石油化工设备在湿硫化氢环境中腐蚀与防护分析
湿硫化氢腐蚀与防护.

氢鼓包
阴极反应生成的原子氢半径很小,只有7.8×10-6mm, 其中约有1/3很容易进入钢的晶格,并在钢的内部缺陷处 (如夹渣、气孔、裂纹、分层等)或晶界上聚集,结合成氢 分子。当在一个狭小的闭塞空间内有大量的氢分子生成时, 此处的压力将高达几百兆帕,从而造成钢材的鼓包或鼓包 开裂。 在这种腐蚀环境中生成的络合物Fe(CN) 64- ,在碱性溶液 中可以大大加剧原子氢的渗透。因为:一方面,氰化物能 溶解FeS保护膜,使钢失去保护;另一方面,它又能阻碍 原子氢结合成分子氢,使溶液中保持着较高的原子氢浓度。 因此,氢渗透率随系统中氰化物浓度的增加而增加。 氢鼓包的产生,主要是由于氢聚集引起。因此,即使在没 有外加应力的情况下,它也能照样发生。严重时,鼓包表 面将会导致开裂(HIC)。
C 腐蚀原因
腐蚀介质主要来源于原油中的氯化物(NaCl、MgCl2、 CaCl2 和有机含氯清蜡剂)和硫化物。 具体腐蚀过程如下:
Fe+2HCl → FeCl2十H2 FeCl2+H2S → FeS↓+HCI FeS+2HCl → FeCl2+H2S
冷凝系统严重腐蚀,尤其是气液两相转变的“露点”部位, 剧烈的腐蚀是由于低pH值的盐酸引起的: Fe+2H+ → Fe2++H2 ↑ FeS+2H+ → Fe2++H2S ↑ 随着冷凝过程的进行,冷凝水量不断增加,HCl水溶液不 断被稀释,pH值提高,腐蚀应有所缓和。但在这一过程 中,H2S的溶解度迅速增加,提供了更多的H+,促进了氢 去极化腐蚀反应:
具体的腐蚀部位、腐蚀形态、腐蚀原因及
机理、防护措施和腐蚀监测手段进行了详
细介绍和探讨。
主要内容
炼油厂的湿硫化氢环境及其防护原则
化工设备在湿硫化氢环境中的腐蚀问题及防护方式研究
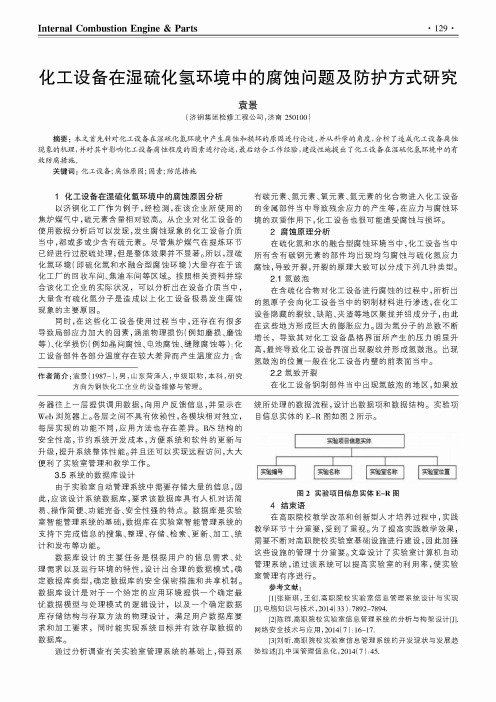
Internal Combustion Engine & Parts• 129 •化工设备在湿硫化氢环境中的腐蚀问题及防护方式研究袁景(济钢集团检修工程公司,济南250100)摘要:本文首先针对化工设备在湿硫化氢环境中产生腐蚀和损坏的原因进行论述,并从科学的角度,分析了造成化工设备腐蚀 现象的机理,并对其中影响化工设备腐蚀程度的因素进行论述,最后结合工作经验,建设性地提出了化工设备在湿硫化氢环境中的有 效防腐措施。
关键词:化工设备;腐蚀原因;因素;防范措施1化工设备在湿硫化氢环境中的腐蚀原因分析以济钢化工厂作为例子,经检测,在该企业所使用的 焦炉煤气中,硫元素含量相对较高。
从企业对化工设备的 使用数据分析后可以发现,发生腐蚀现象的化工设备介质 当中,都或多或少含有硫元素。
尽管焦炉煤气在提炼环节 已经进行过脱硫处理,但是整体效果并不显著。
所以,湿硫 化氢环境(即硫化氢和水融合型腐蚀环境)大量存在于该 化工厂的回收车间、焦油车间等区域。
按照相关资料并综 合该化工企业的实际状况,可以分析出在设备介质当中,大量含有硫化氢分子是造成以上化工设备极易发生腐蚀 现象的主要原因。
同时,在这些化工设备使用过程当中,还存在有很多 导致局部应力加大的因素,涵盖物理损伤(例如磨损、磨蚀 等)、化学损伤(例如晶间腐蚀、电池腐蚀、缝隙腐蚀等);化 工设备部件各部分温度存在较大差异而产生温度应力;含作者简介:袁景(1987-)男,山东菏泽人,中级职称,本科,研究 方向为钢铁化工企业的设备维修与管理。
务器往上一层提供调用数据,向用户反馈信息,并显示在 Web浏览器上。
各层之间不具有依赖性,各模块相对独立,每层实现的功能不同,应用方法也存在差异。
B/S结构的 安全性高,节约系统开发成本,方便系统和软件的更新与 升级,提升系统整体性能。
并且还可以实现远程访问,大大 便利了实验室管理和教学工作。
3.5系统的数据库设计由于实验室自动管理系统中需要存储大量的信息,因此,应该设计系统数据库,要求该数据库具有人机对话简 易、操作简便、功能完备、安全性强的特点。
炼油装置湿硫化氢应力腐蚀分析详解
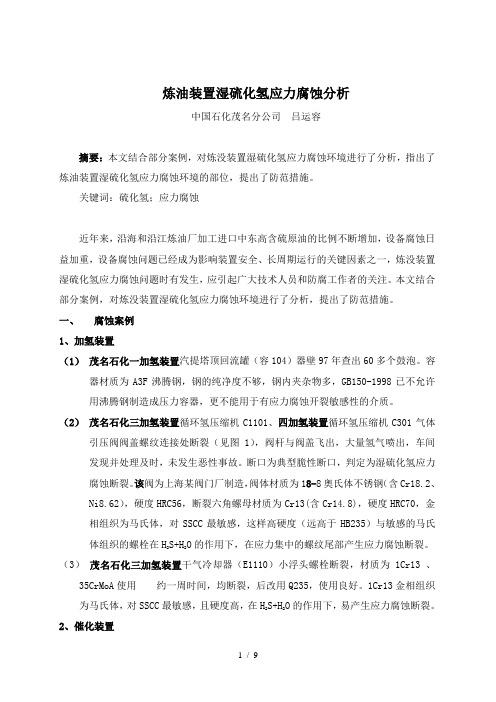
炼油装置湿硫化氢应力腐蚀分析中国石化茂名分公司吕运容摘要:本文结合部分案例,对炼没装置湿硫化氢应力腐蚀环境进行了分析,指出了炼油装置湿硫化氢应力腐蚀环境的部位,提出了防范措施。
关键词:硫化氢;应力腐蚀近年来,沿海和沿江炼油厂加工进口中东高含硫原油的比例不断增加,设备腐蚀日益加重,设备腐蚀问题已经成为影响装置安全、长周期运行的关键因素之一,炼没装置湿硫化氢应力腐蚀问题时有发生,应引起广大技术人员和防腐工作者的关注。
本文结合部分案例,对炼没装置湿硫化氢应力腐蚀环境进行了分析,提出了防范措施。
一、腐蚀案例1、加氢装置(1)茂名石化一加氢装置汽提塔顶回流罐(容104)器壁97年查出60多个鼓泡。
容器材质为A3F沸腾钢,钢的纯净度不够,钢内夹杂物多,GB150-1998已不允许用沸腾钢制造成压力容器,更不能用于有应力腐蚀开裂敏感性的介质。
(2)茂名石化三加氢装置循环氢压缩机C1101、四加氢装置循环氢压缩机C301气体引压阀阀盖螺纹连接处断裂(见图1),阀杆与阀盖飞出,大量氢气喷出,车间发现并处理及时,未发生恶性事故。
断口为典型脆性断口,判定为湿硫化氢应力腐蚀断裂。
该阀为上海某阀门厂制造,阀体材质为18-8奥氏体不锈钢(含Cr18.2、Ni8.62),硬度HRC56,断裂六角螺母材质为Cr13(含Cr14.8),硬度HRC70,金相组织为马氏体,对SSCC最敏感,这样高硬度(远高于HB235)与敏感的马氏体组织的螺栓在H2S+H2O的作用下,在应力集中的螺纹尾部产生应力腐蚀断裂。
(3)茂名石化三加氢装置干气冷却器(E1110)小浮头螺栓断裂,材质为1Cr13 、35CrMoA使用约一周时间,均断裂,后改用Q235,使用良好。
1Cr13金相组织为马氏体,对SSCC最敏感,且硬度高,在H2S+H2O的作用下,易产生应力腐蚀断裂。
2、催化装置(1)茂名石化二催化装置冷305/1、2小浮头螺栓断裂,材质为2Cr13,后改用Q235,使用良好。
关于湿硫化氢对在用设备的损伤分析与预防措施

Ab t a t F rt e d ma e n t e p e s r e s l a s d b th d o e u fd s r c o h a g so h r s u e v s es c u e y we y r g n s l e,a n l ssi i n a ay i s
1 前 言
随着 石化 行业 加 工技 术 的 发展 , 别是 对 高硫 特 原油加工 的 日益 增 多 , 硫化 氢 对 压 力容 器 的腐蚀 愈 加 严重 。众所周 知 , 石油 炼制过 程 中 , 在 原油 中的硫 化 物 以各 种形态 存 在 , 这些 硫 化 物 中参 与 腐蚀 反 应 的主要是 H s和易 分解成 H S的硫化 物 , 般称 其 一 为腐 蚀源 或活性硫 。其 中硫化 氢是 造成炼 油厂设 备
腐蚀性很 强 的 HC , L 原油 中 的硫 化物 则分解 成 H s ,,
化工 部 H J5— 9 钢制 化 工 容器 材 料选 用 规 G1 8《
定》 中对湿 硫 化 氢 环 境 也 基 本 沿 用 了上 述规 定 , 同
时对 温 度 和 P H值 也 给 予 了规 定 , 同时满 足 以下 即
21 0 6月第 1 1年 9卷第 2期
防 腐保 温技 术
关 于 湿 硫 化 氢 对 在 用 设 备 的 损 伤 分 析 与 预 防 措 施
汤 化 公 司安 全 生 产 监 督 办 , 宁 大 连 市 16 3 ; 1 辽 0 2 1 2 .大连 锅 炉 压 力 容 器 检 验 研 究 院 , 宁大 连 市 16 3 ) 辽 0 2 1
p i t n t e i s e to n h rv n ie me s rs a e prp s d. on si h n p c in a d t e p e e t a u e r o o e v
