紫外激光晶圆划片及其优点介绍
激光划片原理和特点
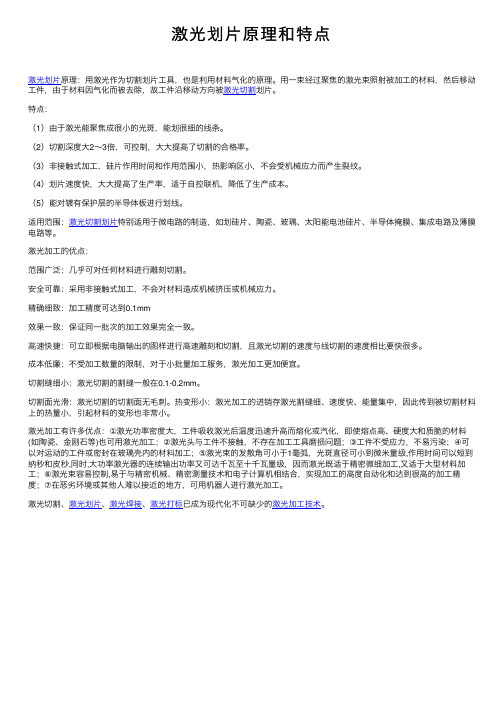
激光划⽚原理和特点激光划⽚原理:⽤激光作为切割划⽚⼯具,也是利⽤材料⽓化的原理。
⽤⼀束经过聚焦的激光束照射被加⼯的材料,然后移动⼯件,由于材料因⽓化⽽被去除,故⼯件沿移动⽅向被激光切割划⽚。
特点:(1)由于激光能聚焦成很⼩的光斑,能划很细的线条。
(2)切割深度⼤2~3倍,可控制,⼤⼤提⾼了切割的合格率。
(3)⾮接触式加⼯,硅⽚作⽤时间和作⽤范围⼩,热影响区⼩,不会受机械应⼒⽽产⽣裂纹。
(4)划⽚速度快,⼤⼤提⾼了⽣产率,适于⾃控联机,降低了⽣产成本。
(5)能对镀有保护层的半导体板进⾏划线。
适⽤范围:激光切割划⽚特别适⽤于微电路的制造,如划硅⽚、陶瓷、玻璃、太阳能电池硅⽚、半导体掩膜、集成电路及薄膜电路等。
激光加⼯的优点:范围⼴泛:⼏乎可对任何材料进⾏雕刻切割。
安全可靠:采⽤⾮接触式加⼯,不会对材料造成机械挤压或机械应⼒。
精确细致:加⼯精度可达到0.1mm效果⼀致:保证同⼀批次的加⼯效果完全⼀致。
⾼速快捷:可⽴即根据电脑输出的图样进⾏⾼速雕刻和切割,且激光切割的速度与线切割的速度相⽐要快很多。
成本低廉:不受加⼯数量的限制,对于⼩批量加⼯服务,激光加⼯更加便宜。
切割缝细⼩:激光切割的割缝⼀般在0.1-0.2mm。
切割⾯光滑:激光切割的切割⾯⽆⽑刺。
热变形⼩:激光加⼯的进销存激光割缝细、速度快、能量集中,因此传到被切割材料上的热量⼩,引起材料的变形也⾮常⼩。
激光加⼯有许多优点:①激光功率密度⼤,⼯件吸收激光后温度迅速升⾼⽽熔化或汽化,即使熔点⾼、硬度⼤和质脆的材料(如陶瓷、⾦刚⽯等)也可⽤激光加⼯;②激光头与⼯件不接触,不存在加⼯⼯具磨损问题;③⼯件不受应⼒,不易污染;④可以对运动的⼯件或密封在玻璃壳内的材料加⼯;⑤激光束的发散⾓可⼩于1毫弧,光斑直径可⼩到微⽶量级,作⽤时间可以短到纳秒和⽪秒,同时,⼤功率激光器的连续输出功率⼜可达千⽡⾄⼗千⽡量级,因⽽激光既适于精密微细加⼯,⼜适于⼤型材料加⼯;⑥激光束容易控制,易于与精密机械、精密测量技术和电⼦计算机相结合,实现加⼯的⾼度⾃动化和达到很⾼的加⼯精度;⑦在恶劣环境或其他⼈难以接近的地⽅,可⽤机器⼈进⾏激光加⼯。
半导体封装领域的晶圆激光划片概述

洗。 冲洗 的作 用是 冷却 的 同时带走切 割 时生成 的粉 尘 , 自动砂轮 划 片工序 如 图 2I 全 | I 。
装 片 位 置 校 准 切 割
@ ⑦
图3 有 效 的 晶 粒 数 量 增 加
上
清沈 / 干燥
过 程 中应 用 。
关 键词 :半 导体 封装 ; 圆, 光划 片 晶 激
中图分 类 号 : N2 5 T 0
文 献标 识 码 : A
文章 编 号 : 0 44 0 (0 0 1—0 90 1 0 —5 72 1 )20 3 .5
La e a e c n n s m i o s r w f r di i g i e c ndu t r e c p ul t0 e d co n a s a i n f l i
半 导 体 元 器 件 的制 造 过 程 可 主 要 分 为 四 个 阶
段 : 料准 备 、 材 晶体 生 长 和 晶 圆准 备 、 圆制 造 、 晶 封
电测 完 毕 的 晶 圆片 在 贴 膜 后 ,通 过 切 割 的方
式 将 晶 圆 分 离 为 晶粒 , 以便进 行 封 装 工 序 。 常 的 通 做 法 是 在 晶 圆上 划 切 出沟 槽 ,然 后 进 行 裂 片 再 将 其 分 离 。 为 半 导 体 封装 的第 一 道 工 序 , 片 质 量 作 划 的好 坏 直 接 影 响 到 整 体 的封 装 质 量 。而 晶 圆 在 划 片过 程 中 容 易 发 生 崩 角 、 层 与 剥 离 等 缺 陷( 图 分 如 1 , 划 片 工 艺 带 来 了挑 战 , 使 划 片 工 艺不 断 向 )给 促 前发展 , 目前 , 片 的方 式 主 要 有 砂 轮划 片和 激 光 划
紫外激光加工技术在硅片晶圆中的应用

武汉元禄光电技术有限公司紫外激光加工技术在硅晶圆中的应用硅材料是地壳中最为丰富的元素半导体,是电子器件中主要的原材料,广泛应用于大规模集成电路领域,我们所熟知的产品有晶圆。
晶圆是半导体行业中最前沿的技术产品,一切的半导体技术从晶圆开始,晶圆我们常称之为硅晶片或硅晶圆。
晶圆的加工是半导体制程中的重要环节,其加工制成也体现着一个国家的先进技术,代表着国家的竞争力。
早在四月份,国内就出现半导体技术被欧美国家卡脖子的情况,引起了大家的广泛关注,同时,也激起了发愤图强,发展半导体技术的口号与行动。
在半导体领域中,前沿的晶圆加工技术是重中之重,如光刻显影技术,我们国家也一直在奋力追赶,引进了7nm工艺的ASML 光刻机,提升工艺制程的品质。
那么你知道在晶圆工艺制程中还有那些重要制程吗?元禄光电带大家了解紫外激光加工技术在硅晶圆工艺制程中的应用。
硅晶圆(图片源自网络)紫外激光加工技术应用到硅晶圆中的设备有紫外激光切割机以及紫外激光打标机,分别对应的是晶圆划线以及晶圆打标。
硅晶圆激光切割硅晶圆在制作过程中通常是制作成分成6/8/12/18寸等多规格晶圆,包含了大量的晶片,应用到半导体制程中需要将晶圆中的晶片切割成一个个小片,再封装到半导体元器件中。
这个工艺制程就需要用到紫外激光切割机,对晶圆进行划片,在裂片的方式加工。
传统的加工方式采用的是刀片的加工模式,而随着晶圆制程的改进,以及碳粉材料参杂的应用,晶圆的硬度越来越高,对加工的要求越来越高,紫外激光技术的应用很好的解决了这种缺陷,尤其是12寸晶圆加入碳粉后,硬度更高,紫外激光切割机的技术优势也就更明显。
武汉元禄光电技术有限公司目前,紫外激光切割机应用到晶圆中采用的是高功率紫外激光器,利用物镜作为光斑聚焦镜,通过高密度高能量光束实现对晶圆的划线,在裂片方式加工。
