15CrMoR制压力容器技术条件
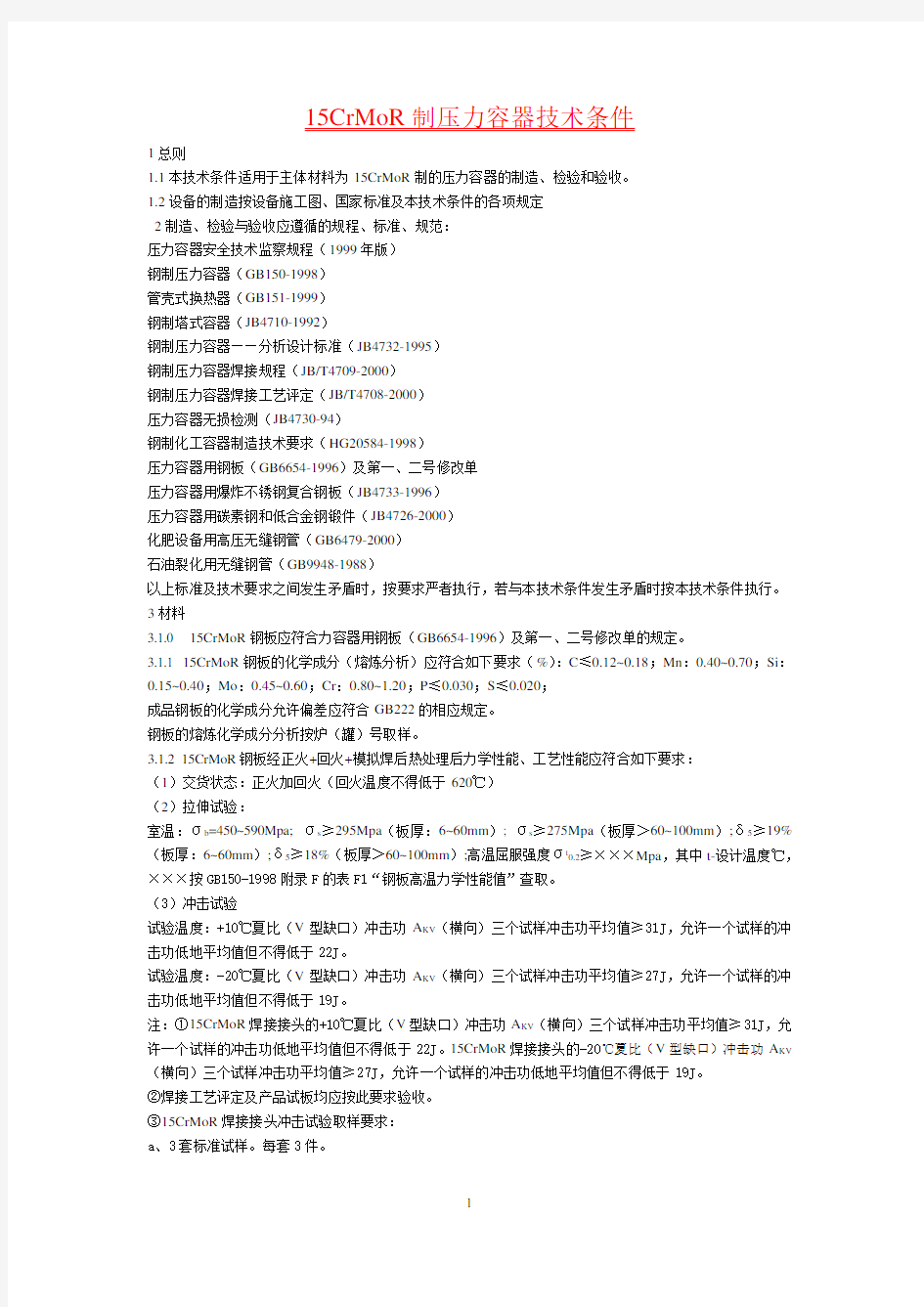

15CrMoR制压力容器技术条件
1总则
1.1本技术条件适用于主体材料为15CrMoR制的压力容器的制造、检验和验收。
1.2设备的制造按设备施工图、国家标准及本技术条件的各项规定
2制造、检验与验收应遵循的规程、标准、规范:
压力容器安全技术监察规程(1999年版)
钢制压力容器(GB150-1998)
管壳式换热器(GB151-1999)
钢制塔式容器(JB4710-1992)
钢制压力容器——分析设计标准(JB4732-1995)
钢制压力容器焊接规程(JB/T4709-2000)
钢制压力容器焊接工艺评定(JB/T4708-2000)
压力容器无损检测(JB4730-94)
钢制化工容器制造技术要求(HG20584-1998)
压力容器用钢板(GB6654-1996)及第一、二号修改单
压力容器用爆炸不锈钢复合钢板(JB4733-1996)
压力容器用碳素钢和低合金钢锻件(JB4726-2000)
化肥设备用高压无缝钢管(GB6479-2000)
石油裂化用无缝钢管(GB9948-1988)
以上标准及技术要求之间发生矛盾时,按要求严者执行,若与本技术条件发生矛盾时按本技术条件执行。3材料
3.1.0 15CrMoR钢板应符合力容器用钢板(GB6654-1996)及第一、二号修改单的规定。
3.1.1 15CrMoR钢板的化学成分(熔炼分析)应符合如下要求(%):C≤0.12~0.18;Mn:0.40~0.70;Si:0.15~0.40;Mo:0.45~0.60;Cr:0.80~1.20;P≤0.030;S≤0.020;
成品钢板的化学成分允许偏差应符合GB222的相应规定。
钢板的熔炼化学成分分析按炉(罐)号取样。
3.1.2 15CrMoR钢板经正火+回火+模拟焊后热处理后力学性能、工艺性能应符合如下要求:
(1)交货状态:正火加回火(回火温度不得低于620℃)
(2)拉伸试验:
室温:σb=450~590Mpa; σs≥295Mpa(板厚:6~60mm); σs≥275Mpa(板厚>60~100mm);δ5≥19%(板厚:6~60mm);δ5≥18%(板厚>60~100mm);高温屈服强度σt0.2≥×××Mpa,其中t-设计温度℃,×××按GB150-1998附录F的表F1“钢板高温力学性能值”查取。
(3)冲击试验
试验温度:+10℃夏比(V型缺口)冲击功A KV(横向)三个试样冲击功平均值≥31J,允许一个试样的冲击功低地平均值但不得低于22J。
试验温度:-20℃夏比(V型缺口)冲击功A KV(横向)三个试样冲击功平均值≥27J,允许一个试样的冲击功低地平均值但不得低于19J。
注:①15CrMoR焊接接头的+10℃夏比(V型缺口)冲击功A KV(横向)三个试样冲击功平均值≥31J,允许一个试样的冲击功低地平均值但不得低于22J。15CrMoR焊接接头的-20℃夏比(V型缺口)冲击功A KV (横向)三个试样冲击功平均值≥27J,允许一个试样的冲击功低地平均值但不得低于19J。
②焊接工艺评定及产品试板均应按此要求验收。
③15CrMoR焊接接头冲击试验取样要求:
a、3套标准试样。每套3件。
b、位置:第一套试样缺口开在焊缝金属上;
第二套试样缺口开在热影响区上;
第一套试样缺口开在邻近热影响的母材上;
(4)冷弯试验
b=2a,180°,d=3a。试验后试样应无裂纹。
3.1.3 15CrMoR钢板应近JB4730-94逐张进行超声检测,合格级别为Ⅰ级。
3.1.4 15CrMoR钢板厚度应以正公差供货。
3.2 15CrMoR锻件应符合JB4726-2000的规定,供货状态为正火加回火(回火温度≥620℃)。15CrMo 锻件熔炼化学成分分析按炉(罐)号取样;15CrMo锻件的力学性能应为正火+回火+模拟焊后热处理后的数值。
3.3 15CrMo无缝管材应符合GB6479-2000《化肥设备用高压无缝钢管》的规定,供货状态为正火加回火。
3.4焊接材料
3.4.1焊接材料应符合下列标准的规定:
GB5117《碳钢焊条》
GB5118《低合金焊条》
GB8110《气体保护焊用碳钢、低合金钢焊丝》
GB5293《碳素钢埋弧焊用焊剂》
GB12470《低合金钢埋弧焊用焊剂》
3.4.2焊条牌号
按图面要求。
4制造的一般要求
4.1设备应按本技术条件、图面要求和订货技术协议书进行制造与验收。主要受压元件及与其相焊的非受压元件用钢必须具有钢厂的钢材质量证明书。制造厂必须对设备的主要受压元件材料按材料标准、设计图纸、技术文件和用户协议书要求的项目进行复检,合格后方可投料制造。
4.2与壳体和封头相焊所有零部件(除垫板外)必须开坡口,所有受压焊接接头必须保证全焊透。
4.3所有焊接表面在施焊前应进行机械加工(或打磨),对于用切割方法制备的焊接坡口,应打磨至显出金属光泽的进行磁粉检测,按JB4730-94标准,其缺陷显示积累长度为Ⅰ级合格。
4.4厚壁管与壳体组焊后,内部应打磨圆滑。
4.5接管等附件在避开筒体纵、环焊缝(包括筒体与封头之间的焊缝),并与焊缝边缘的距离不得小于100mm。
4.6制造厂应根据焊接工艺评定结果编制焊接工艺规程,然后按规程对产品进行焊接。
4.7所有与设备相连接的焊件(永久性焊件及临时性焊件)均应后热处理前焊接完毕,消除应力热处理之后不得再在设备上上旋焊或动火。否则应重新进行焊后热处理。
4.8接管和吊耳、吊柱均不得与与筒体对接缝(包括筒体与封头之间的焊缝)或封头的拼接焊缝相碰,焊缝焊缝边缘的距离不得小于100mm。
4.9 15CrMo钢之间,焊缝坡口及两侧各不小于150mm的范围内的母材始终维持不低于预热温度,且不高于允许的最高层间温度,直至去进行焊后热处理,在焊接过程中,由于某种原因,必须间断焊接工作时,应使焊缝坡口及两侧各不小于150mm的范围内始终处于预热温度下,直至焊接工作重新开始。
4.10所有与15CrMo钢基体相连接的零件及予焊件(如接管、保温支承圈、吊耳、吊柱衬板、垫板、裙座筒节、梯子、平台预焊件等)均应在最终热处理前焊接完毕,最终焊后热处理后不得再在基体上动火引弧。
