15CrMoR制压力容器技术条件
70BJ 010-2011 铬钼钢复合钢板制压力容器制造及验收工程技术条件

公司标准70BJ010-2011代替:70BJ010-2005铬钼钢复合钢板制压力容器制造及验收工程技术条件第 1 页共 18 页朱玫张国信李法海陈崇刚2011-04-15 2011-04-20 编制校审标准化审核审定发布日期实施日期目 次1 范围 (1)2 规范性引用文件 (1)3 总则 (2)4 材料 (2)5 制造 (8)6 无损检测 (12)7 焊后热处理及水压试验 (13)8 涂敷和包装运输 (14)1 范围本标准规定了最高操作温度不大于440℃且壳体基层板厚不大于100mm,基层材料为15CrMoR(H)、14Cr1MoR(H)及与此相当的铬钼钢,复层为S11306、S11348、S30403、S30408、S32168、S31603、S31608及与此相当的不锈钢的铬钼钢复合钢板制压力容器在材料、制造、检验以及包装运输等方面的要求。
本标准适用于按GB 150设计的铬钼钢复合钢板制压力容器的制造及验收,不适用于按分析设计标准设计的铬钼钢复合钢板制压力容器的制造和验收。
2 规范性引用文件TSG R0004-2009 固定式压力容器安全技术监察规程GB150 钢制压力容器GB/T223 钢铁及合金化学分析方法GB/T228 金属拉伸试验方法GB/T229 金属夏比缺口冲击试验方法GB/T232 金属材料弯曲试验方法GB713 锅炉和压力容器用钢板GB985.1 气焊、焊条电弧焊、气体保护焊和高能束焊的推荐坡口GB985.2 埋弧焊的推荐坡口GB/T1184-1996 形状和位置公差未注公差值GB/T1804-2000 一般公差未注公差的线性和角度尺寸的公差GB3077 合金结构钢GB/T 4334 金属和合金的腐蚀不锈钢晶间腐蚀试验方法GB/T4338 金属材料高温拉伸试验GB/T5118 低合金钢焊条GB/T6394 金属平均晶粒度测定法GB6479 高压化肥设备用无缝钢管GB8923 涂装前钢板表面锈蚀等级和除锈等级GB9948 石油裂化用无缝钢管GB/T10561 钢中非金属夹杂物含量的测定标准评级图显微检验法GB24511 承压设备用不锈钢钢板及钢带HG/T20592 钢制管法兰(PN系列)HG/T20615 钢制管法兰(Class系列)JB/T4700 压力容器法兰分类与技术条件JB/T4707 等长双头螺柱JB4708 钢制压力容器焊接工艺评定JB/T4709-2000 钢制压力容器焊接规程JB/T4710 钢制塔式容器JB/T4711 压力容器涂敷与运输包装JB/T4730 承压设备无损检测JB/T4731 钢制卧式容器JB4744 钢制压力容器产品焊接试板的力学性能检验JB/T4747 压力容器用钢焊条订货技术条件NB/T47002.1-2009 压力容器用爆炸焊接复合板第一部分不锈钢-钢复合钢板NB/T47008 承压设备用碳素钢和低合金钢锻件NB/T 47010 承压设备用不锈钢和耐热钢锻件NB/T47013.10 承压设备无损检测第10部分:衍射时差法超声检测SH3022 石油化工设备和管道涂料防腐蚀技术规范SH3043 石油化工设备管道钢结构表面色和标志规定SH/T3074 石油化工钢制压力容器SH/T3524 石油化工静设备现场组焊技术规程SH/T3526 石油化工异种钢焊接规程SH/T3527-1999 石油化工不锈钢复合钢焊接规程ASME SA-335 Standard Specification For Seamless Ferritic Alloy-Steel Pipe For High-Temperature Service3 总则3.1 铬钼钢复合钢板制压力容器按TSG R0004-2009、GB150、JB/T4710(对塔式容器)或JB/T4731(对卧式容器)、设计文件以及本标准的规定进行制造和验收。
15CrMoR产品性能

是压力容器用钢。
属于一种中温抗氢钢,产地:舞钢、首钢、武钢、南钢、15CrMoR新钢、湘钢、济钢。
15CrMoR牌号简介“15”是碳含量成分0.15%“Cr”是成分含有一定化学元素-铬“Mo”是成分含有一定化学元素-钼“R”是容器板容的第一个字母15CrMoR,热处理常采用:正火+回火在550℃以下时,具有较高的持久强度。
执行标准:GB713—2014舞钢临氢15CrMoR(H)执行标准WYJ410-200815CrMoR化学成分C Si Mn P S Cr Mo0.12~0.18 0.15~0.400.40~0.70≤0.025≤0.0100.80~1.200.3~0.60舞钢15CrMoR(H)化学成分成分分析方法C Si Mn P S Cr Mo熔炼分析0.12~0.180.15~0.40 0.40~0.70 ≤0.010≤0.010 0.80~1.20 0.3~0.60产品分析0.10~0.20 0.13~0.43 0.37~0.73 ≤0.012≤0.010 0.75~1.25 0.3~0.62成分分析方法Ni Cu Sb Sn As 【H】熔炼分析≤0.20≤0.20≤0.003≤0.015≤0.016≤2ppm产品分析≤0.20≤0.20≤0.003≤0.015≤0.016≤2ppm 注:回火脆化敏感性系数满足以下要求:X= (10P+5Sb+4Sn+As)×10≤15,式中元素以ppm含量代入,如0.01%以100ppm 代入。
J=(Si+Mn)×(P+Sn)×10≤180,式中元素以重量百分含量代入,如0.01%以0.01代入。
15CrMoR机械性能15CrMoR的力学性能钢板状态力学性能和冷弯性能板厚(mm) 抗拉强度屈服强度伸长率温度冲击功冷弯试验180°b=2a正火加回火6~60450-590≥295≥1920 ≥31d=3a >60~100 ≥275>100-150 440-580 ≥255舞钢15CrMoR(H)的力学性能项目数值单位室温拉伸Rm 厚度≤100mm450~590 MPa>100~150mm 440~580室温拉伸Rp0.2 厚度≤100mm≥295MPa>100~150mm ≥255室温拉伸≥19% 室温拉伸断面收缩率Z ≥45(适用于园拉伸试验)≥40(适用于板拉伸试验)%0°C夏比冲击功(V)型缺口平均值≥55J 高温拉伸屈服强度Rp0.2 详见技术条件MPa 室温弯曲试验d=2a最大模拟焊后热处理和最小模拟焊后热处理执行以下工艺:Max .PWHT::690±10°C×18(0)hMin.PWHT::690±10°C×6h(0)钢板的板标:执行GB713-2008的规定。
15CrMoR (H)中的H代表什么意思

F1根据供需双方协商,室温拉伸、高温拉伸和夏比(V形缺口)冲击试验可以按表3要求在TXT/2板厚取样,性能指标符合表2的要求,原表3要求的取样位置不再执行。
F2根据供需双方协商,厚度≤60mm的钢板可按表4要求进行低温冲击检验,代替0℃冲击功检验,取样及检验方法执行第8条有关0℃冲击功检验规定,试样位置执行表3的规定(在有F1要求时试样位置为TXT/2,不再执行TXT/4).
