关键工艺参数确认的
烘箱验证关键质量控制工艺参数

烘箱验证关键质量控制工艺参数烘箱验证关键质量控制工艺参数1. 引言在制药、食品加工和其他行业中,烘箱是一个重要的设备,用于将原料或产品通过加热达到所需的温度。
为了保证产品的质量和一致性,烘箱的验证成为关键的质量控制过程之一。
烘箱验证包括对各项重要参数的测试和确认,以确保设备能够按照要求正常工作。
本文将重点讨论烘箱验证中的关键质量控制工艺参数。
2. 烘箱验证的目的和意义烘箱验证是为了确保烘箱能够按照规定的条件进行工作,确保产品的质量和安全性。
通过验证关键质量控制工艺参数,可以评估烘箱在不同温度、湿度和时间条件下的稳定性和可靠性。
这有助于预防可能的生产过程问题,减少质量问题的发生。
3. 关键质量控制工艺参数3.1 温度控制在烘箱验证中,温度控制是一个至关重要的参数。
温度对产品质量和达到所需品质的时间具有直接影响。
温度控制的稳定性和精度是验证的关键目标。
为了实现温度的精确控制,烘箱应配备高质量的温度传感器和控制系统。
3.2 时间控制时间控制也是烘箱验证的关键参数之一。
产品在烘烤过程中需要经历一定时间才能达到所需的效果。
验证烘箱的时间控制的目的是确定烘烤时间与产品质量之间的关系,并确保在规定的时间范围内能够达到一致的结果。
3.3 湿度控制湿度是另一个重要的烘箱验证参数。
不同的产品或材料对湿度的要求有所不同。
湿度控制的稳定性对产品的质量和效果也具有重要影响。
在烘箱验证中,湿度控制的准确性和稳定性需要得到重视。
3.4 空气流动除了温度、时间和湿度之外,烘箱内的空气流动也是一个需要验证的关键参数。
在烘箱验证过程中,应检查烘箱内部的风扇工作情况,确保空气能够均匀地流动到所有产品或样本的表面。
这有助于确保产品在烘烤过程中的一致性和质量。
4. 烘箱验证的实施步骤4.1 确定验证的目标和范围烘箱验证之前,首先需要明确验证的目标和范围。
明确验证的目标有助于在验证过程中进行重点关注,确保验证的准确性和全面性。
4.2 确定验证方法和步骤根据验证的目标和范围,制定验证的方法和步骤。
关键工艺参数的定义指南
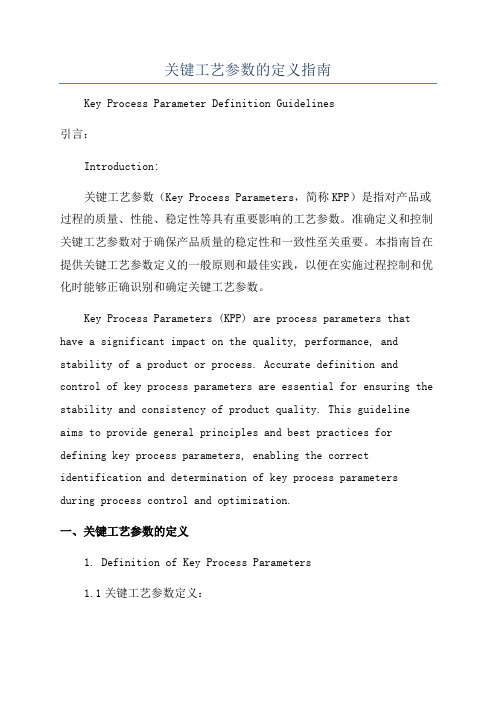
关键工艺参数的定义指南Key Process Parameter Definition Guidelines引言:Introduction:关键工艺参数(Key Process Parameters,简称KPP)是指对产品或过程的质量、性能、稳定性等具有重要影响的工艺参数。
准确定义和控制关键工艺参数对于确保产品质量的稳定性和一致性至关重要。
本指南旨在提供关键工艺参数定义的一般原则和最佳实践,以便在实施过程控制和优化时能够正确识别和确定关键工艺参数。
Key Process Parameters (KPP) are process parameters that have a significant impact on the quality, performance, and stability of a product or process. Accurate definition and control of key process parameters are essential for ensuring the stability and consistency of product quality. This guideline aims to provide general principles and best practices for defining key process parameters, enabling the correct identification and determination of key process parameters during process control and optimization.一、关键工艺参数的定义1. Definition of Key Process Parameters1.1关键工艺参数定义:-关键工艺参数是指直接或间接影响产品质量、性能和稳定性的工艺参数。
关键工艺参数确认的
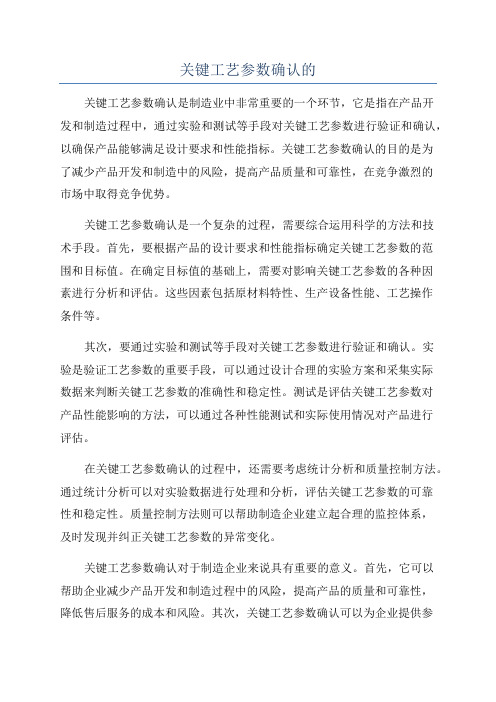
关键工艺参数确认的关键工艺参数确认是制造业中非常重要的一个环节,它是指在产品开发和制造过程中,通过实验和测试等手段对关键工艺参数进行验证和确认,以确保产品能够满足设计要求和性能指标。
关键工艺参数确认的目的是为了减少产品开发和制造中的风险,提高产品质量和可靠性,在竞争激烈的市场中取得竞争优势。
关键工艺参数确认是一个复杂的过程,需要综合运用科学的方法和技术手段。
首先,要根据产品的设计要求和性能指标确定关键工艺参数的范围和目标值。
在确定目标值的基础上,需要对影响关键工艺参数的各种因素进行分析和评估。
这些因素包括原材料特性、生产设备性能、工艺操作条件等。
其次,要通过实验和测试等手段对关键工艺参数进行验证和确认。
实验是验证工艺参数的重要手段,可以通过设计合理的实验方案和采集实际数据来判断关键工艺参数的准确性和稳定性。
测试是评估关键工艺参数对产品性能影响的方法,可以通过各种性能测试和实际使用情况对产品进行评估。
在关键工艺参数确认的过程中,还需要考虑统计分析和质量控制方法。
通过统计分析可以对实验数据进行处理和分析,评估关键工艺参数的可靠性和稳定性。
质量控制方法则可以帮助制造企业建立起合理的监控体系,及时发现并纠正关键工艺参数的异常变化。
关键工艺参数确认对于制造企业来说具有重要的意义。
首先,它可以帮助企业减少产品开发和制造过程中的风险,提高产品的质量和可靠性,降低售后服务的成本和风险。
其次,关键工艺参数确认可以为企业提供参考和依据,帮助企业优化生产工艺和提高产品竞争力。
最后,关键工艺参数确认还可以促进企业的技术创新和发展,为企业带来更多的商业机会和利益。
总之,关键工艺参数确认是制造业中不可或缺的一个环节,它具有重要的意义和价值。
通过科学的实验和测试手段,可以验证和确认关键工艺参数,确保产品的质量和性能指标能够得到满足。
同时,关键工艺参数确认还能够帮助企业降低风险,提高产品竞争力,促进企业的创新和发展。
企业在进行关键工艺参数确认时,需要充分考虑各种因素和方法,并建立起合理的监控体系和质量控制方法,以确保关键工艺参数的准确性和稳定性。
关键质量属性和关键工艺参数
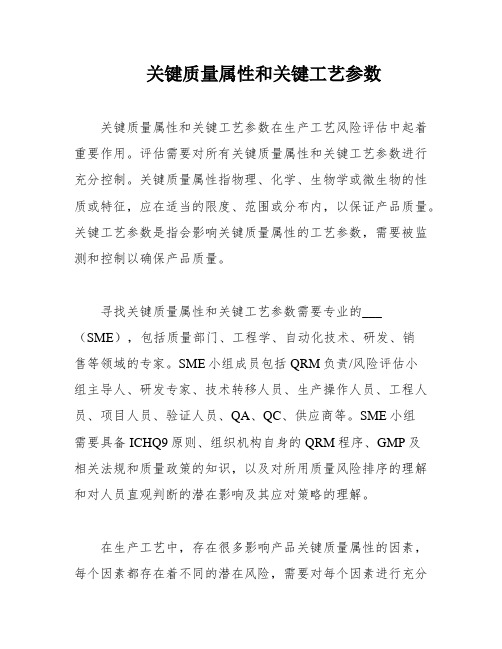
关键质量属性和关键工艺参数关键质量属性和关键工艺参数在生产工艺风险评估中起着重要作用。
评估需要对所有关键质量属性和关键工艺参数进行充分控制。
关键质量属性指物理、化学、生物学或微生物的性质或特征,应在适当的限度、范围或分布内,以保证产品质量。
关键工艺参数是指会影响关键质量属性的工艺参数,需要被监测和控制以确保产品质量。
寻找关键质量属性和关键工艺参数需要专业的___(SME),包括质量部门、工程学、自动化技术、研发、销售等领域的专家。
SME小组成员包括QRM负责/风险评估小组主导人、研发专家、技术转移人员、生产操作人员、工程人员、项目人员、验证人员、QA、QC、供应商等。