4.11禁止在容器的非焊接部位引弧。因电弧擦伤而产生的弧坑、弧疤,割除临时附件后遗留的焊疤,均应打磨光滑,并按JB4730-94进行100%磁粉检测,Ⅰ级合格。
4.12所有焊接表面在施焊前应进行机械加工(或打磨),对于用切割方法制备的焊接坡口,应打磨至显出金属光泽后,并按JB4730-94进行100%磁粉检测,Ⅰ级合格。
4.13 15CrMo法兰接管堆焊(如果设备有的话)
a、不锈钢堆焊层采用双层堆焊,堆焊层材料为00Cr19Ni10,堆焊层最小有效厚度不得小于4mm。堆焊焊条为:过渡层A062,2mm;盖面层A002,≥2mm。
b、必须在焊接工艺评定合格后,制定出合理的接堆积不,方能正式堆焊。
c、锻件的待堆焊表面必须经机械加工或打磨,以去除氧化皮、铁锈,并达到图样要求,经磁粉或渗透检测合格后方可进行堆焊。
d、堆焊层的焊道(包括过渡层和面层)表面应光滑平整,平面度允差≤1mm,堆焊层最厚与最薄之差≤1mm。
e、过渡层和面层应分别按JB4730-94进行100%磁粉检测,其缺陷显示积累长度为等级评定Ⅰ级为合格。
4.14接管与筒体、接管与封头之间的焊缝表面应具有圆滑过渡至母材的几何形状。
4.15焊缝和热影响区表面不允许存在咬边、裂纹、气孔、弧坑、夹杂等缺陷。焊缝上的熔渣和两侧的飞溅物必须打磨并消除干净。
4.16环槽面法兰的环槽密封面和椭圆垫的尺寸应至少每隔60°测量一次,每次测量结果均应在标准的公差范围内。密封面和椭圆垫的表面粗糙度不得低于标准或设计图样的规定。(如果设备有环槽面法兰时有此要求)
4.17壳体的A、B类焊接接头有面应齐平,焊缝加强金属高最大为2mm(如果按JB4732标准制造的话,焊缝加强金属高为0mm)。
4.18各筒体之间,筒体与封头之间环缝错边量应符合GB150(如果设计标准采用JB4732标准的是符合JB4732)或者相关的其它标准的规定。筒节纵缝的错边量应符合GB150(如果设计标准采用JB4732标准的是符合JB4732)或者相关的其它标准的规定。焊缝在其宽度范围内修磨后的斜度至少为1:3,焊缝表面要平滑过渡。
4.19 15CrMo钢弯管外侧壁厚减薄量应小于10%,椭圆度应小于7%。但两端口应修整,其椭圆度应小于2%。弯头应进行热处理,热处理工艺应由制造厂决定,但热处理后应验证其机械性能,并满足相关规定。
4.20热处理后的弯头应对其表面进行磁粉检测,如有缺陷应予以修磨,但修磨后的壁厚就不上于公称壁厚的90%。
4.21加工面和非加工面线性尺寸公差分别按GB/T1804-2000中m级和c级精度要求。
4.22壳体直线度在一米长度内的不得大于1mm,总体直线度不大地10mm。
5热处理
5.0筒体和封头用板材应进行模拟焊后消除应力热处理,模拟焊后热处理温度、时间由制造厂确定。并应检验模拟焊后消除应力热处理状态的机械性能,其要求应符合3.1.2的规定。
5.1所有Cr-Mo钢焊缝,焊前应均匀预热,中间应进行消除应力热处理(ISR)及时做消氢处理(DHT),最后进行最终焊后热处理(PWHT)。
5.2封头热冲压成形后必须进行恢复机械性能及供货状态的热处理。
5.3设备制造完毕后应进行整体消除的热处理。热处理温度由制造厂确定。在最终焊后热处理过程中,每条环焊缝隙外表面上,至少有4对沿圆周均匀的热电偶,每条纵缝上至少有两对热电偶来测量温度,并应采用连续式记录议记录温度变化。
5.4焊后热处理必须保证材料的化学成分、机械性能、金相组织不受破坏。
5.5受压元件的加工成形应采用不破坏材料机械性能及供货状态的方法进行。如果无法满足这一要求,应进行恢复材料机械性能及使用状态的热处理。
5.6制造厂应准备足够多的焊接试板和热处理试板。
5.7模拟焊后消除应力热处理的试板检验合格后,方可对设备进行制造。
6生产试板
6.1当制造厂进行正火处理时,应制作热处理验证试板1块,该试板应取在筒节延伸部分或用相同热处理制度的钢板另制1块在筒节(或封头)上,与筒节(或封头)一起进行加热和冷却。
6.1.1试板受压史及受热史应与完工设备所经历的受压史及受热史相同。
6.1.2试板应进行如下检查:
a、拉力试验,取样1件
b、冲击试验,取样31件
c、拉力及冲击试验取样位置、方向及试验结果应符合GB150的规定。
6.2产品焊接试板
6.2.1筒体A类(纵向)焊缝的产品焊接试板一付。
6.2.2筒节与筒节的B类(环向)焊缝产品焊接试板一付(当制造厂具有丰富的Cr-Mo钢设备的经验,且纵环焊缝采用相同的焊接材料和焊接工艺时可不作环焊缝试板)。
6.2.3代表DN≥150mm的接管的B类焊缝的产品焊接试板一付。
6.2.4球形封头A类焊缝产品焊接试板一付。
6.2.5产品焊接试板应与相应产品焊缝的焊接同时进行,按相同的焊接工艺,使用相同的焊接材料及相同的焊接坡口型式,由焊接产品的焊工焊接。
6.3产品焊接试板需作如下检查:
a、焊接接头常温拉伸试验,取样1件。
b、焊接接头高温拉伸试验,取样1件。高温拉伸试验温度与设备的设计温度相同。
c、夏比(V形缺口)冲击试验,取2套试样,每套3件
其中一套试样缺口开在焊缝金属上,另一套缺口开在热影响区上,试样温度为+10℃,-20℃。
d、室温焊接接头侧弯试样,取试样2件。
以上a~c条的试验结果应符合3.1.2条的规定,d条应符合JB4708中对Cr-Mo钢的规定。a~d条的试验方法符合JB4708的规定
e、在试板T/4处测量硬度,母材、焊缝金属和热影响各测1点,其值均不得大于220HB。
f、化学成分分析,在焊缝上取样。
6.4热处理验证试板和生产焊接试板除满足上述规定外,尚应符合GB150中有关规定。
7试验和检验
7.1用户检验
用户检验员所检验的项目应包括,但以不限于:
(1)目睹、查核、检查或查询由制造厂所做的试验和检验。
(2)主要尺寸的检查
(3)包装之前对产品质量及其完整性的保管情况以及包装、标记进行外观检查,并检查发运的文件。7.2第三方检验
第三方检验机构根据本技术条件,施工图及有关国家法规、标准、设备制造工艺编制检验大纲,并实施设备制造全过程的监督检验。
7.3制造厂的试验和检验
7.3.1试验和检验的项目和内容
(1)设备正式施焊之前,必须按JB4708进行焊接工艺评定。
