新一代晶圆划片技木
碳化硅晶圆划片技术

碳化硅晶圆划片技术碳化硅是宽禁带半导体器件制造的核心材料,SiC器件具有高频、大功率、耐高温、耐辐射、抗干扰、体积小、重量轻等诸多优势,是目前硅和砷化镓等半导体材料所无法比拟的,应用前景十分广阔,是核心器件发展需要的关键材料。
1、碳化硅材料特性碳化硅是ⅠⅤ-ⅠⅤ族二元化合物半导体,具有很强的离子共价键,结合能量稳定,具有优越的力学、化学性能。
材料带隙即禁带能量决定了器件很多性能,包括光谱响应、抗辐射、工作温度、击穿电压等,碳化硅禁带宽度大。
如最常用的4H-SiC禁带能量是 3.23eV,因此,具有良好的紫外光谱响应特性,被用于制作紫外光电二极管。
SiC临界击穿电场比常用半导体硅和砷化镓大很多,其制作的器件具有很好的耐高压特性。
另外,击穿电场和热导率决定器件的最大功率传输能力,SiC热导率高达5W/(cm·K),比许多金属还要高,因此非常适合做高温、大功率器件和电路。
碳化硅热稳定性很好,可以工作在300~600℃。
碳化硅硬度高,耐磨性好,常用来研磨或切割其它材料,这就意味着碳化硅衬底的划切非常棘手。
目前,用于制作电子器件的碳化硅晶圆主要有2种,N型导电晶圆厚度150~350μm,电阻率0.010~0.028Ω·cm2,主要应用于发光二极管、电力电子行业的功率器件。
高纯半绝缘晶圆厚度50~100μm,电阻率1×108Ω·cm2,主要用于微波射频、氮化镓晶体管等领域。
针对半导体行业应用的SiC晶圆划切,研究几种加工方法的特点及应用。
2、碳化硅晶圆划片方法1)砂轮划片砂轮划片机是通过空气静压电主轴驱动刀片高速旋转,实现对材料的强力磨削。
所用的刀片刃口镀有金刚砂颗粒,金刚砂的莫氏硬度为10级,仅仅比硬度9.5级的SiC略高一点,反复地低速磨削不仅费时,而且费力,同时也会造成刀具频繁磨损。
如:100mm(4英寸)SiC晶圆划切每片需要6~8h,且易造成崩边缺陷。
因此,这种传统的低效加工方式已经逐渐被激光划片取代。
多芯片晶圆划片

多芯片晶圆划片随着集成电路技术的不断进步,晶圆划片这项技术也得到了快速发展。
多芯片晶圆划片作为其中的一种划片方式,已经成为了当前半导体工业中的重要制造技术之一。
多芯片晶圆划片是指将一个晶圆上的多个芯片分离出来,以单个芯片的形式进行贴片生产的一种技术。
相对于单一芯片晶圆划片,多芯片晶圆划片的优点在于可以在同一晶圆上生产多种不同的芯片,降低了制造成本,提高了生产效率。
此外,其还可以减少不必要的硅片浪费和化学废液,对环境造成的影响更小。
多芯片晶圆划片的实现需要借助于先进的微电子制造技术。
在晶圆制造过程中,通常需要对晶圆进行薄化处理和抛光处理,以满足后续划片工序的需要。
此外,多芯片晶圆划片还需要使用先进的离线锯切技术,以保证划片后的芯片尺寸、形状和表面平整度等要求。
在实际应用中,多芯片晶圆划片的主要应用领域为物联网、智能终端、通信设备、汽车电子、医疗电子等。
在这些领域中,由于产品体积小、功耗低、生产周期短等特点,对于芯片生产的需求往往十分迫切,而多芯片晶圆划片则能够有效地满足这些需求。
尽管多芯片晶圆划片技术具有广泛的应用前景和较高的市场需求,但其在实际生产过程中仍存在一定的挑战和困难。
例如,在锯切过程中容易出现晶圆表面开裂、封装孔钻位偏差、芯片间平行度不一致等问题,这些问题都需要通过进一步的技术改进和工艺优化来解决。
综上所述,多芯片晶圆划片技术在半导体工业中的应用前景十分广阔,尤其是在物联网、智能终端等领域的发展中具有至关重要的意义。
虽然在实际生产过程中面临着一些技术难题,但通过不断的创新和改进,相信多芯片晶圆划片技术会在未来发挥越来越重要的作用。
晶圆研磨划片流程说明
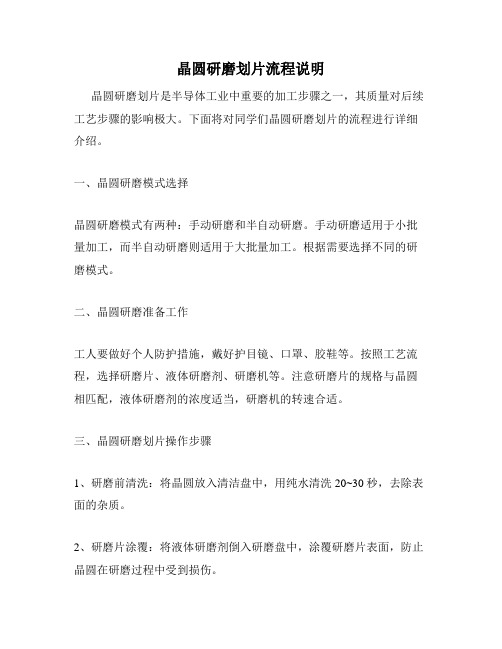
晶圆研磨划片流程说明晶圆研磨划片是半导体工业中重要的加工步骤之一,其质量对后续工艺步骤的影响极大。
下面将对同学们晶圆研磨划片的流程进行详细介绍。
一、晶圆研磨模式选择晶圆研磨模式有两种:手动研磨和半自动研磨。
手动研磨适用于小批量加工,而半自动研磨则适用于大批量加工。
根据需要选择不同的研磨模式。
二、晶圆研磨准备工作工人要做好个人防护措施,戴好护目镜、口罩、胶鞋等。
按照工艺流程,选择研磨片、液体研磨剂、研磨机等。
注意研磨片的规格与晶圆相匹配,液体研磨剂的浓度适当,研磨机的转速合适。