3.2厚度偏差按GB/T709的B类或C类执行,在合同中注明。
3.3钢板理论重量交货,理论计重采用的厚度为钢板允许的最大厚度和最小厚度的算术平均值。钢的密度为7.85g/㎝3
4.临氢15CrMoR和15CrMoR(H)钢板技术要求
4.1临氢15CrMoR和15CrMoR(H)钢板化学成分要求,应符合表1的规定。
表1化学成分Wt%
成分
分析
C
Si
Mn
P
S
max
Cr
Mo
熔炼分析
0.12
~~
0.18
0.15
~~
0.40
0.40
~~
0.70
≤
0.010
≤
0.010
0.8
~~
1.2
0.45
~~
0.60
成品分析
0.10
~~
0.20
0.13
~~
0.43
0.37
~~
0.73
≤
0.012
≤
0.010
0.75
~~
1.25
0.43
J=(Si+Mn)X(P+Sn)X≤180,式中元素以重量百分含量代入,如0.01%以0.01代入。
15CrMoR材料制作过程的注意要点

15CrMoR材料制作过程的注意要点作者:李晓犇秦丽芳赵旭来源:《中国化工贸易·上旬刊》2016年第09期摘要:本单位从某化工公司承接一气化炉制造任务。
因设计温度较高,故选用高温强度和抗氢性能较好的15CrMoR材料,从焊接方法,焊接材料、焊前预热、焊接工艺参数、焊后热处理等方面进行了焊接工艺分析及施工要求,最终使焊接接头性能达到了设计要求,取得了很好的效果。
关键词:15CrMoR;焊接材料;焊接性能分析;焊后热处理;手工焊1 概况2015年,本单位从某化工公司承接一气化炉制造任务。
因设计温度较高故选用高温强度和抗氢性能较好的15CrMoR材料,确定了焊接工艺及施工要求,最终使焊接接头性能达到了设计要求,取得了很好的效果。
2 15CrMoR钢的焊接性分析15CrMoR属低合金高强度中温抗氢耐热钢,供货状态为正火+回火,组织为珠光体+铁素体,亦称珠光体耐热钢,它不仅具有很好的抗氧化性和热强度,还具有比较好的抗氢腐蚀和抗硫腐蚀性能能力,它主要用于设计温度在350℃~500℃的中温压力容器,它的化学成份和机械性能详见GB713-2014,可以通过化学成分确定的碳当量间接评判15CrMoR钢的焊接性。
根据日本JIS和WES 推荐的碳当量公式,计算15CrMoR的碳当量为0.58%。
当Ceq=0.46%时,钢材的淬硬倾向不明显,其焊接性优良;当Ceq=0.46%~0.52%时,钢材的淬硬倾向逐渐明显,其焊接时需适当采取相应的措施。
当Ceq>0.52%时,钢材的淬硬倾向强,属于较难焊接的材料。
可见,15CrMoR钢有很大的淬硬性,如果没有特殊的控制措施,很难避免焊接裂纹的出现,同时返修焊接时拘束度大,易出现较大的拘束应力。
3 焊前准备及焊材、工艺参数的确定3.1 焊接材料及参数根据NB/T47015-2011《压力容器焊接规程》的要求,焊接工艺参数见表一,为了保证焊缝质量,需将R307焊条(Φ3.2,Φ4.0)烘干温度305~400℃,保温1~2h,以保证焊缝金属中扩散氢的含量为最低。
15crmor(h)执行标准

15crmor(h)执行标准15CrMoR(H)是一种常用的高温高压容器用钢,其执行标准是国家标准GB 713-2014《钢板和钢带用压力容器钢》。
本文将对15CrMoR(H)执行标准进行深入研究,探讨其在高温高压容器中的应用以及相关性能要求。
一、15CrMoR(H)的应用背景及特点1. 15CrMoR(H)的应用背景随着工业技术的快速发展和对能源、石油化工等行业需求的增长,高温高压容器在工业生产中扮演着重要角色。
15CrMoR(H)作为一种常见的容器用钢,具有良好的耐热性和耐压性能,在石油化工、电力、核电等领域得到广泛应用。
2. 15CrMoR(H)的特点15CrMoR(H)是一种具有较好耐热性能和抗氧化性能的铁素体钢。
其主要特点如下:(1) 高强度:15CrMoR(H)具有较高强度,可以满足在高温下承受较大内外压力和荷载要求。
(2) 良好的耐热性:15CrMoR(H)的耐热性能较好,可以在高温环境下长时间稳定运行,不易变形和破裂。
(3) 优异的抗氧化性:15CrMoR(H)具有较好的抗氧化性能,可以在高温下长期使用而不易氧化和腐蚀。
(4) 优秀的可焊性:15CrMoR(H)具有良好的可焊性,可以通过焊接工艺与其他材料进行连接,提高整体结构的稳定性。
二、15CrMoR(H)执行标准解读1. 标准编号15CrMoR(H)执行标准为GB 713-2014《钢板和钢带用压力容器钢》。
2. 标准内容GB 713-2014标准详细规定了15CrMoR(H)钢板和钢带用于压力容器的技术要求、试验方法、检验规则以及标志、包装、运输等内容。
其中包括以下方面:(1) 化学成分要求:规定了15CrMoR(H)钢板和钢带中各元素的含量范围及其影响因素。
(2) 机械性能要求:包括抗拉强度、屈服强度、延伸率、冲击韧性等指标的要求。
(3) 金相组织要求:规定了15CrMoR(H)钢板和钢带的金相组织应符合的标准。
(4) 热处理要求:包括15CrMoR(H)钢板和钢带的热处理工艺、温度控制等方面的要求。
15crmor执行标准 -回复

15crmor执行标准-回复基于中国国家标准GB/T 3077-2015,《合金结构钢技术条件》,本文章将一步一步回答关于15CrMoR执行标准的问题。