激光作为先进加工技术的打标,其技术的扩展能力高,可随着晶圆加工工艺制程的提高,而提升激光切割技术工艺品质,可根据需求导入皮秒紫外激光切割机以及飞秒紫外激光切割机,未来紫外激光切割技术在晶圆切割领域将大有可为。
晶圆划片工艺分析
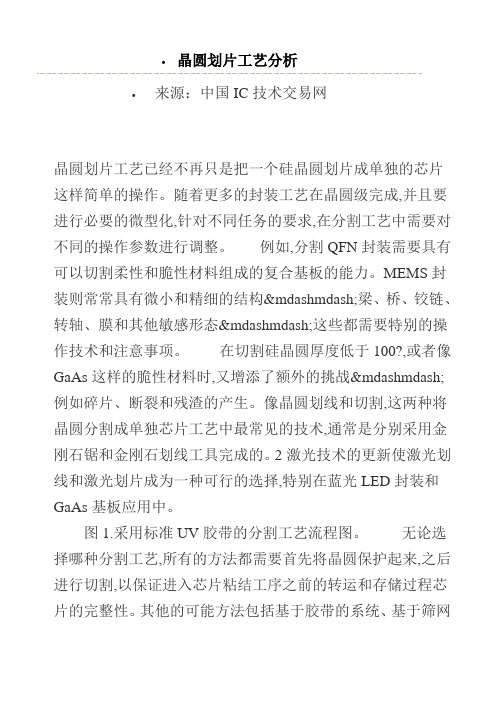
•晶圆划片工艺分析•来源:中国IC技术交易网晶圆划片工艺已经不再只是把一个硅晶圆划片成单独的芯片这样简单的操作。
随着更多的封装工艺在晶圆级完成,并且要进行必要的微型化,针对不同任务的要求,在分割工艺中需要对不同的操作参数进行调整。
例如,分割QFN封装需要具有可以切割柔性和脆性材料组成的复合基板的能力。
MEMS封装则常常具有微小和精细的结构&mdashmdash;梁、桥、铰链、转轴、膜和其他敏感形态&mdashmdash;这些都需要特别的操作技术和注意事项。
在切割硅晶圆厚度低于100?,或者像GaAs这样的脆性材料时,又增添了额外的挑战&mdashmdash;例如碎片、断裂和残渣的产生。
像晶圆划线和切割,这两种将晶圆分割成单独芯片工艺中最常见的技术,通常是分别采用金刚石锯和金刚石划线工具完成的。
2 激光技术的更新使激光划线和激光划片成为一种可行的选择,特别在蓝光LED封装和GaAs基板应用中。
图1.采用标准UV胶带的分割工艺流程图。
无论选择哪种分割工艺,所有的方法都需要首先将晶圆保护起来,之后进行切割,以保证进入芯片粘结工序之前的转运和存储过程芯片的完整性。
其他的可能方法包括基于胶带的系统、基于筛网的系统以及采用其他粘结剂的无胶带系统。
工艺标准的切割工艺中首先是将减薄的晶圆放置好,使其元件面朝下,放在固定于钢圈的释放胶带上。
这样的结构在切割过程中可以保证晶圆,并且将芯片和封装继续保持在对齐的位置,方便向后续工艺的转运。
工艺的局限来自于减薄晶圆的应用,在存储之后很难从胶带上取下晶圆,采用激光的话容易切到胶带,同时在切割过程中冷却水的冲击也会对芯片造成损伤。
基于胶带的分割图2.可处理200或300 mm晶圆的UV固化单元可以放置在桌子上,采用365 nm波长的激光每个小时可以处理50片晶圆。
采用基于胶带的系统时,需要重点考虑置放系统,以及所采用的条带类型是不是适合要切割的材料。
新一代晶圆划片技木
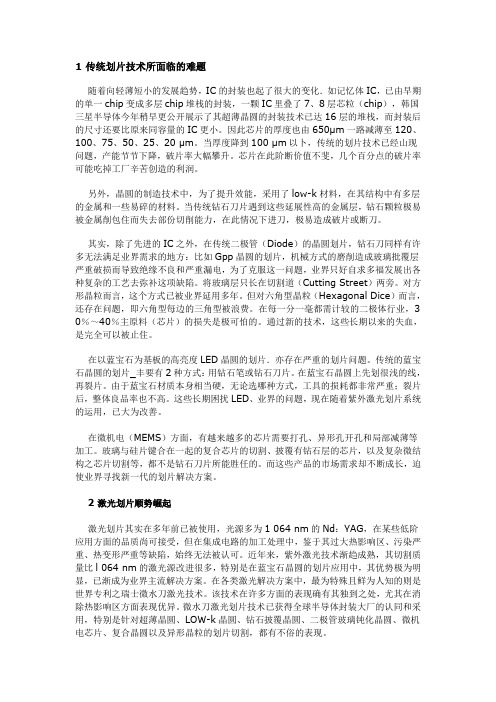
1 传统划片技术所面临的难题随着向轻薄短小的发展趋势,IC的封装也起了很大的变化.如记忆体IC,已由早期的单一chip变成多层chip堆栈的封装,一颗IC里叠了7、8层芯粒(chip),韩国三星半导体今年稍早更公开展示了其超薄晶圆的封装技术已达16层的堆栈,而封装后的尺寸还要比原来同容量的IC更小。
因此芯片的厚度也由650μm一路减薄至120、100、75、50、25、20 μm。
当厚度降到100 μm以卜,传统的划片技术已经山现问题,产能节节下降,破片率大幅攀升。
芯片在此阶断价值不斐,几个百分点的破片率可能吃掉工厂辛苦创造的利润。
另外,晶圆的制造技术中,为了提升效能,采用了low-k材料,在其结构中有多层的金属和一些易碎的材料。
当传统钻石刀片遇到这些延展性高的金属层,钻石颗粒极易被金属削包住而失去部份切削能力,在此情况下进刀,极易造成破片或断刀。
其实,除了先进的IC之外,在传统二极管(Diode)的晶圆划片,钻石刀同样有许多无法满足业界需求的地方:比如Gpp晶圆的划片,机械方式的磨削造成玻璃批覆层严重破损而导致绝缘不良和严重漏电,为了克服这一问题,业界只好自求多福发展出各种复杂的工艺去弥补这项缺陷。
将玻璃层只长在切割道(Cutting Street)两旁。
对方形晶粒而言,这个方式已被业界延用多年。
但对六角型晶粒(Hexagonal Dice)而言,还存在问题,即六角型每边的三角型被浪费。
在每一分一毫都需计较的二极体行业,3 0%~40%主原料(芯片)的损失是极可怕的。
通过新的技术,这些长期以来的失血,是完全可以被止住。
在以蓝宝石为基板的高亮度LED晶圆的划片.亦存在严重的划片问题。
传统的蓝宝石晶圆的划片_丰要有2种方式:用钻石笔或钻石刀片。
在蓝宝石晶圆上先划很浅的线,再裂片。
由于蓝宝石材质本身相当硬,无论选哪种方式,工具的损耗都非常严重;裂片后,整体良品率也不高。
这些长期困扰LED、业界的问题,现在随着紫外激光划片系统的运用,已大为改善。
SP紫外激光LED刻划_(Oct_2009)
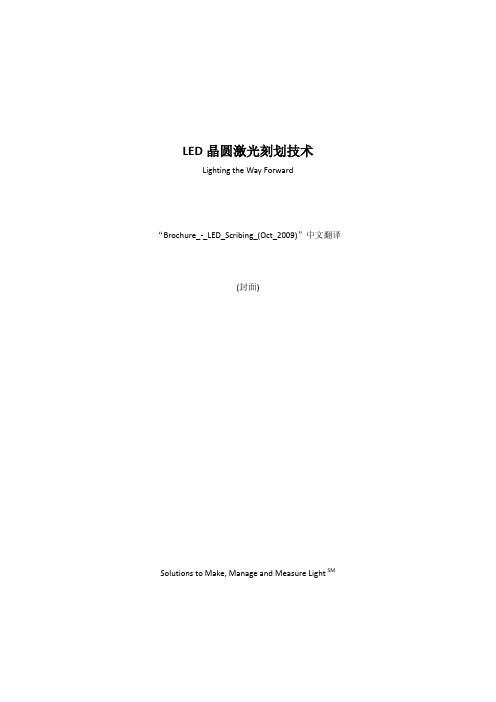
LED晶圆激光刻划技术Lighting the Way Forward “Brochure_-_LED_Scribing_(Oct_2009)”中文翻译(封面)Solutions to Make, Manage and Measure Light SM第一页:照明用LED光源照亮未来温室效应造成的全球气候变暖等负面效应,促成了世界范围绿色节能运动的兴起。
在照明方面,当今世界不断寻求更高效节能的光源作为传统照明光源的替代品,LED光源是最佳的选择,随之而来的是近年来高亮度LED在照明领域的应用持续而迅速的扩大。
LED制造中激光晶圆刻划工艺的引入,使得LED在手机、电视以及触摸屏等LCD背光照明大量使用,而最令人兴奋地是白光LED在照明方面的应用。
当今世界,大约有120亿只白炽灯仍在使用,每年产生大约40,000万亿流明-小时的照明量,这造成了巨大的能量消耗,等同于每年消耗接近10亿吨燃煤。
拿美国而言,照明消耗的能源竟高达全国汽车消耗能源的一半。
美国能源部通过对俄勒冈州家庭照明的最近调查表明LED作为照明源较传统的白炽灯和卤素灯节省大约80%的电能。
