辊压机联合粉磨系统和半终粉磨系统的应用比较
辊压机联合粉磨系统在水泥生产中的应用
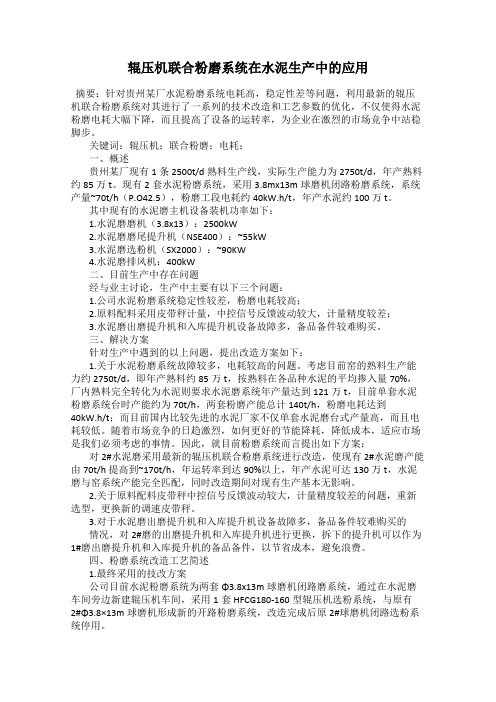
辊压机联合粉磨系统在水泥生产中的应用摘要:针对贵州某厂水泥粉磨系统电耗高,稳定性差等问题,利用最新的辊压机联合粉磨系统对其进行了一系列的技术改造和工艺参数的优化,不仅使得水泥粉磨电耗大幅下降,而且提高了设备的运转率,为企业在激烈的市场竞争中站稳脚步。
关键词:辊压机;联合粉磨;电耗;一、概述贵州某厂现有1条2500t/d熟料生产线,实际生产能力为2750t/d,年产熟料约85万t。
现有2套水泥粉磨系统,采用3.8mx13m球磨机闭路粉磨系统,系统产量~70t/h(P.O42.5),粉磨工段电耗约40kW.h/t,年产水泥约100万t。
其中现有的水泥磨主机设备装机功率如下:1.水泥磨磨机(3.8x13):2500kW2.水泥磨磨尾提升机(NSE400):~55kW3.水泥磨选粉机(SX2000):~90KW4.水泥磨排风机:400kW二、目前生产中存在问题经与业主讨论,生产中主要有以下三个问题:1.公司水泥粉磨系统稳定性较差,粉磨电耗较高;2.原料配料采用皮带秤计量,中控信号反馈波动较大,计量精度较差;3.水泥磨出磨提升机和入库提升机设备故障多,备品备件较难购买。
三、解决方案针对生产中遇到的以上问题,提出改造方案如下:1.关于水泥粉磨系统故障较多,电耗较高的问题。
考虑目前窑的熟料生产能力约2750t/d,即年产熟料约85万t,按熟料在各品种水泥的平均掺入量70%,厂内熟料完全转化为水泥则要求水泥磨系统年产量达到121万t,目前单套水泥粉磨系统台时产能约为70t/h,两套粉磨产能总计140t/h,粉磨电耗达到40kW.h/t;而目前国内比较先进的水泥厂家不仅单套水泥磨台式产量高,而且电耗较低。
随着市场竞争的日趋激烈,如何更好的节能降耗,降低成本,适应市场是我们必须考虑的事情。
因此,就目前粉磨系统而言提出如下方案:对2#水泥磨采用最新的辊压机联合粉磨系统进行改造,使现有2#水泥磨产能由70t/h提高到~170t/h,年运转率到达90%以上,年产水泥可达130万t,水泥磨与窑系统产能完全匹配,同时改造期间对现有生产基本无影响。
半终粉磨工艺和联合粉磨工艺的对比

半终粉磨工艺和联合粉磨工艺的对比1 概述HFCG系列辊压机和SF系列打散分级机是合肥水泥研究设计院在“七五”、“八五”期间先后研制开发的新型增产节能粉碎设备。
自八十年代中期首台辊压机问世并应用于水泥粉磨以来,其显著的增产节能效果受到国际水泥界的普遍重视。
辊压机应用高压料层粉碎的原理,采用单颗粒粉碎群体化的工作方式,使物料粒度迅速减小,<0.08mm的细粉含量可达20-35%,<2mm的物料达到 70%以上。
并且所有经挤压的物料颗粒都存在大量的裂纹,使后续球磨机系统的粉磨状况大为改善,从而大幅度降低粉磨系统的单产电耗。
与辊压机相配套,我院自行研制开发出具有独立知识产权的国家专利产品新型打散分级设备SF系列打散分级机。
该设备与辊压机闭路,构成一种全新的挤压粉磨工艺——挤压联合粉磨工艺。
同时,由于打散机的分级作用,解决了因大颗粒进入选粉机,造成选粉机磨损严重的问题,这也使半终粉磨系统更加成熟、可靠。
打散分级机采用离心冲击破碎及空气动力学原理,集料饼打散与颗粒分级功能于一体,对被挤压后的料饼进行充分地打散和有效地分选,分级粒径可以从0.5-3.5mm 连续调节,大颗粒物料返回辊压机再次挤压,半成品送入球磨机继续粉磨或由选粉机分选至成品。
打散分级机与辊压机构成闭路,可消除因未被充分挤压的物料及边缘漏料对后续球磨系统产生的不良影响,进一步优化磨机系统工况,从而获得大幅度增产节能的效果。
2 应用范围挤压联合粉磨工艺和半终粉磨工艺可应用于年产20万吨以上水泥生产企业的水泥生料、水泥成品粉磨。
既适用于水泥生产企业的新线建设,也适用于老企业的技术改造扩建,可在原有传统粉磨工艺系统的基础上大幅度地提高系统产量,降低系统电耗和研磨体消耗,降低噪音,改善操作环境,提高企业的经济效益。
同时,这两种粉磨工艺系统也可应用于高炉矿渣、煤以及陶瓷、玻璃等建材行业和选矿行业中所有脆性矿物的粉磨作业中。
HFCG系列辊压机和SF系列打散分级机技术性能分见于表l和表2。
小型辊压机联合粉磨系统改为半终粉磨系统的经验

