生产过程防止污染交叉污染混淆和差错的管理规程
22防止生产中污染和混淆管理规程

编号:SMP-SC-00-022-00 页数:1/6文件名称防止生产中污染和混淆治理规程编制者审核者批准者编制日期审核日期批准日期编制依据《药品生产质量治理标准》98 版印数 2 份颁发部门办公室颁发日期年分发部门生产部、质量保证部实施日期月日目的:为了防止生产过程中的污染和混淆,确保药品产品质量。
范围:适用于生产过程中的治理。
职责:分发部门负责实施本规程。
内容:1.定义1.1污染:污染是指原材料或成品被微生物或外来物质所污染。
依据污染的状况一般分为三个方面,一是微生物引起的污染;二是由原料或产品被生产中另外的物料或产品混入引起的污染,如生产设备中的残留物,操作人员的服装引入,散发的尘埃、气体、雾状物等;三是除前述两种污染以外,由其它物质或异物等对药品造成污染。
1.2混淆:混淆指一种或一种以上的其它原料或成品与已标明品名等的原辅料或成品相混,通俗的说法,称为“混药”。
如原辅料与原辅料、成品与成品、标签与标签、有标志的与未标志的、已灭菌与未灭菌的混淆等。
2.造成污染和混淆的缘由2.1产生污染的缘由主要有以下各方面:2.1.1原辅料:购进的原辅料本身质量不好,或在运输、贮存、检验取样、配料过程中造成污染。
原辅料微生物指标超限。
2.1.2内包装材料:用于生产的直接接触药品的内包装材料在使用前消毒〔灭菌〕不彻底或消毒〔灭菌〕后存放条件不符合标准,或放置时间过长等造成污染。
2.1.3设备容器:外表不光滑、平坦,材质不稳定,不易清洁,选型与生产不配套,修理、保养不准时;清洁效果不能保证微生物出去水平及残留限度,清洁剂残留、消毒剂效果不能保证;生产完毕后不准时清洁清场等造成污染。
2.1.4灭菌设备、除菌设备未能到达无菌保证水品。
没有按操作要求操作、设备选型不合理,没有定期验证或没有保持验证状态。
2.1.5环境影响:生产环境如空气中生物粒子过多,车间地面、墙壁、天花板等不平坦、易脱落、长霉、消毒不严格等造成污染。
药品生产质量管理规范
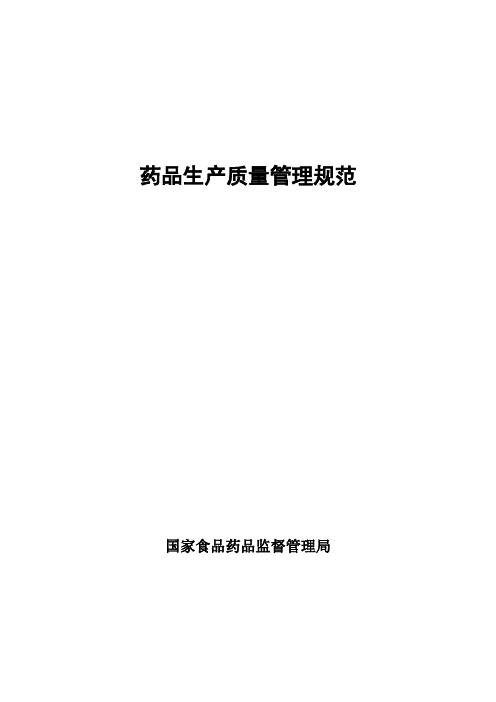
药品生产质量管理规范国家食品药品监督管理局电子版目录第一章总则1第二章质量管理1第三章机构与人员2第一节原则2第二节关键人员2第三节培训4第四节人员卫生4第四章厂房与设施5第一节原则5第二节生产区6第三节仓储区7第四节质量控制区7第五节辅助区8第五章设备8第一节原则8第二节设计和安装8第三节维护和维修8第四节使用、清洁及状态标识9第五节校准9第六节制药用水10第六章物料与产品10第一节原则10第二节原辅料11第三节中间产品与待包装产品12第四节包装材料12第五节成品13第六节特殊管理的物料和产品13第七节其它13第七章确认与验证14第八章文件管理15第一节原则15第二节质量标准16第三节工艺规程17第四节批生产记录18第五节批包装记录19第六节操作规程和记录19第九章生产管理20第一节原则20第二节防止生产过程中的污染和交叉污染21第三节生产操作22第四节包装操作22第十章质量控制与质量保证23第一节质量控制实验室管理23第二节物料和产品放行27第三节持续稳定性考察计划28第四节变更控制29第五节偏差处理29第六节纠正和预防措施30第七节供应商的审计和批准30第八节产品质量回顾分析31第九节投诉32第十一章委托生产与委托检验32第一节原则32第二节委托方33第三节受托方33第四节合同33第十二章产品发放与召回34第一节原则34第二节发放34第三节召回34第十三章药品不良反应34第十四章自检35第一节原则35第二节自检35第十五章术语35第一章总则第一条根据《中华人民共和国药品管理法》和《中华人民共和国药品管理法实施条例》的有关规定,制定本规范.第二条本规范是对药品生产质量进行控制和管理的基本要求,以确保持续稳定地生产出适用于预定用途、符合注册批准或规定要求和质量标准的药品,并最大限度减少药品生产过程中污染、交叉污染以及混淆、差错的风险.第三条药品生产质量管理的特殊要求,以附录的形式发布并根据情况随时修订.第四条企业可以采用经过验证的创新或改进的方法,达到不低于本规范的要求。
药物生产车间污染、交叉污染、混淆的防控解析

药品生产车间污染、交叉污染、混淆、差 错的控制
技术中心 2017、02、24
目录
一、概述 二、污染、交叉污染、混淆、差错的定义 三、GMP有关交叉污染控制的相关条款介绍 四、污染的种类及来源 1污染的种类 2污染的来源 五污染、交叉污染、混淆、差错预防措施
染
事因:操作人员将硫酸长春新碱尾液混于注射用甲氨蝶呤及盐酸阿糖胞 苷药品中,导致了多个批次的药品被硫酸长春新碱污染 后果:造成全国多地区总计130多位患者,受到严重的神经系统和行走 功能损害。
刺五加注射液事件