炼油装置中管道硫化氢腐蚀及防护
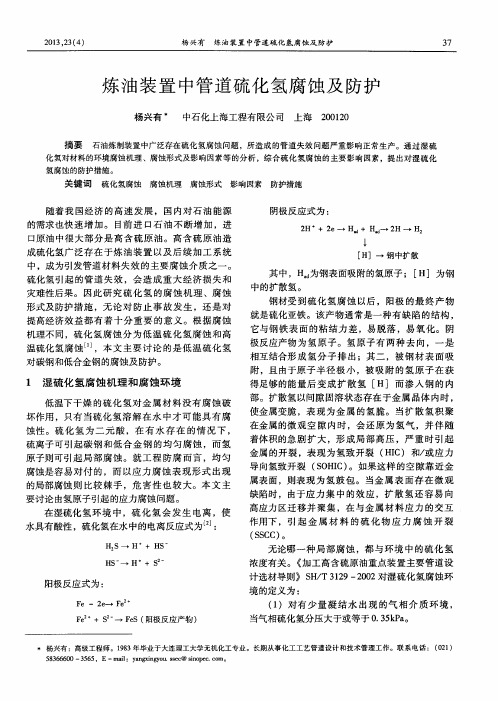
阴极反 应式 为 :
2 H + 2 e Ha d+ H. d _+ 2H _+ H 2
[ H ]一 钢 中扩散
中,成为引发管道材料失效 的主要腐蚀介质之一 。
硫 化氢 引 起 的 管 道 失 效 ,会 造 成 重 大 经 济 损 失 和
其中,H 。 为钢表面吸附的氢原子 ;[ H ]为钢
5 8 3 6 6 6 0 0 —3 5 6 5. E —ma i l :y a n g x i n g y o u . s s c c @s i n o p e c . t o m。
杨 兴有
炼油装置 中管道硫 化氢腐蚀 及防护
3 9
氢鼓 包 是 指 由金 属 内 部 过 高 的 氢 压 力 引起 的
附 ,且 由于原 子 半 径 极 小 ,被 吸 附 的 氢 原 子 在 获
1 湿 硫 化 氢 腐 蚀 机 理 和 腐 蚀 环 境
低温下干燥 的硫化氢对 金属材料没有 腐蚀破 坏作用 ,只有当硫化氢溶解 在水 中才可 能具有腐
蚀性 。硫 化 氢 为 二 元 酸 ,在 有 水 存 在 的 情 况 下 , 硫离 子可 引 起 碳 钢 和低 合 金 钢 的 均 匀 腐 蚀 ,而 氢
H2 S_ + H + HS’ HS一 _ + H +I C ) 。如果这样 的空隙靠近金
属表 面 ,则 表 现 为 氢 鼓 包 。当 金 属 表 面 存 在 微 观 缺 陷时 ,由于应 力 集 中 的 效 应 ,扩 散 氢 还 容 易 向 高应 力 区 迁 移 并 聚 集 ,在 与金 属 材 料 应 力 的交 互
氢腐蚀 的防护措施。
关键 词 硫化氢腐蚀 腐蚀机理 腐蚀形式 影响因素 防护措施
随着 我 国经 济 的 高 速 发 展 , 国 内对 石 油 能 源 的需求 也快 速 增 加 。 目前 进 口石 油 不 断 增 加 ,进 口原油 中很 大 部 分 是 高含 硫 原 油 。高 含 硫 原 油 造 成 硫化 氢 广 泛 存 在 于 炼 油 装 置 以及 后 续 加 工 系 统
预防炼油设备的湿硫化氢腐蚀
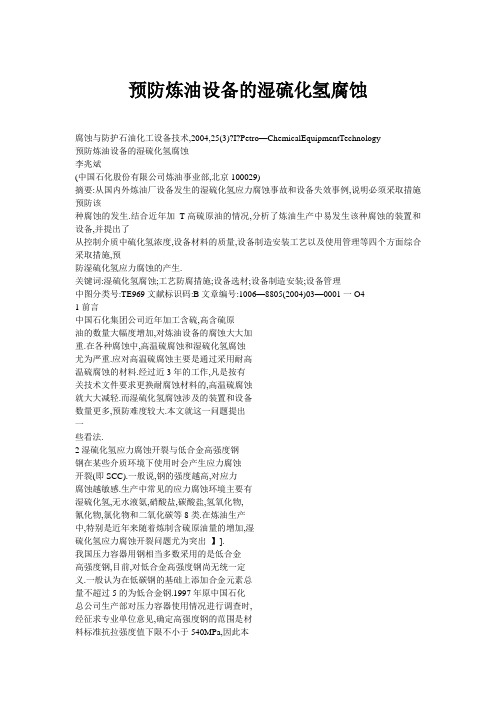
预防炼油设备的湿硫化氢腐蚀腐蚀与防护石油化工设备技术,2004,25(3)?I?Petro—ChemicalEquipmentTechnology预防炼油设备的湿硫化氢腐蚀李兆斌(中国石化股份有限公司炼油事业部,北京100029)摘要:从国内外炼油厂设备发生的湿硫化氢应力腐蚀事故和设备失效事例,说明必须采取措施预防该种腐蚀的发生.结合近年加_T-高硫原油的情况,分析了炼油生产中易发生该种腐蚀的装置和设备,并提出了从控制介质中硫化氢浓度,设备材料的质量,设备制造安装工艺以及使用管理等四个方面综合采取措施,预防湿硫化氢应力腐蚀的产生.关键词:湿硫化氢腐蚀;工艺防腐措施;设备选材;设备制造安装;设备管理中图分类号:TE969文献标识码:B文章编号:1006—8805(2004)03—0001一O41前言中国石化集团公司近年加工含硫,高含硫原油的数量大幅度增加,对炼油设备的腐蚀大大加重.在各种腐蚀中,高温硫腐蚀和湿硫化氢腐蚀尤为严重.应对高温硫腐蚀主要是通过采用耐高温硫腐蚀的材料.经过近3年的工作,凡是按有关技术文件要求更换耐腐蚀材料的,高温硫腐蚀就大大减轻.而湿硫化氢腐蚀涉及的装置和设备数量更多,预防难度较大.本文就这一问题提出一些看法.2湿硫化氢应力腐蚀开裂与低合金高强度钢钢在某些介质环境下使用时会产生应力腐蚀开裂(即SCC).一般说,钢的强度越高,对应力腐蚀越敏感.生产中常见的应力腐蚀环境主要有湿硫化氢,无水液氨,硝酸盐,碳酸盐,氢氧化物,氰化物,氯化物和二氧化碳等8类.在炼油生产中,特别是近年来随着炼制含硫原油量的增加,湿硫化氢应力腐蚀开裂问题尤为突出_】].我国压力容器用钢相当多数采用的是低合金高强度钢,目前,对低合金高强度钢尚无统一定义.一般认为在低碳钢的基础上添加合金元素总量不超过5的为低合金钢.1997年原中国石化总公司生产部对压力容器使用情况进行调查时,经征求专业单位意见,确定高强度钢的范围是材料标准抗拉强度值下限不小于540MPa,因此本文将满足上述两要求的压力容器用钢,称之为低合金高强度钢.就中国石化集团公司实际情况而言,低合金高强度钢主要包含两大类:一类是cr—Mo钢,主要用于锅炉蒸汽系统设备,炼油临氢设备和作为耐温耐蚀材料;另一类是C—Mn系列加入少量微合金元素或合金元素的低合金高强度钢,如15MnV(15MnVR,15MnVg),15MnNbR,18MnMoNbR,14MnMoNbB,20MnMo,07MnCrMoVR,07MnNiCrMoVDR以及FG43,CF62,SPV450,SPV490等.16MnR是目前国内应用最多的压力容器用钢,按技术标准其抗拉强度下限在540MPa以下,但实际产品常常会超过540MPa,而且在生产中16MnR钢制压力容器也多次发生应力腐蚀开裂,所以在讨论低合金高强度钢的应力腐蚀时也常常把16MnR以及日本的SPV355,美国的ASTMA516Gr70等钢种列入这一范围.湿硫化氢环境下的应力腐蚀开裂是指水相或含水物质在露点以下形成的水相与硫化氢共存时,在介质与外力(含内部组织应力及残余应力)协同作用下所发生的开裂.美国腐蚀工程师协会(NACE)T一8—16工作组对湿硫化氢应力腐蚀开裂的机理分为五类,即硫化物应力腐蚀开裂(SS—CC),氢鼓泡(HB),氢致开裂(HIC),应力导向氢致开裂(SOHIC)和碱性应力腐蚀开裂(ASCC).湿硫化氢应力腐蚀开裂较早见于油田设备,收稿日期:2004—03—17作者简介:李兆斌(1942一),男,河北省人.1967年毕业于清华大学精密仪器及机械制造系精密仪器专业,高级工程师.原中国石化股份有限公司炼油事业部副主任,从事石油化工设备管理工作多年.石油化工设备技术管道,在炼油厂和石油化工厂压力容器,工业管道中也多有发生,近年的几起重大事故引起了人们对湿硫化氢应力腐蚀开裂的进一步重视.1984年7月23日美国Unocal公司雷蒙特3号炼油厂的胺吸收塔因硫化氢引起开裂而发生重大爆炸事故,18.8m高的塔上部14m长的一节飞出约lkm,当场死亡17人.该塔材料为ASTMA一516Gr70,事故后分析其含Mn量为1.02~1.1,含碳量为0.22~0.24.该塔设计压力为1.6MPa,设计温度60℃,壁厚25mm,直径2600mm,1970年投用.失效分析中发现含有较多的SOHIC.该塔投用后每两年检查一次, 1974,1976年曾因发生氢鼓泡和分层,分别更换第二圈板并对局部衬蒙乃尔.爆炸后检查在临近修复环焊缝,在容器内表面的硬度达HRC29,靠近熔合线的显微硬度峰值为HRC40~,48,存在对裂纹敏感的显微组织马氏体.在做了大量分析试验后,认为正是在这些”硬的对裂纹敏感的显微组织”处,在操作过程中产生了裂纹,其原因可能是氢应力开裂,并在氢的诱导下裂纹扩展,直到裂纹周向长度达到800mm,发生灾难性爆裂为止.我国近年来在炼油生产中因为硫化氢浓度超标造成压力容器过早报废或被迫降低使用压力的事例时有发生.如某炼油厂4台16MnR制400m.LPG球罐分别在使用了5~6年后被迫报废.该4台球罐由于LPG中硫化氢浓度平均5000ffg/g,致使球罐产生大量裂纹,夹层,鼓泡,腐蚀十分严重. 某公司两台1000m.储存轻烃的球罐,其材质为N—TUF50,操作压力1.7MPa,操作温度20~40.C,规定介质中硫化氢浓度应小于50ffg/g,但抽查中发现超标,多次开罐检查发现大量裂纹, 1997年被迫申请停止储存轻烃.某公司主体材质为07MnCrMoVR制1000m.丙烯球罐,1996年1月投用.1998年5月因该罐混装H.S严重超标的粗丙烯,在很短的时间内,上温带纵缝出现穿透性裂纹而泄漏.开罐检查发现,内壁有数百条典型的应力腐蚀裂纹瞳].NACET一8—11工作组对4987台压力容器的检测结果进行了统计分析,几乎所有与湿硫化氢有关的压力容器都有开裂的可能.