SME小组需要具备ICHQ9原则、组织机构自身的QRM程序、GMP及相关法规和质量政策的知识,以及对所用质量风险排序的理解和对人员直观判断的潜在影响及其应对策略的理解。
在生产工艺中,存在很多影响产品关键质量属性的因素,每个因素都存在着不同的潜在风险,需要对每个因素进行充分的识别分析和评估,以反映工艺的重要性质。
评估小组应该列出将要被评估的工序步骤,通过工艺流程图、SOP或批生产记录来提供这些信息。
关键质量属性判定矩阵可以用来评估不同属性的重要性和关键性,包括鉴别、物化性质、含量、微生物纯度等。
同时,需要使用ICHQ6A决策树来测试晶型和粒度等属性。
自控系统信息了解在质量管理中,CQA(关键质量属性)和CPP(关键生产过程)是非常重要的概念。
要找到CQA和CPP,可以采用以下方法:1.使用ICHQ8(R2)-QbD-系统化的方法和ICHQ9-质量风险管理流程图进行风险评估。
2.使用CQA&CPP风险评估工具-___。
对于___的实施,可以按照以下步骤进行:1.成立一个评估小组。
2.识别已知和潜在的失效模式。
3.识别严重性、可能性和可检测性。
4.详细说明行为。
5.重新评级。
6.详细说明剩余的风险。
7.完成一个简短的摘要。
在进行风险评估时,需要列出将要被评估的工序步骤。
工艺验证和关键工艺参数工艺规程和主批生产记录关键物料供应

记录关键物料供应
2020/11/12
工艺验证和关键工艺参数工艺规程和 主批生产记录关键物料供应
北京市药品质量受权人培训内容
质量管理决定权的行使-工艺验证和 1 关键工艺参数的批准
质量管理决定权的行使-工艺规程 2 和主批生产记录的批准
质量管理否决权的行使-关键物料 3 供应商的审计
• 药品生产过程的验证内容必须包括: –空气净化系统 –工艺用水系统 –生产工艺及其变更 –设备清洗 –主要原辅材料变更 –无菌药品生产过程的验证内容还应增加: 灭菌设备 药液滤过及灌封(分装)系统
工艺验证和关键工艺参数工艺规程和 主批生产记录关键物料供应
1.法规要求-GMP(200909征求意见稿)
工艺验证和关键工艺参数工艺规程和 主批生产记录关键物料供应
1. 法规要求-GMP(200909征求意见稿)
第七章 确认与验证
152条 采用新的生产处方或生产工艺前,应 验证其对常规生产的适用性。生产工艺 在使用规定的原辅料和设备条件下,应 能始终生产出符合预定的用途、符合药 品注册批准或规定的要求和质量标准的 产品。
• 第五十七条
药品生产验证应包括厂房、设施及设备安
装确认、运行确认、性能确认和产品验证。
• 第五十八条
产品的生产工艺及关键设施、设备应按验
证方案进行验证。当影响产品质量的主要因素,如工艺、质
量控制方法、主要原辅料、主要生产设备等发生改变时,以
及生产一定周期后,应进行再验证。
• 第五十九条
应根据验证对象提出验证项目、制定验证
工艺验证和关键工艺参数工艺规程和 主批生产记录关键物料供应
1. 法规要求-GMP(200909征求意见稿)
关键设备工艺参数检查制度和记录

关键设备工艺参数检查制度和记录1. 你知道关键设备工艺参数检查有多重要吗?就好比汽车没了油还能跑吗!比如我们检查反应釜的温度参数,要是没检查好,那生产出来的东西不就全毁啦!所以一定要严格执行关键设备工艺参数检查制度,认真做好记录呀!2. 哎呀,想想如果不认真对待关键设备工艺参数检查制度会怎样?那不就像没头苍蝇乱撞嘛!像检查压缩机的压力参数时,一旦疏忽,那后果可不堪设想啊!必须要重视起来呀!3. 你说关键设备工艺参数检查制度能不严格遵守吗?这就如同建房子不打地基一样危险啊!就拿检查离心机的转速参数来说,不仔细检查记录,出了问题谁负责呀!4. 关键设备工艺参数检查制度可不是闹着玩的呀!这就好像战士上战场不带武器一样!比如检查烘干机的湿度参数,不严格执行,产品质量能有保障吗?5. 难道你还不明白关键设备工艺参数检查制度的意义吗?这简直就是保证一切顺利的法宝呀!像检查混合器的搅拌速度参数,不做好检查记录,那不是给自己找麻烦嘛!6. 你可别小看了关键设备工艺参数检查制度和记录呀!这好比是航海中的灯塔指引方向呢!比如检查蒸馏塔的温度梯度参数,不重视的话,那不是要出大乱子啦!7. 想想看,没有关键设备工艺参数检查制度会怎样?那简直是灾难呀!就像检查传输带的速度参数,不认真检查记录,生产能有序进行吗?8. 关键设备工艺参数检查制度和记录太重要啦!这就好像是人的心脏一样关键呀!像检查过滤器的压差参数,不仔细对待,那怎么行呢!9. 你真的清楚关键设备工艺参数检查制度的必要性吗?这就好像吃饭睡觉一样不可或缺呀!比如检查膨化机的压力参数,不好好检查记录,能放心吗?10. 关键设备工艺参数检查制度绝对不能马虎呀!这就和人的健康一样重要啊!像检查包装机的封口温度参数,不严格检查,产品不就都毁啦!总之,一定要认真执行关键设备工艺参数检查制度,仔细做好记录,这关乎着生产的成败呀!。
持续工艺确认报告

1.产品概述醋酸泼尼松片是固体制剂车间生产的口服片剂,其规格为5mg,包装规格为100片/瓶/盒×10盒/热缩×90热缩/纸箱;批准文号为国药准字H13020588;贮存条件为遮光,密封保存;有效期36个月。
醋酸泼尼松片为肾上腺皮质激素类药,主要用于过敏性与自身免疫性炎症性疾病。
适用于结缔组织病,系统性红斑狼疮,重症多肌炎,严重的支气管哮喘,皮肌炎,血管炎等过敏性疾病,急性白血病,恶性淋巴瘤。
2.生产工艺分析2.1.关键工艺参数的确认2.2.关键工艺参数数据统计趋势分析2.2.1.目的:对关键工艺参数进行持续的工艺确认。
2.2.2.程序:对关键工艺参数进行统计分析汇总结果,详见“附件1”关键工艺参数统计表。
对关键工序物料平衡及成品率进行统计汇总结果,详见“附件2”关键工艺参数统计表。
2.2.3.可接受标准:关键工艺参数单值符合设定的标准要求。
关键工序工艺参数稳定可控,工序能力满足要求。
2.2.4.结论:关键工艺参数单值均符合工艺规程和质量标准设定的标准要求,结论评定详见“附件1、附件2、附件3”。
3.关键工序的物料平衡及成品率统计分析如下3.1.制粒工序结果分析:本次统计的所有批次制粒工序物料平衡呈随机分布,最大值为99.46%,最小值为98.02%,单值均在工艺控制范围(97%~103%)内,说明该过程稳定可控能保证产品质量。
3.2.压片工序结果分析:本次统计的所有批次压片工序物料平衡呈随机分布,最大值为99.80%,最小值为99.70%,单值均在工艺控制范围(98%~100%)内,说明该过程稳定可控能保证产品质量。
3.3.成品率结果分析:本次统计的所有批次成品率呈随机分布,最大值为101.82%,最小值为97.05%,单值均在工艺控制范围(97%~103%)内,说明整个生产过程稳定可控能。
4.产品放行分析4.1.关键质量属性的确认物料名称关键质量属性标准4.2.关键质量属性据统计趋势分析4.2.1.目的:对关键质量属性进行持续的工艺确认。
关键工艺参数确认的

关键工艺参数确认的SOP1目的:定义关键工艺参数,建立关键工艺参数的选择和评估程序,加强对关键工艺参数的理解和识别,便于日常操作。
2范围:总公司及分子公司原料药线的中间体和原料药产品的生产。