三、晶圆研磨划片操作步骤1、研磨前清洗:将晶圆放入清洁盘中,用纯水清洗20~30秒,去除表面的杂质。
2、研磨片涂覆:将液体研磨剂倒入研磨盘中,涂覆研磨片表面,防止晶圆在研磨过程中受到损伤。
3、晶圆放置:将晶圆放到涂有液体研磨剂的研磨片上。
4、研磨:按照研磨机的要求,启动研磨机进行研磨。
研磨的过程中粒度逐渐减小,对晶圆的要求也越来越高。
5、反面研磨:研磨一侧时,需要翻转晶圆进行反面研磨,防止研磨出现不均匀。
6、精磨:对研磨后的晶圆进行精磨,磨削表面,提高表面光洁度。
7、划片:将晶圆用切割机进行切割,得到所需的芯片。
四、晶圆研磨划片质量控制晶圆研磨划片过程中,需要严格控制质量。
研磨后的晶圆表面应该平整光滑,不应有划痕、凹陷和其他缺陷。
芯片的尺寸、设计、位置等参数也需要认真测量和检查。
总之,晶圆研磨划片是制备半导体芯片不可或缺的一步,需要进行科学合理的操作和严格的质量控制。
希望同学们在掌握流程的基础上,不断提高技能水平,为半导体工业的发展做出贡献。
晶圆减薄划片的发展
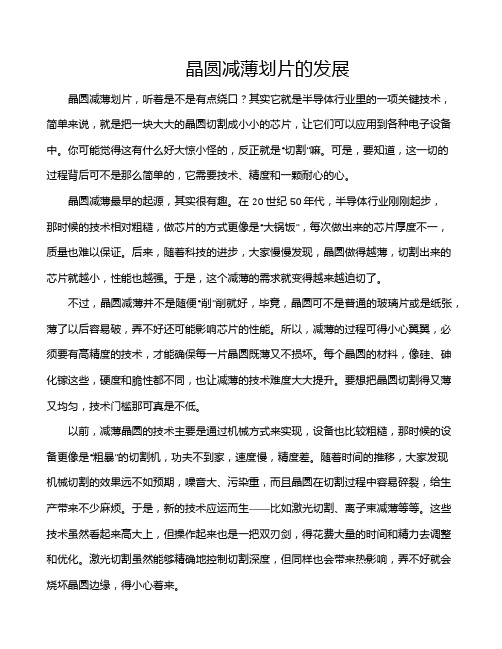
晶圆减薄划片的发展晶圆减薄划片,听着是不是有点绕口?其实它就是半导体行业里的一项关键技术,简单来说,就是把一块大大的晶圆切割成小小的芯片,让它们可以应用到各种电子设备中。
你可能觉得这有什么好大惊小怪的,反正就是“切割”嘛。
可是,要知道,这一切的过程背后可不是那么简单的,它需要技术、精度和一颗耐心的心。
晶圆减薄最早的起源,其实很有趣。
在20世纪50年代,半导体行业刚刚起步,那时候的技术相对粗糙,做芯片的方式更像是“大锅饭”,每次做出来的芯片厚度不一,质量也难以保证。
后来,随着科技的进步,大家慢慢发现,晶圆做得越薄,切割出来的芯片就越小,性能也越强。
于是,这个减薄的需求就变得越来越迫切了。
不过,晶圆减薄并不是随便“削”削就好,毕竟,晶圆可不是普通的玻璃片或是纸张,薄了以后容易破,弄不好还可能影响芯片的性能。
所以,减薄的过程可得小心翼翼,必须要有高精度的技术,才能确保每一片晶圆既薄又不损坏。
每个晶圆的材料,像硅、砷化镓这些,硬度和脆性都不同,也让减薄的技术难度大大提升。
要想把晶圆切割得又薄又均匀,技术门槛那可真是不低。
以前,减薄晶圆的技术主要是通过机械方式来实现,设备也比较粗糙,那时候的设备更像是“粗暴”的切割机,功夫不到家,速度慢,精度差。
随着时间的推移,大家发现机械切割的效果远不如预期,噪音大、污染重,而且晶圆在切割过程中容易碎裂,给生产带来不少麻烦。
于是,新的技术应运而生——比如激光切割、离子束减薄等等。
这些技术虽然看起来高大上,但操作起来也是一把双刃剑,得花费大量的时间和精力去调整和优化。
激光切割虽然能够精确地控制切割深度,但同样也会带来热影响,弄不好就会烧坏晶圆边缘,得小心着来。
再说说划片,这个词听起来像是简单的“切片”,其实并不简单。
划片是在减薄后的晶圆上,按照预设的线路,将晶圆切割成一个个小芯片,这个过程比减薄更加复杂。
你可以想象,把一块厚厚的巧克力蛋糕切成一片一片,不仅要切得均匀,还得保证每一片都完好无损,不能有碎屑,也不能让蛋糕因为切割过度而变形。
晶圆划片工艺流程

晶圆划片工艺流程晶圆划片工艺流程是半导体芯片制造过程中的重要环节,它将大尺寸的晶圆划分为多个小尺寸的芯片。
本文将详细介绍晶圆划片工艺流程的各个步骤。
一、晶圆清洗在划片之前,需要对晶圆进行清洗,以去除表面的杂质和污染物。
清洗晶圆的方法通常包括浸泡、喷洗和超声波清洗等。
清洗后的晶圆表面应该干净无尘,以确保后续工艺的顺利进行。
二、划片布局在划片之前,需要对晶圆进行布局设计,确定每个芯片的位置和大小。
布局设计要考虑到芯片的尺寸、间距和切割线的方向等因素,以最大限度地提高晶圆的利用率。
三、划片划线划片划线是将晶圆划分为多个小芯片的关键步骤。
划片划线通常使用激光划线机进行,激光束在晶圆表面划出所需的切割线。
划线的参数要根据芯片的尺寸和形状进行调整,以确保划片的准确性和效率。
四、划片切割划片切割是将晶圆沿着划线切割成多个小芯片的过程。
切割通常使用划片锯进行,切割锯通过旋转锯片来切割晶圆。
切割时要控制好锯片的速度和切割力度,以避免损伤芯片或晶圆。
五、划片检测在划片完成后,需要对划片的质量进行检测。