在炼油生产中与湿硫化氢有关的工艺设备开裂数量比例如表1 所示.雷蒙特3号炼油厂发生事故后,EXXON公司对美国,加拿大,日本189台压力容器进行了检验,存在裂纹的容器58台,占30.7,裂纹深度大于腐蚀裕度的容器37台,占被检容器的19.6(其中裂纹深度大于容器壁厚1/4的30 台).绝大多数裂纹靠近焊缝,而不在焊缝内.在被检验的容器中的介质有一半不知道硫化氢含量,另一半在200~10000ffg/g之间,介质中有60存在氰化物.表1湿硫化氢环境下炼油装置中设备开裂比例焦化催化裂化催化裂化液化轻烃装置名称烃回收分馏分馏装置石油气回收装置开裂比例,18~1945414138中国石化集团公司炼油厂压力容器的湿硫化氢应力腐蚀主要可能发生的部位是常减压装置的三顶,冷凝器,回流罐;催化裂化装置,焦化装置的分馏塔顶冷却器,回流罐,吸收稳定系统无内衬的设备;催化重整装置的汽提塔回流罐,预加氢产物分离器.力Ⅱ氢裂化装置的高分,低分,脱丁烷塔,脱乙烷塔顶设备,渣油加氢的冷高分,冷低分及分馏塔顶设备;汽,煤,柴油加氢精制装置的汽提塔回流罐;脱硫装置的脱硫塔,再生塔及塔顶设备;含硫污水汽提以及LPG和轻油的储罐等.湿硫化氢应力腐蚀涉及的装置多,设备多,开裂的危害极大,必须引起高度重视.3防止湿硫化氢应力腐蚀开裂的一些措施根据湿硫化氢应力腐蚀开裂机理和工程实践,应从介质环境,设备材料纯净度,性能,质量,设备制造安装的工艺及使用管理四方面采取综合预防措施.3.1严格控制介质中的硫化氢含量《压力容器安全技术监察规程》中对湿H.S应力腐蚀环境作如下界定_3]:”当化工容器接触的介质同时符合下列各项条件时,即湿HS应力腐蚀环境:a.温度≤(60+2P).C,P为压力(表),MPa;b.H2S分压≥0.00035MPa即相当于常温在水中H.S溶解度≥10;C.介质中含有液相水或处于水的露点温度以下;d.pH<9或有氰化物(HCN)存在.”目前首先要控制硫化氢浓度.因为在其他条件相同时,硫化氢浓度越高,产生应力腐蚀的敏感性越大,容器开裂的时间越短.国内负责材料和压力容器研究的科研单位及第25卷第3期李兆斌.预防炼油设备的湿硫化氢腐蚀高等院校的不少专家都倾向于要求低合金高强度钢容器储存的介质中,硫化氢浓度不得大于50f~g/g.国外工业界持这一观点的也很多.不少公司把湿HS浓度的危险性分为三级:HS小于50f~g/g时不开裂;H2S大于50f~g/g开裂;H2S大于50~g/g-F氰化物大于20f~g/g时为易开裂.日本早在1980年就专门对高强度钢球罐作了相应规定,如表2所示.表2含硫化氢的液化石油气球形容器的材料限制高强度钢板硫化氢含tR/~g?g的强度级别>10~≤50>50~≤100as~450MPa无要求热处理aS≥490MPa无要求热处理aS≥685MPa不能用不能用由表2可见:(1)不小于685MPa时,只要硫化氢含量大于10f~g/g,即不能采用,说明在湿硫化氢环境下,对钢材强度有限制;(2)硫化氢含量高,对材料以及热处理要求严格,硫化氢含量大于50f~g/g时必须进行热处理才能使用.以上可以看出硫化氢浓度是必须高度重视的参数.硫化氢含量低于50f~g/g仅能作为一个经验数据或者是目前应当高度重视的一个数据,但不能作为极限浓度,目前也尚未作为统一的压力容器设计的标准,笔者分析,主要有以下原因:(1)有资料报道,对于硫化氢含量小于5O~g/g的水相工艺环境中的压力容器,也还有17的开裂率;(2)湿硫化氢应力腐蚀开裂除与硫化氢含量有关外,还与介质的pH值,其他介质含量(如HCN,C1一,O2,CO2,HC1,H2,S,SO2等)有关; (3)不同材料对湿硫化氢环境下的应力腐蚀开裂敏感性不同,即使同种钢材由于不同生产厂家,不同批次,某些元素成分的实际含量的差异(如Mn,S,P含量),或材料制造过程不同其表现也不相同;(4)压力容器的结构,制造工艺,应力水平不同也对湿硫化氢环境的应力腐蚀开裂有不同的影响;(5)由于装置和设备的大型化,被迫在硫化氢含量较高的情况下采用高强度钢,所以有的设计单位对严格控制硫化氢含量大于50f~g/g时不能应用低合金高强度钢也提出异议.基于以上原因,谨提下述建议:(1)凡工艺技术和产品质量要求介质中硫化氢含量低于压力容器设计中所要求的,应严格按工艺技术和产品质量要求值控制;(2)其他情况下,介质中硫化氢含量应按压力容器设计中的规定值严格控制;(3)压力容器储存介质内硫化氢含量一般不得超过50f~g/g,个别超过50tzg/g而又需采用低合金高强度钢时,必须在设计中提出相应防止硫化氢应力腐蚀的技术要求,如相应的材料洁净度,相应的容器制造,安装工艺和检验技术.3.2严格压力容器用材质量管理钢材中的Ni,S,P,Mn,N,H等对低合金高强度钢抗SSCC性能不利,而Mn,N等是低合金高强度钢中的重要元素,S,P作为杂质应尽量除去l4].国外试验表明,如果能将P,S分别控制在0.008,0.001,则会大大降低湿硫化氢应力腐蚀开裂的可能性.美国开发的抗HIC的A516一Gr70钢,S不大于0.002.法国1990年版压力容器标准附录中对湿硫化氢环境下的碳钢及低合金钢除要求限制焊缝区的硬度和进行PWHT外,还提出如下要求:(1)为减少夹杂物,应限制钢中的硫含量,例如S含量不大于0.002,如能达到0.001则更好,并通过加钙处理使夹杂物成球状.还应限制钢中氧含量,例~nJJ,于0.002;(2)由于磷会促进偏析,引起开裂,应限制钢中磷含量,例如降到0.008;(3)在满足钢的力学性能的条件下,应尽可能降低钢的碳当量.上述(1),(2)要求远高于我国现行普通压力容器用钢标准,我国标准GB6654—1996<<压力容器用钢板》虽经修订,但16MnR的S,P含量仍较高,分别为不大于0.020和不大于0.030.但目前不少企业在控制钢中S,P含量上已取得较大进展,如上海宝钢生产的STE355(DIN1702)钢板,其S,P含量分别为0.003和0.012.我国舞阳钢厂制订了抗硫化氢腐蚀的16MnR(HIC)钢标准,其化学成分中要求P不大于0.015,S石油化工设备技术不大于0.005.并列出了抗硫化氢腐蚀的要求,规定了生产工艺流程.应当重视Mn在钢中的含量.Mn作为提高钢的强度的重要元素在低合金钢中被广泛应用(其他强化元素,如C,V,Nb等),由于该元素的存在使钢材在焊接时易淬硬,从而对氢致开裂很敏感,如焊接工艺不当易产生冷裂纹.有报道16MnR中Mn元素在湿硫化氢应力腐蚀开裂方面是极其有害的,特别是当Mn含量大于1.3时,其危害急剧增加.因此在订货时对16MnR的Mn含量应提出相应要求.钢材强度,硬度增大,硫化氢应力腐蚀敏感性增大,对应用于湿硫化氢环境下的钢板要求其硬度HB不大于200.材料试验可按NACETM0284标准要求进行.SH/T3096~2001《加工高硫原油重点装置主要设备设计选材导则》中已对三类装置15种设备提出采用抗HIC钢].并明确”抗氢致开裂钢是指具有低硫,磷含量,按NACETM0284~压力容器及管线钢抗氢致开裂的评定》方法进行试验,其结果符合规定的裂纹率要求的碳钢或碳一锰钢”.3.3容器的制造安装要从容器成形开始严格控制制造安装质量.其中把好焊接质量关尤为重要.要着力防止焊接冷裂纹和再热裂纹的产生.由于低合金高强度钢中强化元素的存在,焊接时易淬硬,若成形不好,刚性较大,拘束力较高时,焊接工艺不当极易产生冷裂纹.要合理控制线能量防止焊缝和热影响区脆化.降低残余应力对防止湿硫化氢应力腐蚀开裂也很重要.焊后热处理(PWHT)不仅降低残余应力,同时降低硬度.对焊缝金属(WM)和热影响区(HAZ)的硬度各国都很重视.美国对wM硬度在抗SCC时要求HB不大于200,日本要求HB不大于235,我国要求wM,HAZ的HB不大于200.07MnCrMoVR有一定的再热裂纹敏感性,应在PWHT时避开再热裂纹的敏感区.3.4严格管理,认真检验,确保安全(1)严格生产技术工艺管理,确保中间产品,产品的质量,使介质中的H.S含量不超标.原料等发生变化时,必须采取相应的措施.