(2)焊接工艺评定试板、试样应按JB4708规定。
(3)焊接工艺评定内容按下表:
注:该焊接工艺评定应作四个剖面宏观检查,分别检查焊缝尺寸及接缺陷,不得有裂纹、夹渣、未溶透等缺陷。
7.3.2.3射线检查:
A、B类焊缝热处理前应按JB4730进行射线检查,具体项目如下:
7.3.2.4超声检测:
a、主要受压件应按JB4730进行100%超声检测,具体项目如下:
b、ISR后PWHT前应按JB4730进行100%超声检测,具体项目如下:
c 、PWHT后应按JB4730进行100%超声检测,具体项目如下:
d 、水压试验后应按JB4730进行100%超声检测,具体项目如下:
7.3.2.5磁粉检测(MT)
a、焊接前及焊接操作过程中磁粉检测,标准按JB4730进行,不得有任何裂纹和分层等缺陷:
b、焊后或ISR后磁粉检测,标准按JB4730进行,不得有任何裂纹和分层等缺陷:
c、PWHT后磁粉检测,标准按JB4730进行,不得有任何裂纹和分层等缺陷:
d、水压试验后磁粉检测,标准按JB4730进行,不得有任何裂纹和分层等缺陷:
7.3.2.6渗透检测(PT)
a、焊后或ISR后渗透检测,标准按JB4730进行,不得有任何裂纹和分层等缺陷::
b、PWHT后渗透检测,标准按JB4730进行,不得有任何裂纹和分层等缺陷:
c、水压试验后渗透检测,标准按JB4730进行,不得有任何裂纹和分层等缺陷:
7.3.2.7硬度试验
7.3.2.8水压试验
水压试验介质要求:水的温度不得低于15℃。
7.3.2.9特殊的机械性能试验
设备整体消除热处理后,试板应进行如下试验和检验。
7.3.2.10锻件晶粒度测定:
锻件的晶粒度等级为5级或更细。晶粒度测定方法按YB/T5148的规定。
7.3.2.11锻件非金属夹杂物的检验
锻件非金属夹杂物等级不得大于2.5级,检验方法按GB/T10561的规定。
7.3.2.12尺寸检验
8制造及检验报告要求
设备制造完毕后,制造单位须向用户交付下列检查报告及技术资料。
8.1设备竣工图二套
8.2产品质量合格证明书二份,内容除按《容规》附件三之规定的项目外还应具有如下内容:
8.2.1焊接材料理化检验证明书和复验报告。
8.2.2材料代用单。
8.2.3返修详细记录。
8.2.4硬度检测记录。
9铭牌
设备出厂时应在明显位置安装铭牌,并保证铭牌露在保温层外面。铭牌内容按《容规》规定。
10油漆、包装、运输
设备油漆、包装、运输应符合JB/T4711《压力容器涂敷与运输包装》规定外,尚应符合下列要求:
(1)设备外表面应喷砂彻底除锈后,涂防锈漆两道。但焊接件坡口端不应涂漆,而应涂敷一层容易去除的保护涂层。
(2)所有可拆件,在试组装后单独交货。
(3)所有法兰接口应采用最小厚度为6mm,且与法兰外径相同的钢制盲板和最小厚度为3mm的橡胶垫加螺栓紧固,螺栓要等距分布,法兰上每隔一个螺孔装一个螺栓,但不能小于4只,螺栓直径M16~M20,无法兰接口应用钢制盲套罩住,予以保护和防水。
(4)设备卧置裸装发货,发货时设备直接卧置于车底板上,用木板垫平。
(5)所有可拆件,在试组装后单独交货。
(6)对应法兰及连接螺栓单独装箱。法兰面应涂防锈油后用塑料布包扎牢。
压力容器焊接通用工艺
压力容器焊接通用工艺 QB/YR·HJ·T03-2005 № 编制:巩林廷 审核:姚大宝 批准:王桂明 江苏省工业设备安装公司压力容器制造安装厂
钢制压力容器焊接通用工艺 1.适用范围 本工艺适用于江苏省工业设备安装公司压力容器厂制造安装的压力容器产品的焊接工作。 2.焊接工艺评定和焊工 施焊下列各类焊缝的焊接工艺必须按JB4708《钢制压力容器焊接工艺评定》评定合格。 a.受压元件焊缝; b.与受压元件相焊的焊缝; c.熔入永久焊缝的定位焊缝; d.受压元件母材表面堆焊、补焊; e.上述焊缝的返修焊缝。 施焊下列各类焊缝的焊工必须按《锅炉压力容器压力管道焊工考试与管理规则》的规定考试合格; a.受压元件焊缝; b.与受压元件相焊的焊缝; c.熔入永久焊缝内的定位焊缝; d.受压元件母材表面耐蚀层堆焊。 焊接压力容器的焊工取得合格证后,才能在有效期内担任相应合格项目范围内的压力容器产品焊接工作。持证焊工从事产品焊接时,应严格按产品焊接工艺文件的要求进行操作,不得擅自更改工艺。 3.焊接材料 焊接材料主要系指焊条、焊丝、焊剂、气体、电极等。 焊接材料选用原则 应根据母材的化学成份、力学性能、焊接性能结合压力容器的结构特点和适用条件综合考虑选用焊接材料,必要时通过试验确定。 焊缝金属的性能应高于或等于相应母材标准规定值的下限或满足图样规定的技术要求。对各类钢的的焊缝金属要求如下: 相同钢号相焊的焊缝金属
a.碳素钢、低合金钢的焊缝金属应保证力学性能,且不应超过母材标准规定的抗拉强度的上限值加30MPa。 b.高合金钢的焊缝金属应保证力学性能和耐腐蚀性能。 c.不锈钢复合钢板基层的焊缝金属应保证力学性能,且其抗拉强度不应超过母材标准规定的上限值加30MPa;复层的焊缝金属应保证耐腐蚀性能,当有力学性能要求时还应保证力学性能。复层焊缝与基层焊缝以及复层焊缝与基层钢板交界处推荐采用过渡层。 不同钢号相焊的焊缝金属 a.不同钢号的碳素钢、低合金钢之间的焊缝金属应保证力学性能,且其抗拉强度不应超过强度较高母材标准规范的上限值。 b.奥氏体高合金钢与碳素钢或低合金钢之间的焊缝金属应保证抗裂性能和力学性能。宜采用铬镍含量较奥氏体高合金钢母材高的焊接材料。 焊接材料必须有产品质量证明书,并符合相应标准的规定,且满足图样的技术要求,并按JB4708规定通过焊接工艺评定。进厂时按《焊接材料管理制度》的规定验收或复验,合格后方可使用。 焊接材料熔敷金属硫、磷含量规定应与母材一致,选用GB/T5118标准的焊条,应符合下列要求: a.型号为EXXXX—G的焊条应规定出焊缝金属夏比V型缺口冲击吸收功。 b.铬钼钢焊条的焊缝夏比V型缺口冲击吸收功常温时不小于31J。 c.用于焊接低温钢的镍钢焊条的焊缝金属夏比V型缺口冲击吸收功在相应低温时应不小于34J。 常用钢号推荐选用的焊接材料见表1,不同钢号相焊推荐选用的焊接材料见表2。
压力容器焊接技术要求.
