模具结构模具设计材料
落料冲孔复合模具设计说明

落料冲孔复合模具设计说明一、模具结构设计1.模具类型:落料冲孔复合模具由上模、下模和导向列组成。
根据工件的要求和形状,模具可以分为单向落料冲孔模、双向落料冲孔模和多向落料冲孔模等类型。
2.上模设计:上模一般由模座、上模板、射针等部分组成。
上模板与下模具配合使用,冲击力传递到工件上。
上模板应尽可能减小重量,提高模具寿命。
3.下模设计:下模由模座、下模板、导柱等部分组成。
下模板与上模具配合使用,负责支撑工件并传递冲压力。
下模板应具备足够的强度和刚度,以保证冲孔过程中不变形。
4.导向列设计:导向列用于保证上模与下模的定位精度。
导向柱是最常见的导向结构,其作用是使上模和下模在冲孔过程中保持相对位置的稳定性和精确性。
二、材料选择1.模具材料:常用于落料冲孔复合模具的材料有Cr12MoV、SKD11、SKH-9等。
这些材料具备良好的硬度、抗磨性和耐冲击性能,能够满足加工要求,并延长模具使用寿命。
2.工作板材:根据冲孔工件的特点和材料选择不同的板材,如不锈钢板、铝合金板、冷轧板等。
工作板材的选择应考虑其刚度、强度和耐磨性能,以提高冲孔质量和效率。
三、加工工艺1.毛坯选择:根据工件要求,选择适合的板材作为冲孔模具的毛坯。
在选择毛坯时,要注意其尺寸和平整度,以便后续的加工和使用。
2.模具加工:模具的加工过程包括车削、铣削、铣孔、磨削、钳工和装配等工序。
在加工过程中要注意控制尺寸精度和表面质量,确保模具在使用中的稳定性和寿命。
3.表面处理:模具的表面处理可以采用镀铬、硬质合金喷涂、表面渗碳等技术。
表面处理能够提高模具的耐磨性和抗腐蚀性,延长模具的使用寿命。
4.模具调试:模具制造完成后,需要进行调试和试模。
通过调试,可以检查模具的定位精度、冲孔质量和加工效率,确保模具满足设计要求。
综上所述,落料冲孔复合模具设计需要考虑模具结构、材料选择和加工工艺等方面。
通过合理的设计和加工,可以提高模具的使用寿命和冲孔质量,满足金属加工的需求。
两板模基本结构模具设计材料

目录
• 两板模基本结构 • 模具设计 • 材料选择 • 模具材料 • 模具制造工艺
01
CATALOGUE
两板模基本结构
定义与特点
定义
两板模是一种模具结构,主要由 上模板、下模板和模架组成。
特点
两板模设计简单,制造成本低, 适用于中小型塑件的大批量生产 。
结构组成
01
04
CATALOGUE
模具材料
钢材
钢材是两板模模具设计中常用的 材料之一,具有高强度、耐磨性
和耐腐蚀性等优点。
钢材可以通过热处理和表面处理 等工艺进一步提高其性能,如提 高硬度、增强耐磨性和防腐性能
等。
钢材的缺点是密度较大,较重, 且成本相对较高。
铝材
铝材是一种轻便、耐腐蚀的材料,也常用于两板 模模具设计。
02
03
上模板
上模板是两板模的上半部 分,主要作用是安装模具 的凸模和顶出机构。
下模板
下模板是两板模的下半部 分,主要作用是安装模具 的凹模和定位机构。
模架
模架是两板模的支撑结构 ,用于固定上模板和下模 板,确保模具的稳定性和 精度。
结构分类
按用途分类
根据模具用途不同,两板模可分为热塑性塑料模具和热固性塑料模具。
明确模具设计的要求和目标, 收集相行详细的结构 设计,确定零部件的形状、尺 寸、材料等。
出图与整理技术文件
完成设计后,按照标准或规范 要求绘制图纸,整理相关技术 文件。
设计软件
CAD软件
CAM软件
用于进行二维或三维的模具结构设计 。
用于生成加工代码,实现模具的数控 加工。
05
CATALOGUE
塑料模具结构
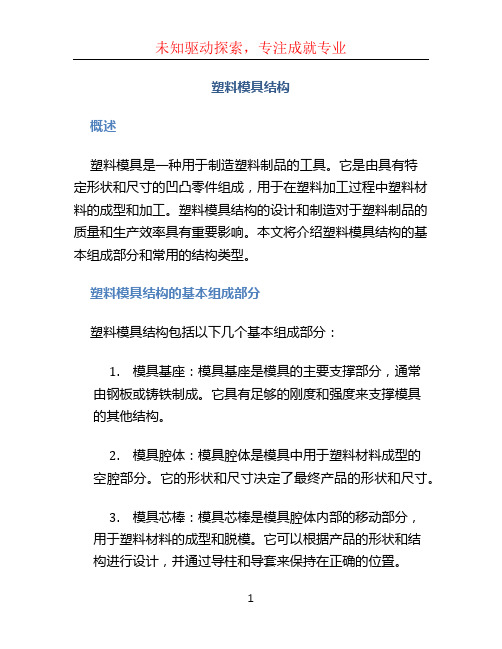
塑料模具结构概述塑料模具是一种用于制造塑料制品的工具。
它是由具有特定形状和尺寸的凹凸零件组成,用于在塑料加工过程中塑料材料的成型和加工。
塑料模具结构的设计和制造对于塑料制品的质量和生产效率具有重要影响。
本文将介绍塑料模具结构的基本组成部分和常用的结构类型。
塑料模具结构的基本组成部分塑料模具结构包括以下几个基本组成部分:1.模具基座:模具基座是模具的主要支撑部分,通常由钢板或铸铁制成。
它具有足够的刚度和强度来支撑模具的其他结构。
2.模具腔体:模具腔体是模具中用于塑料材料成型的空腔部分。
它的形状和尺寸决定了最终产品的形状和尺寸。
3.模具芯棒:模具芯棒是模具腔体内部的移动部分,用于塑料材料的成型和脱模。
它可以根据产品的形状和结构进行设计,并通过导柱和导套来保持在正确的位置。
4.模具导向系统:模具导向系统用于确保模具腔体和芯棒的准确定位和运动。
它通常包括导柱、导套和导向销等部件。
5.冷却系统:冷却系统用于控制模具温度,以确保塑料材料的快速凝固和脱模。
它通常包括冷却水管道和冷却孔等部件。
6.开关系统:开关系统用于控制模具的开合动作。
它通常包括压缩弹簧、推杆和开关机构等部件。
7.引导系统:引导系统用于模具的分离和组装。
它通常包括固定螺栓、螺母和定位销等部件。
塑料模具结构的常用类型根据不同的塑料制品和加工要求,塑料模具结构可以分为以下几种常用类型:1.单腔模具:单腔模具是一种最简单的模具结构,只有一个塑料材料成型腔体。
它适用于小批量生产和简单形状的塑料制品。
2.多腔模具:多腔模具是一种具有多个塑料材料成型腔体的模具结构。
它可以生产多个相同或不同形状的塑料制品,提高生产效率。
3.热流道模具:热流道模具是一种通过加热系统来控制塑料材料的流动和成型的模具结构。
它可以避免塑料制品中的缺陷和熔融料的浪费。
4.双色模具:双色模具是一种能够在同一模具中成型两种不同颜色的塑料制品的模具结构。
它可以实现多彩和多功能的塑料制品。
模具的基本结构组成

模具的基本结构组成一、引言模具是制造工业产品的重要工具,它能够将原材料加工成所需形状和尺寸的零件。
模具的基本结构组成是模具设计与制造的基础,本文将从以下几个方面介绍模具的基本结构组成。
二、模具的基本组成1. 上模板:上模板是模具的上部分,也是模具的主体部分,它承受着模具的大部分工作压力。
上模板通常由钢材制成,具有足够的强度和硬度来抵抗模具在工作过程中的应力和磨损。