划片检测主要包括芯片尺寸、芯片间距和切割线的平直度等方面的检查。
通过检测,可以确保划片的质量符合要求,并及时发现并修复可能存在的问题。
六、划片清洗划片完成后,需要对切割后的芯片进行清洗,以去除切割过程中产生的杂质和污染物。
划片清洗的方法和初始清洗类似,但要更加细致和精确,以确保芯片表面的干净无尘。
七、划片测试在划片完成后,需要对芯片进行测试,以确保其电性能和可靠性符合要求。
划片测试通常包括电性能测试、可靠性测试和封装测试等。
通过测试,可以筛选出不合格的芯片,并保证出货的产品质量。
八、划片分选在划片测试完成后,需要对芯片进行分选,将合格的芯片和不合格的芯片分开。
分选通常使用分选机进行,分选机通过光学检测和机械分选的方式,将芯片按照一定的规则进行分类和分离。
九、划片封装在划片分选完成后,需要对芯片进行封装,以保护芯片表面的电路和结构。
新一代晶圆划片技木
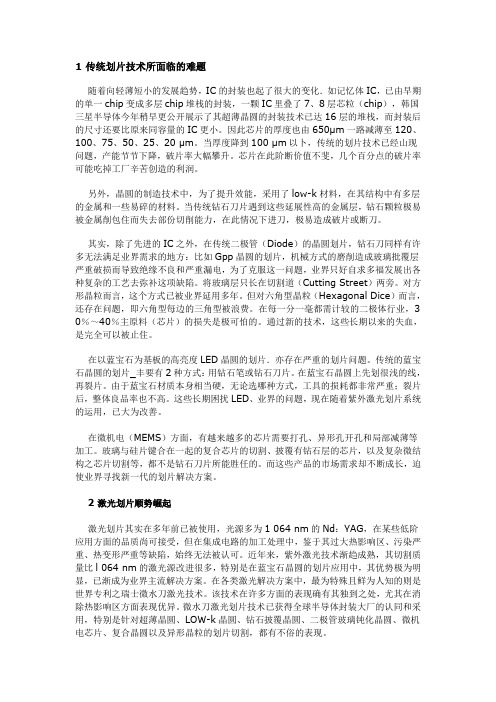
1 传统划片技术所面临的难题随着向轻薄短小的发展趋势,IC的封装也起了很大的变化.如记忆体IC,已由早期的单一chip变成多层chip堆栈的封装,一颗IC里叠了7、8层芯粒(chip),韩国三星半导体今年稍早更公开展示了其超薄晶圆的封装技术已达16层的堆栈,而封装后的尺寸还要比原来同容量的IC更小。
因此芯片的厚度也由650μm一路减薄至120、100、75、50、25、20 μm。
当厚度降到100 μm以卜,传统的划片技术已经山现问题,产能节节下降,破片率大幅攀升。
芯片在此阶断价值不斐,几个百分点的破片率可能吃掉工厂辛苦创造的利润。
另外,晶圆的制造技术中,为了提升效能,采用了low-k材料,在其结构中有多层的金属和一些易碎的材料。
当传统钻石刀片遇到这些延展性高的金属层,钻石颗粒极易被金属削包住而失去部份切削能力,在此情况下进刀,极易造成破片或断刀。
其实,除了先进的IC之外,在传统二极管(Diode)的晶圆划片,钻石刀同样有许多无法满足业界需求的地方:比如Gpp晶圆的划片,机械方式的磨削造成玻璃批覆层严重破损而导致绝缘不良和严重漏电,为了克服这一问题,业界只好自求多福发展出各种复杂的工艺去弥补这项缺陷。
将玻璃层只长在切割道(Cutting Street)两旁。
对方形晶粒而言,这个方式已被业界延用多年。
但对六角型晶粒(Hexagonal Dice)而言,还存在问题,即六角型每边的三角型被浪费。
在每一分一毫都需计较的二极体行业,3 0%~40%主原料(芯片)的损失是极可怕的。
通过新的技术,这些长期以来的失血,是完全可以被止住。
在以蓝宝石为基板的高亮度LED晶圆的划片.亦存在严重的划片问题。
传统的蓝宝石晶圆的划片_丰要有2种方式:用钻石笔或钻石刀片。
在蓝宝石晶圆上先划很浅的线,再裂片。
由于蓝宝石材质本身相当硬,无论选哪种方式,工具的损耗都非常严重;裂片后,整体良品率也不高。
这些长期困扰LED、业界的问题,现在随着紫外激光划片系统的运用,已大为改善。
砷化镓 晶圆划片

砷化镓晶圆划片
砷化镓晶圆划片是将砷化镓晶圆切割成单个芯片的过程。
这个过程对于半导体制造至关重要,因为它决定了芯片的尺寸、形状和最终性能。
在砷化镓晶圆划片过程中,通常使用一种称为"锯切"或"划线"的技术。
该技术使用高速旋转的金刚石锯片或激光束,在晶圆表面划出一系列平行线,将晶圆分割成多个芯片。
这个过程需要高度的准确性和精度,以确保每个芯片的尺寸和形状都符合设计要求。
为了实现高精度的划片,需要使用先进的设备和技术。
这些设备包括高性能的锯床、激光划片机和自动化的晶圆处理系统。
此外,还需要使用先进的控制系统和传感器,以确保划片过程的准确性和一致性。
在划片过程中,还需要考虑到晶圆的材料特性和结构。
砷化镓晶圆相对较脆,容易出现裂纹和破损,因此需要采用适当的工艺和参数来减少这些问题的发生。
总之,砷化镓晶圆划片是半导体制造过程中至关重要的一步,它需要高度的准确性、精度和专业知识。
随着技术的不断发展,划片技术也在不断改进和创新,以满足不断增长的半导体市场需求。
晶圆贴膜金刚刀划片工艺
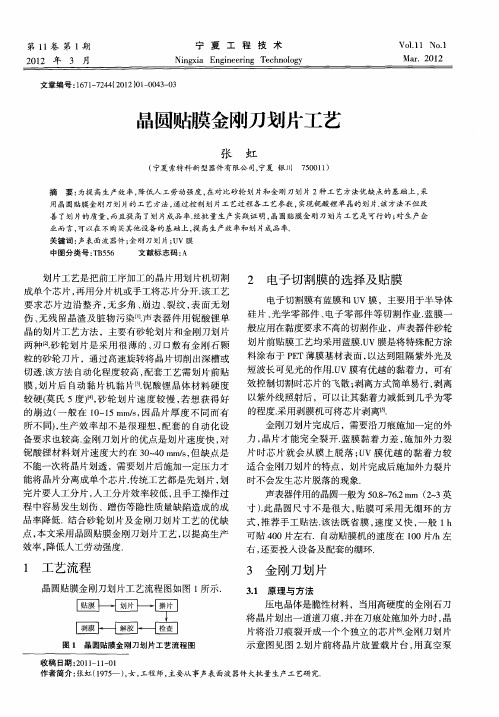
1 工艺流程
晶圆贴膜 金 刚刀划 片工 艺 流程 图如 图 1 所示 .
3 金 刚刀划 片
31 原 理与 方法
.
