腐蚀分析及应对措施研究
硫酸烷基化工艺是一种重要的化工生产方法,但同时也存在着一些腐蚀问题。
本文将分析硫酸烷基化工艺中可能存在的腐蚀问题,并提出相应的解决措施。
硫酸烷基化工艺涉及到硫酸的使用,硫酸具有很强的腐蚀性。
在生产过程中,硫酸可能会与设备和管道内壁接触,导致设备和管道的腐蚀。
硫酸还可能与其他金属离子或化合物形成酸性环境,加速设备和管道的腐蚀。
针对硫酸的腐蚀问题,可以采取以下应对措施:
1. 选择耐腐蚀材料:在设计和选择设备和管道时,应优先选择耐腐蚀材料,例如高合金钢,不锈钢等。
这些材料具有较强的抗硫酸腐蚀能力,可以有效延长设备和管道的使用寿命。
2. 强化涂层保护:在设备和管道内壁涂覆一层耐腐蚀的涂层,可以防止硫酸直接接触设备和管道的金属表面,减少腐蚀的发生。
常用的涂层材料包括聚氨酯涂层、环氧涂层等。
3. 控制工艺条件:在硫酸烷基化工艺中,通过控制工艺条件,如温度、压力和流速等参数,可以减少硫酸对设备和管道的腐蚀。
降低硫酸的浓度和温度,减少腐蚀的程度。
4. 定期维护和检修:对设备和管道进行定期的维护和检修,及时清除设备和管道内的污垢和腐蚀产物,可以减少腐蚀的发生。
定期检查设备和管道的腐蚀情况,及时更换受损的部件,保证设备和管道的正常运行。
针对硫酸烷基化工艺中的腐蚀问题,可以通过选择耐腐蚀材料、强化涂层保护、控制工艺条件和定期维护和检修等措施来解决。
这些措施可以有效降低腐蚀的发生,延长设备和管道的使用寿命,保障硫酸烷基化工艺的安全生产。
烷基化工艺的技术特点及发展状况
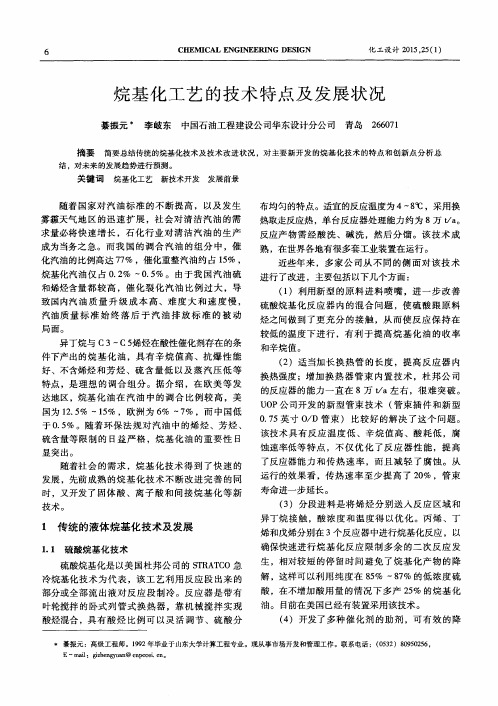
硫含 量等 限 制 的 日益 严 格 ,烷 基 化 油 的 重 要 性 日
显 突出 。
随着社 会 的 需 求 ,烷 基 化 技 术 得 到 了快 速 的
了反应器能力和传热速 率 ,而且减轻 了腐蚀 。从 运行的效果看 ,传热速率至少提高 了 2 0 % ,管束
寿命 进一 步延长 。 ( 3 ) 分段 进料 是 将 烯 烃 分别 送 人 反 应 区域 和 异 丁烷 接 触 ,酸浓 度 和 温 度 得 以优 化 。丙 烯 、丁
6
I GN
化 工设 计 2 0 1 5 , 2 5 ( 1 )
烷基 化工 艺 的技 术 特 点及 发展 状 况
綦 振元 李 岐东 中 国石 油工程 建设 公 司华东 设计 分公 司 青岛 2 6 6 0 7 1
丙烯丁1传统的液体烷基化技术及发展烯和戊烯分别在3个反应器中进行烷基化反应以11硫酸烷基化技术确保快速进行烷基化反应限制多余的二次反应发生相对较短的停留时间避免了烷基化产物的降硫酸烷基化是以美国杜邦公司的stratco急冷烷基化技术为代表该工艺利用反应段出来的解这样可以利用纯度在8587的低浓度硫部分或全部流出液对反应段制冷
烷 基化 汽 油仅 占 0 . 2 % ~ 0 . 5 % 。 由 于我 国 汽 油 硫
布均 匀 的特 点 。适 宜的反应 温度 为 4— 8 ℃ ,采用 换
热取走反应 热 ,单 台反 应器 处理 能力 约 为 8万 t / , a 。 反应 产 物 需 经 酸洗 、碱 洗 ,然 后 分 馏 。该 技 术 成 熟 ,在世 界各 地有很 多套 工业装 置在运 行 。 近些 年来 ,多 家 公 司从 不 同 的侧 面 对 该 技 术
硫酸烷基化反应器内的混合 问题 ,使硫 酸跟原料 烃之间做到了更充 分的接触 ,从而使反应保 持在
硫酸法烷基化工艺的推进
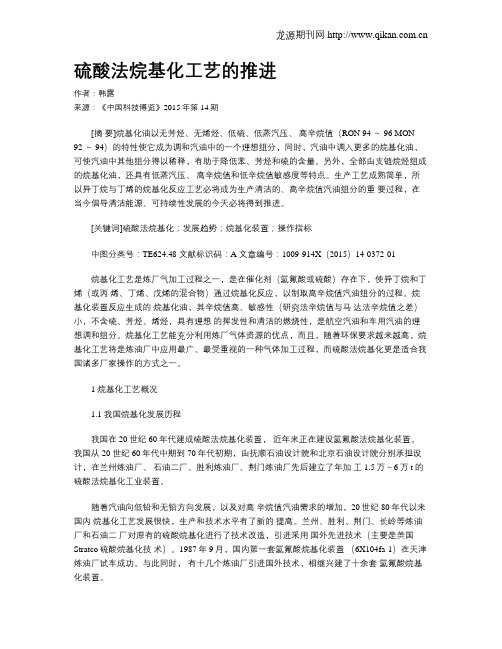
硫酸法烷基化工艺的推进作者:韩露来源:《中国科技博览》2015年第14期[摘要]烷基化油以无芳烃、无烯烃、低硫、低蒸汽压、高辛烷值(RON 94 ~ 96 MON 92 ~ 94)的特性使它成为调和汽油中的一个理想组分,同时,汽油中调入更多的烷基化油,可使汽油中其他组分得以稀释,有助于降低苯、芳烃和硫的含量。
另外,全部由支链烷烃组成的烷基化油,还具有低蒸汽压、高辛烷值和低辛烷值敏感度等特点。
生产工艺成熟简单,所以异丁烷与丁烯的烷基化反应工艺必将成为生产清洁的、高辛烷值汽油组分的重要过程,在当今倡导清洁能源、可持续性发展的今天必将得到推进。
[关键词]硫酸法烷基化;发展趋势;烷基化装置;操作指标中图分类号:TE624.48 文献标识码:A 文章编号:1009-914X(2015)14-0372-01烷基化工艺是炼厂气加工过程之一,是在催化剂(氢氟酸或硫酸)存在下,使异丁烷和丁烯(或丙烯、丁烯、戊烯的混合物)通过烷基化反应,以制取高辛烷值汽油组分的过程。
烷基化装置反应生成的烷基化油,其辛烷值高、敏感性(研究法辛烷值与马达法辛烷值之差)小,不含硫、芳烃、烯烃,具有理想的挥发性和清洁的燃烧性,是航空汽油和车用汽油的理想调和组分。
烷基化工艺能充分利用炼厂气体资源的优点,而且,随着环保要求越来越高,烷基化工艺将是炼油厂中应用最广、最受重视的一种气体加工过程,而硫酸法烷基化更是适合我国诸多厂家操作的方式之一。
1 烷基化工艺概况1.1 我国烷基化发展历程我国在20世纪60年代建成硫酸法烷基化装置,近年来正在建设氢氟酸法烷基化装置。
我国从20 世纪60年代中期到70年代初期,由抚顺石油设计院和北京石油设计院分别承担设计,在兰州炼油厂、石油二厂、胜利炼油厂、荆门炼油厂先后建立了年加工1.5万~6万t的硫酸法烷基化工业装置。
随着汽油向低铅和无铅方向发展,以及对高辛烷值汽油需求的增加,20世纪80年代以来国内烷基化工艺发展很快,生产和技术水平有了新的提高。
SINOALKY硫酸烷基化装置工艺优化及节能措施

SINOALKY硫酸烷基化装置工艺优化及节能措施于吉平1,姚建辉1 ,董明会2(1.中国石油化工股份有限公司石家庄炼化分公司,河北省石家庄市050000;2.中国石油化工股份有限公司石油化工科学研究院,北京市100083)摘要:通过对某装置SINOALKY硫酸烷基化工艺运行能耗数据进行分析,发现通过工艺调整,将脱异丁烷塔操作压力由0.65MPa降至0.45MPa,回流量由123t/h降至44t/h后可降低1.0MPa蒸汽消耗5.5t/h;通过合理调整烷基化反应器的操作参数,烷烯比由14∶1降至10∶1可降低1.0MPa蒸汽消耗5t/h,电耗较设计值降低50%;通过将制冷压缩机出口压力由0.74MPa降至0.5MPa,可降低汽轮机3.5MPa蒸汽消耗13t/h。
通过投用精密聚结器,实现切出产物碱洗水洗流程,一方面可降低1.0MPa蒸汽、除盐水、电、新鲜水等公用工程介质的消耗;另一方面可减少含盐污水外排量、降低酸碱消耗,年综合效益约500万元。