随着市场的持续增长,LED制造业对于产能和成品率的要求变得越来越高。
激光加工技术迅速成为LED制造业普遍的工具,甚者成为了高亮度LED晶圆加工的工业标准。
激光刻划LED刻划线条较传统的机械刻划窄得多,所以使得材料利用率显著提高,因此提高产出效率。
另外激光加工是非接触式工艺,刻划带来晶圆微裂纹以及其他损伤更小,这就使得晶圆颗粒之间更紧密,产出效率高、产能高,同时成品LED器件的可靠性也大大提高。
Spectra-Physics工业激光器具有高峰值功率以及卓越的光束质量等优势,是LED加工的理想工具,为LED工业带来洁净的刻划线条、更高的产能以及成品LED更高的亮度。
激光刻划的优势●可以干净整齐的刻划硬脆性材料●非接触式工艺低运营成本●减少崩边、微裂纹、分层等缺陷的出现●刻划线条窄提高了单片晶圆上的分粒数量●减少微裂纹提高了成品LED器件的长期可靠性●大范围的加工容差使得工艺可控性良好,是低成本高可靠性的工艺。
晶圆激光切割与刀片切割工艺介绍
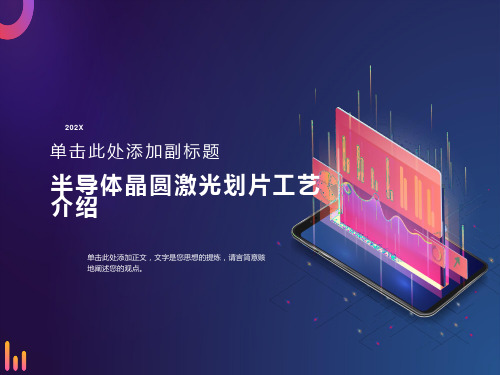
传统刀片划片原理
工作物
例:矽晶片、玻璃
工作物移动的方向
钻石颗粒旋转方向
微小裂纹的范围
特性:容易产生崩碎(Chipp是非机械式的,属于非接触式加工,可以避免出现芯片正面破碎和其它损坏现象,激光划片后需要使用传统工艺将芯片彻底划开。 激光划片采用的高光束质量的光纤激光器对芯片的电性影响较小,可以提供更高的划片成品率。
传统划片方式(砂轮)
激光划片方式(光)
切割速度
40-80mm/s
1-150mm/s
半导体晶圆激光划片工艺介绍
单击此处添加副标题
目录
01
02
03
04
05
06
什么是晶圆划片 ?
晶圆划片(即切割)是半导体芯片制造工艺流程中的一道必不可少的工序,在晶圆制造中属后道工序。将做好芯片的整片晶圆按芯片大小分割成单一的芯片(晶粒),称之为晶圆划片。
半导体器件
4
5
1
2
3
6
传统划片方法---刀片
切割线宽
30~40微米
30~45微米
切割效果
易崩边,破碎
光滑平整,不易破碎
热影响区
较大
较小
残留应力
较大
极小
对晶圆厚度要求
100 um以上
基本无厚度要求
适应性
不同类型晶圆片需更换刀具
可适应不同类型晶圆片
有无损耗
需去离子水,更换刀具,损耗大
损耗很小
成本
成熟工艺成本较低
晶圆激光切割工艺技术
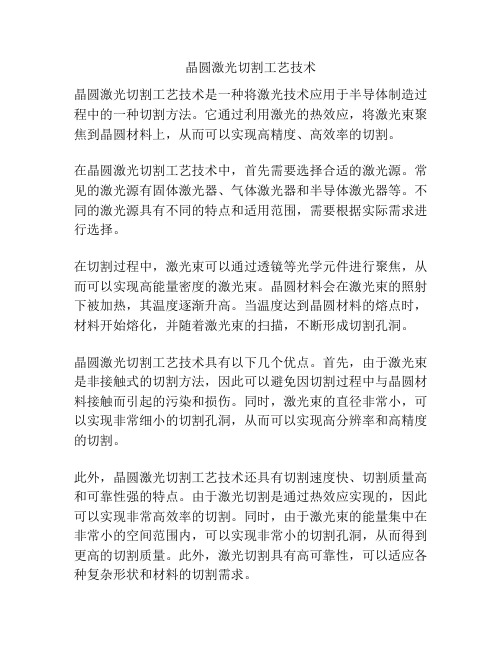
晶圆激光切割工艺技术晶圆激光切割工艺技术是一种将激光技术应用于半导体制造过程中的一种切割方法。
它通过利用激光的热效应,将激光束聚焦到晶圆材料上,从而可以实现高精度、高效率的切割。
在晶圆激光切割工艺技术中,首先需要选择合适的激光源。
常见的激光源有固体激光器、气体激光器和半导体激光器等。
不同的激光源具有不同的特点和适用范围,需要根据实际需求进行选择。
在切割过程中,激光束可以通过透镜等光学元件进行聚焦,从而可以实现高能量密度的激光束。
晶圆材料会在激光束的照射下被加热,其温度逐渐升高。
当温度达到晶圆材料的熔点时,材料开始熔化,并随着激光束的扫描,不断形成切割孔洞。
晶圆激光切割工艺技术具有以下几个优点。
首先,由于激光束是非接触式的切割方法,因此可以避免因切割过程中与晶圆材料接触而引起的污染和损伤。
同时,激光束的直径非常小,可以实现非常细小的切割孔洞,从而可以实现高分辨率和高精度的切割。
此外,晶圆激光切割工艺技术还具有切割速度快、切割质量高和可靠性强的特点。
由于激光切割是通过热效应实现的,因此可以实现非常高效率的切割。
同时,由于激光束的能量集中在非常小的空间范围内,可以实现非常小的切割孔洞,从而得到更高的切割质量。
此外,激光切割具有高可靠性,可以适应各种复杂形状和材料的切割需求。
然而,晶圆激光切割工艺技术也存在一些挑战和难点。
首先,由于激光切割需要对晶圆材料进行加热,因此可能会引起晶圆材料的热应力,从而影响材料的性能和可靠性。
此外,激光切割过程中会产生大量的热量和烟尘,需要进行有效的散热和烟尘处理。
同时,晶圆激光切割工艺技术的设备和操作都需要非常高的技术要求,对操作人员的技术水平和经验要求非常高。
总的来说,晶圆激光切割工艺技术是一种高效、高精度的切割方法,广泛应用于半导体制造领域。
随着激光技术的不断发展和创新,相信晶圆激光切割工艺技术将会越来越成熟和完善,为半导体制造业的发展提供强有力的支持。
晶圆激光划片技术简析
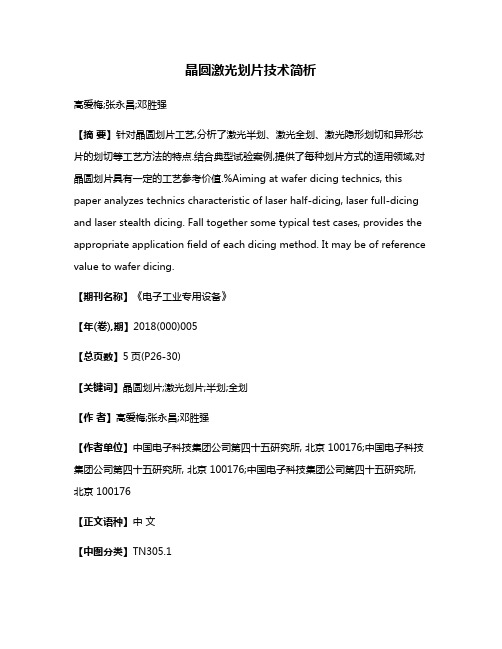
晶圆激光划片技术简析高爱梅;张永昌;邓胜强【摘要】针对晶圆划片工艺,分析了激光半划、激光全划、激光隐形划切和异形芯片的划切等工艺方法的特点.结合典型试验案例,提供了每种划片方式的适用领域,对晶圆划片具有一定的工艺参考价值.%Aiming at wafer dicing technics, this paper analyzes technics characteristic of laser half-dicing, laser full-dicing and laser stealth dicing. Fall together some typical test cases, provides the appropriate application field of each dicing method. It may be of reference value to wafer dicing.【期刊名称】《电子工业专用设备》【年(卷),期】2018(000)005【总页数】5页(P26-30)【关键词】晶圆划片;激光划片;半划;全划【作者】高爱梅;张永昌;邓胜强【作者单位】中国电子科技集团公司第四十五研究所, 北京 100176;中国电子科技集团公司第四十五研究所, 北京 100176;中国电子科技集团公司第四十五研究所, 北京 100176【正文语种】中文【中图分类】TN305.1随着激光器及相关光学元件制造技术的发展,为激光加工设备的开发提供了强大支撑,极大地促进激光微加工应用的广度和深度。