如加氢裂化原料中硫含量上升后,应视情况对循环氢采取脱硫措施;(2)凡在湿硫化氢环境下工作的压力容器,管道必须按规定定期检验.尤其要注意检查储存液态烃压力容器的汽液分界面处,油品储罐的水相部分,轻油储罐的罐顶部位.采用无损探伤检查时,宜采用超声波检查和荧光磁粉检查的方法; (3)当压力容器采用焊接修复时,一定要制订完善的焊接工艺并严格执行;(4)各使用单位必须把储存介质中含有湿硫化氢的压力容器专门列出,对其介质建立定期分析的制度,不得超标.对这些容器的初次开罐检查时间,发现缺陷后的再次开罐检查时间都应按从严的原则确定;尤其要重视LPG和轻烃球形储罐的管理.3结束语(1)湿硫化氢应力腐蚀开裂对炼油厂压力容器危害极大,随着加工含硫原油比例增加,其影响范围将更大,必须高度重视;(2)在诸多措施中,控制介质中硫化氢含量是防止湿硫化氢应力腐蚀开裂的首要措施;(3)对在湿硫化氢环境中工作的压力容器用材应加以限制,应提高钢材的纯净度;(4)严格制造安装工艺是防止湿硫化氢应力腐蚀开裂的重要保证,主要是精确成形,合理的焊接工艺,以防止焊接冷裂纹和再热裂纹的产生,采用PWHT消除或降低残余应力,合理控制线能量以防止焊缝金属和热影响区脆化.严格保证焊缝及热影响区硬度不超过规定值;(5)加强湿硫化氢环境下压力容器的管理.参考文献:1柳曾典.湿硫化氢环境用低合金高强度钢[j].石油化工设备技术,1998,19(5)2王正则.炼油设备中的湿硫化氢腐蚀[J].炼油设计,l994,24(6)3袁榕等.对某些CF一62钢制压力容器中的裂纹分析与防止措施的建议[j].压力容器,2003,(2)4SH/T3O96—2001加工高硫原油重点装置主要设备设计选材导则[S]5国家质量技术监督局.压力容器安全技术监察规程[S].北京:中国劳动社会保障出版社,1999。
《化工安全与防腐》读书报告

《石油化工设备在湿硫化氢环境中的腐蚀与防护》读后感该文介绍了H2S在较湿环境中的腐蚀机理及腐蚀形式,分析了设备在湿H2S 环境中可能引起腐蚀的因素,从设计角度提出了提高化工设备抗湿H2S腐蚀能力的设计要点,并提出在设备制造和检测时应采取防范措施。
通过阅读该文章我对湿H2S对化工设备的腐蚀有了初步的认识,H2S在水中呈现较强的酸性,会对化工设备造成腐蚀,稍不注意会发生应力腐蚀事故。
化工设备表面的钢材在硫化物的溶液中会发生电化学反应造成渗氢从而导致钢材被腐蚀。
钢材被腐蚀程度主要是由钢材的成份与PH值所决定的,钢材中的锰和硫是影响H:S腐蚀的主要元素。
硫会在钢材中形成FeS非金属杂质以及MnS的带状分布,会促使钢材部分显微组织松软,从而增加湿H2S环境下应力氢致开裂的敏感性。
同样锰也在钢材的生产及焊接过程中,形成贝氏体和马氏体等高强低韧的显微金相组织,从而使钢材呈现出高硬度,为焊后组织开裂增添了可能性,导致设备抗硫化物应力腐蚀开裂非常不好。
所以在选用设备的钢材时应该注意钢材的成份,切忌在H2S量较大的场合使用锰和硫含量较高的钢材。
而且要对钢材进行防腐表面处理和回火等增加钢材强度的操作。
关于设备的结构设计上应最好选择连续结构,如为了避免应力集中,焊接件与焊接件的焊缝应过渡圆滑,防止形状突变。
特别对应力较集中的重要方位,应考虑增加其厚度,比如设备的连接处和支承处,在设计时要高度重视。
因为如果结构设计不合乎常规就会造成该位置的应力集中,从而产生局部应力,再在湿H2S 介质的影响下就会导致应力腐蚀,会产生较严重后果。
结构设计导致化工设备被腐蚀主要有:异种钢焊接和设备同一受压元件或尺寸发生突变两种情况。
第一种情况是因为合金成分或金相组织的不同,使焊接接头的局部应力升高,便导致焊缝出现裂纹的情况较多。
所以在设计上最好不要采用异种钢焊接。
第二种情况是固定管板换热器的管板与薄壁筒体的焊接最常见的结构。
这个位置除了焊接热应力外,还存在不连续应力,所以在操作过程中还要认真思考法兰弯矩所带来的弯曲应力。
湿硫化氢环境中设备应力腐蚀分析及控制
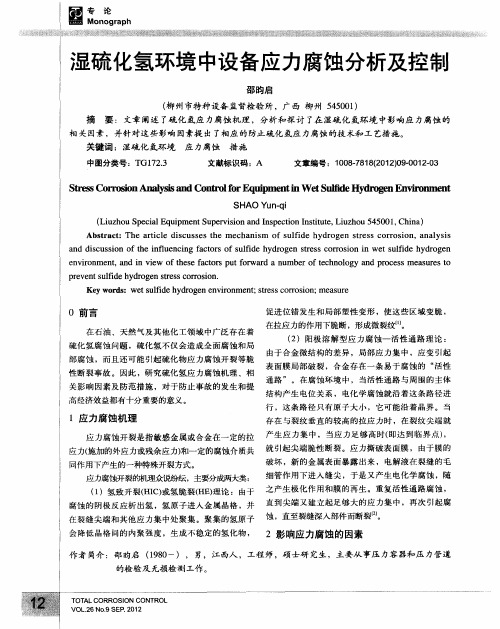
物 力 蚀 裂 利 元 有i nPs 。 当 料 受 超 屈 极 值 , 会 腐 应 腐 开 不 的 素 N M、和 等 因 材 所 譬 值 过 服 限 时 才 对 蚀 、
e v r n n , d i i w ft e e f c o s p t o wa d a n m b ro c n l g n r c s a u e o n io me t a v e o s a t r u r r u e ft h o o y a d p o e s me s r st n n h f e
全面 腐 蚀 控 制
第2 卷第9 0 月 6 期2 1 年9 2
豳 豹
3 1材 料控 制 _ 要严格控制工作环境中的H S 含量 ,按 照有关标
( )选择 合适强度和硬度的材料 。随着材料强 准的规定 ,使硫化氢分压小 于30 a 1 5 P ,另外也可以加
度 的提 高 ,应力 腐蚀破 裂的敏感 性也提 高 ,破 裂临 入一定的缓蚀剂来延缓其腐蚀速率。
会 造成 其化学成 分 、显 微组织 、强度 、硬度 、韧性 在水 中的H s z溶解度大于等于1 0 ; 0×1~ 等不 同 ,因此 ,影响硫 化氢应 力腐蚀 的程 度也会 不 同。硫化氢应 力腐蚀开裂的影响因素主要有 :
, ( )冶金 因素 :金相组织 、化学成分 、强度、 1 硬度 、夹杂和缺 陷 ;
a d d s u so fte i f e c n a t r fs l d y r g n sr s or so n we u fd y r g n n ic si n o h n l n ig fco so u f e h d o e te sc ro i n i ts l e h d o e u i i
石油化工设备在湿硫化氢环境中的腐蚀与防护_姚艾

收稿日期:2008-05-09作者简介:姚 艾(1967-),女,甘肃庆阳市人,工程师,从事特种设备安全方面的工作。
文章编号:1000-7466(2008)05-0096-02石油化工设备在湿硫化氢环境中的腐蚀与防护姚 艾(庆阳市特种设备检验所,甘肃庆阳 745000)摘要:针对石油化工设备在湿硫化氢环境下普遍发生的腐蚀现象,通过对硫化氢腐蚀机理的探讨,分析了影响腐蚀的因素,提出了防止硫化氢腐蚀除降低源头介质中硫的质量分数外,还应对设备设计、制造、检验及使用等环节提出要求,才能保证石油化工设备的安全正常运行。
关键词:石油化工设备;湿硫化氢;腐蚀;防护中图分类号:TQ 050.9 文献标志码:BCorrosion of Petrochemical Equipment in Wet H 2S Condition and the ProtectionYAO Ai(Qing yang Inspection Institution fo r Special Equipments ,Qingy ang 745000,China )A bstract :Large co rrosion o n petrochemical equipments o ccurs under the co ndition o f we t H 2S .Based on the survey of co rrosio n mechanism by w et H 2S ,the facto rs causing corro sion w as ana -ly sed and measured to prevent such co rrosio n by reducing sulfur co ntents from inlet source .The key steps in design ,fabrication ,inspecting ,and usag e w ere introduced .Key words :petrochemical equipment ;w et H 2S ;co rrosio n ;pro tection 2006年8月庆阳市特种设备检验所在对中石油庆阳石化分公司的压力容器进行全面检验时,发现2003年投用的液态烃沉降罐(材质16M nR )罐体内壁表面有氢致鼓包多处,其最大直径约200m m 。