事因::2008年7月1日,昆明特大暴雨造成 库存的刺五加注射液被雨水浸泡,使药品受 到细菌污染。‚完达山药业‛云南销售人员张某 从公司调来包装标签,更换后继续销售。—
三、GMP有关交叉污染控制的相 关条款
第三十三条 参观人员和未经培训的人员不得进入生产区和质量控制区 ,特殊情况确需进入的,应当事先对个人卫生、更衣等事项进行指导。 第三十四条 任何进入生产区的人员均应当按照规定更衣。工作服 的选材、式样及穿戴方式应当与所从事的工作和空气洁净度级别要求相 适应。 第三十五条 进入洁净生产区的人员不得化妆和佩带饰物。 第三十六条 生产区、仓储区应当禁止吸烟和饮食,禁止存放食品 、饮料、香烟和个人用药品等非生产用物品。 第三十七条 操作人员应当避免裸手直接接触药品、与药品直接接 触的包装材料和设备表面。
检验,结果表明无菌检查和热原检查不符合规定。——
差
错 、污染、劣药
后果:全国16个省区共报告‚欣弗‛病例93例,死亡11人,涉 及药品9个批号。
生产过程防止污染交叉污染混淆和差错的管理规程

生产过程防止污染、交叉污染、混淆和差错旳管理规程目旳:建立防止污染、交叉污染、混淆和差错管理规程,规定了在药物生产活动过程中防止污染、交叉污染、混淆和差错管理内容和规定合用范围:合用于药物生产活动过程中防止污染、交叉污染、混淆和差错旳管理职责:生产技术部、质保部、车间对实行本规程负责内容:1.定义1.1污染:在生产、取样、包装或重新包装、贮存或运送等操作过程中,原辅料、中间产品、待包装产品、成品受到具有化学或微生物特性旳杂质或异物旳不利影响。
1.2 交叉污染:不一样原料、辅料及产品之间发生旳互相污染。
1.3混淆:在生产或包装旳过程中,误将一种或一批物料当成了另一种或另一批物料进行使用、操作。
1.4 差错:在生产过程中,由于计量器具未调试到位、或计量方式不对旳、或计数不精确而导致旳错误2. 产生污染、交叉污染、混淆和差错旳原因2.1 人员:操作人员患有传染病、皮肤病等,或未接受卫生方面旳培训,未按规定穿戴工作服,行为不规范、人员带来外部污染,生产人员未按工艺规程和SOP规定操作,工作责任心不强,工作量过大,操作中随意性大等。
2.2 设备:表面不光洁、平整,材质不稳定,不易清洁,设备选型不合理,维修、保养不及时,没有定期验证或没有保持验证状态。
生产中使用旳设备、容器无状态标志,清场不彻底等导致混淆。
2.3 物料:购进旳原辅料自身质量不好,或在运送、贮存、检查取样、配料过程中导致污染。
原辅料微生物指标超限。
原辅料、包装材料、半成品、中间体等无明显标志,放置混乱,散装或放在易破损旳包装中,印刷性包装材料管理不善等。
2.4 文献:文献管理制度不健全,或执行不力,无复核、监控,发现问题未及时查找原因等,尤其是配料、包装等重要部门管理不严格。
2.5 环境:厂房设计不合理,生产环境如空气中粒子过多,车间地面、墙壁、天花板等不平整、易脱落、长霉、消毒不严格等导致污染。
2.6 清洁:清洁效果不能保证微生物除去水平及残留程度,清洁剂残留、消毒剂效果不能保证;生产结束后不及时清洁清场等导致污染。
生产现场防止污染、差错和混淆管理规程
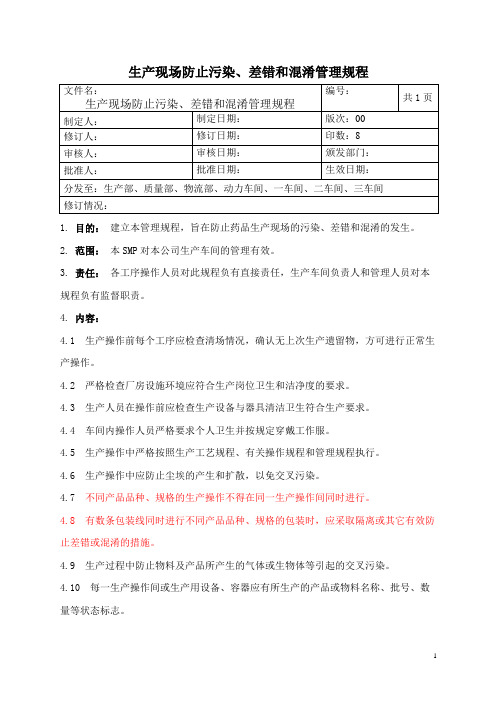
生产现场防止污染、差错和混淆管理规程
1. 目的:建立本管理规程,旨在防止药品生产现场的污染、差错和混淆的发生。
2. 范围:本SMP对本公司生产车间的管理有效。
3. 责任:各工序操作人员对此规程负有直接责任,生产车间负责人和管理人员对本规程负有监督职责。
4. 内容:
4.1 生产操作前每个工序应检查清场情况,确认无上次生产遗留物,方可进行正常生产操作。
4.2 严格检查厂房设施环境应符合生产岗位卫生和洁净度的要求。
4.3 生产人员在操作前应检查生产设备与器具清洁卫生符合生产要求。
4.4 车间内操作人员严格要求个人卫生并按规定穿戴工作服。
4.5 生产操作中严格按照生产工艺规程、有关操作规程和管理规程执行。
4.6 生产操作中应防止尘埃的产生和扩散,以免交叉污染。
4.7 不同产品品种、规格的生产操作不得在同一生产操作间同时进行。
4.8 有数条包装线同时进行不同产品品种、规格的包装时,应采取隔离或其它有效防止差错或混淆的措施。
4.9 生产过程中防止物料及产品所产生的气体或生物体等引起的交叉污染。
4.10 每一生产操作间或生产用设备、容器应有所生产的产品或物料名称、批号、数量等状态标志。
1。
H0024-05 防止药品污染和混淆的管理规定

防止药品污染和混淆的管理规定文件编码H0024-05目的:建立防止药品污染和混淆的管理规定,避免药品在生产过程中发生污染和混淆。
适用范围:适用于车间各工序产品的生产和转运。
职责:生产操作人员执行本规定,车间管理人员、质量保证部QA监督本规定的实施。
内容:1为了防止污染、交叉污染、混淆和差错,各生产工序应按GMP现场管理要求组织生产。