晶圆划片是将制作好图形的晶圆按切割道分割成单一芯片的过程。
随着芯片设计及制造技术的升级,对半导体封装工艺提出新的需求。
如:超薄硅晶圆、低k介质晶圆、含悬梁薄膜结构的微机电系统(MEMS,micro electro mechanical system)器件晶圆、硬脆碳化硅晶圆、软脆碲锌镉晶圆等,使得晶圆划片工艺面临新挑战,需求促进设备加工手段升级。
深紫外LED激光划片工艺论文
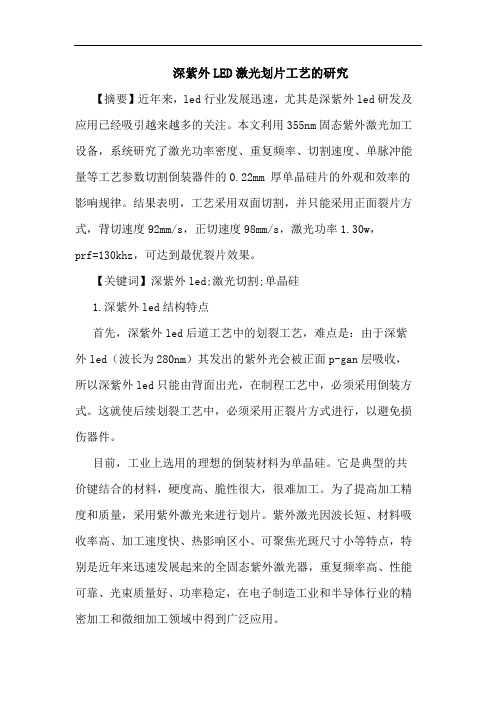
深紫外LED激光划片工艺的研究【摘要】近年来,led行业发展迅速,尤其是深紫外led研发及应用已经吸引越来越多的关注。
本文利用355nm固态紫外激光加工设备,系统研究了激光功率密度、重复频率、切割速度、单脉冲能量等工艺参数切割倒装器件的0.22mm 厚单晶硅片的外观和效率的影响规律。
结果表明,工艺采用双面切割,并只能采用正面裂片方式,背切速度92mm/s,正切速度98mm/s,激光功率1.30w,prf=130khz,可达到最优裂片效果。
【关键词】深紫外led;激光切割;单晶硅1.深紫外led结构特点首先,深紫外led后道工艺中的划裂工艺,难点是:由于深紫外led(波长为280nm)其发出的紫外光会被正面p-gan层吸收,所以深紫外led只能由背面出光,在制程工艺中,必须采用倒装方式。
这就使后续划裂工艺中,必须采用正裂片方式进行,以避免损伤器件。
目前,工业上选用的理想的倒装材料为单晶硅。
它是典型的共价键结合的材料,硬度高、脆性很大,很难加工。
为了提高加工精度和质量,采用紫外激光来进行划片。
紫外激光因波长短、材料吸收率高、加工速度快、热影响区小、可聚焦光斑尺寸小等特点,特别是近年来迅速发展起来的全固态紫外激光器,重复频率高、性能可靠、光束质量好、功率稳定,在电子制造工业和半导体行业的精密加工和微细加工领域中得到广泛应用。
紫外激光加工硅片的研究,国外科研机构起步较早,短波长激光加工硅片的研究和报道的文献较少。
本文利用紫外激光划片设备对深紫外led划硅片工艺进行了深入的研究。
2.实验设备与材料2.1实验设备实验设备激光器采用355nm全固态紫外激光器,最大平均功率2w,重复频率90-150khz,光学系统由扩束镜、全反射镜和聚焦镜组成。
工作台最高速度100mm/s,xy平台定位精度为±3um,xy平台重复精度为±1um,平台旋转精度为±0.001°,定位检测分辨率为±0.5um。
晶圆划片原理
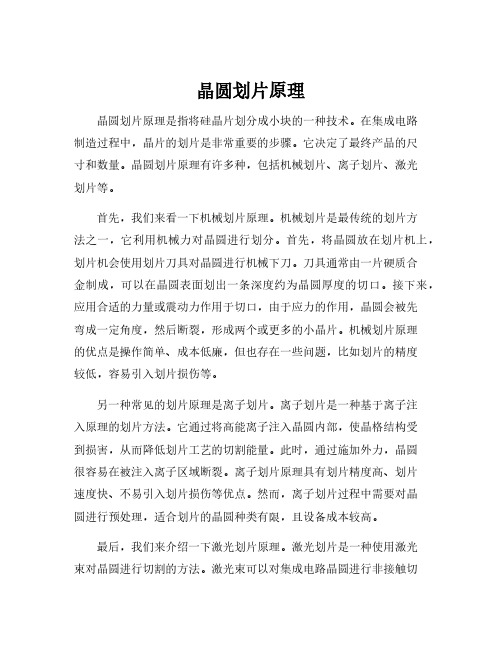
晶圆划片原理晶圆划片原理是指将硅晶片划分成小块的一种技术。
在集成电路制造过程中,晶片的划片是非常重要的步骤。
它决定了最终产品的尺寸和数量。
晶圆划片原理有许多种,包括机械划片、离子划片、激光划片等。
首先,我们来看一下机械划片原理。
机械划片是最传统的划片方法之一,它利用机械力对晶圆进行划分。
首先,将晶圆放在划片机上,划片机会使用划片刀具对晶圆进行机械下刀。
刀具通常由一片硬质合金制成,可以在晶圆表面划出一条深度约为晶圆厚度的切口。
接下来,应用合适的力量或震动力作用于切口,由于应力的作用,晶圆会被先弯成一定角度,然后断裂,形成两个或更多的小晶片。
机械划片原理的优点是操作简单、成本低廉,但也存在一些问题,比如划片的精度较低,容易引入划片损伤等。
另一种常见的划片原理是离子划片。
离子划片是一种基于离子注入原理的划片方法。
它通过将高能离子注入晶圆内部,使晶格结构受到损害,从而降低划片工艺的切割能量。
此时,通过施加外力,晶圆很容易在被注入离子区域断裂。
离子划片原理具有划片精度高、划片速度快、不易引入划片损伤等优点。
然而,离子划片过程中需要对晶圆进行预处理,适合划片的晶圆种类有限,且设备成本较高。
最后,我们来介绍一下激光划片原理。
激光划片是一种使用激光束对晶圆进行切割的方法。
激光束可以对集成电路晶圆进行非接触切割,其原理是通过激光束的热效应,在晶圆上产生局部加热,使局部区域温度升高,从而破坏材料的晶格结构。
接下来,通过外力,晶圆将在切割位置断裂。
激光划片原理具有划片精度高、划片速度快、不易引入划片损伤等优点。
然而,激光划片设备成本较高,使用过程中需要精确控制激光功率和位置,以避免损坏晶圆。
总的来说,晶圆划片原理有多种方法可供选择,每种方法都有其特点和适用范围。
在选择合适的划片方法时,需要综合考虑划片精度、划片速度、成本等因素。
随着集成电路制造工艺的不断进步,晶圆划片技术也在不断发展和创新,为集成电路制造提供了更多选择和可能性。
紫外激光加工技术在硅晶圆中的应用

紫外激光加工技术在硅晶圆中的应用1、紫外激光在晶圆加工中的优势近年来,随着硅片晶圆的发展,国家对半导体行业越来越重视,已经将集成电路作为重点发展的战略产业之一。
在硅晶圆制造过程中,激光加工是非常重要的一项工艺,尤其是紫外激光加工技术。
紫外激光加工称为“光蚀”效应,高能量的光子通过“冷处理”直接破坏材料的化学键,所加工出来的部件具有光滑的边缘和最低限度的炭化。
加之紫外激光能被大多数材料有效地吸收和具有良好的聚焦性能,因此可在很小的空间区域进行精细微加工,从而有着非常广阔的应用前景。
在硅晶圆制程的改进以及碳粉材料参杂的应用下,晶圆的硬度越来越高,对加工的要求也越来越高。
紫外激光加工技术,不仅具有短波长、短脉冲、光束质量优异、高精度、高峰值功率等优势,还能帮助降低成本,提升产能,提高晶圆面积利用率等,因而解决了很多硅晶圆制造上的难题。
比如针对晶圆进行精密划片-尤其是易碎的化合物半导体晶圆如薄硅晶圆,紫外激光能够对硅晶圆进行快速工艺处理。
