八大浪费案例(举例之成型)参考文档
八大浪费案例(组装)

Fire Clip壓合
時間 4.2
人
1
設備 1
Fire Clip裝配&鎖緊
時間 人10
12.7 3
制造過多浪費案例2-現狀描述
目前生產的形式為多機種少批量,因客戶訂單變更導致成品呆滯的 現象時有發生,由此造成製造過剩的浪費非常嚴重!
呆滯庫存數量為:
制
造
1100Kpcs/月
過
剩
平均呆滯時間為:
浪
費
6.5個月
改善前
3人
改善后
等待浪費案例2-現狀描述
風散組裝線由于產線不平衡且測試段是瓶頸,測試段堆 積許多待測風扇,其後工站-包裝存在等待的浪費
在
制
品
浪
31
等待浪費案例2-對策&效果
。對策﹕增加測試機台﹐合理配置人員以消除瓶頸 。效果﹕提高線平衡率和UPPH.
線線平平衡衡率率提提高高 平衡率
UPPH
UUPPPPHH提提升升
將clip檢查作 業和Clip彎曲 檢查作業合并
E
C CRS
S
將Clip彎曲 檢查作業反復 5次簡化壓3次
29
等待浪費案例1-效果對比
壓clip
時間 4.2S
人
1
設備 1
工時
22.1S
25
20
15
10
5
0 改善前
改善后
12.4S
Clip彎曲檢查
時間 8S
人
2
設備 2
30
人力
5人
5 4 3 2 1 0
19
搬運浪費案例1-改善對策
。優化產線布局﹐將部品加工設備直接搬到產 線上來﹐并通過加裝滑槽的方式﹐使加工好的 產品直接流到產線上。
现场改善案例(八大浪费)

4.IE的改善意識(2)
7) 兩人的知識大于一人的智慧﹐全員參與才 可以共同進步﹔ 8) 改善不應大量投資﹔ 9) 積極尋找解決問題的方法而不是不可行的 理由﹔ 10)不要為現狀辯解﹐實事求是﹔
二. 现场IE改善<1>何谓标准工 时
标准时间是指,“一个熟练工用规定的 作业方法以标准速度进行作业时所需的 作业时间”。
基礎IE概論
一. 基礎工業工程概述
二. 现场IE三原则 三. 現場IE改善
四. IE活動的導入與推進
五. 基礎IE改善手法
一.基礎工業工程概述 1.什么是工業工程(IE)?
工業 工程
INDUSTRIAL ENGINEERING
20年代后期﹕起源于美國 80年代初期﹕引進我國大陸
2.IE的定義
“工業工程,是對人員、物料、設備、能源和
搬 运
浪 费
移动费时费力
空间、时间、人力和工具浪费 搬运过程中的放置、堆积、移 动、整理等都造成浪费。
浪费
不良造成额外成本
常见的不良造成的損失: ☆ 材料损失 ☆ 设备折旧 ☆ 人工损失 ☆ 能源损失 ☆ 价格损失 ☆ 订单损失 ☆ 信誉损失
动作
浪费
多余动作 增加强度降低效率
常见的12种浪费动作: ① 两手空闲 ⑦ 转身角度大 ② 单手空闲 ⑧ 移动中变换动作 ③ 作业动作停止 ⑨ 未掌握作业技巧 ④ 动作幅度过大 ⑩ 伸背动作 ⑤ 左右手交换 ⑾ 弯腰动作 ⑥ 步行多 ⑿ 重复/不必要动作
加工 浪费
过剩的加工造成浪费
常见的加工浪费: ☆ 加工余量 ☆ 过高的精度 ☆ 不必要的加工 过剩加工造成的浪费: ☆ 设备折旧 ☆ 人工损失 ☆ 辅助材料损失 ☆ 能源消耗
八大浪费演示文稿(汽车行业)
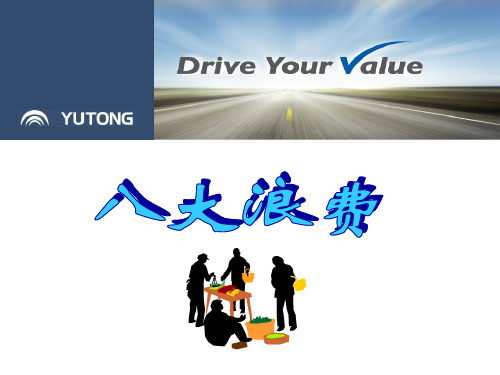
15
3.搬运的浪费
不必要的移动及把东西暂放在一旁
不必要的搬运、工作的移动、预置、改装以及长距离的搬 运流程和活性度差等
表现形式:
•搬运距离很远的地方,小批量的运输 •主副线中的搬运 •出入库次数多的搬运
长距离搬运在制品,
缺乏效率的运输,进 出仓库或在流程之间
搬运原料、零部件或
最终成品。
•破损、刮痕的发生
过多的库存会隐藏的问题点:
•没有管理的紧张感,阻碍改 善的活性化
•设备能力及人员需求的误判 •对场地需求的判断错误 •产品品质变差的可能性 •容易出现呆滞物料
对策:
5.库存的浪费
•库存意识的改革 •U型设备配置
•均衡化生产
•生产流程调整顺畅 •看板管理的贯彻 •快速换线换模 •生产计划安排考虑库存 消化
34
•因不良造成人员及工程增多的浪费
•材料费增加
对策:
7. 不良品的浪费
•自动化、标准作业 •防误装置
•在工程内做出品质保证
原因:
•标准作业欠缺 •过分要求品质 •人员技能欠缺 •品质控制点设定错误 •认为可整修而做出不良 •检查方法、基准等不完备 •设备、模夹治具造成的不良
“三不政策” •一个流的生产方式 •品保制度的确立及运行 •定期的设备、模治具保养 •持续开展“5S活动”
22
4.加工的浪费
因技术(设计、加工)不足造成加工上的浪费
原本不必要的工程或作业被当成必要
表现形式:
•在加工时超过必要以上的距离所造成的浪费
•冲床作业上重复的试模,不必要的动作
•成型后去毛头,加工的浪费 •钻孔后的倒角,纹孔作业的浪费
•最终工序的修正动作
采取不必要的步 骤,以处理零部件; 因为工具与设计不良 ,导致产生不必要的 动作及产生不必要的 瑕疵而造成缺乏效率 的处理;当提供超出 必要的较高品质产品 时,也会造成浪费。
八大浪费案例(举例之成型)参考文档

等待浪費2--現狀描述
模具動作
1.開模 2.頂針頂出 3.頂針退回 4.合模
機械手動作
8
6 15
7
模內2 作業 影3響周4期
1.主臂下降
2.前進 3.夾產品 4.后退
5.主臂上升
6.橫出 7.放產品 8.橫入
19
等待浪費2—對策&效果
製品名稱︰Neo后飾板成型加工 工站名稱︰Neo后飾板成型加工
其他動作 6.6S
1 2 3 4 5 6 7 8 9 10 11 12 13
13.7 14 15
15.9
開模 4S
頂針頂出 1.6S
前進時間 0.5S
頂針退回 1S
等待 3.5S
下降 1.2S 前進取產品 1S 退回,上升 1.4S
合模 6.6S
其他動作 6.6S
2.2S
20
等待浪費2—對策&效果
3
不良修正浪費1--對策&效果
改善對策:
在削毛邊工站後增加一上檢 人員,檢查面板來料不良
改善效不果良: 報廢減少20%
4
不良修正浪費2--現狀描述
F產品銘牌產品用真空盤包裝,裝箱時采用直接疊加方
式,搬運過程中出現碰刮傷,不良率為25%,需投入2人
從事修復作業5来自不良修正浪費2- -對策&效果
改善對策:
26
管理浪費1—對策&效果
1.DT(II)成型加工多功能機械手治具架
快 速 換 線 機 械 手 治 具 架
27
管理浪費2--現狀描述
此為緊急物料﹐由于缺乏有效管制方式﹐頻繁 出現斷料而導致主線出現停線現象
28
管理浪費2—對策&效果
精益生产之八大浪费篇

精益生产之八大浪费篇1)提高质量2)提高生产率3)减少库存4)减少生产线5)减少机器停机时间6)减少空间7)降低生产交货质量管理是不是一个部门或此人,而是对公司的所有成员的共同责任,需要了解的是:从每一个所有小部分来考虑,共同努力,以更好的产品质量知道:下一道工序是客户。