压电晶体是脆性材料 ,当用高硬度的金刚石刀
将 晶 片划 出一道 道刀 痕 , 在刀 痕处 施加 外力 时 , 并 晶
图 1 晶圆贴膜 金刚刀划 片工艺流程图
收稿 日期 :0 1 1 — 1 2 1- 10
第1 1卷 第 1 期
21 年 3 月 02
文章 编 号 :6 17 4 (0 2 0 — 0 3 0 17 — 24 2 1 )1 0 4 — 3
夏 工 程 技 术
E gn e i g e h oo y n i e r T c n l g n
Vo . 1 11 No 1 . Ma .2 2 r 01
效控制切割时芯片的飞散 ; 剥离方式简单易行 , 剥离 以紫外 线照射 后 ,可 以让其 黏着 力减 低到 几乎 为零
的程 度 . 用剥膜 机 可将 芯片 剥离I 采 5 1 . 金 刚刀划 片完 成后 ,需 要沿 刀痕施 加 一定 的外 力, 晶片 才 能完 全 裂 开 . 膜 黏着 力 差 , 蓝 施加 外 力 裂 片 时 芯 片 就会 从 膜 上脱 落 ; V膜 优 越 的 黏 着 力 较 U 适 合 金 刚刀划 片 的特 点 ,划 片完 成后施 加外 力裂 片
片将沿刀痕裂开成一个个独立 的芯片嘲金刚刀划片 . 示 意 图见 图 2 片前 将 晶 片放 置 载 片 台 , 真 空 泵 0 用
作者 简介 : 张虹(95 )女 , 17~ , 工程师 , 主要从事声表面波器件大批 量生产工艺研 究
宁
夏
工
程
技
术
晶圆划片原理
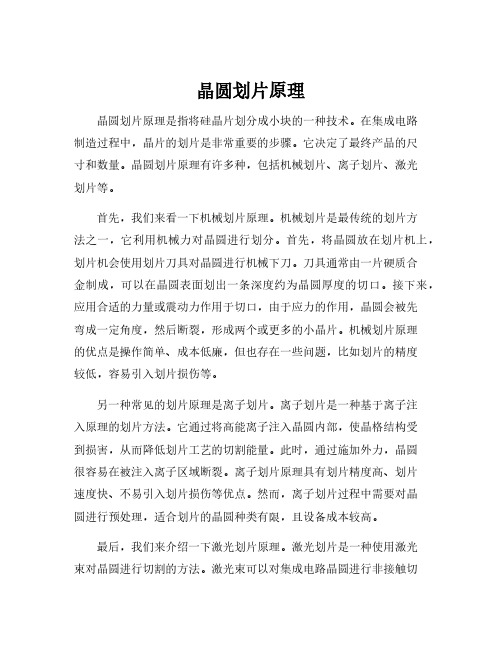
晶圆划片原理晶圆划片原理是指将硅晶片划分成小块的一种技术。
在集成电路制造过程中,晶片的划片是非常重要的步骤。
它决定了最终产品的尺寸和数量。
晶圆划片原理有许多种,包括机械划片、离子划片、激光划片等。
首先,我们来看一下机械划片原理。
机械划片是最传统的划片方法之一,它利用机械力对晶圆进行划分。
首先,将晶圆放在划片机上,划片机会使用划片刀具对晶圆进行机械下刀。
刀具通常由一片硬质合金制成,可以在晶圆表面划出一条深度约为晶圆厚度的切口。
接下来,应用合适的力量或震动力作用于切口,由于应力的作用,晶圆会被先弯成一定角度,然后断裂,形成两个或更多的小晶片。
机械划片原理的优点是操作简单、成本低廉,但也存在一些问题,比如划片的精度较低,容易引入划片损伤等。
另一种常见的划片原理是离子划片。
离子划片是一种基于离子注入原理的划片方法。
它通过将高能离子注入晶圆内部,使晶格结构受到损害,从而降低划片工艺的切割能量。
此时,通过施加外力,晶圆很容易在被注入离子区域断裂。
离子划片原理具有划片精度高、划片速度快、不易引入划片损伤等优点。
然而,离子划片过程中需要对晶圆进行预处理,适合划片的晶圆种类有限,且设备成本较高。
最后,我们来介绍一下激光划片原理。
激光划片是一种使用激光束对晶圆进行切割的方法。
激光束可以对集成电路晶圆进行非接触切割,其原理是通过激光束的热效应,在晶圆上产生局部加热,使局部区域温度升高,从而破坏材料的晶格结构。
接下来,通过外力,晶圆将在切割位置断裂。
激光划片原理具有划片精度高、划片速度快、不易引入划片损伤等优点。
然而,激光划片设备成本较高,使用过程中需要精确控制激光功率和位置,以避免损坏晶圆。
总的来说,晶圆划片原理有多种方法可供选择,每种方法都有其特点和适用范围。
在选择合适的划片方法时,需要综合考虑划片精度、划片速度、成本等因素。
随着集成电路制造工艺的不断进步,晶圆划片技术也在不断发展和创新,为集成电路制造提供了更多选择和可能性。
芯片划片工艺

芯片划片工艺
芯片划片工艺是指将整个晶圆锯割成多个芯片的过程。
具体步骤如下:
1. 选用划片设备:通常采用切割机进行划片操作。
切割机配有锯片,根据需求可调整切割速度和锯片尺寸。
2. 准备晶圆:将待划片的晶圆进行清洗,去除表面杂质,并进行良率和产品布局的检验。
3. 标记划片位置:在晶圆上进行标记,确定划片位置和方向,以确保划片的准确性。
4. 划片过程:将标记好的晶圆放入切割机,启动划片过程。
切割机将按照事先设定的参数进行切割,通过旋转切割盘使锯片划过晶圆。
5. 粗磨与精磨:划片后,芯片表面可能存在一些不平整,需进行粗磨和精磨处理,使芯片达到平整的要求。
6. 清洗和检验:对划片后的芯片进行清洗,去除切割产生的碎片和杂质。
然后对芯片进行外观检验和性能测试,以确保划片后的芯片质量符合要求。
7. 封装和测试:通过封装将芯片与外部部件连接,形成完整的芯片封装器件。
最后进行芯片测试,包括电性能测试和可靠性测试等,以保证芯片品质。
总的来说,芯片划片工艺是将整个晶圆划分成多个芯片的过程,通过一系列的步骤实现划片、磨削、清洗、检验和封装等工艺,最终得到成品芯片。
晶圆划片蓝膜
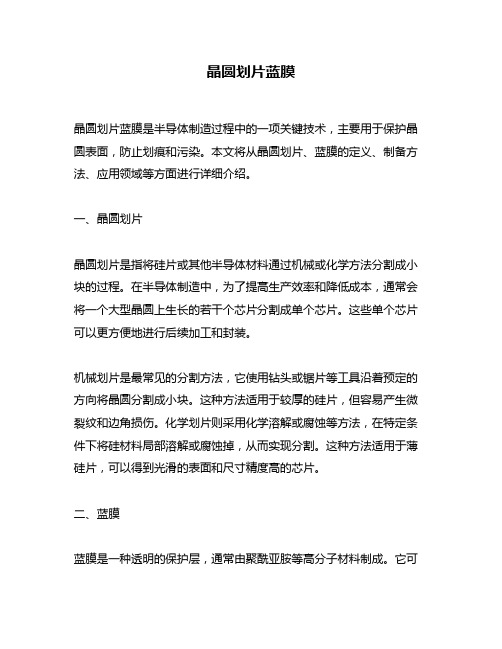
晶圆划片蓝膜晶圆划片蓝膜是半导体制造过程中的一项关键技术,主要用于保护晶圆表面,防止划痕和污染。
本文将从晶圆划片、蓝膜的定义、制备方法、应用领域等方面进行详细介绍。
一、晶圆划片晶圆划片是指将硅片或其他半导体材料通过机械或化学方法分割成小块的过程。
在半导体制造中,为了提高生产效率和降低成本,通常会将一个大型晶圆上生长的若干个芯片分割成单个芯片。
这些单个芯片可以更方便地进行后续加工和封装。
机械划片是最常见的分割方法,它使用钻头或锯片等工具沿着预定的方向将晶圆分割成小块。
这种方法适用于较厚的硅片,但容易产生微裂纹和边角损伤。