2防止药品污染和混淆的具体规程2.1物料分装及称量注意事项2.1.1在物料使用前应确认原辅料的最小包装容器上的标识,应包含物料的名称、规格、批号以及数量。
信息不完整的物料不允许使用。
2.1.2在分装或称量过程中,如有原辅料不慎洒落,操作人员需及时对洒落区域的设备及环境进行清洁操作并更换手套,必要时,需重新更换洁净服后方可继续进行分装或称量操作。
2.2每次生产结束后或转换品种、规格或转入下批产品生产前,应严格执行《车间清洁标准操作管理规定》(H0045-现行版),彻底清场并对作业场所进行仔细检查,确保设备和作业场所无与上批生产有关的物料、产品和文件。
2.3下次生产开始前,应当对前次清场进行确认。
2.4各工序的负责人检查合格后发给“清场合格证”。
未取得“清场合格证”,不得进行生产操作。
2.5当发现产品不符合质量标准、工序可接受标准等情况时,应当对不合格产品进行隔离,挂不合格标识并单独存放,同时向车间管理人员汇报。
3防止药品污染和混淆的控制点3.1不同产品或同一产品不同规格、不同批号的生产操作,不得在同一操作间同时进行。
3.2每一生产操作间或生产用设备、容器应有所生产产品或物料的名称、规格、批号、数量等状态标识,标识应清晰明了。
3.3有数条包装线同时进行包装时,应采取有效的区域隔离,防止污染、交叉污染或混淆的措施。
3.4生产所用的物料、中间产品,应按品名、规格、批号分开存放,并有明显标识,防止物料及产品交叉污染。
3.5生产中,应有防止尘埃产生和扩散的有效措施。
3.6严格执行《复核管理规定》(H0006-现行版),防止差错的产生。
生产管理的GMP要求

➢ 生产车间内工作人员在工作过程中动作要稳、轻、少, 尽量减少不必要的活动和交谈,以免造成过多的积尘、 产尘及空气污染。
第三十二条 企业应当采取适当措施,避免体表有伤 口、患有传染病或其他可能污染药品疾病的人员从事 直接接触药品的生产。
第八十五条 已清洁的生产设备应当在清洁、干燥 的条件下存放。
明确设备清洗后存放的环境条件,目的在于防止设 备清洁后被污染。
• 容器具存放环境是否干燥,减少微生物滋生;
第八十六条 用于药品生产或检验的设备和仪器,应 当有使用日志,记录内容包括使用、清洁、维护和维 修情况以及日期、时间、所生产及检验的药品名称、 规格和批号等。
➢ 人体是药品生产的最大污染源,良好的人员健康和卫 生保证是防止产品受到人为的污染的有效手段。
➢ 为降低人员对生产造成污染的风险,企业所有人员都 应接受卫生要求的培训,建立详细的人员卫生操作规 程,进行定期的健康体检,养成良好的卫生习惯。
第三十条 人员卫生操作规程应当包括与健康、卫生 习惯及人员着装相关的内容。生产区和质量控制区的 人员应当正确理解相关的人员卫生操作规程。企业应 当采取措施确保人员卫生操作规程的执行。
产出来的,而不是检验出来的;
应最大限度地控制工艺的每一步骤,以便最终产 品符合全部质量要求及涉及的规格标准。
* 实施GMP的意义
➢最大限度地保证人民用药安全,维护广大人民群众 的切身利益。
➢是大势所趋,是向传统的经验管理提出了挑战,向 规范化、科学化、制度化管理迈进。
➢是药品质量保证的承诺,目的是为了使制药企业建 立有效运作的质量体系,一切行为按GMP法规办事。
药物生产车间污染、交叉污染、混淆的防控
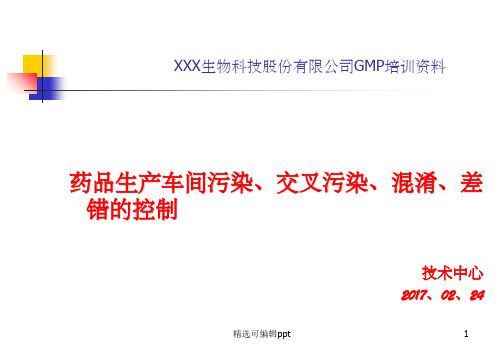
从原辅料来料检查一直到产品使用前的整过时间段的任何环节、产品( 物料)以任何状态存在的情况下都可能出现污染问题;
污染包括化学特性物质污染、微生物污染及异物(物理特性)污染;
污染的结果是对产品质量造成不利影响,由此给企业造成损失;
污染是指对某一种物质或一批次产品造成的影响,结果可能造成劣药、 甚至假药
************* 混淆是发生至少涉及两种/批及两种/批以上物料、产品; 混淆造成的后果可能是污染,甚至产生劣药、假药;
精选可编辑ppt
13
差错
主要是指错误或意外的变化。质量事故中人 为差错占15%左右;产生的原因主要是:
*************** 差错是错误,不等同于误差; 产生差错的因素主要有计量器具调试、计量方式、计数等计量方面;也
精选可编辑ppt
24
三、GMP有关交叉污染控制的相关条款
《生产管理》主要内容
•生产管理的原则(第184~196条,共13条) •防止生产过程中的污染和交叉污染(第197~198条,共2条) •生产操作(第199~201条,共3条) •包装操作(第202~216条,共15条)
•GMP附录一:无菌药品共15章81条 •GMP附录二:原料药共11章49条
第一节 原 则
第七十一条 设备的设计、选型、安装、改造和维护必须符合预定用途,应当尽可能降 低产生污染、交叉污染、混淆和差错的风险,便于操作、清洁、维护,以及必要时进行 的消毒或灭菌。