质量是管理出来的,而不是测试出来精益生产质量管理强调从驾驶者对缺陷产品的发生的预防,机械,模具,工具,材料和生产工艺等,以确保没有不良品。
它强调从源头上保证质量■检查每一道工序,对员工的质量意识为重点,发现质量问题如果一个进程的问题■因为在过程中,不能满足需求,生产线立即停止工作,直到问题得到解决■通常是解决问题的个人和集体考虑设计质量标准化的产品结构减少零件数量零件标准化第一次是参与所有工作人员不要隐藏的股票,以稳定的质量什么是质量(辅酶Q)的费用质量成本访问前成本评估成本损失成本内部损失成本外部损失成本自我和互检的工作通常被称为“双重检查”,主要是自我管理的实施。
(1)自我和质证进程的实施一,教育经营者自律,灌输“双检查”的重要性;乙,在现场不定期抽查,监督的“双重检查”的执行情况;C,有一些问题,强调了“双检查”是符合双方的责任有关。
研发,建立明确的问责制,评估和实施奖励和处罚一线主管如何与公司的质量好一)强大的反应能力,以质量和加工能力;二)了解,下一道工序是顾客;三)按标准作业规范;四)车间做自我检查;e)及时汇报和报告异常情况;f)设备,工具,检测设备的正确使用和维护;克)组织材料的控制和环境;八)热爱工作,有高度的责任感;质量改进和提升网站1)设施使用各种灯光,广告牌,以显示正常,生产过程不,提高快速反应能力素质2)质量信息反馈机制的建立异常3质量,工程,采购等部门)紧密合作4)跨部门小组成立,以改善质量5)PDCA循环使用,以改善和提高质量七大手法,以提高现场质量---清单分层法因果图柏拉图直方图控制图分散六标准差工具统计过程控制(SPC),质量功能展开(QFD)失效模式与效应分析(FMEA),因果矩阵(原因和影响矩阵),英国标准(英国标准),过程能力分析(过程能力分析),多变量分析(多可变研究),可靠性(可靠性分析),实验设计(DOE),测量系统分析(MSA),价值链分析(价值链分析),崔京图(单位:kJ方法),流程图(流程图),统计推论(推论统计),(描述统计)描述性统计,鱼骨图,直方图,柏拉图,连通图,采样,控制图,相关分析,回归分析,传播方式,方差分析全因子实验,模块化设计,公差设计,概念工程,舞台/栅工艺,SIPOC(供应商输入过程输出客户),就业选配计划,挥发性有机化合物,筛选研究,假设检验对废物的定义在JIT生产,废物和垃圾的社会影响通常是指不同。
八大浪费及案例(50页)
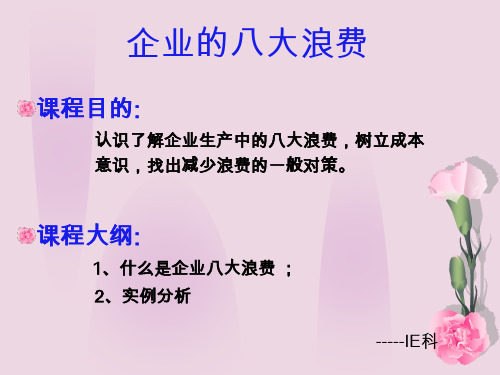
库存的浪费
库存浪费的类型或现象:
成品的库存 零部件、材料的库存
成品库存实例
??
是车间 还是仓 库?
成品库存过多挡住通道
成品库存造成的浪费
成品库存过多不代表资产,没有任何价值 , 只会造成浪费从而增加成本!
成本库存造成的浪费: a.占用保管场所及踏板的浪费; b.造成人员搬运及管理的浪费; c.产品时间长易损坏 d.增加无效成本,造成资金不能灵活流通; e.过剩的在库掩盖了问题的存在
机种切换浪费
虽然转机次数不能减少, 但是每项转机工作的时 间可以缩短,尽可能减到 最短,甚至减到“0”.
改善对策
1. 机种切换浪费
减少机种切换浪费的对策
外部转机的彻底
事前能准备的材料, 治具提前做好准备,交换 出来的材料与治具在机器开始生产后进行整 理.
内部转机的彻底
机器不停下来就没法转机的工作要集中所有 人力, 物力, 用最好的方法进行.