小型辊压机联合粉磨系统改为半终粉磨系统的经验浙江胥口有一条2500t/d 水泥熟料生产线和一条GLF140-65辊压机+直径3.8×13m 球磨机双闭路联合水泥粉磨系统。
胥口于2014年2月将水泥磨联合粉磨工艺改为水泥磨半终粉磨工艺,取得了较好的增产节能效果。
1、技改前的基本情况 1.1 工艺流程及主机设备粉磨系统采用的是国内水泥企业较为普遍的双闭路联合粉磨工艺,工艺流程图见图1,主机设备见表1。
图1 改造前的双闭路联合粉磨工艺表1:技改前主机设备 1.2、存在的主要问题参照国内其他厂家的改造经验,检查胥口南方粉磨系统实际情况,该系统中主要存在以下问题:1、辊压机预磨系统的旋风收尘器入磨的物料中存在有20-30%的30μm 及以下的合格品,在磨内产生过粉磨现象,降低了磨机的粉磨效率。
序号 设备名称 规格、型号及主要参数1 水泥磨机 Ø3.8×13m 两仓水泥磨,电机功率2800kw2 辊压机 GLF140-65 , 通过能力380-480t/h ,电机功率 2×500kw3 V 型选粉机 VX5810,能力450t/h , 处理风量 15000m3/h4辊压机 循环风机 处理风量150000 m3/h ,全压4000Pa, 电机功率200kw5 O-Sepa 选粉机 N2500,处理能力90-150 t/h ,电机功率132kw 6磨内通风风机处理风量50000 m3/h ,全压4000Pa, 电机功率110kw2、磨内物料细度(0.08mm筛筛余)从磨头的20.98%到磨尾的8.12%,只降低了13%;比表面积从磨头的135m2/kg到磨尾的156m2/kg,只增加了21m2/kg,显然粉磨效率是比较低的。
2、改造措施2.1 基本思路采取半终粉磨工艺,在保证水泥质量的前提下,将预粉磨系统中的部分合格细粉通过选粉机分选出来,直接通过斜槽输送入水泥库。
按照其它厂家的经验,采取半终粉磨工艺时,辊压机的装机功率与磨机装机功率的比要大于0.6,而该系统中辊压机的装机功率与磨机装机功率的比只有0.357。
水泥粉磨系统设备及工艺改造对产质量提升
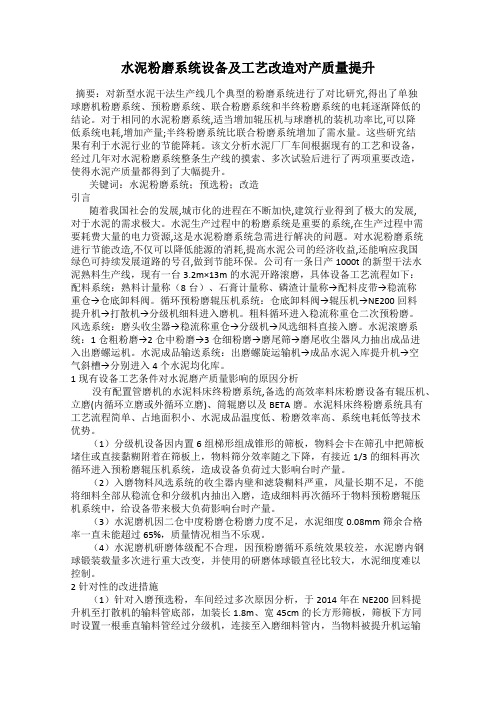
水泥粉磨系统设备及工艺改造对产质量提升摘要:对新型水泥干法生产线几个典型的粉磨系统进行了对比研究,得出了单独球磨机粉磨系统、预粉磨系统、联合粉磨系统和半终粉磨系统的电耗逐渐降低的结论。
对于相同的水泥粉磨系统,适当增加辊压机与球磨机的装机功率比,可以降低系统电耗,增加产量;半终粉磨系统比联合粉磨系统增加了需水量。
这些研究结果有利于水泥行业的节能降耗。
该文分析水泥厂厂车间根据现有的工艺和设备,经过几年对水泥粉磨系统整条生产线的摸索、多次试验后进行了两项重要改造,使得水泥产质量都得到了大幅提升。
关键词:水泥粉磨系统;预选粉;改造引言随着我国社会的发展,城市化的进程在不断加快,建筑行业得到了极大的发展,对于水泥的需求极大。
水泥生产过程中的粉磨系统是重要的系统,在生产过程中需要耗费大量的电力资源,这是水泥粉磨系统急需进行解决的问题。
对水泥粉磨系统进行节能改造,不仅可以降低能源的消耗,提高水泥公司的经济收益,还能响应我国绿色可持续发展道路的号召,做到节能环保。
公司有一条日产1000t的新型干法水泥熟料生产线,现有一台3.2m×13m的水泥开路滚磨,具体设备工艺流程如下:配料系统:熟料计量称(8台)、石膏计量称、磷渣计量称→配料皮带→稳流称重仓→仓底卸料阀。
循环预粉磨辊压机系统:仓底卸料阀→辊压机→NE200回料提升机→打散机→分级机细料进入磨机。
粗料循环进入稳流称重仓二次预粉磨。
风选系统:磨头收尘器→稳流称重仓→分级机→风选细料直接入磨。
水泥滚磨系统:1仓粗粉磨→2仓中粉磨→3仓细粉磨→磨尾筛→磨尾收尘器风力抽出成品进入出磨螺运机。
水泥成品输送系统:出磨螺旋运输机→成品水泥入库提升机→空气斜槽→分别进入4个水泥均化库。
1现有设备工艺条件对水泥磨产质量影响的原因分析没有配置管磨机的水泥料床终粉磨系统,备选的高效率料床粉磨设备有辊压机、立磨(内循环立磨或外循环立磨)、筒辊磨以及BETA磨。
水泥料床终粉磨系统具有工艺流程简单、占地面积小、水泥成品温度低、粉磨效率高、系统电耗低等技术优势。
辊压机联合粉磨工艺系统分析

辊压机联合粉磨工艺系统分析辊压机联合粉磨(或半终粉磨)工艺系统,其技术核心在本质上属于“分段粉磨”。