15CrMoR是一种合金结构钢的牌号,该钢材广泛应用于制造压力容器,如石油、化工、电力等行业。
下面将逐步回答一些与15CrMoR执行标准相关的问题。
1. 15CrMoR执行标准是什么?根据国家标准GB/T 3077-2015,《合金结构钢技术条件》规定,15CrMoR的执行标准是GB 713-2008《压力容器用钢板》。
2. 15CrMoR钢板的化学成分有哪些要求?根据GB 713-2008标准的要求,15CrMoR钢板的化学成分应满足以下要求:- 碳(C)含量为0.12-0.18;- 硅(Si)含量为0.15-0.40;- 锰(Mn)含量为0.40-0.70;- 磷(P)含量≤0.025;- 硫(S)含量≤0.010;- 铬(Cr)含量为0.80-1.10;- 镍(Ni)含量为0.30-0.60;- 钼(Mo)含量为0.15-0.25。
3. 15CrMoR钢板的机械性能要求是什么?根据GB 713-2008标准的要求,15CrMoR钢板的机械性能要求如下:- 屈服强度(σs)不小于295MPa;- 抗拉强度(σb)为450-590MPa;- 延伸率(δ5)不小于22;- 缩颈率(ψ)不小于50。
4. 15CrMoR钢板的热处理要求是什么?根据GB 713-2008标准的要求,15CrMoR钢板的热处理应进行正火和回火。
正火温度为910 - 940,回火温度为680 - 720。
热处理后,需要进行冷却。
5. 15CrMoR钢板的检验要求是什么?根据GB 713-2008标准的要求,15CrMoR钢板应进行化学成分分析、机械性能测试、热处理试验等检验。
对于厚度大于20mm的钢板,还需要进行冲击试验。
总之,15CrMoR执行标准是GB 713-2008,《压力容器用钢板》,根据该标准的要求,15CrMoR钢板的化学成分、机械性能、热处理、检验等方面都有详细的规定。
15crmor标准

15crmor标准
15CrMoR是一种高温压力容器用钢,其标准是WYJ410-2008。
该标准规定了15CrMoR的化学成分、物理性能、力学性能、超声波探伤、表面质量等方面的要求。
15CrMoR的化学成分主要包括碳(C)、硅(Si)、锰(Mn)、硫(S)和磷(P)。
其中,碳和锰是硬度的关键元素,硅则有助于提高加工性能。
对于15CrMoR这种高温压力容器钢,硫和磷要求极低,以确保钢材的抗裂性和韧性。
15CrMoR的物理性能和力学性能也是非常重要的。
它需要具有良好的塑性和韧性,以承受高温和高压的工作环境。
同时,它还需要具有足够的强度和硬度,以承受工作过程中的载荷和应力。
此外,15CrMoR还需要满足超声波探伤的要求。
超声波探伤是一种无损检测方法,可以检测出钢材内部的缺陷和裂纹。
对于15CrMoR这种高温压力容器钢,超声波探伤的要求非常严格,需要满足JB/T4730.3中的Ⅰ级要求。
最后,15CrMoR的表面质量也是非常重要的。
它需要满足GB713的规定,以保证钢材的耐腐蚀性和耐磨损性。
总之,15CrMoR是一种重要的高温压力容器用钢,其标准是WYJ410-2008。
该标准规定了15CrMoR的化学成分、物理性能、力学性能、超声波探伤、表面质量等方面的要求,以确保其安全性和可靠性。
70BJ 010-2011 铬钼钢复合钢板制压力容器制造及验收工程技术条件

成型和热处理的加热过程以及最大或最小模拟焊后热处理;
2)锻件的试样应按 BN/T47008 和表 5 的规定制取。当采用热缓冲环或环段时,应按
NB/T47008 规定制取;
3)钢板的试样应按表 6 规定制取。
表5
锻件取样部位和数量
试验项目
执行标准
数量
热处理条件
常温拉伸试验
GB228
按照 JB4726-94
朱玫 编制
张国信 校审
李法海 标准化审核
陈崇刚 审定
2011-04-15
2011-04-20
发布日期 实施日期
70BJ010-2011
第 2 页 共 18 页
GB/T6394 金属平均晶粒度测定法 GB6479 高压化肥设备用无缝钢管 GB8923 涂装前钢板表面锈蚀等级和除锈等级 GB9948 石油裂化用无缝钢管 GB/T10561 钢中非金属夹杂物含量的测定标准评级图显微检验法 GB24511 承压设备用不锈钢钢板及钢带 HG/T20592 钢制管法兰(PN 系列) HG/T20615 钢制管法兰(Class 系列) JB/T4700 压力容器法兰分类与技术条件 JB/T4707 等长双头螺柱 JB4708 钢制压力容器焊接工艺评定 JB/T4709-2000 钢制压力容器焊接规程 JB/T4710 钢制塔式容器 JB/T4711 压力容器涂敷与运输包装 JB/T4730 承压设备无损检测 JB/T4731 钢制卧式容器 JB4744 钢制压力容器产品焊接试板的力学性能检验 JB/T4747 压力容器用钢焊条订货技术条件 NB/T47002.1-2009 压力容器用爆炸焊接复合板 第一部分 不锈钢-钢复合钢板 NB/T47008 承压设备用碳素钢和低合金钢锻件 NB/T 47010 承压设备用不锈钢和耐热钢锻件 NB/T47013.10 承压设备无损检测 第 10 部分:衍射时差法超声检测 SH3022 石油化工设备和管道涂料防腐蚀技术规范 SH3043 石油化工设备管道钢结构表面色和标志规定 SH/T3074 石油化工钢制压力容器 SH/T3524 石油化工静设备现场组焊技术规程 SH/T3526 石油化工异种钢焊接规程 SH/T3527-1999 石油化工不锈钢复合钢焊接规程 ASME SA-335 Standard Specification For Seamless Ferritic Alloy-Steel Pipe For