所有GMP条件下生产的中间体和原料药必须对关键工艺参数进行确认。
3责任者:研发部、生产技术部、QC QR QA研发部、生产技术部-组织和领导对质量风险进行分析评估-起草确认方案和报告-具体实施确认工作-在确认工作结束后对工艺参数、关键工艺参数进行列表-对工艺耐受性进行分析提供支持-对生产提供支持-提供工艺确认中相关的文件-对工艺执行情况进行评估,并确保任何必要的、额外的工艺确认工作的实施生产部门-组织和领导工艺耐受性分析工作-对工艺耐受性分析进行文件记录-按照工艺规程中的工艺参数执行生产化验室-在工艺确认的过程中提供分析支持-对检测方法进行验证质量管理部-对质量风险分析提供支持-批准确认方案和报告-对工艺耐受性分析工作提供支持-审核和批准的工艺参数列表-对工艺规程中所列的工艺参数的正确实施进行审核-对工艺验证后工艺的实施情况进行评估(产品年度回顾)产品经理或项目负责人-根据产品的需求和客户要求,开始工艺确认工作-审核和批准的生产工艺参数列表-在产品的生命周期内,对进一步的确认工作的申请进行评估4程序名词解释基本原则及内容421在产品小试开发结束后,应初步确定关键工艺参数并将其列入开发报告中422关键工艺参数的确认应该包括:-确定可能影响API质量的工艺参数的关键属性-确定每个关键工艺参数的范围.先决条件4.3.1关键工艺参数应明确界定(最低限度的要求是在实验室条件下的定义),然后确认工作才可以开始4.3.2关键工艺参数的设置,应该经过技术人员组织相关人员组织讨论后,以书面的形式确认。
4.3.3确认关键工艺参数之前,成品的标准很分析方法要提前进行确认。
4.3.4起始原料、中间体和最后中间体应该已经确定。
4.3.5对整个反应过程用到的关键原料、中间体的来源已经确认。
关键工艺参数和重要工艺参数

关键工艺参数和重要工艺参数
关键工艺参数是指在制造过程中对最终产品质量具有决定性影响的工艺参数,是生产过程中必须严格控制的参数。
关键工艺参数的确定通常基于产品特性、制造要求和工艺原理等因素,是保证产品质量、生产效率和加工安全的重要基础。
重要工艺参数则是指对产品质量和生产过程有重要影响的工艺参数,这些参数可能不是直接决定产品质量的参数,但它们对产品的性能、尺寸、形状等有显著影响。
重要工艺参数的确定通常依据经验和工艺要求来确定,对产品质量的稳定性和生产过程的可靠性起着重要作用。
在生产过程中,关键工艺参数和重要工艺参数的确定通常需要经过反复试验和验证,以确保产品质量的稳定性和可靠性。
同时,这些参数的确定也是工艺设计、设备选型、生产计划等后续工作的基础。
因此,正确确定关键工艺参数和重要工艺参数是制造过程中至关重要的环节。
工艺流程中的关键控制参数研究
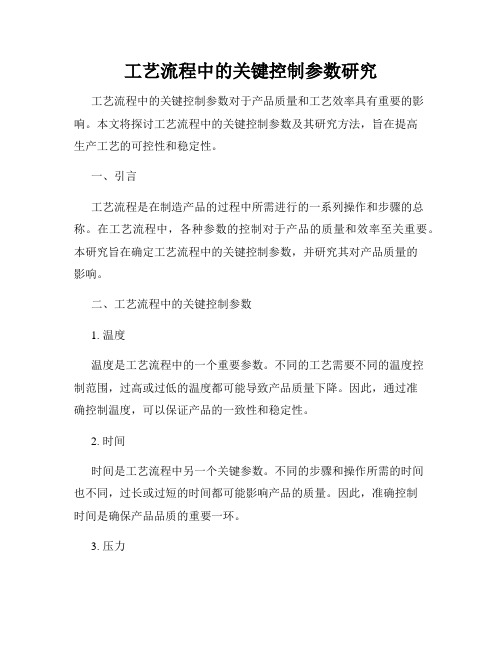
工艺流程中的关键控制参数研究工艺流程中的关键控制参数对于产品质量和工艺效率具有重要的影响。
本文将探讨工艺流程中的关键控制参数及其研究方法,旨在提高生产工艺的可控性和稳定性。
一、引言工艺流程是在制造产品的过程中所需进行的一系列操作和步骤的总称。
在工艺流程中,各种参数的控制对于产品的质量和效率至关重要。
本研究旨在确定工艺流程中的关键控制参数,并研究其对产品质量的影响。
二、工艺流程中的关键控制参数1. 温度温度是工艺流程中的一个重要参数。
不同的工艺需要不同的温度控制范围,过高或过低的温度都可能导致产品质量下降。
因此,通过准确控制温度,可以保证产品的一致性和稳定性。
2. 时间时间是工艺流程中另一个关键参数。
不同的步骤和操作所需的时间也不同,过长或过短的时间都可能影响产品的质量。
因此,准确控制时间是确保产品品质的重要一环。
3. 压力某些工艺流程需要对材料进行压力处理,例如挤压、压制等。
压力的大小直接影响产品的密度和质量。
因此,控制压力是确保产品稳定性和成型质量的关键。
4. 流速对于液体或气体在工艺流程中的流动速度进行控制也非常重要。
过高或过低的流速可能导致物料混合不均或反应不完全,直接影响产品的质量。
5. 浓度某些工艺需要精确控制溶液或混合物的浓度。
过高或过低的浓度都可能引发产品质量问题。
因此,确保浓度的准确控制是工艺流程中的关键控制参数之一。
三、关键控制参数研究方法1. 模拟实验通过建立合适的实验模型,在实验室环境下模拟工艺流程,并通过改变控制参数的数值,观察产品质量的变化。
通过实验数据的采集和统计分析,找出关键控制参数。
2. 规划实验设计使用合适的实验设计方法,如正交试验设计,确定有效的控制参数和响应变量。
通过对实验结果的统计分析,找出关键控制参数及其对产品质量的影响程度。
3. 数值模拟借助计算机仿真软件,建立工艺流程的数值模型。
通过改变关键控制参数的数值,观察产品质量的变化趋势。
通过数据分析,确定关键控制参数的取值范围。
关键工艺参数的定义指南

关键工艺参数的定义指南以下是关键工艺参数定义的指南:1.确定关键质量属性:首先,确定产品的关键质量属性。
这些属性是衡量产品质量的关键因素,例如尺寸、重量、颜色、含量等。
2.识别潜在影响因素:分析工艺过程中可能影响关键质量属性的因素。
这些因素可以是原料特性、设备设置、环境条件、操作员技能等。
3.选择关键工艺参数:从潜在的影响因素中选择关键工艺参数。
这些参数是那些对关键质量属性具有重要影响的因素。
例如,对于一个食品加工工艺,温度、时间和湿度可能是关键工艺参数。
4.确定工艺参数范围:确定每个关键工艺参数的可接受范围。
这些范围应保证产品在质量要求内,并且能够保持稳定的工艺过程。
例如,对于温度参数,确定一个最小和最大值。
5.确定工艺参数分析方法:确定用于分析关键工艺参数的方法。
这可以包括采用实验设计方法、统计分析等。
选择适当的方法可以帮助评估和优化关键工艺参数。
6.确定工艺参数控制方法:确定控制关键工艺参数的方法。
这可以包括设置警戒线、制定监控计划等。
控制方法的目标是确保工艺参数保持在可接受范围内,以保证产品质量。
7.建立监控和反馈机制:建立监控关键工艺参数的机制,以及相关的反馈机制。
这可以包括实时监测、记录和报告关键工艺参数,并对偏离目标值的情况进行相应的调整和改进。
8.进行验证和验证:对关键工艺参数进行验证和验证。
这可以通过实施实验和数据分析来实现。
验证和验证的目的是确认关键工艺参数的有效性和合适性。
9.建立持续改进机制:建立持续改进机制,以优化关键工艺参数。
这可以包括周期性地评估和调整工艺参数,以适应新的要求和技术进步。
总之,关键工艺参数的定义是一个系统的过程,需要综合考虑产品要求、潜在因素和合适的分析和控制方法。
通过对关键工艺参数的明确定义和有效控制,可以确保工艺过程的稳定性和产品质量的符合性。