第二节 设计和安装
第七十四条 生产设备不得对药品质量产生任何不利影响。与药品直接接触的生产
设备表面应当平整、光洁、易清洗或消毒、耐腐蚀,不得与药品发生化学反应、吸附药
第六章物料与产品共有原则、原辅料、中间 产品和待包装产品、包装材料、成品、特殊 管理的物料和产品、其它计七节36条从原辅 料购进、接收、储运、分发等方面强调降低 污染、交叉污染的风险
027防止污染和交叉污染管理规程

Q/JGR 集安广润中药饮片有限公司企业管理标准SMP-SC-027-01 防止污染和交叉污染管理规程2020-06-15 发布 2020-07-15 实施集安广润中药饮片有限公司发布防止污染及交叉污染管理规程1 目的建立防止污染及交叉污染管理规程,防止因控制或人为操作不当造成污染及交叉污染。
2 范围生产车间3 责任生产部责任:制定本规程并监督实施质量管理部责任:进行监督和确认设备管理部责任:保证生产用设备、设施满足药品质量要求生产车间责任:执行本规程4 内容4.1 防止人员污染和交叉污染4.1.1 所有人员都应当接受卫生要求的培训,人员操作严格执行《人员卫生管理规程》,最大限度地降低人员对药品生产造成污染的风险。
4.1.2 各级管理人员严格监控,防止体表有伤口、患有传染病或其他可能污染药品疾病的人员从事直接接触药品的生产。
患有污染药品疾病的人员必须积极主动地配合主管部门的工作。
4.2 防尘措施4.2.1 生产中对产尘操作区域安装防护罩。
4.2.2 员工操作时对于易产尘的物料要轻拿轻放,避免产生粉尘。
4.3 防止厂房设施的污染和交叉污染4.3.1 厂房的选址、设计、布局、建造、改造和维护必须符合药品工艺流程,应当能够最大限度的避免污染、交叉污染、混淆和差错,便于清洁、操作和维护。
厂房地理位置需要控制的原则性要求,进行风险防范,避免受周围环境的影响,远离污染源。
4.3.2 厂区的地面、路面及运输等不应对药品生产造成污染;生产、行政、生活和辅助区总体布局要合理,不得互相妨碍;厂区和厂房内的人、物流走向应当合理。
厂房的设施和安装能够有效的防止昆虫或其它动物进入。
应当采取措施,避免所用的灭鼠药、杀虫剂等对设备、物料、产品造成污染。
严格执行各仓库的管理标准,仓库、车间做好防虫、防鼠工作,有防止昆虫动物进入,并装有捕蚊、虫的设施。
4.3.3 药品生产厂房不得用于生产对药品质量有不利影响的非药品产品。
4.3.4 称量间、外清间,应当保持清洁,防止粉尘扩散、避免交叉污染。
药品生产监督操作规程
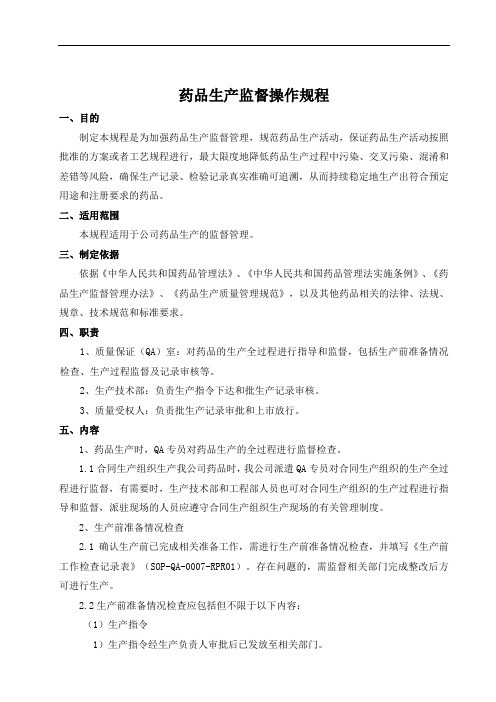
药品生产监督操作规程一、目的制定本规程是为加强药品生产监督管理,规范药品生产活动,保证药品生产活动按照批准的方案或者工艺规程进行,最大限度地降低药品生产过程中污染、交叉污染、混淆和差错等风险,确保生产记录、检验记录真实准确可追溯,从而持续稳定地生产出符合预定用途和注册要求的药品。
二、适用范围本规程适用于公司药品生产的监督管理。
三、制定依据依据《中华人民共和国药品管理法》、《中华人民共和国药品管理法实施条例》、《药品生产监督管理办法》、《药品生产质量管理规范》,以及其他药品相关的法律、法规、规章、技术规范和标准要求。
四、职责1、质量保证(QA)室:对药品的生产全过程进行指导和监督,包括生产前准备情况检查、生产过程监督及记录审核等。
2、生产技术部:负责生产指令下达和批生产记录审核。
3、质量受权人:负责批生产记录审批和上市放行。
五、内容1、药品生产时,QA专员对药品生产的全过程进行监督检查。
1.1合同生产组织生产我公司药品时,我公司派遣QA专员对合同生产组织的生产全过程进行监督,有需要时,生产技术部和工程部人员也可对合同生产组织的生产过程进行指导和监督,派驻现场的人员应遵守合同生产组织生产现场的有关管理制度。
2、生产前准备情况检查2.1确认生产前已完成相关准备工作,需进行生产前准备情况检查,并填写《生产前工作检查记录表》(SOP-QA-0007-RPR01)。
存在问题的,需监督相关部门完成整改后方可进行生产。
2.2生产前准备情况检查应包括但不限于以下内容:(1)生产指令1)生产指令经生产负责人审批后已发放至相关部门。
2)委托生产时,合同生产组织的生产指令应与公司生产技术部下达的生产指令内容一致。
(2)记录发放,受控发放现行版批生产记录、批包装记录和批检验记录。
(3)原辅料、包装材料的检验与放行,生产前原辅料和包装材料完成检验,检验记录完整且填写规范,检验结果符合质量标准并已放行,若有偏差,偏差已调查并关闭。
GMP药品生产质量管理规范(2010年修订)
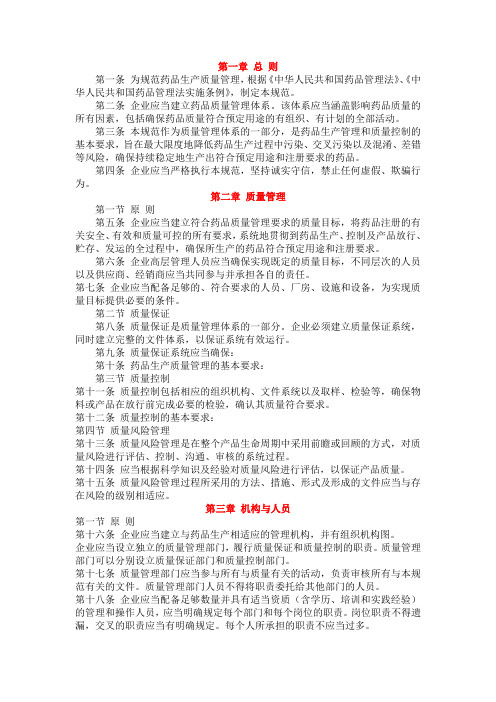
第一章总则第一条为规范药品生产质量管理,根据《中华人民共和国药品管理法》、《中华人民共和国药品管理法实施条例》,制定本规范。