湿硫化氢环境下管线的腐蚀及防护
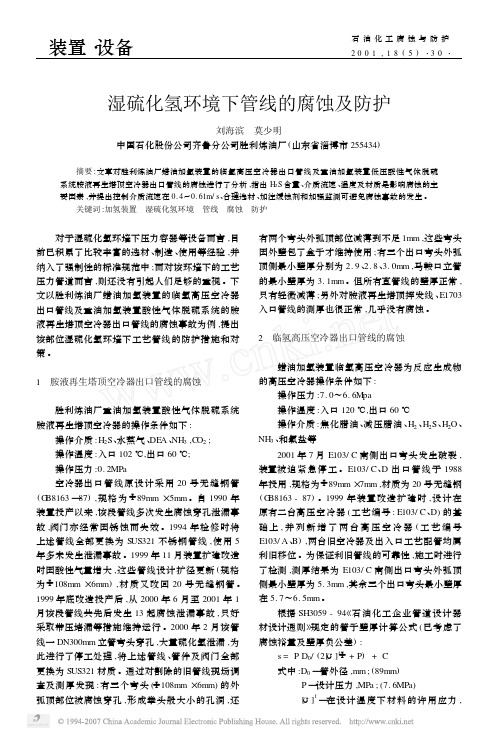
· 32 · 石油化工腐蚀与防护 第 18 卷
有一定的溶解氧 ,会以 FeS 为阴极形成闭塞电池 , 涡流冲蚀减薄 。从测厚计算出的腐蚀率情况来看 ,
产生坑蚀 。
E103/ A 、B4 个出口弯头的局部最大腐蚀率分别为
3 腐蚀原因分析
3. 1 介质的影响 管线腐蚀损坏的根本原因是加氢反应中生成 了大量硫化氢 ,与再生塔内的水蒸气或高压空冷器 的注入水经过冷却后形成了 H2S - NH3 - H2O CO2 的腐蚀环境 。对空冷器出口 20 号钢内表面腐 蚀产物进行 X 射线衍射定性相和能谱分析表明 , 腐蚀产物主要是含铁的硫化物 FeS、FeS2和铁的氧 化物 FeO ( OH) 、FeO 、Fe2O3 , 说 明 腐 蚀 主 要 是 由 H2S、CO2 引起的 。
2 临氢高压空冷器出口管线的腐蚀
蜡油加氢装置临氢高压空冷器为反应生成物 的高压空冷器操作条件如下 :
操作压力 :7. 0~6. 6Mpa 操作温度 :入口 120 ℃,出口 60 ℃ 操作介质 :焦化腊油 、减压腊油 、H2 、H2S、H2O 、 NH3 、和氯盐等 2001 年 7 月 E103/ C 南侧出口弯头发生破裂 , 装置被迫紧急停工 。E103/ C、D 出口管线于 1988 年投用 ,规格为Φ89mm ×7mm ,材质为 20 号无缝钢 ( GB8163 - 87) 。1999 年装置改造扩建时 ,设计在 原有二台高压空冷器 (工艺编号 : E103/ C、D) 的基 础上 ,并列新增了两台高压空冷器 (工艺编号 E103/ A 、B) ,两台旧空冷器及出入口工艺配管均属 利旧移位 。为保证利旧管线的可靠性 ,施工时进行 了检测 ,测厚结果为 E103/ C 南侧出口弯头外弧顶 侧最小壁厚为 5. 3mm ,其余三个出口弯头最小壁厚 在 5. 7~6. 5mm。 根据 SH3059 - 94《石油化工企业管道设计器 材设计通则》规定的管子壁厚计算公式 (已考虑了 腐蚀裕量及壁厚负公差) : s = P D0/ (2[σ]tΦ + P) + C 式中 :D0 —管外径 ,mm ; (89mm)
硫化氢应力腐蚀原理与防护措施

硫化氢应⼒腐蚀原理与防护措施炼油与化⼯REFINING AND CHEMICAL INDUSTRY第20卷碳钢及低合⾦钢在湿度较⼤的硫化氢环境中易发⽣硫化物应⼒腐蚀(SSC),对⽯油、⽯化⼯业装备的安全运⾏构成很⼤的威胁。
对低浓度硫化氢环境,可通过净化材质、⼤幅降低S、P含量、改善材料组织结构等措施,对应⼒腐蚀起到有效抑制作⽤。
⼤庆⽯化公司ATK-101B天然⽓液体球罐(1500m3)在进⾏全⾯检验时,采⽤内表⾯磁粉检测发现27处焊缝纵向裂纹,最长的为1.6m,深度为6mm,见图1。
⽂中以ATK-101B天然⽓液体球罐为对象,对其基础材料分别进⾏硫化氢应⼒腐蚀性能试验和机理分析,并提出防护措施。
1硫化氢腐蚀机理1.1硫化氢的特性H2S在⽔中的溶解度很⼤,⽔溶液具有弱酸性,如在0.1MPa、30℃⽔溶液中H2S饱和浓度为300mg/L,溶液的pH值为4。
H2S不仅对钢材具有强烈的腐蚀性,⽽且对⼈体的健康和⽣命安全也有很⼤的危害性[1]。
H2S应⼒腐蚀的基本类型可分为应⼒腐蚀开裂、氢诱导裂纹、氢⿎泡等。
在ATK-101B天然⽓液体球罐的检测中发现,根据裂纹的宏观和微观形貌特征,可以判定裂纹为应⼒腐蚀开裂,见图2~5。
图2裂纹穿晶扩展图3裂纹台阶穿接特征图4裂纹两侧马⽒体组织图5裂纹内腐蚀产物1.2硫化氢腐蚀规律⽯油加⼯过程中的H2S主要来源于含硫原油中的有机硫化物,如硫醇和硫醚等。
这些有机硫化物在原油加⼯过程中受热会分解出H2S。
⼲燥的H2S对⾦属材料⽆腐蚀破坏作⽤,H2S只有溶解在⽔中,才具有腐蚀性。
在ATK-101B 天然⽓液体球罐的检测中发现,应⼒腐蚀不同于⼀般性腐蚀引起的机械破损,也不是整个储罐的⼤⾯积减薄,⽽是发⽣在局部的罐体区域,具有较⼤的突然性[2]。
1.3腐蚀条件(1)腐蚀环境。
①介质中含有液相⽔和H2S,且H2S浓度越⾼,应⼒腐蚀引起的破裂越可能发⽣。
②⼀般只发⽣在酸性溶液中,pH⼩于6容易发⽣应⼒腐蚀破裂;pH⼤于6时,硫化铁和硫化亚铁所形成的膜有较好的保护性能,不易发⽣应⼒腐蚀破裂。
论述炼油设备的湿硫化氢腐蚀与防治方法

论述炼油设备的湿硫化氢腐蚀与防治方法近年来,石油公司大幅度的增加了对含硫或者高含硫原油的加工数量,因而炼油设备也出现比较严重的腐蚀现象。
而在各个种类的腐蚀中,最为严重或者说对设备伤害最大的是高温硫腐蚀以及湿硫化氢造成的设备损坏。
对于高温硫腐蚀只要更换采用适当的耐高温硫腐蚀的设备材料即可大大的缓解此类腐蚀,但是对湿硫化氢所造成的腐蚀进行防治就会有较大的困难。
含硫原油对设备进行腐蚀从而产生硫铁化合物,而硫铁化合物一旦与空气中的氧气接触,它们就会迅速的发生化学反应,也会产生大量的热。
如果这些热量不能够及时的向周边消散,就会导致设备局部迅速升温,而原油属于可燃物质,这就很可能引起具有可怕后果的自燃事故,也会对人类的正常生活及经济活动带来巨大的损失。
下面我们将会着重讨论引起这类事故主要原理及相应的预防治理措施。
1 湿硫化氢对设备的腐蚀机理湿硫化氢在水中极易发生离解,它的腐蚀过程就是一个化学反应,在阳极会出现一般性腐蚀,结果为产生FeS的膜。
从而使金属表面遭到破坏,形成腐蚀坑而出现回路电池的作用,是破坏程度进一步加深。
而在阴极处会出现因化学反应而生成的活性很强的氢,它会在金属比较脆弱的部位比如金属的缺陷处、焊接缺陷处聚集,产生氢鼓包导致金属结构遭到破坏,即使是高强钢也难逃其魔爪。
这种现象我们通常称其为湿硫化氢应力腐蚀开裂。
一般来说,强度越高的钢越容易因此应力而受到损坏,因为强度越高,钢对应力的腐蚀也就越敏感。
碳酸盐或者是湿硫化氢还有氢氧化物等许多无机物质都是我们生产当中比较常见的应力腐蚀环境。
在我国的炼油企业中,大多数都是采用的低合金高强度钢作为其压力容器的主要材料,而之前我们也明确的表述了湿硫化氢对高强度钢的腐蚀是较为厉害的。
湿硫化氢造成的腐蚀最早出现在油田设备和管道设施上,由于近几年出现的几起重大事故,湿硫化氢也自然而然的走进了我们的视野当中,而这几起事故当中发生在1984年的雷蒙特三号炼油厂的事故就是一个最典型的案例。
浅析炼油设备中的湿硫化氢腐蚀与防护
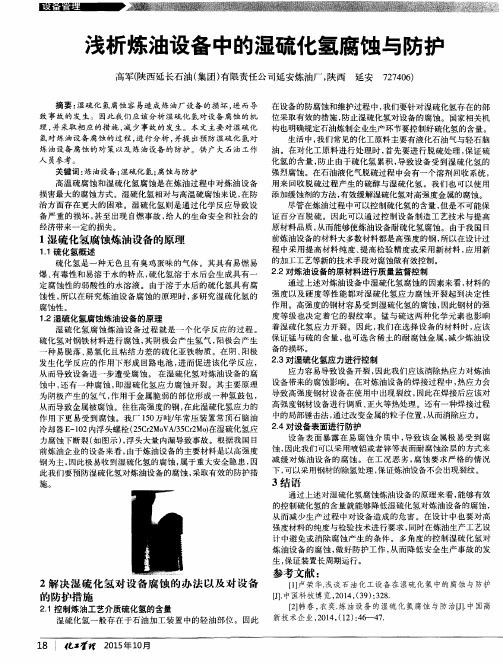
高军 ( 陕 西延 长石 油 ( 集团) 有 限责任 公 司延安炼 油厂 , 陕西 延安 7 2 7 4 0 6 )
摘要 : 湿硫化 氢 腐蚀容 易造 成炼 油厂 设备 的损 坏 , 进 而导 在 设备 的防腐蚀和 维护过程 中 , 我们要针 对湿硫化 氢存在 的部 致事 故的发 生 。 因此 我们 应该 分析 湿硫化 氢对 设备 腐蚀 的机 位采取有效 的措施 , 防 止湿硫化 氢对设备 的腐蚀 。国家相 关机 理, 并采 取相应 的措 施 , 减 少事 故的发 生 。本文 主要 对湿硫 化 构也明确规定石 油炼 制企业生产环 节要 控制好硫化氢 的含量 。 氢对 炼油设备 腐蚀 的过 程 , 进行 分析 , 并提 出预 防湿硫 化 氢对 生活 中 , 我 们常见 的化 工原料 主要有 液化石油 气与轻 石脑 炼油设 备 腐蚀 的对策 以及 炼油设 备 的防护 。供 广 大石 油 工作 油 。在 对化 工原 料进行 处理 时 , 首 先要进 行脱 硫处 理 , 保证 硫
度等级 也决 定 着它 的裂纹 率 。锰与 硫这 两种化 学元 素也 影响 着湿硫 化氢 应 力开裂 。 因此 , 我们 在选 择设备 的材 料时 , 应该 保证锰 与硫 的含 量 , 也 可选含 稀土 的耐 腐蚀金 属 , 减 少炼 油设 备的损坏 。
2 . 3对湿硫化氢应力进行控制