无论是薄的还是厚的晶圆片,能够保持切口边缘平直、精准、光滑,无边缘碎片,尤其针对价格昂贵的砷化镓(GaAs)晶圆更是如此。
2、紫外激光加工技术在硅晶圆中的应用1)晶圆划片短波长(157-248 nm)准分子和紫外DPSS激光的应用已经提高了裸片的成品率,并且证明了激光工艺比传统金刚石划片工艺更具优越性。
紫外激光工艺的切口(在划片时材料损失的部分)比其他技术的更窄。
再加上前端工艺的应用,紫外激光工艺增加了单位晶圆上所分裂出的合格裸片的数量。
紫外激光切割硅晶圆过程,通常是将整个大块的硅晶圆制作成分成6/8/12/18寸等多规格晶圆,再将晶圆中的晶片切割成一个个小片,再封装到半导体元器件中。
这个工艺制程就需要用到紫外激光切割机,主要是利用物镜作为光斑聚焦镜,通过高密度高能量光束来对晶圆进行划片。
华工激光自主研发的紫外激光晶圆划片机,具有国际先进水平。
采用高质量紫外光作为切割源,切割后的芯片质量和切割效率,远超过刀片切割设备,具有自动对位自动调整装置,提高了自动化程度,操作更加便捷。
晶圆划片蓝膜
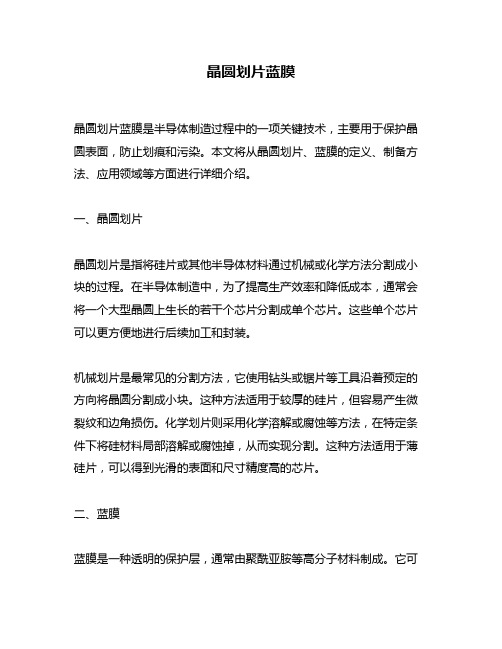
晶圆划片蓝膜晶圆划片蓝膜是半导体制造过程中的一项关键技术,主要用于保护晶圆表面,防止划痕和污染。
本文将从晶圆划片、蓝膜的定义、制备方法、应用领域等方面进行详细介绍。
一、晶圆划片晶圆划片是指将硅片或其他半导体材料通过机械或化学方法分割成小块的过程。
在半导体制造中,为了提高生产效率和降低成本,通常会将一个大型晶圆上生长的若干个芯片分割成单个芯片。
这些单个芯片可以更方便地进行后续加工和封装。
机械划片是最常见的分割方法,它使用钻头或锯片等工具沿着预定的方向将晶圆分割成小块。
这种方法适用于较厚的硅片,但容易产生微裂纹和边角损伤。
化学划片则采用化学溶解或腐蚀等方法,在特定条件下将硅材料局部溶解或腐蚀掉,从而实现分割。
这种方法适用于薄硅片,可以得到光滑的表面和尺寸精度高的芯片。
二、蓝膜蓝膜是一种透明的保护层,通常由聚酰亚胺等高分子材料制成。
它可以覆盖在晶圆表面,保护芯片免受划痕、污染和氧化等影响。
在半导体制造中,蓝膜通常作为划片前的保护层使用。
制备方法主要包括溶液法、浸涂法和喷涂法。
其中溶液法是最常用的方法,它将聚酰亚胺等高分子材料溶解在有机溶剂中,然后通过旋涂或喷涂等方式将其均匀地覆盖在晶圆表面上。
浸涂法则将晶圆浸泡在预先调制好的聚酰亚胺溶液中,使其均匀地吸附在晶圆表面上。
喷涂法则通过高压气体将聚酰亚胺溶液喷射到晶圆表面上。
三、应用领域晶圆划片蓝膜广泛应用于半导体制造领域。
在晶圆加工前,蓝膜可以保护晶圆表面免受划痕和污染。
在晶圆划片过程中,蓝膜可以减少芯片表面的损伤和氧化,从而提高芯片的质量和可靠性。
此外,在芯片封装过程中,蓝膜还可以起到保护作用,防止芯片表面被机械或化学损伤。
除了半导体制造领域外,晶圆划片蓝膜还广泛应用于生物医学、光学器件等领域。
在生物医学领域,晶圆划片蓝膜可以作为细胞培养基质、微流控芯片等材料的基底。
在光学器件领域,晶圆划片蓝膜可以作为玻璃或其他透明材料的保护层。
总之,晶圆划片和蓝膜是半导体制造过程中不可或缺的关键技术。
水切割机高速激光晶圆划片工艺的特点,海德水刀小讲堂

水切割机高速激光晶圆划片工艺的特点,海德水刀小讲堂在划片-裂片工艺中,PCM图形必须设计有直通式划片槽。
金刚石划片工艺不能通过PCM图形进行连续划片。
因而PCM图形必须设计有划片槽。
这就带来了PCM图形测试的问题。
但是,对于激光划片工艺,PCM图形设计已不再是一个问题了。
PCM图形可以设计成有助于当前正在完成的测试项目,而不是有助于裂片方法的要求。
即使没有划片槽,激光划片工艺也不会中断。
采用传统方法裂片时,划片槽上不能有蓝膜或金属残留。
采用锯片切割工艺时,划片槽上的蓝膜/金属残留会增加锯片的磨损,缩短锯片的使用寿命,或者可能在切割时“烧坏”锯片。
在划片-裂片工艺中,划片槽上的蓝膜或金属残留能引起金刚石刀具的跳跃或反弹,从而使某些区域没有产生实际划片操作。
这些区域因而不会在裂片工艺中分裂,这将使晶圆的其余部分不能沿着刀具划过的线条分裂。
划片槽上的蓝膜或金属残留不会影响激光划片工艺的正常进行。
激光工艺能够在蓝膜上划片,这还可以增加光学加工的产能。
传统的裂片工艺花费的时间较多。
例如,裸片尺寸为0.300 mm x 0.360 mm x 4 mil 时,一片晶圆可以切割出大约55,000只裸片。
如果使用锯片(锯片速度= 6.5 mm/s)切割这样一片晶圆,则需要花费大约4个小时;若采用划片-裂片工艺(划片速度= 12.8 mm/s),则需要大约2个小时;但如果采用激光划片工艺(划片速度= 150mm/s),则仅需要大约3分钟。
因而,一套激光划片系统的产能可以取代并超过所有现有的裂片工具产能的总和。
激光划片工艺能够在最后的晶圆自动测试工序中提高产能。
目前,晶圆必须在流片带上伸展开,以防止因裸片相互摩擦而可能发生的芯片丢失。
如果裸片不能均匀地伸展开,则会使测试时间变长,因为必须对每一个裸片进行单独的对准操作以保证自动测试的正确进行。
有时会因为裸片没有对准而对成品率发生影响。
激光划片工艺允许晶圆在薄膜片上进行测试,这就大大地缩短了测试时间,使所有的裸片都能通过自动测试工序。
晶圆划片刀分类

晶圆划片刀分类(最新版)目录1.晶圆划片刀的概述2.晶圆划片刀的分类3.各类晶圆划片刀的特点及应用正文一、晶圆划片刀的概述晶圆划片刀,顾名思义,是一种用于切割晶圆的精密刀具。
在半导体制造过程中,晶圆划片刀发挥着至关重要的作用,它将晶圆按照预定的尺寸和形状进行切割,以便进行后续的封装和测试。
晶圆划片刀的切割质量直接影响到半导体产品的性能和品质。