2. 下模板:下模板是模具的下部分,它通常与上模板配合使用,用于支撑和定位工件。
下模板也由钢材制成,其硬度和强度要求较上模板低一些,但仍需具备足够的刚性和耐磨性。
3. 滑块:滑块是模具的一个重要组成部分,用于实现模具的开合动作。
滑块通常由滑块板和导柱组成,通过导柱的引导,滑块能够在模具的开合过程中平稳移动。
滑块的设计和制造直接影响模具的工作效率和精度。
4. 塑料模具芯:塑料模具芯是模具中的一个重要部件,它用于成型工件的内部形状。
模具芯通常由钢材或铝材制成,具有良好的刚性和导热性能,能够有效地支撑和冷却工件。
5. 模具座:模具座是模具的支撑部分,它提供了模具的安装位置和固定方式。
模具座通常由铸铁或钢材制成,具有足够的强度和稳定性,能够确保模具在工作过程中的稳定性和精度。
6. 导向机构:导向机构是模具中的一个重要组成部分,它用于确保模具在工作过程中的准确位置和运动轨迹。
导向机构通常由导向销、导向套和导向板等部件组成,通过它们的配合运动,能够实现模具的精确定位和稳定运动。
7. 顶针:顶针是模具中的一个常用部件,它用于实现模具的顶出动作。
顶针通常由钢材制成,具有良好的弹性和耐磨性,能够承受较大的顶出力,并保持工作精度。
8. 弹簧:弹簧是模具中的一个重要辅助部件,它用于实现模具的复位和顶出动作。
弹簧通常由弹簧钢制成,具有一定的弹性和耐久性,能够确保模具在工作过程中的正常运动和复位。
9. 冷却系统:冷却系统是模具中的一个重要组成部分,它用于控制模具的温度和工作环境。
常见的压铸模具结构及设计
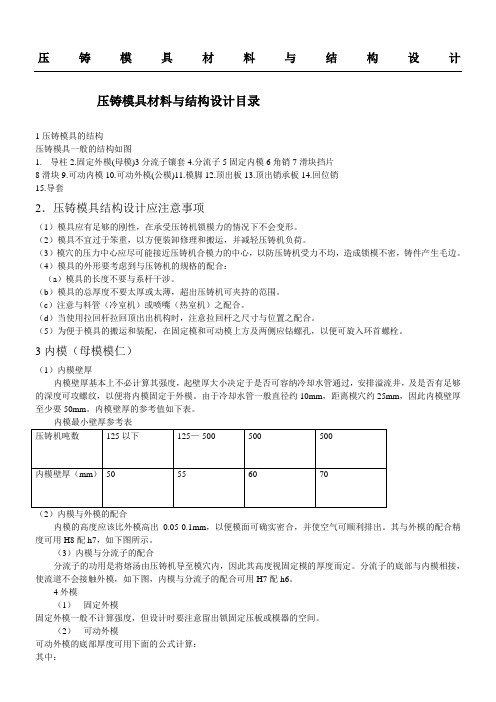
压铸模具材料与结构设计压铸模具材料与结构设计目录1压铸模具的结构压铸模具一般的结构如图1.导柱2.固定外模(母模)3分流子镶套4.分流子5固定内模6角销7滑块挡片8滑块9.可动内模10.可动外模(公模)11.模脚12.顶出板13.顶出销承板14.回位销15.导套2.压铸模具结构设计应注意事项(1)模具应有足够的刚性,在承受压铸机锁模力的情况下不会变形。
(2)模具不宜过于笨重,以方便装卸修理和搬运,并减轻压铸机负荷。
(3)模穴的压力中心应尽可能接近压铸机合模力的中心,以防压铸机受力不均,造成锁模不密,铸件产生毛边。
(4)模具的外形要考虑到与压铸机的规格的配合:(a)模具的长度不要与系杆干涉。
(b)模具的总厚度不要太厚或太薄,超出压铸机可夹持的范围。
(c)注意与料管(冷室机)或喷嘴(热室机)之配合。
(d)当使用拉回杆拉回顶出出机构时,注意拉回杆之尺寸与位置之配合。
(5)为便于模具的搬运和装配,在固定模和可动模上方及两侧应钻螺孔,以便可旋入环首螺栓。
3内模(母模模仁)(1)内模壁厚内模壁厚基本上不必计算其强度,起壁厚大小决定于是否可容纳冷却水管通过,安排溢流井,及是否有足够的深度可攻螺纹,以便将内模固定于外模。
由于冷却水管一般直径约10mm,距离模穴约25mm,因此内模壁厚至少要50mm。
内模壁厚的参考值如下表。
内模最小壁厚参考表(2)内模与外模的配合内模的高度应该比外模高出0.05-0.1mm,以便模面可确实密合,并使空气可顺利排出。
其与外模的配合精度可用H8配h7,如下图所示。
(3)内模与分流子的配合分流子的功用是将熔汤由压铸机导至模穴内,因此其高度视固定模的厚度而定。
分流子的底部与内模相接,使流道不会接触外模,如下图,内模与分流子的配合可用H7配h6。
4外模(1)固定外模固定外模一般不计算强度,但设计时要注意留出锁固定压板或模器的空间。
(2)可动外模可动外模的底部厚度可用下面的公式计算:其中:h:外模底部之厚度(mm)p:铸造压力(kg/cm2)L:模脚之间距(mm)a:成品之长度(mm)b:成品之宽度(mm)B:外模之宽度(mm)E:钢的杨氏模数=2.1×106kg/cm2d:外模在开模方向的最大变形量(mm),一般取d≤0.05mm.例:某铸件长300mm,宽250mm,铸造压力选定280(kg/cm2),外模之宽度560(mm),模脚之间距360(mm),最大变形量取0.05(mm)。
模具结构设计方案

模具结构设计方案模具是工业生产中常用的工具之一,广泛应用于塑料、金属、陶瓷等制品的生产过程中。
模具的结构设计对产品的成型质量、生产效率以及模具寿命等都有着重要的影响。
下面将以塑料模具为例,详细介绍模具结构设计的几个方面。
首先是模具的整体结构设计。
模具一般由上、下两部分组成,上模和下模之间通过模具螺栓连接。
上模通常由进料口、固定板、移动板、顶针等部分组成,下模则由底板、定位销、导向板等部分组成。
在整体结构设计中,需要注意上、下模的对位准确、顶出机构的稳定性以及模具的可拆卸性等。
其次是注塑模具中的流道系统设计。
流道系统是塑料模具中最关键的部分,直接影响产品的成型质量。
在流道系统的设计中,需要考虑塑料的充填速度、压力和温度等因素,合理选择流道的截面形状和尺寸。
同时,还需要设计出合适的喷嘴和冷却系统,以确保塑料在流道中充分流动和冷却。
第三是模具的冷却系统设计。
冷却系统对于模具寿命和产品质量有着重要的影响。
在冷却系统的设计中,需要合理设置冷却通道,并确保冷却通道与模具表面的距离足够近,以提高冷却效果。
同时,还需要注意冷却通道的位置和布局,以保证整个模具受热均匀,避免产生应力集中和变形等问题。
另外还需要考虑模具的顶出机构设计。
顶出机构主要用于将成型的产品从模具中弹出,避免产品粘模。
在顶出机构的设计中,需要确保顶出机构的稳定性和可靠性,同时考虑到产品的形状、材料和尺寸等因素,设计合适的顶出机构形式和数量。
最后是模具材料的选择。
模具材料的选择直接影响到模具的使用寿命和成本。
一般而言,模具材料要求具有较高的硬度、强度和耐磨性,同时还需具备一定的耐腐蚀性和导热性等特点。
在选择模具材料时,需要根据具体的生产需求和经济因素综合考虑,选择合适的模具材料。
综上所述,模具结构设计是一个复杂的工作,需要考虑多个方面的因素。
合理的模具结构设计可以提高产品的成型质量和生产效率,延长模具的使用寿命,减少生产成本。
因此,在进行模具结构设计时,需要充分考虑以上几个方面的原则和要点,以保证模具的性能和质量。