Guide for Defining Key Process ParametersThe definition of key process parameters is important to ensure stability and control of the process. These parametersare key factors that affect product quality, process stability, and equipment performance, and should be evaluated and controlled.Here is a guide for defining key process parameters:1. Determine key quality attributes: Firstly, determine the key quality attributes of the product. These attributes are critical factors for assessing product quality, such as size, weight, color, content, etc.2. Identify potential influential factors: Analyze factors that may influence the key quality attributes during the process. These factors can be material characteristics, equipment settings, environmental conditions, operator skills, etc.4. Determine the range of process parameters: Define the acceptable range for each key process parameter. These ranges should ensure product quality within the requirements and maintain a stable process. For example, for a temperature parameter, determine a minimum and maximum value.5. Determine process parameter analysis methods: Determine the methods for analyzing key process parameters. This can include the use of experimental design methods, statistical analysis, etc. Choosing the appropriate method can help evaluate and optimize key process parameters.6. Determine process parameter control methods: Identify the methods to control the key process parameters. This can include setting control limits, establishing monitoring plans, etc. The aim of control methods is to ensure that process parameters remain within an acceptable range to ensure product quality.8. Perform validation and verification: Validate and verify the key process parameters. This can be done through conducting experiments and analyzing data. The purpose of validation and verification is to confirm the effectiveness and suitability of key process parameters.9. Establish continuous improvement mechanisms: Establish mechanisms for continuous improvement to optimize key process parameters. This can include periodic evaluation and adjustmentof process parameters to adapt to new requirements and technological advancements.In summary, defining key process parameters is a systematic process that requires considering product requirements,potential factors, and appropriate analysis and control methods. By clearly defining and effectively controlling key process parameters, process stability and product quality can be ensured.。
工艺验证和关键工艺参数的批准、工艺规程和主批生产记录的批准

执
• 对于回顾性验证,通常需要考虑10~30个连续生产 批的数据以评估工艺的一致性,但是,在可证明的 情形下,可以考察较少的批次
业
继 师 药
续
教
育
25 Presentation Title / Name / Date
前验证/同步验证
工艺验证需求
验证的一般步骤:
检查可用的现行主批记录和分析规程
检查设备的确认和校验
执
业
继 师 药 向杰
续
教
育
工艺验证和关键工艺参数的批准 工艺规程和主批生产记录的批准
山德士(中国)制药有限公司 北京 2009/06/29 a Novartis company
目录
• 工艺验证的重要性和受权人职责 • 工艺生命周期各阶段的验证 • 工艺设计 – DOE, PAR, PAT
执
业
继 师 药
工艺设计
定义产品
执
业
可接受 的范围
继 师 药
开发工艺
设计工艺
续
教
功能要求
育
初步的产 品规格标 准 工艺规格 标准
优化工艺
放大
商业化
13 Presentation Title / Name / Date
经过证实的可接受的范围
-PAR(Proven Acceptable Range)
最差条件--Worst Case:位于标准操作程序中的一组包括工艺上限和下限
执
业
继 师 药
续
教
育
连续三批验证批:工艺验证通常需要连续三批验证批。因该根据最终的批量 ,使用在认可的工艺参数范围内的目标值,在商业批使用的设备上生产。
19 Presentation Title / Name / Date
工艺参数确认范文
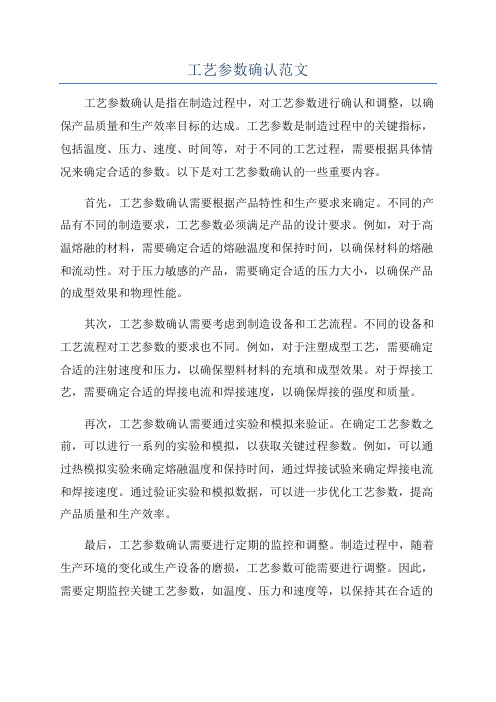
工艺参数确认范文工艺参数确认是指在制造过程中,对工艺参数进行确认和调整,以确保产品质量和生产效率目标的达成。