采取上述措施后装置总能耗降低约30%。
关键词:SINOALKY 硫酸烷基化 工艺节能 反应系统 分馏系统 精制系统 制冷系统 烷基化油是以C8支链烷烃为主不含烯烃与芳烃的混合物,几乎不含硫元素和氮元素,敏感性和蒸气压低,是一种清洁、理想的高辛烷值汽油调合组分。
2020年国Ⅵ汽油标准与乙醇汽油标准的全面实施,将对现有MTBE装置运行造成较大冲击,这意味着市场对烷基化油的需求将出现井喷式增长[1]。
随着环保法规要求的日益严格,生产满足国家环保法规要求的清洁汽油成为当前中国石油化工行业面临的主要任务之一[2]。
拥有中国石化自主知识产权的新型SINOALKY硫酸烷基化装置于2018年6月在某炼油厂开车成功,装置规模为200kt/a,开工后运行平稳,但运行初期综合能耗高于设计值。
后期根据现场操作总结,不断提出技改措施以降低装置能耗,具体措施包括降低脱异丁烷塔的操作压力,调整核心设备反应器的操作参数,降低制冷压缩机出口压力,切出产物碱洗水洗流程等。
硫酸法烷基化的工艺原理和反应系统

硫酸法烷基化的工艺原理和反应系统王欢(大庆炼化公司炼油生产二部,黑龙江 大庆 163000)摘要:烷基化技术包括很多种,其中硫酸法烷基化主要指STRATCO 硫酸法烷基化技术中流出物制冷技术,此工艺技术成熟可靠,有着酸资源丰富,价格便宜,可回收,能够连续保持活性等优点。
该工艺中硫酸腐蚀性较强,设备易腐蚀,消耗酸较大,容易产生大量的酸渣,装置需要长周期运行。
文章主要探讨硫酸法烷基化的加氢硫酸法烷基化和烷基化反应原理和主要的工艺流程。
关键词:硫酸法烷基化;工艺原理;工艺流程中图分类号:TQ111文献标志码:A文章编号:1008-4800(2021)08-0160-02DOI:10.19900/ki.ISSN1008-4800.2021.08.077The Process Principle and Reaction System of Sulfuric Acid AlkylationWANG Huan (Daqing Refining & Chemical Company Production Department II , Daqing 163000, China)Abstract: There are many kinds of alkylation technologies, among which sulfuric acid alkylation mainly refers to the effluentrefrigeration technology in STRATCO sulfuric acid alkylation technology. This process is mature and reliable, has the advantages of rich acid resources, low price, recyclability, and continuous activity. In this process, the sulfuric acid is more corrosive, the equipment is easy to corrode, the consumption of acid is large, and it is easy to produce a large amount of acid slag, the device needs long-term operation. This paper mainly discusses the principle and main process flow of hydrosulfuric acid alkylation and alkylation reaction of sulfuric acid alkylation.Keywords: sulfuric acid alkylation; process principle; process flow0 引言伴随时代的发展,油气生产的标准越来越为严格,在石油炼制工业产业中,通过烷基化技术的运用,可以提高汽油成分中的辛烷值和抗暴性能,从而提高汽油的整体效率,满足化工产业的发展需求。
硫酸烷基化工艺腐蚀分析及应对措施

硫酸烷基化工艺腐蚀分析及应对措施陈子香【摘要】硫酸烷基化的催化剂为浓硫酸,其腐蚀性强,对设备管道等影响较大,若设计时考虑不够周到,设备管道等的腐蚀可能会引起物料泄露,严重时会发生事故.这不仅会影响生产,还有可能造成生命和财产损失.因此,对从事这一行业的人员应该重视此问题.对于此工艺中可能出现的腐蚀问题应详细分析,并提出相应的措施,这样可以给同类项目提供一定的参考.【期刊名称】《天津化工》【年(卷),期】2016(030)006【总页数】3页(P15-17)【关键词】硫酸;烷基化;腐蚀;分析;应对措施【作者】陈子香【作者单位】大连派思燃气系统股份有限公司,辽宁大连116600【正文语种】中文【中图分类】TE624.4+8在石油炼制工业中,异丁烷与丁烯的烷基化(碳四烷基化、异丁烷烷基化)是生产清洁高辛烷值汽油调和组分的重要工艺过程之一,国际上的烷基化技术有:固体酸法、硫酸法和氢氟酸法三种。
固体酸法烷基化技术到目前为止都还没有实现工业化[1]。
氢氟酸烷基化装置和硫酸烷基化装置都是技术成熟可靠的工艺。
氢氟酸烷基化装置具有常温下反应、无需制冷系统的优点,但是催化剂氢氟酸具有强腐蚀性及毒性,对环境危害比较大[2]。
硫酸法烷基化装置酸耗量大,需要废酸处理设施,但作为催化剂,硫酸的腐蚀性及对环境的影响要比氢氟酸小。
从环境保护和安全角度考虑,硫酸烷基化技术更具优势。
硫酸法碳四烷基化工艺[3],由以下几个部分组成:原料水洗、进料制冷部分、反应部分、流出物处理部分、脱异丁烷/正丁烷部分、废酸脱气中和部分、酸储存部分。
工艺流程示意图见图1。
本工艺的工艺原理是异丁烷-丁烯进料与装置循环异丁烷和冷剂一起进入反应器,在硫酸的催化作用下,异丁烷和丁烯发生烷基化反应,生成烷基化油。
异丁烷与丁烯烷基化反应很复杂,主反应符合正碳离子链式反应机理,异丁烷与丁烯加成为异辛烷,副反应主要有自聚、断裂、异构化、酯化等反应。
主反应基本如下:由于过程中有浓硫酸做为催化剂,因此防范浓硫酸对设备及管道组成件的腐蚀至关重要。
硫酸烷基化工艺腐蚀分析及应对措施研究