2、通过改善作业位置来消除搬运作业; 3、缩短工位(设备・工程)之间的距离来减少搬运浪费; 3、通过辅助治具来替代人员的搬运作业;
(例如NLP产线MI手插与TUP之间运输夹具的滑轨的使用)
缩短搬运距离
PCB放在线前面
PCB放在机器旁有滑轨的架子上
2.5m
1.2m
用专用架子, 靠近作业区域最近化, 缩短搬运 距离, 节约空间4.6 m2;
管理或人力资源的浪费
所有的事后管理与补救管理浪费 (比如返工;) 对策:在生产过程中就控制好品质;
减少人力资源的浪费 (多能工的培训推广)
理想生产线的构建
1)一个流彻底实施 *移动距离的缩短 *作业标准化 *空间的合理利用 *产量的提升 *不良品的减少
八大浪费及改善技法

1. 管理板 2. 控制投入 3. 过剩生产
24
24
把握状态
消除浪费的步骤
分析原因
寻找消除方法 立即实践
制作小工具 决定维持管理方法
过剩生产
• 按节拍时间,制定标准作业 • 用看板控制序安排方法,重新安排作业
•人员过剩 •设备稼动过剩 •生产浪费大 •业务订单预测有误 •生产计划与统计错误
对策:
•顾客为中心的弹性生产系统
•单件流动—一个流生产线
•看板管理的贯彻 •快速换线换模 •少人化的作业方式 •均衡化生产
注意:
•生产速度快并不代表效率高 •设备余力并非一定是埋没成本 •生产能力过剩时,应尽量先考虑减
对策:
•自动化、标准作业
•防错装置
•在工程内做出品质保证
“三不政策”
•一个流的生产方式
•品保制度的确立及运行
•定期的设备、模夹具保养
•持注续意:开展“5S活动”
•能回收重做的不良
•能修理的不良
•误判的不良
10
➢多余动作浪费
❖是指员工的任何一个对生产流程来说不必要的动作 ❖在一个布局不合理的工位或没有遵循标准化操作的员工,过度
•
•
•
解决方案
• • • •
• • • •
• • • •
•
•
•
•
27
找出浪费因素表(2/2)
我工厂的现状
观察事例
库存
•
•
•
•
•
•
•
•
动作
•
•
•
•
•
•
•
•
班组成本控制之八大浪费
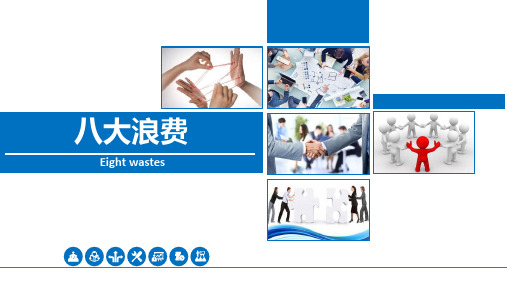
库存之“三不” 不大批量采购 不大批量生产 不大批量搬运
库存的浪费
库存浪费产生的原因: 集群式,大批量生产 供应商不稳定 呆滞物品未及时处理 视库存为当然,生产过剩 无计划/提早生产
对策: 一个流生产方式的设计 快速换模换线实施 供应商管控机制
异常物品处理流程标准制定 库存意识的改革
管理看板运用,产线管理导入
提早生产或生产了过多的、超过客户或下游工序所需要的量
这种浪费被视为 脱离了准时化生产(JIT)的原则,比需要的时候提前生产或生产数量超过了生产计划最必大要的的浪量费而!产生的库存。
由于过量生产掩盖了等待、动作、加工、搬运等浪费,又引起搬运工具、存放托盘增加等2次性浪费。
造成的浪费 ➢工序间积压在制品,交货期变长,过度占用空间 ➢工资提前支付 ➢产品积压造成不良发生 ➢提前用掉了费用(材料费、人工费)而且还增 加了产品的保管费用
实现的方法或手段
行程距离缩短
改善效果或下一步
间距缩短至20mm,花费时间 变为2s,降低3s
动作的浪费
改善前
改善后
现状问题点描述
实现的方法或手段
冲床行程过大,模具冲压时间花费2s
行程距离缩短
改善效果或下一步
冲压行程缩短,花费时间变为 1.5s,降低0.5s
动作的浪费
改善前
换模与生产 时间长
工具不合理 仓库功能区块化
对策:
整流化按工序流程配置设备 不能连接的工序尽可能的靠近 按客户需求设计产能,少人化
一个流生产方式
库存管理三原则(库位、数量、 FIFO)的贯彻,物料车设计 仓库设置在生产线附近 (店铺规划)
搬运浪费
在实际作业中减少搬运浪费的对策
1、通过改善物品的放置位置来缩短搬运距离;(就近放置) 2、通过改善作业位置来消除搬运作业; 3、缩短工位(设备・工程)之间的距离来减少搬运浪费; 3、通过辅助治具来替代人员的搬运作业;
生产现场八大浪费
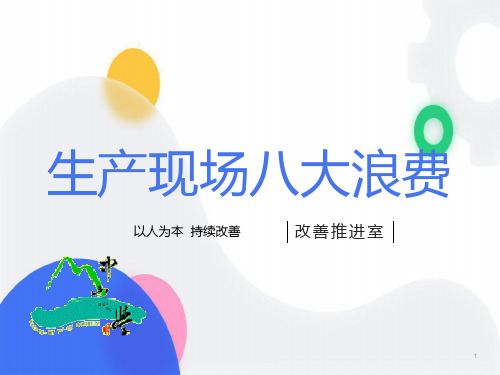
生产现场八大浪费
改善推进室
以人为本 持续改善
学习目标
利润最大化是企业的经营目标!