二、晶圆划片刀的分类根据切割方式和刀片形状,晶圆划片刀主要分为以下几类:1.钻石划片刀钻石划片刀是晶圆划片刀中应用最广泛的一种,其刀片由金刚石或类金刚石材料制成,具有极高的硬度和耐磨性。
钻石划片刀主要通过磨擦和切割的方式将晶圆进行划片。
2.机械划片刀机械划片刀的刀片由硬质合金等金属材料制成,其切割原理是通过刀片与晶圆之间的力学接触,产生划痕并进而实现切割。
相较于钻石划片刀,机械划片刀的切割速度较快,但对晶圆的表面质量有一定影响。
3.激光划片刀激光划片刀是一种采用激光束进行切割的晶圆划片刀。
其主要优势在于切割精度高、速度快,同时对晶圆表面损伤较小。
但激光划片刀的设备投入和技术门槛较高,限制了其广泛应用。
4.电解划片刀电解划片刀是一种通过电解液进行切割的晶圆划片刀。
其切割过程无接触,因此对晶圆表面质量影响较小。
但电解划片刀的切割速度相对较慢,且需要处理电解液,增加了生产过程中的环保压力。
三、各类晶圆划片刀的特点及应用1.钻石划片刀:广泛应用于各类半导体材料的划片,尤其在硅片、蓝宝石片等硬脆材料的切割中表现出色。
2.机械划片刀:适用于对切割速度要求较高,但对表面质量要求相对较低的场合,如 LED 芯片、光电子器件等的制造。
3.激光划片刀:主要应用于对切割精度和速度要求较高的领域,如集成电路芯片的制造等。
4.电解划片刀:适用于对晶圆表面质量要求较高的场合,如 MEMS 器件、光波导器件等的制造。
晶圆划片工艺简介

晶圆划片工艺简介划片工艺流程晶圆经过前道工序后芯片制备完成,还需要经过切割使晶圆上的芯片分离下来,最后进行封装。
不同厚度晶圆选择的晶圆切割工艺也不同:厚度100um以上的晶圆一般使用刀片切割;厚度不到100um的晶圆一般使用激光切割,激光切割可以减少剥落和裂纹的问题,但是在100um以上时,生产效率将大大降低;厚度不到30um的晶圆则使用等离子切割,等离子切割速度快,不会对晶圆表面造成损伤,从而提高良率,但是其工艺过程更为复杂;刀片切割(Blade dicing or blade sawing)刀片切割(锯切)过程中,保护膜的附着与摘除(图片来自网络)为了保护晶圆在切割过程中免受外部损伤,事先会在晶圆上贴敷胶膜,以便保证更安全的“切单”。
“背面减薄(Back Grinding)”过程中,胶膜会贴在晶圆的正面。
但与此相反,在“刀片”切割中,胶膜要贴在晶圆的背面。
而在共晶贴片(Die Bonding,把分离的芯片固定在PCB或定架上)过程中,贴会背面的这一胶膜会自动脱落。
切割时由于摩擦很大,所以要从各个方向连续喷洒DI水(去离子水)。
而且,叶轮要附有金刚石颗粒,这样才可以更好地切片。
此时,切口(刀片厚度:凹槽的宽度)必须均匀,不得超过划片槽的宽度。
很长一段时间,锯切一直是被最广泛使用的传统的切割方法,其最大的优点就是可以在短时间内切割大量的晶圆。
然而,如果切片的进给速度(Feeding Speed)大幅提高,小芯片边缘剥落的可能性就会变大。
因此,应将叶轮的旋转次数控制在每分钟30000次左右。
晶圆划片机晶圆切割时,经常遇到较窄迹道(street)宽度,要求将每一次切割放在迹道中心几微米范围内的能力。
这就要求使用具有高分度轴精度、高光学放大和先进对准运算的设备。
当用窄迹道切割晶圆时,应选择尽可能最薄的刀片。
可是,很薄的刀片(20µm)是非常脆弱的,更容易过早破裂和磨损。
结果,其寿命期望和工艺稳定性都比较厚的刀片差。
晶圆切割uv膜
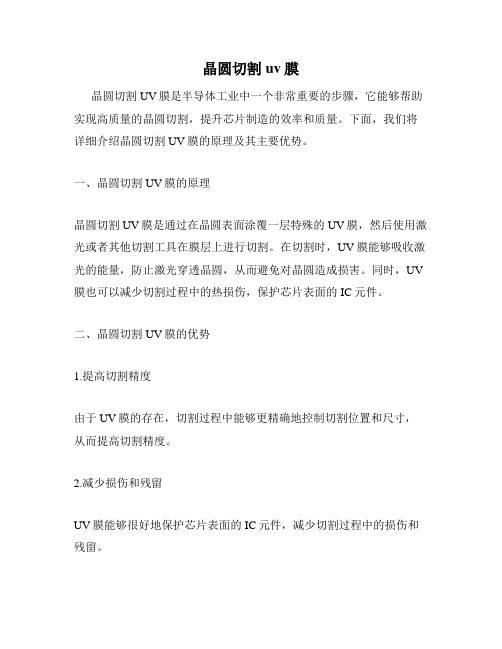
晶圆切割uv膜
晶圆切割UV膜是半导体工业中一个非常重要的步骤,它能够帮助实现高质量的晶圆切割,提升芯片制造的效率和质量。
下面,我们将详细介绍晶圆切割UV膜的原理及其主要优势。
一、晶圆切割UV膜的原理
晶圆切割UV膜是通过在晶圆表面涂覆一层特殊的UV膜,然后使用激光或者其他切割工具在膜层上进行切割。
在切割时,UV膜能够吸收激光的能量,防止激光穿透晶圆,从而避免对晶圆造成损害。
同时,UV 膜也可以减少切割过程中的热损伤,保护芯片表面的IC元件。
二、晶圆切割UV膜的优势
1.提高切割精度
由于UV膜的存在,切割过程中能够更精确地控制切割位置和尺寸,从而提高切割精度。
2.减少损伤和残留
UV膜能够很好地保护芯片表面的IC元件,减少切割过程中的损伤和残留。
3.提高生产效率
晶圆切割UV膜能够提高切割速度和减少切割次数,从而提高生产效率和降低成本。
4.增加安全性
切割时使用UV膜能够避免光污染,减少工作人员的健康风险,增加工作安全性。
以上就是晶圆切割UV膜的原理和优势介绍,通过使用UV膜技术,工业企业能够更好地保护晶圆表面,提升芯片切割质量和生产效率,降低制造成本,同时也能提高工作安全性和人员健康。
圆片等离子划片工艺及其优势

圆片等离子划片工艺及其优势圆片等离子划片工艺是一种先进的半导体加工技术,广泛应用于集成电路、光电子器件、生物芯片等领域。
该工艺通过使用等离子体刻蚀技术,实现对圆片的高精度划片,为微电子制造提供了重要支持。
本文将介绍圆片等离子划片工艺的基本原理、工艺流程以及其在工业应用中的优势。
一、圆片等离子划片的基本原理1.1 等离子体刻蚀技术等离子体刻蚀技术是通过产生高能离子、原子和分子的等离子体,利用其在表面产生的化学反应和物理撞击效应,实现对材料的刻蚀。
在圆片等离子划片工艺中,通常使用的等离子体刻蚀设备包括反应离子刻蚀机(RIE)和平行板等离子体刻蚀机。
1.2 圆片划片的原理圆片划片是指在半导体材料或其他薄膜上划分出所需的小片,以满足特定应用的要求。
等离子体刻蚀技术通过控制离子束的能量、方向和密度,可以实现对材料表面的高精度刻蚀。
在划片过程中,等离子体刻蚀会沿着预定的切割路径进行,形成精确的切割边缘。
二、圆片等离子划片的工艺流程2.1 前处理在进行圆片等离子划片之前,通常需要对切割对象进行前处理。