硫酸烷基化工艺腐蚀分析及应对措施研究硫酸烷基化工艺是工业生产中常见的一种化工生产工艺,其在石化、化肥、农药等行业有着广泛的应用。
在硫酸烷基化过程中,常常会遇到腐蚀问题,腐蚀严重影响了设备的使用寿命和生产效率。
对硫酸烷基化工艺腐蚀分析及应对措施的研究具有重要意义。
一、硫酸烷基化工艺腐蚀分析1. 腐蚀原因分析在硫酸烷基化工艺中,腐蚀主要是由于以下几个原因引起的:(1)介质腐蚀:硫酸烷基化反应中使用的介质中含有大量的硫酸、酸性离子等腐蚀性物质,这些物质可能对设备材料产生腐蚀作用。
(2)温度腐蚀:硫酸烷基化反应需要在一定的温度下进行,高温环境会加剧设备的腐蚀情况。
(1)表面腐蚀:设备表面出现腐蚀斑点、锈蚀等现象。
(2)局部腐蚀:设备的某些局部受到腐蚀,出现孔洞、腐蚀凹陷等情况。
(3)材料疲劳:长期腐蚀会导致设备材料疲劳、脆化,降低了设备的使用寿命。
针对硫酸烷基化工艺中的腐蚀问题,需要进行腐蚀评价分析,根据设备材料、反应条件等因素进行腐蚀风险评估,确定腐蚀程度和影响范围,为后续的防腐措施提供重要依据。
1. 材料选择在硫酸烷基化工艺中需要选择耐酸性能好的材料,如不锈钢、镍基合金、耐酸塑料等,以提高设备的耐腐蚀性能。
2. 表面处理对设备进行表面处理,如镀锌、喷涂耐酸涂料等,提高设备表面的抗腐蚀能力。
3. 设备设计在设备设计过程中,考虑对腐蚀性介质的隔离,减少介质对设备的腐蚀作用。
4. 防腐涂层5. 监测与维护定期对设备进行腐蚀情况的监测和维护,发现问题及时进行修复和更换,延长设备的使用寿命。
6. 新技术应用引进新技术,如防腐蚀合金材料、防腐蚀涂料等,提高设备的耐腐蚀性能。
三、结语硫酸烷基化工艺腐蚀问题是工业生产中常见的难题,为了保证生产设备的安全运行和生产效率的提高,必须加强对硫酸烷基化工艺腐蚀分析及应对措施的研究。
针对硫酸烷基化工艺中的腐蚀问题,必须做好材料选择、设备设计、防腐涂层等工作,同时加强对设备腐蚀情况的监测和维护,引进新技术应用,从源头上预防腐蚀问题的发生。
硫酸烷基化解析

----------------------- Page 1-----------------------文件编码:CHRP-104-PE-OI-0001-2011烷基化装置操作规程版本/状态:B/1分发号:中海石油炼化有限责任公司惠州炼油分公司----------------------- Page 2-----------------------2011年01月01日发布2011月01日实施编写签字表名称签字时间编写人审校人审核人----------------------- Page 3-----------------------专业会审表单位专业名称签字时间技术中技术专业心质量专业指挥中心调度专业动设备专业设备中静设备专业心仪表专业电气专业安全专业HSE中环保专业心消防专业职业卫生专业--------------------- Page 4-----------------------审核签字表中心领导签字时间技术中心经理设备中心经理HSE中心经理批准签字表公司领导签字时间总工程师目录第一章工艺技术规程3第一节设计依据第二节装置概况、特点及工艺原理第三节工艺流程说明第四节工艺指标第五节原材料指标第六节半成品、成品主要性质指标第七节公用工程(水、电、汽、风等)指标第八节主要操作条件及质量指标详见第十二节第九节原材料、公用工程消耗、能耗计算指标和节能措施.第十节物料平衡第十一节主要设备选择及工艺计算汇总第十二节生产控制化验分析第十三节装置内外关系第二章岗位操作法54第一节烷基化装置操作原则第二节预加氢系统操作法第三节烷基化反应系统操作法第四节致冷系统操作法第五节分馏系统操作法第三章岗位开停工规程86第一节开工规程第二节停工规程第四章设备操作规程164第一节大型专用设备操作规程第二节基础设备操作规程第五章事故处理191第一节事故处理原则第二节紧急停工方法第三节事故处理预案第四节事故处理预案演练规定第六章仪表控制系统操作法231第一节仪表控制系统概况及操作第二节工艺操作仪表控制回路说明第四节仪表投用、停用及注意事项第七章操作规定325第一节定期工作规定第二节操作规定第八章安全生产及环境保护330第一节安全知识第二节安全规定第三节烷基化装置防风防台措施第四节同类装置典型事故分析、处理方法及经验教训.第五节烷基化装置易燃易爆物质的安全性质第六节本装置主要有害物质的性质第七节装置污染物主要排放部位和排放的主要污染物.第八节消防器材、设施使用方法及消防规定第九节职业卫生九章附录366 附表一主要设备明细表附表二主要设备结构图附表三装置平面分布图附表四可燃气体报警仪布置图附表五装置消防设施布置图附表六控制参数报警值附表七安全阀定压值附录八工艺流程简图附表九开工统筹图附录十停工统筹图----------------------- Page 7-----------------------惠炼16万吨/年烷基化装置操作规程第3 页共397 页第一章工艺技术规程第一节设计依据1中国海洋石油总公司惠州炼油项目管理项目组关于“惠州炼油项目基础设计工作”的委托书(2005年6月16日);2中国石化工程建设公司与中国海洋石油总公司签订的关于开展“中国海洋石油总公司惠州炼油项目基础设计”的合同和合同附件;3 DUPONT公司提供的硫酸烷基化工艺包;4中国海洋石油总公司惠州炼油项目设计统一规定;5上游MTBE、加氢裂化装置提供的原料液化气量及组成;6中国石化工程建设公司与中国海洋石油总公司召开的PFD、PID等审查会会议纪要。
硫酸烷基化工艺腐蚀分析及应对措施研究

硫酸烷基化工艺腐蚀分析及应对措施研究硫酸烷基化是一种重要的化工生产工艺,但也存在一定的腐蚀问题。
本文就硫酸烷基化工艺的腐蚀问题进行分析,并提出相应的应对措施。
1. 腐蚀症状硫酸烷基化过程中,腐蚀主要表现为设备内部的腐蚀和管道的腐蚀。
设备内部的腐蚀主要表现为反应釜内壁和底部的腐蚀,而管道的腐蚀则表现为管道内壁的腐蚀和管道连接处的腐蚀。
腐蚀症状主要包括:(1)设备内壁和底部出现磨损、毛刺和凸起。
(2)管道内壁出现腐蚀坑和凹陷,管道连接处出现漏气现象。
(3)设备和管道表面出现斑点、腐蚀颜色不同等。
2. 腐蚀原因硫酸烷基化过程中,腐蚀主要是由于以下原因所引起的:(1)化学腐蚀:硫酸极具腐蚀性,因此在硫酸烷基化过程中难免产生化学腐蚀。
(2)机械磨损:在反应釜内部,由于反应物之间的剧烈反应以及搅拌器的搅拌作用,会导致设备内部的机械磨损,从而产生腐蚀。
(3)温度和压力:硫酸烷基化需要在高温高压下进行,高温和高压会使设备产生应力变形,从而大大降低了设备的抗腐蚀能力。