工艺参数是制造过程中的关键指标,包括温度、压力、速度、时间等,对于不同的工艺过程,需要根据具体情况来确定合适的参数。
以下是对工艺参数确认的一些重要内容。
首先,工艺参数确认需要根据产品特性和生产要求来确定。
不同的产品有不同的制造要求,工艺参数必须满足产品的设计要求。
例如,对于高温熔融的材料,需要确定合适的熔融温度和保持时间,以确保材料的熔融和流动性。
对于压力敏感的产品,需要确定合适的压力大小,以确保产品的成型效果和物理性能。
其次,工艺参数确认需要考虑到制造设备和工艺流程。
不同的设备和工艺流程对工艺参数的要求也不同。
例如,对于注塑成型工艺,需要确定合适的注射速度和压力,以确保塑料材料的充填和成型效果。
对于焊接工艺,需要确定合适的焊接电流和焊接速度,以确保焊接的强度和质量。
再次,工艺参数确认需要通过实验和模拟来验证。
在确定工艺参数之前,可以进行一系列的实验和模拟,以获取关键过程参数。
例如,可以通过热模拟实验来确定熔融温度和保持时间,通过焊接试验来确定焊接电流和焊接速度。
通过验证实验和模拟数据,可以进一步优化工艺参数,提高产品质量和生产效率。
最后,工艺参数确认需要进行定期的监控和调整。
制造过程中,随着生产环境的变化或生产设备的磨损,工艺参数可能需要进行调整。
因此,需要定期监控关键工艺参数,如温度、压力和速度等,以保持其在合适的范围内。
如果发现工艺参数超出了设定范围,需要及时调整,以避免对产品质量和生产效率的影响。
总之,工艺参数确认是制造过程中确保产品质量和生产效率的重要环节。
通过合理地确定和调整工艺参数,可以保证产品的设计要求得以满足,同时提高生产效率和降低制造成本。
因此,在制造过程中,工艺参数确认具有重要的意义,需要高度重视和细致操作。
工艺参数的目的及确定方法
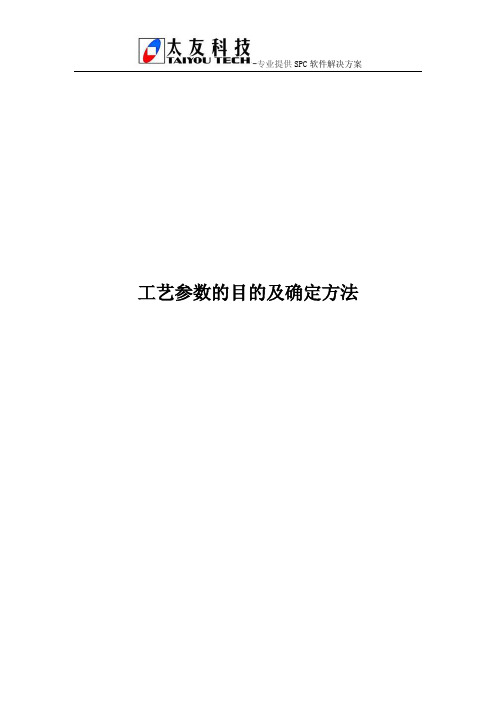
-专业提供 SPC 软件解决方案
工艺参数的目的及确定方法
-专业提供 SPC 软件解决方案
摘要:工艺参数是影响产品质量的核心因素,在生产加工过程中,工艺参数的确 认与选择是控制及稳定产品质量的根本解决方法。
工艺参数是指在完成某项工作的工艺的一系列基础数据或者指标,也就是说 这些基础参数构成了工艺操作或者设计的内容。
工艺参数的分类 温度 数量(重量、体积等) 压力 pH 搅拌速度 时间 其他 例子:焊接工艺参数主要有焊条直径、焊接电流、焊接层数、电源种类及极性等;
工艺参数确认的目的 识别可能影响 API 关键质量特性的工艺参数,识别关键和潜在关键工艺参数; 确定预期会在生产和工艺控制中用到的每一个关键工艺参数的参数范围; 工艺参数确认是工艺验证的一个很重要的部分;
工艺参数确认的流程
工艺参数确认

工艺参数的确认Process Parameter Qualification谢永2013-7-23工艺参数的确认工艺参数确认的背景和目的工艺参数确认的一般流程工艺参数确认的前提质量风险分析和工艺确认方案工艺参数确认质量风险再分析和工艺确认报告关键工艺参数的定义其他工艺参数的分类温度数量(重量,体积等)压力pH搅拌速度时间其他工艺参数范围的确定科学原理文献资料历史数据小试数据(对实验数据的统计学分析)来源于其他公司或客户的数据经验:工艺中偏差和OOS。
参数范围确认试验(正交试验,失败边际试验等)几个名词Design space 设计空间Hold-Point 工艺暂存点Edge of failure 失败边际CriticalDesign SpaceThe multidimensional combination and interaction of input variables (e.g. material attributes) and process parameters that have been demonstrated to provide assurance of quality. Working within the design space is not considered as a change. Movement out of the design space is considered to be a change and would normally initiate a regulatory post approval change process. Design space is proposed by the applicant and is subject to regulatory assessment and approval.Design SpaceICH Q8中的定义The design space is the established range of process parameters that has been demonstrated to provide assurance of quality. In some cases design space can also be applicable to formulation attributes. Working within the design space is not generally considered as a change of the approved ranges for process parameters and formulation attributes. Movement out of the design space is considered to be a change and would normally initiate a regulatory post approval change process.Hold-PointA point in the process for which sufficient stability data was collected to allow storage of the material for a certain length of time under defined conditions. For data collection purposes hold-points are treated as process parameters.Edge of failureThe boundary to a variable or parameter, beyond which the relevant quality attributes or specifications cannot be met.CriticalAny process step, process condition, test requirement, or other relevant parameter or item that must be controlled within predetermined and tight criteria to ensure that the API meets its specifications.