压力容器焊接技术要求
概述 ?1、焊接是压力容器制造的重要工序,焊接质量在很大程度上决定了压力容器的制造质量; ?2、影响焊接质量包含诸多方面内容:焊接接头尺寸偏差、焊缝外观、焊接缺陷、焊接应力与变形、以及焊接接头的使用性能等; ?3、容器产品的设计是获得性能优良的焊接接头的基础:焊接母材的、焊接坡口形式、焊接位置、焊材、无损检测、焊后热处理等的选择,直接关系到焊接质量。
一、压力容器焊接的基本概念 ?1、焊缝形式与接头形式: 从焊接角度看,容器是由母材和焊接接头组成的;焊缝是焊接接头的组成部分。 焊缝有5种:对接焊缝、角焊缝、端接焊缝、塞焊缝和槽焊缝。 焊接接头有12种:对接接头、T型接头、十字接头、搭接接头、角接接头等。 ?2、焊缝区、熔合区和热影响区
?3、焊接性能、焊接工艺评定和焊接工艺规程--压力容器焊接的三个重要环节 焊接性能是焊接工艺评定的基础,焊接工艺评定是焊接工艺规程的依据,焊接工艺规程是确保压力容器焊接质量的行动准则。 ? 3.1、焊接性能:材料对焊接加工的适应性和使用可靠性。 ? 3.2、焊接工艺因素:重要因素;补加因素;次要因素。 ? 3.3、焊接工艺评定: JB4708《钢制压力容器焊接工艺评定》 JB/T4734《铝制焊接容器》 JB/T4745《钛制焊接容器》 ? 3.4、焊接工艺规程:
二、常用焊接方法及特点 ?1、手工电弧焊(SMAW) ?2、埋弧焊(SAW) ?3、钨极气体保护焊(GTAW)?4、熔化极气体保护焊(GMAW)?5、药芯焊丝电弧焊(FCAW)?6、等离子弧焊(PAW) ?7、电渣焊(ESW)
压力容器制造工艺流程
2007年4月,**公司因取《压力容器制造许可证》,需试制一台压力容器。公司决定试制一台自用的储气罐,规格Φ1000×2418×10,设计压力1.78MPa,设计温度40℃,属二类压力容器。通过该压力容器的试制,对压力容器的制造工艺流程有了更深的了解。 工艺流程:下料——>成型——>焊接——>无损检测——>组对、焊接——>无损检测——>热处理——>耐压实验 一、选材及下料 (一)压力容器的选材原理 1.具有足够的强度,塑性,韧性和稳定性。 2.具有良好的冷热加工性和焊接性能。 3.在有腐蚀性介质的设备必须有良好的耐蚀性和抗氢性。 4.在高温状态使用的设备要有良好的热稳定性。 5.在低温状态下使用的设备要考虑有良好的韧性。 (二)压力容器材料的种类 1.碳钢,低合金钢 2.不锈钢 3.特殊材料:①复合材料(16MnR+316L) ②刚镍合金 ③超级双向不锈钢 ④哈氏合金(NiMo:78% 20%合金) (三)常用材料
常用复合材料:16MnR+0Gr18Ni9 A:按形状分:钢板、棒料、管状、铸件、锻件 B:按成分分: 碳素钢:20号钢20R Q235 低合金钢:16MnR、16MnDR、09MnNiDR、15CrMoR、16Mn锻件、20MnMo锻件高合金钢:0Cr13、0Cr18Ni9、0Cr18Ni10Ti 尿素级材料:X2CrNiMo18.143mol(尿素合成塔中使用,有较高耐腐蚀性) 二、下料工具与下料要求 (一)下料工具及试用范围: 1、气割:碳钢 2、等离子切割:合金钢、不锈钢 3、剪扳机:&≤8㎜L≤2500㎜切边为直边 4、锯管机:接管 5、滚板机:三辊 (二)椭圆度要求: 内压容器:椭圆度≤1%D;且≤25㎜ 换热器:DN≤1200㎜椭圆度≤0.5%DN且≤5㎜ DN﹥1200㎜椭圆度≤0.5%DN且≤7㎜ 塔器: DN
压力容器技术规范RevC
120MW热电厂建设项目 (120MW (GROSS) CO-GENERATION POWER PROJECT) 压力容器 (Pressure Vessel) 技术规范 SPECIFICATION 2014年09月
目录 1总则 (1) 2设计依据、设计条件和标准 (1) 3设备运行环境条件 (1) 4技术要求 (5) 5质量保证及考核试验 (8) 6供货范围 (9) 7包装运输 (9) 8技术文件 (10) 9技术服务 (11) 10 附录 (12)
1总则 1.1 本设备规范书适用于巴基斯坦120MW热电厂建设项目的压力容器设计、制造、试验、包装发运和安装等方面的技术要求。 1.2 本设备规范书所提出的是最低限度的技术要求,并未对一切技术细节作出规定,也未充分引述有关标准和规范的条文。供方应保证提供符合本设备规范书和现行工业标准的合格产品及其相应服务。 1.3 如果供方没有以书面方式对本设备规范书的条文提出异议,那么需方将认为供方提出的产品完全符合本设备规范书的要求。 1.4 在签订合同之后,到供方开始制造之日的这段时间内,需方有权提出因规范、标准和规程发生变化而产生的一些补充修改要求,供方应遵守这个要求,具体款项内容由供、需双方共同商定。 1.5 本设备规范书所使用的标准,如遇与供方所执行的标准不一致时,按较高的标准执行。如果本设备规范书与现行使用的有关国家标准以及部颁标准有明显抵触的条文,供方应及时书面通知需方。 2设计依据、设计条件和标准 2.1 设计依据 供方的设计应符合下列文件的要求: 2.1.1《120MW热电厂建设项目通用技术规范书》。这是需方按照和业主的主合同的规定编译的通用技术规范,见附录1。 2.1.2 附录2 为锅炉厂提供的连续排污扩容器外形图,附录3为锅炉厂提供的定期排污扩容器。 2.2标准规范(按照最新版本),包括但不限于以下规范 a)、JB2932《水处理设备制造技术条件》 b)、GB150《钢制压力容器》 c)、TSGR0004-2009固定式压力容器安全技术监察规程 d)、ZBJ98004《水处理设备原材料入厂检验技术条件》 e)、JB2536《压力容器油漆、包装、运输》 f)、JB4730《压力容器无损检测》 2.2.1生产厂家在产品的设计、制造、检验测试及性能考核要求,均应符合国家相关标准及部颁标准,但不限于下列标准,如有更新版本或替代标准,以最新版本或替代标准为准。2.2.2与压力容器有关的所有设备、系统和工程应符合合同签署之日时所知的、设备安装地适用的最新法规、规范和安全规程。 2.2.3各标准之间若发生矛盾时,按较严格的标准执行。 2.2.4投标人应提供设计制造的规范、规程和标准等清单。投标人应列出在选用材料、制造工艺、验收要求中所执行标准的清单。 2.2.5供方所提供的材料及外购设备应符合所应用的标准。 2.2.6仪表、控制装置、执行机构、盘柜、接线盒、电缆及附件、桥架及附件、等的标准和规范,应遵守附录1《120MW热电厂建设项目通用技术规范书》中,“仪表和控制系统要求”部分。 3设备运行环境条件 3.1工程条件及设备运行环境 3.1.1 厂址 The Power Plant Site is located immediately near to existing Fatima Sugar Mill near the city of Sanawan and Multan, in the province of Punjab, Pakistan.It issituated at 75 km of Multan and 425 km of Lahore, the capital of Punjab.The Power Plant will be built close to
16MnDR制压力容器制造技术条件