第二条企业应当建立药品质量管理体系。
该体系应当涵盖影响药品质量的所有因素,包括确保药品质量符合预定用途的有组织、有计划的全部活动。
第三条本规范作为质量管理体系的一部分,是药品生产管理和质量控制的基本要求,旨在最大限度地降低药品生产过程中污染、交叉污染以及混淆、差错等风险,确保持续稳定地生产出符合预定用途和注册要求的药品。
第四条企业应当严格执行本规范,坚持诚实守信,禁止任何虚假、欺骗行为。
第二章质量管理第一节原则第五条企业应当建立符合药品质量管理要求的质量目标,将药品注册的有关安全、有效和质量可控的所有要求,系统地贯彻到药品生产、控制及产品放行、贮存、发运的全过程中,确保所生产的药品符合预定用途和注册要求。
第六条企业高层管理人员应当确保实现既定的质量目标,不同层次的人员以及供应商、经销商应当共同参与并承担各自的责任。
第七条企业应当配备足够的、符合要求的人员、厂房、设施和设备,为实现质量目标提供必要的条件。
第二节质量保证第八条质量保证是质量管理体系的一部分。
企业必须建立质量保证系统,同时建立完整的文件体系,以保证系统有效运行。
第九条质量保证系统应当确保:第十条药品生产质量管理的基本要求:第三节质量控制第十一条质量控制包括相应的组织机构、文件系统以及取样、检验等,确保物料或产品在放行前完成必要的检验,确认其质量符合要求。
第十二条质量控制的基本要求:第四节质量风险管理第十三条质量风险管理是在整个产品生命周期中采用前瞻或回顾的方式,对质量风险进行评估、控制、沟通、审核的系统过程。
第十四条应当根据科学知识及经验对质量风险进行评估,以保证产品质量。
第十五条质量风险管理过程所采用的方法、措施、形式及形成的文件应当与存在风险的级别相适应。
第三章机构与人员第一节原则第十六条企业应当建立与药品生产相适应的管理机构,并有组织机构图。
共线生产防止污染和交叉污染管理规程
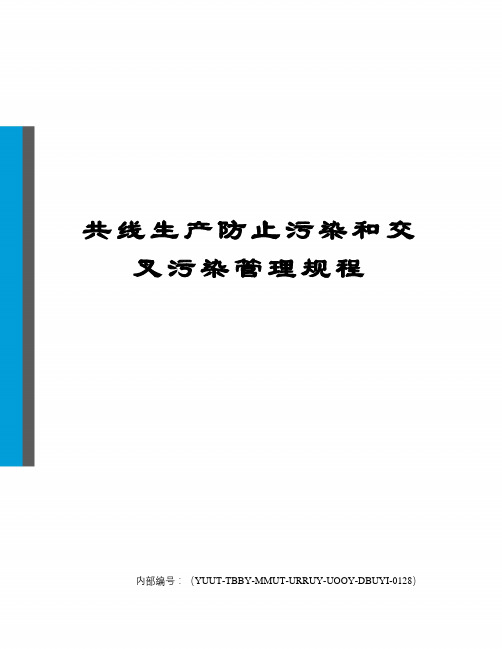
共线生产防止污染和交叉污染管理规程内部编号:(YUUT-TBBY-MMUT-URRUY-UOOY-DBUYI-0128)一、目的Purpose:建立防止交叉污染的管理规程,规范有效控制措施避免对产品造成污染。
二、适用范围 Scope:产品防护对人员、厂房设施及设备、物料、工艺设计的要求及控制措施。
三、职责Responsibility:1. QA对本文件的起草和修订负责;2. 生产管理负责人和质量管理负责人对本文件的批准负责;3. 车间、质量保证科、设备科等对此文件的实施负责。
四、程序Produce:1. 人员:1.1 须健康体检合格并经必要的卫生知识培训,养成良好的卫生习惯。
1.2 进入洁净区人员所穿着的工作服样式及材质应考虑污染和健康、安全问题,确保人员不污染药品,药品不污染人员。
1.3 进入生产区人员须严格遵守行为规范。
1.3.1 进入洁净区按《人员进出生产区的更衣更鞋程序》规定进行操作。
1.3.2 生产区不得存放个人物品,严禁吃食物。
1.3.3 生产区禁止吸烟。
1.3.4 进出洁净区随时关门,动作尽量缓慢,减少人的发尘量。
1.3.5 进入操作室应先检查温湿度、压差等是否符合规定。
1.3.6 避免裸手直接接触药品和设备容器内表面。
1.3.7 禁止直接面对药品打喷嚏或咳嗽。
1.3.8 禁止不同工序、不同品种生产操作室之间操作人员随意走动,如有需要须采取防止交叉污染措施,如按照规定流程更换干净的工作服等。
1.3.9 凡清场合格的房间,门应常闭,无关人员不得随意进入。
清场后不需立即生产的,应上锁管理。
2. 厂房设施:2.1 物流、人流、按工艺流程合理布局,严格划分洁净区域。
2.2 空气流向需按照以下原则确定:由洁净区域流向非洁净区域;由前室或走道流向产生粉尘、湿气的房间。
2.3 洁净区与非洁净区之间、不同等级洁净区之间的压差应≥10Pa,相同洁净等级区域内在生产过程中有粉尘产生的区域保持相对负压和一定的梯度,以防止污染和交叉污染。
生产过程中防止污染和交叉污染管理规程

生产过程中防止污染和穿插污染治理规程文件标题:生产过程中防止污染和交义污染治理规程文件编号SMP-PM-Oxx 版本号Ox 文件级别 2 级制订人年月日制订部门生产技术部审核人年月日颁发部门GMP 办公室审核人年月日批准人年月日生效日期年月日分发至质量治理部、生产技术部、工程设备部、各车间1.目的:建立防止污染和交义污染措施的治理规程,最大限度地降低生产过程中的污染和交义污染,避开混淆和过失。
2.范围:适用于公司生产过程中防止污染和交义污染的治理。
3•职责:车间治理人员对规程的实施负责,QA 监视规程的实施。
4.规程:4. 1 定义4. 1. 1 污染:在生产、取样、包装或重包装、贮存或运输等操作过程中,原辅料、中间产品、待包装产品、成品受到具有化学或微生物特性的杂质或异物的不利影响。