工艺参数确认的背景ICH Q7 12.1112.11 The critical parameters/attributes should normally beidentified during the development stage or from historical data, and the ranges necessary for the reproducibleoperation should be defined. This should include:− Defining the API in terms of its critical product attributes; − Identifying process parameters that could affect the critical quality attributes of the API;− Determining the range for each critical process parameter expected to be used during routinemanufacturing and process control.工艺参数确认的背景ICH Q8It is important to recognize that quality cannot be tested into products; i.e., quality should be built in by design.质量是建立在设计基础上的而不是被检测出来的。
工艺参数验证方法

工艺参数验证方法以下是 7 条关于工艺参数验证方法的内容:1. 你知道用实际生产来验证工艺参数有多重要吗?就好比你要做一道超级美味的菜,不实际做一遍怎么知道味道好不好!比如咱们做面包,你得按照规定的温度、时间去烤,不然烤出来的面包不是硬邦邦就是没熟。
所以啊,直接在实际生产中尝试才能真正确认这些工艺参数是不是可靠。
2. 对比测试这种验证方法可真是个好办法呀!这不就像你挑衣服,要把两件放在一起比一比才知道哪件更好看。
像制造零件,用不同的参数设置做出来,看看哪个效果更棒,就知道哪个参数更合适啦!比如通过对比不同压力下零件的质量,那一下子就清楚压力这个参数该怎么调整啦。
3. 模拟验证可是个神奇的手段哦!可以想象成是给工艺参数来一场“彩排”。
比如说建房子,在电脑上先模拟各种施工情况,这不就相当于提前演练,能发现好多问题呢!然后根据模拟的结果去调整参数,等实际操作时不就更有把握嘛。
4. 统计分析也不容小觑呀!这就好像是你数星星,通过大量的观察和整理,发现规律。
比如说生产一批产品,对各种数据进行分析,哇,就能看出哪个工艺参数对质量的影响最大,然后就可以重点关注和改进它啦。
就像发现了宝藏的线索一样兴奋呢!5. 专家评估验证可是很厉害的哟!这不就像是有个超级懂行的老师来给你把关。
当遇到一些复杂的工艺参数时,专家的经验和判断那可太重要了。
比如说航天发射这种高科技的事儿,专家说这个参数行,那肯定没问题呀,真让人安心呐!6. 实验设计验证就像搭积木一样有趣呢!规划好每一个步骤和参数的组合。
比如做化学实验,设计不同的反应条件,看看会产生什么不同的结果。
这样精心设计的实验,能让我们对工艺参数有更深入、准确的了解,多有意思呀!7. 持续监测验证真的太关键啦!这就像是随时随地有人看着你。
在生产过程中一直盯着那些工艺参数,稍有风吹草动就赶紧发现啦。
就像你开车的时候一直注意着仪表盘,稍有异常就赶紧处理,可不能马虎呀!总之,这些工艺参数验证方法都各有各的好,咱们得根据实际情况灵活运用,才能保证工艺参数的准确性和可靠性呀!。
关键工艺验证方案
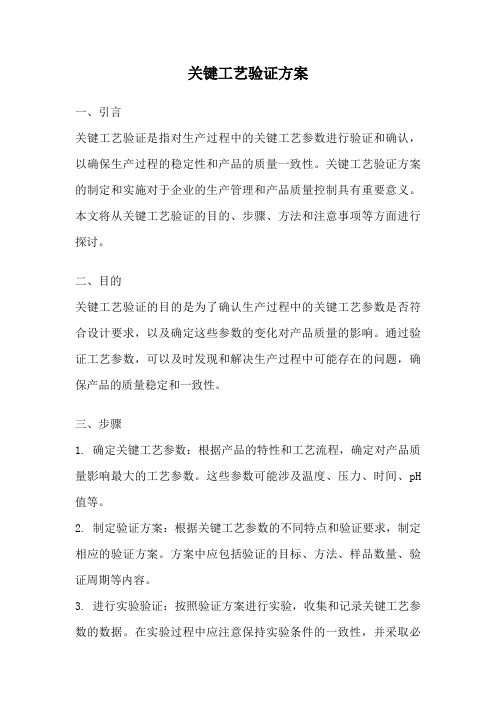
关键工艺验证方案一、引言关键工艺验证是指对生产过程中的关键工艺参数进行验证和确认,以确保生产过程的稳定性和产品的质量一致性。
关键工艺验证方案的制定和实施对于企业的生产管理和产品质量控制具有重要意义。
本文将从关键工艺验证的目的、步骤、方法和注意事项等方面进行探讨。
二、目的关键工艺验证的目的是为了确认生产过程中的关键工艺参数是否符合设计要求,以及确定这些参数的变化对产品质量的影响。
通过验证工艺参数,可以及时发现和解决生产过程中可能存在的问题,确保产品的质量稳定和一致性。
三、步骤1. 确定关键工艺参数:根据产品的特性和工艺流程,确定对产品质量影响最大的工艺参数。
这些参数可能涉及温度、压力、时间、pH 值等。
2. 制定验证方案:根据关键工艺参数的不同特点和验证要求,制定相应的验证方案。
方案中应包括验证的目标、方法、样品数量、验证周期等内容。
3. 进行实验验证:按照验证方案进行实验,收集和记录关键工艺参数的数据。
在实验过程中应注意保持实验条件的一致性,并采取必要的数据处理和分析方法。
4. 结果评估:根据实验数据和分析结果,评估关键工艺参数是否符合设计要求,并判断其对产品质量的影响程度。
如有需要,可以进行追踪实验和修改方案。
5. 结论和建议:根据验证结果,得出结论和建议,用于指导生产过程的优化和改进。
结论和建议应具体、可行,并能够解决实际生产中存在的问题。
四、方法1. 实验方法:根据验证的目标和要求,选择合适的实验方法。
常用的实验方法包括物理实验、化学实验、生物实验等。
在实验过程中应注意实验条件的控制和数据的准确性。
2. 数据分析方法:根据实验数据,采用统计学方法和数据分析软件对数据进行处理和分析。
常用的数据分析方法包括平均值、方差分析、回归分析等。
通过数据分析,可以得出关键工艺参数的变化规律和对产品质量的影响程度。
3. 比较分析法:将不同条件下的实验结果进行比较和分析,以确定关键工艺参数的最佳取值范围。
比较分析可以通过图表、数据对比等方式进行,有助于找出优化工艺参数的方向。
原料药关键工艺参数确定的基本思路
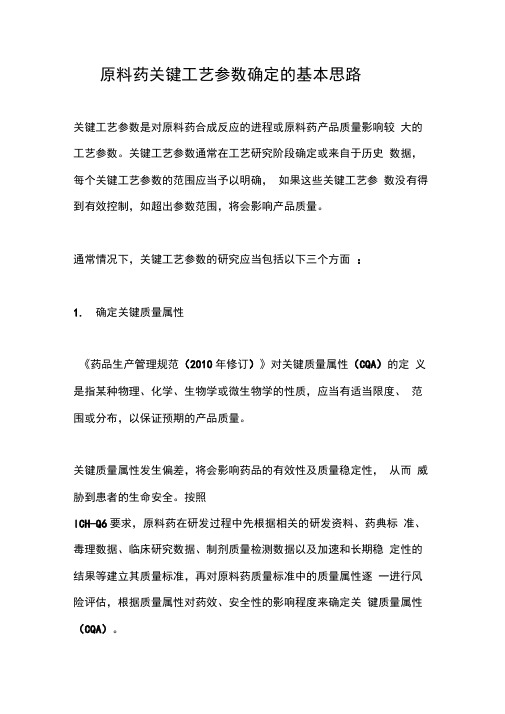
原料药关键工艺参数确定的基本思路关键工艺参数是对原料药合成反应的进程或原料药产品质量影响较大的工艺参数。
关键工艺参数通常在工艺研究阶段确定或来自于历史数据,每个关键工艺参数的范围应当予以明确,如果这些关键工艺参数没有得到有效控制,如超出参数范围,将会影响产品质量。
通常情况下,关键工艺参数的研究应当包括以下三个方面:1.确定关键质量属性《药品生产管理规范(2010年修订)》对关键质量属性(CQA)的定义是指某种物理、化学、生物学或微生物学的性质,应当有适当限度、范围或分布,以保证预期的产品质量。
关键质量属性发生偏差,将会影响药品的有效性及质量稳定性,从而威胁到患者的生命安全。
按照ICH-Q6要求,原料药在研发过程中先根据相关的研发资料、药典标准、毒理数据、临床研究数据、制剂质量检测数据以及加速和长期稳定性的结果等建立其质量标准,再对原料药质量标准中的质量属性逐一进行风险评估,根据质量属性对药效、安全性的影响程度来确定关键质量属性(CQA)。
例如:用于生产口服固体制剂的A原料药,对晶型和粒度有明确要求,在生产过程中不使用金属催化剂。
根据ICH-Q6要求,质量属性对药效和安全性影响的分析包括以下项目:性状:重要影响,通常性状包括了颜色和物理状态,不同的颜色意味着产品中可能引入了微量的杂质,可能影响到患者的安全和药品的疗效,是关键质量属性。