施工规定 SCEQ 0031-2002 实施日期2003年1月7日 中国石化工程建设公司 16MnDR制压力容器制造 技术条件 第 1 页共 3 页1 总则 1.1 范围 本技术条件适用于材料为16MnDR、设计温度不低于 –30℃的钢制低温压力容器的制造、检验和验收。 1.2 说明 容器的制造、检验和验收,除要满足本技术条件外,还应满足图样、相关技术文件以及GB150附录C的要求。 1.3 规范性引用文件 GB 150 《钢制压力容器》 GB 3531 《低温压力容器用低合金钢钢板》 GB/T 5118 《低合金钢焊条》 GB 6479 《高压化肥设备用无缝钢管》 GB/T 8163 《输送流体用无缝钢管》 JB 4708-2000 《钢制压力容器焊接工艺评定》 JB 4727-2000 《低温压力容器用低合金钢锻件》 JB 4730 《压力容器无损检测》 JB 4744-2000 《钢制压力容器产品焊接试板的力学性能检验》 2 材料 材料类型钢号标准号使用状态冲击温度(℃)冲击功 *(J)板材16MnDR GB3531正火-40≥34 10GB/T8163正火-30≥27管材 16Mn GB6479正火-40≥34锻件16MnD JB4727-2000淬火加回火-40≥34焊条J506RH GB/T5118-40≥34 * 注:考虑到低温材料的焊接会使焊缝金属和热影响区的冲击功较母材实物有明显的降低,为确保容器产品焊接接头的低温冲击性能,容器制造厂在材料定货技术要求中对其低温冲击功指标 应留有足够的裕量。
3 材料要求 3.1 板材 1)超声波探伤,按JB4730-94标准进行,且不低于标准中的Ⅲ级要求; 2)探伤范围: ——当板厚δ>16~20 mm,每批抽检20%,至少一张; ——当板厚δ>20 mm,逐张检查。 3.2 锻件 1)当设计压力≥1.6MPa时,按JB4727中III级锻件要求; 2)其余的一般锻件按II级要求。 4 制造和检验 4.1 受压元件用的板材和管材,制造厂应复验低温冲击性能。 4.2 不得在受压元件上刻划或敲打材料标记及焊工钢印。 4.3 对不作焊后消除应力热处理的容器,不得用锤击等强制手段进行成形或组装。 4.4 低温容器施焊前,应按JB4708-2000进行焊接工艺评定试验。其中冲击试验的试验温度应符合第2条表中规定,焊缝和热影响区的V形缺口试件的冲击功不得低于对母材的要求。 4.5 对焊缝的要求: 1)所有焊缝必须采用全焊透工艺; 2)对接焊缝的余高,不得大于焊件板厚的10%,且不大于3 mm,超高部分应予磨平; 3)接管与壳体内表面应齐平,端部尖角应磨成R=3~5mm的圆角; 4)焊缝表面不得有裂纹、气孔、夹渣、咬边等缺陷,表面不应有急剧的形状变化,应平滑过渡。 4.6 修磨与补焊 1)在机械加工、焊接、组装过程中引起的容器表面损伤(如:划痕、焊疤、弧坑等缺陷)都应磨平; 2)修磨后的厚度,不得小于计算厚度加腐蚀余量; 3)修磨的深度不得大于容器名义厚度的5%,且不大于2 mm; 4)补焊: ——需要补焊的部位,焊前应进行磁粉或渗透检测; ——补焊部位的加强高度应大于1.6mm,然后磨平至母材表面;
5压力容器制造过程及质量检验
许可证编号后4位表示证书到期年份 注: ①为“特种设备设计许可印章”字样; ②为“压力容器或者压力管道”字样; ③为设计单位技术负责人姓名,如“×××”; ④为设计单位设计许可证编号,如(“TS 1210040--2008)“; ⑤为设计单位设计许可证批准日期,如“2005年02月10日“; ⑥为设计单位全称。 (3)总图的审批 TSG R1001-2008 第四十三条(一)“D级压力容器主要涉及文件进行涉及、校核、审核3级签署” D级压力容器“主要涉及文件,包括总转图、设计计算书…” ◆总图的主要内容(14个方面) (1)压力容器名称、类别,设计、制造所依据的主要法规、标准; (2)工作条件:工作压力、工作温度、介质毒性程度和爆炸危害程度等; (3)设计条件,包括设计温度、设计载荷(包含压力在内的所有应当考虑的载荷)、介质(组分)、腐蚀裕量、焊接接头系数、自然条件等,对储存液化气体的储罐应当注明装量系数,对有应力腐蚀倾向的储存容器应当注明腐蚀介质的限定含量; (4)主要受压元件材料牌号与标准; (5)主要特性参数(如压力容器容积、换热器换热面积与程数等); (6)压力容器设计使用年限(疲劳容器标明循环次数); (7)特殊制造要求; (8)热处理要求; (9)无损检测要求; (10)耐压试验和泄漏试验要求; (11)预防腐蚀的要求; (12)安全附件的规格和订购特殊要求(工艺系统已考虑的除外); (13)压力容器铭牌的位置; (14)包装、运输、现场组焊和安装要求。
◆特殊要求(6个方面内容) (1)多腔压力容器分别注明各腔的实验压力,有特殊要求时注明共用元件两侧允许的压力差值,以及试验步骤和试验的要求; (2)装有触媒的压力容器和装有充填物的压力容器,注明使用过程中定期检验的技术要求; (3)由于结构原因不能进行内部检验的压力容器,注明计算厚度、使用中定期检验的要求; (4)对不能进行耐压试验的压力容器,注明计算厚度和制造与使用的特殊要求; (5)有隔热衬里的压力容器,注明防止受压元件超温的技术措施; (6)要求保温或者保冷的压力容器,提出保温或者保冷措施。 2)工艺文件(通常考虑8个方面) ①采购技术要求→材料定额或外购、外协件明细表→采购申请单 ②零部件制造工艺路线、总装工艺流程设计 ③工艺装备明细表→工艺装备设计任务书→工艺装备设计 ④焊接工艺→焊接工艺评定任务书(计划)、焊工资格考试计划 ⑤热处理工艺→热处理分包任务书(必要时) ⑥ NDE工艺(通用工艺、专用工艺)→NDE人员资格考试计划 ⑦耐压试验及泄漏性试验工艺 ⑧喷砂、油漆、包装及运输工艺 其中, 采购技术要求,一般情况下不必编写。 当出现下述情况时,必须由技术部门编写: ①材料标准中提供的可选项,如:交货状态、高温拉伸、腐蚀试验、NDE等; ②技术指标比材料标准高; ③特殊的制造、检验或技术指标要求。 ◆材料定额 ①所有用于产品上的材料 板、管、锻、棒、焊、漆等。 (采购锻件回厂自行加工时,应编制定额;如采购成品法兰等,则应编制外购件明细表) ②辅助用料 永久性或一次性工装、工卡具等。 ◆工艺部门编制的采购文件 采购申请单,附: ①材料定额 ②外购件明细表(一般为标准件、机加工成品件等) ③外协件明细表(热处理、成形等) ④采购技术要求(必要时) ◆零部件制造工艺路线 自制件:逐件编制工序说明书; 外购件:编制清单,提交采购申请单; 外协件:编制工序技术要求,提交采购申请单。
压力容器制造通用工艺规程
压力容器制造通用工艺规程 第四版 宜兴制药设备厂 发布日期2004年9月15日实施日期2004年10月1日 目录 一、关于贯彻实施“压力容器制造通用工艺规程”的通知 二、目录 1 三、编制说明 2 1. T.Z04-01压力容器制造工艺规程 3 2. T.Z04-02材料标记移植工艺规程10 3. T.Z04-03划线下料通用工艺规程16 4. T.Z04-04氧—乙炔切割工艺规程18 5. T.Z04-05空气等离子弧切割工艺规程20 6. T.Z04-06封头圆筒制造通用工艺规程21 7. T.Z04-07压力容器组装工艺规程24 8. T.Z04-08钢制压力容器焊接通用工艺规程27 9. T.Z04-09钢制压力容器焊条电弧焊工艺规程37 10.T.Z04-10钢制压力容器埋弧自动焊工艺规程38 11.T.Z04-11钢制压力容器钨极氩弧焊工艺规程40 12.T.Z04-12碳弧气刨工艺规程41 13.T.Z04-13钢制压力容器焊缝隙返修和修补工艺规程43 14.T.Z04-14管壳式换热器通用工艺规程45 15.T.Z04-15强度胀接工艺规程49 16.T.Z04-16不锈钢压力容器制造管理规定51 17.T.Z04-17晶间腐蚀通用工艺规程54 18.T.Z04-18不锈钢酸零部件膏剂酸洗钝化工艺规程56 19.T.Z04-19钢制压力容器热处理工艺规程 58 20.T.Z04-20水压试验操作规程61