4.1. 2 穿插污染:不同原料、辅料及产品之间发生的相互污染。
4.2生产过程中应当尽可能实行措施,防止污染和交义污染4. 2. 1 在分割的区域内生产不同品种的药品;4.2.2 承受阶段性生产方式;4. 2. 3 设置必要的气锁间和排风;空气干净级别不同的区域应当有压差掌握;4. 2. 4 应当降低未经处理或未经充分处理的空气再次进入生产区导致污染的风险;4. 2. 5 在产生穿插污染的生产区内,操作人员应当穿戴该区域专用的防护服;4.2.6承受经过验证或有效的清洁和去污染的操作规程进展设备清洁;必要时,应当对与物料直接接触的设备外表的残留物进展检测;4.2.7承受密闭系统生产;4. 2. 8 枯燥设备的进风应当有空气过滤器,排风应当有防止空气倒流装置;4.2.9 生产和清洁过程中应当避开使用易碎、易脱屑、易发霉器具;应当有防止筛网断裂而造成污染的措施;4. 2. 10 液体制剂的配制、过滤、灌封、灭菌等工序应当在规定的时间内完成。
4.3厂房、设施、设备防止污染和交义污染的措施:4. 3.1 空调净化系统承受的措施:4. 3. 1. 1初效、中效过滤器的阻力到达设定值(设定值为初始阻力的1.5 倍)报警:阻力小于设定值,绿灯亮;阻力大于设定值时,红灯亮,需对过滤器进展清洗或更换。
防止生产过程污染与交叉污染的管理规程

防止生产过程污染和交叉污染的管理规程1目的:建立防止生产过程污染和交叉污染的管理规程,最大限度地降低药品生产过程中污染、交叉污染的风险。
2范围:适用于防止生产区、化验区与仓贮区在生产过程污染和交叉污染的管理。
3职责:生产区、化验区与仓贮区人员负责实施,QA检查员及各部门负责人负责监督执行。
4内容4.1定义4.1.1污染:在生产、取样、包装或重新包装、贮存或运输等操作过程中,原辅料、中间产品、待包装产品、成品受到具有化学或微生物特性的杂质或异物的不利影响。
4.1.2 交叉污染:不同原料、辅料及产品之间发生的相互污染。
4.2防止人员污染和交叉污染:4.2.1所有人员都应当接受卫生要求的培训,人员操作严格执行《人员卫生操作规程》,最大限度地降低人员对药品生产造成污染的风险。
4.2.2 各级管理人员严格监控防止体表有伤口、患有传染病或其他可能污染药品疾病的人员从事直接接触药品的生产。
可能患有污染药品疾病的人员必须积极主动地配合主管部门的管理要求。
4.2.3控制进入洁净区的人和物的数量。
执行《参观人员进出生产区的管理规程》。
4.2.4进入洁净区的人和物严格执行《人员进出洁净区的净化程序》和《物料、容器、工具进出洁净区的净化程序》。
4.2.5进入洁净区的操作人员不得随意离开自己的工作区域(需对岗位培训)而进入其它操作间,确需进入时,应再次执行《人员进出洁净区净化程序》后方可进入。
4.2.6 工作人员在需要进出公共区时,不能同时进出,防止交叉污染。
4.3 防尘措施:生产中对洁净区产尘操作区域进行控制,采取以下方法防止粉尘扩散、避免交叉污染的,并在此基础上不断改进防止尘埃产生和扩散的有效措施。
4.3.1工艺过程产生粉尘的工序的操作应在负压称量室进行,负压称量室设置独立的除尘系统。
4.3.2洁净室密闭,不使外界未经净化的空气进入洁净厂房,必须定期检查送风口、灯罩、安全门等是否有泄漏点。
4.3.3洁净室的地面,墙壁和顶棚等要保持无尘、光滑、无静电,并能经得起清洁、消毒,一旦发生涂层脱落应及时修补。
- 1、下载文档前请自行甄别文档内容的完整性,平台不提供额外的编辑、内容补充、找答案等附加服务。
- 2、"仅部分预览"的文档,不可在线预览部分如存在完整性等问题,可反馈申请退款(可完整预览的文档不适用该条件!)。
- 3、如文档侵犯您的权益,请联系客服反馈,我们会尽快为您处理(人工客服工作时间:9:00-18:30)。
生产过程防止污染、交叉污染、混淆和差错的管理规程目的:建立防止污染、交叉污染、混淆和差错管理规程,规定了在药品生产活动过程中防止污染、交叉污染、混淆和差错管理内容和要求适用范围:适用于药品生产活动过程中防止污染、交叉污染、混淆和差错的管理职责:生产技术部、质保部、车间对实施本规程负责内容:1.定义1.1污染:在生产、取样、包装或重新包装、贮存或运输等操作过程中,原辅料、中间产品、待包装产品、成品受到具有化学或微生物特性的杂质或异物的不利影响。
1.2 交叉污染:不同原料、辅料及产品之间发生的相互污染。
1.3混淆:在生产或包装的过程中,误将一种或一批物料当成了另一种或另一批物料进行使用、操作。
1.4 差错:在生产过程中,因为计量器具未调试到位、或计量方式不正确、或计数不准确而造成的错误2. 产生污染、交叉污染、混淆和差错的原因2.1 人员:操作人员患有传染病、皮肤病等,或未接受卫生方面的培训,未按要求穿戴工作服,行为不规范、人员带来外部污染,生产人员未按工艺规程和SOP 要求操作,工作责任心不强,工作量过大,操作中随意性大等。