15CrMoR技术要求

199
185
175
165
156
150
15CrMoR钢板特点
钢质纯净:P0.010%、S0.005%、[N]70ppm、[O]15ppm、[H]2ppm、钢中夹杂物总量20ppm的高纯净度钢水。
良好的韧性和焊接性。
领先的热处理技术:正火、淬火、回火、调质等热处理加工。
显著提高钢的塑性和冲击韧性,改善钢材的各向异性。
15CrMoR技术要求
15CrMoR钢板是压力容器用钢。属于一种中温抗氢钢
“15”是碳含量成分0.15%
“Cr”是成分含有一定化学元素-铬
“Mo”是成分含有一定化学元素-钼
“R”是容器板容的第一个字母
15CrMoR,热处理常采用:正火加回火
在550℃以下时,具有较高的持久强度。
15CrMoR化学成分
≥295
≥19
20
≥31
d=3a
>60~100
≥275
>100-150
440-580
≥255
15CrMoR高温力学性能
钢板状态
板厚
在下列温度(℃)下的屈服强度(Mpa)不小于
正火加回火
20~60
240
225
210
200
189
179
174
>60~100
220
210
196
186
176
167
162
>60~150
15CrMoR化学成分%
C
Si
Mn
P
S
Cr
Mo
0.12~0.18
0.15~0.40
0.40~0.70
≤0.030
15J025.EQ.21-01 09MnNiDR 制压力容器制造技术条件
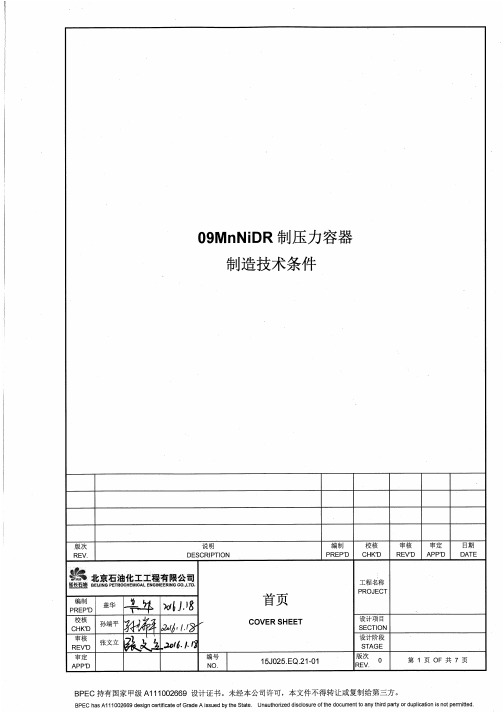
下列文件中的条款通过本规定的引用而成为本规定的条款。凡是注日期的引用文件,其随
器产品焊接接头的低温冲击性能(详见本文件 3.3-6)条),容器制造厂商在材料订货技术要求 中应对其低温冲击功指标留有足够的裕量。
3. 制造和检验
3.1. 一般要求
3.1.1 容器应按 GB 150.1~150.4、《固定式压力容器安全技术监察规程》以及本标准和图样的 规定进行制造、检验与验收。 3.1.2 容器制造厂对 3.1.1 中所指定的技术文件的任何修改(包括材料代用),均必须事先得到 本公司的书面同意。 3.2. 焊工和无损检测人员资格
BPEC 持有国家甲级 A111002669 设计证书。未经本公司许可,本文件不得转让或复制给第三方。
BPEC has A111002669 design certificate of Grade A issued by the State. Unauthorized disclosure of the document to any third party or duplication is not permitted.
的补强锻件应不低于II 级标准,其余锻件应不低于III 级标准,且不低于图纸中的级 别; 3) 钢管——09MnD和09MnNiD,应符合GB 150.2标准附录A; 4) 钢棒——35CrMoA(调质),应符合GB/T 3077标准,且化学成分(熔炼分析)中 硫磷含量应料——焊材的选择应与设备的主体材质相匹配,同时应符合NB/T47018的要 求,并经过焊接工艺评定合格。 2.2. 材料质量证明书
15CrMoR压力容器的焊接工艺的设计说明

1 绪论1.1 焊接技术概述焊接是一种将材料永久性的连接,并成为具有给定功能结构的制造技术。
几乎所有的产品,从几十万吨巨轮到不足1克的微电子元件,在生产制造中都不同程度地应用到焊接技术。
焊接已经渗透到制造业的各个领域,直接影响到产品的质量、可靠性和寿命以及生产的成本、效率和市场反应速度。
近年来,焊接已由一个单一的加工工艺发展成为有科学基础有广泛应用围和前景的焊接工程和焊接产业,在这些产业中,焊接在其中占有重要地位,是决定其产品使用安全的关键。
有些直接出焊接产品或在现场装焊接后投入使用,有些是作成主体结构然后在其上安装动力和机电设备后应用,有焊接结构的质量和安全保证在整体结构设计合理的情况下,主要决定与焊接联结部位的结构、材料匹配、工艺设计、先进的焊接制造工艺及设备和准确的无损检测技术,这些都决定了焊接联结部位的的在和外观质量,形成了分布在各工业和基础设施建设部门各具特色的焊接结构行业,同时也形成了结构焊接需要的焊接设备行业和焊接材料行业。
这些行业是互相关联促进的行业。
焊接结构已有日新月异的发展:在装备制造业结构中用焊接结构局部或全部代替铸件或锻件结构和由局部铸件或锻件焊接成组合结构是大重型结构发展的方向,可大大节约大型铸锻车间及其设备的基本建设投资和生产过程的能源消费,同时还可缩短生产周期;在各种建筑行业广泛采用钢质焊接结构代替钢筋混凝土结构,可达到大跨度、轻自重、工厂造、设计优、工程在建周期短、环境污染少,基础费用省,折除后材料可循环使用,因而符合目前绿色制造和资源循环利用建设节约型社会的大潮流。