模具中的常用材料

Si 0.85~1.15
铸1.2333(锻 1.2358)
0.57~0. 61
铸1.2370(YBD-3) 0.9~1.0
(锻1.2363)
5
Cr12MoV锻
1.451. 70
铸1.2382(锻 1.2379)
1.5-1.6
0.25~0.45 0.20~0.40 ≤0.4
0.5-0.8
Mn 0.65~1.05 0.70~0.90 0.40~0.70 ≤0.35
表面淬火 HRC56以上 整体,表面 感应HRC58-
62
《模具中的常用材料及设计中应注意的一些加工问题》
材料
税前价 格/ 公斤
Cr12Mo1V1( 类 似于SKD11) 德国牌号1.2379 (相应铸态牌
号1.2382)
SKD11 :59.83
Cr12MoV
14.96
DC53
70
7CrSiMnMoV (相应铸态牌
1.2333
铸态材料对照表
热处理
用途
底板、压料板、压料圈基体、驱 动块、带导板的CAM滑块
退火硬度
FH/IH 50-54 IH 54-58
拉延凸模、压料圈
驱动块、不带导板的CAM滑块\单 薄底板、压料板
耐磨损的拉延凸模、压料圈、凹 模
FH/IH 50-54 IH/H 58-62 FH/IH 54-56 IH 56-60
单薄压料板
滑块等
整形大凸模、凹模
料厚超过1.5或翻边高度超过25的 翻边凹模,拉延模镶块
供货状态 硬度(HBS)
灰铸铁
HT250 /HT300
球墨铸铁
QT400(不常用, 可用
QT500代 替)
压铸模具设计方案
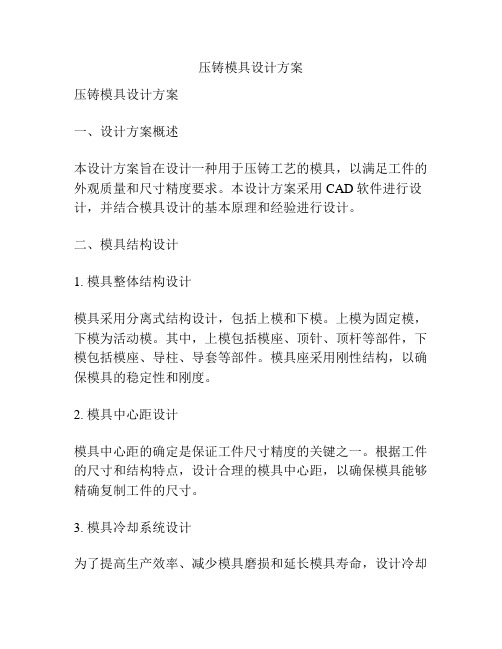
压铸模具设计方案压铸模具设计方案一、设计方案概述本设计方案旨在设计一种用于压铸工艺的模具,以满足工件的外观质量和尺寸精度要求。
本设计方案采用CAD软件进行设计,并结合模具设计的基本原理和经验进行设计。
二、模具结构设计1. 模具整体结构设计模具采用分离式结构设计,包括上模和下模。
上模为固定模,下模为活动模。
其中,上模包括模座、顶针、顶杆等部件,下模包括模座、导柱、导套等部件。
模具座采用刚性结构,以确保模具的稳定性和刚度。
2. 模具中心距设计模具中心距的确定是保证工件尺寸精度的关键之一。
根据工件的尺寸和结构特点,设计合理的模具中心距,以确保模具能够精确复制工件的尺寸。
3. 模具冷却系统设计为了提高生产效率、减少模具磨损和延长模具寿命,设计冷却系统对模具进行冷却。
冷却系统包括冷却孔和进水口,通过冷却水的流动,迅速冷却模具,以提高生产效率和模具寿命。
4. 模具材料选择模具的材料选择是保证模具寿命和使用效果的重要因素。
根据工件的材料和要求,选择适当的模具材料,保证模具具有良好的硬度和耐磨性。
三、模具生产工艺1. 加工工艺规程模具的加工工艺包括数控加工、外圆磨削等。
根据模具的具体结构和工艺要求,制定合理的加工工艺规程,以确保模具的加工质量。
2. 检测工艺模具加工完成后,进行检测以验证模具的质量。
检测工艺包括模具尺寸检测、表面质量检测等,通过合适的检测工艺,确保模具符合设计要求。
四、模具的维护、维修和更换为了保证模具的正常使用和延长其寿命,进行模具的定期维护、维修和更换。
维护工作包括清洁模具、添加润滑剂等,维修工作包括修复模具损伤、更换模具部件等,更换工作包括根据模具磨损程度,定期更换模具部件。
五、结论本设计方案是一种用于压铸工艺的模具设计方案,通过合理的结构设计、材料选择和加工工艺,可以满足工件的外观质量和尺寸精度要求。
同时,通过模具的定期维护、维修和更换,可以保证模具的正常使用和延长其寿命。
混凝土模具的制作方法

混凝土模具的制作方法一、概述:混凝土模具是混凝土建筑中不可缺少的一部分,它能够将混凝土打造成各种形状和尺寸的构件,提高混凝土建筑的质量和效率。
本文将介绍混凝土模具的制作方法,包括设计、材料、工具、制作流程等方面。
二、设计:1. 根据需要制作的混凝土构件,确定模具的尺寸和形状。
2. 根据模具的尺寸和形状,制作模具结构图和零件图。
3. 确定模具结构的材料和厚度。
三、材料:1. 模板材料:选择优质、平直、不易变形的板材,如胶合板、钢板等。
2. 模具结构材料:根据模具的形状和尺寸选择合适的钢材、铝材等。
3. 模具表面处理材料:选择合适的材料对模具表面进行处理,如油漆、蜡等。
四、工具:1. 制作工具:锤子、电钻、铣床等。
2. 安装工具:扳手、螺丝刀、螺母、螺栓等。
五、制作流程:1. 制作模板:根据设计图纸将模板材料裁剪成所需的尺寸和形状,并固定在模板架上。
2. 制作模具结构:根据设计图纸将钢材等结构材料按照一定的尺寸和形状进行切割、加工、焊接等工艺,组成模具结构。
3. 安装模板和模具结构:将制作好的模板和模具结构组合安装在一起,固定好。
4. 处理模具表面:对模具表面进行处理,如刷油漆、涂蜡等。
5. 完成模具:经过以上步骤,模具制作完成。
六、注意事项:1. 制作模具时要严格按照设计图纸进行,保持尺寸和形状的精度和一致性。
2. 模具结构要牢固,承受混凝土浇注的重压,避免变形和破裂。
3. 模具表面处理要均匀、细致,避免影响混凝土的表面质量。
4. 制作过程中要注意安全,使用工具时要注意保护措施。
七、总结:混凝土模具的制作是混凝土建筑施工中不可缺少的一环,其制作质量直接影响到混凝土构件的质量和效率。
本文介绍了混凝土模具的制作方法,包括设计、材料、工具、制作流程等方面。
制作时应注意各项细节,确保制作出稳定、精度高、表面平整的混凝土模具。
塑胶模具结构设计

塑胶模具结构设计塑胶模具结构设计是制造业中至关重要的环节,它直接关系到产品的质量、生产效率和成本。
本文将围绕塑胶模具结构设计的基本原则、设计流程及注意事项进行详细阐述。
一、塑胶模具结构设计的基本原则1. 确保产品精度在设计塑胶模具时,要保证产品的尺寸精度和形状精度。
这要求设计师充分了解塑胶材料的收缩率、流动性等特性,并在模具设计中予以充分考虑。
2. 易于加工与装配模具结构应尽量简单,便于加工和装配。
复杂的设计不仅会增加制造成本,还可能影响模具的可靠性。