化学划片则采用化学溶解或腐蚀等方法,在特定条件下将硅材料局部溶解或腐蚀掉,从而实现分割。
这种方法适用于薄硅片,可以得到光滑的表面和尺寸精度高的芯片。
二、蓝膜蓝膜是一种透明的保护层,通常由聚酰亚胺等高分子材料制成。
它可以覆盖在晶圆表面,保护芯片免受划痕、污染和氧化等影响。
在半导体制造中,蓝膜通常作为划片前的保护层使用。
制备方法主要包括溶液法、浸涂法和喷涂法。
其中溶液法是最常用的方法,它将聚酰亚胺等高分子材料溶解在有机溶剂中,然后通过旋涂或喷涂等方式将其均匀地覆盖在晶圆表面上。
浸涂法则将晶圆浸泡在预先调制好的聚酰亚胺溶液中,使其均匀地吸附在晶圆表面上。
喷涂法则通过高压气体将聚酰亚胺溶液喷射到晶圆表面上。
三、应用领域晶圆划片蓝膜广泛应用于半导体制造领域。
在晶圆加工前,蓝膜可以保护晶圆表面免受划痕和污染。
在晶圆划片过程中,蓝膜可以减少芯片表面的损伤和氧化,从而提高芯片的质量和可靠性。
此外,在芯片封装过程中,蓝膜还可以起到保护作用,防止芯片表面被机械或化学损伤。
除了半导体制造领域外,晶圆划片蓝膜还广泛应用于生物医学、光学器件等领域。
在生物医学领域,晶圆划片蓝膜可以作为细胞培养基质、微流控芯片等材料的基底。
在光学器件领域,晶圆划片蓝膜可以作为玻璃或其他透明材料的保护层。
总之,晶圆划片和蓝膜是半导体制造过程中不可或缺的关键技术。
先进封装中关于晶圆划片的几项技术应用

先进封装中关于晶圆划片的几项技术应用
“中国集成电路设计业2021年会暨无锡集成电路产业创新发展高峰论坛”(ICCAD)于2021年12月22日成功召开。
此论坛在我国集成电路设计产业的发展中一直发挥着推动产业集聚、对接产业资源、掌握行业趋势的重要作用,现已成为国内半导体界最具影响力的行业盛会之一。
和研科技自2011年1月成立以来,经历了初创期、上升期、机遇期、创新期四个阶段。
通过不断开拓和创新,设备从6寸单轴半自动到12寸双轴全自动实现全面覆盖,满足客户的各种需求。
2021年在国内头部企业拿到12寸wafer saw设备的大批量订单,并且在未来还会涉及更广泛的领域。
此次会议,和研科技副总经理—余胡平与大家分享了先进封装中关于晶圆划片的几项技术应用;
过去半个世纪,集成电路从电子管到超大规模集成电路的方向发展,IC集成度越高,伴随对封装技术的要求也是越发的精细化。
划片机是IC封装生产过程中的关键设备之一,用于将含有很多芯片的晶圆切割成一个个晶片颗粒,其切割加工能力一定程度上决定了芯片封装的成品率与性能。
2021年,和研科技自主研发的全自动晶圆划片机DS9260在多个应用领域实现市场突破,包括IC封测、功率半导体、MEMS等,尤其是在封测行业12英寸划片领域,彻底打破了日本企业在这一市场的垄断局面。
半导体划片工序

半导体划片工序
半导体划片工序是半导体制造过程中的重要环节之一,它是将大面积的半导体晶圆切割成小尺寸的芯片或器件的过程。
在半导体划片工序中,需要使用专业的设备和工艺来确保切割的精度和质量。
半导体划片工序的前期准备非常重要。
在准备阶段,需要清洁和检查半导体晶圆,以确保没有杂质和缺陷。
接下来,晶圆会被放置在划片机上,进行切割前的定位和精确定位。
这一步骤的准确性直接影响后续切割的精度和质量。
在半导体划片工序中,切割方式有多种,常见的有机械切割和激光切割。
机械切割是使用划片锯将晶圆切割成芯片,刀片的尺寸和材质决定了切割的精度。
而激光切割则是使用激光束对晶圆进行精确切割,具有更高的精度和效率。
切割后,芯片会被收集和检查。
收集芯片需要使用专用的夹具或机械手臂,以避免损坏芯片。
检查芯片包括外观检查和电性能测试。
外观检查主要是检查芯片的表面是否有损伤和缺陷,电性能测试则是检测芯片的电气特性是否符合要求。
半导体划片工序中,还需要进行后续的清洁和包装。
清洁是为了去除切割过程中产生的杂质和污染物,以确保芯片的质量。
包装是将芯片放置在适当的封装中,以保护芯片不受外界环境的影响,并方
便后续的组装和使用。
总结一下,半导体划片工序是半导体制造中不可或缺的环节。
通过准备、定位、切割、收集、检查、清洁和包装等步骤,确保切割出的芯片具有高精度和良好的品质。
在半导体工业中,划片工序的质量和效率直接影响着整个制造流程的成功与否。
因此,半导体划片工序的技术和工艺的不断创新和提高,对于半导体行业的发展具有重要意义。
新一代晶圆划片技术

De e ing r k Ch a ,Be no d Ri h r h g n r l c ez a e
Ab t a t sr c :W i h e eo m e t o e c n u t r a d e e to i e h o o i s a d t e i c e s g d 。 t t e d v l p n f s mi o d co n l cr n c t c n l g e n h n r a i e h n
晶圆研磨划片流程说明

晶圆研磨划片流程说明晶圆研磨划片是半导体制造过程中的一项关键工艺,主要用于将晶圆切割成各种尺寸的芯片。
本文将详细介绍晶圆研磨划片的流程。
一、晶圆研磨划片前的准备工作在进行晶圆研磨划片之前,首先需要进行一系列的准备工作。
这些工作包括晶圆清洗、对其进行精确定位、确定划片方向和大小等。
晶圆清洗是为了去除表面的杂质和污染物,确保划片过程中的质量。
精确定位是通过光刻技术来实现的,将晶圆上的芯片图案与划片位置进行对应。
确定划片方向和大小是为了满足不同芯片尺寸和应用的需求。
二、晶圆研磨划片的工艺步骤1. 研磨:将晶圆放置在研磨机上,通过旋转研磨盘和磨料的作用,逐渐将晶圆表面的硅材料磨掉。