目前,国内水泥制成工序广泛应用由辊压机+打散分级机(动态分级设备)或V型选粉机(静态分级设备)+管磨机开路(或配用高效选粉机组成双闭路)组成的联合粉磨工艺系统(或由辊压机+V型选粉机(静态分级设备)+高效选粉机+管磨机组成的半终粉磨工艺系统),在实际运行过程中,由于各线生产工艺流程及设备配置、物料粉磨特性、水份等方面因素不尽相同,导致系统产量、质量及粉磨电耗等技术经济指标也参差不齐,本文拟对水泥联合粉磨单闭路(管磨机为开路)及双闭路系统(或半终粉磨系统)中各段常出现的工艺技术与设备故障模式进行探讨分析,并提出了相应的解决办法,仅供粉磨工程技术人员在日常工作中参考,文章中谬误之处恳望予以批评指正:一、辊压机系统故障模式:辊压机挤压效果差故障原因1:1. 被挤压物料中的细粉过多,辊压机运行辊缝小,工作压力低影响分析:辊压机作为高压料床(流动料床)粉磨设备,其最大特点是挤压力高(>150Mpa),粉磨效率高,是管磨机的3-4倍,预处理物料通过量大,能够与分级和选粉设备配置用于生料终粉磨系统。
但由于产品粒度分布窄、颗粒形貌不合理及凝结时间过快、标准稠度需水量大与混凝土外加剂相容性差等工作性能参数方面的原因,国内水泥制备工艺未采用辊压机终粉磨系统,辊压机只在水泥联合粉磨系统中承担半终粉磨(预粉磨)的任务,经施以双辊之间的高压力挤压后的物料,其内部结构产生大量的晶格裂纹及微观缺陷、<2.0mm及以下颗粒与<80um细粉含量增多(颗粒裂纹与粒度效应),分级后的入磨物料粉磨功指数显著下降(15-25%),易磨性明显改善;因后续管磨机一仓破碎功能被移至磨前,相当于延长了管磨机细磨仓,从而大幅度提高了系统产量,降低粉磨电耗。
但辊压机作业过程中对入机物料粒度及均匀性非常敏感,粒状料挤压效果好、粉状料挤压效果差,即有“挤粗不挤细”的料床粉磨特性;当入机物料中细粉料量多时会造成辊压机实际运行辊缝小,主电机出力少,工作压力低,若不及时调整,则挤压效果会变差、系统电耗增加。
卧辊磨在水泥终粉磨系统中的应用

卧辊磨在水泥终粉磨系统中的应用在水泥单位产品的电耗中,有60~70%是消耗在对原料、固体燃料和水泥熟料的粉磨工艺过程上。
以料层挤压粉磨工艺为主的卧辊磨在当前是比较先进的水泥磨机,水泥粉磨系统采用卧辊磨作为预粉磨、半终粉磨设备,其粉磨系统的台时产量可以提高20%以上,相应的电耗也可以得到在幅度降低。
卧辊磨先进的节能效果、生产的灵活性以及系统的可靠性越来越受到水泥用户的表睐。
我们考察了国内、外几家现正使用卧辊磨设备的水泥厂家,通过他们使用卧辊磨设备的情况,对卧辊磨的工艺流程、设备性能及产品的质量特性副会长了一些分析、比较、具体内容如下:1、工艺流程卧辊磨工艺装备用于水泥生产时既可以用做终粉磨,也可以用做预粉磨,多数情况下可以直接作为终粉磨使用。
系统工艺设备的组成主要包括:卧辊磨、出磨提长升机、选粉机、成品收尘器、排风机及入磨与回粉输送设备等,见图1所示:本终粉磨系统与大型球磨机单独组成的终粉磨系统相比,工艺流程简单,设备布置紧凑流畅,主机设备与附属设备相对少些;卧辊磨与辊压机加球磨粉磨系统相比系统组成较接近。
卧辊磨系统与其它粉磨系统的比较见表1所示:表1三种粉磨系统的比较与其它磨机相比,卧辊磨系统投资费用略高,但从运行成本及工作环境方面却具有极大的优势。
采用卧辊磨工艺的电耗与同类生产能力的球磨机工艺系统相比,由吨水泥能耗45 kWh/t降到23.5 kWh/t,每吨水泥可节约电耗21.5 kWh/t,按一年生产72万吨水泥计算,每年可节约800多万元,同时球磨机球耗费用与卧辊磨磨辊及衬板磨损费折算,平均每吨水泥可降低0.37元/t,每年又节约26万多元金属消耗费用,且大大降低了工人的劳动强度。
卧辊磨系统与球磨机系统相比最突出的优点是噪声很小,运转平稳,节能效果显著。
相比之下球磨机噪声大,隔仓板易损坏,经常窜仓,影响水泥的产量及运转率,并且吨水泥能耗高。
带有辊压机的生产系统,需要进行预破碎能耗高,辊子表面的磨损堆焊部分易脱落损坏,并且轴承经常损坏,影响了水泥的运转率,维修量大。
两种水泥立磨终粉磨系统的比较研究

两种水泥立磨终粉磨系统的比较研究第一篇:两种水泥立磨终粉磨系统的比较研究两种水泥立磨终粉磨系统的比较研究0 引言在水泥生产过程中,需要消耗大量的能量,水泥粉磨电耗占水泥生产过程中总电耗的三分之一以上。
多年来,降低水泥粉磨电耗一直是水泥行业技术人员研究的重要课题。
目前在中国的水泥工业中,水泥粉磨主要有管式磨、立磨和辊压机三种粉磨方式,采用辊压机和管式磨组合成的预粉磨、联合粉磨成为主流水泥粉磨技术路线。