目前我国微电子及IT行业中的发展,高强有色金属、光钎、超导和复合材料及高分子材料的应用,都对焊接工艺、设备和材料提出了很多新的要求,因而得到了相应发展。
1.2 压力容器的分类压力容器按其承受压力的高低分为常压容器和压力容器。
压力容器的分类方法很多,主要的分类方法有以下几种:(1)按设计压力划分,可分为低压容器、中压容器、高压容器、超高压容器。
15CrMoR(H)钢板订货技术要求
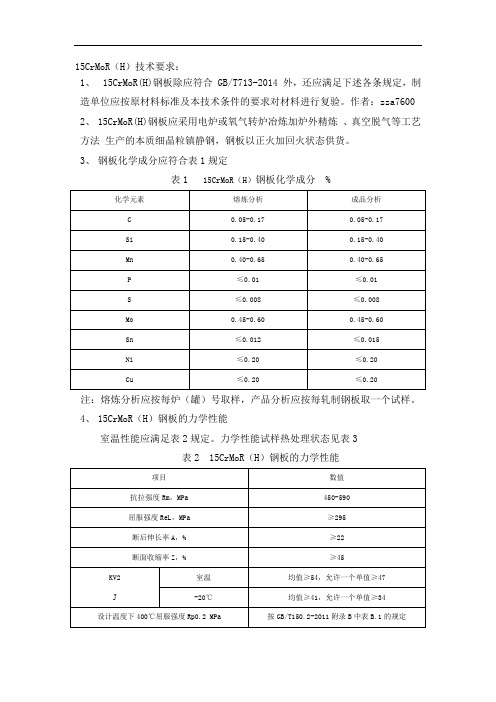
15CrMoR(H)技术要求:1、 15CrMoR(H)钢板除应符合 GB/T713-2014 外,还应满足下述各条规定,制造单位应按原材料标准及本技术条件的要求对材料进行复验。
作者:zza76002、15CrMoR(H)钢板应采用电炉或氧气转炉冶炼加炉外精炼、真空脱气等工艺方法生产的本质细晶粒镇静钢,钢板以正火加回火状态供货。
3、钢板化学成分应符合表1规定表1 15CrMoR(H)钢板化学成分 %注:熔炼分析应按每炉(罐)号取样,产品分析应按每轧制钢板取一个试样。
4、15CrMoR(H)钢板的力学性能室温性能应满足表2规定。
力学性能试样热处理状态见表3表2 15CrMoR(H)钢板的力学性能冷弯试验弯曲180°无裂纹(d=3.0a)硬度(HB)≤2205、钢板力学性能试样的位置、方向、数量及热处理状态应符合表3规定。
表3钢板力学性能试样要求试验项目执行标准试样数量试样位置热处理条件③拉伸试验室温GB/T6396GB/T228每个样坯取1件T*(T/2)横向②NT+Max.PWHT 400℃GB/T228.2每个样坯取1件T*(T/2)横向②NT+Max.PWHT化学分析GB/T223每个样坯取1件T*(T/2)横向②NT室温夏比冲击GB/T229每个样坯取3件T*(T/2)横向②④NT+Min.PWHT-30℃夏比冲击GB/T229每个样坯取3件T*(T/2)横向②④NT+Min.PWHT冷弯试验GB/T6396每个样坯取内、外弯各一件横向NT剪切试验GB/T6396 每个样坯取2件纵向NT注:①每张轧制钢板取一块样坯。
对于横轧钢板应取在边角处,对于纵轧钢板应取在1/4 宽度处。
当钢板长度大于 7 米时,应从钢板两端各取一块样坯。
②T---厚度③NT-正火+回火Max.PWHT—(最大程度的焊后热处理)温度为(675±14)℃×12hMin.PWHT—(最小程度的焊后热处理)温度为(675±14)℃×(2ˆ4)hPWHT 焊后热处理,一般推荐热处理温度为 675±14℃,但需经制造厂通过焊接工艺评定最终确定,持续时间由制造厂提供。
15CrMoR(H)钢板技术条件(1)
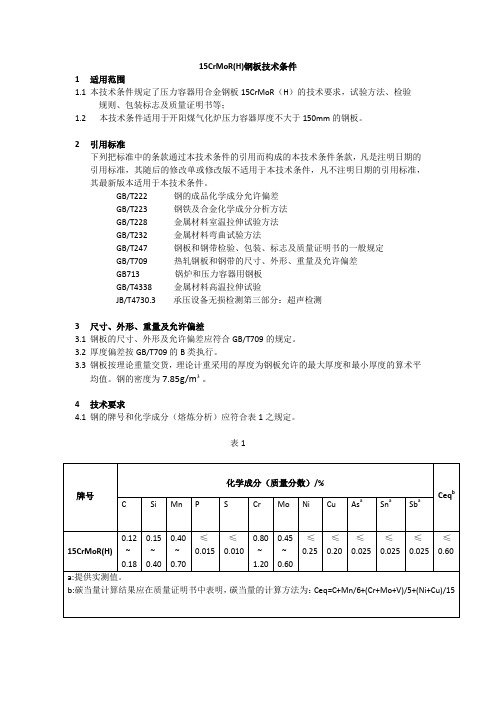
15CrMoR(H)钢板技术条件1适用范围1.1本技术条件规定了压力容器用合金钢板15CrMoR(H)的技术要求,试验方法、检验规则、包装标志及质量证明书等;1.2 本技术条件适用于开阳煤气化炉压力容器厚度不大于150mm的钢板。
2引用标准下列把标准中的条款通过本技术条件的引用而构成的本技术条件条款,凡是注明日期的引用标准,其随后的修改单或修改版不适用于本技术条件,凡不注明日期的引用标准,其最新版本适用于本技术条件。
GB/T222 钢的成品化学成分允许偏差GB/T223 钢铁及合金化学成分分析方法GB/T228 金属材料室温拉伸试验方法GB/T232 金属材料弯曲试验方法GB/T247 钢板和钢带检验、包装、标志及质量证明书的一般规定GB/T709 热轧钢板和钢带的尺寸、外形、重量及允许偏差GB713 锅炉和压力容器用钢板GB/T4338 金属材料高温拉伸试验JB/T4730.3 承压设备无损检测第三部分:超声检测3尺寸、外形、重量及允许偏差3.1钢板的尺寸、外形及允许偏差应符合GB/T709的规定。
3.2厚度偏差按GB/T709的B类执行。
3.3钢板按理论重量交货,理论计重采用的厚度为钢板允许的最大厚度和最小厚度的算术平均值。
钢的密度为7.85g/m³。
4技术要求4.1钢的牌号和化学成分(熔炼分析)应符合表1之规定。
表14.2成品分析允许偏差应符合GB/T222的规定。
4.3制造方法4.3.1冶炼采用电炉+炉外精炼、并经过真空脱气的冶炼工艺。
钢的冶炼和生产工艺应该在质量证明书中注明。
4.3.2用连铸坯轧板,其压缩比不得小于3.4.4交货状态:正火(允许加速冷却)+ 回火回火温度不低于680℃。
4.5力学性能4.5.1钢板的力学性能应符合表2的规定。
表24.5.2钢板三个试样的冲击平均值KV2≥34J,一组试验只允许一个试样KV2<34J,但不得小于27J。
4.5.3其他应符合GB713的规定。
压力容器制造技术标准

检验与验收1.压力容器主要受压部分的焊接接头分为A、B、C、D四类,如图1和图2(a、b)所示.2.制造受压元件的材料应有确认的厂内标记.在制造过程中,如需裁掉原有标记或材料分成几块,应于材料切割前完成标记移植,并保证移植标记的正确、无误、清晰、耐久。
3。
冷卷筒节投料的钢材厚度δs不得小于其名义厚度减去钢板厚度负偏差.若换热器用钢管作圆筒时,其投料壁厚偏差应符合GB/T8163和GB/T4976等钢管的标准规定。
4。
制造中应避免钢板表面的机械损伤.对于尖锐的伤痕以及不锈钢压力容器防腐表面的局部伤痕、刻槽等缺陷应予以修磨,修磨范围的斜度至少为1:3。