3. 应对措施为了解决硫酸烷基化过程中的腐蚀问题,需要采取相应的应对措施,包括:(1)选择合适的材料:在原材料的选择上,应尽量选用耐腐蚀的材料。
例如,采用不锈钢、玻璃钢等材料制造设备和管道,这些材料可以有效提高设备和管道的耐腐蚀性能。
(2)合理的维护保养:对设备和管道进行定期的维护保养,使用防腐材料进行修补和涂层处理,有效延长设备和管道的使用寿命。
同时,应注意设备和管道的清洗,避免在清洗过程中对设备和管道造成二次损伤。
综上所述,硫酸烷基化工艺腐蚀问题的解决需要采取一系列的应对措施,包括选择合适的材料、合理的维护保养和严格控制温度和压力等。
通过这些措施,可以有效保护设备和管道,延长设备和管道的使用寿命。
硫酸烷基化工艺腐蚀分析及应对措施研究

硫酸烷基化工艺腐蚀分析及应对措施研究【摘要】本文针对硫酸烷基化工艺中常见的腐蚀问题进行了深入分析和研究,通过对腐蚀机理、影响因素及应对措施进行论述,总结了现有研究进展。
在腐蚀问题日益凸显的情况下,对腐蚀控制和预防提出了有效的解决方案。
通过本文的研究,可以更好地认识硫酸烷基化工艺中腐蚀问题的本质和特点,为相关行业提供技术支持和参考。
未来的研究方向包括进一步探索腐蚀机理、开发新型抗腐蚀材料以及提高腐蚀控制技术水平,以实现对硫酸烷基化工艺腐蚀问题的更好预防和处理。
【关键词】硫酸烷基化工艺、腐蚀、分析、应对措施、研究背景、研究意义、腐蚀机理、影响因素、常见问题、研究进展、成果总结、未来展望。
1. 引言1.1 研究背景硫酸烷基化工艺是一种常见的化工生产方法,广泛应用于石油化工、合成染料、医药和农药等领域。
随着生产规模的不断扩大和生产条件的复杂化,硫酸烷基化工艺在实际生产中面临着严重的腐蚀问题。
在硫酸烷基化工艺中,金属设备受到硫酸和烷基物所引起的腐蚀威胁,容器、管道和阀门等设备往往存在着腐蚀的风险。
腐蚀不仅会降低设备的使用寿命,还会导致设备的安全隐患和生产事故的发生。
研究硫酸烷基化工艺腐蚀问题及应对措施具有重要意义。
通过对硫酸烷基化工艺腐蚀机理的深入分析,可以更好地了解腐蚀过程中的原理和规律,为腐蚀问题的预防和控制提供科学依据。
探讨硫酸烷基化工艺中常见的腐蚀问题及应对措施,可以有效减少生产中的腐蚀损失,提高设备的稳定性和可靠性。
对硫酸烷基化工艺腐蚀问题的研究具有重要的现实意义和应用价值。
1.2 研究意义硫酸烷基化工艺在化工生产中具有重要的应用价值,能够实现烷基化反应,提高产物的附加值。
随着工艺规模的扩大和生产条件的变化,硫酸烷基化工艺腐蚀问题逐渐凸显出来。
腐蚀问题不仅会影响设备的正常运行,还会危及生产安全,导致生产事故的发生。
研究硫酸烷基化工艺腐蚀分析及应对措施具有重要的意义。
通过对硫酸烷基化工艺腐蚀进行深入研究,可以更好地了解腐蚀机理,找出影响腐蚀的因素,提出有效的应对措施,为化工生产提供技术支撑和保障。
硫酸烷基化工艺腐蚀分析及应对措施研究

硫酸烷基化工艺腐蚀分析及应对措施研究硫酸烷基化工艺是一种在精细化学品生产中广泛使用的化学反应过程,但随着工艺的推广应用,其腐蚀问题日益显著。
针对硫酸烷基化工艺的腐蚀问题,本文进行了相关分析并提出了相应的应对措施。
硫酸烷基化反应过程中存在着许多影响腐蚀的因素,如进料质量、反应温度、反应物浓度、气体流量、反应容器材质等。
其中,温度是影响腐蚀的最主要因素。
反应温度高于170℃时,硫酸烷基化反应会产生大量的硫酸酰烷基,硫酸酰烷基能形成极具腐蚀性的硫酸。
此外,硫酸烷基化反应中的反应物也会影响腐蚀性。
含有醇类反应物的硫酸烷基化反应会产生较高浓度的氯化氢,而氯化氢对不锈钢等材质很容易产生腐蚀作用。
此外,不同反应物的比例也会对腐蚀性产生影响,比如甲苯与氯化硫酸反应的比例过高,会使腐蚀速度加快。
针对硫酸烷基化工艺的腐蚀问题,我们可以从以下方面采取应对措施:1、选择合适材质在硫酸烷基化反应中,由于反应物的不同组合会导致生成的化学物质不同,其对材质的腐蚀程度也不同。
因此,在选择精细化学品生产中的反应容器时,应根据化学反应类型与条件来选用适应性良好的材质,如碳钢、316L不锈钢、锆合金等。
2、控制反应温度反应温度是影响硫酸烷基化反应腐蚀的最主要因素。
降低反应温度可以减少产生的硫酸酰烷基浓度,进而减缓腐蚀的速度。
因此,在生产过程中应控制反应温度在170℃以下。
同时,将硫酸酰烷基排放到处理设备中,在排放前进行稀释也可以减轻腐蚀问题。
3、加入缓蚀剂在反应中加入适当的缓蚀剂,能起到减缓、抑制腐蚀的作用。
常用的缓蚀剂有咪唑类缓蚀剂和卡宾类缓蚀剂等。
4、加强清洗与维护及时清洗反应容器、保养设备,以及设立检测系统进行监测,都能帮助尽早发现、处理反应容器内壁存在的腐蚀问题。
此外,设立防腐涂层也是一种有效的预防措施。
5、规范生产操作生产操作的规范化,能最大程度地避免人为因素引发的安全事故。
在硫酸烷基化反应中,要求合格的操作技术员、表明化学物质的标识、采用个人防护措施等,也有助于减少潜在风险。
硫酸烷基化工艺腐蚀分析及应对措施研究

硫酸烷基化工艺腐蚀分析及应对措施研究硫酸烷基化是一种重要的化工工艺,在石化、制药、农药等领域都有广泛应用。
由于硫酸烷基化过程中存在的腐蚀问题,工艺的稳定性和安全性可能会受到威胁。
对硫酸烷基化工艺的腐蚀问题进行分析并采取相应的应对措施是非常必要的。
硫酸烷基化工艺涉及到硫酸与烷烃反应生成亚硫酸盐的过程。
在该过程中,腐蚀主要由以下两方面导致。
由于反应过程中产生的亚硫酸盐具有腐蚀性,会对设备和管道内壁产生腐蚀。
亚硫酸盐在酸性条件下易于氧化为硫酸,硫酸是一种强酸,具有很强的腐蚀性。
在硫酸烷基化过程中,设备和管道的材料选择非常重要。
一般而言,不锈钢等高耐腐蚀材料是比较常用的选择。
可以通过在设备和管道内部进行涂层处理,增加腐蚀抵抗能力。
还可以定期进行腐蚀监测,及时修复或更换受损的设备和管道,以保障工艺的稳定性和安全性。
在硫酸烷基化过程中,反应温度较高,会导致设备和管道的金属材料受热腐蚀。
高温环境下,金属材料容易发生氧化、蒸发、颗粒剥离等现象,从而降低了设备和管道的使用寿命,甚至引发安全事故。
为了解决这个问题,可以采取降温措施,如在设备和管道周围设置隔热层、增加冷却剂的流速、调整反应温度等。
合理设计设备和管道的结构,选择耐高温材料,也可以有效减少热腐蚀的发生。
为了进一步提高硫酸烷基化工艺的稳定性和安全性,还可以采取以下措施:1. 设备和管道的定期维护和保养,及时发现并处理可能存在的腐蚀问题。
2. 强化操作人员的培训和安全意识,确保他们对工艺过程的理解和控制。