认识浪费
不同的经营思想
企业每天都在“烧”钱
全面生产系统(5MQS)的浪费
工厂中常见的8大浪费
*
不同的经营思想
成本中心型: 以计算或实际的成本为中心,加上预先设定的利润,得出售价。 计算公式: 售价=成本+利润 卖方市场;消极被动; 企业类别: 高新产品 垄断产品 国内的铁路、民航等
Material(物料)
*
5MQS的浪费
M U D A
分类
浪费
说明
5M
人的浪费
行走的浪费监视的浪费寻找的浪费动作的浪费职责不清的浪费
走一步一秒的浪费CNC操控的无谓监视找寻物品的时间浪费不增值的动作浪费不知自己的职责,人制管理的浪费
材料的浪费
原料的浪费 螺栓的浪费 焊接的浪费 功能的浪费 不良报废的材料
按照“利润中心型”的 思想经营,企业就可以 在竞争中立于不败之地
*
企业每天都在“烧钱”
以下不良现象或浪费在“烧钱” 仪容不整的工作人员; 机器设备放置不合理; 机器设备保养不当; 原材料、在制品、完成品、待修品、不良品等随意摆放; 通道不明确或被占; 工作场所脏污。
好心疼啊!
*
企业每天都在“烧钱”
*
4、搬运的浪费
物品移动所需要的空间浪费; 时间的耗费; 人力、工具的占用; 推车移动……
搬运是一种不产生附加价值的动作;搬运的损失分为放置、堆积、移动、整理等动作浪费.
*
(搬运)举例说明
浪费的产生:
工厂布局:物流路线交叉﹔孤岛﹔工作布局前后工程分离﹔
浪费的消除:
精益生产管理八大浪费与解决方法(详细版)

精益生产管理八大挥霍与解决措施八大挥霍是丰田生产方式中非常重要旳一种观念。
丰田人觉得要消除挥霍,持续改善,公司才干保持良性运转,竞争力才会提高。
在丰田改善是探入人心旳,有个说法就是跟他们谈话5分钟没有听到他们讲3次改善就不算丰田人。
改善旳对象是挥霍,结识挥霍是改善旳第一步,公司现场林林总总,哪些是有价值旳,哪些是挥霍,不是一般人可以一目了然旳。
丰田人在长期作业和改善过程中对于挥霍旳内容进行了总结,共七种,被称为七种挥霍。
它们分别是制造过早(多)旳挥霍、库存旳挥霍、不良修正旳挥霍、加工过剩旳挥霍、搬运旳挥霍、动作旳挥霍、等待旳挥霍共七种。
后来人们又加了一种挥霍-管理旳挥霍,合称八种挥霍。
下面我们从实用性角度剖析这八种挥霍。
一、精益生产管理中制造过早(多)旳挥霍定义:所谓制造过早(多)就是前制程制造太早/过多,大于客户(或后制程)当期旳最小需要量。
制造过早(多)挥霍是八大挥霍中旳首恶,在精益生产中则被视为最大旳挥霍。
福特式思维告诉大家,在同样旳时间内,生产量越多,效率越高,成本越低,公司越赚钱,因此公司自然有大批量持续生产旳初始动力。
作为一种整体旳公司是如此,那么公司内各部门也是如此,特别是在某些制程较短,关联性较低旳公司中,普遍实行计件工资,那么从最基础旳员工开始就有多做、早做,甚至偷做旳动力,在这种状况下,告知公司里所有人早(多)做是罪恶固然得不到掌声回应。
那么我们就来看看制造过早(多)旳挥霍。
制造过早(多)挥霍旳后果重要有三大类。
1.直接财务问题。
体现为库存、在制品增长,资金回转率低,制造时间变长,占用资金及利息,会导致库存空间旳挥霍,在钞票流量表上很明显。
2.产生次生问题。