而立磨由于其能耗低、运行稳定、操作简单、维护工作量小,在水泥生料粉磨和煤粉磨中取得了很大成功。
近年来,通过国内外科研工作者的努力,以立磨为代表的新一代水泥粉磨技术在水泥工业上得到了应用和发展[1],尤其是水泥立磨终粉磨技术,以其工艺系统简单、单位电耗低等优点而获得诸多应用,尤其是在国外,水泥立磨终粉磨技术已日趋成熟且应用广泛[1-2]。
目前市场上普遍采用的水泥立磨终粉磨均属内循环立磨,即立磨本体上方设有选粉机。
由于要由喷嘴环高速的喷射气流将大部分物料吹起并带入选粉区域,立磨内部需要通入大量风,且本体阻力损失大,因此这种内循环立磨系统的风机消耗功率比较大,即使是水泥终粉磨系统,其成品电耗也要在28~34kWh/t[3],粉磨节能优势并不是非常明显。
为进一步发挥水泥立磨终粉磨的技术优势,我公司在自主研发外循环立磨装备的基础上,将外循环立磨用于水泥终粉磨系统已获得成功。
本文就针对外循环和内循环两种不同形式的水泥立磨终粉磨系统进行比较分析与探讨。
1 水泥立磨终粉磨工艺流程比较1.1 内循环立磨终粉磨流程内循环水泥立磨终粉磨系统工艺流程见图1。
来自水泥配料站的物料经提升机、喂料皮带经锁风阀喂入内循环立磨,物料在立磨中随着磨盘的旋转从其中心向边缘运动,同时受到磨辊的挤压而被粉碎。
粉碎后的物料在磨盘边缘处被从喷嘴环进入的高速气流带起,粗颗粒落回到磨盘再粉磨;较细颗粒被带到选粉区域,经过选粉机(布置在立磨上方,与立磨成为一个整体)进行分选,分选后的粗粉由内部锥斗返回到磨盘进行循环粉磨,合格细粉被带出立磨,进入袋除尘器收集为水泥成品。
辊压机联合粉磨系统具有优质、高产、低能耗的综合优势
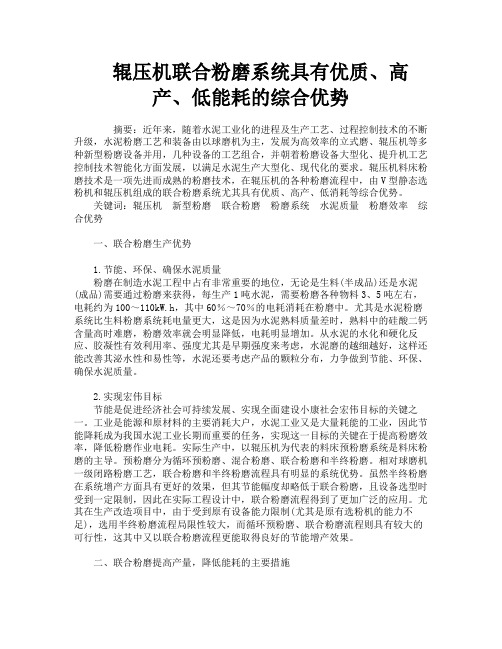
辊压机联合粉磨系统具有优质、高产、低能耗的综合优势摘要:近年来,随着水泥工业化的进程及生产工艺、过程控制技术的不断升级,水泥粉磨工艺和装备由以球磨机为主,发展为高效率的立式磨、辊压机等多种新型粉磨设备并用,几种设备的工艺组合,并朝着粉磨设备大型化、提升机工艺控制技术智能化方面发展,以满足水泥生产大型化、现代化的要求。
辊压机料床粉磨技术是一项先进而成熟的粉磨技术,在辊压机的各种粉磨流程中,由V型静态选粉机和辊压机组成的联合粉磨系统尤其具有优质、高产、低消耗等综合优势。
关键词:辊压机新型粉磨联合粉磨粉磨系统水泥质量粉磨效率综合优势一、联合粉磨生产优势1.节能、环保、确保水泥质量粉磨在制造水泥工程中占有非常重要的地位,无论是生料(半成品)还是水泥(成品)需要通过粉磨来获得,每生产1吨水泥,需要粉磨各种物料3、5吨左右,电耗约为100~110kW.h,其中60%~70%的电耗消耗在粉磨中。
尤其是水泥粉磨系统比生料粉磨系统耗电量更大,这是因为水泥熟料质量差时,熟料中的硅酸二钙含量高时难磨,粉磨效率就会明显降低,电耗明显增加。
从水泥的水化和硬化反应、胶凝性有效利用率、强度尤其是早期强度来考虑,水泥磨的越细越好,这样还能改善其泌水性和易性等,水泥还要考虑产品的颗粒分布,力争做到节能、环保、确保水泥质量。
2.实现宏伟目标节能是促进经济社会可持续发展、实现全面建设小康社会宏伟目标的关键之一。
工业是能源和原材料的主要消耗大户,水泥工业又是大量耗能的工业,因此节能降耗成为我国水泥工业长期而重要的任务,实现这一目标的关键在于提高粉磨效率,降低粉磨作业电耗。
实际生产中,以辊压机为代表的料床预粉磨系统是料床粉磨的主导。
预粉磨分为循环预粉磨、混合粉磨、联合粉磨和半终粉磨。
相对球磨机一级闭路粉磨工艺,联合粉磨和半终粉磨流程具有明显的系统优势。
虽然半终粉磨在系统增产方面具有更好的效果,但其节能幅度却略低于联合粉磨,且设备选型时受到一定限制,因此在实际工程设计中,联合粉磨流程得到了更加广泛的应用。
科技成果——辊压机粉磨系统

科技成果——辊压机粉磨系统适用范围建材行业水泥生产线行业现状原料粉磨:采用球磨机系统电耗23kWh/t;泥粉磨:采用球磨机系统电耗42kWh/t。
目前该技术可实现节能量16万tce/a,减排约42万tCO2/a。
成果简介1、技术原理采用高压挤压料层粉碎原理,配以适当的打散分级烘干装置。
2、关键技术专用磨辊堆焊及修复技术,液压、润滑、喂料、传动、自动控制技术,以及与之相配套的打散分级烘干、球磨机改造等。
3、工艺流程辊压机联合粉磨→半终粉磨→终粉磨。
主要技术指标原料粉磨:采用辊压机终粉磨系统电耗13kWh/t,单位产品节电量10kWh/t。