修磨的深度应不大于该部位钢材厚度δs的5%,且不大于2mm,否则应予以补焊。
5.坡口表面不得有裂纹、分层、夹杂等缺陷6。
标准抗拉强度下限规定值σb≥540MPa的钢材及Cr-Mo低合金钢材经火焰切割的坡口表面,应采用打磨或机械加工的方法清除热影响区和淬硬区,并进行磁粉或渗透检测。
当无法进行磁粉或渗透检测时,应由切割工艺保证坡口质量。
7.A、B类焊接接头对口错边量b(见图3)应符合表1的规定.复合钢板的对口错边量b(见图4)应不大于钢板复层厚度的50%,且不大于2mm。
换热器拼接换热管的对口错边量,应不超过换热管壁厚的15%,且不大于0。
5mm。
表1 mm 对口处钢板厚度δs 按焊接接头类别划分对口错边量bA B≤12 ≤1/4δs ≤1/4δs >12~20 ≤3 ≤1/4δs〉20~40 ≤3 ≤5注:球形封头与圆筒连接的环向接头以及嵌入式接管与圆筒或封头对接连接的A类接头,按B类焊接接头的对口错变量要求. 8。
在环向焊接接头形成的棱角E,用弦长不小于1/6内径Di,且不小于300mm的内样板或外样板检查(见图5),其值不得大于(δs/10+2)mm,且不大于5mm。
在焊接接头轴向形成的棱角E(见图6)用长度不小于300mm的直尺检查,其值不得大于(δs/10+2)mm,且不大于5mm。
压力容器专用钢板标准简介

三、GB19189-(2010)
《压力容器用调质高强度钢板》
1. 07MnMoVR钢板 (1)钢号简介 (2)化学成分
标准
GB19189-2003
GB19189-(2010)
钢号
07MnCrMoVR
07MnMoVR
P%
≤0.025
≤0.020
S%
≤0.010
≤0.010
Pcm %
≤0.20
≤0.20
钢号
12MnNiVR
12MnNiVR
板 厚 mm
12~60
12~60
Rm MPa
610~730
610~730
ReL (Rp0.2)MPa -20℃ KV2 J
≥490 ≥47
≥490 ≥80
四、GB24511-2009 《承压设备用不锈钢钢板及钢带》
1. 钢号 本标准共列入17个钢号。 铁素体型3个钢号:S11306、S11348、S11972。 奥氏体型11个钢号:S30408、S30403、S30409、
2. 09MnNiDR钢板 (1)钢号简介 (2)新旧标准对比
标准
GB3531-1996 GB3531-2008
厚 度 mm
6~60
6~120
-70℃ KV2 J
≥27
≥34
(3)国内外标准对比
标 准 GB3531-2008 EN10028-4:2003 ASME(2007)
钢号
09MnNiDR
一、GB713-2008 《锅炉和压力容器用钢板》
1. Q345R钢板 (1)钢板厚度
标准 钢号 厚 度 mm
GB6654-1996 16MnR 6~120
GB713-2008 Q345R 3~200
15CrMoR反应器技术条件

公司标准70-002/N4代替:15CrMoR反应器制造及验收工程技术条件第 1 页共 15 页目次1 范围 (1)2引用文件 (1)3 总则 (2)4 材料 (2)5 制造、检验和验收 (6)6 技术文件和资料 (12)7 外防腐及运输包装 (12)1 范围1.1 本标准规定了15CrMoR反应器在材料、制造、检验、验收和运输等方面的要求。
1.2 本标准适用于主体材料为15CrMoR钢板制的临氢反应器,其他类似工况的15CrMoR钢板制设备也可参照执行。
2 引用文件GB150-1998 钢制压力容器GB/T196-1981 普通螺纹基本尺寸(直径1-600mm)GB/T197-1981 普通螺纹公差与配合(直径1-355mm)GB/T223-1997 钢铁及合金化学分析方法GB/T228-2002 金属材料室温拉伸试验方法GB/T229-1994 金属夏比缺口冲击试验方法GB/T232-1999 金属材料弯曲试验方法GB/T3077-1999 合金结构钢GB/T4338-1995金属材料高温拉伸试验GB6654-1996 压力容器用钢板GB/T8923-1988涂装前钢材表面锈蚀等级和除锈等级2008-07-08 2008-07-08 编 制 校 审 标准化审核 审 定 发 布 日 期 实 施 日 期第 2 页共15页 7—002/N4GB/T16938-1997 紧固件 螺栓、螺钉、螺柱和螺母通用技术条件JB4708-2000 钢制压力容器焊接工艺评定JB/T4709-2000 钢制压力容器焊接规程JB/T4711-2003 压力容器涂敷与运输包装JB4726-2000 压力容器用碳素钢和低合金钢锻件JB4730-1994压力容器无损检测JB4744-2000 钢制压力容器产品焊接试板的力学性能检验GB/T6394-2002 金属平均晶粒度测定法压力容器安全技术监察规程(1999版)3 总则3.1 反应器应按《压力容器安全技术监察规程》(1999版)、GB150-1998、设计文件以及本标准的规定制造和验收。
- 1、下载文档前请自行甄别文档内容的完整性,平台不提供额外的编辑、内容补充、找答案等附加服务。
- 2、"仅部分预览"的文档,不可在线预览部分如存在完整性等问题,可反馈申请退款(可完整预览的文档不适用该条件!)。