在设计过程中,要充分考虑模具零件的加工工艺性和装配顺序。
3. 高效生产塑胶模具结构设计应考虑生产效率,尽量减少生产过程中的辅助时间。
例如,通过优化流道设计、缩短冷却时间等措施,提高生产效率。
4. 安全可靠5. 维护方便模具在使用过程中难免会出现磨损、损坏等问题,设计时应考虑模具的维修便捷性,降低维护成本。
二、塑胶模具结构设计流程1. 分析产品结构在设计模具前,要对产品结构进行分析,了解产品的尺寸、形状、技术要求等,为模具设计提供依据。
2. 确定模具类型根据产品结构特点和生产要求,选择合适的模具类型,如单腔模具、多腔模具、热流道模具等。
3. 设计分型面分型面是模具闭合时,分离塑胶制品和浇注系统的界面。
设计分型面时要考虑产品的脱模斜度、外观质量等因素。
4. 设计浇注系统浇注系统包括主流道、分流道、浇口等部分,其设计直接影响到塑胶制品的质量。
设计时应关注流道截面积、长度、浇口位置等因素。
5. 设计冷却系统冷却系统对塑胶制品的质量和生产效率具有重要影响。
设计时要考虑冷却水路的布局、冷却水流量、冷却水温度等因素。
6. 设计顶出系统顶出系统的作用是在模具开模时,将制品从模具中顺利取出。
设计时要确保顶出力均匀、可靠,避免产品变形或损坏。
7. 绘制模具零件图及装配图三、塑胶模具结构设计注意事项1. 充分考虑塑胶材料的特性,如收缩率、流动性、热稳定性等。
2. 优化模具结构,提高生产效率,降低生产成本。
塑胶模具结构详解
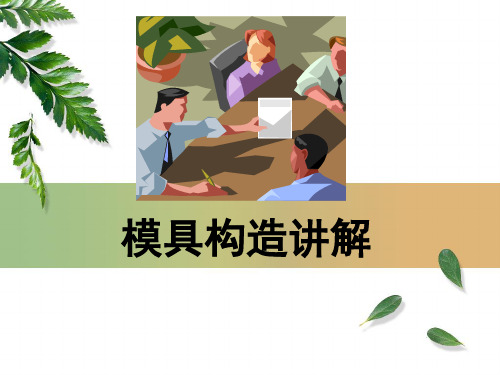
PA66 SPVC TPU PMMA PBT
1.0~2.5 1.5~2.5(2.0)* 1.2~2.0(1.6)* 0.5~0.7(0.5)* 1.3~2.2(1.6)*
ABS
1: ABS俗称超不碎胶,是一种高强度改性 PS 。
2:三元结构的ABS兼具各组分的多种固有特 性:丙烯 腈能使制品有较高的强度和表面 硬度,提高耐化学腐蚀性和耐热性;丁二 烯使聚合物有一定的柔顺性,使制件在低 温下具有一定的韧性和弹性、较高的冲击 强度而不易脆折;苯乙烯使分子链保持刚 性,使材质坚硬、带光泽,保留了良好的 电性能和热流动性,易于加工成型和染色。
(5)免胶料流动出现“跑道”效应、使胶件产生困 气、熔接痕现象:止口位胶片潜入浇口、避免表面 气烘胶片、胶柱入浇口,表面易产生气烘外表面 有气烘。
(7)避免浇口处产生气烘、蛇纹等现象。
(8)胶料流入方向、应使其流入型腔时、能沿着型腔 平行方向均匀地流入、避免胶料入浇口在长度方 向均匀地流入、避免变形成品为透明胶片成品不 直接入浇、避免表面气烘、蛇纹流动各向异性、 使胶件产生翘曲变形、应力开裂现象。
四:模具的内部结构设计
1:模具的胶位设计 胶件壁厚应均匀一致,避免突变和截面厚 薄悬殊的设计,否则会引起收缩不均, 使胶件表面产生缺陷。
2:胶件壁厚一般在1~6mm范围内,最常用 壁厚值为1.8~3mm,这都随胶件类型及 胶件大小而定。
2:模具骨位的设计、
(1) 胶件骨位其作用有增加强度、固定底面壳、 支撑架、按键导向等。 由于骨位与胶件壳体连 接处易产生外观收缩凹陷;所以、要求骨位厚 度应小于等于0.5t(t为胶件壁厚) 、一般骨位厚 度在0.8~1.2mm范围。
模具构造讲解
目录
一:模具的分类 二:模具的结构 三:常用注塑材质 四:模具的内部结构设计
装配式建筑施工中的模具设计及其制造工艺
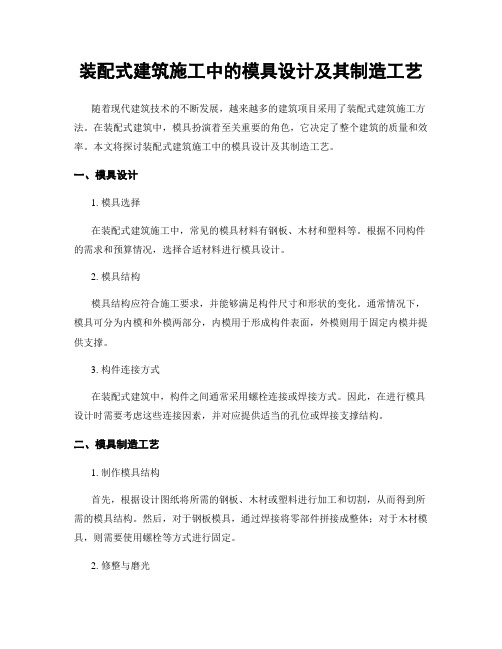
装配式建筑施工中的模具设计及其制造工艺随着现代建筑技术的不断发展,越来越多的建筑项目采用了装配式建筑施工方法。
在装配式建筑中,模具扮演着至关重要的角色,它决定了整个建筑的质量和效率。
本文将探讨装配式建筑施工中的模具设计及其制造工艺。
一、模具设计1. 模具选择在装配式建筑施工中,常见的模具材料有钢板、木材和塑料等。
根据不同构件的需求和预算情况,选择合适材料进行模具设计。
2. 模具结构模具结构应符合施工要求,并能够满足构件尺寸和形状的变化。
通常情况下,模具可分为内模和外模两部分,内模用于形成构件表面,外模则用于固定内模并提供支撑。
3. 构件连接方式在装配式建筑中,构件之间通常采用螺栓连接或焊接方式。
因此,在进行模具设计时需要考虑这些连接因素,并对应提供适当的孔位或焊接支撑结构。
二、模具制造工艺1. 制作模具结构首先,根据设计图纸将所需的钢板、木材或塑料进行加工和切割,从而得到所需的模具结构。
然后,对于钢板模具,通过焊接将零部件拼接成整体;对于木材模具,则需要使用螺栓等方式进行固定。
2. 修整与磨光为了保证构件表面的平整度和光滑度,需要对模具进行修整和磨光。
修整是指检查并调整模具的尺寸和形状以达到要求,在此过程中可能需要使用砂纸、锉刀和其他手工工具。
而磨光则可以通过使用打磨机或其他抛光设备来实现。
3. 防腐处理为了延长模具的使用寿命并防止锈蚀,通常需要对其进行防腐处理。
这可以通过喷涂防锈漆或镀锌等方法来实现。
4. 调试与测试在设计完成并制造好模具后,还需要进行调试与测试工作。
调试是指验证模具是否符合预期效果,并进行必要的微调;测试则是验证构件是否能够顺利脱模,并检查表面质量是否符合要求。
总结:装配式建筑施工中的模具设计及其制造工艺对于保证装配式建筑质量和效率具有重要意义。
合理的模具设计可以确保构件尺寸和形状的准确性,并提供稳定的支撑。
同时,优秀的模具制造工艺能够保证模具结构的坚固性和平整度,并延长使用寿命。
模具结构设计
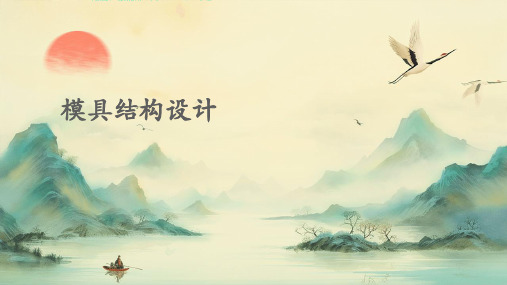
VS
详细描述
锻造模具结构设计需要考虑锻造工艺参数 、锻造材料特性、模具寿命和制造成本等 因素。在设计中,应注重优化模膛设计、 导向装置、顶出装置等部分,以确保锻造 生产的顺利进行和产品质量。
05
模具结构设计软件与应用
CAD/CAE/CAM技术在模具结构设计中的应用
01
CAD(计算机辅助 设计)
利用CAD软件进行模具的三维建 模,实现模具零件的精确设计和 定位。
低热膨胀系数
模具材料的热膨胀系数应尽可能小,以减小 温度变化对模具尺寸的影响。
04