水泥粉磨:采用辊压机半终粉磨系统电耗30kWh/t,单位产品节电量12kWh/t。
技术水平辊压机装置及系统技术先后分获天津市政府和建材联合会科技进步奖,“TRP(R)220-160大型生料辊压机系统装备”项目被列入2014年度国家重点新产品计划项目。
迄今已有300多台TRP型辊压机及其系统在水泥生产线运行,并出口海外市场。
目前该技术在行业内的推广比例达到50%。
典型案例典型用户:拉法基水泥、亚泰集团、尧柏水泥、金隅集团、蒙西水泥、中材水泥、宁夏赛马和祁连山等诸多水泥集团。
典型案例1某2500t/d新型干法水泥生产线原料磨系统改造项目节能技改投资额约3000万元,停产对接时间15天。
同比采用球磨机,节电40%以上(约10kWh/t生料);同比采用球磨机,吨生料粉磨电耗降低10kWh/t计算,年节电1400万kWh,年节电效益约为700多万元(按0.5元/度计算),投资回收期4.0年。
典型案例2某2500t/d新型干法水泥生产线水泥磨系统改造节能技改投资额约3000万元,建设期120天。
比原采用球磨机节电30%以上(约12kWh/t水泥);同比采用球磨机,以年产130万t水泥,吨水泥粉磨电耗降低12kWh/t计算,年节电效益约为780万元(按0.5元/度计算),投资回收期4.0年。
辊压机水泥半终粉磨技术的发展及应用

薹3 7 . 5
5 O
7 5
终韶
.
1 00 % 磨 机
l O 0 %
辊 压 机
图 1 不 同粉 磨 流 程 的 节 电 效 果
.
水泥产品性能的统一协调关注 ,逐渐替代 了一味对 系统 产量 和 电耗 先进 眭的宣扬 。本文 拟在 梳理 辊压 机水 泥半 终粉磨 技术 发展历 程 的基础 上 ,结合 该粉 磨 系 统生 产实践 ,对 比以往 的水 泥粉 磨 系统 ,力求 对该 系统 进行 客观 、公正 的论述 和评 价 。 1 辊压机 水 泥粉磨 技术 的发展 及 其特点 根 据辊 压机 在水 泥 粉磨 系统 中所承 担 的作 用 ,大体可将辊压机水泥粉磨工艺技术在 国内的发 展分为:预粉磨系统 、混合粉磨系统 、联合粉磨系 统 、半 终 粉磨 系统 以及 终粉 磨 系 “ 。这 些 粉磨 系 统 在工 艺流 程和增 产 节能方 面各 有优 势 和不足 ,但
辊 压 机 水 泥 粉磨 技 术 已经 在 我 国引 进 和 推 广 应 用三 十年 ,不论 是水 泥粉磨 系统 的工 艺技术 ,还 是 设备 制造 的加工 技术 ,都取 得 了长足 的进 步和 发 展 ,不 断优 化 的粉 磨 系统工 艺技术 让辊 压机水 泥 粉
磨技术焕发了强大的生命力 ,占据了国内水泥粉磨
预 粉 磨 流程 一 般 采 用 辊 压 机 边 料 循 环 方 式 , 可将 系 统能 力提 高 近5 0 %,系统 电耗 降低 1 5 % ,但
相对于传统的球磨机一级 闭路粉磨系统,预粉磨流 程在 节能增 产方 面取 得 了重 大飞跃 性 突破 。且该 流 程具有投资省 、流程简单 的特点 ,只是其节 电幅度
辊压机终粉磨系统在生料制备中的应用
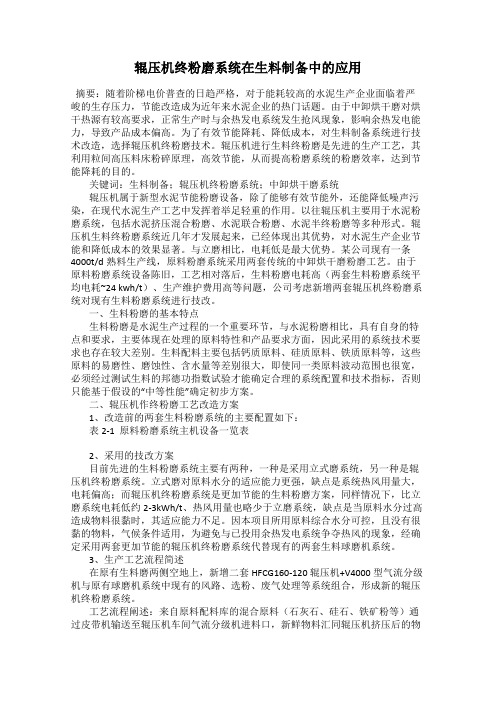
辊压机终粉磨系统在生料制备中的应用摘要:随着阶梯电价普查的日趋严格,对于能耗较高的水泥生产企业面临着严峻的生存压力,节能改造成为近年来水泥企业的热门话题。
由于中卸烘干磨对烘干热源有较高要求,正常生产时与余热发电系统发生抢风现象,影响余热发电能力,导致产品成本偏高。
为了有效节能降耗、降低成本,对生料制备系统进行技术改造,选择辊压机终粉磨技术。
辊压机进行生料终粉磨是先进的生产工艺,其利用粒间高压料床粉碎原理,高效节能,从而提高粉磨系统的粉磨效率,达到节能降耗的目的。
关键词:生料制备;辊压机终粉磨系统;中卸烘干磨系统辊压机属于新型水泥节能粉磨设备,除了能够有效节能外,还能降低噪声污染,在现代水泥生产工艺中发挥着举足轻重的作用。
以往辊压机主要用于水泥粉磨系统,包括水泥挤压混合粉磨、水泥联合粉磨、水泥半终粉磨等多种形式。
辊压机生料终粉磨系统近几年才发展起来,已经体现出其优势,对水泥生产企业节能和降低成本的效果显著。
与立磨相比,电耗低是最大优势。
某公司现有一条4000t/d熟料生产线,原料粉磨系统采用两套传统的中卸烘干磨粉磨工艺。