21.T.Z04-21致密性试验操作规程63 22.T.Z04-22气压试验通用工艺规程65 23.T.Z04-23压力容器涂敷运输包装工艺规程67 编制说明 本规程是压力容器制造通用工艺文件的汇编,共23项通用规程。 为了不断改进和发展,对这些规程进行了更新,文件代号有前置代号和后置代号构成,前置代号有通用(TongYong)和制造(ZhiZao)组成,选取汉语拼音中第一个字母通用为T、制造为Z后置代号有年号和文件号组成,。 例T Z 04 01 文件顺序号 年份 制造 通用 压力容器通用制造工艺规程中第一个文件编号为:T.Z04-01 本手册中各规程均由技术科归口解释。 本厂制造的非《容规》控制的容器及其它产品,均可参照本规程执行。 压力容器制造工艺规程 文件号:T.Z04—01 编制说明 1.为使压力容器的制造符合安全技术法规的要求,提高操作人员的工作质量,保证产品质量,根据国家质量技术监督局颁布的《压力容器安全技术监察规程》和GB150-1998《钢制压力容器》的有关规定,结合本厂产品和加工设备的实际情况,特制定本规程。 2.本规程适用于碳素钢、低合金钢容器的制造。 3.由于产品制造中的焊接、探伤、水压试验、气密性试验、油漆、包装等工序已有单项“规程”、“守则”,本规程不再制定。 4.本规程是压力容器制造的基本要求,操作人员必须遵守设计图样和产品工艺过程卡的有关规定,并满足本规程的要求。 5.操作部门对本规程负责贯彻执行,检验部门负责监督检查。 6.本规程由技术科归口并负责解释。 一.矫形和净化 本工艺适用于钢材在划线、下料前的矫形和净化。 1.钢板矫形 钢板不平会影响划线质量、造成切割弯曲,从而影响产品制造质量,因此,钢板在加工制造前必须进行矫形。 1.1手工矫形:将钢板放在平台上,用锤锤击,或用专用工具进行矫形,手工矫形的工 具有大锤小锤及型锤(不得有锤痕)。 1.2机械矫形:将钢板放在专用矫形机(平板机)上进行,钢板纵向大波浪,弯曲也可在 圈板机上进行矫形。 1.3火焰矫形:通常用氧—乙炔火焰加热钢材变红,然后让其快速冷却,使变形得到矫 正。 2.钢板的不平度一般不得超过表1的规定数值。 表1 单位:mm
压力容器技术要求汇总
盛装极度、高度危害(第一组)介质的 压力容器强制性要求 1. 厚度大于或者等于12mm的碳素钢和低合金钢钢板(不包括多层压力容器 的层板)用于制造压力容器主要受压元件时,应按NB/T 47013.3-2015逐张进行超声检测,合格等级不低于Ⅱ级。[TSG 21-2016 p8 2.2.1.4] 2. 受压元件不得采用铸铁。[TSG 21-2016 p10 2.2. 3.1] 3. 受压元件不得采用铸钢。[TSG 21-2016 p10 2.2. 4.1] 4. 耐压试验合格后,应当进行泄漏试验,泄漏试验的种类、压力、技术要求 等由设计者在设计文件中予以规定。[TSG 21-2016 p19 3.1.18] 5. 接管(凸缘)与壳体之间的焊接接头以及夹套容器的焊接接头,应当采用全 焊透结构。[TSG 21-2016 p21 3.2.2.2] 6. 制备产品焊接试件。[TSG 21-2016 p21 3.2.4.1] 7. 管法兰应当按照HG/T 20592~HG/T 20635系列标准的规定,并且选用 带颈对焊法兰、带加强环的金属缠绕垫片和专用级高强度螺柱组合。[TSG 21-2016 p22 3.2.5] 8. 容器壳体A、B类对接接头,进行全部无损检测(RT/UT)。[TSG 21-2016 p23 3.2.10.2.2.2] 9. 所有焊接接头,需要对其表面进行磁粉(MT)或者渗透(PT)检测。[TSG 21-2016 p24 3.2.10.2.2.4] 10. 盛装极度危害介质的碳钢和低合金钢制压力容器及其受压元件,应当进行 焊后热处理。[TSG 21-2016 p25 3.2.11(2)] 11. 石墨制压力容器的试验压力不得低于1.75倍设计压力。[TSG 21-2016 p29 3.3.1.4] 12. 石墨制压力容器应当在不低于设计压力的试验压力下,进行所有接头和连 接处的泄漏试验,试验方法由设计者规定。[TSG 21-2016 p30 3.3.1.5] 13. 石墨制压力容器,设计者应当在设计文件中提出粘接试件的制作要求,并 且规定试样的数量、制备方式、检验与试验方法、合格指标、不合格复验要求等。[TSG 21-2016 p30 3.3.1.6]
压力容器筒体制造通用工艺守则102
压力容器制造、检验通用工艺规程文件编号Q/PV-Q-3-102-2003 第 1 版 筒体制造通用工艺规程第0 次修改修改日期: 第 1 页共8 页 1总则 1.1 本守则依据GB150—1998《钢制压力容器》和GB151—1999《管壳式换热器》标准,以及《压力容器安全技术监察规程》99版,结合我厂设备及技术力量,编制的压力容器筒体制造通用工艺守则。 1.2 由于压力容器种类较多,各种类型之间要求各不相同,因此,本守则若同产品设计或工艺文件有矛盾时,应以产品设计图样设计要求或工艺文件规定为准。 1.3 操作工人必须熟悉图样和工艺文件,对本岗位所使用的设备结构性能和操作规程必须了解。 1.4 筒体焊缝必须由持证合格焊工施焊。 2 材料 2.1 制造筒体用的材料质量及规格应符合《容规》第10条国标、部标及相应的国家标准、行业标准有关的规定,并具有质量证明书,材料上明显部位有清晰、牢固的钢印标志或其他标志。 2.2 属下列之一的主要受压元件材料应复验 2.2.1 设计图样要求复验的; 2.2.2 用户要求复验的; 2.2.3 制造单位不能确定材料真实性或材料的性能和化学成分有怀疑的; 2.2.4 钢材质量证明书注明复印件无效或不等效的。 2.3 需要代用的材料,原则上应事先取得原设计单位出具的设计更改批准文件。 2.4 制造筒体的钢板表面不得有严重锈蚀或裂纹、斑疤、夹层等影响强度的缺陷。 2.5 严禁使用未经检验或检验不合格的材料。 3 筒体加工 3.1 领料 3.1.1 领料人员应根据领料单、图样、工艺过程卡,核对材料规格,材质标记,并在工艺过批准: 审核:编制: 2003.08.15实施
低温压力容器技术要求汇总
低温压力容器技术要求汇总 1. 钢板逐张超声检测 板厚大于20mm的16MnDR、Ni系低温钢(调质状态除外),逐张检查,不低于Ⅱ级合格。(GB150-2011)用于制造低温压力容器筒体、凸形封头和球壳的钢板,厚度超过以下数值时,需按《承压设备无损检测》JB4730.3进行超声检测,且不低于Ⅲ级。(HG/T20585-2011) 板厚大于16~20mm的钢板,每批抽检20%,最少1张。 板厚大于20mm的钢板,逐张检查。(GB150规定质量等级不低于Ⅱ级) 用作低温压力容器筒体的无缝钢管应逐根按《承压设备无损检测》JB4730.3进行超声检测检查。 2. 焊后热处理 球壳板厚度≥16mm的低温球罐应进行焊后整体热处理。(GB12337-1998附录A) 受压元件焊接接头厚度超过16mm时,低温压力容器或部件全部施焊工作完成后,应进行消除应力热处理。热处理工艺应与焊接工艺评定的热处理制度(温度曲线)一致。(HG/T20585-2011) 3. 100%射线或超声检测 设计温度低于-40℃的或者焊接接头厚度大于25mm的低温容器。(GB150-2011) 低温压力容器的对接接头符合下列情况之一者,应经100%射线或超声检测:(HG/T20585-2011) 盛装易爆介质的容器,且设计压力大于0.6MPa者 设计压力大于等于1.6MPa者 壳体板厚大于25mm者 钢材标准规定的最低抗拉强度Rm>540MPa或合金元素含量大于3%的低合金钢。 设计温度低于-40℃者。 C.无损检验方法和评定标准应符合下列要求 对接接头的射线检测按《承压设备无损检测》的规定进行。射线照相的质量应不低于AB级,焊缝质量不低于Ⅱ级为合格(100%检测及局部检测) 焊接接头的超声检测按《承压设备无损检测》的规定进行,无论100%检测及局部检测均应不低于Ⅰ级要求。 焊接接头的TOFD检测《承压设备无损检测》的规定进行,焊缝质量不低于Ⅱ级为合格(100%检测及局部检测)。 4. 磁粉或渗透检测 10.3.1中低温容器上的A、B、C、D、E类焊接接头,缺陷修磨或补焊处的表面,卡具和拉筋等拆除处的割痕表面。(GB150-2011) 设计温度低于-40℃的低合金钢制低温压力容器上的焊接接头。(TSG R0004-2009) 低温压力容器下列部位应按《承压设备无损检测》进行表面磁粉检测或表面渗透检测。(HG/T20585-2011) a.符合本标准第8.7.1条的对接接头,但无法进行射线或超声检测者。 b.符合本标准第8.7.1条的容器壳体上的C类、D类焊接接头以及附件焊接的角接接头、填角焊缝的可及表面。 c.钢材标准规定的最低抗拉强度Rm>540Mpa的高强度钢容器上的全部焊接接头及热影响区表面。 d.受压壳体上工装卡具、拉筋板等临时附件拆除的焊痕表面,焊补前的坡口及焊补的表面以及电弧擦伤处。设计压力大于或等于1.60Mpa,且设计温度低于-40℃的设备法兰用紧固件材料为铁素体钢时,应逐件进行磁粉检测。(HG/T20585-2011)