研磨的目的是将晶圆表面磨平,去除表面的缺陷和杂质,以便进行后续的划片工艺。
2. 清洗:在研磨完成后,需要对晶圆进行清洗,去除研磨过程中产生的碎屑和残留物。
清洗可以采用化学溶液或超声波清洗设备,确保晶圆表面的干净。
3. 划片:划片是将研磨后的晶圆切割成多个芯片的过程。
划片可以采用机械划片或者激光划片。
机械划片是通过划片刀具在晶圆表面进行切割,而激光划片则是利用激光束来切割晶圆。
划片的目的是将晶圆划分为多个独立的芯片,以便后续的封装和测试。
4. 清洗:在划片完成后,需要再次对芯片进行清洗,去除划片过程中产生的碎屑和残留物。
清洗的目的是确保芯片表面的干净,避免对后续工艺和性能的影响。
5. 检查和筛选:划片完成后,需要对芯片进行检查和筛选。
检查的目的是检测芯片表面是否有缺陷和损伤,确保芯片质量符合要求。
筛选是将芯片按照尺寸、电性能等指标进行分类,以便后续的封装和测试。
三、晶圆研磨划片的注意事项1. 控制研磨划片的厚度:研磨划片的厚度是影响芯片性能的重要参数,需要精确控制。
过厚或过薄都会对芯片的性能和可靠性产生负面影响。
2. 确保划片的平整度:划片后的芯片表面应该保持平整,不应有凹凸或起伏。
平整度的要求与芯片尺寸和应用有关,需要根据具体情况进行调整。
晶圆划片工艺简介

晶圆划片工艺简介划片工艺流程晶圆经过前道工序后芯片制备完成,还需要经过切割使晶圆上的芯片分离下来,最后进行封装。
不同厚度晶圆选择的晶圆切割工艺也不同:厚度100um以上的晶圆一般使用刀片切割;厚度不到100um的晶圆一般使用激光切割,激光切割可以减少剥落和裂纹的问题,但是在100um以上时,生产效率将大大降低;厚度不到30um的晶圆则使用等离子切割,等离子切割速度快,不会对晶圆表面造成损伤,从而提高良率,但是其工艺过程更为复杂;刀片切割(Blade dicing or blade sawing)刀片切割(锯切)过程中,保护膜的附着与摘除(图片来自网络)为了保护晶圆在切割过程中免受外部损伤,事先会在晶圆上贴敷胶膜,以便保证更安全的“切单”。
“背面减薄(Back Grinding)”过程中,胶膜会贴在晶圆的正面。
但与此相反,在“刀片”切割中,胶膜要贴在晶圆的背面。
而在共晶贴片(Die Bonding,把分离的芯片固定在PCB或定架上)过程中,贴会背面的这一胶膜会自动脱落。
切割时由于摩擦很大,所以要从各个方向连续喷洒DI水(去离子水)。
而且,叶轮要附有金刚石颗粒,这样才可以更好地切片。
此时,切口(刀片厚度:凹槽的宽度)必须均匀,不得超过划片槽的宽度。
很长一段时间,锯切一直是被最广泛使用的传统的切割方法,其最大的优点就是可以在短时间内切割大量的晶圆。
然而,如果切片的进给速度(Feeding Speed)大幅提高,小芯片边缘剥落的可能性就会变大。
因此,应将叶轮的旋转次数控制在每分钟30000次左右。
晶圆划片机晶圆切割时,经常遇到较窄迹道(street)宽度,要求将每一次切割放在迹道中心几微米范围内的能力。
这就要求使用具有高分度轴精度、高光学放大和先进对准运算的设备。
当用窄迹道切割晶圆时,应选择尽可能最薄的刀片。
可是,很薄的刀片(20µm)是非常脆弱的,更容易过早破裂和磨损。
结果,其寿命期望和工艺稳定性都比较厚的刀片差。
圆片等离子划片工艺及其优势

圆片等离子划片工艺及其优势圆片等离子划片工艺是一种先进的半导体加工技术,广泛应用于集成电路、光电子器件、生物芯片等领域。
该工艺通过使用等离子体刻蚀技术,实现对圆片的高精度划片,为微电子制造提供了重要支持。
本文将介绍圆片等离子划片工艺的基本原理、工艺流程以及其在工业应用中的优势。
一、圆片等离子划片的基本原理1.1 等离子体刻蚀技术等离子体刻蚀技术是通过产生高能离子、原子和分子的等离子体,利用其在表面产生的化学反应和物理撞击效应,实现对材料的刻蚀。
在圆片等离子划片工艺中,通常使用的等离子体刻蚀设备包括反应离子刻蚀机(RIE)和平行板等离子体刻蚀机。
1.2 圆片划片的原理圆片划片是指在半导体材料或其他薄膜上划分出所需的小片,以满足特定应用的要求。
等离子体刻蚀技术通过控制离子束的能量、方向和密度,可以实现对材料表面的高精度刻蚀。
在划片过程中,等离子体刻蚀会沿着预定的切割路径进行,形成精确的切割边缘。
二、圆片等离子划片的工艺流程2.1 前处理在进行圆片等离子划片之前,通常需要对切割对象进行前处理。
这包括清洁表面、涂覆光刻胶、曝光光刻胶等步骤,以确保划片的准确性和质量。
2.2 划片过程掩膜定义:利用光刻技术在切割对象表面定义出需要划片的区域。
等离子体刻蚀:使用等离子体刻蚀技术,根据掩膜的定义划出所需形状。
该步骤通过控制离子束实现高精度刻蚀。
2.3 后处理划片过程完成后,需要进行后处理以确保切割表面的质量和平整度。
后处理步骤可能包括清洗、除去光刻胶残留、表面处理等。
三、圆片等离子划片工艺的优势3.1 高精度和高效率圆片等离子划片工艺通过精确控制等离子体刻蚀参数,可以实现对材料的高精度切割,划片边缘清晰。
同时,该工艺具有高效率,适用于批量生产。
3.2 适用性广泛圆片等离子划片工艺不仅适用于半导体材料,还适用于陶瓷、玻璃、金属等多种材料。
这种广泛适用性使其在微电子制造和其他领域中得到了广泛应用。
3.3 可控性强等离子体刻蚀技术具有高度的可控性,可以精确控制刻蚀深度、刻蚀速率和表面质量。
- 1、下载文档前请自行甄别文档内容的完整性,平台不提供额外的编辑、内容补充、找答案等附加服务。