3. 加强设备和管道的监测,通过温度、压力、流量等参数的实时监控,及时发现异常情况并采取措施。
4. 对离子膜进行合理选择和保养,防止其受腐蚀。
硫酸烷基化工艺的腐蚀问题是一个需要重视并解决的难题。
通过合理选择材料、加强设备和管道的维护、控制反应温度、加强操作人员培训等措施,可以有效降低腐蚀的发生,提高工艺的稳定性和安全性。
硫酸烷基化技术进展
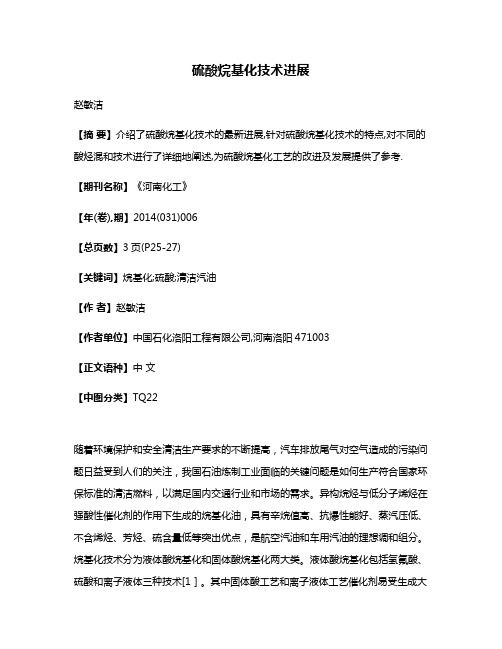
硫酸烷基化技术进展赵敏洁【摘要】介绍了硫酸烷基化技术的最新进展,针对硫酸烷基化技术的特点,对不同的酸烃混和技术进行了详细地阐述,为硫酸烷基化工艺的改进及发展提供了参考.【期刊名称】《河南化工》【年(卷),期】2014(031)006【总页数】3页(P25-27)【关键词】烷基化;硫酸;清洁汽油【作者】赵敏洁【作者单位】中国石化洛阳工程有限公司,河南洛阳471003【正文语种】中文【中图分类】TQ22随着环境保护和安全清洁生产要求的不断提高,汽车排放尾气对空气造成的污染问题日益受到人们的关注,我国石油炼制工业面临的关键问题是如何生产符合国家环保标准的清洁燃料,以满足国内交通行业和市场的需求。
异构烷烃与低分子烯烃在强酸性催化剂的作用下生成的烷基化油,具有辛烷值高、抗爆性能好、蒸汽压低、不含烯烃、芳烃、硫含量低等突出优点,是航空汽油和车用汽油的理想调和组分。
烷基化技术分为液体酸烷基化和固体酸烷基化两大类。
液体酸烷基化包括氢氟酸、硫酸和离子液体三种技术[1]。
其中固体酸工艺和离子液体工艺催化剂易受生成大分子烯烃影响而失活,催化剂费用昂贵、对原料要求高、流程复杂。
因此固体酸催化工艺和离子液体工艺还未能实现工业化。
氢氟酸法烷基化技术的弱点是采用的氢氟酸催化剂具有腐蚀性、挥发性和毒性,因此,该工艺的发展受到阻碍。
相比氢氟酸法工艺,硫酸法工艺则不会产生有毒的气体,操作相对安全,而且硫酸资源丰富,价格便宜,生成的烷基化油质量高,更适合我国的国情。
1 硫酸法烷基化技术烷基化反应的控制步骤为异丁烷向硫酸的传质,在硫酸法烷基化过程中,由于硫酸催化剂的高黏度、高密度、高表面张力特点,而且异丁烷在硫酸中的过程溶解性低,突出了该工艺过程的化学反应与分子扩散的矛盾,微观混和状态直接影响了反应产物的选择性和收率,因此对酸烃混和的要求非常严格。
在反应过程中,应使酸烃两相充分地混和,以稀释烯烃,防止局部浓度过高,抑制烷基化副反应的产生;反应结束后,酸烃乳化液应快速分离,减少烷基化油和硫酸之间的二次反应[2]。
硫酸法烷基化装置腐蚀影响因素分析及防护措施

硫酸法烷基化装置腐蚀影响因素分析及防护措施摘要:在硫酸法烷基化装置运行过程中,硫酸会对装置造成较为严重的腐蚀影响。
做好腐蚀问题的防护是确保装置安全运行的关键。
基于此,文章对硫酸法烷基化装置的易腐蚀部位进行了分析,以及分析了影响装置腐蚀的相关因素,最后对装置的腐蚀防护措施进行了有效探讨,以提高烷基化装置的安全生产运行效果。
关键词:硫酸法;烷基化装置;腐蚀;影响;措施一、硫酸法烷基化装置易腐蚀部位(一)反应部位在装置运行过程中,反应器、酸烃聚结分离器、闪蒸罐等相关的设备、容器会受到硫酸的影响而产生均匀、轻微的腐蚀,在容器的器壁、底部都能够观察到浮锈,以及有液体流经留下的轻微流痕。
(二)反应化学处理部位装置中进行酸洗的筒体腐蚀痕迹较轻,但是内部的合金填料会受到较为严重的腐蚀,即便是没有穿孔的位置也只剩薄薄的一层。
同时,碱洗罐注入位置也会遭到严重腐蚀,尤其是在注入点的液体流态较为复杂,在中和反应时也会形成水分偏析现象,运行一段时间后也会由于内部沟槽冲蚀发生管线腐蚀泄漏。
即使是碱洗罐上封头在其内表面也会出现氧化腐蚀现象。
(三)分馏部位在装置的分馏过程中,脱异丁烷冷却位置会出现集中腐蚀,反应产物即便是经过酸洗、碱洗、水洗也不能完全去除脂类杂质,在反应塔的高温环境下会分解形成二氧化硫与水融合形成亚硫酸,进而对分馏塔造成腐蚀。
尤其是塔顶水冷器的腐蚀更为明显,管束腐蚀较为均匀。
以及在塔底的反应物中烷基硫酸盐与硫酸脂受高温分解、聚合,导致管束出现沉淀物堆积形成腐蚀。
(四)制冷压缩部位制冷压缩设备材质主要为碳钢,闪蒸气相夹带酸的影响会使得冷剂空冷器管束出现酸腐蚀,形成与脱异丁烷塔顶空冷管束一样的腐蚀问题。
(五)浓硫酸储罐部位酸储与输送设备以碳钢为主要材质,运行基本平稳,但是在新酸泵出口管线弯头位置会发生腐蚀问题,包括废酸泵出口管线也会腐蚀变薄、泄漏。
尤其是在夏季管线温度可达40摄氏度,泵口温度升高与发生湍流,会手打硫酸腐蚀问题进一步加重。
硫酸法烷基化产品质量影响因素及优化措施分析

硫酸法烷基化产品质量影响因素及优化措施分析摘要:硫酸法烷基化产品的质量会受到多种因素的影响,特别是对于硫酸法烷基化装置所生产的烷基化油,这种产品的辛烷值较高,硫含量较低,具有无烯烃、无芳烃、不含氧等特点,是汽油的最理想成分之一。
因此通过调整烷基化原料的组成,去除其中杂质的含量,确保生产设备的安全稳定运行就必须加强对于影响生产质量的因素分析,提升产品质量。
关键词:硫酸法烷基化产品;原料成分;因素分析引言:烷基化油的拂程很宽,顺应了当前新配方汽油的发展需求,如果只是使用烷基化油代替MTBE,就会导致原本的部分异构化物很难成为汽油的调和组分。
然而现在通过减小雷德蒸汽压的方式能够有效促进调和,因此就如何提升烷基化装置的生产效率以及生产稳定性,降低整个装置的运行成本成为当前生产中急剧待解的问题。
1硫酸法烷基化简介硫酸法烷基化是一种物制冷技术,这种技术已经有了较长时间的发展,艺术整体较为成熟,有很多工业企业都是以此技术为基础的生产装置。
我国是在上个世纪80年代引入的硫酸烷基化装置采用该技术进行生产,硫酸烷基化的主要优点是酸资源较为丰富,技术应用价格便宜,生产成本低,而且在回收的过程中因为硫酸烷基化的产品活性较高,可以让整个装置运行周期变得更长。
但是由于硫酸会腐蚀生产设备,硫酸法烷基化工艺的消耗酸会较大,而且会产生大量的污染物导致周围环境受到污染。
因此需要建立废酸再生装置来保证生产过程的环保性,由于生产而污染环境[1]。
2 原料对产品质量影响2.1原料各组分(1)丙烷及正丁烷这两种物质在玩机化反应过程中不会参加反应,因为这两种物质都属于惰性组分。
如果其含量过高会降低异丁烷进入酸相的速度,进而导致整个反应过程受到影响,使得烯烃在烷基化反应中发生自聚反应。
(2)丁烯在生产的过程中C8组分含量高,其中特别是2,2,4-三甲基戊烷的含量是最高的,并且由于异丁烯的活性是高于正丁烯的活性,催化剂的作用下容易发生自身聚合,从而溶解在酸相中,形成一种新的ASO酸性油。