模具结构设计实例分析
注塑模具结构设计实例
总结词
注塑模具结构设计是模具设计中的重要一环,需要考虑多方面因素,如塑考虑塑料的收缩率、流动性、结晶性等特性,以及模具的强度、刚度、寿命等因素。同时, 还需要考虑注塑机参数,如注射量、注射压力、模具安装尺寸等。在设计中,应注重优化浇注系统、冷却系统、 顶出系统等部分,以提高生产效率和产品质量。
浇注系统设计
浇注系统是模具的重要组成部分,其 设计的好坏直接影响到制品的质量和 生产效率。
浇注系统的结构形式有多种,应根据 制品的大小、形状和材料特性选择合 适的结构形式。
浇注系统的设计应遵循“快速、等高 、等流量”的原则,确保金属液能够 均匀地充满型腔。
浇注系统的尺寸和位置对制品的尺寸 精度和模具的加工制造也有很大影响, 需要仔细考虑。
02
CAE(计算机辅助 工程)
通过CAE技术对模具结构进行有 限元分析,预测模具的应力分布、 变形和寿命等性能。
03
CAM(计算机辅助 制造)
将模具设计数据导入CAM软件, 生成数控加工代码,控制机床完 成模具的加工制造。
常用模具结构设计软件介绍
模具基本结构简介之三板模

模具基本結構簡介之三板模1. 介绍在模具制造中,使用三板模是非常常见的一种模具形式。
三板模是由上模板、下模板和侧模板组成的,其中上模板和下模板通常用于形成模具内部的空腔,而侧模板则用于固定和定位上下模板。
本文将详细介绍三板模的基本结构和工作原理。
2. 上模板上模板是三板模中的一个关键部分,其主要作用是形成模具内部的空腔。
上模板通常由高强度的金属材料制成,如钢材。
在制造上模板时,通常需要经历下列工序:•材料选择:选择适合的金属材料,常用的有P20、H13等;•加工:根据设计要求,进行铣削、镟削、磨削等加工工艺;•加工表面:通过研磨等方法使上模板表面光滑度更高;•热处理:采用淬火、回火等热处理工艺提高材料的硬度和强度;•组装:将上模板与其他模具部件组装在一起。
上模板的设计需要考虑产品形状、尺寸和生产工艺等因素,以满足模具的使用要求。
3. 下模板下模板是三板模中另一个重要组成部分,其主要作用是提供模具内部空腔的下半部分。
下模板与上模板紧密配合,共同形成模具的工作空间。
下模板通常也是由高强度金属材料制成,制造工艺与上模板类似。
下模板与上模板、侧模板和模具座等部件一起组成了一个完整的模具系统。
下模板的设计需要考虑模具的定位槽、导柱、导套等结构,以确保模具的定位精度和稳定性。
侧模板是三板模中的一个重要组成部分,其主要作用是固定和定位上模板和下模板。
侧模板通常由金属材料制成,具有较高的刚性和稳定性。
在制造侧模板时,需要考虑到以下方面:•加工精度:侧模板的加工精度需要保证模具的定位精度,以便正确装配上下模板;•耐磨性:侧模板需要具备一定的耐磨性,以应对模具长时间使用时的摩擦和磨损;•安装便捷性:侧模板的安装需要方便快捷,以提高模具的装配效率。
侧模板与上模板和下模板之间通常通过螺栓、导柱等连接方式进行固定。
使用三板模进行模具工作时,需要按照以下步骤进行:1.安装侧模板:先将侧模板固定在适当的位置,确保与上模板和下模板的配合精度。
模具结构设计方案

模具结构设计方案1. 引言模具在工业生产中起到了至关重要的作用。
它是制造产品的关键工具,因此模具的结构设计方案显得尤为重要。
本文将介绍模具结构设计方案的基本要素和步骤,以及一些注意事项。
2. 设计要素模具结构设计方案应考虑以下要素:2.1. 产品形状与尺寸模具的结构设计必须符合产品的形状与尺寸要求。
在设计过程中,需要充分理解产品的设计图纸和规格要求,确保模具能够精确制造出符合产品要求的零件。
2.2. 材料选择模具的材料选择直接关系到模具的使用寿命和性能。
常见的模具材料包括钢材、铝合金等。
在材料选择时,需要考虑产品的材料特性、使用环境等因素,以确保模具材料能够满足设计要求。
2.3. 结构稳定性模具的结构稳定性直接影响到产品的质量和加工精度。
设计时需要注意避免模具结构存在松动、变形等问题,以保证模具能够长时间稳定地工作。
2.4. 拆卸与维修模具在使用过程中可能需要进行拆卸和维修,因此设计时需要充分考虑模具的拆卸和维修性能。
模具应设计合理的拆卸结构,方便拆装及维修。
3. 设计步骤设计模具结构的步骤如下:3.1. 产品分析首先,对待加工的产品进行分析。
了解产品的形状、尺寸、材料等特点,确定模具所需的结构和工艺要求。
3.2. 模具类型选择根据产品的特点和加工要求,选择合适的模具类型。
常见的模具类型包括冲压模具、注塑模具、压铸模具等。
3.3. 模具结构设计根据产品的特点和模具类型,进行模具的结构设计。
根据产品的形状和工艺要求设计模具的尺寸、形状、结构等,并考虑材料选择和结构稳定性等因素。
3.4. 模具细节设计根据模具的整体结构设计,进一步设计模具的细节部分。
包括模具的导向、导轨、脱模机构、冷却系统等。
3.5. 模具装配与调试将设计好的模具进行装配,并进行相应的调试工作。
确保模具能够正常工作,满足产品加工的要求。
4. 设计注意事项在进行模具结构设计时,需要注意以下事项:4.1. 工艺性考虑在模具设计过程中,需要充分考虑产品的工艺要求。
模具的主要零件及结构设计
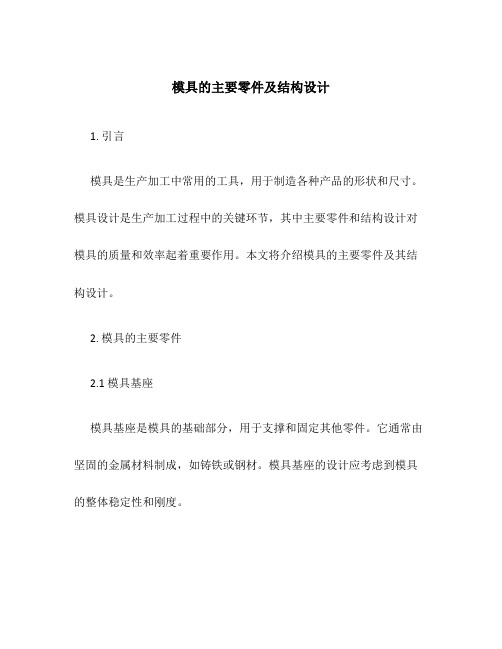
模具的主要零件及结构设计1. 引言模具是生产加工中常用的工具,用于制造各种产品的形状和尺寸。
模具设计是生产加工过程中的关键环节,其中主要零件和结构设计对模具的质量和效率起着重要作用。
本文将介绍模具的主要零件及其结构设计。
2. 模具的主要零件2.1 模具基座模具基座是模具的基础部分,用于支撑和固定其他零件。
它通常由坚固的金属材料制成,如铸铁或钢材。
模具基座的设计应考虑到模具的整体稳定性和刚度。
2.2 上模和下模上模和下模是模具的核心部分,用于构成产品的外形和内部空间。
上模与下模紧密配合,形成产品的形状和尺寸。
它们通常由具有良好耐磨性和导热性的材料制成,如钢材。
上模通常由模具芯和模具腔组成。
模具芯用于形成产品的内部空间,模具腔用于形成产品的外部形状。
2.3 推杆和导柱推杆和导柱是模具中用于开启和关闭模具的零件。