2.2 设备:表面不光洁、平整,材质不稳定,不易清洁,设备选型不合理,维修、保养不及时,没有定期验证或没有保持验证状态。
生产中使用的设备、容器无状态标志,清场不彻底等造成混淆。
2.3 物料:购进的原辅料本身质量不好,或在运输、贮存、检验取样、配料过程中造成污染。
原辅料微生物指标超限。
原辅料、包装材料、半成品、中间体等无明显标志,放置混乱,散装或放在易破损的包装中,印刷性包装材料管理不善等。
2.4 文件:文件管理制度不健全,或执行不力,无复核、监控,发现问题未及时查找原因等,特别是配料、包装等重要部门管理不严格。
2.5 环境:厂房设计不合理,生产环境如空气中粒子过多,车间地面、墙壁、天花板等不平整、易脱落、长霉、消毒不严格等造成污染。
2.6 清洁:清洁效果不能保证微生物除去水平及残留限度,清洁剂残留、消毒剂效果不能保证;生产结束后不及时清洁清场等造成污染。
..2.7 生产过程:生产过程控制不规范,生产中敞口生产,密闭不严,管道中有死角,生产周期过长,操作不当等。
3. 防止污染、交叉污染、混淆和差错的措施生产过程中产生污染、交叉污染、混淆和差错的可能随时存在,必须在全过程各个环节都加强管理和监控。
除了对生产中人员、设备、物料、文件、环境、清洁等引起污染、交叉污染、混淆和差错的因素进行控制外,还要采取相应的措施。
3.1 人员3.1.1 所有人员都应接受卫生方面的培训后上岗,熟练掌握生产区域人员更衣、卫生操作,最大限度地降低人员对药品生产造成污染的风险。
3.1.2 当对人员健康进行管理,并建立健康档案。
直接接触药品的生产人员上岗前应当接受健康检查,以后每年至少进行一次健康检查。
3.1.3 禁止体表有伤口、患有传染病或其他可能污染药品疾病的人员从事直接接触药品的生产。
3.1.4 选用洁净服材质符合要求,洁净服穿戴符合规范。
3.1.5员工按操作规程办事,按规定如实填写记录、遇事及时汇报上级等,最大程度地防止发生混药混批。
3.1.6 外来人员必须经过批准并在指定人员的陪同及指导下方可进入车间。
3.1.7 任何私人药品均不得带入车间。
3.2 设备、环境3.2.1 厂房的选址、设计、布局、建造、改造和维护必须符合药品生产要求,应当能够最大限度地避免污染、交叉污染、混淆和差错,便于清洁、操作和维护。
3.2.2 应当根据厂房及生产防护措施综合考虑选址,厂房所处的环境应当能够最大限度地降低物料或产品遭受污染的风险。
3.2.3应当有整洁的生产环境;厂区的地面、路面及运输等不应当对药品的生产造成污染;生产、行政、生活和辅助区的总体布局应当合理,不得互相妨碍;厂区和厂房内的人、物流走向应当合理。
3.2.4 厂房、设施的设计和安装应当能够有效防止昆虫或其它动物进入。
应当采取必要的措施,避免所使用的灭鼠药、杀虫剂、烟熏剂等对设备、物料、产品造成污染。
3.2.5 为降低污染和交叉污染的风险,厂房、生产设施和设备应当根据所生产药品的特性、工艺流程及相应洁净度级别要求合理设计、布局和使用,并符合下列要求:.2.(一)应当综合考虑药品的特性、工艺和预定用途等因素,确定厂房、生产设施和设备多产品共用的可行性,并有相应评估报告;(二)生产特殊性质的药品,如高致敏性药品(如青霉素类)或生物制品(如卡介苗或其他用活性微生物制备而成的药品),必须采用专用和独立的厂房、生产设施和设备。
青霉素类药品产尘量大的操作区域应当保持相对负压,排至室外的废气应当经过净化处理并符合要求,排风口应当远离其他空气净化系统的进风口;(三)生产β-内酰胺结构类药品、性激素类避孕药品必须使用专用设施(如独立的空气净化系统)和设备,并与其他药品生产区严格分开;(四)用于上述第(二)、(三)项的空气净化系统,其排风应当经过净化处理;(五)药品生产厂房不得用于生产对药品质量有不利影响的非药用产品。
3.2.6 生产区和贮存区应当有足够的空间,确保有序地存放设备、物料、中间产品、待包装产品和成品,避免不同产品或物料的混淆、交叉污染,避免生产或质量控制操作发生遗漏或差错。
3.2.7 制剂的原辅料称量通常应当在专门设计的称量室内进行。
产尘操作间(如干燥物料或产品的取样、称量、混合、包装等操作间)应当保持相对负压或采取专门的措施,防止粉尘扩散、避免交叉污染并便于清洁。
3.2.8 用于药品包装的厂房或区域应当合理设计和布局,以避免混淆或交叉污染。
如同一区域内有数条包装线,应当有隔离措施。
3.2.9 通常应当有单独的物料取样区。
取样区的空气洁净度级别应当与生产要求一致。
如在其他区域或采用其他方式取样,应当能够防止污染或交叉污染。
3.2.10 实验室的设计应当确保其适用于预定的用途,并能够避免混淆和交叉污染,应当有足够的区域用于样品处置、留样和稳定性考察样品的存放以及记录的保存。