这包括清洁表面、涂覆光刻胶、曝光光刻胶等步骤,以确保划片的准确性和质量。
2.2 划片过程掩膜定义:利用光刻技术在切割对象表面定义出需要划片的区域。
等离子体刻蚀:使用等离子体刻蚀技术,根据掩膜的定义划出所需形状。
该步骤通过控制离子束实现高精度刻蚀。
2.3 后处理划片过程完成后,需要进行后处理以确保切割表面的质量和平整度。
后处理步骤可能包括清洗、除去光刻胶残留、表面处理等。
三、圆片等离子划片工艺的优势3.1 高精度和高效率圆片等离子划片工艺通过精确控制等离子体刻蚀参数,可以实现对材料的高精度切割,划片边缘清晰。
同时,该工艺具有高效率,适用于批量生产。
3.2 适用性广泛圆片等离子划片工艺不仅适用于半导体材料,还适用于陶瓷、玻璃、金属等多种材料。
这种广泛适用性使其在微电子制造和其他领域中得到了广泛应用。
3.3 可控性强等离子体刻蚀技术具有高度的可控性,可以精确控制刻蚀深度、刻蚀速率和表面质量。
紫外激光在半导体芯片切割中优势的研究

紫外激光在半导体芯片切割中优势的研究摘要:紫外激光加工是指激光束作用于物体表面,引起物体形状或性能改变的过程,它具有无接触、无切削力、热影响区域小、清洁环保等优点。
经过聚焦的激光束具有很高的功率密度,可以瞬间使任何固体材料熔化或蒸发。
激光束的空间和时间可控性好,对加工对象的形状、尺寸及加工环境的要求具有很大的自由度,能够实现多种激光加工工艺。
关键词:紫外激光;半导体芯片切割;优势为了适应不断发展的大规模化生产,从产量和成本角度来看,传统的管芯分离技术也不再实用,紫外激光切割技术将成为具有巨大潜力的应用,他将成了这类应用的关键技术。
1 紫外激光加工特点自20世纪激光器问世不久,激光加工技术就受到人们的重视。
经过50多年的发展,已成为先进制造技术的重要组成部分。
基于激光束单色性好、能量密度高、空间控制性和时间控制性好等优点,目前已广泛应用于材料加工等领域。
其中紫外激光因波长短、材料吸收率高、热影响区小等特点,微加工时容易获得更高的加工精度和质量,已引起电子制造、通讯工程、生物医学、精密机械、航空航天和国防军事等领域工程技术人员的高度重视。
近年来,紫外激光器的应用是工业激光市场增长最快的部分之一,尤其是高功率全固态紫外激光器,具有电光转换效率高、脉冲重复频率高、性能可靠、体积小型、光束质量好、平均功率和单脉冲激光能量稳定等特点,在电子工业精密制造和微细加工领域中占有重要的地位。
红外或可见光波段激光束的加工机理是将光能转变为热能,使物质熔化或蒸发的方式来进行加工。
这种方式不可避免地导致激光能量以热传导和热辐射方式向材料加工区域周围扩散,产生重熔层和热影响区,因而限制了微细加工边缘质量和精度。
紫外激光由于光子能量高,在与高分子聚合物材料作用时,可将光能转变为光化学能直接破坏部分连接物质原子或分子组分的化学键,达到去除材料的目的。
这种将物质分离成原子的过程是一个光化学作用的冷过程,对加工区域周边几乎无热损伤,可获得极高的加工质量和加工尺寸精度。
- 1、下载文档前请自行甄别文档内容的完整性,平台不提供额外的编辑、内容补充、找答案等附加服务。
- 2、"仅部分预览"的文档,不可在线预览部分如存在完整性等问题,可反馈申请退款(可完整预览的文档不适用该条件!)。
- 3、如文档侵犯您的权益,请联系客服反馈,我们会尽快为您处理(人工客服工作时间:9:00-18:30)。
力夹在了那本书里,还给了袁慕野。木子不再是那个什么不懂的小女孩了,她知
时间变长,因为必须对每一个裸片进行单独的对 准操作以保证自动测试的正确进行。有时会因为 裸片没有对准而对成品率发生影响。激光划片工 艺允许晶圆在薄膜片上进行测试,这就大大地缩 短了测试时间,使所有的裸片都能通过自动测试 工序。
在所有窄带紫外光源中准分子激光器所提 供的功率最大、波长最短(351,308,248,193,以 及 157nm)。准分子激光的光子成本低于 DPSS 激
光,但是,其系统的复杂度较高且存在维护难和 其他问题,因此并不是晶圆切割工艺的理想选 择。准分子激光的优势在于微机械加工、大面积 图案转移和大量平行区域的分步重复工艺。而紫 外 DPSS 激光则更适于晶圆划片应用。借助于准 分子激光(193nm),JPSA能在一个小时内处理3片 晶圆,每片成本为 8 美元,系统正常运行时间为 97%。这是准分子激光系统所能达到的非常好的 性能状态。而一个优化的紫外 DPSS 激光(266nm) 系统每小时能处理 7 到 10 片晶圆,每片成本低于 1.50 美元,正常运行时间﹥99.9%。这两种工艺已 经在多台设备上,每周 7 天/每天 24 小时地连续
力集中,但这种应力很容易消除。
激光工艺的优点
在划片-裂片工艺中,PCM 图形必须设计有直 通式划片槽。金刚石划片工艺不能通过 PCM 图形 进行连续划片。因而 PCM 图形必须设计有划片槽。 这就带来了 PCM 图形测试的问题。但是,对于激 光划片工艺,PCM 图形设计已不再是一个问题了。 PCM 图形可以设计成有助于当前正在完成的测试 项目,而不是有助于裂片方法的要求。即使没有 划片槽,激光划片工艺也不会中断。
激光能对所有第 III-V 主族材料包括第 IV 主族 材料如硅(Si)和锗(Ge)的晶圆进行快速工艺处 理。无论是薄的还是厚的晶圆片,切口宽度均小 于 3 微米,切口边缘平直、精准、光滑,没有边缘 碎片,尤其砷化镓(GaAs)晶圆更是如此。砷化镓 晶圆昂贵,所以晶圆面积价值非常高。采用紫外 激光划片工艺使得切口更紧密、更精细并且更光 滑,能够在每片晶圆上分裂出更多数量的裸片, 并因为损坏的裸片非常少而获得更高的成品率。
传统的裂片工艺花费的时间较多。例如,裸