由于原料粉磨系统设备陈旧,工艺相对落后,生料粉磨电耗高(两套生料粉磨系统平均电耗~24 kwh/t)、生产维护费用高等问题,公司考虑新增两套辊压机终粉磨系统对现有生料粉磨系统进行技改。
一、生料粉磨的基本特点生料粉磨是水泥生产过程的一个重要环节,与水泥粉磨相比,具有自身的特点和要求,主要体现在处理的原料特性和产品要求方面,因此采用的系统技术要求也存在较大差别。
生料配料主要包括钙质原料、硅质原料、铁质原料等,这些原料的易磨性、磨蚀性、含水量等差别很大,即使同一类原料波动范围也很宽,必须经过测试生料的邦德功指数试验才能确定合理的系统配置和技术指标,否则只能基于假设的“中等性能”确定初步方案。
二、辊压机作终粉磨工艺改造方案1、改造前的两套生料粉磨系统的主要配置如下:表2-1 原料粉磨系统主机设备一览表2、采用的技改方案目前先进的生料粉磨系统主要有两种,一种是采用立式磨系统,另一种是辊压机终粉磨系统。
水泥辊压机半粉磨系统新工艺及其装备的研究与应用

水泥辊压机半终粉磨系统新工艺及其装备的研究与应用以辊压机为代表的料床预粉磨系统是料床粉磨的主导,预粉磨分为循环预粉磨、混合粉磨、联合粉磨和半终粉磨。
相对球磨机一级闭路粉磨工艺,联合粉磨和半终粉磨流程具有明显的系统优势。
以往,半终粉磨在系统增产方面具有更好的成效,但其节能幅度却略低于联合粉磨,且设备选型时受到必然限制,因此在实际工程设计中,联合粉磨流程取得了加倍普遍的应用。
为了提高水泥粉磨工艺水平,江苏吉能达建材设备工程技术人员潜心研究,研发了水泥辊压机(立磨)半终粉磨新工艺及其装备。
采纳多级分选、分段粉磨的新工艺,将专用分级机设置在辊压机预粉磨系统中的v型选粉机出风口。
该项新工艺新设备在中材苏州天山(286.67元/吨,0%)水泥成功应用,生产P·O42.5水泥由技改前的220~230t/h提高到目前的290~320t/h,比表面积380m2/kg以上,粉磨电耗由35kWh/t降至27kWh/t。
为水泥辊压机(立磨)粉磨系统的节能降耗探讨了一条新途径。
一、对粉磨工艺系统进行技改的思路一、多级分选、分段粉磨二、辊压机做功越多,系统节电成效越明显,联合(半终 )粉磨系统都必需重视辊压机预粉磨系统做功。
3、对管磨机而言,必需突出“磨内磨细为第一要素”的原那么,多制造合格产品。
4、配套新型高效选粉机任何选粉机的分级进程都能够简单地分三个环节:分散、分级、搜集。
分散是前提,分级是核心,搜集是保证。
成品搜集的问题随着除尘技术的进展已取得了解决。
研究和解决配套半终粉磨工艺系统的选粉机的技术问题应围绕着双向分级来进行,既要搜集成品,又要将无益于球磨机粉磨的大颗粒分离。
五、适应新标准的质量要求。
二、新工艺新技术开发研究进程(1)配套分级设备对球破磨-球磨机粉磨系统进行过研究。
大钢球破碎,在破碎进程中采纳风选原理,把细小颗粒及时带走,实现边粉磨边分选,减少垫层产生的无功浪费,同时减少了过粉磨。
集破碎、研磨、分级功能为一体,提高破碎效率,粉磨能力,而且具有自动粗细分级功能,分级精度高,可再也不单独配套分级设备。
辊压粉磨系统的分级机配置与应用比较
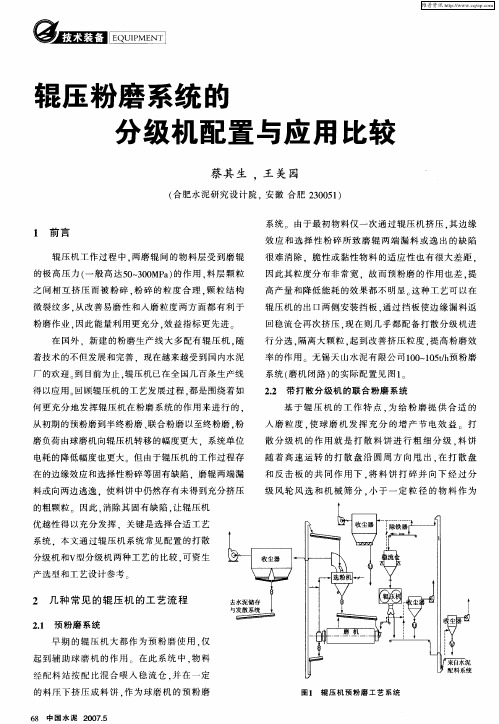
【 兰
j
辊压粉磨 系统 的 分 级机 配置 与应 用 比较
蔡其 生 .王 美 园
( 合肥 水泥研 究设计 院 , 徽 合 肥 2 0 5 ) 安 3 0 1
1 前 言
辊压机 工作 过程 中 . 两磨 辊 间的物 料层 受到 磨辊 的极 高压 力 ( 一般 高达5 ~ 0 MP ) 0 30 a 的作用 . 层 颗粒 料 之 间相 互挤 压 而被 粉碎 . 粉碎 的粒 度合 理 . 粒结 构 颗 微裂 纹多 . 改善 易磨性 和人 磨粒 度两 方面都 有 利于 从 粉磨 作业 , 因此能量 利用 更充分 , 效益 指标更 先进 。 在 国外 .新建 的粉磨 生产 线大 多配 有辊 压机 . 随
l6 5
l2 5
lO l
7 2
圈2
打 散 机 结 构 示 慝
圈 3 打 散 分 级 机 的 挤 压 联 合 粉 唇 系 统 工 艺 示 意 图
半 成 品 入磨 粉 磨 至 成 品 . 颗 粒 物 料 则 返 回辊 压 机 大 重新 挤 压 见 图2 由于打 散分级 机具 有机械 打 散 、 选 和机械 筛分 风
的粗颗粒 因此 . 除其 固有缺 陷 。 消 让辊 压机