3.2.11 设备所用的润滑剂、冷却剂等不得对药品或容器造成污染,应当尽可能使用食用级或级别相当的润滑剂。
应当选择适当的清洗剂清洁设备,并防止这类设备成为污染源。
3.2.12 生产设备应易于清洁。
设备中应尽量避免出现凹槽等难清洁部位。
使用结束后必须将产品及包装材料从设备上清理出去,并按规定程序进行清洁、清洗、灭菌。
3.3 物料3.3.1应当建立物料和产品的操作规程,确保物料和产品的正确接收、贮存、发放、使用和发运,防止污染、交叉污染、混淆和差错。
3.3.2 制剂所用的原辅料要控制微生物限度,以有效地减少微生物造成的污染。
.3.3.3.3固体制剂中间产品要规定贮存期和贮存条件。
3.3.4 要有明确的物料状态标志,防止物料的混淆。
3.3.5 生产操作应当能够防止中间产品或原辅料被其它物料污染。
3.4 清洁3.4.1 生产设备清洁的操作规程应当规定具体而完整的清洁方法、清洁用设备或工具、清洁剂的名称和配制方法、去除前一批次标识的方法、保护已清洁设备在使用前免受污染的方法、已清洁设备最长的保存时限、使用前检查设备清洁状况的方法,使操作者能以可重现的、有效的方式对各类设备进行清洁。
3.4.2 清洁方法应当经过验证,证实其清洁的效果,以有效防止污染和交叉污染。
清洁验证应当综合考虑设备使用情况、所使用的清洁剂和消毒剂、取样方法和位置以及相应的取样回收率、残留物的性质和限度、残留物检验方法的灵敏度等因素。
3.4.3 应当按照操作规程对纯化水管道进行清洗消毒,并有相关记录。
发现制药用水微生物污染达到警戒限度、纠偏限度时应当按照操作规程处理。
3.4.4 严格控制清洁(消毒)的物品的存放要求以及存放时间,超过规定时间要再次清洁(消毒)。
3.5 生产过程3.5.1 不得在同一生产操作间同时进行不同品种和规格药品的生产操作,除非没有发生混淆或交叉污染的可能。
3.5.2 在生产的每一阶段,应当保护产品和物料免受微生物和其他污染。
3.5.3 生产过程中应当尽可能采取措施,防止污染和交叉污染,如:(一)在分隔的区域内生产不同品种的药品;(二)采用阶段性生产方式;(三)设置必要的气锁间和排风;空气洁净度级别不同的区域应当有压差控制;(四)应当降低未经处理或未经充分处理的空气再次进入生产区导致污染的风险;(五)在易产生交叉污染的生产区内,操作人员应当穿戴该区域专用的防护服;(六)采用经过验证或已知有效的清洁和去污染操作规程进行设备清洁;必要时,应当对与物料直接接触的设备表面的残留物进行检测;(七)采用密闭系统生产;(八)干燥设备的进风应当有空气过滤器,排风应当有防止空气倒流装置;(九)生产和清洁过程中应当避免使用易碎、易脱屑、易发霉器具;使用筛网时,应当.4.有防止因筛网断裂而造成污染的措施;3.5.4 包装操作规程应当规定降低污染和交叉污染、混淆或差错风险的措施。
有数条包装线同时进行包装时,应当采取隔离或其他有效防止污染、交叉污染或混淆的措施。
3.5.5 样品从包装生产线取走后不应当再返还,以防止产品混淆或污染。
3.5.6 生产前要认真检查、核对生产指令、物料,确认生产环境无上批生产的遗留物,确认设备、容器等“已清洁”,生产结束后已经做好清洁、清场工作。
3.5.7 生产过程中必须按工艺要求及控制要点进行中间检查,填写生产记录和检查记录,并归入批生产记录中。
3.5.8 应制定取样操作规程,有防止取样过程中污染和交叉污染的注意事项,降低取样过程产生的各种风险。
3.6 明确状态标志3.6.1生产状态标志必须标明正在生产的情况,内容包括正在生产的品名、规格、批号等。
3.6.2 生产设备状态标志必须标明设备名称、设备性能状况、负责人等,停运的设备标明其性能状况,清洁状态、待修或维修,对已损坏报废的设施,必须从生产线上搬出。
3.6.3 容器状态标志必须标明容器的情况,如内容物品名、规格、批号、状态等。
3.6.4卫生状态标志必须标明房间、设备、容器等卫生状况,如已清洁、已消毒、已清场等。
3.7 洁净区控制3.7.1各项操作在规定的符合标准的洁净区内进行,洁净区设立气锁间对空气系统进行有效隔离,产尘部位设立排风除尘装置;空气洁净度级别不同的区域应当有压差控制;保证不同级别压差要求,洁净区与非洁净区之间、不同洁净区之间压差不低于10Pa;必要时相同洁净区的不同功能区之间也要保持一定得压差。
生产过程中防止粉尘飞扬,有粉尘的岗位要安装捕尘设施。
3.7.2 净化空调系统3.7.2.1 对洁净空调系统进行确认,确保净化空调系统达到设计标准。
必须保证洁净级别的悬浮粒子和微生物不超过标准,对其进行监控。
3.7.2.2 定期检查净化系统的密封性、高效过滤器的完整性,降低未经处理或未经充分处理的空气再次进入生产区导致污染的风险;3.7.2.3 切实作好净化空调系统的维护,根据环境检测数据和规定更换初效,中效及高效.5.过滤器。