70BJ 010-2011 铬钼钢复合钢板制压力容器制造及验收工程技术条件
公司标准70BJ010-2011 代替:70BJ010-2005 铬钼钢复合钢板制压力容器 制造及验收工程技术条件第 1 页共 18 页 朱玫张国信李法海陈崇刚2011-04-15 2011-04-20 编制校审标准化审核审定发布日期实施日期 目 次 1 范围 (1) 2 规范性引用文件 (1) 3 总则 (2) 4 材料 (2) 5 制造 (8) 6 无损检测 (12) 7 焊后热处理及水压试验 (13) 8 涂敷和包装运输 (14) 1 范围 本标准规定了最高操作温度不大于440℃且壳体基层板厚不大于100mm,基层材料为 15CrMoR(H)、14Cr1MoR(H)及与此相当的铬钼钢,复层为S11306、S11348、S30403、S30408、S32168、S31603、S31608及与此相当的不锈钢的铬钼钢复合钢板制压力容器在材料、制造、检验以及包装运输等方面的要求。 本标准适用于按GB 150设计的铬钼钢复合钢板制压力容器的制造及验收,不适用于按分析设计标准设计的铬钼钢复合钢板制压力容器的制造和验收。 2 规范性引用文件 TSG R0004-2009 固定式压力容器安全技术监察规程 GB150 钢制压力容器 GB/T223 钢铁及合金化学分析方法 GB/T228 金属拉伸试验方法 GB/T229 金属夏比缺口冲击试验方法 GB/T232 金属材料弯曲试验方法 GB713 锅炉和压力容器用钢板 GB985.1 气焊、焊条电弧焊、气体保护焊和高能束焊的推荐坡口 GB985.2 埋弧焊的推荐坡口 GB/T1184-1996 形状和位置公差未注公差值 GB/T1804-2000 一般公差未注公差的线性和角度尺寸的公差 GB3077 合金结构钢 GB/T 4334 金属和合金的腐蚀不锈钢晶间腐蚀试验方法 GB/T4338 金属材料高温拉伸试验 GB/T5118 低合金钢焊条
试论压力容器制造过程中存在的问题与解决措施
试论压力容器制造过程中存在的问题与解决措施 随着我国工业生产水平的不断提升,压力容器已经成为一种广泛应用的工业设备,对其制造质量提出了更高的要求。压力容器的制造质量对其使用过程有着重要的影响,如果制造质量不符合使用需求,则可能会造成安全事故的发生。基于此,文章主要针对压力容器制造过程中存在的问题以及相应的解决措施进行简单的分析。 标签:压力容器;容器制造;制造质量 压力容器是生产领域中常用的一种设备,尤其是在很多大规模企业生产中有着广泛应用。当前,我国有很多压力容器的制造企业,可以满足不同领域、不同生产要求的压力容器制造。通常压力容器制造需要经过设计、制造和安装几个基本环节,而每个环节都会涉及到相应的工艺和技术,所以要实现对压力容器制造质量的有效控制,就必须要注重每个环节的质量控制,通过有效的管理措施,提升压力容器的制造质量。 1 压力容器的特点 1.1 压力容器的产品结构和参数具有多样性 压力容器在工业生产领域中有着广泛的应用,在制药、化工、石油等领域都发挥着重要的作用。压力容器的品种和结构十分多样,以满足不同生产领域的使用需求,所以在压力容器的参数设计和制造工艺方面也存在很大的差异性。 1.2 压力容器的安全性要求较高 压力容器的制造过程必须要严格按照其应用的标准和规范的要求进行,而且在不同时期、不同领域内的压力容器设计规范方面具有明显的时效性。通常情况下,压力容器内盛装的介质多为易燃、易爆、剧毒等物质,并且在高温、高压的环境下运行,所以对压力容器的安全性有着较高的要求,除了要遵守基本的制造规范和标准之外,还需要根据不同的使用环境和时间要求,制定详细的标准和规范,才能满足压力容器的安全性要求。 1.3 压力容器的制造过程中相似信息的利用 在压力容器的制造构成中会存在很多相似的信息,如容器的外观形状、产品结构以及制造的工艺流程等,都存在着不同程度的相似性,如果可以对这些相似的信息进行有效的利用,便可以节约一定的制造成本,有利于提高制造企业的效益。 2 压力容器制造过程中存在的问题
压力容器标准
压力容器法规、标准介绍 一、压力容器法.规、标准体系 我国的特种设备法规体系主要分以下五个层次 法律—行政法规—部门规章—安全技术规范—引用标准”。 第一层次:法律 根据宪法和立法法的规定,由全国人民代表大会及其常委会制定法律。 如《安全生产法》、《劳动法》、《产品质量法》、《计量法》、《标准化法》、《行政许可法》等; 2012年8月,十一届全国人大常委会第二十八次会议初次审议了《中华人民共和国特种设备安全法(草案)》。 第二层次:行政法规 由国家最高行政机关—由国务院制定的行政法规 《特种设备安全监察条例》(第373号国务院令),2003年3月公布,自2003年6月1日起施行。 2009年1月14日《国务院关于修改(特种设备安监察条例)的决定》(第549号国务院令)公布。 第三层次:行政规章 由国务院各部门制定的部门规章,如: 《锅炉压力容器制造监督管理办法》(总局令第22号)自2003年1月1日起施行; 《特种设备作业人员监督管理办法》(总局令第140号)自2011年7月1日起施行; 第四层次:安全技术规范(规范性文件) 是政府对特种设备的安全性能和相应的设计、制造、安装、改造、维修、使用和检验检测等所作出的一系列规定,是必须强制执行的文件,安全技术规范是特种设备法规标准体系的主体,是在世界经济一体化中各国贸易性保护措施在安全方面的体现形式,其作用是把法律、法规和行政规章的原则规定具体化。 TSG Z0004-2007特种设备制造、安装、改造、维修质量保证体系基本要求 TSG Z0004-2007特种设备制造、安装、改造、维修许可鉴定评审细则 TSG R1001-2008压力容器压力管道设计许可规则 TSG R0004-2009 固定式压力容器安全技术监察规程 TSG R0002-2005 超高压容器安全技术监察规程 TSG R7001-2004 压力容器定期检验规则 TSG R6001-2008压力容器安全管理人员和操作人员考核大纲 TSG R3001-2006压力容器安装改造维修许可规则
压力容器焊接通用工艺
压力容器焊接通用工艺 QB/YRHJT03-2005 编制:巩林廷 审核:姚大宝 批准:王桂明 江苏省工业设备安装公司压力容器制造安装厂
钢制压力容器焊接通用工艺 1.适用范围本工艺适用于江苏省工业设备安装公司压力容器厂制造安装的压力容器产品的焊接工作。 2.焊接工艺评定和焊工 2.1施焊下列各类焊缝的焊接工艺必须按JB4708《钢制压力容器焊接工艺评定》评定 合格。 a. 受压元件焊缝; b. 与受压元件相焊的焊缝; c. 熔入永久焊缝的定位焊缝; d. 受压元件母材表面堆焊、补焊; e. 上述焊缝的返修焊缝。 2.2 施焊下列各类焊缝的焊工必须按《锅炉压力容器压力管道焊工考试与管理规则》的规定考试合格; a. 受压元件焊缝; b. 与受压元件相焊的焊缝; c. 熔入永久焊缝内的定位焊缝; d. 受压元件母材表面耐蚀层堆焊。 焊接压力容器的焊工取得合格证后,才能在有效期内担任相应合格项目范围内的压力容器产品焊接工作。持证焊工从事产品焊接时,应严格按产品焊接工艺文件的要求进行操作,不得擅自更改工艺。 3. 焊接材料 3.1 焊接材料主要系指焊条、焊丝、焊剂、气体、电极等。 3.2 焊接材料选用原则 应根据母材的化学成份、力学性能、焊接性能结合压力容器的结构特点和适用条件综合考虑选用焊接材料,必要时通过试验确定。 焊缝金属的性能应高于或等于相应母材标准规定值的下限或满足图样规定的技术要求。对各类钢的的焊缝金属要求如下:
3.2.1 相同钢号相焊的焊缝金属 a. 碳素钢、低合金钢的焊缝金属应保证力学性能,且不应超过母材标准规定的抗拉强度的上限值加30MPa。 b. 高合金钢的焊缝金属应保证力学性能和耐腐蚀性能。 c. 不锈钢复合钢板基层的焊缝金属应保证力学性能,且其抗拉强度不应超过母材标准规定的上限值加30MPa复层的焊缝金属应保证耐腐蚀性能,当有力学性能要求时还应保证力学性能。复层焊缝与基层焊缝以及复层焊缝与基层钢板交界处推荐采用过渡层。 3.2.2 不同钢号相焊的焊缝金属 a. 不同钢号的碳素钢、低合金钢之间的焊缝金属应保证力学性能,且其抗拉强度不应超过强度较高母材标准规范的上限值。 b. 奥氏体高合金钢与碳素钢或低合金钢之间的焊缝金属应保证抗裂性能和力学性能。宜采用铬镍含量较奥氏体高合金钢母材高的焊接材料。 3.3 焊接材料必须有产品质量证明书,并符合相应标准的规定,且满足图样的技术要求,并按JB4708 规定通过焊接工艺评定。进厂时按《焊接材料管理制度》的规定验收或复验,合格后方可使用。 3.4焊接材料熔敷金属硫、磷含量规定应与母材一致,选用GB/T5118标准的焊条,应符合下列要求: a. 型号为EXXX—G的焊条应规定出焊缝金属夏比V型缺口冲击吸收功。 b. 铬钼钢焊条的焊缝夏比V型缺口冲击吸收功常温时不小于31J。 c. 用于焊接低温钢的镍钢焊条的焊缝金属夏比V型缺口冲击吸收功在相应低温时应不小于34J。 3.5 常用钢号推荐选用的焊接材料见表1,不同钢号相焊推荐选用的焊接材料见表2
(情绪管理)CMR制压力容器技术条件
15CrMoR制压力容器技术条件 1总则 1.1本技术条件适用于主体材料为15CrMoR制的压力容器的制造、检验和验收。 1.2设备的制造按设备施工图、国家标准及本技术条件的各项规定 2制造、检验与验收应遵循的规程、标准、规范: 压力容器安全技术监察规程(1999年版) 钢制压力容器(GB150-1998) 管壳式换热器(GB151-1999) 钢制塔式容器(JB4710-1992) 钢制压力容器——分析设计标准(JB4732-1995) 钢制压力容器焊接规程(JB/T4709-2000) 钢制压力容器焊接工艺评定(JB/T4708-2000) 压力容器无损检测(JB4730-94) 钢制化工容器制造技术要求(HG20584-1998) 压力容器用钢板(GB6654-1996)及第一、二号修改单 压力容器用爆炸不锈钢复合钢板(JB4733-1996) 压力容器用碳素钢和低合金钢锻件(JB4726-2000) 化肥设备用高压无缝钢管(GB6479-2000) 石油裂化用无缝钢管(GB9948-1988) 以上标准及技术要求之间发生矛盾时,按要求严者执行,若与本技术条件发生矛盾时按本技术条件执行。3材料 3.1.0 15CrMoR钢板应符合力容器用钢板(GB6654-1996)及第一、二号修改单的规定。 3.1.1 15CrMoR钢板的化学成分(熔炼分析)应符合如下要求(%):C≤0.12~0.18;Mn:0.40~0.70;Si:0.15~0.40;Mo:0.45~0.60;Cr:0.80~1.20;P≤0.030;S≤0.020; 成品钢板的化学成分允许偏差应符合GB222的相应规定。 钢板的熔炼化学成分分析按炉(罐)号取样。 3.1.2 15CrMoR钢板经正火+回火+模拟焊后热处理后力学性能、工艺性能应符合如下要求: (1)交货状态:正火加回火(回火温度不得低于620℃) (2)拉伸试验: 室温:σb=450~590Mpa; σs≥295Mpa(板厚:6~60mm); σs≥275Mpa(板厚>60~100mm);δ5≥19%(板厚:6~60mm);δ5≥18%(板厚>60~100mm);高温屈服强度σt0.2≥×××Mpa,其中t-设计温度℃,×××按GB150-1998附录F的表F1“钢板高温力学性能值”查取。 (3)冲击试验 试验温度:+10℃夏比(V型缺口)冲击功A KV(横向)三个试样冲击功平均值≥31J,允许一个试样的冲击功低地平均值但不得低于22J。 试验温度:-20℃夏比(V型缺口)冲击功A KV(横向)三个试样冲击功平均值≥27J,允许一个试样的冲击功低地平均值但不得低于19J。 注:①15CrMoR焊接接头的+10℃夏比(V型缺口)冲击功A KV(横向)三个试样冲击功平均值≥31J,允许一个试样的冲击功低地平均值但不得低于22J。15CrMoR焊接接头的-20℃夏比(V型缺口)冲击功A KV (横向)三个试样冲击功平均值≥27J,允许一个试样的冲击功低地平均值但不得低于19J。 ②焊接工艺评定及产品试板均应按此要求验收。 ③15CrMoR焊接接头冲击试验取样要求: a、3套标准试样。每套3件。
最新压力容器制造技术条件 (2)
压力容器制造技术条 件(2)
压力容器制造技术条件FABRICATION SPECIFICATION OF PRESSURE VESSEL
工程名:云南先锋化工有限公司3万吨/年粗粉连续分离提纯项目 PROJECT 设备位号: C-2011 ITEM 设备名称:二甲酚塔釜再沸器 EQUIPMENT 图号:JYR10-52-T01 DWG NO。 设计单位:四川宜宾江源化工机械制造有限责任公司 DESIGNER 1 总则 1.1 本技术条件适用于采用常规设计的管壳式换热器和钢制压力容器。 1.2 容器的制造、检验与验收,除应满足本技术条件外,还应满足图样、GB150- 1998《钢制压力容器》、GB151-1999《管壳式换热器》、HG20584-1998《钢制化工容器制造技术要求》、TSG R0004-2009《固定式压力容器安全技术监察规程》的规定。当以上文件之间或以上文件与本技术条件的要求发生矛盾时,原则上应按严者的要求执行或以书面的形式向我部门提出,由我部门负责解释或提出处理意见。
1.3 本技术条件引用的标准包括标准的修改单,但设备订货合同生效后的标准修改 单除外。 2 材料 2.1 板材 2.1.1 0Cr18Ni9钢板应符合GB/T4237《不锈钢热轧钢板和钢带》的规定,使用状 态为固溶热处理,表面加工质量为1D级。 2.1.2 0Cr18Ni9钢板应按GB/T4334-2008《不锈钢硫酸—硫酸铜腐蚀试验方法》进 行晶间腐蚀倾向试验,试样应进行敏化处理,弯曲试验后,试样表面不得 有晶间腐蚀裂纹。 2.2 锻件 2.2.1 0Cr18Ni9锻件应符合JB4728-2000《压力容器用不锈钢锻件》的规定,使用 状态为固溶热处理。 2.2.2 0Cr18Ni9锻件应按GB/T4334-2008《不锈钢硫酸—硫酸铜腐蚀试验方法》进 行晶间腐蚀倾向试验,试样应进行敏化处理,弯曲试验后,试样表面不 得有晶间腐蚀裂纹。 2.2.3 锻件级别按图样规定。 2.3 钢管 2.3.1 0Cr18Ni9换热管应符合GB13296-2007《锅炉、热交换器用不锈钢无缝钢 管》的规定,使用状态为固溶热处理,表面应进行酸洗处理,换热管应逐 根进行水压试验和涡流探伤检查。 2.3.2 0Cr18Ni9换热管应按GB/T4334-2008《不锈钢硫酸—硫酸铜腐蚀试验方法》 进行晶间腐蚀倾向试验,试样应进行敏化处理,弯曲试验后,试样表面不 得有晶间腐蚀裂纹。 2.3.3 0Cr18Ni9钢管应符合GB/T14976-2002《输送流体用不锈钢无缝钢管》的规 定,使用状态为固溶热处理,表面应进行酸洗处理。 2.3.4 0Cr18Ni9钢管应按GB/T4334-2008《不锈钢硫酸—硫酸铜腐蚀试验方法》进 行晶间腐蚀倾向试验,试样应进行敏化处理,弯曲试验后,试样表面不得 有晶间腐蚀裂纹。 2.4 螺柱和螺母 2.4.1 螺柱和螺母材料应符合相应标准或图样的规定。