基 于 辊 压 机 的 工 作 特 点 . 给粉 磨 提 供合 适 的 为 人 磨 粒 度 , 球 磨 机 发 挥 充 分 的增 产 节 电 效 益 。打 使 散 分 级 机 的作 用 就 是 打 散 料 饼 进 行 粗 细 分 级 . 饼 料
O3 7 .l
打散 分 级机 4 2 l 6 .x 3 35 开路 ) 5 0(
O2 l .8
打 散 分 级 机 4 2 l 6 .× 3 35( 5 0闭路 1
辊压机在水泥粉磨系统中的应用探讨

辊压机在水泥粉磨系统中的应用探讨摘要:目前国内水泥粉磨系统常采用的主要有两种工艺形势,一是传统的球磨机开路或闭路粉磨系统,二是辊压机+球磨机的挤压联合粉磨系统,辊压机、球磨机可以双闭路或单闭路。
辊压机+球磨机的挤压联合粉磨系统的核心是:物料经过辊压机挤压粉碎后再通过打散分级或选粉回路,将其粗颗粒返回辊压机与新给物料混合继续挤压直至合格粒径,以确保喂入球磨机的物料颗粒结构松散、粒度均匀,从而提高磨机台时产量。
文中对辊压机在水泥粉磨系统中的应用进行了分析。
关键词:辊压机;水泥粉磨系统;应用1导言在水泥生产过程中,粉磨系统电耗占全部生产用电的60%~70%,因此,降低粉磨系统电耗是水泥生产企业节能降耗的主要目标之一。
在常见的大型粉磨设备中,辊压机的能量利用率为600m2/kJ,球磨机为240~320m2/kJ。
新建或改造的粉磨系统,生料粉磨系统大多采用辊压机终粉磨系统,水泥粉磨系统辊压机与球磨机组成的联合粉磨系统。
2工程概况某地工程项目预分解窑水泥生产线,以将水泥制成工序。
工程建设人员采用两套大型机械设备,组成大型开路联合粉磨系统。
经分析,该系统应用的技术特点主要集中在,充分发挥了磨前辊压机段的高效率优势。
即挤压后,料饼进入了动态与静态两级高细气流分级设备,从而使物料分析更为精确、分级效率更高。
但由于当前运行的水泥粉磨生产线,其原配置辊压机规格偏小,因此,无法满足物料的处理能力、做功以及入磨入料中细粉使用等方面的需求。
为此,相关建设人员应在明确水泥粉磨系统预粉磨能力应用现状的情况下,找出优化实践控制的方法策略。
3辊压机系统设备分析气流分级机在使用过程中发现循环提升机入V选物料分布均匀性不好,通过分级机打散板磨损情况进行检查,出现偏料情况通过对现有入V选溜子内部增加打散板,调整物料在溜子内流速、流向,仍不能有效提升入V选溜子物料的均匀分布。
通过对V选下料取样分析,物料在通过V选后仍有0.08mm筛余在12%~15%左右,与先进公司数据通过提高V选效率,通过V选后物料0.08筛余能够达到5%~8%之间。
两种水泥辊压机半终粉磨系统工艺比较分析

两种水泥辊压机半终粉磨系统工艺比较分析王涛;钟根;康宇【摘要】本文阐述了两种不同形式的水泥辊压机半终粉磨系统:双精细选粉机半终粉磨系统,单精细选粉机半终粉磨系统.从系统配置、复杂程度、运行控制特点、可变化性以及对水泥质量的可控制性等方面比较分析了各自的优缺点,探讨两种辊压机半终粉磨形式在不同情况下的实际应用.【期刊名称】《水泥工程》【年(卷),期】2017(000)002【总页数】4页(P24-27)【关键词】水泥;辊压机;半终粉磨【作者】王涛;钟根;康宇【作者单位】南京凯盛国际工程有限公司,江苏南京210036;南京凯盛国际工程有限公司,江苏南京210036;南京凯盛国际工程有限公司,江苏南京210036【正文语种】中文【中图分类】TQ172.6+32随着水泥辊压机粉磨技术与系统的不断发展,水泥生产企业有更多的工艺选择。
目前水泥辊压机半终粉磨工艺在国内得到大范围的应用,半终粉磨系统的提产节电效果受到广泛关注[1,2],特别是近年来,无论是新建辊压机粉磨系统还是对原有辊压机粉磨系统的技术改造,半终粉磨系统工艺成了水泥辊压机的主流粉磨工艺。
所谓的辊压机半终粉磨系统,即将辊压机预粉磨系统产生的符合水泥细度要求的细粉提前选出,直接加入到成品中[1],不再进行后续粉磨工序,减少该部分细粉在球磨机内的过粉磨现象,增加球磨机粉磨效率,达到增加产量、降低电耗的目的[3]。
辊压机半终粉磨系统的主要工艺组成为“辊压机系统+球磨机系统”,从工艺实现形式上,半终粉磨系统又可分为“前后分别采用一套精细选粉机半终粉磨系统(又称双精细选粉机半终粉磨系统)”、“前后共用一套精细选粉机半终粉磨系统(又称单精细选粉机半终粉磨系统)”两种半终粉磨形式,这两种形式各有特点,本文对两种形式的辊压机半终粉磨系统进行比较分析,以供广大的水泥技术工作者参考。
1.1 双精细选粉机半终粉磨系统双精细选粉机辊压机半终粉磨系统工艺流程见图1。