- 3、如文档侵犯您的权益,请联系客服反馈,我们会尽快为您处理(人工客服工作时间:9:00-18:30)。
15CrMoR制压力容器技术条件1总则1.1本技术条件适用于主体材料为15CrMoR制的压力容器的制造、检验和验收。
1.2设备的制造按设备施工图、国家标准及本技术条件的各项规定2制造、检验与验收应遵循的规程、标准、规:压力容器安全技术监察规程(1999年版)钢制压力容器(GB150-1998)管壳式换热器(GB151-1999)钢制塔式容器(JB4710-1992)钢制压力容器——分析设计标准(JB4732-1995)钢制压力容器焊接规程(JB/T4709-2000)钢制压力容器焊接工艺评定(JB/T4708-2000)压力容器无损检测(JB4730-94)钢制化工容器制造技术要求(HG20584-1998)压力容器用钢板(GB6654-1996)及第一、二号修改单压力容器用爆炸不锈钢复合钢板(JB4733-1996)压力容器用碳素钢和低合金钢锻件(JB4726-2000)化肥设备用高压无缝钢管(GB6479-2000)石油裂化用无缝钢管(GB9948-1988)以上标准及技术要求之间发生矛盾时,按要求严者执行,若与本技术条件发生矛盾时按本技术条件执行。
3材料3.1.0 15CrMoR钢板应符合力容器用钢板(GB6654-1996)及第一、二号修改单的规定。
3.1.1 15CrMoR钢板的化学成分(熔炼分析)应符合如下要求(%):C≤0.12~0.18;Mn:0.40~0.70;Si:0.15~0.40;Mo:0.45~0.60;Cr:0.80~1.20;P≤0.030;S≤0.020;成品钢板的化学成分允许偏差应符合GB222的相应规定。
钢板的熔炼化学成分分析按炉(罐)号取样。
3.1.2 15CrMoR钢板经正火+回火+模拟焊后热处理后力学性能、工艺性能应符合如下要求:(1)交货状态:正火加回火(回火温度不得低于620℃)(2)拉伸试验:室温:σb=450~590Mpa; σs≥295Mpa(板厚:6~60mm); σs≥275Mpa(板厚>60~100mm);δ5≥19%(板厚:6~60mm);δ5≥18%(板厚>60~100mm);高温屈服强度σt0.2≥×××Mpa,其中t-设计温度℃,×××按GB150-1998附录F的表F1“钢板高温力学性能值”查取。
(3)冲击试验试验温度:+10℃夏比(V型缺口)冲击功A KV(横向)三个试样冲击功平均值≥31J,允许一个试样的冲击功低地平均值但不得低于22J。
试验温度:-20℃夏比(V型缺口)冲击功A KV(横向)三个试样冲击功平均值≥27J,允许一个试样的冲击功低地平均值但不得低于19J。
注:①15CrMoR焊接接头的+10℃夏比(V型缺口)冲击功A KV(横向)三个试样冲击功平均值≥31J,允许一个试样的冲击功低地平均值但不得低于22J。
15CrMoR焊接接头的-20℃夏比(V型缺口)冲击功A KV(横向)三个试样冲击功平均值≥27J,允许一个试样的冲击功低地平均值但不得低于19J。
②焊接工艺评定及产品试板均应按此要求验收。
③15CrMoR焊接接头冲击试验取样要求:a、3套标准试样。
每套3件。
b、位置:第一套试样缺口开在焊缝金属上;第二套试样缺口开在热影响区上;第一套试样缺口开在邻近热影响的母材上;(4)冷弯试验b=2a,180°,d=3a。
试验后试样应无裂纹。
3.1.3 15CrMoR钢板应近JB4730-94逐进行超声检测,合格级别为Ⅰ级。
3.1.4 15CrMoR钢板厚度应以正公差供货。
3.2 15CrMoR锻件应符合JB4726-2000的规定,供货状态为正火加回火(回火温度≥620℃)。
15CrMo锻件熔炼化学成分分析按炉(罐)号取样;15CrMo锻件的力学性能应为正火+回火+模拟焊后热处理后的数值。
3.3 15CrMo无缝管材应符合GB6479-2000《化肥设备用高压无缝钢管》的规定,供货状态为正火加回火。
3.4焊接材料3.4.1焊接材料应符合下列标准的规定:GB5117《碳钢焊条》GB5118《低合金焊条》GB8110《气体保护焊用碳钢、低合金钢焊丝》GB5293《碳素钢埋弧焊用焊剂》GB12470《低合金钢埋弧焊用焊剂》3.4.2焊条牌号按图面要求。
4制造的一般要求4.1设备应按本技术条件、图面要求和订货技术协议书进行制造与验收。
主要受压元件及与其相焊的非受压元件用钢必须具有钢厂的钢材质量证明书。
制造厂必须对设备的主要受压元件材料按材料标准、设计图纸、技术文件和用户协议书要求的项目进行复检,合格后方可投料制造。
4.2与壳体和封头相焊所有零部件(除垫板外)必须开坡口,所有受压焊接接头必须保证全焊透。
4.3所有焊接表面在施焊前应进行机械加工(或打磨),对于用切割方法制备的焊接坡口,应打磨至显出金属光泽的进行磁粉检测,按JB4730-94标准,其缺陷显示积累长度为Ⅰ级合格。
4.4厚壁管与壳体组焊后,部应打磨圆滑。
4.5接管等附件在避开筒体纵、环焊缝(包括筒体与封头之间的焊缝),并与焊缝边缘的距离不得小于100mm。
4.6制造厂应根据焊接工艺评定结果编制焊接工艺规程,然后按规程对产品进行焊接。
4.7所有与设备相连接的焊件(永久性焊件及临时性焊件)均应后热处理前焊接完毕,消除应力热处理之后不得再在设备上上旋焊或动火。