- 2、"仅部分预览"的文档,不可在线预览部分如存在完整性等问题,可反馈申请退款(可完整预览的文档不适用该条件!)。
- 3、如文档侵犯您的权益,请联系客服反馈,我们会尽快为您处理(人工客服工作时间:9:00-18:30)。
1 传统划片技术所面临的难题随着向轻薄短小的发展趋势,IC的封装也起了很大的变化.如记忆体IC,已由早期的单一chip变成多层chip堆栈的封装,一颗IC里叠了7、8层芯粒(chip),韩国三星半导体今年稍早更公开展示了其超薄晶圆的封装技术已达16层的堆栈,而封装后的尺寸还要比原来同容量的IC更小。
因此芯片的厚度也由650μm一路减薄至120、100、75、50、25、20 μm。
当厚度降到100 μm以卜,传统的划片技术已经山现问题,产能节节下降,破片率大幅攀升。
芯片在此阶断价值不斐,几个百分点的破片率可能吃掉工厂辛苦创造的利润。
另外,晶圆的制造技术中,为了提升效能,采用了low-k材料,在其结构中有多层的金属和一些易碎的材料。
当传统钻石刀片遇到这些延展性高的金属层,钻石颗粒极易被金属削包住而失去部份切削能力,在此情况下进刀,极易造成破片或断刀。
其实,除了先进的IC之外,在传统二极管(Diode)的晶圆划片,钻石刀同样有许多无法满足业界需求的地方:比如Gpp晶圆的划片,机械方式的磨削造成玻璃批覆层严重破损而导致绝缘不良和严重漏电,为了克服这一问题,业界只好自求多福发展出各种复杂的工艺去弥补这项缺陷。
将玻璃层只长在切割道(Cutting Street)两旁。
对方形晶粒而言,这个方式已被业界延用多年。
但对六角型晶粒(Hexagonal Dice)而言,还存在问题,即六角型每边的三角型被浪费。
在每一分一毫都需计较的二极体行业,3 0%~40%主原料(芯片)的损失是极可怕的。
通过新的技术,这些长期以来的失血,是完全可以被止住。
在以蓝宝石为基板的高亮度LED晶圆的划片.亦存在严重的划片问题。
传统的蓝宝石晶圆的划片_丰要有2种方式:用钻石笔或钻石刀片。
在蓝宝石晶圆上先划很浅的线,再裂片。
由于蓝宝石材质本身相当硬,无论选哪种方式,工具的损耗都非常严重;裂片后,整体良品率也不高。
这些长期困扰LED、业界的问题,现在随着紫外激光划片系统的运用,已大为改善。
在微机电(MEMS)方面,有越来越多的芯片需要打孔、异形孔开孔和局部减薄等加工。
玻璃与硅片键合在一起的复合芯片的切割、披覆有钻石层的芯片,以及复杂微结构之芯片切割等,都不是钻石刀片所能胜任的。
而这些产品的市场需求却不断成长,迫使业界寻找新一代的划片解决方案。
2 激光划片顺势崛起激光划片其实在多年前已被使用,光源多为1 064 nm的Nd:YAG,在某些低阶应用方面的品质尚可接受,但在集成电路的加工处理中,鉴于其过大热影响区、污染严重、热变形严重等缺陷,始终无法被认可。
近年来,紫外激光技术渐趋成熟,其切割质量比l 064 nm的激光源改进很多,特别是在蓝宝石晶圆的划片应用中,其优势极为明显,已渐成为业界主流解决方案。
在各类激光解决方案中,最为特殊且鲜为人知的则是世界专利之瑞士微水刀激光技术。
该技术在许多方面的表现确有其独到之处,尤其在消除热影响区方面表现优异。
微水刀激光划片技术已获得全球半导体封装大厂的认同和采用,特别是针对超薄晶圆、LOW-k晶圆、钻石披覆晶圆、二极管玻璃钝化晶圆、微机电芯片、复合晶圆以及异形晶粒的划片切割,都有不俗的表现。
3 微水刀激光科技3.1 技术原理几千年来"水火不融"的观念于1993年被瑞士杰出的科学家Dr.Bernold Richerz hagen打破。
他巧妙地结合水刀技术和激光技术的优点,创造出微水刀激光(Laser M icro Jet)。
更精确的说法是水导激光(Water Jet Guided Laser)。
他将激光聚焦后导入比发丝还细的微水柱中,从而引导光束,并冷却工件,消除了传统激光热影响区(Heat Affected Zone)过大的缺陷。
大大提高了激光切割的质量,因而非常适合半导体、医疗器材、电子、航天等高精密、高洁净要求的加工。
从图l可看出激光束(Laser Beam)由上方导入,经过聚焦镜及水腔(Water Ch amber)的窗户进入,聚焦于喷嘴(Nozzle)的圆心.图1 微水刀激光原理低压纯净水从水腔左边进入,经钻石喷嘴(Diamond Nozzle)上的微孔喷出。
由于喷嘴考虑到流体力学的设计,出来的水柱像光纤一样既直又圆。
水柱的直径根据喷嘴孔径而异,一般比人的头发还细,有100~30 μm多种规格。
激光被导入水柱中心,利用微水柱与空气界面全反射的原理,激光将沿着水柱行进。
在水柱维持稳定不开花的范围内都能进行加工。
通常有效的工作距离为喷嘴孔径的l 000倍。
如喷嘴为100 μm,则其有效工作距离为1 00mm。
这是传统激光所望尘莫及的,因为传统激光只能在焦点处加工。
激光光源可选配不同的波长,只要该波长的能量不会被水吸收即可。
精密加工常用的波长,1 064~355 nm。
另外,用于微加工的激光几乎都是脉冲激光(Pulsed Laser),传统激光不论是脉冲或连续,总会有能量残留在切割道上,该能量的累积和传导是造成烧伤切割道旁热损伤的主要原因。
而微水刀激光因水柱的作用,将每个脉冲残留的热量迅速带走,不会累积在工件上,因此切割道干净利落。
热影响区的困扰得到大幅改善。
因此,Laser MicroJet技术才适用于半导体等高精密的应用。
3.2 特点相对于传统激光,微水刀激光有很多显著的特点。
如无热影响区(Zero Heat Affe cted Zone),完全不烧伤工件,切割道干净利落、无熔渣、无毛刺、无热应力、无机械应力、无污染,极适合半导体、电子、医疗、航天等高精密器件切割加工。