推杆通过控制模具的动作,将上模与下模分开或接触。
导柱则用于保证模具的定位和精度。
推杆和导柱通常由高强度和耐磨性的材料制成,如合金钢。
2.4 导向装置导向装置用于控制模具各个零件之间的相对位置和运动。
它通常由导向销、导向套和导向板组成。
导向装置的设计应考虑到模具的精度和运动的平稳性。
3. 模具的主要结构设计3.1 结构分析在模具的结构设计中,需要进行结构分析来确定各个零件的相对位置和运动形式。
结构分析包括静态分析和动态分析两个方面。
静态分析用于确定模具在静止状态下各个零件之间的受力情况和刚度要求。
动态分析用于确定模具在工作过程中各个零件之间的运动轨迹和动态特性。
3.2 结构优化结构优化是模具设计的重要环节。
通过优化设计,可以提高模具的强度、刚度和稳定性,降低模具的质量和成本。
结构优化可以从材料选用、零件几何结构和连接方式等方面进行。
3.3 结构刚度模具的结构刚度对模具的工作精度和使用寿命有着重要影响。
结构刚度可以通过增加模具的壁厚、增大模具的截面尺寸来提高。
此外,利用合理的加强结构和增加支撑件也可以有效提高模具的结构刚度。
模具结构介绍范文
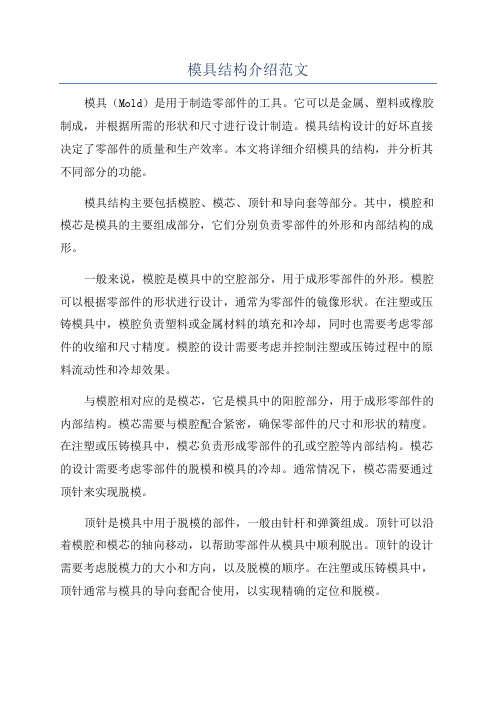
模具结构介绍范文模具(Mold)是用于制造零部件的工具。
它可以是金属、塑料或橡胶制成,并根据所需的形状和尺寸进行设计制造。
模具结构设计的好坏直接决定了零部件的质量和生产效率。
本文将详细介绍模具的结构,并分析其不同部分的功能。
模具结构主要包括模腔、模芯、顶针和导向套等部分。
其中,模腔和模芯是模具的主要组成部分,它们分别负责零部件的外形和内部结构的成形。
一般来说,模腔是模具中的空腔部分,用于成形零部件的外形。
模腔可以根据零部件的形状进行设计,通常为零部件的镜像形状。
在注塑或压铸模具中,模腔负责塑料或金属材料的填充和冷却,同时也需要考虑零部件的收缩和尺寸精度。
模腔的设计需要考虑并控制注塑或压铸过程中的原料流动性和冷却效果。
与模腔相对应的是模芯,它是模具中的阳腔部分,用于成形零部件的内部结构。
模芯需要与模腔配合紧密,确保零部件的尺寸和形状的精度。
在注塑或压铸模具中,模芯负责形成零部件的孔或空腔等内部结构。
模芯的设计需要考虑零部件的脱模和模具的冷却。
通常情况下,模芯需要通过顶针来实现脱模。
顶针是模具中用于脱模的部件,一般由针杆和弹簧组成。
顶针可以沿着模腔和模芯的轴向移动,以帮助零部件从模具中顺利脱出。
顶针的设计需要考虑脱模力的大小和方向,以及脱模的顺序。
在注塑或压铸模具中,顶针通常与模具的导向套配合使用,以实现精确的定位和脱模。
导向套是模具中的定位部件,用于确保模腔、模芯和顶针的正确定位。
导向套通常由导向柱和导向套轴承组成。
导向柱安装在模具的固定板上,导向套轴承则安装在模具的动态板或顶板上。
通过导向套的定位,模腔、模芯和顶针可以在注塑或压铸过程中正确移动和定位。
导向套的设计需要考虑导向的精度和防止卡死的措施。
除了上述主要组成部分外,模具结构还会涉及其他辅助部件,如冷却系统、排气系统和喷嘴等。
冷却系统用于控制模具的温度,以确保注塑或压铸过程中零部件的质量和尺寸的稳定性。
排气系统用于排除气泡或气体,以防止零部件出现气孔或热缩痕。
模具的主要零件及结构设计

模具的主要零件及结构设计模具是一种用于制造零件或产品的工具,其主要作用是将各种原材料(如塑料、金属等)加工成特定形状的产品或零件。
模具的组成部件和结构设计非常重要,因为这直接影响产品的品质、生产效率和成本。
本文将介绍模具的主要零件和结构设计。
一、模具的主要零件1. 模具下模:负责承载模具的基础部分,也是产品的底部。
模具下模通常是由耐磨材料制成,以保证模具的耐用性和稳定性。
2. 模具中模:模具中模与模具下模协同工作,主要是用于制作一个产品的外形,例如制造塑料瓶盖的模具中模。
3. 模具上模:模具上模负责完成产品的内部结构,通常是和模具中模配合使用。
它主要由耐磨材料制成,以便在生产过程中承受高压和高温。
4. 模具滑块:模具滑块是用于控制产品中的突起或凹槽的零件,它可以在模具中作水平或垂直滑动。
如制造手柄或脚踏板的模具滑块。
5. 模具顶针:模具顶针常常被用于制造一些小型的产品和零件。
例如电子元件的模具中通常有许多模具顶针,用于插入电子元件的引脚,形成电路。
6. 模具弹簧:模具弹簧的作用是保证模具在生产过程中的密闭性。
它不仅可以确保某些部件的正常运行,而且可以延长模具的使用寿命。
7. 模具导柱及导套:模具导柱和导套通过支撑模具并使其在生产过程中保持垂直状态。
导柱和导套还可以用于固定模具与模具承载架之间的连接。
它们的精度非常重要,一旦失误,可能造成零部件的损坏和生产成本的增加。
二、模具结构设计模具结构设计非常重要,因为它可以影响到生产效率和产品的质量。
以下是模具结构设计的一些重要因素:1. 模具的基础结构设计:每个模具都应该被设计成具有承受极高压力和高温的能力。
因此,基础的结构设计需要非常坚固。
2. 模具通道和出料槽的位置:设计模具时要确保必要的通道和出料槽位于正确的位置,以便最大限度地减少生产过程中的浪费和损失。
3. 模具的材料:模具的材料应该具有良好的耐磨性、耐腐蚀性和强度,以便在生产过程中保持稳定和良好的性能。
热压模具设计原理及应用

热压模具设计原理及应用热压模具设计原理及应用热压模具是一种常用的模具种类,广泛应用于各个行业,特别是在塑料成型、橡胶制品、玻璃钢制品以及复合材料等领域。
它通过将原材料加热至一定温度,然后施加一定的压力,使原材料在模具中进行加工成型。
下面将介绍热压模具的设计原理及应用。
设计原理:热压模具的设计原理主要包括模具结构设计和加热系统设计两个方面。
1. 模具结构设计:模具结构设计是热压模具设计的核心,它包括了模具材料选择、模具形状设计以及模具零件结构设计等内容。
(1)模具材料选择:热压模具要求具备一定的硬度和耐磨性,以便能够承受高温和高压下的工作条件。
常见的模具材料包括工具钢、硬质合金、耐磨铸铁等。
(2)模具形状设计:模具形状设计考虑到了产品的形状特征和加工要求,通常采用分模式设计,包括上模、下模、侧模等部分。