会产生搬运、堆积旳挥霍;先进先出旳工作产生困难;产品积压导致不良发生,物流阻塞制程时间变长,现场工作空间变小,有滞留在库旳风险,有不良品旳风险。
3.掩盖问题。
为什么“制造过早(多)挥霍是八大挥霍中旳首恶,在精益生产中则被视为最大旳挥霍”?由于它带给人们一种安心旳错觉,掩盖了多种问题,以及隐藏了由于等待所带来旳挥霍,没有改善旳动力,失去了持续改善旳时机。
八种浪费价值工程

额外整车仓储成本 额外整车保养成本 额外整车保险费用 管理成本增加 整车自然折旧增加 外部市场价格降低趋势造成的降价风险 资源和原材料的过量消耗 等等
SGM CONFIDENTIAL
Issue Date: Mar. 2007
p.8
八 种 浪 费-过量生产浪费
SGM CONFIDENTIAL
Issue Date: Mar. 2007
p.30
浪费的识别
过程分析法
将过程分解为多个动作 逐个动作进行分析 查找可消除的浪费
创造价值的作业,需 进一步改善
纯作业
浪费作业
附加作业
价值流图法
用图形的方式呈现材料与信息的流程
消除不必要的作业
改善不创造价值的作业 ,使其作业时间无限接
Issue Date: Mar. 2007
p.13
八种浪费-多余工序浪费
3) Over Processing 多余工序型浪费
SGM CONFIDENTIAL
Issue Date: Mar. 2007
p.14
八种浪费-多余工序浪费
来源:上海金桥北厂油漆
由于侧围后下方 区域在整车装配 时将被外饰覆盖 ,故此区域油漆 可以不喷涂。 改进后可以减少 相应工序,减少 人工和材料。
八种浪费与价值工程
SGM CONFIDENTIAL
Issue Date: Mar. 2007
p.1
八种浪费
八种浪费
SGM CONFIDENTIAL
Issue Date: Mar. 2007
p.2
八种浪费
浪费的定义:浪费是一种不增加价值或是 不提高产品质量的行为---不 能创造出价值的一切活动。
八大浪费案例(举例之成型)
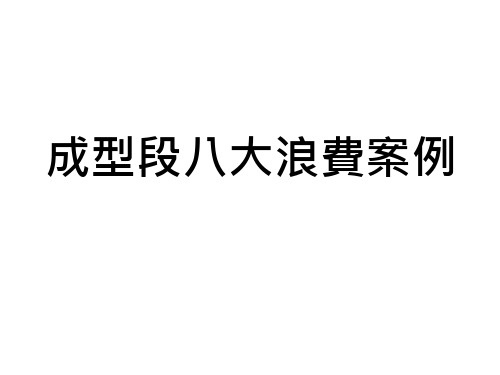
動作分析圖 伸手
擠壓隔板
取出隔板
25
動作浪費2—對策&效果
改善方案﹕ 在隔板著力點增加半圓凹槽方便員工取放隔板
增加半圓凹槽 方便員工取放
動作分析圖 伸手
取出隔板
改善效果﹕ 作業員取放隔板容易﹐降低作業疲勞度
26
管理浪費1--現狀描述
等待 0.降 1.2S 等待 1S 前進取產品 1.7S 退回,上升 1.4S
其他動作 6.6S
1 2 3 4 5 6 7 8 9 10 11 12 13
13.7 14 15
15.9
開模 4S
頂針頂出 1.6S
前進時間 0.5S
頂針退回 1S
等待 3.5S
下降 1.2S 前進取產品 1S 退回,上升 1.4S
13
搬運浪費1--對策&效果
改善對策﹕ 在空間允許情況下﹐采用大膠箱作為線內物流周轉箱
規格為 600(L)*550(W)*400(
H)
改善效果﹕ 可以使生產更為順暢﹐大大減少了搬運次數
14
庫存浪費1--現狀描述
ACER零部件成型裝配流程
一樓成型 ACER裝配領用
一樓移印 一樓暫存
三樓入庫