鉴别:重要影响,缺少鉴别,可能造成服用错误的药品将危及患者的安全,是关键质量属性。
含量:重要影响,药品含量太低,患者不能服用到有效剂量的有效成分,将影响到药效发挥;含量太高,患者接触超高剂量有效成分,可能危及患者安全,是关键质量属性。
有机杂质:重要影响,超过安全限度的有机杂质将危及患者安全,是关键质量属性。
无机杂质:轻微影响,由于原料药的药物服用剂型是口服固体制剂,所以生产工艺中产生少量无机杂质对药效没有显著影响,对患者安全产生影响也甚微,非关键质量属性。
残留溶剂:重要影响,生产中残留溶剂,可能会对原料药的稳定性产生影响、或影响制剂生产工艺、毒性溶残将危及患者安全,是关键质量属性。
工艺管理控制程序
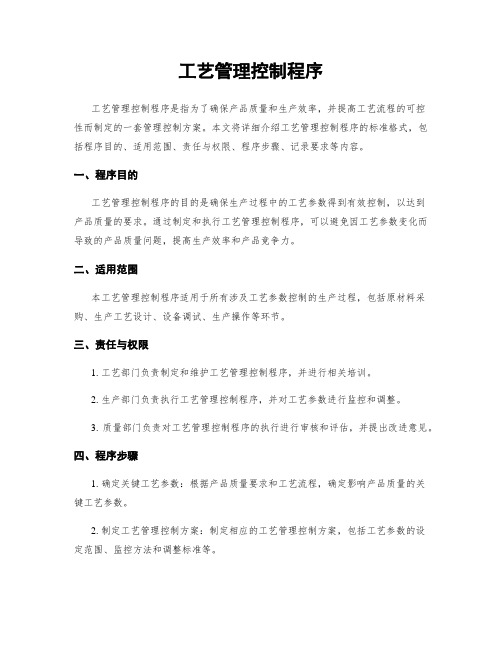
工艺管理控制程序工艺管理控制程序是指为了确保产品质量和生产效率,并提高工艺流程的可控性而制定的一套管理控制方案。
本文将详细介绍工艺管理控制程序的标准格式,包括程序目的、适用范围、责任与权限、程序步骤、记录要求等内容。
一、程序目的工艺管理控制程序的目的是确保生产过程中的工艺参数得到有效控制,以达到产品质量的要求。
通过制定和执行工艺管理控制程序,可以避免因工艺参数变化而导致的产品质量问题,提高生产效率和产品竞争力。
二、适用范围本工艺管理控制程序适用于所有涉及工艺参数控制的生产过程,包括原材料采购、生产工艺设计、设备调试、生产操作等环节。
三、责任与权限1. 工艺部门负责制定和维护工艺管理控制程序,并进行相关培训。
2. 生产部门负责执行工艺管理控制程序,并对工艺参数进行监控和调整。
3. 质量部门负责对工艺管理控制程序的执行进行审核和评估,并提出改进意见。
四、程序步骤1. 确定关键工艺参数:根据产品质量要求和工艺流程,确定影响产品质量的关键工艺参数。
2. 制定工艺管理控制方案:制定相应的工艺管理控制方案,包括工艺参数的设定范围、监控方法和调整标准等。
3. 培训操作人员:对相关操作人员进行培训,确保其了解工艺管理控制程序的要求和操作方法。
4. 监控工艺参数:在生产过程中,对关键工艺参数进行实时监控,并记录监控数据。
5. 分析监控数据:定期对监控数据进行分析,评估工艺参数是否在设定范围内,并制定相应的调整措施。
6. 调整工艺参数:根据监控数据的分析结果,对工艺参数进行调整,以确保产品质量的稳定性。
7. 记录与报告:对工艺参数的监控数据、调整记录等进行记录和归档,并定期向相关部门汇报。
五、记录要求1. 工艺参数监控记录:记录每次对工艺参数进行监控的日期、时间、监控数值等信息。
2. 工艺参数调整记录:记录每次对工艺参数进行调整的日期、时间、调整前后数值等信息。
3. 培训记录:记录对操作人员进行的工艺管理控制程序培训的日期、培训内容、培训人员等信息。
ASTME2500确证方法--关键质量属性关键工艺参数关键方面

ASTME2500确证⽅法--关键质量属性关键⼯艺参数关键⽅⾯术语解释关键质量属性(Critical Quality Attributes, CQA):指产品的物理、化学、⽣物或微⽣物性质或特征,应在适当的限度、范围或分布之内,以确保预期的产品质量。
关键⼯艺参数(Critical Process Parameter, CPP):该⼯艺参数的波动会影响到产品关键质量属性⽽应该被监测或控制,以确保能⽣产出预期质量的产品。
关键⽅⾯(Critical Aspect, CA):⽣产系统的关键⽅⾯通常是功能,特征,性能,和持续保持产品质量和患者安全所必须的⽣产⼯艺和系统的性能或特征。
他们应该在科学的产品和⼯艺的理解基础上进⾏确定并记录。
确证(Verification):是⼀个系统的⽅法,⽤来证实⽣产系统、单独或联合操作,是否符合其预定⽤途,是否已正确安装,并正确运⾏。
这是⼀个总称,它包括所有确保系统适合其⽤途的⽅法,如确认,调试和确认,确证,系统验证或其他。
ASTM E2500 确证⽅法ASTM E2500 -13 《制药、⽣物制药⽣产系统和设备的规范、设计和确证标准指南》以风险和科学为基础的⽅法,对潜在可能影响产品质量和患者安全的⽣产系统和设备的规范,设计和确证进⾏描述。
同时还描述了⼀个系统的、⾼效的和有效的⽅式,确保⽣产系统和设备符合预期的使⽤⽬的,⽽且对与产品质量和患者安全相关的风险进⾏有效管理。
关键质量属性CQA &关键⼯艺参数CPP &关键⽅⾯CAPDA技术报告54-5《⽣产系统设计、确认和运⾏活动中的质量风险管理》中,应⽤了下图(Figure6.1.1-1制药⽣产层级图)不仅形象的展⽰了从“患者”到“⽣产和⽀持系统关键⽅⾯”之间的关系,还清晰的展⽰了关键质量属性CQA、关键⼯艺参数CPP与关键⽅⾯CA的关系。
在上图中,对应患者层⾯需确定产品预期⽤途并预先定义质量⽬标(关于临床相关性,效⼒,和安全性),即质量⽬标产品概况(QTPP),再确定产品的关键质量属性(CQA),然后⼯艺的每⼀步均必须考虑关键质量属性且必须将⼯艺风险评估与关键质量属性(CQA)相关联。
- 1、下载文档前请自行甄别文档内容的完整性,平台不提供额外的编辑、内容补充、找答案等附加服务。
- 2、"仅部分预览"的文档,不可在线预览部分如存在完整性等问题,可反馈申请退款(可完整预览的文档不适用该条件!)。
- 3、如文档侵犯您的权益,请联系客服反馈,我们会尽快为您处理(人工客服工作时间:9:00-18:30)。
关键工艺参数确认的S O P1 目的:定义关键工艺参数,建立关键工艺参数的选择和评估程序,加强对关键工艺参数的理解和识别,便于日常操作。
2 范围:总公司及分子公司原料药线的中间体和原料药产品的生产。
所有GMP条件下生产的中间体和原料药必须对关键工艺参数进行确认。
3 责任者:研发部、生产技术部、QC、QR、QA研发部、生产技术部-组织和领导对质量风险进行分析评估-起草确认方案和报告-具体实施确认工作-在确认工作结束后对工艺参数、关键工艺参数进行列表-对工艺耐受性进行分析提供支持-对生产提供支持-提供工艺确认中相关的文件-对工艺执行情况进行评估,并确保任何必要的、额外的工艺确认工作的实施生产部门-组织和领导工艺耐受性分析工作-对工艺耐受性分析进行文件记录-按照工艺规程中的工艺参数执行生产化验室-在工艺确认的过程中提供分析支持-对检测方法进行验证质量管理部-对质量风险分析提供支持-批准确认方案和报告-对工艺耐受性分析工作提供支持-审核和批准的工艺参数列表-对工艺规程中所列的工艺参数的正确实施进行审核-对工艺验证后工艺的实施情况进行评估(产品年度回顾)产品经理或项目负责人-根据产品的需求和客户要求,开始工艺确认工作-审核和批准的生产工艺参数列表-在产品的生命周期内,对进一步的确认工作的申请进行评估4 程序基本原则及内容4.2.1在产品小试开发结束后,应初步确定关键工艺参数并将其列入开发报告中4.2.2关键工艺参数的确认应该包括:-确定可能影响API质量的工艺参数的关键属性-确定每个关键工艺参数的范围. 先决条件4.3.1关键工艺参数应明确界定(最低限度的要求是在实验室条件下的定义),然后确认工作才可以开始4.3.2关键工艺参数的设置,应该经过技术人员组织相关人员组织讨论后,以书面的形式确认。