否则应重新进行焊后热处理。
4.8接管和吊耳、吊柱均不得与与筒体对接缝(包括筒体与封头之间的焊缝)或封头的拼接焊缝相碰,焊缝焊缝边缘的距离不得小于100mm。
4.9 15CrMo钢之间,焊缝坡口及两侧各不小于150mm的围的母材始终维持不低于预热温度,且不高于允许的最高层间温度,直至去进行焊后热处理,在焊接过程中,由于某种原因,必须间断焊接工作时,应使焊缝坡口及两侧各不小于150mm的围始终处于预热温度下,直至焊接工作重新开始。
4.10所有与15CrMo钢基体相连接的零件及予焊件(如接管、保温支承圈、吊耳、吊柱衬板、垫板、裙座筒节、梯子、平台预焊件等)均应在最终热处理前焊接完毕,最终焊后热处理后不得再在基体上动火引弧。
4.11禁止在容器的非焊接部位引弧。
因电弧擦伤而产生的弧坑、弧疤,割除临时附件后遗留的焊疤,均应打磨光滑,并按JB4730-94进行100%磁粉检测,Ⅰ级合格。
4.12所有焊接表面在施焊前应进行机械加工(或打磨),对于用切割方法制备的焊接坡口,应打磨至显出金属光泽后,并按JB4730-94进行100%磁粉检测,Ⅰ级合格。
4.13 15CrMo法兰接管堆焊(如果设备有的话)a、不锈钢堆焊层采用双层堆焊,堆焊层材料为00Cr19Ni10,堆焊层最小有效厚度不得小于4mm。
堆焊焊条为:过渡层A062,2mm;盖面层A002,≥2mm。
b、必须在焊接工艺评定合格后,制定出合理的接堆积不,方能正式堆焊。
c、锻件的待堆焊表面必须经机械加工或打磨,以去除氧化皮、铁锈,并达到图样要求,经磁粉或渗透检测合格后方可进行堆焊。
d、堆焊层的焊道(包括过渡层和面层)表面应光滑平整,平面度允差≤1mm,堆焊层最厚与最薄之差≤1mm。
e、过渡层和面层应分别按JB4730-94进行100%磁粉检测,其缺陷显示积累长度为等级评定Ⅰ级为合格。
4.14接管与筒体、接管与封头之间的焊缝表面应具有圆滑过渡至母材的几何形状。
4.15焊缝和热影响区表面不允许存在咬边、裂纹、气孔、弧坑、夹杂等缺陷。
焊缝上的熔渣和两侧的飞溅物必须打磨并消除干净。
4.16环槽面法兰的环槽密封面和椭圆垫的尺寸应至少每隔60°测量一次,每次测量结果均应在标准的公差围。
密封面和椭圆垫的表面粗糙度不得低于标准或设计图样的规定。
(如果设备有环槽面法兰时有此要求)4.17壳体的A、B类焊接接头有面应齐平,焊缝加强金属高最大为2mm(如果按JB4732标准制造的话,焊缝加强金属高为0mm)。
4.18各筒体之间,筒体与封头之间环缝错边量应符合GB150(如果设计标准采用JB4732标准的是符合JB4732)或者相关的其它标准的规定。
筒节纵缝的错边量应符合GB150(如果设计标准采用JB4732标准的是符合JB4732)或者相关的其它标准的规定。
焊缝在其宽度围修磨后的斜度至少为1:3,焊缝表面要平滑过渡。
4.19 15CrMo钢弯管外侧壁厚减薄量应小于10%,椭圆度应小于7%。
但两端口应修整,其椭圆度应小于2%。
弯头应进行热处理,热处理工艺应由制造厂决定,但热处理后应验证其机械性能,并满足相关规定。
4.20热处理后的弯头应对其表面进行磁粉检测,如有缺陷应予以修磨,但修磨后的壁厚就不上于公称壁厚的90%。
4.21加工面和非加工面线性尺寸公差分别按GB/T1804-2000中m级和c级精度要求。
4.22壳体直线度在一米长度的不得大于1mm,总体直线度不10mm。
5热处理5.0筒体和封头用板材应进行模拟焊后消除应力热处理,模拟焊后热处理温度、时间由制造厂确定。
并应检验模拟焊后消除应力热处理状态的机械性能,其要求应符合3.1.2的规定。
5.1所有Cr-Mo钢焊缝,焊前应均匀预热,中间应进行消除应力热处理(ISR)及时做消氢处理(DHT),最后进行最终焊后热处理(PWHT)。
5.2封头热冲压成形后必须进行恢复机械性能及供货状态的热处理。
5.3设备制造完毕后应进行整体消除的热处理。
热处理温度由制造厂确定。
在最终焊后热处理过程中,每条环焊缝隙外表面上,至少有4对沿圆周均匀的热电偶,每条纵缝上至少有两对热电偶来测量温度,并应采用连续式记录议记录温度变化。
5.4焊后热处理必须保证材料的化学成分、机械性能、金相组织不受破坏。
5.5受压元件的加工成形应采用不破坏材料机械性能及供货状态的方法进行。
如果无法满足这一要求,应进行恢复材料机械性能及使用状态的热处理。
5.6制造厂应准备足够多的焊接试板和热处理试板。
5.7模拟焊后消除应力热处理的试板检验合格后,方可对设备进行制造。
6生产试板6.1当制造厂进行正火处理时,应制作热处理验证试板1块,该试板应取在筒节延伸部分或用相同热处理制度的钢板另制1块在筒节(或封头)上,与筒节(或封头)一起进行加热和冷却。
6.1.1试板受压史及受热史应与完工设备所经历的受压史及受热史相同。
6.1.2试板应进行如下检查:a、拉力试验,取样1件b、冲击试验,取样31件c、拉力及冲击试验取样位置、方向及试验结果应符合GB150的规定。
6.2产品焊接试板6.2.1筒体A类(纵向)焊缝的产品焊接试板一付。
6.2.2筒节与筒节的B类(环向)焊缝产品焊接试板一付(当制造厂具有丰富的Cr-Mo钢设备的经验,且纵环焊缝采用相同的焊接材料和焊接工艺时可不作环焊缝试板)。
6.2.3代表DN≥150mm的接管的B类焊缝的产品焊接试板一付。