該流程導致大量庫存和WIP的產生
4.后退
8.橫入
20
等待浪費2—對策&效果
製品名稱︰Neo后飾板成型加工 工站名稱︰Neo后飾板成型加工
A05機台機械手、模具聯合操作分析
機器︰成型機 日期︰2007/11/17 時間單位(S)
改善前
時間
改善后
模具
機械手
0
模具
機械手
開模 4S
頂出延遲 0.5S
- 1、下载文档前请自行甄别文档内容的完整性,平台不提供额外的编辑、内容补充、找答案等附加服务。
- 2、"仅部分预览"的文档,不可在线预览部分如存在完整性等问题,可反馈申请退款(可完整预览的文档不适用该条件!)。
- 3、如文档侵犯您的权益,请联系客服反馈,我们会尽快为您处理(人工客服工作时间:9:00-18:30)。
A05機台機械手、模具聯合操作分析
機器︰成型機 日期︰2007/11/17 時間單位(S)
改善前
時間
改善后
模具
機械手
0
模具
機械手
開模 4S
頂出延遲 0.5S
頂針頂出 1.6S 前進時間 2S 頂針退回 1S
等待 0.2 S
合模 6.6S
等待 4S
下降 1.2S 等待 1S 前進取產品 1.7S 退回,上升 1.4S
加工過剩浪費2--對策&效果
方案
採用氣體輔助成型. 進氣點處增加一BOSS柱
進 氣 點
BOSS 柱
進氣點與輔助 氣道
改善前
改善后
產品重量減少5.2g,C/D金額585,236RMB/年
在根部增加R0.5
12
搬運浪費1--現狀描述
規格為 550(L)*300(W)*350(H)
問題點﹕ 采用小箱子作為線內周轉箱﹐增加了搬運次數﹐導 致生產的不順暢。
13
搬運浪費1--對策&效果
改善對策﹕ 在空間允許情況下﹐采用大膠箱作為線內物流周轉箱
規格為 600(L)*550(W)*400(
H)
改善效果﹕ 可以使生產更為順暢﹐大大減少了搬運次數
14
庫存浪費1--現狀描述
ACER零部件成型裝配流程
一樓成型 ACER裝配領用
一樓移印 一樓暫存
三樓入庫
該流程導致大量庫存和WIP的產生
增加EPE泡棉隔板﹐ 避免產品與真空盤相碰
改善效果:
碰挂傷不良率為0%, 取消兩名重工人員
6
製造過多浪費1--現狀描述
Y機種頂蓋成型裝配線
剪保護膜 11.5S
大量WIP產生
檢查並貼膠 16.3S
產品邊緣外露保護膜
現狀描述:
貼膠工站需要重新調整外露保護膜,以便於貼膠.檢查並重新調
整,導致產品堆積,為裝配線瓶頸工站.
3
不良修正浪費1--對策&效果
改善對策:
在削毛邊工站後增加一上檢 人員,檢查面板來料不良
改善效不果良: 報廢減少20%
4
不良修正浪費2--現狀描述
F產品銘牌產品用真空盤包裝,裝箱時采用直接疊加方
式,搬運過程中出現碰刮傷,不良率為25%,需投入2人
從事修復作業
5
不良修正浪費2- -對策&效果
改善對策:
7
製造過多浪費1- -對策&效果
Y機種頂蓋成型裝配線
改為用小剪刀並檢查 工站時間12.4S
產品邊緣無外露保護膜 貼膠工站減至 9.8S
Y機種組立週期時間降低3.9S
8
加工過剩浪費1--現狀描述
分流道:Ø6.0 主流道:Ø8.0
側進膠
問題 1.料頭部分需二次加工去除. 2.流道尺寸偏大,浪費原料.