应 力容易导致 设备开 裂 , 因此我们 应该消除 热应 力对 炼油 设备带 来的腐蚀 影响 。在 对炼油 设备的焊 接过程 中 , 热应 力会 导致高 强度钢材 设备在使 用 中出现 裂纹 , 因此在 焊接后应 该对 高强 度钢材设 备进行调 质 、 正火等热 处理 。还 有一种焊接 过程 中的局部锤 击法 , 通 过改变金属 的粒 子位置 , 从而消除应 力。
石油化工设备在湿硫化氢环境中的腐蚀与防护措施

石油化工设备在湿硫化氢环境中的腐蚀与防护措施作者:张彦杰来源:《环球市场》2019年第33期摘要:本文在全面了解腐蚀原理的基础上,对湿硫化氢环境下石油化工设备腐蚀情况、影响因素进行了分析,并提出了几点防护措施。
关键词:湿硫化氢;石油化工设备;腐蚀原理一、腐蚀原理在湿硫化氢环境中,石油化工设备多会出现四种腐蚀情况,即氢鼓包(HB)、氢致开裂(HIC)、硫化氢应力腐蚀开裂(sscc)和应力导向氢致开裂(SOHIC),四种腐蚀机理各有不同,如应力导向氢致开裂(SOHIC),此类开裂裂缝较为细小,多处于夹杂物和缺陷出,裂纹方向基本相同,是较为常见的一种腐蚀开裂情况。
硫化氢应力腐蚀开裂(SSCC)则是指湿硫化氢分子会形成氢原子,当钢内进入氢原子之后,便会对钢内部造成影响,从而产生钢脆弱,导致应力开裂。
氢致开裂(I-IIC)是指有氢气泡存于钢材内部,在压力增加的同时,较小的氢气泡则会逐步产生裂纹,随着时间的延长,裂纹将呈阶梯状连在一起,此时在表面的裂纹将呈带状分布,开裂程度越来越严重,危害越来越大,最终影响设备正常运行。
氢鼓泡(HB)是指设备在被含硫化物腐蚀的过程中,将会有氢原子被分解出来,且涌入钢材内,并形成氢气,具有较大膨胀力,当分子聚集到一定程度时,将大大增加对外界的压力,并由此构成氢鼓泡,产生裂纹。
一般情况下,这种裂纹多出现于设备内壁。
一般情况下,这种腐蚀很难恢复,检修难度较大。
在机械设备腐蚀过程中,设备的腐蚀反应过程如下:硫化氢在水中发生电离:渗透到钢材内)通过上述反应过程,在水溶液内硫化氢内的氢离子将被分解出来,由钢内获取电子之后,可还原为氢原子。
氢原子的亲和力较强,极易结合起来并构成氢分子排出。
若由硫化物、氰化物等存于环境内,将会影响氢原子的亲和力,甚至破坏氢分子产生的反应。
这种情况下,钢内部极易渗入氢原子,并在晶格内溶解。
氢原子溶解后,游离性极强,将会对钢材的流动性、断裂行为等产生不利影响,甚至出现氢脆情况。
湿硫化氢环境腐蚀与防护讲解

湿硫化氢环境腐蚀与防护第一章总则1.1 为规范湿硫化氢环境腐蚀与防护工作,防止发生安全事故,依据国家有关法规、标准,制定本指导意见。
1.2石油化工装置在湿硫化氢环境(含有气相或溶解在液相水中,不论是否有氢气存在的酸性工艺环境)使用的静设备,为抵抗硫化物应力腐蚀开裂(SSC)、氢诱导开裂(HIC)和应力导向氢诱导开裂(SOHIC),在设计、材料、试验、制造、检验等方面的要求。
生产、技术、设计、工程、检修、科研等部门应积极参与和配合设备管理部门做好相关工作。
1.3对处于湿硫化氢腐蚀环境中的设备抗 SSC、HIC/SWC 和 SOHIC 损伤的最低要求,其中包括碳钢和低合金钢,以及碳钢及低合金钢加不锈钢的复合钢板制造的设备。
但不包括采用在金属表面(接触介质侧)增加涂层(如喷铝等)防止基体材料腐蚀开裂的设备。
1.4凡处于湿硫化氢环境中的设备在材料选择、设备制造与检验均应满足本标准的要求,否则可能导致设备 SSC、HIC/SWC 和 SOHIC 的破坏。
1.5不包括湿硫化氢引起的电化学失重腐蚀和其他类型的开裂。
1.7 湿硫化氢腐蚀环境的定义与分类:1.7.1 介质在液相中存在游离水,且具备下列条件之一时称为湿硫化氢腐蚀环境:(1)在液相水中总硫化物含量大于 50ppmw;或(2)液相水中 PH 小于 4 且总硫化物含量大于等于 1ppmw;或(3)液相水中 PH 大于 7.6 及氢氰酸(HCN)大于等于 20ppmw,且总硫化物含量大于等于 1ppmw;或(4)气相中含有硫化氢分压大于 0.0003MPa(0.05psia)。
1.7.2 根据湿硫化氢腐蚀环境引起碳钢和低合金钢材料开裂的严重程度以及对设备安全性影响的大小,把湿硫化氢腐蚀环境分为 2 类,在第I 类环境中主要关注 SSC,而在第Ⅱ类环境中,除关注 SSC 外,还要关注HIC 和 SOHIC 等损伤。
具体划分类别如下:第 I 类环境(1)操作介质温度≤ 120℃;(2)游离水中硫化氢含量大于 50ppmw;或(3)游离水的 PH < 4,且含有少量的硫化氢;或(4)气相中硫化氢分压大于 0.0003MPa(绝压);或(5)游离水中含有少量硫化氢,溶解的 HCN 小于 20ppmw,且 PH >7.6。
湿硫化氢环境腐蚀与防护
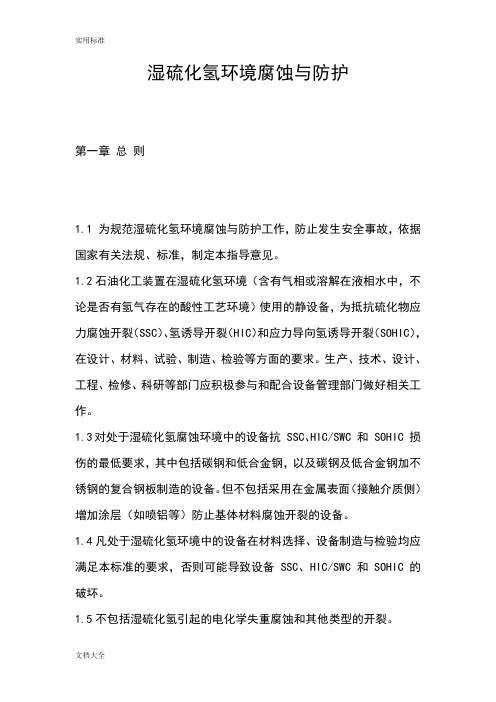
湿硫化氢环境腐蚀与防护第一章总则1.1 为规范湿硫化氢环境腐蚀与防护工作,防止发生安全事故,依据国家有关法规、标准,制定本指导意见。
1.2石油化工装置在湿硫化氢环境(含有气相或溶解在液相水中,不论是否有氢气存在的酸性工艺环境)使用的静设备,为抵抗硫化物应力腐蚀开裂(SSC)、氢诱导开裂(HIC)和应力导向氢诱导开裂(SOHIC),在设计、材料、试验、制造、检验等方面的要求。
生产、技术、设计、工程、检修、科研等部门应积极参与和配合设备管理部门做好相关工作。
1.3对处于湿硫化氢腐蚀环境中的设备抗 SSC、HIC/SWC 和 SOHIC 损伤的最低要求,其中包括碳钢和低合金钢,以及碳钢及低合金钢加不锈钢的复合钢板制造的设备。
但不包括采用在金属表面(接触介质侧)增加涂层(如喷铝等)防止基体材料腐蚀开裂的设备。
1.4凡处于湿硫化氢环境中的设备在材料选择、设备制造与检验均应满足本标准的要求,否则可能导致设备 SSC、HIC/SWC 和 SOHIC 的破坏。
1.5不包括湿硫化氢引起的电化学失重腐蚀和其他类型的开裂。
1.7 湿硫化氢腐蚀环境的定义与分类:1.7.1 介质在液相中存在游离水,且具备下列条件之一时称为湿硫化氢腐蚀环境:(1)在液相水中总硫化物含量大于 50ppmw;或(2)液相水中 PH 小于 4 且总硫化物含量大于等于 1ppmw;或(3)液相水中 PH 大于 7.6 及氢氰酸(HCN)大于等于 20ppmw,且总硫化物含量大于等于 1ppmw;或(4)气相中含有硫化氢分压大于 0.0003MPa(0.05psia)。
1.7.2 根据湿硫化氢腐蚀环境引起碳钢和低合金钢材料开裂的严重程度以及对设备安全性影响的大小,把湿硫化氢腐蚀环境分为 2 类,在第I 类环境中主要关注 SSC,而在第Ⅱ类环境中,除关注 SSC 外,还要关注HIC 和 SOHIC 等损伤。
具体划分类别如下:第 I 类环境(1)操作介质温度≤ 120℃;(2)游离水中硫化氢含量大于 50ppmw;或(3)游离水的 PH < 4,且含有少量的硫化氢;或(4)气相中硫化氢分压大于 0.0003MPa(绝压);或(5)游离水中含有少量硫化氢,溶解的 HCN 小于 20ppmw,且 PH >7.6。
石油化工设备腐蚀的防护与监测
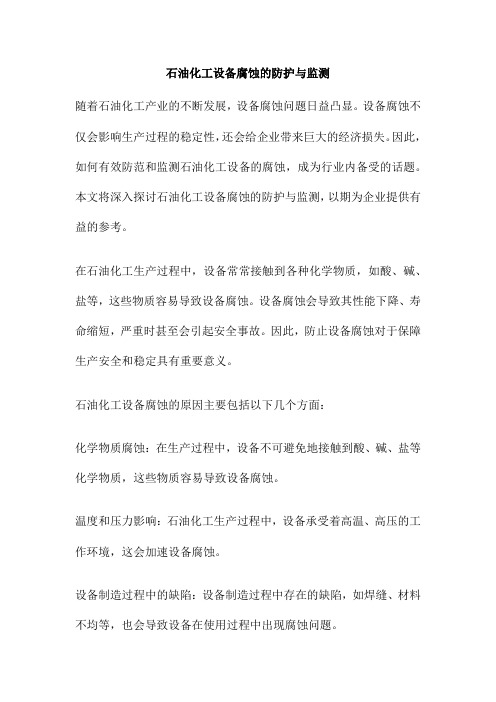
石油化工设备腐蚀的防护与监测随着石油化工产业的不断发展,设备腐蚀问题日益凸显。
设备腐蚀不仅会影响生产过程的稳定性,还会给企业带来巨大的经济损失。
因此,如何有效防范和监测石油化工设备的腐蚀,成为行业内备受的话题。
本文将深入探讨石油化工设备腐蚀的防护与监测,以期为企业提供有益的参考。
在石油化工生产过程中,设备常常接触到各种化学物质,如酸、碱、盐等,这些物质容易导致设备腐蚀。
设备腐蚀会导致其性能下降、寿命缩短,严重时甚至会引起安全事故。
因此,防止设备腐蚀对于保障生产安全和稳定具有重要意义。
石油化工设备腐蚀的原因主要包括以下几个方面:化学物质腐蚀:在生产过程中,设备不可避免地接触到酸、碱、盐等化学物质,这些物质容易导致设备腐蚀。