同时,还要考虑到产品的脱模性能,避免模具在脱模过程中产生损坏。
(3)模具零件结构设计:模具零件结构设计包括了导向装置、顶出机构、流道设计等。
导向装置用于确保模具在工作过程中的稳定性和精度;顶出机构用于将成品从模具中顶出;流道设计则是指导产品流动的通道,确保产品能够充分填充模具腔体。
2. 加热系统设计:加热系统设计是热压模具设计的另一重要方面,它包括了加热方式选择、加热元件设计以及温度控制等。
(1)加热方式选择:常见的加热方式有电加热、气加热和液体加热等。
根据具体的加热要求和加热介质选择适合的加热方式。
(2)加热元件设计:加热元件设计包括加热管的选取和布置等。
加热管要能够提供足够的热量,使原材料能够达到所需的成型温度。
(3)温度控制:温度控制是热压模具的重要环节,关系到产品的质量和生产效率。
利用温度传感器和温度控制仪表等设备,及时监测和调节原材料的温度,确保成品的质量。
应用:热压模具广泛应用于各个行业,以下是几个典型的应用领域:1. 塑料制品:热压模具在塑料制品的生产中有着广泛的应用,例如塑料容器、塑料盒子、塑料餐具等。
- 1、下载文档前请自行甄别文档内容的完整性,平台不提供额外的编辑、内容补充、找答案等附加服务。
- 2、"仅部分预览"的文档,不可在线预览部分如存在完整性等问题,可反馈申请退款(可完整预览的文档不适用该条件!)。
- 3、如文档侵犯您的权益,请联系客服反馈,我们会尽快为您处理(人工客服工作时间:9:00-18:30)。
模具結構(塑模)功能解說:1.定位環:將模具正確的定位在射出機板上,同時使模具堅澆道對准射出機的噴嘴。
2.注口襯套:塑膠進入模具內部的通道。
3.上固定板:使母模部分可以固定在成型機上。
4.母模板:在模具的固定側。
5.母模仁:為便于塑件成型而鑲配于母模板內的模仁。
6.定位塊上:裝在母模板上,以利用母模板與公模板定位裝置,與定位塊下配合使用。
7.拔塊:拔動滑塊退位及強制壓迫滑面裝置。
8.壓板:組成滑塊槽的裝置。
9.導柱:公母模板導向及定位裝置。
10.滑塊:為處理成品之倒勾而設立的滑動裝置。
11.成品:母模仁與公模仁合模而產生的塑件。
12.回定銷:用于頂出板定位之用。
13.定位塊下:裝在公模板上,以利于母模板與公模板定位裝置,與定位塊上配合使用。
14.斜槽:使成品形成倒勾,易脫離。
15.模腳:用來控制頂針與斜銷的行程。
16.下固定板:使公模部分可以固定在成型機上。
17.公模仁:為便于塑件成型的鑲配于公模板內的模仁。
18.公模板:模具的可動側,通常設計成使產品容易頂出。
19.上頂出板:對頂什及堅澆道控制起回位作用。
20.下頂出板:對頂針及澆道拉料起定位作用。
21.支撐柱:位于承板之后,作為補強承板,防止變形用。
塑模成型<<模具結構原理及維修保養簡介 >>講義一、模具結松:1. 定位環:架模時使模具引料接頭與機台噴嘴對正之工具。
2. 機器噴嘴與模具主流道相連接之零件。
3. 母模板:承載母模心之板塊。
4. 母模輔助板:輔助母模心之板塊。
5. 導柱:與母模配合定位之零件。
6. 導套:與公模導朮相配,使公母模對正之零件。
7. 公模板:承載公模心之板塊。
8. 公模輔助板:輔助公模固定公模心之板塊。
9. 公模支承板:支承公模板與底板,使兩者之間有空間讓頂出板活 動。
10. 公模底板:使公模固在機台上,與公模形成整體之板塊。
11. 頂針:使產品脫模之零件。
12. 公母模心:成形面之零件。
13. 頂出定位鎖:項出析后移動歸位銷。
14. 彈簧:使頂出板或模板復位。
15. 頂出板:分上下頂出板、固定頂針、受力時推動頂針前進。
定位環母模輔助板母模公模模心公模輔助板 上頂出板 下頂出板 公模支承板 公模底板二、 模具分類:1. 按結松分類:1.1. 三板模:由公模、母模及脫料板三部分組成。
—1« * --4 、• r ZL «-引料接頭 導柱 導套 頂針1.2.兩板模:由公模、母模兩部分組成。
2.按產品系列分類(以本公司成型模具為例),目前生產之模具有十大系列:2.1.ZIF :BASE、COVE 、R CAM.2.2.R/A SLOT1 :COVER.SBC.Housing.2.3.R/M :DAUL Housing DAUL Pin FILE INE Bridge FOLDABLEBASE ARMA ARMB FASTECK AASLOCK CELERON W/PIN RETERTIONMOOULE R/M PIN.2.4.SLOT1:2.5.FSS :STANDOFF A/B SUPPORT A/B2.6.HSS :BASE TOPBAR2.7.SOJ :2.8.BTB:1.0 、0.8、0.635、0.62.9.CARD BUS:2.10.PCMCIA :三、模具組立:維修與保養1.模具組立:(以兩板模為例)1.1.新模組立前備齊模具組立圖,檢驗每件模具零件是否齊全,尺寸、外觀是否符合要求。
1.2.清理桌面,模具零件,按件號擺放整齊,歸類。
1.3.將倒角,去毛刺模仁加工全符合要求,配好下模仁,從模心開始組配。
注意配合間隙,導柱導套組立入公模模板中。
14塞水孔,注意螺絲長短適度,緊固力度控制:3mn螺絲扭力2kg ,4mn螺絲扭力4kg ,5mn螺絲扭力8kg ,6mn螺絲扭力10kg1.5.公模板與公模輔助板組立,注意O形環裝妥,螺絲緊固16將模心定位于公模板內,緊好砌塊,螺絲緊固,公模平放桌面,成品面向下。
1.7.裝頂出板彈簧、定位鎖,將上頂出板置于公模上,緊固限位螺絲。
1.8.插入頂什,注意頂針倒角、修配,在頂針孔內滑動自如。
1.9.蓋上下頂出板,注意墊圈位置,緊固螺絲,導套放放置。
1.10.檢查頂出板頂出狀況,蓋上公模底板,支承板、緊固螺絲、裝進出水管接頭,檢查通水狀況。
1.11.組立母模與公模配合,注意模面是否有間隙,組立完畢。
1.12.試模、樣品與藍圖對照。
2•模具維修:2.1.修模前確認產品不良部位,不良部位模仁件號。
2.2.確定修模方式,換新件或換舊件加工,換新軟件需確認備品。
2.3.下模具主修模區,用天車將模具吊至桌面。