硫酸烷基化工艺腐蚀分析及应对措施研究

硫酸烷基化工艺腐蚀分析及应对措施研究硫酸烷基化工艺是一种广泛应用于石油化工行业的重要技术。
由于硫酸具有很强的腐蚀性,对于硫酸烷基化设备的腐蚀问题一直是工艺研究和应用的难点之一。
本文将对硫酸烷基化工艺的腐蚀问题进行分析,并提出相应的应对措施。
我们需要了解硫酸烷基化工艺中可能存在的腐蚀问题。
硫酸本身是一种强酸,具有很强的腐蚀性,可以腐蚀大部分金属和非金属材料。
在硫酸烷基化工艺中,硫酸会与烷基化原料和反应产物产生直接接触,导致设备表面腐蚀。
硫酸烷基化反应中常常伴随着高温和高压的条件,进一步加剧了设备的腐蚀问题。
接下来,我们需要分析硫酸烷基化设备的腐蚀机理。
硫酸可以通过两种主要的腐蚀机理对设备进行腐蚀,即酸腐蚀和氧化腐蚀。
酸腐蚀是指硫酸直接与设备表面的金属发生反应,形成金属离子和硫酸盐,同时释放出氢气。
氧化腐蚀是指硫酸中存在的氧气参与腐蚀反应,形成金属氧化物。
针对硫酸烷基化设备腐蚀问题,我们可以采取以下应对措施:1. 材料选择:选择抗硫酸腐蚀性能优良的材料作为设备的构建材料。
常见的抗硫酸腐蚀材料有不锈钢、镍基合金等。
根据不同的工艺条件,可以使用涂层材料或陶瓷材料进行保护。
2. 设备设计:设计合理的设备结构和附属设备,减少硫酸接触表面积和腐蚀程度。
可以采用短管道、可拆卸的衬里等方式。
3. 操作控制:严格控制工艺操作参数,如温度、浓度、压力等,避免过高或过低的条件对设备造成腐蚀。
定期进行设备检修,及时清理设备内部的硫酸结垢和腐蚀产物。
4. 表面处理:对设备表面进行防腐处理,如采用表面镀锌、喷涂防腐漆等方式,形成一层保护膜,阻止硫酸对设备表面的直接腐蚀。
硫酸烷基化工艺的腐蚀问题是一个复杂而严重的技术难题。
通过合理的材料选择、设备设计、操作控制和表面处理等措施,可以有效地减少硫酸对设备的腐蚀,延长设备的使用寿命,提高生产效率和安全性。
对于硫酸烷基化设备的腐蚀问题还需要进一步的研究和探索,以不断改进和优化工艺。
硫酸法烷基化工艺技术探析
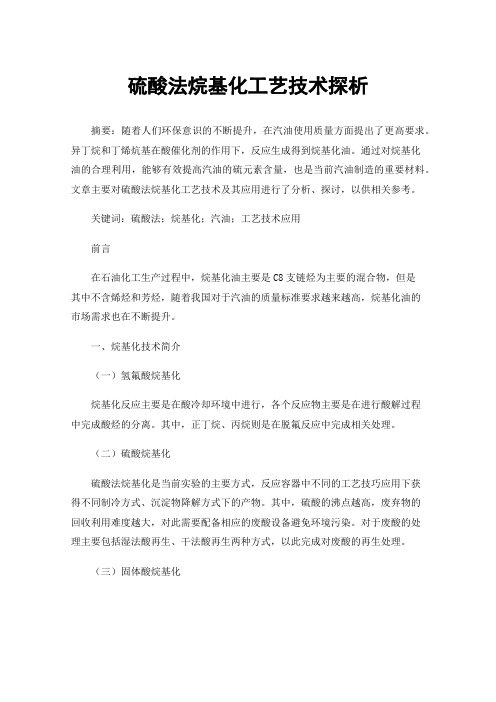
硫酸法烷基化工艺技术探析摘要:随着人们环保意识的不断提升,在汽油使用质量方面提出了更高要求。
异丁烷和丁烯炕基在酸催化剂的作用下,反应生成得到烷基化油。
通过对烷基化油的合理利用,能够有效提高汽油的硫元素含量,也是当前汽油制造的重要材料。
文章主要对硫酸法烷基化工艺技术及其应用进行了分析、探讨,以供相关参考。
关键词:硫酸法;烷基化;汽油;工艺技术应用前言在石油化工生产过程中,烷基化油主要是C8支链烃为主要的混合物,但是其中不含烯烃和芳烃,随着我国对于汽油的质量标准要求越来越高,烷基化油的市场需求也在不断提升。
一、烷基化技术简介(一)氢氟酸烷基化烷基化反应主要是在酸冷却环境中进行,各个反应物主要是在进行酸解过程中完成酸烃的分离。
其中,正丁烷、丙烷则是在脱氟反应中完成相关处理。
(二)硫酸烷基化硫酸法烷基化是当前实验的主要方式,反应容器中不同的工艺技巧应用下获得不同制冷方式、沉淀物降解方式下的产物。
其中,硫酸的沸点越高,废弃物的回收利用难度越大,对此需要配备相应的废酸设备避免环境污染。
对于废酸的处理主要包括湿法酸再生、干法酸再生两种方式,以此完成对废酸的再生处理。
(三)固体酸烷基化在进行固体酸烷基化过程中,主要是借助烷基化、催化反应来进行相关工艺的操作,使得反应物和催化剂分析。
这一反应过程对于设备的要求较低,并且不会出现酸泄漏问题,操作优势较为明显。
(四)离子液烷基化主要是借助对混合碳四原料的合理利用在离子液催化剂的作用下完成异丁烷与烯烃的反应,进而获得烷基化油。
这种类型的烷基化油的辛烷值较高,且不含烯烃、芳烃,敏感度也较小,与其他化合物具备较好的调和性,挥发性、清洁性能都较为明显,是汽油生产过程中最为理想的原料,在实际生产中也主要依靠烷基化技术进行生产设备的基础安装。
二、烷基化工艺(一)CDALKY工艺的应用主要是通过加热碳四混合料分离原材料,再在反应器中与异丁烷进行融合混合,最后在反应器顶端中进行分离反应,进而顺利进入压缩机内部。
硫酸烷基化工艺腐蚀分析及应对措施研究

硫酸烷基化工艺腐蚀分析及应对措施研究硫酸烷基化是一种重要的有机合成反应,广泛应用于化工和医药领域。
然而,使用硫酸进行烷基化反应时,往往存在腐蚀问题,对设备和安全产生一定的影响。
本文结合实际生产中的案例,对硫酸烷基化工艺的腐蚀问题进行分析,并提出相应的应对措施。
一、腐蚀原因分析烷基化反应中出现的腐蚀问题主要来自于以下方面:1.硫酸本身具有强酸性,在高温下对金属设备具有腐蚀作用。
2.烷基化反应的原料、中间体和产物中可能存在对设备具有腐蚀作用的化学物质,如硫醇、烷基溴化物和烷基硫醇等。
3.烷基化反应中产生的副产物如硫酸缩水甘油醚等,可能对设备具有腐蚀作用。
二、应对措施1.选择合适的反应器材料。
选用耐酸、耐腐蚀的材料,如不锈钢、玻璃钢等。
应避免使用烷基化反应前处理中使用不锈钢材料。
2.对设备进行防腐处理。
表面涂覆防酸材料或进行防酸涂层处理可有效避免硫酸对设备的腐蚀作用。
同时,进行定期维修和保养,及时更换老化的设备和耗损严重的构件。
3.采用节流泄压装置。
烷基化反应中,由于反应过程中产生的气体量较大,如采用传统的泄压装置,可能会造成大量的物料和反应废气泄漏,而增加环境污染和安全事故的风险。
采用节流泄压装置,可有效降低废气排放,同时更能保障设备的安全稳定运行。
4.加强储罐管理。
硫酸烷基化反应中,应对储罐进行定期检查,及时处理罐底沉淀和壁面污垢。
针对容积较大的储罐,应实行分段喷淋、定时螺旋搅拌等措施,保持反应物的均匀混合,避免死角和积存的沉淀物。
5.加强现场安全操作。
进行硫酸烷基化反应时,应制定详细的操作规程,定期开展安全培训和演练,建立安全意识。
现场操作人员应佩戴防护设备,避免直接接触反应液体,同时应对设备及时进行维护和检查。
三、结论在硫酸烷基化反应过程中,腐蚀问题是无法避免的,但通过选用适当的材料及技术手段,可以降低腐蚀作用,避免设备出现损坏,并减少环境污染和安全事故的风险。
因此,合理选择设备和储罐材料,采取适当的安全防护措施,加强设备维护管理,能够有效降低硫酸烷基化反应中的腐蚀作用,保障设备安全稳定运行。
烷基化反应报告