温度和压力影响:石油化工生产过程中,设备承受着高温、高压的工作环境,这会加速设备腐蚀。
设备制造过程中的缺陷:设备制造过程中存在的缺陷,如焊缝、材料不均等,也会导致设备在使用过程中出现腐蚀问题。
维护不当:设备维护不当,如清洗不干净、润滑不足等,也会引起设备腐蚀。
针对石油化工设备腐蚀的原因,可以采取以下防护措施:选择合适的材料:根据不同工艺和介质,选择具有抗腐蚀性能的材料,如不锈钢、合金等。
改善防腐设计:优化设备结构,减少焊缝、死角等易腐蚀区域,提高设备的抗腐蚀性能。
加强内部维护:建立完善的维护制度,定期清洗设备,保持设备内部清洁,防止化学物质沉积对设备造成腐蚀。
涂层防护:在设备表面涂覆防腐涂层,如油漆、树脂等,以隔离设备与化学物质的接触,降低腐蚀速率。
排污和排水:定期排放设备中的废液和污水,以减少设备中的有害物质,降低腐蚀风险。
缓蚀剂应用:在生产过程中加入缓蚀剂,有效减缓设备的腐蚀速率。
为了及时发现石油化工设备的腐蚀问题,采取有效的监测方法至关重要。
以下是一些常用的设备腐蚀监测方法:外观检查:定期对设备表面进行检查,特别是注意焊缝、接头等易腐蚀区域,以发现设备表面的锈蚀、色变等现象。
石化设备H2S腐蚀及控制

石化设备H2S腐蚀及控制摘要:文章针对石油炼制过程中存在的硫化物腐蚀问题,从腐蚀原因分析,腐蚀机理及腐蚀控制三方面较为系统的总结了炼油厂防止硫化氢腐蚀技术,为石化企业安全生产提供有益借鉴。
关键词:石化;H2S;腐蚀国内外已经报道过多起由于硫铁化合物所引发的事故,其中在湿H2S环境条件下的应力腐蚀开裂引起的失效事例的报道也有逐渐上升的趋势。
1腐蚀原因分析高温硫化物的腐蚀,主要是指石油炼制企业在炼制含硫或高硫原油时,发生在常减压装置240℃以上的高温重油部位以及催化裂化、延迟焦化、热裂化等装置及相应管线等部位的腐蚀。
硫化物对设备的腐蚀与温度有关。
当系统温度条件达到240℃以上时,原油中所含的硫化物开始分解,生成H2S,随着生产过程中产生的H2s逐渐累积,在高压容器或装置内部达到一定浓度后,就会对设备产生腐蚀。
研究表明,这类腐蚀会随环境温度的升高而进一步加剧腐蚀的程度。
腐蚀产物以硫铁化合物的形式存在,一方面降低了设备的机械强度和热效率,使相同压力条件下,受H2S腐蚀影响的设备易于产生应力开裂,也对设备的安全运行产生隐患。
另一方面,发生了腐蚀的设备在停工检修时,由于空气的大量流入,使腐蚀产物硫铁化合物与氧气充分接触,会发生热化学反应放出热量,此时。
需要采取相应措施,防止可能产生的因局部温度迅速升高而引起的易燃物燃烧,杜绝可能对设备、人员和安全生产带来的隐患。
综合分析表明,高温、高压、湿H2S环境下,H2S应力腐蚀是导致炼油厂设备常常受损害的最主要原因。
由于在石油炼制过程中,存在于湿H2S环境条件下的设备占有很大比例,这类具有潜在的腐蚀开裂破坏机理的环境条件给设备带来了很大隐患,大大增加了石油炼制设备的安全风险。
2腐蚀类型通过目前行业内部发生的相关事故原因分析表明,原油品质是影响炼制设备腐蚀的主要原因,由于原油中所含硫在高温高压条件下分解生成H2S,对设备产生腐蚀。
而针对常规原油设计建造的而石化炼制设备,会因原油含硫的增高而加剧设备的腐蚀程度,从而缩短安全使用期。
炼油设备中的湿硫化氢腐蚀与防护

2
湿硫化氢环境中过程设备的腐蚀开裂过
钢在湿硫化氢环境中的腐蚀反应过程如下 : 硫化氢在水中发生分解 : H2S Ω H + + HS ↓
H +S
+ 2-
程
钢在 H2S 的水溶液中发生电化学反应 : 阳极反应 : Fe ϖ Fe 2 + + 2e ϖ FeS ↓ + Fe + HS ϖ FeS ↓+ H 阴极反应 :2H + + 2e ϖ 2H ϖ H2 ↑ ↓ 2H ( 渗透到钢材中)
Fe +S
2+ 2+ 2-
从以上反应过程可以看出 , 硫化氢在水溶液中
・ 58 ・
化 工 设 备 与 管 道
第 40 卷
在氢分压的作用下 , 不同层面上的相邻氢鼓泡 裂纹相互连接 , 形成阶梯状特征的内部裂纹称为氢 诱导开裂 ,裂纹也可扩展到金属表面 。HIC 和钢材内 部的夹杂物或合金元素在钢中偏析产生的不规则微 观组织密切相关 , 而与钢材中的拉应力无关 。因而 , 焊后热处理不能改善钢材对 HIC 的抗力 。
1
前言
离解出的氢离子 , 从钢中得到电子后还原成氢原 子。 氢原子间有很大的亲和力 ,易结合在一起形成氢 分子排出 。但是 , 如果环境中存在硫化物 、 氰化物将 会削弱氢原子间的亲和力 , 致使氢分子形成的反应 被破坏 。 这样一来 ,极小的氢原子就很容易渗入到钢 的内部 ,溶解在晶格中 。 固溶于晶格中的氢原子具有 很强的游离性 , 它影响钢材的流动性和断裂行为 , 导 致氢脆的发生 。
( 1) 钢材的强度等级
感性越大 。 而 H2S 浓度越高 ,断裂时间越短 。 对低碳 钢 : 介质中 H2S 浓度在 2~ 150mg/ L 时 , 腐蚀速度增 加很快 ; < 50mg/ L 时 , 破坏时间很长 ; 150~ 400mg/ L 时腐蚀速度是恒定的 ; 增加到 1600mg/ L 时腐蚀速度 下降 。 当 H2S 浓度在 1600~ 2420mg/ L 时腐蚀速度基 本不变 。 对高强钢 : 在很低浓度 ( 1mg/ L 以下) 仍能迅 速引起 SSCC 破坏 。当钢材自身强度级别越高 、 焊接 接头的硬度偏高时 ,开裂速度加快 。 前面例 1 所述中 H2S 浓度虽然在不开裂范围内 , 但在实际调查中得 知 , 在以往的操作中对 H2S 含量的控制不是很严格 , 重视程度也不够 , H2S 浓度有一定的波动 , 抽查中曾 达到 3000~ 5000pp m。 随着问题的出现及炼高硫原油 量的不断增加 , 现该厂制定了一系列管理措施 , 严格 控制 H2S 的浓度 。 如将油品进行脱硫后存入产品罐 , 并对产品定期进行化验 。 用液化石油气 、 轻石脑油为化工原料时 , 应严格 进行脱硫处理 。 如匹配好适宜的缓蚀剂 。 当选用强度 偏高的零部件时 , H2S 含量应控制更低 。在脱硫过程 中 , 应注意脱硫塔后部及溶剂回收系统中的残留的 湿 H2S - CO2 的再腐蚀 。 6. 2 严格控制湿硫化氢环境的 p H 值 当 p H 值较低时 , 湿 H2S 离解过程中生成的 H + 浓度增加 , 大量的 [ H] 渗入钢中 , 加速了氢鼓泡 、 氢 诱导裂纹 、 和应力向氢诱导裂纹的腐蚀过程 , 尤其是 高强钢更为敏感 。国内外的试验证实 ,当 p H > 5 时 , 氢致开裂的敏感性可减缓 , 调节好介质中的 p H , 可 缓和湿硫化氢环境下的氢腐蚀 。 6. 3 消除应力处理
石油化工设备在湿硫化氢环境中的腐蚀与防护

Ab t a t La g o r s o n p t o h m ia q i me t c u s u d r t e c n ii n o tH 2 . sr c : r e c r o i n o e r c e c le u p n s o c r n e h o d t fwe o S
油加 工的第 一道 工 序 、 油 厂二 次 加 工装 置 的轻 油 炼 部位 、 石油化 工催 化装 置及 液化 石油气 储罐 等部 位 。
根据 有关 文献 并结 合 庆 阳石 化 分 公 司 的实 际情 况 , 设备 介质 中存 在硫化 氢成 分是 导致 上述压 力容 器发
生腐 蚀损 坏 的根本原 因 。
另外, 在使 用 中也 存 在 着许 多 引 起 局部 高应 力 的因 素 , 括 力 学 或 化 学 损 伤 , 如磨 损 、 蚀 、 包 诸 磨 点 蚀 、 间腐蚀 、 晶 浓差 电池 腐 蚀 、 隙腐 蚀 等 各 种 形 式 缝 的局部 腐蚀 ; 构件 各 部 分处 于不 同 温度 下 产 生 的 温 差 应力 ; 、 、 、 碳 氢 氮 氧等 气态 碳化 物介质 扩散 进入 金
1 原 因 分 析
庆 阳石化 分 公 司所 用 原油 中含硫 量 有 时偏 高 ,