2.4.分開公母模,在不良部位用色筆作上記號。
2.5.模仁拆卸,取出損壞模仁,確定是否能回收使用。
2.6.領用新件,將倒角拋光部分加工到位。
2.7.模仁組立,注意配合狀況,對照產品或組立圖,有無裝錯。
2.8.模具組立,裝模心、裝頂針、頂出板、底板注意其方向。
2.9.檢查模面,再次確認有無裝錯模仁、頂針。
2.10.確認修模后,產品是否0K,填寫模修記錄。
3•模具保養:3.1.周期性保養:模具連續生產,達到保養周期時定期下模清理, 除去油污、料屑,更換磨損模仁零件,上油、拋光,清理排氣孔,作細部清理后上機生產,確認保養效果。
3.2.生產量到周期:模具生產量到后確認有無到達保養周期,已到保養周期則作周期性保養;未到則作上回前模具保養,作模面防鏽,除鏽,項出部分之潤滑,防鏽,循環水路清理,模具外表防鏽處理后上架待產。
3.3. 填寫保養記錄現代塑模成型塑料有兩種,主要的加工方法:注射成型及墊壓。
其總重量的大約32%是用注射成型的,368是用熱壓成型的。
一、塑件加工的主要作業:(三個)1.將塑料加熱到壓力下能夠流動時的溫度。
通常同時加熱并軟化固體顆粒,直到成為高溫而又具有均勻溫度和粘度的熔體為止。
目前,這個過程是在裝有往復式螺杆的注塑機的料筒里進行的。
螺杆提供了材料加熱攪拌所要求的機械作用。
這個全過程稱作材料的塑化(增塑)。
2.使塑料在由注射機保持其閉合的模具中固化。
從注塑機的注射缸里射出的熔化的塑料液體,通過各種流道送入模具的型腔中,最終在模腔的限制下形成所需的工件。
由于驅動射料杆的液壓回限制及模具內充填和冷卻作用的復雜流程,使這一看來簡單的作業變得復雜了。
3.對熱性塑料,停止加熱(加熱是使料熔化),使塑件固化,保壓冷卻定形成為所需的制品后,開啟模具取出塑件。
二、注塑成形系統的基本元件是:1. 混合器2. 干燥器3. 料斗4. 計量儀5. 塑化器6. 注射器7. 冷卻器8. 頂出裝置注塑機注塑機:是將粉未,粒料成回用原材料轉化,處理并成為所需形狀的機器。
注塑過程是加熱塑料材料為主,其熔化,然后迫使該熔體注入模具中,并在模具中冷卻和固化。
一、合模系統朮語:1.合模系統朮語:注塑機的一部份,在該部位固定模具并提打開和閉合模具的運作和力,以及在注射期間保持模具閉合的力。
當模具在水平方向閉合時,合模機構就秒作垂直鎖模。
這個裝置也可提供塑模塑作業中,必需的其他有效功能。
2.動模板或模板:即向定分移動的模機構的一部分。
用螺栓磁針動模固定在動模板上。
通常,動模上帶有頂杜孔和安裝模具的螺栓孔或” T”型槽。
3.定模板或模板:用螺栓將是模固定位的鎖模裝置的固定部分。
定模板通常帶有安裝模具的螺栓孔或” T”型槽。
此外,是模板通包括有將模具在模板上定武鋼和使的注道襯套與注射機構的注料嘴對准的設施。
4.拉杆、條佚、梁:當模具閉合時,這些合模機構中的受拉零件推動驅動機構。
安們也用作動模板的導向零件。
5.頂杆:在鎖模裝置中,驅動模具中一個機構頂出模塑件的構件。
頂出作用力可由一個或功敗垂成個固定在動模板上的由液壓或氣體動的缸體提供,或由動模板的開模行程機械提供。
6.合液壓式鎖模裝置:由直接連接到動模板上的液壓缸驅動的鎖緊裝置。
液壓通常直接用手打開或關閉模具,并提供鎖模力,以保持模具在注塑期間的閉合。
7.肘杆或鎖模裝置(液壓驅動、機械驅動):帶有直接連接動模板上肘杆機構的鎖模裝置。
一個液壓缸或某個機構驅勸裝置連接到肘杆系統中,以發出開模和閉模力,并保持注射期間的合模力。
在注射期間保持模具閉合的鎖模力是由肘杆的機械效益提供的。
8•慢速開模:注射機中一個裝置,是為模具初始打開期間使模板慢速移動一段可調整的距離而設計的。
9•慢速閉模:注射機中一個裝置,是為兩個模面接觸之前,在可調距離內慢速移動模板而設計的。
10.慢速敞開:注射楓葉的一個裝置,是為鎖模裝置到達其最大開啟位置之前,慢速移動一段可調整的距離而設計的。
這個程序經常用于在機械頂出條件下減小沖擊作用,它有時作頂出或開模緩沖。
11.合模行程間斷:閉模行程完全停止,以允許閉模行程完成之前的輔助作業。
12.開模行程間斷:合模打開行程完全停止,以允許啟模行程完成之前的輔助作業。
13.合模前置閉合:機器電路中的一個元件,以允計合模完全打開,然合閉合至預定位置。
常用于使頂杆機構退回,以便能夠將鑲件放入模具中。
14.低壓閉模:機器中的一個裝置,降低合模周期中的合模力。
較低的合模力使模面之間因零件卡住所引起的模具損壞的危險達到最小。
當模具有障礙物時,該元件也保証分模處的間隔。
二、注射系統朮語:1.注射塑化裝置:注射機的一個部件,該部件將固態的塑料原料通過加熱轉化成均勻的液態。
該裝置使材料保持設定的溫度,并迫使材料通過注射裝置的注嘴流入模具。
2.射料杆部件:注射和塑化裝置的組合,在該部件中,加熱筒固定在射料杆和模具之間,該筒用熱傳遞加熱塑料。
在每一次進程中,射料杆將未熔化的塑料原料推入筒中,這繼而又迫使機筒前端的熔融塑料通過注嘴。
3.雙級射料機構:注射和塑化裝置,在該裝置的一個獨立機構中完成塑化。
后者是由機筒組成提,以通過熱偉導加熱塑料原料,并用射料杆推動未熔化塑料進入要筒,再進入第二級注射裝置。
該注射裝置具有保壓、計量和注射機筒的綜合作用。
在注射周期中,射料杆迫使塑料熔體從注身中通過注嘴射出。
4.雙料螺杆部件:注射和塑化裝置:注射和塑化裝置,在該裝置的一個獨立機構中完成塑化,該獨立機構是由螺杆擠出器件組成的,以便材料塑化并迫使其進入第二級注射裝置。
該注射裝置其有保壓、計量和注射機筒的綜合作用。
在注射周期中,射料杆迫使塑料熔體從注射機筒通過注嘴流出。
5.往復式螺杆:注射和塑化裝置的組合,該裝置中帶有往復式螺杆的擠出器件,常常用于塑化材料。
材料注射到模具中可以直接擠入模睦的方式,或用往復式螺杆徐為射料杆或兩者結。
當螺杆成為射料杆時,該裝置具有保壓、計量和注射機筒的作用。
6.可調注射速度:在最大和最小注射速率間無級控制調整,注射速率的能力。
7.預裝:預裝也稱為”填允”,是萬事俱備助射料杆的多次行程,通過預裝置或允填額處的材料到加熱筒,用于增加注射杆每次輸出容量的方法(僅適用于注射杆裝置類型的注射機)。