片尺寸为 0.300mmx0.360mmx4mil时,一片晶圆可 以切割出大约 55,000 只裸片。如果使用锯片(锯 片速度=6.5mm/s)切割这样一片晶圆,则需要花 费大约 4 个小时;若采用划片-裂片工艺(划片速 度=12.8mm/s),则需要大约 2 个小时;但如果采用 激光划片工艺(划片速度=150mm/s),则仅需要大 约 3 分锺。因而,一套激光划片系统的产能可以 取代并超过所有现有的裂片工具产能的总和。
对这些不同波长的激光所进行的开发,使它 们特别适合于晶圆切割应用。这些激光在 JPSA
力夹在了那本书里,还给了袁慕野。木子不再是那个什么不懂的小女孩了,她知
上用于切割蓝色 LED(发光二极管)和蓝宝石晶圆, 其速度为 75mm/s。每小时晶圆处理能力超过 9 片 (标准 2 英寸晶圆,裸片尺寸 350μ m×350μ m), 切口却很小(﹤3μ m)。激光工艺具有产能高、对 LED 性能影响小的特点,容许晶圆的形变和弯曲, 其切割速度远高于传统机械切割方法。对于第 III-V 主族半导体,例如砷化镓(GaAs)和磷化铟 (InP),典型的切口深度为 40μ m,切割速度为 150mm/s 以上。
采用传统方法裂片时,划片槽上不能有蓝膜
力夹在了那本书里,还给了袁慕野。木子不再是那个什么不懂的小女孩了,她知
或金属残留。采用锯片切割工艺时,划片槽上的 蓝膜/金属残留会增加锯片的磨损,缩短锯片的 使用寿命,或者可能在切割时“烧坏”锯片。在 划片-裂片工艺中,划片槽上的蓝膜或金属残留 能引起金刚石刀具的跳跃或反弹,从而使某些区 域没有产生实际划片操作。这些区域因而不会在 裂片工艺中分裂,这将使晶圆的其余部分不能沿 着刀具划过的线条分裂。划片槽上的蓝膜或金属 残留不会影响激光划片工艺的正常进行。激光工 艺能够在蓝膜上划片,这还可以增加光学加工的 产能。
裸片尺寸的减小已经把某些产品的宽高比 降低到 2:1,有效地提高了机械式划片-裂片系统 的额定能力的极限。有时候因为不需要裂片而使 芯片获得较高的成品率。晶圆切割机速度低,能
力夹在了那本书里,还给了袁慕野。木子不再是那个什么不懂的小女孩了,她知
造成裸片边缘的破碎,有时还可能因此而毁掉裸 片。狭窄(30 微米宽)的划片槽要求锯片有非常薄 的厚度,而这又使得锯片很容易磨损。
1ci0f6c7b 金世豪/
紫外激光带来更高的成品率
短波长(157-248nm)准分子和紫外 DPSS 激光 的应用已经提高了裸片的成品率,并且证明了激 光工艺比传统金刚石划片工艺更具优越性。紫外 激光工艺的切口(在划片时材料损失的部分)比 其他技术的更窄。再加上前端工艺的应用,紫外 激光工艺增加了单位晶圆上所分裂出的合格裸 片的数量。
紫外激光加工称为“光蚀”效应,高能量的 光子通过“冷处理”直接破坏材料的化学键,所 加工出来的部件具有光滑的边缘和最低限度的 炭化。加之紫外激光能被大多数材料有效地吸收 和具有良好的聚焦性能,因此其可在很小的空间 区域进行精细微加工,从而有着非常高的研究价 值和广阔的应用前景。
紫外激光晶圆划片工艺
用紫外(UV)激光对晶圆进行精密划片是晶 圆-尤其是易碎的化合物半导体晶圆如薄硅晶圆 -划片裂片的替代工艺。二极管泵浦固态(DPSS)
新型窄脉宽、短波长紫外 DPSS 激光提供了 极大的工艺灵活性,它可以调整脉冲形状、重复 率、色谱、光束质量等等。谐波生成技术使更短 波长的激光能够用于处理各种不同的材料。DPSS 激光具有极好的光束质量和最高的重复率,并具 有精细工艺所要求的最小光束直径。典型 地,JPSA 使用的 DPSS 激光是钒酸盐(Nd:YVO4)基 激光器产生的。所输出的红外(IR)激光的光束直 径约为 1μ m。高效的频率转换能力使输出激光在 355nm 和 266nm 波长处,有数瓦的可用输出功率。
域。整个晶圆因此而节省了很大的面积。
对于砷化镓(GaAs)晶圆,裂片工艺有两种: 非接触式(裸露的气桥)和接触式。每一种裂片方 法都有一个宽高比参数,是由设备制造商标示的, 定义为裸片厚度断面的长度/宽度。一个特定的 晶圆切割机划片-裂片系统标示的宽高比,对于 非接触式裂片方法为 7:1,接触式裂片为 3:1。
采用砷化镓(GaAs)芯片的高频电子线路要 求芯片在电路板上有精确的几何位置布局,以减 少气桥和阻抗失配。整齐、精确的芯片要求裸片
力夹在了那本书里,还给了袁慕野。木子不再是那个什么不懂的小女孩了,她知
的位置布局更精确、整体封装更好以及电气性能 更佳。
在巿场需求驱动下,裸片成本不断降低,尺 寸越来越小。裸片尺寸的减小正在给划片-裂片 工艺带来新的问题。划片槽宽度从 100 微米降到 30 微米,裸片尺寸也随之减小。30 微米的尺寸超 出了传统锯片切割工艺允许的极限。采用激光划 片工艺后,划片槽宽度进一步降低到 15-20 微米。 另外,被称为“拉练”(用于阻止表面裂纹发生) 的区域也被省掉了。由于划片槽宽度的减小“、 拉 练”空间的节省以及下列所述的设计规则的缘故, 每个裸片的每个边都要节省约 24 微米的晶圆区
结论:相对于机械式划片工艺,紫外激光工 艺具有更多优点。这些优点包括消耗成本低、维 护费用少、产能高、晶圆面积利用率高等。激光 工艺更易于进行自动化操作,从而降低人力成 本。紫外激光技术还有很大的待开发潜能,因而 该工艺将会继续发展。我们预言激光工艺将在单
位晶圆裸片数量和缩短投资回收期方面有进一 步的发展。
力夹在了那本书里,还给了袁慕野。木子不再是那个什么不懂的小女孩了,她知
运行了一年半并通过测试,准分子激光系统的单 独测试时间甚至更长。
材料的去除工艺被称为激光剥蚀,这是一种 以微量材料吸收高能激光划片工艺需要更大的晶圆 弯曲形变,从而会造成裸片边缘的不“整齐”。实 际上,金刚石划片工艺在整个工艺过程中会产生 机械应力。而非机械式的、无热能的激光划片工 艺在材料内部根本不产生任何应力。紫外激光所 产生的陡峭的 V 形切口会在其尖端产生很强的应