从设备 使用 单位 的分 析 数 据 得 知 , 出现 问题 设 备 已 的介 质 中不 同程 度都含 有硫 。原油 在提炼 中虽经脱 硫处 理但脱 硫 效 果 并 不 稳 定 , 因此 , 硫 化 氢 环 境 湿 ( S H。 +H。 型 的腐 蚀 环 境 ) 泛 存 在 于炼 油 厂 原 O 广
分析 了影响 腐蚀 的 因素 , 出 了防止硫化 氢腐 蚀 除降低 源 头介 质 中硫 的质 量分数 外 , 应对设 备设 提 还 计、 制造 、 验及使 用等 环节提 出要 求 , 检 才能保 证石 油化 工设备 的 安全 正常运 行 。
- 1、下载文档前请自行甄别文档内容的完整性,平台不提供额外的编辑、内容补充、找答案等附加服务。
- 2、"仅部分预览"的文档,不可在线预览部分如存在完整性等问题,可反馈申请退款(可完整预览的文档不适用该条件!)。
- 3、如文档侵犯您的权益,请联系客服反馈,我们会尽快为您处理(人工客服工作时间:9:00-18:30)。
石油化工设备在湿硫化氢环境中的腐蚀与防护分析摘要:石油化工设备在湿硫化氢环境中经常被腐蚀,这种腐蚀现象对设备的危害极大。
本文对硫化氢腐蚀产生的原因,腐蚀的几种形式,影响腐蚀的因素以及解决腐蚀的措施都进行了深入的分析。
为了保证设备的使用寿命,必须采取必要的防腐措施。
关键词:石油化工设备湿硫化氢原因机理影响措施
一、前言
2006年8月,中石油某分公司在本市的某特种设备检验所全面检验了压力容器。
发现三年前刚刚投入使用的液态烃沉降罐,其罐体内部出现了多处氢致鼓包,最大鼓包的直径居然有200mm。
其他出现鼓包的地方是富气水洗罐、储存液化石油气的储罐、异构化装置、换热器。
这些地方不但出现了鼓包,还出现了分层和微裂纹现象。
如果不改变原工艺条件,有些设备的缺陷还会不断产生,已有的缺陷还会继续发展。
这些缺陷虽然多,但大部分的缺陷具有相同点,因此,对这些缺陷可以进行集中研究,研究意义重大。
二、产生的原因
中石化某分公司用的原油,有些含硫量比较高。
使用设备的单位对数据进行分析后得知,出现问题的设备都含有硫,只不过有些含硫量大,有些含硫量小而已。
原油在提炼时,固然有脱硫处理这一环节,但脱硫后的效果并不稳定。
湿硫化氢环境是指一种硫化氢加水的腐蚀环境。
因此,湿硫化氢环境广泛存在于炼油工序中,主要存在于以下部位:
(一)第一道工序的全部部位;
(二)二次加工中储存液化石油气的储罐;
(三)二次加工中催化装置;
(四)二次加工中轻油部位。
根据对该分公司实际情况的调查,并结合相关文献,分析出设备被腐蚀的根本原因是:设备介质中些许硫化氢的存在。
此外,在使用中也存在一些别的因素导致的局部高应力,这些因素包括:化学损伤、力学损伤、缝隙腐蚀、浓差电池腐蚀、晶间腐蚀、点蚀、磨蚀、磨损、温差应力(构件各部分的环境温度不同导致)、残存应力的存在等还有就是氧、氮、氢、碳等气态碳化物进入金属构件的内部。
这些因素都能引起局部高应力。
设备处在腐蚀环境中,再加上高应力的作用,腐蚀和损坏就在所难免了。
三、腐蚀的机理
在湿硫化氢的腐蚀环境中,碳钢设备容易发生两种腐蚀:一是应力腐蚀开裂;二是均匀腐蚀。
开裂的形式有以下四种:(一)应力导向氢导致的开裂:
这种开裂方式是:夹杂物和缺陷处存在一排排的小裂纹(因为氢聚集而形成),这些小裂纹的发展方向和应力的方向垂直,由应力引导着发展。
这种开裂一般发生在高应力集中区和焊接接头的热影响区,如应力腐蚀开裂的地方、裂纹状缺陷的地方、突变呈几何形状的地方和接管处。
(二)硫化物、应力导致的腐蚀开裂:
湿硫化氢会产生氢原子,这些氢原子会渗透到钢内部,溶解在晶格中,最终导致氢脆,在残余应力或外加应力的影响下,形成开裂。
这种开裂一般发生在高硬度区如焊缝、热影响区等。
(三)氢致开裂:
在钢材内部有氢气泡存在的区域,当这些区域氢的压力不断增高时,小的鼓泡裂纹就会逐渐互相连接,这些具有阶梯状特点的氢致开裂,分布方向平行于表面。
钢中的mns如果含有带状组织分布,会使氢致开裂更加敏感。
(四)氢鼓泡:
含硫化合物在腐蚀碳钢的过程中,会析出一些氢原子,这些原子向钢中渗透,最终在缺陷、夹渣、裂纹等处聚集而形成分子,从而产生很大的膨胀力。
分子不断聚集,对晶格界面的压力也就不断增大,最终导致界面裂开而形成氢鼓泡。
这种开裂形式主要分布在设备的内壁浅表面。
四、影响因素
当ph值接近弱碱性或中性时,钢中氢的溶解量最低,当ph值接近强酸性或强碱性时,也就是过高或过低时,钢中氢的溶解量都会很高。
空气中的氨离子,会使硫化氢的应力腐蚀更加敏感。
当ph 值接近强酸性时,也就是比较低时,二氧化碳会使硫化氢的应力腐蚀更加敏感。
当ph值接近强碱性,也就是比较高时,二氧化碳起的作用则相反。
介质中硫的质量分数越高,就越容易发生硫化氢腐蚀。
原油中
的硫化物经过裂化或催化,形成硫化氢,同时原油中还含有氰化物,氰化物会对硫化氢的腐蚀起明显的促进作用。
氰化物在呈碱性的湿硫化氢溶液中,会起两种作用:
(一)将溶液中的缓蚀剂去掉;
(二)将硫化铁的保护膜溶解掉,使硫化氢腐蚀的速度更加快,而且还会使金属的表面更容易被氢渗透。
钢中硫元素、磷元素、镍元素、氢元素的质量分数越高,钢的硬度也就越高,就越容易被硫化氢腐蚀。
温度对腐蚀也有影响,但对不同类型的腐蚀影响程度也不一样,硫化氢在20℃的环境下,应力腐蚀最强,温度无论升高还是降低,应力腐蚀的敏感性都会随之降低。
应力包括:薄膜应力、焊接残余应力和强行装配组焊导致的附加应力等。
较高的局部应力、高浓度的硫化氢和水、高强度的钢焊缝区存在的淬硬组织都很容易导致硫化氢应力腐蚀的发生。
五、解决措施
(一)合理选择用材
如果只是硫化氢的浓度大于50mg/l,那么在这种环境中,壳体材质最好选用抗拉强度小于或等于414mpa的碳锰钢或碳钢。
如果不但硫化氢的浓度大于50mg/l,而且氰化物的浓度也在20mg/l以上,那么在这种腐蚀环境中,壳体材质最好选用碳锰钢或碳钢,而且要加上0cr13钢,组成复合钢板,内件最好用0cr13钢,而且,所有的钢都要用真空脱气法来制造。
此外,努力提高钢材的纯度,
将钢中的磷、硫、锰的质量分数降到最低,也是降低腐蚀的不错措施。
(二)制造环节的措施
第一、将焊缝硬度控制在200hb以下;第二、尽量降低焊缝中合金的含量;第三、设备焊后要进行热处理,这样做可以消除焊接的残余应力;第四、在设备制造过程中,要用射线和超声波对焊缝进行探伤检查;第五、设备的几何尺寸一定要符合相关的标准规定;第六、竭力避免进行强力组装。
(三)检验环节的措施
在检验压力容器时,要完成以下检测:第一、x射线探伤;第二、超声波探伤;第三、内表面溶剂去除渗透检测(或内表面荧光磁粉渗透检测);第四、锂氏硬度检测;第五、测厚;第六、认真观察设备的结构和表面状况。
如果发现缺陷,应该根据缺陷的数量、缺陷的发生部位、缺陷的形态,再加上上面六种检验的结果,进行分析判断,必要时还可以再结合硬度检测、强度检测、无损探伤的结果,最终确认缺陷的性质,消除隐患,保证设备在使用时的安全。
全相检验和一些其他的检验手段也可以确认缺陷的性质。
(四)使用环节的措施
在使用过程中,要严格按工艺操作的规程进行有关防腐的测试,同时及时添加碱和缓蚀剂等,设备的高位部位,要做好日常的腐蚀监控,并加强防护力度。
六、结语
上文通过对中石油某分公司出现问题的分析,可以得出导致石油化工设备在湿硫化氢环境中被腐蚀的原因很多,加速腐蚀的因素也很多。
在石油化工行业中,含硫化氢石油的装置大部分由碳钢组成,因此,腐蚀问题可以说是全行业的问题,解决此类问题意义重大。
如果想解决此类问题,保证设备安全、稳定的运行,避免操作人员人身安全受到威胁,那么必须从维护、使用、检验、制造甚至是设计等环节找到问题所在,从根本上解决设备的腐蚀问题。
参考文献:
[1] 姚艾. 石油化工设备在湿硫化氢环境中的腐蚀与防护[j].石油化工设备,2008,37(05).
[2] 赫荣鑫,周忠凯,韩冰. 湿硫化氢环境下金属材料的应力腐蚀原因分析与预防[j].石油和化工设备,2011,14.
[3] 郑结根. 液化石油气(lpg)球罐的湿硫化氢腐蚀与防护[j].石油化工设备技术,2005,26(06).。