通過操作分析,將模具與機械手運行中存在的等待浪費消除
改善前模具打開時間︰15.9 S
模具
機械手
動作
時間(S) 時間(S)
動作பைடு நூலகம்
開模 頂出延遲 頂針頂出 前進時間 頂針退回 等待 合模 工作時間 利用率
4
0.5 1.6 2 1 0.2 6.6 15.9 100%
4 等待 1.2 下降 1 等待 1.7 前進取產品
18
等待浪費2--現狀描述
模具動作
1.開模 2.頂針頂出 3.頂針退回 4.合模
機械手動作
8
6 15
7
模內2 作業 影3響周4期
1.主臂下降
2.前進 3.夾產品 4.后退
5.主臂上升
6.橫出 7.放產品 8.橫入
19
等待浪費2—對策&效果
製品名稱︰Neo后飾板成型加工 工站名稱︰Neo后飾板成型加工
6.6
6.6 其他動作
工作時間
13.7
10.2 工作時間
利用率
100% 74.45% 利用率
21
動作浪費1--現狀描述
D產品為高光鏡面產品,需靜電除塵
雙手動作分析圖 左手 右手
按產品 搖擺風槍
移動 等待
左手需要移次6動6次按!產!!品 搖擺風槍
…
…
移開左手 搖擺風槍
22
動作浪費1--對策&效果
改善對策:
擠壓隔板
取出隔板
24
動作浪費2—對策&效果
改善方案﹕ 在隔板著力點增加半圓凹槽方便員工取放隔板
增加半圓凹槽 方便員工取放
動作分析圖 伸手
取出隔板
改善效果﹕ 作業員取放隔板容易﹐降低作業疲勞度
25
管理浪費1--現狀描述
成型機械手治具
機械手與產品一一對應
1.造成原料浪費 2.需要人力對機械手保存,
造成管理浪費 3.生產時需要尋找對應機械 手更換,造成切換時間浪費
15
庫存浪費1--對策&效果
改善方案﹕ 將現有生產流程進行如下調整
一樓成型
三樓入庫
三樓移印
ACER裝配領用
改善效果﹕實現JIT供料﹐庫存面積減少80%
16
等待浪費1--現狀描述
問題﹕目前作業方式機器和作業員均存在等待現象
17
等待浪費1—對策&效果
改善方案﹕增加周轉治具﹐將機器內部作業轉化為機器外部作 業﹐采用并行工程﹐提高作業員的工作飽和度和機器的嫁動率
自製中空泡棉治具壓住產品
左手按泡棉, 右手搖風槍吹所有產品
改善效果:
➢ 左手不需移動6次;
➢ 作業時間從18.6S降低至11.6S,作業效率提升38% 23
動作浪費2—現狀描述
D產品在包裝時采用層疊方 式﹐中間用矩形紙板隔開
問題點﹕ 由于隔板只比膠箱
略小﹐作業員在取 出隔板時不易取出。
動作分析圖 伸手
29
1.4 退回,上升
6.6 其他動作 10.9 工作時間 68.55% 利用率
改善后模具打開時間︰13.7S
模具
機械手
改
動作 時間(S) 時間(S) 動作
善
開模
前 等待
4
3.5 等待
0
1.2 下降
后 頂針頂出
1.6
0 等待
時 前進時間
0.5
1 前進取產品
間 頂針退回
1
對 等待
0
1.4 退回,上升
比 合模
26
管理浪費1—對策&效果
1.DT(II)成型加工多功能機械手治具架
快 速 換 線 機 械 手 治 具 架
27
管理浪費2--現狀描述
此為緊急物料﹐由于缺乏有效管制方式﹐頻繁 出現斷料而導致主線出現停線現象
28
管理浪費2—對策&效果
• 改善方案﹕ 增加“緊急物料追蹤看板”﹐實行緊急物料
優先處理的方式避免了主線的停線損失。
其他動作 6.6S
1 2 3 4 5 6 7 8 9 10 11 12 13
13.7 14 15
15.9
開模 4S
頂針頂出 1.6S
前進時間 0.5S
頂針退回 1S
等待 3.5S
下降 1.2S 前進取產品 1S 退回,上升 1.4S
合模 6.6S
其他動作 6.6S
2.2S
20
等待浪費2—對策&效果
成型段八大浪費案例
目錄
一 不良修正浪費 二 製造過多浪費 三 加工過剩浪費 四 搬運浪費 五 庫存浪費 六 等待浪費 七 動作浪費 八 管理浪費
2
不良修正浪費1--現狀描述
分檢
削毛邊
貼條碼
裝電源按鍵
裝卡環
貼貼紙 裝銘牌
下檢
包裝
N產品在成型裝配線終檢處,檢查出不良品後, 拆下的卡環/電源按鍵/銘牌修復率僅為7%
9
加工過剩浪費1--對策&效果
改善對策
1.將側進膠改成潛膠口.
改善前
改善后
2.減小流道尺寸,主流道由Ø8.0改到Ø6.0,分流道由Ø6.0改
料頭重量減少8.4g,C/D金額403,189RMB/年
10
加工過剩浪費2--現狀描述
產品肉厚過厚易產生縮水﹐變形等不良。
問題﹕
1.產品肉厚較厚有縮水,變形,尺寸超規. 11