微水刀激光适用于从金属到其合金的多种材料,如不锈钢、钛、钼、镁、镍、铜、I nvar等,以及硅(Silicon)、锗(Ge)、砷化镓(GaAs)等半导体材料,乃至碳化硅(Sic)、CBN、钻石、陶瓷、橡胶……软硬通吃。
甚至可同时切割橡胶及不锈钢片而不烧伤橡胶层,这在传统激光是完全不可能的事情。
该项技术可用于切割、钻孔、挖槽、打印、表面热处理等多项极细微及复杂的形状加工。
超薄硅片(Ultra Thin Silicon Wafer)切割速度比传统钻石刀快5~10倍,并且可以切任意形状,功能超强,在半导体芯片切割的应用上,突破了多年来芯片划片只能走直线的桎锢。
从此设计者可以毫无限制地发挥其创意。
从图2、图3两张不锈钢切割的照片可清楚地看出热影响区(HAZ)大小所造成的差异。
传统激光因热影响区过大,无法进行精微切割,大大限制了其应用领域。
图 2 不锈钢片以传统激光切割热耦传严重图 3 不锈钢片微水刀激光切割微水刀激光(Laser Micro Jet)以其优异的断热切割技术,大幅开拓精密微加工的领域,催生了许多新产品、新工艺。
4 低介电系数材料和超薄晶圆的划片问题原来只用于高阶产品的超薄晶圆(Ultra thin wafer)已经越来越普及,而且越来越薄。
处理超薄晶圆不仅是Silicon substrate本身厚度的问题,在加上许多硬脆易碎及延展性高的金属Pad后,问题更加复杂。
钻石刀片既使小心翼翼地切过Silicon sub strate,但金属层的碎屑却可能包粘在钻石颗粒上,使切削能力大打折扣。
此时若维持进刀速度,必然造成破片断刀的结果。
各主要划片机厂,如Disco、TSK.等均转向激光,由此可见机械方式已经到了克服不了的困境。
不幸的是激光也有激光的问题。
在此,就钻石刀片,传统激光及微水刀激光的特性探讨如下:4.1 钻石刀片易造成wafer表面崩边或龟裂。
遇金属层易断刀破片,切割速度慢,破片率高。
但在切割Silicon substrate时断面平整,深度控制容易。
在使用DAF(Die Attach Fil m)时可正好切穿DAF而不伤Blue Tape。
4.2 传统激光传统激光(Conventional Laser)或称干式激光(Dry Laser),因为热影响区的问题未克服,仅能用在低阶芯片,如太阳能芯片等。
采用3倍频方式虽然有改善,但也只能划划线。
如果切穿同样烧伤芯片和DAF及Blue Tape。
4.3 微水刀激光可以轻易去除切割道表层材料及Silicon substrate。
切割超薄片(50 μm)时速度比diamond saw快数倍。
缺点为与干式激光同样会烧坏DAF,切割断面不如机械磨削光滑。
从上述看来各有所长,也各有缺陷。
4.4 解决方案既然没有十全十美的方法,只好退而求其次。
对Diamond Saw而言,难解决的是Wafer的表层材料。
对微水刀激光而言,头痛的是会烧坏DAF。
因此如各取所长,分成2个步骤处理,就差强人意。
首先用微水刀激光划浅浅的一刀,加工手段上称之为开槽(Grooving),以清除切割道上所有的材料,不管是金属或易碎材料。
微水刀激光可以选用与切割道(Cutting S treet)同宽的喷嘴,像推土机一样一次推掉表层上各种找麻烦的材料,露出Silicon S ubstrate。
再接着用Diamond Saw切穿silicon substrate和DAF,并刚好停在 Bl ue Tape表面上。
因为Grooving 只能去除表层几十微米的深度,微水刀激光可以250 mm/s的高速进行。
就生产线的平衡来看,一台微水刀激光系统需至少5台以上Diamond Saw与之配合才消化得掉。
从设备投资的角度来看,这似乎是最有效益的方式。
不仅不会因为引进新设备而闲置旧机器,反而会提高产能,真正相辅相成,相得益彰。
微水刀激光尚可从事异型晶粒切割,打通孔或盲孔等钻石刀具作不了的事情,见图4、图5。
图 4 Silicon wafer 激光打孔图 5 较大显微镜照片孔径100微米5 瑞士喜诺发公司之半导体晶圆划片系列全系列均配备高精度线性滑轨及CNC控制,TFT LCD触控萤幕及先进人机界面软件,CCD Camera,自动视觉瞄准,远端通讯诊断。
可切任何形状品粒,如六角形,圆形和不规则形。
5.1 设备介绍(1)LDS 200A/LDS:300A。
LDS 200A/LDS:300A一全自动200 mm/30 0 mm硅片水刀激光切割系统,Cassette to Cassette,自动视觉系统对位,切割,清洁,进退料一气呵成。
适合连续人量生产。
住超薄硅片切割之表现比传统钻石刀切割方式快数倍。
(2)LDS 200C。
LDS 200C一自动200 mm硅片水刀激光切割系统,人工或视觉系统自动瞄准,切割,切割完了自动以超纯水清洗,手动进退料,适合量产。
(3)LDS 200M。
LDS 200M一手动200 mm硅片水刀激光切割系统,手动进退料,人工或视觉系统自动对准。
切割,适合研究发展或少量多样生产形态用途。
(4)LGS 200。
LGS 200为200 mm Cassette to Cassette水刀激光全自动硅片削边系统,特别适用于超薄硅片外圆之削边,大幅降低超薄片(Ultra thin wafer)之破片率,并可作钻孔(Hole drilling),开槽(Slotting),异型晶粒切割(Free shape chip dicing)等用途。