该工艺形式为目前辊压机半终粉磨系统的常用形式。
水泥联合粉磨和半终粉磨优化试验

水泥联合粉磨和半终粉磨优化试验
张晓峰;郝巧趁;白永刚
【期刊名称】《水泥》
【年(卷),期】2019(0)10
【摘要】在“辊压机+V型选粉机+球磨机+高效选粉机”联合粉磨系统中,辊压机系统产生的微粉(3~32μm)可达到35%~40%,为此,通过分流阀将辊压机系统产生的微粉按不同比例加入成品形成半终粉磨。
对原材料细度、成品颗粒级配和物理性能进行分析验证,通过试验调整细度指标,可找出辊压机系统产生的微粉最佳掺入量,在保持水泥强度和与外加剂相容性基本不改变前提下,实现提高产量和降低电耗的目的。
【总页数】4页(P37-40)
【作者】张晓峰;郝巧趁;白永刚
【作者单位】邯郸金隅太行水泥有限责任公司
【正文语种】中文
【中图分类】TQ172.637
【相关文献】
1.水泥联合粉磨改半终粉磨的提产改造
2.水泥半终粉磨系统的优化和质量改善
3.水泥联合粉磨系统与半终粉磨系统运行电耗评价
4.辊压机水泥半终粉磨系统的优化措施
5.水泥联合(半终)粉磨系统管磨机一仓仓长的探讨
因版权原因,仅展示原文概要,查看原文内容请购买。
- 1、下载文档前请自行甄别文档内容的完整性,平台不提供额外的编辑、内容补充、找答案等附加服务。
- 2、"仅部分预览"的文档,不可在线预览部分如存在完整性等问题,可反馈申请退款(可完整预览的文档不适用该条件!)。
- 3、如文档侵犯您的权益,请联系客服反馈,我们会尽快为您处理(人工客服工作时间:9:00-18:30)。
2
中图分类号:TQ 72.632 文献标识码:B 文章编号: 008-0473(20 7)02-002 -04 DOI 编码: 0. 6008/ki. 008-0473.20 7.02.003
辊压机联合粉磨系统和半终粉磨系统的应用比较
摘 要 单,水泥质量稳定,但电耗高于半终粉磨系统。
关键词 0 引言
公司两条水泥粉磨生产线,2010年投产的1号磨是辊压机联合粉磨系统,2015 年投产的2号磨为辊压机半终粉磨系统。
本文就该两种粉磨系统在该公司的应用状况进行比较。
1 工艺介绍
辊压机半终粉磨工艺流程见图1,辊压机联合粉磨工艺流程见图2。
图1 辊压机半终粉磨工艺流程
辊压机半终粉磨工艺,本质就是在原联合粉磨系统中的辊压机预粉磨环节增设一台成品专用选图2 辊压机联合粉磨工艺流程
2 主要设备配置
两种粉磨系统主要设备配置见表1。
半终粉磨系统特点:半终粉磨系统的设备配置比联合粉磨系统有更大的处理能力,这是提高系统产能的前提,单机设备富余量大,才有系统提产空间。
半终粉磨系统主要设备装机容量增加大约835 kW,设备投资增加300万元左右。
2.1 选粉机
半终粉磨系统所用的选粉机采用下进风方式,气流通过具有一定角度的翼型导流装置与分级
32μm~200μm物料进球磨机粉磨;0μm~32μm 内风速不均匀,风量略显不足,水平风道易积料;
半终粉磨系统改为三仓磨,全磨采用钢球,以提高与联合粉磨系统相比,半终粉磨系统平均台表1 两系统主要设备配置及技术参数
表3 联合粉磨系统磨机级配
段选取的细粉量,寻求产量与需水量的平衡,经实践验证,选取的细粉量占水泥成品20%左右较为合适。
磨机研磨体全部使用钢球,有助于提高水泥颗统影响较大,各子系统平衡较难,同等条件下调整到正常状态耗时较长。
半终粉磨系统操作画面见图3,联合粉磨系统操作画面见图4。
24
图3
半终粉磨系统操作画面
系统效率。
5 结束语
(1)辊压机联合粉磨系统和半终粉磨系统对
比,半终粉磨系统主要设备装机容量加大约835 kW,设备投资增加300万元左右,平均台产提高50 t/h,水泥电耗下降约6 kWh/t,节电效果显著。
图4
联合粉磨系统操作画面
(2)辊压机半终粉磨系统,是在辊压机预粉磨环节,增加一台专用选粉机,选取部分细粉作为水泥成品,提高了系统产量,但水泥需水量也有所增加。
生产过程中不能盲目追求高产,要寻求产量与需水量的平衡,选取的细粉量占水泥成品20%左右较合适,产品实物质量与联合粉磨基本相当。
(3)半终粉磨系统操作较为复杂,对物料适应性较差,选粉机内部磨损较快,要加强设备维护,确保稳定的产能和效率。
(4)为充分发挥半终粉磨系统高台产、低电耗的技术优势,必须控制物料综合水分以及进入辊压机的物料粒径,减少稳流仓内物料细粉比例,避免塌料现象,保持系统操作稳定。
(收稿日期:2016-12-28)。