烷基化反应报告烷基化反应专题报告班级:学号:姓名:完成日期:烷基化反应专题报告前言随着我国国民经济可持续发展国策的实施,汽车排放尾气对空气的污染问题成为我们关注的焦点,我国石油炼制工业面临的最关键问题就是如何生产符合国家日益严格的环保标准的清洁燃料,以满足国内交通行业和市场的需求。
石油炼制过程中的烷基化反应是指在酸性催化剂的作用下,烷烃分子与烯烃分子的化学加成反应,在反应过程中烷烃分子中活泼氢原子的位置被悉听所取代,由于异构烷烃中叔碳原子上的氢原子比正构烷烃中碳原子上的氢原子活泼的多,因此参加烷基化反应烷烃。
反应生成异辛烷(烷基化汽油)的催化反应过程。
烷基化汽油具有以下特点:该种汽油具有辛烷值高(RON95~98) 、敏感性低(RON 与MON 之差一般≤3) 康保性能好;蒸汽压低、燃烧热值高、不含烯烃芳烃硫含量也低。
燃烧完全而清洁,不污染环境等优点,是航空汽油和车用汽油的理想调和油。
真是由于烷基化的各种优点,使它成为石油加工过程的重要过程之一,越来越受到广泛关注。
烷基化原理及影响因素一、烷基化原理碳四烷基化遵循正碳离子反应机理,其过程主要包含四个步骤:步骤1:叔丁基正碳离子的生成步骤2:叔丁基正碳离子与丁烯加成生成碳八正碳离子叔丁基正碳离子与不同的丁烯异构体进行烷基化反应可以生成不同的碳八正碳离子。
TMP+和DMH+分别是三甲基戊烷和二甲基己烷的正碳离子。
TMP组分是烷基化油中的理想组分,具有较高的辛烷值(RON 100~109),而DMH的辛烷值较低(RON 55~76),DMH组分的大量存在会降低烷基化油的品质。
步骤3:碳八正碳离子的异构生成的碳八正碳离子会通过氢转移或甲基转移而生成更稳定的正碳离子。
步骤4:氢转移形成碳八异构烷烃碳八正碳离子异构体通过快速地与异丁烷进行氢转移反应形成不同的辛烷异构体,同时产生了新的叔丁基正碳离子以维持链式反应的继续。
二、碳四烷基化过程的影响因素影响碳四烷基化过程的主要因素主要有原料性质组成、反应压力、反应温度、反应时间、烷烯比、酸烃比、分散作用等。
- 1、下载文档前请自行甄别文档内容的完整性,平台不提供额外的编辑、内容补充、找答案等附加服务。
- 2、"仅部分预览"的文档,不可在线预览部分如存在完整性等问题,可反馈申请退款(可完整预览的文档不适用该条件!)。
- 3、如文档侵犯您的权益,请联系客服反馈,我们会尽快为您处理(人工客服工作时间:9:00-18:30)。
ST RA T CO 硫酸烷基化工艺技术特点及影响因素分析厉建伦(齐鲁石化公司胜利炼油厂,淄博,255434)摘要 本文着重介绍了胜利炼油厂引进的ST RAT CO 硝酸烷基化装置的工艺技术特点,并分析了影响硫酸烷基化反应的主要因素及控制最佳反应操作条件、降低酸耗、提高产品质量和收率和途径。
收稿日期:1994-10-22;修改稿收到日期:1995-04-18。
1 前 言硫酸烷基化工艺是以石油液化气C 4馏份为原料生产高辛烷值汽油组份的炼油工艺。
我厂原4.5×104t/a 硫酸烷基化装置已投产20多年,工艺落后,设备陈旧,消耗高,产率低,迫切需要技术改造。
为满足汽油改质的需要,我们建设了一套具有世界先进工艺水平的6×104t /a 硫酸烷基化装置。
该装置系美国STRATCO 公司专利技术——流出物致冷工艺。
于1992年11月5日正式投料并转入试生产。
它具有工艺简单、操作方便、产品质量高等明显优点。
2 装置工艺技术特点该工艺与国内现有的硫酸烷基化工艺相比具有以下特点。
2.1 采用了ST RATCO 卧式偏心高效反应器采用ST RA TCO 反应器是这种工艺的主要特点。
该反应器装有一个大功率的搅拌器和内循环夹套,用以完成酸、烃乳化液的混合和循环。
反应器中设有910m 2的冷却管束,通过反应流出物闪蒸取走反应热。
由于反应器内部循环流率很高,有利于热量扩散,从而使各点反应温度保持均匀。
搅拌器较高的能量还使得酸、烃有较大的接触界面,进料中的烯烃能在酸乳化液中迅速分散。
反应器的这些结构特点,有利于提高烷基化油收率和质量。
卧式偏心反应器与高位酸沉降器构成乳化液循环是ST RA TCO 技术的核心部分,与泵抽送的酸循环相比,改善了反应条件。
新鲜酸进入酸循环管随循环酸与混有致冷剂的烯烃进料,各自在叶轮入口处进入反应器,经入口喷嘴立即被旋转着的叶轮吸入而使酸烃呈乳化状态,并快速离开叶轮。
此时,反应原料与催化剂(H 2SO 4)受喷嘴和叶轮的强烈切割和激烈搅拌,在反应器入口即被充分混合,加速了烷基化反应,生成烷基化油。
反应产物(含iC 04)经上升管进入酸沉降器进行酸烃分离,这样经反应器和沉降器之间的上升管和下降管,乳化液同时在这二者之间循环。
进入沉降器的乳化液分离出反应产物烃相,在酸相没有完全沉降之前通过下降管被叶轮的搅拌作用所吸引,迅速返回到反应器。
调节下降管上的酸循环阀门可以有效地改变酸循环速率,控制其在沉降器内的停留时间,抑制因酸相沉积而发生的副反应。
以一定速度转动着的叶轮还促进了液体的高速流动,强化了管束的传热效果,反应—沉降系统中的酸循环借助上升管和下降管中物流的比重差自然循环。
烷基化反应过程由反应物自烃相向酸相的传质所控制。
在硫酸法烷基化过程中,由于硫酸催化剂的高粘度、高密度、高表面张力和异丁烷在硫酸中的低溶解性,突出了该工艺过程的化学反应与分子扩散的矛盾,微观混合状态直接影响着反应产物的选择性和收率,因此对酸烃混合的要求非常严格。
在反应过程中,不互溶的酸烃(反应物)应充分混合,以稀释烯烃防止局部浓度过高,并尽量扩大异丁烷与酸相的接触面,抑制烷基化副反应的产生。
反应完毕后,酸烃(反应产物)沉降物应快速分离,以保持酸烃两相中异丁烷浓度,卧式偏心反应器的结构的循环系统,使酸烃两相混合分布均匀,并且混合比例可调,较好地满足了硫酸烷基化反应对酸烃两相接触的技术要求。
在卧式偏心反应器中,酸烃两相间保持着反复地剧烈接触,形成一个较大的相接触面,增加了异丁烷向酸催化剂的传质区域,使酸相内反应消耗了的异丁烷能得到及时补充。
酸烃混合均匀以及在沉降器中酸烃两相的快速分离,抑制了副反应的发生。
反应放出的热量被反应器内的管束及时取走,这样可控制一个较低的反应温度,且分布均匀。
所有这些条件,保障了产品烷基化油的质量,并实现高收率和低能耗。
2.2 采用反应流出物致冷工艺反应流出物致冷是STRATCO工艺的另一特点。
反应流出物中液相异丁烷的一部分(包括丙烷和正丁烷)在反应器冷却管束中降压闪蒸,吸收烷基化反应热量,以达到控制反应温度的目的。
反应流出物在闪蒸罐中气液分离后,气相进入致冷压缩机,经压缩机压缩、冷凝后再循环回反应器。
致冷剂进入反应器使反应器内异丁烷的量增加了约一倍,提高了反应器内循环异丁烷与烯烃的分子比。