4.3.3确认关键工艺参数之前,成品的标准很分析方法要提前进行确认。
4.3.4起始原料、中间体和最后中间体应该已经确定。
4.3.5对整个反应过程用到的关键原料、中间体的来源已经确认。
4.3.6中间体的质量标准的设置应该要确保由这个标准下的中间体可以得到合格的最终产品。
中间体的标准设置的时候,应该考虑到可能影响的成品的全部标准。
4.3.7当中间体有明确验收标准时可以作为设置关键工艺参数的参考标准。
4.3.8涉及到工艺变更的时候,必须重新评估关键工艺参数的设置。
. 质量风险评估14.4.1质量风险评估是确定这些参数对最终产品质量的影响。
因此要考虑设置关键工艺参数的全过程,包括从研发开始到放大生产的整个过程。
4.4.2对这个风险进行评估的时候,应该是由技术人员组织各相关人员进行评估。
最后由QA对结果进行确认。
4.4.3进行质量风险评估的时候可按照如下程序进行:4.4.3.14.4.3.3 这个参数对产品质量的影响情况4.4.3.4 是否存在可能由于操作原因或分析原因导致的偏差4.4.3.5 偏差发生时会造成多大的风险4.4.3.5 放大时可能产生的放大效应是否已经考虑在内4.4.3.6 过程中是否可以设置监控点4.4.3.7 设备的特性是否会对这个参数的设置造成影响4.4.3.8 中间监控是合理,是否有代表性4.4.4虽然强调产品的质量是设计出来的,但是要同时考虑产品的质量不是孤立的,应该是和其他方面都有紧密的相连的。
比如实际的操作情况、生产能力、三废的处理能力、安全、环境、健康等其它因素。
4.4.5如果有充分的理由证明参数不会对产品的质量和收率造成关键影响,参数可以不设置为关键参数,但是必须要形成书面的确认材料,并且要由QA进行确认。
4.4.6所有的非关键工艺参数均为潜在的关键工艺参数,在实际生产中需要继续保持跟踪,确认它们对产品的质量和收率造成的影响程度。
4.4.7质量风险评估的确认过程应该由技术人员提出,并拟定相应的文件,最后由QA确认。
4.4.8质量风险评估的确认文件应包括以下资料-工艺简介-所有的原材料以及供应商-原料的质量标准和分析方法-可能存在的质量风险-评估的理由-参数的设置范围、设置的依据4.4.9关键工艺参数的设置应该尽可能在实验室阶段确认,然后根据具体情况确认放大后的参数。
实验室确认阶段需要有详细的数据支持。
实验室不能确认的参数,可以转移至放大过程中进行确认。
在实验室确认的时候,所有的原材料的规格应该尽可能和放大生产中用到的保持一致。
原料的供应商和质量情况应该有详细记录。
由于特殊原因不能使用同样级别的原料的时候应该有充分的理由确认不是由于原料级别的原因导致产品的质量或收率出现异常。
所有的分析方法,包括原料、中间体、中控过程、成品的分析方法应该是经过确认的,并证明是合理的。
应该对产品的物理、化学和微生物等方面的质量特性进行确认研究参数范围制定的意图是给生产提供一个适当的范围,以减少可控的异常发生,但是它们并不是一定要延伸到失败的边缘。
在选择的时候通常要包括至少两次的预期范围内的运行数据。
参数范围的制定可参考附录1 。
参数设置的目的是提供一个可供操作的空间,保证产品的质量。
产品在放大的时候要关注由于放大效应引起的参数的设置,特别是“时间”参数和“稳定”因素。
操作的时候,合理的中断操作,要制定相应的时间点和时间限。
质量风险评估24.5.1质量风险评估2的目的是为了确认关键工艺参数存在的风险。
在确认之前,这些参数都应该被视为潜在的关键工艺参数。
风险评估的结果应该形成书面报告。
4.5.2参数列为非关键,应该有足够的理由证明它对中间体、成品没有重大的质量或收率影响。
4.5.3经过确认的可接受范围比较窄的工艺参数,也应该被列为潜在的关键工艺参数。
4.5.4参数列为关键或非关键,如果有非常明确的科学理论依据的时候,可以没有数据支持。
. 关键工艺参数确认报告4.6.1根据生产的过程和结果,由技术人员组织相关人员对全过程进行评估,形成书面文件,并且由QA进行确认。
确保由这些参数范围内生产出来的产品在质量上和收率上都可以达到预期的水平。
4.6.2确认报告应该包括以下内容:- 质量风险评估1、质量风险评估2- 确认方案- 确认方案的变更- 实验室数据的索引- 所有结果的总结- 工艺参数的列表- 所有确认的供应商的列表- 对未解决问题的讨论4.6.3参数列表应该包含一个简要的对所有参数进行测试的结果,包括制定它们的依据、可以接受的范围和简短的评估意见。
任何潜在的影响(影响质量,影响收率,影响操作等)都应该提到。
应注意潜在的关键工艺参数。
4.6.4对提供关键原料的供应商应该进行审计,确保它们的质量体系在华海许可的范围内。
4.6.5确认报告由技术人员完成,最后由QA批准后归档保存。
关键工艺参数确认过程4.7.1在对工艺进行确认前,首先要对车间、设备等进行确认。
确认所用到的设备能符合工艺的要求。
4.7.2应该根据预先指定的方案对工艺进行确认。
分析人员对各中间体、中控、成品进行检测。
4.7.3由生产技术人员组织项目组对整个过程进行确认。
确认包括生产的确认和分析的确认,整个确认过程需要由QA人员同时跟进。
4.7.4合理的工艺参数范围的建立应该同时考虑到设备的性能和过程控制系统的使用范围,同时还要考虑可操作性、安全性和生产能力等问题。
4.7.5在放大的过程中,要考虑到放大效应和由于设备原因造成的质量风险。
在放大过程中应该也是一个优化的过程,进行确认的过程中要同时找出有效的纠正措施。
4.7.6生产的时候要考虑到实际存在的固有的偏差。
工艺参数的制定要考虑到这一点,通常情况下应该设置 / - 3个标准偏差的仪器测量偏差。
4.7.7由其它因素确立的关键工艺参数(科学推理、生产能力等)也应该有详细的列表。
在注册中需要体现出来。
4.7.8所有的偏差应该记录在案。
并且由技术人员组织相应的人员进行调查。
发生重大偏差的时候,整个过程需要调查清楚,并形成详细的调查报告,根据实际情况决定是否需要对工艺进行重新评估。
4.7.9如果在设置的参数范围内发生偏差,参数的范围应该缩小,直至证明该范围内的操作可以接受为止。
. 正常生产过程中工艺参数4.8.1整个生产过程的关键工艺参数都应该有详细的记录。
4.8.2整个生产过程的关键工艺参数应该严格控制。
以确保它们存在的意义,保证产品的质量。
4.8.3所有偏离关键工艺参数范围的偏差都应该被作为重大偏差进行调查处理。
4.8.4非关键工艺参数的范围的偏离,应该将原因彻底查清楚,通过最后产品质量的评估确认它是否应该被列入关键工艺参数。
4.8.5如果没有超出相应的参数范围,如果在运行过程中,总是偏离参数的中间值,应该重新对参数的设置范围进行调查和评估,需要调整的时候,应该要有书面的调查结果和处置意见,最后由QA确认后进行调整。
. 再确认4.9.1关键工艺参数的资格确认应该包含在产品的整个生命周期。
4.9.2由于工作经验和知识的增加,同时也有些参数在生产过程中可能会调整,另外外部的一些工艺条件也可能发生变化(新的原料供应商、新的设备等)。
在这种情况下,全部或部分的关键工艺参数进行重新确认是非常有必要的。
确认的过程和按照新的关键参数确认过程进行。
. 附录附录1 :关键工艺参数设置指导意见5.本文件更改历史情况。