流出物致冷工艺使反应器内保持最高的异丁烷浓度,在搅拌器的搅拌作用下,提高了管束的传热效果,使整个反应器内温度保持均匀,有利于烷基化主反应的进行。
2.3 反应流出物采用浓硫酸洗及碱水洗正常生产中,反应部分来的反应流出物夹带少量酸及烯烃与硫酸反应生成的硫酸酯。
这些酯类如不加以脱除,将在下游的脱异丁烷塔分解放出SO2(在高温条件下),遇到水分,则会严重腐蚀设备,并导致脱异丁烷塔的重沸器结垢。
STRATCO工艺对反应流出物采用浓酸洗及碱水洗的精制流程,同时在这些设备中设置了静电沉降器。
这种精制流程同我厂前套烷基化装置的碱洗、水洗工艺相比,能更有效地脱除引起下游系统腐蚀和结垢的硫酸酯。
反应流出物首先与新酸混合进入酸洗静电沉降器。
硫酸酯属于极性分子,硫酸属于极性溶剂。
极性分子溶于极性溶剂中,吸收了反应产物中绝大部分硫酸酯的浓硫酸从沉降器底部连续排出进入反应器。
硫酸酯是反应的中间产物,进入反应器后又继续参与烷基化反应,提高了烷基化油收率。
经酸洗沉降后的反应流出物携带极微量的硫酸酯和硫酸进入碱洗电沉降器。
电沉降器的作用在于使极微小的极性颗粒凝聚沉降。
经酸洗、碱水洗的反应流出物较好地脱除了硫酸酯,避免了对下游设备的腐蚀。
2.4 分馏系统采用单塔产品分馏由于采用了先进的反应器且连续排出90%浓度的废酸,使产品质量得到了控制,反应过程中不生成重质油,故可使产品在一个塔中完成轻组分(异丁烷)和重组分(烷基化油)的分离。
实际生产中,只要反应条件控制适当,烷基化油的干点基本上在190~200℃。
3 反应影响因素分析3.1 反应温度烷基化反应的基本反应式为:C4H10+C4H8H2SO4C8H18+Q该反应是放热反应。
降低温度,有利于烷基化油的生成。
但如温度低于4℃时,硫酸的粘度会随之增加,不利于烯烃分子向酸相的扩散与酸烃乳化液的生成,烯烃之间迭合的副反应也会随之增加,影响烷基化油的收率和质量,而且还会增加搅拌机的动力消耗。
如果反应温度过高,虽然有助于均匀酸烃乳化液的生成,但也加剧了副反应。
当反应温度上升到15~20℃时,烯烃聚合成胶状物,导致酸耗急剧增加,烷基化油质量和收率下降。
因此,理想的反应温度应控制在4~10℃。
3.2 异丁烷浓度异丁烷浓度一般以反应器进料中异丁烷与烯烃比率和反应流出物中异丁烷含量来表示。
提高异丁烷浓度能减少副反应和降低酸耗,提高产品的辛烷值和产率。
根据以上烷基化反应式,其化学平衡常数为:K=〔C8H18〕〔C4H10〕〔C4H8〕当温度、压力一定时,K为恒值。
在烷基化反应过程中,反应温度、压力保持恒定,烯烃进料也稳定。
按化学平衡移动的原理,增大异丁烷浓度,化学平衡向右移动,有利于烷基化主反应的进行。
因此,只有保持较高的异丁烷浓度,才有利于烷基化油的生成。
生产中以保持较高的异丁烷浓度来扩大异丁烷与酸相的接触面,使烯烃分子充分均匀扩散到异丁烷分子中。
如果异丁烷不足,烯烃分散不均匀,在硫酸的催化作用下,烯烃之间发生聚合反应生成二聚体。
二聚体继续与烯烃聚合生成三聚体等多聚物,形成大分子的烷烃,降低了产品的质量和收率;而且由于烯烃不能在酸和异丁烷形成的相中均匀分散,硫酸与烯烃加成生成酸性的硫酸氢乙酯和中性的硫酸二乙酯,增加了硫酸的消耗。
因此,在硫酸烷基化反应中,较高的异丁烷浓度不仅有利于烯烃进入酸相参加反应,还抑制了副反应。
图1为反应流出物中异丁烷浓度与烷基化油辛烷值关系图。
它表明烷基化油辛烷值随反应流出物中异丁烷浓度的增加而递增。
流出物中异丁烷浓度的提高,可通过调节循环异丁烷量和纯度来实现。
但异丁烷浓度过高,会增大动力消耗。
实际生产中,反应进料中异丁烷与烯烃比率为8~10∶1,反应流出物中异丁烷在烃相中的体积含量为62%~70%,此时反应效果最佳,又不致增加动力消耗。
图1 异丁烷浓度与辛烷值关系图系统中正丁烷的累积,对异丁烷纯度影响很大,从而影响烷基化油的质量和收率。
正丁烷在烷基化反应中不参与化学反应,它是异丁烷的稀释剂,降低了异丁烷纯度。
正丁烷随循环异丁烷进入反应器,和异丁烷一起共图2 正丁烷浓度与干点关系同与硫酸和烯烃接触,减少了烯烃同硫酸和异丁烷相接触的机会,使一些烯烃进行迭合反应,而不与异丁烷反应,降低了烷基化油的质量和收率。
由于正丁烷的存在降低了反应流出物中异丁烷含量。
图2为反应流出物中正丁烷含量对烷基化油干点影响的关系图。
为降低流出物中正丁烷含量,必须从分馏塔的正丁烷侧线抽出除去不参与化学反应的正丁烷,才能实现生产条件的优化。
3.3 酸浓度与酸烃比硫酸浓度的高低,对烷基化油质量和收率有直接影响。
酸浓度为95%~96%时最为适宜,在此浓度下,硫酸的催化作用最佳,最有利于烷基化主反应的进行,烷基化油的质量和收率都较高;低浓度酸将促进副反应,增加酸耗并降低烷基化油辛烷值。
因为较低的硫酸浓度会使硫酸的催化作用变差,使部分烯烃和硫酸作用生成硫酸酯。
硫酸酯溶于硫酸中,又降低了硫酸浓度,导致了酸耗急剧增加,并且降低了烷基化油产率;另一方面,较低的硫酸浓度,使烯烃聚合的副反应加剧,增加了产品中的重质组分,降低了烷基化油辛烷值。
当酸浓度由94%降到89%时,烷基化油的马达法辛烷值可降低1.8个单位,烷基化油的干点可由189℃上升到204℃。
当硫酸浓度低于88%时,硫酸迅速被稀释,此时无论向系统内补加多少新酸,酸浓度都会无可逆转地变稀。
为保证烷基化油质量,又不致使酸耗太高,我们控制反应酸浓度90%左右。
酸烃比是烷基化反应中的一个重要参数,它直接影响着烷基化反应效果的好坏。
酸烃比为酸循环量与烃的总进料比值,它表示烷基化过程中酸与烃的分散状态。
若酸烃体积比>1,则反应器内酸为连续相,烃为分散相,烃分散到硫酸中,形成酸包油状态;若酸烃比<1,则反应器内烃为连续相,酸为分散相,形成油包酸,此时反应效果变差,使反应器中烯烃占优势,缺乏足够的异丁烷,从而促进烯烃聚合。
理论上酸过量有利于提高产品质量,但生产中由于反应温度较低,酸粘度较大,过量酸需消耗大量能量,因此生产上一般控制酸烃比为1.1∶1左右。
4 结束语综上所述,该工艺由于采用了先进的反应器并进行了取热方式、酸循环等方面的改进,改善了反应操作条件,抑制了烷基化副反应的发生,提高了烷基化油质量和收率,其产品质量、收率、酸耗等各项指标均优于传统的硫酸烷基化工艺;所以,ST RATCO硫酸烷基化流出物致冷工艺比较先进,操作平稳,反应系统操作方便,分馏系统操作弹性大,大大提高了生产中的自动化程度,降低了职工劳动强度;而且由于流出物精制过程和原料脱水工艺的改进,降低了酸耗,提高了产品收率。